- Фосфорнокислый цинк однозамещенный (монофосфат) Zn2HPO4;
- Азотнокислый цинк Zn(NO3)2;
- Азотнокислый барий, технический Вa(NО3)2, который может быть заменен азотнокислым кальцием Са(NO3)2.
- препарат «мажеф» - 25-30;
- азотнокислый цинк - 35-40;
- фтористый натрий - 5-10;
- температура, °С - 15-30;
- продолжительность, мин - 40.
- монофосфат цинка - 60-70;
- азотнокислый цинк - 80-100;
- азотнокислый натрий - 0,2-1,0;
- общая кислотность, точки - 75-95;
- температура, °С - 15-30;
- продолжительность, мин - 15-25.
- условия повышенной влажности;
- при воздействии горюче-смазочных материалов;
- в средах органических растворителей;
- под напряжением до 1000 В.
- при помощи препаратов «Мажеф»;
- с применением фосфорной кислоты;
- с помощью монофосфата цинка;
- с помощью фосфатирующей пасты.
- 40 г/л фосфорной кислоты;
- азотнокислый цинк – 200 г на 1 л;
- сернокислого натрия 8 г на 1 л;
- окиси цинка – 15 г на 1 л.
- монофосфат цинка в количестве 20 г на 1 л;
- нитрат натрия – 35 г. на 1 л.
- марганец;
- цинк;
- фосфаты железа.
- при чрезмерной влажности;
- под воздействием агрессивных химических растворителей;
- при контакте с моторными маслами;
- при высоком электрическом напряжении;
- в качестве основы под лакокрасочным покрытием.
- кислота фосфорная – не более 40;
- азотнокислый цинк – около 200;
- окись цинка – 15;
- натрий сернокислый – 8.
- Желательно надевать специальные защитные очки.
- Чтобы предотвратить отравление выделяющимися парами проводите работу на улице или в вентилируемом помещении.
- По завершении процедуры следует тщательно вымыть руки, чтобы частицы химикатов не попали на слизистые оболочки глаз, ротовой полости.
- Самый простой способ приготовления фосфатирующей пасты, с помощью которой можно обработать вертикальные участки, следующий: нужно смешать «Мажеф» или самодельный раствор из фосфорной кислоты и азотнокислого цинка с нейтральным наполнителем – тальком, пудрой, каолином. Главное – соблюсти пропорцию (3 части раствора на 2 рассыпчатого вещества).
- В фосфатные растворы можно добавлять обезжиривающие компоненты – это позволит сохранить силы на этапе подготовки к фосфатированию металла. Для этого в 1 л воды необходимо добавить по 45 г нитрата натрия и монофосфата натрия, а также половину столовой ложки моющего средства. Время нахождения детали в фосфатирующей ванне следует увеличить в два раза.
- Чтобы удалить ржавчину с поверхности металла необходимо к фосфорной кислоте добавить сложные полифосфаты. Повысить эффективность приготовленного раствора поможет специальный смачиватель – он очистит поверхность железа.
- Ускоритель фосфатирования – вещество, добавляемое в состав для обработки поверхностей. С его помощью весь процесс занимает минимум времени.
- цинка
- железа
- марганца
- распыление,
- нанесение валиком,
- нанесение кистью.
-
Фосфатирование стали
-
Фосфатирование воды
-
Химическое фосфатирование
-
Черное фосфатирование
-
Цинковое фосфатирование
- твердость. Металлы становятся более устойчивыми к появлению внешних повреждений.
- устойчивость к влиянию электрического тока.
- улучшаются сроки эксплуатации тех или иных металлических изделий, которые были обработаны методом фосфатирования.
- прочность покрытия. Металлы покрываются дополнительной защитной пленкой, которая придает им особые свойства.
- Размеры оцинкованного профлиста
- Оцинковка в рулонах окрашенная
- Оцинковка кузова автомобиля своими руками гальваническим методом
- Линия горячего цинкования
- Гост на цинкование горячее
- Цинкование труб
- Лист оцинкованный профильный
- Оцинкованный рифленый лист
- Цинкование гост
- Размеры профлиста оцинкованного
- Цинковая пластина
Технология фосфатирования металла: химическое, оксидное, цинковое. Цинкование или фосфатирование что лучше
Фосфатирование
Фосфатирование используют для дополнительной защиты от коррозии, улучшения твердости, износостойкости, повышения электроизоляционных свойств основного покрытия на черных и цветных металлах. Суть процесса фосфатирования состоит в создании на поверхности защищаемого изделия слоя малорастворимых фосфатов железа, цинка или марганца.
Фосфатированию подвергаются: чугун, низколегированные, углеродистые стали, кадмий, цинк, медь, сплавы меди, алюминий.
Фосфатированию плохо поддаются высоколегированные стали.
Изделия, подвергшиеся фосфатированию, эксплуатируются даже в тропиках. Фосфатная пленка не боится органических масел, смазочных, горячих материалов, толуола, бензола, всех газов, кроме сероводорода.
Под воздействием щелочей, кислот, пресной, морской воды, аммиака, водяного пара покрытие довольно быстро разрушается. Непродолжительный срок службы покрытия также связан с его низкой эластичностью и прочностью.
Процесс фосфатирования нашел широкое применение в автомобильной промышленности. Фосфатная пленка – наилучший грунт. Стальной корпус автомобиля перед покраской подвергают фосфатированию, а далее окрашивают эмалями.
Фосфатное покрытие
Толщина и структура фосфатного покрытия
Толщина фосфатного слоя составляет от 2 – 8 до 40 - 50 мкм (зависит от режима фосфатирования, подготовки поверхности, состава раствора для фосфатирования). Толщина покрытия связана с его структурой. Мелкокристаллические защитные слои имеют меньшую толщину (1 – 5 мкм) и обладают более выраженной защитной способностью. В связи с этим их намного чаще используют. Получают такие покрытия из цинкфосфатных растворов, которые содержат ускорители (окисляющие элементы). Мелкокристаллические слои не используются в качестве самостоятельных защитных. После получения такого слоя поверхность подвергают дополнительной обработке лакокрасочными материалами.
Крупнокристаллические фосфатные слои более толстые, получают их из марганцевофосфатных растворов. После промасливания могут служить самостоятельными покрытиями.
Кристаллы фосфатов имеют пластинчатую структуру, благодаря чему пленка отлично впитывает различные пропитки, лаки, удерживая их в себе.
Фосфатное покрытие состоит из двух слоев. Первый, плотно прилегающий к поверхности слой, плотно связан с металлом, незначительной толщины, имеет пористую структуру, а также гладкий и достаточно эластичный. Он состоит, в большей части, с монофосфатов железа. Второй слой (наружный) – состоит из монофосфатов марганца, вторичных и третичных фосфатов. Он более хрупкий, кристаллический. Характеристиками именно наружного слоя обуславливается ценность фосфатных пленок.
Цвет фосфатного покрытия
Цвет фосфатного покрытия колеблется от светло-серого до темно серого (почти черного). Светло-серые фосфатные пленки образуются на цветных металлах и малоуглеродистых сталях. Предварительно подвергшихся пескоструйной обработке поверхностях, в растворах повышенной кислотности.
Если чугунное (либо из высоколегированной стали) изделие предварительно подвергалось травлению, и концентрация ортофосфорной кислоты больше обычного - фосфатный слой получается более темного оттенка. Фосфатное покрытие зеленоватого оттенка образуется на поверхности стали, содержащей никель и хром.
Свойства фосфатного покрытия
Полученное фосфатное покрытие может использоваться как самостоятельное защитное, но в большинстве случаев его используют как основу под лакокрасочное, смазочное, либо перед пассивированием. То, что его очень редко используют, как самостоятельное, можно объяснить тем, что оно легко разрушается под воздействием кислот и щелочей.
Фосфатное покрытие не подвергается воздействию кислорода воздуха, смазок, масел, керосина, не смачивается расплавленными металлами. Фосфатный слой может выдержать непродолжительное влияние температуры около 500 °С. Наибольшая минусовая температура, при которой не разрушается покрытие -75 °С. При длительной выдержке фосфатный слой теряет свои защитные свойства и постепенно разрушается.
