- Аустенитные
- Ферритные
- Ферро-аустенитные
- Мартенситные
- разнообразие изделий (лист, рулон, труба, профиль, круг, угол, квадрат,шестигранник)
- большой выбор видов поверхности (шлифованная, полированная, матовая, декоративная)
- множество марок обладающих различными качествами
- легкий процесс обработки, формирования и сборка выполненных из нее деталей
- долговечность материала
- высокая температура плавки
- Важным их свойством является устойчивость к царапинам.
- На декоративных листах не остаются отпечатки пальцев.
- Строительстве и архитектуре
- Пищевой промышленности
- Бытовых приборах
- Химической и нефтехимической промышленности
- Целлюлозно-бумажном производстве
- Электроэнергетике
- Охране окружающей среды
- Транспортном машиностроении
- Как паять стальную проволоку оловом
- Сталь как делается
- Т образный стальной уголок
- Черная нержавеющая сталь
- Прочность сталь
- Срок эксплуатации труб стальных
- Средство для удаления ржавчины с нержавеющей стали
- Сталь рулонная холоднокатаная
- Высокоуглеродистая сталь пв
- Стальная проволока 4 мм вес 1 метра
- Рулонная холоднокатаная сталь
Энциклопедия по машиностроению XXL. Нержавеющая сталь ферритная
Ферритная нержавеющая сталь - Энциклопедия по машиностроению XXL
Ферритные нержавеющие стали имеют наилучшую коррозионную стойкость после медленного охлаждения от температуры 925 °С или после отжига при 650—815 °С . Недавно разработанные ферритные нержавеющие стали повышенной чистоты содержат добавки молибдена и пониженные количества углерода и азота. Типичные сплавы имеют следующие составы, % [c.301]
Холодная деформация любой нержавеющей стали обычно оказывает меньшее влияние на стойкость к общей коррозии, если при обработке не достигается температура, достаточная для протекания диффузионных процессов. Фазовые изменения, вызываемые холодной обработкой метастабильных аустенитных сплавов, не сопровождаются существенным изменением коррозионной стойкости . К тому же закаленная аустенитная нержавеющая сталь (с гранецентрированной кубической решеткой), содержащая 18 % Сг и 8 % Ni, имеет примерно такую же коррозионную стойкость, как закаленная ферритная нержавеющая сталь (с объемно-центрированной кубической решеткой), которая содержит такое же количество хрома и никеля, но меньше углерода и азота [11]. Однако, если аналогичный сплав, содержащий смесь аустенита и феррита, кратковременно нагревать при 600 °С, то возникает разница в химическом составе двух фаз и образуются гальванические пары, ускоряющие коррозию. Иными словами, различие в составе, независимо от того, чем оно вызвано, больше влияет на коррозионное поведение, чем структурные изменения в гомогенном сплаве. По-видимому, это можно отнести в целом к металлам и сплавам. [c.302]Практические рекомендации по использованию новых ферритных нержавеющих сталей 37 277 [c.31]
Ферритные нержавеющие стали (27% Сг). . . [c.110]
Ферритные нержавеющие стали, имеющие повышенное содержание Сг или добавки ферритообразующих элементов. Они не подвержены фазовому превращению а у. К этому же классу относятся стареющие ферритные нержавеющие стали, в которых при определенных режимах термообработки из феррита выделяется ст - фаза [c.5]
Сг—15Р —5В. .... 0,74 Ферритные нержавеющие стали [c.260]
Во время быстрого охлаждения с температур выше 980 С по границам зерен выпадают карбиды. Такое выпадение карбидов, свойственное всем ферритным нержавеющим сталям, сопровождается существенным ухудшением коррозионной стойкости. Сварной шов особенно склонен к этому виду коррозии. [c.283]
Для выявления карбидов и сг-фазы в аустенитной или ферритной нержавеющей стали. Условия травления температура 20— 30 °С. напряжение 3 В. Катод из нержавеющей стали [c.45]
В растворе сульфата железа в серной кислоте ни одна из сталей 26—1S не оказалась устойчивой к МКК. Неустойчивость к МКК в этом растворе, а также в азотной кислоте отмечена и для обычных ферритных нержавеющих сталей, стабилизированных титаном. Коррозия в этом случае обусловлена селективным растворением карбидов или нитридов титана в среде с высоким окислительным потенциалом. [c.167]
ГОСТ 6032—58. Методы испытания на межкристаллитную коррозию аустенитных и аустенитно-ферритных нержавеющих сталей, Стандартгиз, 1958. [c.238]
Методы испытания на межкристаллитную коррозию аустенитных и аустенитно- ферритных нержавеющих сталей приведены в ГОСТ 6032-58. [c.89]
Ферритная нержавеющая сталь [c.530]
Некоторые составы зарубежных ферритных нержавеющих сталей [c.36]
В состав применяемых в настоящее время нержавеющих сталей и сплавов наряду с хромом, алюминием и никелем входят в различном сочетании марганец, кремний, вольфрам, кобальт и другие элементы. Такие стали и сплавы в различной степени чувствительны к термическому воздействию при нагреве, что в значительной мере затрудняет установление технологического режима резки. Это обусловливается следующими свойствами сталей. Теплопроводность, как правило, уменьшается с увеличением степени легирования стали и числа легирующих элементов. С повышением содержания углерода теплопроводность понижается. Аналогичное влияние оказывает кремний и марганец. Особенно сильно снижают теплопроводность хром и никель. Кроме того, в некоторые марки сталей входят два и более легирующих элемента, суммарное действие их сильнее, чем одного из них в таком же количестве. Так, например, теплопроводность аустенитных сталей при 540° колеблется в пределах 0,01984—0,02025 кал/см- сек- град. Значения коэффициента теплопроводности для мартенситных и ферритных нержавеющих сталей колеблется в пределах 0,02187— 0,02284 кал[см сек град, причем эти значения уменьшаются с увеличением содержания хрома от 12 до 26%. С другой стороны, теплопроводность обычной углеродистой стали составляет более 0,0405 кал/см сек град, а теплопроводность низколегированных сталей, содержащих до 5% Сг, немного ниже. [c.23]
Стали без фазового превращения так называемые ферритные нержавеющие стали с повышенным содержанием хрома или дополнительно легированные другими ферритообразующими элементами. К этому классу относятся также ферритные стали, способные при известных условиях нагрева выделять из феррита а-фазу, — так называемые стареющие ферритные нержавеющие стали. [c.8]
Испытание на межкристаллитную коррозию сварных соединений аустенитных и аустенитно-ферритных нержавеющих сталей производится по методике, изложенной в ГОСТ 6032-58. [c.138]
Нержавеющие хромистые стали хорошо свариваются. Однако ферритные нержавеющие стали при этом обладают одним существенным недостатком, а именно, возникающей при перегреве крупнозернистостью, которая не устраняется последующей термической обработкой из-за отсутствия фазовых превращений в этих сталях. Крупнозернистость вызывает повышенную хрупкость. Введение титана и азота в ферритные нержавеющие стали оказывает сдерживающее влияние на рост зерна и устраняет крупнозернистость. [c.170]
Значительно меньшее практическое применение нашли аустенитно-ферритные нержавеющие стали, характеризующиеся нестабильностью свойств. [c.172]
Значительное влияние структуры и металлургических факторов. Например, ферритные нержавеющие стали (объемноцентри-рованная кубическая решетка) гораздо более устойчивы к ионам С1 , чем аустенитные (гранецентрированная кубическая решетка). Латуни р и V (>40 % Zn) разрушаются в воде, но а-латунь (70 % Си, 30 % Zn) разрушается лишь в аммиаке или аминах. Любой крупнозернистый металл более склонен к КРН, чем тот же металл с более мелкими зернами, независимо от того, является ли растрескивание меж- или транскристаллитным. [c.138]
Сенсибилизация ферритных нержавеющих сталей наблюдается при температурах, превышающих 925 °С стойкость к межкристаллитной коррозии восстанавливается при кратковременном (10—60 мин) нагреве при 650—815 °С. Следует отметить, что эти температурные интервалы заметно отличаются от соответствующих интервалов для аустенитных нержавеющих сталей. Для ускоренных испытаний на межкристаллитную коррозию применяют аналогичные растворы (например, кипящий раствор USO4— h3SO4 или 65 % HNO3). Скорость межкристаллитной коррозии и степень поражения сталей обоих классов в этих растворах примерно одинаковы. Однако в сварных изделиях разрушения в ферритных сталях происходят как в области, непосредственно прилегающей к месту сварки, так и самом сварном шве, а в аустенитных сталях разрушения локализованы в околошовной зоне. [c.309]
Высокохромистые двухфазные аустенитно-ферритные стали обладают высокой коррозионной стойкостью, коррозионно-усталостной про шостью. хорошими механическими характеристиками. Благодаря высокой стойкости к коррозии под действием кавитации из этих сталей целесообразно изготовлять детали насосов высокой подачи для перекачки морской воды. Двухфазные аустенигно-ферритные нержавеющие стали находят широкое применение в химической и нефтехимической промышленности в качестве коррозионно-стойких конструкционных материалов. Стойкость к коррозии в морской воде этих сталей сравнима со стойкостью аустенитных сталей, т.е. достаточно высока, а сравнивае-мость и обрабатываемость лучше. [c.20]
Поверхность ферритной нержавеющей стали 430 примерно через год после начала экспозиции в морской атмосфере частично покрывается ржавчиной. Более высокое содержание хрома (17 /о) но сравнению со сталью 410 повышает стойкость к питтинговой коррозии. Скорость общей коррозии в морской атмосфере, аналогичной атмосфере Кристобаля, настолько мала, что с большим трудом может быть определена путем измерения массы [31]. [c.58]
Сталь 430, ферритный сплав, подобно мартенситным сталям, подвержена местной коррозии как на малых, так и на больших глубинах. В Кюр-Биче максимальная глубина питтинга на образцах из этой стали за 1,5 года достигла 1,5 мм [4] хотя отдельные пластинки в начальный период экспозиции могут совсем не иметь ниттингов. Более длительный по сравнению со сталью 410 индукционный период местной коррозии, иногда наблюдавшийся на стали 430, может объясняться более высоким содержанием хрома, однако полной уверенности в этом нет. Например, при глубоководных коррозионных испытаниях, результаты которых приведены в табл. 19. расположенные рядом образцы из сталей 410 и 430 корродировали примерно одинаково. Однажды начавшись, в дальнейшем коррозия может протекать с очень высокой скоростью. Как и в случае стали 410, ни высокая скорость потока воды, ни катодная защита не обеспечивают надежного предупреждения коррозии, поэтому сталь 430 и другие подобные ей ферритные нержавеющие стали не рекомендуется применять в условиях погружения. [c.64]
Влияние температуры полностью неясно тенденция к растрескиванию может быть максимальной при промежуточных температурах, но не наблюдается иммунитета и при низких и высоких температурах. Тенденция к растрескиванию является функцией содержания никеля в сплавах 17—19% Сг-ЬРе. Так, ферритные нержавеющие стали (мало никеля) и инконель-600 (много никеля) явно устойчивы. Инколой-800, хотя и лучше нержавеющих сталей типа 300, но не имеет иммунитета к растрескиванию в среде, содержащей хлориды и кислород, при наличии напряжения. [c.257]
Для ферритных нержавеющих сталей по сравнению с аусте-нитньши характерен больший перенос массы в среде натрия, особенно при содержании в них хрома менее 10—12% и при температурах более 550° С. Для сталей с содержанием хрома, превышающим 12%, интенсивность переноса массы та же, что и для хромоникелевых сталей, однако их стойкость в гораздо большей степени, чем стойкость хромоникелевых сталей, зависит от содержания в жидком металле кислорода. [c.292]
Технология горячей обработки стали типа Х18Н10Т должна строиться с учетом изменения сопротивления деформации по мере роста температуры металла, пониженной теплопроводности стали, макроструктуры и фазового состава металла в литом состоянии, химического состава, в том числе микросодержания полезных и вредных элементов. Фундаментальные исследования Н. С. Алферовой [216] показали повышение пластичности хромоникелевой нержавеющей стали с титаном и ниобием по мере повышения температуры, но до определенного предела (рис. 73). Одновременно была показана пониженная пластичность аустенитной нержавеющей стали, особенно с повышенным содержанием а-фазы, по сравнению с углеродистой и ферритной нержавеющей сталью. Наибольшая пластичность стали типа Х18Н10Т была при 1175—1250° С. [c.300]
В структуре аустенито-ферритной нержавеющей стали типа 12Х18Н10Т (ГОСТ 5949—75) присутствует некоторое количество а-фазы. Ее тем больше, чем выше концентрация ферритообразующих элементов (Сг, Т1, 51) и ниже концентрация аустенитообразующих элементов (С, N1). [c.345]
Ферритные нержавеющие стали по коррозионной стойкости в средах, не содержащих ионы хлора, не уступают классическим хро-моникелевшл сталям аустенитного класса и обеспечивают чистоту находящегося в них продукта. Наиболее слабым местом как по прочности, так и по коррозионной стойкости в этих сталях являются сварше соединения. Само понятие свариваемости включает в себя отсутствие коррозионно-активных участков металла в шве и зоне термического влияния (з.т.в.) сварного соединения, определение которых трудоемко и неоднозначно. [c.44]
Особенно сильной коррозии часто подвергаются сварные соединения, если не приняты меры к тому, чтобы их потенциал не оказался менее благородным, чем потенциал основного металла. Бровер наблюдал сильную коррозию сварного шва на трубках из нержавеющей стали типа 304 (18-8). Трубки многократно травили ингибированной 10%-ной соляной кислотой при температуре 70° С. Лабораторные коррозионные испытания подобных пар в ингибированной соляной кислоте показали, что коррозия в основном развивается на сварном шве (более 250 MMjeod). Скорость коррозии металла шва (сталь типа 312) в изолированном виде оказалась в 12—15 раз больше скорости коррозии малоуглеродистой стали или нержавеющей стали типа 304. Разрушение сварного шва в теплообменниках автор объясняет возникновением контактной коррозии между аустенитной и ферритной фазами сплава. Исследования стационарных потенциалов и поляризационных характеристик типичных аустенитных и ферритных нержавеющих сталей подтвердили это предположение. Было показано, что наиболее целесообразно в этом случае использовать инконель А и сварочные электроды из стали типа 310 (24—26% Сг 19—22% Ni макс. 0,25% С). Для трав- [c.185]
На практике в качестве анодных ингибиторов используются анионы, однако не следует считать, что только анионы функционируют при анодном ингибировании. Например, в случае нержавеющих сталей ингибированию может способствовать окислительно-восстановительная система Fe VFe за счет пассивирования.. При низких концентрациях и активных значениях потенциалов восстановление служит дополнительной катодной реакцией и увеличивает скорость растворения. Однако, как в примерах, приведенных в разд. 2.8, если катодная плотность тока превысит критическую плотность тока анодной реакции, то наступает пассивирование металла. Эта ситуация представлена диаграммой (фиг. 70), иллюстрирующей влияние концентрации ингибитора и скорости потока на коррозию ферритной нержавеющей стали в присутствии сульфата трез валенТного железа [91]. Этот тип ингибирования, который вызывает пассивность, несколько отличается от ингибиторного действия хроматов и нитритов, так как последние теряют кислород в процессе восстановления. Поскольку некоторые авторитетные специалисты называют такие ингибиторы пассиваторами то этот термин должен включать не только окислительно-восстановительные системы типа Fe /Fe , пример которой приводился вывде, но также систему Нг/Н на нержавеющей стали, содержащей благородные легирующие добавки (разд. 2.8). [c.145]
В высокохромистых ферритных нержавеющих сталях (после закалки или нормализации с высоких температур) наиболее быстро растворяются в слабоокислительных условиях неравновесные обогащенные железом карбиды хрома, которые выпадают по границам зерен в процессе охлаждения. В дур-алюмине наибольшей скоростью растворения обладает интерметаллид СиАЬ, в то время как обедненный твердый раствор растворяется гораздо медленнее. Возникающие внутренние напряжения во всех случаях будут способствовать активации границ зерен. Внутренние напряжения могут усиливаться вследствие образования продуктов коррозии по границам зерен. Межкристаллитная коррозия гетерогенных сплавов может развиваться и в условиях, когда вся поверхность металла находится в активном состоянии, если имеется большая разница в равновесных потенциалах или поляризуемости структурных составляющих и физически неоднородных участков гетерогенного сплава. Она может медленно развиваться и при пассивнохМ состоянии зер на и границ зерен, если есть значительная разница в их скоростях растворения. [c.57]
То, что критерий играет важную роль в развитии усталостных трещин, хорошо иллюстрируют примеры, приведенные на рис. 4.12 и 4.13 [35, 36]. Из рис. 4.12 видно, что изменение температуры испытания от комнатной до 700 °С сильно изменяет значения образцов из ферритной нержавеющей стали системы 18%Сг-МЬ. С увеличением температуры кинетические кривые усталости смещаются в сторону меньших значений Аномальное поведение этой стали при температуре испытаний 500 °С авторы [35] связывают с эффектом закрытия вершины усталостной трещины, вызванным пластическим поведением. Изменение режимов отпуска закаленной высокопрочной легированной стали 300-М (0,42С 0,76Сг 1,76М1 0,41Мо вес. %) в пределах от 100 до 650 С с соответствующими значениями предела прочности от 2338 до 1186 МПа также сильно влияет на изменение положения начальных участков кинетических диаграмм усталостного разрушения (см. рис. 4.13) [36]. [c.127]В табл. 4 приведены основные дефекты структуры стали. Ряд методов определения качества структуры стандартизован. Метод определения величины зерна стали (ГОСТ 5639-51). Методы определения неметаллических включений в стали (ГОСТ 1778-62). Эталоны микроструктуры стали (ГОСТ 8233-56 и ГОСТ 5640-59). Метод определения глубины обезуглероживания стальных полуфабрикатов и деталей микроанализом (ГОСТ 1763-42). Метод определения окалиностой-кости стали (ГОСТ 6130-52). Метод испытания стали на чувствительность к механическому старению (ГОСТ 7268-54). Методы испытания на межкристаллитную коррозию аустенитных и аустенитно-ферритных нержавеющих сталей (ГОСТ 6032-58). Методы определения микроструктуры твердых металлокерамических сплавов (ГОСТ 9391-60) и макроструктуры стали (ГОСТ 10243-62). Методы определения структуры серого и высокопрочного чугуна (ГОСТ 3443-57). [c.8]
Ппним из путей решения важней народнохозяйственной пробле-ш экономии остродефицитного никеля является значительное расширение применения в качестве конструкционного материала для аппаратуры химических производств экономнолегированных аустенит-но-ферритных нержавеющих сталей. [c.11]
mash-xxl.info
ферритная нержавеющая сталь - патент РФ 2250272
Изобретение относится к металлургии, в частности к сталям для трубосварочного производства, продукция которого применима в пищевой, химической, сельскохозяйственной и автомобильных отраслях, например при изготовлении гильз доильных стаканов и деталей глушителя автомобилей. Заявлена ферритная нержавеющая сталь, содержащая компоненты в следующем соотношении в мас.%: углерод 0,01-0,05; кремний 0,1-0,8; марганец 0,1-0,8; хром 13,0-18,0; титан 0,05-0,5; алюминий 0,01-0,1; кальций 0,001-0,02; цирконий 0,005-0,035; азот 0,001-0,025; бор 0,0003-0,005; барий 0,001-0,1; магний 0,001-0,02; РЗМ 0,001-0,05; никель 0,1-0,95; ванадий 0,01-0,35; молибден 0,01-0,5; вольфрам 0,01-0,3; железо – остальное. Техническим результатом изобретения является повышение пластичности и предела текучести стали и повышение производительности сварки труб. 2 табл.
