- низкоуглеродистая (где присутствует до 0,25% углерода),
- среднеуглеродистая (от 0,25% до 0,6% углерода в сплаве)
- высокоуглеродистая (до 2% углерода).
- низколегированные стали (в их сплаве менее 4% легирующих добавок)
- среднелегированные (от 4% до 11% легирующих элементов в сплаве)
- высоколегированные стали (в них более 11% легирующих элементов).
- коррозийностойкие аустенитные стали
- жаростойкие аустенитные стали
- жаропрочные аустенитные стали
- хладостойкие аустенитные стали
- доэвтектоидные стали (то есть, стали с содержанием углерода менее 0,8%)
- эвтектоидные стали (стали с содержанием 0,8% углерода в сплаве)
- заэвтектоидные стали (содержание углерода от 0,8% до 2%).
- сталь А – без указания химического состава, но с гарантией определенных механических свойств;
- сталь Б – химические свойства указываются, но не гарантируются механические свойства материала;
- сталь В – гарантируются определенные химические и механические свойства материала.
- стали хромистые ферритного класса
- стали хромокремнистые мартенситного класса
- хромоникелевые стали аустенитно-ферритного класса
- хромоникелевые аустенитные стали.
- Марки стали перлитного класса
- Малоуглеродистая сталь
- Сталь какого рода
- Малоуглеродистая сталь
- Сталь какого рода
- Что такое сталь определение
- Что такое сталь определение
- Круг сталь
- Круг сталь
- Сталь 45 свариваемость
- Сталь 45 свариваемость
Перлитный класс стали: описание и сварка. Марки стали перлитного класса
Сталь - перлитный класс - Большая Энциклопедия Нефти и Газа, статья, страница 2
Сталь - перлитный класс
Cтраница 2
Стали перлитного класса с содержанием углерода не выше 0 35 % и легирующих элементов в сумме до 2 - 5 % пользуются широким распространением благодаря повышенным механическим свойствам и относительно невысокой их стоимости. [16]
Стали перлитного класса обычно охлаждают по первому способу, тогда как стали мартенситного класса - по второму или третьему способу. [17]
Стали перлитного класса обычно охлаждают по первому способу, тогда как стали мартенситного класса ( закаливающиеся на воздухе) - по второму или третьему способу. При прокатке стали на крупные размеры ( более 20 мм) прутки помещают в колодцы с температурой, превышающей температуру наибольшей скорости перлитного превращения аустенита. При медленном охлаждении это превращение проходит практически полностью, что обеспечивает отсутствие трещин. [18]
Стали перлитного класса являются сравнительно малолегированными сталями, содержащими при 0 12 % С 0 5 или 1 % Сг и 0 3 или 0 5 % Мо. Присадка ванадия измельчает зерно, а также повышает жаропрочность. После охлаждения изделий на воздухе получается перлитная структура с карбидом М3С, после закалки в масле - мартенсит-бейнит. [19]
Стали перлитного класса характеризуются относительно малым содержанием легирующих элементов, мартенситного - более значительным и, наконец, аустенитного - высоким содержанием легирующих элементов. [20]
Стали перлитного класса являются сравнительно малолегированиыми сталями, которые при 0 12 % С содержат 0 5 или 1 % Сг и 0 3 или 0 5 % Мо. Присадка ванадия измельчает зерно, а также повышает - жаропрочность. После охлаждения изделий на воздухе получается перлитная структура с карбидом МзС, после закалки в масле - мартенсит-бейнит. [21]
Стали перлитного класса, как не содержащие большого количества хрома, естественно, не обладают высокой жаростойкостью и их нельзя применять при температурах выше 550 - 580 С. [22]
Сталь перлитного класса является наиболее распространенным конструкционным материалом во всех отраслях промышленности, в том числе и в наиболее квалифицированном машиностроении. Сталь этого класса, как правило, содержит наименьшее количество легирующих элементов. [23]
Стали перлитного класса характеризуются относительно малым содержанием легирующих элементов, мартенситного - более значительным и, наконец, аустенитного - высоким содержанием легирующих элементов. [25]
Стали перлитного класса содержат незначительное количество легирующих элементов ( обычно не более 5 - 6 %), хорошо обрабатываются давлением и резанием. После закалки и отпуска заметно повышают механические свойства. Большинство конструкционных и инструментальных сталей относятся к сталям перлитного класса. [26]
Стали перлитного класса содержат до 0 16 % С и молибдена до 0 7 %, который увеличивает температуру рекристаллизации феррита и тем самым повышает жаропрочность. Аналогично, но слабее действует хром. Присадка ванадия измельчает зерно, а также повышает жаропрочность. [27]
Для стали перлитного класса, к которой относятся марки, указанные в таблице на стр. При изготовлении крупных турбинных поковок из стали Р2 или пружин и крепежных деталей паровых турбин из стали ЭИ723 с низкими остаточными напряжениями применяется двойная нормализация с последующим высоким от пуском. [28]
Для стали перлитного класса С-кривая ( фиг. [29]
Структура стали перлитного класса в отожженном состоянии представлена на фиг. [30]
Страницы: 1 2 3 4
www.ngpedia.ru
Перлитный класс стали: описание и сварка
Бизнес 20 мая 2018Перлитный класс стали - это металл, принадлежащий к низколегированному и среднелегированному типу. Чаще всего такое сырье используется в качестве конструкционной или инструментальной стали. Перлитная и ферро-перлитная структура данного материала после прохождения отжига или же после проката отлично поддается обработке любыми режущими инструментами.
Общее описание стали
Для того чтобы перлитный класс стали имел достаточно высокие механические параметры эксплуатации, необходимо провести закалку. Чаще всего для этого используется масло, а также нужно правильно провести процедуру отпуска. Благодаря такой обработке, удается повысить такой параметр, как прочность, к примеру, или износостойкость и твердость.
Стали перлитного класса выделяются минимальным содержанием легирующих элементов. Среднее содержание в мартенстиных сталях, а наибольшее количество в аустенитных.
Из-за малого количества добавок и модификаторов такие свойства, как жаростойкость, к примеру, также достаточно малы потому, что недостаточно хрома в составе. Использовать такой материал с температурой более 550-580 градусов по Цельсию нельзя.
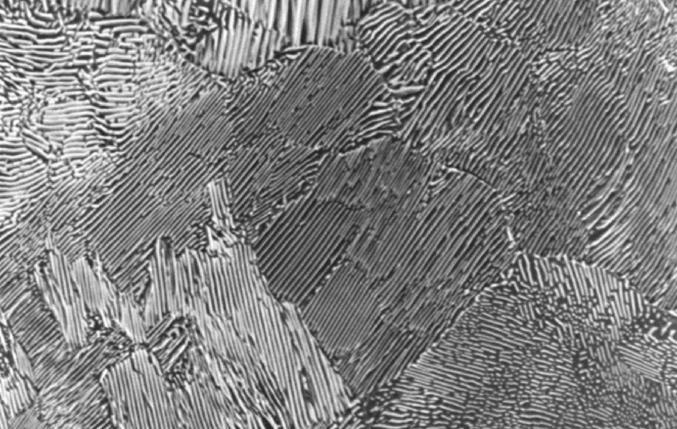
Марки и характеристики
Разнообразие марок стали перлитного класса не слишком большое, всего их около восьми. Среди них есть 12Х1МФ (12ХМФ), 20Х1М1Ф1ТР (ЭП182) и другие. На сегодняшний день используется то название марок, которое идет первым. Маркировка, указанная в скобках - это старая, однако она все еще может кое-где встречаться. Стоит отметить, что сталь данного класса при содержании углерода до 0,35% от всей массы и с количеством легирующих элементов до 2-5% достаточно популярна. Основная причина широкого распространения - это дешевизна и относительно неплохие механические качества.