Фосфатное покрытие отличается высоким электросопротивлением, может выдержать напряжение до 500 В. Чтоб повысить пробивное напряжение готового фосфатного покрытия (до 1000 В) – его дополнительно пропитывают бакелитовыми либо масляными лаками. Фосфатное покрытие по твердости мягче стали, но более твердое, чем латунь или медь.
При щелочном оксидировании стали полученный защитный слой имеет меньшую защитную способность, чем обычные фосфатные слои.
Подготовка поверхности перед операцией фосфатирования играет важную роль, т.к. от ее способа и качества во многом зависят свойства полученного покрытия, а именно – структура, адгезионная способность, толщина, цвет фосфатной пленки.
При фосфатировании заранее протравленной поверхности (с использованием HCl, h3SO4, h4PO4) образуются крупнокристаллические, рыхлые фосфатные слои, толщиной до 40 – 50 мкм. Они обладают достаточно низкими защитными свойствами, поэтому для улучшения качества пленки деталь промывают в 3 – 5 % растворе кальцинированной соды, а далее в воде и затем только фосфатируют. Или же в 1 – 2 % растворе хозяйственного мыла и 5 – 8 % растворе кальцинированной соды при температуре 55 – 60 °С.
Мелкокристаллические, тонкие (толщиной от 5 до 10 мкм) пленки образуются на поверхностях, обработанных пескоструйным методом с последующим обезжириваниям (с использованием органических растворителей или же химическим способом), также механически обработанные кругом, и т.п. Такие фосфатные пленки отличаются хорошей адгезией к поверхности и высокими защитными свойствами.
Суть процесса фосфатирования
Фосфорная кислота (h4PO4) образует три вида солей (именно на свойствах солей фосфорной кислоты и основан метод защиты): дигидрофосфаты, моногидрофосфаты, фосфаты.
Дигидрофосфаты Me(h3PO4)2 – однозамещенные соли, где Me – двухвалентный металл. Образуются сразу при первичном контакте металла с фосфорной кислотой. Взаимодействие описывается реакцией:
Me + 2h4PO4 → Me(h3PO4)2 + h3↑.
При дальнейшем взаимодействии кислоты с металлом (концентрация кислоты уменьшается) образуются двухзамещенные (моногидрофосфаты MeHPO4) и трехзамещенные (фосфаты Me3(PO4)2) соли.
Реакции образования вторичных и третичных солей:
Me(h3PO4)2 ↔ MeHPO4 + h4PO4 - продуктами реакции являются двухзамещенная соль и свободная ортофосфорная кислота;
3Me(h3PO4)2 ↔ Me3(PO4)2 + 4h4PO4 – образуется трехзамещенная соль, свободная ортофосфорная кислота.
Труднорастворимые фосфаты железа – основная составляющая часть фосфатных покрытий. Их качество определяется свободной и основной кислотностью раствора, природой катионов металла, концентрацией монофосфатов.
При введении в раствор для фосфатирования окислительных анионов (например, ClO3, NO2, NO3) процесс формирования защитной пленки значительно ускоряется.
При фосфатировании на поверхности металла наблюдается два основных процесса – осаждение фосфатов и растворение основного металла.
Фосфатирование черных металлов
Сегодня самое широкое применение получил препарат для фосфатирования Мажеф. Выпускается в виде серой массы, расфасованной по бочкам или ящикам. Отличается характерным кисловатым запахом. Название препарата произошло от первых букв его составных частей: марганец, железо, фосфорная кислота.
Фосфатная пленка при использовании данного препарата обладает хорошими защитными свойствами.
Процесс получения фосфатной пленки с использованием данного препарата имеет свои недостатки: высокие температуры, узкий рабочий интервал температур, длительность операции, наводораживание стали (из-за сильного выделения водорода). Чтоб снизить наводораживание уменьшают длительность процесса.
Фосфатирование может быть электрохимическим и химическим.
Химическое фосфатирование черных металлов, в свою очередь, подразделяется на холодное, нормальное и ускоренное.
Холодное фосфатирование
Холодное фосфатирование проводится без подогрева рабочих растворов. Фосфатное покрытие получается довольно тонким и используется в качестве основы под покраску. В основу растворов для холодного фосфатирования входят препарат Мажеф и однозамещенный фосфат цинка (Zn(h3PO4)2). NaNO2 и NaF играют роль активаторов процесса.
Составы для холодного фосфатирования:
Состав №1: 25 – 30 г/л пр. Мажеф, 35 – 40 г/л Zn(NO3)2•6h3O, 5 – 10 г/л NaF, длительность обработки 40 минут;
Состав №2: 60 – 70 г/л Zn(h3PO4)2, 80 – 100 г/л Zn(NO3)2•6h3O, 0,3 – 1.0 г/л NaNO2, продолжительность обработки 15 – 25 мин.;
Состав №3: 100 г/л Zn(h3PO4)2, 6 г/л NaF, 2 г/л NaNO2, длительность обработки 30 - 40 минут;
Состав №4: 18 – 21 г/л ZnO, 80 – 85 г/л h4PO4, 1 - 2 г/л NaNO2, продолжительность обработки 15 – 20 минут.
Если температуру раствора увеличить – можно получить мелкокристаллическое покрытие.
Растворы для холодного фосфатирования довольно быстро гидролизуются (при контакте составных веществ с водой разлагаются основные молекулы и образуются новые соединения), увеличивается свободная кислотность раствора. Это отрицательно сказывается на качестве фосфатного покрытия, т.к. слой получается пористый и с низкими защитными характеристиками. Поэтому холодное фосфатирование используется довольно редко.
Нормальное фосфатирование
Препарат Мажеф, используемый также и при нормальном фосфатировании, имеет химический состав: 2,4 – 2,5 % Fe, 14 % Mn, 46 – 52 % фосфатов, 1 % SO42-, самую малость ионов хлора и CaO, 1 – 2 % h3O.
Однозамещенные соли ортофосфорной кислоты, марганца, железа (MnHPO4, Fe(h3PO4)2, Mn(h3PO4)2) и являются основой препарата.
Наилучший результат фосфатирования дает раствор, содержащий 30 – 33 г/л препарата Мажеф. Температура – 97 – 98 °С. Если вести процесс при более высоких температурах – образуется много шлама, а при более низких – покрытие имеет кристаллическую структуру.
Длительность процесса нормального фосфатирования: время выделения водорода + выдержка около 5 – 10 минут. Кислотность раствора (общая) должна составлять около 30 точек, свободная 3 – 4 точки. (Точка – мера общей и свободной кислотности раствора. Одна точка показывает количество мм 0,2 н. раствора щелочи, израсходованного на процесс титрования 10 мл фосфатного раствора).
Если свободная кислотность превышает указанное значение – ухудшаются свойства фосфатного слоя, а сам процесс затягивается по времени. При уменьшении – полученные пленки слишком тонкие и незащитные.
При повышении концентрации препарата Мажеф до 100 – 200 г/л получают более толстые фосфатные слои с повышенными защитными свойствами и мелкокристаллической структуры. С повышением концентрации немного уменьшают температуру рабочего р-ра (до 80 – 85 °С).
При фосфатировании высоколегированных сталей количество препарата Мажеф составляет около 30 – 32 г/л. Дополнительно вводят 10 – 12 % BaCl2 для улучшения качества фосфатного слоя. Изделие выдерживают в рабочем растворе 45 – 60 минут при температуре около 100 °С.
Ускоренное фосфатирование
Ускоренное фосфатирование получило довольно широкое промышленное применение, т.к. процесс ведется быстрее, чем при нормальном, и имеет свои преимущества.
Длительность процесса ускоренного фосфатирования (с использованием препарата Мажеф) составляет 8 – 15 минут. Рабочий раствор подогревают до температуры 45 – 65 °С (или же 92 – 96 °С, если использовать электролит №2). Дополнительно вводят окислители (NaF, Zn(NO3)2 и др.), благодаря которым ускоряется процесс фосфатирования, выделяется намного меньше водорода и окисляется Fe2+ до Fe3+.
