- аустенитные 04Х18Н10Т, 12Х18Н9Т, 12Х18Н12Т, 06Х18Н11;
- аустенитно-мартенситные 09Х15Н8Ю, 09Х17Н7Ю;
- аустенитно-ферритные 12Х21Н5Т, 08Х22Н6Т, 08Х21Н6М2Т.
ХРОМОНИКЕЛЕВЫЕ АУСТЕНИТНО-МАРТЕНСИТНЫЕ И МАРТЕНСИТНО-ФЕРРИТНЫЕ СТАЛИ. Аустенитно мартенситные стали
АУСТЕНИТНО-МАРТЕНСИТНЫЕ СТАЛИ (Савченко В. С.)
СВАРКА И СВАРИВАЕМЫЕ МАТЕРИАЛЫ
19.1. Состав, структура и назначение сталей
К аустенитно-мартенситному классу в соответствии с ГОСТ 5632—72 относятся стали, имеющие структуру аустенита и мартенсита, количество которых можно изменить в широких пределах К этому классу относятся стали, химический состав которых выбран с соотношением легирующих элементов, обеспечивающих начало мартенситного превращения при 20—60 °С. Представители этого класса сталей приведены в табл 19 1, 19 2
Ориентировочно оценку структуры сталей в зависимости от состава можно определить по диаграмме Я М Потака, В А Сагалевич (рис 13.3).
ХИМИЧЕСКИЙ СОСТАВ НЕКОТОРЫХ СТАЛЕЙ АУСТЕНИТО - МАРТЕНСИТНОГО КЛАССА ([1], ГОСТ 5632—72)
|
Продолжение табл. 19.1
|
* S < 0,020 %. Р < 0 035 % ** [N ] ~ 0,07 |
Стали аустенитно-мартеиситного (переходного) класса, лежащего между мартенситным и аустенитным, в зависимости от термической обработки имеют структуру н обладают свойствами, близкими к свойствам сталей аустенитного или мартенситного классов
После закалки с температуры, достаточной для растворения карбидов, структура сталей переходного класса в основном аустенитиая, хотя в зависимости от марки стали и условий, заданных при выплавке, сталь может содержать некоторое количество мартенсита Однако этот аустенит неустойчив и при охлаждении до отрицательных температур (рис 19 1) либо пластической деформации при температурах у-^а-превращения сравнительно легко превращается в мартенсит, причем полнота мартенситного превращения в последнем случае зависит от температуры деформации Деформация аустенита при температуре 100—200 °С замедляет мартенситное превращение практически до нуля Структурное состояние определяет механические характеристики сталей (табл 19 3)
ТАБЛИЦА 19 2 РЕКОМЕНДУЕМЫЕ РЕЖИМЫ ТЕРМИЧЕСКОЙ ОБРАБОТКИ
|
Указанные стали рекомендуются к применению как высокопрочные стали для изделий, работающих в атмосферных условиях, уксуснокислых и других солевых средах, а также для упругих элементов Учитывая высокую пластичность и вязкость металла после закалки, из сталей целесообразно изготовлять детали посредством глубокой штамповки с последующим упрочнением отпуском Значительное количество остаточного аустенита при соответствующих режимах термообработки обеспечивает высокую пластичность и ударную вязкость сталей при отрицательных температурах и позволяет рекомендовать стали для изделий криогенной техники, работающих до температур —196 °С [3] В этом случае для обеспечения высокой надежности в эксплуатации стали не следует подвергать старению
Рис 19 1 Структура стали 07Х16Н6 (а) и шва (б) аналогичного состава после полного цикла термической обработки Х200 |
19.2. Свариваемость сталей
19.2 1. Структура, свойства металла шва и зоны термического влияния
После сварки сталей, прошедших полный цикл упрочняющей термообработки и имеющих благодаря этому мартенситную структуру, наблюдается широкая зона, имеющая после высокотемпературного нагрева структуру аустенита. Ширина зоны определяется температурой обратного мартенситного превращения металла (Ас—Ас3) (650—750 °С). Одновременно в интервале температур 550—900 °С происходит интенсивное выделение карбидов (рис 19 2), особенно по границам аустенитных зерен. Кроме того, в узкой зоне, примыкающей к поверхности сплавления, наблюдается образование некоторого количества
6- феррита Структурные превращения в зоне термического влияния приводят к снижению пластичности и ударной вязкости металла, а также его чувствительности к концентраторам
ТАБЛИЦА 19 3 МЕХАНИЧЕСКИЕ СВОЙСТВА СТАЛЕЙ АУСТЕНИТНО МАРТЕНСИТНОГО КЛАССА ПРИ НОРМАЛЬНЫХ ТЕМПЕРАТУРАХ [i J
|
Рис 19 3 Изменение ударной вязкости О 1 KCV-m металла ЗТВ в стали 07Х16Н6 6 = = 11 мм в состоянии после сварки (сварка в ар гоне плавящимся электродом диаметр про волоки 2,0 мм /св=350 А) [2] |
Рис 19 2 Структура зоны термине ского влияния сварного соединения стали 07Х16И6 в состоянии после свар ки X100 |
напряжений (рис. 19.3). Кроме того, эти превращения снижают коррозионную стойкость и стойкость против межкристаллит- ной коррозии ЗТВ.
19.2.2. Хрупкость сварных соединений
Обратное мартенситное превращение в ЗТВ и ограниченный объем последующего мартенситного превращения при охлаждении до комнатной температуры исключает при сварке сталей этого класса образование холодных трещин. Вместе с тем интенсивное выделение карбидов, и особенно образование 6-феррита, приводят к хрупкому разрушению сварных соединений в зонах структурных изменений, особенно при понижении температуры до —196 °С. Последнее объясняется резким снижением пластичности 6-феррита. В этом случае полная термообработка (закалка, обработка холодом, отпуск) позволяет получить оптимальные соотношения аустенита и мартенсита, а также отсутствие 6-феррита. При этом восстанавливается вязкость зоны сплавления при сохранении прочностных характеристик сварного соединения на уровне 0,9 ов основного металла в случае выполнения сварки материалами мартенситного либо аустенитно-мартенситного класса.
19.3. Технология сварки и свойства соединений
19.3.1. Выбор сварочных материалов
Соединения стали аустенитно-мартенситного класса целесообразно выполнять аргонодуговой сваркой без присадки (тонколистовые детали) либо с присадкой перечисленными ниже материалами, а также контактной точечной и роликовой сваркой и электронно-лучевой сваркой.
В случае сварки соединений, для которых отсутствует требование равнопрочности, допускается ручная электродуговая сварка электродами, дающими аустенитный наплавленный металл, либо механизированная сварка под слоем флюса марки АН-26с по ГОСТ 9087—81 либо марки 48-ОФ-6 по ОСТ 5.9206—76.
Выбор присадочного материала осуществляют, исходя из требований прочности сварного соединения. В случае отсутствия требований высокой прочности к швам в качестве присадочной можно рекомендовать аустенитную проволоку Св-01X19Н18Г10АМ4 (ТУ 14-1-1892—71) либо Св-08Х21Н10Г6 (ГОСТ 2246—70), обладающих хорошей стойкостью против образования горячих трещин и высокой прочностью и пластичностью в широком интервале температур, в том числе отрицательных (до —196 °С).
ТИПИЧНЫЕ СВОЙСТВА СВАРНЫХ СОЕДИНЕНИЙ ИЗ НЕРЖАВЕЮЩИХ СТАЛЕЙ АУСТЕНИТНО-МАРТЕНСИТНОГО КЛАССА
|
При наличии требований высокой прочности сварных соединений рекомендуется к применению аустенитно-мартенситные проволоки СВ-07Х16Н6, Св-08Х17Н5МЗ, Св-09Х15Н9Ю (ТУ I4-I-997— 74), Св-01Х12Н11М2ТС (ТУ 14-1-3482—82).
