- Завершение подготовки поверхности (растворение оксидов железа, заново образовавшихся на поверхности во время промывки),
- Защита поверхности деталей с помощью пассивированной пленки флюса от дальнейшего окисления стали,
- Обеспечение хорошей смачиваемости расплавленным цинком.
- Качество стали;
- Качество цинка;
- Температура цинкового расплава;
- Продолжительность погружения;
- Скорость погружения и поднятия;
- Охлаждение.
- Получение на обрабатываемой поверхности равномерного флюсового слоя.
- Подогрев изделия перед оцинковкой облегчает нагрев рабочей ванны цинкования, улучшая технологические параметры процесса.
- После сушки образуется плотная солевая пленка на обрабатываемой поверхности, которая предохраняет изделия от окисления перед цинкованием.
- улучшении внешнего качества изделия,
- увеличению эксплуатационного срока,
- устойчивости е агрессивным влияниям окружающей среды.
- Экономичность
- Доступ к труднодоступным элементам
- Погружение металла в ванну с горячим цинком
- ванны для мелкогабаритных изделий,
- ванны для обработки цинковым сплавом труб,
- ванны для крупногабаритных изделий.
- системе электронагревания,
- жидкому топливу,
- сжиженному газу,
- каменному углю.
- Данная технология применяется даже для обработки изделий сложной геометрической формы. В частности, так обрабатываются трубы.
- Поврежденные механическим воздействием участки цинкового покрытия могут восстанавливаться сами без постороннего вмешательства.
- Устойчивость покрытия при взаимодействии с жидкими средами в 6 раз выше, чем в случае с другими методами оцинковки. Поэтому к данной технологии прибегают при обработке труб и емкостей.
- Эффективно устраняются многие дефекты: поры, раковины и пр.
- Эксплуатация труб и метизов, покрытых цинком по этой технологии, требует минимум финансовых затрат. Поверхности не требуется регулярная окраска, так как уже имеется защита от негативного воздействия внешней среды. Это весьма актуально для труб, эксплуатирующихся в труднодоступных местах (под землей, в стенах).
- Обрабатываемая поверхность тщательно подготавливается.
- Изделие погружается в расплавленный цинк и в результате буквально обволакивается им.
- механическую обработку;
- обезжиривание;
- промывку;
- травление;
- промывку после травления;
- флюсование;
- просушку.
- кислотность;
- плотность;
- содержание железа.
- Наличие мощной вытяжки, удаляющей из воздуха пары, которые интенсивно образуются в процессе цинкования.
- Оборудование должно обеспечивать соблюдение скорости погружения в расплав детали и времени выдержки ее в нем.
- После извлечения из емкости обработанная деталь качественно охлаждается.
- Изделия погружаются в емкость с расплавленным цинком.
- Детали выдерживаются 4−10 мин.
- Извлечение детали из расплава, скорость выполнения которого во многом определяет толщину формируемого покрытия.
- Принудительное или естественное охлаждение.
- Навеска заготовок на траверсы. Здесь используются специальные опорные конструкции, крюки, петли из стальной проволоки ГОСТ 3282-74 (диаметр 3 и 4 мм), прокат стальной горячекатаный ГОСТ 2590-2006 (диаметр 6 мм).
- Обезжиривание. Этот процесс предполагает очистку поверхности заготовки от смазочных материалов, таких как минеральные масла и силиконовые смазочные материалы. Для этого детали помещаются в специальную емкость с обезжиривателем, температура которого поддерживается на уровне 24-26 градусов. При таких условиях продолжительность очистки варьируется от 15 до 20 минут. Чтобы ускорить процесс обезжиривания до 10 минут, температуру подымают до 28-30 градусов.
- Травление предполагает очистку поверхности детали от окалины (FeO-Fe3O4- Fe2O3) и ржавчины (FeO, Fe2O3 х nh3O). Обработка металла производится в водном растворе соляной кислоты согласно ГОСТ 857-95. Длительность травления варьируется от 20 до 90 минут, что уже зависит от концентрации компонентов и температурного режима раствора. Толщина заготовки никак не влияет на данный процесс.
- Чтобы обеспечить безопасность, во время травления обязательно производится удаление паров кислоты с помощью специальных вытяжек. Для оценки качества очистки используется только визуальная оценка.
- Флюсование производится с целью обеспечения качественного сцепления цинка поверхностью металла. Эта технология предполагает использование специальных веществ - флюсов, в качестве которых выступает смесь нескольких солей: хлористый аммоний (Nh5Cl); хлористый цинк (ZnCl2).
- После химической реакции данные вещества образуют на поверхности пленку, которая предотвращает дальнейшее окисление металла. Процесс флюсования в гальванике производится при температуре раствора 40 (используется дополнительно сушильная печь) или 70 градусов. Длительность процесса не превышает 45 секунд.
- Сушка изделия выполняется в специальной печи при температуре, не превышающей 120 градусов и продолжительности до 1 часа.
- Непосредственно горячее цинкование. Этот процесс предполагает погружение заготовки в емкость с расплавленным цинком. Раствор может легироваться алюминием с использованием сплава марки ЦА-10. Процентное соотношение этого вещества должно варьироваться от 0,05 до 0,2 % от количества цинка. Цинкование производится при температуре 450 градусов.
- Охлаждение. Данная процедура предполагает изъятие заготовки из раствора цинка и помещение ее в емкость с водой, температура которой не должна быть выше 80 градусов.
- на поверхности основного металла не допускается: закатанная окалина, заусеница, поры, включения, сварочные шлаки, остатки формовочной массы, графита, смазки, металлической стружки, маркировочной краски;
- на поверхности литых изделий не должно быть пор и усадочных раковин;
- сварочные швы должны быть равномерными, плотными и сплошными по всей длине;
- острые углы и кромки изделий, за исключением технически обоснованных случаев, должны быть скруглены радиусом не менее 0,3 мм;
- поверхность изделий, подлежащих горячему цинкованию, должна быть очищена обезжириванием, последующим травлением, затем зафлюсована;
- степень очистки поверхности от окалины и продуктов коррозии - 1 по ГОСТ 9.402-80.
- Необходимая площадь: от 1500 м2
- Стоимость: от 1.500.000 €
- Необходимая площадь: от 2200 м2
- Стоимость: от 3.000.000 €
Горячее цинкование: экономика и технология. Цинкование горячее технология
Технология процесса горячего цинкования
Как любая обработка поверхности, горячее цинкование требует правильной подготовки поверхности для того, чтобы во время погружения деталей в ванну цинкования реакция железа и цинка была однородной.