Раствор №1: 30 – 40 г/л препарата Мажеф, 50 – 65 г/л Zn(NO3)2•6h3O, 2 – 5 г/л NaF;
Раствор №2: 30 – 40 г/л препарата Мажеф, 50 – 70 г/л Zn(NO3)2•6h3O, 4 – 5 г/л NaNO3, 0,1 – 1,0 г/л h4PO4.
После ускоренного фосфатирования изделия обрабатывают раствором бихромата калия, а далее – сушат.
Пленки, полученные при ускоренном фосфатировании, небольшой толщины и не отличаются высокими защитными свойствами, поэтому их используют как основу (грунт) для лакокрасочных покрытий.
Ускоренное фосфатирование может проводится и с использованием других растворов, например, цинкофосфатных (основа – первичный фосфат цинка).
Составы для ускоренного фосфатирования с применением цинкофосфатных растворов:
Состав №1: 8 – 12 г/л Zn(h3PO4)2, 10 – 20 г/л Zn(NO3)2•6h3O, 30 – 40 г/л Ba(NO3)2, температура 75 – 85 °С, продолжительность 3 - 10 минут;
Состав №2: 28 – 36 г/л Zn(h3PO4)2, 42 – 58 г/л Zn(NO3)2•6h3O, 9,5 – 15,0 г/л h4PO4, температура 85 – 95 °С, продолжительность 10 – 25 минут.
Покрытия, полученные в вышеописанных электролитах, состоят с Zn3(PO4)2•4h3O и Zn2Fe(PO4)2•4h3O. Большая часть фосфатов образуется на поверхности в первые минуты процесса, когда скорость нарастания фосфатов превышает скорость их растворения. При одинаковых значениях этих скоростей рост фосфатной пленки прекращается.
Ускоренное фосфатирование можно проводить как погружением в ванну с раствором, так и распылением состава на поверхность.
Для струйного ускоренного фосфатирования часто используют раствор на основе препарата Мажеф следующего состава: 30 – 60 г/л пр. Мажеф, 50 – 70 г/л Zn(NO3)2•6h3O, 2 – 4 г/л NaNO2. Температура раствора - 15 – 25 °С, рН 2,6 – 3,2.
Широко используются концентраты для фосфатирования стали (на основе первичных фосфатов), такие, как КФЭ-1, КФЭ-2, КФ-1, КФ-3.
Чтоб улучшить структуру покрытия в основной р-вор вводят оксалаты цинка (до 0,1 г/л). При фосфатировании в таком растворе с поверхности изделия удаляется ржавчина.
Частным случаем химического - является черное фосфатирование. Используется в оптическом приборостроении. Фосфатная пленка черного цвета более привлекательна на вид и более коррозионноустойчива, чем полученные другими способами. Процесс черного фосфатирования состоит с двух частей. Сначала, предварительным фосфатированием, получают черную пленку. Далее, при фосфатном пассивировании, заполняются поры начального слоя.
Электрохимическое фосфатирование
Электрохимическое фосфатирование проводят в растворах схожего состава, но с использованием постоянного либо переменного тока. Это позволяет повысить производительность процесса.
Детали развешивают на катодных штангах, анодами служат пластины (цинк или углеродистая сталь, зависит от состава электролита). Плотность тока – от 0,3 до 3 А/дм2. Продолжительность процесса – от 5 до 20 мин.
Полученные пленки используются в качестве подслоя для лакокрасочного покрытия.
Недостаток электрохимического фосфатирования – низкая рассеивающая способность электролита. Вследствии, на деталях сложной формы фосфатное покрытие ложится неравномерно.
Фосфатирование цветных металлов
Фосфатированию часто подвергают многие цветные металлы. Чаще всего это цинк, магний, алюминий, кадмий, никель, титан.
Фосфатирование титана проводят для повышения его износостойкости, антифрикционных свойств. Процесс ведется при температуре 98 – 99 °С около 10 – 30 минут. Применяемый состав: 10 – 100 г/л ортофосфорной кислоты и такое же количество фторидов (NaF, Nh5F или KF).
Магний фосфатируют в р-рах однозамещенных фосфатов для защиты от коррозии. Фосфатирование магния (как и алюминия) применяют реже, чем его оксидирование.
Для кадмия, алюминия, цинка и большинства цветных металлов фосфатная пленка используется в качестве основы перед нанесением лакокрасочного покрытия.
Алюминий фосфатируют в растворах ортофосфорной кислоты с содержанием CrO3 и NaF или HF. Пленки имеют голубовато-зеленый цвет, поэтому процесс получил название «голубое фосфатирование». Получившийся фосфатный слой тонкий (около 3 мкм), гладкий, аморфный, не отличается высокими защитными свойствами (имеет низкие прочностные характеристики). Состав покрытия таков: около 50 – 55% CrPO4, 17 – 23% AlPO4, 22 – 23% воды. После промывки в холодной воде и сушки при температуре ниже 60 °С фосфатная пленка становится более прочной, может выдержать температуру до 300 °С. Если готовое фосфатное покрытие на протяжении 10 минут обрабатывать в 10 % растворе K2Cr2O7 (при температуре 75 – 80 °С) – его коррозионная стойкость значительно увеличится.
Для фосфатирования кадмия, цинка применяют универсальный цинк-фосфатный раствор. Для получения фосфатной пленки на цинке можно использовать раствор на основе композиции Ликонда Ф1А, обработка ведется при температуре 19 – 40 °С на протяжении 5 – 10 минут. В итоге – на поверхности цинка образуется мелкокристаллическая серо-дымчатая фосфатная пленка с высокими защитными свойствами (лучше, чем при хроматировании).
Никель (его сплавы) фосфатируют только матовый, на блестящем покрытие почти не осаждается. Рекомендованный состав раствора: 15 г/л h4PO4, 13 г/л NaF, 200 г/л Zn(NO3)2. Длительность обработки – 35 – 45 минут при температуре 25 – 35 °С. рН раствора около 2,0.
Улучшение защитных свойств фосфатных пленок
Фосфатные пленки не обладают достаточными защитными свойствами из-за своей пористой структуры, поэтому после получения их еще дополнительно обрабатывают. Для этого применяют пассивирующие растворы K2Cr2O7 (калия дихромат) либо Na2Cr2O7 (натрия дихромат). Процесс ведется при температуре 70 – 80 °С. Пассивирование фосфатных пленок возможно в двух составах: 80 – 100 г/л хромата и 3 – 5 г/л. Для первого раствора время выдержки составляет 10 – 20 минут, и дополнительная промывка до сушки. Для второго – 1 – 3 минуты, после фосфатирования изделие сушат без предварительной промывки.После проведения операции пассивирования готовые изделия пропитывают минеральным маслом (горячим), а далее гидрофобизируют (3 – 5 мин). Для гидрофобизации применяют 10 % раствор в бензине кремнийорганической жидкости ГФЖ-94.Если деталь предназначена для холодной деформации – ее промывают и обрабатывают около 3 – 5 минут при 60 – 70 °С в мыльном растворе (70 – 100 г/л хозяйственного мыла).
www.okorrozii.com
Фосфатирование металла и стали

Фосфатирование следует рассматривать как химический процесс образования фосфорнокислых солей железа, цинка и марганца на поверхности черных металлов. Фосфатирование является одним из самых простых, экономичных и надежных способов массовой защиты от коррозии для деталей из черных металлов, главным образом, для углеродистых и низколегированных сталей и для чугуна.
Основным ценным свойством фосфатной пленки является ее высокая коррозионная устойчивость во всех видах горючих, смазочных и органических масел, в бензоле, толуоле и во всех газах, кроме сероводорода. В очень агрессивных средах, например в щелочах, кислотах, аммиаке, в пресной и морской воде и в водяном паре фосфатная пленка нестойка. 0днако ее коррозионная стойкость может быть повышена во много раз после пропитывания ее смазочными маслами или лаками. Фосфатная пленка является наилучшим грунтом под окраску стальных корпусов легковых машин, которые после штамповки фосфатируют кругом и по фосфатному грунту окрашивают эмалями.
