- Цинкование листа
- Цинкование проволоки
- Цинкование труб
- Цинкование различных изделий
- В промышленной среде 65 лет
- В тропической среде: 70 лет
- В пригородной среде: 85 лет
- В загородной среде: 120 лет.
- В 1742 году французский химик и физик Поль Жак Малуэн (1701—1778) описал метод цинкования железа погружением в ванну с расплавленным цинком в докладе французской Королевской академии.
- В 1836 году французский химик Станислас Сорель (1803—1871) получил патент на данный метод цинкования железа, после очистки его сначала 9 % раствором серной кислоты (h3SO4) и затем флюсом — хлоридом аммония (Nh5Cl).
-
Ванна с расплавленным цинком для горячего цинкования
-
Горячеоцинкованная балка
-
Горячеоцинкованный Z профиль
-
Стальной прокат, готовый к горячей оцинковке
- Коррозионная устойчивость в 5-7 раз превышает электрооцинкованный крепёж и приближается к устойчивости нержавеющей стали.
- Покрытие само себя восстанавливает на повреждённых участках.
- Покрытие более устойчиво к сколам при ударах, чем аналогичные по коррозионной устойчивости полимерные лакокрасочные покрытия.
- Требует специальной высадки под толщину покрытия. Нельзя, из-за значительной толщины покрытия, просто купить болты без покрытия и оцинковать их горячим методом.
- Не все типоразмеры доступны (только от М8).
- Внешний вид — серый матовый.
- Из-за неравномерной толщины покрытия невозможно достичь высокой точности изделия.
- Гайки поставляются покрытыми транспортировочной смазкой (видно на фото — гайка блестит), для защиты от коррозии повреждённых проточкой участков внутренней резьбы.
- Электролитическое цинкование (здесь- ЭЦ, или электроцинкование, также — гальваническое цинкование, англ. zinc electroplating, zinc plating, фр. zingage electrolytique, нем. elektrolytische Verzinkung)- самое распространённое для крепежных изделий покрытие. Главные достоинства — низкая цена и привлекательный внешний вид (обычно глянцевый серебристый, голубоватый либо жёлтый, бывает и матовый). Возможно ЭЦ деталей с пластиковыми элементами, например самоконтрящихся гаек. Главные недостатки — недостаточная коррозионная устойчивость делает это покрытие скорее транспортировочно-декоративным. Предназначено для деталей, используемых в сухих помещениях. Подвергает покрываемые детали водородному охрупчиванию, поэтому применимо для деталей класса прочности до 10.9.
- Дельта (Дакромет) — ближайшее к горячему цинкованию по цене, коррозионной устойчивости и внешнему виду покрытие, третье по распространённости покрытие для крепежных изделий. Главное достоинство — малая толщина (до 10 мкм) позволяет получить высокую точность детали, поэтому это покрытие получило широкое распространение в автомобильной промышленности. Позволяет покрывать детали любого класса прочности. Более привлекательный, чем у Г/О внешний вид — поверхность также матовая, но более ровная, без наплывов и бугорков; кроме того, возможны разные оттенки — от светло-серого (серебристого) до чёрного. Препятствует водородному охрупчиванию. Возможно покрытие деталей с пластиковыми элементами, например, самоконтрящихся гаек. Недостаток — покрытие легче, чем Г/О скалывается и неспособно самовосстанавливаться на повреждённых участках. Поэтому, например, на днищах автомобилей часто применяют Г/О крепёж.
- Термодиффузионное цинкование (ТДЦ, англ. sherardising, фр. cherardisation, нем. sherardisieren) примерно в два раза дороже, чем Г/Ц и Дельта (Дакромет), поэтому значительно менее распространено. Требует специальной высадки под толщину покрытия. Технология ТДЦ позволяет наносить цинковое покрытие любой толщины, в зависимости от требований. Но для получения удовлетворительной коррозионной устойчивости требуется толщина покрытия, не позволяющая нанесение на стандартно высаженные болты, из-за значительной толщины (от 40 мкм). Невозможно термодиффузионное цинкование деталей с пластиковыми элементами, например, самоконтрящихся гаек. Температура процесса 290—450 °C позволяет покрывать детали класса прочности до 10.9 — то есть, так же, как и Г/О.
- Газотермическое напыление — позволяет качественно наносить цинковое покрытие толщиной 200+ мкм на внешние поверхности крупногабаритных деталей непосредственно на месте монтажа, но неприменимо для крепежа, резьб, внутренних поверхностей диаметром менее 500 мм из-за технологических ограничений.
- осмотр на месте у Клиента;
- консультации в области подбора оборудования для цеха горячего цинкования;
- комплексное выполнение проекта цеха горячего цинкования;
- шеф-монтаж оборудования, входящего в линию горячего цинкования;
- запуск, обучение.
