- МНЖМц 30-1-1. 30% его состава это никель, 1% железа и 1% марганца.
- МН19 по своему составу отличается от вышеуказанной марки отсутствием железа и марганца: 19% никель, остальное медь.
- При изготовлении узлов и деталей морской промышленности: охладители, расширительные бочки и прочее.
- В электротехнике из сплава мельхиора производят устройства для преобразования тепловой энергии в электрическую – термогенераторы. Помимо этого, мельхиор является материалом для изготовления особо точных резисторов.
- Мельхиор служит сырьем для изготовления медицинского инструмента: хирургические пинцеты, скальпели, офтальмоскопы и прочее.
- Эстетические свойства мельхиора позволили ему занять определённую нишу в ювелирном деле, изготавливая ювелирные украшения.
- Производят столовые приборы и посуду.
- Мельхиор активно используется в нумизматике при изготовлении монет. Так, в плане на 2018 год Центрального банка РФ указано о чеканке юбилейных монет номиналом в 10 рублей из сплава мельхиора на сумму 15 000 000 руб.
- Мельхиор применяется при производстве трубопроводов. Причем изготовляют как трубы, так и фитинги для их соединения. Сюда относятся переходники, тройники, крестовины, ниппеля, накидные гайки, шаровые краны, дроссели и прочее.
- Самое простое – это осмотреть изделие на предмет наличия проб серебра. Мельхиоровый сплав, как правило, имеет только клеймо, например, «МН» – медь и никель.
- Также вид металла определяют с помощью воды. Изделие погружают в воду на несколько часов. Если по истечении времени поверхность воды покроется зеленоватой пленкой, значит это мельхиор.
- Одним из надежных способов определения мельхиора является использование ляписного карандаша. При натирании его о сплав на поверхности металла проявляются темные пятна.
- Нанесение капли йода на серебро оставит на нем пятно, в то время как на мельхиоре нет. Недостатком данного метода трудность удаления этого пятна впоследствии.
- ↑ Мельхиор — Большая советская энциклопедия. — М.: Советская энциклопедия. 1969—1978.
зоны Гинье-Престона;
кристаллы метастабильной фазы;
кристаллы стабильной фазы.
- Стальная труба размеры водопроводная
- Труба стальная бесшовная горячедеформированная гост 8732 78
- Теплоемкость нержавеющей стали
- Обозначение легирующих элементов в стали
- Прокат круглый стальной
- Стали сплавы
- Труба водопроводная стальная размеры
- Шлифованная нержавеющая сталь
- Гост трос стальной гост 2688
- Типы стали
- Лист стальной оцинкованный гост
2)Классификация медных сплавов. Латуни и бронзы, их состав, марки, свойства, применение. Сплав в состав которого не входит медь мельхиор латунь дюралюминий сталь
Мельхиор состав сплава, свойства, применение
Французские ученые Майо и Шорье в начале 19-го века исследовали возможности модифицирования медных сплавов. Четыре года экспериментов показали, что добавление никеля в состав сплава увеличивало коррозионные свойства. Первоначально сплав назвали Майшор, по первым трем буквам изобретателей. Активное использование сплава в Германии трансформировало его название с учетом немецкого произношения – мельхиор, которое и используется до сих пор. О том, что из себя представляет сплав и по каким причинам он так полюбился немцам, и пойдет речь ниже.
Мельхиоровые сплавы: виды и химический состав
Мельхиор представляет собой сплав меди, основным легирующим элементом которого является никель. Для увеличения коррозионной стойкости к морской воде в сплав добавляют соединения железа и марганца.
Существует около 65 видов мельхиора, но основное распространение в производстве получили:
Известен также трехкомпонентный медноникелевый сплав – нейзильбер. Помимо никеля и меди, его состав содержит 13-45% цинка. Нейзильбер в сравнении с мельхиором характеризуется более высоким значением прочности. Хорошо обрабатывается давлением. В свойстве сопротивляться коррозии сплав нейзильбера уступает мельхиору, но при этом достаточно устойчив к большинству соляных растворов и органических кислот.
Физикомеханические характеристики
Сплав мельхиор внешне похож на серебро, но отличается меньшим значением плотности, которая составляет 8900 кг\м3. Температура плавления мельхиора зависит от марки сплава и колеблется в пределах 1190-1230 ºС.
Удельное электрическое сопротивление мельхиора – 285 нОм*м, что выше аналогичного показателя меди почти в 20 раз. Уменьшение в сплаве содержания железа и марганца способствует свойству проводить электрический ток.
Мельхиор обладает высоким значением температурного коэффициента линейного расширения 16*10-6 1\Со. Сплав не реагирует на магнитное поле.
Прочностные характеристики мельхиора сравнимы с аналогичными показателями стали Ст.3. Временное сопротивление на разрыв находится в пределах 390-400 МПа. Сплав мельхиор не отличается высокой твердостью. В среднем она составляет 65-70 единиц по шкале Бринелля.
Для увеличения твердости сплав подвергают термической обработке, в которую входит нагрев до температуры 250-300 Со и медленное охлаждение в печи. Также механические свойства мельхиора повышает нагартовка его поверхности.
