- получение эксплуатационных свойств наподобие повышения прочности, снижения напряжения металла, упрочнения сварных швов и прочее. Используется при производстве, например, нефтяных трубопроводов, газопроводов, котлов;
- формирование определенной структуры и появление качеств, необходимых для дальнейшей отделки – например, легкость в механической обработке. Востребовано в машиностроении;
- восстановление пластичности – требуется для дальнейшей деформации. Такой операции подвергают изделия на промежуточной стадии изготовления;
- образование диффузионной связи в многослойных, свертных паяных трубах, в биметаллических с тем, чтобы увеличить надежность и износостойкость изделия;
- выравнивание структуры трубопровода сварного или литого с переменной геометрией – например, бурильные. Таким образом, добиваются, например, упрочнения сварных швов.
- технологический отжиг – при холодной обработке стали в какой-то момент дальнейшее воздействие становится невозможным: твердость превышает пластичность. Чтобы вновь сделать сплав пригодным для упрочнения, материал прогревают до температуры, при которой пластичность металла увеличивается. Как правило, это низкие докритические величины, так что отжиг, в целом, оказывается достаточно дешевой процедурой;
- отжиг перед штамповкой – горячекатаная сталь при резке, рубке, штамповке может давать трещины. Чтобы этого избежать, сплав нагревают до температуры меньше температуры плавления, выдерживают и остужают;
- отжиг перед резкой – процедура проводится на станках при разных режимах, это определяется типом стали;
- отжиг – изделия, получаемые на станках, редко когда подвергаются этой процедуре. А вот изделия из высокоуглеродистых сталей перед формовкой, гибкой следует отжигать при низкой температуре, чтобы снизить твердость сплава.
- Нормализация с отпуском – производств для снятия различных видов напряжения металла. Отпуск может производиться при низкой – до 250С, средней – до 300. С, и высокой температуре – выше 500 С.
- Закалка – наиболее дорогостоящий способ. Обработка торцов труб или всего изделия производится при высокой критической температуре и быстро охлаждается. Цель процедуры – увеличение твердости, прочности изделий и снижение пластичности. Производится закалка в специальных печах, где удерживается температура от 800. С до 1300 С.
Восстановление или изготовление резиновых патрубков. Обработка патрубков
Обработка труб термическая, механическая от коррозии
Термическая обработка трубы – завершающая стадия изготовления металлопроката. Сталь – сплав очень сложный и неоднозначный. Механическая или температурная процедура позволяет придать изделию иные свойства и устранить некоторые недостатки. Производится процедура с самыми разными целями.
Назначение термической обработки
Такой вид воздействия на уже готовые металлические изделия, позволяет достичь нескольких целей:
Отделка стальной трубы может быть разной. Так, упрочнению подвергается все изделие целиком, а для повышения способности к соединению, например, процедуре подвергаются только торцы, с тем, чтобы улучшить качество кромки.
Термическая обработка
Труба по сравнению с другими видами металлопроката обладает рядом особых качеств: развитая поверхность, геометрические размеры, внутренняя полость, разная толщина стенок и прочее. Эти характеристики создают определенную сложность для температурных процедур. Для изделия с разной толщиной стенок и диаметром необходимо использовать различные станки.
Основные методы температурного воздействия таковы.
1) Отжиг – наиболее популярный способ увеличения прочности стальных изделий. Проводится отжиг на самых разных стадиях. Классифицируется именно по этому признаку:
2) Нормализация – по сути дела, это перекристаллизация под действием определенной температуры, которая позволяет получить необходимые физические свойства изделия из стали более дешевой марки. Выполняется операция после прокатки, когда трубопровод уже потемнел. При этом крупнозернистая и неоднородная структура сплава меняется, становясь более однородной. Соответственно, обретает более высокую прочность.
После нормализации изделия охлаждают. Скорость охлаждения также определяют качества трубопровода: предел прочности высаженных концов увеличивается на 4,5%, предел текучести – на 5,4%, ударная вязкость – на 17%.
Все виды термических операций повышают стойкость сплавов к коррозии. Однако специально для улучшения антикоррозийных свойств ни отжиг, ни закалка не производятся.
Механическая обработка трубы
По сути, все их разнообразие сводится к 3 операциям: перерезка, нарезание резьбы и изгибание. Все такого рода работы осуществляют на специальных машинах, однако при небольшом диаметре допускается и использование ручного инструмента. В качестве способа улучшить защиту от коррозии, такая процедура не применяется. Более того, после нарезки и сгибания требуется отделка торцов и кромки, а также покраска изделия.
Предварительным этапом служит разметка. Отмечают ту длину, которую должна иметь стальная труба после нарезки, а не до. Дело в том что при соединении фрагментов трубопровода они входят друг в друга на длину конца и резьбу, соответственно, их фактическая длина оказывается меньше.
