- Изначально формируется электрическая дуга, которая зажигается между электродом аппарата и его соплом либо между электродом и разрезаемым металлом. Температура такой дуги составляет 5000 градусов.
- После этого в сопло оборудования подается газ, который повышает температуру дуги уже до 20000 градусов.
- При взаимодействии с электрической дугой газ ионизируется, что и приводит к его преобразованию в струю плазмы, температура которой составляет уже 30000 градусов.
- обычный воздух;
- технический кислород;
- азот;
- водород;
- аргон;
- пар, полученный при кипении воды.
- аппараты косвенного действия — резка выполняется бесконтактным способом;
- аппараты прямого действия — резка контактным способом.
- источника питания;
- плазмотрона;
- кабелей и шлангов, с помощью которых выполняется соединение плазмотрона с источником питания и источником подачи рабочего газа;
- газового баллона или компрессора для получения струи воздуха требуемой скорости и давления.
- рабочего сопла;
- электрода;
- изолирующего элемента, который отличается высокой термостойкостью.
- Основы резки металлов плазмой
- Характеристики и принцип резки металла плазмой
- Скорость и точность резки металла плазмой
- Плазменная резка цветных металлов
- Где применяется плазменный раскрой металла
- Резка металла плазмой – преимущества и недостатки
- Сравнение плазменной и лазерной резки металла
- Что такое плазменная резка металла?
- На чем основан принцип проведения работ?
- Какие сферы применения имеет этот способ раскроя материалов?
- Скорость - струя направляется под высоким давлением на поверхность материала. Можно сказать, что плазменный раскрой металла основан на разогревании металла до температуры плавления и быстрого выдувания его. Рабочая скорость струи при этом составляет от 1,5 до 4 км в сек.
- Температура - для образования плазмы необходимо практически моментально разогреть воздух до 5000-30000°C. Высокая температура достигается благодаря созданию электрической дуги. При достижении необходимой температуры воздушный поток ионизируется и меняет свои свойства, приобретая электропроводность. Технология плазменной резки металла подразумевает использование систем нагнетания воздуха, а также осушителей, которые удаляют влагу.
- Наличие электрической цепи. Все о раскрое металла плазмой можно узнать только на практике. Но некоторые особенности необходимо учитывать еще до приобретения установки. Так, существуют плазмотроны косвенного и прямого воздействия. И если для вторых обязательно, чтобы обрабатываемый материал пропускал электричество и был включен в общую электрическую сеть (выступая в роли электрода), то для первых такой необходимости нет. Плазма для резки металла в таком случае получается с помощью встроенного электрода внутри держателя. Этот способ используют для металлов и других материалов, которые не проводят электричество.
Компрессор под давлением подает воздух на горелку плазмотрона.
- Воздушный поток моментально разогревается благодаря воздействию на него электрического тока. По мере нагревания воздушная масса начинает пропускать сквозь себя электричество, в результате чего и образуется плазма. В некоторых моделях вместо воздуха используют инертные газы.
- Резка стали плазмой, если рассмотреть ее более подробно осуществляется методом быстрого узконаправленного нагревания поверхности до необходимой температуры с последующим выдуванием расплавленного металла.
- При выполнении работ неизбежно образуются отходы от плазменной резки. Отходы включают высечку или остатки листа после высечения необходимых деталей, а также окалины или остаток расплавленного металла.
- алюминий до 120 мм;
- медь 80 мм;
- углеродистая и легированная сталь до 50 мм;
- чугун до 90 мм.
- Плазменно-дуговая - способ подходит для всех видов металла, которые в состоянии проводить электрический ток. Обычно плазменно-дуговую резку используют для промышленного оборудования. Суть способа сводится к тому, что плазма образовывается за счет дуги, которая появляется непосредственно между поверхностью обрабатываемого материала и плазмотроном.
- Плазменно-струйная – в этом случае дуга возникает в самом плазмотроне. Плазменно-струйный вариант обработки более универсален, позволяет разрезать неметаллические материалы. Единственным недостатком является необходимость периодической замены электродов.
Конусность - в зависимости от профессионализма мастера и производительности установки, конусность может составлять от 3° до 10°.
- Оплавление кромки - независимо от того, какие режимы резки металла используются и от профессионализма мастера выполняющего работы по обработке металла, не удается избежать небольшого оплавления поверхности при самом начале выполнения работ.
- Характеристики реза - качество и скорость плазменной резки металла зависит от того, какие именно операции необходимо выполнить. Так разделительный рез с низким качеством выполняется быстрее всего, при этом большинство ручных установок способны разрезать металл до 64 мм. Для фигурной резки возможна обработка деталей толщиной всего до 40 мм.
- Скорость выполнения работ - обычная резка металла с помощью плазматрона осуществляется быстро и с минимальным расходом электроэнергии и напряжения. Скорость плазменной резки металла согласно техническим характеристикам ручных установок и ГОСТ составляет не более 6500 мм в минуту.
Резка нержавеющих сталей - для выполнения операций не рекомендуется использование сжатого воздуха, в зависимости от толщины материала может применяться азот в чистом виде, либо смешанный с аргоном. Необходимо учитывать, что нержавеющая сталь чувствительна к воздействию переменного тока, это может привести к изменению ее структуры и как следствие быстрому выходу из эксплуатации. Резка нержавейки плазмой осуществляется с помощью установки использующей принцип косвенного воздействия.
- Плазменная резка алюминия - для материала с толщиной до 70 мм, может использоваться сжатый воздух. Применение его нецелесообразно при малой плотности материала. Более качественный рез листа алюминия до 20 мм достигается при использовании чистого азота, а более 70 мм до 100 мм включительно с помощью азота с водородом. Резка алюминия плазмой при толщине от 100 мм осуществляется смесь аргона с водородом. Этот же состав рекомендовано использовать для меди и высоколегированной толстостенной стали.
Обработка металлопроката - с помощью плазмы удается разрезать практически любой тип металла, включая цветной, тугоплавкий и черный.
- Изготовление металлоконструкций.
- Художественная ковка и обработка деталей. С помощью плазменного резака можно сделать деталь практически любой сложности.
- Различные виды промышленности, машиностроение, капитальное строительство зданий авиастроение и др. – во всех этих сферах деятельности не обойтись без использования плазменных резаков.
- Высокая производительность и скорость обработки деталей. По сравнению с обычным электродным методом можно выполнить объемы работ от 4 до 10 раз больше.
- Экономичность - плазменный метод намного выигрывает на фоне стандартных способов обработки материалов. Единственные ограничения связанны с толщиной металла. Нецелесообразно и экономически невыгодно разрезать с помощью плазмы сталь толще 5 см.
- Точность - деформации от тепловой обработки практически незаметны и не требуют дополнительной обработки впоследствии.
- Безопасность.
- Ограничения, связанные с толщиной реза. Даже у мощных установок максимальная плотность обрабатываемой поверхности не может быть выше, чем 80-100 мм.
- Жесткие требования относительно выполнения обработки деталей. От мастера требуется четко придерживаться угла наклона резака от 10 до 50 градусов. При несоблюдении этого требования нарушается качество реза, а также ускоряется износ комплектующих.
- Источник тока (питающийся от 220 V для небольших моделей, и 380 V для промышленных установок, рассчитанных на большую толщину металла) выдает требуемое напряжение.
- По кабелям ток передается на плазмотрон (горелку в руках сварщика-резчика). В устройстве находится катод и анод — электроды, между которыми загорается электрическая дуга.
- Компрессор нагнетает поток воздуха, передающегося по шлангам в аппарат. В плазмотроне имеются специальные завихрители, способствующие направлению и закручиванию воздуха. Поток пронизывает электрическую дугу, ионизируя ее и разгоняя температуру во много раз. Получается плазма. Данная дуга называется дежурной, поскольку горит для поддержания работы.
- Во многих случаях используется кабель массы, который подсоединяется к разрезаемому материалу. Поднеся плазмотрон к изделию, дуга замыкается между электродом и поверхностью. Такая дуга называется рабочей. Большая температура и давление воздуха пронизывают требуемое место в изделии, оставляя тонкий рез и небольшие наплывы, легко удаляемые постукиванием. Если контакт с поверхностью теряется, то дуга автоматически продолжает гореть в дежурном режиме. Повторное поднесение к изделию позволяет сразу продолжать резку.
- После окончания работы, кнопка на плазмотроне отпускается, что выключает все виды электрической дуги. Некоторое время выполняется продувка воздухом системы для удаления мусора и охлаждения электродов.
- Возможность обрабатывать любые виды стали, включая металлы с высоким коэффициентом теплового расширения.
- Разрезание материалов не проводящих электрический ток.
- Высокая скорость проводимых работ.
- Легкая обучаемость рабочему процессу.
- Разнообразные линии реза, включая фигурные формы.
- Высокая точность резки.
- Малая последующая обработка поверхности.
