- Закалка в одной среде
- Ступенчатая закалка
- Закалка в двух средах
- Поверхностная закалка (лазерная, токами высокой частоты)
- Бронзы (сплавы меди) подвергают отжигу при температуре чуть ниже температуры плавления, а потом закалке с охлаждением водой. Температура закалки от 750 до 950С в зависимости от состава сплава. Отпуск при 200-400С производят в течение 2-4 часов. Наибольшие показатели твердости, до HV300 (около HRC 34) можно при этом получить для изделий из бериллиевых бронз.
- Твердость серебра можно повысить отжигом до температуры, близкой к температуре плавления (тусклый красный цвет) с последующей закалкой.
- Различные сплавы никеля подвергают отжигу при 700-1185С, такой широкий диапазон определяется разнообразием их составов. Для охлаждения используют соляные растворы, частички которых потом удаляют водой либо защитные газы, препятствующие окислению (сухой азот, сухой водород).
- Сплавы алюминия, например, дуралюмины (4-5% меди) и сплавы с добавлением никеля и железа выдерживают в пределах часа при температуре 100-180С
- Сплавы никеля подвергают старению в 2-3 этапа, что в сумме занимает от 6 до 30 часов при температурах от 595 до 845С. Некоторые сплавы подвергают предварительной закалке при 790-1220С. Детали из никелевых сплавов помещают в дополнительный контейнеры, чтобы предохранить от контакта с воздухом. Для нагрева используют электрические печи, для мелких деталей могут применяться соляные электродные ванны.
- Мартенситно-стареющие стали (высоколегированные безуглеродистые сплавы железа) стареют около 3 часов при 480-500С после предварительного отжига при 820С
- неметаллическими: углеродом (цементация) и азотом (азотирование) применяются для повышения износостойкости колен, валов, шестерней из низкоуглеродистых сталей
- металлическими: например, кремнием (силицирование) и хромом помогает повысить износо- и коррозионную стойкость деталей
- Фото стальной уголок
- Вес нержавеющей стали
- Сталь 12х18н10т температура плавления
- Угловая сталь 50х50
- Сталь с полимерным покрытием листовая
- Характеристики круг стальной
- Труба бесшовная гост 8732 стальная
- Сталь латунь
- Сталь нержавеющий
- Гост трубы стальные горячекатаные
- Конструкционные качественные стали
Как вырезать заготовку из пластины и не отпустить сталь. Как отпустить сталь
Как не допустить самопроизвольного отпуска стали?
Чтобы понять, о чем идет речь в заголовке, нам придется хотя бы поверхностно изучить, что такое твердость и прочность, а также закалка стали.
Чем отличается твердость от прочности, как они связаны и почему сложно заполучить сразу и то, и другое
Чего мы хотим от готового стального изделия (в нашем случае – ножа)? Конечно, прочности и твердости. Но в быту мы мало задумываемся над тем, что между этими понятиями в физике существует серьезная разница. Давайте разберемся.
Представьте себе лист чугуна. Это очень твердый, но при этом хрупкий материал: это значит, что он выдерживает огромное давление на сжатие, но совершенно не приспособлен для ударных или изгибных нагрузок. Иными словами, при высокой твердости у него отсутствует прочность. Напротив, лист танковой брони обладает отличной прочностью, чтобы выдержать попадание пуль и снарядов. Но нож из него не сделаешь: вязкая броня заточку держать не будет.
Как это относится к стали? Просто: при закалке (процедуре, направленной на повышение твердости) сталь неизбежно теряет в прочности. До закалки отпущенную прочную и вязкую пластину из стали невозможно разбить или пробить, но можно поцарапать или согнуть; после закалки ею можно царапать другие стали, зато теперь она ломается чуть ли не руками.
Что делать? Именно для решения этого вопроса и был изобретен отпуск стали.
Что представляет собой отпуск стали и зачем он нужен
Отпуск – это не совсем повторная закалка, хотя в чем-то эти процедуры и похожи. Сталь под закалку нагревают до оптимальной именно для нее температуры, а не до которой в принципе способен «разогнаться» горн, после чего охлаждают – в масле, воде или иных средах. А вот отпускают ее уже после охлаждения. Для этого ее повторно нагревают при намного меньшей температуре, после чего снова охлаждают в закалочной среде.
Как определяют температуры закалки и отпуска?
Для обычных марок сталей температуры обычно уже известны мастеру. Закалочные печи оснащены специальными термодатчиками, позволяющими настроить необходимую температуру. Если же работать в горне без датчиков, то можно ориентироваться на визуальные признаки: грубо говоря, при достижении заготовкой белого цвета сталь уже перекалена и никуда не годится, а вот светло-желтый цвет говорит о достижении той самой экстремальной температуры, которая нам нужна для закалки. Цвет стали меняется, и опытный мастер может определить нужную температуру нагрева «на глаз».
С отпуском ситуация аналогичная – так называемый «цвет побежалости» характеризует необходимую температуру отпуска, которую подбирают согласно назначению изделия. Низкотемпературный отпуск сохранит твердость в ущерб пластичности, а высокотемпературный – наоборот.
Что касается ножей, здесь мы говорим чаще всего о низкотемпературном отпуске, до 250 °С, реже – о среднетемпературном. Чем выше температура отпуска, тем более стойкой будет сталь к ударным нагрузкам, а это обычно нужно для деталей движущихся механизмов. Для стали, из которой сделан нож, важнее баланс между твердостью и прочностью: клинок должен быть в меру износостойким* и при этом быть устойчивым к ударным нагрузкам.
Чаще всего цвет каления, как это называется у профессионалов, будет варьироваться от вишневого до желтого, но, повторим, ориентироваться только на цвет нельзя: универсальной температуры отпуска для разных сталей и для изделий разного назначения просто не бывает.
* Почему мы не ставим перед собой задачи сделать так, чтобы сталь ножа вообще не истиралась? Это откат в каменный век: орудия из кремня были очень твердыми и поэтому чрезвычайно хрупкими и неудобными в работе. К тому же невозможность истирания стали привела бы и к невозможности ее наточить, ведь в основе и затупления, и заточки лежит один и тот же процесс – механический износ сплава.
Когда происходит нежелательный отпуск и как его избежать
Ковка
Прежде всего, конечно, речь идет о термомеханической обработке стали. После закалки сталь особенно уязвима – она очень тверда, но ее можно разбить щелчком пальцев, так как в процессе закалки она утеряла прочность. Чтобы сделать материал заготовки функциональным, требуется отпуск.