Механические свойства сварных соединений, полученных с применением некоторых из указанных сварочных материалов, приведены в табл. 19.4.
Прочность сварных соединений, сваренных аустеннтной присадочной проволокой, выше прочности самой присадки. Это объясняется стеснением деформации металла шва из-за более высокой прочности основного металла. Такой эффект по мере увеличения ширины шва и зоны с аустенитной структурой уменьшается.
19.3.2. Выбор режимов сварки
Режим сварки выбирают, исходя из способа сварки, толщины свариваемого материала, диаметра сварочной проволоки н других параметров.
Приведенные режимы сварки (табл. 19.5) могут быть скорректированы в зависимости от типа соединения, наличия разделки кромок, качества сборки, наличия либо отсутствия подкладки, положения шва в пространстве и т. д.
19.3.3. Выбор послесварочной термообработки
Влияние термического цикла сварки приводит к структурным изменениям, приводящим к охрупчиванию металла ЗТВ сталей, а также снижению их коррозионной стойкости и стойкости против межкристаллитной коррозии. Поэтому при изготовлении ответственных конструкций, к которым предъявляются требования высокой прочности, вязкости и коррозионной стойкости сварных соединений, целесообразно предусмотреть полный цикл
ОРИЕНТИРОВОЧНЫЕ РЕЖИМЫ СВАРКИ ВЫСОКОЛЕГИРОВАННЫХ СТАЛЕЙ АУСТЕНИТНО-МАРТЕНСИТНОГО КЛАССА
|
термообработки, включающий закалку, обработку холодом и отпуск. Режим термообработки в этом случае выбирают аналогичным термообработке основного металла (см. табл. 19.2).
В случае выполнения сварки крупногабаритных изделий, исключающих возможность закалки, следует сварное соединение подвергнуть обработке холодом и последующему отпуску. При этом несколько повышается ударная вязкость сварного соединения.
19.3.4. Коррозионная стойкость соединений
Стали аустенитно-мартенситного класса имеют после закалки с температур, достаточных для растворения карбидов, высокую коррозионную стойкость, определяемую прежде всего высоким содержанием хрома. Сварные соединения имеют равную коррозионную стойкость с основным металлом.
Мартенситное превращение при обработке холодом сталей,
ТАБЛИЦА 19 6 КОРРОЗИОННАЯ СТОЙКОСТЬ СТАЛЕЙ АУСТЕНИТНО - МАРТЕНСИТНОГО КЛАССА В РАЗЛИЧНЫХ СРЕДАХ [1]
|
прошедших закалку, не влияет на коррозионную стойкость и способность сталей к пассивации.
Низкотемпературный отпуск и старение после обработки холодом также не вызывают каких-либо изменений общей коррозионной стойкости.
Стали аустенитно-мартенситного класса 09X15Н8Ю,
07X16Н6, 08XI7H5M3 в соответствии с требованиями ГОСТ 6032—84 после полного цикла термообработки стойки также против межкристаллитиой коррозии. Вместе с тем при нагреве выше 500 °С наблюдается интенсивное падение стойкости против межкристаллитиой коррозии в связи с выделением по границам бывших аустенитных зерен карбидов, богатых хромом.
Холодная пластическая деформация сталей аустенитно-мартенситного класса, при которой образуется до 75 % мартенсита, не уменьшает склонность стали к общей и межкристаллитиой коррозии. Таким образом, нержавеющие стали рассматриваемого класса и их сварные соединения во многих случаях имеют хорошее сочетание высокой прочности и коррозионной стойкости в агрессивных средах (табл. 19.6).
39.1. Классификация пористых материалов Пористые материалы (ПМ) на металлической основе применяются в каче
msd.com.ua
Высокопрочная коррозионностойкая сталь аустенитно- мартенситного класса
Изобретение относится к металлургии, в частности к созданию высокопрочной корозионно-стойкой стали аустенитно-мартенситного класса, предназначенной для изготовления высоконагруженных крупногабаритных деталей машин, таких как шасси, рамы, лонжероны, узлы поворота, силовой крепеж и др., работающих при температуре от -70 до +300°С. Заявленная сталь содержит компоненты в следующем соотношении, мас.%: углерод 0,18-0,21; хром 13-14; никель 4-4,5; молибден 2,3-2,8; кремний 1,7-2,5; кобальт 3,5-4,5; азот 0,06-0,09; марганец 0,1-1,0; иттрий 0,001-0,05; церий 0,001-0,05; лантан 0,001-0,05; железо остальное. При этом сумма Y+Ce+La0,l %, а соотношение компонентов, определяющих фазовый состав стали, характеризуется следующими формулами: Км=Cr+Mo+l,5Ni+30(C+N)+0,7(Mn+Si)=30-35; Кф=Cr+Mo+2Si-{l,5Ni+30(C+N)0,7Mn}=5-5,5, где Км - эквивалент мартенситообразования, а Кф - эквивалент ферритообразования. Техническим результатом изобретения является повышение прочности, пластичности, ударной вязкости и сопротивления коррозионному растрескиванию. 1 з.п.ф-лы, 2 табл.
Изобретение относится к области металлургии, в частности к высокопрочным коррозионно-стойким сталям аустенитно-мартенситного класса, обладающих супервысокой прочностью, хорошей свариваемостью и высоким сопротивлением коррозионному растрескиванию. Сталь предназначена для изготовления высоконагруженных крупногабаритных деталей машин: шасси, рамы, лонжероны, узлы поворота, силовой крепеж и др., работающих при t = -70 - +300oC во всеклиматических условиях, в том числе в морской среде.
Известны коррозионно-стойкие стали для силовых деталей машин, в том числе самолетных конструкций: 17-4PH (США) (New developments in high strength stainless steels, DMIC Report 223, January 3, 1966 г.) и сталь 13X11H6M2C (а.с. 647355, БИ N 6 от 15.02.79 г.). Сталь 17-4PH имеет следующий химический состав, мас.%: C - 0,07 Cr - 15,5-17,5 Ni - 3-5 Nb - 0,15-0,45 Cu - 3-5 Si - 1,0 Fe - Остальное После закалки с 1040oC и отпуска при 470oC 1 час сталь имеет следующие механические свойства:


























Формула изобретения
1. Высокопрочная коррозионно-стойкая сталь аустенитно-мартенситного класса, содержащая углерод, хром, никель, молибден, кремний, азот, марганец, железо, отличающаяся тем, что сталь дополнительно содержит кобальт, иттрий, церий и лантан при следующем соотношении компонентов, мас.%: Углерод - 0,18 - 0,21 Хром - 13 - 14 Никель - 4 - 4,5 Молибден - 2,3 - 2,8 Кремний - 1,7 - 2,5 Кобальт - 3,5 - 4,5 Азот - 0,06 - 0,09 Марганец - 0,1 - 1,0 Иттрий - 0,001 - 0,05 Церий - 0,001 - 0,05 Лантан - 0,001 - 0,05 Железо - Остальное при этом сумма Y+Ce+La
РИСУНКИ
Рисунок 1www.findpatent.ru
Технология сварки аустенитно-мартенситных сталей
Рекомендуем приобрести:
Установки для автоматической сварки продольных швов обечаек - в наличии на складе! Высокая производительность, удобство, простота в управлении и надежность в эксплуатации.