Сталь перлитного класса чаще всего используется, как конструкционный материал. Стоит также отметить, что свариваемость стали с содержанием углерода до 0,35% и легирующими элементами в пределах 3-4%, достаточно неплохая.
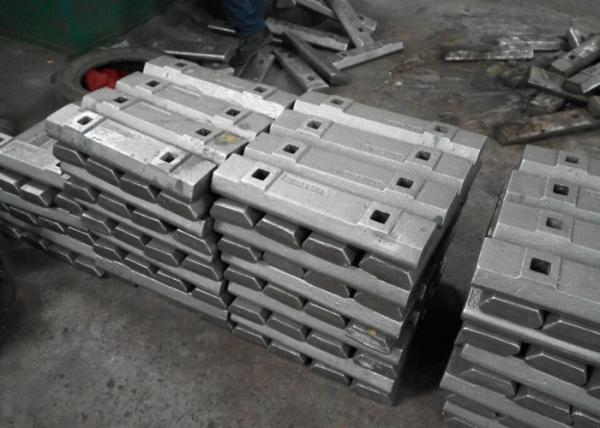
Видео по теме
Сварка перлитной стали
Стоит отметить, что при сварке сталей перлитного класса наиболее выгодным будет использовать элементы, которые применяются при сварке стали с низким коэффициентом легирования. Если для этого используется ручная электрическая дуговая сварка, то лучше всего применять такие электроды, которые имеют фтористо-кальциевое покрытие. В таком случае будет обеспечена высокая устойчивость металла шва против таких дефектов, как кристаллизация, к примеру. Кроме того, прочность сварного шва также будет достаточно удовлетворительной.
Что касается режимов сварки, а также температуры, которая должна использоваться для такого материала, то наиболее выгодно использовать те варианты, которые подходят для работы с высоколегированной сталью.
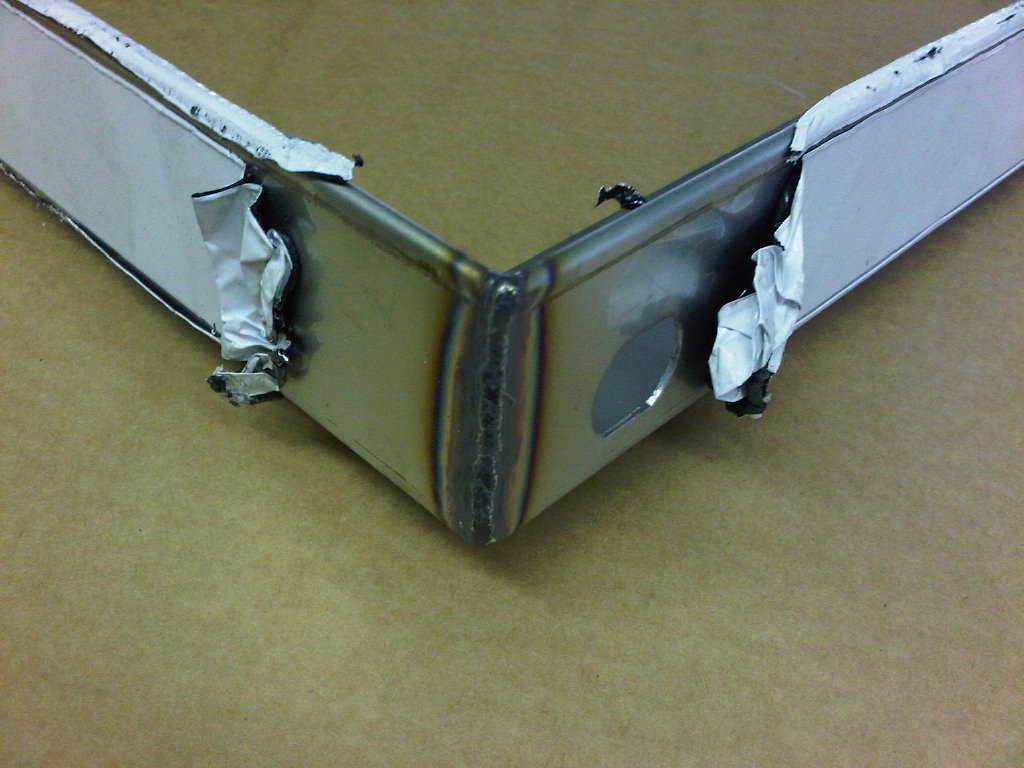
К примеру, если марка перлитной стали 15ХМ или 12ХМ, то температура во время сварки должна быть примерно 400-450 градусов по Цельсию. Для работы применяется ручная электродуговая сварка. В качестве электродов чаще всего выбираются такие марки, как Э42А или проволока типа Св-08А. Что касается процедуры отпуска после сварки, то ее можно не проводить вовсе или же проводить при температуре 630-650 градусов по Цельсию.
Источник: fb.ruКомментарии

Похожие материалы

В наше время достаточно сложно переоценить значение продуктов металлургии, которые широко используются в промышленности, строительстве, изготовлении бытовой утвари, предметов домашнего пользования. Но особого внимания...

В «Мире Варкрафта» существует среди игроков тенденция коллекционировать транспортные средства. Каждый пользователь желает получить всех доступных маунтов, и в это число обязательно должен войти Аннигилятор...

Уют, удобство и стиль – три кита, на которых строится оформление любого дома или квартиры. Как известно, уютная домашняя атмосфера, в которую так хочется погрузиться после тяжелого трудового дня, состоит из незн...

В последнее время для рукодельниц появилось огромное количество новых современных материалов для работы. Одним из таких новшест является фоамиран. Это мягкий и пластичный материал, из которого очень легко изготовлять ...

Сталь является одним из самых важных конструкционных металлов. Она нашла широчайшее применение в строительстве, машиностроении, а также многих других отраслях. У этого металла много самых разных марок, и все они отлич...

Клей "холодная сварка" представляет собой состав, предназначенный для соединения деталей без использования температурного воздействия. Склеивание осуществляется за счет пластичной деформации массы и ее проникновения в...

Земля – космическое тело, входящее в состав Солнечной системы. Рассматривая происхождение материков и океанов, стоит коснуться вопроса возникновения планеты.Как образовалась наша планетаПроисхожд...

Пожалуй, нет в истории бывшего Советского Союза эпизода более романтичного и драматичного, чем освоение Крайнего Севера. Необходимость в этом была первостатейной: в тех краях залегает огромное количество полезных иско...

Мытищи – это во всех отношениях приятный город, расположенный недалеко от Москвы. Он очень тихий, приветливый, дружелюбный. Здесь можно найти огромное количество достопримечательностей, которые стоит осмотреть. ...

Очень часто хочется украсить стол чем-то необычным и уникальным. Как правило, многие хозяйки к десертам подают фруктовые нарезки. Более оригинальной подачу сладкого салата сделают поделки из яблок и бананов. Кстати, о...
monateka.com
виды, классы, информация по стали и металлопрокату
Словом «сталь» обозначают сплавы железа с углеродом и другими химическими элементами, отвечающие следующим условиям: углерода в сплаве от 0,1% до 2,14%, а железа – не менее 45%. Существуют обычные углеродистые стали, стали легированные и высоколегированные. В последних двух случаях в сплав добавляются легирующие элементы, которые придают стали особую прочность.
