-
шарикоподшипниковые (из них делают ролики и шарики подшипников),
-
графитизированные (из них создают поршни, коленчатые валы и прочие фасонные отливки),
-
высокомарганцовистые (из этих сталей делают звенья гусениц и многое другое).
- российского производства: 18ХГНМФР
- импортного производства: hardox, raex, fora, xar
- Высокомарганцовые;
- Шарикоподшипниковые;
- Конструкционные;
- Пружинные;
- Для цементации;
- Для азотирования;
- Специальные.
- 95Х18МФ / 1.4112;
- Raex 300, 400, 450, 500;
- Х12МФ / 1.2379;
- Х12В / 1.2436;
- 40Х13 / 1.4034;
- Р6М5 / 1.3343;
- 5ХН2МФ / 1.2714;
- Hardox 400, 450, 500, 550;
- 4Х5М3Ф / 1.2367;
- 5ХНМ;
- 20Х13 / 1.4021;
- 40Х / 1.7035;ХВГ9ХФ / 1.2235.
- Ковши экскаваторов;
- Кузова самосвалов;
- Инструменты и оборудование для горнодобывающей промышленности;
- Запчасти к строительной и сельхозтехнике;
- Цементовозы;
- Бронированные двери;
- Сейфы;
- Простенки зданий.
- Срок службы дымохода из нержавеющей стали
- Трубные линии для производства стальной трубы
- Стальная труба масса
- Лист перфорированный стальной гост
- Сталь кобальтовая
- Классификация стали if
- Швеллер стальной горячекатаный 10п
- Прокат стали это
- Труба прямоугольная из нержавеющей стали гост
- Круглая оцинкованная сталь гост
- Отпуск после закалки стали 40х
Износостойкие стали, их марки и назначение. Износостойкие марки стали
Марки износостойкой стали, применение износостойких сталей
Сталь – это соединение железа с углеродом и прочими элементами, которое можно подвергать ковке или деформации. Классификация стали происходит по составу химических элементов, по методу изготовления и количеству вредных примесей, по способу применения и по микроструктуре.
Одним из видов стали являются износостойкие стали. Это специальные сплавы, которые предназначены для эксплуатации в экстремально тяжелых условиях. Они способны выдержать исключительный абразивный износ и воздействия скольжения или ударов.
Износостойкие стали обладают повышенной твердостью, благодаря применению в составе марганца и прочих легирующих элементов. Стали с таким составом склонны к интенсивному наклепу.
Чем больше на элемент воздействуют сверхнагрузки, вызывающие в стали напряжения, которые больше ее предела текучести, тем интенсивнее происходит повышение ее твердости и износостойкости, при стандартно значительной вязкости.
Марки износостойкой стали
В промышленности широко используются материалы наклепного типа, к примеру, 110г13. Также для деталей механизмов применяется марка 110г13л, в составе которой имеется от 1 до 1,4 процента углерода. Используется высокомарганцовистая сталь Г13г13.
Что касается зарубежных марок, то обычно предпочтение отдается относительно стойким к износу материалам Hardox, Raex, Fora, Xar.
В рамках замещения импортных материалов, в нашей стране широко используется более доступная по цене, но при этом превосходящая аналоги российская бронесталь типа А3. В России применяется и марка 45Х2НМФБА.
Назначение износостойких сталей
Такие материалы производят для агрегатов и оборудования, применяемого в промышленных областях, связанных с лесопильным и горно-добывающим делом, переработкой отходов, обработкой почвы и не только.
Эти стали легко переносят удары, абразивное трение и высокое давление. Из них делают, к примеру, экскаваторные ковши, черпаки землеройных машин, щеки камнедробилок, гусеничные траки и многие другие детали.
Подобные стали требуются для элементов подобных агрегатов. Они делятся на три типа:
atl-met.ru
Износостойкие стали
Подробности Дата публикацииНаша компания изготавливает детали из импортных высококачественных износостойких сталей по эскизам и чертежам заказчиков.
