- Подвергаться обработке по данной технологии могут даже детали, отличающиеся высокой сложностью геометрической формы. В частности, такую технологию активно используют для обработки труб.
- Поврежденные в результате механического воздействия участки цинкового покрытия могут самовосстанавливаться, причем происходить это может без постороннего вмешательства.
- По сравнению с другими способами оцинковки, метод горячего цинкования позволяет сформировать покрытие, устойчивость которого при взаимодействии с жидкими средами выше в 6 раз. Именно по этой причине такую технологию и применяют для обработки труб и различных емкостей.
- Горячая оцинковка позволяет эффективно устранять многие дефекты обрабатываемой поверхности, такие как раковины, поры и др.
- Эксплуатация труб и других метизов, которые покрыты цинком по данной технологии, требует минимальных финансовых затрат. Их поверхности, в частности, не требуют регулярной окраски, так как уже надежно защищены от воздействия негативных факторов внешней среды. Это очень актуально для труб, которые эксплуатируются в труднодоступных местах (в стенах, под землей и т.д.).
- Обрабатываемую поверхность тщательно подготавливают к процедуре.
- Изделие погружают в емкость с расплавленным цинком, в результате чего оно буквально обволакивается данным металлом.
- механической обработки;
- обезжиривания;
- промывки;
- травления;
- промывки после травления;
- флюсования;
- просушки.
- Обязательно наличие мощной вытяжки, которая удалит из воздуха пары, интенсивно образующиеся при цинковании.
- Оборудование для горячего цинкования должно обеспечивать строгое соблюдение скорости погружения изделия в расплав, а также времени его выдержки в нем.
- Обработанная деталь после извлечения из емкости с цинком должна качественно охлаждаться.
- Погружение изделия в емкость с расплавленным цинком.
- Выдержка, время которой может составлять от 4 до 10 минут.
- Извлечение обрабатываемой детали из емкости с расплавом, от скорости выполнения которого во многом зависит толщина формируемого покрытия.
- Охлаждение, которое может выполняться принудительно или протекать естественным путем.
- Обработка может производится к деталям любой формы и сложности, так как подразумевает опускание изделия целиком в ванны с цинком.
- При незначительных механических повреждениях, покрытие имеет свойства к самовосстановлению, при некоторых случаях без вмешательства человека.
- Горячее цинкование осуществляется при обработке емкостей и труб, так как стойкость к коррозии и другим воздействиям повышается более, чем в 5 раз.
- В процесс обработки забиваются все мелкие недостатки изделий.
- Эксплуатация не требует дальнейшего ухода за поверхностями, так как защищена слоем цинка.
- Обезжиривание происходит при средней температуре +70 ⁰С, происходит для равномерно расположенного слоя цинка. Если не удалится масляное загрязнение, оцинкованный кусок может обвалиться.
- После происходит промывание, в процессе которого удаляются средства, используемые при обезжиривании.
- Соляной кислотой производится травление, слой окалины удаляется с поверхности металла, под воздействие попадает и коррозия.
- После каждого воздействия определенного средства необходимо осуществлять промывку детали.
- Флюсование обеспечивает хорошее прилегании цинка к поверхности в последующем, противостоит окислению в процессе производства.
- Сушка детали производится в специально отведенной для этого печи.
- Сушильная и цинковальная печи.
- Теплообменник.
- Цинковальные ванны, их количество определяется разновидностью производимых частей.
- Ванна для охлаждения.
- Грейфер, предназначенный для удаления гарт цинка.
- На этапе погружения детали, при повышении температуры, разрушается флюсовая пленка, которая служит для соединения цинка с металлом. Скорость процесса погружения подбирается оптимальной, нельзя допустить полное разрушение пленки, но и остаточный толстый слой.
- Продолжительность операции подбирается от сложности конструкции, время цинкования определено не более 10 минутами.
- Регулируется скорость вынимания для контроля остаточного слоя горячего цинка на металле.
- Требования к металлу, при данном разделе описаны категории изделий из стали, которые можно обрабатывать.
- Внешний вид и качество покрытия, а также толщина готового изделия определены согласно ГОСТу.
- Методы контроля качества определяются способами определения качества готовой продукции.
- Возможность обработки изделий любых форм и конфигураций.
- Способность самостоятельного восстановления участка металлоконструкции при механических повреждениях.
- Высокая степень устойчивости перед жидкостями.
- Дефекты основы тщательно скрываются под слоем цинка.
- Оборудование для горячего цинкования простое и понятное в эксплуатации.
- Значительная экономия – изделия не требуют регулярной обработки и окрашивания.
- Навешивание изделий на траверсу – подвешиваются с помощью крюков и проволоки. Помимо крюков, применяется также прокат сортовой стальной горячекатаный круглый (ГОСТ 2590-2006).
- Обезжиривание – поверхность тщательно очищается от масляной пленки и различного рода загрязнений.
- Промывка – выполняется с целью удаления остатков травильных растворов с поверхности.
- Флюсование хлористым аммонием – нанесение водного химического состава, необходимого для возможности получения желаемого покрытия. В качестве флюса используются хлориды аммония и цинка.
- Сушка – после помещения в сушильную камеру, высушивается флюс и производится прогрев металла до 120°С.
- Цинкование – конструкция окунается в расплавленный цинк, избыток которого стекает обратно в ванну. Применяется расплав цинка марки ЦВ или ЦВО (ГОСТ 3640-94).
- Охлаждение – при горячем цинковании температура вытащенной из расплава конструкции 450°С. Охлаждается до температуры окружающей среды на свежем воздухе или с использованием ванны с чистой водой.
- Снятие металлоизделий с траверсы – готовый продукт снимается с траверсы, при необходимости запаковывается и отвозится на склад.
- Цинковое покрытие увеличивает срок эксплуатации изделий в среднем на 30 лет.
- После обработки методом горячего цинкования изделия не требуют ухода и текущего ремонта.
- Цинковое покрытие имеет возможность самовосстановления в случае механического повреждения.
- Сохраняется высокая теплопроводность изделий, так как цинк отлично проводит тепло.
- Возможность покрытия внутренностей изделия сможет обеспечить только горячее цинкование. ГОСТ предъявляет свои требования к оцинковке изделий.
- Благодаря высокому качеству подготовки и самого процесса оцинковки можно гарантировать высокое качество полученных изделий.
- Оборудование для горячего цинкования дает возможность обрабатывать далеко не все детали. Все зависит от габаритов изделий, ведь они просто могут не поместиться в ванну.
- Большой расход цинкового расплава.
- Некоторые изделия могут иметь неравномерный слой цинкового покрытия.
- Обезжиривание поверхности изделия для удаления жировых и масляных пятен. Операция проводится при температуре 80-80 градусов.
- Промывка изделия.
- Травление. Деталь опускают в ванну с соляной кислотой для удаления с ее поверхности различных оксидов (ржавчины, потемнения, окалины), которые образуются в процессе хранения изделия.