Мельхиор считается высокопластичным сплавом. Относительное удлинение на сжатие МН19 равно 35%. Введение марганца и железа в состав мельхиора снижает пластичность. Так, относительное удлинение на сжатие сплава МНЖМц 30-1-1 уже составляет 25%.
Химические характеристики
Мельхиор относится к группе коррозионностойких материалов. Его отличительной особенностью является повышенная устойчивость к воздействию морской и пресной воды, а также насыщенного водяного пара.
Мельхиор не растворяется в солях, не вступает в химические реакции с большинством органических кислот. Сплав не окисляется при температурах до 150ºС.
Технологические характеристики
Сплав мельхиор подвергается всем типам технологических операций. По причине наличия высокой пластичности легко поддается горячей и холодной обработке давлением: штамповке, ковке и чеканке. Обладает и высокой скоростью обработки резанием данный сплав.
Также мельхиор хорошо поддается пайке. Для того, чтобы швы не уступали в своих прочностных свойствах основному сплаву, используют специальные оловянно-свинцовые и серебряные припои.
Область применения
В силу всех вышеперечисленных качеств мельхиоровые сплавы нашли следующее использование в разных отраслях производства:
Ценообразование
Стоимость на мельхиоровые сплавы образуется исходя из значения котировок меди и никеля на мировых биржах цветных металлов. В основном пункты приёма металлолома ориентируются на лондонскую биржу.
Наиболее ценны мельхиоры, в которых больше содержания никеля в составе. Связано это с его высокой стоимостью.
Особое внимание стоит обратить на состояние поверхности при сдаче лома мельхиора. Следы от удаления ржавчины, а уж тем более ее наличие, сильно снижает стоимость лома на рынке цветных металлов.
Также немаловажное значение имеет форма проката. Самым ценным считается мельхиоровый круг, т. к. при одинаковом весе мельхиоровая труба занимает больше места при транспортировке. Соответственно, увеличиваются затраты пунктов приема на перемещение металлолома.
Также влияет на показатель стоимости объем поставок. Как правило, металлоприёмщики делаются наценку при работе с мельхиоровым ломом свыше 50 килограмм. Происходит это из-за уменьшения времени на реализацию продукции: чем больше лома, тем быстрее его можно отправить на переработку.
Мельхиор стоит меньше, чем чистые металлы. Причиной этому служит высокая стоимость на проведения переработки: отделения исходных компонентов друг от друга. На октябрь 2017 года средняя цена на мельхиор за грамм по России составляет 0,2 рубля.
Как отличить серебро от мельхиора
Определение типа материала возникает при оценке стоимости изделия. Стоит отметить, что наиболее точную информации об этом вы можете получить непосредственно у специалистов ювелирного дела. Но также существуют несколько способов отличить серебро от мельхиора в домашних условиях:
Рейтинг: 0/5 - 0 голосов
prompriem.ru
6. Сплавы на основе меди. Латуни и бронзы: маркировка, термическая обработка, применение.
Медь имеет гранецентрированную кубическую решетку. Плотность меди 8,94 г/см3, температура плавления 1083oС.
Характерным свойством меди является ее высокая электропроводность, поэтому она находит широкое применение в электротехнике. Технически чистая медь маркируется: М00 (99,99 % Cu), М0 (99,95 % Cu), М2, М3 и М4 (99 % Cu).
Механические свойства меди относительно низкие: предел прочности составляет 150…200 МПа, относительное удлинение – 15…25 %. Поэтому в качестве конструкционного материала медь применяется редко. Повышение механических свойств достигается созданием различных сплавов на основе меди.
Различают две группы медных сплавов: латуни – сплавы меди с цинком, бронзы – сплавы меди с другими (кроме цинка) элементами.
Латуни.
Латуни могут иметь в своем составе до 45 % цинка. Повышение содержания цинка до 45 % приводит к увеличению предела прочности до 450 МПа. Максимальная пластичность имеет место при содержании цинка около 37 %.
При сплавлении меди с цинком образуется ряд твердых растворов (рис.21.2).
Рис.21.2. Диаграмма состояния медь – цинк
Из диаграммы состояния медь – цинк видно, что в зависимости от состава имеются однофазные латуни, состоящие из – твердого раствора, и двухфазные () – латуни.
По способу изготовления изделий различают латуни деформируемые и литейные.
Деформируемые латуни маркируются буквой Л, за которой следует число, показывающее содержание меди в процентах, например в латуни Л62 содержится 62 % меди и 38 % цинка. Если кроме меди и цинка, имеются другие элементы, то ставятся их начальные буквы ( О – олово, С – свинец, Ж – железо, Ф – фосфор, Мц – марганец, А – алюминий, Ц – цинк). Количество этих элементов обозначается соответствующими цифрами после числа, показывающего содержание меди, например, сплав ЛАЖ60-1-1 содержит 60 % меди, 1 % алюминия, 1 % железа и 38 % цинка.
Однофазные – латуни используются для изготовления деталей деформированием в холодном состоянии. Изготавливают ленты, гильзы патронов, радиаторные трубки, проволоку.
Для изготовления деталей деформированием при температуре выше 500oС используют () – латуни. Из двухфазных латуней изготавливают листы, прутки и другие заготовки, из которых последующей механической обработкой изготавливают детали. Обрабатываемость резанием улучшается присадкой в состав латуни свинца, например, латунь марки ЛС59-1, которую называют “автоматной латунью”.