Горячее цинкование. Горячего цинкования
Горячее цинкование — НКП "Центр по развитию цинка"

Горячее цинкование – процесс, защищающий железо и сталь от образования ржавчины. В сущности, он предполагает погружение металлоконструкции с химически чистой поверхностью в ванну с расплавленным цинком, который реагирует с железом с образованием защитной пленки. Этот принцип остается неизменным в течение 150 лет существования процесса цинкования, но обширные исследования по всем аспектам технологиипревратили современное цинкования в технически контролируемое производство.В силу того, что расплавленный цинк не может вступать в реакцию с металлом или сталью покрытой вторичной окалиной или маслом, металлоконструкция перед погружением в nрасплавленный цинк должна пройти процесс очистки, который включает обезжиривание, пескоструйную очистку и кислотное травление. Затем металлоконструкцию покрывают флюсом для активации поверхности, что улучшает ее «смачивание» цинком и их взаимодействие при погружении. При извлечении конструкции избыток цинка стекает обратно в ванну. Оцинкованное изделие погружают в ванну с водой для охлаждения или оно остывает на воздухе.Процесс горячего цинкования – процесс, защищающий железо и сталь от образования ржавчины. В сущности, он предполагает погружение металлоконструкции с химически чистой поверхностью в ванну с расплавленным цинком, который реагирует с железом с образованием защитной пленки. Этот принцип остается неизменным в течение 150 лет существования процесса цинкования, но обширные исследования по всем аспектам технологии превратили современное цинкования в технически контролируемое производство.
Существуют два основных способа цинкования различающиеся по методу нанесения флюса. При цинковании с расплавленным флюсом материал после травления и промывки погружают в цинковую ванну, на поверхности которой плавает слой флюса. При сухом цинковании слой флюса высушивают на поверхности материала перед погружением в чистую ванну с расплавленным цинком.
Процесс оцинковывания состоит из трех основных этапов: подготовка поверхности, оцинковывание и осмотр.
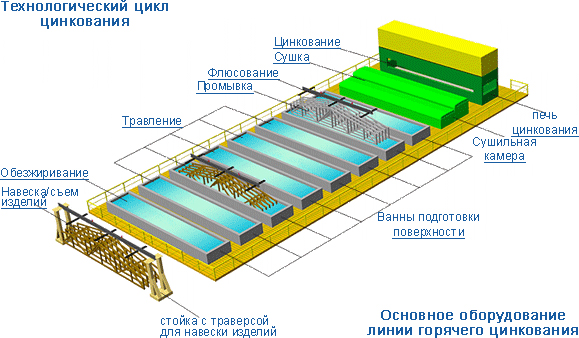
Подготовка поверхности
Подготовка поверхности является наиболее важным этапом при нанесении покрытия. Нарушение покрытия до окончания ожидаемого срока действия, в большинстве случаев, происходит из –за неправильной подготовки поверхности.Этап подготовки поверхности в процессе оцинкования имеет свои собственные способы осуществления контроля качества, при которых подаваемый цинк не вступает в реакцию со стальной поверхностью, если она не полностью чистая. Любые нарушения и несоответствия на этапе подготовки поверхности будут видны при извлечении стали из расплавленного цинка, т.к. грязные участки останутся без покрытия. Необходимо сразу же предпринять действия по устранению ошибки.Окраска на месте или другие антикоррозийные методы, применяемые на рабочей площадке, могут потребовать привлечение субподрядчиков и/или рабочих групп для подготовки поверхности нанесения покрытия. Это может вызвать проблемы организации деятельности, задержки по времени, ошибки и споры, касающиеся разделения ответственности и финансовых обязательств. Как только проект был отправлен и принят на заводе по цинкованию, существует только один пункт ответственности, согласно которому материал, выходящий с линии, должен быть должным образом оцинкован. Это обязательство несет производитель цинкового покрытия. Подготовка поверхности состоит из трех шагов: чистка щелочью, травление кислотой и флюсование.
Оцинкование
На этом этапе материал полностью погружается в ванну, состоящую минимум на 98% из чистого расплавленного цинка. Химический состав ванны определен Американским Обществом Тестирования и Материалов (ASTM) в спецификации В6. Температура в ванне поддерживается на уровне 850 F (454 C).
Изготовленные изделия погружаются в ванну на достаточно продолжительное время до достижения температуры ванны. Изделия медленно вынимаются из ванны, и избыток цинка удаляется путем дренажа, вибрирования и/или центрифугирования.
Химические реакции, которые приводят к образованию и структурированию оцинкованной поверхности, продолжаются после того, как предметы будут извлечены из ванны и до тех пор, пока они будут примерно такой же температуры, как и ванна. Изделия охлаждаются либо в воде, либо на атмосферном воздухе сразу же после извлечения из ванны.
Проверка
Два свойства покрытия после горячего цинкования, которые тщательно рассматриваются после процесса цинкования, — толщина покрытия и внешний вид покрытия. Различные простые физические и лабораторные тесты выполняются для определения толщины, однородности, уровня прилипания и внешнего вида.
Изделия подвергаются цинкованию в соответствии с разработанными, принятыми и одобренными стандартами ASTM, Канадской ассоциацией по стандартизации (CSA) и американской ассоциацией государственных дорожных и транспортных органов (AASHTO).
Эти стандарты охватывают все положения – от минимальной требуемой толщины поверхности для различных категорий оцинкованных изделий до химического состава цинкового металла, используемого в процессе.
Методы тестирования и интерпретации результатов представлены в публикации Проверка горячеоцинкованных изделий после выпуска, опубликованных AGA и распространяемых AGA или местным производителем цинкового покрытия. Этот буклет содержит цветные и крупные фотографии для визуальной проверки.