Последовательность этапов следующая: обезжиривание, промывка, травление, промывка и флюсование.
1. Обезжиривание
Назначение обезжиривания – удаление масла, загрязнений от этого зависит качество цинкования в целом. Обработка осуществляется с помощью обезжиривающего реагента, выбранного в зависимости от загрязняющего вещества, при температуре от 60 до 80°C. Удаление масляных пятен является необходимым перед этапом травления, во избежание дефектов цинкования металла таких как, например, отсутствие или расслоение цинкового покрытия.
2. Промывка после обезжиривания
Промывка должна выполняться эффективно, она позволит удалить с деталей жирные вещества и пену, оседающую на деталях из ванны обезжиривания.
3. Травление
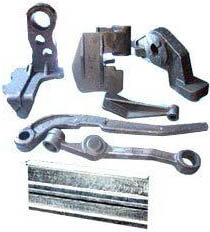
Операция травления состоит из очистки поверхности металла, посредством удаления с нее слоя оксидов, образующихся в результате горячей обработки (окалина) или неблагоприятных условий хранения (ржавчина).
Обработка выполняется с помощью соляной кислоты, имеющей концентрацию от 120 до 210 г/л, при температуре окружающей среды (20 - 25°C). Преимуществом соляной кислоты является хорошая растворимость хлоридов железа и достижение чистой блестящей поверхности и достаточной смачиваемости расплавленным цинком.
Рекомендуется добавлять ингибиторы для удаления только окислов и гидроксилов, ограничивая воздействие на основной метал и избегая риска водородного насыщения.
Правильный контроль концентрации ванны позволит оптимизировать качество обработки, расходы, выбросы и, как следствие, защиту окружающей среды. Для дефектных изделий предусмотрена ванна для удаления цинкового покрытия, которая позволяет очищать детали за счет использования отработанного раствора кислоты.
4. Промывка после травления
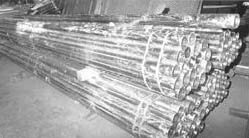
За травлением следует тщательная промывка для нейтрализации возможных остаточных следов кислоты и удаления солей. Использование нескольких последовательных промывочных ванн позволит оптимизировать промывку и сократить расход воды.
5. Флюсование
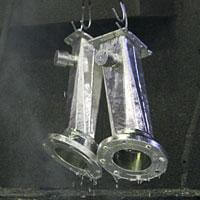
Операция "флюсование" имеет три цели:
Применяемый флюс состоит из хлорида цинка и хлорида аммония.
Обработка выполняется концентрированным раствором флюса (400 - 600 г/л) при температуре 60°C.
Раствор ванны флюсования должен периодически контролироваться (плотность, pH и содержание железа). Очистка осуществляется с помощью добавления перикиси водорода, которая непрерывно осаждает соли трёхвалентного железа на дно ванны, а далее осадок попадает в систему отстаивания и фильтрации.
6. Предварительный нагрев, сушка перед нанесением цинка
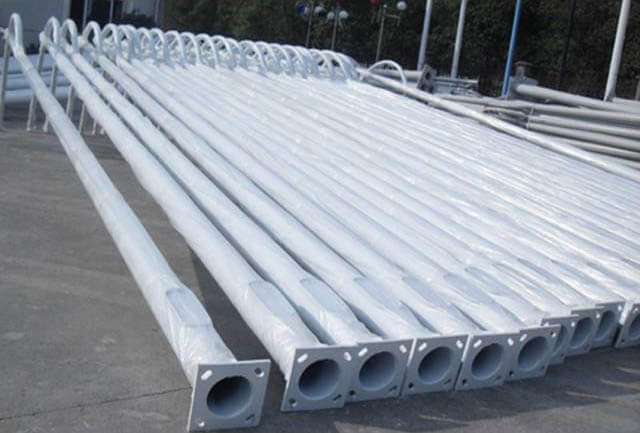
Данная операция после флюсования позволяет испарять влагу с поверхности деталей и в пустотелых элементах, во избежание выплескивания цинка парами воды во время погружения в печь и деформации деталей. Она также позволяет предварительного нагревать детали приблизительно до 100°C, что эффективность печи цинкования, экономит энергию и снижает себестоимости цинкования.
Время сушки превышает время цинкования, следовательно, сушильная печь должна иметь несколько камер (минимум 2). Принятая в расчет производительность - максимальная загрузка сушильной печи.
Загрузочное и разгрузочное устройства обеспечат своевременное перемещение садок и оптимальной нагрузке печи цинкования.
7. Цинкование
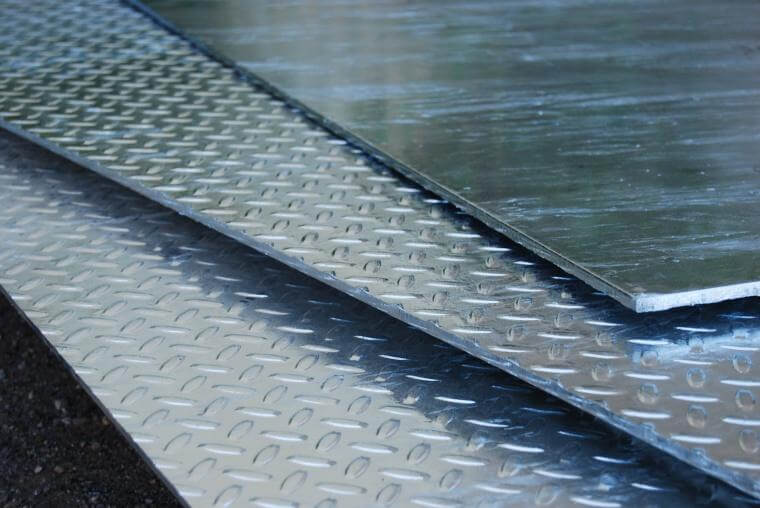
После всех предварительно описанных операций, можно считать, что контакт между сталью и жидким цинком будет обеспечен наилучшим образом.
Основные параметры успешной операции:
Температура цинкового расплава составляет 419°C, цинкование выполняется в классических пределах от 445 до 460°C, что позволяет сократить образование штейна, оксидов и т.д.
Вытяжка отходящих газов обеспечивается системой аспирации и фильтрации в полном соответствии с экологическими нормами.
