- 29 ноября
- 84 просмотров
- 51 рейтинг
- Виды электродов для сварки нержавеющей стали
- Особенности электродов для сварки нержавейки
- Этапы сварки нержавейки электродом
- Вольфрамовые электроды для сварки нержавейки
- ЦЛ-11-2, ЦЛ-11-2.5, ЦЛ-11-3, ЦЛ-11-4, ЦЛ-11-5;
- ЦТ-15;
- ОЗЛ6 (8).
- посредством воздействия высокой температурой, которая должна превышать значение в 1000 градусов Цельсия;
- за счет механической обработки, для которой используют шлифовальные материалы и инструменты;
- Помочь может и травление фосфорной или азотной кислотой. Эффект от этой процедуры будет заключаться не только в удалении слоя хрома, но и в придании шву повышенной прочности.
- особое внимание следует уделить работе по соединению заготовок, осуществляемой в температурном диапазоне 450- 500 градусов Цельсия. Подобная ситуация чревата риском образования кристаллизационных трещин, что негативным образом сказывается на прочности конструкции.
- Если сварка изделий из нержавейки выполняется долгое время в температурном диапазоне от + 360 до + 550 градусов Цельсия, то это может привести снижению пластических свойств изделия, что увеличивает его хрупкость.
- при возможности следует обеспечить минимальный шаг между прихватками, поскольку во время соединения нержавейки приходится использовать более длинные прихватки.
- еще до начала сварочных работ следует предварительно нагреть изделие до отметки 1000-1200 градусов Цельсия, после чего заготовке необходимо дать остыть на воздухе в течение 3 часов.
- чтобы получить качественный результат в процессе соединения нержавеющих сталей, следует выполнять эту операцию за минимальное время, стараясь свести к минимуму воздействие заготовки теплом. Если возникнет такая ситуация, то можно выполнить несколько проходов друг за другом, причем изделие необходимо охладить до + 100 градусов Цельсия.
- Автор: Фёдор Ильич Артёмов
- 6;
- 5;
- 4;
- 3;
- 2,5;
- 2;
- 1,6;
- 1,5;
- 1,4;
- 1,2;
- 1;
- 0,8;
- 0,7;
- 0,6;
- 0,5;
- 0,45;
- 0,4;
- 0,3;
- 0,25;
- 0,2.
- 12 – содержание углерода составляет 0,12%;
- Х18 – содержание хрома составляет 18%;
- Н10 – содержание никеля составляет 10%;
- Т – содержание титана составляет около 1%.
- ООО Металопром;
- Укринтерсталь;
- ИнтерПромАльп;
- Мицар.
- мартенситные нержавеющие стали;
- хромистые или ферритные стали;
- аустенитные стали.
Какими электродами варить сталь 12х18н10т. Электроды для сварки нержавеющей стали 12х18н10т
12Х18Н10Т электроды для сварки
Какими электродами варить сталь 12х18н10т.
В наше время практически всем людям доступны почты все марки и виды электродов. Электроды делятся по разным классам по своим характеристикам, например их можно поделить на электроды для сварки высоколегированных и низколегированных сталей. Также электроды делятся на классы по материалу покрытия: основное, кислотное и обычное. Список классов, на которые делятся электроды очень большой, поэтому нет смысла его полностью перечислять. Одним из видов электродов являются электроды для сварки стали 12х18н10т, то есть они предназначены для сварки хромоникелевых сталей.
Этот вид стали используется в тех случаях, когда изделие должно быть максимально устойчивым от коррозии и не поддаваться другим факторам окружающей среды. Также к изделиям, которые сварены электродами для сварки стали 12х18н10т предъявляются повышенные требования устойчивости от межкристаллической коррозии.
Во всем мире очень ценятся изделия из нержавеющей стали, поэтому популярность электродов для сварки стали 12х18н10т продолжает расти с каждым днем. Однако многих людей эти электроды привлекают еще и своим прекрасным сочетанием цены и качества. Поистине, такое сочетание встречается крайне редко, поэтому это как раз и является одним из самых главных преимуществ именно этих электродов.
А теперь давайте поговорим о самом процессе сваривания электродами для сварки хромоникелевых сталей. Сварка этими электродами производится во всех пространственных положениях при использовании постоянного тока обратной полярности. Также этим электродам сродни еще и такие качества, например стабильное горение дуги, низкое разбрызгивание металла, отличное формирование шва и легкая отделяемость шлака от поверхности изделия.
Непосредственно перед самим началом сваривания Вам необходимо прокалить электроды для сварки стали 12х18н10т в специальной печи для прокалки электродов при температуре от 300 до 350 градусов по Цельсию в течение одного часа. После полного остывания электроды готовы к использованию. Швы, сваренные этими электродами, могут поддаваться воздействию температуры до 350 градусов. Сварка электродами для сварки хромированной стали может, производится, как и ручная, так и дуговая в инертном газе.
Также для сварки этими электродами применяются еще и такие виды сварки, как плазменная сварка, импульсно-дуговая сварка, точечная и роликовая сварка, сварка в среде активных газов, сварка под флюсом, а также возможна и сварка сопротивления. Во время сваривания образуется пористый оксидный слой, который содержит в своем составе хром. Это приводит к снижению к устойчивости от коррозии, поэтому если Вам необходима высокая устойчивость к коррозии, то Вам нужно поддать материал последующей обработке для того чтобы изделие осталось таким же еще через несколько десятков лет.
Вот уже долгое время многие хозяиновитые люди продолжают сваривать для своего дома изделия из хромированной стали. Они без проблем заказывают их через пункт меню «Контакты» и остаются довольными.
elektrod-3g.ru
Виды и особенности электродов по нержавейке
Оглавление: [скрыть]
Использовать электроды по нержавейке необходимо для соединения разнообразных стальных конструкций. Оксид хрома образует на стали защитную пленку, которая придает ей нержавеющей стойкости и защищает от коррозии. В состав металла может входить никель, марганец и титан. Такую сталь широко используют в пищевой, химической и нефтехимической отраслях производства. Поэтому от правильно выбранного электрода будет зависеть прочность и долговечность всей конструкции.
Схема сварки нержавейки.
Виды электродов для сварки нержавеющей стали
Какой бы агрессивной ни была окружающая рабочая среда, воздействующая на стальную конструкцию, решение все же есть. Современные производители находят все новые составы для покрытия электродов, чтобы они при расплавлении и окислительно-восстановительных реакциях в газовой среде образовывали прочные сварочные швы. Особенностью электродов для различных видов стали является содержимое шлака, которое образуется при сгорании его основы.
Схема устройства электрода.
Электроды по нержавейке должны легко зажигаться и устойчиво гореть при сварочной дуге, равномерно расплавляться и покрывать шов изделия и легко удаляться после варки.
Электроды для сварки нержавеющей стали бывают нескольких видов, но зарекомендовали себя только некоторые из них:
Резкие перепады температуры или давления для нержавеющей стали, сваренной такими электродами, совсем не страшны.
Вернуться к оглавлению
Каждый мастер сварочных работ однажды задавался вопросом о том, какими электродами варить нержавейку.
Их всех объединяет похожий состав покрытия, именуемый флооритно-кальциевый тип. Хромоникелевые стали 12Х18Н10Т, 12Х18Н9Т, 08Х18Н12Т, 08Х18Н12Б, имеющие высокие требования к качеству шва, свариваются именно такой маркой электродов. Все пространственные положения швов обрабатываются током, который имеет обратную полярность. На 1 кг наплавленного металла расходуют 1,5 кг ЦЛ-11. И ЦТ-15. Чаще всего применяют электроды данной марки для сварки основных узлов в машиностроительной, нефтяной и химической промышленности. Данный вид электродов имеет сопротивление в семь раз больше, чем у обычных.
Таблица разновидностей электродов.
Если толщина нержавеющего металла менее 0,8 мм, то лучше всего использовать капельный перенос покрытия электрода и импульсную сварку.
Часто в быту многие сварщики используют вольфрамовые электроды, а для создания защитной среды — аргон. Он повышает качественные показатели электрической дуги и, соответственно, стойкость шва.
Тонколистный металл и трубы можно с легкостью соединять с помощью вольфрамовых электродов. Сварочный ток находится в пределах от 80 А и до 130 А в зависимости от толщины металла.
Присадочная проволока, которую вы выбрали для сварки, по химическому составу должна быть похожа на нержавейку. Тогда и качество шва буде выше.
Вернуться к оглавлению
Работать с нержавеющей сталью должен профессионал. Это точная и трудоемкая работа, при которой нужно добиться такого результата, чтобы соединение вышло очень похожим на основной металл. Для начала нужно тщательно зачистить края нержавейки до гладкого состояния, а место соединения обезжирить ацетоном или растворителем.
В качестве сварочного аппарата используют инвертор. Он удобен в транспортировке, питается от сети. При помощи электрики образовывается дуга для сваривания металла.
Состав и механические свойства разных марок нержавеющей стали.
Мощность тока не должна превышать допустимые нормы. В противном случае электрод может быстро сгореть или шов будет неплотным.
Большое сопротивление при варке нержавеющей стали — это одна из отличительных сторон работы, включая постоянный ток, имеющий обратную полярность. Тепло электроды проводят плохо. Это и есть причина их мгновенного разрушения при использовании тока высокого значения. Чтобы шов был максимально прочным, нужно его охлаждать. Используют для этого обдув воздухом и прокладку из меди. Если в состав стали входит никель или хром, то для охлаждения подойдет вода.