Для разметки можно применять мерное устройство.
trubygid.ru
Оборудование для наружной обработки труб

Дробеметные машины с маркировкой «ДК-Р» предназначены для удаления коррозионных образований и окалин. Оснащение машин предусматривает удаление остатков абразивных частиц, оставшихся после процесса обработки. Их удаление происходит при помощи системы обдува и щеток.
В дробеметах с верхним положением турбин при подаче по рольгангу изделия получают вращение. В процессе обработки труб, данная особенность обеспечивает качественную обработку всей площади поверхности, т.к. абразивное сечение, создаваемое турбинами, имеет угол в 180 град. Рабочая камера в дробеметах подобного типа способна единовременно пропускать только по одному изделию.
В дробеметах с круговым расположением турбин, благодаря абразивному сечению в 360 град., отсутствует необходимость вращения изделий. Рабочая камера такого дробемета одновременно может пропускать несколько изделий.
Оборудование для удаления абразива с запорной арматуры и фитингов
Обработка запорной арматуры может выполняться различными типами пескоструйного оборудования, в зависимости от массы и габаритов изделий. Малогабаритные заготовки с небольшой массой или элементы, требующие деликатную обработку, подвергаются обдуву в эжекторных камерах вида «АК-300, АК-400». Запорная арматура с более высоким показателем массы обрабатывается в камерах напорного вида «АКН и АКН-О».
Купить пескоструйное оборудование для обработки труб можно в компании «Термал-Спрей-Тек». Здесь вы найдете широкий модельный ряд оборудования, которое сертифицировано по ГОСТ и соответствуют самым строгим требованиям эффективности и безопасности.
Оборудование для обработки труб изнутри
Для обработки поверхности внутри остовов нефтяных насосов длиной до 9000 мм, еще до нанесения защитного покрытия, используется комплекс автоматизированного типа АКН-305-В4А. Очитка поверхности выполняется штангой с сопельным узлом, адаптированным под необходимый диаметр трубы, каретка обеспечивает движение штанги, напорная установка нужна для подачи дроби к соплу под действием давления.
В приемной камере осуществляется сбор дроби, фильтр удаляет пыль из рабочей зоны. В начальном положении каретка с соплом располагается в начале установки. Деталь выкладывается на пандус. Конец трубы заводится в приемную камеру. Оператор подбирает сопло с насадкой по диаметру трубы и подает штангу в трубу. Происходит процесс удаления ржавчины, при этом каретка с соплом двигается вдоль трубы. Сопло имеет форму струи на 360 град.
После завершения процесса, каретка с соплом устанавливается в исходное положение. Затем, происходит этап продувки. Заготовка снимается с пандуса и заводится на повторный цикл. Контроллер «Siemens» отвечает за автоматический режим и наладку параметров.
Для очищения внутренней поверхности трубы с диаметром до 530 мм используются установки АКН-308-В4А. В автоматизированном комплексе такого типа, напорные бочки двигаются вместе со штангами. Благодаря этому, существенно снижаются потери при разгоне абразива. Приемная камера осуществляется сбор дроби, фильтр располагается на одной подвижной платформе с приемной камерой.
o-trubah.com
Восстановление или изготовление резиновых патрубков.
На многих редких или старых мотоциклах, да и автомобилях тоже, резиновые патрубки со временем начинают дубеть и трескаться. И если для транспорта свежих готов выпуска, можно легко приобрести новую резиновую деталь в магазине, то для аппаратов древних годов выпуска, или просто редких (антикварных) моделей, резиновые детали не так то просто найти в магазине, тем более в глубинке. Можно конечно изготовить новый патрубок из куска шланга, подходящего диаметра, но многие патрубки имеют в сечении не простую форму (например в форме ступеньки, или загиба), поэтому обычный прямой шланг здесь не подойдёт. Предлагаю довольно простой способ восстановления резиновых деталей в домашних условиях, и причём не только восстановление старых, но и изготовление новых деталей.
Для работы потребуется медицинский бинт, или лучше тонкая стеклоткань, и качественный силиконовый герметик, устойчивый к бензину и маслу. Очень рекомендую использовать качественный герметик «Виктор рейнз», который при застывании превращается в бензо-маслостойкую резину.
Ремонт резинового патрубка довольно прост: повреждённый патрубок зачищаем мелкой наждачной бумагой, зачищая также дыры или трещины, затем обезжириваем его с помощью антисиликона (он не растворяет резину) и обмазываем подготовленный патрубок тонким слоем герметика, причём заполняем также дыры и трещины (там где дыры, заклеиваем их изнутри скотчем, он не позволит герметику выступить во внутрь патрубка, а когда герметик высохнет, то скотч убираем). Работаем в медицинских латексных перчатках. Далее, пока герметик не высох, обматываем патрубок заранее отрезанной узкой (ширина примерно 2 см) лентой тонкой стеклоткани, виток к витку.