Сварочные экраны и защитные шторки - в наличии на складе! Защита от излучения при сварке и резке. Большой выбор. Доставка по всей России!
Состав, структура и назначение сталей
К аустенитно-мартенситному классу в соответствии с ГОСТ 5632—72 относятся стали, имеющие структуру аустенита и мартенсита, количество которых можно изменить в широких пределах К этому классу относятся стали, химический состав которых выбран с соотношением легирующих элементов, обеспечивающих начало мартенситного превращения при 20—60 °С. Представители этого класса сталей приведены в табл 19 1, 19 2.
Стали аустенитно-мартеиситного (переходного) класса, лежащего между мартенситным и аустенитным, в зависимости от термической обработки имеют структуру н обладают свойствами, близкими к свойствам сталей аустенитного или мартенситного классов.
После закалки с температуры, достаточной для растворения карбидов, структура сталей переходного класса в основном аустенитная, хотя в зависимости от марки стали и условий, заданных при выплавке, сталь может содержать некоторое количество мартенсита Однако этот аустенит неустойчив и при охлаждении до отрицательных температур (рис 19 1) либо пластической деформации при температурах γ→α сравнительно легко превращается в мартенсит, причем полнота мартенситного превращения в последнем случае зависит от температуры деформации Деформация аустенита при температуре 100—200 oС замедляет мартенситное превращение практически до нуля Структурное состояние определяет механические характеристики сталей (табл 19 3).
Указанные стали рекомендуются к применению как высокопрочные стали для изделий, работающих в атмосферных условиях, уксуснокислых и других солевых средах, а также для упругих элементов Учитывая высокую пластичность и вязкость металла после закалки, из сталей целесообразно изготовлять детали посредством глубокой штамповки с последующим упрочнением отпуском Значительное количество остаточного аустенита при соответствующих режимах термообработки обеспечивает высокую пластичность и ударную вязкость сталей при отрицательных температурах и позволяет рекомендовать стали для изделий криогенной техники, работающих до температур —196 °С. В этом случае для обеспечения высокой надежности в эксплуатации стали не следует подвергать старению.
Структура, свойства металла шва и зоны термического влияния
После сварки сталей, прошедших полный цикл упрочняющей термообработки и имеющих благодаря этому мартенситную структуру, наблюдается широкая зона, имеющая после высокотемпературного нагрева структуру аустенита. Ширина зоны определяется температурой обратного мартенситного превращения металла (Ас1—Ас3) (650—750 °С). Одновременно в интервале температур 550—900 °С происходит интенсивное выделение карбидов (рис 19 2), особенно по границам аустенитных зерен. Кроме того, в узкой зоне, примыкающей к поверхности сплавления, наблюдается образование некоторого количества δ-феррита Структурные превращения в зоне термического влияния приводят к снижению пластичности и ударной вязкости металла, а также его чувствительности к концентраторам напряжений (рис. 19.3). Кроме того, эти превращения снижают коррозионную стойкость и стойкость против межкристаллитной коррозии ЗТВ.
Хрупкость сварных соединений
Обратное мартенситное превращение в ЗТВ и ограниченный объем последующего мартенситного превращения при охлаждении до комнатной температуры исключает при сварке сталей этого класса образование холодных трещин. Вместе с тем интенсивное выделение карбидов, и особенно образование δ-феррита, приводят к хрупкому разрушению сварных соединений в зонах структурных изменений, особенно при понижении температуры до —196 °С. Последнее объясняется резким снижением пластичности δ-феррита. В этом случае полная термообработка (закалка, обработка холодом, отпуск) позволяет получить оптимальные соотношения аустенита и мартенсита, а также отсутствие δ-феррита. При этом восстанавливается вязкость зоны сплавления при сохранении прочностных характеристик сварного соединения на уровне 0,9 σв основного металла в случае выполнения сварки материалами мартенситного либо аустенитно-мартенситного класса.
Технология сварки и свойства соединений
Выбор сварочных материалов
Соединения стали аустенитно-мартенситного класса целесообразно выполнять аргонодуговой сваркой без присадки (тонколистовые детали) либо с присадкой перечисленными ниже материалами, а также контактной точечной и роликовой сваркой и электронно-лучевой сваркой.
В случае сварки соединений, для которых отсутствует требование равнопрочности, допускается ручная электродуговая сварка электродами, дающими аустенитный наплавленный металл, либо механизированная сварка под слоем флюса марки АН-26с по ГОСТ 9087—81 либо марки 48-ОФ-6 по ОСТ 5.9206—76.
Выбор присадочного материала осуществляют, исходя из требований прочности сварного соединения. В случае отсутствия требований высокой прочности к швам в качестве присадочной можно рекомендовать аустенитную проволоку Св-01X19Н18Г10АМ4 (ТУ 14-1-1892—71) либо Св-08Х21Н10Г6 (ГОСТ 2246—70), обладающих хорошей стойкостью против образования горячих трещин и высокой прочностью и пластичностью в широком интервале температур, в том числе отрицательных (до —196 °С).
При наличии требований высокой прочности сварных соединений рекомендуется к применению аустенитно-мартенситные проволоки Св-07Х16Н6, Св-08Х17Н5МЗ, Св-09Х15Н9Ю (ТУ 14-1-997—74), Св-01Х12Н11М2ТС (ТУ 14-1-3482—82).
Механические свойства сварных соединений, полученных с применением некоторых из указанных сварочных материалов, приведены в табл. 19.4.
Прочность сварных соединений, сваренных аустенитной присадочной проволокой, выше прочности самой присадки. Это объясняется стеснением деформации металла шва из-за более высокой прочности основного металла. Такой эффект по мере увеличения ширины шва и зоны с аустенитной структурой уменьшается.
Выбор режимов сварки
Режим сварки выбирают, исходя из способа сварки, толщины свариваемого материала, диаметра сварочной проволоки и других параметров.
Приведенные режимы сварки (табл. 19.5) могут быть скорректированы в зависимости от типа соединения, наличия разделки кромок, качества сборки, наличия либо отсутствия подкладки, положения шва в пространстве и т. д.
Выбор послесварочной термообработки
Влияние термического цикла сварки приводит к структурным изменениям, приводящим к охрупчиванию металла ЗТВ сталей, а также снижению их коррозионной стойкости и стойкости против межкристаллитной коррозии. Поэтому при изготовлении ответственных конструкций, к которым предъявляются требования высокой прочности, вязкости и коррозионной стойкости сварных соединений, целесообразно предусмотреть полный цикл термообработки, включающий закалку, обработку холодом и отпуск. Режим термообработки в этом случае выбирают аналогичным термообработке основного металла (см, табл. 19.2).
В случае выполнения сварки крупногабаритных изделий, исключающих возможность закалки, следует сварное соединение подвергнуть обработке холодом и последующему отпуску. При этом несколько повышается ударная вязкость сварного соединения.
Коррозионная стойкость соединений
Стали аустенитно-мартенситного класса имеют после закалки с температур, достаточных для растворения карбидов, высокую коррозионную стойкость, определяемую прежде всего высоким содержанием хрома. Сварные соединения имеют равную коррозионную стойкость с основным металлом.
Мартенситное превращение при обработке холодом сталей, прошедших закалку, не влияет на коррозионную стойкость и способность сталей к пассивации.
Низкотемпературный отпуск и старение после обработки холодом также не вызывают каких-либо изменений общей коррозионной стойкости.