Приступая к работе, нужно настроить ток и выбрать электроды по нержавейке. К металлу их подносят очень аккуратно, чтобы не было залипаний. Клемму массы подключают к материалу. Затем поджигают дугу. Под углом к поверхности металла подносят электрод и придерживают его на расстоянии нескольких миллиметров. Образовавшуюся окалину аккуратно убирают с помощью молотка и тщательно зачищают шлифовальными кругами или металлической щеткой. Но полностью удалить слой оксида сможет только раствор кислоты. Готовую конструкцию опускают в ванну с данным веществом и после удаления окалины шлифуют.
Важной особенностью при сварочных работах является контроль промежутка дуги. Шов будет выглядеть криво, если промежуток дуги слишком большой, и, наоборот, не успеет схватиться, если он маленький. Ведь с помощью дуги плавится нержавеющий металл.
Угол наклона электрода для нержавейки должен быть не большим и не маленьким.
Вернуться к оглавлению
При работе с вольфрамовыми электродами используют постоянный источник тока. Эти навыки можно получить только тогда, когда имеется значительная практика работы с нержавейкой. Ведь сварка такого вида металла должна выполняться поэтапно, с соблюдением всех правил, написанных в инструкции. Качество шва не будет идеальным, если кромки деталей не прошли предварительную подготовку к сварке. Для тонких металлов, листов стали, различных конструкций из труб, которые предназначены для водопровода или отопления, подойдет аргонодуговая сварка с использованием неплавящегося электрода. При этом электродные покрытия и флюсы не применяют, а вот дополнительное наплавление металла вполне возможно. Шов при такой сварке получается очень качественный.
В проволоке для присадки должно быть больше легируемого элемента, чем в нержавейке. Работу выполняют точно, без колебаний, потому что возле шва может произойти окисление, и он потеряет прочность.
Важным моментом при работе с вольфрамовыми электродами является недопустимость попадания в ванну сварки вольфрама. Чтобы это предупредить, нужно произвести зажигание на угольном или графитовом листе. Как только работа подойдет к завершению, через 15 секунд нужно прекратить подачу аргона, тогда электрод прослужит дольше и не окислится.
Успех сварочных работ напрямую зависит от ваших знаний, умений и опыта.
expertsvarki.ru
Электроды для сварки коррозионно-стойких сталей и сплавов.
Сеть профессиональных контактов специалистов сварки. | ||
Темы: Электроды сварочные, Сварка стали , Ручная дуговая сварка.
Электроды этой группы обеспечивают получение сварных соединений, обладающих требуемой стойкостью против коррозии в атмосферной, кислотной, щелочной и других агрессивных средах.
Некоторые электроды данной группы имеют более широкую область применения и их можно использовать не только для получения соединений с требуемыми коррозионной стойкостью, но и как электроды, обеспечивающие высокую жаростойкость и жаропрочность металла шва.
Согласно действующей классификации к высоколегированным сталям относят сплавы, содержание железа в которых более 45%, а суммарное содержание легирующих элементов не менее 10%, считая по верхнему пределу при концентрации одного из элементов не менее 8% по нижнему пределу. К сплавам на никелевой основе относят сплавы с содержанием не менее 55% никеля. Промежуточное положение занимают сплавы на железоникелевой основе.
В соответствии с ГОСТ 10052-75 электроды для сварки высоколегированных коррозионно-стойких, жаростойких и жаропрочных сталей и сплавов по химическому составу наплавленного металла и механическим свойствам металла шва и наплавленного металла классифицированы на 49 типов (например, электроды типа Э-07Х20Н9, Э-10Х20Н70Г2М2Б2В, Э-28Х24Н16Г6). Наплавленный металл значительной части электродов, регламентируется техническими условиями предприятий - изготовителей.
Химический состав и структура наплавленного металла электродов для сварки высоколегированных сталей и сплавов отличаются (иногда существенно) от состава и структуры свариваемых материалов. Выбирая электроды, внимание обращают на обеспечение: основных эксплуатационных характеристик сварных соединений (механических свойств, коррозионной стойкости, жаростойкости, жаропрочности), стойкости металла шва против образования трещин, требуемого комплекса сварочно-технологических свойств.
Электроды для сварки высоколегированных сталей и сплавов имеют покрытия основного, рутилового и рутилово-основного видов.
Из-за низкой теплопроводности и высокого электросопротивления скорость плавления, а следовательно и коэффициент наплавки электродов со стержнями из высоколегированных сталей и сплавов существенно выше, чем у электродов для сварки углеродистых, низколегированных и легированных сталей. Вместе с тем повышенное электросопротивление металла электродного стержня обуславливает необходимость применения при сварке пониженных значений тока и уменьшения длины самих стержней (электродов). В противном случае из-за чрезмерного нагрева стержня возможен перегрев покрытия и изменение характера его плавления, вплоть до отваливания отдельных кусков.
Сварка, как правило, производится постоянным током обратной полярности.
Электроды | Тип электродов по ГОСТ 10052-75 или тип наплавленного металла | Диаметр, мм | Основное назначение | Дополнительная или сопутствующая области применения |
УОНИ-13/НЖ 12Х13 | Э-12Х13 | 2,0;2,5;3,0; 4,0;5,0 | Сварка хромистых сталей типа 08Х13, 12Х13 | Наплавка уплотнительных поверхностей стальной арматуры |
ОЗЛ-22 | Э-02Х21Н10Г2 | 3,0;4,0 | Сварка оборудования из сталей типа 04Х18Н10, 03Х18Н12, 03Х18Н11, работающего в окислительных средах, подобных азотной кислоте | |
ОЗЛ-8 | Э-07Х20Н9 | 2,0;2,5;3,0; 4,0;5,0 | Сварка сталей типа 08Х18Н10, 12Х18Н9, 08Х18Н10Т, когда к металлу шва не предъявляют жесткие требования стойкости к межкристаллитной коррозии (далее -МКК) | |
ОЗЛ-8С | 08Х20Н9КМВ | 2,5;3,0;4,0 | Сварка сталей типа 08Х18Н10, 12Х18Н9, 08Х18Н10Т, когда к металлу шва не предъявляют жесткие требования стойкости к МКК | Сварка с повышенной производительностью |
ОЗЛ-14 | Э-07Х20Н9 | 3,0;4,0 | Сварка сталей типа 08Х18Н10, 12Х18Н9, 08Х18Н10Т, когда к металлу шва не предъявляют жесткие требования стойкости к МКК | Возможна сварка переменным током |
ОЗЛ-14А | Э-04Х20Н9 | 3,0;4,0;5,0 | Сварка сталей типа 08Х18Н10, 08Х18Н10Т, 06Х18Н11, 08Х18Н12Т, когда к металлу шва предъявляют требования стойкости к МКК | |
ОЗЛ-36 | Э-04Х20Н9 | 3,0;4,0 5,0 | Сварка сталей типа 08Х18Н10, 06Х18Н11, 08Х18Н12Т, 08Х18Н10Т, когда к металлу шва предъявляют требования стойкости к МКК | |
ЦЛ-11 | Э-08Х20Н9Г2Б | 2,0;2,5;3,0; 4,0;5,0 | Сварка сталей типа 12Х18Н10Т, 12Х18Н9Т, 08Х18Н12Т, 08Х18Н12Б, когда к металлу шва предъявляют жесткие требования стойкости к МКК | Сварка оборудования из сталей типа 12Х18Н10Т, 12Х18Н9Т, 08Х18Н12Т, 08Х18Н12Б для пищевой промышленности |
ЦЛ-11СЧ | Э-08Х20Н9Г2Б | 2,5;3,0;4,0 | Сварка сталей типа 08Х18Н10, 08Х18Н12Б и 08Х18Н10Т, когда к металлу шва предъявляют требования стойкости к МКК | |
ОЗЛ-7 | Э-08Х20Н9Г2Б | 2,0;2,5;3,0; 4,0;5,0 | Сварка сталей типа 08Х18Н10, 08Х18Н12Б, 08Х18Н10Т, когда к металлу шва предъявляют жесткие требования стойкости к МКК | Сварка оборудования из сталей типа 08Х18Н10, 08Х18Н12Б, 08Х18Н10Т для пищевой промышленности |
ЦТ-15 | Э-08Х19Н10Г2Б | 2,0; 2,5; 3,0; 4,0; 5,0 | См. группу Электроды для сварки жаростойких и жаропрочных сталей и сплавов | Сварка сталей типа 12Х18Н9Т, 12Х18Н12Т, Х20Н12Т-Л, Х16Н13Б, когда к металлу шва предъявляют жесткие требования стойкости к МКК |
ЦЛ-9 | Э-10Х25Н13Г2Б | 3,0;4,0;5,0 | Сварка двухслойных сталей со стороны легированного слоя из сталей типа 12Х18Н10Т, 12Х18Н9Т, 08Х13, когда к металлу шва предъявляют требования стойкости к МКК | |
ОЗЛ-40 | 08Х22Н7Г2Б | 3,0;4,0 | Сварка сталей марок 08Х22Н6Т, 12Х21Н5Т | |
ОЗЛ-41 | 08Х22Н7Г2М2Б | 3,0;4,0 | Сварка стали марки 08Х21Н6М2Т | Возможна сварка стали марки 03Х24Н6АМ3 |
ОЗЛ-20 | Э-02Х20Н14Г2М2 | 3,0;4,0 | Сварка оборудования из сталей типа 03Х16Н15М3, 03Х17Н14М2, работащего в средах высокой агрессивности | Возможна сварка оборудования из стали 08Х17Н15М3Т, работающего в средах высокой агрессивности |
ЭА-400/10У | 08Х18Н11М3Г2Ф | 2,0;2,5;3,0; 4,0;5,0 | Сварка оборудования из сталей типа 08Х18Н10Т, 10Х17Н13М2Т, работающего в агрессивных средах при температуре до 350°С, когда к металлу шва предъявляют требования стойкости к МКК | |
ЭА-400/10Т | ||||
ЭА-400/10СЭ | ||||
НЖ-13 | Э-09Х19Н10Г2М2Б | 3,0;4,0;5,0 | Сварка оборудования из сталей типа 10Х17Н13М3Т, 08Х21Н6М2Т, 10Х17Н13М2Т, работающего при температуре до 350°С, когда к металлу шва предъявляют требования к стойкости к МКК | |