Изобретение относится к области металлургии, в частности к ферритным нержавеющим сталям, и может быть использовано в трубосварочном производстве, продукция которого применима в пищевой, химической, сельскохозяйственной и автомобильных отраслях, например при изготовлении гильз доильных стаканов и деталей глушителя автомобилей,
Известны составы ферритных нержавеющих сталей, используемых как в листовом, так и в трубосварочном производстве.
В настоящее время существует проблема, в том, что все известные ферритные нержавеющие стали из-за высокого содержания углерода и незначительного содержания легирующих элементов недостаточно пластичны и имеют низкий предел текучести. Использовать их в трубосварочном производстве, например при изготовлении из сварных труб гильз доильных стаканов и деталей глушителя автомобилей, практически невозможно, так как при сферическом обжиме с утонением и гибкой таких труб идет повышенный брак.
Известна ферритная нержавеющая сталь 08Х18Т1, ГОСТ 5632-72, содержащая в мас.%:
углерод не более 0,8
кремний не более 0,8
марганец не более 0,7
хром не более 17,0-19,0
титан 0,6-1,0
Примеси:
сера не более 0,025
Фосфор не более 0,035
железо - остальное
Эта сталь используется для производства сварных труб сахарной и автомобильной промышленности.
Однако известная сталь имеет ряд недостатков: склонность к росту зерна феррита при сварке, пониженную вязкость и пластичность. Известная сталь легирована одним стабилизирующим элементом титаном (0,6-1,0%). Содержание титана, необходимое для стабилизации, не должно быть превышено, иначе образуется оксидная пленка, ухудшающая вязкость, качество поверхности и деформируемость стали при сварке труб. При содержании титана более 0,75% образуются титаниды, вызывающие охрупчивание стали в результате дисперсионного твердения при термической обработке.
Кроме того, плены титана, совместно с другими неметаллическими включениями, образуют на границе зерен феррита крупные паукообразные включения, сильно понижающие пластичность стали, а также способствующие получению трещин и порезов при производстве из сварных труб методом сферического обжима с утонением гильз доильных стаканов и при гибке деталей глушителя автомобиля.
За прототип выбрана нержавеющая сталь (см. патент RU №2017856, кл. С 22 С 38/32, 1994 г. Б.15), содержащая следующие компоненты, в мас.%:
углерод 0,01-0,08
кремний 0,1-0,8
марганец 0,1-0,8
хром 13,0-18,0
титан 0,05-0,5
алюминий 0,01-0,1
кальций 0,001-0,02
цирконий 0,005-0,035
азот 0,001-0,025
бор 0,0003-0,005
барий 0,001-0,1
магний 0,001-0,02
РЗМ 0,001-0,05
железо остальное
Однако предложенный состав известной стали предназначен для получения листового проката с хорошей штампуемостью, повышенной трещиноустойчивостью и полируемостью при вторичной деформации после глубокой вытяжки изделий. Использование этого состава стали для производства сварных труб механизированной аргонодуговой сваркой двухдуговым плазмотроном и их последующей обработки методом сферического обжима с утонением и гибкой, в частности для гильз доильного стакана и для деталей глушителя автомобиля, осуществлять практически невозможно из-за повышенного брака по трещинам, порезу и т.д.
Микроструктура стали состоит из зерен феррита, карбидов и карбонитридов титана и циркония и карбида хрома типа Сr 23С6, располагающегося в основном по границам зерен. Следует отметить, что когда карбиды хрома в известной стали образуют при первичной кристаллизации и термической обработке карбидную сетку по границам зерен, то происходит резкое снижение пластичности и предела текучести стали. Величина зерна феррита - основного металла сварных труб, определяемая ее первичной кристаллизацией, должна быть по нормам не крупнее пятого бала по ГОСТ 5639-82, а в зоне сварки не крупнее второго бала, но на практике при сварке труб из-за низкой скорости сварки величина зерна в зоне сварки была один балл, что приводило к повышению брака при производстве деталей доильного оборудования и глушителей автомобилей, а также к снижению качества труб при испытаниях на сплющивание и раздачу конусом.
Кроме этого, известная сталь, имея низкую прочность, текучесть и пластичность, не может сопротивляться возникающим напряжениям при обжиме с утонением и гибкой, что заставляло применять для вышеуказанных изделий дорогостоящую хромоникелевую сталь 12Х18Н10Т. При этом состав известной стали не позволял иметь при сварке труб высокий тепловой эффект мощности сварочной дуги и повышать скорость сварки труб 42×2 мм более 0,8 м/мин, а труб 43×1,5 мм более 1,5 м/мин из-за непровара, трещин и других дефектов, что отрицательно сказывается на производительности.
Задача предлагаемого изобретения состояла в разработке состава ферритной нержавеющей стали, позволяющего улучшить качество сварных труб путем повышения пластичности и предела текучести, а также повысить производительность сварки труб.
Поставленная задача достигается тем, что в известный состав ферритной нержавеющей стали, содержащей углерод, кремний, марганец, хром, титан, алюминий, кальций, цирконий, азот, бор, барий, магний, РЗМ и железо, дополнительно вводят никель, ванадий, молибден и вольфрам при следующем соотношении компонентов, в мас.%:
углерод 0,01-0,05
кремний 0,1-0,8
марганец 0,1-0,8
хром 13,0-18,0
титан 0,05-0,5
алюминий 0,01-0,1
кальций 0,001-0,02
цирконий 0,005-0,035
азот 0,001-0,025
бор 0,0003-0,005
барий 0,001-0,1
магний 0,001-0,02
РЗМ 0,001-0,05
никель 0,1-0,95
ванадий 0,01-0,35
молибден 0,01-0,5
вольфрам 0,01-0,3
железо остальное
Сталь может содержать примеси, в мас.%: сера до 0,25, фосфор до 0,35 и медь до 0,3.
Сущность изобретения состоит в следующем.
В состав предлагаемой стали с целью улучшения качества сварки труб путем повышения их прочностных и пластичных свойств введено 0,1-0,95% никеля. Он образует твердый раствор с ферритом, изменяя кристаллическую решетку феррита и упрочняя междуатомные связи. Никель в ферритной нержавеющей стали в вышеуказанных количествах способствует появлению -
-превращений. Оно протекает не до конца, что тем не менее дает заметное повышение предела текучести, не снижая пластичности. Превышение содержания никеля более 0,95% приводит к появлению аустенита в структуре стали, что неблагоприятно сказывается на качестве труб.
Дополнительное введение 0,01-0,35% ванадия в предлагаемую сталь основано на образование карбидов, карбонитридов и нитридов, которые выделяются в высокодисперсном состоянии и равномерно располагаются внутри зерен и упрочняют сталь. Ванадий повышает точку Ас 3 стали, что благоприятно сказывается при сварке труб. Ванадий измельчает зерно феррита основного металла и сварочного шва, способствуя получению стали с мелкозернистой структурой при первичной кристаллизации, что увеличивает сопротивление стали сдвиговой деформацией при обжиме с утонением и гибке сварных труб при производстве деталей доильного оборудования и глушителей автомобиля.
Введение в сталь ванадия ниже 0,01% не приводит к заметному повышению свойств стали, более 0,35% ухудшает релаксационную стойкость стали и увеличивает загрязнение стали нитридами ванадия.
Дополнительное введение в состав предлагаемой стали 0,01-0,5% молибдена и 0,01-0,3% вольфрама содействует образованию карбидных и карбонитридных фаз, способствующих измельчению ферритного зерна. Молибден и вольфрам, растворяясь в феррите, увеличивает энергию межатомных связей и сопротивление упругой деформации решетки твердого раствора феррита, упрочняют его и повышают термическую стойкость. Свойство феррита, дополнительно упрочненного молибденом и вольфрамом, не зависят от того, как охлаждалась сталь - быстро или медленно, что очень полезно при сварке труб. Одновременно молибден и вольфрам, входя в состав упрочняющей карбидной фазы типа (Cr, Mo, W, V, Fe, Si)23С6, повышают прочность межатомных связей в ней, снижают ее способность к коагуляции и тормозят образование карбидной сетки, что снижает хрупкость и повышает пластичность сварных труб.
Кроме этого в предлагаемой стали снижено содержание основного элемента, влияющего на качество сварки труб - углерода с 0,08% до 0,05%, что позволило также уменьшить склонность стали к охрупчиванию в сварных соединениях. Общепринятое содержание углерода до 0,08% оказывает неблагоприятное действие при сварке труб, так как он расширяет интервал кристаллизации и усиливает склонность стали к образованию горячих и холодных трещин. Благодаря снижению содержания углерода уменьшается интенсивность образования карбидной сетки хромистого карбида типа (Cr, Mi, Mo, W, Fe, Si)23С6 и его количества в твердом растворе феррита и по границам зерен вследствие его растворения нитридами титана, циркония и ванадия, что повышает качество металла и улучшает свариваемость труб.
Дополнительное комплексное введение никеля, ванадия, молибдена и вольфрама и предлагаемое соотношение компонентов предлагаемой ферритной нержавеющей стали способствуют повышению качества сварных труб за счет:
- упрочнения твердого раствора феррита за счет увеличения параметра решетки легированного феррита с 2,86Å до 2,94 Å;
- образования сложных дисперсных карбидов и карбонитридов, содержащих, кроме хрома, титана, циркония, еще ванадий, вольфрам и молибден;
- создания условия для развития преимущественно внутризеренных сегрегации и выделения высокодисперсных карбидов, карбонитридов и нитридов округлой формы как в теле зерна, так и по границам при охлаждении стали от температуры сварки и при термической обработке;
- затруднения коагуляции упрочняющих карбидных и карбонитридных фаз, благодаря уменьшению диффузионной подвижности и снижению коэффициентов диффузии и самодиффузии;
- получения умельченной структуры основного металла, металла сварочного шва и околошовной зоны после сварки труб за счет дополнительного легирования и увеличения скорости сварки;
- замедления скорости разупрочнения стали, что способствует уменьшению глубины и ширины зоны разупрочнению после сварки труб.
Следует отметить, что совместное введение в предлагаемую ферритную нержавеющую сталь никеля, ванадия, молибдена и вольфрама в пределах, указанных выше, а также снижение содержания углерода до 0,05% дало возможность увеличить скорость сварки труб в 1,5 раза и повысить тепловой эффект мощности сварочной дуги за счет увеличения силы тока дуги. Это позволило уменьшить объем поверхности расплава металла и снизить неоднородность металла сварочного шва. При этом в швах отсутствуют дефекты, зерна феррита структуры шва ориентированы по следам дендритной структуры, причем размер зерна значительно уменьшается.
Пример получения вещества
В 000 НПИФ “Сплав” в производственных условиях изготавливают ферритную нержавеющую сталь, содержащую в мас.%:
хром металлический ГОСТ 5905-67 - 16,5
ферросилиций ГОСТ 1415-70 - 0,5
ферромарганец ГОСТ 4755-70 - 0,5
ферротитан ГОСТ 4761-67 - 0,6
азотированный марганец ТУ 14-5-59-75 - 0,1
электродный бой - 0,02
алюминий ГОСТ 11070-74 - 0,1
ферросиликобарий ТУ 14-5-160-84 - 0,05
никель Н-1 ГОСТ 849-70 - 0,5
феррованадий ГОСТ 4760-84 - 0,2
ферромолибден ГОСТ 4759-79 - 0,3
ферровольфрам ГОСТ 17293-71 - 0,15
лигатура РЗМ ФСЗО ТУ 14-5-136-8 - 0,15
силикокальций ГОСТ 4762-71 - 0,03
ферробор ФБ-В ТУ 14-5-14-72 - 0,01
ферросиликоцирконий ФСЦР-50 ТУ 14-5-3-77 - 0,05
ферросиликомагниевый сплав ТУ 14-05-134-86 - 0,03
армко–железо - остальное
Выплавку стали производили в индукционной печи с основной футеровкой. При этом армко-железо, хром, электродный бой, азотированный марганец, никель, ферромолибден и ферровольфрам вводили непосредственно в завалку вместе со шлаковой смесью, состоящей из свежеобожженной извести, плавикового штата и магнезита.
После полного расплавления вводили ферросилиций, ферромарганец, алюминий, ферротитан. При нагреве металла до температуры 1610°С перед разливкой вводили силикокальций, феррованадий, ферросиликоцирконий, лигатуру РЗМ и ферросиликомагниевый сплав (по известной технологии).
Аналогично были приготовлены еще четыре состава предлагаемой стали с различным содержанием компонентов и составов (таблица 1).
Металл разливали сифоном в изложницы. Дальнейший передел слитков на холоднокатанный рулонный лист проводили на заводе “Запорожсталь” по принятой для ферритных нержавеющих сталей технологии. Рулоны на сварку труб поставляли с поверхностью в состоянии прокатки, термообработки и травления. Режим термической обработки: закалка - 850°С, охлаждение в воде.
В таблице 1 представлены составы испытываемых ферритных нержавеющих сталей.
Таблица 1 | |||||
Компоненты | Содержание в мас % | ||||
I | II | III | IV | V | |
Углерод | 0,008 | 0,01 | 0,03 | 0,05 | 0,06 |
Кремний | 0,08 | 0,1 | 0,4 | 0,8 | 0,9 |
Марганец | 0,08 | 0,1 | 0,4 | 0,8 | 0,85 |
Хром | 12,5 | 13,0 | 15,5 | 18,0 | 18,5 |
Титан | 0,04 | 0,05 | 0,3 | 0,5 | 0,55 |
Алюминий | 0,008 | 0,01 | 0,05 | 0,1 | 0,12 |
Кальций | 0,0008 | 0,001 | 0,01 | 0,02 | 0,022 |
Цирконий | 0,036 | 0,035 | 0,02 | 0,005 | 0,004 |
Азот | 0,0009 | 0,001 | 0,012 | 0,025 | 0,026 |
Бор | 0,0002 | 0,0003 | 0,004 | 0,005 | 0,006 |
Барий | 0,0009 | 0,001 | 0,05 | 0,1 | 0,11 |
Магний | 0,0009 | 0,001 | 0,01 | 0,02 | 0,021 |
РЗМ | 0,0009 | 0,001 | 0,02 | 0,05 | 0,051 |
Никель | 0,09 | 0,1 | 0,46 | 0,95 | 0,96 |
Ванадий | 0,009 | 0,01 | 0,18 | 0,35 | 0,36 |
Молибден | 0,009 | 0,01 | 0,25 | 0,5 | 0,51 |
Вольфрам | 0,009 | 0,01 | 0,15 | 0,3 | 0,31 |
Сера | 0,01 | 0,012 | 0,018 | 0,025 | 0,026 |
Фосфор | 0,036 | 0,035 | 0,02 | 0,012 | 0,01 |
Медь | 0,001 | 0,01 | 0,15 | 0,3 | 0,31 |
Железо | остальное | остальное | остальное | остальное | остальное |
Сварку труб производили из холоднокатаной рулонной стали толщиной 1,5-2 мм на Новомосковском трубном заводе на стане АДС 20-76 в специальной камере аргонодуговой сваркой двухдуговым плазмотроном конструкции НИАТ. Перед сваркой осуществляли предварительный подогрев трубной заготовки через высокочастотный индуктор при температуре 200-300°С. Газовая защита при сварке и остывающего шва производили чистым аргоном. Первая дуга плазмотрона производила подогрев и подплавление кромок, а вторая проплавляла металл. Скорость сварки и ток первой и второй дуги плазмотрона фиксировался самопишущим прибором Н-340.
РЕЖИМЫ СВАРКИ | |||||
Диаметр и толщина трубы, мм | |||||
Скорость Сварки, м/мин | Сварочный ток, А | Напряжение, В | |||
1-й дуги | 2-й дуги | 1-й дуги | 2-й дуги | ||
42×2 | 0,8 | 70-100 | 100-130 | 15-18 | 16-20 |
42×2 | 1,2 | 100-130 | 120-160 | 15-18 | 17-20 |
43×1,5 | 1,5 | 90-120 | 120-150 | 15-18 | 17-20 |
43×1,5 | 2,0 | 100-130 | 150-180 | 15-18 | 17-20 |
Для снятия внутренних напряжений сварного шва в линии стана осуществляли 1-ю термообработку с помощью кольцевого многовиткового индуктора путем нагрева до температуры 800±20°С с последующим струйным водяным охлаждением. Вторую термическую обработку производили после калибровки и правки труб в проходных электропечах типа СРО 8/100 при температурах 810-860°С со скоростью движения труб 0,7 м/мин.
Механические испытания труб производили согласно ГОСТ 10006-80 и ГОСТ 8695-75. Механические свойства металла сварочного шва определяли на продольных плоских образцах с шириной рабочей части 1,2 мм. Процент увеличения наружного диаметра сварной трубы при испытании на раздачу конусом определяли по 10 образцам на патрубках длиной 100 мм путем ввода конусной оправки, имеющей наклон 1:10 или угол наклона, равный 60°, до появления трещины на розданной части патрубка.
Испытание сварного соединения на статический изгиб производили по ГОСТ 6996-66 на 5 образцах каждой плавки. Оно характеризуется углом изгиба, при котором в растянутой зоне образовывалась первая трещина, развивающаяся в процессе испытания.
В таблице 2 представлены характеристики показателей и свойства металла сварных труб.