- Меньшее загрязнение окружающей среды.
- Безопасность для сварщика ввиду отсутствия газовых баллонов.
- Мобильность при транспортировке оборудования имеющего малые размеры и вес.
- Разрезаемое изделие выставляется так, чтобы под ним был просвет в несколько сантиметров. Для этого используются подкладки под края, или конструкция устанавливается на край стола, чтобы обрабатываемая часть была над полом.
- Разметку линии реза лучше выполнять черным маркером, если работа ведется на нержавеющей стали или алюминии. Когда предстоит разделать «черный» металл, то линию лучше провести тоненьким мелком, который четче виден на темной поверхности.
- Важно убедиться, что шланг от горелки не лежит рядом с местом реза. Сильный перегрев может его испортить. Начинающие сварщики могут из-за волнения это не увидеть и повредить оборудование.
- Надеваются защитные очки. Если работать предстоит долго, то лучше воспользоваться маской, которая закроет не только глаза, но и все лицо от ультрафиолета.
- Если резка будет вестись на подложках выставленных на полу, то следует подложить лист металла, чтобы брызги не испортили покрытие пола.
- Перед началом работы необходимо убедиться, что компрессор набрал достаточное давление, а водяные модели разогрели жидкость до нужной температуры.
- Запуском кнопки зажигается дуга.
- Держать плазмотрон необходимо перпендикулярно разрезаемой поверхности. Допускается небольшой угол отклонения относительно этого положения.
- Начало реза лучше производить с края изделия. Если необходимо начать с середины, то желательно просверлить тоненькое отверстие. Это поможет избежать перегрева и впадины в этом месте.
- При ведении дуги необходимо соблюдать дистанцию к поверхности в 4 мм.
- Для этого важен упор под руки, который осуществляется локтями об стол или об колени.
- При ведении реза важно зрительно удостоверяться в появлении просвета на пройденном участке, иначе придется проводить резку повторно.
- Когда линия разреза заканчивается, необходимо соблюсти предосторожность, чтобы деталь не упала на ноги.
- Отпускание кнопки прекращает горение дуги.
- Молотком отбивается тонкий слой шлака по краям реза. Если есть необходимость, то проводится дополнительная зачистка изделия на наждачном круге.
- типы деталей, которые будут вырезаться;
- количество промышленных изделий в партии;
- желаемую скорость и качество резки;
- стоимость расходных материалов.
- общую стоимость эксплуатации конфигурации, в том числе электроэнергии, газа и труда.
- энергоисточник;
- резак;
- компрессорная установка или баллон с газом для подачи воздуха;
- соединительные кабели.
- Инвертор. Имеет массу достоинств: обеспечивает стабильность образования дуги; высокий показатель КПД, в отличие от трансформатора; легкий вес и невысокая стоимость; возможность применения в малодоступном месте. Единственным минусом системы является то, что он неспособен резать детали более 30 мм.
- Трансформатор. Основным достоинством устройства является устойчивость к перепадам напряжения электросети. Также можно отметить, что он дает резать металлические детали большой толщины. Главный недостаток – существенная масса, низкий КПД.
- Рабочий электрод;
- Рабочее сопло;
- Изолирующий элемент, обладающий высокой термоустойчивостью.
- изготовление изделий с различными фигурными очертаниями;
- проделывание сквозных проемов в металлическом элементе;
- производство деталей для сваривания, штамповки и контактного возделывания;
- плазменная резка труб;
- литейная обработка.
- Простой способ. При разрезе применяется воздух либо азот и электричество. Длиновые показатели электрической дуги ограничены. Этот метод применим для стали с низким содержанием вспомогательных примесей, то есть низколегированного типа. Газообразный кислород выступает в роли режущего компонента. Для данного метода характерна – ровная кромка и отсутствие заусениц. Основное использование — ручная резка.
- Смешение двух газов. Одна газовая составляющая плазменной резки направляется на возникновение плазмы, другая выполняет защитную функцию от неблагоприятного воздействия атмосферы. Качественные характеристики разрезания металла увеличиваются.
- С водной защитой. Эта модификация предполагает применение в технологии воды, вместо газообразного элемента. Водная основа обеспечивает оптимальное охлаждение сопла и заготовительного элемента. Все вредные вещества поглощаются водными массами.
- Со впрыскиванием воды. Газ направляется на образование плазмы, а водные массы в вихревую дугу. Это позволяет увеличить ее сжатие, тем самым повышая плотность и температурные показатели.
- На первом этапе образовывается электродуга, разжигающееся между электродом устройства и соплом. Температурные показатели могут достигать 5 тысяч градусов.
- Подается газовый элемент, повышая температурное значение уже до 20 тысяч.
- Происходит взаимодействие газа и электрической дуги – ионизация. Температура увеличивается до 30 тысяч градусов.
- Универсальность технологического процесса.
- Автоматическая плазменная резка.
- Высокие показатели скорости операции при работе с материалами средней и малой толщины.
- Высокоточный и качественный рез, исключив дополнительных механических операций.
- При работе с электроплазменной средой практически исключается загрязнение воздуха.
- Нет необходимости предварительного разогрева поверхности, что снижает временные рамки прожига.
- Выполняемые работы считаются относительно безопасными, так как нет необходимости волочить за собой баллоны с газом, которые являются взрывоопасными.
- Ценовая составляющая плазмотрона и его конструкционные особенности, что повышает себестоимость выполнения работ по резке металла.
- Незначительная толщина прореза.
- Высокие показатели шума, так как газовый элемент из плазмотрона выходит на околозвуковой скорости.
- Необходимо качественное техническое обслуживание агрегата.
- Если в качестве газообразного элемента используется азот, то это способствует выделению большого количества вредных веществ в атмосферу.
- К конфигурации плазмотрона нельзя подключить дополнительный плазменный резак для ручной обработки металлической поверхности.
- Тепловой микроклимат в зоне работающего человека;
- Облучение ультрафиолетовым спектром;
- Влияние расплавленного металла;
- Увеличенное напряжение;
- Труба бесшовная 8732 78 труба стальная бесшовная горячедеформированная
- Уголок стальной гнутый неравнополочный
- Почему ржавеет нержавеющая сталь
- Сталь с покрытием полиэстер
- Стальной провод
- Стальной провод
- Монтаж гофрированной трубы из нержавеющей стали
- Монтаж гофрированной трубы из нержавеющей стали
- Марки стали перлитного класса
- Марки стали перлитного класса
- Малоуглеродистая сталь
Резка металла плазмой. Металлообрабатывающее оборудование. Плазменная резка стали
Плазменная резка металла – аппараты, технология, видео процесса
В последнее время использование плазменного потока для раскроя материалов набирает все большую популярность. Еще более расширяет сферу использования данной технологии появление на рынке ручных аппаратов, с помощью которых выполняется плазменная резка металла.
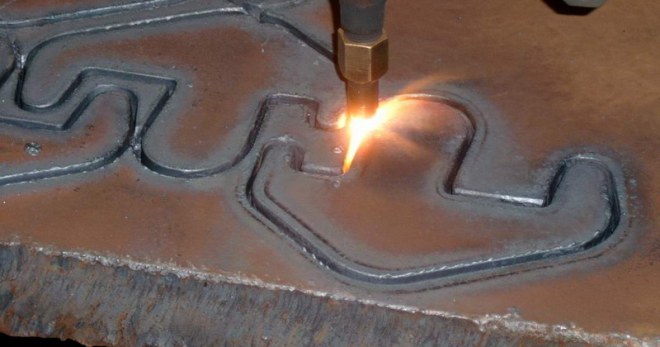
Плазменная резка металла значительной толщины
Суть плазменной резки
Плазменная резка предполагает локальный нагрев металла в зоне разделения и его дальнейшее плавление. Такой значительный нагрев обеспечивается за счет использования струи плазмы, формируют которую при помощи специального оборудования. Технология получения высокотемпературной плазменной струи выглядит следующим образом.
Полученная плазменная струя характеризуется ярким свечением, высокой электропроводностью и скоростью выхода из сопла оборудования (500–1500 м/с). Такая струя локально разогревает и расплавляет металл в зоне обработки, затем осуществляется его резка, что хорошо видно даже на видео такого процесса.
В специальных установках для получения плазменной струи могут использоваться различные газы. В их число входят:
Технология резки металла с использованием плазмы предполагает охлаждение сопла оборудования и удаление частичек расплавленного материала из зоны обработки. Обеспечивается выполнение этих требований за счет потока газа или жидкости, подаваемых в зону, где осуществляется резка. Характеристики плазменной струи, формируемой на специальном оборудовании, позволяют произвести с ее помощью резку деталей из металла, толщина которых доходит до 200 мм.