С течением времени система разделилась на четыре разных производства, а именно:
zdc.ru
Горячее цинкование Википедия
Кристаллическая поверхность горячеоцинкованного металлаГорячее цинкование — покрытие металла (обычно железа или стали) слоем цинка для защиты от коррозии путём окунания изделия в ванну с расплавленным цинком при температуре около 460 °C. Под атмосферным воздействием чистый цинк (Zn) вступает в реакцию с кислородом (O2) и формирует оксид цинка (ZnO), с последующей реакцией с диоксидом углерода (CO2) и формированием карбоната цинка (ZnCO3), обычно серого матового, достаточно твёрдого материала, останавливающего дальнейшую коррозию материала.
Горячее цинкование считается одним из самых надёжных, экономичных и потому распространённых методов защиты железа и стали от коррозии.
Для металлоконструкций горячее цинкование является бесспорно самым распространённым видом покрытия.
Толщина цинкового слоя колеблется от 30 до 100 мкм, обычно — от 45 до 65 мкм.
По данным American Galvanizer Association горячее цинкование обеспечивает защиту от коррозии:
История
Фото
Горячее цинкование крепежных изделий
Процесс
Горячеоцинкованные болты, гайки и шайбыТехнология нанесения покрытия такова. После обезжиривания, промывки, травления и повторной промывки, детали в барабане окунают в ванну (обычно керамическую) с расплавленным цинком. Вращением барабана обеспечивают поток цинковой массы относительно деталей для заполнения всех пор и микротрещин. Затем барабан вынимают из ванны и раскручивают для удаления излишков цинка центрифугированием. Однако на внутренней резьбе (на гайках) все же остаются излишки цинка, поэтому внутреннюю резьбу после цинкования протачивают. Отсутствие покрытия на внутренней резьбе не влияет на коррозионную устойчивость соединения, если гайка применяется с горячеоцинкованным болтом или шпилькой. Благодаря высокой анодности цинка по отношению к железу при температурах до 70°, цинк сам покрывает непокрытые и повреждённые участки детали со скоростью около 2 мм в год. В данном случае цинк с наружной резьбы болта, благодаря разности потенциалов цинка и железа в естественной влажной и кислой среде переносится на участки внутренней резьбы гайки, оставшиеся при проточке резьбы без покрытия.
Достоинства
Главным функциональным достоинством горячеоцинкованного крепежа является экономия на эксплуатации сооружений, благодаря отсутствию необходимости их перекрашивать.
Недостатки
Сравнительный анализ
коррозия электро- и горячеоцинкованных болтов, 5 суток в р-рах NaCl, HCl и в воде Крепеж с покрытием Дельта (Дакромет)Горячее цинкование (Г/Ц) является вторым по распространённости после электролитического.
См. также
Примечания
Литература
wikiredia.ru
Горячее цинкование | Защитные покрытия металлов
Цинк является одним из наиболее реакционно способных металлов. Вычисленная свободная энергия при коррозии в гидрат окиси составляет 71500 кал на 1 г-атом металла.
Пленка, образующаяся на поверхности корродирующего цинка и состоящая из продуктов коррозии, определяет конечную скорость течения процесса коррозии.
Под воздействием кислорода воздуха с малой или средней влажностью свежеподготовленная поверхность покрывается псевдоаморфной пленкой окиси цинка, переходящей несколько часов спустя в обычную кристаллическую пленку, рост которой обусловлен линейной зависимостью. Следовательно, скорость коррозии цинка определяется скоростью перехода псевдоаморфной окиси в нормальную окись цинка, пористость которой не может служить препятствием к продолжению процесса окисления.
Характер коррозионного процесса цинка в атмосфере с повышенной влажностью меняется — он становится электрохимическим. Так, при достижении в атмосфере 75%-ной влажности продукты коррозии цинка представляют уже расплывающуюся пленку, которая ускоряет дальнейший процесс коррозии, способствуя подводу влаги к поверхности металла.
В сельских, городских и приморских местностях дождевые осадки смывают большую часть продуктов коррозии цинка. Остающиеся на поверхности продукты коррозии становятся основными по своему характеру и несколько замедляют в дальнейшем скорость коррозионного процесса. В атмосфере, загрязненной промышленными газами, такая пленка не образуется и коррозия протекает быстро, не проявляя тенденций к замедлению.
Таким образом, становится очевидным, что скорость коррозии цинка в сильной степени определяется наличием влаги в окружающей атмосфере и степенью загрязненности последней промышленными газами.
Потемнение цинковых покрытий со временем не сказывается на их защитных свойствах, но для сохранения лучшего внешнего вида существует ряд мероприятий: нанесение бесцветного лака, пассивация, фосфатирование с последующим окрашиванием и др. К таким мероприятиям иногда прибегают в целях сохранения внешнего вида и повышения химической стойкости оцинкованной продукции.
Цинк является наиболее распространенным металлом, применяемым для защиты железа и его сплавов от атмосферной коррозии. По литературным данным, около 40% мировой добычи цинка потребляется для защиты черных металлов от коррозии.