Для чего вообще железо смешивать с углеродом? Это начали делать после того, как открыли влияние углерода на железо, выявили, как изменяются после этого физические свойства железа: оно становится более прочным, крепким, но при этом теряет пластичность. Добавление легирующих элементов еще больше усиливает этот эффект.
Между собой стали подразделяются по различным признакам, а потому существует несколько их классификаций. Давайте рассмотрим их по порядку и начнем с уже упоминавшихся трех классов, сгруппированных по химическим признакам:
УГЛЕРОДИСТЫЕ СТАЛИ
К таким сталям относят любые сплавы железа и углерода, не содержащие дополнительных легирующих элементов, и предназначенные для конструкционных и инструментальных задач. В свою очередь, углеродистая группа делится на подгруппы по количеству углерода в сплаве:
Главное отличие углеродистых сталей – их высокие прочность и твердость, а в химическом плане – еще и малое содержание иных примесей.
ЛЕГИРОВАННЫЕ СТАЛИ
Так называют все сплавы железа и углерода с добавлением (для прочности конечного продукта) легирующих элементов. Так же, как и углеродистые, стали легированные разделяются по подгруппам, в зависимости от качества и количества легирующей примеси в них:
В качестве легирующих элементов могут выступать хром (Cr), никель (Ni), молибден (Mo). В сочетании с железом и углеродом они обеспечивают получившийся материал износостойкостью и высокой прочностью.
Далее, стали можно разгруппировать по их структуре:
АУСТЕНИТНАЯ СТАЛЬ
Аустенитными сталями называют железные сплавы, которые при кристаллизации образуют однофазную аустенитную структуру γ-Fe c гранецентрированной кристаллической решеткой и сохраняют ее при охлаждении до криогенных температур. Данный класс также можно разделить на подгруппы:
Другое название данного класса сталей – «сталь аустенитного класса».
ФЕРРИТНАЯ СТАЛЬ
Так называется сталь со структурой из легированного феррита с допустимыми добавлениями карбидов. Ферритную сталь (иное название – сталь ферритного класса) получают с добавлением к железу небольшого количества углерода и большой доли легирующего элемента, например, ванадия или кремния.
МАРТЕНСИТНАЯ СТАЛЬ
Мартенсит – это игольчатая микроструктура в некоторых чистых металлах и закаленных металлических сплавах. Мартенситными сталями, в свою очередь, называют сплавы с преобладанием мартенсита в структуре. Помимо железа в таких сплавах содержится небольшое количество углерода (около 0,2%), и сравнительно большое количество хрома – от 11% до 17%. Допускается и наличие в мартенситной стали других элементов: никеля, ванадия или молибдена. Стали мартенситного класса стойки к щелочным средам, способны к самозакаливанию, обладают невысокой пластичностью и высокой жаропрочностью.
БЕЙНИТНАЯ СТАЛЬ
Бейнитом называют структуру стали, которая образуется в ходе промежуточного превращения аустенита. Поэтому иногда такую структуру называют «промежуточной». Химически сталь бейнитного класса отличается наличием легирующих добавок и низким содержанием углерода.
ПЕРЛИТНАЯ СТАЛЬ
Стали перлитного класса объединяют из следующих подгрупп:
Все они отличаются сравнительно небольшим содержанием легирующих элементов.
Другой, наиболее простой способ классификации стали – по ее качеству, которое зависит от характеристик элементов, участвующих в создании сплава, и их количества в нем.
СТАЛЬ ОБЫКНОВЕННОГО КАЧЕСТВА
Самый дешевый вид стали, что обусловлено качеством сплава. В стали обыкновенного качества допускается присутствие загрязнений, сторонних (то есть, не входящих в «рецептуру» сплава) элементов и даже неметаллических вкраплений. Вместе с тем, у обыкновенной стали есть свои градации качества: А, Б и В, при этом, в маркировке стали указываются только буквы «Б» и «В». Если же в указании марки стали обыкновенного качества нет буквенного обозначения, то подразумевается по умолчанию, что она относится к классу «А». В чем же особенности этих подклассов?
Из марок стали обыкновенного качества не рекомендуется изготавливать изделия, которые должны выдерживать большие нагрузки во время эксплуатации. Другое название стали обыкновенного качества – «рядовая сталь».
КАЧЕСТВЕННАЯ СТАЛЬ
К составу этой стали предъявляются гораздо более высокие требования, чем к предыдущей. В ней тоже допускаются включения неметаллических элементов, но совсем незначительные. Содержание серы в сплаве такой стали – не более 0,4%. Столько же может содержаться и фосфора – не более четырех десятых процента.
Плавят качественные стали в мартенах и кислородных конвертерах. Более высокие свойства качественной стали позволяют изготавливать изделия, которые допустимо использовать в сферах, где на них будет оказываться большая физическая нагрузка.
ВЫСОКОКАЧЕСТВЕННАЯ СТАЛЬ
К составу этого вида стали предъявляются высокие стандарты. В сплаве не должно быть неметаллических вкраплений, процентное соотношение вредных примесей допускается совсем мизерное (серы – до 0,030%, фосфора – до 0,035%). Также понижено допустимое присутствие в высококачественном сплаве углерода.
Высококачественные стали выплавляются в электрических и кислых мартенах. Изготавливать из них можно любые металлические изделия, без боязни быстрой поломки или недостаточной износостойкости. При этом, нужно учитывать, что высококачественный сплав отличается повышенной вязкостью, нежели качественный.
СТАЛЬ ОСОБО ВЫСОКОКАЧЕСТВЕННАЯ
Особо высококачественные стали изготавливаются с помощью самых современных методов, позволяющих не допускать сторонних, не входящих в «рецептуру» элементов и добиваться предельно высокой частоты сплава. Плавка таких сталей производится в электропечах с электрошлаковым переплавом. В химическом составе особо высококачественных сплавов практически нет газов и неметаллических вкраплений.
В конце марки особо высококачественных сталей принято ставить букву Ш. Поскольку производство таких материалов довольно трудоемкое и дорогое, то изготавливают из них изделия с наиболее ответственными функциями.
Наконец, популярно разделение сталей по их назначению. Такая классификация содержит большое множество групп:
КОНСТРУКЦИОННЫЕ СТАЛИ
Применяются для изготовления механизмов, деталей, конструкции в строительстве, машиностроении, автомобилестроении, судостроении. Внутри этой группы сталей есть свои подгруппы, которые состоят из сплавов, различающихся между собой прежде всего качеством.
ИНСТРУМЕНТАЛЬНЫЕ СТАЛИ
Так называют стали, которые содержат от 0,7% углерода и выше. Содержание серы и фосфора в сплаве определяет качество инструментальной стали (она может быть качественной и высококачественной).
Отличаются инструментальные стали невысокой стоимостью, высокой твердостью, но, при этом, невысокой износостойчивостью.
Внутри группы принято деление на следующие подгруппы:
инструментальные углеродистые стали
инструментальные легированные стали
инструментальные валковые стали
стали инструментальные штамповые
стали инструментальные быстрорежущие.
По названию всей группы не трудно догадаться, что из такого рода материалов изготавливают различные инструменты: метчики, топоры, молотки, пилы, фрезы и прочее.
НЕРЖАВЕЮЩИЕ СТАЛИ
Другое их название – «коррозийно-стойкие стали». Само название указывает на главное их свойство: они не подвержены коррозийным влияниям и стойки к воздействию агрессивных сред. Достигается это за счет включения в сплав с железом металла с антикоррозийными свойствами. Чаще всего в этой роли в нержавеющих сталях выступает хром или соединение хрома и никеля. Чем больше содержание хрома в сплаве, тем более коррозийно-стойкой оказывается сталь.