Износостойкие стали:
Износостойкие стали описываются как "феномен металлических поверхностей", которые перемещаются относительно друг друга получения изношены из-за царапин на поверхности друг с другом или в связи с металлической адгезии. Свойства износостойких сталей дает им возможность противостоять износу, из-за трения, удара или сжимающих нагрузок от внешних факторов, таких как цемент, песок, камни и т.д., и предназначены для использования в строительстве оборудования и для замены изношенных деталей. Самосвальные кузова, подъемно-транспортное оборудование и дробильные машины, например, подвергаются непрерывному, абразивному и ударному износу. В качестве решения, специальные конструкционные стали были разработаны, которые обладают высокой устойчивостью к износу и истиранию. Факторы, влияющие на износостойкость сталей. Есть четыре основных фактора, которые имеют значительное влияние на износостойкость сталей. Это (I) термообработка, (II) легирующих добавок, (III) влияние содержания углерода, и (IV) эффекты карбидов, как первичный, так и вторичный. Большой фактором, влияющим на износостойкость является 'твердость'. В общем, износ возрастает сопротивление как материала становится все труднее. Существует прямая связь между твердостью и износостойкостью. Сопротивление стальной поверхности от износа в первую очередь зависит от "эффективной" твердости в результате разрушающего действия абразивных частиц и зависит от деформационного упрочнения скорость стали под применяемых условий. Факторы, влияющие на пластическую деформацию, например, размера зерна, температура рекристаллизации, твердость, скорость деформации, также влияют на износ сталей. В отличие от монокристаллов, имеющих свободные границы, зерна поликристаллического стали находятся под влиянием их neighours в процессе деформации, их действие на ограничения деформации мере, когда средний диаметр зерна больше, чем микроскопических областей контакта. Таким образом связываться через большое количество зерен резко снижает скорость износа. Поэтому большой размер зерна нежелательно для хорошей износостойкостью свойства стали. Оксидная пленка выпускается в воздух в результате механического окисления предотвращает контакт металл / металл и снижает скорость износа до тех пор, пока слой оксида остается связан с поверхностью. Стали которые противостоят эффекту окисления, скорее всего, обладают тяжелой адгезией и переносом металла, особенно если они также обладают низкой прокаливаемостью. Текстура поверхности износа дорожки значительной степени зависит от микроструктуры материала. Разрывная структура является преимуществом в Одер ингибировать серьезный рост зерна. Таким образом углеродистые стали менее подвержены износу, чем однородного нержавеющей стали. Из-за структуры феррито-перлитной стали в С износа ограничена ферритового компонента и, следовательно, только за счет увеличения углерода, содержание феррита может быть уменьшено и твердость может быть увеличена в результате чего в увеличении износа тивление. Закалка становится легко, как количество углерода возрастает. Если количество углерода превышает 0,6%, твердость закаленного становится почти постоянным. Хотя когда твердость становится постоянной, износостойкость не станет стабильным в этой точке, но увеличивает износостойкость далее при увеличении содержания углерода. Когда стали материал закаленное, утюг и углерод вместе и материальные превращается в мартенсит. Это мартенсит является эффективным для износостойкости. Однако в высокой углеродистой стали или высоколегированной стали, не весь материал превращается в мартенсит при закалке и отжиге, и около 20% до 30% материала остается аустенита. Это остаточный аустенит не хорошо для износостойкости. Наличие сплава карбидов повышает износостойкость сталей. Следовательно легирующие элементы, такие как хром, ванадий, вольфрам. молибден способствуют износостойкости в сталях. Карбиды будучи самым трудным компонентом в микроструктуре оказывает решающее влияние на износостойкость. Кроме того, чем меньше размер карбидов в стали, тем выше будет его износостойкость. Есть три основных пути укрепления структуры сталей по (I) легирования, (II) термическая обработка (II) наклеп. Эффект упрочнения на углеродистых сталей на износостойкость показано на фиг.1. износостойкость Рис. 1