Из различных методов цинкования изделий и конструкций из железа, стали и чугуна на долю горячего метода, по данным авторитетных литературных источников, приходится 95—98%.
Горячее цинкование в качестве средства защиты железа и стали от агрессивной атмосферной коррозии в настоящее время вытесняет способ окрашивания. Это объясняется тем, что горячеоцинкованная продукция, в особенности с дополнительным окрашиванием, надежно защищена от коррозии в течение нескольких десятилетий, в то время как пятикратное окрашивание при помощи коррозионностойкого лака требует обновления (в агрессивной атмосфере) каждые 5 лет. Следовательно, горячее цинкование имеет несомненное преимущество перед окрашиванием с точки зрения экономии рабочей силы.
Причинами, которые все более усложняют проблемы защиты стали от коррозии, являются развивающаяся индустриализация и тем самым повышенное загрязнение атмосферы такими коррозионными агентами, как двуокись серы, хлороводород, сероводород, органические сернистые соединения, нитраты, аммиак и пр. Резко возрастает потребление воды для промышленных целей и тем самым ее загрязнение.
Постепенный переход в строительстве и промышленности к более легким конструкциям уменьшает их толщину, что в свою очередь обусловливает необходимость более надежной защиты от коррозии, причем горячее цинкование играет при этом доминирующую роль. Горячему цинкованию прерывистым способом подвергаются различные строительные детали, элементы различных конструкций, а также детали машин, в частности резьбовые, а непрерывным методом — оцинкованная жесть, непрерывная полоса и проволока.
В настоящее время мировая ежегодная горячеоцинкованная стальная продукция составляет свыше 20 млн. т, в том числе: 11 млн. т жести и непрерывной полосы, 2,5 млн. т труб, 2,5 млн. т проволоки, 5,0 млн. т готовых изделий.
По роду коррозионного воздействия различают коррозию в атмосфере, в жидких средах и в почве.
Атмосферная коррозия протекает с различной интенсивностью в зависимости от относительной влажности атмосферы и степени загрязнения ее различными промышленными газами, в особенности двуокисью серы, копотью, пылью и другими загрязнениями. Вследствие амфотерности цинка его коррозионная стойкость наиболее сильно выражена в слабо кислых и не сильно щелочных средах, — при значениях водородного показателя в пределах 6—12; при более низких и более высоких значениях рН скорость коррозии резко возрастает (рис. 44).
Рис. 44. Влияние водородного показателя на скорость коррозии цинкаРис. 45. Влияние температуры воды на скорость коррозии цинка
Большой интерес представляет коррозионное поведение цинка в воде. В зависимости от состава воды и, в частности, от содержания в ней кислорода при температуре, превышающей 60° С, цинк покрывается плотной защитной пленкой и электродный потенциал цинка и железа меняются своими местами — цинк перестает защищать электрохимически железо от коррозии (рис. 45). Скорость растворения цинка меньше, чем железа в парах воды в 7 раз, в дистиллированной воде в 10 раз, в соленой воде в 8 раз, в подкисленной воде (рН ≈ 4) в 4 раза, в слабощелочной среде (рН~10) в 11 раз. В атмосферных условиях промышленных, городских и сельскохозяйственных районов коррозионная стойкость цинка примерно в 20 раз больше, чем стали, что в значительной степени определяется строением защитных пленок их продуктов коррозии. В сухих тропических районах горячее цинковое покрытие теряет в год примерно 2 мкм, во влажных 3 мкм и в приморских 6 мкм.
В тех случаях, когда горячеоцинкованные стальные конструкции предназначены для длительной эксплуатации в агрессивных условиях или в целях эстетики горячее цинкование технически и экономически целесообразно комбинировать с последующей окраской. Тогда целостность лакокрасочного покрытия после определенного периода эксплуатации не влечет за собой коррозию стали с образованием трудно удаляемой ржавчины, так как от этого предохраняет цинк, продукты коррозии которого заполняют несплошности, образовавшиеся в верхнем лакокрасочном покрытии, возобновляющемся после истечения определенного срока. Для прочного сцепления цинкового и лакокрасочного покрытий цинк обрабатывают различными химическими или металлургическими методами, подвергая его, например, фосфатированию, хроматированию, отжигу и др.
При горячем методе цинкования минимальная толщина покрытия составляет 47—86 мкм при толщине покрываемой стали 1—7 мм. Горячеоцинкованная продукция находит весьма разнообразное применение: в строительстве (кровля, устройства для верхнего света, противогрозовые установки, водосточные трубы, газопроводы, трубы для подачи холодной и горячей воды и частично для нагревательных целей), в энергетике (для защиты от коррозии опор линий высоковольтных электропередач, различного рода арматуры электрофицированных железных дорог), в сельском хозяйстве (при сооружении хлевов для крупного рогатого скота, свиней), в горнорудной промышленности (проволока, вагонетки и другие средства транспорта).
www.stroitelstvo-new.ru
Горячее цинкование полос. Производство проката |
Первые агрегаты непрерывного горячего цинкования (АНГЦ) полосы построены в Польше. Разработчиком технологии и оборудования был Сендзи- мир. Первый агрегат цинкования создан в 1931 г. для производства ленты шириной 300 мм, в 1933 г. — второй, для ленты шириной 700 мм, третий — в 1934 г. — для ленты шириной 1000 мм. С 1936 г. агрегаты горячего цинкования, работающие по технологии Сендзимира, начали работать в США, во Франции, Англии и других странах Европы [103].