Латуни имеют хорошую коррозионную стойкость, которую можно повысить дополнительно присадкой олова. Латунь ЛО70-1 стойка против коррозии в морской воде и называется “морской латунью“.
Добавка никеля и железа повышает механическую прочность до 550 МПа.
Литейные латуни также маркируются буквой Л, После буквенного обозначения основного легирующего элемента (цинк) и каждого последующего ставится цифра, указывающая его усредненное содержание в сплаве. Например, латунь ЛЦ23А6Ж3Мц2 содержит 23 % цинка, 6 % алюминия, 3 % железа, 2 % марганца.. Наилучшей жидкотекучестью обладает латунь марки ЛЦ16К4. К литейным латуням относятся латуни типа ЛС, ЛК, ЛА, ЛАЖ, ЛАЖМц. Литейные латуни не склонны к ликвации, имеют сосредоточенную усадку, отливки получаются с высокой плотностью.
Латуни являются хорошим материалом для конструкций, работающих при отрицательных температурах.
Бронзы
Сплавы меди с другими элементами кроме цинка назаваются бронзами.
Бронзы подразделяются на деформируемые и литейные.
При маркировке деформируемых бронз на первом месте ставятся буквы Бр, затем буквы, указывающие, какие элементы, кроме меди, входят в состав сплава. После букв идут цифры, показавающие содержание компонентов в сплаве. Например, марка БрОФ10-1 означает, что в бронзу входит 10 % олова, 1 % фосфора, остальное – медь.
Маркировка литейных бронз также начинается с букв Бр, затем указываются буквенные обозначения легирующих элементов и ставится цифра, указывающая его усредненное содержание в сплаве. Например, бронза БрО3Ц12С5 содержит 3 % олова, 12 % цинка, 5 % свинца, остальное – медь.
Оловянные бронзы При сплавлении меди с оловом образуются твердые растворы. Эти сплавы очень склонны к ликвации из-за большого температурного интервала кристаллизации. Благодаря ликвации сплавы с содержанием олова выше 5 % имеют в структуре эвтектоидную составляющую Э(), состоящую из мягкой и твердой фаз. Такое строение является благоприятным для деталей типа подшипников скольжения: мягкая фаза обеспечивает хорошую прирабатываемость, твердые частицы создают износостойкость. Поэтому оловянные бронзы являются хорошими антифрикционными материалами.
Оловянные бронзы имеют низкую объемную усадку (около 0,8 %), поэтому используются в художественном литье.
Наличие фосфора обеспечивает хорошую жидкотекучесть.
Оловянные бронзы подразделяются на деформируемые и литейные.
В деформируемых бронзах содержание олова не должно превышать 6 %, для обеспечения необходимой пластичности, БрОФ6,5-0,15.
В зависимости от состава деформируемые бронзы отличаются высокими механическими, антикоррозионными, антифрикционными и упругими свойствами, и используются в различных отраслях промышленности. Из этих сплавов изготавливают прутки, трубы, ленту, проволоку.
Литейные оловянные бронзы, БрО3Ц7С5Н1, БрО4Ц4С17, применяются для изготовления пароводяной арматуры и для отливок антифрикционных деталей типа втулок, венцов червячных колес, вкладышей подшипников.
Алюминиевые бронзы, БрАЖ9-4, БрАЖ9-4Л, БрАЖН10-4-4.
Бронзы с содержанием алюминия до 9,4 % имеют однофазное строение – твердого раствора. При содержании алюминия 9,4…15,6 % сплавы системы медь – алюминий двухфазные и состоят из– и– фаз.
Оптимальными свойствами обладают алюминиевые бронзы, содержащие 5…8 % алюминия. Увеличение содержания алюминия до 10…11 % вследствие появления – фазы ведет к резкому повышению прочности и сильному снижению пластичности. Дополнительное повышение прочности для сплавов с содержанием алюминия 8…9,5 % можно достичь закалкой.
Положительные особенности алюминиевых бронз по сравнению с оловянными:
меньшая склонность к внутрикристаллической ликвации;
большая плотность отливок;
более высокая прочность и жаропрочность;
меньшая склонность к хладоломкости.
Основные недостатки алюминиевых бронз:
значительная усадка;
склонность к образованию столбчатых кристаллов при кристаллизации и росту зерна при нагреве, что охрупчивает сплав;
сильное газопоглощение жидкого расплава;
самоотпуск при медленном охлаждении;
недостаточная коррозионная стойкость в перегретом паре.
Для устранения этих недостатков сплавы дополнительно легируют марганцем, железом, никелем, свинцом.
Из алюминиевых бронз изготавливают относительно мелкие, но высокоответственные детали типа шестерен, втулок, фланцев литьем и обработкой давлением. Из бронзы БрА5 штамповкой изготавливают медали и мелкую разменную монету.
Кремнистые бронзы, БрКМц3-1, БрК4, применяют как заменители оловянных бронз. Они немагнитны и морозостойки, превосходят оловянные бронзы по коррозионной стойкости и механическим свойствам, имеют высокие упругие свойства. Сплавы хорошо свариваются и подвергаются пайке. Благодаря высокой устойчивости к щелочным средам и сухим газам, их используют для производства сточных труб, газо- и дымопроводов.