Здесь важно не переборщить. Экспериментальным путем было выяснено, что повторная закалка (то есть доведение до экстремальной температуры) ни к чему хорошему не приведет, делать ее не следует; а вот нагрев до более низких температур – то, что надо. Но если мастер попросту проворонил нужный момент, происходит высокотемпературный отпуск, иначе говоря – та самая нежелательная повторная закалка, при которой сталь снова теряет прочность. Впрочем, слишком низкий отпуск заготовке тоже не показан: это может негативно сказаться на свойствах уже готового клинка, который в результате окажется непрочным.
Заточка
Второй момент, куда более опасный – это слесарные операции и заточка на шлифовальных кругах. Ковку все-таки делают профессионалы, и там риск перекалить заготовку, в принципе, минимален. А вот отделочные операции (в т. ч. заточка, которую делает чаще всего владелец и только изредка – профессионал) представляют для ножа много опасностей, среди которых искажение геометрии клинка и многое другое. Но сейчас нас интересует именно самопроизвольный отпуск.
На шлифовальном круге из-за большой скорости вращения зона контакта круга с заготовкой быстро достигает критически высоких температур. Поскольку сталь теплопроводна, в зоне контакта перегревается и клинок ножа. Да не просто перегревается, а именно раскаляется – только попробуйте потрогать инструмент, который только что отняли от шлифовального круга. В месте контакта меняется и цвет стали на коричневый. Догадываетесь, что происходит? Температура там куда выше, чем положенная для отпуска; она легко переваливает за безопасную для закалки клинка отметку. Происходит нежелательный дополнительный отпуск, который, как мы помним, ведет к потере твердости и упругости стали.
При заточке ножа температура возрастает, проконтролировать ее без опыта и навыков невозможно. Если она превышает допустимую норму, происходит самопроизвольный отпуск и режущая кромка теряет свои свойства. Поэтому и при заточке, и при выполнении слесарных операций так важно регулярно охлаждать клинок, помещая его, например, в емкость с водой.
Что делать? Некоторые специалисты рекомендуют охлаждать клинок, а иногда и сам заточной инструмент обычной проточной водой. Но это решает только часть проблемы, притом что охлаждение снижает скорость работы и используется только при заточке. Поэтому второе, что мы делаем для выполнения слесарных операций по выведению спусков – понижаем скорость вращения круга до 60 оборотов в минуту, и это максимум.
Подобный способ заточки для хороших ножей все-таки не очень подходит. На обычном шлифовальном круге можно точить косы, топоры, недорогие универсальные и кухонные ножи, но никак не более-менее стоящие экземпляры. Для них изобретено множество других способов заточки, в том числе и такие же быстрые механизированные – например, заточные машины с водными камнями. Чем они отличаются от обычных? Во-первых, у них иной материал абразивного инструмента, который относится более бережно к поверхности клинка и не снимает слишком много стали. Во-вторых, в конструкции есть специальный резервуар, который не только подает воду безопасным для электрических частей способом, но и смачивает поверхность диска, в результате чего на ней образуется суспензия, дополнительно полирующая нож. То есть на такой машине делается не только аккуратная заточка, но и доводка режущей кромки (если подобрать круг правильной зернистости). Ну и, конечно, скорость вращения здесь куда ниже, поэтому абразивный инструмент более щадяще относится к ножу.
Такие машинки специально предназначены для заточки ножей: благодаря использованию специальных водных кругов, выделяющих суспензию, водяному охлаждению и малой скорости вращения они не вредят ножу в процессе заточки. Второе и третье фото – это заточной круг с гридностью #1000 и доводочный с гридностью #6000
***
Итак, что мы выяснили? Сырой стали правильный температурный режим закалки придает твердость, но отнимает прочность; вернуть прочность можно с помощью правильного режима отпуска – низкотемпературного нагрева с последующим охлаждением. При неаккуратной заточке на шлифовальном круге температурные режимы могут быть превышены, в результате чего произойдет самопроизвольный отпуск и клинок ножа просто-напросто утратит рабочие свойства. Избежать этой ситуации помогают специальные машинки для заточки ножей.
www.tojiro.ru
как отпустить сталь Видео
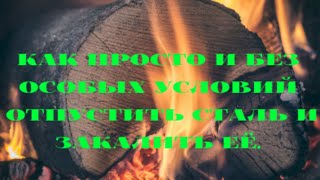
2 г. назад
Покажу как просто и без особых условий отпустить сталь и закалить её.
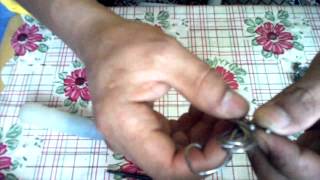
5 г. назад
ОТПУСК СТАЛИ ПОСЛЕ ЗАКАЛКИ ПРОСТО ДЕЛАЕМ ДОМА THE HOLIDAYS ARE A SIMPLE WAY Моя партнерка рекомендую!
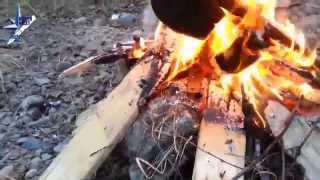
5 г. назад
Отжиг быстрореза в обычном костре. Цели отжига — снижение твёрдости для повышения обрабатываемости, улучш...

1 г. назад
https://vk.com/iddeddin я ВК Еще давно решил изготовить нож из напильника но столкнулся с проблемой при закалке,данно...
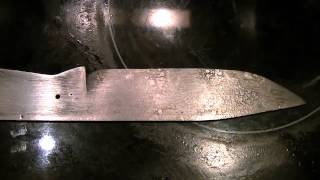
6 г. назад
В качестве комментария могу сказать, что не всегда больше- значит лучше, в данном случае наддув на мой взгля...
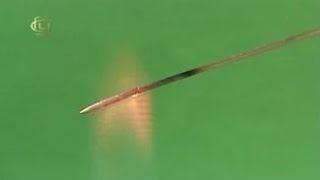
2 г. назад
Неорганическая химия. Металлы побочных подгрупп. № 4. Школьный химический эксперимент. Первый образователь...
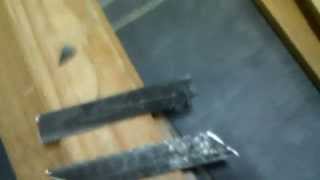
4 г. назад
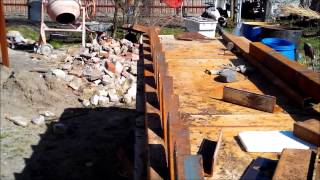
3 г. назад
В данном видео показано как можно попытаться исправить сваренную электродуговой сваркой деталь если ее...