СТАЛИ ЖАРОПРОЧНЫЕ
Главное их отличие – стойкость к высоким температурам, высокие показатели ползучести и длительной прочности (это основные характеристики жаропрочных материалов). Изделия из таких сталей можно использовать длительное время в условиях высокой температуры, не опасаясь, что они начнут деформироваться и разрушаться. Соответственно, из жаропрочных сталей делают лопатки паровых турбин, газовые турбины, котельные установки, детали ракет и многое другое.
При создании жаропрочного сплава внимание прежде всего обращают на следующие характеристики основного компонента: температура плавления, легирование, режимы уже пройденной им термообработки.
По легированию жаропрочных сталей их подразделяют на уже рассмотренные на этой странице классы:
ферритные
мартенситные
мартенситно-ферритные
аустенитные.
СТАЛИ ЖАРОСТОЙКИЕ
Другое название – «окалиностойкие стали». Они отличаются стойкостью к коррозийному воздействию в газовых средах при повышенных температурах (имеются в виду температуры выше 550 °C). Поверхность их не окисляется и не начинает разрушаться при таком температурном режиме, что позволяет изготавливать из них изделия, которые предназначены для функционирования в условиях повышенных температур. Изделиями могут быть части двигателей машин и самолетов, конструкционные части печей, трубы теплоприемников.
Чтобы добиться окалиностойких свойств, в сплав добавляют некоторые элементы, которые при повышении температур образуют на поверхности стали защитный слой. В современной металлургии элементами этими выступают хром или кремний, которые при окислении образуют оксиды. От количества хрома или кремния зависит степень жаростойкости материала. Чтобы добиться наиболее высоких жаростойких свойств, в сплав вводят и хром, и кремний одновременно.
Внутри жаростойких сталей есть свое разделение на группы, различающиеся составом и структурой:
И КРИОГЕННЫЕ СТАЛИ.
Остались еще вопросы?Оставьте заявку и мы Вам перезвоним.
mirsplava.ru
НИЗКОЛЕГИРОВАННЫЕ ПЕРЛИТНЫЕ СТАЛИ (Хакимов А. Н.)
СВАРКА И СВАРИВАЕМЫЕ МАТЕРИАЛЫ
8.1. Назначение сталей
Низкоуглеродистые низколегированные стали перлитного класса применяются в различных конструкциях взамен углеродистых, обеспечивая снижение металлоемкости на 20—50 %. Оии широко используются в строительстве трубопроводов, конструкций газонефтехимических производств, судов, мостов и других сооружений, эксплуатируемых в температурном интервале от —70 до +475°С в зависимости от химического состава и структурного состояния, обеспеченного термообработкой.
8.2. Состав сталей
Одним из наиболее эффективных средств повышения качества низкоуглеродистых сталей является их упрочнение за счет легирования такими элементами, как Si, Мп, и повышения дисперсности структуры посредством термической или термомеханической обработки.
Содержание С в низколегированных сталях ие превышает 0,23 %. В зависимости от легирующих элементов, суммарное содержание которых в составе стали не превышает 5%, различают марганцовистые, кремнемарганцовистые, хромокремнемарганцовистые и другие стали, представленные в табл. 8.1. По содержанию S и Р эти стали можно отнести к качественным
ТАБЛИЦА 8.1 ХИМИЧЕСКИЙ СОСТАВ И МЕХАНИЧЕСКИЕ СВОЙСТВА НИЗКОЛЕГИРОВАННЫХ СТАЛЕЙ
|
сталям В последние годы расширяется производство и применение рафинированных посредством электрошлакового, вакуумного переплава сталей, обработанных в ковше синтетическими шлаками с целью снижения содержания серы в их составе для повышения сопротивляемости образованию слоистых (ламинарных) трещин. .
8.3. Механические свойства сталей
Введение в состав низкоуглеродистых сталей легирующих элементов (до 2 % каждого и до 5 % суммарно) способствует повышению прочности и сопротивления хрупкому разрушению, не ухудшая их свариваемости
Прочность сталей Показатели механических свойств сталей представлены в табл 8 1
Они характерны для проката в горячекатаном либо в нормализованном состояниях Термическое упрочнение позволяет дополнительно на 20—50 % увеличить уровень показателей прочности
Ударная вязкость. По ударной вязкости, в особенности при отрицательных температурах, низколегированные стали превосходят низкоуглеристые стали Термическое упрочнение позволяет повысить уровень ударной вязкости в 1,5—2 раза и обеспечить высокую сопротивляемость хрупкому разрушению низколегированных сталей
8.4. Свариваемость сталей
Легирующие элементы оказывают существенное влияние на показатели свариваемости сталей. Увеличение содержания элементов, повышающих закаливаемость, сопровождается снижением сопротивления сварных соединений образованию холодных трещин [1]. Элементы, упрочняющие твердый раствор, способствуют, как правило, снижению ударной вязкости металла в околошовной участке ЗТВ сварных соединений.
8.4.1. Типы структур в зоне термического влияния
Наиболее распространенные в металлургической практике легирующие элементы Мп, Сг, Мо снижают диффузионную подвижность С и, как следствие, увеличивают уровень значений характеристических длительностей Тф, тп, те, понижают температурный интервал y-v a-превращения. Поэтому при общепринятых режимах сварки в околошовном участке возрастает вероятность образования мартенсита и понижается сопротивляемость сварных соединений образованию холодных трещин.
8.4.2. Влияние легирующих элементов
Мп упрочняет феррит, снижает температуру начала у-э-а-пре - вращения, способствует процессу карбидообразования. Сг и Мо существенно снижают критическую скорость охлаждения, подавляют перлитное превращение, расширяют область промежуточных превращений на диаграмме.
Такие элементы, как Al, Ті, Nb, интенсифицируют процесс у-*- ос-превращения при высоких температурах, способствуя увеличению числа центров кристаллизации и получению мелкозернистой структуры.
8.4.3. Выбор тепловых режимов сварки
Одним из технологических средств, снижающих вероятность появления холодных трещин, является предварительный и сопутствующий подогрев [1].
Ъ*в>°/о Толщина проката, мм Рис 8 I Определение температуры подогрева в зависимости от Сэкв и толщины свариваемого проката {31 |
Для определения температуры подогрева стали с целью предотвращения образования холодных трещин в зависимости от содержания в ней химических элементов и толщины проката можно воспользоваться графиками, приведенными на рис. 8.1
[3] . Значения Сэкв, отложенные по оси абсцисс, определяют как:
Сэкв = с + Мп/6 + Si/5 + Сг/6 +
+ Ni/12+Mo/4 + V/5 + Cu/7+ Р/2.
Здесь символы обозначают содержание соответствующих химических элементов в процентах.
Предельное их содержание не должно превышать 0,5 % С;
1,6% Мп; 1 % Сг; 3,5 % N1;
0,6 % Мо; 1 % Си. Как видно, необходимая температура подогрева возрастает с увеличением степени легированности стали и толщины свариваемого проката.
Другая методическая последовательность, рассмотренная в работе [3], позволяет дифференцированно определять условия подогрева для корневых и заполняющих швов в соответствии с номограммой, представленной на рис. 8.2.