Анализируя данные таблицы 2, приходим к выводу, что оптимальное содержание компонентов в ферритной нержавеющей стали для сварки труб при их последующей обработке методом сферического обжима с утонением и гибкой находится в пределах (мас.%):
Углерод 0,01-0,05
Кремний 0,1-0,8
Марганец 0,1-0,8
Хром 13,0-18,0
Титан 0,05-0,5
Алюминий 0,01-0,1
Кальций 0,001-0,02
Цирконий 0,005-0,035
Азот 0,001-0,025
Бор 0,0003-0,005
Барий 0,001-0,1
Магний 0,001-0,02
РЗМ 0,001-0,05
Никель 0,1-0,95
Ванадий 0,01-0,35
Молибден 0,01-0,5
Вольфрам 0,01-0,3
Железо остальное
При введении в состав предлагаемой ферритной нержавеющей стали меньше нижнего предела никеля, ванадия, молибдена и вольфрама не видно заметного эффекта в улучшении качества сварки труб, а также в повышении производительности их изготовления.
При составе компонентов стали в пределах оптимальных улучшается качество свариваемых труб, позволяющих повысить показатели по испытаниям на раздачу конусом, сплющивании и гибке, что позволило производить из них детали доильного оборудования и глушителя автомобилей методом сферического обжима с утонением и гибкой. Кроме этого, оптимальный состав позволил повысить производительность сварки труб, предел текучести и относительное удлинение. Если компоненты состава превышают допустимые пределы (см. таблицу 2), то мы имеем снижение свойств и харпактеристик показателей, так как они сами начинают способствовать увеличению сопротивления деформации и охрупчиванию.
Использование предлагаемого состава стали позволяет за счет улучшения качества сварных труб изготавливать детали доильного оборудования и глушителя автомобилей. Дополнительное преимущество имеем в повышении производительности изготовления сварных труб, предела текучести и относительного удлинения сварного шва.
Промышленное опробование сварных труб размером 42×2 мм из предлагаемого состава ферритной нержавеющей стали производили на Резекненском заводе доильного оборудования. Из труб методом сферического обжима с утонением по существующей на заводе серийной технологии изготовили 1500 штук гильз доильного стакана. Брак по трещинам составил всего 0,5%. При изготовлении этих деталей из хромоникелевой аустенитной стали 12Х18Н10Т брак достигал 5%.
Опробование изготовления 1000 деталей глушителя №2103-1201048/50 из труб размером 45×1,5 мм показало, что брак по гибке снижается на 30% по сравнению с производством этих деталей из стали 08Х18Т1.
Таким образом, использование предлагаемой ферритной нержавеющей стали в трубосварочном производстве, продукция которого идет для изготовления деталей доильного оборудования и автомобильной, сахарной и других отраслей промышленности, в том числе при производстве гильз доильных стаканов и деталей глушителя автомобилей, получаемых из сварных труб методом сферического обжима с утонением и гибкой, дает значительный экономический эффект и имеет большой спрос в вышеуказанных отраслях.
ФОРМУЛА ИЗОБРЕТЕНИЯ
Ферритная нержавеющая сталь, содержащая углерод, кремний, марганец, хром, титан, алюминий, кальций, азот, цирконий, бор, магний, барий, РЗМ и железо, отличающаяся тем, что она дополнительно содержит никель, ванадий, молибден и вольфрам при следующем соотношении компонентов, мас.%:
углерод 0,01-0,05
кремний 0,1-0,8
марганец 0,1-0,8
хром 13,0-18,0
титан 0,05-0,5
алюминий 0,01-0,1
кальций 0,001-0,02
цирконий 0,005-0,035
азот 0,001-0,025
бор 0,0003-0,005
барий 0,001-0,1
магний 0,001-0,02
РЗМ 0,001-0,05
никель 0,1-0,95
ванадий 0,01-0,35
молибден 0,01-0,5
вольфрам 0,01-0,3
железо остальное
www.freepatent.ru
ЭКОНОМИЧНАЯ ФЕРРИТНАЯ НЕРЖАВЕЮЩАЯ СТАЛЬ
[0001] Настоящая заявка представляет собой заявку на патент, по которой испрашивается приоритет на основании предварительной заявки на патент №61/619048 под названием "Ферритная нержавеющая сталь с 21-процентным содержанием хрома" ("21% Cr Ferritic Stainless Steel,"), поданной 2 апреля 2012 года. Содержание заявки №61/619048 включено в настоящую заявку посредством ссылки.
Краткое описание изобретения
[0002] Существует потребность в получении ферритной нержавеющей стали, обладающей коррозионной устойчивостью, сравнимой с таковой у нержавеющей стали марки 304L в системе ASTM, но при этом по существу не содержащей никель, стабилизированной титаном и ниобием для обеспечения защиты от межкристаллитной коррозии и содержащей хром, медь и молибден для обеспечения сопротивления точечной коррозии без ущерба для сопротивления коррозионному растрескиванию под напряжением. Такая сталь особенно подходит для товарных стальных листов, которые обычно находят применение на предприятиях общественного питания, в архитектурных компонентах, и автомобильной промышленности, в том числе, но не ограничиваясь ими, в устройствах для отвода выхлопных газов и элементах селективного каталитического восстановления (СКВ) коммерческих и пассажирских транспортных средств.
Подробное описание изобретения
[0003] У ферритных нержавеющих сталей относительные количества титана, ниобия, углерода и азота регулируют для достижения субравновесного качества поверхности, по существу, равноосной зернистой структуры литья и, по существу, полной стабилизации в отношении межкристаллитной коррозии. Кроме того, регулируют относительное содержание хрома, меди и молибдена с целью оптимизировать коррозионную устойчивость.
[0004] Субравновесные расплавы, как правило, определяются как композиции с содержанием титана и азота, достаточно низким для тог о, чтобы они не образовывали нитридов титана в расплаве сплава. Такие осадки могут образовывать дефекты, такие как поверхностно-строчечные дефекты или расслоения во время горячей или холодной прокатки. Такие дефекты могут ухудшать формуемость, коррозионную устойчивость и внешний вид. Фиг. 1 была получена из приводимой в качестве примера фазовой диаграммы, построенной для одного из вариантов реализации ферритной нержавеющей стали с помощью термодинамического моделирования для элементов титана и азота при температуре ликвидуса. Для того чтобы, по существу, не содержать нитридов титана и считаться субравновесным, уровни содержания титана и азота в ферритной нержавеющей стали должны находиться в левой или нижней части кривой растворимости, показанной на фиг. 1. Кривая растворимости нитрида титана, показанная на фиг. 1, может быть математически представлена следующим образом:
Уравнение 1: Timax=0,0044(N-1,027),
где Timax представляет собой максимальную концентрацию титана в процентах по массе и N представляет собой концентрацию азота в процентах по массе. Все концентрации здесь будут даваться в процентах по массе, если специально не указано иное.
[0005] На основании уравнения 1 можно заключить, что если содержание азота в одном из вариантов реализации поддерживают на уровне или ниже 0,020%, то концентрацию титана в этом варианте реализации следует поддерживать па уровне или ниже 0,25%. Если позволить концентрации титана превысить 0,25%, то это может привести к образованию осадков нитрида титана в расплавленном сплаве. Однако на фиг. 1 также показано, что концентрация титана выше 0,25% могут быть допустимы, если содержание азота меньше, чем 0,02%.
[0006] Варианты реализации ферритной нержавеющей стали демонстрируют равноосную литую, прокатанную и отожженную зернистую структуру без больших столбчатых зерен в слябах или ленточных зерен в прокатанном листе. Эта отонченная зернистая структура может улучшить формуемость и прочность. Для достижения этой зернистой структуры должны быть достаточные содержания титана, азота и кислорода, чтобы обеспечить затравку в затвердевающих слябах и обеспечивать центры для начала образования равноосных зерен. В таких вариантах минимальные уровни титана и уровни азота показаны на фиг. 1 и выражаются следующим уравнением:
Уравнение 2: Timin=0,0025/N,
где Timin представляет собой минимальную концентрацию титана в процентах по массе и N представляет собой концентрацию азота в процентах по массе.
[0007] На основании уравнения 2 можно заключить, что если содержание азота поддерживают на уровне или ниже 0,02% в одном из вариантов реализации, то минимальная концентрация титана составляет 0,125%. Параболическая кривая, представленная на фиг. 1, показывает, что равноосная зернистая структура может быть достигнута при содержании азота выше 0,02%, если общая концентрация титана уменьшена. При содержаниях титана и азота, находящихся справе или выше графика уравнения 2 ожидается образование структуры из равноосных зерен. Это соотношение между субравновесностыо и содержаниями титана и азота, которые привели к получению равноосной зернистой структуры, представлено на фиг. 1, на которой минимальное уравнение титана (Уравнение 2), нанесено на фазовую диаграмму ликвидуса на фиг. 1. Область между двумя параболическими линиями представляет собой диапазон содержаний титана и азота в вариантах реализации настоящего изобретения.
[0008] Полностью стабилизированные расплавы ферритной нержавеющей стали должны иметь достаточно титана и ниобия для объединения с растворимыми углеродом и азотом, присутствующими в стали. Это помогает предотвратить образование карбида хрома и нитридов и снижение межкристаллитной коррозионной устойчивости. Минимальные содержания титана и углерода, необходимые для полной стабилизации лучше всего могут быть представлены следующим уравнением:
Уравнение 3: Ti+Cbmin=0,2%+4(С+N),
где Ti представляет собой количество титана в процентах по массе, Cbmin представляет собой минимальное количество ниобия в процентах по массе, С представляет собой количество углерода в процентах по массе и N представляет собой количество азота в процентах по массе.
[0009] В описанном выше варианте реализации уровень титана, необходимый для равноосной зернистой структуры и условий субравновесия, был определен, когда максимальный уровень азота составил 0,02%. Как описано выше, из соответствующих уравнений 1 и 2 было получено минимальное содержание титана 0,125% и максимальное содержание титана 0,25%. В таких вариантах реализации, используя максимум 0,025% углерода и применяя уравнение 3, потребовалось бы минимальное содержание ниобия от 0,25% до 0,13% соответственно для минимального и максимального уровней титана. В некоторых таких вариантах реализации целевое значение для концентрации ниобия было бы 0,25%.
[0010] В некоторых вариантах реализации, поддерживая содержание меди между 0,40-0,80% в матрице, состоящей примерно из 21% хрома и 0,25% молибдена, можно достичь общей коррозионной устойчивости, сопоставимой, если не лучше, чем у имеющейся в наличии марки 304L. Единственное исключение может быть в присутствии силыюкислого восстанавливающего хлорида, подобного соляной кислоте. Сплавы с добавлением меди демонстрируют улучшенные рабочие характеристики в серной кислоте. Когда содержание меди поддерживают между 0,4-0,8%), скорость анодного растворения уменьшается и электрохимический потенциал пробоя достигает максимума в нейтральных хлоридных средах. В некоторых вариантах реализации оптимальные уровни содержания хрома, молибдена и меди в весовых процентах удовлетворяют следующим двум уравнениям:
Уравнение 4: 20,5<=Cr+3,3Мо;
Уравнение 5: 0,6<=Cu+Мо<=1,4, где Cumax<0,80.
[0011] В некоторых вариантах реализации ферритная нержавеющая сталь может содержать углерод в количестве от примерно 0,020 или менее процентов по массе.
[0012] В некоторых вариантах реализации ферритная нержавеющая сталь может содержать марганец в количестве от примерно 0,40 или менее процентов по массе.
[0013] В некоторых вариантах реализации ферритная нержавеющая сталь может содержать фосфор в количестве от примерно 0,030 или менее процентов по массе.
[0014] В некоторых вариантах реализации ферритная нержавеющая сталь может содержать серу в количестве от примерно 0,010 или менее процентов по массе.
[0015] В некоторых вариантах реализации ферритная нержавеющая сталь может содержать кремний в количестве от примерно 0,30-0,50 процентов по массе. Некоторые варианты могут содержать примерно 0,40% кремния.
[0016] В некоторых вариантах реализации ферритная нержавеющая сталь может содержать хром в количестве от примерно 20,0-23,0 процентов по массе. Некоторые варианты могут содержать примерно 21.5-22 процентов по массе хрома, и некоторые варианты могут содержать примерно 21,75% хрома.
[0017] В некоторых вариантах реализации ферритная нержавеющая сталь может содержать никель в количестве от примерно 0,40 или менее процентов по массе.
[0018] В некоторых вариантах реализации ферритная нержавеющая сталь может содержать азот в количестве от примерно 0,020 или менее процентов по массе.
[0019] В некоторых вариантах реализации ферритная нержавеющая сталь может содержать медь в количестве от примерно 0,40-0,80 процентов по массе. Некоторые варианты реализации могут содержать примерно 0,45-0,75 процентов по массе меди и некоторые варианты реализации могут содержать от примерно 0,60% меди.
[0020] В некоторых вариантах реализации ферритная нержавеющая сталь может содержать молибден в количестве от примерно 0,20-0,60 процентов по массе. Некоторые варианты реализации могут содержать примерно 0,30-0,5 процентов по массе молибдена, и некоторые варианты реализации могут содержать от примерно 0,40% молибдена.
[0021] В некоторых вариантах реализации ферритная нержавеющая сталь может содержать титан в количестве от примерно 0,10-0,25 процентов по массе. Некоторые варианты реализации могут содержать примерно 0,17-0,25 процентов по массе титана, и некоторые варианты реализации могут содержать от примерно 0,21% титана.
[0022] В некоторых вариантах реализации ферритная нержавеющая сталь может содержать ниобий в количестве от примерно 0,20-0,30 процентов по массе. Некоторые варианты реализации могут содержать от примерно 0,25% ниобия.
[0023] В некоторых вариантах реализации ферритная нержавеющая сталь может содержать алюминий в количестве от примерно 0,010 или менее процентов по массе.
[0024] Ферритные нержавеющие стали получают с применением технологических условий, известных в данной области, для применения в получении ферритных нержавеющих сталей, таких, как способы, описанные в патентах США №6855213 и №5868875.
[0025] В некоторых вариантах реализации ферритные нержавеющие стали могут также содержать другие элементы, известные в сталелитейной области, которые могут быть либо добавлены преднамеренно, либо присутствовать в виде остаточных элементов, т.е. примесей из способа получения стали.
[0026] Расплав железа для ферритной нержавеющей стали получают в плавильной печи, такой как электродуговая печь. Этот расплав железа может быть получен в плавильной печи из твердого железосодержащего лома, лома углеродистой стали, лома нержавеющей стали, твердого железа, содержащего материалы, содержащие оксиды железа, карбида железа, железа прямого восстановления, железа горячего брикетирования, или расплав может быть получен вверх по потоку из плавильной печи в доменной печи или любом другом устройстве для выплавки чугуна, способном обеспечивать расплав железа. Расплав железа затем будет очищен в плавильной печи или переведен в очищающий сосуд, такой как аргон-кислород-обезуглероживающий сосуд или вакуум-кислород-обезуглероживающий сосуд, за которым следует участок отделки, такой как металлургическая печь-ковш или участок загрузки проволоки.
[0027] В некоторых вариантах реализации сталь отливают из расплава, содержащего достаточное количество титана и азота, но регулируемое количество алюминия, для образования небольших включений оксида титана, чтобы обеспечить необходимые ядра для образования равноосной зернистой структуры литья таким образом, что отожженный лист, получаемый из этой стали, также имеет улучшенные рифленые характеристики.
[0028] В некоторых вариантах реализации титан добавляют в расплав для раскисления перед литьем. Раскисление расплава с титаном образует мелкие включения оксида титана, которые обеспечивают наличие ядер, что приводит к литой равноосной мелкозернистой структуре. Чтобы свести к минимуму образование включений глинозема, то есть оксида алюминия Al2O3, в этот очищенный расплав можно не добавлять алюминий в качестве раскислителя. В некоторых вариантах реализации титан и азот могут присутствовать в расплаве перед литьем в таком количестве, что отношение содержания продукта взаимодействия титана и азота к остаточному алюминию составляет, по меньшей мере, 0,14.
[0029] Если сталь должна быть стабилизирована, то может быть добавлено достаточное количество титана помимо того, что необходимо для раскисления, для объединения с углеродом и азотом в расплаве, но предпочтительно меньше, чем требуется для насыщения азотом, то есть в субравновесном количестве, тем самым избегая или, по меньшей мере, сводя к минимуму осаждение крупных включений нитрида титана до затвердевания.
[0030] Литая сталь подвергается горячей обработке в лист. В этом описании термин "лист" подразумевает непрерывную полосу или мерные длины листов, образованные из непрерывной полосы, а термин "подвергается горячей обработке" означает, что литая сталь будет подогрета, если это необходимо, а затем уменьшена до заданной толщины, например, посредством горячей прокатки. В случае горячей прокатки стальной сляб подогревают до 2000-2350°F (1093-1288°C), применяют горячую прокатку при конечной температуре 1500-1800°F (816-982°C) и сматывают в рулон при температуре 1000-1400°F (538-760°C). Горячекатаный лист также известен как "горячая полоса". В некоторых вариантах реализации горячая полоса может быть отожжена при пиковой температуре металла 1700-2100°F (926-1149°C). В некоторых вариантах реализации горячая полоса может быть очищена от окалины и холоднокатана, по меньшей мере, на 40% до требуемой конечной толщины листа. В других вариантах реализации горячая полоса может быть очищена от окалины и холоднокатана, по меньшей мере, на 50% до требуемой конечной толщины листа. После чего холодногокатаный лист может быть окончательно отожжен при пиковой температуре металла 1700-2100°F (927-1149°C).
[0031] Ферритная нержавеющая сталь может быть получена из листа горячей обработки, сделанного несколькими способами. Лист может быть получен из слябов, образованных из слитков или слябов непрерывного литья толщиной 50-200 мм, которые нагревают до 2000-2350°F (1093-1288°C), с последующей горячей прокаткой, чтобы получить стартовый лист горячей обработки толщиной 1-7 мм, или лист может быть подвергнут горячей обработке из полосы непрерывного литья в толщинах 2-26 мм. Настоящий способ применим к листу, полученному с помощью способов, в которых слябы непрерывного литья или слябы, полученные из слитков, подают непосредственно на стан горячей прокатки с или без существенного подогрева, или слитки подвергаются горячей обработке в слябы достаточной температуры для того, чтобы быть горячекатаными в лист с или без дальнейшего подогрева.
ПРИМЕР 1
[0032] Для получения композиций ферритной нержавеющей стали, имеющей в результате общую коррозионную устойчивость, сравнимую с аустенитной нержавеющей сталью марки 304L, серия лабораторных плавок была расплавлена и проанализирована на устойчивость к локальной коррозии.
[0033] Первый набор плавок был расплавлен в лаборатории с применением средств для плавления на открытом воздухе. Цель этих серий расплавов на открытом воздухе состояла в том, чтобы лучше понять роль хрома, молибдена и меди в ферритной матрице, и в том, чтобы определить, как изменения в составе повлияют на коррозионное поведение по сравнению со сталью марки 304L. Составы вариантов реализации, использованные в исследованиях расплавов на открытом воздухе, приведены в таблице 1.