- Промывка в нескольких ваннах с целью удаления остатков кислоты.
- Флюсование. Это образование защитной пленки флюса, которая препятствует дальнейшему окислению металла, а также улучшает адгезию поверхности с цинковым расплавом. Деталь обрабатывается раствором флюса при температуре около 60 градусов.
- Сушка изделия при температуре 100 градусов. Удаляется влага с поверхности изделия, которая способна вызвать разбрызгивание цинка при погружении в него детали.
- Цинкование. Деталь погружается в расплав цинка с температурой 440-460 градусов. В ванне с цинком изделие находится 3-10 минут.
К сведению: толщина будущего покрытия зависит не только от марки стали, но и от времени извлечения детали из ванны. Скорость кристаллизации цинка для различных деталей регулируется индивидуально.
- Охлаждение готового изделия.
- Промышленное и частное строительство. Любые металлические конструкции и изделия подвергаются подобной обработке с целью продления своего ресурса и защиты от всевозможных воздействий. Чего стоят только водопроводные трубы, металлические сетки для ограждений, оконные отливы, профнастил и масса других изделий.
- Защита металлических емкостей, труб, баков, посуда и прочей хозяйственной утвари.
- Компоненты изделий, эксплуатирующихся под открытым небом, также нуждаются в подобной защите. Это вышки, опоры мостов и ЛЭП, радиомачты, ретрансляторы и т. д.
- Дорожное строительство. Дренажные трубы, ограждения, мостовые конструкции, перила и прочие элементы, подверженные влиянию влаги.
- Закалка инструментальной стали
- Сталь горячекатаная круглая
- Оцинкованной стали гост
- Как правильно закалить сталь в домашних условиях
- Сталь 20 плотность кг м3
- Как отпустить сталь
- Фото стальной уголок
- Вес нержавеющей стали
- Сталь 12х18н10т температура плавления
- Угловая сталь 50х50
- Сталь с полимерным покрытием листовая
Гальваническое цинкование металла: технология, оборудование. Сталь горячего цинкования
Горячее цинкование металлоконструкций: технология, ГОСТ
Горячее цинкование – это метод покрытия поверхности металлического изделия слоем цинка, уступающий по своей популярности только гальванической технологии оцинковки. Между тем по стоимости выполнения, а также по долговечности формируемых цинковых покрытий данный способ превосходит электрохимическое цинкование.
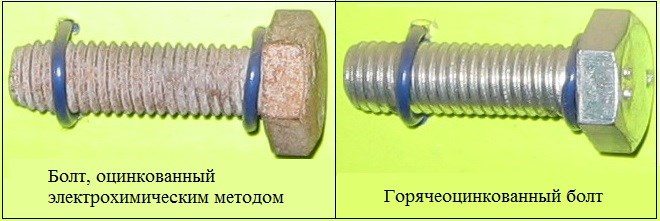
Результаты испытаний болтов с различной оцинковкой в растворе соляной кислоты
Ознакомиться с требованиями ГОСТ к горячим цинковым покрытиям можно, скачав документ в формате pdf по ссылке ниже. ГОСТ 9.307-89 Единая система защиты от коррозии и старения. Покрытия цинковые горячие. Общие требования и методы контроляСкачатьЗачем металлические изделия подвергают цинкованию
Цинкование предполагает, что на поверхность металлического изделия наносится слой цинка, толщина которого может находиться в интервале 40–65 мкм. За счет такого покрытия обеспечивается не только барьерная, но и электрохимическая защита металла от коррозии. Оцинкование, которое можно выполнять по разным технологиям, используется преимущественно по отношению к стали.
Горячее цинкование металла, если сравнивать его с другими технологиями, отличается оптимальным сочетанием доступной стоимости технологического процесса с высокими защитными свойствами получаемого цинкового слоя. Нанесенное методом горячего цинкования покрытие даже при эксплуатации изделия в самых неблагоприятных условиях способно прослужить не менее 65–70 лет, полностью сохранив свои защитные свойства.
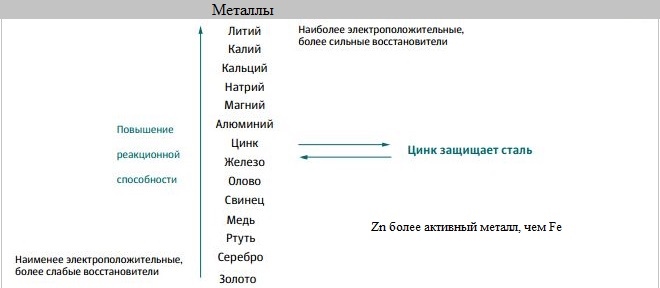
Положение цинка в электрохимическом ряду металлов
Преимущества метода
Горячее цинкование металлоконструкций при сравнении с другими технологиями имеет ряд весомых преимуществ.
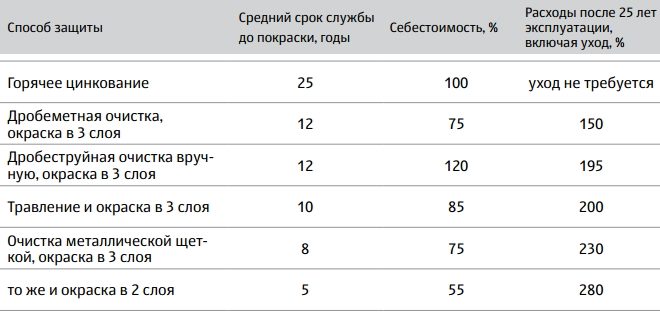
Сравнение стоимости и работоспособности горячеоцинкованной стали с другими методами защиты
Как выполняется горячее цинкование
Выделяют два этапа горячего цинкования:
Все нюансы выполнения такой технологической операции регламентирует ГОСТ 9.307-89.
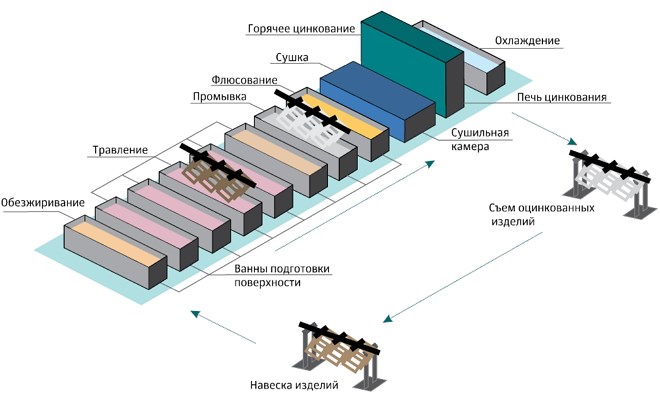
Технологический цикл цинкования
Технология горячего цинкования требует тщательного подхода к выполнению всех ее этапов. Чтобы понять их суть и назначение, каждый из них стоит рассмотреть подробнее.
