- Разгрузка металлоизделий, входной контроль основного металла, химикатов, металлов, конструкций и деталей.
- Дробеструйная очистка. Применяется перед травлением для очистки неподготовленного металла от прокатной окалины и ржавчины. Очистка увеличивает скорость травления. Она также используется после травления – для удаления оставшихся после травления окалины и травильного шлама с наружной и внутренней поверхности труб и изделий, а также для насечки с целью создания шероховатой поверхности, улучшающей адгезию цинка и стали и, как следствие, увеличение срока службы цинкового покрытия.
- Обдувка воздухом после дробеструйной очистки применяется для удаления с поверхности металлопроката остатков дроби и пыли.
- Монтаж металлоизделий на подвесы или технологические кассеты.
- Обезжиривание. На этом этапе происходит удаление с поверхности металлоизделий и конструкций жировых пятен, масел и других синтетических загрязнений, замедляющих и ухудшающих процесс травления, а также снижающих адгезию цинка.
- Промывка. Горячая и холодная промывка металлоизделий водой, при которой происходит смыв твердых металлических частиц с поверхности цинкуемых изделий и предотвращение переноса обезжиривающего раствора в последующие ванны.
- Травление является важным этапом подготовки поверхности металлоизделий для горячего цинкования, при этом происходит удаление с поверхностей деталей остатков ржавчины и окалины, а также химическая активация поверхности металлоизделия (удаление окисной пленки) без ее повреждения.
- Промывка в холодной воде для смыва остатков кислоты.
- Флюсование осуществляется путем погружения изделий в крепкий водный раствор подогретого флюса с последующим его осушением перед внесением в оцинковочную ванну. Поверхность изделий после флюсования покрыта равномерным серым кристаллическим налетом. Это окончательный этап подготовки поверхности, который необходим для нанесения защитного слоя на поверхность покрываемых металлоизделий. Во время флюсования удаляются оксиды, и не образуются на поверхности металла до цинкования.
- Сушка. При сушке происходит удаление влаги с поверхности конструкций. Нагрев изделий происходит до температуры 100-120°С. Этот этап служит температурной подготовкой для процесса горячего цинкования.
- Нанесение защитных обмазок для защиты резьбы и участков под сварку (сварка оцинкованных деталей вредна для сварщика) там, где это необходимо.
- Горячее цинкование. Формирование цинкового покрытия за счет реакции между поверхности металлоизделия и цинком, которые вместе формируют сплав. Температура расплавленного цинка около 450°С.
- Охлаждение. После выгрузки изделий из ванны цинкования производится их охлаждение в ванне с водой или воздушное охлаждение.
- Зачистка металлоконструкций. На участке производится зачистка изделий от наплывов, снятие защиты, калибровка резьбы, отверстий.
- Контроль качества. Контроль качества цинкового покрытия. Осуществляется в соответствии с ГОСТ 9.307-89 "Покрытия цинковые горячие" визуальными и приборными методами. По требованию заказчика производится маркировка и комплектование оцинкованных изделий.
- Ванна для обезжиривания (14,8х1,5х2,2м) 1 шт.
- Ванна для травления (14,8х1,5х2,2м) 6 шт.
- Ванна для удаления цинка (14,8х1,5х2,2м) 1 шт.
- Ванна для промывки после травления (14,8х1,5х2,2м) 1 шт.
- Ванна флюсования (14,8х1,5х2,2м) 1 шт.
- Сушильная камера 2 шт.
- Ванна цинкования (14,5х1,5х2,2м) и печь для плавления цинка 1 шт.
- Охлаждающая ванна
- Ванна пассивации
- Кабина удаления и вытяжки «белого дыма» 1 шт.
- Пульт управления 1 шт.
- Канал удаления дымовых газов
- Экономайзер горячих газов
- Вентилятор дымовых газов
- Генератор горячего воздуха
- Рабочая площадка
- Оборудование для регенерации и обезжелезивания флюса 1 шт.
- Кабина сбора кислотного тумана с устройством вытяжки кислотного тумана 60 000 м3/час, промывочная башня кислотного тумана, трубопровод РРН замкнутых путей до промывочной башни 1 шт.
- Установка нейтрализации отработанной кислоты 1 шт.
- Транспортировочная платформа на рельсовых путях 1 шт.
- Кран-балка однорельсовая 4 шт.
- Емкости с запасами свежей кислоты 4 шт.
- Разгрузочная площадка
- Кран-балка двухрельсовая 2 шт.
- Система очистки «белого дыма» и удаления пыли 1 шт.
- Машина для сбора цинкового шлака с поверхности ванны цинкования 1 шт.
- Цинковый насос 1 шт.
- холодное цинкование покраской
- цинкование напылением (газотермическое напыление цинка)
- гальваническое цинкование
- термодиффузионное цинкование
- горячее цинкование
- подготовка поверхности (очистка, травление, сушка)
- нанесение покрытия
- сушка
- нанесение защитного слоя (лака, краски)
- Автоматизированная линия горячего цинкования рулонной стали, состоящая из следующего основного оборудования:
- Автоматизированные линии полимерного или лакокрасочного покрытия оцинкованной рулонной стали, в том числе состоящие из следующего оборудования:
- Разматыватель
- Электросварочная машина с правильными роликами для сшивки полосы
- Вертикальный петлевой накопитель полосы
- Секция подготовки полосы
- Нагревательная печь
- Валковая машина для нанесения грунтовки
- Печь для затвердевания грунтового покрытия
- Валковая машина для нанесения лакокрасочного покрытия
- Печь для затвердевания лакокрасочного покрытия
- Ламинатор
- Вертикальный петлевой накопитель полосы
- Наматыватель
- Автоматизированные линии горячего цинкования стальной проволоки, в том числе состоящие из следующего оборудования:
- Разматыватель проволоки
- Секции электролитического обезжиривания
- Секции промывки
- Печь отжига (восстановления)
- Секции охлаждения
- Секции флюсования
- Секции сушки
- Ванны горячего цинкования
- Секции удаления излишков цинка
- Секции охлаждения
- Наматыватель проволоки
- Линии горячего цинкования металлоконструкций, включающие следующее оборудование:
- Кран-балка с траверсой для перемещения металлоконструкций
- Ванна предварительной подготовки металлоконструкций
- Секция химической подготовки металлоконструкций
- Ванны обезжиривания
- Ванны травления
- Ванны промывки
- Ванны флюсования
- Печь осушки металлоконструкций после флюсования
- Плавильная печь
- Электронагреватели
- Ванна цинкования
- Ванна пассивирования и охлаждения
- Система упаковки
- 1 шт. ванна обезжиривания
- 3 шт. ванна травления
- 1 шт. промывочная ванна
- 1 шт. ванна флюсования
- 1 шт. ванна для промывки сита
- 1 шт. мостовой кран для перемещения сит
- 1 шт. отсос кислотных отходящих газов
- 1 шт. система нагреваниа для ванн обезжиривания, травления и флюсования
- 1 шт. предохранительная сточная яма от протечек кислоты
- 7 шт. автоматические устройства вращения сит
- холодное цинкование покраской
- цинкование напылением (газотермическое напыление цинка)
- гальваническое цинкование
- термодиффузионное цинкование
- горячее цинкование
- подготовка поверхности (очистка, травление, сушка)
- нанесение покрытия
- сушка
- нанесение защитного слоя (лака, краски)
- Автоматизированная линия горячего цинкования рулонной стали, состоящая из следующего основного оборудования:
- Автоматизированные линии полимерного или лакокрасочного покрытия оцинкованной рулонной стали, в том числе состоящие из следующего оборудования:
- Разматыватель
- Электросварочная машина с правильными роликами для сшивки полосы
- Вертикальный петлевой накопитель полосы
- Секция подготовки полосы
- Нагревательная печь
- Валковая машина для нанесения грунтовки
- Печь для затвердевания грунтового покрытия
- Валковая машина для нанесения лакокрасочного покрытия
- Печь для затвердевания лакокрасочного покрытия
- Ламинатор
- Вертикальный петлевой накопитель полосы
- Наматыватель
- Автоматизированные линии горячего цинкования стальной проволоки, в том числе состоящие из следующего оборудования:
- Разматыватель проволоки
- Секции электролитического обезжиривания
- Секции промывки
- Печь отжига (восстановления)
- Секции охлаждения
- Секции флюсования
- Секции сушки
- Ванны горячего цинкования
- Секции удаления излишков цинка
- Секции охлаждения
- Наматыватель проволоки
- Линии горячего цинкования металлоконструкций, включающие следующее оборудование:
- Кран-балка с траверсой для перемещения металлоконструкций
- Ванна предварительной подготовки металлоконструкций
- Секция химической подготовки металлоконструкций
- Ванны обезжиривания
- Ванны травления
- Ванны промывки
- Ванны флюсования
- Печь осушки металлоконструкций после флюсования
- Плавильная печь
- Электронагреватели
- Ванна цинкования
- Ванна пассивирования и охлаждения
- Система упаковки
- Завершение подготовки поверхности (растворение оксидов железа, заново образовавшихся на поверхности во время промывки),
- Защита поверхности деталей с помощью пассивированной пленки флюса от дальнейшего окисления стали,
- Обеспечение хорошей смачиваемости расплавленным цинком.
- Качество стали;
- Качество цинка;
- Температура цинкового расплава;
- Продолжительность погружения;
- Скорость погружения и поднятия;
- Охлаждение.
- Инжиниринг
- Изготовление
- Поставка и доставка до места
- Шеф-монтаж,
- Надзор за индивидуальными и групповыми испытаниями
- Надзор за вводом в промышленную эксплуатацию
- Обучение
- Документация и чертежи
- Два стеллажа, на которые подаются рулоны с помощью мостового крана.
- Два приводных стеллажа для выполнения операции по снятию обвязочной ленты и позиционирования рулона
- Две тележки для рулонов
- Два перемещающихся разматывателя с прижимными роликами
- Две 3 роликовых правильные машины
- Двое обрезных ножниц верхнего реза гильотинного типа
- Стыкосварочная роликовая машина и вырубной пресс
- Горизонтальный входной петленакопитель
- Горизонтальная печь отжига: печь будет иметь секцию предварительного нагрева, секцию безокислительного отжига, секцию нагрева с радиантными трубами, секцию выдержки, секцию струйного охлаждения и выходную секцию
- Керамическая ванна для цинкового покрытия
- Оборудование для нанесения покрытия, включая погружные ролики и газовые ножи.
- Кран, предназначенный для оборудования ванны (ролики и газовые ножи)
- Башня охлаждения с воздушными охладителями, верхними роликами и баком водяного охлаждения
- Дрессировочная клеть и правильная машина для обеспечения необходимой плоскостности и требуемых механических характеристик.
- Участок пассивации с валковой машиной (коутером)
- Горизонтальный выходной петленакопитель (200м)
- Стенд горизонтальной и вертикальной инспекции
- Обеспечение свободного места для будущей промасливающей машины
- Выходные гильотинные ножницы, подобные ножницам на входе
- Одна моталка
- Два выходных стеллажа для рулонов, расположенных в пролетах для хранения
- Электрооборудование и оборудование регулирования
- Приводные тянущие и прижимные ролики: нитрильный каучук.
- Ролики станции натяжения: карбид вольфрама
- Отклоняющие ролики:
- перед ванной цинкования: без покрытия
- после ванны цинкования: хромированные
- 2 ручных устройства контроля центральной позиции (1 на каждом разматывателе)
- 1 центрирующее роликовое устройство на входе входного петленакопителя
- 1 центрирующих роликовых устройства внутри петленакопителя
- 1 центрирующее роликовое устройство перед печью
- 1 центрирующее роликовое устройство после водяного охлаждения
- 1 центрирующее роликовое устройство на входе выходного петленакопителя
- 1 центрирующих роликовых устройства внутри петленакопителя
- 1 центрирующее роликовое устройство на выходе выходного петленакопителя
- 1 контроль положения кромки на моталке
- 1 фиксированная ванна с керамическим покрытием для нанесения покрытия с нормальным узором кристаллизации (подогреваемая с помощью 2 индукторов со специальным регулирующим оборудованием управления).
- Устройство подачи слитков: Цинковые слитки будут погружаться автоматически в ванну с цинковым расплавом
- 3 ролика (направляющий ролик, корректирующий ролик и стабилизирующий ролик) разработаны для поддержания положения полосы при выходе из ванны.
- Все оборудование для поддержания этих трех роликов
- Станция натяжения для создания натяжения полосы на участке дрессировочной клети;
- Четырехвалковая дрессировочная клеть с устройством быстрой перевалки валков;
- Установка для влажной дрессировки, в которой применяется раствор, смешанный с деминерализованной водой или чистая деминерализованная вода
- Промывочное и сушильное оборудование после мокрой дрессировки
- Станция натяжения для создания натяжения полосы на участке правильно-растяжной машины
- Правильно-растяжная машина
- Выходная станция натяжения для регулирования натяжения полосы между дрессировочной клетью/ правильно-растяжной машиной и выходным петленакопителем.
- Гост на цинкование горячее
- Цинкование труб
- Лист оцинкованный профильный
- Оцинкованный рифленый лист
- Цинкование гост
- Размеры профлиста оцинкованного
- Цинковая пластина
- Термодиффузионное цинкование метизов
- Оцинковка что это
- Оцинковка это
- Кислые электролиты цинкования
Линии горячего цинкования чугунных шапок стеклянных изоляторов. Линия горячего цинкования
Линия горячего цинкования — УралТехИмпорт
Линия горячего цинкования
При «сухом» цинковании слой флюса на поверхности конструкции высушивают перед погружением в чистую ванну с расплавленным цинком.
Распечатать информацию по оборудованиюСуществуют два основных способа горячего цинкования, различающиеся по методу нанесения флюса. При цинковании с расплавленным флюсом конструкцию погружают в цинковую ванну, на поверхности которой плавает слой флюса. При «сухом» цинковании слой флюса на поверхности конструкции высушивают перед погружением в чистую ванну с расплавленным цинком. Именно этот метод – более трудоёмкий, но дающий более высокое качество покрытия. В целом процесс горячего цинкования включает в себя до 15 операций технологического цикла.
Предполагаемый перечень оборудования входящего в линию горячего цинкования:
ut-import.ru
Оборудование для горячего цинкования металла (стали)