Важным свойством фосфатных пленок, особенно после пропитки их смазочными маслами, является существенное снижение трения при операциях холодного волочения, прокатки и глубокой вытяжки листовой стали. При введении этой операции снижается и потребная мощность оборудования и улучшается качество обработки. Фосфатирование применяется для защиты от коррозии цветных металлов (алюминия, цинка, магния и других металлов) и для гальванических покрытий, но основной областью применения все же является обработка черных металлов.
Высоколегированные стали, особенно хромовольфрамовые, хромованадиевые и стали, легированные медью, фосфатируются с трудом и образуют пленку низкого качества. Нержавеющие стали совсем не поддаются фосфатированию.
При перегибании фосфатированного листа железа на 180° фосфатная пленка дает трещину и осыпается в точках изгиба, но не отслаивается и не допускает дальнейшего проникновения коррозии под пленку. Пластичные кристаллы нерастворимых фосфатов создают высокоразвитую микропористую структуру фосфатной пленки. Поэтому фосфатная пленка хорошо впитывает и прочно удерживает различные лаки, краски и смазки. Пленка обладает высокими электроизоляционными свойствами, которые могут быть повышены путем ее пропитывания специальными изоляционными лаками. Толщина фосфатной пленки колеблется от 7-8 мкм до 40-50 мкм и зависит от вида механической обработки, способа подготовки поверхности к покрытию, а также от состава раствора и режима фосфатирования.
Фосфатирование не изменяет механических свойств стали. Твердость и износостойкость фосфатной пленки невелики. Жаростойкость и электроизоляционные свойства ее сохраняются до 550-600 °С.
Подготовка поверхности к фосфатированию существенно сказывается на качестве фосфатной пленки. Так, детали, имеющие чистовую механическую обработку кругом, фосфатируются с образованием тонкой, мелкокристаллической пленки толщиной до 6-10 мкм. Такие же результаты дает подготовка поверхности посредством очистки металлическим песком, гидропескоочистки и сухой галтовки с песком.
Травление приводит к образованию рыхлой, крупнокристаллической пленки толщиной до 40-50 мкм. Поэтому детали после травления промывают в 3-5%-ном растворе кальцинированной соды, затем промывают в воде и фосфатируют.
Высокотемпературное фосфатирование
Высокотемпературное фосфатирование проводят при температуре от 50 до 98 °С в различных препаратах. Наилучшая по качеству фосфатная пленка образуется при воздействии препарата «мажеф», который выпускается в виде серой массы с характерным кислым запахом и поставляется в деревянных ящиках или бочках. Этот препарат получил название по начальным буквам его составных частей: марганца, железа и фосфорной кислоты. Соответственно составу этого препарата и фосфатная пленка на черных металлах состоит из солей этих металлов, имеет темной серый цвет и пористую, мелкокристаллическую структуру.
Этот вид фосфатирования является наиболее распространенным процессом, так как раствор весьма прост по составу, а получаемая фосфатная пленка наиболее доброкачественна. 0бщепри-нятая концентрация препарата «мажеф» при фосфатировании равна 27-32 г/л. Растворение препарата «мажеф» сопровождается частичным его разложением, с образованием нерастворимых соединений, осаждающихся на дне ванны. Полностью удалять этот осадок со дна ванны нельзя, так как он участвует в образовании фосфатной пленки.
Зарядка ванны препаратом «мажеф» проста и состоит в отвешивании препарата из расчета 30 г/л и в засыпке его в кипящую воду в ванну при механическом перемешивании или барботиро-вании сжатым воздухом.
Для правильной эксплуатации ванны и получения доброкачественной фосфатной пленки необходимо, чтобы фосфатный раствор после зарядки или корректирования имел требуемую кислотность.
При фосфатировании без добавок процесс ведут при температуре раствора 96-98 °С. Для получения заданной температуры раствор доводят до кипения, после чего выключают нагревание и, дав осесть взмученному осадку, загружают деталь. Для поддержания температуры подогревание раствора ведут непрерывно, не давая раствору вскипеть, так как взмученный осадок, поднимаясь со дна, осаждается на поверхности деталей, придавая им грязный серый вид и ухудшая качество фосфатной пленки.
Реакция препарата «мажеф» с поверхностью деталей сопровождается бурным выделением водорода, которое постепенно снижается и заканчивается полностью, когда вся поверхность деталей покроется, без просветов, нерастворимой пленкой.
Для полной уверенности в окончании процесса детали выдерживают в ванне в течение 5-10 мин, после чего выгружают, промывают и сушат.
Продолжительность фосфатирования зависит от назначения фосфатной пленки. Так, при фосфатировании в целях защиты от коррозии, выдержка зависит от марки стали и состава раствора и колеблется в пределах от 15-20 мин до 1 ч. Для электроизоляционного покрытия обычно достаточно 30-40 мин, а для предохранения от затекания расплавленного металла достаточно 20-30 мин.
Приспособления для завешивания деталей при фосфатировании изготовляют из углеродистой стали. Мелкие крепежные детали фосфатируют в железных сетчатых корзинках (достаточно глубоких) для удобства перетряхивания деталей и устранения непокрытых участков. При наличии большой программы мелкие детали загружают в стальные перфорированные барабаны и фосфатируют в ваннах при их вращении, как это делается при гальванических покрытиях.
Корпус ванны фосфатирования сваривают из листового железа, без футеровки внутри. При подогревании паром ванну снаружи футеруют теплоизоляционной массой или обшивают деревом. В этом случае глухой паровой змеевик делают съемным и располагают его по задней стенке ванны, но ни в коем случае не по дну. Все указанные требования связаны с тем, что через несколько дней паровые змеевики, даже при их расположении вертикально, вдоль задней стенки ванн, покрываются твердой коркой нерастворимых фосфатов. Эта корка непрерывно увеличивается и в результате настолько затрудняет теплопередачу, что процесс нагревания до необходимой температуры удлиняется до нескольких часов, а затем достижение рабочей температуры становится невозможным. Именно поэтому корректировщик фосфатных ванн должен внимательно следить за длительностью нагревания и своевременно останавливать ванны для текущей очистки змеевиков. Для этой цели удаляют из ванны съемный змеевик, обрубают зубилом или молотком корку фосфатов и отбивают эту корку со стенок и дна ванны, после чего монтируют змеевик и заряжают ванну.
Для изготовления змеевиков применяют фосфористую бронзу, латунь или некелированные, или хромированные стальные трубы. Возможно также покрытие стальных змеевиков фторопластом.
Более удобен электрический нагрев ванн. Для этой цели наружный стальной кожух ванны футеруют внутри огнеупорным кирпичом, располагая нагревательные элементы вдоль стенок ванны, а корпус ванны делают съемным для удобства ремонта. Удаление водорода и паров воды производят посредством бортовых вентиляционных отсосов, а верх ванны после загрузки деталей закрывают крышкой.
Весьма экономичным мероприятием является покрытие зеркала ванны слоем поплавков из пустотелого полиэтилена или пенопласта.
Удельный расход препарата «мажеф» составляет 120-140 г на метр квадратный фосфатируемой поверхности. При фосфатировании деталей с большой поверхностью корректирование раствора производят после выгрузки каждой партии деталей. При накоплении на дне ванны большого количества осадка, мешающего нормальной эксплуатации ванны, раствор сливают, осадок вычищают из ванны и производят вновь зарядку ванны.
Помимо препарата «мажеф» при высокотемпературном фосфатировании применяются составы на основе следующих компонентов:
При фосфатировании крупных деталей применяются электролиты, состав (г/л) и режимы обработки представлены в табл. 5.18.
Фосфатированные детали пассивируют раствором двухромовокислого калия концентрацией 2-3 г/л и сушат. Фосфатная пленка имеет светло-серый цвет, толщину 8-10 мкм, мелкокристаллическую структуру, обладает электроизоляционными свойствами и пригодна в качестве грунта под окраску или промасливание.
Низкотемпературное фосфатирование
Низкотемпературное фосфатирование можно использовать в качестве грунта под окраску, применяется следующий состав (г/л) и режим обработки:
Этот состав также используют для грунтовки перед окраской, с повышением концентраций препарата «мажеф» до 50-60 г/л и азотнокислого цинка до 50 и даже до 90 г/л. Фосфатная пленка имеет темно-серый цвет, мелкокристаллическую структуру и обладает хорошей сплошностью.