Подготовка металлического изделия к процедуре
ГОСТ указывает, что поверхность, которую необходимо подвергнуть горячему цинкованию, должна быть тщательно подготовлена. Такая подготовка состоит из нескольких процедур:
При помощи механической обработки с поверхности удаляются загрязнения, продукты окисления, следы ржавчины, а также шлаковые включения. ГОСТ также предписывает, что острые углы и кромки, имеющиеся на изделии, должны быть скруглены, что также решается на этапе механической обработки. Для выполнения механической обработки в производственных условиях используются пескоструйные установки.
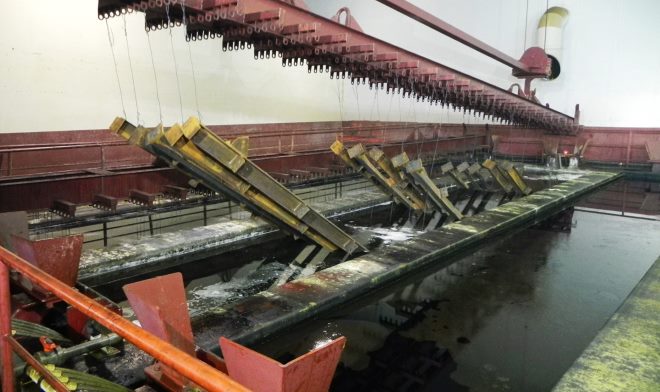
Обезжиривание металлоизделий в растворе ортофосфорной кислоты
Обезжиривание, которое выполняется при температуре около 75°, необходимо выполнять перед горячим цинкованием для того, чтобы улучшить адгезию формируемого защитного слоя с цинкуемым изделием. Присутствие на обрабатываемой поверхности жировых и масляных пятен может привести к тому, что на таких участках цинковое покрытие будет иметь неравномерную толщину или даже отслаиваться.
Выполняют обезжиривание при помощи специальных химических реагентов, список которых приводит соответствующий ГОСТ. Их остатки впоследствии должны быть полностью удалены с поверхности изделия, для чего его подвергают промывке.
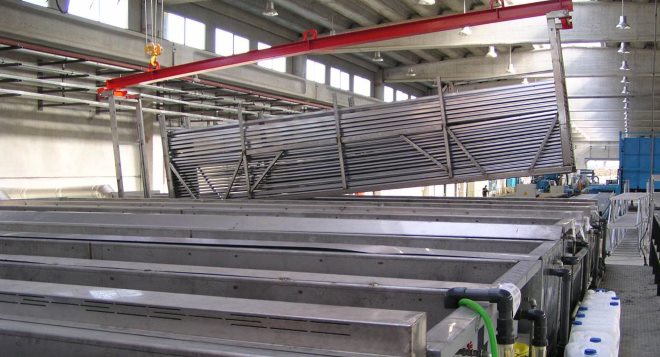
Промывочные емкости для длинномерных изделий
ГОСТ также указывает, что на трубах или других изделиях, подвергаемых горячему цинкованию, не должно быть окисленных участков, а также старого цинкового покрытия, если оно наносилось ранее. Для того чтобы выполнить эти требования, обрабатываемую поверхность подвергают травлению. С этой целью обычно используется раствор соляной кислоты. Выполняют такую процедуру при комнатной температуре (22–24°), а концентрацию раствора кислоты выбирают в зависимости от того, насколько сильно поверхность загрязнена окислами и следами коррозии.
Как правило, для выполнения травления используют растворы, в которых содержится 140–200 граммов кислоты на 1 литр. При выполнении травления раствор кислоты может сильно повредить обрабатываемую поверхность. Чтобы такого не происходило, а также чтобы минимизировать выделение водорода из травильного раствора, в него вводят специальные вещества, которые называются ингибиторами. Как и после обезжиривания, после травления изделие необходимо тщательно промыть, чтобы удалить остатки использованных химических веществ.

Подготовленные к оцинковке изделия
Флюсование перед горячим цинкованием, технология которого предусматривает тщательную подготовку обрабатываемой детали, позволяет решить сразу две важных задачи: предотвратить процесс окисления и улучшить адгезию наносимого покрытия с основным металлом. В процессе флюсования, выполняемого при температуре 60°, на обрабатываемую поверхность наносится тонкий слой флюса, содержащегося в специальном растворе. В качестве флюса, как правило, используются хлориды аммония и цинка. Их смешивают с водой в соотношении 500 граммов на литр, чтобы приготовить раствор для флюсования. При выполнении флюсования очень важно следить за такими параметрами используемого раствора, как содержание железа, плотность и кислотность. Если концентрация железа в растворе превышена, в него вводят перекись водорода, которая способствует образованию солей железа, выпадающих в осадок.
Любой цех горячего цинкования в обязательном порядке должен быть оснащен термическими печами, в которых обрабатываемое изделие просушивают после выполнения флюсования. Такая термическая обработка позволяет не только удалить остатки жидкости, которая ухудшает качество готового цинкового покрытия, но и нагреть деталь до температуры 100°, что дает возможность снизить затраты на осуществление основной технологической операции.
Как осуществляется технологический процесс
Сам процесс нанесения защитного цинкового слоя, для чего может использоваться линия горячего цинкования или более простое оборудование, заключается в погружении детали в емкость с расплавленным цинком. Температура, при которой цинковый расплав находится в таких емкостях, выбирается в зависимости от ряда факторов, к числу которых относятся и геометрические параметры обрабатываемого изделия. В среднем значение такой температуры находится в интервале 420–455°.
Если в качестве оборудования применяется не агрегат для непрерывного горячего цинкования (АНГЦ), а более простые технические устройства, необходимо обеспечить выполнение следующих условий на производственном участке.
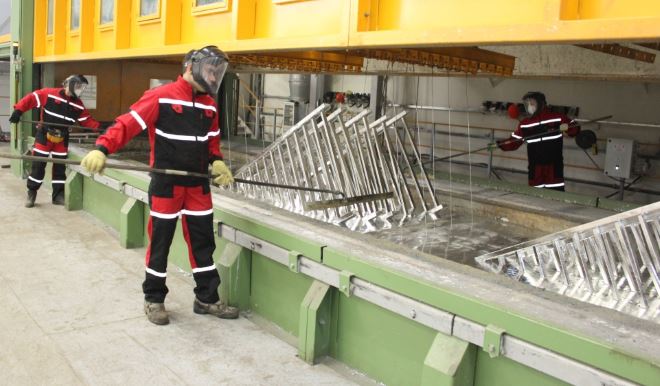
Ванна для цинкования может достигать в длину 14 и более метров
Горячее цинкование метизов выполняется в следующей последовательности:
Данная технология, преимущества использования которой были отмечены выше, отличается и относительно невысокой сложностью. Для осуществления такой процедуры нет необходимости готовить сложные электролитические растворы, чем на производственных предприятиях занимается гальваник.