Устройство и принцип действия плазменной резки
Аппараты плазменной резки успешно используются на предприятиях различных отраслей промышленности. С их помощью успешно выполняется резка не только деталей из металла, но и изделий из пластика и натурального камня. Благодаря таким уникальным возможностям и своей универсальности, данное оборудование находит широкое применение на машиностроительных и судостроительных заводах, в рекламных и ремонтных предприятиях, в коммунальной сфере. Огромным преимуществом использования таких установок является еще и то, что они позволяют получать очень ровный, тонкий и точный рез, что является важным требованием во многих ситуациях.
Оборудование для плазменной резки
На современном рынке предлагаются аппараты, с помощью которых выполняется резка металла с использованием плазмы, двух основных типов:
Оборудование первого типа, в котором дуга зажигается между электродом и соплом резака, используется для обработки неметаллических изделий. Такие установки преимущественно применяются на различных предприятиях, вы не встретите их в мастерской домашнего умельца или в гараже ремонтника.
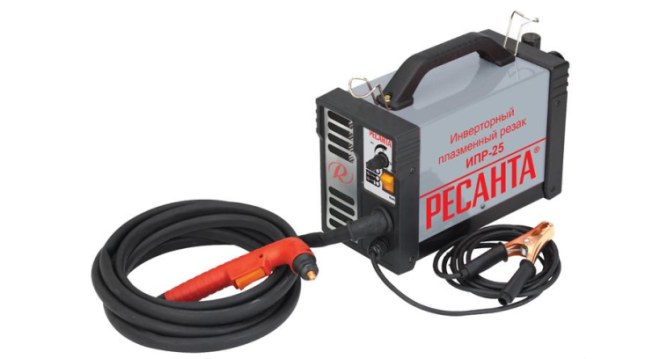
Аппарат для плазменной резки Ресанта ИПР-25
В аппаратах второго типа электрическая дуга зажигается между электродом и непосредственно деталью, которая, естественно, может быть только из металла. Благодаря тому, что рабочий газ в таких устройствах нагревается и ионизируется на всем промежутке (между электродом и деталью), струя плазмы в них отличается более высокой мощностью. Именно такое оборудование может использоваться для выполнения ручной плазменной резки.
Любой аппарат плазменной резки, работающий по контактному принципу, состоит из стандартного набора комплектующих:
Главным элементом всех подобных устройств является плазмотрон, именно он отличает такое оборудование от обычного сварочного. Плазмотроны или плазменные резаки состоят из следующих элементов:
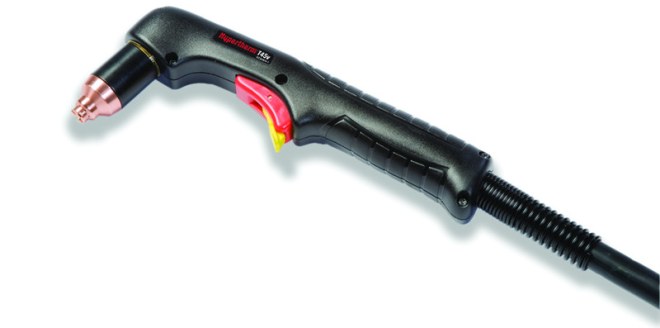
Резак для ручной плазменной резки
Основное назначение плазмотрона состоит в том, чтобы преобразовать энергию электрической дуги в тепловую энергию плазмы. Газ или воздушно-газовая смесь, выходящие из сопла плазмотрона через отверстие небольшого диаметра, проходят через цилиндрическую камеру, в которой зафиксирован электрод. Именно сопло плазменного резака обеспечивает требуемую скорость движения и форму потока рабочего газа, и, соответственно, самой плазмы. Все манипуляции с таким резаком выполняются вручную: оператором оборудования.
Учитывая тот факт, что держать плазменный резак оператору приходится на весу, бывает очень сложно обеспечить высокое качество раскроя металла. Нередко детали, для получения которых была использована ручная плазменная резка, имеют края с неровностями, следами наплыва и рывков. Для того чтобы избежать подобных недостатков, применяют различные приспособления: подставки и упоры, позволяющие обеспечить ровное движение плазмотрона по линии раскроя, а также постоянство зазора между соплом и поверхностью разрезаемой детали.
Необходимые источники питания
Несмотря на то что все источники питания для плазменных резаков работают от сети переменного тока, часть из них может преобразовывать его в постоянный, а другие — усиливать его. Но более высоким КПД обладают те аппараты, которые работают на постоянном токе. Установки, работающие на переменном токе, применяются для резки металлов с относительно невысокой температурой плавления, к примеру, алюминия и сплавов на его основе.
В тех случаях, когда не требуется слишком высокая мощность плазменной струи, в качестве источников питания могут использоваться обычные инверторы. Именно такие устройства, отличающиеся высоким КПД и обеспечивающие высокую стабильность горения электрической дуги, используются для оснащения небольших производств и домашних мастерских. Конечно, разрезать деталь из металла значительной толщины с помощью плазмотрона, питаемого от инвертора, не получится, но для решения многих задач он подходит оптимально. Большим преимуществом инверторов является и их компактные габариты, благодаря чему их можно легко переносить с собой и использовать для выполнения работ в труднодоступных местах.
Более высокой мощностью обладают источники питания трансформаторного типа, с использованием которых может осуществляться как ручная, так и механизированная резка металла с использованием струи плазмы. Такое оборудование отличается не только высокой мощностью, но и более высокой надежностью. Им не страшны скачки напряжения, от которых другие устройства могут выйти из строя.
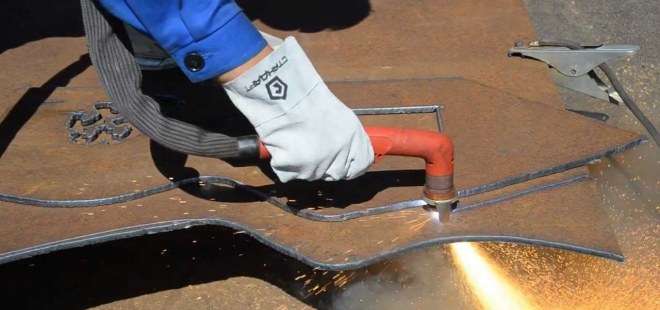
Резка по шаблону
У любого источника питания есть такая важная характеристика, как продолжительность включения (ПВ). У трансформаторных источников питания ПВ составляет 100%, это означает, что их можно использовать целый рабочий день, без перерыва на остывание и отдых. Но, конечно, есть у таких источников питания и недостатки, наиболее значимым из которых является их высокое энергопотребление.
Как выполняется ручная плазменная резка?
Первое, что необходимо сделать для того чтобы начать использование аппарата для плазменной резки металла, — это собрать воедино все его составные элементы. После этого инвертор или трансформатор подсоединяют к заготовке из металла и к сети переменного тока.
Далее технология резки предусматривает приближение сопла устройства к заготовке на расстояние порядка 40 мм и зажигание так называемой дежурной дуги, за счет которой будет осуществляться ионизация рабочего газа. После того как дуга загорелась, в сопло подается воздушно-газовый поток, который и должен сформировать плазменную струю.
Когда из рабочего газа сформируется плазменная струя, обладающая высокой электропроводностью, между электродом и деталью создается уже рабочая дуга, а дежурная автоматически отключается. Задача такой дуги состоит в том, чтобы поддерживать требуемый уровень ионизации плазменной струи. Случается, что рабочая дуга гаснет, в таком случае следует перекрыть подачу газа в сопло и повторить все описанные действия заново. Лучше всего, если нет опыта выполнения такого процесса, посмотреть обучающее видео, где подробно показана ручная резка металла.
Оценка статьи:

Поделиться с друзьями:
met-all.org
Плазменная резка металлов, все о раскрое плазмой
Для резки металлов используют несколько различных методов отличающихся друг от друга себестоимостью и эффективностью. Некоторые способы используются исключительно для промышленных целей другие также можно применять и в быту.- Содержимое:
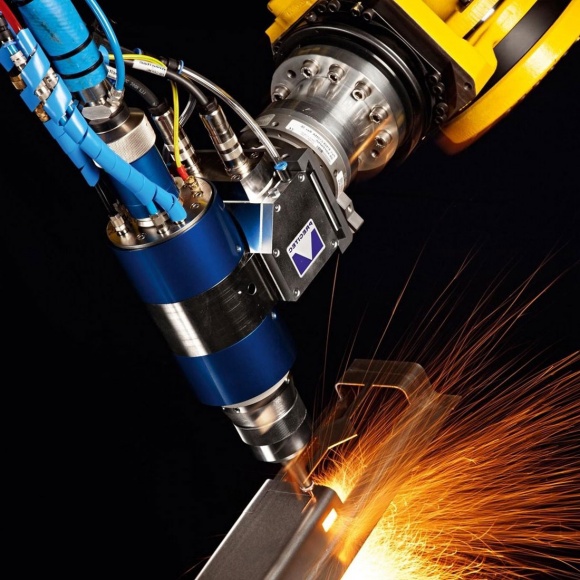
Основы резки металлов плазмой
Чтобы понять основы резки металла с помощью плазменного метода следует для начала уяснить, что же такое плазма? От правильного понимания того как устроен плазматрон и принципов работы с ним зависит качество конечного результата.Термическая плазменная обработка металлов зависит от параметров рабочей струи газа или жидкости, направленной под давлением на обрабатываемую поверхность. Для достижения необходимых результатов струю доводят до следующих характеристик:
Еще один важный момент, который следует учитывать, это то, что плазменная резка толстого металла практически не выполняется, так как это ведет к увеличенным материальным затратам и малоэффективно.
