- Диаметр труб внутренний и внешний
- Диаметр трубопроводов
- Площадь сечения профильной трубы
- Нефтегазопроводные трубы
- Труба для стока воды
- Как сделать дугу из профильной трубы своими руками
- Пластиковые профильные трубы
- Скотч для теплоизоляции труб
- Каучуковый утеплитель для труб
- Машина трубогибочная
- Трубы толстостенные медные
Правила сооружения и эксплуатации магистральных газопроводов. Монтаж магистральных трубопроводов высокого давления
Трубопроводы высокого давления монтажу - Справочник химика 21
Трубопроводы высокого давления, поступающие на монтаж с сертификатами, хранят на складе вместе с документами. Фасонные детали трубопроводов (отводы, переходные втулки, тройники, крестовины, штуцеры) изготовляют нз тех же материалов, что и трубопроводы, в специализированных цехах. Их маркируют и отправляют на монтаж вместе с документами. [c.58]
Оборудование НАС монтируется на фундаменте. Сначала устанавливают аккумуляторы, затем насосы и вспомогательное оборудование, после чего осуществляют монтаж трубопроводов, гидроаппаратуры, регулирующих устройств и электрооборудования. Перед началом монтажа осматривают наружную и внутреннюю поверхности баллонов. Соединения очищают от следов коррозии. Установка баллонов должна быть строго вертикальной, допускаемое отклонение оси баллона от вертикали не более 0,001 его высоты. Трубопроводы высокого давления подвергают тщательному осмотру, недопустимо повреждение их. Сборку трубопроводов производят после проверки совпадений фланцев, прямолинейности труб, правильности колен и уклона. Магистральные опоры под трубопроводы должны быть забетонированы. [c.215]Широко применяют сварные фасонные части. При этом к качеству сварки предъявляют высокие требования, особенно при монтаже трубопроводов высокого давления. Сварные отводы обычно делают из нескольких частей (рис. 104). Для удобства монтажа концы труб, привариваемых к отводам, делают с косым срезом. Трубопроводы высокого давления (свыше 10 МПа) монтируют с помощью литых или кованых фасонных частей. [c.124]
Трубопроводы высокого давления монтируют из толстостенных труб и специальных соединительных частей, поставляемых в соответствии с ГОСТами и техническими условиями, а также специальной арматуры, рассчитанной на высокое давление. Все элементы трубопроводов обязательно сопровождаются необходимой технической документацией и имеют клейма, предусмотренные техническими условиями на монтаж трубопроводов. [c.275]
При монтаже трубопроводов высокого давления на 320 и 700 кгс/см длину ключей для сборки фланцевых соединений рекомендуется ограничивать величинами, приведенными в табл. 12.1. Применяемые прокладочные, набивочные и другие материалы, используемые для монтажа арматуры, должны соответствовать требованиям технической документации. [c.282]
Методы сборки трубопроводов высокого давления не отличаются от методов сборки обычных трубопроводов. Крепление трубопроводов осуществляется на более жестких и прочных опорах, кронштейнах, консолях и т. п. Монтаж производится специально обученными рабочими. Общий вид смонтированного трубопровода высокого давления показан на рис. 122. [c.245]
Значительно изменились конструкции отдельных видов основного технологического оборудования. Так, например, появились холодильники с воздушным охлаждением вместо водяных, турбокомпрессоры высокого давления вместо поршневых, трубопроводы высокого давления на сварке вместо резьбового и фланцевого соединений и т. д. Все это требует применения при монтаже технологического оборудования высококвалифицированного труда работников специальной профессии- -монтажников. [c.3]
Инструкция по изготовлению и монтажу трубопроводов высокого давления [c.298]
При монтаже трубопроводов высокого давления устанавливают опорные металлоконструкции и подвески, поднимают и укладывают трубы, соединительные детали и арматуру на опоры, соединяют все детали на фланцах с линзовыми уплотнениями, устанавливают компенсационные участки и компенсаторы. При сборке фланцевых соединений линзы заводят на место при помощи специальных щипцов. Фланцевые соединения затягивают равномерно попеременным затягиванием крест-накрест гаек с постоянным контролем параллельности фланцев. При сборке трубных узлов под сварку смещение кромок деталей не должно превышать 10% толщины стенки до 20 мм и быть не более 2 мм при толщине стенки более 20 мм, отклонение прямолинейности 1 мм, перпендикулярности плоскости торца труб к оси детали — 0,5 мм. [c.443]
Требования, которые следует учитывать при проектировании монтажа и эксплуатации трубопроводов высокого давления, принципиально не отличаются от требований, предъявляемых к трубопроводам нормального давления. Однако в связи с тем, что последствия, которые могут иметь место при неисправностях линий высокого давления неизмеримо тяжелее, следует эти требования повторить и детализировать. [c.249]
В связи с тем, что на трубопроводах высокого давления получаются большие габаритные размеры фланцевых соединений с большим весом, необходимо стремиться к монтажу трубопроводов на сварке, сводя до необходимого минимума количество разъемных (фланцевых) соединений. [c.250]
При монтаже трубопроводов высокого давления так же, как и при монтаже трубопроводов низкого и нормального давлений, требуется ряд фасонных частей (фитингов) для осуществления поворота линий, ответвлений, изменения размеров сечения линий и т. д. Применяют фитинги следующих наименований колена, калачи, угольники, тройники, переходы, вставки, карманы и др. [c.262]
МОНТАЖ- ЭКСПЛУАТАЦИИ И РЕВИЗИЯ ТРУБОПРОВОДОВ ВЫСОКОГО ДАВЛЕНИЯ [c.305]
Монтаж трубопроводов высокого давления в отличие от монтажа трубопроводов нормального давления имеет некоторые особенности как технического, так и организационно-документального порядка. [c.305]
При оформлении приемки смонтированных коммуникаций трубопроводов высокого давления к приемо-сдаточному акту должны быть приложены следующие документы складская ведомость труб высокого давления ведомость проверки труб перед выдачей их в монтаж заводские сертификаты и документы по проведенной выборочной проверке механических свойств материала труб сертификаты, паспорты и акты на фасонные части, арматуру и крепежные изделия, полученные от заводов-изготовителей ведомость проверки резьбы фланцевых соединений высокого давления исполнительная схема коммуникаций высокого давления с нанесенными на нее номерами труб, фланцев фасонных частей, крепежа, сварных швов и т. п. с приложением сводной ведомости документация о выполненном на месте монтажа гнутье труб документация о выполнении сварки трубопроводов высокого давления результаты гидравлического испытания трубопроводов акт комиссии по приемке трубопроводов высокого давления после монтажа. [c.214]
На монтаж холодильника, маслоотделителя и трубопроводов компрессора ЦКО-10/290-320 распространяются указания о монтаже аппаратов и трубопроводов высокого давления, приведенные в п. 5, гл. 1. [c.238]
МОНТАЖ ТРУБОПРОВОДОВ ВЫСОКОГО ДАВЛЕНИЯ [c.407]
Примерная удельная трудоемкость операций по монтажу трубопроводов высокого давления приведена в табл. 1. [c.407]
При монтаже трубопроводов высокого давления применяют П-образные компенсаторы двух типов гнутые (для трубопроводов небольших диаметров) и собранные на фланцах из прямых труб и готовых соединительных частей. Компенсаторы могут быть выполнены плоскими или пространственными. [c.413]
По окончании монтажа трубопроводов высокого давления составляется акт, подтверждающий выполнение работ в соответствии с проектом и техническими условиями на монтаж, а также соблюдением установленных правил и норм (СНиП П1-Г.9-62, Нормы и технические условия на проектирование, монтаж и эксплуатацию стальных внутризаводских и цеховых газопроводов для горючих газов в пожаро- и взрывоопасных производствах химической цро-мышленности , НиТУ ХП—62 и др ). [c.414]
При монтаже трубопроводов высокого давления рубашки надеваются на трубы до навертывания фланцев, а их уплотнение осуществляется только при помощи сальников. Звено, состоящее из грубы с навернутыми фланцами и рубашки с надетыми, но не затянутыми сальниками, должно поступать в монтаж в собранном виде. [c.432]
При монтаже и ремонте трубопроводов высокого давления применяют арма-туру, рассчитанную на условное давление Ру = 250 кГ/см . [c.67]
Трубопроводы и арматура установок высокого давления являются весьма ответственной частью оборудования и должны находиться под постоянным контролем обслуживающего персонала. Разрыв трубопроводов высокого давления приводит к тяжелым последствиям — взрывам, пожарам, травмированию обслуживающего персонала и др. Поэтому изготовлению трубопроводов и арматуры, их испытанию, монтажу коммуникаций и контролю за ними должно быть уделено особое внимание. [c.351]
Для трубопроводов высокого давления кроме перечисленной документации необходимы дополнительно записи по термообработке труб после гнутья (если таковое производилось на монтаже) и по термообработке сварных стыков [c.397]
В маслоподвалах и в тех помещениях, где монтируются компрессорные установки, воздуходувные машины, центрифуги, турбогенераторные установки, эксгаустеры, подъемные машины, прокатные станы и другие сложные агрегаты, а также связанные с ними трубопроводы высокого давления и трубопроводы, изготовленные из специальных материалов и сталей, должны быть закончены, также устройство бетонных полов, внутренняя штукатурка (если она предусмотрена проектом), остекление окон и фонарей (независимо от времени года) и навеска дверей и врезка замков. В машинных залах должны быть окрашены стены и потолки. Если по техническим условиям на монтаж тех или иных видов оборудования и трубопроводов или по другим заранее установленным требованиям производство монтажных работ допускается только при положительной температуре, то до наступления зимы должны быть закончены работы по утеплению соответствующих помещений и оборудованию их системой отопления. [c.375]
При проектировании трубопроводов высокого давления следует учитывать значительный вес вентилей и, как правило, предусматривать для них отдельные опоры, при этом короткие отрезки трубопроводов не Н ждаются в подвешиваниии. Для облегчения монтажа вентилей над ними должно быть оставлено пространство для подъезда крана или подвешивания талей. Тепловое расширение трубопроводов высокого давления обычно не вызывает осложнений, так как оно компенсируется прису-И1ей таким труба.м гибкостью. [c.588]
В тех случаях, когда трасса трубопровода предусматривает естественные повороты, необходимость в установке компенсаторов отпадает, так как гибкость прямых участков трубопровода, расположенных под углом друг к другу, обеспечивает возможность са-мокомпенсации. Этот способ весьма удобен, и, наряду с гнутыми компенсаторами, самокомпенсация используется при монтаже трубопроводов высокого давления (исключение составляют трубопроводы с рубашками). [c.224]
Прокладка и эксплуатация трубопроводов высокого давления имеет свои особенности. На изготовление частей трубопроводов высокого давления 10,0—85 н/мм (100—850 атм), монтаж трубопровода и сдачу его в эксплуатацию имеются специальные технические условия. Трубопроводы высокого давления прокладывают из бесшовных толстостенных труб, изготовленных из углеродистой или легированной стали. Аварии на коммуника- [c.342]