Оценка статьи:

Поделиться с друзьями:
met-all.org
технология и метод по ГОСТ
Изделия, изготавливаемые из стали, подвергаются агрессивным воздействиям окружающей среды. Образование коррозии невозможно предупредить без обработки после производства изделия. Наиболее действенным, долговечным способом является горячее цинкование. Популярность появилась после проверки временем обработанных изделий и экономичности производства.

Горячее цинкование стали
Для каких целей металлоконструкции подвергают оцинковке
Процесс подразумевает наложение тонкого слоя цинка, перед нанесением поверхность обрабатывается механическими и химическими способами. Покрытие обеспечивает защиту не только барьерную, но и электрохимическую реакцию. Горячее цинкование используется в большинстве случаев при работе с металлами, так как оно наиболее подвержено градирующим процессам. Способ горячего цинкования является наиболее приемлемым, так как имеет сбалансированную стоимость процесса, высокий результат.

Способ горячего цинкования на производстве
Основное назначение цинкования – повышение прочности металлоконструкции. Оцинкованную деталь не нужно окрашивать для защиты от коррозии, в совокупности процесс приближен к стоимости окраски, но имеет больше преимуществ.
Происхождение метода
В конце 17 века проводились первые опыты по погружению металлической детали в горячий цинк. Французский химик отметил появление защитного слоя после процедуры – оцинковка металла. В 1836 году во Франции отдается патент на применение горячего цинка с целью использования для антикоррозийных свойств металлоконструкций. Метод горячего цинкования был налажен уже через 10 лет после открытого патента, а широкое распространение получил в середине прошлого века.

Применение оцинкованных изделий
Изделия, обработанные цинком возможно использовать при любых условиях, кроме щелочной среды. Изготовление представлено некоторыми сложностями во время производства, однако они перевешиваются плюсами.
Достоинства и недостатки метода
Основными преимуществами метода является стоимость при долгосрочном использовании. Уход после процедуры горячего цинкования за деталью не требуется при отсутствии механических воздействий. Цинкование металлоконструкций имеет ряд преимуществ:

Оцинкованные листы
Недостатки существуют абсолютно при каждой работе, обработка цинковым слоем происходит неравномерно. Повышенный расход материала при выполнении работ, обусловленность формой ванны, детали большего размера обработать не получится. Изделия, обработанные слоем цинка получаются габаритнее, обработанные изделия могут доставить трудностей при монтаже или сварке.
Технология горячего цинкования
Обработка происходит в соответствие с ГОСТ, выполняется в множество этапов, которые требуют подготовки. Технология горячего цинкования применяется только после соблюдения всех условий по производству. Перед работами обезжириваются детали, происходит удаление масла, других составов. Горячая оцинковка требует нескольких ванн и печей для сушки, печей для процесса, а также зоны, в которой детали подвергаются охлаждению.

Технология горячего цинкования
Общими правилами установлена, что процесс разбит на этапы. Подготовка поверхности происходит в несколько раз, осуществляются различные работы. Цинкование, процесс состоящий их трёх фаз, которые тщательно соблюдаются. После завершения основных процессов происходит аспирация и транспортировка, действия происходят автоматически.
Подготовка поверхности
Особо важный этап – подготовка, включает множество подтипов:
Наиболее важным процессом отмечается флюсование. Флюс, благодаря химическим свойствам, окончательно удаляет серную кислоту, влагу. Горячее цинкование использует своеобразный флюсовой слой.
Оборудование
Процесс горячего цинкование требует большого помещения и видов оборудования. Основные станки и приборы для обработки:

Завод горячего цинкования
Перечисленное оборудование не включает в себя автоматизированную линию для транспортировки детали, подготовке к процессу и очистных сооружений, которые обязательно понадобятся для массового производства.
Цинкование
Определенная технология цинкования и ее соблюдение позволяют добиться прочности, надежности детали. Для получения результата необходимо следовать последовательности, которая описана в технологии горячего цинкования металлоконструкций:

Сушка оцинкованных изделий
Качественная сталь, соблюдение температурного режима обработки (450 ⁰С), степень охлаждения полностью зависят на готовый результат. Сушка изделия зачастую происходит на открытом воздухе.
Контроль качества покрытий по ГОСТ 9-307
Важные моменты при процедуре описаны контролем Госстандарта. Требований к обработке существует множество, основные из них:

Процесс горячего цинкования труб
Контроль и его методы подразумевают проверку готовой продукции путем нанесения механических повреждений или специальных меток. Горячее цинкование металлоконструкций определяется также температурным воздействием, изделие нагревается до 200 ⁰С, визуально проверяется на наличие повреждений либо отслаивания металла.
Если вы нашли ошибку, пожалуйста, выделите фрагмент текста и нажмите Ctrl+Enter.
stankiexpert.ru
О методе горячего цинкования металла
Горячее цинкование, как указано ранее, является процессом погружения сварных изделий из стали в ванну, содержащую расплавленный цинк. Этот процесс по своей сути простой, который обеспечивает явное преимущество по сравнению с другими методами защиты от коррозии. В то время как сталь металлургически вступает в реакцию с расплавленным цинком, образуется плотно скрепленный сплав, которорый обеспечивает превосходную защиту от коррозии стали.
Информация в данном разделе по прочности, долговечности, стоимости и устойчивости применима только к горячему цинкованию. Важно понимать, что не все цинковые покрытия созданы одинаково, таким образом, применение любой из представленной информации о горячем цинковании в других цинковых покрытиях не является точным и не рекомендуется к применению.
Для того, чтобы понять метод горячего цинкования металла и его эволюцию, имеет смысл начать с самого истока, с 79 года нашей эры.
История метода горячего цинкования
79 лет до н.э
Первые записи об использовании цинка в строительстве, которые можно было бы считать зарождением цинкования.
1742 год
Первая зарегистрированная история цинкования, когда Поль Жак Малуин, французский химик, представил в Королевской академии наук несколько экспериментов связанных с покрытием железа, расплавленным цинком.
1772 год
Луиджи Гальвани, тезка гальванизации, исследовал электрохимический процесс, который происходит между металлами во время экспериментов по электрофизиологии.
1801 год
Алессандро Вольта способствовал исследованиям по гальванизации, когда он обнаружил электрический потенциал между двумя металлами, создавая первый в мире химический источник тока.
1829 год
Майкл Фарадей обнаружил жертвенное действие цинка в ходе эксперимента с участием цинка и соленой воды.
1837 год
Французский инженер Станисла́с Соре́ль получил патент на процесс цинкования.
1850 год
Британская промышленность стала потреблять 10000 тонн цинка в год для производства оцинкованной стали.
1870 год
Соединенные Штаты были немного позади и в 1870 г. был открыт первый завод цинкования. В то время, сталь вручную погружали в ванну с цинком.
2000 год
Достижения в области металлургии и технологии изготовления ванн, повысили эффективность процесса и устойчивости покрытия.