[0034] Как погружение в хлорид железа, так и электрохимические тесты были использованы для оценки составов, приведенных в Таблице 1, и сравнения с рабочими характеристиками стали марки 304L.
[0035] Образцы были протестированы путем определения потери массы после 24-часового воздействия раствором хлорида железа (до 6%) при 50°C, используя методики, описанные в ASTM G48-тестовом способе А точечной коррозии хлоридом железа. Этот тестовое воздействие оценивает основную устойчивость к точечной коррозии во время воздействия кислой, сильно окисляющей, хлоридной среды.
[0036] В из предварительных тестов следовало, что более высокое содержание хрома в ферритных сплавах, в которых имеется небольшая добавка меди, привело бы к наибольшей коррозионной устойчивости композиции в рамках серии. Композиция, имеющая наибольшее содержание меди, равное в 1%, не показывала такие же высокие характеристики, как другие химические составы. Однако это поведение могло быть следствием худшего, по сравнению с идеальным, качества поверхности вследствие способа плавления.
[0037] Более тщательное исследование прочности пассивирующей пленки и репассивационного поведения проводили с применением электрохимических методов, которые включали как диаграммы коррозионного поведения (ДКП), так и циклическую поляризацию в деаэрированной, разбавленной, нейтральной хлоридной среде. Электрохимическое поведение, наблюдаемое для этого набора образцов, полученных плавлением на открытом воздухе, показало, что комбинация примерно 21% хрома в присутствии примерно 0,5% меди и небольшой добавка молибдена, обеспечила три главных усовершенствования по сравнению со сталью марки 304L. Во-первых, добавка меди, привела к уменьшению начальной скорости анодного растворения на поверхности; во-вторых, присутствие меди и присутствие небольшого количества молибдена в химического составе с 21-процентным содержанием хрома помогло в образовании прочной пассивирующей пленки; и, в-третьих, молибден и высокое содержание хрома помогли в улучшении репассивационного поведения. Содержание меди в химическом составе для расплава, включающем 21-процентный хром с остаточным молибденом, казалось, имел "оптимальный" уровень в том отношении, что добавление 1% меди привело к уменьшению отдачи. Это подтверждает поведение, наблюдаемое в тесте точечной коррозии хлоридом железа. Дополнительные расплавляющие химические составы были подвергнуты вакуумной плавке в надежде создать более чистые образцы стали и определить оптимальную добавку меди в целях достижения наилучшей общей коррозионной устойчивости.
ПРИМЕР 2
Второй набор химических составов для расплава, приведенный в таблице 2, был подвергнут плавлению. Составы в этом исследовании представлены ниже.
Указанные выше плавки отличаются, главным образом, содержанием меди. Дополнительные вакуумные плавки, имеющие составы, приведенные в таблице 3, также были выполнены в целях сравнения. Образец, используемый для сравнения, представлял собой лист стали марки 304L, имеющийся в продаже.
[0040] Химические составы из таблицы 3 были вакуумно расплавлены в слитки, горячекатаны при температуре 2250°F (1232°C), очищены от окалины и холоднокатаны на 60%. Холоднокатаный материал имел окончательный отжиг при 1825°F (996°C) с последующим окончательным удалением окалины.
ПРИМЕР 3
[0041] Сравнительные исследования, проведенные на упомянутых выше вакуумных расплавах из примера 2 (определенных по их идентификационным номерам), были испытаны химически погружением в соляную кислоту, серную кислоту, гипохлорит натрия и уксусную кислоту.
[0042] 1% раствор соляной кислоты. Как показано на фиг. 2, химический тест на погружение показал благоприятное воздействие никеля в восстанавливающей кислой хлоридной среде, такой как соляная кислота. Сталь марки 304L превзошла все химические составы, изученные в этой среде. Добавление хрома привело к снижению общей скорости коррозии, и присутствие меди и молибдена привело к дальнейшему снижению скорости коррозии, но воздействие одной лишь меди были минимальным, как показано на графике линией, обозначенной как Fe21CrXCu0.25Mo, на фиг. 2. Такое поведение подтверждает преимущества добавок никеля для условий эксплуатации, таких, как те, что описаны ниже.
[0043] 5% раствор серной кислоты. Как показано на фиг. 3, в тесте погружения, состоящем из восстанавливающей кислоты, которая является высокопроцентным сульфатом, сплавы с содержанием хрома между 18 и 21% ведут себя аналогично. Добавление молибдена и меди существенно снизило общую скорость коррозии. При оценке воздействия одной лишь меди на скорость коррозии (как показано на фиг. 3 линией, обозначенной как Fe21CrXCu0,25Mo), оказалось, что существует прямая взаимозависимость, при которой более высокое содержание меди приводит к более низкой скорости коррозии. При содержании меди 0,75%) общая скорость коррозии стала выравниваться и была в пределах 2 мм/год, что характерно для стали марки 304L. Содержание молибдена на уровне 0,25% имеет большое влияние на скорость коррозии в серной кислоте. Однако резкое снижение скорости было также объяснено присутствием меди. Хотя сплавы из примера 2 имеют скорость коррозии не ниже чем у стали марки 304L, они показали улучшенную и сравнимую коррозионную устойчивость в условиях восстанавливающей серной кислоты.
[0044] Уксусная кислота и гипохлорит натрия. При погружении в кислую среду, состоящую из уксусной кислоты и 5-процентного раствора гипохлорита натрия, коррозия была сравнима с таковой у стали марки 304L. Скорости коррозии были очень низкими, и при добавлении меди не удалось обнаружить значимой тенденции в отношении коррозии. Все исследуемые химические составы из примера 2, имеющие уровень хрома выше 20%, были в пределах показателя 1 мм/год стали марки 304L.
ПРИМЕР 4
[0045] Электрохимические оценки, включающие диаграммы коррозионного поведения (ДКП) и исследования циклической поляризации, были выполнены и сравнивались с поведением стали марки 304L.
[0046] Диаграммы, характеризующие коррозию, были получены для химических составов, полученных в условиях вакуумной плавки в примере 2 и для стали марки 304L в 3,5% хлориде натрия с целью изучения воздействия меди на анодное растворение. Анодный выступ представляет собой электрохимическое растворение, которое имеет место на поверхности материала до достижения пассивированного состояния. Как показано на фиг. 4, добавление по меньшей мере 0,25% молибдена и минимум примерно 0,40% меди уменьшает плотность тока во время анодного растворения ниже измеренного значения для стали марки 304L. Следует также отметить, что максимальная добавка меди, которая позволяет плотности анодного тока оставаться ниже измеренной для стали марки 304L, составляет примерно 0,85%, как показано на графике линии, определенной как Fe21CrXCu.25Mo на фиг. 4. Это показывает, что небольшое количество регулируемой добавки меди, находящейся в присутствии 21%) хрома и 0,25% молибдена, действительно замедляет скорость анодного растворения в разбавленных хлоридах, но существует оптимальное количество для того, чтобы поддерживать скорость медленнее показанной для стали марки 304L.