Стали аустенитно-мартенситного класса 09X15Н8Ю, 07X16Н6, 08XI7H5M3 в соответствии с требованиями ГОСТ 6032—84 после полного цикла термообработки стойки также против межкристаллитной коррозии. Вместе с тем при нагреве выше 500 °С наблюдается интенсивное падение стойкости против межкристаллитной коррозии в связи с выделением по границам бывших аустенитных зерен карбидов, богатых хромом.
Холодная пластическая деформация сталей аустенитно-мартенситного класса, при которой образуется до 75 % мартенсита, не уменьшает склонность стали к общей и межкристаллитной коррозии. Таким образом, нержавеющие стали рассматриваемого класса и их сварные соединения во многих случаях имеют хорошее сочетание высокой прочности и коррозионной стойкости в агрессивных средах (табл. 19.6).
www.autowelding.ru
АУСТЕНИТНО-МАРТЕНСИТНЫЕ СТАЛИ (Савченко В. С.)
19.1. Состав, структура и назначение сталей
К аустенитно-мартенситному классу в соответствии с ГОСТ 5632—72 относятся стали, имеющие структуру аустенита и мартенсита, количество которых можно изменить в широких пределах К этому классу относятся стали, химический состав которых выбран с соотношением легирующих элементов, обеспечивающих начало мартенситного превращения при 20—60 °С. Представители этого класса сталей приведены в табл 19 1, 19 2
Ориентировочно оценку структуры сталей в зависимости от состава можно определить по диаграмме Я М Потака, В А Сагалевич (рис 13.3).
ХИМИЧЕСКИЙ СОСТАВ НЕКОТОРЫХ СТАЛЕЙ АУСТЕНИТО — МАРТЕНСИТНОГО КЛАССА ([1], ГОСТ 5632—72)
|
Продолжение табл. 19.1
|
* S < 0,020 %. Р < 0 035 % ** [N ] ~ 0,07 |
Стали аустенитно-мартеиситного (переходного) класса, лежащего между мартенситным и аустенитным, в зависимости от термической обработки имеют структуру н обладают свойствами, близкими к свойствам сталей аустенитного или мартенситного классов
После закалки с температуры, достаточной для растворения карбидов, структура сталей переходного класса в основном аустенитиая, хотя в зависимости от марки стали и условий, заданных при выплавке, сталь может содержать некоторое количество мартенсита Однако этот аустенит неустойчив и при охлаждении до отрицательных температур (рис 19 1) либо пластической деформации при температурах у-^а-превращения сравнительно легко превращается в мартенсит, причем полнота мартенситного превращения в последнем случае зависит от температуры деформации Деформация аустенита при температуре 100—200 °С замедляет мартенситное превращение практически до нуля Структурное состояние определяет механические характеристики сталей (табл 19 3)
ТАБЛИЦА 19 2 РЕКОМЕНДУЕМЫЕ РЕЖИМЫ ТЕРМИЧЕСКОЙ ОБРАБОТКИ
|
Указанные стали рекомендуются к применению как высокопрочные стали для изделий, работающих в атмосферных условиях, уксуснокислых и других солевых средах, а также для упругих элементов Учитывая высокую пластичность и вязкость металла после закалки, из сталей целесообразно изготовлять детали посредством глубокой штамповки с последующим упрочнением отпуском Значительное количество остаточного аустенита при соответствующих режимах термообработки обеспечивает высокую пластичность и ударную вязкость сталей при отрицательных температурах и позволяет рекомендовать стали для изделий криогенной техники, работающих до температур —196 °С [3] В этом случае для обеспечения высокой надежности в эксплуатации стали не следует подвергать старению
Рис 19 1 Структура стали 07Х16Н6 (а) и шва (б) аналогичного состава после полного цикла термической обработки Х200 |
19.2. Свариваемость сталей
19.2 1. Структура, свойства металла шва и зоны термического влияния
После сварки сталей, прошедших полный цикл упрочняющей термообработки и имеющих благодаря этому мартенситную структуру, наблюдается широкая зона, имеющая после высокотемпературного нагрева структуру аустенита. Ширина зоны определяется температурой обратного мартенситного превращения металла (Ас—Ас3) (650—750 °С). Одновременно в интервале температур 550—900 °С происходит интенсивное выделение карбидов (рис 19 2), особенно по границам аустенитных зерен. Кроме того, в узкой зоне, примыкающей к поверхности сплавления, наблюдается образование некоторого количества
6- феррита Структурные превращения в зоне термического влияния приводят к снижению пластичности и ударной вязкости металла, а также его чувствительности к концентраторам
ТАБЛИЦА 19 3 МЕХАНИЧЕСКИЕ СВОЙСТВА СТАЛЕЙ АУСТЕНИТНО МАРТЕНСИТНОГО КЛАССА ПРИ НОРМАЛЬНЫХ ТЕМПЕРАТУРАХ [i J
|
Рис 19 3 Изменение ударной вязкости О 1 KCV-m металла ЗТВ в стали 07Х16Н6 6 = = 11 мм в состоянии после сварки (сварка в ар гоне плавящимся электродом диаметр про волоки 2,0 мм /св=350 А) [2] |
Рис 19 2 Структура зоны термине ского влияния сварного соединения стали 07Х16И6 в состоянии после свар ки X100 |
напряжений (рис. 19.3). Кроме того, эти превращения снижают коррозионную стойкость и стойкость против межкристаллит- ной коррозии ЗТВ.
19.2.2. Хрупкость сварных соединений
Обратное мартенситное превращение в ЗТВ и ограниченный объем последующего мартенситного превращения при охлаждении до комнатной температуры исключает при сварке сталей этого класса образование холодных трещин. Вместе с тем интенсивное выделение карбидов, и особенно образование 6-феррита, приводят к хрупкому разрушению сварных соединений в зонах структурных изменений, особенно при понижении температуры до —196 °С. Последнее объясняется резким снижением пластичности 6-феррита. В этом случае полная термообработка (закалка, обработка холодом, отпуск) позволяет получить оптимальные соотношения аустенита и мартенсита, а также отсутствие 6-феррита. При этом восстанавливается вязкость зоны сплавления при сохранении прочностных характеристик сварного соединения на уровне 0,9 ов основного металла в случае выполнения сварки материалами мартенситного либо аустенитно-мартенситного класса.
19.3. Технология сварки и свойства соединений
19.3.1. Выбор сварочных материалов
Соединения стали аустенитно-мартенситного класса целесообразно выполнять аргонодуговой сваркой без присадки (тонколистовые детали) либо с присадкой перечисленными ниже материалами, а также контактной точечной и роликовой сваркой и электронно-лучевой сваркой.
В случае сварки соединений, для которых отсутствует требование равнопрочности, допускается ручная электродуговая сварка электродами, дающими аустенитный наплавленный металл, либо механизированная сварка под слоем флюса марки АН-26с по ГОСТ 9087—81 либо марки 48-ОФ-6 по ОСТ 5.9206—76.
Выбор присадочного материала осуществляют, исходя из требований прочности сварного соединения. В случае отсутствия требований высокой прочности к швам в качестве присадочной можно рекомендовать аустенитную проволоку Св-01X19Н18Г10АМ4 (ТУ 14-1-1892—71) либо Св-08Х21Н10Г6 (ГОСТ 2246—70), обладающих хорошей стойкостью против образования горячих трещин и высокой прочностью и пластичностью в широком интервале температур, в том числе отрицательных (до —196 °С).