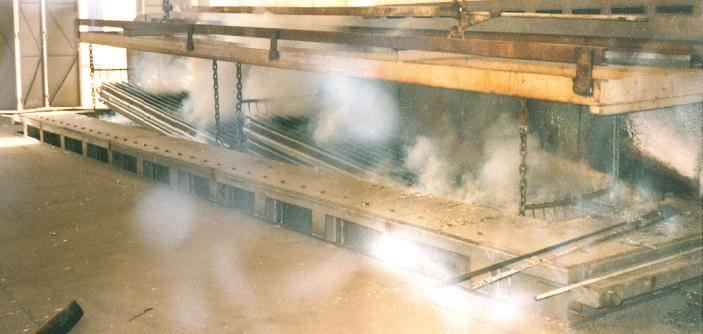
Фаза погружения:
Во время этой фазы имеют место несколько этапов: теплообмен внутри детали, расплав и разрушение флюса на поверхности деталей, приводящее к оптимальной смачиваемости расплавленного цинка.
Скорость погружения тоже является важным фактором. Слишком медленная скорость приведет к освобождению поверхности стали от пассивированной пленки с риском повторного окисления, а слишком быстрая скорость погружения приведет к захвату с поверхности остатков солей, флюс не успеет расплавится и, как следствие, это вызывает образование дефектов.
Длительность погружения:
Длительность погружения изменяется в зависимости от садки (массы, размеров, формы), в среднем от 3 до 10 мин. Перед удалением деталей необходимо удалить шлак с помощью скребка с поверхности расплава, во избежание его оседания на деталях.
Фаза извлечения из ванны:
Скорость извлечения влияет на конечную толщину полученного покрытия. Она воздействует на толщину слоя чистого цинка (мкм), связанную с растеканием цинка и скоростью отвердевания.
Скорости подбираются, исходя из производительности, длительности погружения и качеством поверхности (подтёки, капли), учитывая регулировку наклона деталей на монтаже в зависимости от их геометрии.
8. Охлаждение
Охлаждение происходит на открытом воздухе на участке складирования и хранения совмещенной с участком ОТК перед упаковкой.
galvanazing-line.ru
Технологический процесс горячего цинкования — Цинковый портал
Технологический процесс горячего цинкования — это закономерная последовательность технологических операций по предварительной подготовки металлической поверхности перед оцинковкой, цинкования, финишной обработки . Качество цинкового покрытия напрямую зависит от тщательного соблюдения технологического процесса горячего цинкования.
Предварительный этап технологического процесса горячего цинкования
1. Загрузка металлоизделий
Обрабатываемые детали закрепляются на специальном транспортном приспособлении (траверсе) при помощи проволоки. Для различных по габаритным размерам изделий используется проволока определенной толщины. Обязательным условием при горячем цинковании является наличие на каждом обрабатываемом изделии технологических отверстий для крепежа.
Схема участка горячего цинкования
2. Горячее цинкование. Обезжиривание
Процесс предварительной подготовки перед горячим цинкованием включает в себя удаление с обрабатываемой поверхности органических (жировых) и неорганических (пыль, стружка) загрязнений.

Обезжиривание изделий может производиться:
· химическим способом,
· электрохимическим методом,
·путем термической обработки (отжиг).
Химическое и электрохимическое обезжиривание производятся в водных растворах, содержащих щелочь (натр едкий), тринатрийфосфат, жидкое мыло. Поверхностно — активные вещества вводят в рабочий раствор для уменьшения коэффициента сцепления масла и жировых загрязнений с обрабатываемой поверхностью.
Состав и режим химического обезжиривания горячего цинкования
• Натр едкий – 25 г/л, • Сода кальцинированная – 50 г/л, • Тринатрийфосфат – 15г/л, • Жидкое стекло – 3 г/л.Температура рабочего раствора находится в диапазоне от 80 до 90 ° С.
Альтернативой щелочного обезжиривания при горячем цинковании может служить кислотное удаление жировых пленок и неорганических загрязнений. Основным компонентом рабочего раствора является фосфорная кислота. Рабочая температура технологической операции – 40 ÷ 50 ° С.
Электрохимическое обезжиривание
Состав рабочего раствора такой же, как и при химическом обезжиривании.
Температура электрохимического процесса – 70 ÷80 ° С.
Плотность тока – 2 ÷ 5 А/дм2.
ЭХО активно используется для удаления травильного шлама.

Недостатком электрохимического обезжиривания является:
· наводораживание поверхностного слоя, потому закаленные тонкостенные детали не следует обрабатывать таким способом;
· низкая рассеивающая способность (сложнопрофильные, рельефные изделия не очищаются должным образом в глубоких канавках и впадинах).
3. Промывка
Для удаления остатков щелочного раствора, эмульсии и других остаточных продуктов, обрабатываемые изделия тщательно промывают сначала в промывке с горячей водой, а затем в холодной проточной воде.

Следы коррозии, термическую окалину можно удалить с обрабатываемой поверхности, применяя
· химическую обработку — травление,
· механический способ.
4. Травление
При химическом удалении загрязнений с металлической поверхности в процессе горячего цинкования используются кислотные составы:
• 18 ÷ 22 % — ный водный раствор серной кислоты, • 20 ÷ 25 % — ный водный раствор соляной кислоты.
Каждый травильный состав обладает определенными специфическими свойствами.
При химической обработке в серной кислоте термическая окалина удаляется на 15 ÷ 20 % от основного объема, при травлении в соляной кислоте этот показатель увеличивается до 40 ÷ 50%.
После травления в кислотном соляном растворе поверхность имеет более гладкую текстуру, чем после обработки в серном растворе.
Травление обрабатываемого изделия в серной кислоте может привести к повреждению матричной основы («растравливанию»). Для устранения этой проблемы используют специальные ингибиторы.
Химическая обработка в соляной кислоте практически не наводораживает поверхностный слой изделия.
Для травления в серной кислоте рабочий раствор необходимо нагреть до 60 ÷ 80 °C.
Себестоимость состава травления в соляной кислоте выше, чем в серном растворе.
Отработанную серную кислоту можно использовать в дальнейшем для других технологических нужд.
Механический метод очистки
Сущность метода — воздействие на обрабатываемую поверхность мелких, дисперсионных частиц под высоким давлением.
Оборудование для очистки – дробеструйный агрегат, дробеметный аппарат.
5. Промывка
Промывка производится в проточной воде. Служит для удаления травильного раствора и остатков химического воздействия. Температура технологической операции – 25 ÷ 30°C.
6. Флюсование
Заключительная подготовительная операция перед цинкованием. Флюсование предназначено для химического удаления
• образовавшихся после травления металлических оксидов и солей с обрабатываемой поверхности, • солей с поверхности расплавленного цинка в местах соприкосновения при погружении изделия в рабочий раствор, • для улучшения параметра смачиваемости обрабатываемой поверхности расплавленным цинком при погружении (путем снижения коэффициента поверхностного натяжения цинкового расплава).