Характеристики и принцип резки металла плазмой
Основной принцип работы плазменной резки металла можно описать следующим образом:Существуют два основных способа обработки материалов, от которых зависят характеристики плазменной резки. А именно:
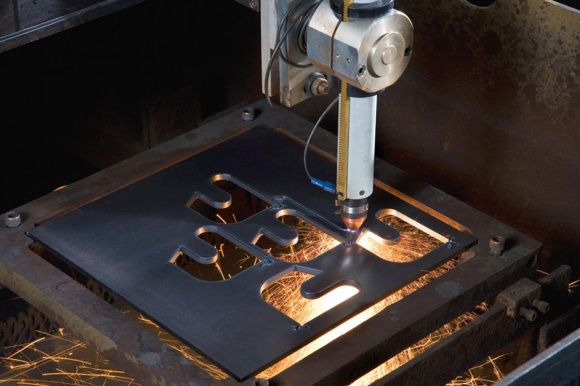
Плазменная резка металла работает как обычная дуговая, но без использования привычных электродов. Но эффективность способа обработки прямо пропорциональна толщине обрабатываемого материала.
Скорость и точность резки металла плазмой
Как и при любом другом виде термической обработки, при плазменной резке металла происходит определенное оплавление металла, что отражается на качестве реза. Существуют и другие особенности, которые являются характерными для этого метода. А именно:От профессионализма мастера во многом зависит качество выполнения работ. Чистый и точный рез с минимальным отклонением от необходимых размеров может выполнить только работник с профильным образованием. Без соответствующей подготовки выполнить фигурную резку вряд ли получится.
Плазменная резка цветных металлов
При обработке цветных металлов используются разные способы резки в зависимости от типа материала, его плотности и других технических характеристик. Для разрезания цветных сплавов требуется соблюдения следующих рекомендаций.Где применяется плазменный раскрой металла
Использование плазмотронов не зря пользуется такой большой популярностью. При относительно простой эксплуатации и незначительной стоимости ручной установки (по сравнению с другим оборудованием для резки) удается достичь высоких показателей относительно качества реза.Применение плазменной резки металла получило распространение в следующих сферах производства:
Применение станков с плазменной резкой не заменило ручных установок. Так художественная резка металла плазмой позволяет сделать уникальные детали точно соответствующие замыслу художника, для использования их в качестве декоративных украшений для заборов и лестниц, а также перил, ограждений и т. д.
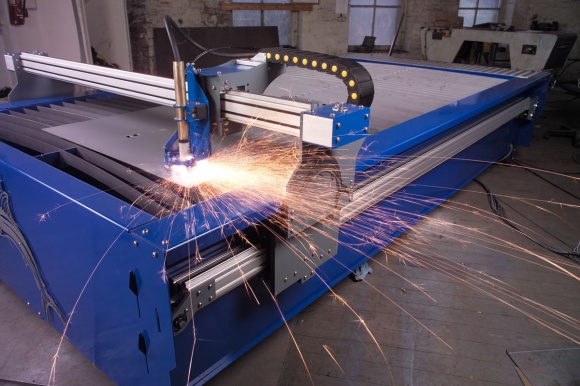
Резка металла плазмой – преимущества и недостатки
Без резки металла не может обойтись практически ни одно промышленное предприятие, так или иначе связанное с металлопрокатом. Быстрое разрезание листового материала на заготовки, декоративная фигурная резка металла плазмой, вырезание точных отверстий – все это можно выполнить достаточно быстро с помощью плазмотрона. Плюсы, которые имеет метод, заключаются в следующем:Все эти преимущества плазменной резки металла объясняют, почему метод пользуется настолько широкой популярностью не только в промышленных, но и бытовых целях.
Но говоря о плюсах необходимо заметить и некоторые отрицательные стороны:
Сравнение плазменной и лазерной резки металла
Отличие лазерной резки металла от плазменной заключается в методах воздействия на поверхность материала.Лазерные установки обеспечивают большую производительность и скорость обработки деталей, при этом после выполнения операции наблюдается меньший процент оплавленности. Минусом лазерного оборудования является его высокая стоимость, а также то, что толщина разрезаемого материала должна быть меньше 20 мм.
По сравнению с лазером плазмотрон имеет меньшую стоимость, более широкую сферу применения и функциональные возможности.
stroy-plys.ru
Плазменная резка металла - что это такое, технология
Плазменная резка металла хорошо подходит для разделывания высоколегированных сталей. Такой метод превосходит газовые резаки минимальной зоной прогрева, позволяющей быстро произвести рез, но избежать деформации поверхности от перегрева. В отличие от механических способов реза («болгаркой» или станком), плазмотроны способны выполнять разделывание поверхности по любому рисунку, получая уникальные цельные формы с минимальными отходами материала. Как устроенны и работают подобные аппараты? Какова технология процесса резки?
Что такое плазменная резка?
Плазменная резка металла и ее принципы работы основаны на усилении электрической дуги, путем разгона газом под давлением. Это увеличивает температуру режущего элемента в несколько раз, в отличие от пропан-кислородного пламени, что позволяет быстро осуществить рез, не дав высокому коэффициенту теплопроводности материала передать температуру на остальную часть изделия и деформировать конструкцию.
Плазменная резка металла на видео дает общее представление о происходящем процессе. Суть метода следующая:
Режущий элемент — ионизированная дуга плазмотрона, позволяет не только разделывать материал на части, но и сваривать его обратно. Для этого используют присадочную проволоку, соответствующую по составу для конкретного вида металла, а вместо обычного воздуха подается инертный газ.
Разновидности плазменной резки и принципов работы
Разделывание металлов ионизированной высокотемпературной дугой имеет несколько модификаций по используемому подходу и предназначению. В одних случаях электрическая цепь, для выполнения реза, должна замкнуться между плазмотроном и изделием. Это подходит для всех видов токопроводящих металлов. От аппарата исходит два провода, один из которых проходит в горелку, а второй крепится к обрабатываемой поверхности.
Второй метод заключается в горении дуги между катодом и анодом, заключенными в сопле плазмотрона, и способности осуществить рез этой же дугой. Данный способ хорошо подходит к материалам неспособным проводить ток. В этом случае от аппарата исходит один кабель ведущий к горелке. Дуга постоянно горит в рабочем состоянии. Все это относится к воздушно-плазменной резке металла.
Но бывают модели плазморезов, где в качестве ионизирующего вещества используется пар от заливаемой жидкости. Такие модели работают без компрессора. В них имеется небольшой резервуар для заливки дистиллированной воды, подающейся на электроды. Испаряясь, создается давление, усиливающее электрическую дугу.
Преимущества плазморезов
Принципы работы плазменной резки, использующей высокотемпературную дугу, позволяют получать ряд преимуществ перед другими видами разделывания металла, а именно:
Технология плазменной резки металла
Как работает плазменная резка показано на видео. Посмотрев несколько таких уроков можно приступать к самостоятельным пробам. Процесс осуществляется в следующей последовательности:
Используемое оборудование
Чтобы осуществлять плазменную резку используются различные аппараты и приспособления. Источник тока может быть небольших размеров, и содержать в себе трансформатор, несколько реле и осциллятор. Маленькие модели очень компактны для переноса и работы на высоте. Они способны разрезать металлы до 12 мм толщиной, чего достаточно для большинства видов работ на производстве и дома. Крупные аппараты имеют похожую схему устройства, но обладают более мощными параметрами за счет использования материалов большего сечения, и повышенными входящими значениями напряжения. Такие модели перевозятся на тележках, а работа с изделиями ведется плазмотроном, крепящимся к кронштейну. Им можно резать материалы толщиной до 100 мм.
Плазмотроны как больших, так и малых аппаратов устроены одинаково, но отличаются по размерам. У всех есть рукоятка и кнопка пуска. В каждом имеется электрод стержневой (катод) и внутреннее сопло (анод), между которыми горит дуга. Завихритель потоков направляет воздух и разгоняет температуру. Изолятор защищает внешние части от перегрева и преждевременного контакта электродов. Наружные сопла устанавливаются в зависимости от разрезаемой толщины. Наконечники закрывают сопло от брызг расплавленного металла. На конец плазмотрона могут одеваться различные насадки, помогающие сохранять дистанцию во время работы и убирающие нагар с фасок. Компрессор подает воздух через шланг, а его выход регулируется клапаном.