3 г. назад
Новая рукоять на старый клинок + ножны.

7 мес. назад
Где взять, как работать, плюсы и минусы Инстаграм - https://www.instagram.com/piwell_inst/ Паблос - https://vk.com/pi_well TWITCH - https://go.twitch....
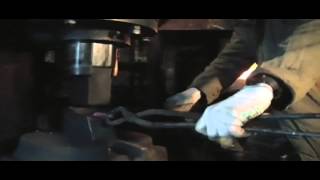
6 г. назад
Закалка-отпуск. Цвета побежалости Кузнечный Форум: http://forum.ostmetal.info Сане Климу. "Фейсбук": http://www.facebook.com/profile.php?...

5 г. назад
Внимание! Внимание! Внимание! Это не урок.В видео представлены мои личные наработки и не более. Закалка...

3 г. назад
Как раскалить металл до 900 градусов без спичек и без огня. Сварка, сварочные электроды и всё что с этим связа...
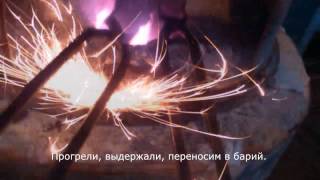
2 г. назад
Процесс термообработки изделий из быстрорежущей стали Р6М5 на соляных ваннах в промышленных условиях.
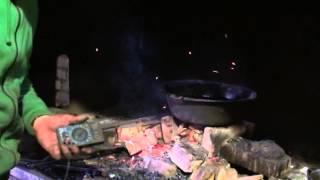
3 г. назад
Отпуск ножа в масле.
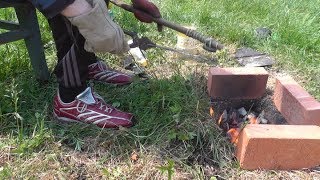
5 г. назад
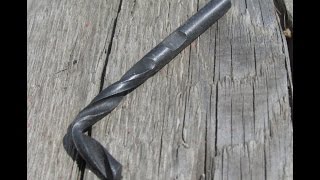
1 г. назад
Один из множества способов сверления легированной стали.
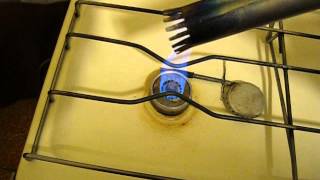
5 г. назад
ПРОСТОЙ СПОСОБ РАСКАЛИТЬ ДО КРАСНА ДЕТАЛЬ НА ГАЗОВОЙ ПЛИТЕ (для отпуска или закалки)
videoprime.ru
как отпустить сталь Видео
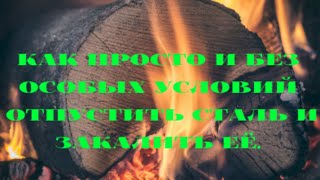
2 г. назад
Покажу как просто и без особых условий отпустить сталь и закалить её.
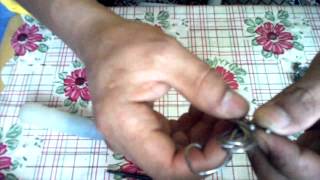
5 г. назад
ОТПУСК СТАЛИ ПОСЛЕ ЗАКАЛКИ ПРОСТО ДЕЛАЕМ ДОМА THE HOLIDAYS ARE A SIMPLE WAY Моя партнерка рекомендую!
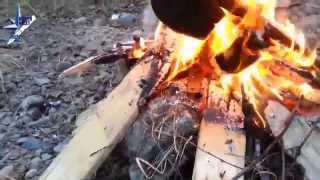
5 г. назад
Отжиг быстрореза в обычном костре. Цели отжига — снижение твёрдости для повышения обрабатываемости, улучш...

1 г. назад
https://vk.com/iddeddin я ВК Еще давно решил изготовить нож из напильника но столкнулся с проблемой при закалке,данно...
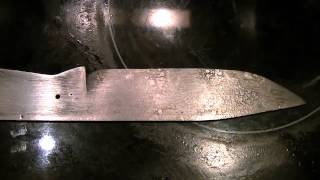
6 г. назад
В качестве комментария могу сказать, что не всегда больше- значит лучше, в данном случае наддув на мой взгля...
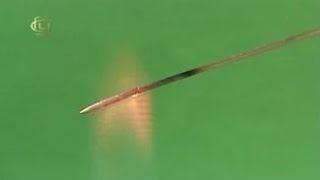
2 г. назад
Неорганическая химия. Металлы побочных подгрупп. № 4. Школьный химический эксперимент. Первый образователь...
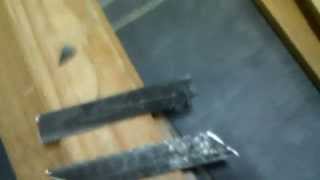
4 г. назад
Обратите внимание в описание, т.к. телефон садился и на факты не было времени говорить▽▽▽ Извините...
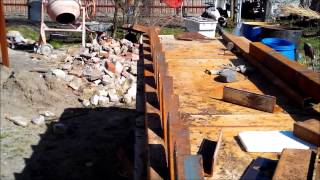
3 г. назад
В данном видео показано как можно попытаться исправить сваренную электродуговой сваркой деталь если ее...

3 г. назад
Новая рукоять на старый клинок + ножны.

7 мес. назад
Где взять, как работать, плюсы и минусы Инстаграм - https://www.instagram.com/piwell_inst/ Паблос - https://vk.com/pi_well TWITCH - https://go.twitch....
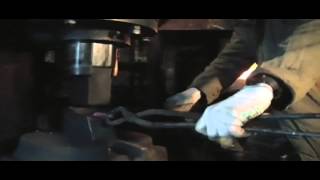
6 г. назад
Закалка-отпуск. Цвета побежалости Кузнечный Форум: http://forum.ostmetal.info Сане Климу. "Фейсбук": http://www.facebook.com/profile.php?...

5 г. назад
Внимание! Внимание! Внимание! Это не урок.В видео представлены мои личные наработки и не более. Закалка...

3 г. назад
Как раскалить металл до 900 градусов без спичек и без огня. Сварка, сварочные электроды и всё что с этим связа...
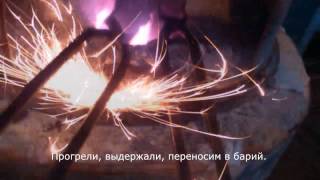
2 г. назад
Процесс термообработки изделий из быстрорежущей стали Р6М5 на соляных ваннах в промышленных условиях.