Основной задачей цинкования металла является образование непроницаемого для окружающей среды покрытия, защищающего основной металл от необратимого процесса коррозии. Цинкование поверхности металла, особенно стали, это наиболее эффективный способ борьбы с коррозией, т.к. металлический цинк обладает уникальными химическими свойствами. Вода практически не вступает во взаимодействие с цинком. При контакте с воздухом цинк образует равномерную устойчивую непроницаемую пленку из оксида цинка (ZnO) и карбоната цинка (ZnCO3 ), в отличие от ржавчины, которая создает пористую проницаемую структуру, не защищая основной металл, что приводит со временем к его полному разрушению. Дополнительным преимуществом цинка является то, что он имеет более низкий электрохимический потенциал, чем железо и в присутствии воды цинк выполнят функцию анода, а железо выступает катодом и поверхность основного металла (стали) во влажной среде пассивируется, что тормозит коррозионные процессы окисления. Это свойство цинка дает ему неоспоримые преимущества перед остальными способами защиты стали от коррозии. Цинк является довольно мягким металлом, но даже в случае механического нарушения защитного слоя, цинк, в присутствии влаги являясь анодом, «затягивает» возникшее повреждение, образуя новый защитный слой.
Существуют следующие виды цинкования стальных изделий:
Холодное цинкование покраской осуществляется нанесением на подготовленную стальную поверхность жидкой смеси, содержащей мелкодисперсный цинковый порошок и жидкое связующее. При этом методе цинкования готовая поверхность содержит 89-93% цинка, а толщина слоя может существенно варьироваться. Метод холодного цинкования не технологичен и приводит к существенному удельному расходу цинка и применяется для цинкования уже собранных металлоконструкций, восстановления поврежденной поверхности на металлических изделиях после эксплуатации, а также для цинкования единичных стальных изделий в ограниченных количествах. Из-за пористой структуры слоя цинка требуется дополнительное лакокрасочное покрытие.
Цинкование напылением (газо-термическое напыление цинка) осуществляется распылением в потоке горячего газа (например, воздуха) расплавленного цинка. Расплавленный цинк для распыления получают газопламенным или электродуговым способом плавления. Также как и холодное цинкование покраской метод газо-термического напыления мало технологичен и используется для покрытия цинком крупногабаритных деталей и металлоконструкций. Метод не применим для цинкования внутренних полостей небольшого диаметра и мелко-профильных поверхностей. Толщина покрытия обычно превышает 200 мкм. Слой цинка имеет более надежное сцепление с металлом, чем при холодном цинковании, однако также имеет пористую структуру и требует дополнительного лакокрасочного покрытия.
Гальваническое цинкование проводится в электролите содержащим соли цинка под действием постоянного тока. При этом стальная деталь является катодом, а пластина цинка – анодом. Метод цинкования в электролите не имеет широкого промышленного применения. Толщина цинкового гальванического покрытия составляет 20 – 30 мкм. Методом гальванического цинкования поверхности изделий обычно пользуются для декоративных целей.
Термодиффузионное цинкование проводится в ограниченном пространстве муфельной печи или реторты, в которое помещаются цинкуемые стальные детали и цинковая порошковая смесь для термодиффузионного цинкования. При температурах 4000С – 5500С происходит проникновение цинкового тумана в поверхностный слой стального изделия. При данном методе образуется прочный слой цинка, толщина которого определяется потребностями заказчика, но обычно не менее 25 мкм. Термодиффузионное цинкование позволяет наносить тонкие покрытия на маленькие металлические изделия со сложной конфигурацией, в том числе внутренними углублениями, отверстиями и резьбой. Недостатком данного метода является периодичность процесса, возможность его применения к ограниченному размеру деталей и высокая себестоимость нанесения покрытия.
Горячее цинкование является самым высокопроизводительным и технологичным способом нанесения покрытия. Качество покрытия, а также ее надежность и долговечность существенно превосходят другие методы цинкования. Покрытие цинком методом горячего цинкования осуществляется погружением изделия из стали в ванну с расплавленным цинком при температуре 440 – 4700С. Толщина цинкового покрытия находится в диапазоне 30 – 100 мкм. Данный метод особенно эффективен при непрерывном технологическом процессе, например, при цинковании рулонной стали или стальной проволоки, а также при непрерывно-периодическом процессе цинкования отдельных стальных деталей от 0,5 до 12 метров. Более мелкие изделия, например, крепеж цинкуют, опуская в ванну с цинком специальный барабан, однако после цинкования резьбовые соединения требуют дополнительной механической обработки.
Все перечисленные методы цинкования при промышленном применении всегда имеют ряд этапов:
Последняя стадия является не обязательной, но желательной. Цинк является мягким металлом и нанесение дополнительного защитного слоя увеличивает твердость покрытия и соответственно долговечность защиты.
Исходя из выше изложенного, можно сделать вывод, что наиболее эффективным методом борьбы с коррозией металла является цинкование его поверхности. Наиболее технологичным с точки зрения автоматизации процесса, оптимальным по качеству покрытия в сочетании с высокой производительностью и себестоимостью является метод горячего цинкования стали.
Специалисты производственно- инжиниринговой компании ENCE GmbH в соответствии с техническим заданием и потребностями заказчика готовы разработать, скомплектовать и осуществить поставку "под ключ" следующие автоматизированные технологические линии для горячего цинкования в широком диапазоне производительности для различных стальных изделий:
Производственно-инжиниринговая компания ENCE GmbH поставляет также вспомогательное оборудование и запасные части к линиям горячего цинкования. На своей производственной площадке в Республике Корея – машиностроительный завод BUKANG компания производит по разработанным чертежам погружное оборудование и специальные детали из специального сплава – стеллен, который имеет повышенную устойчивость и работоспособность при работе в расплаве цинка. Сервисные инженеры нашей компании готовы выехать на действующее предприятие для оценки работы действующего оборудования, снять размеры проблемных быстроизнашивающихся деталей и предложить аналоги из высокопрочных и износостойких сплавов или предложить комбинированные детали с керамическим покрытием или вставкой. Кроме того компания ENCE GmbH предоставляет заказчикам следующее вспомогательное оборудование:
galvanazing-line.ru
Линии горячего цинкования чугунных шапок стеклянных изоляторов
2. Участок цинкования мелких деталей
2.1 Общее описание
Участок цинкования мелких деталей спроектирован оборудован печью 2000х1000Х1500мм, и является частью участка общего цинкования. Траверсы, которые держат материал, состоят из сит Ø1200х600мм, которые используются для работы полуавтоматической линии предварительной обработки с ваннами обезжиривания, травления, мойки и флюсования. Траверсы с ситами после предварительной обработки разгружаются на ленточный конвейер, и затем они готовы для подачи на манипулятор для подачи на цинкование. Материал хранится в соответствующих корзинках из нержавеющей стали. Манипулятор подцепляет корзинку с материалом, автоматически подает ее в ванну с цинком и перемещает в продольном направлении. После завершения цикла у корзинки подаются в центрифугу. Затем корзина отправляется в ванну охлаждения и на участок выгрузки. Все вышеописанные действия выполняются автоматически, без участия оператора.
2.2 Зоны загрузки и выгрузки небольших деталей
Загрузочный вибростол
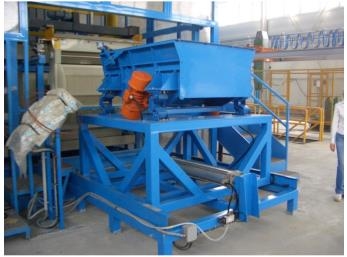
Вибростол оснащен вибрирующей поверхностью из полипропилена, которая подсоединена к электромагниту с настраиваемой интенсивностью, и опорной рамой из трубчатой панели на 4 резиновых подшипниках. Запускается вручную, поскольку оператор должен удалить крышку каждого сита, запустить вибростол, заполнить сито до необходимого количества, выключить вибростол, закрыть сито крышкой и передать в следующую секцию.
2.3. Установка предварительной обработки
2.3.1 Поддоны предварительной обработки
Поддоны предварительной обработки мелких деталей состоят из прочных сварных металлоконструкций из HEB 100 и UNP 100, окрашенных битумно-эпоксидной смолой. Внутри все поддоны проложены 15-миллиметровым PP (полипропиленом) по стандарту DVS 2205 и оснащены фланцами для загрузки и выгрузки химической продукции.
2.3.2 Система транспортировки сит
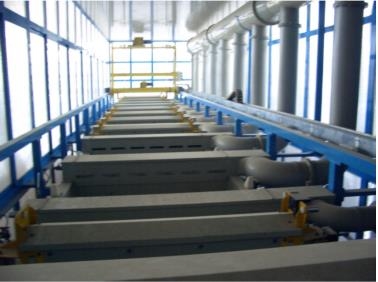
Направляющие из нержавеющей стали смонтированы в верхней части поддонов, внутри которых скользит подвижная каретка, поддерживающая траверсы. Как только траверсы достигают заранее заданной позиции, погружены и оставлены на травление в течение предварительно установленного времени, подвижная каретка двигает другие траверсы. В конце процесса травления сито погружается в ванну с водой для мойки до возврата на начальную позицию. Вся зона предварительной обработки оборудована системами отсоса, которые содержат рабочее пространство в соответствии с экологическими правилами и нормами безопасности. Кислотные пары обрабатываются и смачиваются на той же установке. Автоматическая линия предварительной обработки состоит из:
2.3.3 Сита
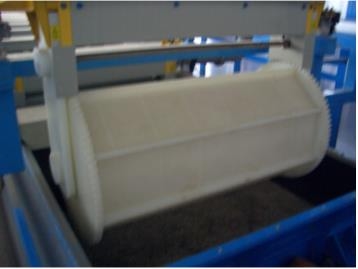
2.4 Ленточная сушилка
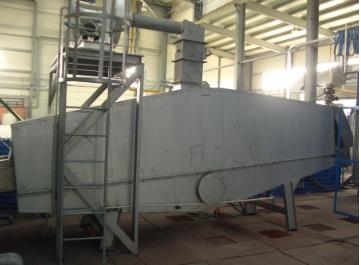
2.5. Участок цинкования мелких деталей
Печь цинкования
Керамическая печь со следующими техническими характеристиками:
2.6 Вспомогательное оборудование участка цинкования
2.6.1 Металлические конструкции для укрытия помещения с печью, поддерживающие балки и металлические листы.
Включает в себя структурные части печи, с помещением и крышками изложниц. Критерий расчета и размера работ по покрытию помещения с печью учитывает тот факт, что эта поверхность должна нести также вес цинковых брикетов, которые буду опускаться в ванну. Плановый размер помещения с печью: 15 х 10 м
Прочная самоподдерживающая рама для покрытия помещения с печью из металлических листов и профилей, состоящих из нескольких элементов для облегчения сборки и транспортировки. Прочная самоподдерживающая рама для покрытия изложниц из металлических листов и профилей, состоящих из нескольких элементов для облегчения сборки и транспортировки.
2.6.2 Дымоходы
2.6.3 Станция снижения давления газа второй ступени
2.6.4 Робот-манипулятор для небольших деталей
2.7 Система транспортировки
Установка используется для транспортировки корзин с деталями из зоны загрузки до положения захвата их манипулятором. Каждая установка изготовлена из металлической рамы и трубной панели, ряда холостых и приводных роликов, 5 кВт мотор-редуктора, концевого выключателя-«рычага» для управления чувствительным манипулятором и приводной цепи от мотора-редуктора до последнего ролика. Загрузочное место деталей в корзинах оснащено встроенным тензометром, который подает сигнал, о том что процессом наполнения корзинок завершен, и они передаются до точки захвата манипулятором.
2.8 Вспомогательное оборудование
2.8.1 Центрифуга
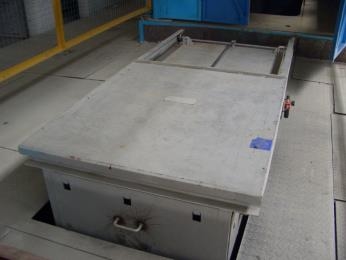
Центрифуги состоят из двигателя 7,5 кВт, ≈62 об/мин, которые подсоединены системой лент к опоре, где помещаются корзинки с деталями. Центрифугирование обеспечивает удаление избытка цинка с оцинкованных деталей.
2.8.2 Опрокидыватель корзин
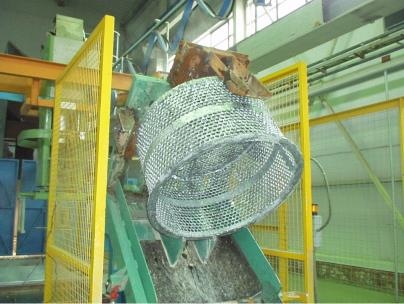
Опрокидыватель корзин (так называемый первый опрокидыватель) располагается на выходе из центрифуги и применяется для подачи оцинкованных деталей на второй опрокидыватель, который располагается внутри ванны охлаждения. Это обеспечивает постоянное увлажнение оцинкованной корзины, которая сразу готова для следующего рабочего цикла, и предотвращает образование выбросов или взрывов в ванне из-за погружения влажного объекта.
2.8.3 Охлаждающий опрокидыватель
Охлаждающий опрокидыватель (так называемый второй опрокидыватель) служит для сбора деталей из корзин, блокируется жесткими шарнирами первого опрокидывателя охлаждающей ванны. Поставляется с опорной рамой из трубчатой панели, четырьмя гидравлическими поршнями (один на подъем и один на опускание, один для движения вправо/влево, один для активации правого зажима и один для левого) и отверстиями для слива охлаждающей воды.
2.8.4 Охлаждающая ванна
Ванна изготовлена из металлического листа, используется для охлаждения материала после центрифуги. Из-за постоянно испарения, вызванного погружением деталей после цинкования, ванна подсоединена к водной системе цеха и подготовлена для автоматического пополнения уровня воды.
2.8.5 Поддерживающая башня для манипулятора
Это железная структура на колесах. Применяется для поддержки манипулятора во время простоев. При обычном процессе цинкования манипулятор передвигается в зону стоянки, для легкой эксплуатации в зоне рядом с печью. Во время цинкования башня передвигается в рабочее положение. Изготавливается из металлических профилей, с колесами для ручного перекатывания.
2.8.6 Корзины для цинкования
Корзины, в которые складываются детали, изготовлены из нержавеющей стали AISI 304. Представляют собой легковесную конструкцию со штангой и цилиндром из перфорированного металлического листа. В эти корзины помещаются детали и во время фазы цинкования они полностью опускаются в расплав цинка. Отверстия в корзинках позволяют цинку поступать к деталям, которые нужно оцинковать. Также они позволяют избыткам цинка стекать при выходе из ванны. Рекомендуется иметь в распоряжении по крайней мере 10 корзин.
2.8.7 Электрический монорельсовый потолочный кран
Карусель состоит из трех лебедок, предназначенных для подачи материала из секции предварительной обработки до ванны охлаждения. Мостовой кран поставляется в сборе со всеми деталями.
galvanazing-line.ru
Оборудование для горячего цинкования металла (стали)
Производственно-инжиниринговая компания ENCE GmbH (ЭНЦЕ ГмбХ) (Швейцария) совместно со своим партнером компанией ANDRITZ Metals (Германия) (Sundwig GmbH (Зундвиг ГмбХ)) и на базе собственного инжинирингового центра и машиностроительного завода BUKANG (Республика Корея) предлагает технологические линии, отдельное оборудование и комплектующие для горячего цинкования рулонной стали, стальной проволоки и отдельных стальных изделий.