Изобретение плазменной резки позволило ускорить работу со многими легированными сталями, а точность линии реза и возможность производить изогнутые фигуры, помогают получать разнообразные изделия для производственных процессов. Понимание функционирования аппарата и сути выполняемой им работы поможет быстро освоить это полезное изобретение.
Поделись с друзьями
1
0
0
0
svarkalegko.com
Резка металла плазмой. Металлообрабатывающее оборудование
Плазменная резка применяется при обработке проводящих металлов. Обрабатываемый материал получает энергию от источника тока посредством ионизированного газа. Стандартная система включает источник тока, контур зажигания и резак, которые обеспечивают подачу электроэнергии, ионизацию и управление, необходимые для качественной высокопроизводительной резки различных металлов.
Выход источника постоянного тока задает толщину и скорость обработки материала и поддерживает дугу.
Контур зажигания выполняется в виде высокочастотного генератора переменного напряжения 5–10 тыс. В частотой 2 МГц, которое создает высокоинтенсивную дугу, ионизирующую газ до состояния плазмы.
Резак является держателем для расходных деталей — сопла и электрода — и обеспечивает охлаждение этих деталей газом или водой. Сопло и электрод сжимаются и поддерживают ионизированную струю.
Ручные и механизированные системы служат для разных целей и требуют разного оборудования. Только пользователь может определить, какая из них лучше всего подходит для его нужд.
Резка металла плазмой представляет собой термический процесс, при котором пучок ионизированного газа нагревает электропроводный металл до температуры, превышающей точку его плавления, и удаляет расплавленный металл через проделанное отверстие. Между электродом в горелке, к которому подведен отрицательный потенциал, и заготовкой с положительным потенциалом возникает электрическая дуга и происходит резка материала ионизированным потоком газа под давлением при температуре от 770 до 1400 °C. Струя плазмы (ионизированного газа) концентрируется и направляется через сопло, где она уплотняется и становится способной расплавить и разрезать самые разные металлы. Это основной процесс как для ручной, так и для механизированной плазменной резки.
Ручная резка
Ручная резка металла плазмой производится с помощью достаточно небольших устройств с плазменной горелкой. Они маневренны, универсальны и могут быть использованы для выполнения различных задач. Их возможности зависят от силы тока режущей системы. Параметры установок ручной резки варьируются от 7–25 А до 30–100 А. Некоторые устройства, однако, позволяют получить до 200 ампер, но они не являются широко употребительными. В ручных системах в качестве плазмообразующего и защитного газа обычно используется технический воздух. Они сконструированы таким образом, чтобы их можно было использовать с различным входящим напряжением, которое может изменяться от 120 до 600 В, а также использоваться в одно- или трехфазных сетях.
Ручная плазма для резки металла обычно используется в мастерских, занимающихся обработкой тонких материалов, заводских службах технического обслуживания, ремонтных мастерских, пунктах приема металлолома, при строительно-монтажных работах, в судостроении, автомастерских и художественных мастерских. Как правило, ее применяют для обрезки излишков. Обычный 12-амперный плазменный аппарат разрезает максимум 5-мм слой металла со скоростью около 40 мм в минуту. 100-амперное устройство режет 70-мм слой со скоростью до 500 мм/мин.
Как правило, ручная система выбирается в зависимости от толщины материала и желаемой скорости обработки. Устройство, которое обеспечивает высокую силу тока, работает быстрее. Однако при резке с большой силой тока становится труднее контролировать качество работы.
Машинная обработка
Механизированная резка металла плазмой производится на установках, которые, как правило, значительно больше ручных, и используется в сочетании с раскройными столами, в том числе с водяной ванной или с платформой, оборудованной различными приводами и двигателями. Кроме того, механизированные системы оборудуются ЧПУ и управлением высотой струи режущей головки, которая может включать в себя предустановку высоты резака и контроль напряжения. Механизированные системы плазменной резки могут устанавливаться на другое металлообрабатывающее оборудование, такое как штамповочные прессы, лазерные резаки или роботизированные системы. Размер механизированной конфигурации зависит от размера стола и используемой платформы. Раскроечный станок может быть меньше, чем 1200х2400 мм и больше, чем 1400х3600 мм. Такие системы не очень подвижны, поэтому до установки следует предусмотреть все их компоненты, а также место их расположения.
Требования к питанию
Стандартные источники питания обладают максимальным диапазоном силы тока от 100 до 400 А для кислородной резки и от 100 до 600 А для азотной. Многие системы работают в более низком диапазоне, например, от 15 до 50 А. Существуют системы с азотной резкой с силой тока 1000 А и выше, но они редки. Входное напряжение для механизированных плазменных систем составляет 200–600 В в трехфазной сети.
Требования к газу
Для резки мягкой и нержавеющей стали, алюминия, а также различных экзотических материалов обычно используются сжатый воздух, кислород, азот и смесь аргона с водородом. Их комбинации служат плазмообразующим и вспомогательным газом. Например, при резке мягкой стали пусковым газом часто является азот, плазмообразующим – кислород, а сжатый воздух используется как вспомогательный.
Кислород употребляется для мягкой углеродистой стали, потому что он производит высококачественные разрезы в материале толщиной до 70 мм. Кислород также может исполнять роль плазмообразующего газа для нержавеющей стали и алюминия, но результат получается не совсем аккуратным. Азот служит плазменным и вспомогательным газом, поскольку он обеспечивает отличную резку практически любого типа металла. Используется при больших токах и позволяет обрабатывать листовой прокат толщиной до 75 мм и в роли вспомогательного газа для азотной и аргон-водородной плазмы.
Сжатый воздух – наиболее распространенный газ как плазменный, так и вспомогательный. Когда производится слаботочный раскрой листового металла толщиной до 25 мм, оставляет окисленную поверхность. При резке воздухом, азотом или кислородом является вспомогательным газом.
Смесь аргона с водородом, как правило, используется для обработки нержавеющей стали и алюминия. Обеспечивает высококачественный разрез, и необходима для механизированной резки листов толщиной более 75 мм. Диоксид углерода также может быть использован в роли вспомогательного газа, когда производится резка металла плазмой азота, так как это позволяет работать с большинством материалов и гарантирует хорошее качество.
Смесь азота с водородом и метан также иногда применяются в процессе плазменной резки.
Что потребуется еще?
Выбор плазмы и вспомогательных газов – только два из важнейших решений, которые необходимо принимать во внимание при установке или использовании механизированной плазменной системы. Емкости для газа можно приобрести или арендовать, они доступны в различных размерах, и для их хранения необходимо создать соответствующие условия. Установка системы требует значительного количества электропроводки и труб для газа и охлаждающей жидкости. Помимо самой механизированной плазменной системы, требуется подобрать стол, раскроечный станок, ЧПУ и THC. OEM-производители обычно предлагают множество вариантов оборудования, которое подойдет для любой конфигурации устройства.
Нужна ли механизация?
Из-за сложности выбора механизированного процесса плазменной резки, необходимо уделить много времени исследованию различных конфигураций и критериев системы. Следует учесть:
Размер, форма и количество производимых частей может определять необходимое производственное промышленное оборудование – тип ЧПУ, стола и платформы. Например, производство деталей небольшого размера может потребовать платформы со специализированным приводом. Реечные приводы, сервоприводы, приводные усилители и датчики, используемые на платформах, определяют качество резки и максимальную скорость системы.
Качество и скорость также зависит от того, какое металлообрабатывающее оборудование, ЧПУ и газы используются. Механизированная система с регулируемым током и потоком газа в начале и в конце резки уменьшит расход материалов. Кроме того, с ЧПУ с большим объемом памяти и выбором возможных установок (например, высоты факела в конце разреза) и быстрая обработка данных (входной/выходной коммуникации) снизит простои и увеличит скорость и точность работы.
В конечном счете решение о покупке или обновлении механизированной системы плазменной резки или использовании ручной должно быть обоснованным.
Плазменная резка металла: оборудование
Hypertherm Powermax45 – переносной аппарат с большим числом стандартных компонентов на основе инвертора, т. е. биполярного транзистора с изолированным затвором. Работать с ним очень легко, независимо от того, режется ли тонкая сталь или листовой прокат толщиной 12 мм со скоростью 500 мм/минуту или 25 мм со скоростью 125 мм/мин. Устройство способно генерировать большую мощность для резки различных видов токопроводящих материалов, таких как сталь, нержавеющая сталь и алюминий.
Система питания имеет преимущество перед аналогами. Входное напряжение – 200-240 В однофазного тока силой 34/28 А при мощности 5,95 кВт. Изменения входного напряжения сети компенсируются технологией Boost Conditioner, благодаря которой резак демонстрирует повышенную производительность на низких напряжениях, при колебаниях входной мощности, а также при питании от генератора. Внутренние компоненты эффективно охлаждаются с помощью системы PowerCool, обеспечивающей повышенную производительность, время работы и надежность устройства. Другой важной особенностью этого продукта является соединение горелки FastConnect, которое облегчает механизированное использование и повышает универсальность.