Методика пользования номограммой на примере сварки корневого шва стали толщиной 30 мм при значении тока 250 А, напряжении дуги 25 В, скорости сварки 25 см/мин представлена ниже:
Восстанавливаем перпендикуляр из точки а, соответствующей /=250 А, до пересечения с прямой, соответствующей напряжению 25 В, и получаем точку б в квадранте I. Затем проводим горизонталь б — в до пересечения с прямой, соответствующей скорости сварки 25 см/мин, в квадранте //. После этого опускаем перпендикуляр из точки в до пересечения с кривой, соответствующей толщине проката 30 мм, и получаем точку г; затем проводим горизонталь г — д до пересечения с прямой 1, соответствующей условиям сварки корневого шва в квадранте IV, восстанавливаем перпендикуляр из точки бив точке е определяем температуру подогрева, соответствующую 150 °С
Рис. 8.2. Номограмма для определения режимов сварки и предварительного подогрева сталей с содержанием Сэкв<0,6 %, іде СзкВ «C + Ni/15+Mo/4+ (Cr+V)/5 + Cu/13 + P/2 - t - + 0,0024s (s — толщина проката, мм) [3] / — при сварке кория шва; 2 — при сварке заполняющих швов; кривая А отражает условие необходимости применения подогрева, а прямая Б — температуру нижией гра* ницы интервала подогрева |
8.5. Технология сварки и свойства сварных соединений
Технология сварки низколегированных сталей должна проектироваться с учетом того обстоятельства, что при уменьшении погонной энергии и увеличении интенсивности охлаждения в металле шва и зоны термического влияния возрастает вероятность распада аустенита с образованием закалочных структур. При атоіуі будет отмечаться снижение сопротивляемости сварных соединений образованию холодных трещин и хрупкому разрушению. При повышенных погонных энергиях наблюдается рост зерна аустенита и образуется грубозернистая фер - рито-перлитная структура видманштеттового типа с пониженной ударной вязкостью.
8.5.1. Ручная сварка
Технология рунной дуговой сварки низколегированных сталей практически не отличается от соответствующей технологии сварки низкоуглеродистых сталей.
Сварку низколегированных сталей осуществляют электродами типа Э46А и Э50А с фтористо-кальциевым покрытием, которые позволяют достигать более высокую стойкость против образования кристаллизационных трещин и повышенную пластичность по сравнению с электродами других типов. Для сталей марок 09Г2, 09Г2С, 16ГС, 17ГС, 10Г2, 10Г2С1 рекомендуют применять электроды УОНИ 13/55, К-5А, АНО-11 (тип Э50А).
Для сварки кольцевых швов трубопроводов, работающих при температурах до —70 °С, например из стали 09Г2С, применяют электроды ВСН-3 (тип Э50АФ) с фтористо-кальциевым покрытием.
8.5.2. Сварка под флюсом
Технология сварки под флюсом низколегированных сталей практически такая же, как и для низкоуглеродистых сталей. В качестве флюсов при однодуговой сварке применяют флюсы марок АН-348А и ОСЦ-45, а при многодуговой на повышенной скорости — АН-60.
Для сталей марок 16ГС, 09Г2С, 10Г2С1 при эксплуатации не ниже —40 °С рекомендуется использовать сварочные проволоки Св-08ГА, Св-ЮГА, а при температурах эксплуатации до ■—70 °С (сталь 09Г2С в нормализованном состоянии) —сварочные проволоки Св-ЮНМА, Св-ЮНЮ, Св-08МХ с целью обеспечения достаточного уровня ударной вязкости.
8.5.3. Электрошлаковая сварка
Электрошлаковая сварка по общепринятой технологии сталей толщиной свыше 30 мм осуществляется, как правило, с последующей или сопутствующей нормализацией с целью повышения ударной вязкости металла шва и ЗТВ до регламентируемого уровня. Сварку сталей 16ГС, 09Г2С, 14Г2 осуществляют
с применением флюса АН-8 и сварочных проволок Св-08ГС, Св-10Г2. Режимы термообработки аналогичны указанным в гл. 7 для низкоуглеродистых сталей.
Сварка с регулированием термических циклов. Для кольцевых швов аппаратов газонефтехймических производств с толщиной стенки до 100 мм при температуре эксплуатации не ниже —40 °С (сталь 16ГС) и не ниже —55 °С (сталь 09Г2С) в соответствии с ОСТ 291—81 допускается применять электро - шлаковую сварку с регулированием термических циклов в сочетании с последующим отпуском [4]. При этом удается не только обеспечить равнопрочность, но н достаточно высокий уровень сопротивления сварных соединений хрупкому разрушению без применения последующей высокотемпературной термообработки.
Например, значения KCU~40 металла шва и околошовного участка составляют от 0,6 до 0,7 МДж/м2, а основного металла— стали 16ГС толщиной 60 мм — 0,8 МДж/м2.
Соответствующие данные для сварных соединений стали 09Г2С толщиной 60 мм при температуре испытаний —60 °С равны 0,66 и 0,75 МДж/м2, а для основного металла 0,58МДж/м2.
По уровню параметров трещиностойкости металл шва и зоны термического влияния не уступают основному металлу — нормализованной стали 09Г2С, имеющей следующие показатели: os = 550 МПа; ат = 370 МПа; Аю = 67,5 МПа-м1/2; С = 6,32х 10~14; п = 3,82; dl/dN при А/Сіс = /Сіс/1,5 составляет 0,68-10~3 мм/цикл.
Увеличение интенсивности охлаждения при электрошлаковой сварке с регулированием термических циклов предотвращает образование структурно-свободного феррита при у-*- а-превра - щении. Отмеченное препятствует протеканию коррозионных процессов, а уменьшение размеров карбидных частиц, играющих роль коллекторов водорода, тормозит катодную реакцию при эксплуатации сварных соединений в коррозионно-активных средах.
Особенностью термоупрочненных сталей является их склонность к разупрочнению при сварке.
Применение сопутствующего охлаждения позволяет обеспечить равнопрочность сварных соединений с основным термоупрочненным металлом и повысить их сопротивление хрупкому разрушению. Например, при механизированной дуговой сварке под флюсом по общепринятой технологии коэффициент прочности сварных соединений сталей 14ГН, 16ГС, 09Г2С толщиной 12 мм составил 0,75—0,77, а при сварке с сопутствующим охлаждением— не менее 0,98. Значения критических температур перехода в хрупкое состояние металла околошовного участка сварных соединений при переходе от общепринятой технологии к технологии сварки с сопутствующим охлаждением снизились на 40—50 °С и достигли уровня Ткр основного термоупрочненного металла.
При переходе от общепринятой технологии электрошлаковой сварки к технологии электрошлаковой сварки с регулированием термических циклов термоупрочненной стали 09Г2С (сварочная проволока Св-10НМ, флюс АН-8, последующий отпуск при 640 °С) коэффициент прочности сварных соединений повышается с 0,89 до 0,99, значения KCU~40 металла шва — с 0,12 до 0,72, а металла околошовного участка — с 0,08 до 0,42 МДж/м2.
9.1. Назначение сталей
Широкое применение при изготовлении конструкций ответственного иазна - значения — таких, как сосуды высокого давления, танкеры, суда, ледоколы, береговые и морские нефтегазовые сооружения, находят микролегирован - иые стали. Наряду с экономией легирующих элементов при их использовании особенно в термо - и термомеханически обработанном состояниях обеспечиваются высокая прочность и сопротивляемость хрупкому разрушению металла.
9.2. Состав сталей
В микролегированных сталях содержание углерода, как правило, не превышает 0,20 %. Микролегирующие элементы, входящие в состав сталей, находятся в следующих пределах, %: Al<0,06; Cr<0,25; Zr<0,15;
V<0,15; Ті 0,1—0,2; Nb<0,06; Mo<0,20; B<0,05.