НЖ-13С | Э-09Х19Н10Г2М2Б | 2,5;3,0;4,0;5,0 | Сварка оборудования из сталей типа 10Х17Н13М2Т, 10Х17Н13М3Т и 08Х21Н6М2Т, работающего при температуре до 350°С, когда к металлу шва предъявляют требования стойкости к МКК | Высокая производительность сварки |
НИАТ-1 | Э-08Х17Н8М2 | 2,0;2,5;3,0; 4,0;5,0 | Сварка сталей типа 08Х18Н10, 12Х18Н10Т и 10Х17Н13М2Т, когда к металлу шва предъявляют требования стойкости к МКК | |
ОЗЛ-3 | 14Х17Н13С4Г | 3,0;4,0;5,0 | Сварка оборудования из стали 15Х18Н12С4ТЮ, работающего в средах повышенной агрессивности, когда к металлу шва не предъявляют требования стойкости к МКК | |
ОЗЛ-24 | 02Х17Н14С5 | 3,0;4,0 | Сварка оборудования из сталей типа 02Х8Н20С6, работающего в условиях производства 98%-ной азотной кислоты | |
ОЗЛ-17У | 03Х23Н27М3Д3Г2Б | 3,0;4,0 | Сварка оборудования из сплавов марок 06ХН28МДТ, 03ХН28МДТ и стали 03Х21Н21М4ГБ преимущественно толщиной до 12 мм, работающего в средах серной и фосфорной кислот с примесями фтористых соединений | |
ОЗЛ-37-2 | 03Х24Н26М3Д3Г2Б | 3,0;4,0 | Сварка оборудования из сплавов марок 03Х23Н25М3Д3Б, 06ХН28МДТ, 03ХН28МДТ и стали 03Х21Н21М4ГБ преимущественно толщиной до 12 мм, работающего в средах серной и фосфорной кислот с примесями фтористых соединений | |
ОЗЛ-21 | Э-02Х20Н60М15В3 | 3,0 | Сварка оборудования из сплавов типа ХН65МВ, ХН60МБ, работающего в высокоагрессивных средах, когда к металлу шва предъявляют требования стойкости к МКК | |
ОЗЛ-25Б | Э-10Х20Н70Г2М2Б2В | 3,0;4,0 | См. группу Электроды для сварки жаростойких и жаропрочных сталей и сплавов | Сварка коррозионно-стойких конструкций и оборудования из сплава ХН78Т |
Copyright. При любом цитировании материалов Cайта, включая сообщения из форумов, прямая активная ссылка на портал weldzone.info обязательна.
weldzone.info
Электроды для сварки нержавейки: виды, правила выбора для стали, рекомендации
Во время выполнения сварки очень важно обеспечить качественное соединение. Причем помимо профессионализма сварщика, на это оказывает влияние то, каков сварочный аппарат для работ, а также качество электродов. И потому важно очень тщательно выбирать этот расходный материал.
Следует упомянуть и о том, что для сварки определенного металла должен применяться электрод соответствующей марки. Особую группу образуют электроды, предназначенные для сварки нержавеющей стали, которые отличаются определенными характеристиками.
Особенности сварки высоколегированной стали
Используя электроды для сварки высоколегированных сталей, очень важно получить прочный шов, который должен соотноситься по своим характеристикам со свариваемым материалом. Для соединения нержавеющей стали необходимо выбирать такой расходный материал, с помощью которого можно создать шов, который не только будет иметь красивый вид, аккуратное исполнение, но и будет способен противостоять разрыву и внешним факторам.
Последняя стадия производства электродов для нержавейки в обязательном порядке предусматривает проведение серьезных испытаний, чтобы убедиться, что они обладают необходимым химическим составом.
Проблему придания электродам исключительных характеристик, способных обеспечить эффективность их работы, решают путем использования для них в качестве материала хромоникелевых сплавов, особенностью которых является наличие способности эффективно противостоять коррозии уже в момент создания первого слоя шва. Сварка нержавеющей стали должна проводиться с применением специального оборудования, которое обеспечит хорошо направленный ток, или же аппарата, имеющего встроенный осциллятор.
Виды электродов
Попытаемся выяснить, какие электроды можно применять для сваривания нержавеющих сталей. Чаще всего среди подобных электродов, при помощи которых соединяют изделия из нержавеющей стали, используют такие разновидности этого расходного материала, как:
Чтобы оценить все их возможности и принять правильное решение, будет полезно вначале познакомиться с их характеристиками.
ЦЛ-11
Основное назначение подобных электродов заключается в соединении хромоникелевых сталей, которые эффективно противостоят коррозии. Эти электроды предлагаются следующих марок 08Х18Н12Б, 08Х18Н12Т, 12Х18Н9Т, 12Х18Н10Т. Иными словами, ЦЛ-11 лучше всего применять тогда, когда требуется создать сварной шов, который должен удовлетворять более строгим требованиям в плане стойкости к воздействию межкристаллической коррозии. Создавать соединение при помощи подобного расходного материала можно вне зависимости от положения. Исключением лишь является вертикальное, при котором используется постоянный ток.
Электроды ЦЛ-11 рассчитаны на соединение нержавеющей стали в условиях температуры, не превышающей 450 градусов Цельсия. Важной особенностью является наличие специального покрытия, содержащего карбонаты и фтористые соединения. Среди достоинств, которыми обладают подобные электроды, следует выделить устойчивость к межкристаллической коррозии, пластичность и высокую ударную вязкость создаваемых с их помощью слов. Также этот расходный материал позволяет избежать возникновения горячих трещин, сводит к минимуму возникновение брызг металла, а также позволяет сделать аккуратный и ровный шов.
ОЗЛ-6
Применяемые для сварки нержавеющих сталей электроды подобного типа рассчитаны на сварку в условиях высоких температур с применением литейного оборудования в окислительной среде. Сами работы можно выполнять вне зависимости от положения шва за исключением вертикального. При работе с этими электродами удается создать шов, способный перенести температуру до 1000 градусов Цельсия.
Этот расходный материал может применяться для ручной дуговой сварки жаростойких нержавеющих сталей, соединение которых выполняется посредством постоянного тока. Применяемое для них покрытие характеризуется наличием карбонатов и фтористых соединений. Если говорить о положительных качествах подобного расходного материала, то следует выделить повышенную жаростойкость металла шва, невосприимчивость к межкристаллической коррозии, высокие характеристики пластичности и ударной вязкости шва, низкий уровень разбрызгивания металла и аккуратное исполнение шва.
НЖ-13
Электроды этого типа предназначены для соединения изделий из пищевой нержавеющей стали при помощи ручной дуговой сварки, предусматривающей использование постоянного тока. В то же время они подходят и для сваривания современных нержавеющих сталей, в составе которых представлены хромоникелевомолибденовые или хромоникелевые сплавы.
Важность правильного выбора
Чтобы при работе с нержавейкой создаваемое соединение получилось достаточно качественным, следует еще до проведения работ выполнить расчеты компонентов, которые потребуется использовать для этого. Также необходимо определиться с подходящим сварочным оборудованием. Желательно иметь в наличии и специальную сварочную головку, при помощи которой можно соединять тонкостенные трубы из нержавейки. Так можно добиться высокой защиты при использовании кольцевой камеры.
Выбирая электрод, следует помнить о том, что он должен использоваться лишь для выполнения конкретных задач. Иными словами, не стоит соединять между собой изделия из цветного металла электродом, который изначально создавался для сваривания нержавеющей стали. Решив воспользоваться неподходящим типом электродов, вы не можете быть уверены в том, что созданный таким образом шов надолго останется прочным. Для принятия верного решения в отношении подходящего электрода для нержавеющих сталей рекомендуется вначале изучить прайс-лист предприятия-изготовителя или же ознакомиться с обучающим видео.
В то же время необходимо иметь в виду, что в продаже можно встретить электроды, у которых может присутствовать покрытие или же не быть его. Этот расходный материал может отличаться и по другим признакам: типу на плавящиеся и неплавящиеся, рабочему току, который может быть постоянным или переменным. По этой причине принимать решение в пользу того или иного электрода следует с учетом всех особенностей запланированных работ.
Технологические особенности
Сваривая изделия из нержавейки, следует помнить о том, что создаваемое соединение отличается хрупкостью и низкой устойчивостью к коррозии. Когда металл подвергается нагреву в температурном диапазоне 500-800 градусов, наблюдается выпад карбидов хрома, что приводит к разрушению заготовки во время ее использования.
Чтобы сталь смогла противостоять разрушающим процессам, необходимо провести мероприятия по уменьшению эффекта выпадения карбидов. Это позволит стабилизировать свойства металла на участке шва.