Операция по нанесению флюса может проходить двумя способами.
1. Расплавленное флюсование («мокрый» способ). Флюсовый слой находится непосредственно на зеркале расплава цинка. Обрабатываемое изделие перед оцинковкой проходит сначала безводный расплавленный флюсовый слой, а затем погружается в рабочий цинковый расплав. 2. Флюсование в специальном водном растворе с последующей сушкой. После такого способа обработки на металлической поверхности образуется слой «сухого» флюса.
Флюсовая смесь состоит из солей хлористого цинка и хлористого аммония.
Состав и режим флюсования
• раствор хлористого цинка (водный) – 150 ÷ 300 г/л. • раствор (водный) хлористого аммония — 100 ÷ 150г/л.Температура обработки – 60 °C.
7. Сушка
Сушка офлюсованных изделий позволяет решить ряд технологических вопросов.
Сушку производят в специальных камерах. Для ускорения процесса и улучшения качества обработки сушильные камеры оснащают системой рециркуляции горячего воздуха.
Продолжительность обработки и температурный режим зависят от массы обрабатываемых изделий.
Оптимальная температура поверхности после сушки находится в диапазоне от 120 до 150°C, при таком нагреве флюс не разлагается, сохраняя технологические свойства.
Горячее цинкование
1. Цинкование
При горячем цинковании обрабатываемое изделие погружают в цинковый расплав (450°C). Погружение деталей в рабочий раствор производится на большой скорости, чтобы предотвратить возможность дополнительного окисления обрабатываемой поверхности.
Скорость извлечения изделий из рабочего расплава невелика. Это дает возможность излишкам расплава стечь обратно в ванну цинкования. Чтобы получить равномерное покрытие по всей длине, на поверхности обрабатываемой детали должны присутствовать дополнительные технологические отверстия (для улучшения оттока излишков расплава).
Толщина цинкового слоя напрямую зависит от
• времени выдержки в цинковом расплаве, • температуры цинкового расплава, • скорости извлечения детали после оцинковки.
Финишная обработка технологического процесса горячего цинкования
1. Охлаждение
Обработанное изделие после оцинковки имеет температуру поверхности ~ 450°C. Охлаждение до комнатной температуры может производиться:
• на открытом воздухе, • в специальной ванне с чистой водой.
2. Разгрузка металлоизделий
Оцинкованные изделия снимаются со специального транспортного приспособления (траверсы).
Путем шлифования убираются застывшие излишки цинкового расплава.
Контролируемые параметры технологического процесса горячего цинкования — это толщина цинкового покрытия и внешний вид изделия.Готовые изделия после технологического процесса горячего цинкования пакетируются для последующей транспортировки.
www.zinkportal.ru
Горячее цинкование, технология, методы, ванна для горячего цинкования
В современном мире для покрытия металлов защитным раствором применяются различные вещества. одним из самых распространенных является цинк, который покрывает слой тонким слоем и выполняет помимо декоративной функции еще и защитную.
Горячее цинкование металлоконструкций
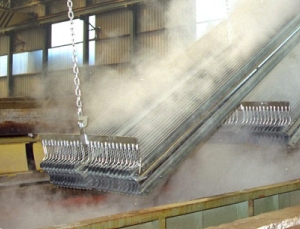
На современных промышленных предприятиях не редко используется горячее цинкование при обработке стальных материалов. Данный метод обработки представляет собой процедуру, которая заключается в погружении предметов из стальных материалов в специально разработанную емкость с расплавленным цинком. Его температура нагрева составляет не менее 450 градусов Цельсия.
Данная процедура не является сложной, если в наличии имеется необходимое оборудование. Она является проверенным методом покрытия стальной поверхности защитной пленкой, эффективность которой проверена многими годами использования. Ее толщина тщательным образом контролируется, чтобы металлу была обеспечена надежная защита от влияния окружающей среды.
Благодаря цинковому сплаву обеспечивается гораздо более долгая защита от коррозии, чем при использовании обычных методов, в числе которых и адгезия. Во время данного процесса между железным сплавом и цинковым появляется взаимодействие. Они соединяются в одно вещество. Это не просто адгезия железа к цинку. Это уже отдельное вещество, состоящее из смешивания сплавов этих двух металлов. Благодаря этому антикоррозийное свойство сохраняется на более продолжительный период времени.
Кроме придания металлу устойчивости к появлению коррозии обработка горячим цинковым сплавом придает металлу еще ряд свойств, которые проявляются в:
Главным отличием покрытия стали цинковым сплавом от всех других методов обработки является то, что этот метод защиты является более надежным. Цинк помогает контролировать появление ржавчины и других дефектов на предметах из стали. Другие же методы лишь маскируют недостатки.
Внимание: На сталь, покрытую цинковым сплавом можно нанести лакокрасочное покрытие, которое может придать не только привлекательный внешний вид с эстетической точки зрения, но и обеспечить двойную защиту металла.
Таблица 1. Сравнение показателей стоимости и срока службы стали после горячего цинкования с другими способами защиты (себестоимость принята за 100%)
Горячее цинкование | 25 | 100 | уход не требуется |
Дробеметная очистка, окраска в три слоя | 12 | 75 | 150 |
Дробесруйная очистка вручную, окраска в три слоя | 12 | 120 | 195 |
Травление и окраска в три слоя | 10 | 85 | 200 |
Очистка металлической щеткой и окраска в три слоя | 8 | 75 | 230 |
То же и окраска в два слоя | 5 | 55 | 280 |
Метод горячего цинкования
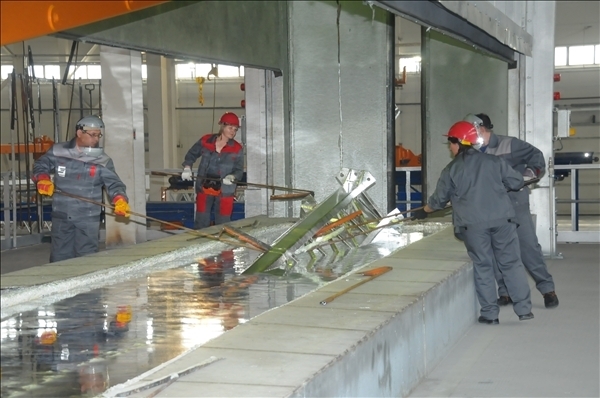
У данного метода обработки стальных предметов имеется большое количество достоинств, которые делают его таким популярным:
Во время погружения отдельных элементов в ванну с горячим цинком происходит покрытие защитным слоем сразу всех элементов предмета. Покрытию подвергаются даже самые недоступные участки, которые можно с легкостью пропустить, используя другие методы обработки.