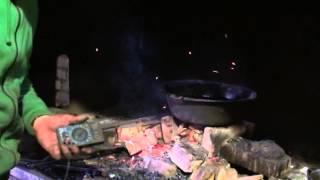
3 г. назад
Отпуск ножа в масле.
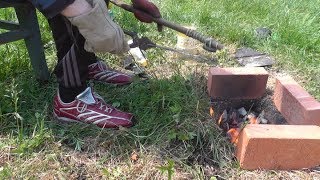
5 г. назад
Видео о закалке самодельного ножа в домашних условиях, для плейлиста, посвященного изготовлению ножа с...
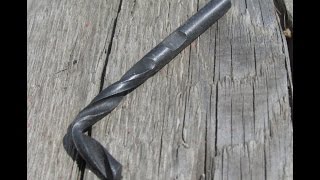
1 г. назад
Один из множества способов сверления легированной стали.
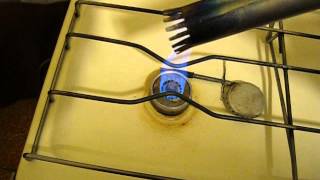
5 г. назад
ПРОСТОЙ СПОСОБ РАСКАЛИТЬ ДО КРАСНА ДЕТАЛЬ НА ГАЗОВОЙ ПЛИТЕ (для отпуска или закалки)
kahn-russia.ru
Руководство как повысить твердость стали и цветных металлов

Технологии придания большей твердости металлам и сплавам совершенствовались в течение долгих веков. Современное оборудование позволяет проводить термическую обработку таким образом, чтобы значительно улучшать свойства изделий даже из недорогих материалов.
Закалка стали и сплавов
Закалка (мартенситное превращение) — основной способ придания большей твердости сталям. В этом процессе изделие нагревают до такой температуры, что железо меняет кристаллическую решетку и может дополнительно насытиться углеродом. После выдержки в течение определенного времени, сталь охлаждают. Это нужно сделать с большой скоростью, чтобы не допустить образования промежуточных форм железа.В результате быстрого превращения получается перенасыщенный углеродом твердый раствор с искаженной кристаллической структурой. Оба эти фактора отвечают за его высокую твердость (до HRC 65) и хрупкость.Большинство углеродистых и инструментальных сталей при закаливании нагревают до температуры от 800 до 900С, а вот быстрорежущие стали Р9 и Р18 калятся при 1200-1300С.

Микроструктура быстрорежущей стали Р6М5: а) литое состояние; б) после ковки и отжига;в) после закалки; г) после отпуска. ×500.
Режимы закалки
Нагретое изделие опускают в охлаждающую среду, где оно остается до полного остывания Это самый простой по исполнению метод закалки, но его можно применять только для сталей с небольшим (до 0,8%) содержанием углерода либо для деталей простой формы. Эти ограничения связаны с термическими напряжениями, которые возникают при быстром охлаждении — детали сложной формы могут покоробиться или даже получить трещины.
При таком способе закалки изделие охлаждают до 250-300С в соляном растворе с выдержкой 2-3 минуты для снятия термических напряжений, а затем завершают охлаждение на воздухе. Это позволяет не допускать появления трещин или коробления деталей. Минус этого метода в сравнительно небольшой скорости охлаждения, поэтому его применяют для мелких (до 10 мм в поперечнике) деталей из углеродистых или более крупных — из легированных сталей, для которых скорость закалки не столь критична.
Начинается быстрым охлаждением в воде и завершается медленным — в масле. Обычно такую закалку используют для изделий из инструментальных сталей. Основная сложность заключается в расчете времени охлаждения в первой среде.
Применяется для деталей, которые должны быть твердыми на поверхности, но иметь при этом вязкую сердцевину, например, зубья шестеренок. При поверхностной закалке внешний слой металла разогревается до закритических значений, а затем охлаждается либо в процессе теплоотвода (при лазерной закалке), либо жидкостью, циркулирующей в специальном контуре индуктора (при закалке током высокой частоты)
Отпуск
Закаленная сталь становится чрезмерно хрупкой, что является главным недостатком этого метода упрочнения. Для нормализации конструкционных свойств производят отпуск — нагрев до температуры ниже фазового превращения, выдержку и медленное охлаждение. При отпуске происходит частичная «отмена» закалки, сталь становится чуть менее твердой, но более пластичной. Различают низкий (150-200С, для инструмента и деталей с повышенной износостойкостью), средний (300-400С, для рессор) и высокий (550-650, для высоконагруженных деталей) отпуск.
Таблица температур закалки и отпуска сталей
№ п/п | Марка стали | Твёрдость (HRCэ) | Температ. закалки, град.С | Температ. отпуска, град.С | Температ. зак. ТВЧ, град.С | Температ. цемент., град.С | Температ. отжига, град.С | Закал. среда | Прим. |
1 | 2 | 3 | 4 | 5 | 6 | 7 | 8 | 9 | 10 |
1 | Сталь 20 | 57…63 | 790…820 | 160…200 | 920…950 | Вода | |||
2 | Сталь 35 | 30…34 | 830…840 | 490…510 | Вода | ||||
33…35 | 450…500 | ||||||||
42…48 | 180…200 | 860…880 | |||||||
3 | Сталь 45 | 20…25 | 820…840 | 550…600 | Вода | ||||
20…28 | 550…580 | ||||||||
24…28 | 500…550 | ||||||||
30…34 | 490…520 | ||||||||
42…51 | 180…220 | Сеч. до 40 мм | |||||||
49…57 | 200…220 | 840…880 | |||||||
<= 22 | 780…820 | С печью | |||||||
4 | Сталь 65Г | 28…33 | 790…810 | 550…580 | Масло | Сеч. до 60 мм | |||
43…49 | 340…380 | Сеч. до 10 мм (пружины) | |||||||