Отношения твердости и упрочнения Пример износостойких сталей Износостойкие специальные конструкционные стали являются, как правило, закаленного или закалки и отпуска, и есть прекрасная мартенситной или мартенситной-бейнитный микроструктуру. Закаленной и отпущенной стали приспособлены для различных приложений с достаточной прочности и стойкости достигается либо за счет процесса термообработки или термомеханической прокатки. Твердость этих сталей предназначена, чтобы иметь требуемую износостойкость вместе с необходимой жесткостью в экономичным способом. Эти стали производятся в толщинах до 120 мм. Они производятся под торговыми названиями XAR, BRINAR, DILLIDUR и HARDOX т.д. Нормализованная специальная конструкционная сталь с твердостью 300 HB теперь доступен для конструкций, подвергающихся низким или умеренным уровнем износа, таких как захватов металлолома, в то время как HB сорт 600 отвечает экстремальные требования износостойкости. Покрытие твердости спектр от 300 до 600 НВ, подходящий материал, таким образом, доступны каждый тип износа подвергается применения. Сорт наиболее используется в настоящее время является сталь с твердостью 400 НВ, что составляет около пяти раз столь прочным, как обычной конструкционной стали. Стали с 450 HB, еще одного модифицированного сорта, показать даже более высокую твердость и, в то же время, хорошую прочность. Это позволяет реализовать более стабильных и легких конструкций, которые также высокой устойчивостью к износу воздействия. Основными направлениями использования для HB стали 450 включают производство самосвальных кузовов и режущими кромками. Все износ стойких сталей содержат хром в качестве легирующей добавки, которая оказалась очень эффективной, особенно в странах с низким кислоты СМИ. Высокая прочность обеспечивает хорошую стабильность формы и, таким образом, немного деформации. Из тонкого листового металла, позволяющие большую чистую нагрузку также возможны. Стали имеют уровень прочности, что гарантирует высокую ударопрочность даже при самых сложных условиях, таких как суб минусовых температурах, например. Носите сопротивление стали не представляют никаких проблем при воздействии пламени, плазменной и лазерной резки. Они показывают хорошую свариваемость и низкой чувствительностью к холодному растрескиванию. Аустенитная марганца (Mn) стали является очень жестким и пластичный материал, обладающий высокой ударной вязкости. Mn сталь представляет собой мягкий материал, имеющий первоначальную твердость около 220 до 240 НВ. Износостойкий из Mn стали основана на явлении упрочнения. Когда поверхность Mn стали в условиях интенсивной нагрузки воздействия или сжимающей нагрузки, он твердеет от поверхности, а основной материал остается жестким. Глубина и твердость рабочей закаленной поверхности изменяются в зависимости от применения и Mn марки стали. Работа закаленный слой может быть 10 мм до 15 мм глубиной и твердость может быть до 560 HB в первичных обращений. Соотношение Mn / C, и количество хрома также относятся к желаемой износостойкости этих сталей.
xn--80ackzrdjcch6bye.xn--p1ai
Износостойкие стали
Количество просмотров публикации Износостойкие стали - 2038
Конструкционные стали специального назначения
Рессорно-пружинные стали
– высокоуглеродистые, содержат 0,5…0,8%С. Применяются для пружин, рессор и других упругих элементов.
Термообработка: закалка + средний отпуск. Структура - троостит отпуска. Свойства: высокие пределы упругости, текучести и выносливости. Рессорно-пружинные стали должны иметь высокую прокаливаемость, пластичность, вязкость, релаксационную стойкость.
Углеродистые стали: 55, 60, 65, 70, 75, 80, 85. Применяются для пружин малого сечения (до 10 мм), эти стали имеют низкую релаксационную стойкость.
Легированные стали. Основными легирующими элементами в рессорно-пружинных сталях являются кремний (1…3% Si), марганец (~1% Мn), хром (~1%Cr), ванадий (~0,15%V), никель (до 1,7%Ni). Их вводят для повышения прокаливаемости, релаксационной стойкости и выносливости.
Кремнистые стали: 55С2, 60С2А, 70С3А применяют для автомобильных рессор, пружин вагонов. Кремний повышает прочность феррита͵ предел упругости, предел текучести, но способствует обезуглероживанию и графитизации. Эти недостатки устраняют добавками Cr, V, W, Ni: 60С2ХА, 65С2ВА, 60С2Н2А. Такие стали применяют для крупных тяжелонагруженных пружин и рессор.
Стали, не содержащие кремния, применяются для автомобильных рессор (50ХГА), клапанных пружин (50ХФА, 50ХГФА).
Предел выносливости рессор должна быть повышен в 1,5…2 раза путем поверхностного пластического деформирования: гидроабразивной или дробеструйной обработкой.
Шарикоподшипниковые стали применяются для подшипников качения (шарики, ролики, кольца). Οʜᴎ содержат в среднем 1% углерода, стали должны иметь высокую твердость, износостойкость, контактную выносливость и сквозную прокаливаемость.