[0047] Методом циклической поляризации были получены поляризационные кривые для экспериментальных химических составов из примера 2 и для стали марки 304L в 3,5% растворе хлорида натрия. Эти кривые характеризуют свойства ферритной нержавеющей стали при анодной поляризации, включая область активного анодного растворения, область пассивации, область транспассивации и область пробоя пассивирующего слоя. Кроме того, обратный ход этих поляризационных кривых позволяет определить репассивациопный потенциал.
[0048] Потенциал пробоя, показанный на вышеупомянутых кривых циклической поляризации, был задокументирован, как показано на фиг. 5 и на фиг. 6, и оценен для измерения воздействия добавок меди, если таковые имеются. Потенциал пробоя был определен как потенциал, при котором ток начинает воспроизводимо проходить через пробитый пассивирующий слой, и имеет место активная инициация точечной коррозии.
[0049] Так же, как и в случае со скоростью растворения, добавление меди, как показано на фиг. 5 и 6 линией, обозначенной Fe21CrXCu.25Mo, по-видимому, укрепляет пассивирующий слой и показывает, что существует оптимальное количество, необходимое для достижения максимальной эффективности меди по отношению к инициации точечной коррозии. Диапазон максимальной прочности пассивирующего слоя, как было обнаружено, составил 0,5-0,75% меди в присутствии 0,25% молибдена и 21% хрома. Эта тенденция поведения была подтверждена ДКП, полученными в ходе изучения анодного растворения, о котором говорилось выше, хотя из-за различий в скорости сбора данных, значения сдвинулись в более низкую область.
[0050] При оценке репассивационного поведения химических составов, расплавленных в вакууме, в примере 2 было показано, что содержание хрома, равное 21%, и небольшая добавка молибдена могут максимизировать репассивационную реакцию. Зависимость репассивационного потенциала от содержания меди, по-видимому, становилась неблагоприятной, по мере увеличения содержания меди, как показано на фиг. 7 и фиг. 8 линией, обозначенной как Fe21CrXCu.25Mo. До тех пор, пока уровень хрома составлял примерно 21%, и присутствовало небольшое количество молибдена, исследованные химические составы из примеров 2 могли достичь репассивационного потенциала, который был выше, чем у стали марки 304L, как показано на фиг. 7 и фиг. 8.
ПРИМЕР 5
Ферритную нержавеющую сталь состава, приведенного ниже в таблице 4 (ID 92, пример 2), сравнивали со сталью марки 304L с составом, приведенным в таблице 4.
[0052] Два материала продемонстрировали следующие механические свойства, приведенные в таблице 5, когда тестировались в соответствии со стандартными ASTM-тестами:
Материал из примера 2, ID 92, демонстрирует большее электрохимическое сопротивление, более высокий потенциал пробоя и более высокий репассивационный потенциал, чем у сравниваемой стали марки 304L, как показано на фиг. 9 и фиг. 10.
Следует понимать, что в настоящем изобретении могут быть сделаны различные модификации без отклонения от его сущности и объема. Таким образом, рамки настоящего изобретения должны быть определены из приложенной формулы изобретения.
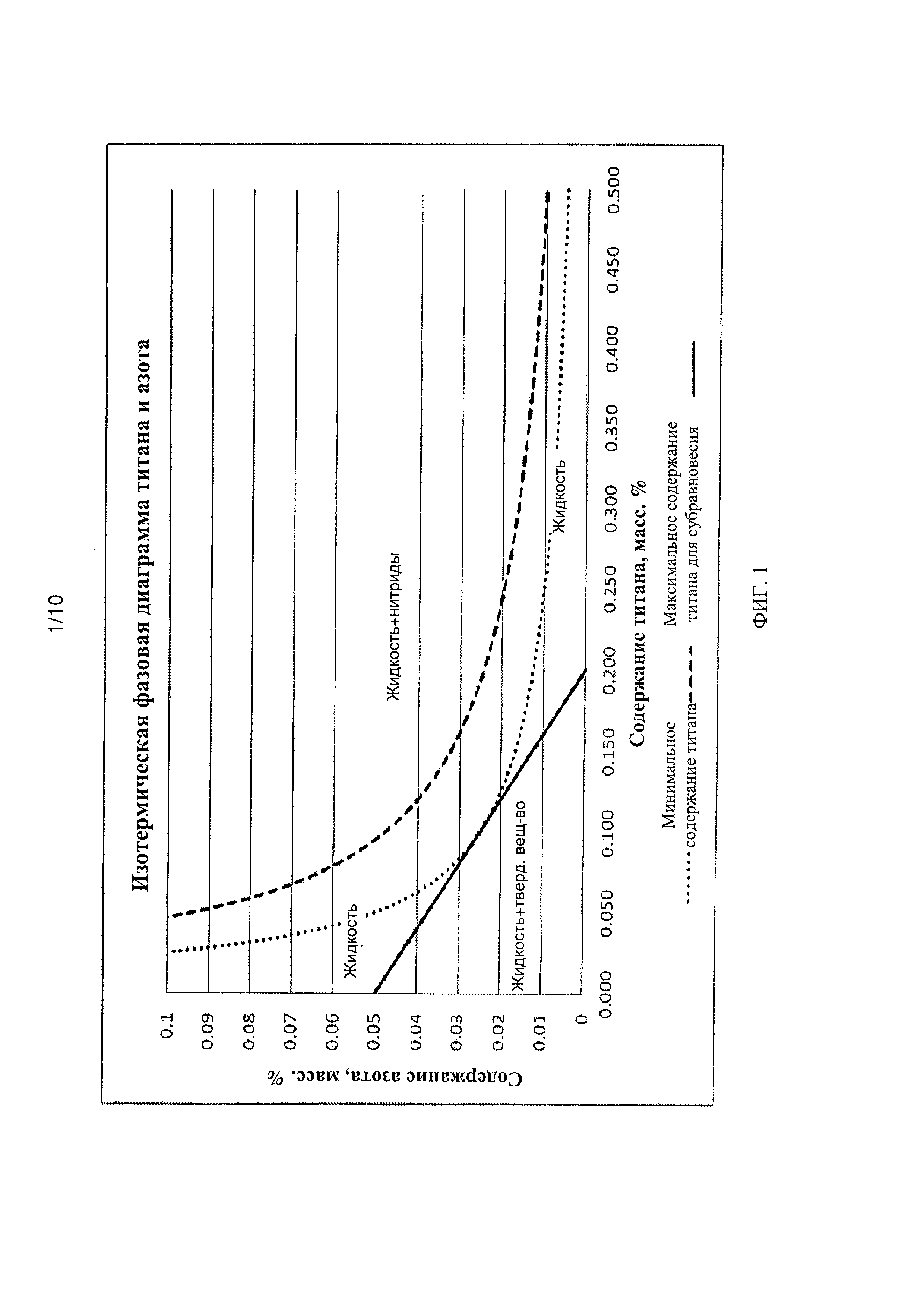
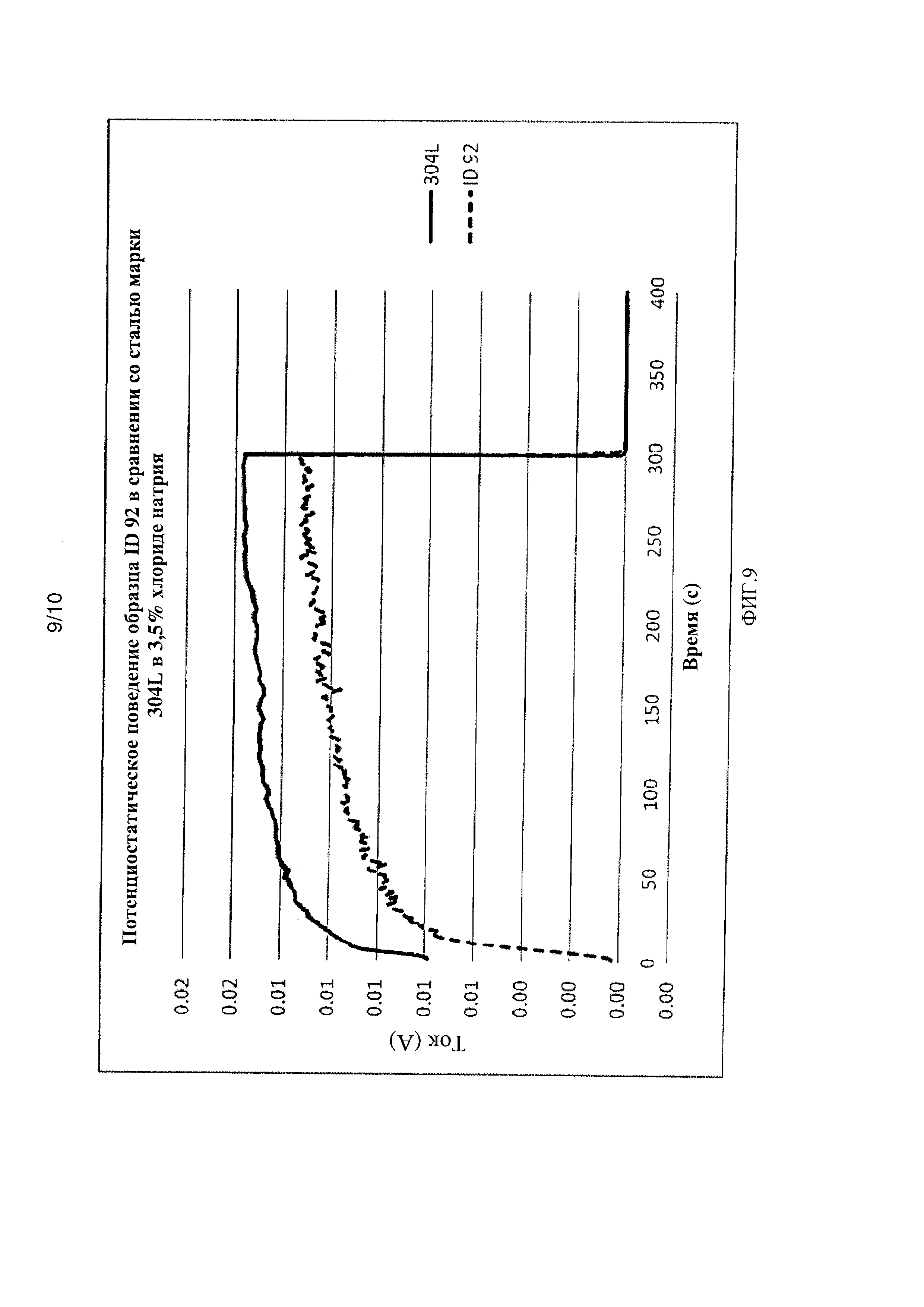
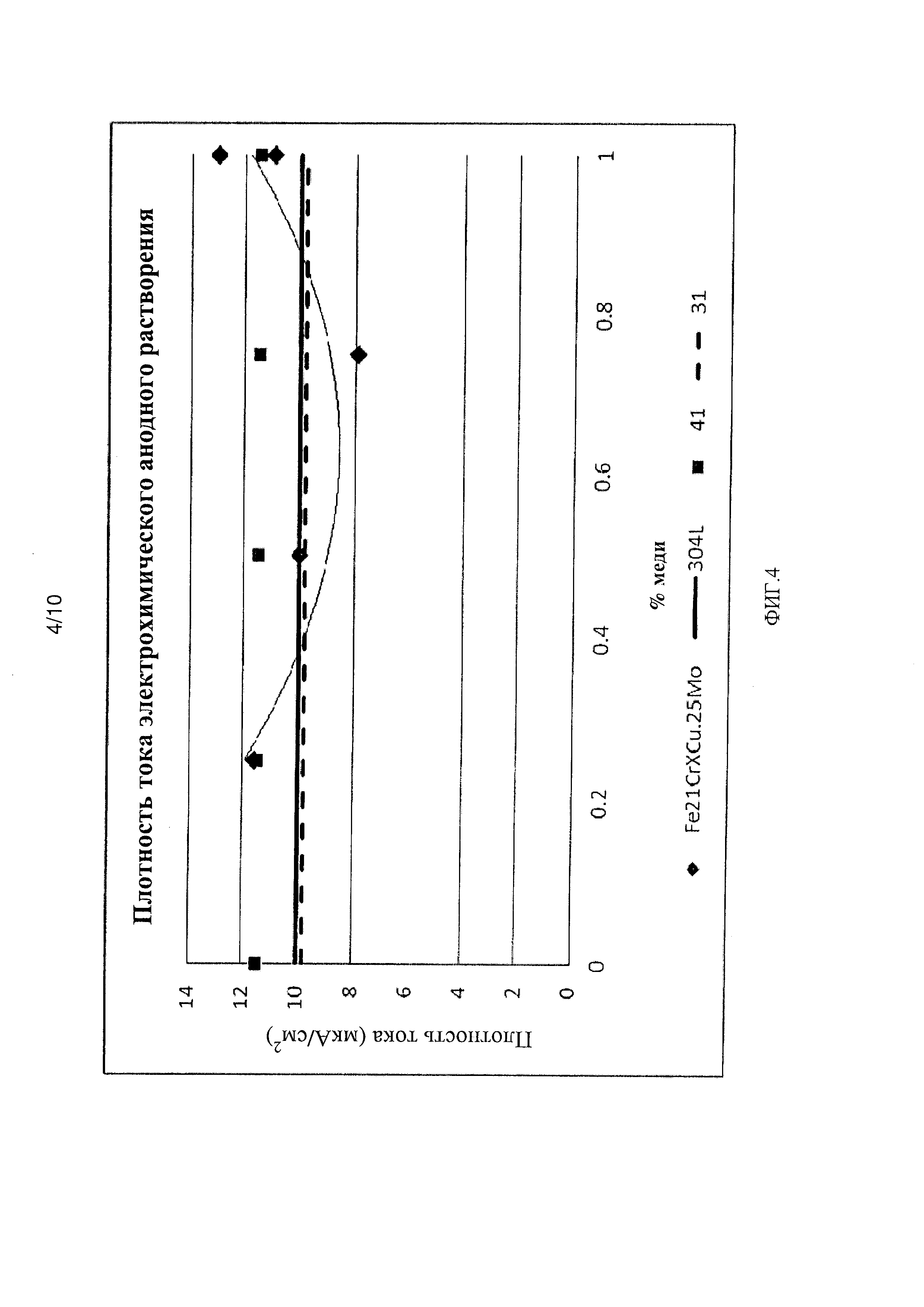
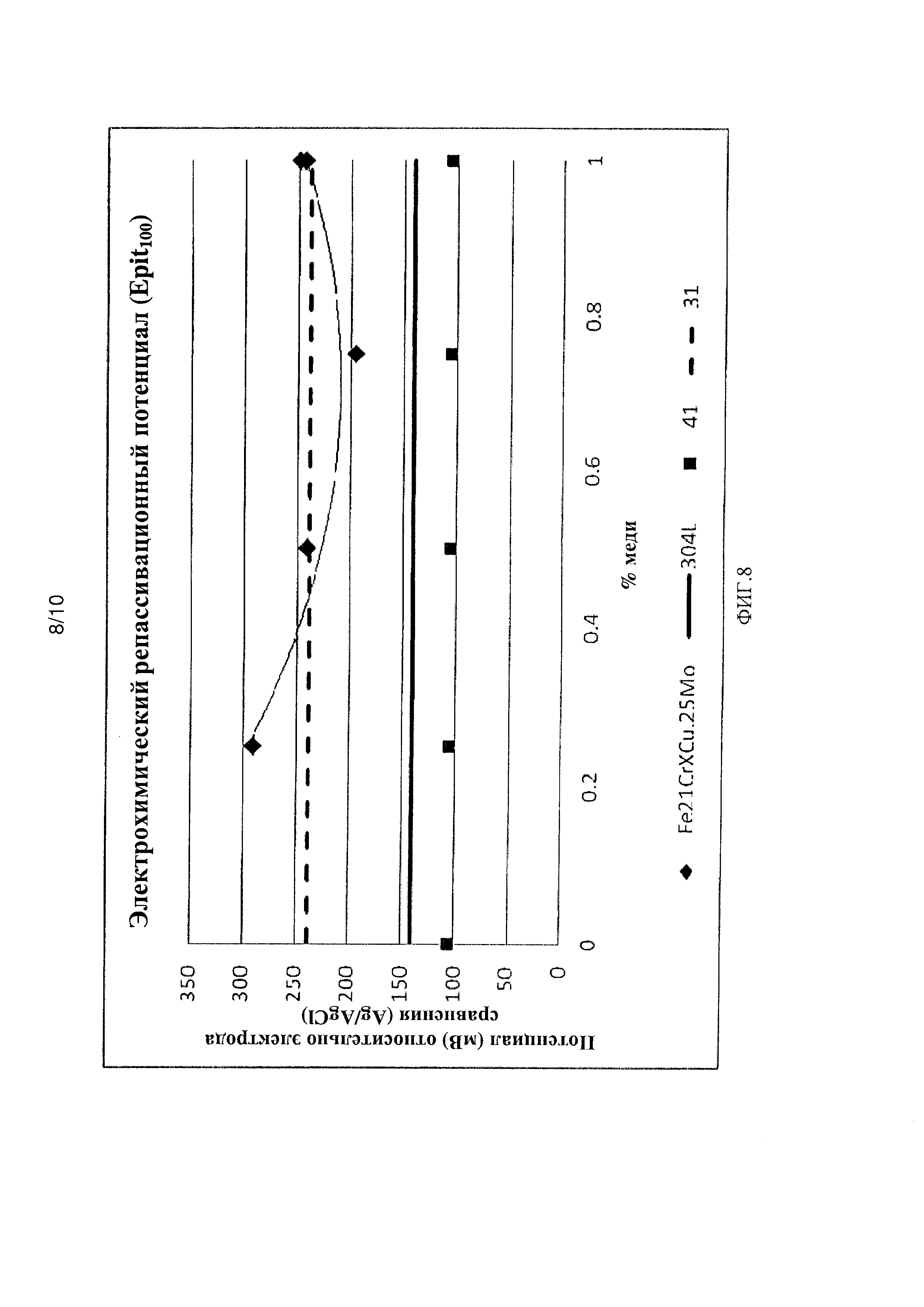
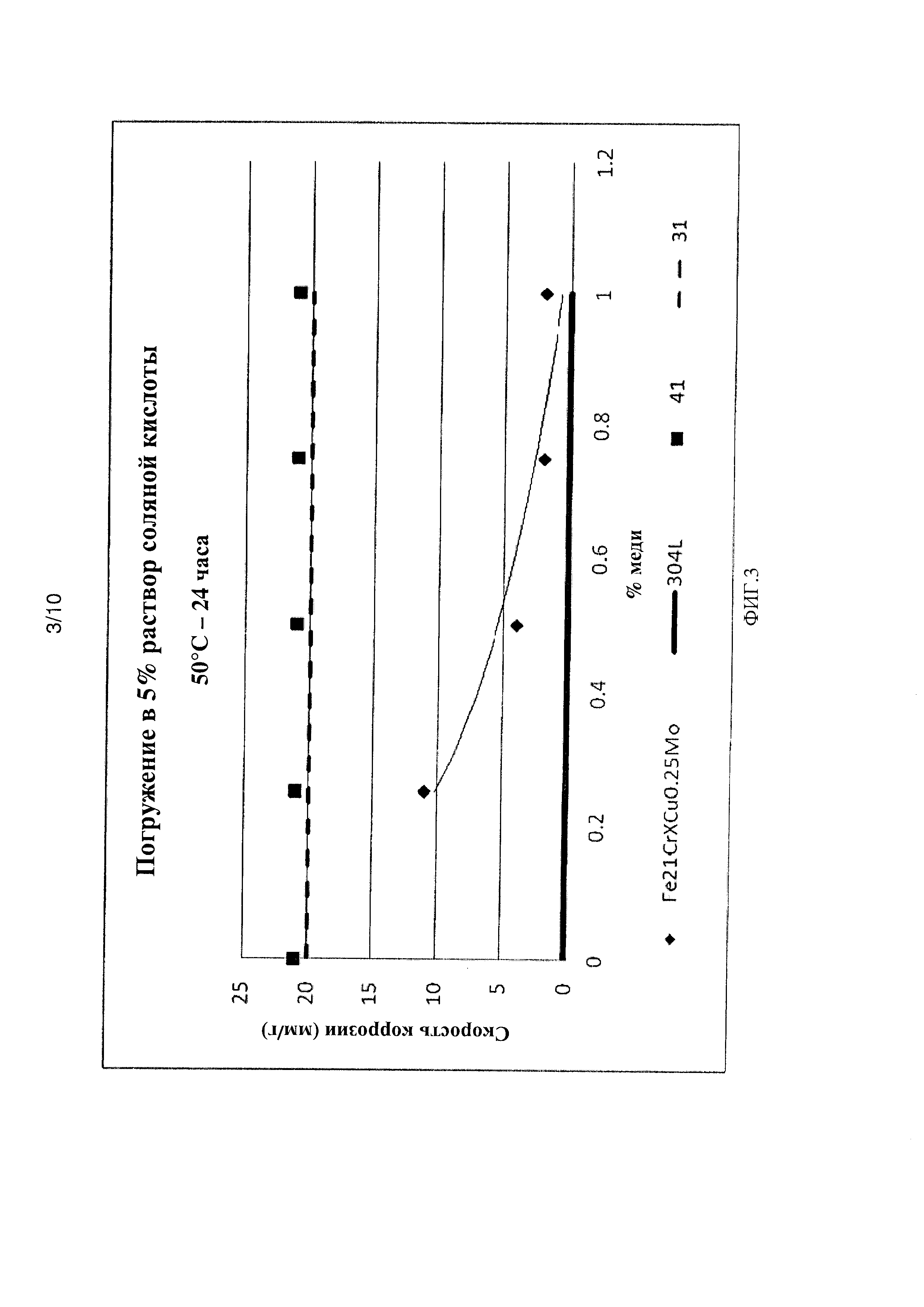
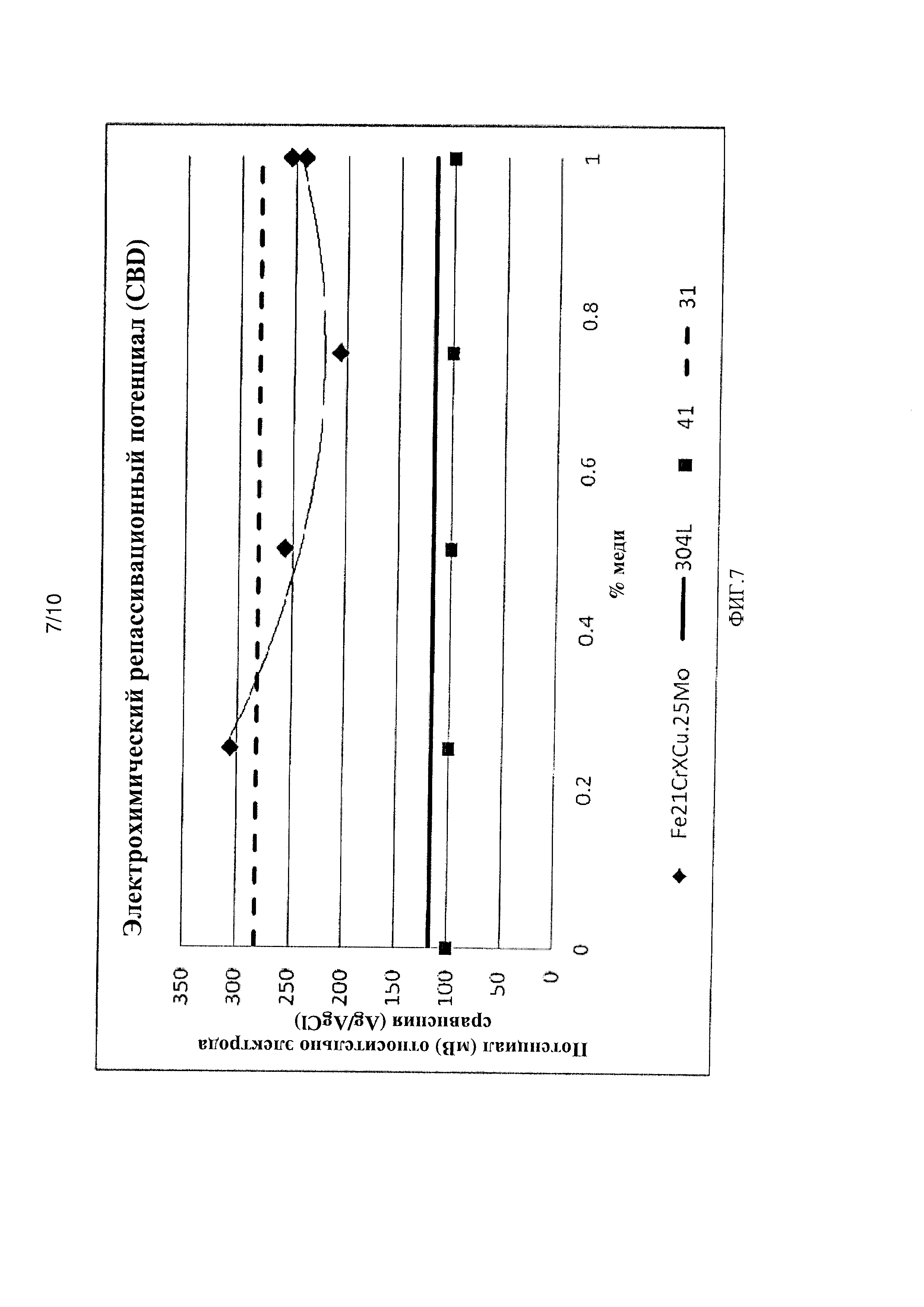
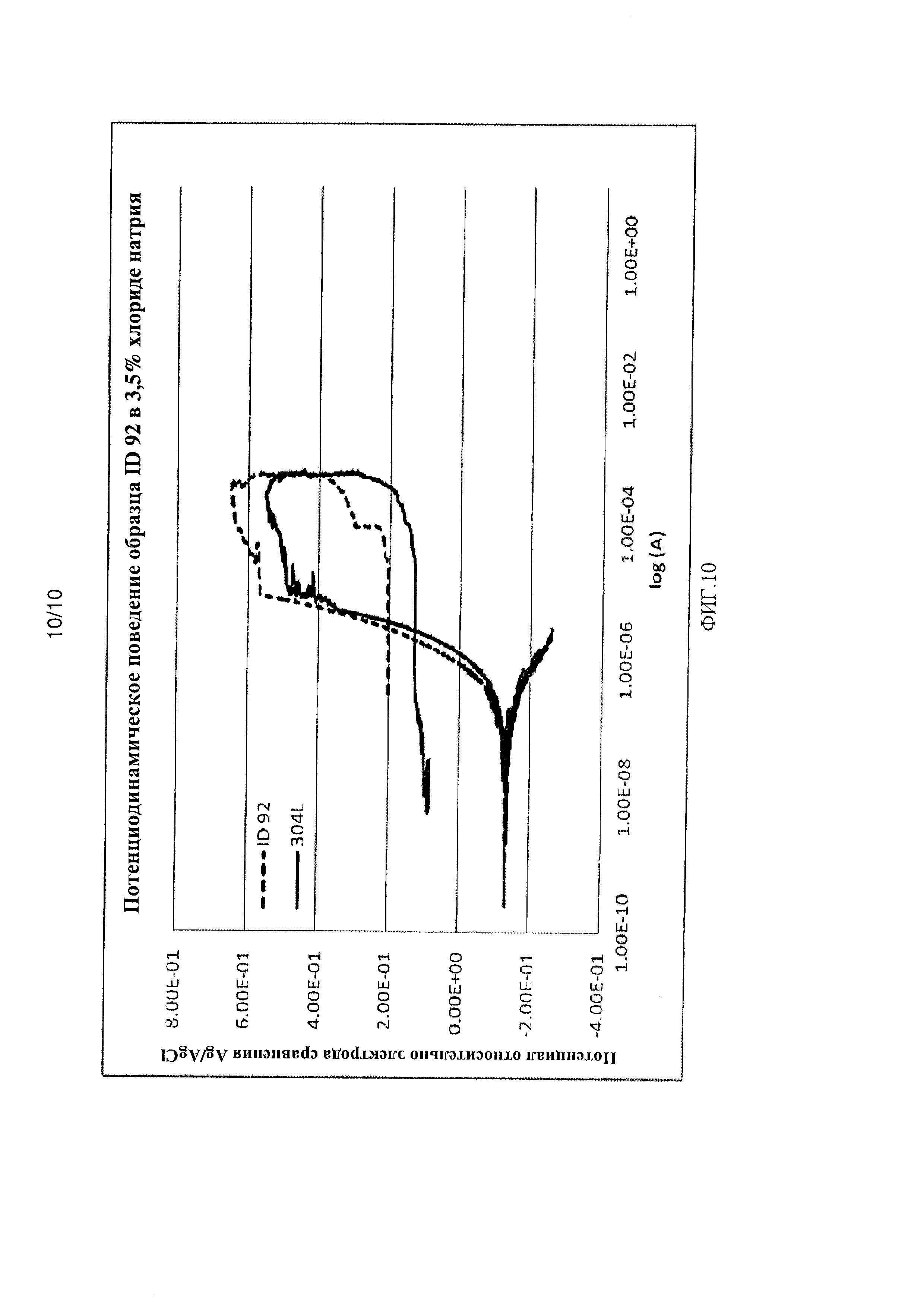
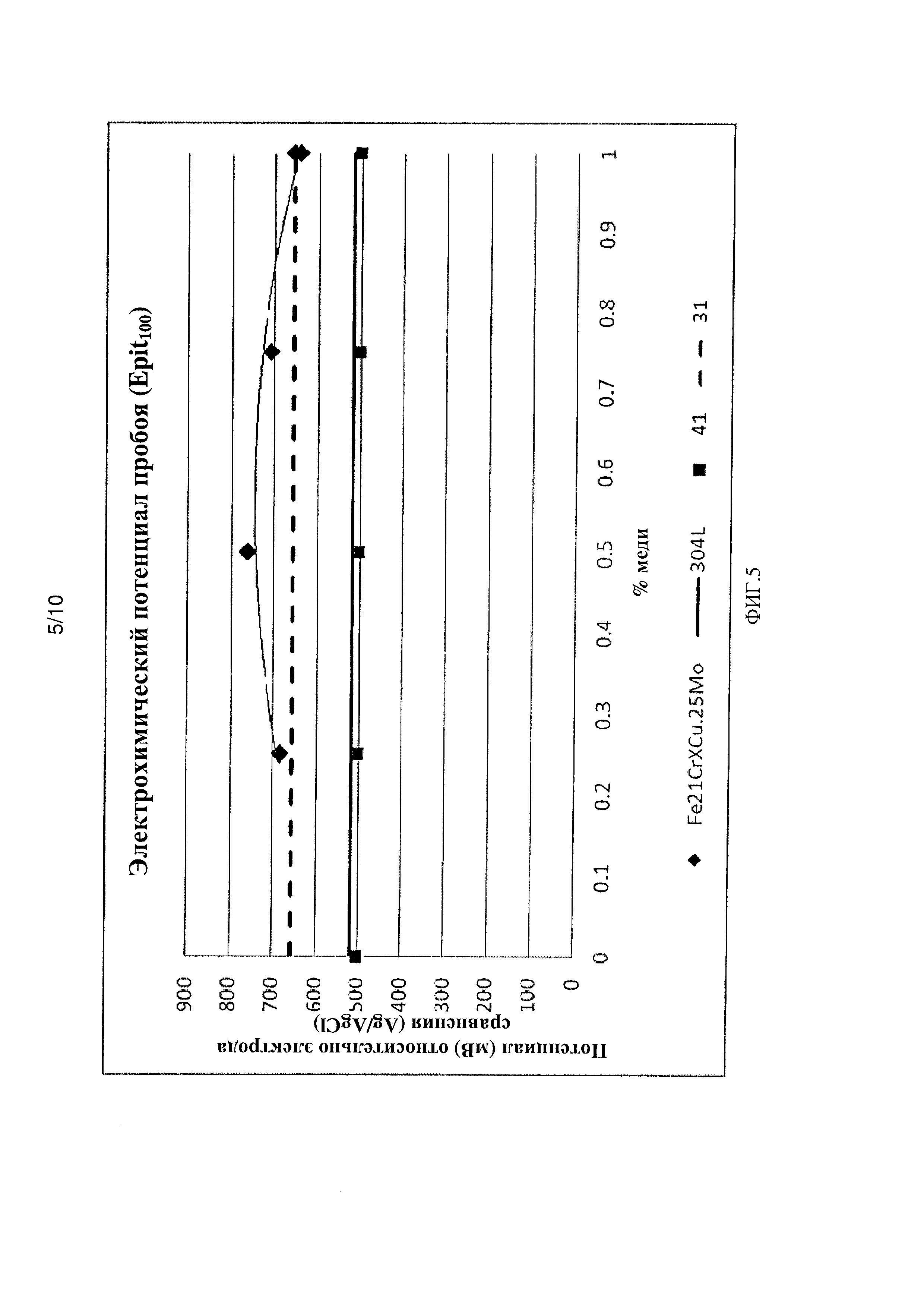
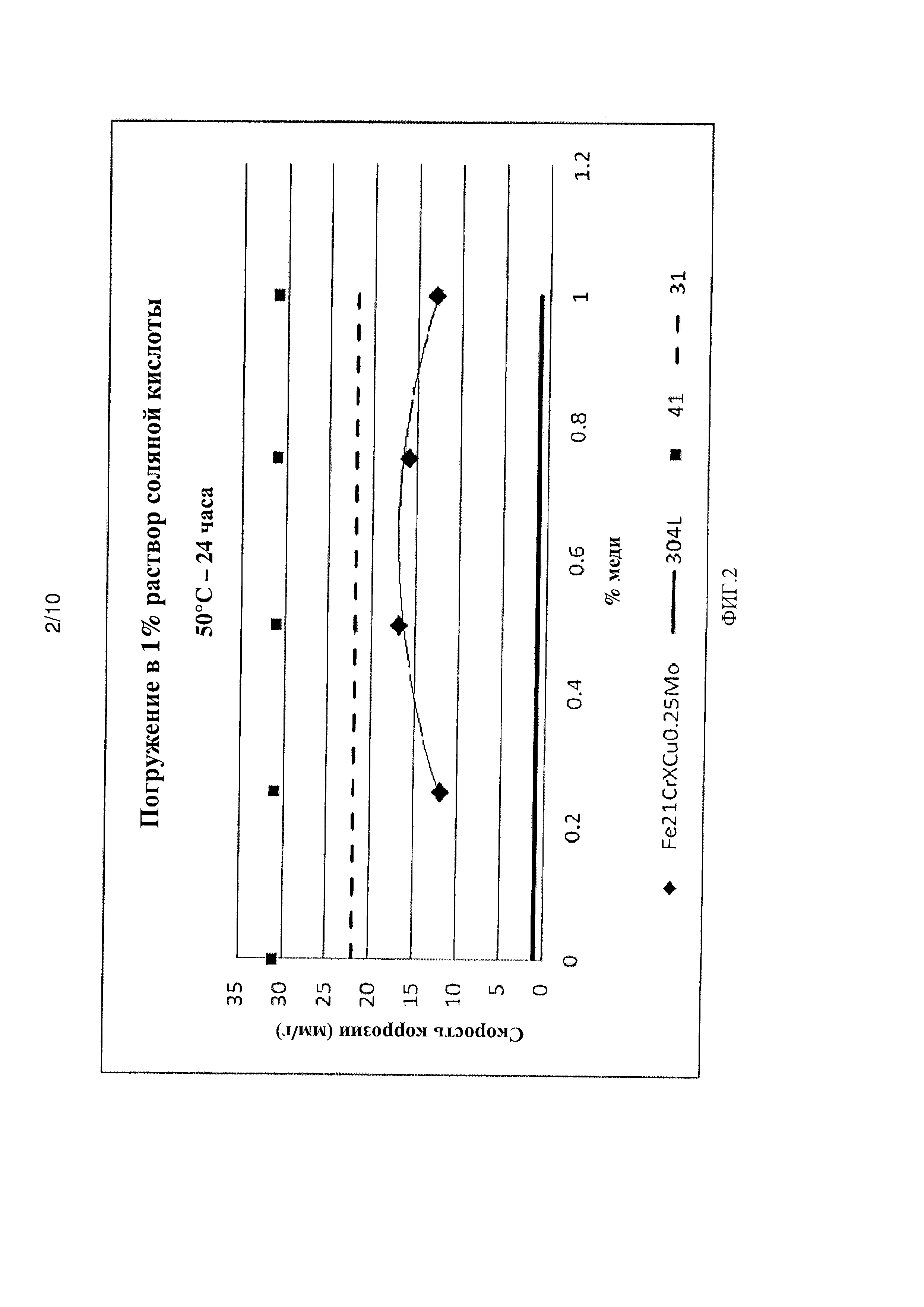

edrid.ru
Ферритная нержавеющая сталь | Банк патентов
Изобретение относится к металлургии, в частности к сталям для трубосварочного производства, продукция которого применима в пищевой, химической, сельскохозяйственной и автомобильных отраслях, например при изготовлении гильз доильных стаканов и деталей глушителя автомобилей. Заявлена ферритная нержавеющая сталь, содержащая компоненты в следующем соотношении в мас.%: углерод 0,01-0,05; кремний 0,1-0,8; марганец 0,1-0,8; хром 13,0-18,0; титан 0,05-0,5; алюминий 0,01-0,1; кальций 0,001-0,02; цирконий 0,005-0,035; азот 0,001-0,025; бор 0,0003-0,005; барий 0,001-0,1; магний 0,001-0,02; РЗМ 0,001-0,05; никель 0,1-0,95; ванадий 0,01-0,35; молибден 0,01-0,5; вольфрам 0,01-0,3; железо – остальное. Техническим результатом изобретения является повышение пластичности и предела текучести стали и повышение производительности сварки труб. 2 табл.
Изобретение относится к области металлургии, в частности к ферритным нержавеющим сталям, и может быть использовано в трубосварочном производстве, продукция которого применима в пищевой, химической, сельскохозяйственной и автомобильных отраслях, например при изготовлении гильз доильных стаканов и деталей глушителя автомобилей,
Известны составы ферритных нержавеющих сталей, используемых как в листовом, так и в трубосварочном производстве.
В настоящее время существует проблема, в том, что все известные ферритные нержавеющие стали из-за высокого содержания углерода и незначительного содержания легирующих элементов недостаточно пластичны и имеют низкий предел текучести. Использовать их в трубосварочном производстве, например при изготовлении из сварных труб гильз доильных стаканов и деталей глушителя автомобилей, практически невозможно, так как при сферическом обжиме с утонением и гибкой таких труб идет повышенный брак.
Известна ферритная нержавеющая сталь 08Х18Т1, ГОСТ 5632-72, содержащая в мас.%:
углерод не более 0,8
кремний не более 0,8
марганец не более 0,7
хром не более 17,0-19,0
титан 0,6-1,0
Примеси:
сера не более 0,025
Фосфор не более 0,035
железо - остальное
Эта сталь используется для производства сварных труб сахарной и автомобильной промышленности.
Однако известная сталь имеет ряд недостатков: склонность к росту зерна феррита при сварке, пониженную вязкость и пластичность. Известная сталь легирована одним стабилизирующим элементом титаном (0,6-1,0%). Содержание титана, необходимое для стабилизации, не должно быть превышено, иначе образуется оксидная пленка, ухудшающая вязкость, качество поверхности и деформируемость стали при сварке труб. При содержании титана более 0,75% образуются титаниды, вызывающие охрупчивание стали в результате дисперсионного твердения при термической обработке.
Кроме того, плены титана, совместно с другими неметаллическими включениями, образуют на границе зерен феррита крупные паукообразные включения, сильно понижающие пластичность стали, а также способствующие получению трещин и порезов при производстве из сварных труб методом сферического обжима с утонением гильз доильных стаканов и при гибке деталей глушителя автомобиля.
За прототип выбрана нержавеющая сталь (см. патент RU №2017856, кл. С 22 С 38/32, 1994 г. Б.15), содержащая следующие компоненты, в мас.%:
углерод 0,01-0,08
кремний 0,1-0,8
марганец 0,1-0,8
хром 13,0-18,0
титан 0,05-0,5
алюминий 0,01-0,1
кальций 0,001-0,02
цирконий 0,005-0,035
азот 0,001-0,025
бор 0,0003-0,005
барий 0,001-0,1
магний 0,001-0,02
РЗМ 0,001-0,05
железо остальное
Однако предложенный состав известной стали предназначен для получения листового проката с хорошей штампуемостью, повышенной трещиноустойчивостью и полируемостью при вторичной деформации после глубокой вытяжки изделий. Использование этого состава стали для производства сварных труб механизированной аргонодуговой сваркой двухдуговым плазмотроном и их последующей обработки методом сферического обжима с утонением и гибкой, в частности для гильз доильного стакана и для деталей глушителя автомобиля, осуществлять практически невозможно из-за повышенного брака по трещинам, порезу и т.д.