Процедура обработки стали цинком не является сложной. Для этого достаточно лишь опустить металлический материал в сплав и подождать определенное количество времени.
На проведение процедуры горячего цинкования предметов из стали не затрачивается изначально большого количества средств. Данный процесс отличается своей дешевизной и способностью изготовлять изделия, которые в среднем служат не менее двадцати лет.
При обработке предметов из стали обычными методами появляется большое количество трудностей, потому что в некоторые места практически невозможно добраться. При обработке цинковым сплавом такого не происходит.
Технология горячего цинкования
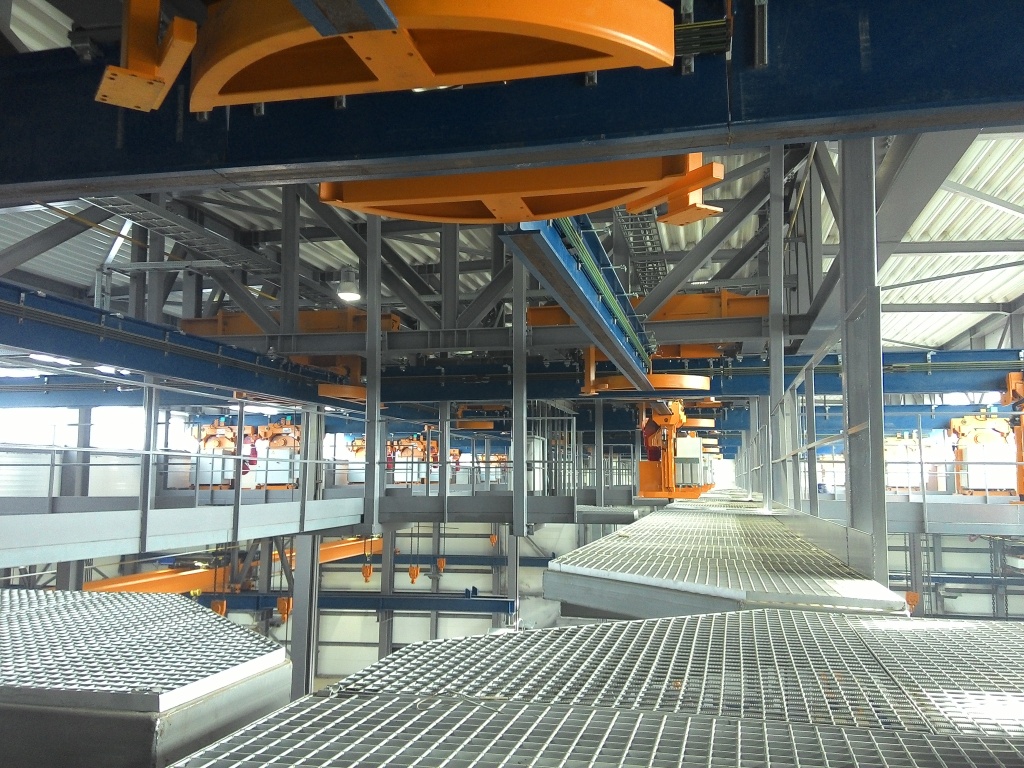
Технология горячего цинкования делится на несколько этапов:
1. подготовка поверхностиПеред процедурой необходимо тщательным образом подготовить стальную поверхность к нанесению цинковой пленки. Сначала необходимо обезжирить поверхность, чтобы с нее были удалены масла или загрязнения. После этого нужно тщательным образом промыть материала или изделия из стали, что поверхность была идеально чистой. На следующем этапе подготовки важно произвести процедуру травления. Она заключается в устранении с поверхности всех оксидов металла. Сделать это можно благодаря нагретой соляной кислоте или ингибоиторам. После этого проводится обработка металла специальными веществами для того, чтобы остановить процессы окисления. На заключительном этапе осуществляется сушка металла или металлического предмета.
2. Подготовка цинкового сплаваНа данном этапе осуществляется нагревание цинка до температуры 450 градусов Цельсия.
Важно: Во время погружения материалов для покрытия их цинковым сплавом необходимо соблюдать определенную скорость, потому что медленное погружение позволит на поверхности металла образоваться оксидам, чего нельзя допустить.
Данный этап является завершающим. Он осуществляется на открытом воздухе. Сплав на поверхности стали застывает.
Оборудование для горячего цинкования

В современном мире для процедуры горячего цинкования используются виды оборудовании, которые подходят для сильного нагревания цинка. К ним относится ванна горячего цинкования. Ведущими поставщиком такого оборудования в мире является Китай.
Ванна горячего цинкования
Есть несколько категорий таких ванн:
Они отличаются своими размерами. Он способна нагреваться благодаря:
У каждой ванны имеется своя система нагревания, которая позволяет за короткое время расплавить цинк и нагреть его до определенной температуры.
lkmprom.ru
Оцинкование металлоконструкций, горячее оцинкование изделий из металла
Горячая оцинковка применяется более 250 лет, и по-прежнему это наиболее дешевый и эффективный способ защиты металлических изделий от коррозии. Известно, что изделия из черных металлов ржавеют очень быстро, из-за чего толщина их несущего каркаса становится гораздо меньше расчетной, что нередко является причиной разрушения всей конструкции, порой влекущее трагичные последствия.
Горячее оцинкование защитит изделия из черных металлов и оборудование от коррозии и позволит эксплуатировать их в течение положенного срока. Обычно оцинкованные изделия служат 25−30 лет.
Преимущества горячего цинкования
При горячем цинковании металлоконструкций поверхность металлического изделия покрываются слоем цинка, и по популярности метод уступает лишь гальванической технологии. По стоимости выполнения и долговечности формируемых покрытий этот способ превосходит электрохимический.
Метод предполагает нанесение на поверхность металлоизделия слоя цинка толщиной 40−65 мкм. Это покрытие обеспечивает барьерную и электрохимическую защиту от коррозии. Главным образом цинкуется сталь.
Горячая оцинковка, в сравнении с другими технологиями, отличается оптимальным сочетанием стоимости процесса и обеспечения высоких защитных свойств слоя цинка. Обработанное изделие даже в очень неблагоприятных условиях может прослужить 65−70 лет, сохраняя эти свойства.