Горячее цинкование полос
По способу Сендзимира очистку исходной полосы производят в линии путем окислительного нагрева до 470-480°С с образованием на поверхности полосы тонкой окисной пленки, которая восстанавливается при последующем отжиге в восстановительной водородной атмосфере. Охлажденную после этого до 480-520°С полосу с чистой активной поверхностью погружают в цинковый расплав при 450°С.
Для горячего цинкования стальных полос толщиной 0,3-4 мм применяет, в основном, метод бесфлюсового цинкования в непрерывных линиях. В последнее время широко применяют способ безокислительного нагрева полосы в продуктах неполного сгорания при незначительной разнице температур газовой среды (1100-1300°С) и нагреваемого металла (до 700°С). Скорость движения полосы до 3-4 м/с, время нагрева 10-15 с.
При горячем цинковании в цинковом расплаве покрытие на поверхности основного металла состоит из промежуточного диффузионного слоя относительно чистого цинка и далее следуют слои различных фаз. При цинковании металла в непрерывных линиях толщина промежуточного слоя доходит до 7-10% общей толщины покрытия. Поскольку промежуточный слой более хрупкий, чем цинковое покрытие, то чем он меньше, тем лучше.
По способу нанесения возможны двустороннее и одностороннее покрытия. При двустороннем покрытии цинк наносят на обе стороны, причем толщина покрытия одинакова. Обычно же внутренняя сторона изделия либо не требует вообще цинкового покрытия, либо требует покрытия меньшей толщины. В связи с этим разработан ряд способов получения одностороннего цинкового покрытия.
Двустороннее цинкование с удалением покрытия с одной стороны. Этот метод реализован впервые в конце 70-х годов прошлого века. Удаление цинка производят применением шлифовального валка, абразивной ленты, металлической вращающейся щетки (рис.146). Щетку заключают в колпак, в котором поддерживают вакуум. Отделенные частицы цинка, улавливают и используют повторно. Для предотвращения кристаллизации цинка из-за выделения тепла при механической обработке другой стороны полосы опорный ролик охлаждают. Недостатком способа является его достаточно высокая стоимость.
![]() |
Рис. 146. Схема размещения металлической щетки для удаления покрытия с одной стороны полосы, выходящей из ванны цинкования: 1 — реверсивная металлическая щетка; 2 — опорный приводной ролик; 3 — колпак; 4— полоса; 5 — ванна цинкования
Для снятия цинкового слоя с одной стороны полосы применяют также сдувание его сжатым газом. При производстве полос с разной толщиной цинкового покрытия применяют электролитическое растворение цинка с одной стороны и одновременное нанесение его на другую сторону полосы. При этом в агрегате производят предварительную частичную механическую зачистку покрытия щетками с одной стороны полосы, далее следует травление для удаления с цинкового покрытия оксидной пленки (таким образом обеспечивается хорошая адгезия электролитически осаждаемого цинка на сторону с более толстым покрытием), электролитическое растворение цинка с предварительно зачищенной стороны и одновременное нанесение его на другую сторону полосы. Заключительные операции — промывка полосы и механическая зачистка щетками оцинкованной стороны полосы и очистка рыхлого налета солей электролита со второй стороны полосы с нанесенным тонким покрытием с помощью ролика с поверхностью из мелкого абразива. В электролитическом процессе используется так называемый биполярный эффект. Постоянный ток разной полярности подводят к противоположным нерастворимым электродам. Непосредственно электрического контакта с полосой нет. Используется кислый сульфатный электролит. Таким методом получают полосу толщиной 0,6- 1,5 мм, шириной до 1780 мм с цинковым покрытием 61-98 г/м с одной стороны и менее 30 г/м2 с другой.
Двустороннее цинкование с нанесением на обратную сторону маскировочного покрытия. Для этой цели применяют специальные составы (не вступающие в реакцию с цинковым расплавом) — слой пленки окислов, фольги и т.п.
В качестве легирующих материалов в работе рекомендованы: сажа от сгорания углеводородов; краска, содержащая сажу и сложные композиции на основе окислов или солей.
Рис. 147. Схема размещения основного оборудования для нанесения на стальную полосу одностороннего покрытия из железоцинкового сплава с использованием маскирующего покрытия:
1 — разматыватель; 2 — ванна электролитической очистки; 3 — узел нанесения маскировочного покрытия; 4 — печь предварительной сушки; 5 — печь безокислнтельного нагрева; 6 — печь восстановительного нагрева; 7— ванна цинкования; 8 — устройство пламенной очистки; 9 — воздушный нож; 10 — печь термодиффузионного отжига; 11 — устройство для удаления маскировочного покрытия; 12 — дрессировочная клеть; 13 — ванна фосфатирования; 14 — узел промасливания; 15 — моталка
Рис. 149. Схема устройства огневой очистки поверхности маскировочного покрытия от частиц цинка: 1 — полоса; 2 — ванна цинкования; 3 — погружной р |
dlja-mashinostroitelja.info
Горячее цинкование — Цинковый портал
В основе технологии горячего цинкования лежит принцип диффузионного перемешивания веществ. Молекулы (атомы) одного вещества внедряются в кристаллическую решетку другого и перераспределяются в ней (атомы цинка внедряются в поверхностный слой стального изделия, формируя защитный слой) в процессе горячего цинкования.