Свинцовые бронзы, БрС30, используют как высококачественный антифрикционный материал. По сравнению с оловянными бронзами имеют более низкие механические и технологические свойства.
Бериллиевые бронзы, БрБ2, являются высококачественным пружинным материалом. Растворимость бериллия в меди с понижением температуры значительно уменьшается. Это явление используют для получения высоких упругих и прочностных свойств изделий методом дисперсионного твердения. Готовые изделия из бериллиевых бронз подвергают закалке от 800oС, благодаря чему фиксируется при комнатной температуре пересыщенные твердый раствор бериллия в меди. Затем проводят искусственное старение при температуре 300…350oС. При этом происходит выделение дисперсных частиц, возрастают прочность и упругость. После старения предел прочности достигает 1100…1200 МПа.
studfiles.net
Мельхиор (сплав) Википедия
Пять швейцарских франковМельхио́р (нем. Melchior, искаженное от фр. Maillot-Chorier) — однофазный сплав меди, в основном, с никелем, иногда с добавками железа и марганца, получивший своё название по именам французских изобретателей из Лиона Майо (Maillot) и Шорье (Chorier), которые создали свой сплав в 1819 году.[1]
Обычно в состав мельхиора входит 5—30 % никеля, ≤0,8 % железа и ≤1 % марганца, хотя в отдельных случаях он отличается от этих пропорций. Раньше под мельхиором понимались не только медно-никелевые сплавы, но и сплавы меди с никелем и цинком (нейзильберы), а также посеребрённая латунь, из-за чего изделия из этих материалов часто называют мельхиоровыми.
Помимо мельхиора существуют и другие медно-никелевые сплавы: как частный случай — монель, содержание никеля в котором достигает 67 %, а также нейзильбер, в котором дополнительно присутствует цинк и другие. Например, при изготовлении проволочных резисторов используется сплав, близкий по химическому составу к мельхиору, содержащий 59 % меди и 41 % никеля — константан.
Сплавы типа мельхиора представляет собой твердые растворы, поэтому они хорошо обрабатываются в холодном и горячем состояниях. Мельхиор отличается высокой коррозионной стойкостью в пресной и морской воде, сухих газах, а также в атмосферных условиях. С увеличением содержания никеля коррозионная стойкость, а также прочность увеличиваются.
Этимология
Сплав меди с никелем был известен ещё в III веке до н. э. как «белая медь». Современное название произошло от имён его «изобретателей» — французов Майо и Шорье (фр. Maillot, Chorier). Французское название Maillot-Chorier в немецком языке исказилось в Melchior, и затем распространилось в русском. В современных европейских языках cплавы меди с никелем часто связаны с латинским названием его компонентов — Cupronickel (в отличие от названий сплавов меди с никелем и цинком, которые обычно называют никелевым серебром — Nickel silver, германским серебром — German silver, новым серебром — New silver, Neusilber; при этом название Mailechort тоже иногда употребляется по отношению сплавам меди с никелем и цинком — нейзильберам).
Свойства
Основные характеристики: серебристый цвет, высокая коррозионная стойкость, температура плавления 1170°С (зависит от состава сплава), пластичен, хорошо обрабатывается давлением (штампуется, режется, чеканится) в холодном и горячем состоянии, паяется, полируется.
По внешним характеристикам мельхиор похож на серебро, но обладает большей механической прочностью.
Применение
Сплав широко применяют для изготовления посуды и недорогих ювелирных и художественных изделий. Большинство современных монет серебристого цвета изготавливают из мельхиора (обычно 75 % меди и 25 % никеля с незначительными добавками марганца).
В зависимости от состава, мельхиор может быть электронегативным относительно морской воды, из-за чего применяется в производстве высококачественных деталей морских лодок. Из мельхиора изготовляют также термогенераторы, точные резисторы и так далее.
Мельхиор также применяется в производстве медицинского инструмента.
См. также
Примечания
Ссылки
wikiredia.ru
2)Классификация медных сплавов. Латуни и бронзы, их состав, марки, свойства, применение.
Медь и ее сплавы
Медь имеет гранецентрированную кубическую решетку. Плотность меди 8,94 г/см3, температура плавления 1083oС.
Характерным свойством меди является ее высокая электропроводность, поэтому она находит широкое применение в электротехнике. Технически чистая медь маркируется: М00 (99,99 % Cu), М0 (99,95 % Cu), М2, М3 и М4 (99 % Cu).
Механические свойства меди относительно низкие: предел прочности составляет 150…200 МПа, относительное удлинение – 15…25 %. Поэтому в качестве конструкционного материала медь применяется редко. Различают две группы медных сплавов: латуни – сплавы меди с цинком, бронзы – сплавы меди с другими (кроме цинка) элементами.
Латуни.
Латуни могут иметь в своем составе до 45 % цинка. Повышение содержания цинка до 45 % приводит к увеличению предела прочности до 450 МПа. Максимальная пластичность имеет место при содержании цинка около 37 %.
По способу изготовления изделий различают латуни деформируемые и литейные.
Деформируемые латуни маркируются буквой Л, за которой следует число, показывающее содержание меди в процентах, например в латуни Л62 Латуни имеют хорошую коррозионную стойкость, которую можно повысить дополнительно присадкой олова. Латунь ЛО70-1 стойка против коррозии в морской воде и называется “морской латунью“.