Стеклоткань закрепляем в конце патрубка например с помощью прищепки. Стеклоткань пропитывается герметиком, но всё равно нужно сверху нанести ещё один или два слоя герметика. Остаётся дождаться когда герметик высохнет и затем подрезать лишний кусок стеклоткани (там где она была зажата прищепкой). В итоге у вас получится армированный стеклотканью прочный патрубок,, который не смотря на то, что станет чуть толще, будет выглядеть как новый. При желании верхний слой высохшего герметика можно шлифануть наждачной бумагой (а можно и подкрасить краской для резины, она продаётся для подкраски шин).
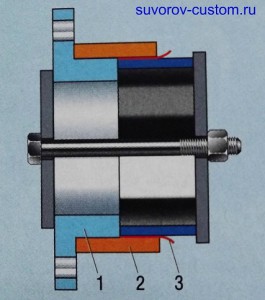
Изготовление нового резинового патрубка: 1 — фланец для крепления к цилиндру, 2 — стеклоткань с герметиком, 3 — клеёнка.
Если же ваш патрубок сильно старый и порванный и буквально рассыпается в руках, то можно изготовить новый. Для этого нужно снять с цилиндра двигателя металлический фланец (на рисунке он голубого цвета), и притянуть его с помощью двух шайб и длинного тонкого болта к патрубку карбюратора. Смотрим рисунок и всё станет понятно, только на рисунке карбюратор не показан, а вместо него нарисована синяя трубка. Карбюратор для этой цели надо будет разобрать, удалив на время ремонта заслонку с иглой, чтобы они не мешали вставить болт.
Также не забудьте прежде чем обмазывать герметиком патрубки карбюратора и фланца, патрубок карбюратора обмотать тонкой клеёнкой (можно вырезать из целофанового пакета), прослойка из клеёнки показана на рисунке красным цветом, и она не позволит карбюратору приклеится к новому патрубку, а значит карбюратор можно будет всегда снять без проблем.
Когда всё это дело стянете с помощью болта, гаек и шайб, можно будет обмазывать детали герметиком и обматывать стеклотканью по методике описанной выше. Только при изготовлении нового патрубка, намотайте не один, а два слоя стеклоткани (между каждым слоем ткани — слой герметика), ну и в конце нанесите слой герметика потолще. После высыхания герметика, можно будет вытащить карбюратор, затем шлифануть новый патрубок наждачной бумагой и при желании подкрасить. Останется надеть на новый патрубок стяжные хомуты, вставить карбюратор и стянуть хомуты. И новый патрубок из армированого стеклотканью прочного материала готов.
Ну а если ваш патрубок имеет ступенчатую или кривую форму (с загибом), или имел, но рассыпался, то придётся склеить его макет из бумаги или картона (можно использовать при работе скотч), ну а затем уже этот макет примерить на мотоцикле, и если его форма подойдёт по месту, то останется макет обмазать герметиком, и армировать стеклотканью как описано выше в тексте. Надеюсь у вас получится. Удачи!
suvorov-castom.ru
Способ изготовления патрубков
Изобретение относится к обработке металлов давлением, в частности к листовой штамповке, и может быть использовано в различных отраслях машиностроения при изготовлении патрубков. Цель изобретения - экономия металла за счет уменьшения технологического припуска и снижение трудоемкости изготовления. Листовую заготовку 1 выполняют с выступами в зоне наименьшей деформации А. Затем заготовку укладывают на прижим 2 в матрицу, фиксируют выступами в пазах прижима, штампуют элемент патрубка. Далее обрезают выступы, производят сварку патрубка из двух элементов. 6 ил.