Сталь ШХ15 содержит ~1%С и 1,5%Cr. Термообработка: закалка в масле с температуры 820…850°С + низкий отпуск при 150…170°С. Структура – мартенсит и дисперсные карбиды. Сталь ШХ15СГ дополнительно содержит 0,8%Si и 1,2%Mn для повышения прокаливаемости, и применяется для крупногабаритных подшипников.
Износостойкая аустенитная сталь Гадфильда 110Г13Л содержит 1,1%С, 13%Mn, (Л–литейная). Структура после литья: аустенит легированный + карбиды (Fe,Mn)3С. Для растворения хрупких карбидов и получения однородной аустенитной структуры сталь подвергают закалке в воде от температуры 1100°С.
Сталь обладает высокой износостойкостью в условиях динамического износа, благодаря способности аустенита к деформационному упрочнению (наклепу). При ударных нагрузках в поверхностном слое по границам зерна аустенита выделяются карбиды марганца. Это приводит к обеднению аустенита углеродом и легирующими элементами. В результате температуры МН и МК повышаются, аустенит частично превращается в мартенсит, что повышает твердость и износостойкость.
Применение: траки гусеничных машин, ковши экскаваторов, крестовины железнодорожных путей и т.п.
referatwork.ru
Конструкционные износостойкие стали

Под термином «конструкционные стали» подразумевается ряд сплавов, используемых в изготовлении разнообразных узлов, деталей, конструкций и механизмов в машиностроении и строительной области. Конструкционные стали отличаются от других типов особой прочностью.
Конструкционные стали имеют несколько классификаций. В частности их можно разделить по содержанию углерода и добавок на углеродистые и легированные; по способам обработки (цементуемые и улучшаемые), по предназначению – пружинные, подшипниковые. Особую категорию таких сталей составляют износостойкие сплавы, разрабатываемые для работы в экстремально тяжелых условиях, где присутствует высокий абразивный износ, износ в результате скольжения и ударов.Эти сплавы разрабатываются специально для механизмов и оборудования, работающих в горно-добывающей и лесопильной промышленности, на переработке отходов и металлолома, в строительстве дорог, почвообработке и т. д.
Износостойкие стали должны обладать повышенной твердостью. Этого добиваются различными способами. Как правило, для получения данного типа сплавов используются разнообразные легирующие элементы, в частности, марганец. Из отечественных сплавов такой сталью является высокомарганцовистая сталь Г13. Она имеет от 1 до 1,4% углерода и от 12 до 14% марганца в своем составе. Поскольку эта сталь относится к аустенитным, ее характерной особенностью является только стойкость к интенсивному наклепу.
Шарикоподшипниковые стали предназначены для работы в условиях повышенного истирающего износа, возникающего вследствие трения скольжения и трения качения. Эти стали содержат приблизительно 1% углерода и до 1,5% хрома. К таким сплавам относятся отечественные стали ШХ6, ШХ9, ШХ15.
Особняком стоят высокопрочные износостойкие легированные военные стали типа А3 и стали производства концерна SSAB Oxelosund AB, в частности, линейка сплавов, объединенных общим названием Hardox. Так же, как и вышеописанные марки шарикоподшипниковых сталей, Хардокс-стали имеют в своем составе высокое содержание хрома. Например, в марке Hardox 500 от 1 до 1,5% в зависимости от толщины листа. Однако содержание углерода в этих сплавах намного ниже. Отдельные марки этого бренда включают всего 0,2% С. Концентрация углерода влияет на такие характеристики сталей, как твердость и прочность. Несмотря на то, что сплавы Hardox относятся к низкоуглеродистым, они, тем не менее, являются высокопрочными. К примеру, сталь Hardox 450 обладает твердостью в 425-475 НВ и прочностью на разрыв – 1400 МПа. Производитель добивается этого, применяя различные инновационные методики, например, миролегирование, продувку инертными газами в ковше, а также выбирая исходное сырье по высоким стандартам. На заводах концерна практикуется, в частности, использование руды с низким содержанием серы. Сравнительные испытания на Уралвагонзаводе иностранных и Российских сталей в рамках программы импортозамещения показывают, что ХАРДОКС многократно проигрывает А3.