Принято выделять несколько методов соединения изделий из нержавейки:
Использовать ручную сварку эффективно при условии, что свариваемый лист нержавейки имеет толщину 1,5 мм. Для более тонких заготовок следует применять ручную дуговую сварку, осуществляемую с помощью вольфрамовых электродов. Также здесь уместной будет и импульсная дуговая сварка, для которой в качестве расходного материала применяются плавящиеся электроды. Чтобы выполнить ручную дуговую сварку, можно применять такое сварочное оборудование, как инвертор. Есть сети немало видео, где рассказывается об особенностях выполнения сварки с помощью инверторного аппарата.
Задуматься об использовании плазменного метода можно вне зависимости от толщины, которую имеет нержавеющая сталь. В то же время часто применяют и плазменный метод дуговой сварки под флюсом, который получил наибольшее распространение в строительстве и промышленности. Когда изделия будут сварены, в обязательном порядке необходимо выполнить обработку металла, а помимо этого, усилить важные сварочные швы. Когда на нержавейке создается соединение, шов покрывается тонким слоем хрома, который не следует оставлять. Убрав его, можно повысить характеристики прочности соединения и решить проблему коррозии. Удалить подобный слой можно с помощью следующих методов:
Несколько рекомендаций
Если вы планируете сваривать нержавеющую сталь, то вам будут полезны следующие рекомендации:
Заключение
Сварка нержавеющих сталей отличается от соединения других металлов своими особенностями. Причем это касается не только использования определенного типа электродов, но и самого процесса выполнения сварки. Всем этим моментам необходимо уделить особое внимание, поскольку каждый из них может в итоге повлиять на качество создаваемого соединения. Главное, о чем следует помнить — нержавеющая сталь отличается достаточной хрупкостью, а поэтому необходимо стараться свести к минимуму длительность воздействия металлов теплом.
stanok.guru
www.samsvar.ru
Электроды для Сварки Стали 12х18н10т
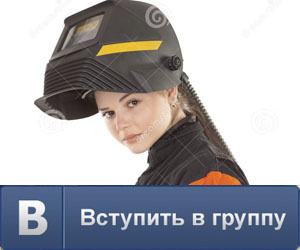
В наше время практически всем людям доступны почты все марки и виды электродов. Электроды делятся по разным классам по своим характеристикам, например их можно поделить на электроды для сварки высоколегированных и низколегированных сталей. Также электроды делятся на классы по материалу покрытия: основное, кислотное и обычное. Список классов, на которые делятся электроды очень большой, поэтому нет смысла его полностью перечислять. Одним из видов электродов являются электроды для сварки стали 12х18н10т, то есть они предназначены для сварки хромоникелевых сталей.
Этот вид стали используется в тех случаях, когда изделие должно быть максимально устойчивым от коррозии и не поддаваться другим факторам окружающей среды. Также к изделиям, которые сварены электродами для сварки стали 12х18н10т предъявляются повышенные требования устойчивости от межкристаллической коррозии.
Во всем мире очень ценятся изделия из нержавеющей стали, поэтому популярность электродов для сварки стали 12х18н10т продолжает расти с каждым днем. Однако многих людей эти электроды привлекают еще и своим прекрасным сочетанием цены и качества. Поистине, такое сочетание встречается крайне редко, поэтому это как раз и является одним из самых главных преимуществ именно этих электродов.
А теперь давайте поговорим о самом процессе сваривания электродами для сварки хромоникелевых сталей. Сварка этими электродами производится во всех пространственных положениях при использовании постоянного тока обратной полярности. Также этим электродам сродни еще и такие качества, например стабильное горение дуги, низкое разбрызгивание металла, отличное формирование шва и легкая отделяемость шлака от поверхности изделия.
Непосредственно перед самим началом сваривания Вам необходимо прокалить электроды для сварки стали 12х18н10т в специальной печи для прокалки электродов при температуре от 300 до 350 градусов по Цельсию в течение одного часа. После полного остывания электроды готовы к использованию. Швы, сваренные этими электродами, могут поддаваться воздействию температуры до 350 градусов. Сварка электродами для сварки хромированной стали может, производится, как и ручная, так и дуговая в инертном газе.
Также для сварки этими электродами применяются еще и такие виды сварки, как плазменная сварка, импульсно-дуговая сварка, точечная и роликовая сварка, сварка в среде активных газов, сварка под флюсом, а также возможна и сварка сопротивления. Во время сваривания образуется пористый оксидный слой, который содержит в своем составе хром. Это приводит к снижению к устойчивости от коррозии, поэтому если Вам необходима высокая устойчивость к коррозии, то Вам нужно поддать материал последующей обработке для того чтобы изделие осталось таким же еще через несколько десятков лет.
Вот уже долгое время многие хозяиновитые люди продолжают сваривать для своего дома изделия из хромированной стали. Они без проблем заказывают их через пункт меню «Контакты» и остаются довольными.
elektrod-3g.ru
12Х18Н10Т сварка стали
Особенности сварки нержавейки 12Х18Н10Т
Сварка нержавейки
12Х18Н10Т. Особенности сварки нержавейки.
Сварка стали – основной технологический процесс практически любого производства изделий из металла. С VII века до нашей эры и до наших дней сварка широко применяется как основной способ образования неразъемных соединений металлов. С самого зарождения и вплоть до XIX века н.э. в применялся метод кузнечной сварки металлов. Т.е. свариваемые детали нагревались и затем спрессовывались ударами молота. Эта технология достигла своего пика к середине XIX века, когда по ней стали изготавливать даже такие ответственные изделия как железнодорожные рельсы и магистральные трубопроводы.
Однако сварные соединения, особенно в массовом, промышленном масштабе отличались невысокой надежностью и нестабильным качеством. Это зачастую приводило к авариям из-за разрушения детали в месте шва.
Открытие электродугового нагрева и высокотемпературного газо-кислородного горения наряду с возросшими требованиями к качеству сварного соединения совершили мощный технологический прорыв в области сварки, в результате чего создалась технология бескузнечной сварки - такой, какую мы привыкли наблюдать сегодня.
С появлением легированной стали процессы сварки усложнились в связи с необходимостью предотвращения карбидации легирующих элементов, в основном – хрома. Появились методы сварки в инертных средах или под флюсом, а также технологии долегирования сварного шва.
Рассмотрим особенности сварки аустенитных сталей на примете наиболее распространенной нержавеющей стали 12Х18Н10Т.
Сталь 12Х18Н10Т относиться к хорошо свариваемым. Характерной особенностью сварки этой стали является возникновение межкристаллитной коррозии. Она развивается в зоне термического влияния при температуре 500-800?С. При пребывании металла в таком критическом интервале температур по границам зерен аустенита выпадают карбиды хрома. Все это может иметь опасные последствия - хрупкие разрушения конструкции в процессе эксплуатации.
Чтобы добиться стойкости стали нужно исключить или ослабить эффект выпадения карбидов и стабилизировать свойства стали в месте сварного шва.
При сварке высоколегированных сталей используют электроды с защитно-легирующим покрытием основного вида в сочетании с высоколегированным электродным стержнем. Применение электродов с покрытием основного вида позволяет обеспечить формирование наплавленного металла необходимого химического состава, а также других свойств путём использования высоколегированной электродной проволоки и долегирования через покрытие.
Сочетание легирования через электродную проволоку и покрытие позволяет обеспечить не только гарантированный химический состав в пределах паспортных данных, но и некоторые другие свойства, предназначенные для сварки аустенитных сталей 12Х18Н10Т, 12Х18Н9Т, 12Х18Н12Т и им подобных.
Содержащийся в электродных стержнях титан при сварке практически полностью окисляется. По этой причине при сварке покрытыми электродами в качестве элемента-стабилизатора используют ниобий. Коэффициент перехода ниобия из стержня при сварке покрытыми электродами составляет 60-65%.
Сварку высоколегированных сталей под флюсом осуществляют с применением или нейтральных по кислороду фторидных флюсов, или защитно-легирующих в сочетании с высоколегированной электродной проволокой. С металлургической точки зрения для сварки высоколегированных сталей наиболее рациональны фторидные флюсы типа АНФ-5, которые обеспечивают хорошую защиту и металлургическую обработку металла сварочной ванны и позволяет легировать сварочную ванну титаном через электродную проволоку. При этом процесс сварки малочувствителен к образованию пор в металле шва из-за водорода. Однако фторидные бескислородные флюсы имеют относительно низкие технологические свойства. Именно низкие технологические свойства фторидных флюсов служат причиной широкого использования для сварки высоколегированных сталей флюсов на основе оксидов.
Сварку высоколегированных сталей для снижения вероятности формирования структуры перегрева, как правило, выполняют на режимах, характеризующихся малой величиной погонной энергии. При этом предпочтение отдают швам малого сечения, получаемым при использовании электродной проволоки небольшого диаметра (2-3мм). Поскольку высоколегированные стали обладают повышенным электросопротивлением и пониженной электропроводностью, то при сварке вылет электрода из высоколегированной стали уменьшают в 1,5-2 раза по сравнению с вылетом электрода из углеродистой стали.
При дуговой сварке в качестве защитных газов используют аргон, гелий (реже), углекислый газ.
Аргонодуговую сварку выполняют плавящимися и неплавящимися вольфрамовыми электродами. Плавящимся электродом сваривают на постоянном токе обратной полярности, используя режимы, обеспечивающие струйный перенос электродного металла. В некоторых случаях (в основном при сварке аустенитных сталей) для повышения стабильности горения дуги и особенно снижения вероятности образования пор из-за водорода при сварке плавящимся электродом используют смеси аргона с кислородом или углекислым газом (до 10%).