Технологические характеристики процесса горячего цинкования
При горячем цинковании скорость диффузионного процесса напрямую зависит от• температурного режима, • агрегатное состояние взаимодействующих веществ.

Плотность поверхностного слоя — 7,13 г/см3. Микротвердость цинкового слоя после горячего цинкования составляет 360 МПа.
При горячем цинковании процесс протекает путем кратковременного погружения металлоизделия в расплавленный цинк (рабочая температура раствора ~ 450 градусов, время выдержки – 9-12 мин).
Твердость и износостойкость покрытия увеличивается за счет формирования на поверхности защитного слоя, состоящего из карбоната цинка. При извлечении обрабатываемой детали из расплавленного раствора происходит ряд последовательных химических реакций. Сначала образуется оксид цинка (цинк вступает в реакцию с кислородом, окисляется). Затем в результате взаимодействия диоксида углерода и оксида цинка получается устойчивое, твердое соединение – карбонат цинка.
Цинковое покрытие после финишной обработки имеет серый, матовый цвет. Для улучшения декоративных характеристик в цинковый расплав добавляют алюминий, никель (вместе или раздельно).
После горячего цинкования слой наносимого покрытия может находиться в диапазоне от 30 до 200 мкм. Толщина цинкового слоя зависит от• рабочей температуры расплавленного раствора, • временного интервала погружения, • скоростного режима извлечения обрабатываемого изделия из ванны цинкования, • финишного удаления излишков цинкового расплава.
Высокая износостойкость цинкового покрытия, большая толщина защитного слоя увеличивают срок эксплуатации обрабатываемых изделий.

В среднем металлоконструкции после горячей оцинковки служат 60 лет и больше.
Приоритеты технологии горячего оцинкования
1. Высокая устойчивость к химическому воздействию. 2. Способность защитного слоя к самовосстановлению в местах механического повреждения. 3. Высокие механические характеристики, ударная устойчивость. 4. Длительный срок эксплуатации обработанных деталей. 5. Простота технологического процесса. 6. Возможность оцинковать крупногабаритные изделия и конструкции. 7. Высокая электро- и теплопроводность цинкового покрытия.
Недостатки процесса горячего цинкования
1. Отсутствует возможность наложить слой с точными (жесткими) геометрическими параметрами, неравномерность толщины финишного покрытия (наплывы, утолщения). 2. Невозможность создать на обрабатываемой поверхности слой толщиной от 4 мкм (минимальная толщина покрытия 30 мкм). 3. Технология не позволяет обрабатывать мелкогабаритные изделия. 4. При обработке сложных, геометрических конструкций обязательно наличие дополнительных технологических отверстий для удаления излишков цинка.
Области применения изделий после горячего цинкования
Большая толщина наносимого покрытия, высокая коррозионная устойчивость, длительный срок эксплуатации – параметры, которые учитываются при создании ответственных металлоизделий. Горячей оцинковке подвергаются :• строительные металлоконструкции, • линии электропередач, • дорожные и мостовые опоры, • осветительные и рекламные конструкции, • дорожные, оградительные приспособления.
Горячее цинкование используется в трубопрокатном производстве. Горячеоцинкованые трубопроводы используются в нефтяной и газодобывающей промышленности (добыча и переработка). Оцинкованные изделия и конструкции используют в коммунальном хозяйстве, сельскохозяйственной отрасли.В автомобилестроении активно применяют оцинкованный, тонколистовой, холоднокатаный прокат (изготовление кузовных панелей). Разработана специальная методика высокоскоростного, горячего цинкования проволоки.
www.zinkportal.ru
Горячее цинкование (цинкование в расплаве цинка)
Северо-Западный государственный заочный технический университет.
РЕФЕРАТ
ТЕМА: Горячее цинкование (цинкование в расплаве цинка).
Составил: Подало А.Г.