СОЮЗ СОВЕТСНИХ
СОЦИАЛИСТИЧЕСНИХ
РЕСПУБЛИК (11 4 В 21 С 37/28
ОПИСАНИЕ ИЗОБРЕТЕНИЯ
Н А ВТОРСКОМ,Ф СВИДЕТЕЛЬСТВУ
ГОСУДАРСТВЕННЫЙ КОМИТЕТ
ПО ИЗОБРЕТЕНИЯМ И ОТКРЫТИЯМ
ПРИ П НТ СССР (21) 4276748/25-27 (22) 06)07,87 (46) 30.08.89. Бюл. М 32 (71) Проектно- конструкторский, технологический, экспериментальный институт машиностроения (72) В.М,Чеканов, С,П.Нефедов и Л.В.Турукин (53) 621.774.72(088.8) (56) Авторское свидетельство СССР
У 370993, кл. В 21 С 37/28, 1971. (54) СПОСОБ ИЗГОТОВЛЕНИЯ ПАТРУБКОВ (57) Изобретение относится к обработке металлов давлением, в частности к
„,Я0„„3 503926 А 1
2 листовой штамповке, и может бйть ис- . пользовано в различных отраслях машиностроения при изготовлении патрубков, Цель изобретения — экономия металла за счет уменьшения технологического припуска и снижение трудоемкости изготовления. Листовую заготовку 1 выполняют с выступами в зоне наименьшей деформации А.Затем заготовку укладывают на прижим 2 в .матрицу, фиксируют выступами в па,зах прижима, штампуют элемент патрубка. Далее обрезают выступы, производят сварку патрубка из двух элементов
6 ил, 1503926
Изобретение относится к обработке металлов давлением, в частности к листовой штамповке, и может быть использовано в различных отраслях ма— шиностроения при изготовлении патрубков.
Цель изобретения — экономия металла за счет уменьшения технологического припуска и снижение трудоемкости 10 изготовления.
На фиг,1 представлена исходная листовая заготовка с выступами в soне наименьшей деформации А; на фиг,2формовка элемента патрубка в штампе: 15 на фиг,3 — то же, схема; на фиг,4 заготовка с обрезанным технологическим припуском; на фиг,5 — патрубок после сварки его элементов; нафиг.6 то же, вид сбоку, 20
Способ осуществляется следующим образом.
Hs листа или полосы производят вырубку исходной заготовки с двумя выступами, расположенными с двух сторон в зоне наименьшей деформации (фиг. 1). Вырубленную заготовку 1 укладывают на прижим 2 и матрицу 3 и фиксируют выступами в пазах прижи ма.. Пуансон 4 прижимает к прижиму и деформирует деталь (фиг,2 и 3). На заключительной операции обрезают выступы (фиг.4), после чего производят сварку двух половинок патрубка (фиг.5 и 6).
Пример. Исходную заготовку толщиной 2 мм вырубают с выступами в месте контакта прижима и пуансона. Выступ имеет ширину 3 мм и высоту ( мм. Заготовку помещают в штамп заt жимая по выступам. Формуют полупатрубок, обрезают выступы и сваривают готовый патрубок из двух элементов, Формула изобретения
Способ изготовления патрубков. путем получения листовой заготовки с технологическим припуском, зажима заготовки по этому припуску, формовки, обрезки припуска и сварки элементов патрубка, отличающийся тем, что, с целью экономии металла за счет уменьшения технологического припуска и снижения трудоемкости изготовления, технологический припуск выполняют в виде по крайней мере двух выступов, расположенных в зоне наименьшей деформации, а формовку осуществляют за один переход.! 503926
Составитель Е,Гурьева
Редактор Т.Парфенова Техред M.Êîäàíè÷ Корректор Л.Бескид
Заказ 5184/12 Тирам 693 Подписное
ВНИИПИ Государственного комитета по изобретениям и открытиям при I KHT СССР
113035, Москва, Ж-35, Рауаская наб., д. 4/5
Производственно-издательский комбинат "Патент", г. Уигород, ул. Гагарина, 101



Похожие патенты:
Изобретение относится к обработке металлов давлением ,в частности, к штамповке эластичной средой, и может быть использовано в различных отраслях машиностроения при изготовлении деталей из трубчатых заготовок
Изобретение относится к обработке металлов давлением и может быть использовано при производстве отводов методом горячей протяжки трубных заготовок
Изобретение относится к обработке металлов давлением, в частности к пневмотермической формовке заготовок в состоянии сверхпластичности) и может быть использовано в различных отраслях машиностроения при изготовлении труо ocfuoii ({ Jp- - bi
Изобретение относится к обработке металлов давлением, а именно к заготовкам для получения крутоизогнутого патрубка с фланцем, и может найти применение в машиностроительной, авиационной и других отраслях промышленности
Изобретение относится к кузнечнопрессовому оборудованию, а именно к конструкциям штамповочных оправок, используемых при штамповке фитингов из трубных заготовок жидкостью
Изобретение относится к машиностроению , в частности к конструкции оборудования для обработки труб большого диаметра
Изобретение относится к технологии гибки труб и позволяет получать качественные трубные колена, а также уменьшать их вес при сохранении несущей способности
Изобретение относится к обработке металлов давлением