Добавка никеля и железа повышает механическую прочность до 550 МПа.
Литейные латуни также маркируются буквой Л, После буквенного обозначения основного легирующего элемента (цинк) и каждого последующего ставится цифра, указывающая его усредненное содержание в сплаве. Например, латунь ЛЦ23А6Ж3Мц2 содержит 23 % цинка, 6 % алюминия, 3 % железа, 2 % марганца.. Наилучшей жидкотекучестью обладает латунь марки ЛЦ16К4. К литейным латуням относятся латуни типа ЛС, ЛК, ЛА, ЛАЖ, ЛАЖМц.
Латуни являются хорошим материалом для конструкций, работающих при отрицательных температурах.
Бронзы
Сплавы меди с другими элементами кроме цинка назаваются бронзами.
Бронзы подразделяются на деформируемые и литейные.
При маркировке деформируемых бронз на первом месте ставятся буквы Бр, затем буквы, указывающие, какие элементы, кроме меди, входят в состав сплава. После букв идут цифры, показавающие содержание компонентов в сплаве. Маркировка литейных бронз также начинается с букв Бр, затем указываются буквенные обозначения легирующих элементов и ставится цифра, указывающая его усредненное содержание в сплаве. Например, бронза БрО3Ц12С5 содержит 3 % олова, 12 % цинка, 5 % свинца, остальное – медь.
Оловянные бронзы При сплавлении меди с оловом образуются твердые растворы. Благодаря ликвации сплавы с содержанием олова выше 5 % имеют в структуре эвтектоидную составляющую Э(), состоящую из мягкой и твердой фаз. Такое строение является благоприятным для деталей типа подшипников скольжения: мягкая фаза обеспечивает хорошую прирабатываемость, твердые частицы создают износостойкость. Поэтому оловянные бронзы являются хорошими антифрикционными материалами.
В деформируемых бронзах содержание олова не должно превышать 6 %, для обеспечения необходимой пластичности, БрОФ6,5-0,15.
В зависимости от состава деформируемые бронзы отличаются высокими механическими, антикоррозионными, антифрикционными и упругими свойствами, и используются в различных отраслях промышленности. Из этих сплавов изготавливают прутки, трубы, ленту, проволоку.
Литейные оловянные бронзы, БрО3Ц7С5Н1, БрО4Ц4С17, применяются для изготовления пароводяной арматуры и для отливок антифрикционных деталей типа втулок, венцов червячных колес, вкладышей подшипников.
Билет 11
Упрочняющая термическая обработка сплавов с переменной растворимостью компонентов в твердом состоянии. Структура и свойства закаленных сплавов. Виды выделений при старении, их влияние на свойства сплавов.
_Термическая обработка сплавов с переменной растворимостью компонентов в твердом
состоянии Переменная растворимость компонентов в твердом состоянии дает возмож-ть
значительно упрочнять сплавы путем термической обработки. Это привело к широкому использованию сплавов этого типа — стареющих сплавов в качестве конструкционных материалов повышенной и высокой прочности; применяют стареющие сплавы на алюминиевой, медной, железной, никелевой, кобальтовой, титановой и других основах.
Рассмотрим принцип упрочняющей термической обработки стареющих сплавов на примере системы с промежуточным соединением (рис. а). К термически упрочняемым относятся сплавы составов от точки а до
промежуточного соединения А В
т п, в которых при охлаждении из твердого раствора выделяются вторичные
кристаллы AтB п. При этом степень упрочнения тем выше, чем больше масса вторичных кристаллов и равновесном сплаве (рис.б).
Рассмотрим для примера сплав I состава точки С который в равновесном состоянии имеет двухфазную структуру, состоящую из кристаллов твердого раствора а концентрации точки а и относительно крупных вторичных кристаллов AтBп .Сопротивление движению дислокаций подрастает по мере уменьшения расстояний между частицами упрочняющей фазы, т. е. сплав I станет прочнее, когда и место немногочисленных крупных включений образуется большое количество мелких. Наибольшее препятствие для движения дислокаций создают включения, отстоящие друг от друга на 25-50 межатомных расстояний. В большинстве стареющих сплавов желательная дисперсная структура образуется в результате термической обработки, состоящей из двух операций закалки и старения. При закалке сплавы нагревают до температур, обеспечивающих распад вторичных кристаллов. Для рассматриваемого сплава I такой будет температура, несколько превышающая t (см. рис. а). Быстрым охлаждением с температуры закалки полностью подавляют процесс выделения вторичных кристаллов и в результате получают одно-
фазный сплав - перенасыщенный компонентом В твердый раствор. Перенасыщение твердого раствора относительно мало сказывается на повышении твердости и прочности, незначительно изменяется и пластичность сплавов.
Пересыщенный твердый раствор представляет собой неравновесную структуру с повышенным уровнем свободной энергии. Поэтому, как только подвижность атомов окажется достаточно большой, твердый раствор будет распадаться - начнется процесс старения. Старение, происходящее при повышенных температурах, называют искусственным. В сплавах на основе низкоплавких металлов старение может происходить при температуре 20-25 С в процессе выдержки после закалки; такое старение называют естественным. При старении уменьшается концентрация пересыщающего компонента в твердом растворе; этот компонент расходуется на образование выделений. Тип выделений (кристаллическая структура), их размер и характер сопряженности с решеткой твердого раствора зависят как от вида сплава, так и от условий старения т. е. от температуры и времени выдержки.