ТИПИЧНЫЕ СВОЙСТВА СВАРНЫХ СОЕДИНЕНИЙ ИЗ НЕРЖАВЕЮЩИХ СТАЛЕЙ АУСТЕНИТНО-МАРТЕНСИТНОГО КЛАССА
|
При наличии требований высокой прочности сварных соединений рекомендуется к применению аустенитно-мартенситные проволоки СВ-07Х16Н6, Св-08Х17Н5МЗ, Св-09Х15Н9Ю (ТУ I4-I-997— 74), Св-01Х12Н11М2ТС (ТУ 14-1-3482—82).
Механические свойства сварных соединений, полученных с применением некоторых из указанных сварочных материалов, приведены в табл. 19.4.
Прочность сварных соединений, сваренных аустеннтной присадочной проволокой, выше прочности самой присадки. Это объясняется стеснением деформации металла шва из-за более высокой прочности основного металла. Такой эффект по мере увеличения ширины шва и зоны с аустенитной структурой уменьшается.
19.3.2. Выбор режимов сварки
Режим сварки выбирают, исходя из способа сварки, толщины свариваемого материала, диаметра сварочной проволоки н других параметров.
Приведенные режимы сварки (табл. 19.5) могут быть скорректированы в зависимости от типа соединения, наличия разделки кромок, качества сборки, наличия либо отсутствия подкладки, положения шва в пространстве и т. д.
19.3.3. Выбор послесварочной термообработки
Влияние термического цикла сварки приводит к структурным изменениям, приводящим к охрупчиванию металла ЗТВ сталей, а также снижению их коррозионной стойкости и стойкости против межкристаллитной коррозии. Поэтому при изготовлении ответственных конструкций, к которым предъявляются требования высокой прочности, вязкости и коррозионной стойкости сварных соединений, целесообразно предусмотреть полный цикл
ОРИЕНТИРОВОЧНЫЕ РЕЖИМЫ СВАРКИ ВЫСОКОЛЕГИРОВАННЫХ СТАЛЕЙ АУСТЕНИТНО-МАРТЕНСИТНОГО КЛАССА
|
термообработки, включающий закалку, обработку холодом и отпуск. Режим термообработки в этом случае выбирают аналогичным термообработке основного металла (см. табл. 19.2).
В случае выполнения сварки крупногабаритных изделий, исключающих возможность закалки, следует сварное соединение подвергнуть обработке холодом и последующему отпуску. При этом несколько повышается ударная вязкость сварного соединения.
19.3.4. Коррозионная стойкость соединений
Стали аустенитно-мартенситного класса имеют после закалки с температур, достаточных для растворения карбидов, высокую коррозионную стойкость, определяемую прежде всего высоким содержанием хрома. Сварные соединения имеют равную коррозионную стойкость с основным металлом.
Мартенситное превращение при обработке холодом сталей,
ТАБЛИЦА 19 6 КОРРОЗИОННАЯ СТОЙКОСТЬ СТАЛЕЙ АУСТЕНИТНО — МАРТЕНСИТНОГО КЛАССА В РАЗЛИЧНЫХ СРЕДАХ [1]
|
прошедших закалку, не влияет на коррозионную стойкость и способность сталей к пассивации.
Низкотемпературный отпуск и старение после обработки холодом также не вызывают каких-либо изменений общей коррозионной стойкости.
Стали аустенитно-мартенситного класса 09X15Н8Ю,
07X16Н6, 08XI7H5M3 в соответствии с требованиями ГОСТ 6032—84 после полного цикла термообработки стойки также против межкристаллитиой коррозии. Вместе с тем при нагреве выше 500 °С наблюдается интенсивное падение стойкости против межкристаллитиой коррозии в связи с выделением по границам бывших аустенитных зерен карбидов, богатых хромом.
Холодная пластическая деформация сталей аустенитно-мартенситного класса, при которой образуется до 75 % мартенсита, не уменьшает склонность стали к общей и межкристаллитиой коррозии. Таким образом, нержавеющие стали рассматриваемого класса и их сварные соединения во многих случаях имеют хорошее сочетание высокой прочности и коррозионной стойкости в агрессивных средах (табл. 19.6).
hssco.ru
Хромоникелевые стали | Учебные материалы
Никель относится к числу металлов, легко приобретающих пассивность, хотя его пассивирующая способность меньше хрома и молибдена. Ni — аустенитообразующий элемент, поэтому сталь, содержащая 18 % Сr и 9 % Ni, при комнатной температуре имеет структуру аустенита.
Нержавеющие стали, имеющие аустенитную структуру, обладают более высокой коррозионной стойкостью, лучшими технологическими свойствами по сравнению с хромистыми нержавеющими сталями, в частности лучшие свариваются. Они сохраняют прочность до более высоких температур, и в то же время аустенитные стали не теряют пластичности при низких температурах.
Хромоникелевые стали в зависимости от состава и структуры подразделяются на стали аустенитного, аустенитно-мартенситного и аустенитно-ферритного классов. На рисунке 49 приведена диаграмма Шеффлера, позволяющая определять структуру стали в зависимости от ее состава.
Эквивалентные содержания никеля и хрома зависят от химического состава стали и определяются по формулам:
Сrэ=% Сr + % Mo + 2×% Fe + 2×% Ti + 0,5×% Nb + % W + 0,5×% Ta + 1,5×% Si;
Niэ= % Ni + 30×% С + 30×% N + 12×% B + % Сo + 0,5×% Mn.
Хромоникелевые стали выпускаются марок:
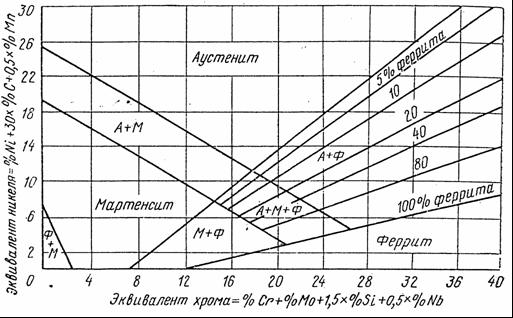
Рисунок 49 — Структурная диаграмма Шеффлера
Вторая и третья группы сталей являются заменителями аустенитных сталей. Термическая обработка нержавеющих сталей аустенитного класса заключается в закалке в воде с 1050…1100 0С. Нагрев до этих температур вызывает растворение карбидов хрома М23С6, а быстрое охлаждение фиксирует состояние пересыщенного твердого раствора. Кроме того, при закалке происходят рекристаллизационные процессы, устраняющие последствия пластической деформации. В результате закалки твердость сталей аустенитного класса не повышается, а снижается.
Основным способом упрочнения аустенитных сталей является наклеп: при деформации порядка 80…90 % предел текучести может достигать 1000…1200 МПа, а предел прочности 1200…1400 МПа при сохранении достаточно высокой пластичности. Но этот способ упрочнения применим лишь для таких видов изделий, как тонкий лист, лента, проволока и т.п. Все аустенитные стали не магнитны. Хорошо работают в растворах азотной, уксусной, фосфорной, органических кислот, растворах солей, щелочей, в атмосферных условиях.
Аустенитно-мартенситные стали
Стали аустенитно-мартенситного класса обладают более высокой прочностью. Упрочняются закалкой от 975 0С, а для перевода большей части аустенита в мартенсит подвергают обработке холодом в интервале температур от минус 50 0С. После этого проводится отпуск при 450…500 0С; при этом из мартенсита выделяются частицы интерметаллидов типа Ni3Al.
Аустенитно-ферритные стали
Предложены как заменители аустенитных сталей с целью экономии никеля. Они имеют прочность и твердость выше, но пластичность и ударную вязкость ниже, чем аустенитные стали. Эти стали не обладают стабильностью свойств: их свойства зависят от соотношения ферритной и аустенитной фаз. Закалка проводится с 1000…1150 0С.