При монтаже арматуры следует ограничивать силовое воздействие на арматуру, во избежание деформации, заклинивания подвижных соединений и возникновения ледопустимых напряжений. Гайки шпилек и болтов затягиваются равномерно и постепенно с разных сторон фланца. Усилие затяга должно быть соразмерно диаметру и материалу крепежа и, как правило, должно контролироваться путем применения ключей с ограничением крутящего момента или усилия на рукоятке ( тарированных ключей ). Арматура, работающая на трубопроводах высокого давления, нуждается в особо тщательном контроле усилий затяга шпилек, что обеспечивается измерением удлинения шпилек при затяжке. Перед установкой шпилек в таких трубопроводах резьбу шпилек протирают графитом, водно-графитовой эмульсией или наносят смазку ВНИИНП-232, чтобы воспрепятствовать- схватыванию металла шпилек и гаек и обеспечить возможность разборки соединения после длительной эксплуатации. [c.282]
Кованые и литые стальные детали трубопроводов (отводы, тройники, крестовины, переходы) изготовляют по особому заказу по индивидуальным чертежам. Применяются в тех случаях, когда запрещается установка сварных фасонных деталей, а также когда условия монтажа не допускают применения гнутых деталей. На трубопроводах высокого давления (свыше 64 кгс1см ) применяются литые или кованые тройники, переходы, крестовины. Отливки из углеродистой стали марок 15Л, 20Л, 25Л применяются на трубопроводах с температурой среды до 450°. Для работы при температурах среды свыше 450° применяются отливки из легированных сталей. [c.50]
Трубопроводы высокого давления применяются в промышленных установках синтеза аммиака, полиэтилена, метилового спирта, гидрирования углей и в других производствах с давлением среды в сотни атмосфер. Применение высоких давлений предъявляет повышенные требования к качеству работ по сооружению трубопроводов. Монтаж трубопроводов высоких давлений ведется с особой тщательностью, в соответствии с требованиями ведомственных технических условии. При монтаже трубопроводов химических предприятий пользуются техническими условиями, разработанными ГИАП, а в газовой и топливной промышленности — Гипрогазтоппромом. В соответствии с этими техническими условиями трубопроводы высокого давления делятся на три категории Стабл. И). [c.244]
Приемка производится специальной комиссией, осуществляющей наружный осмотр смонтированных коммуникаций высокого давления проверку полноты и качества монтажа, в частности проверку наличия шпилек, гаек, линз и их соответствие орнаментовке сравнение готовой коммуникации с ее исполнительной схемой и одновременный осмотр всех клейм проверку правильности гнутья труб (радиус гибов, эллиптичность) выборочную разборку одного или двух фланцевых соединений, проверку резьб, линз, уплотнительной поверхности труб наружный осмотр сварных соединений трубопроводов высокого давления (в соответствии с п. 64 ТУ 8101—54) проверку полноты документации. [c.214]
Монтаж трубопроводов высоких давлений ведется в соот ветствии с техническими условиями, разработанными проектными организациями для химической, газовой и нефтяной промышленности. В соответствии с этими техническими условиями все рабочие температуры в установках высокого давления делятся на три температурные ступени I ступень — интервал рабочих температур от —50 до -Ь200°С II ступень — интервал рабочих температур от -t-201 до -Ь400°С III ступень — интервал рабочих температур от +401 до -Ь510°С. [c.13]
В технологических трубопроводах резьбовые соединения труб и деталей имеют ограниченное применение их используют главным образом при монтаже водогазопроводных труб, систем маслосмазки, а также трубопроводов высокого давления. [c.102]
chem21.info
Монтаж - трубопровод - высокое давление
Монтаж - трубопровод - высокое давление
Cтраница 1
Монтаж трубопроводов высокого давления в отличие от монтажа трубопроводов нормального давления имеет некоторые особенности как технического, так и организационно-документального порядка. [1]
Монтаж трубопроводов высоких давлений ведется в соот: ветствии с техническими условиями, разработанными проектными организациями для химической, газовой и нефтяной промышленности. В соответствии с этими техническими условиями все рабочие температуры в установках высокого давления делятся на три температурные ступени: I ступень - интервал рабочих температур от - 50 до 200 С; II ступень - интервал рабочих температур от 201 до 400 С; III ступень - интервал рабочих температур от 401 до 510 С. [2]
При монтаже трубопроводов высокого давления на 320 и 700 кгс / см2 длину ключей для сборки фланцевых соединений рекомендуется ограничивать величинами, приведенными в табл. 12.1. Применяемые прокладочные, набивочные и другие материалы, используемые для монтажа арматуры, должны соответствовать требованиям технической документации. [3]
При монтаже трубопроводов высокого давления устанавливают опорные металлоконструкции и подвески, поднимают и укладывают трубы, соединительные детали и арматуру на опоры, соединяют все детали на фланцах с линзовыми уплотнениями, устанавливают компенсационные участки и компенсаторы. При сборке фланцевых соединений линзы заводят на место при помощи специальных щипцов. Фланцевые соединения затягивают равномерно попеременным затягиванием крест-накрест гаек с постоянным контролем параллельности фланцев. При сборке трубных узлов под сварку смещение кромок деталей не должно превышать 10 % толщины стенки до 20 мм и быть не более 2 мм при толщине стенки более 20 мм, отклонение прямолинейности 1 мм, перпендикулярности плоскости торца труб к оси детали - 0 5 мм. [4]
При монтаже трубопроводов высокого давления применяют П - образные компенсаторы двух типов: гнутые ( для трубопроводов небольших диаметров) и собранные на фланцах из прямых труб и готовых соединительных частей. Компенсаторы могут быть выполнены плоскими или пространственными. [6]
При монтаже трубопроводов высокого давления нельзя допускать натяги, подгибы и другие способы, могущие вызвать перенапряжение в отдельных местах трубопровода. Очистку уплотнительных поверхностей на фланцах производят заранее, до установки узлов трубопровода на место. [7]
При монтаже трубопроводов высокого давления рубашки надеваются на трубы до навертывания фланцев, а их уплотнение осуществляется только при помощи сальников. Звено, состоящее из грубы с навернутыми фланцами и рубашки с надетыми, но не затянутыми сальниками, должно поступать в монтаж в собранном виде. [8]
Работы по монтажу трубопроводов высокого давления подразделяют на заготовительные, сварочные и монтажные. В связи с большим объемом заготовительных работ ( комплектование труб и деталей, разметка, резка и обработка концов труб под нарезание резьб и сварку, гнутье труб, предварительный контроль качества труб на магнофлокс и гидравлические испытания, а также ревизия и испытание арматуры) их выполняют в монтажных мастерских современными индустриальными методами. Заготовительные работы, выполняют в мастерской монтажной организации в цехах трубных заготовок, имеющих участки трубопроводов высокого и низкого, давления, а в цехах металлоконструкций изготавливают onojibi, подвески, крепежные хомуты, кронштейны и другие изделия. В цехах трубных заготовок или на специальной площадке монтажных мастерских на сборочных стендах с использованием подъемных механизмов технологического оборудования и инструмента собирают, сваривают транспортабельные узлы трубопроводов ( плоских и пространственных) и устанавливают на них соединительные части и арматуру. Индустриализация изготовления - узлов трубопроводов значительно повышает качество монтажных работ, производительность труда и сокращает сроки монтажа. Основой правильной организации заготовительных работ в монтажных мастерских являются поточность и максимальная механизация всех операций технологических процессов. [9]
Работы по монтажу трубопроводов высокого давления подразделяют на заготовительные и монтажно-сбо-рочные. [10]
Специфика технологического процесса монтажа трубопроводов высокого давления зависит от конструктивных особенностей деталей трубопроводов и их расположения в разнообразных производственных установках высокого давления. [11]
Для изготовления и монтажа трубопроводов высокого давления наиболее распространенных производств Минмонтажспец-строй СССР разработал и утвердил типовые технологические карты, которые содержат все данные, требуемые техническими условиями. [12]
Анализ работ при монтаже трубопроводов высокого давления позволяет установить, что основной объем падает на заготовительные операции. В табл. 37 приведены ориентировочные данные трудоемкости отдельных заготовительных и монтажно-сборочных работ. [13]
Отсутствие литературы по вопросам монтажа трубопроводов высокого давления создает серьезные затруднения при подготовке и повышении квалификации инженерно-технических работников, поэтому в настоящей книге автор обобщает многолетний производственный опыт в этой области, с учетом всего нового и передового, что появилось в практике изготовления и монтажа трубопроводов высокого давл ения в последние годы. [14]
Работы по изготовлению и монтажу трубопроводов высокого давления проводятся с соблюдением основных нормативных документов ( МРТУ 26 - 01 - 9 - 67, ТУ 8100 - 50, ПУГ-69) а также технических условий на отдельные трубопроводы высокого давления. [15]
Страницы: 1 2 3
www.ngpedia.ru
Проблемы механизации строительства магистральных трубопроводов большого диаметра высокого давления | Статьи | ТРУБОПРОВОД.рф
Обзор сессии проблемного научно-технического совета Российского союза нефтегазостроителей.
Дальнейшее развитие трубопроводного транспорта России будет обеспечиваться сооружением сверхдальних магистралей нового поколения с высоким уровнем безопасности, надежности и эффективности, достигаемых, в том числе, за счет снижения собственного энергопотребления и использования высокого давления.
Ниже приведен перечень с краткой технической характеристикой проектируемых и строящихся в настоящее время магистральных трубопроводов высокого давления (ТАБЛИЦА 1).
Таб.1 Проектируемые и строящиеся магистральные трубопроводы высокого давления (10 Мпа и выше)
(Толщина стенки труб указана применительно классу безопасности участка: нормальный - Н; средний - С; высокий – В. Отдельные трубопроводы рассчитывались по методике СНиП 2.05.06-85* «Магистральные трубопроводы». Для таких трубопроводов принята аналогия: III-IV категория нормальная; I-II категория - средняя; категория В - высокая.)
Таб. 1 (продолжение)
Как видно из таблицы 1, в ближайшее время будут строиться магистральные трубопроводы диаметром 1020-1420 мм на давление:
• сухопутные нефтепроводы — 10-14 МПа;
• морские газопроводы - до 20-22 МПа.
Для прокладки магистральных трубопроводов предусматривается использование труб из сталей класса прочности Х6О, Х70 и Х80. Определяющий техническую политику в проектировании и строительстве СНиП 2.05.06-85* «Магистральные трубопроводы распространяется на системы с рабочим давлением до 10 МПа. Для трубопроводов высокого давления (выше 10 МПа) общероссийские нормативные документы пока не разработаны. Для каждого проекта сухопутных трубопроводов высокого давления составляются специальные технические условия. В более выигрышном положении оказалась прокладка морских трубопроводов, для которых ОАО «Газпром» утвердил в 2006 г. норвежский стандарт DNV-05-F 101 «Подводные трубопроводные системы» как стандарт СТО Газпром 2-3-7-050-2006.