Основной задачей цинкования металла является образование непроницаемого для окружающей среды покрытия, защищающего основной металл от необратимого процесса коррозии. Цинкование поверхности металла, особенно стали, это наиболее эффективный способ борьбы с коррозией, т.к. металлический цинк обладает уникальными химическими свойствами. Вода практически не вступает во взаимодействие с цинком. При контакте с воздухом цинк образует равномерную устойчивую непроницаемую пленку из оксида цинка (ZnO) и карбоната цинка (ZnCO3 ), в отличие от ржавчины, которая создает пористую проницаемую структуру, не защищая основной металл, что приводит со временем к его полному разрушению. Дополнительным преимуществом цинка является то, что он имеет более низкий электрохимический потенциал, чем железо и в присутствии воды цинк выполнят функцию анода, а железо выступает катодом и поверхность основного металла (стали) во влажной среде пассивируется, что тормозит коррозионные процессы окисления. Это свойство цинка дает ему неоспоримые преимущества перед остальными способами защиты стали от коррозии. Цинк является довольно мягким металлом, но даже в случае механического нарушения защитного слоя, цинк, в присутствии влаги являясь анодом, «затягивает» возникшее повреждение, образуя новый защитный слой.
Существуют следующие виды цинкования стальных изделий:
Холодное цинкование покраской осуществляется нанесением на подготовленную стальную поверхность жидкой смеси, содержащей мелкодисперсный цинковый порошок и жидкое связующее. При этом методе цинкования готовая поверхность содержит 89-93% цинка, а толщина слоя может существенно варьироваться. Метод холодного цинкования не технологичен и приводит к существенному удельному расходу цинка и применяется для цинкования уже собранных металлоконструкций, восстановления поврежденной поверхности на металлических изделиях после эксплуатации, а также для цинкования единичных стальных изделий в ограниченных количествах. Из-за пористой структуры слоя цинка требуется дополнительное лакокрасочное покрытие.
Цинкование напылением (газо-термическое напыление цинка) осуществляется распылением в потоке горячего газа (например, воздуха) расплавленного цинка. Расплавленный цинк для распыления получают газопламенным или электродуговым способом плавления. Также как и холодное цинкование покраской метод газо-термического напыления мало технологичен и используется для покрытия цинком крупногабаритных деталей и металлоконструкций. Метод не применим для цинкования внутренних полостей небольшого диаметра и мелко-профильных поверхностей. Толщина покрытия обычно превышает 200 мкм. Слой цинка имеет более надежное сцепление с металлом, чем при холодном цинковании, однако также имеет пористую структуру и требует дополнительного лакокрасочного покрытия.
Гальваническое цинкование проводится в электролите содержащим соли цинка под действием постоянного тока. При этом стальная деталь является катодом, а пластина цинка – анодом. Метод цинкования в электролите не имеет широкого промышленного применения. Толщина цинкового гальванического покрытия составляет 20 – 30 мкм. Методом гальванического цинкования поверхности изделий обычно пользуются для декоративных целей.
Термодиффузионное цинкование проводится в ограниченном пространстве муфельной печи или реторты, в которое помещаются цинкуемые стальные детали и цинковая порошковая смесь для термодиффузионного цинкования. При температурах 4000С – 5500С происходит проникновение цинкового тумана в поверхностный слой стального изделия. При данном методе образуется прочный слой цинка, толщина которого определяется потребностями заказчика, но обычно не менее 25 мкм. Термодиффузионное цинкование позволяет наносить тонкие покрытия на маленькие металлические изделия со сложной конфигурацией, в том числе внутренними углублениями, отверстиями и резьбой. Недостатком данного метода является периодичность процесса, возможность его применения к ограниченному размеру деталей и высокая себестоимость нанесения покрытия.