Механические свойства некоторых хромоникелевых сталей после закалки приведены в таблице 12.
Таблица 12 — Механические свойства сталей в закаленном состоянии
Марка стали | sigmaв, МПа | sigma0,2, МПа | d, % | y, % |
04Х18Н1008Х18Н1012Х18Н1017Х18Н1009Х15Н8Ю:закалказакалка + отпуск09Х17Н7Ю08Х22Н6Т | 450480500580 9001300900960 | 180200200220 2501100700370 | 40404040 30201022 | 60555550 65504051 |
Коррозионностойкие сплавы на железоникелевой и никелевой основе
Они применяются для обеспечения более высокой коррозионной стойкости в таких средах, как серная и соляная кислоты. В этих случаях используют сплавы на железоникелевой основе, например, сплав 04ХН40МДЮ, имеющий после закалки и отпуска при 650…700 0С структуру аустенит и интерметаллидную g- фазу типа Ni3 (Ti, Al). Сплав предназначен для работы при больших нагрузках в растворах серной кислоты.
Для работы в соляных средах, растворах серной, азотной, фосфорной кислот применяется никелевый сплав Н70МФ. Сплав ХН65МВ применяется для работы при повышенных температурах во влажном хлоре, солянокислотных и сернокислых средах, хлоридах, смесях кислот и других агрессивных средах.
dprm.ru
ХРОМОНИКЕЛЕВЫЕ АУСТЕНИТНО-МАРТЕНСИТНЫЕ И МАРТЕНСИТНО-ФЕРРИТНЫЕ СТАЛИ
Высоколегированные хромоникелевые коррозионно-стойкие стали послужили основой для создания высокопрочных сталей, обладающих одновременно и высокой ударной вязкостью. По принципу упрочнения эти стали можно подразделить на две группы — мартенситно-стареющие и аустенитно-мартенситные (промежуточные). Стали первой группы условно подразделяют на две подгруппы — низкоуглеродистые и безуглеродистые (по данным Я — М. Потака).
Низкоуглеродистые мартенситно-стареющие стали по своему химическому составу относятся к сталям мартенситного класса. При закалке таких сталей с температуры аустенитизации ~ 1000 °С их структура должна состоять из мартенсита и небольшого количества остаточного аустенита (~ 10 %), поскольку температура начала и конца мартенситного превращения выше 20 °С (по данным Я. М. Потака у стали 08Х15Н5Д2Т Мн = 130 °С, Мк = — 30 °С). Наличие в стали небольшого количества остаточного аустенита способствует повышению ударной вязкости стали, а мартенситная основа — повышению прочности. Если количество аустенита после закалки оказывается слишком большим и отрицательно сказывается на прочности, оно может быть снижено путем охлаждения закаленной стали — обработкой холодом (при температуре до —70 °С).
Дополнительное повышение прочности закаленной стали достигается при старении — отпуске на температуру —450 °С, когда достигается максимальная прочность. Упрочнение при старении происходит в результате выделения интерметаллидных фаз (NiTi, NiAl, Ni3Ti, Ni3Al и др.), т. е. главным образом соединений, содержащих титан и алюминий. Значение легирования титаном состоит и в том, что титан, связывая углерод в карбиды, уменьшает его содержание в мартенсите (в виде перенасыщенного раствора) и тем самым способствует повышению ударной вязкости стали. Повышению вязкости этих сталей после старения способствует наличие значительного количества никеля, увеличивающего способность дислокаций к перемещению (по данным Я. М. Потака).
Безуглеродистые хромоникелевые мартенситно-стареющие стали содержат до 0,03 % С. Это определяет, с одной стороны, возможность сохранения мартенситом вязкости, а с другой — эффективность развития процесса старения, связанного с наличием в стали титана. В стали также должно быть определенное количество молибдена для предотвращения чрезмерного охрупчивания при старении. После закалки стали становятся почти полностью мартенситными (количество остаточного аустенита ~ 3 %) в связи с низким содержанием в них углерода. Эти стали наряду с высокой прочностью имеют хорошие кислотостойкость, хладостойкость и высокий предел упругости.
Стали переходного класса — аустенитно-мартенситные приобретают такое состояние после охлаждения из аустенитной области в связи с тем, что определяемая составом температура начала их мартенситного превращения находится вблизи нормальной (20—60 °С). Достаточно быстрое охлаждение может зафиксировать почти полностью аустенитное состояние стали, но аустенит должен быть нестабильным и распадаться при пластической деформации с образованием мартенсита. Такой же распад нестабильного аустенита достигается обработкой холодом при —50 -4- —70 °С. Отпуск стали, обработанной на мартенситно-аустенитную структуру, как и сталей рассмотренных типов, приводит к остариванию мартенсита и повышению прочности стали. Содержание углерода в этих сталях может быть более высоким, чем в мартенситно-стареющих, так как наличие значительного количества аустенита обеспечивает получение достаточной ударной вязкости.
Коррозионно-стойкие высокопрочные стали вполне технологичны. Их следует обрабатывать в состоянии до старения. После нагрева до аустенитного состояния и неполного охлаждения (выше 200 °С), когда стали остаются аустенитными, они хорошо деформируются (табл. 10.7).
Несмотря на сложный химический состав, высокое содержание легирующих элементов и в некоторых случаях сложность фазовых и структурных изменений, хромоникелевые высоколегированные стали различного назначения можно отнести к удовлетворительно, а иногда и хорошо свариваемым. Однако сварка этих сталей и обеспечение требуемых свойств сварных соединений часто требуют принятия специальных мер. Важные исследования по сварке высоколегированных хромоникелевых сталей были проведены в ИЭС им. Е. О. Патона Б. И. Медоваром, Н. И. Каховским, К. А. Ющенко и др.
Сложность сварки хромоникелевых высоколегированных сталей во многом определяется их структурным классом и состоянием, фазовыми превращениями, которые могут протекать при сварочном нагреве и охлаждении, и специфическими требованиями к свойствам, которыми должны обладать сварные соединения жаропрочных, хладостойких, кислотостойких и высокопрочных сталей.
Основные трудности сварки связаны со склонностью к образованию горячих трещин в швах и околошовных зонах (аустенитные стали) и склонностью к образованию холодных трещин в ЗТВ (мартенситные и аустенитно-мартенситные стали), с появлением после сварочного нагрева в высокотемпературной зоне 6-феррита, выделением карбидов из аустенита в определенных участках ЗТВ и ухудшением в этих местах стойкости против межкристаллитной коррозии (МКК) и других свойств. Определенные осложнения вносит повышенное, по сравнению, с железом, сродство хрома к кислороду и вследствие этого его повышенная окисляемость и возможная в связи с этим загрязненность металла шва. В аусте-
9BS
ните с высоким содержанием никеля растворимость водорода повышена, что может стать причиной повышенной пористости.
hssco.ru
МАРТЕНСИТНО-СТАРЕЮЩИЕ СТАЛИ (Лазько В. Е.)
СВАРКА И СВАРИВАЕМЫЕ МАТЕРИАЛЫ
20.1. Состав, структура сталей и их назначение
Мартенситно-стареющие стали отличает особый механизм упрочнения, основанный иа выделениях иитерметаллидов типа Ni (Ті, Ai), Ni3Ti, Ni3Mo при нагреве 400—550 °С твердых рартворов железа с никелем и добавками различных элементов замещения При этом обеспечивается ств= 1500-4-2000 МПа, а для ряда композиций до 2800 МПа. Максимальное упрочнение при старении достигается в безуглеродистых сплавах как необходимом условии предотвращения связывания легирующих элементов в карбиды. Поэтому образующийся при закалке таких сталей мартенсит сравнительно мягок (ств = 700—1100 МПа) и пластичен.