Без высококлассной механизации всех видов строительно-монтажных и специальных работ, включая контроль их качества, не представляется возможным выполнение гигантских объемов земляных, сварочных, изоляционных работ при сооружении переходов через реки, автомобильные и железные дороги на тысячекилометровых трассах газопроводов и нефтепроводов.
СООРУЖЕНИЕ МАГИСТРАЛЬНЫХ ТРУБОПРОВОДОВ БОЛЬШОГО ДИАМЕТРА ВЫСОКОГО ДАВЛЕНИЯ ИМЕЕТ СПЕЦИФИЧЕСКИЕ ОСОБЕННОСТИ, КОТОРЫЕ ПОТРЕБУЮТ ПЕРЕСМОТРА ПРИНЦИПОВ И СХЕМ ОРГАНИЗАЦИИ И ТЕХНОЛОГИИ СТРОИТЕЛЬСТВА, ОБЕСПЕЧЕННОСТИ СРЕДСТВАМИ МЕХАНИЗАЦИИ ВСЕГО КОМПЛЕКСА РАБОТ.
Во времена функционирования Миннефтегазстроя была отработана как обязательная норма успешного строительства линейной части магистральных трубопроводов комплексная механизация и автоматизация поточного выполнения всех технологических строительно-монтажных операций. Использование научных основ, методов и типовых схем позволяло не только формировать оптимальные комплексы специальной технологической техники, но и определять направления модернизации, технические параметры недостающих машин и механизмов.
Планировалась долгосрочная модернизация и создание средств механизации для трубопроводного строительства. Крупное специализированное конструкторское бюро «Газстроймашина», используя опыт тракторной и других отраслей машиностроения, создавало новые образцы техники. Действовали единые правила испытания опытных образцов. До серийного производства их доводили на общемашиностроительных заводах и специализированных предприятиях по выпуску техники для сооружения трубопроводов. Такая практика в силу изменения сегодня потеряна.
Задачи механизации строительства трубопроводов, создания новых машин и механизмов выведены из сферы государственного управления и деятельности заказчика строительства. Возможности же строителей в создании новой техники весьма ограничены, оплата выполнения конструкторских работ, выпуска опытных образцов и постановки новых машин на серийное производство для отдельных организаций неподъемна. К тому же утрачены прежние производители техники для строительства трубопроводов.
Kак правило, комплектование средств механизации производится под конкретные проекты. Недостающие по требуемым техническим параметрам машины и механизмы приобретаются за рубежом. Однако, как показала практика, даже в широком арсенале зарубежной техники не всегда возможно найти специальные строительные машины, удовлетворяющие требованиям эффективного производства работ на многолетнемерзлых грунтах, в заболоченной тундре и горных районах. В то же время созданная еще в советское время для этих целей техника осталась в образцах. Так, например, в пяти экземплярах был изготовлен экскаватор траншейный роторный ЭТР-307. Этот экскаватор способен разрабатывать траншею полного профиля для трубопроводов диаметром 1420 мм в мерзлых грунтах V-VIII категорий в условиях Крайнего Севера. Его применение после модернизации могло бы решить многие проблемы прокладки трубопроводов по ямальским трассам. Строительные организации обращаются с просьбой к ОАО «Газпром» профинансировать изготовление такой техники.
ЗАО «Ямалгазинвест» и ОАО «ВНИПИгаздобыча» — заказчик и генеральный проектировщик газопровода Бованенково-Ухта (первенца гигантского трубопроводного проекта «Газовый Ямал» общей производительностью 250 млрд м3 в год) поручили ЗАО «Газстроймашина» и «НГС-оргпроектэкономика» составить каталог специальных технических средств, необходимых для строительства линейной части этого газопровода.
Основным материалом для разработки данного каталога явились принятые проектные решения, о которых рассказала главный инженер проекта ОАО "ВНИПИгаздобыча" С.А.Дзюба. Предусмотрено строительство двухниточного магистрального газопровода диаметром 1420 мм, рассчитанного на рабочее давление 11,8 МПа, девяти двухцеховых компрессорных станций (ГПА 16, ГПА 25), на переходе через Байдарацкую губу — четырехниточного перехода из труб диаметром 1220 мм. В проекте впервые применяются высокопрочные марки стали для строительства трубопровода — К65, Х80 и внутреннегладкостное покрытие. Общая протяженность трубопроводов от трех газовых промыслов Бованенковского месторождения составляет 1100 км.
ФОТО 1. Дорожно-строительный комплекс "ПОЛЯРНЫЙ СЛОН"
ФОТО 2. Роторный экскаватор типа ЭТР-309
В течение последних трех лет проводились широкомасштабные инженерно-геологические изыскательские работы с привлечением специализированных организаций. В первую очередь это касалось трассы на участке сплошного распространения многолетнемерзлых грунтов до компрессорной станции Воркутинская и по трассе морского перехода в створе Байдарацкая-Ярынская.
В результате тщательных расчетов, моделирования теплотехнического взаимодействия трубы и грунта были установлены температурные режимы участков. Для транспорта по территории полуострова требуется охлаждение газа на месторождении до отрицательных температур (-2 0С). На участке перехода через Байдарацкую губу газ должен быть теплым. На КС «Ярынская» следует подать газ с температурой 0 °С.
Температура газа при транспортировке определила основные конструкции линейной части. На участке выхода с Бованенковского месторождения и до 60-го км трассы температура газа не превышает —7 °С. Таким образом, нет активного воздействия холодного трубопровода на сезонно деятельный слой, ареал обмерзания трубы не мешает нормальной работе сезонного талого слоя. Участок проектируется без теплоизоляции.
Затем температура газа снижается до -10 °С, появляется необходимость изолировать верхний сегмент трубопровода для того, чтобы уменьшить приток холода в сезонно деятельный слой (толщина изоляции — 50 мм до 90-го км трассы). Там, где температура газа опускается ниже 12 °С, необходима кольцевая изоляция всего трубопровода.
При транспорте холодного газа на участках распространения талых грунтов применяется сплошная теплоизоляция. На русловой части используются утяжелители чугунные кольцевые, а в пойменной части — утяжелители типа УБО. Применение теплоизоляции по расчетам позволило уменьшить обмерзание трубы.
НА ОСНОВЕ ИНЖЕНЕРНО-ГЕОКРИОЛОГИЧЕСКОГО РАЙОНИРОВАНИЯ ОПРЕДЕЛЕНЫ ЧЕТЫРЕ ХАРАКТЕРНЫХ УЧАСТКА ТРАССЫ. ЭТО ПОЛУОСТРОВ, УЧАСТОК ОТ КС «ЯРЫНСКАЯ» ДО КС «ГАГАРАЦКАЯ», КС «ГАГАРАЦКАЯ»-КС «УСИНСКАЯ», КС «УСИНСКАЯ»-УХТА.
Первый участок на территории Ямала - наиболее сложный и ответственный. Специфика связана с многолетнемерзлыми грунтами сплошного типа, их большой льдистостью и просадочностью при оттаивании: грунты находятся в слабоустойчивом состоянии. В этих супесях очень сложно обеспечить устойчивое положение трубопровода, к тому же имеют место сильные проявления склоновых процессов. Второй участок - это выход из Байдарацкой губы, от КС до КС «Гагарацкая». Также сплошное распространение многолетнемерзлых грунтов. Первые 30-40 км выхода из губы очень сложные, проблемы сходны с ямальскими. Далее трасса проходит в районе Полярного Урала, появляются скальные участки, и здесь несущая способность грунтов повышается.
Очень сложен специфический участок от КС «Гагарацкая» до КС «Усинская». Заканчивается мерзлота сплошного типа, начинается островная мерзлота. Существенно меняются грунтовые условия; суглинки, участки с высокой льдистостью, просадочные карстовые участки. Острую дискуссию вызвал вопрос: холодным или теплым следует транспортировать газ по этому району?
И последний участок от КС «Усинская» до Ухты характеризуется большой обводненностью территории, заболоченностью, проявлением карстозвых процессов, имеют место эрозионные и оползневые зоны.
На участках транспортировки теплого газа, помимо теплоизоляции, предусматривается термостабилизация в местах просадочных грунтов и подсыпка основания трубопровода для уменьшения воздействия на вечную мерзлоту.
С учетом уклонов местности на полуострове до 30 необходимо применять противоэрозионные контейнеры, термостабилизацию и теплоизоляцию на береговых участках и при пересечении водотоков. При пересечении рек, наряду с традиционным траншейным методом, будет применяться наклонно направленное бурение.
На переходе через Байдарацкую губу расчеты делались по нормам DNV. На первую нитку необходимо порядка 1 млн т труб, из них 65% составляют трубы с толщиной стенки 27,7 мм. Погонный метр трубы весит почти тонну.
Транспортная схема доставки техники и грузов для строительства и эксплуатации стала серьезной проблемой. Пришли к выводу о необходимости достройки железной дороги Обекая-Бованенково. В настоящее время есть железная дорога до станции Пайота. Предполагается также строительство автозимников.
Доставка тяжелых труб с изоляцией требует особого внимания. Принято решение о том, что строительство трубопровода на полуострове Ямал необходимо выполнить в один зимний период, поскольку нельзя оставлять трубу без холодного газа летом для предупреждения обводнения траншеи и ее разрушения.
Предусматривается несколько промежуточных баз с использованием ледовых площадок для сварки двухтрубных секций. Далее трубы будут развозить по специальным снеговым карманам.
На участках, кроме головного, предполагается двухлетний цикл строительства. Рекомендовано применение 18-метровых труб, хотя будут сложности с изготовлением и транспортировкой. Такая длина труб позволяет уменьшить объем сварки в полтора раза и обеспечить заданный темп строительства.
Необходимо применение соответствующей для Ямала землеройной роторной техники. Возможно применение комбинированных способов разработки траншеи в зависимости от грунтовых условий и от рельефа местности. Для укладки трубопровода с такими весовыми характеристиками необходимо 11 -12 трубоукладчиков.
Комплекс для сварки труб с такими параметрами, так же как и нормативы на сварку трубопроводов с рабочим давлением 11,8 МПа, находится в разработке. На всю трассу потребуется 22 строительных потока с привлечением тяжелой техники. Необходимо до 700 тяжелых трубоукладчиков, 16 роторных экскаваторов типа ЭТР-309, экскаваторы одноковшовые, 315 постов ручной сварки, бульдозеры тяжелые, более 200 плетевозов грузоподъемностью 40-48 т.
Предполагается строительство двух дорог 4-й категории с использованием различных геотекстильных материалов, осноования из георешеток, защитного слоя и укладки плит.
О разработке каталога и выборе необходимых специальных технических средств для строительства линейной части газопровода Бованенково-Ухта доклад сделал заместитель генерального директора АО «НГС-оргпроектэкономика» Ю.А.Маянц.
После распада СССР значительно сократились объемы трубопроводного строительства в нашей стране. Это повлекло за собой сокращение, а зачастую и полную остановку разработки и выпуска новой техники для этих работ. Отсутствие долгосрочных контрактов привело к значительной сверхнормативной наработке техники и невозможности вкладывать существенные средства в создание и закупку новых машин.