Горячее цинкование является самым высокопроизводительным и технологичным способом нанесения покрытия. Качество покрытия, а также ее надежность и долговечность существенно превосходят другие методы цинкования. Покрытие цинком методом горячего цинкования осуществляется погружением изделия из стали в ванну с расплавленным цинком при температуре 440 – 4700С. Толщина цинкового покрытия находится в диапазоне 30 – 100 мкм. Данный метод особенно эффективен при непрерывном технологическом процессе, например, при цинковании рулонной стали или стальной проволоки, а также при непрерывно-периодическом процессе цинкования отдельных стальных деталей от 0,5 до 12 метров. Более мелкие изделия, например, крепеж цинкуют, опуская в ванну с цинком специальный барабан, однако после цинкования резьбовые соединения требуют дополнительной механической обработки.
Все перечисленные методы цинкования при промышленном применении всегда имеют ряд этапов:
Последняя стадия является не обязательной, но желательной. Цинк является мягким металлом и нанесение дополнительного защитного слоя увеличивает твердость покрытия и соответственно долговечность защиты.
Исходя из выше изложенного, можно сделать вывод, что наиболее эффективным методом борьбы с коррозией металла является цинкование его поверхности. Наиболее технологичным с точки зрения автоматизации процесса, оптимальным по качеству покрытия в сочетании с высокой производительностью и себестоимостью является метод горячего цинкования стали.
Специалисты производственно- инжиниринговой компании ENCE GmbH в соответствии с техническим заданием и потребностями заказчика готовы разработать, скомплектовать и осуществить поставку "под ключ" следующие автоматизированные технологические линии для горячего цинкования в широком диапазоне производительности для различных стальных изделий:

Производственно-инжиниринговая компания ENCE GmbH поставляет также вспомогательное оборудование и запасные части к линиям горячего цинкования. На своей производственной площадке в Республике Корея – машиностроительный завод BUKANG компания производит по разработанным чертежам погружное оборудование и специальные детали из специального сплава – стеллен, который имеет повышенную устойчивость и работоспособность при работе в расплаве цинка. Сервисные инженеры нашей компании готовы выехать на действующее предприятие для оценки работы действующего оборудования, снять размеры проблемных быстроизнашивающихся деталей и предложить аналоги из высокопрочных и износостойких сплавов или предложить комбинированные детали с керамическим покрытием или вставкой. Кроме того компания ENCE GmbH предоставляет заказчикам следующее вспомогательное оборудование:

Специалисты производственно-инжиниринговой компании ENCE GmbH готовы оказать техническую помощь и дать консультацию по любому оборудованию, входящему в комплект линии горячего цинкования, а также по индивидуальному заказу провести модернизацию действующего производства с целью повышения производительности цинкования, повышения качества покрытия и снижения себестоимости производства готовой продукции.
Более подробно о компании ENCE GmbH (ЭНЦЕ ГмбХ) и поставляемом компанией оборудовании, в том числе и на других языках, можно ознакомиться на следующих страницах сайта:
Русский - www.ence.ch/rus/equipment_and_partnersEnglish - www.ence.ch/eng/equipment_and_partnersDeutsch - www.ence.ch/deu/equipment_and_partnersFrancais - www.ence.ch/fra/equipment_and_partnersItaliano - www.ence.ch/ita/equipment_and_partnersEspanol - www.ence.ch/esp/equipment_and_partners
или на сайтах нашей сервисной компании ООО ИНТЕХ ГмбХ (LLC INTECH GmbH) на различных языках:
Русский - www.intech-gmbh.ru/equip_meEnglish - www.intech-gmbh.com/equip_meDeutsch - www.intech-gmbh-rus.de/equip_meFrancais - www.intech-gmbh.be/equip_meItaliano - www.intech-gmbh-rus.ch/equip_meEspanol - www.intech-gmbh.es/equip_mePortugues - www.intech-gmbh.com.br/equip_me非鉄冶金と鉄鋼業、採鉱・選鉱業のお取引先 - www.intech-gmbh.jp/equip_me我们的客户 - www.intech-gmbh.sg/equip_me
o.galvanazing-line.ru
Технология процесса горячего цинкования