Cегодня
На сегодняшний день более 10 млн. тонн цинка ежегодно потребляется в мире. Для горячей оцинковки стали потребляется – более 2 млн. тонн для обработки методом окунания и более 5 млн.тонн для непрерывного процесса оцинкования. Цинкование встречается почти в каждой крупной отрасли, где используется сталь. Коммунальная, химическая, целлюлозно-бумажная, автомобильная и транспортная промышленность, только некоторые из областей, которые исторически широко использовали цинкование для защиты от коррозии. Они продолжают делать это сегодня. Метод горячего цинкования имеет доказанную и возрастающую историю успеха в бесчисленных применениях по всему миру.
gorjachee-cinkovanie.ru
Горячее цинкование металлоконструкций: особенности технологии
Горячее цинкование металлоконструкций благодаря особенностям технологии позволяет выполнять качественную защиту изделий от разрушительных коррозийных процессов. Полученный слой обладает отменными показателями прочности к механическим воздействиям. Представленный метод защиты является самым надежным и экономичным.
Что такое горячее цинкование металла и чем оно отличается от холодного? Перед использованием важно изучить особенности технологического процесса, а также ознакомиться с достоинствами и недостатками метода.
Для чего металлоконструкции подвергают оцинковке?
Метод предполагает покрытие слоем цинка металлического изделия, с толщиной в пределах 40-65 мкм. Такой тип покрытия обеспечивает высокий барьерный и электрохимический уровень защиты от коррозийных процессов.
Услуги горячего цинкования в Минске весьма доступны, цена приемлема, при этом на выходе получается прочный цинковый слой с высокими защитными показателями. Полученная поверхность изделия сохраняет свои свойства на протяжении 60-70 лет, независимо от условий эксплуатации. Специалисты, приходящее на предлагаемые вакансии, проходят специальное обучение, что помогает повысить качество и прочность продукции.
Преимущества данного метода
Обработанные представленным методом изделия применяются фактически в любых условиях, исключение составляют сильная кислотная и щелочная среда.
Основные преимущества:
Для наилучшей степени покрытия изделий, на производствах используется низкоуглеродистая сталь ГОСТ 380-94, 1050-88, 27772-88.
Единственным недостатком метода отмечают ограниченность размеров деталей, которые зависят от параметров емкости с расплавленным цинком. На предприятиях крупногабаритного производства изделия обрабатывают с использованием агрегатов непрерывной оцинковки, цена на такой процесс соответственно выше.
Технологический процесс
Метод горячего цинкования заключается в опускании изделий в ванну с цинком, температурный показатель которого достигает 450°С. В итоге на металлической поверхности образуется прочное покрытие из 4-х слойного железо-цинкового сплава, которое отличается исключительными антикоррозийными возможностями. Наружная плоскость обработанного изделия на 99,9% состоит из цинка.
Для получения качественных металлических покрытий, соответствующих необходимым стандартам, важно тщательно подготовить поверхность, которая будет подвергаться оцинковке. Современные заводы цинкования горячего используют ряд химических подготовок, которые состоят из ванн для горячего цинкования, заполненных определенными составляющими.
Технология горячего цинкования, в том числе и горячее цинкование труб, состоит из следующих этапов:
Представленная технология отличается относительно невысокой сложностью. Процедура не требует подготовки сложных электротехнических растворов, которые на производстве готовят гальваники. Гальваническая линия горячего цинкования состоит из полного комплекса обработки, начиная с подготовки и заканчивая закреплением.
Таким же образом получаются лотки горячего цинкования, которые используются преимущественно для построения кабельных трасс с целью прокладки проводов и кабелей.
При использовании металлоконструкций для заземления, это лучший вариант защиты изделий от коррозии. Стальная полоса в качестве заземлителя может быть различных размеров, изготавливается согласно ГОСТу, что гарантирует высокое качество продукции и исключает погрешности в размерах. Заземляющая полоса не подвергается возникновению ржавчины и способна прослужить долгий срок.
Железные листы предварительно подвергаются протравливанию с применением серной и соляной кислоты (ГОСТ 857-95). После того как лист протравлен в первой ванне с кислотным раствором, его погружают в чан с чистой водой.
По завершении обмывки лист погружается в третью ванну, с таким же кислотным раствором, что и в первой. Затем изделие поступает в сушильную камеру и просушивается. Перед погрузкой в аппарат на поверхность листов наносят раствор из нашатыря, хлористого цинка и соляной кислоты. По завершении процедуры, изделие отправляется в чан с расплавленным цинком.
Обязательно определяется глубина обезуглероженного слоя. Измерения проводятся с использованием окуляра-микрометра. Глубина проверяется в готовой продукции и на промежуточных этапах. Полученные данные позволяют определить уровень обезуглероживание на каждой стадии и подобрать условия дальнейшей обработки, чтобы выполнить требования потребителя касательно приемлемой глубины обезуглероживания.
Видео: этапы горячего цинкования.
Процесс холодной оцинковки
Холодное цинкование позволяет получить прочный слой на металлической поверхности, обладающий высокими эксплуатационными характеристиками. Стоит отметить тот факт, что в данном случае не требуется применение специализированного оборудования, что позволяет осуществить цинкование своими руками в домашних условиях и значительно сэкономить в цене.
Принцип методики заключается в нанесении специальной цинкосодержащей смеси на обрабатываемое изделие. Полученный защитный слой содержит 89-93% цинка. Отличие от горячей технологии заключается в невозможности использования холодного метода для изделий, предназначенных для заземления.
Плюсы и минусы очевидны, к холодному оцинкованию прибегают в случаях, когда обеспечение защиты от коррозийных процессов невозможно по другим технологиям.
Услуги по обработке стали горячим цинкованием, как правило, заказываются совместно с работами по производству деталей. Это помогает значительно сэкономить в цене. Занятие вакансии технолога требует специального образования и дополнительной подготовки. Работы выполняются на современном оборудовании, с применением новейших технологий, что обеспечивает высокое качество и долговечность продукции.
metmastanki.ru
Гальваническое цинкование металла: технология, оборудование
Гальваническое цинкование – эффективный и недорогой, а потому распространенный способ защиты черных металлов от коррозии. Чаще всего его используют при производстве метизов и крепежных изделий, а также стальной сетки.
Способы нанесения цинкового покрытия
Антикоррозионное цинкование выполняется различными способами, а срок службы покрытия зависит от толщины защитного слоя.
Способ нанесения покрытия зависит от его необходимых свойств, размеров изделия, условий его дальнейшей эксплуатации.
Самый простой и технологичный, но недостаточно обеспечивающий стойкость к механическим воздействиям защитного слоя, – это холодное цинкование с помощью грунтов, в которых в большом количестве содержится высокодисперсный цинковый порошок.