55…61 | 160…220 | Сеч. до 30 мм | |||||||
5 | Сталь 20Х | 57…63 | 800…820 | 160…200 | 900…950 | Масло | |||
59…63 | 180…220 | 850…870 | 900…950 | Водный раствор | 0,2…0,7% поли-акриланида | ||||
«— | 840…860 | ||||||||
6 | Сталь 40Х | 24…28 | 840…860 | 500…550 | Масло | ||||
30…34 | 490…520 | ||||||||
47…51 | 180…200 | Сеч. до 30 мм | |||||||
47…57 | 860…900 | Водный раствор | 0,2…0,7% поли-акриланида | ||||||
48…54 | Азотирование | ||||||||
<= 22 | 840…860 | ||||||||
7 | Сталь 50Х | 25…32 | 830…850 | 550…620 | Масло | Сеч. до 100 мм | |||
49…55 | 180…200 | Сеч. до 45 мм | |||||||
53…59 | 180…200 | 880…900 | Водный раствор | 0,2…0,7% поли-акриланида | |||||
< 20 | 860…880 | ||||||||
8 | Сталь 12ХН3А | 57…63 | 780…800 | 180…200 | 900…920 | Масло | |||
50…63 | 180…200 | 850…870 | Водный раствор | 0,2…0,7% поли-акриланида | |||||
<= 22 | 840…870 | С печью до 550…650 | |||||||
9 | Сталь 38Х2МЮА | 23…29 | 930…950 | 650…670 | Масло | Сеч. до 100 мм | |||
<= 22 | 650…670 | Нормализация 930…970 | |||||||
HV > 670 | Азотирование | ||||||||
10 | Сталь 7ХГ2ВМ | <= 25 | 770…790 | С печью до 550 | |||||
28…30 | 860…875 | 560…580 | Воздух | Сеч. до 200 мм | |||||
58…61 | 210…230 | Сеч. до 120 мм | |||||||
11 | Сталь 60С2А | <= 22 | 840…860 | С печью | |||||
44…51 | 850…870 | 420…480 | Масло | Сеч. до 20 мм | |||||
12 | Сталь 35ХГС | <= 22 | 880…900 | С печью до 500…650 | |||||
50…53 | 870…890 | 180…200 | Масло | ||||||
13 | Сталь 50ХФА | 25…33 | 850…880 | 580…600 | Масло | ||||
51…56 | 850…870 | 180…200 | Сеч. до 30 мм | ||||||
53…59 | 180…220 | 880…940 | Водный раствор | 0,2…0,7% поли-акриланида | |||||
14 | Сталь ШХ15 | <= 18 | 790…810 | С печью до 600 | |||||
59…63 | 840…850 | 160…180 | Масло | Сеч. до 20 мм | |||||
51…57 | 300…400 | ||||||||
42…51 | 400…500 | ||||||||
15 | Сталь У7, У7А | НВ <= 187 | 740…760 | С печью до 600 | |||||
44…51 | 800…830 | 300…400 | Вода до 250, масло | Сеч. до 18 мм | |||||
55…61 | 200…300 | ||||||||
61…64 | 160…200 | ||||||||
61…64 | 160…200 | Масло | Сеч. до 5 мм | ||||||
16 | Сталь У8, У8А | НВ <= 187 | 740…760 | С печью до 600 | |||||
37…46 | 790…820 | 400…500 | Вода до 250, масло | Сеч. до 60 мм | |||||
61…65 | 160…200 | ||||||||
61…65 | 160…200 | Масло | Сеч. до 8 мм | ||||||
61…65 | 160…180 | 880…900 | Водный раствор | 0,2…0,7% поли-акриланида | |||||
17 | Сталь У10, У10А | НВ <= 197 | 750…770 | ||||||
40…48 | 770…800 | 400…500 | Вода до 250, масло | Сеч. до 60 мм | |||||
50…63 | 160…200 | ||||||||
61…65 | 160…200 | Масло | Сеч. до 8 мм | ||||||
59…65 | 160…180 | 880…900 | Водный раствор | 0,2…0,7% поли-акриланида | |||||
18 | Сталь 9ХС | <= 24 | 790…810 | С печью до 600 | |||||
45…55 | 860…880 | 450…500 | Масло | Сеч. до 30 мм | |||||
40…48 | 500…600 | ||||||||
59…63 | 180…240 | Сеч. до 40 мм | |||||||
19 | Сталь ХВГ | <= 25 | 780…800 | С печью до 650 | |||||
59…63 | 820…850 | 180…220 | Масло | Сеч. до 60 мм | |||||
36…47 | 500…600 | ||||||||
55…57 | 280…340 | Сеч. до 70 мм | |||||||
20 | Сталь Х12М | 61…63 | 1000…1030 | 190…210 | Масло | Сеч. до 140 мм | |||
57…58 | 320…350 | ||||||||
21 | Сталь Р6М5 | 18…23 | 800…830 | С печью до 600 | |||||
64…66 | 1210…1230 | 560…570 3-х кратн. | Масло, воздух | В масле до 300…450 град., воздух до 20 | |||||
26…29 | 780…800 | Выдержка 2…3 часа, воздух | |||||||
22 | Сталь Р18 | 18…26 | 860…880 | С печью до 600 | |||||
62…65 | 1260…1280 | 560…570 3-х кратн. | Масло, воздух | В масле до 150…200 град., воздух до 20 | |||||
23 | Пружин. сталь Кл. II | 250…320 | После холодной навивки пружин 30-ть минут | ||||||
24 | Сталь 5ХНМ, 5ХНВ | >= 57 | 840…860 | 460…520 | Масло | Сеч. до 100 мм | |||
42…46 | Сеч. 100..200 мм | ||||||||
39…43 | Сеч. 200..300 мм | ||||||||
37…42 | Сеч. 300..500 мм | ||||||||
НV >= 450 | Азотирование. Сеч. св. 70 мм | ||||||||
25 | Сталь 30ХГСА | 19…27 | 890…910 | 660…680 | Масло | ||||
27…34 | 580…600 | ||||||||
34…39 | 500…540 | ||||||||
«— | 770…790 | С печью до 650 | |||||||
26 | Сталь 12Х18Н9Т | <= 18 | 1100…1150 | Вода | |||||
27 | Сталь 40ХН2МА, 40ХН2ВА | 30…36 | 840…860 | 600…650 | Масло | ||||
34…39 | 550…600 | ||||||||
28 | Сталь ЭИ961Ш | 27…33 | 1000…1010 | 660…690 | Масло | 13Х11Н2В2НФ | |||
34…39 | 560…590 | При t>6 мм вода | |||||||
29 | Сталь 20Х13 | 27…35 | 1050 | 550…600 | Воздух | ||||
43,5…50,5 | 200 | ||||||||
30 | Сталь 40Х13 | 49,5…56 | 1000…1050 | 200…300 | Масло |
Термообработка цветных металлов
Сплавы на основе других металлов не отвечают на закалку столь же ярко, как стали, но их твердость тоже можно повысить термообработкой. Обычно используют сочетание закалки и предварительного отжига (нагрева выше точки фазового превращения с медленным охлаждением).