Линия цинкования состоит из ванн, обеспечивающих подготовку поверхности перед цинкованием, одной сушильной трехкамерной печи для сушки деталей перед входом в ванну цинкования, одной печи цинкования и одной зоны охлаждения и контроля.
1. Подготовка поверхности:

Как любая обработка поверхности, горячее цинкование требует правильной подготовки поверхности для того, чтобы во время погружения деталей в ванну цинкования реакция железа и цинка была однородной.
Последовательность этапов следующая: обезжиривание, промывка, травление, промывка и флюсование.
1.1 Обезжиривание:

Назначение обезжиривания – удаление масла, загрязнений от этого зависит качество цинкования в целом. Обработка осуществляется с помощью обезжиривающего реагента, выбранного в зависимости от загрязняющего вещества, при температуре от 60 до 80°C. Удаление масляных пятен является необходимым перед этапом травления, во избежание дефектов цинкования металла таких как, например, отсутствие или расслоение цинкового покрытия.
1.2 Промывка после обезжиривания:
Промывка должна выполняться эффективно, она позволит удалить с деталей жирные вещества и пену, оседающую на деталях из ванны обезжиривания.
1.3 Травление:

Операция травления состоит из очистки поверхности металла, посредством удаления с нее слоя оксидов, образующихся в результате горячей обработки (окалина) или неблагоприятных условий хранения (ржавчина).
Обработка выполняется с помощью соляной кислоты, имеющей концентрацию от 120 до 210 г/л, при температуре окружающей среды (20 - 25°C). Преимуществом соляной кислоты является хорошая растворимость хлоридов железа и достижение чистой блестящей поверхности и достаточной смачиваемости расплавленным цинком.
Рекомендуется добавлять ингибиторы для удаления только окислов и гидроксилов, ограничивая воздействие на основной метал и избегая риска водородного насыщения.
Правильный контроль концентрации ванны позволит оптимизировать качество обработки, расходы, выбросы и, как следствие, защиту окружающей среды. Для дефектных изделий предусмотрена ванна для удаления цинкового покрытия, которая позволяет очищать детали за счет использования отработанного раствора кислоты.
1.4 Промывка после травления:

За травлением следует тщательная промывка для нейтрализации возможных остаточных следов кислоты и удаления солей. Использование нескольких последовательных промывочных ванн позволит оптимизировать промывку и сократить расход воды.
1.5 Флюсование:
Операция флюсования имеет три цели:

Применяемый флюс состоит из хлорида цинка и хлорида аммония.
Обработка выполняется концентрированным раствором флюса (400 - 600 г/л) при температуре 60°C.
Раствор ванны флюсования должен периодически контролироваться (плотность, pH и содержание железа). Очистка осуществляется с помощью добавления перикиси водорода, которая непрерывно осаждает соли трёхвалентного железа на дно ванны, а далее осадок попадает в систему отстаивания и фильтрации.
1.6 Предварительный нагрев, сушка перед нанесением цинка:

Данная операция после флюсования позволяет испарять влагу с поверхности деталей и в пустотелых элементах, во избежание выплескивания цинка парами воды во время погружения в печь и деформации деталей. Она также позволяет предварительного нагревать детали приблизительно до 100°C, что эффективность печи цинкования, экономит энергию и снижает себестоимости цинкования.
Время сушки превышает время цинкования, следовательно, сушильная печь должна иметь несколько камер (минимум 2). Принятая в расчет производительность - максимальная загрузка сушильной печи.
Загрузочное и разгрузочное устройства обеспечат своевременное перемещение садок и оптимальной нагрузке печи цинкования.
1.7 Цинкование:
После всех предварительно описанных операций, можно считать, что контакт между сталью и жидким цинком будет обеспечен наилучшим образом.

Основные параметры успешной операции:
Температура цинкового расплава составляет 419°C, цинкование выполняется в классических пределах от 445 до 460°C, что позволяет сократить образование штейна, оксидов и т.д.
Вытяжка отходящих газов обеспечивается системой аспирации и фильтрации в полном соответствии с экологическими нормами.

Фаза погружения:
Во время этой фазы имеют место несколько этапов: теплообмен внутри детали, расплав и разрушение флюса на поверхности деталей, приводящее к оптимальной смачиваемости расплавленного цинка.
Скорость погружения тоже является важным фактором. Слишком медленная скорость приведет к освобождению поверхности стали от пассивированной пленки с риском повторного окисления, а слишком быстрая скорость погружения приведет к захвату с поверхности остатков солей, флюс не успеет расплавится и, как следствие, это вызывает образование дефектов.
Длительность погружения:
Длительность погружения изменяется в зависимости от садки (массы, размеров, формы), в среднем от 3 до 10 мин.Перед удалением деталей необходимо удалить шлак с помощью скребка с поверхности расплава, во избежание его оседания на деталях.
Фаза извлечения из ванны:
Скорость извлечения влияет на конечную толщину полученного покрытия. Она воздействует на толщину слоя чистого цинка (мкм), связанную с растеканием цинка и скоростью отвердевания.
Скорости подбираются, исходя из производительности, длительности погружения и качеством поверхности (подтёки, капли), учитывая регулировку наклона деталей на монтаже в зависимости от их геометрии.
1.8 Охлаждение:
Охлаждение происходит на открытом воздухе на участке складирования и хранения совмещенной с участком ОТК перед упаковкой.
Система аспирации, фильтрации и автоматическая система транспортировки.

Система аспирации отходящих газов, установленная на ваннах, и вытяжной кожух, установленный на траверсах перемещения, будут гарантировать стабильную вытяжку паров, и эффективно защитят все оборудование от коррозии, возникающей из-за паров соляной кислоты. А фильтры очистят от пыли и паров кислоты в полном соответствии с экологическими нормами РФ.
Полностью автоматическая система транспортировки линии горячего цинкования предназначена для подачи, разгрузки и погружения цинкуемых деталей в соответствии с заданными технологическими параметрами. Управление может осуществляться через пульт управления оператора посредством PLC фирмы Siemens или промышленным компьютером с необходимым программным обеспечением. Также управление линией может осуществляться в ручном режиме.
Мостовые краны, траверсы и конвейеры над травильными ваннами и печи цинкования металла работают в критических загрязненных и температурных условиях, а также химической коррозии, поэтому решения, подбор материального исполнения узлов и агрегатов, комплектация, шефмонтаж, гарантийное и сервисное обслуживание должно осуществляться специалистами фирмы ENCE GmbH, имеющими богатый опыт в области гальванизации и прошедшими обучение в на ведущих предприятиях ЕЭС.