Такое положение дел и решение довольно локальной строительной задачи — освоение Ямала — требует весьма осмотрительно относиться к подбору техники и, соответственно, — принимаемым проектным решениям.
При этом первой задачей становится обеспечение строительства дорожной сетью необходимого качества. Очевидно, что для Ямала это — строительство снежно-ледовых дорог повышенной прочности. В настоящее время уже работает несколько комплексов «Полярный слон», которые используют известную технологию предварительного нагрева поверхности снега с последующим его виброуплотнением.
Создание дорожной сети позволит широко применить различные машины для транспортировки грузов, которые используют в качестве базовых — серийно выпускаемые колесные и гусеничные машины.
Учитывая, что к настоящему времени еще не утеряно производство ряда видов техники, ее можно модернизировать для строительства на Ямале.
К машинам такого класса следует отнести экскаватор ЭТР-309, разработанный по договору с ОАО «Газпром», но так и не ставший серийной машиной.
Следующая проблема, решение которой проблематично с отечественной техникой — сварка. Существующие трубосварочные базы плохо приспособлены для сварки труб высокого класса прочности в сложных климатических условиях.
Высокая прочность труб создаст проблемы и для их холодного гнутья. Станок для операций с трубами такой прочности и размеров пока заявлен только фирмой "CRC-Evans".
Хотя бы в минимальных количествах для специальных работ должны быть использованы тяжелые снегоболотоходы и специальные машины на их базе.
Подбор и анализ необходимых образцов техники приводит к выводу о необходимости какой-либо, централизации в обеспечении строительства машинами. Лизинговых же фирм необходимого уровня у нас в стране не существует.
ПРИ ОСНАЩЕНИИ СТРОИТЕЛЬСТВА ТЕХНИКОЙ НЕОБХОДИМО УЧИТЫВАТЬ ЕЩЕ НЕСКОЛЬКО АСПЕКТОВ:
• снижение общего уровня квалификации персонала в сочетании с усложнением технологии требует активного внедрения средств электронного автоматического управления и компьютерной техники;
• особого внимания требует так называемая «винтаризация» техники, т, е. обеспечение ее оборудованием ДЛЯ работы в условиях низких температур;
• необходимо тщательно анализировать применяемые технологии на предмет их экономической целесообразности на всех этапах проектирования. Конечно, это удлинит процесс проектирования, но существенна сократит сроки и стоимость строительных работ;
• совершенно очевидно, что делать ставку на приобретение импортной техники недопустимо, Это определяется не «ура-патриотизмом», а тем, что затраты валюты на закупку продукции, которая вполне может выпускаться отечественными предприятиями, прямое экономическое преступление против России.
Специальные технические средства для строительства трубопроводов высокого давления.
1. Из серийно выпускаемой техники для прокладки трубопроводов высокого давления можно использовать:
• трубоплетевоз грузоподъемностью до 30 т;
• снегоболотоход грузоподъемностью от 10 до 30 т;
• гусеничные трубоукладчики с грузовым моментом от 50 до 108 тс-м;
• большинство трубозахватных и трубоподъемных средств;• трубогибочный станок фирмы "CRC-Evans";
• зарубежные станки для обработки торцов труб;
• тяговые лебедки ЛП152 и ЛП302;
• лебедка скреперная с тягой 30 тс — ЛС302;
• зарубежное оборудование для бестраншейной прокладки газопроводов методом наклонно направленного бурения;
• колесные сварочные агрегаты мощностью 100 и 200 кВт;
• гусеничные сварочные агрегаты мощностью 100 кВт;
• роторный траншейный экскаватор ЭТР 254А для использования на отдельных участках.
К специфике магистральных трубопроводов большого диаметра высокого давления следует отнести: новые конструктивные и технические решения; существенное повышение толщины стенок труб, трубных деталей и соответственное увеличение их массы; изменение жесткости плетей; использование труб более высокого класса прочности Х80, XI00; новые технологии сварки и новые сварочные материалы для обеспечения высоких показателей предела текучести сварного соединения; усложнение транспортных и грузоподъемных операций, трубоукладочных работ; выполнение переходов методом наклонно направленного бурения, а также повышенные требования к обеспечению безопасности эксплуатации с минимальным уровнем риска.
Это далеко не полный перечень специфики строительства трубопроводов такого класса. Практически все традиционно применяемые технологические операции сооружения линейной части магистральных трубопроводов должны претерпеть изменения.
Чтобы иметь представление о физических параметрах труб (толщина стенки, масса) для трубопроводов высокого давления диаметром 530-1420 мм в сравнении с трубами на обычное давление 5,5-7,5 МПа, в РОССНГС были составлены ТАБЛИЦЫ 2-5 применительно к сталям классов прочности Х70 и Х80 по трем классам безопасности.
Таб. 2 Толщины стенок труб в зависимости от диаметра и внутреннего давления (сталь класса прочности Х70), мм
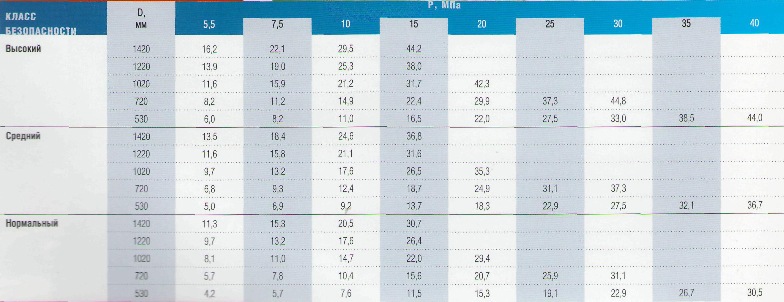
Поскольку расчет выполнялся и для труб на давление выше 10 МПа, а также для морских трубопроводов, использовались методики ASME B31.8 и DNV. Как следует из данных ТАБЛИЦ 2 и 4 толщины стенок труб для газопроводов высокого давления достигают 30-40 мм и более. Такие трубы по внешнему виду напоминают орудийные стволы с большой жесткостью.
Таб. 3. Масса одной трубы (12 м) в зависимости от диаметра и внутреннего давления (сталь класса прочности Х70), т.
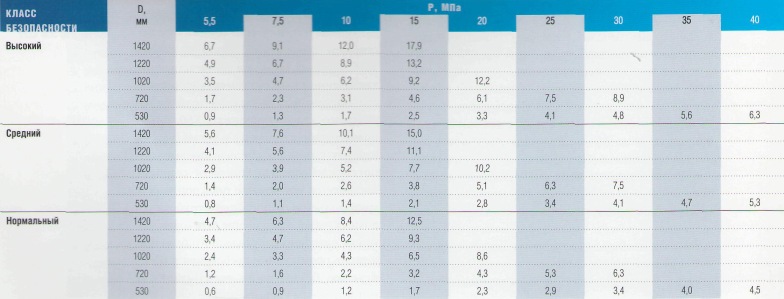
Было трудно представить, как укладывать такие трубы по рельефу местности будущей трассы. Исследования укладки толстостенных труб по заданному радиусу упругого изгиба показали, что укладка трубопровода заданного диаметра практически не зависит от уровня расчетного давления (толщины стенки).
Укладка плетей из труб с новыми параметрами реальна в рамках принятого радиуса изгиба трубопроводов. При этом не потребуется дополнительных земляных работ планировке трассы, возведения ряда дополнительных сооружений, тоннелей, эстакад, спрямляющих естественную кривизну поверхности и удорожающих строительство.
Таб. 4. Толщины стенок труб в зависимости от диаметра и внутреннего давления (сталь класса прочности Х80), мм
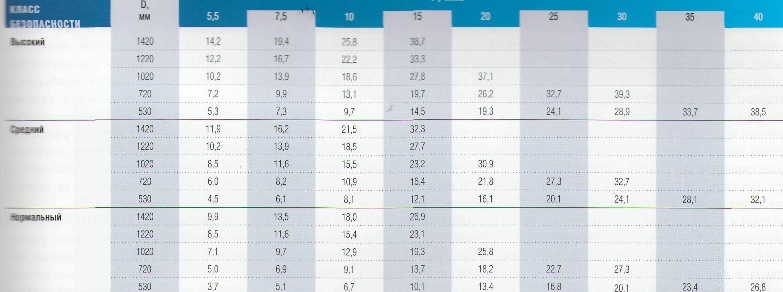
КОНЕЧНО, ЗАКАЗЧИК И СТРОИТЕЛИ ЗАИНТЕРЕСОВАНЫ В ДЛИННОМЕРНЫХ ТРУБАХ — 18 И 24 М. ПРИМЕНЕНИЕ ТРУБ ДЛИНОЙ 24 М ПОЗВОЛИТ СНИЗИТЬ ОБЪЕМЫ СТРОИТЕЛЬНО-МОНТАЖНЫХ РАБОТ НА 40% И СОКРАТИТЬ РАСХОДЫ НА ЖЕЛЕЗНОДОРОЖНЫЕ ПЕРЕВОЗКИ ПОЧТИ В ДВА РАЗА. ОДНАКО НЕ СЛЕДУЕТ ЗАБЫВАТЬ 0 МАССЕ ТРУБ БОЛЬШОГОДИАМЕТРА И ВЫСОКОГО ДАВЛЕНИЯ (см. ТАБЛИЦЫ З И 5).
Таб. 5. Масса одной трубы (12 м) в зависимости от диаметра и внутреннего давления (сталь класса прочности Х80), т
Так, трубы диаметром 1420 мм из сталей класса прочности Х70 для давления 10 МПа будут иметь массу 12 т, для давления 15 МПа — около 18 т, даже из сталей класса прочности Х80 (К65) для 10 МПа их масса составит 10,6 т и для 15 МПа — 15,7 т.
Об использовании труб из сталей более высокого класса прочности говорить преждевременно, хотя японские производители готовы уже в настоящее время выпускать трубы из сталей XI00 и даже Х120. Для тяжелых труб, особенно соединенных в секции, потребуются новые транспортные средства, более мощные трубоукладочные механизмы при строительстве. Конечно, заказ труб определенной длины будет ориентирован на рельеф местности по трассе, на транспортные возможности. Требования к геометрическим параметрам труб, свариваемости трубных сталей и другим показателям, которые в первую очередь интересуют строителей трубопроводов высокого давления, будут более жесткими.
Генеральный директор 000 «Лизингстроймаш» АГ.Горбунов отметил ряд организационных и технических проблем, с которыми встречаются строители при выполнении работ. В полученных к производству работ проектных материалах имеют место большие отклонения от фактического рельефа местности, что вызывает увеличение объемов планировочных работ, срезки грунта и дополнительные издержки. В чертежах закладываются уклоны более 30°, что превышает допустимые уклоны для работы механизмов. Отсутствуют специальные машины для переработки в щепу порубочных остатков и их утилизации. Отсюда дополнительные затраты, связанные с вывозом порубочных остатков за пределы полосы отвода в специальные карьеры. Из-за отсутствия специальной техники для вывозки и раскладки труб в горных условиях трассы применяется сложная традиционная технология буксирования.