Изобретение относится к машиностроению и может быть использовано при изготовлении угольников различных трубопроводных систем
Изобретение относится к обработке металлов давлением, в частности к устройствам стесненного изгиба с осевым сжатием трубчатых заготовок, и может быть использовано при изготовлении крутоизогнутых угольников в строительстве, машиностроении и других отраслях промышленности
Изобретение относится к обработке металлов давлением, в частности к способам гибки трубчатых заготовок, совмещенной с вытяжкой, и может быть использовано при изготовлении крутоизогнутых угольников в различных отраслях машиностроения
Изобретение относится к обработке металлов давлением и может быть использовано при изготовлении трубных изделий типа емкостей тороидальной формы, змеевиков, крутоизогнутых колен
Изобретение относится к обработке металлов давлением, в частности к способам изготовления крутоизогнутых отводов
Изобретение относится к машиностроению и может быть использовано для изготовления отводов
Изобретение относится к области механической обработки давлением цилиндрических поверхностей и может быть использовано для получения неразъемных соединений, например фланцев с переходниками и переходников с трубами
Изобретение относится к обработке металлов давлением, а именно к способам формообразования полых изделий из трубных заготовок
Изобретение относится к обработке металлов давлением, а именно к способам формообразования полых изделий из трубных заготовок
Изобретение относится к обработке металлов давлением, в частности к листовой штамповке, и может быть использовано в различных отраслях машиностроения при изготовлении патрубков
www.findpatent.ru
Устройство для механической обработки поверхности сваренных патрубков
ОП ИСАНИЕ
ИЗОБРЕТЕН ИЯ ") 578I63
Союз Советских
Социалистических
Республик .. .. (6!) Дополнительное к авт. свид-ву— (22) Заявлено 08.06.72 (21) 1797454/25-8 (51) М. Кл е В 23 В 5/12
В 210 43/00 с присоединением заявки ¹ 1797455/25-8
Государственный комитет
Совета Министров СССР ао делам изобретений и открытий (23) Приоритет— (43) Опубликовано 30.10.77. Бюллетень ¹ 40
145) Дата опубликования описания 02.12.77 (53) УДК 621.941.279-229.2 (088.8) (72) Авторы изобретения
3 I"
H. Н. Зорев, Л. Я. Кадигробов, Н. Г. Титова и И, И. Петрушина
Центральный научно-исследовательский институт технологии: машиностроения (71) Заявитель (54) УСТРОЙСТВО ДЛЯ МЕХАНИЧЕСКОЙ ОБРАБОТКИ
ПОВЕРХНОСТИ СВАРЕННЫХ ПАТРУБКОВ
Изобретение может найти применение при обработке патрубков.
Известны устройства для обработки патрубков в месте их сварного шва, помещаемые в патрубок и выполненные в виде поддерживаемого опорами корпуса с инструментом, снабженным приводом.
Цель изобретения — расширение возможностей обработки поверхностей патрубков в стесненных условиях.
Для этого корпус предлагаемого устройства выполнен составным из двух частей, поддерживаемых опорами и соединенных подшипником скольжения, причем одна из его частей установлена в опоре жестко, а другая — с возможностью вращения и несет выдвижной инструмент.
На фиг. 1 схематически изображено предлагаемое устройство, разрез; на фиг. 2 — вариант устройства, позволяющего разрезать цилиндрические патрубки изнутри в месте сварного шва.
Устройство помещается между патрубками 1 и 2 с помощью разжимных самоцентрирующих патронов 3 и 4, несущих подвижную оправку 5 (см. фиг. 1) с суппортом 6 для крепления режущего инструмента 7, и электродвигатель 8. Подвижная оправка 5 обхватывает неподвижный корпус 9 планетарного редуктора и соединена с его выходным ва2 лом 10 посредством водила 11 с зубчатыми колесами 12, входящими в зацепление с внутренним зубчатым колесом 13 оправки 5. При этом на ходовом винте 14 суппорта6укреплена звездочка 15, взаимодействующая с неподвижным упором 16 корпуса 9 планетарного редуктора и служащая для осевой подачи режущего инструмента 7.
Подвижная оправка 5 сопрягается с вы«одным валом планетарного редуктора посредством радиально-упорных подшипников 17, а с наружной поверхностью неподвижного корпуса 9 — посредством укрепленных в нем бронзовых вкладышей 18.
Каждая из поддерживающи«опор снабжена механизмом управления кулачков, выполненным в виде червячной передачи, причем хвостовики червяков 19 выведены на торцовую поверхность опор 20.
Устройство вводится в патрубок с помощью домкрата. При этом кулачки опор сжаты, а инструментальный суппорт с ходовым винтом снят.
Устройство перемещают в осевом направ ; ленин до тех пор, пока кольцо сварного шва 21 не окажется на уровне середины направляющих скольжения суппорта 6. После этого с помощью механического ключа Вращают червяки 19, разжимают кулачки опэр предварительно, а окончательно — вручную.