Металл | Температураотжига, C° | Охлаждающая среда |
МедьЛатунь Л96Латунь Л90-Л62МельхиорНейзильберСереброАлюминийДюралюминий | 500 — 600540 — 600600 — 700650 — 700700 — 750650 — 700300 — 350360 — 380 | ВодаНа открытом воздухеНа открытом воздухеВодаВодаВодаНа открытом воздухеОхлаждение в печи |
Оборудование и материалы
Для нагрева металла при термообработке используются 4 основных типа печей:— соляная электродная ванна— камерная печь— печь непрерывного горения— вакуумная печь
В качестве закалочных сред, в которых происходит охлаждение, используются жидкости (вода, минеральное масло, специальные водополимеры (Термат), растворы солей), воздух и газы (азот, аргон) и даже легкоплавкие металлы. Сам агрегат, где происходит охлаждение, называется закалочная ванна и представляет собой емкость, в которой происходит ламинарное перемешивание жидкости. Важной характеристикой закалочной ванны является качество удаления паровой рубашки.
Старение и другие методы повышения твердости
Старение — еще один вид термообработки, позволяющий повысить твердость сплавов алюминия, магния, титана, никеля и некоторых нержавеющих сталей, которые подвергают предварительной закалке без полиморфного превращения. В процессе старения увеличиваются твердость и прочность, а пластичность понижается.
Химико-термическая обработка — насыщение поверхностного слоя легирующими элементами,
Цементирование и азотирование производят в шахтных электропечах. Существуют также универсальные агрегаты, позволяющие проводить весь спектр работ по термохимической обработке стальных изделий.
Обработка давлением (наклеп) — увеличение твердости в результате пластической деформации при относительно низких температурах. Таким образом происходит упрочнение низкоуглеродистых сталей при холодной объемной штамповке, а также чистых меди и алюминия.
В процессе термической обработки изделия из стали могут претерпевать поразительные превращения, приобретая износостойкость и твердость, в разы большую чем у исходного материала. Диапазон изменения твердости сплавов из цветных металлов при термической обработке гораздо меньше, но их уникальные свойства зачастую и не требуют масштабного улучшения.
www.m-deer.ru
Как вырезать заготовку из пластины и не отпустить сталь
Тюменец 14-12-2011 15:32Добрый день, мастера.Имеется нож от рубанка из стали 8х6нфт Советского производства с заводской ТО. По ширине лишние 1.5 см. Если буду вырезать болгаркой с периодическим поливанием водой на какое расстояние от реза сталь отпустится и отпустится ли вообще. До этого делал в основном из быстрореза и таких вопросов не возникало. Просто на наждаке довольно долго снимать 1.5 см закаленой пластины.
Veger 14-12-2011 15:38Без фанатизма, с водой. Контроль пальцами - очень горячо это около 70 гр.
Сургутянин 14-12-2011 15:54Поливать водой почаще, и отрезАть со стороны будущего обуха.
Младшший 14-12-2011 16:07возьмите диск 1,2 мм. или 0,8 мм. он и режет быстрее, и греет соотв. меньше.
vekt1or 14-12-2011 17:51опрыскивание водой ,налитой в пульверизатор для глажения белья,облегчает процесс охлаждения заготовки в разы.Проверено Сержантом и мной лично
ТЁМА Минск 14-12-2011 20:33quote:Originally posted by Младшший:возьмите диск 1,2 мм. или 0,8 мм. он и режет быстрее, и греет соотв. меньше. Тогда я бы сказал так: возьми 0,8 или 1,0. Будет резать быстрее, чем 1,2 или 1,6, и тем более, чем 2,0.
пользую пульверизатор для опрыскивания цветов из касторамы, там воздух насосом нагнетается, нажимаешь рычаг и струей поливаешь..... без фанатизма ни разе ничего не отпустил..
ДокВВ 14-12-2011 21:25резать с обуха. самым тонким диском. сначала проводите по будущей линии несколько раз быстро,что б сталь не нагрелась,делаете канаву в пару мм глубиной. потом врезаеиесь в торец пластины по канаве и отрезаете. сталь даже нагреваться неуспевает.железки 2-4 мм даже нагреваться не успевают,никакой побежалости. толще надо охлаждать обязательно.
Bedalaga 15-12-2011 01:06quote:потом врезаеиесь в торец пластины по канаве Лучше не врезаться, а так и резать по канавке быстрыми проходами, периодически сбрызгивая водойTRYP 15-12-2011 01:16quote:Лучше не врезаться, а так и резать по канавке быстрыми проходами, периодически сбрызгивая водой а если еще и прижать к рихтовочной плите... плита толстая греется хуже и забирает тепло от заготовкиVarnas 15-12-2011 01:27да просто можно прижать струбицой к мокрой тряпке. Пар повалил - сниай и прополоскайв холодкой воде.
Тюменец 15-12-2011 06:39Спасибо всем откликнувшимся, буду резать аккуратно, торопится то некуда.
struk 15-12-2011 09:37через смоченную тряпочку заготовку прижать к достаточно большой железяке я к двутавру 40 прижимаю пульверизатором переодически побрызгивать и тонкий диск 0,8
Нестор74 15-12-2011 10:36откликнусь пожалуй тоже. Постоянно с этими железками работаю. почти весь свой "железный импрессионизм" на них выполнял. Проблем с отпуском не было, резал болгаркой не торопясь, брызгал водой, как уже сказали.
C_Cat 15-12-2011 10:46Самое важное место у будущего острия. А отпуск обуха при резе ИМХО - гут: "зонная анти-закалка"
Вот только на сколько хороша первичная ТО?Если нож для электрорубанка, то может быть и мягковат.
Барм 15-12-2011 11:55Я бы сказал, что тут проблема не с тем, как бы неотпустилось.Поливай водичкой и не усердствуй.А с тем, как бы ОТПУСТИТЬ.Монтаж с таким полотном без проблем только всадной.На расклеп или на гайку, хвостовик отпускается с большим трудом, многократный нагрев.А накладной монтаж, тоже проблематично получить отверстие, я применяю электролитическую эрозию(травление).Зы ТО обычно нормальное, конечно не 61 единиц, но вполне вполне...