В общем случае при распаде перенасыщенных твердых растворов могут возникать образования следующих типов (они перечисляются и порядке возрастания энергии активации зарождения):
Зоны Гиньс-Престона (зоны ГП) представляют собой весьма малые (субмикроскопические) обьемы твердого раствора с резко повышенной концентрацией растворенного компонента, сохраняющие решетку растворителя. Скопление растворенных атомов вызывает местное изменение периода решетки твердого раствора. При значительной разнице в размерах атомов А и В, как это, например, наблюдается в сплавах Al-Cu, зоны ГП имеют форму дисков, толщина которых (учитывая искажения решетки) составляет несколько межатомных расстояний (рис. а), диаметр 10-50 нм. Диски закономерно ориентированы относительно пространственной решетки растворителя. При небольшом различии в атомных диаметрах компонентов, как, например, в сплавах Al-Zn, обогащенные зоны имеют форму сфер.
Метастабильные фазы имеют иную пространственную решетку, чем твердый раствор, однако существует сходство в расположении атомов в определенных атомных плоскостях той ил иной решетки, что вызывает образование когерентной {или полу когерентной) границы раздела. Когерентная граница при некотором различии кристаллической структуры приводит к появлению переходной зоны с искаженной решеткой (рис.,6). Для метастабильных фаз характерна высокая дисперсность, что значительно повышает сопротивление движению дислокаций.Стабильная фаза т п, имеет сложную пространственную решетку с пониженным числом элементов симметрии и е большим числом атомов в элементарной ячейке. Вторичные кристаллы со стабильной структурой в большинстве сплавов выделяются в виде достаточно крупных частиц. Значительное различие кристаллической структуры твердого раствора и стабильных кристаллов приводит к образованию некогерентной границе раздела(рис. в) и, соответственно, к минимальным искажениям решетки твердого раствора вблизи границы. Упрочнение сплава при образовании стабильных кристаллов оказывается меньшим, чем при образовании зон ГП и мета стабильных когерентных кристаллов. Кривые старения (рис.) принят строить в координатах твердость (прочность)-длительность старения (при постоянной температуре). Условно примем, что максимальное упрочнение сплава I (см. рис. 5.4) достигается при выделении зон ГП.
ТемператураtO выбрана настолько невысокой, что распада пересыщенного твердого раствора не происходит и, соответственно, не наблюдается изменения твердости (прочности) закаленного сплава. Старение при температуре tl, вызывает повышение прочности вследствие образования зон ГП; если данная температура недостаточна для того, чтобы активировать зарождение метастабильных кристаллов, то твердость (прочности) достигнет максимального значения и в дальнейшем не будет изменяться сколь угодно длительное время (рис. 5.6, сплошная линия). Если температура tl достаточная для зарождения метастабильных кристаллов, то твердость после достижения максимального значения начнет понижаться, сплав будет "перестариваться" (рис. 5.6, штриховая линия).
studfiles.net
5.1. Некоторые сведения об истории медных сплавов
Древние мастера по металлу не оставили описаний приемов обработки и составов сплавов, применявшихся для изготовления разных предметов. Такая литература появляется только в средневековье, но в ней названия сплавов и терминология не всегда поддаются расшифровке, поэтому источником сведений являются исключительно сами вещи. Существует множество работ, посвящённых результатам исследований древних предметов. Из них мы узнаем, что первое появление изделий из меди археологи относят к VII тыс. до н.э. Это были кованые предметы из самородной меди. Затем появляется металлургическая медь и сплавы меди с другими металлами. На протяжении нескольких тысячелетий в основном из меди и ее сплавов изготавливались различные предметы: орудия труда, оружие, украшения и зеркала, посуда, монеты. Составы древних сплавов весьма разнообразны, в литературе их условно называют бронза. К наиболее ранним относятся мышьяковистые и оловянистые бронзы. Кроме олова и мышьяка в древних сплавах часто присутствует свинец, цинк, сурьма, железо и другие элементы в виде микропримесей, которые попадали в металл с рудой. Состав сплава подбирался весьма рационально в зависимости от функционального назначения предмета и используемой техники изготовления. Так, для литья художественных изделий был выбран рецепт тройного сплава медь-олово-свинец, применявшийся в античной Греции, в Римской империи, на Ближнем и Среднем Востоке, в Индии; в Китае бронза была одним из самых распространенных сплавов. На литых предметах из такой бронзы со временем образуется красивая патина, которая в некоторых случаях сохраняется и на археологических предметах.
Сплавы получали не только из чистых металлов, но и путем смешивания различных руд, в результате чего получали такие сплавы как латунь и медно-никелевый сплав, за много веков до того как научились добывать металлический цинк и никель. Латунь впервые упоминается в VIII в. до н.э. Известный исследователь древних технологий Форбес считает, что народы Малой Азии первыми стали получать латунь. В новое время металлический цинк и латунь впервые получили в Англии лишь в 1738- г.