Отсутствует эффективное оборудование для рыхления и разработки скальных грунтов в охранных зонах и других местах, где нельзя производить буровзрывные работы. Использование бульдозеров с рыхлителями вызывает увеличение затрат по засыпке трубопровода. Из-за высокой стоимости камнедробильных машин засыпка на горных участках производится привозным песком с большими потерями. Только применение инвентарной опалубки позволило снизить потери песка.
Нарушенная система подготовки рабочих кадров в учебно-курсовых комбинатах с прохождением производственной практики и наставничеством обернулась острой нехваткой квалифицированных операторов и машинистов, особенно имеющих опыт работы в горных условиях и на заболоченных участках.
Заместитель главного конструктора ОАО «Ирмаш» (Брянск) В.М.Максимов сообщил, что акционерное общество сохранило специалистов, традиции и опыт производства роторных экскаваторов.
По предложению ОАО «Стройтрансгаз» Ирмаш взял на себя обязательства изготовить по проекту СКВ «Газстроймашина» головной образец модернизированного роторного экскаватора ЭТР-254А. Предприятие справилось с этой задачей. В кратчайшие сроки подготовлено производство по созданию новой, довольно сложной машины, и в конце 2004 г. головной образец этого экскаватора выдержал квалификационные испытания.
При относительно небольших объемах работ по технологическому оснащению завод готов приступить к серийному производству не только экскаваторов ЭТР-254А, но и, при необходимости, ЭТР-309.
Траншейный роторный экскаватор ЭТР-254А предназначен для разработки траншей под магистральные трубопроводы диаметром от 1220 до 1420 мм в талых грунтах до IV категории включительно, а также в мерзлых и грунтах с полной глубиной промерзания. В талых грунтах, до II категории включительно, траншеи могут отрываться с откосами в верхней части, а в грунтах IV категории и мерзлых — без откосов.
В 2006 г. ОАО «Ирмаш» приступило к производству принципиально новой землеройной техники — экскаватора траншейного цепного ЭТЦ-250.
Экскаватор ЭТЦ-250 предназначен для рытья траншей под прокладку газопроводов, водопроводов и электрокабелей в грунтах I-IV категорий, а также мерзлых грунтах сезонного промерзания. Оборудованный направляющими для трубы, экскаватор способен одновременно отрывать траншею глубиной до 2,5 м и шириной 250, 400 или 500 мм и укладывать в нее полиэтиленовую трубу. Экскаватор комплектуется летней и зимней цепями.
В нефтегазовой отрасли на землеройно-профилировочных работах при строительстве и ремонте площадок, дорог, для очистки подъездных дорог от снега и грязи может использоваться автогрейдер ГС-18-06 с тяговым усилием 9 т и двигателем ЯМЗ 236 М2 мощностью 180 л.с.
Грейдер, выпускаемый ОАО «Ирмаш», имеет гидромеханическую передачу в приводе задних ведущих колес. На машине устанавливается основной отвал с ножами из профильного проката и передний отвал с прямым ножом. В конструкции машины предусмотрена установка заднего рыхлителя и системы автоматики.
Подвел итог сказанному главный научный консультант РОССНГС д.т.н. профессор О.М.Иванцов. Анализ требуемых средств механизации для строительства и выполнения транспортных работ при прокладке трубопроводов большого диаметра высокого давления, выполненный СКВ «Газстроймашина» и АО «НГС-оргпроектэкономика», показал возможность применения и для этого класса трубопроводов общепринятой организационно-технологической схемы поточно-расчлененного сооружения магистралей.
Наибольшую трансформацию претерпит технология выполнения сварочно-монтажных работ, связанная не только со значительным увеличением толщин труб и жесткостью плетей, но и применением труб более высокого класса прочности Х80.
Взгляд на зарубежную практику выполнения проектов с применением высокопрочных труб убеждает в преимущественном использовании автоматической сварки со свободным формированием шва тонкой проволокой в среде защитных газов (известные нам технологии CRC, Price и др.). Начато применение технологии сварки на весу (без подкладки) с использованием импульсной техники STT (Lincoln Electric). Все технологии ориентированы на поточно-расчлененный метод выполнения работ, что позволяет добиться темпа сварки колонной от 6 до 12 минут, т.е. обеспечить за световой день сварку 1 км трассы.
По просьбе РОССНГС Институт электросварки имени Е.О.Патона ранжировал перспективные отечественные сварочные технологии для использования при строительстве трубопроводов высокого давления.
Помимо модернизации технологии автоматической сварки с использованием комплексов «Стык» и контактной сварки нового поколения предложены новые технологии.
СРЕДИ ИНТЕРЕСНЫХ РАЗРАБОТОК — ТЕХНОЛОГИЯ ЭЛЕКТРОДУГОВОЙ АВТОМАТИЧЕСКОЙ СВАРКИ НЕПЛАВЯЩИМСЯ ЭЛЕКТРОДОМ С ИСПОЛЬЗОВАНИЕМ АКТИВИРУЮЩЕГО ФЛЮСА, КОТОРЫЙ НАНОСИТСЯ НА КРОМКИ ТРУБЫ ПЕРЕД СВАРКОЙ. ТЕХНОЛОГИЯ УСПЕШНО ИСПОЛЬЗУЕТСЯ ПРИ СВАРКЕ ТОЛСТОСТЕННЫХ ТРУБ В АТОМНОЙ ЭНЕРГЕТИКЕ, ЗА ОДИН ПРОХОД ПРОПЛАВЛЯЮТСЯ КРОМКИ ТРУБ ТОЛЩИНОЙ ДО 6 ММ.
Интересны предложения по комбинированной сварке толстостенных труб, при которой корневой шов сваривается контактным, а заполняющие швы — электродуговым способом. В этой работе участвует ОАО «Стройтрансгаз».
xn--90acg2babefdpm.xn--p1ai
Соединение трубопроводов высокого давления
Проектирование и монтаж трубопроводов высокого давления — технологически сложный процесс, к которому предъявляют строгие требования. Изложены они в многочисленных госстандартах, а выполнение контролируют надзорные органы федерального и муниципального уровня. Согласование и утверждение проекта отдельного взятого трубопровода во многом зависит от выбранных материалов: труб, соединительных элементов, запорной арматуры, расходных материалов и, конечно, герметиков. Учитывая последствия от перебоя в работе трубопровода высокого давления или аварийной ситуации хотя бы на одном из его участков, вопрос о качестве и эффективности герметизирующих материалов решается каждый раз индивидуально. С учетом транспортируемого вещества, его агрессивности, давления, температуры и возможного воздействия внешних факторов.
Трубопроводы высокого давления
Главная функция трубопровода — доставить продукт до места потребления или переработки. Магистраль транспортирует газообразные, парообразные, жидкие вещества на самые разные расстояния. Это могут быть сотни километров, если говорить о крупных федеральных магистралях, или локальные сети, так называемые технологические трубопроводы. В процессе эксплуатации на трубопровод и на каждый отдельный участок постоянно действуют нагрузки. Они делятся на основные и дополнительные. Основную нагрузку на трубопровод оказывает давление транспортируемого продукта. Проектирование, выбор материалов, монтаж и запуск магистрали всегда осуществляется с учетом расчетного, условного, рабочего и пробного давления. Инженеры просчитывают минимальную и возможную максимальную нагрузку на трубопровод в нормальных и экстренных ситуациях.
Расчеты выполняет компьютерная техника, и на основе этих результатов осуществляется закупка допустимых элементов всей магистрали с обязательным учетом пульсации давления, перемены температур (внутренней и внешней), вибраций, гидравлических ударов, изменений в окружающей среде и проч.
Трубопроводом высокого давления называют сеть с давлением транспортируемого вещества свыше 25 атмосфер. При этом принципиальное значение имеет вид вещества и его агрессивность. На территории России функционирует множество магистралей с давлением свыше 100 атмосфер, которые являются объектами повышенной опасности и требуют особых условий при монтаже и дальнейшем использовании. В целом, монтаж трубопровода высокого давления ведется строго по проектам и техническим условиям, разработанным отдельно для химической, газовой, нефтяной и нефтеперерабатывающей промышленности, систем водо- и пароснабжения.
Материалы и соединения трубопроводов высокого давления
Магистральный трубопровод представляет собой систему, состоящую из:• Непосредственно труб• Крепежных и соединительных элементов• Уплотнителей• Запорной и регулирующей арматуры• Опорных конструкций• Контрольно-измерительных приборов• Антикоррозийных элементов• И других деталей, которые применяют в соответствии с проектом.
Для магистралей высокого давления предназначены следующие виды труб:• Стальные — углеродистая и легированная сталь холодного проката• Медные• Пластиковые — изготовленные из полиэтилена
Соединение труб между собой, а также с ответвлениями и различными аппаратами бывает двух видов:• Разъемное• Неразъемное
Сразу оговоримся, что в условиях высокого давления транспортируемого вещества, стремятся к минимизации разъемных соединений. Бесшовный трубопровод является наиболее герметичным и безопасным. Неразъемные соединения получаются при помощи шовной сварки, сварки плавлением или пайки.
Разъемные соединения получают тоже несколькими способами. Один из самых распространенных — соединение на фланце. Есть также резьбовые, штуцерные, бугельные, грувлочные.
Фланцевое соединение по конструкции своей напоминает бутерброд. В профессиональной среде его так и называют — «фланцевый бутерброд». Между двумя фланцами помещают прокладку и уплотнительное кольцо, а скрепляют части болтами с гайками. Для уплотнения фланцевых соединений используют прокладки:• Металлические• Неметалличесике• Комбинированные
По своему свойству прокладки бывают:• Упругими• Жесткими
По конструкции:• Плоскими• Зубчатыми• Гофрированными• Линзовыми
По форме:• Квадратными• Круглыми• Овальными и др.
Выбор прокладки зависит от формы и размера фланца, транспортируемого вещества и его характеристик. Необходимо учитывать и качество фланца. Нередко производственный брак или механическое воздействие при монтаже приводят к образованию впадин, зазоров, микротрещин. А с учетом опасных и сложных условий эксплуатации трубопровода высокого давления этот факт вынуждает начать поиск более эффективных герметиков.
Главная задача герметика — заполнить все пространство внутренней поверхности фланца, включая дефекты. И обеспечить надежную герметизацию участка на протяжении всего срока эксплуатации трубопровода с учетом возможных изменений внутренней и внешней среды.
Есть ли иные варианты герметизировать фланцевые соединения трубопроводов высокого давления? Безусловно, есть. Это анаэробные герметики, используемые ранее в оборонной и космической отрасли. Пример такого продукта — СтопМастерГель Красный, выпускаемый для резьбовых и фланцевых соединений.