Основной системой легирования мартеиситно-стареющей стали, обеспечивающей максимальный уровень прочности, является железоникелевый сплав (18—25% Ni), содержащий добавки Мо, Со, Ті и Al (Н18К9М5Т, Н18К8М5ТЮ, Н18К12М5Т и др.). Другой распространенной системой, обеспечивающей уровень прочности сГв=£Д600 МПа, является железохромоникелевый сплав (10—13% Сг и 5—10% Ni) с добавками Мо, Со, Ті и А1 (Х11Н10М2ТЮ, Х12Н9К4МВТ, 03Х12К14Н5М5Т и др.). В структуре этих сталей может быть 10—40 % остаточного аустенита Третьей системой легирования мартенситио-стареющих сталей, обеспечивающей уровень прочности Ов<Д500 МПа, является сплав Fe с 12% Ni и дополнительным легированием Си, Мп, V и другими элементами, вызывающими умеренное старение (Н12М2Д2ТЮ, 03h22X5M3, Н8Г4ФЗД2 и др.). Четвертой системой легирования - является железоиикелькобальтовый сплав (9% Ni — 4% Со) с добавками карбидообразующих элементов и содержанием С 0,2—0,4 %. Смешанный карбидно-интерметаллидный механизм упрочнения обеспечивает уровень прочности Ств= 1300-г-2000 МПа. Химический состав некоторых мар - тенситно-стареющих сталей и их свойства приведены в табл. 20.1
Микроструктура типичных мартенситио-стареющих сталей представляет так называемый «массивный» мартенсит в виде пакетов ферритных пластин, разделенных малоугловыми границами. Высокая плотность дислокаций и границ в объеме мартенсита обеспечивает однородное распределение выделяющихся при старении частиц с расстоянием между ними 0,2—0,5 мкм.
Мартеиситно-стареющие стали изготавливаются в виде поковок, штамповок, листов, отливок, прутков и проволоки, в том числе и сварочной Для стабилизации значений пластических характеристик, увеличения усталостной прочности и предотвращения водородного охрупчивания применяется вакуумный переплав металла, повышающий чистоту по содержанию неметаллических включений, газов и примесей Цветных металлов. Для уменьшения содержания углерода и азота в некоторых случаях применяют электронно-лучевой переплав.
Относительно высокая стоимость мартенситио-стареющих сталей ограничивает применение конструкциями, где на первый план выдвигается необходимость обеспечения повышенной удельной прочности, в том числе и при сварке закаленных элементов, при низкой чувствительности к наличию над-
Т А БЛИЦ А 20.1 ХИМИЧЕСКИЙ СОСТАВ И МЕХАНИЧЕСКИЕ СВОЙСТВА МАРТЕНСИТИО-СТАРЕЮЩИХ СТАЛЕЙ
|
резов и трещииоподобиых дефектов Типичные области применения: оболочки летательных аппаратов, корпуса двигателей, сосуды высокого давлення, изделия криогенного назначения и др. [1].
20.2. Свариваемость сталей
20.2.1. Фазовые и структурные превращения
По свариваемости мартенситно-стареющие стали превосходят широко используемые углеродистые легированные стали. Они мало чувствительны к образованию горячих и холодных трещин; обеспечивают повышенный уровень механических свойств сварных соединений в нетермообработанном состоянии и возможность достижения равнопрочности основному металлу проведением после сварки старения.
Высокая прокаливаемость мартенситно-стареющих сталей предопределяет получение мартенситной структуры независимо от скорости охлаждения после аустенитизации. Повышенное содержание легирующих элементов может сместить температуру окончания мартенситного превращения ниже комнатной, что обусловит наличие в структуре определенного количества остаточного аустенита. Другой причиной его появления является нагрев закаленной стали на температуру, близкую к 600 °С, что приводит к обратному а—у-превращению.
Как при сварке в термоупрочненном, так и отожженном состоянии старение в зоне термического влияния происходит там, где нагрев достигал температур 480—540 °С. В тех случаях ЗТВ, где температура была 650 °С, мартенсит распадается на феррит и обогащенный никелем и, следовательно, стабильный аустенит. При охлаждении до комнатной температуры эти структурные составляющие сохраняются и не претерпевают изменений в результате старения после сварки.
ТАБЛИЦА 20.2 ХИМИЧЕСКИЙ СОСТАВ И СВОЙСТВА СВАРОЧНЫХ ПРОВОЛОК
|
20.2.2. Сопротивляемость ГТ
Благодаря низкому содержанию углерода в большинстве марок мартенситио-стареющих сталей сопротивляемость ГТ находится на высоком уровне (табл. 20.2). Случаи поражения сварных швов горячими трещинами наблюдались при содержании С 0,1—0,2 % или наличии в сварочной проволоке редкоземельных элементов свыше 0,03 %. Согласно [1], сварочная проволока не должна также содержать Са, В и Zr. Легирование Со до 5 % приводит к увеличению сопротивляемости трещинам [2].
20.2.3. Сопротивляемость ХТ
Безуглеродистые и малоуглеродистые мартенситно-стареющие стали проявляют чувствительность к образованию ХТ только в ' присутствии Н. Неравномерность распределения водорода по зонам сварного соединения предопределяет места преимущественного зарождения трещин по центру сварного шва, линии сплавления и карбидной сетке в зоне термического влияния. Особенно неблагоприятна многопроходная сварка, при которой увеличение продолжительности пребывания металла в температурном интервале выпадения карбидов и интерметаллидов приводит к росту размеров включений, повышению локального напряженного состояния и концентрации Н, облегчающих зарождение трещин. Предотвращение образования ХТ достигается при наличии в структуре свыше 20 % остаточного аустенита. Действие легирующих элементов обусловлено в основном влиянием двух факторов: изменения растворимости Н и содержания остаточного аустенита в металле шва. При мартенситной структуре повышение содержания Мо и Ni ухудшает, а Мп и Со увеличивает сопротивление холодным трещинам в соответствии с изменением растворимости Н. В то же время Ni и Мо могут играть положительную роль, если при легировании образуется остаточный аустенит.
20.2.4. Структурные и технологические дефекты сварных соединений
Низкий уровень содержания элементов-раскислителей (С, Si и Мп) в мартенситио-стареющих сталях обусловливает определенные трудности с предотвращением образования пористости, несплавлений и загрязненности неметаллическими включениями металла шва. Развитие указанных явлений в существенной мере зависит от содержания А1 и Ті, определяющих также и уровень прочности соединения. Типичное содержание А1 и Ті в сварочных проволоках вызывает неравномерное окисление легирующих элементов в зоие сварки и, как следствие, нестабильность
состава и свойств металла шва. Окисление титана, кроме того, приводит при сварке малых толщин к образованию на поверхности металла шва местных утолщений в виде пленки окислов, а также криволинейной форме соединения вследствие повышенного эффекта блуждания дуги (перемещения анодного пятна на участок металла, свободного от шлаков).
Специфический дефект сварных швов—дендритный излом, сопровождаемый резким ухудшением ударной вязкости и усталостной прочности металла шва. В первую очередь этому способствует укрупнение размера зерна в металле шва с более высоким содержанием Ni при чрезвычайной устойчивости возникшей крупнозернистой структуры к различного вида термической обработке (структурная наследственность). Другая причина связана с высокой химической неоднородностью распределения элементов, в частности Ті и Мо, способствующих неравномерному распаду твердого раствора при старении с образованием скоплений грубых частиц по границам крупнозернистого металла. Обычно применяемая для предотвращения грубокри - сталл'итной структуры металла шва регламентация 1,5—4 % б-феррита, препятствующего прорастанию дендритов через несколько слоев, ограничена только группой нержавеющих мар - тенситно-стареющих сталей, где возможно добиться необходимого соотношения между феррито - и аустенитообразующими элементами.