Сварку неплавящимся вольфрамовым электродом в основном осуществляют на постоянном токе прямой полярности. В некоторых случаях при наличии в сталях значительного количества алюминия используют переменный ток для обеспечения катодного разрушения оксидной плёнки.
Применение дуговой сварки в атмосфере углекислого газа позволяет снизить вероятность образования пор в металле шва из-за водорода; при этом обеспечивается относительно высокий коэффициент перехода легкоокисляющихся элементов. Так, коэффициент перехода титана из проволоки достигает 50%. При сварке в атмосфере аргона коэффициент перехода титана из проволоки составляет 80-90%. При сварке в углекислом газе сталей, имеющих высокое содержание хрома и низкое содержание кремния, на поверхности шва образуется тугоплавкая трудноудаляемая оксидная плёнка. Её присутствие затрудняет проведение многослойной сварки.
При сварке сталей с малым содержанием углерода (ниже 0,07-0,08%) возможно науглероживание наплавленного металла. Переход углерода в сварочную ванну усиливается при наличии в электродной проволоке алюминия, титана, кремния. В случае сварки глубокоаустенитных сталей некоторое науглероживание металла сварочной ванны в сочетании с окислением кремния снижает вероятность образования горячих трещин. Однако науглероживание может изменить свойства металла шва и, в частности, снизить коррозийные свойства. Кроме того наблюдается повышенное разбрызгивание электродного металла. Наличие брызг на поверхности металла снижает коррозийную стойкость.
Технологии сварки нержавеющих высоколегированных сталей постоянно совершенствуются. На данном этапе при строгом соблюдении технологического процесса качество сварного шва нержавейки практически не уступает по своим свойствам металлу соединяемых деталей и гарантирует высочайшую надежность сварного соединения.
Посмотреть специальные предложения на продажу стали 12Х18Н10Т .
http://www.avers-steel.ru
legkoe-delo.ru
Технологическая свариваемость стали 12Х18Н10Т при КШС
Шовная сварка - весьма эффективный способ соединения тонколистовой стали расплавлением током сжатого участка между деталями и образованием ядра с перемешанным закристаллизовавшимся металлом. Формирование ядра в случае точечной сварки происходит при преимущественном тепловыделении в зоне контакта и интенсивном теплоотводе в электроды и холодные слои металла. Участки контакта вначале нагреваются током неравномерно, а затем ток перераспределяется между горячим и холодным металлом, температура нагрева выравнивается, и между деталями появляется расплавленное ядро. Рост кристаллитов ядра точки направлен в сторону участка наибольшего теплоотвода, который может быть усилен, например, за счет увеличения отношения контактной поверхности электрода к толщине детали.
Величина усилия сжатия электродов должна быть оптимальной. Если она недостаточна, то возможен выплеск или выдавливание расплава между свариваемыми деталями, а при охлаждении ядра возможно образование в нем усадочных раковин и трещин. Чрезмерное усилие при сжатии электродов приводит к образованию значительных вмятин на поверхности свариваемых деталей, что в дальнейшем может отрицательно сказаться на работоспособности конструкций.
Одна из основных трудностей при сварке данной стали - предупреждение образования в швах и околошовной зоне горячих трещин. Предупреждение образования этих дефектов достигается: а) Ограничением в основном и наплавленном металлах содержанием вредных (серы, фосфора) и легирующих (свинца, олово, висмута) примесей, а так же газов - кислорода и водорода. Для этого следует использовать стали и сварочные материалы с минимальным содержанием названных примесей. б) Получением такого химического состава металла шва, который обеспечил бы в нем двухфазную структуру. Поэтому в швах стремятся получить аустенитную структуру с мелкодисперсными карбидами и интерметаллидами. Азот - сильный аустенизатор, способствует измельчению структуры за счет увеличения центров кристаллизации в виде тугоплавких нитридов. Поэтому азотизация металла шва способствует повышению их стойкостью против горячих трещин. Высокоосновные флюсы и шлаки, рафинируя металл шва и иногда модифицируя его структуру, повышают стойкость против горячих трещин. Механизированные способы сварки, обеспечивая равномерное проплавление основного металла по длине шва и постоянство термического цикла сварки, позволяют получить более стабильные структуры на всей длине сварного соединения; в) Уменьшением силового фактора, возникающего в результате термического цикла сварки, усадочных деформаций. Снижение его действия достигается ограничением силы сварочного тока. Требуемые свойства во многом достигается термообработкой (аустенизацией) при температуре 1050-1110о С, снимающие остаточные сварочные напряжения, с последующим стабилизирующим отпуском при температуре 750-800о С. Предупреждение образования в швах и околошовной зоне горячих трещин позволяет производить ТКС без образования выплесков. А поскольку выплески являются одними из основных дефектов при ТКС, то для оценки свариваемого сплава к их образованию вводят коэффициент кв. Он представляет собой отношение максимального диаметра ядра dкр, который удаётся получить без выплеска за счёт увеличения только сварочного тока, и минимально допустимого диаметра ядра dmin. Наиболее целесообразно применение электродов сферической формы с радиусом округления 50-150 мм. В этом случае большая часть сварочного тока протекает через центральные участки контакта, способствуя созданию благоприятных условий нагрева при образовании ядра точки и возникновению минимальной, не защищенной от вредного контакта с газами воздуха, зоны разогрева. Обязательное интенсивное внутреннее охлаждение электродов способствует равномерному росту кристаллитов в ядре точки. При точечной сварке данной стали высокие показатели механических свойств сварного соединения могут быть получены в относительно широком интервале изменения параметров режима даже без защиты зоны разогрева инертными газами. При этом необходимо стремиться к выполнению сварки в минимальные промежутки времени. В связи с такими свойствами стали 12Х18Н10Т, при ТКС не потребуется использовать дополнительные усилия (проковка) и циклограмма процесса сварки должна быть такой, какая показана на рис.3.1.
Рис 3.1 Циклограмма усилия сжатия.
Режим сварки определяется частными значениями ряда регулируемых параметров - величиной сварочного тока, длительностью его протекания (τсв), сварочным усилием (Fсв) и усилием проковки (Fков). Этот режим должен обеспечить наиболее благоприятную программу нагрева и деформации металла при сварке с целью получения заданных эксплуатационных характеристик соединений. Во многих случаях качество соединений определяется диаметром ядра и плотностью литого металла. Минимально допускаемый диаметр ядра зависит от толщины свариваемых деталей. Сила тока зависит от толщины деталей (размеров шва) и длительности импульса.
Низкое сопротивление пластической деформации делает процесс сварки малочувствительным к образованию конечных выплесков - одному из наиболее распространенных дефектов соединений. Пластичный металл хорошо уплотняет зазор и препятствует выбросу жидкого металла из ядра сварной точки. Склонность процесса к выплескам можно оценить величиной критического диаметра ядра (dя. кр.),т.е. наибольшим диаметром точки, который можно получить при данных условиях сварки (усилие и продолжительность импульса).
4. Выбор и расчёт основных параметров режима сварки []
Параметрами режима контактной шовной сварки являются:
диаметр рабочей поверхности электрода dр;Sр;fр, мм;
время сварки:
время импульса tсв, с;
время паузы tn, с.
усилие на электродах Fсв, кН;
шаг точек tш, мм;
скорость шовной сварки Vсв, м/с;
сварочный ток Iсв, А.
Шовная сварка может рассматриваться как точечная для случая очень близкого расположения сварных точек, т. е. при значительном шунтировании сварочного тока.
Диаметр рабочей поверхности электрода.
Из справочной литературы принимаем данное равным = 5 мм.
Время сварки.
Время (длительность) импульса сварочного тока tСВ (с):
для алюминиевых сплавов
где – толщина более тонкого листа, м.
Рекомендуемый размер роликов для толщины = 0,5 мм
Sp=8 мм; fр=4 мм; Rp=25-50 мм.
Время (длительность) паузы между импульсами сварочного тока
определяют из следующих соотношений между временем импульса tсв и продолжительностью одного сварочного цикла tц = tсв + tп :
для нержавеющих, жаропрочных сталей и титана
В расчете принимаем среднее значение:
Из формулы получаем:
Сварочное усилие Fсв (Н) между роликами:
Для нержавеющих, жаропрочных сталей и титана Fсв определяют
по формуле
В расчете принимаем среднее значение:
При некачественной сборке и жёсткой конструкции сварного узла Fсвувеличивают на 10 %.
Шаг точек , (мм) при шовной сварке устанавливается в
зависимости от толщины свариваемых деталей, а также требований герметичности (перекрытие литых зон составляет 20–50 %). Шаг точек
tШ (мм) ориентировочно определяется для герметичных швов по следующим зависимостям:
для нержавеющих и жаропрочных сталей
В расчете принимаем среднее значение:
где – толщина более тонкой детали, мм.