Большое значение при изготовлении вещей имел цвет металла после шлифовки и полировки. В средневековых источниках сплавы называются по цвету: красная медь, латунь - желтая медь; зелёная медь - бронза, белая медь или белая бронза - светлые сплавы. С XVIII века в связи с развитием промышленности и возможностью получать различные металлы в чистом виде возникли новые композиции сплавов. Большое распространение получили сплавы, похожие по цвету на золото. Как правило, они состояли из меди, цинка и олова в разных соотношениях.
В зависимости от состава бронза условно делалась на медальную (монетную), в которой олова - 3-8%, цинка - 1%; пушечную, содержащую 10% олова; колокольную, в которой олова 20%, и зеркальную - 30% олова. В XVIII в. появились разнообразные сплавы на основе меди. Ормолу - разновидность латуни, в состав которой входят в равных частях медь и олово или только медь и цинк. Ормолу применялась главным образом для украшения французской мебели и мебели, выполненной во французском стиле. Иногда отливки из ормолу обрабатывали гравировкой или золотили. Гравированный рисунок делали более рельефным путем втирания черного пигмента. Латунь шла также для выделки самоваров, кофейников и других предметов домашнего обихода, осветительных приборов, ручек, кухонной утвари; некоторые предметы лудились. Латунь, содержащая до,10% цинка, называлась томпак. Она широко использовалась в XVIII веке для изготовления дешевых ювелирных украшений. Латунь с содержанием до 20% цинка называлась полутомпак, с 30% цинка - адмиралтейская латунь. Сплавы на медной основе мельхиор и нейзильбер - использовались как заменители серебра. В старой литературе нейзильбер иногда называется аргентан, варшавское серебро, иногда этим названием определяется посеребренная латунь. Отсутствие четкого соответствия названия составу привело к тому, что даже в справочной и специальной литературе позднего времени даны разные составы этих сплавов или разные названия одного сплава. Поэтому приводим определение этих двух похожих по внешнему виду сплавов, данное в Энциклопедическом словаре 1985 г. Мельхиор - сплав, изобретенный во Франции, содержит в своем составе медь главным образом с никелем (5-30%). Обладает высокой стойкостью на воздухе и в воде, хорошо обрабатывается.
Нейзильбер (буквально, новое серебро) - немецкий сплав, содержащий медь - основа, никель (5-35%) и цинк (13-45%). Обладает высокой коррозионной стойкостью и прочностью, удовлетворительной пластичностью.
Сплавом XX века является алюминиевая бронза с содержанием 5% алюминия. Этот сплав прекрасно обрабатывается и по цвету похож на золото. Иногда его называют французским золотом. Французким золотом называют также сплав, состоящий из 58% красной меди, 16% олова и 25% цинка, цветом и блеском действительно похожей на золото. Так называемый британский металл состоит из олова, сурьмы с добавлением меди. Этот сплав обладает прекрасными литейными свойствами, легко обрабатывается инструментами, хорошо принимает полировку и не тускнеет на воздухе. Из него изготовляли в большом количестве предметы домашнего обихода.
Таким образом, видим, что по названию, которое дается в старых руководствах по обработке металлов и справочниках, определить состав и содержание в сплаве легирующих элементов сплава трудно.
Технология изготовления различных предметов из металла также претерпела эволюцию: первые изделия изготовлялись холодной ковкой, затем было освоено литье, сначала в открытую форму, затем в закрытую и., как наиболее развитая техника литья, литье по выплавляемым моделям; восковое литье в Египте было уже в III тыс. до н.э. Холодной ковке на смену пришла горячая ковка и использование термообработки для получения специальных свойств металлов. По-разному конструктивно оформлялись предметы, в определенный период появляется ковочная сварка, пайка, сочетание кованых и литых элементов. Предметы перестают иметь чисто утилитарное значение; украшаются насечкой и инкрустацией ножны и рукояти мечей и кинжалов, становятся нарядными элементы конской упряжи и снаряжения всадников, появляется художественно украшенная посуда. Получают развитие различные технические и ювелирные приемы работы с металлами. Нужно заметить, что все это уходит в глубокую древность. Так, в царских гробницах Ура (29 в. до н.э.) был найден золотой кинжал в ножнах, в декорировке которого применялись зернь и филигрань. С древнейших времен стали использовать украшение предметов из меди и медных сплавов другими металлами. Золотилась или серебрилась вся поверхность или выявлялся таким способом рисунок. Появляется инкрустация из золота и серебра. Некоторые предметы декоративно-прикладного искусства из металла имели искусственную патину. Первые опыты по патинированию металлов начались, видимо, в Европе с эпохи Возрождения, вдохновленной открытием античного искусства. Искусство барокко почти всегда предпочитало светлый блестящий металл. В предметах прикладного искусства в стиле рококо старались еще более усилить блеск, чистой бронзы обильным применением позолоты и сплавов, имитировавших золото. Золочение; было очень разнообразным., В ХVIII в. появляется матовое золочение, позолота различных оттенков. Иногда на одной вещи сочеталось матовое и блестящее золочение. Лишь в конце XVIII - нач. XIX в. искусственная патинировка опять входит в моду. Её вдохновителем явилась античность после раскопок Помпеи и Геркуланума. Своеобразное применение она нашла в стиле ампир. Патинировались отдельные детали бронзовых украшений мебели, часов, подсвечников. Почти всегда патинирование детали сочеталось с золочением. Плотная черно-зеленая патина, нанесённая без учета моделировки, полностью скрывала цвет металла. Массовое патинирование под старину началось с середины XIX века. В это время было создано большее число всех известных ныне способов патинировки. Кроме патинирования химическими веществами, применялись пигменты на связующем, масляное горячее патинирование, покрытие цветным лаком. Способы патинировки были секретом мастера или мастерской.