По объему цинковальных производств второе место занимает горячее цинкование. Покрытие, получаемое таким способом, качественное и долговечное, но экологически небезопасное, так как используется расплав цинка, да еще на поддержание его температуры немногим меньше 500 °С необходимо большое количество электроэнергии, химические методы подготовки поверхности.
Очень похож на горячее цинкование более технологичный, но менее производительный метод термодиффузионного нанесения защитного слоя. Он используется, когда задаются высокие требования к толщине и внешнему виду покрытия.
Еще один способ цинкования – это газо-термическое напыление, которое используется для защиты крупногабаритных изделий и конструкций, которые в ванну просто невозможно поместить.
Гальваническое цинкование лишено многих недостатков других способов нанесения покрытия и имеет свои положительные стороны.
Преимущества гальванического цинкования
Способ нанесения цинкового покрытия путем электролиза наиболее распространен.
Основным достоинством, из-за которого применяется именно гальваническое цинкование металла, является высокая степень защищенности поверхности материала от коррозии. Тонкий слой цинка увеличивает срок службы изделий в несколько раз, а значит, и снижает затраты на их техническое обслуживание и замену.
Покрытие получается ровным, без потеков и капель, сохраняется и форма, и размер изделия. Нанести его можно на предметы любой, даже самой сложной формы.
Гладкие и блестящие декоративные покрытия не требуют в большинстве случаев дополнительной обработки.
Кроме того, сам процесс нанесения цинкового покрытия требует незначительных расходов, а гальванические агрегаты обладают высокой производительностью.
Недостатки гальванического цинкования
Способ нанесения защитного покрытия электролизом не лишен недостатков.
Основной недостаток – низкая адгезия цинка с металлом, из-за которой поверхность изделия необходимо тщательно зачищать.
Минусом также является образование в процессе нанесения покрытия ядовитых отходов, требующих серьезной очистки.
Несоблюдение режимов может привести к наполнению водородом основного металла, что приводит к хрупкости самого изделия и к нарушению качества покрытия.
Принцип действия
Гальваническое цинкование основано на принципе защитного действия, который определяется разностью электрохимических потенциалов цинка и железа. Поскольку цинк имеет меньший электрохимический потенциал, покрытие из него является протекторной защитой для черных металлов. То есть во влажной среде электрохимической коррозии подвергается именно он.
При окислении железа образуются оксиды, имеющие больший объем, чем первоначальный металл. Оксидная пленка становится рыхлой и пропускает к еще не окисленному металлу кислород. А на цинке при окислении пленка образуется тонкая и плотная, она не пропускает кислород вглубь металла, защищая не только покрытие, но и основной металл под ним.
Виды гальванического цинкования
Цинкование гальваническое – технология, представляющая собой электролиз, т. е. электрохимические окислительно-восстановительные процессы в электролите под действием постоянного электрического тока.
По составу электролита цинкование делится на три вида: кислотное, цианидное и щелочное.
Чаще всего используется метод нанесения цинкового покрытия в слабокислых электролитах, особенно для чугунных и стальных деталей сложной конфигурации. Изделия из углеродистых и легированных сталей при этом виде цинкования меньше подвергаются возникновению водородной хрупкости, да и внешний вид получается превосходный, с замечательным декоративным эффектом в широкой цветовой гамме.
Дополнительная защита при цинковании
Защитное действие покрытий из цинка зависит от его толщины, которая при гальваническом нанесении всего 5 мкм, и характера электролита.
В некоторых случаях защитные свойства цинкового покрытия увеличиваются пассивированием, фосфатированием или покраской.
Пассивирование (хроматирование) – химическая обработка изделий в растворах с хромовой кислотой либо ее солями, в результате которой на поверхности образуются хроматные пленки. Это процесс усиливает не столько защитные свойства, сколько декоративные, потому что в результате усиливается блеск покрытия, и оно может быть окрашено в различные цвета.
При фосфатировании (обработке в солях фосфорной кислоты) оцинкованных изделий на поверхности пленка образуется фосфатная. После фосфатирования может еще наноситься лакокрасочное покрытие.
Этапы гальванического цинкования
На производстве гальваническое цинкование состоит из нескольких технологических процессов, каждый из которых завершается промывкой водой в проточной ванне или щеточно-моечным способом.
Сначала изделия тщательно очищаются от ржавчины, окалины, технологической смазки, остатков охлаждающей жидкости или краски и обезжириваются в щелочных растворах. Затем происходит обезжиривание электролитическое.
После него протравливаются в водном растворе соляной кислоты, при котором поверхность окончательно очищается без нарушения поверхностного слоя и происходит ее декапирование – активация перед нанесением цинкового покрытия. Только потом производится собственно цинкование.
После него, при необходимости, изделия осветляются и очищаются от окисной пленки в водном растворе азотной кислоты, затем фосфатирование, пассивация и сушка.
При цинковании различных изделий могут выполняться дополнительные операции. Например, полосу перед цинкованием разматывают, сваривают концы, правят, а после него промасливают и сматывают.
Оборудование гальванического цинкования
Гальваническая линия - это определенная последовательность промывочных и технологических ванн, в которых создаются одно- или многослойное цинковое покрытие с требуемыми функциональными свойствами.
В соответствии с объемами производства используется оборудование с различной степенью механизации. На крупных предприятиях устанавливаются механизированные линии с автоматическим управлением. Существуют линии с частичным или полным ручным управлением, а также мини-линии.
Линия гальванического цинкования состоит не только из ванн. В нее входят транспортные системы различной конструкции, обязательно оборудование для очистки сточных вод, вспомогательное оборудование, к которому относятся приспособления для цинкования, ТЭНы, теплообменники, катодные и анодные штанги.
В дополнительное оборудование входят системы вентиляции, сушильные камеры и шкафы, холодильное оборудование, фильтровальные установки, оборудование получения демиводы, насосы.
Электролиты для цинкования
Для гальванического цинкования в зависимости от назначения изделия применяют электролиты, которые делятся на две основные группы.
Электролиты, в которых цинк находится в виде простых гидратированных ионов, называют простыми кислыми. Это борфтористоводородные, сульфатные и хлоридные растворы.
Сложные комплексные кислые и щелочные электролиты содержат цинк в комплексных ионах с положительным и отрицательным зарядом. Это аммиакатные, пирофосфатные, цианидные и другие растворы.
От того, какой электролит применяется, зависит в первую очередь скорость осаждения, а затем качество осадков цинка на изделии (катоде).
Из комплексных электролитов цинк оседает на катоде при высоком рассеивании ионов. При увеличении плотности тока выход металла снижается и увеличивается выход водорода.
Поэтому цинкование в сложных электролитах производится при малой плотности тока, а покрытие получается очень качественное, мелкозернистое и равномерное.
В слабокислых простых электролитах гальваническое цинкование, в домашних условиях в том числе, проходит при большой плотности тока, с большей, чем при использовании сложных растворов, скоростью. Внешний вид изделий получается хороший, но покрытие не очень качественное и подходит только для изделий достаточно простой формы.