Тюменец 15-12-2011 12:44Да монтаж предполагается всадной, а твердость по ощущениям и по отзывам здесь практикующих нормальная.
prim2005 15-12-2011 12:54quote:А с тем, как бы ОТПУСТИТЬ.Монтаж с таким полотном без проблем только всадной.На расклеп или на гайку, хвостовик отпускается с большим трудом, многократный нагрев.А накладной монтаж, тоже проблематично получить отверстие, я применяю электролитическую эрозию(травление).Зы ТО обычно нормальное, конечно не 61 единиц, но вполне вполне...Со сверловкой никаких проблем, сверлится пером для стекла и кафеля. Подробности в теме "Сверлим быстрорез"ТЁМА Минск 15-12-2011 15:12quote:Originally posted by C_Cat:Если нож для электрорубанка, то может быть и мягковат.Кстати, да. Я делал, но только из 9ХФ. Носил на твердомер, оказалось 48-50 единиц всего. Не факт, что все ножи такие. Видел, мужик на барахолке продаёт 65Г ножи, и табличку выставил "55 единиц"
найди отрезной вулканит.даже водой поливать не надо будет)) на сухую не горит. проверено))
Нестор74 15-12-2011 17:36quote:Если нож для электрорубанка, то может быть и мягковат.а это смотря когда сталюку изладили. Будучи начинающим сделал из такой полосы по неопытности, получился нож, которым очень хорошо разве что повидло резать, в крайнем случае масло, но только не мёрзлое

ее довольно трудно отпустить-смотрите диаграмму отпуска.. вкратце до 400 греть можно спокойно
quote:Originally posted by Миха_А:Летом в инструментальном магазине купил пару ножей для эл.рубанка, но надолго отложил.надо чтоб ГМЗ было написано или НМЗ их 8х6нфт тока в нижнем вроде делалиТюменец 19-12-2011 12:12Пластина 610*40*3 завернута в промасленную бумагу, 450 руб. Эта маркировка "правильная"?
на мою похожа, она скорее всего. шоркните надфилем по обуху, всё ясно станет.
влад-ч 19-12-2011 15:43Отрезные круги по нержавейке грызут каленку быстрее и греют меньше.
Sagamore 19-12-2011 18:29quote:Originally posted by Нестор74:Вот с такой и работаю, приходится караулить на рынке у старьевщиков, когда попадается - покупаю. Раз наткнулся на одного деда, у него такой сталюки дохренаПрактически моя история


она с ГМЗ. твердость 58-61 на них как правило. резать любой металл для нашего дела рекомендуюю миллиметровым кругом метабо(рублей 60 за 125 размер)
papay1975 19-12-2011 23:20Sagamore
А что за дедок и на каком рынке?Надо свои запасы стали пополнить,но пока не нашел где.
Chipper 20-12-2011 03:53В зимнее время года могу посоветовать использовать снег :-). Крепим заготовку на бруске струбциной, обкладываем снегом и вперед. Главное не торопиться...
guns.allzip.org
Закалка, отжиг, отпуск — Сделай сам – портал самодельщиков
Часто приходится сталкиваться с необходимостью повысить прочность и твердость металла или готового изделия, иногда же, наоборот, желательно сделать металл более мягким, легче поддающимся обработке. И в том, и в другом случае нужный эффект достигается термической обработкой, заключающейся в нагреве материала до определенной температуры с последующим быстрым (или медленным) охлаждением. Таким образом, путем изменения режима термической обработки удается получать различные физико-механические свойства металлов. К основным операциям термической обработки относят отжиг, нормализацию, закалку и отпуск (рис.).
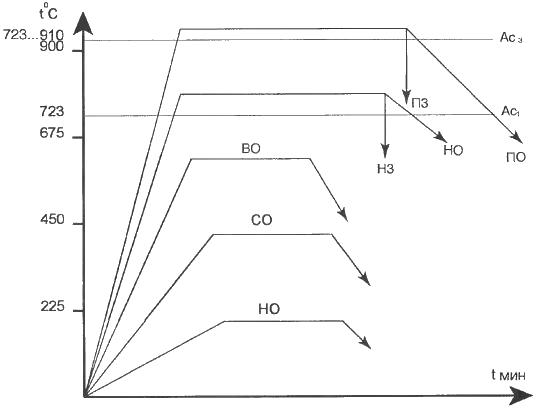
Режимы термической обработки: ПЗ и ПО - полные закалка и отжиг; НЗ и НО - неполные закалка и отжиг; ВО, СО и НО - высокий, средний и низкий отступ соответственно
Как известно, термической обработке с целью изменения структуры и свойств подвергают многие металлы и их сплавы. Например, чтобы восстановить пластичность сплава на основе меди, подвергнутого холодной деформации, сплав подвергают отжигу. Правда, другой вид термической обработки - закалка для многих медных сплавов невозможен. Но здесь мы не будем говорить о термообработке цветных металлов, а рассмотрим (очень коротко!) технологию термической обработки стали (ее основных видов). Сразу поясним, что сплавы на основе железа (то есть стали), содержащие от 0,02 до 0,8% углерода, называют доэвтектоидными, сталь с 0,8% - эвтектоидной, а сплавы, где присутствует от 0,8 до 2,14%С - заэвтектоидными. Еще в тексте упомянуты температуры АС1 и АС3, значения которых для конкретной марки стали можно найти в любом соответствующем справочнике.
Отжиг заключается в нагреве стали (доэвтектоидной - выше температуры АС3, а заэвтектоидной - выше температуры АС1) с последующим медленным охлаждением вместе с печью. Если нагреть доэвтектоидную сталь выше АС1, но ниже АС3, то полной перекристаллизации металла не произойдет. Такую термическую обработку называют неполным отжигом, который применяют для улучшения обрабатываемости резанием доэвтектоидных сталей (см. таблицу 1). Подобный отжиг конструкционных легированных сталей проводят при 750...770°С с последующим охлаждением со скоростью 30...60°С/ч, причем чем выше легированность стали, тем медленнее ее охлаждение. Отжиг снижает твердость и повышает вязкость стали, улучшает ее обрабатываемость и стабилизирует физические свойства.
Таблица 1. Режимы отжига
Нормализация отличается от отжига повышенной скоростью охлаждения, которое проводят не в печи, а на воздухе (спокойном или движущемся). Нормализацию осуществляют для размельчения зерна металла и повышения прочности последнего. Эффект, получаемый от нормализации, зависит от состава стали. Для низкоуглеродистых сталей нормализацию применяют вместо отжига. Нормализация с целью размельчения зерен обеспечивает большую производительность при последующей обработке металла резанием, а также позволяет получить более чистую поверхность обрабатываемых деталей. Нормализацию с последующим высоким отпуском (при температуре 600...650°С) часто используют для исправления структуры легированных сталей, применяя ее вместо полного отжига, так как производительность этих двух операций (нормализации и отпуска) выше, чем одного отжига.