o.galvanazing-line.ru
Цинкование стальной полосы, Линия горячего цинкования, Технология линии горячего цинкования стальной полосы
1. Описание
Мы имеем богатый и передовой технический опыт в работе с современным оборудованием, предназначенным для агрегатов по обработке стальной полосы. Агрегаты разработаны в соответствии с самыми современными технологиями для достижения высокой производительности и являются удобными в обслуживании установками, а также имеют высокую степень автоматизации, благодаря чему требуется ограниченное количество операторов. Агрегаты соответствуют самым строгим требованиям ведущих производителей стали.
Наше предложение разработано для покрытий с нормальным рисунком кристаллизации и без рисунка кристаллизации.
Настоящий проект включает в себя:
2. Основные этапы обработки стальной полосы
Стальная полоса перемещается слева направо - вид со стороны обслуживания. Предлагаемая обработка полосы включает в себя следующие основные этапы:
3. Исходный материал
3.1. Исходные рулоны
3.2. Исходная стальная полоса
Геометрические характеристики
Качество поверхности стальной полосы и загрязнение
Физические и химические характеристики
Низкоуглеродистая холоднокатаная неотожженная сталь
Максимальное изменение полосы
4. Выпускаемый материал
4.1. Выпускаемые рулоны
Покрытие: диапазон цинка – 60 (при менее, чем 70 м/мин) - 300 г/м2 (обе стороны)
Растяжение после дрессировочной клети и правильно-растяжной машины
2 % макс. для марки CQ 0.3 % макс. для марки FH
Химическая обработка:
Низкоуглеродистая холоднокатаная отожженная и оцинкованная сталь
5. Скорость агрегата и значения ускорения
5.1. Скорость
5.2. Значения ускорения и замедления
Входная и выходная секции
6. Производственное время
Расчет чистого рабочего времени
7. Цинковое покрытие (GI)
Максимальная скорость технологического процесса 90 м/мин
8. Параметры обработки стальной полосы
8.1.Диаметр роликов
Ролики входной секции:
8.2. Длина бочки роликов
8.3. Покрытие роликов
9. Натяжение полосы
Таблица натяжения полосы для максимального сечения (= 2500 мм²) во время устойчивой работы агрегата.
10. Центрирование стальной полосы
Для достижения отличного центрирования полосы мы поставляем следующие центрирующие устройства, расположенные на агрегате:
Перечень основных последовательностей
Погрузка рулона: ручная операция Автоматическое замедление входной секции в конце рулона и на переднем конце полосы Автоматическое слежение и позиционирование заднего конца полосы на входных ножницах Автоматическое слежение и позиционирование в сварочной машине Отрезание концов: ручная последовательность Aвтоматическое позиционирование переднего конца полосы на входных ножницах Автоматическая заправка в сварочную машину Отрезание концов: ручная последовательность Накопление полосы Автоматическое управление перемещением входного петленакопителя Автоматическое управление перемещением выходного петленакопителя Автоматическое разделение рулона в выходной секции Автоматическая остановка выходной секции при приближении сварного шва Удаление сварного шва вручную Отбор образцов в ручную Автоматическая смотка Автоматическое позиционирование заднего конца полосы в конце смотки Снятие рулонов: ручная операция.
11. Общее описание оборудования
11.1. Сварочная машина
Сварочная машина для сварки внахлестку
11.2. Печь отжига
Печь отжига для данного проекта – безокислительная горизонтальная печь.
11.3. Секция нанесения покрытия
Ванны
Мы предусматриваем следующее оборудование
Оборудование нанесения покрытия
Оно включает в себя:
Отжимное оборудование
Данная система позволяет осуществлять отжим полосы с помощью ее обдува холодным воздухом.
Погрузочно-разгрузочное оборудование
Эти специальные устройства облегчают установку и техобслуживание различных элементов оборудования ванны.
Стенд для техобслуживания
Данный стенд позволяет операторам выполнять работы по техобслуживанию, а также осуществлять подготовку к автономной работе всего оборудования ванны и отжимного оборудования. В него также входит печь для предварительного нагрева новых роликов перед погружением в ванну цинкования.
11.4. Измерение толщины покрытия
Мы предлагаем толщиномер холодного типа. Данная система представляет собой оборудование на основе рентгеновского или изотопного флуоресцентного измерения веса покрытия. Толщиномер расположен за закалочной ванной.
11.5. Дрессировочная клеть и правильная машина
Включены четырехвалковая дрессировочная клеть и правильно-растяжная машина. Основные позиции:
11.6. Секция пассивации
Мы предлагаем горизонтальную секцию с валковой машиной (коутером) для нанесения пассивирующего покрытия с Cr или без. Затем полоса сушится посредством обдува горячим воздухом.
www.intech-gmbh.ru
Применение индукционного нагрева в линиях горячего цинкования стальной ленты