20.3. Технология сварки и свойства сварных соединений
20.3.1. Способы сварки плавлением
Мартенситно-стареющие стали могут свариваться всеми видами сварки. Благодаря специфическому механизму упрочнения технология изготовления различных изделий из этих сталей отличается простотой и надежностью. Это связано как с возможностью сваривать без подогрева и последующего немедленного отпуска, так и обеспечить близкие к основному металлу свойства применением после сварки простой операции старения.
Наиболее распространенными способами сварки мартенсит - но-стареющих сталей являются ЭЛС и аргонодуговая сварка вольфрамовым электродом: импульсная, с поперечными колебаниями электрода, со сканирующей дугой (для малых толщин) и в щелевую разделку (для больших толщин). Указанные способы сварки обеспечивают мелкозернистое строение металла шва, малый перегрев околошовной зоны и близкие к основному металлу механические свойства. Для устранения глубоко залегающих дефектов применяют вращающийся неплавящийся электрод при осевой подаче присадочной проволоки. Используемые присадочные проволоки обычно имеют близкий к основному металлу состав (табл. 20.2). Для компенсации потерь упрочняющих элементов при выгорании их содержание может быть увеличено по сравнению со свариваемой сталью [1].
К достаточно распространенным способам дуговой сварки следует отнести ручную штучными электродами с покрытием и/ автоматическую под слоем флюса. Имеется ряд работ о возч можности получения качественных сварных соединений при ис/ пользовании самозащитной порошковой проволоки или сварке в углекислом газе [3, 4].
Весьма перспективно применение лазерной сварки, позволяющей получить соединения с большей стойкостью против коррозионного растрескивания, чем при ЭЛС и АДС.
20.3.2. Способы сварки давлением
Контактная стыковая сварка Сопротивлением весьма подходит для соединения мартенситио-стареющих сталей. Этот способ с успехом применяется, когда необходимо получить более или менее одинаковые сварные детали, и он очень удобен при проведении предварительных опытов по нахождению оптимальных условий сварки.
Наиболее широко распространена контактная точечная сварка. Сравнительно мягкий и пластичный мартенсит предотвращает преждевременное разрушение по присущему этому типу соединений концентратору напряжений, что наблюдается при сварке обычной высокопрочной стали.
Для изготовления единичных деталей применяется диффузионная сварка и сварка взрывом. Для определенных деталей перспективна сварка трением.
20.3.3. Меры предотвращения дефектов
Для предотвращения пористости при сварке все материалы и агрегаты должны быть скрупулезно чистыми. Детали, изготовленные резанием с использованием СОЖ, необходимо обезжирить, а затем промыть горячей водой для удаления натрийсодержащих веществ на свариваемых кромках, вызывающих пористость н интенсивное разбрызгивание. Для снижения концентрации растворенных элементов и получения более гладкого сварного шва кромки листа должны быть по возможности скошены.
Особое внимание следует уделять закреплению и установке свариваемого изделия в приспособлении. При некачественной подгонке сварочных стыков, когда зазоры в корневой части составляют около 1,6 мм, предотвращение горячих трещин представляет серьезную проблему. Особо подвержены растрескиванию при кристаллизации угловые швы, поскольку проплавление более тонкой пластины увеличивает ширину зазора между сварочными кромками, тем самым задерживая кристаллизацию центральной части шва. Сопротивляемость горячим трещинам і можно повысить увеличением коэффициента формы шва, что (достигается переходом от однопроходной к двухпроходной сварке, увеличением угла разделки кромок и изменением состава защитного газа. Сварка на пониженных токах также способствует устранению трещин вследствие перехода от швов с вогнутой формой к выпуклой.
I Для предупреждения формирования по высоте сварного шва оревого столба кристаллитов и возникновения древовидного излома при многопроходной сварке следует стремиться к щелевой разделке кромок. Целесообразно также менять от слоя к слою направление сварки, что дезориентирует структуру металла шва, снижая чувствительность к горячим трещинам и образованию дендритного излома. Этим же целям служит и сварка на оптимальных скоростях, приводящая к смене ячеистой на дендритную структуру металла шва.
Для предотвращения холодных трещин следует ограничивать содержание Н в соединении менее 0,5—0,8 см3/100 г. Это достигают как проведением-обезводороживающего отжига основного металла и сварочной проволоки, так и отпуска или старения после сварки в интервале 300—540 °С. Следует тщательно контролировать проведение многопроходной сварки, добиваясь отсутствия мартенситного превращения в нижележащих слоях перед выполнением последующих слоев (сварка с предварительным и сопутствующим подогревом, регулирование термического цикла сварки и др.). Это уменьшает уровень максимальных напряжений I и II рода и предотвращает карбидные выделения в корне шва, являющиеся местами аккумуляции водорода и зарождения холодных трещин.
Для гомогенизации и измельчения структуры металла шва перед окончательной термообработкой целесообразно проводить нормализацию с температур 1000—1050 °С. Это позволяет получать соединения с близкими к основному металлу пластическими и вязкими свойствами.
20.3.4. Механические свойства сварных соединений
Проведение после сварки упрочняющей термообработки делает сварное соединение равнопрочным основному металлу в случае идентичности химического состава. Однако небольшое снижение пластичности и вязкости металла шва может определить возникновение хрупкого разрушения, когда в условиях высокопрочного состояния уровень данных показателей для основного металла близок к минимально допустимым. Поэтому уровень прочности металла шва обычно не стремятся повысить сверх
Ов-1700 МПа. В тех случаях, когда для обеспечения работоспособности конструкции важна ударная вязкость, применяют сварку без последующей термообработки. При этом предел і прочности соединений близок Ов-1000 МПа при KCU = / = 1 МДж/м2. При многослойной сварке применяют подогрев,/ предотвращающий охлаждение наплавленных слоев ниже тем 1 ператур у—a-превращения с явлением подстаривания. В про/ тивном случае старение мартенсита нижних слоев сопровождается возрастанием прочности и твердости и снижением вязкости металла шва. При этом достигается комплекс механических свойств, промежуточный между свойствами закаленного и термоупрочненного состояния. Для ряда мартенситио-стареющих сталей повышения надежности сварных соединений достигают отказом от проведения старения после сварки или применяют подстаривание при более низкой температуре (~350 °С) для ограничения уровня прочности металла шва и околошовной зоны.
20.3.5. Служебные свойства сварных соединений
Температура эксплуатации мартенситио-стареющих сталей не превосходит 400 °С в связи с явлениями старения н перестари - вания. Высокая хладностойкость позволяет успешно эксплуатировать сварные изделия до температур —70-------------------------- 100 °С, а из от
дельных марок стали и при криогенных температурах. Важнейшее свойство сварных изделий — высокая несущая способность при приложении статических нагрузок, в том числе и при наличии концентраторов напряжений. Это не касается конструкций, работающих в условиях вибрационных нагрузок, где преимуществ по сравнению с высокопрочными низколегированными сталями не наблюдалось. При о0,2^1400 МПа в ряде случаев отмечалось ускоренное развитие трещин в сварных соединениях. Другим перспективным направлением использования мартенсит - но-стареющих сталей являетс
msd.com.ua