Микроструктура стали состоит из зерен феррита, карбидов и карбонитридов титана и циркония и карбида хрома типа Сr 23С6, располагающегося в основном по границам зерен. Следует отметить, что когда карбиды хрома в известной стали образуют при первичной кристаллизации и термической обработке карбидную сетку по границам зерен, то происходит резкое снижение пластичности и предела текучести стали. Величина зерна феррита - основного металла сварных труб, определяемая ее первичной кристаллизацией, должна быть по нормам не крупнее пятого бала по ГОСТ 5639-82, а в зоне сварки не крупнее второго бала, но на практике при сварке труб из-за низкой скорости сварки величина зерна в зоне сварки была один балл, что приводило к повышению брака при производстве деталей доильного оборудования и глушителей автомобилей, а также к снижению качества труб при испытаниях на сплющивание и раздачу конусом.
Кроме этого, известная сталь, имея низкую прочность, текучесть и пластичность, не может сопротивляться возникающим напряжениям при обжиме с утонением и гибкой, что заставляло применять для вышеуказанных изделий дорогостоящую хромоникелевую сталь 12Х18Н10Т. При этом состав известной стали не позволял иметь при сварке труб высокий тепловой эффект мощности сварочной дуги и повышать скорость сварки труб 42×2 мм более 0,8 м/мин, а труб 43×1,5 мм более 1,5 м/мин из-за непровара, трещин и других дефектов, что отрицательно сказывается на производительности.
Задача предлагаемого изобретения состояла в разработке состава ферритной нержавеющей стали, позволяющего улучшить качество сварных труб путем повышения пластичности и предела текучести, а также повысить производительность сварки труб.
Поставленная задача достигается тем, что в известный состав ферритной нержавеющей стали, содержащей углерод, кремний, марганец, хром, титан, алюминий, кальций, цирконий, азот, бор, барий, магний, РЗМ и железо, дополнительно вводят никель, ванадий, молибден и вольфрам при следующем соотношении компонентов, в мас.%:
углерод 0,01-0,05
кремний 0,1-0,8
марганец 0,1-0,8
хром 13,0-18,0
титан 0,05-0,5
алюминий 0,01-0,1
кальций 0,001-0,02
цирконий 0,005-0,035
азот 0,001-0,025
бор 0,0003-0,005
барий 0,001-0,1
магний 0,001-0,02
РЗМ 0,001-0,05
никель 0,1-0,95
ванадий 0,01-0,35
молибден 0,01-0,5
вольфрам 0,01-0,3
железо остальное
Сталь может содержать примеси, в мас.%: сера до 0,25, фосфор до 0,35 и медь до 0,3.
Сущность изобретения состоит в следующем.
В состав предлагаемой стали с целью улучшения качества сварки труб путем повышения их прочностных и пластичных свойств введено 0,1-0,95% никеля. Он образует твердый раствор с ферритом, изменяя кристаллическую решетку феррита и упрочняя междуатомные связи. Никель в ферритной нержавеющей стали в вышеуказанных количествах способствует появлению γ-α-превращений. Оно протекает не до конца, что тем не менее дает заметное повышение предела текучести, не снижая пластичности. Превышение содержания никеля более 0,95% приводит к появлению аустенита в структуре стали, что неблагоприятно сказывается на качестве труб.
Дополнительное введение 0,01-0,35% ванадия в предлагаемую сталь основано на образование карбидов, карбонитридов и нитридов, которые выделяются в высокодисперсном состоянии и равномерно располагаются внутри зерен и упрочняют сталь. Ванадий повышает точку Ас 3 стали, что благоприятно сказывается при сварке труб. Ванадий измельчает зерно феррита основного металла и сварочного шва, способствуя получению стали с мелкозернистой структурой при первичной кристаллизации, что увеличивает сопротивление стали сдвиговой деформацией при обжиме с утонением и гибке сварных труб при производстве деталей доильного оборудования и глушителей автомобиля.
Введение в сталь ванадия ниже 0,01% не приводит к заметному повышению свойств стали, более 0,35% ухудшает релаксационную стойкость стали и увеличивает загрязнение стали нитридами ванадия.
Дополнительное введение в состав предлагаемой стали 0,01-0,5% молибдена и 0,01-0,3% вольфрама содействует образованию карбидных и карбонитридных фаз, способствующих измельчению ферритного зерна. Молибден и вольфрам, растворяясь в феррите, увеличивает энергию межатомных связей и сопротивление упругой деформации решетки твердого раствора феррита, упрочняют его и повышают термическую стойкость. Свойство феррита, дополнительно упрочненного молибденом и вольфрамом, не зависят от того, как охлаждалась сталь - быстро или медленно, что очень полезно при сварке труб. Одновременно молибден и вольфрам, входя в состав упрочняющей карбидной фазы типа (Cr, Mo, W, V, Fe, Si)23С6, повышают прочность межатомных связей в ней, снижают ее способность к коагуляции и тормозят образование карбидной сетки, что снижает хрупкость и повышает пластичность сварных труб.
Кроме этого в предлагаемой стали снижено содержание основного элемента, влияющего на качество сварки труб - углерода с 0,08% до 0,05%, что позволило также уменьшить склонность стали к охрупчиванию в сварных соединениях. Общепринятое содержание углерода до 0,08% оказывает неблагоприятное действие при сварке труб, так как он расширяет интервал кристаллизации и усиливает склонность стали к образованию горячих и холодных трещин. Благодаря снижению содержания углерода уменьшается интенсивность образования карбидной сетки хромистого карбида типа (Cr, Mi, Mo, W, Fe, Si)23С6 и его количества в твердом растворе феррита и по границам зерен вследствие его растворения нитридами титана, циркония и ванадия, что повышает качество металла и улучшает свариваемость труб.
Дополнительное комплексное введение никеля, ванадия, молибдена и вольфрама и предлагаемое соотношение компонентов предлагаемой ферритной нержавеющей стали способствуют повышению качества сварных труб за счет:
- упрочнения твердого раствора феррита за счет увеличения параметра решетки легированного феррита с 2,86Å до 2,94 Å;
- образования сложных дисперсных карбидов и карбонитридов, содержащих, кроме хрома, титана, циркония, еще ванадий, вольфрам и молибден;
- создания условия для развития преимущественно внутризеренных сегрегации и выделения высокодисперсных карбидов, карбонитридов и нитридов округлой формы как в теле зерна, так и по границам при охлаждении стали от температуры сварки и при термической обработке;
- затруднения коагуляции упрочняющих карбидных и карбонитридных фаз, благодаря уменьшению диффузионной подвижности и снижению коэффициентов диффузии и самодиффузии;
- получения умельченной структуры основного металла, металла сварочного шва и околошовной зоны после сварки труб за счет дополнительного легирования и увеличения скорости сварки;
- замедления скорости разупрочнения стали, что способствует уменьшению глубины и ширины зоны разупрочнению после сварки труб.
Следует отметить, что совместное введение в предлагаемую ферритную нержавеющую сталь никеля, ванадия, молибдена и вольфрама в пределах, указанных выше, а также снижение содержания углерода до 0,05% дало возможность увеличить скорость сварки труб в 1,5 раза и повысить тепловой эффект мощности сварочной дуги за счет увеличения силы тока дуги. Это позволило уменьшить объем поверхности расплава металла и снизить неоднородность металла сварочного шва. При этом в швах отсутствуют дефекты, зерна феррита структуры шва ориентированы по следам дендритной структуры, причем размер зерна значительно уменьшается.