ТАБЛИЦА 9.1 ХИМИЧЕСКИЙ СОСТАВ И МЕХАНИЧЕСКИЕ СВОЙСТВА МИКРОЛЕГИРОВАННЫХ СТАЛЕЙ
|
Продолжение табл. 9.1
|
Суммарное содержание Zr и Ті ие превышает 0,2%, a Nb, Ті и W — 0,16 %. В качестве микролегирующих элементов используют редкоземельные (Се, La, Y), а также N
Микролегирующие элементы вводят в состав стали как в процессе ее выплавки, так и в ходе виепечной обработки. Они могут присутствовать в металле в составе включений вторых фаз или непосредственно в матрице Например, в сталях, микролегированных V и Nb (иногда дополнительно А1 и Ті) в сочетании с повышенным до 0,03 % содержанием N, образуются дисперсные карбонитридные фазы, существенно повышающие их прочность.
Для повышения ударной вязкости и снижения анизотропии свойств ограничивают содержание S в составе стали до 0,005-—0,012 %.
Химический состав ряда марок микролегированных сталей приведен в табл. 9.1. Аналогами этих марок сталей в зарубежной практике являются стали типов Х55—Х80.
Известно, что С относительно слабо влияет на предел текучести сталей с феррито-перлитиой структурой. Однако с увеличением содержания С в составе стали существенно снижаются вязкопластические свойства и ухудшается свариваемость. Поэтому в последние годы получают распространение малоперлитные стали с ограниченным содержанием С (доі0,12%). Для компенсации понижения прочности их легируют марганцем до 1,7 % микро - легируют V, Сг, Мо. К отечественным малоперлитным сталям относятся стали марок 07Г2ФБ, 08Г2СФБ, 09Г2ФБ.
Из микролегированных сталей с бейнитиой структурой нашли применение марки 12Г2СМФ и 12ГН2МФАЮ.
msd.com.ua
Низколегированная сталь - перлитный класс
Низколегированная сталь - перлитный класс
Cтраница 1
Низколегированные стали перлитного класса сваривают тоже нормальным пламенем. Чтобы легирующие элементы ( хром, молибден, кремний) не выгорали, нужно стремиться не перегревать металл. С и замедление охлаждения сварного соединения путем подогрева охлаждающегося шва пламенем горелки позволяют избежать появления горячих трещин. [1]
Низколегированные стали перлитного класса с содержанием углерода не выше 0 35 % и легирующих элементов, составляющих до 3 - 4 %, свариваются в большинстве случаев вполне удовлетворительно. [2]
Низколегированные стали перлитного класса по ГОСТ 5058 - 57 применяются для изготовления различных элементов и изделий трубопроводов, в том числе стали марок 14ХГС и 19Г применяются для трубопроводов, работающих при давлении до 40 ати и температуре-до 350 С. [3]
Низколегированная сталь перлитного класса 38ХЮ в контакте с асбес-тографитовой набивкой имеет низкую коррозионную стойкость. Добавка к набивке 5 % - ной алюминиевой пудры улучшает антикоррозионные свойства стали примерно в 3 раза. [4]
Состав низколегированных сталей перлитного класса стабилизировался н новых путей его принципиального изменения пока не найдено. Значительное улучшение свойств достигнуто совершенствованием технологии производства и применением микролегн-рования. [5]
Состав низколегированных сталей перлитного класса стабилизировался и новых путей его принципиального изменения пока не найдено. Значительное улучшение свойств достигнуто совершенствованием технологии производства и применением микролеги-рования. [6]
Эти стали относятся к низколегированным сталям перлитного класса. [7]
Высокопрочная сталь ЗОХГСНА является низколегированной сталью перлитного класса. [8]
Стали этого класса по своим свойствам являются средними между низколегированными сталями перлитного класса и высоколегированными аустенитно-го. После термической обработки они обладают высокими механическими свойствами. Основной вид термической обработки, придающий оптимальные свойства - закалка или нормализация с последующим высоким отпуском. Иногда используется смягчающая обработка, заключающаяся в отжиге. [9]
Этому виду термообработки подвергаются сварные соединения трубопроводов малого диаметра из низколегированных сталей перлитного класса, выполненные газовой сваркой. [11]
Нормализации чаще всего подвергаются сварные соединения тонкостенных труб малого диаметра из низколегированных сталей перлитного класса, сваренные газовой сваркой, которые в исходном состоянии ( после сварки) имеют крупнозернистую структуру с пониженными пластическими свойствами. [12]
Известно, что изменение свойств феррита приводит к существенному изменению ползучести низколегированных сталей перлитного класса. В этих случаях молибден преимущественно входит в твердый раствор, значительно повышая энергию межатомных связей в решетке а - Fe. Легирование молибденом графитизированных сталей значительно задерживает разупрочнение феррита, и, кроме того, уже при незначительном содержании хрома и молибдена в сталях образуются сложные карбиды, которые, в свою очередь, снижают склонность сталей к ползучести. [13]
Для изготовления деталей стационарных паровых турбин и котельных установок используются углеродистые или низколегированные стали перлитного класса. [14]
Трубопроводы и арматура второго контура с водяным теплоносителем изготовляются из углеродистых или низколегированных сталей перлитного класса, так как параметры среды допускают применение этих сталей. [15]
Страницы: 1 2
www.ngpedia.ru
Сталь перлитного класса - Энциклопедия по машиностроению XXL
Стали перлитного класса характеризуются относительно малым содержанием легирующих элементов, мартенситного — более значительным и, наконец, аустенитного — высоким содержанием легирующих элементов. [c.361]Для легированных сталей перлитного класса (как и для углеродистых) кривая скорости охлаждения на воздухе будет пересекать область перлитного распада и будут получаться структуры — перлит, сорбит, тростит. [c.361]
В настоящем разделе предпринята попытка сформулировать деформационно-силовой критерий зарождения усталостного разрушения применительно к ОЦК металлам, в частности к сталям перлитного класса, основываясь на некоторых физико-меха-нических представлениях о накоплении повреждений при усталости [74, 79, 85, 126]. Разрабатываемый подход позволит ответить на некоторые открытые вопросы в проблеме малоцикловой усталости материалов, в частности, касающиеся влияния на долговечность максимальных напряжений и нестационарности нагружения. [c.136]
Стали перлитного класса содержат сравнительно небольшое количество легирующих элементов (не более 5—6%). После охлаждения на воздухе аустенит в этих сталях распадается при высоких температурах с образованием феррито-цементитной смеси (перлита, сорбита пли тростита). К этому классу принадлежит большинство конструкционных и инструментальных сталей. [c.174]Величина i(9) слабо зависит от содержания легирующих элементов в сталях перлитного класса, но возрастает с увеличением содержания углерода. [c.476]
Для высокохромистых сталей ферритного класса значение п заметно выше, чем у сталей перлитного класса. [c.476]
Для сталей перлитного класса, содержащих небольшое количество легирующих элементов, кривая скорости охлаждения на воздухе пересекает обе ветви С-кривых в области перлитного превращения (рис. 87, а). У сталей мартенситного класса, содержащих большее количество легирующих элементов, вследствие чего С-кривые сдвинуты вправо, а мартенситная точка — ближе к 0° С, кривая скорости охлаждения на воздухе не пересекает С-кривых (рис. 87, б) при температуре 20" С структура стали будет состоять из мартенсита. При значительном содержании легирующих элементов и углерода в стали С-кривые значительно сдвинуты вправо (рис. 87, в), а мартенситная точка находится ниже 0° С. Таким образом, при охлаждении на воздухе сталь сохраняет аустенитную структуру при температуре 20° С (рис. 87, в). [c.120]