Далее в направляющие скольжения помещают инструментальный суппорт 6 с ходовым винтом 14, и включают привод ходового винта, при этом предварительно вручную устанавливают вылет инструмента на суппорте.
От электродвигателя 8 вращаются шестерни 22 — 25, водило 11, на котором закреплены зубчатые колеса 12, имеющие одинаковое количество зубьев.
Из четырех зубчатых колес 12 два входят в зацепление с внутренней поверхностью корпуса 9, а два оставшихся — с внутренним зубчатым колесом 13 подвижной оправки 5.
Поскольку существует разница между зубьями колес 26 и 13 в один зуб, то подвижная оправка 5 вынуждена вместе с суппортом 6 и инструментом 7 вращаться относительно неподвижного корпуса 9.
Осевое перемещение инструмент получает после каждого оборота при взаимодействии звездочки 15, сидящей на конце ходового
578163
4 .винта 14, с неподвижным упором 15, укрепленным на жестко закрепленной в опоре части корпуса. При этом ходовой винт поворачивается на определенный угол, а инструмент перемещается в осевом, направлении.
Формула изобретения
Устройство для механической обработки щ поверхности сваренных патрубков, размещаемое в патрубке и выполненное в виде поддерживаемого опорами корпуса с инструментом, содержащим привод, о тл и ч а ю щ ее с я тем, то, с целью расширения технологических возможностей, корпус устройства выполнен составным из двух частей, поддерживаемых опорами и соединенных подшипником скольжения, причем одна из его частей установлена в опоре жестко, а другая — с возмож20 ностью вращения и несет выдвижной инструмент.
Редактор О. Юркова
Составитель Е. Макарова
Тек ред Н. Рыбкина
Корректоры Н, Федорова и А. Степанова
Заказ 7483
Подписное
410Т, Загорский филиал
Изд. № 87I Тираж !207
НПО Государственного комитета Совета Министров СССР ио делам изобретений и открытий! !3035, Москва, )К-35, Раушская наб., д, 4/5



www.findpatent.ru
Обработка стальных труб
Категория: Отопительные системы
Обработка стальных труб
Обработка стальных труб состоит из трех операций: перерезки, нарезания резьбы и изгибания. Обрабатывают трубы как на станках, так и при помощи ручного инструмента.
Прежде чем подвергнуть обработке отрезок трубы, необходимо установить ту конечную длину, которую он должен иметь после обработки.
Заготовленный для монтажа отрезок трубы с нарезанными на нем резьбами при ввертывании в фасонную часть или муфтовую арматуру не доходит до их середины, а входит в них не более чем на длину короткой резьбы. Поэтому различают чисто теоретическую длину изделия, замеренную по длине в натуре или определяемую по чертежу между центрами фасонных частей так называемую строительную длину, и фактическую длину заготовляемой детали с учетом некоторых расстояний между центрами фасонных частей и витками внутренних резьб, ближайшими к этим центрам, — так называемую монтажную длину.
Таким образом, в трубопроводе, соединяемом на резьбе, монтажная длина всегда меньше строительной. Разницу в длине называют скидом. При разметке труб для фланцевых соединений требуется давать припуск на отгибаемый борт или на разбортовку кромки отреза к фаске фланца.
С учетом указанных соображений производят разметку труб и их перерезку.
Для механизации разметки труб можно использовать специальное мерное устройство. Оно может обрабатывать трубы с условным проходом от 15 до 60 мм и длиной отмеряемых участков от 40 до 5000 мм.
При перерезке требуется, чтобы плоскость сечения по перерезу была перпендикулярна оси трубы (за исключением случаев, когда нужен скос), а кромка была чистой, без внешних и внутренних заусенцев. Внешние заусенцы могут затруднить нарезку резьбы и привести к порче нарезающий инструмент, а внутренние — сузить проход трубы и, если их много, увеличить сопротивление сети пропуску транспортируемой среды.
Ручными инструментами для перерезки труб служат ножовочные станки и роликовый труборез. Ножовочный станок перерезает трубу медленнее трубореза, но зато почти не оставляет заусенцев; труборез работает быстро, но оставляет внутренние и наружные заусенцы, которые приходится удалять.
Любой труборез, независимо от его конструкции, состоит из корпуса, режущих роликов и нажимной части. Ролики имеют чечевицеобразное сечение.
Для механической перерезки труб существуют две разновидности станков: одни действуют по принципу ручного однороликового трубореза, режущей деталью которых является режущий ролик-диск, а другие станки имеют резец, аналогичный резцу токарного станка.
Малая механизация перерезки труб диаметром 15— 50 мм осуществляется с помощью универсального построечного механизма. Механизм весит около 90 кг. Он снабжен двумя выдвижными рукоятками, посредством которых легко переносится двумя рабочими.