Указанный раствор в смеси с тальком в соотношении 3:2 применяют для фосфатирования больших поверхностей. Эти растворы можно наносить кистью. Для получения надежных результатов нанесение раствора производят трехкратно, с промежуточными сушками на воздухе. Затем детали промывают струей воды и раствором двухромовокислого калия концентрацией 23 г/л и сушат.
Таблица 5.18. Составы электролита и режимы работы.
Компоненты |
I |
II |
Монофосфат цинка |
8-12 |
35-37 |
Азотнокислый цинк |
10-20 |
52-53 |
Азотнокислый барий |
30-40 |
- |
Ортофосфорная кислота |
- |
15-16 |
Температура, °С |
75-85 |
85-95 |
Продолжительность, мин |
3-10 |
15-20 |
Следует отметить, что фосфатирование в указанных и прочих холодных растворах дает хорошие результаты лишь для деталей, обработанных кругом механически или посредством пескоструйной очистки. Травленая поверхность черных металлов непригодна для этой цели.
Фосфатирование для защиты от коррозии всех деталей, кроме тонкостенных, 1 и 2-го классов точности типа пружин производится в следующем растворе (г/л) и режиме работы:
После фосфатирования детали пассивируют в растворе хромового ангидрида концентрацией 0,1 г/л в течение 1 мин при 50-70 °С. Пленка имеет серый цвет и применяется в качестве грунта под окраску.
Электроизоляционное фосфатирование
Фосфатная пленка всегда обладает высокими электроизоляционными свойствами. Особенностями электроизоляционного фосфатирования является специальная подготовка поверхности к покрытию и контроль электроизоляционных свойств. Так, при фосфатировании статорного и трансформаторного железа, ленты и прочих деталей, изготовленных из кремнистых, электротехнических марок листового железа, необходимо прежде всего удалить окись кремния, покрывающую после проката всю поверхность листа. Для этой цели пластины, штампованные из листа, монтируют в приспособлениях так, чтобы они располагались вертикально, с минимальными зазорами для смывания раствором, затем детали обезжиривают в горячем щелочное растворе, промывают и стравливают окись кремния в растворе соляной кислоты плотностью 1,19 г/см3 с добавкой 5%-ного раствора фтористого калия или натрия и 5 г/л уротропина при 15-25 °С в течение 10-15 мин.
После травления детали промывают в холодной проточной воде, пассивируют их поверхность погружением в раствор кальцинированной соды, промывают и завешивают в ванну для фосфатирования. В тех случаях, когда толщина фосфатного слоя не сказывается на точности сборки машин, фосфатирование ведут в горячем растворе соли «мажеф» концентрацией 30 г/л в течение не менее 30-40 мин. При этом толщина фосфатной пленки достигает 15-20 мкм. Фосфатированные детали промывают в холодной проточной воде, пассивируют в течение 10 мин в горячем 5-10%-ном растворе двухромовокислого калия, снова промывают в горячей воде и сушат. Фосфатная пленка имеет серый цвет, мелкокристаллическую структуру.
Электроизоляционные свойства проверяют при заданном давлении груза, удельная величина которого в каждом отдельном случае определяется техническими требованиями. Для получения тонкой электроизоляционной пленки толщиной, не превышающей 7-10 мкм, применяют фосфатирование в растворе с добавками монофосфата и азотнокислого цинка, описанных выше.
Возможно Вас так же заинтересуют следующие статьи: comments powered by HyperCommentsecm-zink.ru
Фосфатирование металла: преимущества и методы обработки
Проблема защиты металлов и сплавов от коррозионных процессов встала еще с тех пор, как люди научились добывать металл из руды. Технологии производства значительно изменились и стали более современными, однако коррозия все равно разрушает изделия и конструкции. Для защиты металлических поверхностей применяют покрытие цинком, но это не обеспечивает максимальной защиты. Современная промышленность применяет более совершенный способ защиты от неблагоприятных воздействий – фосфатирование металла. С помощью данной технологии можно не только сберечь изделие или поверхность, но и получить повышенную износостойкость материала.
Что такое фосфатирование
Технология предполагает обработку металлических поверхностей специальными растворами, в основе которых лежат фосфорнокислые соли. В результате образуется прочная защитная пленка. Среди видов фосфатирования наиболее популярный метод – нанесение фосфатирующих грунтов. Также применяют и гидроабразивную, и химическую обработку металлов.
Фосфатная пленка позволяет в несколько раз улучшить защитные характеристики и срок эксплуатации лакокрасочного покрытия. За счет низкой электропроводности пленка также улучшает адгезию и препятствует подпленочным коррозионным процессам. Нередко технология применяется на изделиях перед покраской по порошковой технологии.
Фосфатная пленка легко выдерживает воздействия органических веществ – это различные масла, смазочные и горячие материалы, любые газы, кроме сероводорода.
Данная технология позволяет обрабатывать чугун, низколегированные, а также углеродистые стали. Фосфатные покрытия могут наноситься на цинк, кадмий, медные сплавы, алюминий. Фосфатируют и высокоуглеродистую сталь. Но, несмотря на свои высокие защитные качества фосфатное покрытие может разрушиться под воздействием щелочей, морской воды, пара воды, кислоты, пресной воды, а также водяного пара.
Защитная пленка образуется за счет окунания изделия в специальную ванну, где находится фосфатирующий раствор. Также можно наносить покрытие методом распыления в струйной камере. В зависимости от состава растворов, на поверхности могут образовываться фосфаты с хорошо выраженной кристаллической решеткой или же без нее.
Кристаллическая пленка оседает из раствора с катионами тяжелых металлов, а аморфную пленку получают из раствора кислых фосфатов щелочных металлов или кислого фосфата аммония.
С помощью фосфатирования металлы можно длительно эксплуатировать в тяжелых условиях, таких как:
Основные методы обработки
Получить защитную фосфатную пленку можно разными способами, а выбор конкретного метода очень зависит от детали, которую нужно обработать, а также от области применения детали или конструкции. В промышленности чаще всего применяются следующие способы фосфатирования:
Препаратом «Мажеф»
Это не что иное, как химическое фосфатирование, при котором деталь окунается в ванну со специальным раствором. Химической обработке подвергают низкоуглеродистые стали. Чаще всего данный способ применяется для подготовки металлоконструкций и изделий под покраску для получения надежных антикоррозийных грунтов.
Мажеф — это сочетание марганца, железа и фосфора. Продукт напоминает соль или порошок зеленоватого цвета.
Концентрация раствора в ванне – не более 40 г на 1 л. Чтобы получить пленку химическим методом, изделие помещается в готовый состав, который подогревают и доводят до температуры кипения. Рекомендуется периодическое помешивание. Кипятят ванну в течение 15-20 минут. Этого вполне хватит, чтобы сталь покрылась слоем защитной пленки.
Чтобы при помощи химического способа получить высококачественную пленку, толщина которой составляет от 5 до 10 мкм, необходимо предварительно тщательно подготовить поверхность при помощи абразивной очистки или с использованием пескоструйного аппарата.
Состав рекомендуется готовить с некоторым избытком, так как в процессе нагревания часть его испарится. Общая кислотность устанавливается при помощи титрования по фенолфталеину. Уровень свободной кислотности можно выяснять при помощи индикаторов метилоранжа.
На видео: фосфатирование солью Мажеф.
Фосфорной кислотой
Фосфорную кислоту используют для получения покрытия холодным методом. Чтобы процесс фосфатирования протекал максимально стабильно, температура раствора должна находиться в диапазоне 18-25 градусов. Чтобы добиться покрытий с высоким качеством и прочностью, нужно четко соблюдать количество действующих ингредиентов. В промышленности применяется следующая концентрация:
В данном растворе деталь или конструкции из металлов обрабатывают в течение 30 минут. Этого вполне достаточно, чтобы на поверхности образовались фосфаты.
Технология подойдет для обработки больших деталей посредством струйного метода. Данный вариант по сравнению с фосфатированем в ваннах дает возможность значительно снизить продолжительность процесса, а также уменьшить расход материала.