Эффективным направлением является использование в различных частях сварных конструкций разнородных материалов, наиболее полно отвечающих требованиям эксплуатации, применение двухслойного проката со специальными свойствами облицовочного слоя и других сочетаний. Примером может служить ротор газовой турбины. По ободу диск ротора подвергается действию высоких температур и относительно небольших усилий, а центральная часть работает в условиях невысоких температур и воздействия больших усилий Подобрать материал, одинаково хорошо работающий в этих условиях, очень трудно. Поэтому целесообразно изготовить сварной ротор центральную часть из высокопрочной стали перлитного класса, а обод диска из жаропрочной аустенитной (рис. 6.21). [c.171]
Для парогенераторов горизонтального типа в качестве материала корпуса широко использовалась известная углеродистая конструкционная сталь 22К, обладающая хорошими технологическими свойствами. Она хорошо поддается ковке, прокатке, штамповке, хорошо сваривается. Опыт эксплуатации парогенераторов показал и ее хорошие эксплуатационные качества. При повышении единичной мощности парогенератора использование этой стали связано с существенным утолщением стенок корпуса. Для снижения массогабаритных характеристик парогенератора может оказаться целесообразным применение более прочных низколегированных сталей перлитного класса. [c.251]
Подогреватели ПНД и ПВД находятся под действием питательной воды котлов и отборного пара паровых турбин, который, конденсируясь, образует дренажи с различным содержанием Игольной кислоты - диоксида углерода. Содержание его в различных частях трубчатой системы ПНД и ПВД может достигать в зависимости от степени конденсации греющего пара нескольких миллиграмм на 1 кг сконденсированного пара. Особенно велика концентрация его в дренажах ПНД и ПВД при недостаточных отсосах неконденсирующихся газов (СО2 и О2) из паровых полостей этих видов оборудования. В этих случаях наблюдается интенсивная коррозия, особенно ПВД, трубчатая система которых изготовлена из стали перлитного класса. Температура среды в зависимости от параметра пара объекта может достигать 300 °С. При этих условиях протекает коррозия с водородной деполяризацией, которая сопровождается наводораживанием металла. Коррозия носит в основном равномерный характер с образованием трещин и появлением хрупких разрущений [12]. [c.79]
Сталь перлитного класса [c.311]
СТАЛЕЙ ПЕРЛИТНОГО КЛАССА [c.174]
На рис. 88 показано, что с увеличением сопротивления срезу износостойкость различных сталей перлитного класса как в хрупкой, так и в вязкой области линейно возрастает. [c.175]
Мартенситный класс. Стали этого класса по своим свойствам являются средними между низколегированными сталями перлитного класса и высоколегированными аустенитно-го. После термической обработки они обладают высокими механическими свойствами. Основной вид термической обработки, придающий оптимальные свойства,— закалка или нормализация с последующим высоким отпуском. Иногда используется смягчающая обработка, заключающаяся в отжиге. Режимы термической обработки сталей этого класса по ГОСТ 10500—63 и ГОСТ 5949—61 приведены в табл. 2. [c.94]
TOB на разупрочнение стали связано с их распределением в феррите и карбидах. Известно, что изменение свойств феррита приводит к существенному изменению ползучести низколегированных сталей перлитного класса. В этих случаях молибден преимущественно входит в твердый раствор, значительно повышая энергию межатомных связей в решетке а — Fe. Легирование молибденом графитизированных сталей значительно задерживает разупрочнение феррита, и, кроме того, уже при незначительном содержании хрома и молибдена в сталях образуются сложные карбиды, которые, в свою очередь, снижают склонность сталей к ползучести. [c.113]
Так, для конструкционных углеродистых и легированных сталей перлитного класса, для которых НВ >. 160, зависимость условного предела текучести oi твердости описывается уравнением Оо,г = 0,367 НВ. Для стали с НВ [c.308]
В сталях перлитного класса ниедение молибдена н небольшом ьоличестие увеличивает температуру рекристаллизации феррита и тем самым повыи ает жаропрочность. Аналогично, но слабее, действует хром (см, рис. 344). [c.465]Стали перлитного класса являются сравнительно малолегироваиными сталями, которые при 0,12%С содержат 0,5 пли 1% Сг и 0,3 или 0.5% Но. Прп- [c.465]
Стали перлитного класса содержат до 0,16% С и молибдена до 0,7%, который увеличивает температуру рекристаплизации феррита и тем са.мым повышает жаропрочность. Аналогично, но слабее действует хром. Присадка ванадия измельчает зерно, а также повышает жаропрочность Обычный режим термической обработки - закалка в масле или нормализация при температурах 950.. 1030 с и отпуск при 720. 750 С (Ас1 = 760 С). Предельная рабочая температура 550.. 580 С. Структура сталей после охлаждения на воздухе перлит и карбиды МзС. Область применения сталей приведена в табл 13. [c.102]
По показателям степени окисления между сталями перлитного и аустенитного класса находится ферритно-мартенситная сталь 12Х11В2МФ (среднее значение и=0,55). Относительно высокое значение п для этой стали в сравнении со сталями перлитного класса также подтверждает большое влияние взаимодействия хрома и хлоридов на процесс коррозии. [c.140]
Исследование кинетики высокотемпературной коррозии сталей под влиянием летучей золы березовского угля Канско-Ачинского бассейна (табл. 4.6), как и под влиянием назаровского угля, проводилось с вырезанными из котельных труб плоскими шлифованными образцами. Образцы из стали 20 испытывались при температурах 450 и 500 °С, сталей перлитного класса 12ХШФ и 12Х2МФСР в интервале температур от 500 до 650 °С, а аустенитной стали 12Х18Н12Т — в промежутке 550—650 °С [134]. Максимальная продолжительность испытаний 4000 ч. [c.158]
Кинетика высокотемпературной коррозии сталей под влиянием летучей золы лейпцигского бурового угля (табл. 4.6) исследовалась в показанной на рис. 3.6 лабораторной установке с вырезанными из котельных труб шлифованными плоскими образцами. Образцы из стали 20 испытывались в интервале температур 450—550 С, сталей перлитного класса 12ХШФ и 12Х2МФСР — в промежутке [c.160]
Сталь ЭИ572Л аустенитного класса способна выдерживать длительную работу в течение 8000—10 000 час. при температуре 600° и напряжении порядка 24— 25 кгс/мм . Сталь ЭИ415Л, относящаяся к жаропрочным сталям перлитного класса, рассчитана на длительную работу при температуре 525° С и напряжении 27— 28 кгс/мм . [c.263]
Фактических данных по коррозионному растрескиванию титановых сплавов в кислотах очень мало. В отличие от нейтральных растворов растрескивание в кислотах, как правило, происходит при заметной и даже высокой интенсивности общей коррозии, поэтому прежде всего необходимо определить возможность использования титановых сплавов из соображений допустимой общей коррозии. Следует, однако, отметить, что даже при больмшй-хкорости коррозии титана не снижается опасность коррозионного растрескивания в отличие от поведения сталей перлитного класса. Имеющиеся данные о коррозионном растрескивании титановых сплавов в кислых растворах относятся главным образом к слабым растворам (и частично — к растворам средней концентрации) соляной и [c.48]