Гальваническое цинкование
Технологический процесс непосредственно цинкования происходит в ванне с электролитом. В нее опускаются изделия из черного металла, к которым через специальные электроды подводится электрический ток (катод), и чистый цинк в виде шаров или пластин, уложенных в специальные сетчатые секции (анод).
В процессе электрохимической реакции под воздействием электрического тока плотностью от 1 до 5 А/дм цинк растворяется в электролите, затем его ионы оседают на катоде, образуя гальваническое покрытие толщиной 4-25 мкм.
Именно с использованием такой технологии получают крепежные изделия (болты и гайки) с равномерным и блестящим покрытием.
Автоматизированная линия для гальванического цинкования
Современная линия гальванического цинкования – это полностью автоматизированная линия, на которой осуществляются все этапы нанесения покрытия, включая сварку и качественное обезжиривание изделий разного назначения и конфигурации.
Автоматическая линия в общем случае состоит из комплекта технологических гальванических ванн, модульных выпрямителей, стенда загрузки/разгрузки, транспортного оборудования, оборудования для вытяжной вентиляции, подвода воды и отвода канализационных стоков, металлокаркаса с трапом обслуживания.
Гальванические ванны могут изготавливаться из нержавеющей стали, стали, футерованной полимерными материалами или резиной. Современные ванны, сваренные из листовых полимеров, все больше вытесняют металлические емкости. Выбор материала ванн зависит от состава и концентрации электролита и рабочей температуры.
Коммуникации систем водоснабжения и канализации, и в большинстве случаев вентиляции располагаются под ваннами и также изготавливаются из полипропилена.
Размеры линии определяются ее производительностью и габаритами гальванических ванн.
Гальваническое цинкование происходит с образованием сточных вод с высокой концентрацией ионов тяжелых металлов. Поэтому их отстаивают, фильтруют, нейтрализуют, используют химическое осаждение, сорбцию и другие процессы в емкостях из инженерных полимеров.
Электролитическое цинкование в домашних условиях
Гальваническое цинкование, своими руками производимое, начинается с подбора материалов. Электролитом может служить раствор хлорида цинка и соляной кислоты в дистиллированной воде. Это так называемая паяльная кислота, которая чаще всего используется в домашних условиях. Умельцы протравливают цинк в аккумуляторной серной кислоте и получают электролит ZnSO4, но этот процесс опасен, поскольку при реакции выделяется взрывоопасный водород и теплота. В электролите ни в коем случае не должно быть осадка из нерастворенных кристаллов соли.
Чистый цинк можно купить в магазине химреактивов или на радиорынке, а можно получить из солевых батареек или плавких предохранителей, сохранившихся со времен Советского Союза.
Гальванической ванной может служить стеклянная или пластиковая емкость. В нее устанавливаются штативы для анода и катода. Анод – это пластина цинка, к которой от источника питания подсоединяется «плюс». Чем больше анод, тем более равномерным получится покрытие на катоде, изделии, на которое будет наноситься защитное покрытие. Анодов может быть несколько, их можно располагать вокруг катода на одинаковом расстоянии, чтобы его поверхность покрывалась цинком равномерно и одновременно со всех сторон. К катоду подсоединяется «минус» источника питания.
Даже когда в домашних условиях производится цинкование гальваническое, технология обязательно включает тщательную очистку и обезжиривание детали, а также ее активацию в растворе кислоты.
Источник питания – это автомобильный аккумулятор с лампой накаливания небольшой мощности или другого потребителя в схеме, чтобы сила тока в цепи была ниже, или блок питания с постоянным напряжением на выходе. Главное, чтобы не было бурного кипения электролита в процессе цинкования.
Собственно цинкование происходит, когда аноды и катод опущены в электролит и замкнута электрическая цепь. Чем дольше длится процесс, тем толще слой цинка получается на изделии.
С помощью гальванического цинкования защитное покрытие на изделиях становится точным, равномерным и гладким, с декоративным эффектом. Его используют и в промышленности, и в домашних условиях, несмотря на то что требуется очистка сточных вод от экологически опасных отходов.
fb.ru
Горячее цинкование металла: технология и оборудование
Одно из наиболее надежных покрытий для металлических изделий получают методом горячего цинкования. Срок службы такого покрытия составляет около 50 лет. Горячее цинкование металла осуществляется путем погружения изделия в расплав цинка. В результате этого на поверхности металла образуется защитное покрытие, называемое карбонатом цинка, устойчивое к физическим воздействиям, не допускающее возникновения коррозии.
Горячему цинкованию можно подвергать любые виды сталей, но качество полученных поверхностей будет различным. Это зависит от химического состава конкретного металла. Различие будет касаться цвета, блеска поверхности, толщины покрытия, адгезионной способности изделия.
Преимущества и недостатки горячего цинкования
Почему так ценится горячее цинкование? Давайте убедимся в этом сами, взглянув на некоторые факты:
Нельзя умолчать и о некоторых минусах горячего цинкования:
Технология горячего цинкования
Линии горячего цинкования состоят из нескольких последовательных операций, выполнение которых обязательно. Большую часть занимает предварительная подготовка изделия. Перечислим все этапы и дадим комментарии к ним:
Метод горячего цинкования, несмотря на свою громоздкость и длительность, позволяет получить покрытие высочайшего качества.
Области применения изделий, подвергнутых горячему цинкованию
Вывод
Метод горячего цинкования является весьма надежным и современным способом защиты металлических конструкций от воздействия неблагоприятных внешних условий. Результаты, полученные при помощи данного метода, существенно расширяют возможности по внедрению металлоконструкций в нашу жизнь.
Вконтакте
Google+
Одноклассники
sarstroyka.ru
Частые вопросы про горячее цинкование
1. Сварные шлаки вымываются при необходимых условиях в цинковании.
2. Причины для дуплексного покрытия: цинк и краска.
3. Как очистить белый налет.
4. Процесс цинкования. Производство.
5. Стальные крепления при горячей оцинковке.
6. Восстановление поврежденных или непокрытых участков покрытий при горячем цинковании.
1. Сварные шлаки вымываются при необходимых условиях в цинковании.
При цинковании сварных металлоконструкций горячим методом, чистота области сварки значительно влияет на качество и внешний вид цинкового покрытия вокруг сварного шва.
Если электрод с покрытием используется во время сварки, весь сварочный шлак должен быть убран до цинкования, иначе цинковое покрытие не будет прилипать к месту сварки (в результате чего образуются голые пятна в покрытии).
Химические моющие растворы, используемые в процессе гальванизации, не могут удалить сварной флюс и шлак. Таким образом, сварочный шлак должен быть удален шлифованием, абразивной струйной очисткой, проволочной щеткой, огневой очисткой или сколами.