Факел Powermax45 имеет конструкцию с двойным углом, который продлевает срок службы сопла и снижает эксплуатационные расходы. Он оснащен функцией Conical Flow, повышающей плотность энергии дуги, благодаря чему значительно сокращает дросс и производится высококачественная плазменная резка. Цена Powermax45 – 1800 $.
Hobart AirForce 700i
Hobart AirForce 700i обладает наибольшей режущей способностью данной линейки: номинальная толщина резки – 16 мм со скоростью 224 мм/мин, а максимальная – 22 мм. По сравнению с аналогами, рабочая сила тока устройства на 30% меньше. Плазменный резак подойдет для станций техобслуживания, ремонтных мастерских и при сооружении небольших построек.
Устройство отличается легким, но мощным инвертором, эргономичным пусковым предохранителем, эффективным потреблением воздуха и недорогими расходными материалами горелки, благодаря чему производится безопасная, качественная и недорогая плазменная резка. Цена AirForce 700i составляет 1500 $.
В комплект входит эргономичная ручная горелка, кабель, 2 сменных наконечника и 2 электрода. Потребление газа составляет 136 л/мин при давлении 621–827 кПа. Вес аппарата – 14,2 кг.
40-амперный выход обеспечивает исключительную производительность резки листового металла – быстрее, чем механические, газовые и плазменные устройства других изготовителей.
Miller Spectrum 625 X-treme
Miller Spectrum 625 X-treme – небольшой аппарат, достаточно мощный для резки различных видов стали, алюминия и других проводящих ток металлов.
Питается от сети переменного тока напряжением 120-240 В, автоматически подстраиваясь под поданное напряжение. Легкий и компактный дизайн делает устройство весьма портативным.
Благодаря технологии Auto-Refire дуга контролируется автоматически, избавляя от необходимости постоянно нажимать кнопку. Номинальная толщина резки при токе 40 А составляет 16 мм при скорости 330 мм/мин, а максимальная – 22,2 мм при 130 мм/мин. Потребляемая мощность – 6,3 кВт. Вес аппарата в ручном исполнении составляет 10,5 кг, а с машинным резаком – 10,7 кг. В качестве плазменного газа используется воздух или азот.
Надежность Miller 625 обеспечивается технологией Wind Tunnel. Благодаря встроенному высокоскоростному вентилятору пыль и мусор не попадают внутрь устройства. Светодиодные индикаторы информируют о давлении, температуре и мощности. Цена аппарата – 1800 $.
Lotos LTP5000D
Lotos LTP5000D – портативный и компактный плазменный аппарат. При весе 10,2 кг проблем с его перемещением не возникнет. 50-амперный ток, производимый цифровым преобразователем, а также мощный транзистор MOSFET обеспечивают эффективный рез мягкой стали толщиной 16 мм и 12 мм нержавеющей стали или алюминия.
Устройство автоматически подстраивается под напряжение и частоту сети. Длина шланга – 2,9 м. Вспомогательная дуга с металлом не контактирует, что позволяет использовать аппарат для резки ржавых, необработанных и окрашенных материалов. Устройство безопасно в использовании. Сжатый воздух, применяемый для резки, не вреден для человека. А крепкий ударопрочный корпус надежно защищает аппарат от попадания пыли и мусора. Цена Lotos LTP5000D – 350 $.
При покупке плазменного резака нужно всегда отдавать предпочтение качеству. Следует остерегаться искушения приобрести дешевый низкокачественный аппарат, так как его быстрый износ в долгосрочной перспективе приведет к гораздо большим затратам. Конечно, переплачивать также не стоит, есть достаточно достойных бюджетных вариантов без аксессуаров и высоких мощностей, которые могут никогда не понадобиться.
fb.ru
Плазменная резка металла: технология и нюансы работы
Машиностроение и тяжелую промышленность нельзя представить без сварки и резки металлических поверхностей. На крупных производственных объектах, занимающихся обработкой, применяется специальная резка металла плазмой.
Плазма, что это?
Под плазменным элементом понимают токопроводящий газ, ионизирующийся под действием высоких температур. Значение температурного показателя в рабочей зоне достигает 25 000 – 30 000 градусов. Газ подается к обрабатываемому изделию под давлением, то есть струей.
Эта разновидность резки подразумевает сочетание двух дуг – газовой и электрической. Источник плазменной резки производится в специальном приборе, называемым плазмотроном.
Как устроен плазморез?
Плазменный раскрой металла включает нескольких составных систем:
Энергоисточник
В качестве энергобазы может выступать:
Плазмотрон
Это устройство представляет собой электроплазменный резак, благодаря которому разрезается металлическая деталь. Он считается главным «механизмом» плазмореза.
Плазмотрон включает:
Горелка плазмореза
Необходимо предварительно определиться с материалом, который необходимо прорезать и условиями работы.
Стоит отметить, что системы с медным соплом обладают значительной прочностью и быстро охлаждаются воздушными массами. А это очень хорошо.
На рукояти плазморезов подобного вида есть возможность закрепить вспомогательные элементы, поддерживающие насадку сопла на требуемой дистанции. Это облегчает процесс эксплуатирования.
Для разреза тонкого металла следует выбрать установку, в горелку которой поступает кислород, а для толстого изделия – азот.
Показатели мощности
Главным принципом в работе плазменной резки считается мощность. Выбирая мощность агрегата необходимо учитывать свойства изделия, с чем придется работать. По этому признаку будут отличаться габариты сопла и вид газообразной смеси.
Чтобы справиться с изделием из металла 30 мм достаточно выбрать мощность агрегата 50-90А.
Если толщина реза превышает 30 мм, то профессионалы советуют приобрести плазморез с мощностью 100-170А.
Покупая агрегат, следует учесть силу тока и напряжение, которое он способен выдержать.
Быстрота, время, затраченное на разрез
Данное значение измеряется в см, которые разрезает агрегат за 1 или 5 мин
Если на устройстве указывается, что длительность эксплуатирования равна 80 процентам, то этот показатель означает, что резак будет работать 8 мин, а далее 2 мин аппаратура будет остывать.
Если при эксплуатировании потребуется делать длинные разрезы, то рационально выбирать устройства с увеличенной продолжительностью работы.
Раскрой струей плазмы
Принцип оптимальной работы плазменной резки заключается в разрезании металлических деталей струей плазмы, не проводящей электричество. При раскрое этим способом дуга возникает между насадкой плазмотрона и рабочим электродом, а возделываемое изделие в электрической цепочке не участвует. Для разреза детали применяется плазменная струя.
Плазменно – дуговая резка характеризуется тем, что воздействию подвергаются токопроводящие элементы. Дуга при этом способе образуется между возделанной деталью и рабочим электродом, ее основание совмещается с электроплазменным потоком. Струя возникает в результате поступления газа и последующей его ионизацией.
Метод плазменно-дуговой резки используется при:
Плазменно-дуговая резка достаточно эффективна и хорошо себя зарекомендовала в возделывании металлов.
Разновидности плазменного раскроя
Разрезание поверхностей из металла с использованием плазмы различают на несколько типов, все зависит от атмосферы процесса:
Технологические особенности резки
Как работает плазменная резка? Принцип работы плазмореза заключается в локальном нагревании поверхности металла в зоне раздела и его последующем плавлении. Нагревание происходит потоком плазмы, который формируется путем специального оборудования. Технологические особенности получения плазмы выглядят так:
Для полученной струи плазмы для резки металла плазмой характерно: яркая потоковая вспышка и усиленный выход из сопла устройства. Струя разогревает поверхность и расплавляет деталь в точечной области воздействия, в результате чего выполняется резка металла плазмой.
Как осуществляется ручная электроплазменная разрезка?
Принцип плазменной резки металла начинается с подключения устройства, тем самым собирая все составные части в единую систему. Далее инвертор либо трансформатор подключают к сети переменного тока и металлической детали.
Осуществление резки предусматривает удерживание сопла агрегата к обрабатываемой поверхность на дистанцию 4 см и вспышка дежурной дуги, вследствие которой будет возникать ионизация газа. Далее в сопло поступает газообразный воздух, в результате чего должен сформироваться электроплазменный поток.
Стоит отметить, что когда электроплазменная струя сформирована, первоначальная дуга отключается автоматом. Задача вспомогательной струи заключается в поддержание ионизации потока плазменного компонента. Бывают случаи, когда рабочая дуга угасает, значит нужно перекрыть доступ газа в сопло и повторить процедуру заново.