Лабораторные испытания на истирание и износ не дают ХАРДОКСУ эксплуатироваться более 3 месяцев, тогда как А3 практически вечен.
В отечественной практике используется в качестве износостойкого сплава также сталь с высоким содержанием углерода и кремния – так называемая графитизированная сталь. Количество этих двух элементов варьирует от 1,3 до 1,75%. За счет присутствия кремния часть углерода образует графит. Эти сплавы применяются для выплавки валов, производства штампов, калибров, пресс-форм.
Высокомарганцевые стали наподобие марки Г13 уступает по твердости (эта характеристика составляет примерно 200-250 НВ), но относится к недорогим вариантам износостойких сталей. Максимальную износостойкость этот сплав приобретает после закалки при температуре от 1000 до 1100 °С и охлаждении на воздухе. Такая сталь может быть применена для производства звеньев тракторных гусениц, крестовин, устанавливаемых на железных дорогах.
Использование износостойких сталей является весьма выгодным и перспективным в любой отрасли, где детали, узлы и другие изделия из стальных сплавов подвергаются повышенным нагрузкам. Поэтому с каждым днем спрос на такие стали неуклонно и стремительно растет.
Под термином «конструкционные стали» подразумевается ряд сплавов, используемых в изготовлении разнообразных узлов, деталей, конструкций и механизмов в машиностроении и строительной области. Конструкционные стали отличаются от других типов особой прочностью.
Конструкционные стали имеют несколько классификаций. В частности их можно разделить по содержанию углерода и добавок на углеродистые и легированные; по способам обработки (цементуемые и улучшаемые), по предназначению – пружинные, подшипниковые. Особую категорию таких сталей составляют износостойкие сплавы, разрабатываемые для работы в экстремально тяжелых условиях, где присутствует высокий абразивный износ, износ в результате скольжения и ударов.Эти сплавы разрабатываются специально для механизмов и оборудования, работающих в горно-добывающей и лесопильной промышленности, на переработке отходов и металлолома, в строительстве дорог, почвообработке и т. д.
Износостойкие стали должны обладать повышенной твердостью. Этого добиваются различными способами. Как правило, для получения данного типа сплавов используются разнообразные легирующие элементы, в частности, марганец. Из отечественных сплавов такой сталью является высокомарганцовистая сталь Г13. Она имеет от 1 до 1,4% углерода и от 12 до 14% марганца в своем составе. Поскольку эта сталь относится к аустенитным, ее характерной особенностью является только стойкость к интенсивному наклепу.
Шарикоподшипниковые стали предназначены для работы в условиях повышенного истирающего износа, возникающего вследствие трения скольжения и трения качения. Эти стали содержат приблизительно 1% углерода и до 1,5% хрома. К таким сплавам относятся отечественные стали ШХ6, ШХ9, ШХ15.
Особняком стоят высокопрочные износостойкие легированные военные стали типа А3 и стали производства концерна SSAB Oxelosund AB, в частности, линейка сплавов, объединенных общим названием Hardox. Так же, как и вышеописанные марки шарикоподшипниковых сталей, Хардокс-стали имеют в своем составе высокое содержание хрома. Например, в марке Hardox 500 от 1 до 1,5% в зависимости от толщины листа. Однако содержание углерода в этих сплавах намного ниже. Отдельные марки этого бренда включают всего 0,2% С. Концентрация углерода влияет на такие характеристики сталей, как твердость и прочность. Несмотря на то, что сплавы Hardox относятся к низкоуглеродистым, они, тем не менее, являются высокопрочными. К примеру, сталь Hardox 450 обладает твердостью в 425-475 НВ и прочностью на разрыв – 1400 МПа. Производитель добивается этого, применяя различные инновационные методики, например, миролегирование, продувку инертными газами в ковше, а также выбирая исходное сырье по высоким стандартам. На заводах концерна практикуется, в частности, использование руды с низким содержанием серы. Сравнительные испытания на Уралвагонзаводе иностранных и Российских сталей в рамках программы импортозамещения показывают, что ХАРДОКС многократно проигрывает А3.
Лабораторные испытания на истирание и износ не дают ХАРДОКСУ эксплуатироваться более 3 месяцев, тогда как А3 практически вечен.