2006 год
С о д е р ж а н и е :
1. ПОДГОТОВКА ПОВЕРХНОСТИ 2
1.1. Удаление жировых загрязнений, ржавчины и окалины 2
1.2. Флюсование 4
1.3. Особенности подготовки полосовой стали 5
1.3.1. Химическая подготовка 5
1.3.2. Термическая подготовка 6
2. ВЛИЯНИЕ ХИМИЧЕСКОГО СОСТАВА СТАЛИ,
ТЕМПЕРАТУРЫ И ПРОДОЛЖИТЕЛЬНОСТИ ЦИНКОВАНИЯ
НА ТОЛЩИНУ,СТРУКТУРУ И СВОЙСТВА ПОКРЫТИЯ 10
3. ВЛИЯНИЕ ХИМИЧЕСКОГО СОСТАВА РАСПЛАВА ЦИНКА
НА СВОЙСТВА ЦИНКОВЫХ ПОКРЫТИЙ 16
4. ОСНОВНЫЕ СПОСОБЫ ЦИНКОВАНИЯ ПОЛОСЫ 19
4.1.Способ «Армко-Сендзимир» 19
4.2. Способ «Юнайтед Стейтс Стил» 19
4.3.Способ «Кук-Нортман» 19
4.4.Способ «Селас» 19
5. ЦИНКОВАНИЕ ТРУБ И ПРИМЕНЯЕМОЕ ОБОРУДОВАНИЕ 21
5.1. «Сухой» способ 21
5.2. «Свинцовый» способ 23
6. ДЕФЕКТЫ ПОВЕРХНОСТИ ОЦИНКОВАННЫХ ИЗДЕЛИИ 24
Список литературы 25
1. ПОДГОТОВКА ПОВЕРХНОСТИ
Цинкование стальных изделий погружением в расплавленный цинк состоит из подготовки их поверхности к цинкованию и самого процесса нанесения цинкового покрытия.
Подготовка поверхности включает операции удаления жировых и других загрязнений, окалины, ржавчины, нанесение слоя флюса.
Процесс цинкования заключается в погружении изделий в ванну с расплавленным цинком, выдержке в нем определенное время, извлечении изделий из расплава. Следует
отметить, что обычно на практике все эти операции выполняются непрерывно в едином технологическом потоке.
Подготовка поверхности является важным этапом при цинковании. Хорошо подготовленная поверхность гарантирует полное взаимодействие стали с расплавленным цинком и сцепление цинкового покрытия с металлом основы.
Опыт работы показывает, что значительная часть брака. При цинковании в расплаве вызывается некачественной предварительной обработкой их поверхности. Таким образом, подготовку поверхности стальных изделий перед цинкованием необходимо проводить тщательно, строго соблюдая последовательность технологических операций и их режим.
1.1. Удаление жировых загрязнений, ржавчины и окалины
Удаление жировых и других загрязнений с поверхности изделий из черных металлов (обезжиривание) можно производить путем химической или электрохимической обработки их в щелочных растворах, а также путем отжига, в процессе которого эти загрязнения сгорают (окисляются). В процессе обезжиривания, помимо жиров и масел, происходит удаление и других механических загрязнений (стружка, пыль и др.).
Для обезжиривания широко используют водные щелочные растворы, содержащие едкий натр, тринатрийфосфат и жидкое стекло. Для уменьшения силы сцепления масла с поверхностью изделия в обезжиривающие растворы вводят поверхностно-активные вещества — эмульгаторы. После обезжиривания изделия тщательно промывают, чтобы удалить с их поверхности остатки обезжиривающего раствора.
На поверхности стальных изделий могут возникать оксиды различного состава и строения. Это прежде всего зависит от состава стали, способа изготовления и последующей обработки изделий, условий их хранения и транспортировки.
Обычно горячему цинкованию подвергают изделия из углеродистых и низколегированных сталей. Поверхность таких изделий обычно покрыта ржавчиной и окалиной.
Ржавчина (условно можно выразить формулой Foe • Fe2 O3 • nh3O) образуется на стальных изделиях в кислородсодержащей среде в присутствии влаги при комнатной температуре. Вначале на поверхности стали во влажной
атмосфере образуется гидрат закиси железа Fe(OH)2 , который в дальнейшем окисляется кислородом. Вследствие губчатого строения и наличия многочисленных капилляров ржавчина затрудняет обезжиривание поверхности стали.
Окалина на стальных изделиях обычно образуется в процессе их изготовления (например, при горячей прокатке, прессовании) или последующей термической обработки. В отличие от ржавчины окалина образуется при повышенных температурах (400°С и выше).
Состав, строение, толщина, равномерность распределения окалины по поверхности изделия зависит от многих факторов (например, состава стали, температуры и продолжительности окисления, содержания кислорода в окружающей среде).
В основном окалина состоит из оксидов железа, близких по составу к FeO (вюстит), Fe3 O4 (магнетит), Fe2 O3 (гематит). Непосредственно на стали находится вюстит, затем располагаются магнетит и гематит. Вюстит имеет пористое строение и низкую прочность, магнетит и гематит, наоборот, обладают высокой прочностью и плотным строением. Следует отметить, что окалина с трехслойным строением образуется на стали при температуре выше 570 °С при избытке кислорода в атмосфере и достаточно быстром охлаждении до низких температур. В других случаях окалина состоит из двух или одного слоя. Чаще всего слои FeO—Fe3 O4 — Fe2 O3 взаимно проникают друг в друга.
Обычно на стали образуется многокомпонентная сложного состава окалина, которая является результатом окисления не только железа, но и присутствующих в стали различных примесей (Mn, Si, P, S, N1, Сг, Си и др.). Примеси в окалине находятся либо в виде металлических включений (например, Ni, Си), либо в виде оксидов.
Окалина на кремнистых сталях существенно отличается от окалины, образующейся на углеродистых и нержавеющих сталях. В процессе термической обработки кремнистых сталей в окислительных средах наряду с внешним окислением происходит процесс внутреннего окисления стали. В слое, в котором происходит внутреннее окисление, появляются вкрапления двуокиси кремния. Под этим слоем находится обезуглероженный слой чистого феррита.