Плюсы метода следующие:
Этапы оцинковки металлоконструкций
Два этапа:
Нюансы горячей оцинковки металла регламентирует ГОСТ 9 .307−89.
Подготовка изделия к процедуре
Согласно ГОСТ, поверхность, подлежащая обработке, должна тщательно подготовиться. Подготовка включает:
Механическая обработка удаляет загрязнения, следы ржавчины, продукты окисления, шлаковые включения. ГОСТ предписывает скруглять острые кромки и углы на изделии, и это тоже делается путем механической обработки. На производстве используют пескоструйные установки.
Обезжиривание выполняется примерно при 75 °C перед основной процедурой для улучшения адгезии защитного слоя с обрабатываемым изделием. Присутствие на поверхности изделия пятен жира и масла может привести к формированию на этих участках неравномерной толщины или отслаивания. Обезжиривание выполняется с помощью химических реагентов, список которых регламентирует соответствующий ГОСТ. Остатки веществ впоследствии должны удалиться промывкой.
Согласно тому же ГОСТ, на трубах и прочих цинкуемых изделиях не должно быть окисленных участков и старого покрытия. Для выполнения этих требований поверхность протравливается обычно соляной кислотой. Процедура выполняется при температуре 22−24 °C, а концентрация раствора кислоты выбирается в зависимости от степени загрязнения поверхности следами коррозии и окислами.
Как правило, для травления используются растворы, где в 1 л воды растворяется 140−200 г кислоты. При травлении раствор может сильно повредить поверхность. Во избежание этого и для минимизации выделения водорода из раствора в состав его вводятся ингибиторы. После травления изделие тщательно промывается для удаления остатков использованных химических веществ.
Флюсование перед цинкованием
Технология предусматривает тщательную подготовку обрабатываемого изделия, позволяет предотвратить окисления и улучшить адгезию покрытия с металлом.
При флюсовании, выполняемом при 60 °C, обрабатываемая поверхность покрывается тонким слоем флюса, который содержится в специальном растворе. Обычно в качестве флюса используются хлориды цинка и аммония, которые смешиваются с водой в соотношении 500 г на 1 л для приготовления раствора для процедуры. При флюсовании крайне важно следить за следующими параметрами раствора:
Когда концентрация железа превышена, в раствор вводится перекись водорода, способствующая образованию солей железа, которые выпадают в осадок.
В любом цехе горячей оцинковки непременно должны иметься термические печи, в которых обрабатываемое изделие после флюсования просушивается. Благодаря подобной термической обработке удаляются остатки жидкости, ухудшающей качество готового цинкового покрытия, деталь нагревается до 100 °C, что позволяет сократить затраты на основную технологическую операцию.
Технология нанесения слоя цинка
Нанесения защитного цинкового слоя может производиться с помощью линии горячей оцинковки или более простого оборудования. Процесс предполагает погружение детали в расплавленный цинк. Температуру, при которой расплав находится в емкостях, определяет ряд факторов, в числе которых геометрические параметры изделия. В среднем температура составляет 420−455 °C .
Если оборудование не АНГЦ (агрегат для непрерывного горячего цинкования), а более простые технические устройства, на производственном участке обеспечивается выполнение таких условий:
Метизы оцинковываются так:
Представленная технология отличается сравнительно невысокой сложностью. Для осуществления процедуры отсутствует необходимость готовить сложные электролитические растворы, какие делает на производстве гальваник.
У этого метода есть и недостатки. Наиболее серьезный из них в том, что размеры обрабатываемых деталей, ограничиваются размерами емкости с расплавленным цинком. На крупных производственных предприятиях обработка габаритных изделий осуществляется путем применения АНГЦ.
tokar.guru
Горячее цинкование. Технология и режимы
Гальваника включает в себя несколько методов покрытия металлов, основывающихся на различных химических и физических процессах. Одним из таких является горячее цинкование. Оно применяется в промышленности для защиты стальных изделий. Основным компонентом здесь выступает слой цинка, наносящийся в расплавленном виде на каркас.
Чтобы добиться прочного и качественного покрытия, заготовки изготавливаются из низкоуглеродистой стали ГОСТ 380-94, 1050-88, 27772-88. Процентное соотношение кремния в данном составе не должно превышать 0,37% (рекомендованное значение не больше 0,25%), количество углерода достигать меньше 0,25%.
В зависимости от соотношения указанных ранее химических элементов, можно получить различную реактивность поверхности.
Специфика горячего цинкования
Состоит процесс из таких технологических операций:
Горячее цинкование, которое предлагает гальваника, позволяет получить качественное и прочное покрытие стальных заготовок, увеличивая срок их работы в несколько раз.
prodnisha.ru
Технология горячего цинкования
Для обеспечения перемещения изделий при горячем цинковании они должны быть закреплены на специальных траверсах.
Перед горячим цинкованием изделия подвергаются химической обработке, т.к. поверхности изделий, предназначенных для горячего цинкования, должны быть чистыми. Стадии процесса:Обезжиривание: перед травлением металлов (удаление окисей химическим способом, без которого невозможно цинкование) необходимо удалить маслянистые и смазочные вещества с их поверхности. Таким образом, цель обезжиривания – удаление с поверхности маслянистых и/или смазочных веществ с использованием кислотных растворов.
Травление: необходимо для удаления оксидов железа с поверхности материалов. Для травления используют кислоту с ингибитором коррозии, который необходим для остановки продолжения эффекта травления металла после удаления окиси.
Промывка: для полного удаления кислотного раствора после травления производится промывка изделий в ванной с водой.
Флюсование: производится в горячем жидком растворе хлористого цинка/аммония с целью подготовки поверхности металла для правильной «реакции» с расплавленным цинком и для предотвращения образования окиси при последующем процессе сушки.
Сушка: изделия помещают в камеру сушки, где циркулирует горячий воздух при температуре около 100° C. Таким образом, материал сушится и нагревается, что позволяет снизить термошок от высоких температур горячего цинкования.
Цинкование: производится погружением в цинк, содержание чистого цинка не менее 98,5 %, при температуре около 450° C. При горячем цинковании допускаются добавки алюминия или иных элементов в соответствии со спецификой требований цинкования.