В отечественной практике используется в качестве износостойкого сплава также сталь с высоким содержанием углерода и кремния – так называемая графитизированная сталь. Количество этих двух элементов варьирует от 1,3 до 1,75%. За счет присутствия кремния часть углерода образует графит. Эти сплавы применяются для выплавки валов, производства штампов, калибров, пресс-форм.
Высокомарганцевые стали наподобие марки Г13 уступает по твердости (эта характеристика составляет примерно 200-250 НВ), но относится к недорогим вариантам износостойких сталей. Максимальную износостойкость этот сплав приобретает после закалки при температуре от 1000 до 1100 °С и охлаждении на воздухе. Такая сталь может быть применена для производства звеньев тракторных гусениц, крестовин, устанавливаемых на железных дорогах.
Использование износостойких сталей является весьма выгодным и перспективным в любой отрасли, где детали, узлы и другие изделия из стальных сплавов подвергаются повышенным нагрузкам. Поэтому с каждым днем спрос на такие стали неуклонно и стремительно растет.
irontub.ru
4.4. Износостойкие стали.
Необходимым условием обеспечения износостойкости при большинстве видов изнашивания является высокая твердость поверхности. При работе в условиях больших давлений и ударов наибольшей работоспособностью обладают аустенитные стали с низкой исходной твердостью, но способные из-за интенсивного деформационного упрочнения (наклепа) формировать высокую твердость поверхности в условиях эксплуатации.
Наибольшей износостойкостью при абразивном изнашивании обладают материалы, структура которых состоит из частиц твердой карбидной фазы и удерживающих их высокопрочной матрицы. Такие материалы обычно используют в виде наплавочных. Они представляют собой сплавы с высоким содержанием углерода (до 4 %) и карбидообразующих элементов (Cr, W, Ti). В их структуре может быть до 50 % специальных карбидов, увеличение количества которых сопровождается ростом износостойкости. Структуру матричной фазы регулируют введением марганца или никеля. Она может быть мартенситной, аустенитно-мартенситной и аустенитной.
Для деталей, работающих без ударных нагрузок, применяют сплавы с мартенситной структурой.
К ним относятся сплавы типа У25Х38, У30Х23Г2С2Т (цифры, стоящие после буквы "У", показывают содержание углерода в десятых долях процента). Детали, работающие при значительных ударных нагрузках (зубья ковшей экскаваторов, пики отбойных молотков и др.), изготовляют из сплавов с аустенитно-мартенситной (У37Х7Г7С) или аустенитной (У11Г13, У30Г34) матрицей. Для обеспечения устойчивости к усталостному виду изнашивания, которому обычно подвергаются детали подшипников качения, используются высокоулеродистые хромистые подшипниковые стали, такие как ШХ4, ШХ15, ШХ15ГС и ШХ20ГС. Они содержат примерно 1 % углерода (ГОСТ 801-78), цифра означает массовую долю хрома в десятых долях процента.
Трение с высокими давлениями и ударным нагружением характерно для работы траков гусеничных машин, крестовин железнодорожных рельсов, ковшей экскаваторов и других деталей. Их изготавливают из высокомарганцовистой аустенитной стали 110Г13Л, содержащей 1,1 % С и 13 % Mn.
Высокая износостойкость этой стали обусловлена способностью аустенита к сильному деформационному упрочнению. В условиях ударного воздействия твердость этой стали возрастает с НВ = 2000 МПа до НВ = 6000 МПа.
Сталь плохо обрабатывается резанием, поэтому детали получают литьем. Соответствие некоторых отечественных марок легированных подшипниковых сталей с зарубежными аналогами представлено в таблице 4.5.
Таблица 4.5
Аналоги зарубежных подшипниковых сталей
Страны СНГ (ГОСТ) | Евронормы | США (стандарты) | Япония (JIS) | Китай (GB) |
ШХ4 | 100Cr2 (1.3501)* | 50100 | - | G20Cr2Ni4 |
ШХ15 | 100Cr6 (1.3505)* | 52100 | SUJ2 | GCr15 |
ШХ15СГ | 100CrMn6 (1.3520)* | A485 | SUJ3 | GCr15SiMn |
Примечание: * - цифровое обозначение.
Контрольные вопросы
1. Какую сталь целесообразно использовать для изготовления ковшей экскаваторов?
2. Какие марки износостойких сталей Вы знаете?