Метод с монофосфатами цинка
Данная технология применяется для защиты металлов, которые будут применяться в электрической отрасли, а также на машиностроительных производствах. Поверхность или деталь помещают в раствор из следующих веществ:
Процесс фосфатирования проходит при температуре раствора 60 градусов. Для покрытия металлов плотной фосфатной пленкой необходимо около 20 минут. Для проведения процесса также нужна ванна.
Что касается качества покрытия, то фосфатные пленки аналогичны по характеристикам тем, которые получают с использованием раствора Мажефа. Так можно обеспечить высокую степень защиты любому металлу.
Для обработки оцинкованных сталей лучше применять раствор, в котором используется сернокислый цинк, азотный цинк, фосфорная кислота, фтористый натрий. Процесс проводят при температурах около 60 градусов, а длительность его составляет до 20 минут. В данном растворе можно обрабатывать цинк, углеродистые стали, никель.
Обработка фосфатирующими пастами
В данном случае применяются специальные фосфатирующие грунты. Преимущество в том, что можно выполнять фосфатирование стали и других сплавов при комнатной температуре. Смесь наносится на поверхность детали с помощью обычной кисти. Для обработки не нужны ванны, а это значит, что такому фосфатированию можно подвергать материалы в домашних условиях. Этот способ часто используют автовладельцы и автопроизводители.
В составе грунта металлический пигмент, а также растворитель, в основе которого лежит ортофосфорная кислота. В краске чаще всего содержится цинк. При взаимодействии с ортофосфорной кислотой продукты коррозии укрепляются, создавая прочный защитный фосфатный слой.
Фосфатирующая паста широко применяется для обработки поверхностей деталей из черных и цветных сплавов любых размеров. Прогрунтованные поверхности пассивируются, что также улучшает их адгезионные качества.
Фосфатирование в домашних условиях
Нередко появляется нужда в фосфатировании различных деталей в домашних условиях. Чаще всего используется фосфатирование алюминия, но также можно обрабатывать разные виды сталей и не только. Технология домашнего получения фосфатных покрытий немного отличается от промышленной – полноценная химическая обработка для многих недоступна. Преимущественно используется электрохимическая обработка.
Для получения защитных пленок нужен постоянный либо переменный ток. В роли электролита используются растворы фосфорной кислоты или раствор «Мажеф». Деталь, которую нужно покрыть фосфатами, ставят на электрод, опущенный в ванну с кислотой. В качестве анода применяются цинковые стержни, к которым также подсоединяют электрический ток.
Чтобы получить качественный результат, достаточно напряжения в 25 В. Процесс получения пленки займет около 30 минут. Метод идеально подойдет для различных деталей прямолинейной формы. Объемные геометрические изделия таким методом обрабатывать сложнее, так как на сложную деталь слой ляжет неравномерно, что снизит ее защитные качества.
С помощью технологии фосфатирования можно надежно защитить металлические изделия от разрушительного воздействия коррозии. Многие способы доступны в домашних условиях, что очень важно – дома многие работают с различными металлами и хотят, чтобы детали имели большой срок службы.
Получение состава из подручных средств (1 видео)
Разные материалы для антикоррозийной защиты (18 фото)
gidpokraske.ru
цинкование, фосфатирование, хроматирование, анодирование, меднение, кадмирование.
В настоящее время в любых работах все реже используется крепеж без покрытия, т.к. большинство организаций предпочитают покупать покрытые, а не "черные" крепежные изделия. Это происходит потому что помимо механического воздействия на детали существует воздействие окружающей среды, которое негативно влияет на внешний вид и некоторые характеристики изделия. Процесс, при котором происходит разрушение детали при контакте с внешней средой называется коррозией. В соответствии с ГОСТ 1759.4—87 для крепёжных деталей предусмотрены различные покрытия. Выбор вида покрытия для определенного материала выполняется по ГОСТу. Толщина покрытий (устанавливается по согласованию) выбирается в зависимости от шага резьбы.
Если говорить о защитных свойствах покрытий, то стоит обратить внимание на то, что покрытие может обеспечивать механическую и электрохимическую защиту. При этом, анодные покрытия обеспечивают и механическую и электрохимическую защиту, а катодные - только механическую. Кратко расскажем о разнице анодных и катодных покрытий: покрытия, которые выполнены из материала, потенциал которого отрицательнее потенциала защищаемого металла, называются анодными, катодные же покрытия те, у которых потенциал более положителен, чем у защищаемого металла.
Существуют различные покрытия изделий из металла, которые применяются с целью изоляции изделий от агрессивной среды. Опишем наиболее распространенные из них. Цинкование представляет собой нанесение на металлическое изделие цинка, либо его сплава с целью придания его поверхности требуемых химических и физических свойств, самое важное их которых - сопротивление коррозии. Основные методы цинкования:• Окраска (холодное цинкование)• горячее цинкование • Гальваническое (нанесение гальванических покрытий)• Напыление цинка (цинкование напылением, газо-термическое)• термодиффузионное цинкование Фосфатирование - это химический процесс, при котором происходит взаимодействие компонентов фосфатирующего раствора с поверхностью металла. Фосфатирование металла обеспечивает требуемую степень защитных свойств лакокрасочных покрытий. В результате тормозится развитие подплёночной коррозии, а также существенно улучшается адгезия покрытия к металлу. Хроматирование представляет собой химическое пассивирование электролитически оцинкованных деталей, суть которого состоит в кратковременном погружении деталей в раствор сильных окислителей. В результате хроматрования на поверхности оцинкованной детали образуется прочная плотная плёнка оксидов цинка, что значительно улучшает устойчивость её к коррозии. Анодирование — это процесс создания на поверхности металлов и сплавов оксидной плёнки при помощи их анодной поляризации в проводящей среде. Меднение представляет собой процесс нанесения гальваническим методом медного покрытия на стальные изделия. Как правило, используется для защиты участков металлических изделий от цементации. Этому процессу подвергаются те участки металлического изделия, которые подлежат последующей обработке резанием. Кадмирование - это процесс нанесения на поверхность металлических изделий кадмиевых покрытий при помощи метода электролитического осаждения. Целью данного процесса является защита от атмосферной коррозии изделий. Также такое гальваническое покрытие используют в декоративных целях с целью придания приятного внешнего вида поверхности.
rskrepeg.ru
Фосфатирование металла в домашних условиях
С тех пор как люди научились изготовлять металл, перед человечеством встал острый вопрос обеспечения защиты полученной продукции от разрушения коррозией. Ржавчина – главный враг любой металлической поверхности и по сей день. Многолетнее усовершенствование способов и средств, предназначенных для предотвращения коррозии, несомненно, позволило достичь невероятных результатов в борьбе с естественными химическими процессами. И все же гарантировать стопроцентную неподверженность коррозии невозможно.
Можно ли обработать металл самому в домашних условиях?
На сегодняшний день среди доступных способов защиты железных материалов от влияния разрушительных факторов стоит отметить фосфатирование. Металл после проведения соответствующей химической реакции приобретает повышенную износостойкость, что позволяет значительно продлить срок его прямой эксплуатации.
Лучшей защитой железа от ржавчины и гнили является покрытие его поверхности тонкой, едва заметной пленкой. В домашних условиях фосфатирование металла кажется сложнейшей задачей, относящейся к разряду невыполнимых. Действительно, ведь только в промышленных цехах имеется необходимое оборудование, требуемые реагенты. На самом же деле при соблюдении комплекса правил и условий достичь желаемого результата сможет любой человек, не имеющий профессионального технического образования.