Гнутье труб производится как в холодном, так и в нагретом состоянии. Холодное гнутье применяют для труб диаметром от 15 до 200 мм включительно. Трубы бесшовные диаметром от 219 до 376 мм включительно гнут в нагретом состоянии. Трубы водогазопроводные больших диаметров, как правило, не гнут совсем, а необходимые отводы выполняют сваркой соответственно выкроенным сегментам.
Для гнутья холодным способом пользуются специальными станками. Гнутье горячим способом выполняют на особых трубогибочных площадках, оснащенных специальным оборудованием.
К изгибу стальной трубы предъявляются два требования: у трубы должно быть плавное очертание изгиба без переломов, здесь недопустимы ни деформации в поперечном сечении изгиба, ни разрывы по шву.
Радиус изгиба зависит от диаметра трубы и толщины ее стенки. Чем меньше радиус изгиба, тем больше металл вытягивается по выпуклой стороне отвода и тоньше становится стенка этой стороны, следовательно, труба ослабляется и одновременно больше становится сопротивление отвода движению протекающей среды, т. е. гидравлическое сопротивление. В то же время увеличение радиуса изгиба создает затруднение монтажного порядка, так как отвод получается громоздким и ось его слишком отходит от стены, на которой прокладывается труба.
Таким образом, в интересах прочности и уменьшения гидравлических сопротивлений следует гнуть трубы с возможно большим радиусом изгиба, а по монтажным условиям добиваться минимального радиуса.
Гнутая деталь — это отрезок трубопровода, на котором согнуты один или несколько отводов, расположенных в одной или нескольких плоскостях.
При изготовлении такой детали задача монтажника так определить длину прямого отрезка трубы, чтобы после выполнения на нем необходимых изгибов он приобрел точную монтажную длину, а изделие можно было свободно вмонтировать в соответствующий участок трубопровода без дополнительных отрезок и повторного нарезания резьб. Эту длину называют заготовительной.
Для определения заготовительных длин отрезков труб при гнутье составлены специальные таблицы. Для холодного гнутья труб диаметром 15, 20, 25 мм ручным способом пользуются трубогибом СТВ конструкции Вольнова (рис. 1). Он имеет неподвижный полуролик и подвижный полный ролик. Оси обоих закреплены в вилке поводка. На стержень станка насаживается труба-рычаг длиной около 1,5 м. При перезаправке станка с одного диаметра на другой необходима смена обоих роликов. Кроме одноручьевых трубогибов применяются двухручьевые. Все они крепятся к верстаку.
Механизированные трубогибочные станки работают на том же принципе с использованием соответствующих роликов и полуроликов с применением электропривода.
Какая бы форма роликов ни применялась в трубо-гибочных станках, профиль сечения по изгибу всегда в той или иной мере приобретает овальное очертание.
Устранить этот недостаток можно только путем применения особых оправок, обработанных на токарном станке и вставляемых внутрь трубы на участке изгиба.
Фигурное гнутье уточек и скоб может быть выполнено не на гибочных станках, а штампованием на фрикционных прессах.
Трубы диаметром 218 мм и выше гнут не в холодном, а в горячем состоянии. Для того чтобы предотвратить водиться. Конусная резьба, нарезаемая, как правило, за один проход, может быть также выполнена и цельной плашкой, так называемой леркой.
Рис. 2. Ключи для свертки труб
Направляющая деталь предназначена обеспечить устойчивое положение клуппа во время работы, благодаря чему предотвращается возможность перекоса резьбы.
Корпус клуппа конструируется в зависимости от типа плашек, которые должны быть надежно закреплены в плашечных гнездах корпуса.
В центральных заготовительных мастерских и монтажных заводах нарезание трубных резьб производится на специальных станках.
Для производства сборочных операций применяют трубные ключи (рис. 2), а для зажима труб — прижимы различных конструкций.
Для механического навертывания фитингов может использоваться специальный механизм, работающий от пневматической сети.