3. Как достигается высокая износостойкость стали ШХ15?
4. Какие легирующие элементы повышают износостойкость сталей?
5. Какой сталью можно заменить износостойкий чугун?
6. Какие существуют зарубежные аналоги подшипниковых сталей отечественного производства?
7. Как изменяется износостойкость сталей, легированных хромом?
8. Как влияет кремний на износостойкость сталей?
9. Как влияет марганец на износостойкость сталей?
10. В каких эксплуатационных условиях следует применять сталь марки 110Г13Л?
11. Как изменяется износостойкость сталей, легированных марганцем?
12. Почему износостойкие стали марки 110Г13Л плохо свариваются?
13. Что обеспечивает устойчивость к усталостному виду изнашивания в износостойких сталях?
14. Что является необходимым условием обеспечения износостойкости при большинстве видов изнашивания поверхности.?
15. Почему износостойкие стали марки 110Г13Л не подвергаются обработке резанием?
16. Как расшифровать марку износостойкой сталиУ37Х7Г7С?
studfiles.net
Износостойкие стали С500 лучшие в мире износостойкие стали
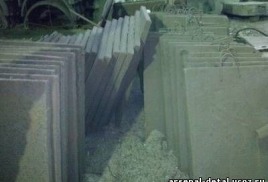
Стали и сплавы износостойкие в условиях истирающего износа (трения качения, трения скольжения). В подобных условиях работают детали типа шарико- и роликоподшипников, валы, детали дорожных и землеройных машин.
Чтобы материал имел повышенную износостойкость в таких условиях, необходима высокая твердость.
Наряду с высокоуглеродистыми сталями в качестве износостойких материалов используют белый чугун, твердые сплавы. Последние имеют исключительно высокую износостойкость.
Особую группу износостойких сталей составляют шарикоподшипниковые стали, имеющие около 1 % C и от 0,6 до 1,5 % Cr: ШХ6 (0,6 % C), ШХ9 (0,9 % C), ШХ15 (1,5 % C) и др.
В качестве износостойкого сплава используется и графитизированная сталь. Такая сталь имеет в своем составе повышенное содержание углерода (1,3…1,75 %) и кремния (1,3…1,75). Благодаря этому часть углерода в стали выделяется в виде графита.
Графитизированные стали применяется для изготовления штампов, калибров, валов.
Износостойкие материалы в условиях действия ударного изнашивания в абразивной струе. Типичными – деталями подвергающимися подобному износу, являются рабочие органидезинтеграторов (мельниц для дробления песка).
Наиболее износостойкими материалами в условиях ударного абразивного износа являются сталь С500. Износоустойчивая броня С500 нашла широкое применение в цементной и горношахтной промышленности. Полезные свойства: износостойкость, ударопрочность, пулестойкость, абразивная устойчивость, взрывозащита, идеальная свариваемость, позволяют навсегда забыть о ХАРДОКС и стали 110г13, г13, 110г13л (литой вариант).
Износостойкая высокомарганцовистая сталь марки Г13 для работы в условиях изнашивания, сопровождаемого большими удельными нагрузками. Сталь Г13 имеет в своем составе 1…1,4 % углерода и 12…14 % марганца, она имеет аустенитную структуру и относительно низкую твердость (200…250 HB). Сталь Г13 широко используется для изготовления таких деталей, как корпуса шаровых мельниц, щек камнедробилок, крестовин рельсов, гусеничных траков, козырьков землечерпалок и т.д. Склонность к интенсивному наклепу является характерной особенностью сталей аустенитного класса.
Износостойкая, ударопрочная пулестойкая сталь С-500 превосходит 110г13 и ХАРДОКС в 10-ки раз в сложных условиях изнашивания, сопровождаемого большими удельными и ударными нагрузками
Стали и сплавы износостойкие в условиях истирающего износа (трения качения, трения скольжения). В подобных условиях работают детали типа шарико- и роликоподшипников, валы, детали дорожных и землеройных машин.
Чтобы материал имел повышенную износостойкость в таких условиях, необходима высокая твердость.
Наряду с высокоуглеродистыми сталями в качестве износостойких материалов используют белый чугун, твердые сплавы. Последние имеют исключительно высокую износостойкость.