Плюсы и минусы плазменного раскроя
К основным положительным характеристикам применения плазменной системы относят следующие аспекты:
К минусам электроплазменной технологии относят:
Также существенным недостатком при работе плазменной установки считается отклонение от перпендикуляра резания на угол не более 50 градусов.
Основные аспекты правил безопасности
Технология плазменной резки металла является опасной для рабочего и окружающих. При осуществлении операции профессионалы своего дела рекомендуют использовать защитный костюм сварщика и специальный щиток с затемненными стеклами. При разрезе металлических поверхностей возможно воздействие нежелательных эффектов:
Температурные показатели при резке плазмой достигают тысяч градусов по Цельсию. Человек может получить ожоги во время проведения резки. Ожоговый риск снижается, если процесс автоматизирован. Излучение, которое возникает в период эксплуатирования устройства способно вызвать ожоги глазного сектора работающего. Чтобы это не произошло достаточно пользоваться маской либо щитком с защитными темными стеклами. На практике щиток менее комфортен, так как приходится постоянно придерживать рукой, а это сковывает и ограничивает движения сварщика.
Техника безопасности на месте резки металла плазмой включает в себя внимательный осмотр оборудования на наличие неисправностей. Стоит помнить, что неисправным устройством пользоваться нельзя, даже если очень нужно. При проведении резания не следует стучать плазмотроном для удаления расплавленных остатков. В противном случае он повредится. Также во время проведения работ необходимо постоянного контролировать напряжение сети.
Плазменно-дуговая резка и раскрой металлических поверхностей струей плазмы достаточно широко используются в промышленном секторе. Плазменная современная резка труб с ЧПУ по праву является незаменимым оборудованием для производственных компаний, так как все можно сделать с высокой точностью и производительностью. Плазморезом можно пользоваться для разделения различных элементов. Что важно, то устройство подходит и для спаивания. Например, с его помощью проводятся различные операции закалки, зачистки, а также сваривание припоями. Металлическая поверхность в этой ситуации быстрее охлаждается, нежели при стандартной резке кислородом.
Внешние особенности
При плазморезке собственными силами следует обратить внимание на компактность прибора. Ими просто управлять и не требуют особого опыта. Если чувствуете неуверенность в своих силах, то рекомендуем посмотреть обучающее видео.
oxmetall.ru
Лазерная или плазменная резка металла: что лучше?
Технологии лазерной и плазменной резки материалов имеют одну область применения и являются конкурирующими технологиями. Потребитель задаётся естественным вопросом: "Лазерная или плазменная резка металла: что лучше?". Обо всём по порядку.
Лазерная резка металла
В качестве инструмента при лазерной резке очень упрощенно используется сфокусированный лазерный луч. При непрерывном режиме работы лазерный луч нагревает обрабатываемый материал до температуры плавления, полученный расплав удаляется струей газа под высоким давлением. При сублимационной лазерной резке металла материал под воздействием лазерного импульса испаряется в зоне резки.
Плазменная резка металла
Плазменная резка заключается в проплавлении разрезаемого металла за счет теплоты, генерируемой сжатой плазменной дугой, и интенсивном удалении расплава плазменной струей. Плазменная дуга получается из обычной в специальном устройстве – плазмотроне – в результате ее сжатия и вдувания в нее плазмообразующего газа.
Преимущества лазерной резки металла
Лазерная резка, в отличие от плазменной, обеспечивает получение более точных по перпендикулярности кромок и более узких прорезей применительно к характерному для процесса диапазону толщин. Сфокусированное лазерное излучение позволяет нагревать достаточно узкую зону обрабатываемого материала, что уменьшает деформации при резке. При этом получаются качественные и узкие резы со сравнительной небольшой зоной термического воздействия. Дополнительным преимуществом лазерной резки является точность получаемых деталей, особенно при образовании вырезов, небольших фигур сложной конфигурации и четко очерченных углов. Одним из главных достоинств данного вида обработки является её высокая производительность. Лазерная резка особенно эффективна для стали толщиной до 6 мм, обеспечивая высокие качество и точность при сравнительно большой скорости разрезания. При лазерной обработке на тонколистовом материале не остается окалины, что позволяет сразу передавать детали на следующую технологическую операцию. Кромки реза у листов толщиной до 4 мм и меньше остаются гладкими и прямолинейными, а у листов большей толщины кромки имеют некоторые отклонения со скосом примерно 0,5°. Диаметры отверстий, вырезанных лазером, имеют в нижней части несколько больший диаметр, чем в верхней, но остаются круглыми и хорошего качества. Для металла толщиной 20–40 мм лазерная резка применяется значительно реже плазменной, а для металла толщиной свыше 40 мм – практически не используется.
Преимущества плазменной резки металла
Плазменная резка, по сравнению с лазерной, эффективна при обработке значительно более широкого по толщине диапазона листов при относительно хорошем качестве реза. Данный вид обработки экономически целесообразен для резки алюминия и сплавов на его основе толщиной до 120 мм; меди толщиной до 80 мм; легированных и углеродистых сталей толщиной до 150 мм; чугуна толщиной до 90 мм. На материалах толщиной 0,8 мм и меньше, использование плазменной резки находит ограниченное применение. Для плазменной резки характерна некоторая конусность поверхности реза 3° - 10° . При вырезании отверстий, особенно на больших толщинах, наличие конусности уменьшает диаметр нижней кромки отверстия, на детали толщиной 20 мм разница диаметра входного и выходного отверстия может составить 1 мм. Следует учитывать, что плазменная резка металла имеет ограничения по минимальному размеру отверстия. Отверстия хорошего качества получаются при диаметре не меньшем толщины разрезаемого плазмой листа. При данном способе реза присутствует кратковременный термический обжиг кромки разрезаемого металла. Все это приводит к ухудшению качества деталей. Чаще всего на этих деталях присутствует небольшая окалина, которая легко удаляется.
Лазерная или плазменная резка металла?
Итак, лазерная или плазменная резка металла: что лучше? Сравнивая два описанных выше способа, можно прийти к выводу, что результаты лазерной и плазменной резки примерно одинаковы при обработке металлов малой толщины. Если говорить об обработке металлов, толщина которых превышает 6 мм, то здесь лидирующие позиции занимает плазменная технология, которая превосходит лазерную и по скорости выполнения операций, и по уровню энергетических затрат. Но следует учитывать, что качество деталей, полученных при лазерной резки на малых толщинах, значительно выше, чем при использовании плазмы, и целесообразным является использование этой технологии при получения изделий сложной формы, для которых особое значение играет высокая точность и максимальное соответствие проекту. Следует отметить, что лазерное излучение, в отличие от плазмы, является широкоуниверсальным инструментом (кроме резки оно применяется также для маркировки, упрочнения, разметки и т.п.). Также сроки службы расходных материалов при лазерной резке несравнимо более длительные, чем при плазменной.
Цена станка и стоимость эксплуатации
Немаловажной характеристикой является стоимость установок. Станки плазменной резки дешевле лазерных, но при сравнении стоимости эксплуатации установок следует учитывать ряд одинаковых или аналогичных параметров, существующих при работе этих установок и влияющих на эксплуатационные расходы. Это относится, в первую очередь, к стоимости расходных материалов, а также электроэнергии и вспомогательных газов.
Лазерная резка металла - расходные материалы
К числу основных газов, используемых при лазерной резке, относятся воздух и кислород (при резке углеродистой стали) или азот (при резке коррозионно-стойкой стали и алюминия). Энергетические расходы включают расходы на электроэнергию, потребляемую самой установкой, электроэнергию для лазера и охлаждающего устройства, а к числу расходуемых компонентов относятся внутренняя и внешняя оптика, линзы, сопла, фильтры. Периодичность замены расходных компонентов, используемых в установке лазерной резки, составляет от нескольких недель до нескольких лет, в зависимости от многих параметров.
Плазменная резка металла - расходные материалы
При осуществлении плазменной резки в основном используют воздух и кислород. К энергетическим расходам здесь относят расходы на электроэнергию для создания плазмы и для питания самой установки для плазменной резки. В числе расходуемых компонентов – сопло, электрод, рассекающее кольцо, крышки, керамическая направляющая и экран. Как вариант можно использовать слаботочные электроды и сопла, что ведет к повышению качества резки, но при этом снижается ее производительность.
Производительность
Другие параметры, например, количество вырезаемых отверстий на одну деталь, оказывают влияние на часовую стоимость эксплуатации плазменной установки в большей степени, чем на тот же показатель для лазерной, поскольку расходуемые компоненты, например, сопла и электроды рассчитаны на определенное количество стартов или прошивок. Чем больше отверстий требуется прошивать в детали для ее резки, тем выше стоимость часа работы плазменной установки.
Качество деталей
Сравнивая качество получаемых деталей и исходя из стоимости затрат на расходные материалы, можно прийти к выводу, что лазерная резка эффективнее плазменной для более тонких листовых материалов, а плазменная — для более толстых. Следует учитывать, что эксплуатационные расходы для обоих типов резки имеют широкий разброс и во многом определяются геометрическими параметрами заготовки, числом отверстий в ней, видом и толщиной разрезаемого материала.