Сварной шлак образуется при плавлении, начинает таять от покрытого флюсом сварочного провода/электрода, затем оседает в области шва. Поэтому, только сварные швы, выполненные с покрытым проводом, восприимчивы к формированию сварного шлака. Швы, выполненные голым проводом не имеют на своей поверхности шлака, следовательно, не требуют очистки абразива для этой конкретной цели.
Ниже приведен список общих процессов сварки и потенциал для формирования сварного шлака:
Процесс сварки | Потенциал для формирования сварного шлака |
Электро-дуговая сварка (ручная) | Да |
Электрод с флюсом | Да |
Порошковая дуговая сварка | Да |
Дуговая сварка под флюсом | Да |
Гранулированный флюс | Да |
Газовая дуговая сварка металла/инертная газовая сварка | Нет |
Газовая вольфрамовая дуговая сварка/инертная газовая сварка | Нет |
Плазменная сварка | Нет |
2. Причины для дуплексных систем
Есть семь причин для лакокрасочного или порошкового покрытия металлической поверхности, защищенной горячим цинкованием:
1. Увеличенная прочность – синергетический эффект между оцинкованной сталью и краской, цинковое гальванизированное покрытие, является защитным барьером для чистой стали, катодным образом защищает ее и обеспечивает защиту от коррозии. Краска обеспечивает защитный барьер цинкового покрытия.
2. Экономичность – потому что цинк увеличивает срок службы краски, меньше требуется обслуживания в течение всего срока службы.
3. Непринужденность в перекрашивании – цинковое покрытие требует минимальной подготовки поверхности при перекрашивании.
4. Эстетика – желанием цвет для конструкции или для брендинга.
5. Безопасность – очень высокие оцинкованные конструкции должны быть окрашены в ярко-оранжевый и белый цвет для четкой видимости воздушного движения.
6. Длительный срок службы оцинкованной стали – большие конструкции зачастую не могут быть повторно гальванизированы после десятилетий воздействия окружающей средой, таким образом, лучшее средство для сохранения конструкции в обслуживании — применить краску, неорганическую богатую цинком, которая обеспечивает защитный барьер и катодную защиту.
7. Кодирование цвета – пар, вода и другие жидкие системы трубопровода часто рисуют на производственных объектах, чтобы отличить их при быстром ремонте и для безопасности.
3. Как очистить белый налет
Обработка белого налета начинается с сушки гальванизированной поверхности. Пока налет остается на цинковой поверхности, и воздушный поток ограничен, механизм коррозии будет продолжаться, и может повредить цинковое покрытие и основную сталь.
После того, как гальванизированные поверхности высушены, процессы обработки зависят от серьезности белого налета. После сушки легкого налета, изделие можно оставить, пока не появится нужный воздушный поток. Белый налет преобразуется в цинковый налет, поскольку он реагирует с углекислым газом в воздухе.
Если воздушный поток будет ограничен, то налет должен быть удален, счистив его жесткой ощетиненной нейлоновой щеткой.Белый налет средней и тяжелой степени должен быть удален с гальванизированного покрытия, чтобы не сформировался цинковый налет, иначе это повлияет на срок службы цинкового покрытия и основной стали.
После удаления налета, счистив его жесткой ощетиненной нейлоновой щеткой и соответствующим моющим раствором, лучше измерить цинковую толщину покрытия, чтобы гарантировать, что соответствующее цинковое покрытие останется на основной стали. Когда налет средней или тяжелой степени становится черным, то сталь должна быть повторно гальванизирована.
4. Процесс цинкования. Производство.
Процесс гальванизации горячим методом, также известен как общая гальванизация, которая производит цинковое покрытие на железе и стальных продуктах путем погружения изделия в ванну с жидким цинком. Прежде чем покрыть изделие, сталь очищают от масла, жиров, почвы, прокатной окалины и ржавчины.
Цикл очистки, как правило, состоит из стадии обезжиривания, с последующим кислотным травлением для удаления окалины и ржавчины, что предупреждает окисление стали прежде, чем опуститься в литой цинк.Существует два различных метода плавления: сухое и влажное. Сухой процесс осуществляется путем предварительного плавления в растворе цинка хлорида аммония. Влажный процесс использует поток расплавленной течи на цинковой поверхности ванны.
Горячее цинкование покрытия используется на множестве материалов размером от мелких деталей, таких как гайки, болты и гвозди до очень больших структурных форм. Размер цинковых ванн и обработка материалов ограничивается размером стали, которая должна быть оцинкована.Большая ванна горячего цинкования имеет размеры 13 метров в длину и глубиной 3 метра. Однако максимальный размер цинковой ванны, существенно увеличивается, погружая одну часть продукта и затем другую.Поскольку изделие погружено в расплав цинка, цинковые потоки покрывают металлоизделие полностью, даже области сложных форм для полной защиты от коррозии.
5. Стальные крепления при гальванизировании.
Большинство конструкций хорошо поддаются процессу гальванизации, в том числе асимметричные конструкции или изделия, содержащие участки неодинаковой толщины. Важно понимать, что, так как во время цинкования сталь подвергается температурным изменениям, изделия асимметричной конструкции или с участками неравной толщины могут иметь различное тепловое расширение и сжатие под напряжением, что приводит к изменению формы и / или выравниванию (искривлению и искажению).
Постоянные или сменные крепления, используемые после гальванизации, обеспечивают стабильность во время теплового цикла расширения и сокращения. Иногда, когда крепления не используются, а деформирование и/или искажение все же происходят, часть вернется к своей первоначальной форме во время остывания.
6. Восстановление поврежденных или непокрытых участков покрытий при горячем цинковании.
Хотя оцинкованные покрытия обладают высокой стойкостью к истиранию, повреждение покрытия может произойти из-за чрезвычайно грубой обработки, методов монтажа или в условиях эксплуатации. Небольшие участки оцинкованного изделия могут быть непокрытыми из-за невидимых загрязняющих веществ, которые в процессе очистки, неспособной их удалить.Существуют доступные методы, гарантирующие целостность покрытия после гальванизации. Стандартная практика для ремонта поврежденных и непокрытых областей методом горячего погружения оцинкованного покрытия разрешает три принятых методов ремонта:
• Применение цинконаполненных красок
• Покрытие с цинковым припоем
• Распыление литым (металлизирующим) цинком
Подкраску и выбранный метод ремонта стоит рассматривать индивидуально. Защита от коррозии должна всегда быть главным фактором, при определении использования и условия на основе других технических характеристик. Применение цинконаполненных красок часто ошибочно называют “холодным цинкованием”, и могут быть целесообразно применены для подкраски и ремонта, но так же, как и в случае применения каких-либо других красок, процедуры подготовки поверхности, изложенные в D6386, следует строго придерживаться для того, чтобы обеспечить лучшую производительность. Важно отметить, что ни один из трех методов ремонта не обеспечивает ту же самую защиту от коррозии как гальванизация горячим методом.
Вы все еще ищете правильный ответ? Спросите наших специалистов.
gorjachee-cinkovanie.ru