Пример получения вещества
В 000 НПИФ “Сплав” в производственных условиях изготавливают ферритную нержавеющую сталь, содержащую в мас.%:
хром металлический ГОСТ 5905-67 - 16,5
ферросилиций ГОСТ 1415-70 - 0,5
ферромарганец ГОСТ 4755-70 - 0,5
ферротитан ГОСТ 4761-67 - 0,6
азотированный марганец ТУ 14-5-59-75 - 0,1
электродный бой - 0,02
алюминий ГОСТ 11070-74 - 0,1
ферросиликобарий ТУ 14-5-160-84 - 0,05
никель Н-1 ГОСТ 849-70 - 0,5
феррованадий ГОСТ 4760-84 - 0,2
ферромолибден ГОСТ 4759-79 - 0,3
ферровольфрам ГОСТ 17293-71 - 0,15
лигатура РЗМ ФСЗО ТУ 14-5-136-8 - 0,15
силикокальций ГОСТ 4762-71 - 0,03
ферробор ФБ-В ТУ 14-5-14-72 - 0,01
ферросиликоцирконий ФСЦР-50 ТУ 14-5-3-77 - 0,05
ферросиликомагниевый сплав ТУ 14-05-134-86 - 0,03
армко–железо - остальное
Выплавку стали производили в индукционной печи с основной футеровкой. При этом армко-железо, хром, электродный бой, азотированный марганец, никель, ферромолибден и ферровольфрам вводили непосредственно в завалку вместе со шлаковой смесью, состоящей из свежеобожженной извести, плавикового штата и магнезита.
После полного расплавления вводили ферросилиций, ферромарганец, алюминий, ферротитан. При нагреве металла до температуры 1610°С перед разливкой вводили силикокальций, феррованадий, ферросиликоцирконий, лигатуру РЗМ и ферросиликомагниевый сплав (по известной технологии).
Аналогично были приготовлены еще четыре состава предлагаемой стали с различным содержанием компонентов и составов (таблица 1).
Металл разливали сифоном в изложницы. Дальнейший передел слитков на холоднокатанный рулонный лист проводили на заводе “Запорожсталь” по принятой для ферритных нержавеющих сталей технологии. Рулоны на сварку труб поставляли с поверхностью в состоянии прокатки, термообработки и травления. Режим термической обработки: закалка - 850°С, охлаждение в воде.
В таблице 1 представлены составы испытываемых ферритных нержавеющих сталей.
Таблица 1 | |||||
Компоненты | Содержание в мас % | ||||
I | II | III | IV | V | |
Углерод | 0,008 | 0,01 | 0,03 | 0,05 | 0,06 |
Кремний | 0,08 | 0,1 | 0,4 | 0,8 | 0,9 |
Марганец | 0,08 | 0,1 | 0,4 | 0,8 | 0,85 |
Хром | 12,5 | 13,0 | 15,5 | 18,0 | 18,5 |
Титан | 0,04 | 0,05 | 0,3 | 0,5 | 0,55 |
Алюминий | 0,008 | 0,01 | 0,05 | 0,1 | 0,12 |
Кальций | 0,0008 | 0,001 | 0,01 | 0,02 | 0,022 |
Цирконий | 0,036 | 0,035 | 0,02 | 0,005 | 0,004 |
Азот | 0,0009 | 0,001 | 0,012 | 0,025 | 0,026 |
Бор | 0,0002 | 0,0003 | 0,004 | 0,005 | 0,006 |
Барий | 0,0009 | 0,001 | 0,05 | 0,1 | 0,11 |
Магний | 0,0009 | 0,001 | 0,01 | 0,02 | 0,021 |
РЗМ | 0,0009 | 0,001 | 0,02 | 0,05 | 0,051 |
Никель | 0,09 | 0,1 | 0,46 | 0,95 | 0,96 |
Ванадий | 0,009 | 0,01 | 0,18 | 0,35 | 0,36 |
Молибден | 0,009 | 0,01 | 0,25 | 0,5 | 0,51 |
Вольфрам | 0,009 | 0,01 | 0,15 | 0,3 | 0,31 |
Сера | 0,01 | 0,012 | 0,018 | 0,025 | 0,026 |
Фосфор | 0,036 | 0,035 | 0,02 | 0,012 | 0,01 |
Медь | 0,001 | 0,01 | 0,15 | 0,3 | 0,31 |
Железо | остальное | остальное | остальное | остальное | остальное |
Сварку труб производили из холоднокатаной рулонной стали толщиной 1,5-2 мм на Новомосковском трубном заводе на стане АДС 20-76 в специальной камере аргонодуговой сваркой двухдуговым плазмотроном конструкции НИАТ. Перед сваркой осуществляли предварительный подогрев трубной заготовки через высокочастотный индуктор при температуре 200-300°С. Газовая защита при сварке и остывающего шва производили чистым аргоном. Первая дуга плазмотрона производила подогрев и подплавление кромок, а вторая проплавляла металл. Скорость сварки и ток первой и второй дуги плазмотрона фиксировался самопишущим прибором Н-340.
РЕЖИМЫ СВАРКИ | |||||
Диаметр и толщина трубы, мм | |||||
Скорость Сварки, м/мин | Сварочный ток, А | Напряжение, В | |||
1-й дуги | 2-й дуги | 1-й дуги | 2-й дуги | ||
42×2 | 0,8 | 70-100 | 100-130 | 15-18 | 16-20 |
42×2 | 1,2 | 100-130 | 120-160 | 15-18 | 17-20 |
43×1,5 | 1,5 | 90-120 | 120-150 | 15-18 | 17-20 |
43×1,5 | 2,0 | 100-130 | 150-180 | 15-18 | 17-20 |
Для снятия внутренних напряжений сварного шва в линии стана осуществляли 1-ю термообработку с помощью кольцевого многовиткового индуктора путем нагрева до температуры 800±20°С с последующим струйным водяным охлаждением. Вторую термическую обработку производили после калибровки и правки труб в проходных электропечах типа СРО 8/100 при температурах 810-860°С со скоростью движения труб 0,7 м/мин.
Механические испытания труб производили согласно ГОСТ 10006-80 и ГОСТ 8695-75. Механические свойства металла сварочного шва определяли на продольных плоских образцах с шириной рабочей части 1,2 мм. Процент увеличения наружного диаметра сварной трубы при испытании на раздачу конусом определяли по 10 образцам на патрубках длиной 100 мм путем ввода конусной оправки, имеющей наклон 1:10 или угол наклона, равный 60°, до появления трещины на розданной части патрубка.
Испытание сварного соединения на статический изгиб производили по ГОСТ 6996-66 на 5 образцах каждой плавки. Оно характеризуется углом изгиба, при котором в растянутой зоне образовывалась первая трещина, развивающаяся в процессе испытания.
В таблице 2 представлены характеристики показателей и свойства металла сварных труб.
Анализируя данные таблицы 2, приходим к выводу, что оптимальное содержание компонентов в ферритной нержавеющей стали для сварки труб при их последующей обработке методом сферического обжима с утонением и гибкой находится в пределах (мас.%):
Углерод 0,01-0,05
Кремний 0,1-0,8
Марганец 0,1-0,8
Хром 13,0-18,0
Титан 0,05-0,5
Алюминий 0,01-0,1
Кальций 0,001-0,02
Цирконий 0,005-0,035
Азот 0,001-0,025
Бор 0,0003-0,005
Барий 0,001-0,1
Магний 0,001-0,02
РЗМ 0,001-0,05
Никель 0,1-0,95
Ванадий 0,01-0,35
Молибден 0,01-0,5
Вольфрам 0,01-0,3
Железо остальное
При введении в состав предлагаемой ферритной нержавеющей стали меньше нижнего предела никеля, ванадия, молибдена и вольфрама не видно заметного эффекта в улучшении качества сварки труб, а также в повышении производительности их изготовления.
При составе компонентов стали в пределах оптимальных улучшается качество свариваемых труб, позволяющих повысить показатели по испытаниям на раздачу конусом, сплющивании и гибке, что позволило производить из них детали доильного оборудования и глушителя автомобилей методом сферического обжима с утонением и гибкой. Кроме этого, оптимальный состав позволил повысить производительность сварки труб, предел текучести и относительное удлинение. Если компоненты состава превышают допустимые пределы (см. таблицу 2), то мы имеем снижение свойств и харпактеристик показателей, так как они сами начинают способствовать увеличению сопротивления деформации и охрупчиванию.
Использование предлагаемого состава стали позволяет за счет улучшения качества сварных труб изготавливать детали доильного оборудования и глушителя автомобилей. Дополнительное преимущество имеем в повышении производительности изготовления сварных труб, предела текучести и относительного удлинения сварного шва.
Промышленное опробование сварных труб размером 42×2 мм из предлагаемого состава ферритной нержавеющей стали производили на Резекненском заводе доильного оборудования. Из труб методом сферического обжима с утонением по существующей на заводе серийной технологии изготовили 1500 штук гильз доильного стакана. Брак по трещинам составил всего 0,5%. При изготовлении этих деталей из хромоникелевой аустенитной стали 12Х18Н10Т брак достигал 5%.
Опробование изготовления 1000 деталей глушителя №2103-1201048/50 из труб размером 45×1,5 мм показало, что брак по гибке снижается на 30% по сравнению с производством этих деталей из стали 08Х18Т1.
Таким образом, использование предлагаемой ферритной нержавеющей стали в трубосварочном производстве, продукция которого идет для изготовления деталей доильного оборудования и автомобильной, сахарной и других отраслей промышленности, в том числе при производстве гильз доильных стаканов и деталей глушителя автомобилей, получаемых из сварных труб методом сферического обжима с утонением и гибкой, дает значительный экономический эффект и имеет большой спрос в вышеуказанных отраслях.
Формула изобретения
Ферритная нержавеющая сталь, содержащая углерод, кремний, марганец, хром, титан, алюминий, кальций, азот, цирконий, бор, магний, барий, РЗМ и железо, отличающаяся тем, что она дополнительно содержит никель, ванадий, молибден и вольфрам при следующем соотношении компонентов, мас.%:
углерод 0,01-0,05
кремний 0,1-0,8
марганец 0,1-0,8
хром 13,0-18,0
титан 0,05-0,5
алюминий 0,01-0,1
кальций 0,001-0,02
цирконий 0,005-0,035
азот 0,001-0,025
бор 0,0003-0,005
барий 0,001-0,1
магний 0,001-0,02
РЗМ 0,001-0,05
никель 0,1-0,95
ванадий 0,01-0,35
молибден 0,01-0,5
вольфрам 0,01-0,3
железо остальное
MM4A Досрочное прекращение действия патента из-за неуплаты в установленный срок пошлины заподдержание патента в силе
Дата прекращения действия патента: 06.09.2011
Дата публикации: 27.06.2012
bankpatentov.ru
#TITLE# || KOBELCO - KOBE STEEL, LTD. -
Сварка нержавеющей стали
1. Свойства нержавеющей стали
За счет добавления хрома (Cr) к железу (Fe), железо становится устойчивым к коррозии в атмосферных условиях. Когда содержание хрома повышается до 11-12% и более, устойчивость стали к коррозии становится примечательно высокой.
Поэтому сталь с таким высоким содержанием хрома получила название нержавеющей стали, при этом "нержавеющая" означает, что она не подвержена коррозии и ржавлению.
Высокая устойчивость нержавеющей стали к коррозии объясняется тем, что хром в ее составе окисляется в атмосферных условиях и формирует на поверхности стали защитную пленку, так называемую пассивную пленку.
В зависимости от условий окружающей среды, в которых будет использоваться нержавеющая сталь, содержание хрома увеличивают, и в состав стали также добавляется никель (Ni) и другие элементы.
Однако устойчивость к коррозии достигается в принципе за счет хрома, поэтому хром является важнейшим элементом в составе нержавеющей стали. Стандарт JIS определяет нержавеющую сталь как "легированную сталь, содержащую в своем составе хром или хром и никель для повышения устойчивости к коррозии, при этом содержание никеля составляет около 10,5% или более." Справочник по сварке AWS (Выпуск 4) также определяет нержавеющую сталь как "легированную сталь с определенным содержанием хрома не менее 11%, с наличием других легирующих добавок или без них."
Нержавеющая сталь обладает высокой жаропрочностью, а также устойчивостью к коррозии, что делает ее широко применимой в разных областях - от предметов домашнего обихода до химического оборудования, судов, вагонов, машин для переработки пищевых продуктов, строительных материалов и оборудования для АЭС, поэтому нержавеющая сталь играет важную роль в разных отраслях индустрии.

2. Разные типы нержавеющей стали
Нержавеющую сталь можно разделить на два класса - хромовую нержавеющую сталь и хромоникелевую нержавеющую сталь.
Эти два класса могут быть далее классифицированы на основании металлографических структур стали, как показано на Илл.1. Хромовая нержавеющая сталь может быть разделена на мартенситную и ферритную, а хромоникелевая нержавеющая сталь может быть разделена на аустенитную, аустенитно-ферритную (дуплексную) и дисперсионно-твердеющую сталь.

Илл. 1 Классификация нержавеющей стали
(1) Мартенситная нержавеющая сталь
Типичной маркой мартенситной нержавеющей стали согласно стандарту JIS является SUS410 (AISI 410) (См. Таблицу 1.).
Эта сталь содержит 13% хрома, и ее металлографическая структура при комнатной температуре является мартенситной, она твердая и хрупкая.
Хотя при использовании стали этой марки можно получить хорошие механические качества путем тепловой обработки (отпуска), она уступает другим маркам нержавеющей стали в устойчивости к коррозии из-за низкого содержания хрома.
Мартенситная нержавеющая сталь используется для лопастей турбин, клапанов и рессор, требующих высокой прочности, устойчивости к снашиванию и термостойкости.
Таблица 1. Требования к химическому составу мартенситных нержавеющих сталей (взято из JIS G 4305−1999 и дополнено AISI)*1 (%) Марка стали JIS (AISI) C Si Mn P S CrSUS410 (410) | Макс. 0.15 | Макс. 1.00 | Макс. 1.00 | Макс. 0.040 | Макс. 0.030 | 11.50~13.50 |
SUS410S (410S) | Макс. 0.08 | Макс. 1.00 | Макс. 1.00 | Макс. 0.040 | Макс. 0.030 | 11.50~13.50 |
(Примечание) *1. Требования AISI приводятся в соответствующей спецификации. |
(2) Ферритная нержавеющая сталь
В Таблице 2 представлены типичные марки ферритной нержавеющей стали.
Она содержит около 18% хрома и обладает ферритной металлографической структурой, которая отличается мягкостью и хорошей механической обрабатываемостью. Однако при нагревании при высокой температуре возникают металлургические проблемы.
По сравнению с мартенситной нержавеющей сталью она отличается более высокой устойчивостью к коррозии, и даже устойчива к воздействию азотной кислоты (HNO3) благодаря более высокому содержанию хрома.
Ферритная нержавеющая сталь широко используется для интерьеров и экстерьеров архитектурных сооружений, кухонных приспособлений, автомобилей, и бытовых электроприборов.
Таблица 2. Требования к химическому составу ферритных нержавеющих сталей (взято из JIS G 4305 и дополнено AISI)*1 (%) Марка сталиJIS (AISI) C Si Mn P S Cr Mo N ДругиеSUS405 (405) | Макс. 0.08 | Макс. 1.00 | Макс. 1.00 | Макс. 0.040 | Макс. 0.030 | 11.50~14.50 | - | - | Al : 0.10~0.30 |
SUS430 (430) | Макс. 0.12 | Макс. 0.75 | Макс. 1.00 | Макс. 0.040 | Макс. 0.030 | 16.00~18.00 | - | - | - |
SUS430LX (-) | Макс. 0.030 | Макс. 0.75 | Макс. 1.00 | Макс. 0.040 | Макс. 0.030 | 16.00~19.00 | - | - | Ti or Nb :0.10~1.00 |
SUS444 (444) | Макс. 0.025 | Макс. 1.00 | Макс. 1.00 | Макс. 0.040 | Макс. 0.030 | 17.00~20.00 | 1.75~2.50 | Макс. 0.025 | Ti, Nb, Zr илиобщее 8×(C%+N%)~0.80 |
(Примечание) *1. Требования AISI приводятся в соответствующей спецификации. |
(3) Аустенитная нержавеющая сталь
В Таблице 3 представлены типичные марки аустенитной нержавеющей стали.
Самая распространенная марка аустенитной нержавеющей стали - SUS304 или AISI 304 (18%Cr−8%Ni). SUS316 или AISI 316 (18%Cr−12%Ni−2%Mo), также широко применяемая, обладает более высокой устойчивостью к коррозии.
Аустенитная нержавеющая сталь обладает хорошей устойчивостью к коррозии, обрабатываемостью, механическими свойствами и свариваемостью. Она широко используется в производстве сосудов для хранения, теплообменников, водоочистных сооружений, кухонных приспособлений, ванн, раковин и т.д.