Анаэробные герметики в форме гелей высокой степени вязкости образуют ровное плотное покрытие, заполняя все уплотняемое пространство фланца, включая трещины, впадины и т.д. Герметик полимеризируется внутри соединения — там, где нет доступа кислороду. Твердый полимер надежно скрепляет «фланцевый бутерброд» и препятствует утечке транспортируемого вещества. Гарантия защиты от утечек составляет 20 лет.
Анаэробный герметик СтопМастерГель Красный подходят для:• Трубопроводов высокого давления — с показателем 40 атмосфер и выше• Рабочего диапазона температур от -60 до +150°C и кратковременного нагрева до +200°C• Нейтральных и агрессивных сред• Транспортировки нефти, нефтехимии и нефтепродуктов; природного и сжиженного газа; воды, пара, сжатого воздуха
Преимущества геля в сравнении с прокладками для фланцев
• Эластичная текстура• Удобное нанесение• Экономичный расход• Ускорение сборки одного соединения в 2-3 раза, а значит, и сборки всей магистрали• Полимеризация состава в течение 5 минут• Возможность юстировки и демонтажа вне зависимости от времени сборки соединения• 100%-ная защита от коррозии за счет высокой адгезии к материалу фланца и полностьюсинтетического состава
Анаэробный СтопМастерГель Красный имеет ограниченное применение в системе трубопроводов высокого давления. Все разрешительные документы, сертификаты и условия использования герметика можно получить по запросу.
re-st.ru
Монтаж - магистральный трубопровод - Большая Энциклопедия Нефти и Газа, статья, страница 1
Монтаж - магистральный трубопровод
Cтраница 1
Монтаж магистральных трубопроводов производят в следующей последовательности: предварительный монтаж, демонтаж, травление и окончательный монтаж. Трубопроводы укладываются на подготовленные или заделанные кронштейны в соответствии с проектом горизонтально, вертикально или наклонно. [1]
Монтаж магистрального трубопровода и ответвлений от него для подачи сжатого воздуха к группе цилиндров производится в соответствии с технической документацией и чертежами. [2]
Монтаж магистральных трубопроводов в настоящее время осуществляется по двум основным схемам: 1) одиночные трубы собираются и свариваются в секции на трубосварочных базах, а затем эти секции развозятся по трассе и там свариваются в непрерывную нитку; 2) одиночные трубы развозятся по трассе, где на специализированных стыковых машинах свариваются в непрерывную нитку. Более распространена первая схема. [3]
Монтаж магистральных трубопроводов производится после установки оборудования на фундаментные болты. При монтаже магистральный трубопровод укладывается горизонтально, вертикально или наклонно. Прямые участки трубопровода, соединенные при помощи фитингов, фланцев или сварки, не должны иметь вида ломаной линии. Соединение трубопроводов гайками или муфтами производится на нитролаке, а сварка труб выполняется преимущественно в стык с тщательной подгонкой торцов труб друг к другу. [4]
Монтаж магистральных трубопроводов большого сечения выполняют предварительно протравленными трубами. Такой метод монтажа применяют в закрытых проходных траншеях ( тоннелях), демонтаж труб в которых для последующей протравки усложнен или осуществить невозможно. [6]
Монтаж магистральных трубопроводов систем отолления на резьбе выполняют в такой последовательности: 1) размечают оси магистралей и места установки средств крепления, устанавливают опоры или подвески; 2) раскладывают монтажные узлы на опоры или подвешивают их к строительным конструкциям; 3) собирают узлы на льне и сурике или же стыкуют узлы и сваривают стыки; 4) выверяют магистрали и закрепляют на опорах или подвесках. [8]
При монтаже магистральных трубопроводов на чердаке вначале размечают оси магистрали на поверхности строительных конструкций и устанавливают подвески или настенные опоры по намеченным осям. После этого собирают и крепят магистральный трубопровод на подвесках или опорах, выверяют магистрали и соединяют трубопровод на резьбе или сварке; затем присоединяют стояки к магистрали. [9]
Работы по монтажу магистральных трубопроводов осуществляются в соответствии со строительными нормами и правилами ( СНиП) и техническими условиями ( ТУ), утвержденными Госстроем СССР, Госгортехнад-зором и различными ведомствами. [10]
Большей частью при монтаже магистральных трубопроводов применяется фланцевое соединение. Для воздухопроводов употребляются паронитовые или картонные прокладки толщиной 1 5 - 2 мм на графитовой пасте. [11]
Большей частью при монтаже магистральных трубопроводов применяют фланцевое соединение. Для воздухопроводов используют паронитовые или картонные прокладки толщиной 1 5 - 2 мм на графитовой пасте. Фланцы устанавливают только в тех местах, где требуется разъемное соединение, а в остальных местах трубы сваривают в стык электросваркой. [12]
Широко распространенными механизмами при монтаже цеховых и магистральных трубопроводов являются ручные тали и рычажные лебедки. Небольшие габариты и вес, простота и надежность конструкции позволяют использовать их при самых разнообразных работах. Основным назначением талей и рычажных лебедок при монтаже трубопроводов являются подъем, опускание и перемещение узлов и элементов трубопроводов и поддержание их при стыковке и сборке в стесненных и труднодоступных местах. Обслуживают такие тали один, а иногда двое рабочих. Тали большей грузоподъемности применяются гораздо реже в связи с их большим весом. Подвешивание тяжелых талей без применения дополнительных грузоподъемных механизмов затруднительно. [13]
Какие требования необходимо выполнять при монтаже магистральных трубопроводов систем отопления. [14]
Монтаж системы водяного отопления включает следующие работы: подготовку и установку нагревательных приборов, монтаж магистральных трубопроводов и стояков с подводками к нагревательным приборам и испытание системы. [15]
Страницы: 1 2 3
www.ngpedia.ru
Правила сооружения и эксплуатации магистральных газопроводов, Приказ Миннефтепрома СССР от 31 августа 1951 года №1411
В части мер пожарной безопасности согласовано с ГУПО МВД СССРУтверждены и введены в действие приказом Министерства нефтяной промышленности N 1411 от 31 августа 1951 года
ОБЩАЯ ЧАСТЬ
Настоящие правила обязательны для организаций всех министерств и ведомств, ведущих работы по проектированию, строительству и эксплуатации магистральных газопроводов, вне зависимости от вида транспортируемого по ним горючего газа.Магистральными называются газопроводы, по которым газ от места добычи или производства подается к городам, населенным пунктам или промышленным предприятиям. К магистральным газопроводам относятся также устраиваемые от них ответвления для подачи газа городам, населенным пунктам или предприятиям, расположенным по трассе магистрального газопровода.Магистральные газопроводы разделяются на:
а) высокого давления - при давлении газа свыше 10 кг/см,
б) среднего давления - при давлении газа от 3 до 10 кг/см,
в) низкого давления - при давлении газа ниже 3 кг/см.Правила содержат основные требования к устройству и по эксплуатации магистральных газопроводов, ответвлений от них и сооружаемых на них газораспределительных станций (ГРС).Отступления от настоящих правил, вызываемые технической необходимостью, разрешаются органами Государственной газовой технической инспекции, а в части мер пожарной безопасности органами Государственного пожарного надзора.Проекты магистральных газопроводов до утверждения в установленном порядке должны согласовываться с Государственной газовой технической инспекцией.С выпуском настоящих правил утрачивают силу "Временные правила проектирования, строительства и эксплуатации магистральных газопроводов и ответвлений от них" и "Временные правила по устройству, монтажу и эксплуатации газорегулировочных, газосборных и контрольно-распределительных пунктов на газопроводах" Государственной газовой технической инспекции Главгазтоппрома при Совете Министров СССР.
Глава I. УСТРОЙСТВО МАГИСТРАЛЬНЫХ ГАЗОПРОВОДОВ
А. ТРАССА МАГИСТРАЛЬНОГО ГАЗОПРОВОДА
§ 1. Трасса магистрального газопровода должна быть по возможности наиболее короткой и с наименьшим числом поворотов. Рекомендуемые углы поворотов трассы не более 60°.§ 2. При разбивке трассы непосредственное примыкание друг к другу кривых не допускается. Прямые вставки между обратными или смежными кривыми как в горизонтальной, так и в вертикальной плоскостях должны составлять не менее 5 м.§ 3. Ширина полосы, на которой производится топографическая съемка по трассе магистрального газопровода, составляет:
а) на ровной незастроенной местности - 40 м;
б) на пересеченной местности - до 100 м;
в) в местах пересечения железных и шоссейных дорог, линий электропередач высокого напряжения - 100 м;
г) при переходах рек дюкерами на расстояние между нитками дюкеров плюс по 50 м от оси крайних ниток;
д) в сторону железных и шоссейных дорог, городов, населенных пунктов, промышленных объектов, отдельных строений и др. объектов сверх указанных расстояний производится полуинструментальная съемка на расстояние, соответствующее нормам разрыва, указанным в §§ 9-12 настоящих правил.§ 4. В процессе изысканий ось трассы магистрального газопровода закрепляется в натуре знаками - деревянными в лесной зоне и металлическими или железобетонными в безлесной зоне, располагаемыми в пределах видимости, но не реже 0,5 км и с обязательной установкой их на углах поворота трассы. Угловые знаки закрепляются дополнительными знаками, отнесенными от оси трассы на расстояние, обеспечивающее их сохранность при проведении строительства газопровода.Одновременно в 10 м от оси трассы производится установка постоянных и временных реперов, чередуемых через 3 км друг от друга.Места перехода рек, каналов и озер закрепляются постоянными столбами по обоим берегам.§ 5. Привязку трассы магистрального газопровода к пунктам триангуляции и полигонометрии, а также пунктам Государственной и ведомственной нивелировки следует производить согласно действующим инструкциям Главного управления геодезии и картографии.§ 6. При производстве технических изысканий должны быть выполнены инженерно-геологические, геофизические и гидрологические работы и собраны все необходимые метеорологические сведения. Программа работ устанавливается организацией, проектирующей газопровод.
§ 7. Полоса отвода для магистральных газопроводов составляет:для одного газопровода - 10 м,для двух параллельно уложенных газопроводов - 20 м,для трех параллельно уложенных газопроводов - 30 м.§ 8. Магистральные газопроводы должны укладываться в земле.Глубина заложения устанавливается;
а) газопроводов, транспортирующих осушенный газ, на глубине 0,8-1,0 м, считая от верха трубы при условии, что температура грунта на этой глубине не ниже минус 1°. При наличии на указанной глубине более низкой температуры глубина заложения газопровода соответственно увеличивается.