Скорость шовной сварки Vсв, (мм/с) определяют по формуле
Сила сварочного тока Iсв (A), необходимая для образования
соединения, может быть определена по закону Джоуля–Ленца [3]
где – время сварки, с; – конечное значение сопротивления деталей, Ом; m – коэффициент, учитывающий изменение сопротивления деталей в процессе сварки (для низкоуглеродистых сталей m=1; для коррозионностойких сталей – 1,2; алюминиевых и магниевых сплавов –
1,5; сплавов титана – 1,4).
cyberpedia.su
Сварка сталь 20 и 12Х18Н10Т
Сварка сталь 20 и 12Х18Н10Т Добрый день! По чертежу необходимо сварить сталь 20 и 12Х18Н10Т. Варятся два изделия наружным диаметром 16мм, внутренний диаметр 11мм, толщина стенки выходит 2,5мм. Условное давление 16МПа. Подскажите, насколько прочным будет это соединение? Какие сложности возникнут при сварке столь неоднородных металлов? Сварка сталь 20 и 12Х18Н10Т Купил для сварки разнородных сталей OK Tigrod 309L и OK Tigrod 309LSi Если подробнее то здесь http://www.esab.com/...ilar-metals.pdf Сварка сталь 20 и 12Х18Н10Т Да так, по мелочи: - высокая вероятность межкристаллитной коррозии в переходной зоне сварного шва - риск образования горячих трещин в процессе сварки - риск растрескивания/коробления готового изделия при нагреве свыше 300С из за большой разницы коэффициента теплового расширения Оценить прочность соединения очень сложно т.к. тут всё будет зависеть от огромного числа факторов, но однозначно можно сказать, что оно будет хрупким и малоустойчивым к вибрационным и динамическим нагрузкам. Применять желательно электроды 06Х18Н10Т(более пластичен соответственно меньше вероятность горячих трещин) и минимизировать размеры сварочной ванны. Сварка сталь 20 и 12Х18Н10Т Откройте ссылку, которую дал Krivtsov1175, и сделайте так, как там пишут. Следите за тем, чтобы в шов попало как можно больше присадочного и как можно меньше основного (чёрного) материала. С какого перепугу должна получиться межкристаллитная коррозия и горячие трещины - убей Бог, не пойму. Если в шов попадёт много чёрной стали, получится мартенсит. Если соблюдать правила, про которые пишет ESAB, всё будет нормально. Температурное расширение отличается примерно на 6 микрон на кельвин на метр. На диаметре 16 мм сильно заметно не будет, даже при 300 градусах.Сообщение отредактировал Fuchs: 29 May 2014 - 16:00
Сварка сталь 20 и 12Х18Н10ТFuchs (29 May 2014 - 15:58) писал:
С какого перепугу должна получиться межкристаллитная коррозия и горячие трещины - убей Бог, не пойму.
Межкристаллитная коррозия нормальное явление для нетермобработанного на аустенит 12Х18Н10Т(видел много раз), а тут дело усугубляется неизбежным соседством зон избытка хрома с зонами недостатка т.к. времени нагрева при сварке крайне недостаточно для диффузионного выравнивания фаз. Трещины в данном соединении могу образоваться вследствие пресыщения дислокациями за счёт неравновесной кристаллизации металла сварочной ванны. Именно для минимизации риска образования горячих трещин и желательно использовать присадку с пониженным содержанием углерода дабы перлитное расширение снизило уровень напряжений в сварочном шве.Fuchs (29 May 2014 - 15:58) писал:
Температурное расширение отличается примерно на 6 микрон на кельвин на метр. На диаметре 16 мм сильно заметно не будет, даже при 300 градусах.
Тут вероятнее всего Вы правы, разница в 5 микрон на метр при 300С не столь критична.В остальном всё верно, соблюдая правила по ссылке которую дал Krivtsov1175 всё получится без особых проблем.
Сварка сталь 20 и 12Х18Н10ТYkpoII (30 May 2014 - 06:00) писал:
Межкристаллитная коррозия нормальное явление
не для этой стали. Она специально стабилизирована титаном и очень хорошо противостоит межкристаллитной коррозии. Горячие трещины могут образоваться при сварке стопроцентного аустенита, чего в данном случае не наблюдаем, или ежли в чёрной стали повышенное содержание серы, чего тоже нет. А если б даже и было в чернухе много серы, она хорошо растворяется в дельта-феррите, коего в 12Х18Н10Т от 5 до 10 процентов, и не образует с никелем легкоплавкой эфтектики. Единственная проблема, могущаяя возникнуть при сварке этих сталей - образование мартенсита по линии сплавления между черной (ферритной) сталью и нержавеющщим (аустенитным) швом. И чтобы этого избежать, надо внимательно изучить диаграмму Шеффлера, чтобы правильно выбрать присадку и максимально допустимое смешение. Сварка сталь 20 и 12Х18Н10Т Здравствуйте. А что насчёт нюансов по сварке листовых 12Х18Н10Т и 20Х13 ?www.chipmaker.ru
12Х18Н10Т. Особенности сварки нержавейки
Сварка стали – основной технологический процесс практически любого производства изделий из металла. С VII века до нашей эры и до наших дней сварка широко применяется как основной способ образования неразъемных соединений металлов. С самого зарождения и вплоть до XIX века н.э. в применялся метод кузнечной сварки металлов. Т.е. свариваемые детали нагревались и затем спрессовывались ударами молота. Эта технология достигла своего пика к середине XIX века, когда по ней стали изготавливать даже такие ответственные изделия как железнодорожные рельсы и магистральные трубопроводы.
Однако сварные соединения, особенно в массовом, промышленном масштабе отличались невысокой надежностью и нестабильным качеством. Это зачастую приводило к авариям из-за разрушения детали в месте шва.
Открытие электродугового нагрева и высокотемпературного газо-кислородного горения наряду с возросшими требованиями к качеству свраного соединения совершили мощный
технологический прорыв в области сварки, в результате чего создалась технология бескузнечной сварки - такой, какую мы привыкли наблюдать сегодня.
С появлением легированной стали процессы сварки усложнились в связи с необходимостью предотвращения карбидации легирующих элементов, в основном – хрома. Появились методы сварки в инертных средах или под флюсом, а также технологии долегирования сварного шва.
Рассмотрим особенности сварки аустенитных сталей на примете наиболее распространенной нержавеющей стали 12Х18Н10Т.
Сталь 12Х18Н10Т относиться к хорошо свариваемым. Характерной особенностью сварки этой стали является возникновение межкристаллитной коррозии. Она развивается в зоне термического влияния при температуре 500-800?С. При пребывании металла в таком критическом интервале температур по границам зерен аустенита выпадают карбиды хрома. Все это может иметь опасные последствия - хрупкие разрушения конструкции в процессе эксплуатации.
Чтобы добиться стойкости стали нужно исключить или ослабить эффект выпадения карбидов и стабилизировать свойства стали в месте сварного шва.
При сварке высоколегированных сталей используют электроды с защитно-легирующим покрытием основного вида в сочетании с высоколегированным электродным стержнем. Применение электродов с покрытием основного вида позволяет обеспечить формирование наплавленного металла необходимого химического состава, а также других свойств путём использования высоколегированной электродной проволоки и долегирования через покрытие.
Сочетание легирования через электродную проволоку и покрытие позволяет обеспечить не только гарантированный химический состав в пределах паспортных данных, но и некоторые другие свойства, предназначенные для сварки аустенитных сталей 12Х18Н10Т, 12Х18Н9Т, 12Х18Н12Т и им подобных.
Содержащийся в электродных стержнях титан при сварке практически полностью окисляется. По этой причине при сварке покрытыми электродами в качестве элемента-стабилизатора используют ниобий. Коэффициент перехода ниобия из стержня при сварке покрытыми электродами составляет 60-65%.
Сварку высоколегированных сталей под флюсом осуществляют с применением или нейтральных по кислороду фторидных флюсов, или защитно-легирующих в сочетании с высоколегированной электродной проволокой. С металлургической точки зрения для сварки высоколегированных сталей наиболее рациональны фторидные флюсы типа АНФ-5, которые обеспечивают хорошую защиту и металлургическую обработку металла сварочной ванны и позволяет легировать сварочную ванну титаном через электродную проволоку. При этом процесс сварки малочувствителен к образованию пор в металле шва из-за водорода. Однако фторидные бескислородные флюсы имеют относительно низкие технологические свойства. Именно низкие технологические свойства фторидных флюсов служат причиной широкого использования для сварки высоколегированных сталей флюсов на основе оксидов.
Сварку высоколегированных сталей для снижения вероятности формирования структуры перегрева, как правило, выполняют на режимах, характеризующихся малой величиной погонной энергии. При этом предпочтение отдают швам малого сечения, получаемым при использовании электродной проволоки небольшого диаметра (2-3мм). Поскольку высоколегированные стали обладают повышенным электросопротивлением и пониженной электропроводностью, то при сварке вылет электрода из высоколегированной стали уменьшают в 1,5-2 раза по сравнению с вылетом электрода из углеродистой стали.
При дуговой сварке в качестве защитных газов используют аргон, гелий (реже), углекислый газ.
Аргонодуговую сварку выполняют плавящимися и неплавящимися вольфрамовыми электродами. Плавящимся электродом сваривают на постоянном токе обратной полярности, используя режимы, обеспечивающие струйный перенос электродного металла. В некоторых случаях (в основном при сварке аустенитных сталей) для повышения стабильности горения дуги и особенно снижения вероятности образования пор из-за водорода при сварке плавящимся электродом используют смеси аргона с кислородом или углекислым газом (до 10%).
Сварку неплавящимся вольфрамовым электродом в основном осуществляют на постоянном токе прямой полярности. В некоторых случаях при наличии в сталях значительного количества алюминия используют переменный ток для обеспечения катодного разрушения оксидной плёнки.