Внешний слой окалины состоит из вюстита с вкраплениями магнетита. Таким образом, наличие в составе окалины кремнистых сталей большой доли чистого феррита и инертного кремнезема определяет особенности ее травления. При прокатке образуется, в основном, вюстит, который сравнительно легко растворяется в кислоте; при отжиге листов образуются гематит и магнетит — труднорастворимые при травлении. Следовательно, наилучшей сталью для цинкования является холоднокатаная. Следует отметить, что особенно разнообразная по толщине, структуре и составу окалина может возникать на трубах, что обусловлено условия-Ми их производства.
Удаление ржавчины и окалины можно производить химическим и механическим методами.
Химический метод (травление) получил широкое распространение при подготовке поверхности изделий перед горячим цинкованием. Обычно травлением удаляют ржавчину и окалину с поверхности листов, полосы, труб, проволоки и других стальных изделий при подготовке их к цинкованию. На практике для травления изделий из углеродистых и низколегированных сталей широко применяют 18— 22%-ные водные растворы серной кислоты или 20— 25 %-ные водные растворы соляной кислоты.
Сравнивая достоинства и недостатки травильных растворов на основе серной и соляной кислот, следует отметить, что при травлении в серной кислоте растворяется не более 15—20 % окалины, в соляной до 40—50%. Поверхность стали после травления в растворах соляной кислоты получается более гладкой, чем после травления в растворах серной кислоты. Травление в серной кислоте из-за «перетрава» поверхности стали нельзя проводить без ингибиторов (замедлителей) кислотной коррозии. В этой связи необходимо отметить что с появлением надежных ингибиторов кислотной коррозии (ПКУ, ХОСП-10, БА-6, И-1-В и др.) достаточно хорошее качество поверхности достигается как при травлении в солянокислых, так и при травлении в сернокислых растворах. Выбор типа травильного раствора обусловлен в основном технико-экономическими соображениями.
Перспективно применение травильных растворов, содержащих смеси серной и соляной кислот.
Очистку стальной поверхности от ржавчины и окалины можно производить и механическим методом. Наиболее широко применяют дробеструйный или дробеметный способы, которые обеспечивают качественную подготовку поверхности стальных изделий.
Следует отметить, что для участков цинкования небольшой мощности (например, участки судоремонтных заводов), производящих цинкование изделий различной конфигурации, целесообразно использование дробеструйной обработки. Это позволяет получать качественно очищенную достаточно шероховатую, реакционно активную поверхности на стальных изделиях сложной конфигурации.
После травления изделия промывают в воде для удаления с их поверхности остатков травильного раствора и солей железа. Количество железа на поверхности стальных изделий может достигать 3—3,2 r/м2 после сернокислотного и 2—2,5 г/м2 после солянокислого травления в зависимости от концентрации и вязкости травильного раствора. Поэтому промывку изделий после сернокислотного травления желательно проводить сначала в горячей (60 °С) воде, а затем — в холодной. Если необходимо смыть остатки травильного шлама, применяют промывку из брандспойта или струйное промывание водой под давлением более 4-105 Па.
Учитывая, что после травления в соляной кислоте на поверхности стали остается примерно в 1,5 раза меньше солей железа, а также, что железные соли соляной кислоты смываются с протравленной поверхности значительно лучше, чем соли серной кислоты, производят обработку изделий в водном растворе соляной кислоты (50 г/л) при 18— 20°С (например, при цинковании труб). Эту операцию называют декапированием или подтравливанием. При этом происходит переход сульфата железа в хлорид:
FeSO4 + 2HClFeCl2 f h3 SO4 .
Затем изделия промывают в холодной проточной воде.
mirznanii.com
Горячее цинкование | Оборудование для цехов горячего цинкования
Компания ПОЛИГОНАЛЬ предлагает широкий спектр инжиниринговых услуг по проектированию и вводу в эксплуатацию цехов горячего цинкования металлических конструкций погружением в расплав цинка. При проектировании мы используем линии горячего цинкования на базе газовых и электрических печей со стальной ванной. Как специалисты с многолетним опытом, мы предлагаем комплексные решения, подобранные по индивидуальным потребностям Клиента.
В объем нашего предложения входит:
Процесс горячего цинкования состоит из погружения предварительно подготовленного стального изделия в ванну с расплавленным цинком при температуре около 450°C.
При погружении происходит диффузия цинка с железом с образованием сплавов Fe-Zn и на поверхности остается чистый цинк. Горячее цинкование погружением является наиболее оптимальным и эффективным методом при покрытии изделия слоем цинка, защищающим его от коррозии, и считается одним из самых надежных.
Горячее цинкование позволяет не только создать защитное покрытие для предотвращения воздействия на стальные конструкции атмосферных явлений, но и обеспечивает анодную защиту стали в случае повреждения защитного слоя цинка.
Технология горячего цинкования позволяет создать защитный слой и на внутренней поверхности изделий, в особенности в случае цинкования полых или трубообразных изделий. При эксплуатации изделия в особых условиях на цинковое покрытие наносится слой краски. Такая система покрытия может увеличить срок годности горячего цинкового покрытия вдвое.
polygonal.com.ua