б) газопроводов, транспортирующих неосушенный газ, на 100 мм ниже глубины промерзания грунта, но не менее 0,8 м, считая от верха трубы.Глубина промерзания грунта должна приниматься по средним данным многолетних наблюдений метеорологических станций, произведенных над поверхностью со снежным покровом.Примечание. Для северных районов и районов вечной мерзлоты допускается надземная прокладка магистральных газопроводов осушенного газа;
в) под судоходными реками, каналами, озерами и другими водными преградами - в траншеях на глубине не менее 0,8 м, считая от верха трубы до дна реки, канала или озера, и не менее 0,5 м под несудоходными реками, каналами или озерами;
г) при прокладке газопровода в скалистых грунтах на дне траншеи должна быть сделана подушка толщиной 20 см из утрамбованного песка или мягкого грунта, предохраняющая газопровод и его противокоррозийную изоляцию от повреждений;
д) при прокладке газопровода по заболоченным местам и на участках с грунтами, не выдерживающими нагрузку более 0,25 кг/см, под газопровод должно устраиваться искусственное основание с таким расчетом, чтобы уложенный на это основание газопровод не давал просадок как после укладки, так и после засыпки его грунтом. В случае устройства свайного основания газопровод должен опираться на все сваи.§ 9. Прокладка магистральных газопроводов по территориям городов, населенных пунктов, заводских поселков, промышленных предприятий и в границах железнодорожных станций не допускается.Минимальные расстояния от границы полосы отвода магистрального газопровода:до красной планировочной линии города, населенного пункта или заводского поселка с количеством жителей более 1000 человек, до границы отдельно стоящего промышленного предприятия союзного и республиканского значения или ж.д. станции - 200 м;до красной планировочной линии населенного пункта или заводского поселка с количеством жителей менее 1000 человек, или до границы промышленного предприятия местного значения - 100 м;до отдельно стоящих зданий - 50 м.Ответвления низкого давления от магистральных газопроводов допускается прокладывать через населенные пункты с количеством жителей менее 1000 человек при соблюдении требований, предусмотренных для газопроводов высокого давления "Правилами устройства и эксплуатации газовых сетей в городах и населенных пунктах" Государственной газовой технической инспекции и при условии установки на входе и выходе газопровода из населенного пункта отключающих задвижек.§ 10. При прохождении магистрального газопровода по землям гослесфонда устанавливается охранная зона по 100 метров в каждую сторону от границ полосы отвода.§ 11. При прокладке магистрального газопровода параллельно магистральному ж.д. пути на перегоне расстояние между ними должно составлять не менее 150 м, считая от оси газопровода до оси крайнего ж.д. пути.§ 12. При прокладке магистрального газопровода параллельно автомобильным дорогам I и II класса расстояние между ними должно составлять не менее 30 м, считая от оси газопровода до бровки дороги.§ 13. При прокладке магистрального газопровода параллельно воздушной линии электропередачи высокого напряжения расстояние между осью опор линии и газопроводом должно быть не менее высоты наиболее высокой опоры на участке параллельного прохождения.§ 14. При прокладке магистрального газопровода параллельно канализационному или водосточному коллекторам, или водопроводу расстояние между ними в свету должно быть не менее 10 м.В случае, если это расстояние не может быть выдержано, допускается его уменьшение до 6 м при условии сварки стыков газопровода на подкладных кольцах или наварки на стыки усилительных муфт.§ 15. Прокладка магистрального газопровода в одном тоннеле или траншее с другими трубопроводами, а также с силовыми и осветительными кабелями воспрещается.§ 16. При параллельной прокладке двух магистральных газопроводов расстояние между ними должно быть 10 м, за исключением участков переходов через магистральные железнодорожные пути и автодороги I и II классов, где это расстояние должно быть не менее 30 м.§ 17. Прокладка магистральных газопроводов всех давлений по железнодорожным мостам и мостам автомобильных дорог I и II класса не допускается.Расстояние между газопроводом и железнодорожным или шоссейным мостом должно составлять не менее 300 м, причем пересечение газопроводом реки или канала желательно производить ниже моста по течению реки или канала.§ 18. Переходы магистральных газопроводов через реки, каналы и другие водные препятствия, как правило, следует делать подводными. В отдельных случаях возможно устройство воздушных переходов.§ 19. Переход магистральным газопроводом рек и каналов шириной в межень меньше 20 м с устойчивыми руслами и берегами осуществляется дюкером в одну нитку.§ 20. Переход магистральным газопроводом рек, каналов и других водных препятствий шириной в межень более 20 м и менее широких рек с неустойчивыми руслами и берегами, осуществляется дюкерами в две и более нитки с разрывом между ними не менее 30 м. Количество ниток при устройстве через реки, каналы и другие водные препятствия воздушных переходов газопроводов определяется проектной организацией, в зависимости от конструкции переходов. Переходы газопроводов через судоходные реки или каналы должны быть согласованы с соответствующим бассейновым управлением.§ 21. При пересечении оврагов, логов и ручьев, а также железных и автомобильных дорог магистральный газопровод прокладывается в одну нитку.На переходах оврагов, логов и ручьев с берегами или руслами, подвергающимися размыву, должны быть предусмотрены меры по их укреплению.§ 22. На подводных и речных переходах (дюкерах) магистральных газопроводов устанавливается охранная зона (заградительная), отмечаемая в обе стороны сигнальными знаками на расстоянии 100 м от оси газопровода и подводного кабеля связи.
Б. ОСНОВНЫЕ СООРУЖЕНИЯ ПО ТРАССЕ МАГИСТРАЛЬНОГО ГАЗОПРОВОДА
§ 23. Пересечение магистральным газопроводом путей железных дорог осуществляется в футляре из стальной трубы диаметром на 100-200 мм больше диаметра газопровода.Глубина укладки газопровода в месте пересечения определяется из того условия, что расстояние от верхней образующей футляра газопровода до подошвы шпал железнодорожного пути должно быть не менее 1,8 м.Концы футляра должны быть выведены на 2 м за подошву насыпи, но не менее 25 м от осей крайних путей магистральной дороги и не менее 15 м от осей подъездных путей. На концах футляра устраиваются сальниковые уплотнения, рассчитываемые на давление газа (при разрыве газопровода) в футляре, исходя из принятого диаметра вытяжной свечи.От футляра делается вытяжная свеча, которая отводится на расстояние не менее 40 м от оси крайнего ж.д. пути магистральной дороги и на 25 м от оси подъездного пути при условии расположения основания свечи и головки рельса на одной отметке.При расположении основания свечи и головки рельса на разных отметках расстояние от оси крайнего ж.д. пути до свечи увеличивается на 5 м на каждый метр превышения отметки головки рельс над основанием свечи.Высота свечи от уровня земли должна быть не менее 5 м.При пересечении магистральным газопроводом электрифицированных железных дорог газопровод должен быть покрыт весьма усиленной изоляцией и защищен от блуждающих токов.Примечание. В случае установки на газопроводе у пересечения железных дорог отключающих устройств (задвижки, краны) они должны быть расположены на расстоянии не менее 150 м от оси крайних путей магистральной железной дороги и не менее 50 м от оси крайнего подъездного пути.§ 24. Пересечение магистральным газопроводом автомобильных дорог I и II классов осуществляется в футляре из стальной трубы диаметром на 100-200 мм больше диаметра газопровода. Концы футляра должны быть выведены на расстояние 10 м в стороны от обочин дороги. На концах футляра устанавливаются сальниковые уплотнения. От футляра делается вытяжная свеча, которая отводится на расстояние не менее 20 м от обочины дороги при условии расположения основания свечи и полотна дороги на одной отметке.При расположении основания свечи и полотна дороги на разных отметках расстояние от вытяжной свечи до обочины дороги увеличивается на 5 метров на каждый метр превышения отметки полотна дороги над основанием свечи. Высота свечи от уровня земли должна быть не менее 3 м.Примечание. В случае установки на газопроводе у пересечения дорог отключающих устройств (задвижки, краны) они должны располагаться на расстоянии не менее 100 м от оси дороги.§ 25. При пересечении магистральным газопроводом воздушной линии электропередачи высокого напряжения расстояние от стенки газопровода до края фундамента опоры должно приниматься с расчетом, чтобы строительство газопровода не вызвало нарушения фундамента опоры, и должно составлять не менее 5 м.§ 26. При пересечении магистральным газопроводом канализационных или водосточных коллекторов, водопровода и т.п. с прохождением газопровода выше или ниже этих коллекторов или трубопроводов он не должен иметь сварных стыков на расстоянии менее 3-х метров в каждую сторону, считая от стенки коллектора или трубы. В противном случае сварные стыки газопровода, расположенные ближе 3-х метров от стенки коллектора или трубы, усиливаются наваркой муфт. В месте пересечения вокруг коллектора или трубы делается перемычка из утрамбованной глины.В случае, если магистральный газопровод проходит при пересечении через канализационный или водосточный коллектор, он должен быть заключен в футляр, не имеющий сварных стыков и покрытый весьма усиленной изоляцией. Концы футляра выводятся в каждую сторону от наружной стенки коллектора не менее чем на 3 метра.Место прохождения футляром через стенки коллектора должно быть тщательно уплотнено, а на концах футляра сделан дренаж.Заключенный в футляр участок газопровода не должен иметь сварных стыков и должен быть покрыт весьма усиленной изоляцией.§ 27. Повороты магистральных газопроводов высокого и среднего давления диаметром 500 мм и менее должны осуществляться при помощи гнутых колен.На газопроводах низкого и среднего давления, а также на газопроводах высокого давления диаметром более 500 мм допускается установка сварных колен. Колена должны иметь не менее трех звеньев и радиус кривизны не менее трех диаметров. При углах до 15° допускается сварка труб газопровода путем скоса их концов без вставки колен.§ 28. На магистральных газопроводах на расстоянии друг от друга в среднем 20 километров устанавливаются задвижки для возможности отключения отдельных участков газопровода. Количество и расположение задвижек определяется проектом.Кроме того, установка задвижек обязательна в следующих местах:
а) на обоих берегах каналов, рек, озер и других водных препятствий, пересекаемых дюкерами в две и более нитки;
б) при подвеске газопроводов к специальным мостам, по обеим сторонам моста;
в) на каждом ответвлении от магистрального газопровода.§ 29. Отключающие задвижки следует устанавливать в колодцах с крышками, открывающимися по всему периметру колодца и запираемыми на замок. Колодцы и крышки должны быть выполнены из несгораемых материалов. Конструкция колодцев и крышек должна обеспечивать невозможность проникновения в колодец грунтовых вод и атмосферных осадков.Вварные задвижки или краны возможно устанавливать на газопроводе без устройства колодцев. В этом случае управление ими должно быть выведено на поверхность земли в несгораемый, запираемый и вентилируемый шкаф.Вокруг колодцев и шкафов, в случае установки задвижек без колодцев, должны прокладываться минерализованные полосы шириной 2-2,5 м.Такие же полосы должны прокладываться и вокруг усадеб линейных обходчиков.§ 30. Для удаления из газопровода конденсата при транспортировке жирного и влажного газа устанавливаются конденсатосборники.§ 31. Сооружаемые на магистральных газопроводах установки по осушке газа, очистке от сероводорода, бензола, газового бензина, нафталина и т.п. должны располагаться на головном участке газопровода с тем, чтобы в магистральный газопровод подавался очищенный и осушенный газ.Точка росы осушенного газа должна быть на 2-3° ниже минимальной температуры газа в газопроводе.Содержание сероводорода в газе, предназначаемом для бытовых целей, не должно превышать 0,02 г/нм. В остальных случаях возможное содержание в транспортируемом газе сероводорода принимается в зависимости от влажности газа и характера его использования.Содержание в газе бензола и газового бензина не должно превышать 10 г/нм.Содержание в газе нафталина не должно превышать летом 0,1 г/нм, зимой 0,05 г/нм.§ 32. Компрессорные станции магистральных газопроводов, транспортирующих искусственный горючий газ с заводов, где он вырабатывается, при размещении их на площадке завода должны располагаться таким образом, чтобы газопровод выходил за пределы территории завода, не пересекая ее.§ 33. Расположение линейных компрессорных станций непосредственно у трассы магистрального газопровода не разрешается. Разрыв между ними, считая от границы станции до оси газопровода, должен составлять не менее 100 метров.При размещении линейной компрессорной станции вблизи пересекаемой магистральным газопроводом реки, канала или заболоченного участка ее следует по возможности расположить после перехода газопроводом указанных препятствий, чтобы давление газа в газопроводе на переходе было минимальным.Схема подсоединения линейной компрессорной станции к магистральному газопроводу должна обеспечивать возможность его работы при выключенной станции.§ 34. При подходе к компрессорной станции двумя и более нитками газопровода разрыв между ними на расстояние от станции до 300 метров должен быть не менее 30 метров.