Отопительные системы - Обработка стальных трубgardenweb.ru
Обработка - стальная труба - Большая Энциклопедия Нефти и Газа, статья, страница 1
Обработка - стальная труба
Cтраница 1
Обработка стальных труб состоит из трех операций: перерезки, нарезания резьбы и изгибания. Обрабатывают трубы как на станках, так и при помощи ручного инструмента. [1]
Обработка стальных труб ( см. разд. [2]
Для обработки стальных труб различного назначения в зависимости от количества труб применяют ручной или механический инструмент, приспособления и механизмы. Так, для резки труб диаметром от / 2 до 1 применяют усиленный ручной труборез; для обработки торцов труб ( развертки и снятия внутренних заусенцев) - специальный райбер или конические развертки; для изгибания радиусов труб и уток в зависимости от диаметра труб и толщины стенки - различные гидравлические трубогибы; для изгибания радиуса труб диаметром от 1 / 2 до 2 - гидравлический ручной трубогиб или трубогиб с электрическим приводом. [3]
Технология обработки стальных труб и сборки их в транспортабельные монтажные узлы строится по принципу поточности по следующей схеме. [4]
При обработке стальных труб широко используется в электромонтажных организациях предварительная заготовка стальных ( водопроводных, газовых) труб на трубо-обрабатывающих, трубоотрезных, трубонарезных и гибочных станках и приспособлениях. Для облегчения втягивания проводов в трубы внутрь их вдувается тальк. Трубопроводы собираются в мастерских по узлам и доставляются на монтажный объект, где и производится окончательная сборка и монтаж. [5]
При обработке стальных труб широко используется в электромонтажных организациях предварительная заготовка стальных ( во допроводных, газовых) труб на трубообрабатывающих, трубоотрез-ных, трубонарезных и гибочных станках и приспособлениях. Для облегчения втягивания проводов в трубы внутрь их вдувается тальк. Трубопроводы собираются в мастерских по узлам и доставляются на монтажный объект, где и производится окончательная сборка н монтаж. [6]
Технологический процесс обработки стальных труб диаметром выше 50 мм, а также изготовление изделий и узлов из этих труб состоит из следующих операций. [7]
Технологическую линию по обработке стальных труб устанавливают в мастерских монтажных управлений, расходующих от 150 до 500 км труб в год. Линия размещается на площади 300 дг2; производительность линии 800 - 1000 м обработанных труб в смену. На линии выполняют следующие операции: разгрузку труб, складирование их по размерам, райберовку, очистку от ржавчины ( внутри и снаружи), окраску и сушку труб, их укладку, отрезку труб по размерам, нарезку труб, гибку, комплектование трубных блоков и складирование для монтажа. Все эти операции механизированы, весь процесс обработки труб осуществляется поточно. Линию обслуживают двое рабочих. [8]
Технологическая линия по обработке стальных труб обеспечивает выполнение следующих операций: складирование необработанных труб на стеллажах по сортам и размерам, окраску, сушку труб, складирование окрашенных труб на стеллажах, разметку и резку, зачистку ( раззенковку) концов труб после резки, нарезку резьбы, изгибание труб, комплектацию и маркировку. Подъем со стеллажей и транспортирование труб к месту обработки, а также движение по поточной линии, сборку трубных заготовок в пакеты и блоки выполняют с помощью электрической тали, мостового крана, вагонеток узкой колеи, рольгангов и других механизмов в зависимости от местных условий и возможностей. [9]
При современных индустриальных методах монтажа обработку стальных труб выполняют в монтажных мастерских на поточных технологических линиях. На этих же линиях производят заготовку элементов трубных разводок и сборку их в трубные пакеты, блоки, чтобы максимально сократить продолжительность работ по сборке трубных трасс на монтаже. [10]
Одновременно в мастерских монтажно-заготовительных участков на поточных технологических линиях производятся обработка стальных труб и заготовка элементов трубных проводок с последующей сборкой их в трубные пакеты, блоки и узлы. [11]
Обработка стальных труб при современных индустриальных методах монтажа выполняется в монтажных мастерских на технологических линиях. Для выполнения всех операций по обработке груб станки располагают в определенной технологической последовательности. На линиях соблюдается принцип поточности и механизации основных трудоемких операций и производятся заготовка элементов трубных разводок и сборка их в пакеты, блоки и узлы, чтобы максимально сократить продолжительность работ по сборке трубных трасс на монтаже. [12]
Пример специальной переносной машины показан на фиг. Она предназначена для обработки стальных труб, вырезки различных отверстий на поверхности труб, отрезки трубы под любыми углами к ее продольной оси, изготовления из труб фасонных частей и прочих работ. Изменяя с помощью поворотного механизма S плоскость вращения направляющей 5, можно получить любое движение резака на поверхности трубы, вырезая отверстие требуемого очертания. [13]
Существуют два способа очистки - химический и механический. Химический способ целесообразно применять при необходимости обработки стальных труб в больших количествах и наличии канализации для сброса вредных стоков. Оборудование для такой очистки промышленность не выпускает, поэтому его изготовляют различные ведомства по индивидуальным проектам. В настоящее время на МЗМ в основном используют механический способ очистки - с помощью щеток и вращающейся штанги. Существуют и другие виды механической очистки, которые разрабатываются индивидуально для конкретной базы. [15]
Страницы: 1 2
www.ngpedia.ru