Особую группу износостойких сталей составляют шарикоподшипниковые стали, имеющие около 1 % C и от 0,6 до 1,5 % Cr: ШХ6 (0,6 % C), ШХ9 (0,9 % C), ШХ15 (1,5 % C) и др.
В качестве износостойкого сплава используется и графитизированная сталь. Такая сталь имеет в своем составе повышенное содержание углерода (1,3…1,75 %) и кремния (1,3…1,75). Благодаря этому часть углерода в стали выделяется в виде графита.
Графитизированные стали применяется для изготовления штампов, калибров, валов.
Износостойкие материалы в условиях действия ударного изнашивания в абразивной струе. Типичными – деталями подвергающимися подобному износу, являются рабочие органидезинтеграторов (мельниц для дробления песка).
Наиболее износостойкими материалами в условиях ударного абразивного износа являются сталь С500. Износоустойчивая броня С500 нашла широкое применение в цементной и горношахтной промышленности. Полезные свойства: износостойкость, ударопрочность, пулестойкость, абразивная устойчивость, взрывозащита, идеальная свариваемость, позволяют навсегда забыть о ХАРДОКС и стали 110г13, г13, 110г13л (литой вариант).
Износостойкая высокомарганцовистая сталь марки Г13 для работы в условиях изнашивания, сопровождаемого большими удельными нагрузками. Сталь Г13 имеет в своем составе 1…1,4 % углерода и 12…14 % марганца, она имеет аустенитную структуру и относительно низкую твердость (200…250 HB). Сталь Г13 широко используется для изготовления таких деталей, как корпуса шаровых мельниц, щек камнедробилок, крестовин рельсов, гусеничных траков, козырьков землечерпалок и т.д. Склонность к интенсивному наклепу является характерной особенностью сталей аустенитного класса.
Износостойкая, ударопрочная пулестойкая сталь С-500 превосходит 110г13 и ХАРДОКС в 10-ки раз в сложных условиях изнашивания, сопровождаемого большими удельными и ударными нагрузками
irontub.ru
Износостойкая сталь: виды, марки и применение
Износостойкая сталь: виды, марки и применение
Износостойкие стали получили широкое применение в разных сферах промышленности и просто жизнедеятельности человека. Такие марки стали отличаются высоким сопротивлением истиранию и контактного износа и широко применяются в Украине в машиностроении, горнодобывающей промышленности, сельском хозяйстве, строительстве.
Основные группы износостойкой стали
На сегодняшний день, износостойкая сталь представлена в Украине в широком ассортименте и различных групп и марок. Вот перечень основных групп:
В зависимости от области применения, необходимо подбирать определенные виды износостойкой стали. Они различаются по своему строению, способу производства и характеристикам. Износ подразделяют на два основных вида.
Абразивный - характеризуется поверхностным истиранием. Происходит в процессе трения твердых частиц, которые движутся в струе газа или жидкости.
Контактный износ происходит из-за трения двух и больше поверхностей друг об друга. Обычно сопровождается ударами и повышенным давлением.
Основные сферы применения износостойкой стали
Износостойкая сталь широко применяется в самых различных сферах народного хозяйства, для производства механизмов и деталей для: экскаваторов, гусеничных вездеходов, тракторов, дорожной техники, инструмента. Также износостойкую сталь используют при производстве пружин, крестовин рельсов, подшипников и прочих деталей и элементов, которые подвержены интенсивному износу или работают на удар.
Самые распространенные марки износостойкой стали
В настоящее время в Украине наиболее востребованными и применяемыми являются износостойкая сталь следующих марок:
Из износостойких сталей импортного производства следует отметить продукцию следующих брендов - xar, raex, hardox, fora, российская - 65Г. Кроме вышеперечисленных, есть еще сталь Swebor (Швеция). Это бронированная сталь отличается своей универсальностью и отличными эксплуатационными характеристиками. Сталь Swebor характеризуется высокой устойчивостью к абразивному типу износа и в настоящее время широко применяется в аграрном секторе, промышленности, машиностроении, строительстве. Из нее делают:
Это далеко не полный перечень, где применяется сталь Swebor. Особо стоит остановиться на бронированной стали Swebor ARMOR. Благодаря уникальным характеристикам в области баллистической защиты, такая сталь широко используется при возведении стратегических объектов, строительстве тиров, банковских и прочих финансовых учреждений.
promrf.ru