Реагенты, которые понадобятся для фосфатирования
Дополнительным преимуществом домашнего фосфатирования является его универсальность: прочная защитная пленка образуется на поверхностях практически любых сплавов, за исключение высоколегированной стали. Кроме того, поверхностный слой отлично сцепливается с основанием железной заготовки. В качестве материалов для фосфатирования металла используют:
Преимущества фосфатной обработки железа
Современные технологии нанесения фосфорнокислого химического состава позволяют покрывать металлические поверхности с минимальной толщиной – не более 5 микрометров. Такой способ обработки железа предотвращает его разрушение и обеспечивает защиту от внешнего воздействия, гарантируя продолжительное использование металлического изделия в любых условиях, в том числе:
Фосфатирование металла под покраску обеспечит надежную защиту материалу, однако при попадании в кислотную или щелочную среду изделие по-прежнему останется уязвимым. К тому же при окрашивании любой железной поверхности лакокрасочные материалы намного глубже проникают в слои защитной пленки, обладающей высоким уровнем пористости. Улучшенная адгезия поверхности сплавов – еще один положительный момент, позволяющий сказать да фосфатированию перед покраской металла.
Технология и методика промышленного фосфатирования
Прежде чем приступать к нанесению пленочного слоя, важно разобраться в составе среды, в которую будет помещено железо. Технология фосфатирования металла с последующим окрашиванием лакокрасочным веществом не подходит для домашнего осуществления. С помощью препарата «Мажеф», раствором которого наполняют огромные емкости на предприятии, железо покрывают тончайшим, но очень прочным и практичным слоем. Полностью помещенное в фосфатирующую ванну металлическое изделие нагревают до предельных температур и кипятят на протяжении получаса. После этого железо достают, пленке дают полностью застыть, укрепиться, по окончании процесса поверхность гальванизируют с помощью абразивных или пескоструйных аппаратов.
Использование вышеуказанного метода можно назвать оправданным только в случае обработки крупногабаритных конструкций. Подобные услуги по фосфатированию металла, оказываемые в промышленных металлопрокатных цехах, обойдутся заказчику в приличную сумму.
Как обработать металл дома: «холодная» гальваника
Для гальванизации некрупных изделий целесообразнее прибегнуть к элементарной технологии. Речь идет о фосфатировании металла ортофосфорной кислотой, приготовление которой доступно даже в домашних условиях. Для успешной реакции следует придерживаться правильной концентрации химических элементов. Далее указаны составляющие раствора в соотношении количества вещества (в граммах) на 1 литр воды:
Процедура не займет много времени – на приготовление раствора и непосредственную химическую реакцию потребуется порядка получаса. Одним из основных требований, которого стоит придерживаться в ходе обработки железа, является правильная концентрация раствора и его температура (не менее +18 °C и не более +25 °C). Данный способ позволяет получить холодное фосфатирование металла в домашних условиях, однако его качество значительно уступает обработке железного изделия с помощью препарата «Мажеф» - максимальная толщина полученной пленки, как правило, не превышает 5 мкм.
Электрохимическое фосфатирование железных деталей
Большинство технологий по обработке металлических изделий, не заслуживших популярности на производстве, успешно используются любителями. Таковой является и электрохимическая обработка железа, подразумевающая покрытие поверхности надежной пленкой за счет электролитной реакции и тока. В основе принципа действия данного способа лежит использования фосфорной кислоты или препарата «Мажеф».
На железную заготовку, подлежащую фосфатированию, устанавливают электрод. Конструкцию опускают в ванную с приготовленным заблаговременно раствором, а в качестве анода используют цинковые стержни – к ним также необходимо подвести электричество. Чтобы качественно обработать металл вовсе не обязательно прибегать к использованию высоковольтной сети, достаточно 25 V переменного или постоянного электрического тока.
«Мажеф» - лучший состав для грунтовки металла перед покраской
Процедура фосфатирования длится недолго – в среднем, до получаса. Данная техника является идеальной для обработки прямолинейных некрупных изделий. Для предметов с более сложной геометрической конструкцией следует выбирать иной способ фосфатирования железа во избежание неравномерного распределения гальванизирующей пленки. Используемый на производстве и в домашних условиях «Мажеф» является высококачественным грунтовым составом, обладающим всеми сертификатами и соответствующий ГОСТу. Фосфатирование металла автомобильного кузова – одна из самых распространенных причин использования вещества. Чтобы уберечь машину от ржавчины, «Мажеф» наносят даже в тех местах, где, как заведомо известно, краска долго не продержится (к примеру, на днище автомобиля).
Чтобы приступить к обработке металла, с поверхности устраняют грязь, пыль, частицы битума и досконально обезжиривают ее. Рабочую смесь приготовить можно и самостоятельно, но существенно сэкономит время и позволит равномерно распределить состав аэрозольная форма выпуска. При этом некоторые реагенты наносят на обрабатываемое железо с помощью кисти. Но этот способ распределения не подходит при отсутствии опыта работ по грунтованию поверхностей – крайне важно проследить за равномерностью нанесения фосфатного состава.
Рекомендации по использованию фосфатных составов
При обработке мелких металлических деталей с «Мажефом» возможным становится и горячий способ наслоения защитной пленки. Альтернативой приобретенному составу можно считать смесь азотнокислого цинка и фосфорной кислоты. В ходе приготовления массы нельзя ни на секунду забывать об осторожности и элементарной технике безопасности:
Завершающая обработка после фосфатирования деталей
Как правило, фосфатирование металла в домашних условиях не является окончательным этапом обработки изделия. Поскольку пористость структуры гальванической защитной пленки может повлиять на ее дальнейшую функциональность и эксплуатационные свойства, металлическую поверхность пассивируют. В качестве растворов, обеспечивающих гладкость и ровность покрытия, используют калия дихромат или натрия дихромат. В процессе финишной обработки металла крайне важно не упустить температурные показатели: предметы с фосфатными пленками погружают в 80-градусные растворы и выдерживают их не менее 20 минут. После пассивирования изделия обрабатывают машинным маслом, после чего используют раствор из бензина и кремнийорганической жидкости в соотношении 1:10.
Как проверить качество защитной пленки на металле?
Показателем того, что полученное покрытие соответствует заявленным характеристикам, считается его мелкокристаллическая структура и минимальное количество пор. На производстве учитывается также удельная масса нанесенного слоя: вес пленки не должен превышать трех граммов на 1 кв. метр. Нормальное фосфатирование (обработка металла происходит при температурах кипения) позволяет получить крепкое покрытие, толщина которого может достигать 7 мкм, а при холодном типе воздействия гальванизирующий слой выходит меньшей толщины, а значит, обладает более низким качеством.
Несколько советов по фосфатированию: что нужно знать?
Для успешного фосфатирования металла вне производственных цехов важно обратить внимание на следующие моменты:
Фосфатная обработка железных конструкций из любого сплава
Учитывая, что одновременное проведение нескольких процессов фосфатирования металла является весомым преимуществом не только в промышленности, но и в быту, данная отрасль может стать потенциальным направлением к усовершенствованию существующих технологий гальваники. Помимо финансовой экономии, которая является очевидной при домашнем фосфатировании, такая обработка железа имеет ряд других достоинств. Например, фосфатные составы способны защитить от разрушения не только черные, но и цветные сплавы (медь, кадмий, алюминий и т. д.).
Чтобы уберечь металл от ржавчины, вызываемой наружными факторами, климатическими условиями, его обрабатывают сразу же после приобретения. В случае размещения обработанных железных изделий в помещении с чрезмерной влажностью на их поверхности может образоваться голубоватый налет – никакой опасности самому металлу он не несет, а на практике нередко приобретает декоративное значение.
fb.ru
Технология фосфатирования металла: химическое, оксидное, цинковое
Во многих отраслях промышленности технология фосфатирования применяется для защиты черных и цветных металлов от коррозии и увеличения срока их эксплуатации. Наиболее популярен этот метод в автомобилестроении. У обработанных деталей, покрытых тонким слоем фосфатов железа, марганца или цинка, повышаются электроизоляционные свойства и прочностные характеристики. Однако защитная пленка недостаточной толщины довольно быстро разрушается под воздействием пресной или морской воды, водяного пара и различных кислот. Поэтому, обычно, после фосфатирования, метизы проходят процесс окрашивания специализированными эмалями.
Фирма "ГалСервис", занимающаяся нанесением различных гальванических покрытий, готова предложить своим клиентам услуги по различным современным способам химического фосфатирования металлов и многие другие виды работ.