Применение дуговой сварки в атмосфере углекислого газа позволяет снизить вероятность образования пор в металле шва из-за водорода; при этом обеспечивается относительно высокий коэффициент перехода легкоокисляющихся элементов. Так, коэффициент перехода титана из проволоки достигает 50%. При сварке в атмосфере аргона коэффициент перехода титана из проволоки составляет 80-90%. При сварке в углекислом газе сталей, имеющих высокое содержание хрома и низкое содержание кремния, на поверхности шва образуется тугоплавкая трудноудаляемая оксидная плёнка. Её присутствие затрудняет проведение многослойной сварки.
При сварке сталей с малым содержанием углерода (ниже 0,07-0,08%) возможно науглероживание наплавленного металла. Переход углерода в сварочную ванну усиливается при наличии в электродной проволоке алюминия, титана, кремния. В случае сварки глубокоаустенитных сталей некоторое науглероживание металла сварочной ванны в сочетании с окислением кремния снижает вероятность образования горячих трещин. Однако науглероживание может изменить свойства металла шва и, в частности, снизить коррозийные свойства. Кроме того наблюдается повышенное разбрызгивание электродного металла. Наличие брызг на поверхности металла снижает коррозийную стойкость.
Технологии сварки нержавеющих высоколегированных сталей постоянно совершенствуются. На данном этапе при строгом соблюдении технологического процесса качество сварного шва нержавейки практически не уступает по своим свойствам металлу соединяемых деталей и гарантирует высочайшую надежность сварного соединения.
www.metallurg-company.ru
www.samsvar.ru
Сварка 12х18н10т
Сварка - очень важный процесс в любом производстве, где имеют дело с металлом. Сварка известна достаточно давно, ещё с 7-го века до нашей эры. Тогда применялась кузнечная сварка, когда нагретые детали спрессовывались под ударами молота. Но со временем технология сварки, всё более или более совершенствовалась.
Но сварные соединения зачастую не блистали своим качеством и были не вполне надёжны. Что, в свою очередь, приводило в разрывам в местах швов.
Прорыв в сварке произошёл с открытием высокотемпературного газо-кислородного горения и электродугового горения. В результате создалась техногия сварки такая, какую мы привыкли видеть сегодня. А с тех пор как появились легированные стали процесс ещё больше усложнился.
Здесь мы рассмотрим особенности сварки нержавеющей стали 12Х18Н10Т.
Данный материал - хорошосвариваемый. Однако, при сварки (температура 500-800 градусов Цельсия) образуется межкристальная коррозия. При этом по границам зерен аустенита выпадают карбиды хрома. Это может иметь неприятные последствия - разрушение детали при эксплуатации.
Чтобы справится с этим явлением надо уменьшить эффект выпадения карбидов и стабилизировать свойства стали.
Для этого при сварке высоколегированных сталей применяют электроды с защитно-легирующим покрытием основного вида в сочетании с высоколегированным электродным стержнем. Это обеспечивает нужный химический состав и свойства. Что прекрасно подходит для для сварки аустенитных сталей 12Х18Н10Т, 12Х18Н9Т, 12Х18Н12Т и им подобных. Сварка 12х18н10т – это сложный и тонкий процесс. Для качественного применения и получения отличного результата необходимо учитывать ряд тонкостей.
Титан, который содержится в электродных стержнях - практически весь окисляется при сварке, поэтому в виде элемента-стабилизатора применяют ниобий. Коэффициент перехода ниобия составляет шестдесят - шестдесят пять процентов.
При сварке аустенитного проката надо учесть отличие его физических свойств: удельное электрическое сопротивление, коэффициент теплового расширения, точка плавления, теплопроводность. Особого внимания заслуживает сварка 12х18н10т, так как марку этой стали широко используют. Поэтому подход к применению нержавейки такого типа требует аккуратности и осторожности.
Сварку можно осуществлять следующими методами: ручная дуговая, дуговая сварка вольфрамовым электродом в инертной среде, дуговая сварка плавящим электродом в инертном газе, сварка в среде активных газов, импульсно-дуговая сварка, плазменная сварка, дуговая сварка под флюсом, сварка сопротивления, точечная и роликовая. Выбор подходящего вида сварки зависит от ширины вашего листа.
На поверхности сварного соединения образуется пористый оксидный слой, содержащий хром. Что приводит к снижению стойкости к коррозии. Если необходима высокая стойкость к коррозии, материал должен пойти последующую обработку.
Под термообработкой растворение внутри конструкции, при помощи которого сглаживаются различия присадочных материалов.
Для последующей обработки швов зачастую применяют травление. Именно травление помогает удалить вредный пористый оксидный слой. Травление выполняют путём погружения, поверхностного нанесения или покрытия пастой. С учетом всего вышесказанного, сварка 12х18н10т станет простым процессом и даст прекрасные результаты. Покупая листы из различных марок стали, помните, что даже такие жесткие и прочные материалы требуют бережного и осторожного обращения.
radiussteel.ru
Присадочная проволока для сварки нержавейки 12Х18Н10Т
Для сварки нержавейки, при помощи газовой или аргонодуговой сварки, используются проволока из нержавеющей стали. В зависимости от своего состава, она может иметь различные свойства, более пригодные для того или иного случая. Присадочная проволока для сварки нержавейки 12Х18Н10Т относится к сортовому прокату, обладающему круглым сечением диаметра. Ее производят из жаростойкой нержавейки с высоким уровнем легирования. Данное изделие должно соответствовать ГОСТ 18143-72.
Проволока для сварки нержавейки 12Х18Н10Т по ГОСТ 18143-72
Сфера использования сварочной проволоки достаточно широка, так как она встречается в строительстве, в энергетике, машиностроении, пищевой промышленности и на заводах по добыче и переработке газа и нефти. Ведь она имеет не только хорошую коррозийную стойкость, но и сопротивление к агрессивным средам. Здесь достаточно высокое содержание хрома. Он защищает от окисления поверхности. Для сварки применяется холодно тянутая проволока, которая обладает относительно небольшой стоимостью и при этом сохраняет свои полезные свойства. Она дает шов высокого качества, даже при работе с таким сложно свариваемым металлом. Некоторые трубы для водопроводов изготавливают из такого же сорта стали, так что при их ремонте сварочная проволока 12х18н10т оказывает лучшим вариантом.
Разновидности проволоки для нержавейки 12Х18Н10Т 
Данная марка выпускается в нескольких основных разновидностях. По точности производства выделяют изделия нормальной и высокой точности. Исходя из пластичных свойств, выделяют первый и второй класс. Согласно типу обработки может быть оксидированная и светлая сварочная проволока. По способу изготовления выделяют горячекатаную и холоднокатаную.
Разновидность проволоки для сварки нержавейки 12Х18Н10Т
Химический состав сварочной проволоки для нержавейки 12Х18Н10Т 
Свойства изделия определяются его составом. В данную марку входят следующие химические элементы:
Химических элемент | Содержание в составе, % |
Углерод | 0,11 |
Кремний | 0,8 |
Марганец | 2 |
Никель | 10 |
Хром | 18 |
Титан | 1 |
Железо | Основа |
Номенклатура 
Сварочная проволока для нержавейки 12Х18Н10Т обладает достаточно широкой номенклатурой и выпускается в следующих размерах диаметра:
Технические характеристики марки 
Проволока для сварки нержавейки 12Х18Н10Т может менять свои свойства, в зависимости от диаметра. Это незначительные отклонения, которые все же стоит учитывать при подборе материала для работы. Таблица характеристик выглядит следующим образом:
Марка проволоки | Диаметр присадочного материала, мм | Горячекатаная | Холоднокатаная | ||
Сопротивление разрыву временное, Н/мм2 | Удлинение относительное, % при длине образца 0,1 м. | ||||
1 класс | 2 класс | ||||
12Х18Н10Т | 0,2-1 | 590-880 | 25 | 20 | 1130-1470 |
1,1-3 | 540-830 | ||||
3,1-7,5 | 1080-1420 |
Особенности выбора 
Сваривание изделий из нержавеющей стали является очень сложным процессом, в котором может появиться много брака. Чтобы избежать этого, требуется очень точно подобрать состав материала. Сварочная проволока для сварки стали 12Х18Н10Т является специфическим продуктом, который способен подойти не для всех видов легированной стали. Ведь основным правилом подбора является идентичность состава. Наиболее удобным вариантом здесь будет сварка труб из нержавейки такого же сорта. Стоит отметить, что при подборе присадочного материала на производстве, где все компоненты еще можно менять, все делают для удобства, так как можно изменить состав основного металла, чтобы удобно его было соединять данной проволокой, а также практически не возникает проблем с подбором других сварочных материалов. В частной сфере ситуация выглядит несколько по-иному, так как там материалы применяются преимущественно для ремонта и требуется точный выбор. Изучив состав основного металла и присадочной проволоки, можно точно определиться с выбором.
Марка проволоки удобна тем, что у нее широкая номенклатура. Не возникает проблем с подбором требуемой толщины. Даже в тех моментах, где не допускается большой разброс и погрешность, когда речь идет о небольших размерах, то здесь шаг диаметра идет 0,1-0,2 мм. Все это позволяет без проблем с пережиганием основного металла получить качественное сварочное соединение. Естественно, что не у всех бывает возможность иметь весь ряд, поэтому, при выборе стоит ориентироваться, чтобы толщина основного металла совпадала с величиной диаметра проволоки.
«Важно!