Параметры | Лазерная резка | Плазменная резка |
Ширина реза | Ширина реза постоянна (0,2 - 0,375 мм) | Ширина реза не постоянна из-за нестабильности плазменной дуги (0,8 - 1,5 мм) |
Точность резки | Как правило ±0,05 мм (0,2 - 0,375 мм) | Зависит от степени износа расходных материалов ±0,1 - ±0,5 мм |
Конусность | Менее 1° | 3° - 10° |
Минимальные отверстия | При непрерывном режиме диаметр примерно равен толщине материала. Для импульсного режима минимальный диаметр отверстия может составлять одну треть толщины материала. | Минимальный диаметр отверстий составляет 1,5 от толщины материала, но не менее 4мм. Выраженная склонность к эллиптичности, (возрастает с увеличением толщины материала). |
Внутренние углы | Высокое качество углов | Происходит некоторое скругление угла, из нижней части среза удаляется больше материала, чем из верхней. |
Окалина | Обычно отсутствует | Обычно имеется (небольшая) |
Прижоги | Незаметны | Присутствуют на острых наружных кромках деталей |
Тепловое воздействие | Очень мало | Больше, чем при лазерной резке |
Производительность резки металла | Очень высокая скорость. При малых толщинах обычно с заметным снижением при увеличении толщины, продолжительный прожиг больших толщин. | Быстрый прожиг; очень высокая скорость при малых и средних толщинах обычно с резким снижением при увеличении толщины. |
Лазерная резка металла
Лазерная резка металла особенно эффективна для стали толщиной до 6 мм, обеспечивая высокие качество и точность при сравнительно большой скорости разрезания. Кромки реза у листов толщиной до 4 мм и меньше остаются гладкими и прямолинейными, а у листов большей толщины кромки имеют некоторые отклонения со скосом примерно 0,5о. Диаметры отверстий, вырезанных лазером, имеют в нижней части несколько больший диаметр, чем в верхней, но остаются круглыми и хорошего качества.
Плазменная резка металла
Плазменная резка металла, по сравнению с лазерной, эффективно при обработке значительно более широкого по толщине диапазона листов при относительно хорошем качестве реза. Данный вид обработки экономически целесообразен для резки алюминия и сплавов на его основе толщиной до 120 мм; меди толщиной до 80 мм; легированных и углеродистых сталей толщиной до 150 мм; чугуна до 90 мм. На материалах толщиной 0,8 мм и меньше, использование плазмы находит ограниченное применение.
Итак: что лучше?
Таким образом, лазерная резка эффективнее плазменной для более тонких листовых материалов, а плазменная - для более толстых. Следует учитывать, что эксплуатационные расходы для обоих типов резки имеют широкий разброс и во многом определяются геометрическими параметрами заготовки, числом отверстий в ней, видом и толщиной разрезаемого материала.
Лазерная или плазменная резка металла: что лучше?
www.novator-grp.ru
Резка плазмой металла
Новые технологии обработки твердотельных материалов позволяют быстро и качественно справиться практически с любой структурой. Металл легко поддается резке с помощью абразивных и лазерных устройств. Даже традиционные механические головки с алмазными дисками обеспечивают качественный раскрой толстых листов. Одним из самых эффективных способов решения подобных задач является резка металла плазмой. Фото, представленное ниже, иллюстрирует данный процесс.
Общие сведения о технологии
Методика специально рассчитывается на обработку металла без применения пильных инструментов. Как и другие техники термического раскроя, этот способ заключается в создании реза в структуре материала посредством точечного воздействия луча на рабочий участок. Непосредственно резка плазмой выполняется за счет теплового излучения, источником которого является специальный инструмент. Как правило, это машина, снабженная плазмотроном.
В целом процесс напоминает классическую сварку, но есть и принципиальные отличия. К примеру, выдувание воздушных потоков в результате образует полость с расплавленной массой. Подготовленная таким образом основа более податлива, поэтому резка плазмой дает возможность оператору получать раскрой с высокой точностью независимо от параметров заготовки.
Применение резки плазмой
Оборудование для плазменной обработки позволяет выполнять операции с заготовками из цветных и черных металлов. Также в зависимости от устройства пользователь может резать сплавы и тугоплавкие заготовки толщиной порядка 40 мм. Данная технология успешно применяется в художественных мастерских. Отчасти эту сферу использования таких инструментов можно сравнить с ковкой. Специалисты выполняют оригинальные декоративные изделия для украшения ворот, оград и мебели. Изготовление предметов с криволинейной линией раскроя также позволяет выполнять резка плазмой. Фото ниже демонстрирует пример фигурной обработки.
Кроме творческих направлений метод используется на производствах, а также в строительной сфере. Плазмой можно обрабатывать любые металлы, которые проводят электрический ток. В некоторых областях важна не столько резка заготовок, сколько обработка кромок. Подобные операции также выполняют плазморезы.
Принцип действия плазмореза
Начинается процесс с того, что между заготовкой и электродом в плазморезе формируется электрическая дуга. Иногда отдельное зажигание происходит в контакте между соплом аппарата и электродом. Образование плазменного потока реализуется за счет газа, подаваемого в головку прибора. Далее под высоким давлением происходит выработка электрической дуги с температурным режимом порядка 15000 °С. В зависимости от характеристик материала применяется та или иная газовая среда. Например, резка листового металла плазмой с применением водорода или азота подходит для цветных сортов. С другой стороны, кислород будет оптимальным вариантом для обработки черного металла. В процессе работы от оператора требуется полный контроль активной струи. Сразу после активации электрической дуги начинается выработка дежурного потока плазмы. Управляя аппаратом, пользователь регулирует параметры формируемого факела, направляя его на линию реза в заготовке.
Виды оборудования для резки
Как правило, плазморезы делят на трансформаторные аппараты и устройства инверторного типа. Первую группу представляют модели, специально рассчитанные на резку металлических листов толщиной 35-40 мм. Инверторы отличаются скромными размерами и в то же время более высокой производительностью по сравнению с трансформаторами. Однако, высокое качество обработки при меньших затратах электроэнергии обеспечивается только в случаях, если осуществляется резка плазмой металла, толщина которого не превышает 30 мм. Также аппараты различаются по типу системы охлаждения форсунки – в частности, существуют жидкостные и воздушные модели. В первом случае охлаждающей средой выступает струя воды, а во втором – газ. В крупных агрегатах чаще применяется вода, что позволяет увеличивать точность операций. В целях обеспечения высокого рабочего ресурса технологи рекомендуют использовать газовые системы охлаждения.
Чем выгодна резка плазмой?
Обычно конкуренция между технологиями резки твердотельных материалов происходит в параметрах точности и скорости реза. Однако, появление новых методов расширило возможности обработки, увеличив и базовые требования к качеству операций. По совокупности рабочих показателей плазменная резка является одной из самых выгодных технологий такого типа. В первую очередь это обусловлено возможностью точечного локального раскроя без деформации окружающей зоны. Даже резка нержавеющей стали плазмой выполняется без термической деформации заготовки, хотя для обработки такого материала требуется использование аппарата высокой мощности. Кроме того, подчеркивается высокая скорость выполнения раскроя. Если подобрать соответствующую силу тока, то с тонким листом можно справиться за считаные секунды без потери в качестве.
Что учесть в выборе плазмореза?
Как уже отмечалось, в выборе устройства немалое значение имеет сила тока аппарата, которая позволит справляться с тем или иным сортом металла. Например, модели на 40-50 Ампер подходят для работы с латунью, медью, алюминием и другими цветными металлами, но их потенциала недостаточно для качественной и уверенной резки стали. Для работы с черными сортами металла желательно изначально ориентироваться на аппараты, сила тока которых составляет не менее 100 А. И это без учета толщины заготовки. Как правило, резка плазмой выполняется из расчета 5 А на 1 мм. Также стоит учитывать продолжительность активной работы плазмореза. У представителей начального уровня, к примеру, этот интервал составляет не более 10 мин., после чего оператору приходится делать технический перерыв.
Заключение
При всех достоинствах технологии плазменной обработки, она не является лучшим способом резки металла. Например, гидроабразивная методика отличается возможностью выполнения раскроя в заготовках практически любой толщины. При этом техника обходится дешевле в обслуживании и требует минимальных энергозатрат. В свою очередь, резка плазмой металла предлагает высокую скорость и соответствующее качество результата. Что самое важное, техническая организация данного процесса предполагает лишь приобретение специального аппарата. Использовать же плазморез может любой желающих в бытовых условиях – но, конечно, при надлежащей подготовке. Для сравнения, абразивная операция не обходится без применения массивных агрегатов, подающих струи воды или воздуха в смеси с частицами песка.
fb.ru