Таблица 3. Требования к химическому составу аустенитных нержавеющих сталей(взято из JIS G 4305−1999 и дополнено AISI)*1 (%) Марка сталиJIS (AISI) C Si Mn P S Ni Cr Mo Cu N ДругиеSUS304 (304) | Макс. 0.08 | Макс. 1.00 | Макс. 2.00 | Макс. 0.045 | Макс. 0.030 | 8.00~10.50 | 18.00~20.00 | - | - | - | - |
SUS304L (304L) | Макс. 0.030 | Макс. 1.00 | Макс. 2.00 | Макс. 0.045 | Макс. 0.030 | 9.00~13.00 | 18.00~20.00 | - | - | - | - |
SUS304LN (304LN) | Макс. 0.030 | Макс. 1.00 | Макс. 2.00 | Макс. 0.045 | Макс. 0.030 | 8.50~11.50 | 17.00~19.00 | - | - | 0.12~0.22 | - |
SUS309S (309S) | Макс. 0.08 | Макс. 1.00 | Макс. 2.00 | Макс. 0.045 | Макс. 0.030 | 12.00~15.00 | 22.00~24.00 | - | - | - | - |
SUS310S (310S) | Макс. 0.08 | Макс. 1.50 | Макс. 2.00 | Макс. 0.045 | Макс. 0.030 | 19.00~22.00 | 24.00~26.00 | - | - | - | - |
SUS316 (316) | Макс. 0.08 | Макс. 1.00 | Макс. 2.00 | Макс. 0.045 | Макс. 0.030 | 10.00~14.00 | 16.00~18.00 | 2.00~3.00 | - | - | - |
SUS316L (316L) | Макс. 0.030 | Макс. 1.00 | Макс. 2.00 | Макс. 0.045 | Макс. 0.030 | 12.00~15.00 | 16.00~18.00 | 2.00~3.00 | - | - | - |
SUS316LN (316LN) | Макс. 0.030 | Макс. 1.00 | Макс. 2.00 | Макс. 0.045 | Макс. 0.030 | 10.50~14.50 | 16.50~18.50 | 2.00~3.00 | - | 0.12~0.22 | - |
SUS317 (317) | Макс. 0.08 | Макс. 1.00 | Макс. 2.00 | Макс. 0.045 | Макс. 0.030 | 11.00~15.00 | 18.00~20.00 | 3.00~4.00 | - | - | - |
SUS317L (317L) | Макс. 0.030 | Макс. 1.00 | Макс. 2.00 | Макс. 0.045 | Макс. 0.030 | 11.00~15.00 | 18.00~20.00 | 3.00~4.00 | - | - | - |
SUS321 (321) | Макс. 0.08 | Макс. 1.00 | Макс. 2.00 | Макс. 0.045 | Макс. 0.030 | 9.00~13.00 | 17.00~19.00 | - | - | - | Ti : 5×C% мин. |
SUS347 (347) | Макс. 0.08 | Макс. 1.00 | Макс. 2.00 | Макс. 0.045 | Макс. 0.030 | 9.00~13.00 | 17.00~19.00 | - | - | - | Nb : 10×C% мин. |
SUS329 J3L*2 (31803) | Макс. 0.030 | Макс. 1.00 | Макс. 2.00 | Макс. 0.040 | Макс. 0.030 | 4.50~6.50 | 21.00~24.00 | 2.50~3.50 | - | 0.08~0.20 | - |
SUS329 J4L*2 (32250) | Макс. 0.030 | Макс. 1.00 | Макс. 1.50 | Макс. 0.040 | Макс. 0.030 | 5.50~7.50 | 24.00~26.00 | 2.50~3.50 | - | 0.08~0.30 | - |
SUS630*3 (S17400) | Макс. 0.07 | Макс. 1.00 | Макс. 1.00 | Макс. 0.040 | Макс. 0.030 | 3.00~5.00 | 15.00~17.50 | - | 3.00~5.00 | - | Nb : 0.15~0.45 |
(Примечание) *1. Требования AISI приводятся в соответствующей спецификации.*2. Аустенитно-ферритная нержавеющая сталь (Дуплексная)*3. Дисперсионно-твердеющая нержавеющая сталь |
3. Физические свойства нержавеющей стали
В Таблице 4 представлено сравнение физических свойств нержавеющих и углеродистых сталей.
При сварке нержавеющих сталей необходимо учитывать то, что физические свойства нержавеющих сталей и углеродистых сталей значительно отличаются, и это прямо или косвенно влияет на их свариваемость.
Например, при том, что коэффициент термического расширения мартенситной и ферритной нержавеющей стали почти такой же, что и у углеродистой стали, для аустенитной нержавеющей стали этот показатель в 1,5 раза выше по сравнению с углеродистой сталью. Это означает, что деформация и напряжение при сварке аустенитной нержавеющей стали гораздо выше, чем при сварке углеродистой стали.
Более того, если сварное соединение, содержащее аустенитную сталь и углеродистую сталь, подвергается воздействию термических циклов, в нем возникают термические напряжения из-за разницы коэффициентов термического расширения двух материалов. Поэтому использование сварных соединений с разными металлами, включая аустенитную нержавеющую сталь, в условиях циклических изменений температуры является проблематичным.
Кроме того, электрическое сопротивление нержавеющей стали намного выше, чем углеродистой стали, поэтому при дуговой сварке в защитной среде происходит обгорание покрытых электродов из нержавеющей стали. Таким образом, подходящий сварочный ток ниже, чем для электродов из углеродистой стали.
Мартенситные и ферритные нержавеющие стали являются ферромагнитыми, тогда как аустенитные нержавеющие стали обычно немагнитные.
Однако нередко сварочные материалы из аустенитной нержавеющей стали отчасти содержат ферритную структуру, в таких случаях сталь в определенной мере обладает магнитными свойствами.
Наличие или отсутствие магнитных свойств позволяет определить марку стали при сварочных процедурах. В частности, предварительное нагревание не применяется для немагнитных нержавеющих сталей, но оно часто бывает эффективным для магнитных нержавеющих сталей.
Таблица 4. Сравнение физических свойств Углеродистаясталь Мартенситнаянержавеющая сталь Ферритнаянержавеющая сталь Аустенитнаянержавеющая стальТеплопроводимость10−2Cal/cm/sec℃ | Примерно 11 | Примерно 6 | Примерно 6 | Примерно 4 |
Коэффициент термическогорасширения 10−6/℃ | Примерно 11 | Примерно 11 | Примерно 11 | Примерно 17 |
Электрическое сопротивлениеμΩcm | 15 | 57 | 60 | 72 |
Магнитные свойства | Да | Да | Да | Нет |
Верх страницы
www.kobelco-welding.jp
Сталь ферритная - Энциклопедия по машиностроению XXL
Хромистые стали ферритные и мартенситно-ферритные обладают некоторой склонностью к межкристаллитной коррозии (м. к. к.). Особо высокую склонность к м. к. к. они приобретают после быстрого охлаждения с высоких температур. Для восстановления стойкости против м. к. к, возможно применение высокого отпуска, причем его температура и длительность [c.270]Кроме того, существуют стали ферритного и аустенитного классов. [c.173]
Стали ферритного класса [c.266]Хорошие свойства стали ферритного класса приобретают после горячей обработки давлением и кратковременного отжига при 760— 780° С при этом возникает мелкозернистая структура (рис. 15.7). [c.267]
Упрочнению ультразвуком поддаются низкоуглеродистые стали, стали ферритного и аустенитного классов и цветные металлы, зффект упрочнения которых особенно велик. [c.178]
Влияние состава и структурных особенностей на зависимость Ста—0—е становится тем слабее, чем выше температура деформации. Исключение составляют высокохромистые ферритные стали, у которых явление рекристаллизации не осложнено действием упрочняющих примесей и при высоких температурах рекристаллизация развивается значительно сильнее, чем у других сталей. Этим можно объяснить отличающийся от других сталей высокий скоростной эффект у сталей ферритного класса, содержащих не менее 23% Сг. Большой скоростной эф- [c.474]
Для высокохромистых сталей ферритного класса значение п заметно выше, чем у сталей перлитного класса. [c.476]
Сталь с легированной хромом и никелем поверхностью рекомендуется для замены нержавеющих сталей ферритного класса и в отдельных средах — аустенитного. [c.206]
Ферритный класс. Стали ферритного типа при нагреве и охлаждении не имеют превращений а- у состоят из твердого раствора с а-решеткой. Некоторые стали этого класса при высоких температурах попадают в двухфазную область a-f-y [19] и относятся к полуферритным сталям. Примером полу-ферритной стали является 17%-ная хромистая нержавеющая сталь с 0,10% С марки XI7. Режимы термических обработок, которым подвергаются эти стали, приведены в табл. 5. [c.99]Установлено, что хромоникелевые аустенитные стали менее устойчивы к коррозии при 540—600°С в расплавленном свинце, чем стали ферритного и перлитного типов. Более низкая устойчивость хромоникелевых сталей объясняется избирательным, растворением никеля в свинце. [c.90]
Стали ферритного класса по сравнению с аустенитными при обычных комнатных 1ем-пературах имеют меньшую пластичность при холодной пластической деформации их механическая прочность увеличивается в меньшей степени (при этом значительно падает удлинение) они обладают большей способностью к рекристаллизации, причем процесс рекристаллизации протекает при относительно более низких температурах и сопровождается значительным падением ударной вязкости В области высоких температур феррит обладает более высокими пластическими свойствами и низкой сопротивляемостью деформации и т. п. [c.10]
Физические свойства хромистых нержавеющих коррозионностойких стале ферритного, мартенсито-ферритного и мартенситного классов [c.14]
Температурный режим горячей обработки давлением И отжига хромистых сталей ферритного, мартенсито-ферритного и мартенситного классов [c.16]
ВЫСОКОХРОМИСТЫЕ СТАЛИ ФЕРРИТНОГО КЛАССА [c.20]
Одним из существенных недостатков высокохромистых сталей ферритного класса, кроме указанных, является их склонность к охрупчиванию в результате нагрева металла в интервале температур 450—500° С. Этот вид охрупчивания чаще всего наблюдается на ферритных сталях, содержащих 25—30% Сг, и проявляется в снижении ударной вязкости, относительного удлинения, уменьшении электросопротивления, повышении модуля упругости, твердости и коэрцитивной силы [141. [c.22]
Для сталей ферритного класса желательно, чтобы температура окончания операции горячей деформации была возможно ниже 700° С). [c.52]
Стали ферритного класса, например, склонны к росту зерна и под воздействием сварочного нагрева сильно снижаются их пластические свойства. Ударная вязкость при этом значительно падает. [c.54]
Кремний подобно хрому действует как ферритообразующий элемент, сильно ограничивая у-область. Это приводит к тому, что стали с малым содержанием С уже при 6% Сг и 2% Si относятся к сталям полуферритного типа, а при большем содержании Si — к сталям ферритного типа, не имеющим превращений у а.. [c.129]
По данным работы [17], длительная прочность перлито-ферритного ковкого чугуна при 425° С (соответствующая испытаниям в течение 4000 ч) одинакова с литой сталью марки 25Л после отжига, в то время как кратковременная прочность стали при этой температуре выше, чем чугуна. При температурах более высоких, чем 500°, длительная прочность феррито-перлитного чугуна оказывается меньше, чем указанной стали. Ферритный ковкий чугун при всех температурах имеет длительную и кратковременную прочность ниже, чем сталь. Сопротивление ползучести ковкого чугуна выше, чем серого, но ниже, чем высокопрочного чугуна. [c.124]
Также может быть получен класс аустенитных сталей. При достаточно высоком содержании. элементов, раси1иряющих у-область, получаются стали, в которых сохраняется аустенит при охлаждении до комнатной температуры. Следовательно, кроме доэвтектоидного, эвтектоидного, заэвтектоидного п ледебурнтного классов, могут еще быть легированные стали ферритного и аустанитного классов . [c.360]
Сталь Х28, содержащая до 27—30% Сг и 0,15% С, принадлежит к сталям ферритного класса и не подвергается закалке. Стали Х17 и Х28 обладают достаточно высокой пластичностью как в горячем, так и в холодном состоянии. Однако сварка для них опасна вследствие пониженной пластичности сварных швов и появления в зоне термического влияния склонности к меж-кристаллитиой коррозии. [c.217]
Для сталей ферритного класса влияние положительной асимметрии цикла на кинетику усталостных трещин бьио учтено следующим образом [42] [c.301]
Анализ экспериментального материала, полученного на сталях ферритного, перлитного и аустенитного классов, и никелевых сплавах показал, что если величина пластической деформации, накопленной до агонийной стадии разрушения, >2%, то длительная прочность образцов с кольцевыми подрезами средней жесткости (теоретический коэффициент концентрации напряжений А =4%) не ниже соответствующей прочности гладких образцов — материал не чувствителен к надрезу. Следовательно, в условиях дли- [c.73]
В настоящее время накоплен достаточный материал о количественном и качественном влиянии легирующих добавок на свойства малоуглеродистых низколегированных сталей ферритно-перлитного класса. Интервалы содержаний легирующих элементов в данных сталях составляют лищь некоторую часть от их предела растворимости в а-железе. [c.66]
В качестве примера можно рассмотреть анализ и оценку V, VIII и IX уровней дерева целей. При анализе V уровня была поставлена задача разработки литейной сваривающейся стали ферритно-перлитного класса. Для решения ее был использован ряд прогностических приемов составление банка данных и обработка его с использованием методов параметрического прогнозирования, оценка установленных закономерностей на основе экспертного опроса, методы математического моделирования. [c.220]
Элементы, стоящие в строке 1, являются основными егирующими добавками к сталям ферритно-перлит-юго класса. Распределение этих элементов по частоте (X использования в легирующем комплексе для еталей количеством углерода не более 0,20% (по данным ОСТа и ТУ) (рис. 33) показало, что в большинстве лучаев для легирования применяется комбинация из [c.221]
Самой высокой коррозионной устойчивостью в расплавленном свинце обладают тантал и ниобий. Железо, углеродистая сталь, хромистые и хромоникелевые стали имеют хорошую устойчивость до 500—600°С. При более высоких температурах она понижается, так как наблюдается растворение преимущественно по границам зерен. Стали перлитного типа устойчивы к действию свинца при температурах до 600°С. Хромистые нержавеющие стали ферритного и мартенсигного типов (1X13, Х17) обладают высокой коррозионной устойчивостью до 540°С. [c.90]
К первой группе относят металлы и сплавы, обладающие удовлетворительными механическими характеристиками при обычных климатических температурах (до —50 °С) углеродистые стали ферритного и мартенсит-ного классов, некоторые низколегированные и инструментальные стали и композиционные материалы на основе кобальта. [c.309]
Химический состав хромистых нержавеющих коррозионностойких сталей ферритного, мартенсито-феррнтного и мартенситного классов [c.12]
Механические свойства хромистых нержавеющих сталей ферритного, мартенсито-ферритного и иартенситного классов после оптимальной термической обработки [c.15]
Такая склонность к росту зерна и хрупкому разрушению в производстве и переработке толстолистовых высокохромистых сталей Х25Т, Х28, а также 0XI7T или других сталей ферритного класса вызывает значительные трудности. [c.20]
Ввиду повышенной склонности сталей ферритного класса к росту зерен необходимо стремиться к увеличению скоростей сварки и достаточно интенсивному охлаждению шва и околошовной зоны, не допуская сильного перегрева металла при формировании сварного шва. Соблюдение этих условий также способствует повышению сопротивляемости стали межкристаллитпой коррозии. [c.22]
Наиболее важными особеииостяии рассматриваемых технологических процессов для нержавеющих сталей являются следующие. При горячей деформации сталей ферритного класса во избежание значительного роста зерна и снижения [c.51]
По сравнению с указанными двухфазными сталями значительно менее технологичны стали ферритного класса 0Х17Т, Х25Т и др. [c.65]
При вальцовке, раскрое и отбортовке толстолистовой стали ферритного класса (например, марок 0Х17Т, Х25Т и др.) необходимо проводить подогрев металла, в том числе сварных соединений до температуры 100° С, благодаря чему значительно улучшаются технологические свойства стали, в частности, повышаю1ся удлинение и ударная вязкость. [c.66]
При температурах ниже 600° С во многих случаях стали ферритного или мар-тенситного класса имеют явные преимущества по сравнению с малолегированными. [c.122]
Характерным примером сталей ферритного класса является сталь 12X17 (табл. 9). Отожженная при 780 и 850°С, она имеет предел выносливости соответственно 240 и 270 МПа, Закалка стали от 1100°С с последующим отпуском при 580 и 550°С привела к повышению временного сопротивления на 140-150 МПа и не оказала существенного влияния на предел выносливости. Условный предел коррозионной выносливости этой стали составляет 130—150 МПа и мало зависит от режимов термической обработки. [c.61]
Образование — Тепловой эффект 6—166 Ферритнап сталь — см. Сталь ферритная Ферритные сплавы — 3—331 Феррованадий — Химический состав 6 — 5 Ферровольфрам — Химический состав 6 — 5 Ферродинамические приборы 1 (1-я) — 524 Ферромагнитные материалы — Кривые намагничивания 3 — 180 [c.319]
A i 1 1 Ar 1 Сталь ферритного или полул ферритного класса 7,12 [c.689]
mash-xxl.info
Нержавеющая сталь
Нержавеющая сталь - это хромосодержащий сплав стали. Минимальное содержание хрома в стандартной нержавеющей стали составляет 10.5%. Хром обеспечивает стали"нержавеющие" свойства, другими словами улучшает стойкость к коррозии. Лучшая сопротивляемость коррозии обеспечивается оксидной пленкой, покрывающей поверхность стали. Этот чрезвычайно тонкий слой также обладает свойством самовосстанавливаться. Кроме хрома типичными элементами этого сплава также являются молибден, никель и азот. Никель добавляется главным образом для улучшения пластичности и вязкости сплава. Добавление в сплав этих элементов позволяет получить различные виды кристаллических решеток, что в свою очередь, позволяет добиться различных свойств стали.
Существует четыре основных вида нержавеющей стали:
Аустенитная сталь
Аустенитная сталь является наиболее широко распространенным типом нержавеющей стали. Содержание никеля в такой стали составляет не менее 7%, что придает ей пластичность, широкий спектр температурных режимов, не магнитные свойства и хорошую пригодность к сварке.
Ферритная нержавеющая сталь
Ферритная нержавеющая сталь имеет свойства близкие к свойствам малоуглеродистой стали но с лучшей сопротивляемостью коррозии. Наиболее распространенными видами такой стали являются сплавы с содержанием хрома 12% и 17%. Сплавы с содержание мхрома около 12% используются в основном в строительстве, а стали, содержащиеоколо 17% хрома, используются в домашнем хозяйстве, бойлерах, стиральных машинах и комнатных декоративных элементах.
Ферро-аустенитная (дуплексная) нержавеющая сталь
Ферро-аустенитная (дуплексная) нержавеющая сталь имеет обе ферритную иаустенитную структуру кристаллической решетки - отсюда ее название"дуплексная нержавеющая сталь". Эта сталь имеет некоторое содержание никеля, что частично обуславливает ее аустенитную структуру. Дуплексная структура предоставляет одновременно прочность и гибкость. Дуплексные стали чаще всего используются в нефтехимической, целлюлозно-бумажной промышленностяхи судостроительстве.
Мартенситная сталь
Мартенситная сталь содержит в основном от 11% до 13% хрома и прочна и жестка при средней сопротивляемости коррозии. Эта сталь используется в основном для производства турбин и клинков.
Нержавеющая сталь - это сплав железа с хромом. Её антикоррозийные свойства появляются благодаря наличию на поверхности металла слоя оксида хрома. Этот защитный слой очень устойчив и даже после механического или химического повреждения быстро приобретает свой прежний вид и антикоррозийные качества металла остаются без изменений. Материал очень практичный, одновременно благородный и эстетичный. Благодаря разнообразию марок и видов поверхности он в состоянии удовлетворять разные условия, которые появляются перед строительными и отделочными материалами.
Кроме антикоррозийного свойства у нержавеющей стали следует отметить следующие качества:
Надежность элементов из нержавеющей стали намного выше чем у других отделочныхматериалов. Их вид не изменяется в течении десятков лет. Нержавеющая сталь имеет намного более высокие жаропрочные свойства, чем другие стали.
Существуют декоративные листы из нержавеющей стали. Эти листы имеют ряд свойствдающих им преимущество над традиционными листами - шлифованными или полированными:
Нержавеющую сталь используют во всех сферах деятельности человека, начиная от тяжелого машиностроения, заканчивая электроникой и точной механикой. Наиболеебольшее применение она нашла в:
www.amisto.ru