Линии горячего цинкования широко используют при производстве стальной ленты с защитным покрытием. Покрытие из цинка или соединений цинка наносится на поверхность ленты посредством погружения ее в ванну с расплавом.
Сталь для производства оцинкованной ленты поступает после холодной или горячей прокатки, и для придания ленте требуемых свойств необходим ее отжиг, который можно проводить в рулонах в периодическом режиме путем их выдержки в специальных печах. Этот процесс характеризуется низкой производительностью, и часто не достигается требуемое качество продукции. В последнее время для отжига все больше используют прогрессивные непрерывные технологии с размоткой рулонов перед отжигом. Однако смена сортамента ленты при непрерывном производстве вызывает необходимость частого изменения режима работы линии. На современных линиях непрерывного цинкования это может приводить к снижению выхода годной ленты на 10-15%.
Применение индукционного нагрева в линиях непрерывного цинкования существенно улучшает ситуацию - существенно уменьшается брак, увеличивается производительность на той же площади, повышается рентабельность. Существуют и дополнительные факторы, содействующие применению индукционного нагрева в линиях непрерывного цинкования. Среди них - сокращение длины линии и продолжительности процесса при той же производительности, легкость в управлении и автоматизации, улучшение экологической обстановки.
Технологическая линия
Перед горячим цинкованием стальная лента должна быть очищена от масла, загрязнений поверхности. При использовании высокоэффективных методов очистки поверхности ленты можно применять любой тип нагрева: прямой газовый нагрев, радиационный нагрев (с использованием газа или электричества) и индукционный нагрев. Совместное использование электролитической очистки и радиационного нагрева превалирует в высокопроизводительных линиях горячего цинкования. Однако в этом случае инерционность линии достаточно большая. Поэтому при частой смене размеров ленты и режимов отжига используют другую технологию - пламенные печи с восстановительной атмосферой. Их успешно применяют не только для нагрева, но и подготовки поверхности ленты к цинкованию. В обоих случаях применение индукционного нагрева позволяет повысить качество продукции и производительность линии.
Рис. 1. Температурный профиль для режима горячего цинкования ленты коммерческого качества, толщина ленты - 0,78 мм, скорость движения ленты - 90 м/мин (температура после нагрева: t1 - предварительного отходящими газами, t2 - прямого газового, tЗ - индукционного, t4 - газового, t5 - радиационного, t6 - температура после охлаждения)
Типичный температурный профиль ленты на протяжении всей линии для продукции коммерческого качества (среднетемпературный отжиг) перед погружением ленты в цинковую ванну представлен на рис. 1. Лента поступает через предварительный нагреватель в печь прямого газового нагрева, где происходит окончательная зачистка и подготовка поверхности ленты. При этом масло выпаривается, лента очищается и удаляется тонкая оксидная пленка. Горелки печи работают в специальном режиме для снижения и удаления оксидной пленки. Расположение индукционных нагревателей между пламенной и радиационной газовой печью обеспечивает быструю перенастройку линии на новые размеры ленты.
Из индукционных нагревателей лента поступает в радиационные печи, используемые для нагрева и выдержки, и окончательно доводится до нужной температуры в зависимости от требуемой степени отжига (низкотемпературный - 549 °С, среднетемпературный - 732 °С и высокотемпературный - 845 °С). Затем лента попадает в зону охлаждения, где охлаждается до температуры, необходимой для нанесения цинкового покрытия.
Качество продукции существенно зависит от соблюдения температурного режима. Например, температура на выходе из предварительного нагревателя t1 не может превышать 260 °С. При выходе из газовой печи температура ленты t2 должна быть в диапазоне от 538 до 746 °С. Для режима коммерческого качества температура в точке t4 должна быть 732 °С. Допустимый диапазон температуры 730-760 °С. Температура после зоны охлаждения t6 должна быть в диапазоне 465-477 °С.
Разработанные модели
Необходимые данные для проектирования индукционного нагревателя могут быть получены из тепловой модели обработки ленты на каждом участке линии. Такая модель была разработана для рассмотрения процесса передачи тепла в линии гальванизации, включая рассмотрение электромагнитных процессов в индукционных нагревателях. Модель НТМ (Heat Traпsfer Model) позволяет рассчитать температурное поле ленты на каждом участке линии и получать данные для разработки и оптимизации оборудования.
Модель планирования производства РРМ (Productioп Plaпniпg Model) была разработана для оптимизации порядка обработки рулонов ленты различных толщин. После ввода данных о размерах модель рассчитывает оптимальный порядок подачи рулонов для увеличения качества продукции, уменьшения брака и увеличения производительности линии. Одновременно такое рассчитываются для каждой ленты оптимальная скорость линии и необходимая мощность индукторов.
Линия горячей гальванизации является системой, состоящей из установок с распределенными параметрами и большой тепловой инерцией.
Для моделирования динамических режимов системы управления разработана специальная модель DTM (Dyпamic Transition Model). Она прогнозирует изменение температуры ленты в каждой точке линии в переходных режимах. Основные управляющие воздействия - скорость линии и мощность индукторов. Учитываются все динамические характеристики электроприводов и технологических устройств.
Принципы построения системы управления линии непрерывного цинкования.
Значительная часть потерь производительности и снижение качества происходит при смене размеров ленты или режимов отжига. При длине линий, достигающих нескольких сотен метров, и большой инерционности газовых печей изменение режима их работы приводит к переходным процессам - температура на значительной длине ленты не удовлетворяет необходимым условиям, что и является причиной образования брака.
Ввод в линию индукционных нагревателей создает дополнительный канал управления. Их практическая без инерционность позволяет получать необходимую температуру на выходе из радиационной печи t4 при смене ленты или режима отжига.
Также можно работать с различными толщинами ленты на одной скорости без изменений в настройке воздушных ножей, обеспечивающих стабильную величину покрытия, что ведет к повышению качества продукции. На рис. 2 показаны температурные профили лент с различной толщиной, которые двигаются в линии с одной скоростью. Лента с большей толщиной после прохождения печи прямого газового нагрева имеет меньшую температуру, чем лента с меньшей толщиной. Изменение мощности индукционных нагревателей позволяет получить такую температуру на выходе из индуктора для каждой толщины ленты, чтобы после дальнейшего прохождения через радиационную печь на выходе иметь необходимую температуру по технологии.
Рис. 2. Температурные профили для режимов отжига ленты коммерческого качества при скорости 91 м/мин для различной толщины ленты: 1 - 0,7 мм; 2 - 0,75 мм; 3 - 0,8 мм; 4 - 0,9 мм; 5 - 1 мм.
Чем больше мощность индукционных нагревателей, тем для большего диапазона толщин ленты можно реализовывать «оптимальные» переходные процессы (только путем изменения мощности индукторов). Зная ограничения на максимальную разницу в размерах ленты, которая допускается при сварке двух лент (обычно она составляет 20%), можно определить необходимую мощность индукторов для реализации «оптимальных» переходных процессов.
Другой особенностью этих переходных процессов является то, что температурные кривые пересекаются в одной точке - точке А (рис. 2). Расположение этой точки и уровень температуры в ней для каждого режима отжига не меняется при различных толщинах ленты и скорости линии. Эти данные получены с помощью нелинейной модели расчета температурных режимов нагрева ленты (НТМ). В линейном случае и при допущении равномерности температуры по ширине ленты температуру в точке А и ее положение внутри индуктора (рис. 3) можно определить по простым формулам:
где t0 - температура ленты на входе; tf - выходная температура ленты; а - активная длина печи с прямым газовым нагревом; b - активная длина индукторов; с - активная длина радиационной печи; Р0 - средняя удельная мощность прямого газового нагрева; Рc - средняя удельная мощность радиационного нагрева.
Систему управления по контролю температуры в одной точке можно применять при «оптимальных» переходных процессах и для «глубоких» переходных процессов (изменение мощности индукторов и скорости движения ленты).Каскадный управляющий контур последовательно изменяет мощность индукционных нагревателей и скорость движения ленты в линии для получения необходимой температуры в точке А.
Эта система особенно эффективна при работе линии без изменения режима отжига и при частой смене размеров ленты, когда газовые печи работают в одном режиме (при одной рабочей температуре, которая поддерживается локальной системой управления). При изменении режима обработки необходимо перенастраивать печи, точка управления А изменится и основное преимущество этой системы управления - простота - будет утеряно.
Рис. 3. Особая точка А в линии горячего цинкования ленты с применением индукционного нагрева (ПГН - зона прямого газового нагрева; ИН - зона индукционного нагрева; РН - радиационного нагрева)
Также можно использовать данную систему управления при разделении всей номенклатуры ленты на группы, в которых могут быть реализованы «оптимальные» переходные процессы, тем самым снизив количество «глубоких» переходных процессов. Потеря качества продукции будет значительно снижена путем уменьшения «глубоких» переходных процессов.
Преимущество применения индукционного нагрева при «глубоких» переходных процессах показано на рис. 4, где приведены отклонения температуры ленты в точке t4 от температуры 735 °С при изменении толщины ленты с 0,9 до 1,5 мм (данные получены при помощи модели DTM). Без индукторов для ленты толщиной 0,9 мм необходима скорость 68,8 м/мин и для более толстой ленты - 1,5 мм - 41,3 м/мин. При использовании индукторов скорость ленты толщиной 0,9 мм - 86,8 м/мин, для ленты толщиной 1,5 мм - 54,8 м/мин. Это позволяет существенно снизить колебания температуры ленты при переходных процессах.
Рис. 4. Температурные переходные процессы при смене ленты с толщиной 0,9 мм на ленту с толщиной 1,5 мм при режиме горячего цинкования ленты коммерческого качества (1 - без индукторов, v = 68,8/ 41,3 м/мин; 2 - с индукторами, v = 86,8/54,8м/мин,Р = 1150/1390 кВт; 3 - с индукторами, v = 94,5/58,2 м/мин, Р = 1840/1750 кВт)
Рис. 5. Изменение скорости ленты v, мощности индукторов Р, температуры ленты на входе индукторов (t2) и после газового нагрева (t4) при смене ленты толщиной 0,9 мм на ленту толщиной 1,5 мм с использованием индукторов.
Удовлетворительные результаты при «глубоких» переходных процессах могут быть получены с помощью простых алгоритмов. Например, изменение скорости входящей ленты происходит при входе сварного шва в предварительный нагреватель, а мощность индукторов изменяется при входе сварного шва в индукторы (рис. 5). Расположение сварного шва является указателем начала переходных процессов, и для достижения лучших результатов очень важным является точное определение его местоположения.
Заключение
Выявлена особая точка в линиях непрерывной термообработки ленты. Поддержание постоянной температуры всего сортамента ленты в этой точке на расчетном уровне позволяет оптимизировать тепловые переходные режимы в линии и снизить брак, связанный со сменой номенклатуры ленты. На этом принципе строится запатентованная система управления в линиях горячего цинкования стальной ленты нового поколения.
Возможно Вас так же заинтересуют следующие статьи: comments powered by HyperCommentsecm-zink.ru