Закалка заключается в нагреве стали на 30...50°С выше температур АС3 (для доэвтектоидных сталей) или АС1 (для заэвтектоидных сталей), некоторой выдержке металла при соответствующей температуре для завершения фазовых превращений и последующем его охлаждении со скоростью выше критической. При нагреве стали выше температуры АС3 закалку называют полной, при нагреве выше АС1 (на 30...50°С) - неполной. Неполную закалку (НЗ) для доэвтектоидных сталей, как правило, не применяют, а используют ее главным образом при термической обработке инструментальных сталей (см. таблицу 2). Охлаждение углеродистых сталей проводят чаще всего в воде, а легированных - в масле или в других средах. Закалка не является окончательной операцией термической обработки. Дело в том, что в результате закалки сталь приобретает хрупкость и в ней возрастают внутренние напряжения. Чтобы избавиться от того и другого, сталь после закалки обязательно отпускают. Инструментальную сталь, в основном, подвергают подобной термообработке (закалке и отпуску) для повышения твердости, износостойкости и прочности, а конструкционную - как для увеличения прочности и твердости, так и для придания ей достаточной высокой пластичности и вязкости.
Таблица 2. Режимы закалки
Охлаждение при закалке не должно вызывать закалочных дефектов: трещин, деформаций, коробления и возникновения высоких растягивающих остаточных напряжений в поверхностных слоях. Чаще всего для закалки используют кипящие жидкости: воду, водные растворы солей и щелочей, масла. Вода как охлаждающая среда имеет существенные недостатки: с одной стороны, высокая скорость охлаждения воды нередко приводит к образованию закалочных дефектов; с другой стороны, с повышением температуры ее закалочная способность резко ухудшается. Наиболее высокой и равномерной охлаждающей способностью отличаются холодные 8...12%-ные водные растворы соли или едкого натра, которые хорошо зарекомендовали себя на практике.
Легированные стали закаливают в минеральном масле. Преимуществом масла является небольшая скорость охлаждения, что снижает возможность возникновения закалочных дефектов. К недостаткам масла следует отнести повышенную его способность воспламеняться (температура вспышки 165...300°С), а также довольно высокую стоимость. Температуру масла поддерживают в пределах 60...90°С (вязкость масла в этом случае оказывается минимальной).
Отпуск стали заключается в нагреве закаленной стали до температуры ниже АС1, выдержке при заданной температуре и последующем охлаждении с определенной скоростью. Отпуск является окончательной операцией термической обработки, в результате которой сталь приобретает оптимальные механические свойства (см. таблицу 3). Кроме того, отпуск полностью или частично устраняет внутренние напряжения, возникающие при закалке. Эти напряжения снимаются тем полнее, чем выше температура отпуска.
Таблица 3. Режимы отпуска
Скорость охлаждения после отпуска в значительной степени влияет на значение остаточных напряжений в металле. Чем медленнее протекает охлаждение, тем меньше становятся остаточные напряжения. По этой причине изделия сложной формы во избежание их коробления после отпуска при высоких температурах следует охлаждать медленно, а изделия из легированных сталей, склонных к отпускной хрупкости, после отпуска при 500...650°С во всех случаях следует охлаждать быстро. Различают три вида отпуска: низкий, средний и высокий.
Низкий (низкотемпературный) отпуск проводят с нагревом до 250°С. При этом снижаются внутренние напряжения в металле, повышается его прочность и немного улучшается вязкость, причем все это осуществляется без заметного снижения твердости стали. Закаленная сталь, содержащая 0,5...1,3% углерода, после низкого отпуска сохраняет твердость в пределах HRC 58...63, а следовательно, характеризуется высокой износоустойчивостью. Однако такое изделие (если оно не имеет вязкой сердцевины) не выдерживает значительных динамических нагрузок. Низкотемпературному отпуску подвергают режущий и измерительный инструмент из углеродистых и низколегированных сталей, а также детали, претерпевшие поверхностную закалку, цементацию. Продолжительность отпуска обычно 1...2,5 ч.
Средний (среднетемпературный) отпуск ведут при температуре 350...500°С. Применяют этот отпуск, главным образом, при термообработке сталей для пружин и рессор. В результате подобного отпуска обеспечиваются высокие пределы упругости и выносливости металла. Твердость стали HRC 39...44.
Высокий (высокотемпературный) отпуск осуществляют при температуре 500...600°С. Высокий отпуск обеспечивает у стали наилучшее соотношение прочности и вязкости.
Термическую обработку, состоящую из закалки и высокого отпуска, называют улучшением. Обычно улучшению подвергают среднеуглеродистые конструкционные стали, к которым предъявляются высокие требования по пределам текучести и выносливости, а также по ударной вязкости. Улучшение значительно повышает конструктивную прочность стали, уменьшая чувствительность к концентраторам напряжений, развитию трещин, снижает температуру верхнего и нижнего порога хладколомкости. Отпуск при температуре 550...600°С почти полностью снимает остаточные напряжения, возникающие при закалке.
Уже многие годы при термообработке стальных изделий я пользуюсь приведенными таблицами, составленными в студенческие годы при написании курсового проекта. Думаю, что они могут быть полезными и другим мастеровым людям.
В заключение немного о маркировке и классификации сталей по назначению. Единой мировой системы маркировки сталей не существует. В России марки углеродистой стали обыкновенного качества обозначаются буквами Ст и номером (Ст0, Ст1, Ст2 и т.д.). В данном случае цифры обозначают порядковый номер стали. В зависимости от особенностей производства эти стали получают тот или иной индекс. Например, СтГпс - полуспокойная сталь с повышенным содержанием Mn. Качественные углеродистые стали маркируют двузначными числами, показывающими среднее содержание в них С в сотых долях процента: 05, 08, 45 и т.д. Инструментальные углеродистые стали обозначают буквой У с цифрами (У7, У8, У10 и т.д.), где цифры - содержание углерода в десятых долях процента. Обозначение легированных сталей включает в себя буквы, указывающие, какие компоненты входят в состав стали, и цифры, характеризующие их содержание. Заметим, что первые цифры марки обозначают среднее содержание в стали С, причем у конструкционных сталей это содержание дано в сотых долях процента, а у инструментальных и нержавеющих - в десятых долях процента. Так, сталь марки 3X13 содержит 0,3%С и 13%Cr. При этом, если содержание легирующего элемента не превышает 1,5%, то цифра за соответствующей буквой не ставится. О применении тех или иных сталей можно судить по таблице 4.
Таблица 4. Классификация сталей по назначению и рекомендуемые режимы окончательной термической обработки
homemade-product.ru