Охлаждение: производится погружением в горячую воду только изделий такой конструкции, которые не деформируются и не разрушатся. Пассивация: после горячего цинкования материал может быть обработан раствором из несодержащих хром органических солей, который предотвращает образование белой окиси, т.е. того налета оксидированного цинка, который образуется в результате хранения изделий во влажных и непроветриваемых помещениях. Пассивация производится путем погружения конструкций в специальный раствор и сушится при температуре 70°C перед его упаковкой. Проверка: два свойства покрытия после горячего цинкования, которые тщательно рассматриваются после процесса цинкования, — толщина покрытия и внешний вид покрытия. Различные простые физические и лабораторные тесты выполняются для определения толщины, однородности, уровня прилипания и внешнего вида.
Горячее цинкование - требования к изделиям
В конструкциях изделий, подлежащих горячему цинкованию, не должно быть карманов, закрытых полостей и воздушных мешков; все полости должны быть доступны для беспрепятственного поступления и выхода из них жидкостей, расплавленного цинка и газов.Полые изделия и изделия сложной формы подвергают пробному горячему цинкованию.
Не допускается во избежание взрыва наносить покрытия на изделия, имеющие закрытые полости.
Сварку элементов конструкций следует производить встык, либо двухсторонними швами, либо односторонним швом с подваркой.
Не допускается цинковать изделия со сварными соединениями внахлест.
Требования к поверхности основного металла:
Горячее цинкование - характеристика химического состава стали
Для наилучшего покрытия методом горячего цинкования используются заготовки из низкоуглеродистой стали ГОСТ 380-94, 1050-88, 27772-88. Сталь должна содержать кремния Зависимость внешнего вида цинкового покрытия от химического состава стали приведена в таблице:polygonal.com.ua
Горячее цинкование: экономика и технология
За последние 15 лет у нас в стране сформировалась новая отрасль — горячее цинкование готовых деталей и конструкций. Если ранее такие производства существовали, как не большие вспомогательные цеха на судостроительных комбинатах, с размерами ванн 3,5-7метров, то сейчас это самостоятельные производства цинкующие металлоконструкции своего производства, а так же выполняющие заказы на защиту от коррозии поступающие от сторонних организаций. За эти годы в России появилось свыше 50 новых заводов, большинство из которых имеет линии длинной 12-13 метров, позволяющие цинковать крупногабаритные металлоконструкции, например элементы ЛЭП. Причём эти заводы построены по последнему слову техники и отвечают всем требованиям, как технологической, так и экологической безопасности. Оборудование поставляется ведущими западными фирмами: W.Pilling, BISOL, WESTECH, INGENIA, Sirio, Maccabeo, KVK, Koerner, LOI и другие. Химические реактивы для нужд наших заводов поставляются, как иностранные компании Herwig, Soprin так и отечественный ИНТЕРХИММЕТ.

В настоящее время Россия занимает первое место в мире по темпам роста числа заводов горячего цинкования. Чем же был обусловлен такой взрывной рост этой отрасли. Дело в том, что в начале 2000-х ряд отраслей, а именно железные и автомобильные дороги, строители ЛЭП, в рамках оптимизации своих расходов на обслуживание инфраструктуры своих объектов приняли решение на повсеместное использование оцинкованной металлопродукции. Это позволило увеличить срок службы изделий в 4-5 раз, снизить расходы на эксплуатацию и ремонт. Более того были подготовлены внутренние ТУ (технические условия) оговаривающие использование оцинкованных металлоконструкций. Именно потребность этих заказчиков позволило успешно развиваться отрасли горячего цинкования.
Сейчас, на фоне постоянного роста числа предприятий горячего цинкования, на рынке наблюдается некоторое снижение числа заказов в пересчете на 1 завод. Для этого есть как субъективные, так и объективные причины. На фоне после кризисных явлений снизилось общее количество инвестиций во все отрасли экономики. У основных заказчиков — энергетиков, происходит объединение МРСК и ФСК — с неясной судьбой денежных потоков по приобретению новых и замен старых линий электропередач. Наблюдаемое уменьшение заказов создает иллюзию насыщения рынка, однако, это не так! Если рассмотреть структуру европейского, американского и российского рынка горячее оцинкованных конструкций мы увидим, что «ведущими заказчиками» за рубежом являются строители, у нас они занимают почетное второе место, не говоря уже об отсутствии в структуре отечественного рынка потребности сельского хозяйства. Если к западным строителям добавить заказы для нужд городской инфраструктуры, то доля этого сегмента рынка составит 45-55% от общего объема рынка! К сожалению, строители, не имеющие даже своего министерства и оперирующие устаревшими СНиПами, не могут и не хотят использовать защищённые от коррозии конструкции. Для них использование оцинкованного проката это вынужденная мера и является скорее исключением. Причина в том, что «заказчик», «проектировщик», «строитель» и «потребитель» это совершенно разные организации преследующие совершенно разные цели и задачи! Эффективные менеджеры от строительства, использующие дешёвые не качественные материалы не заинтересованы в увеличении срока службы зданий и сооружений! Чем быстрее проржавеет, тем раньше можно получить заказ на строительство нового или ремонт — это вообще золотое дно – только успевай красить!
Кроме того, вследствие молодости отрасли горячего цинкования ощущается острая нехватка специалистов и технического персонала и следовательно высокая себестоимость цинкования, из-за элементарного отсутствия опыта и не подготовленности персонала. Овладение опытом западных коллег и постоянное снижение технологических издержек производства позволит снизить стоимость цинкования и привлечь новых клиентов.
Таким образом, ситуация на рынке услуг горячего цинкования далеко не критическая и имеет великолепные перспективы роста! Если на Урале число заводов ГЦ удовлетворительное, то в Центральной Россиии, в Сибири и на Дальнем Востоке, их всё ещё не хватает.
Нужно проводить активную рекламную и просветительскую работу по информированию о преимуществах оцинкованного металлопроката. Активно сотрудничать с проектировщиками и архитекторами, вести просветительскую работу с заказчиками и городскими властями, объясняя порочность практики постоянной окраски.
Необходимо постоянно повышать технический уровень персонала, овладевать всеми нюансами технологии цинкования. Именно для этого НКП «Центр по развитию Цинка», проводит обучающие семинары, ближайший из которых состоится в конце мая в Санкт-Петербурге. Семинар, который мы организуем в ноябре, во время проведения выставки Металл-Экспо, призван улучшить представление о рынке ГЦ и его структуре. Словом, отрасль горячего цинкования имеет хорошие перспективы и остается весьма привлекательной с точки зрения инвестиций.
В целом процесс горячего цинкования состоит в погружении стальной конструкции, химически очищенной от масел, окислов и окалины в расплав цинка с температурой 4500 C.
Сама технология горячего цинкования начинается с навески металла на траверсы. Это операция совершается с помощью гидравлических подъемников в специально отведенной для этих целей зоне.