На трубопрокатных заводах ингибитор И-1-В почти полностью заменил ингибитор 4M. Однако и он мало эффективен при травлении труб котельных сталей марок 20,12Х1МФ, 15Х1М1Ф. Для травления этих сталей в настоящее время начинают применять ингибиторы С-5 и ХОСП-10, а для сталей перлитного класса — ингибитор КИ-1. Этот ингибитор эффективен также при травлении труб из углеродистых и низколегированных сталей. Предпочтение следует отдать травлению труб в растворах соляной кислоты. Однако переход на солянокислое травление задерживается из-за отсутствия установок для регенерации отработанных растворов и промывных вод, содержащих соляную кислоту, из-за необходимости замены старого травильного оборудования на новое, обеспечивающее интенсивное травление и выполнение санитарных норм травильных отделений. Для солянокислых сред уже испытаны ингибиторы И-1-В, катапин ВВП, ПКУ, БА-6. [c.71]
Движущей силой этого типа нестабильности является межфаз-ная поверхностная энергия, которая снижается по мере уменьшения величины межфаз ной поверхности. Сфероидизация в сталях перлитного класса — один из наиболее известных примеров такой нестабильности. Грэхем -и Крафт [12] рассмотрели факторы, влияющие на высокотемпературную стабильность эвтектических композитных материалов. Они указали на существование особого кристаллографического соответствия между фазами, которое не меняется при огрублении эвтектической структуры. Они установили также, что, хотя механизм роста фаз состоит в растворении одной из них и в повторном осаждении ее на имеющихся зернах, процесс лимитируется скоростью диффузии, а не скоростью растворения. Для анализа иопользовались уравнения Томсона — Фрейндлиха, определяющие концентрацию элемента у поверхности волокна известного радиуса кривизны. [c.90]
Большинство исследований влияния ввда напряженного состояния на закономерности ползучести выполнены на чистых металлах (алюминий, медь, свинец и др.). Из материалов энергетического машиностроения наиболее часто в качестве объекта исследования использовалась сталь аустенитного класса Х18Н10Т, иногда стали перлитного класса. [c.163]
Одним из эффективных способов использования ресурса жаропрочности сталей перлитного класса может явиться предварительное упрочнение металла труб методом механико-термической обработки (ММТО), основанной на создании стабильной полигональной структуры и упрочнении ферритной составляющей. [c.248]
В различных отраслях машиностроения широко применяют аустенитную сталь 110Г13Л, однако ее износостойкость в условиях ударно-абразивного изнашивания практически не изучена. Механические свойства сталей перлитного и аустенитного класса при отпуске изменяются по-разному. С повышением температуры -отпуска прочностные характеристики (ов, Оо,2 HR ) сталей перлитного класса снижаются, а показатели пластичности (йн, б, i 3) —увеличиваются. [c.167]
Действительно, влияние механических свойств на износостойкость стали перлитного класса в хрупкой и вязкой областях разрушения различно в вязкой области разрушения с увеличением предела прочности износостойкость стали Д7ХФНШ повышается, максимальная износостойкость проявляется на границе хрупко-вязкого перехода. [c.168]
Испытания стали 110Г13Л показывают, что износостойкость ее также существенно зависит от относительных удлинения и сужения в отличие от сталей перлитного класса Д7ХФНШ при всех значениях энергии удара (5 и 10 Дж) с увеличением относительных удлинения [c.168]
В Институте машиноведения нами проведены испытания стали ТС при температуре 550 С в условиях мягкого и жесткого нагружения без выдержек и с выдержками 1 и 5 мин, а также испытания на ползучесть и длительную пластичность. Как показывает обработка экспериментальных данных, и для этой стали использование критериального уравнения в форме (1.2.8), (1.2.9) дает вполне удовлетворительные результаты (рис. 1.2.5, точки 1). Подобные данные получены в работе [23] на аналогичной ТС стали перлитного класса 15Х1М1Ф при 565 С и длительностях выдержки 5 и 50 мин (рис. 1.2.5, точки 2). [c.32]
Применяемая в настоящее время для изготовления глубиннонасосных штанг легированная сталь перлитного класса 20Н2М не отвечает требованиям нефтедобывающей промышленности (большое число обрывов колонн, приводящих к длительным остановкам скважин). Это связано с тем, что в стали при термообработке возникают закалочные напряжения и деформации (закалка в воде), причем, как правило, растягивающие поверхностные остаточные напряжения,/что существенно снижает коррозионно-усталостную стойкость штанг. Кроме того, значительное содержание никеля в стали повышает ее стоимость. [c.249]
Кроме классов сталей, предусмотренных ГОСТ 5632—72, существуют еще средне- и сложнолегированные теплостойкие стали перлитного класса. В табл. 9 приведены механические свойства и режимы термической обработки сталей этого класса по ГОСТ 10500—63. [c.108]
Экранные трубы и пароперегреватели изготовляют преимущественно из стали перлитного класса марки 12Х1МФ, легированной хромом, молибденом и ванадием. При изготовлении элементов котла, работающих при повышенных температурах (примерно 500 °С), применяют аустенитную сталь 08Х18Н12Т. [c.178]
mash-xxl.info
Легированная сталь - перлитный класс
Легированная сталь - перлитный класс
Cтраница 1
Легированные стали перлитного класса обладают повышенными, по сравнению с углеродистыми сталями, механическими свойствами. Они закаливаются, при этом на механические свойства после закалки влияет содержание в них углерода и легирующих примесей, а также температура отпуска после закалки: с повышением температуры отпуска предел прочности понижается, а пластичность возрастает; с понижением температуры отпуска предел прочности возрастает, а пластичность падает. [1]
Для легированных сталей перлитного класса ( как и для углеродистых) кривая скорости охлаждения на воздухе будет пересекать область перлитного распада и стали будут получать структуры - перлит, сорбит, троостит. [2]
Для легированных сталей перлитного класса ( как и для углеродистых) кривая скорости охлаждения на воздухе будет пересекать область перлитного распада и будут получаться структуры - перлит, сорбит, тростит. [4]
В легированных сталях перлитного класса глубина закалки значительно больше. [6]
Отливки из легированных сталей перлитного класса подвергаются, как правило, следующим видам термической обработки: гомогенизирующему отжигу, нормализации, закалке и отпуску. [7]
Отливки из легированных сталей перлитного класса подвергаются гомогенизирующему отжигу ( массивные отливки), нормализации, закалке и высокому отпуску. Отливки из легированных сталей аустенитного класса ( например, отливки из высокомарганцовой стали) подвергаются закалке. [8]
Для различных групп легированной стали перлитного класса существуют предельные температуры, выше которых применение данных материалов в условиях длительной ползучести не может быть рекомендовано. [9]
При электротермической обработке легированных сталей перлитного класса ( типа 15ХМ) требуемые свойства обеспечиваются при выдержке в течение до 3 мин. [10]
Турбина изготовлена полностью из легированных сталей перлитного класса. Ротор высокого давления - цельнокованый. Семь дисков ротора среднего давления откованы заодно с валом, остальные четыре диска насадные. Ротор низкого давления состоит из вала л восьми насадных дисков. [11]
Эти соотношения сравнительно хорошо характеризуют легированные стали перлитного класса. В меньшей степени они характерны для высоколегированных аустенитных сталей, не обладающих большой деформационной способностью при высоких температурах. [12]
Обшивка испарительной части изготовлена из легированной стали перлитного класса, допускающей температуру до 600 С. Внутренняя обшивка в области пароперегревателя состоит из двух поясов. [14]
Однако отмеченное явление при сварке малоуглеродистых и легированных сталей перлитного класса не приводит к сколько-нибудь существенным отрицательным последствиям. [15]
Страницы: 1 2 3
www.ngpedia.ru