В. ТРУБЫ И МАТЕРИАЛЫ, ПРИМЕНЯЕМЫЕ ПРИ СВАРКЕ МАГИСТРАЛЬНОГО ГАЗОПРОВОДА
§ 35. Магистральные газопроводы выполняются из стальных труб ГОСТ 3101-46*, ГОСТ 301-50**, ГОСТ 4015-52*** из стали Ст.2-Ст.4 (МСт.2-МСт.4) по ГОСТ 380-50* и Ст.10-Ст.20 по ГОСТ 1050-52*.________________* На территории Российской Федерации документ не действует. Действуют ГОСТ 8731-74, ГОСТ 8732-78, здесь и далее по тексту;** На территории Российской Федерации документ не действует. Действуют ГОСТ 8731-74, ГОСТ 8732-78, ГОСТ 8733-74, ГОСТ 8734-75;*** На территории Российской Федерации действуют ГОСТ 10704-91, ГОСТ 10706-76, здесь и далее по тексту;* На территории Российской Федерации действуют ГОСТ 380-2005, ГОСТ 535-2005, ГОСТ 14637-89, здесь и далее по тексту;* На территории Российской Федерации действует ГОСТ 1050-88, здесь и далее по тексту. - Примечание изготовителя базы данных. Указанные марки сталей согласно ГОСТ 380-50 и ГОСТ 1050-52 характеризуются следующим химическим составом:
Марка стали | Содержание в % | ||||
Углерод | Марганец | Кремний | Сера | Фосфор | |
Ст.2 (МСт-2) | 0,09-0,15 | 0,35-0,50 | - | 0,055 | 0,050 |
Ст.3 (МСт-3) | 0,11-0,22 | 0,35-0,60 | 0,12-0,35 | 0,055 | 0,050 |
Ст.4 (МСт-4) | 0,18-0,27 | 0,40-0,70 | 0,12-0,35 | 0,055 | 0,050 |
Не более | |||||
Ст.10 | 0,05-0,15 | 0,35-0,65 | 0,17-0,37 | 0,045 | 0,045 |
Ст.15 | 0,10-0,20 | 0,35-0,65 | 0,17-0,37 | 0,045 | 0,045 |
Ст.20 | 0,15-0,25 | 0,35-0,65 | 0,17-0,37 | 0,045 | 0,045 |
и механическими свойствами:
Марка стали | Механические свойства | ||
Предел прочности при растяжении,кг/мм | Относительное удлинение | ||
Для длинного образца | Для короткого образца | ||
% не менее | |||
Ст.2 (МСт-2) | 34-42 | 26 | 31 |
Ст.3 (МСт-3) | 38-47 | 23-21 | 27-25 |
Ст.4 (МСт-4) | 42-52 | 21-19 | 25-23 |
Ст.10 | 32 | - | 31 |
Ст.15 | 35 | - | 27 |
Ст.20 | 40 | - | 25 |
Трубы ГОСТ 3101-46 должны относиться к 1 классу. Трубы ГОСТ 4015-52 допускаются только для газопроводов низкого и среднего давлений.Применение труб из новых марок стали возможно по согласованию с Государственной газовой технической инспекцией.§ 36. Применение для магистральных газопроводов и ответвлений от них труб с условным диаметром менее 100 мм не рекомендуется.§ 37. Толщина стенки трубы магистрального газопровода определяется при проектировании его, исходя из максимально возможного давления в газопроводе, но не должна быть менее 5 мм для труб с условным проходом до 200 мм и не менее 6 мм для труб с условным проходом свыше 200 мм.На участках переходов газопроводом естественных и искусственных препятствий (овраги, балки, болота, ручьи, пруды и озера, реки, железные дороги и автодороги I и II классов), а также на участках, прокладываемых в грунтах, не допускающих нагрузки более 0,5 кг/см, толщина стенок труб должна быть увеличена на 1-2 мм. Повышенная толщина стенок труб должна быть и на подходах газопровода к компрессорным станциям на расстоянии не менее 0,5 км от станции.§ 38. Соединение труб осуществляется ручной дуговой автоматической электросваркой под флюсом и газопрессовой сваркой.Газовая сварка допускается для магистральных газопроводов среднего и низкого давлений диаметром не более 150 мм.§ 39. При ручной электросварке магистральных газопроводов должны применяться высококачественные электроды марок Э 42 и Э 42А по ГОСТ 2523-51*.________________* На территории Российской Федерации документ не действует. Действуют ГОСТ 9466-75, ГОСТ 9467-75, здесь и далее по тексту. - Примечание изготовителя базы данных. Механические свойства металла шва и сварного соединения, полученных наплавкой электродами Э 42 и Э 42А без последующей термообработки, должны удовлетворять согласно ГОСТ 2523-51 следующим требованиям:
Марка электрода | При применении электродов диаметром более 3 мм | При применении электродов диаметром 3 мм и менее | Марка проволоки по ГОСТ 2246-54* | |||
Металл шва | Сварное соединение | |||||
Предел прочности при растяжении, кг/мм | Относительное удлинение, % | Ударная вязкость, кг/см | Предел прочности при растяжении, кг/мм | Угол загиба, градусы | ||
Не менее | ||||||
Э 42 | 42 | 18 | 8 | 42 | 120 | 1, 1А |
Э 42А | 42 | 22 | 14 | 42 | 180 | 1А |
________________ |
docs.cntd.ru
МОНТАЖ МАГИСТРАЛЬНЫХ ТРУБОПРОВОДОВ для транспортировки нефти
МОНТАЖ МАГИСТРАЛЬНЫХ ТРУБОПРОВОДОВ
Неравномерное размещение двух основных видов энергетического сырья — нефти и природного газа — вызывает необходимость их транспортировки на значительные расстояния. Самый дешевый способ транспортирования этих видов сырья — подача их по магистральным трубопроводам. Другие современные способы транспортировки энергетического сырья посредством танкеров с большой грузоподъемностью или специальных судов для перевозки сжиженных газов служат только дополнением к трубопроводному транспорту; танкеры представляют собой звенья, которые соединяют магистрали, подведенные к морским портам. Благодаря использованию танкеров и газовозов можно значительно ограничить строительство приморских трубопроводов, но на суше оптимальным решением для транспортировки энергетического сырья являются магистральные трубопроводы. Железнодорожный транспорт в цистернах не может применяться с этой целью, так как он не способен справиться с постоянно растущими потребностями в нефти и природном газе. Строительство магистральных трубопроводов получило большое развитие после второй мировой войны, и в этой области был достигнут необычайно быстрый прогресс.
Магистральные трубопроводы являются стальными конструкциями, специфика которых заключается главным образом в следующем:
их длина составляет несколько тысяч километров;
эксплуатационное давление внутри трубы колеблется в пределах нескольких мегапаскалей;
трасса трубопровода характеризуется изменчивостью рельефа местности и физико-механических свойств грунта;
трубы заглубляются в грунт, представляющий собой весьма агрессивную иногда среду с точки зрения коррозии;
на трассе трубопровода имеются такие препятствия, как железнодорожные насыпи, реки, болота, овраги.
Кроме того, следует добавить, что возможная авария трубопровода, особенно предназначенного для транспортировки нефти. представляет серьезную опасность для окружающей среды.
Из сказанного выше вытекает, что качество сооружения магистральных трубопроводов должно быть высоким. Однако строительство затрудняется полевыми условиями работы, так как изготовление укрупненных секций труб ограничивается возможностями их транспортировки по местным дорогам или даже по бездорожью. Следующим элементом, осложняющим строительство, является необходимость синхронизации работы бригад различного профиля, так как технология строительства магистральных трубопроводов требует выполнения следующих непосредственно друг за другом работ, связанных со сваркой труб, проверкой качества сварных швов, антикоррозионной изоляцией труб, а также с отрывком и засыпкой траншей. Привлечение к работе в тяжелых полевых условиях высококвалифицированных специалистов, которые нужны для строительства таких ответственных объектов, как трубопроводы, также представляет собой проблему. Строительство магистральных трубопроводов всегда связано с высокими темпами работ, что неизбежно вследствие необходимости быстрого возврата больших капиталовложений, выделенных на строительство.
Чтобы справиться с перечисленными выше трудностями, необходимо иметь высокопроизводительное специальное оборудование, пригодное для выполнения самых разнообразных работ, которые требуется осуществить при строительстве трубопроводов. Характеристика этого оборудования приведена далее при описании монтажа линейной части трубопроводов, за исключением тех единиц оборудования, которые непосредственно не связаны с сооружением стальных конструкций (например, не дана характеристика экскаваторов, применяемых при выполнении траншей под трубопроводы).
Особую проблему представляет сооружение переходов трубопроводов через местные препятствия, особенно через водные преграды. Существует два общих решения — подводные дюкеры и надземные переходы. В настоящее время предпочитают применять первое решение, так как оно более дешевое. Воздушные переходы трубопроводов над водными препятствиями применяют главным образом при необходимости перехода через горные реки с нестабилизированным и каменистым дном.
Надземные переходы трубопроводов через препятствия характеризуются большим разнообразием типов конструкций, зависящих от длины препятствия, характера его берегов, вида трубопровода (нефтепровод или газопровод), его диаметра, а также от числа труб, переходящих через препятствие.
При таком большом разнообразии типов конструкций трубопроводных переходов невозможно подробно описать их монтаж, поэтому здесь приводится лишь несколько примеров, характеризующих разную технику монтажа.
Обширный опыт прокладки -магистральных трубопроводов накоплен. при сооружении газопровода Оренбург - Западная граница СССР протяженностью 2750 км, построенного с участием специалистов социалистических стран и в том числе ПНР
http://www.bibliotekar.ru
legkoe-delo.ru