В основе химического фосфатирования металлических изделий лежит разогретая смесь солей марганца, железа и фосфора. Сокращенно этот препарат называется Мажеф. Процесс обработки деталей в специальной стальной ванной в среднем занимает 1-1,5 часа. Толщина фосфатного слоя может составлять от 2 до 50 мкм. Все зависит от обрабатываемой поверхности и состава подготовленного раствора. Стоит отметить, что слой толщиной в несколько мкм пригоден только в качестве основы под лакокрасочные покрытия. Более толстые пленки могут служить как самостоятельные защитные покрытия. Они способны выдерживать непродолжительное влияние температуры до 500 °С и сохранять свои свойства при минусовых температурах.
Если в смесь Мажефа добавить окислители (азотнокислые соли кальция или бария), то можно получить бесщелочное оксидирование (или оксидное фосфатирование). Покрытие, нанесенное в результате такой обработки, считается более прочным. Антикоррозийные и адгезионные свойства оксидно-фосфорной пленки значительно превосходят свойства других защитных пленок.
Процесс бесщелочного оксидирования проходит при 80 градусах за 15-20 минут. После нанесения покрытия, детали просушивают горячим воздухом или сразу же опускают в нагретое масло. Готовые изделия приобретают темный, почти черный цвет, и сохраняют свой металлический блеск.
Наряду с оксидным фосфатированием широкое распространение получила технология фосфатирования металлов с помощью цинка. На поверхность изделия вещество наносится путем иммерсии (погружения), напыления или их комбинацией. Процесс цинкового фосфатирования, по сравнению с другими способами нанесения антикоррозионных покрытий, требует больше этапов обработки. Он включает в себя предварительную очистку металла, промывку водой, нанесение защитной пленки. После изделие необходимо еще раз промыть: сначала водой, затем – кислотой. Это улучшит сцепление поверхности с лакокрасочными изделиями.
Цинковое фосфатирование дает наилучший защитный эффект, но в реализации процесс нанесения защитного слоя стоит дороже остальных технологий. При данном методе обработки на поверхности металлического изделия образуется покрытие кристаллической структуры. Пленка толщиной в 7-8 мкм способна выдерживать напряжение 300–500 В, благодаря своему высокому удельному электролитическому сопротивлению, и обеспечивать работоспособность металлических конструкций до 400–500 °С.
Подробнее обо всех видах работ, сроках выполнения заказов и стоимости различных услуг Вы можете узнать у наших менеджеров. Закажите обратный звонок, и мы ответим на интересующие Вас вопросы.
adamant74.ru
Фосфатирование металла, стали, виды и преимущества
Фосфатирование поверхности
Сегодня для защиты металлических изделий от образования коррозийного налета применяется большое количество способов. Все они направлены на то, чтобы создать на поверхности тонкий защитный слой, который будет длительное время защищать от процесса окисления металла. Обработка металлов фосфатирующими растворами является эффективным методом борьбы с образованием ржавчины.
Для проведения процедуры фосфатирования необходимо изначально провести подготовку металлов или металлических изделий. Для того чтобы вещества раствора лучше адгезировались нужно тщательно обезжирить и промыть поверхность, которая будет подвергаться обработке. Только в этом случае покрытие будет качественным и продержится достаточно длительное время. При необходимости металлический материал перед процедурой можно отшкурить при помощи наждачной бумаги.
Фосфатирование металла
Фосфатирование представляет собой один из самых действенных методов борьбы с ржавчиной. Данный способ обработки
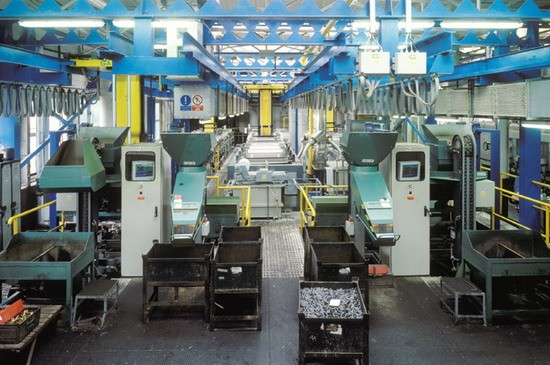
металлических покрытий относится к разряду дополнительных. Этот метод основан на том, что металлы при погружении в фосфатирующее вещество покрываются его компонентами. Они оседают на поверхности и образуют дополнительную защитную пленку.
Процедура фостфатирования металлических покрытий позволяет наилучшим образом подготовить их к нанесению лакокрасочного покрытия. Данная мера позволяет металлу реже подвергаться образованию коррозии. Данный метод походит для дополнительной обработки и черный и цветных типов металлов.
Фосфатирование металлов в промышленных масштабах осуществляется путем распыления или погружения изделий в вещество.
Оно изготовлено из:
Данные элементы образуют единое вещество, которое при взаимодействии другими металлами адгезируется с ними и обеспечивает надежную защиту от процесса окисления и образования коррозии.
На многочисленных промышленных предприятиях данный метод подразумевает качественное нанесение раствора на металлические изделия.
Делается это несколькими способами:
Процесс фосфатирования не занимает много времени. После проведения такой процедуры необходимо дать изделиям из обработанных металлов просохнуть.
На сегодняшний день данная процедура обработки доступна для различных элементов. Фосфатирование стали подразумевает нанесение на поверхность изделия из данного материала фосфатирующего вещества. Благодаря этому на поверхности металла образуется дополнительная защитная пленка, которая практически никак внешне не заметна.
Для обработки барабанный котлов применяется фосфатирование воды. В этом случае вода с растворенными в ней фосфатами вводится в барабан.
Важно: У данного метода есть большое количество противников Не рекомендуется его использовать, когда котел нагревается.
Таблица 1: Пригодность фосфатирования как основы для нанесения лаковых покрытий на различные металлические поверхности
Тип фосфатированияОбрабатываемые металлические поверхностиСтальОцинкованная стальАлюминийКислое щелочное фосфатирование | + | + | + |
Цинковое фосфатирование | + | + | + |
Низкоцинковое фосфатирование | + | + | + |
Mn модифицированное низкоцинковое фосфатирование | + | + | + |
Никелевое фосфатирование | o | + | - |
Цинко-кальциевое фосфатирование | + | o | - |
Пояснения: + - пригодно; o - условно пригодно; - -непригодно
Виды фосфатирования
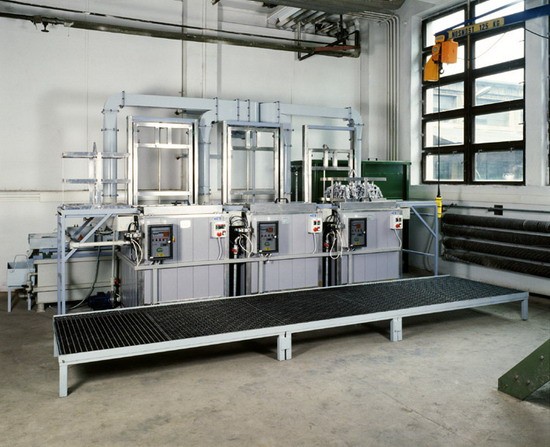
Сегодня имеется большое количество видов фосфатирования.
Из них выделяются следующие:
Данная процедура применяется по отношению к тем металлам, которые обладают не прочной структурой. Среди них выделяются: алюминий, низколегированная сталь и магний, цинк. К одному из подтипов химического фосфатирования относится аморфоное фосфатирование. Для поведения данной процедуры используются фосфаты железа.
Данный процесс обработки металлических изделий относится к разряду декоративных. Он предполагает образование на их поверхности пленки черного цвета. Она является достаточно плотной и придает любому изделию дополнительную прочность.
Процесс обработки металлов цинковыми фосфатами и сплавами данного металла является одним из самых действенных методов укрепления структуры любого металла. В результате покрытие обладает оптимальной толщиной и приятным серебристым оттенком.
Преимущества фосфатирования
Фосфатирование используется в большинстве случаев для придания металлическим поверхностям дополнительной защиты от образования коррозийного налета. Благодаря фосфатирвоанию металлы приобретают следующие положительные качества:
Процедура фосфатирования на производственных предприятиях не используется так часто, как анодирование, например.
lkmprom.ru