Дальше, траверсы с навешанным черным металлом перемещаются в зону химической подготовки, где последовательно проходят ванны: обезжиривания, травления, промывки и флюсования. Операция обезжиривания обеспечивает удаление грязи и жиров с поверхности цинкуемых изделий. Травление предназначено для удаления с поверхности металла изделий окислов, препятствующих образованию качественных цинковых покрытий. Промывка служит для удаления остатков кислоты и солей железа с поверхности металлоконструкций. Задачами флюсования является: удаление с поверхности изделий оставшиеся после травления солей железа, не полностью удаляемые при промывке; растворение окислов, которые образуются на протравленной поверхности при взаимодействии с водой и воздухом; очищение зеркала расплава от окислов цинка в месте выхода металлоконструкции из ванны горячего цинкования; способствовать смачиванию поверхности металлоконструкции расплавленным цинком снижая его поверхностное натяжение и увеличивая физико-механическое сцепление железа и цинка. Ванны химической подготовки представляют собой металлический жесткий каркас с химически стойкой футеровкой. Многие производители оборудования уверяют насколько важен выбор материала для футеровки, и что от этого выбора зависит работа всего завода и качество получаемой продукции, но они лукавят: от выбора материала ванны может зависеть только возможная долговечность самой ванны. Также не стоит забывать, что никакой супер-материал никогда не защитит ванну от ошибок рабочих, которые могут плохо закрепить металл на траверсе. На новых заводах ванны устанавливают в вытяжной короб для предотвращения вредных выбросов во внутрицеховое пространство и в окружающую среду, но это скорее эстетическая мера: на производительность и на качество продукции никак не влияет. Нужно помнить, что установка кожуха обязательно влечет за собой автоматизацию крановой системы в зоне химической подготовки, так как управлять кранами, работающими внутри кожуха, через просмотровые окна очень сложно. Воздух, удаляемый из вытяжного короба зоны предварительной подготовки, проходит очистку в скруббере. Отработанные растворы и промывные воды поступают на установки нейтрализации или передаются для очистки на другие предприятия.
Пройдя обработку на участке химической подготовки поверхности, металлоконструкции, на тех же траверсах, подаются в сушильную печь, представляющую собой камеру с циркулирующим нагретым воздухом. Операция сушки и предварительного нагрева металлоконструкций происходит при температуре 1200 C. Главной задачей сушки является удаление избытка воды из флюса, а также предварительный нагрев изделий перед цинкованием.
После сушки металлоконструкции переносятся к печи цинкования, где металл окунают в расплав цинка при температуре 4500 С. Обычно печь цинкования – это металлическая конструкция со встроенными горелками. Внутри нее находится ванна цинкования. Над печью устанавливают защитно-вытяжной короб, который служит для улавливания так называемых «белых дымов» и для защиты персонала от возможных выплесков цинка. И конструктивно может быть подвижным или стационарным. После цинкования металлоконструкции подвергаются охлаждению, а также в случае необходимости пассивации, и после отправляются в зону разгрузки, где их снимают с траверс.
Сердце линии — печь горячего цинкования. Главное различие печей – это используемое для нагрева топливо. Во всём мире большее распространение получил газовый нагрев, но также встречаются печи с электрическим нагревом и на жидком топливе. Электрический нагрев в нашей стране в основном используется на старых печах «шахтного» типа. На современных печах также можно встретить данный нагрев, но большого распространения он не получил из-за более сложной конструкции печи и большого потребления электроэнергии. Но этот энергоноситель может быть хорошей альтернативой газу в регионах с дешевой электроэнергией: например рядом с крупными электростанциями. Также редким явлением среди печей является использование жидкого топлива – мазута. Линии с этим нагревом можно встретить лишь в странах Персидского залива. В свою очередь самые распространённые газовые печи разделяются по типу горелок — плоскопламенные и высокоскоростные. При плоскопламенном нагреве горелки располагаются по периметру ванны и пламя горелок направлено перпендикулярно к стенкам ванны. Наиболее совершенным и современным считается высокоскоростной нагрев ванны цинкования. В данном исполнении горелки располагаются вдоль стенок ванны напротив друг друга. Данный способ нагрева был разработан английской фирмой Hasco-Thermic в 1976 году, но и до сих пор данный метод совершенствуется за счёт внедрения и использования современных систем горения, контроля и управления печью. Отходящие горячие газы используют для подогрева ванн химической подготовки или сушильной печи, прогоняя их через специальные теплообменники. Стоит обратить внимание, что выбор качественной и производительной печи во многом гарантирует успешную работу всего цеха, так как её мощность является главным тормозом наращивания объемов производства. Что касается ванны, которую нагревает печь, то все основные поставщики оборудования используют ванны немецкой фирмы Pilling. Исключением является только китайские коллеги, которые используют ванны своего собственного производства, но, сожалению, низкого качества и с малым сроком эксплуатации. По размеру ванны сейчас преобладает длина 13 метров, и наметилась тенденция на увеличение ширины, что связано с увеличением объема цинкования многогранных опор.
Если рассмотреть планировки линий, то самый распространённый вариант – это классическое линейное расположение с различными вариациями. При линейной схеме все оборудование установлено по одной оси в одном пролете здания. Передача металла из заготовительного пролета в технологический осуществляется с помощью рельсовых тележек. Все технологические операции совершаются с помощью мостовых кранов, защитно-вытяжной короб в данном варианте подвижный, и крепится на двух балочном кране над печью. Первое усовершенствование этой линии произошло за счет установки кольцевого монорельса вместо двухбалочного крана. В этом исполнение передача траверсы на участке от сушильной печи до тележки совершается с помощью тельферных пар, которые движутся по кольцу монорельса. Дальнейшая эволюция этой линии связана с установкой кожуха над зоной химической подготовки и с автоматизацией крановой системы внутри её. Само здание для этого типа представляет собой двух пролетный цех, с шириной пролета 18 метров.
Совершенно новый вид полностью автоматизированной линии был разработан австрийской компанией Ingenia GmbH. Основной принцип данного цеха – полностью закольцованная система, где всеми основными процессами управляет автоматика по заданной программе. Перемещения по всем технологическим этапам происходит с помощью автоматических тельферных пар, а изменение направления их движения совершается с помощью поворотных столов. Большое количество зон загрузки и выгрузки, также является огромным плюсом данной линии. Данные факторы позволяют увеличить производительность данной линии до 50000 тонн в год.
В цифрах данное производство выглядит так:
Линия с ванной 7 метров:
Линия с ванной 13 метров:
zdc.ru