При сваривании требуется использовать предварительный подогрев, а также постепенное остывание, когда сваренный шов прогревается горелкой»
Расшифровка 
Маркировка проволоки содержит сведения о тех элементах, которые задают основные свойства материалу и их содержание оказывается решающим. В данном случае ситуация обстоит так:
Особенности сварки
Чтобы соединение получилось максимально качественным, а при самом процессе возникало минимальное количество проблем, следует придерживаться точных режимов соединения:
Толщинапроволоки,мм | Тип | Сила тока,А |
Ручная сварка | ||
123 | Металл с отбортовкой | 35-6065-120100-140 |
123 | Положение металла встык | 40-7075-120120-160 |
Автоматическая сварка | ||
12,54 | Положение встык | 60-120110-200130-250 |
124 | Положение встык с присадкой | 80-140140-240200-280 |
Производители
Данная марка производится такими компаниями как:
svarkaipayka.ru
12Х18Н10Т. Особенности сварки нержавейки | ГК "АРС"
Сварка стали – основной технологический процесс практически любого производства изделий из металла. С VII века до нашей эры и до наших дней сварка широко применяется как основной способ образования неразъемных соединений металлов. С самого зарождения и вплоть до XIX века н.э. в применялся метод кузнечной сварки металлов. Т.е. свариваемые детали нагревались и затем спрессовывались ударами молота. Эта технология достигла своего пика к середине XIX века, когда по ней стали изготавливать даже такие ответственные изделия как железнодорожные рельсы и магистральные трубопроводы.
Однако сварные соединения, особенно в массовом, промышленном масштабе отличались невысокой надежностью и нестабильным качеством. Это зачастую приводило к авариям из-за разрушения детали в месте шва.
Открытие электродугового нагрева и высокотемпературного газо-кислородного горения наряду с возросшими требованиями к качеству свраного соединения совершили мощный
технологический прорыв в области сварки, в результате чего создалась технология бескузнечной сварки - такой, какую мы привыкли наблюдать сегодня.
С появлением легированной стали процессы сварки усложнились в связи с необходимостью предотвращения карбидации легирующих элементов, в основном – хрома. Появились методы сварки в инертных средах или под флюсом, а также технологии долегирования сварного шва.
Рассмотрим особенности сварки аустенитных сталей на примете наиболее распространенной нержавеющей стали 12Х18Н10Т.
Сталь 12Х18Н10Т относиться к хорошо свариваемым. Характерной особенностью сварки этой стали является возникновение межкристаллитной коррозии. Она развивается в зоне термического влияния при температуре 500-800?С. При пребывании металла в таком критическом интервале температур по границам зерен аустенита выпадают карбиды хрома. Все это может иметь опасные последствия - хрупкие разрушения конструкции в процессе эксплуатации.
Чтобы добиться стойкости стали нужно исключить или ослабить эффект выпадения карбидов и стабилизировать свойства стали в месте сварного шва.
При сварке высоколегированных сталей используют электроды с защитно-легирующим покрытием основного вида в сочетании с высоколегированным электродным стержнем. Применение электродов с покрытием основного вида позволяет обеспечить формирование наплавленного металла необходимого химического состава, а также других свойств путём использования высоколегированной электродной проволоки и долегирования через покрытие.
Сочетание легирования через электродную проволоку и покрытие позволяет обеспечить не только гарантированный химический состав в пределах паспортных данных, но и некоторые другие свойства, предназначенные для сварки аустенитных сталей 12Х18Н10Т, 12Х18Н9Т, 12Х18Н12Т и им подобных.
Содержащийся в электродных стержнях титан при сварке практически полностью окисляется. По этой причине при сварке покрытыми электродами в качестве элемента-стабилизатора используют ниобий. Коэффициент перехода ниобия из стержня при сварке покрытыми электродами составляет 60-65%.
Сварку высоколегированных сталей под флюсом осуществляют с применением или нейтральных по кислороду фторидных флюсов, или защитно-легирующих в сочетании с высоколегированной электродной проволокой. С металлургической точки зрения для сварки высоколегированных сталей наиболее рациональны фторидные флюсы типа АНФ-5, которые обеспечивают хорошую защиту и металлургическую обработку металла сварочной ванны и позволяет легировать сварочную ванну титаном через электродную проволоку. При этом процесс сварки малочувствителен к образованию пор в металле шва из-за водорода. Однако фторидные бескислородные флюсы имеют относительно низкие технологические свойства. Именно низкие технологические свойства фторидных флюсов служат причиной широкого использования для сварки высоколегированных сталей флюсов на основе оксидов.
Сварку высоколегированных сталей для снижения вероятности формирования структуры перегрева, как правило, выполняют на режимах, характеризующихся малой величиной погонной энергии. При этом предпочтение отдают швам малого сечения, получаемым при использовании электродной проволоки небольшого диаметра (2-3мм). Поскольку высоколегированные стали обладают повышенным электросопротивлением и пониженной электропроводностью, то при сварке вылет электрода из высоколегированной стали уменьшают в 1,5-2 раза по сравнению с вылетом электрода из углеродистой стали.
При дуговой сварке в качестве защитных газов используют аргон, гелий (реже), углекислый газ.
Аргонодуговую сварку выполняют плавящимися и неплавящимися вольфрамовыми электродами. Плавящимся электродом сваривают на постоянном токе обратной полярности, используя режимы, обеспечивающие струйный перенос электродного металла. В некоторых случаях (в основном при сварке аустенитных сталей) для повышения стабильности горения дуги и особенно снижения вероятности образования пор из-за водорода при сварке плавящимся электродом используют смеси аргона с кислородом или углекислым газом (до 10%).
Сварку неплавящимся вольфрамовым электродом в основном осуществляют на постоянном токе прямой полярности. В некоторых случаях при наличии в сталях значительного количества алюминия используют переменный ток для обеспечения катодного разрушения оксидной плёнки.
Применение дуговой сварки в атмосфере углекислого газа позволяет снизить вероятность образования пор в металле шва из-за водорода; при этом обеспечивается относительно высокий коэффициент перехода легкоокисляющихся элементов. Так, коэффициент перехода титана из проволоки достигает 50%. При сварке в атмосфере аргона коэффициент перехода титана из проволоки составляет 80-90%. При сварке в углекислом газе сталей, имеющих высокое содержание хрома и низкое содержание кремния, на поверхности шва образуется тугоплавкая трудноудаляемая оксидная плёнка. Её присутствие затрудняет проведение многослойной сварки.
При сварке сталей с малым содержанием углерода (ниже 0,07-0,08%) возможно науглероживание наплавленного металла. Переход углерода в сварочную ванну усиливается при наличии в электродной проволоке алюминия, титана, кремния. В случае сварки глубокоаустенитных сталей некоторое науглероживание металла сварочной ванны в сочетании с окислением кремния снижает вероятность образования горячих трещин. Однако науглероживание может изменить свойства металла шва и, в частности, снизить коррозийные свойства. Кроме того наблюдается повышенное разбрызгивание электродного металла. Наличие брызг на поверхности металла снижает коррозийную стойкость.
Технологии сварки нержавеющих высоколегированных сталей постоянно совершенствуются. На данном этапе при строгом соблюдении технологического процесса качество сварного шва нержавейки практически не уступает по своим свойствам металлу соединяемых деталей и гарантирует высочайшую надежность сварного соединения.
gkars.ru
Электроды По нержавейке и Для нержавейки
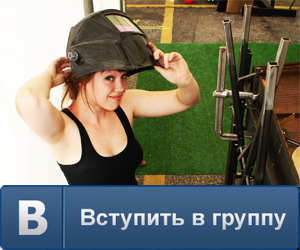
Нержавеющие стали подразделяются на три больших категории:
Стали содержащие хром менее 12%, называются нержавеющими. Хром образует защитную пленку на поверхности металла состоящую из оксида хрома. Благодаря ней стали обладают нержавеющими и коррозиестойкими свойствами. Но при разрушении этой пленки при воздействии, каких либо химических или механических воздействий, сталь теряет свою коррозиестойкий. Но пленка оксида хрома имеет свойство восстанавливаться при взаимодействии с кислородом.
Нержавеющие стали, на сегодняшний день очень широко применяются в для изготовления посуды для пищевой промышленности, в химической и нефтехимической промышленности, а также при изготовление оборудования, которое в процессе эксплуатации подвергается воздействие высоких температур.
Сварка нержавеющих сталей производиться вольфрамовыми электродами, они имеют электрическое удельное сопротивление в шесть раз превышающие сопротивление обычных электродов. Для выполнения сварочных работ на трубах и тонких листах выбирают дуговую сварку с использованием плавящимися электродами. При выполнении сварочных работ на нержавеющей стали, плавящимися электродами в инертном газе создает импульсную дугу и позволяется сваривать весьма тонкие листы толщиной до 0,8 мм.
Существуют универсальные виды электродов подходящие для всех видов сварочных работ по нержавейки. Такие электроды из-за высокого содержания в металле, из которого изготовлен электрод хрома и никеля очень высоко и благодаря этому фактору образуются весьма прочные соединения. Следует отметить, что такие же электроды используются для сварки углеродистых сталей с нержавеющими листами. В современной промышленности нержавеющие электроды практически не заменимы для выполнения работ по легированным сталям, а также к сталям, содержащим высокое количество легирующих примесей.
Получаемый в процессе сварочных работ шов обладает высокими высокой стойкостью к межкристаллитной коррозии. При выполнение сварных работ расход сварных электродов составляет, 1 килограмм на 1,5 килограмма стали. При использовании сварочных электродов для работы с теплоустойчивыми легированными сталями позволяют получить шов способный выдержать темпера ту до 600С.
elektrod-3g.ru