Первоисточник:
РЕСТАВРАЦИЯ МЕТАЛЛА. Методические рекомендации. ВНИИР. сост. М.С.Шемаханская М., 1989art-con.ru
Медь и ее сплавы с оловом, цинком, алюминием, никелем, серебром, железом, свинцом

Минерал меди
Металл, имеющий розовато-красный цвет и температуру плавления – 1083 °С, называется медью. Для этого химического элемента не свойственно содержать полиморфные соединения. Его кристаллизация происходит в гранецентрированной решетке. Влага и углекислый газ оказывает медленное воздействие, вещество обретает зеленый цвет после покрытия пленкой. Этот налет служит в качестве защиты для меди от коррозии.
Где используется медь и ее сплавы? В технике при низких температурах медь и ее сплавы выступают в качестве традиционных материалов. Также, как и для серебра, химического элемента, существенно иметь высокие механические свойства и теплопроводность, обладать коррозийной стойкостью.
Механические и технологические свойства такого элемента, как сплавы на основе меди нарушаются под влиянием вредных примесей таких, как серы и кислорода, висмута и свинца.
Основные технологические процессы получения металла:
1. Для обогащения руды используют метод флотации, при помощи которой соединения меди и пустой породы проходят смачивание. Отдельно подготавливается суспензия с флотационным агентом и соединяется с размельченной рудой. В качестве флотационного агента можно использовать пихтовое масло, благодаря которому на поверхности рудных частичек образуется пленка. На поверхности руды собираются пузырьки, они появляются от продувки воздухом, затем образуется пена. На дно опускается пустая порода, не прошедшая смачивания маслом. До 30% меди находится в собранной и высушенной пене – концентрате.
Подробнее о методе флотации
2. Сернистый газ получается в результате обжига концентрата. Таким образом, получается обожженный медный концентрат и серная кислота, без содержания алюминия. Затем в отражательных печах получается медный штейн, ингредиент, в состав которого входит сульфид железа и медь.

Заливка штейна в конвертер
3. Для продувки штейна предусмотрены конвертеры с кислородом, в них получается черновая медь. У такого ингредиента содержится 1,5% примеси без серебра и алюминия. Во время продувки участвует кварцевый песок, окись железа образуется благодаря переходящим сульфидам, после этого образуется шлак. Серная кислота получается благодаря поступлению сернистого газа.
4. Черновая медь очищается при помощи огневого или электролитического метода. Деревянные жерди используются при огневом способе, а затем происходит пропускание воздуха. Примеси выводятся благодаря окислению жердей кислородом воздуха. Электролитический метод включает в себя установление меди в качестве анода, а медные листы служат в виде катода. Анод начинается растворяться, когда проходит ток, при этом на дне происходит оседание меди на катоде. Изделия из меди и серебра, имеющие вес 60-90 кг можно получить в течение 10 дней. В это время дно ванны наполняется шламом – осадком примеси. Чаще всего шлам состоит из серебра – 35%, золота – 1% и селена – 6%, без железа и свинца, а вот алюминия здесь не обнаружено.
Сплавы химического элемента – меди
Латунь
На основе меди получается двойной или многокомпонентный сплав – латунь, мягче и легче стали. В ней легирует главный ингредиент – цинк. В отличие от меди у металла больше прочности, устойчивости перед коррозиями, а также лучшая обрабатываемость, как у железа и стали. Химический элемент, как алюминий с легкостью можно разрезать, или разлить. Цинк в латуни содержится до 45%, а вот серебра и железа нет. Чем больше металл находится в составе, тем становится менее прочным. Сплавы на основе меди не содержат легирующие ингредиенты больше 7-9%.
Технологический признак металла состоит из литейных и деформируемых веществ. Из этих элементов изготавливают фасонные отливки, они выглядят в форме чушки.
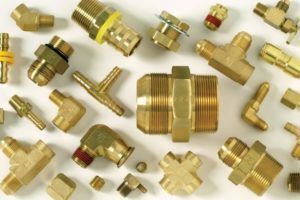
Изделия из латуни
Из деформируемых латуней делают простые элементы. Проволока, прутки, полосы, ленты, трубы, листы, и другие прокатные, а также прессованные изделия считаются полуфабрикатами латуни, напоминающие изделия из алюминия. В общем, и химическом машиностроении металл, так как и бронза широко используется.
Немного о бронзе

Бронза
Бронза — это сплав меди, в который добавляется олово, марганец, алюминий, свинец, кремний, бериллий, чего нет в стали. Бронза, наподобие серебра, она устойчивая перед коррозией, у нее высокие антифрикционные и хорошие литейные свойства, её легко можно обработать резанием. Чтобы улучшить механические характеристики, а также придать особые свойства металлу — бронза, для легирования используют никель, железо, цинк, титан, фосфор.

Химический состав и механические свойства некоторых бронз
Если к химическому элементу добавить марганец, у элемента появится устойчивость к коррозии, при добавлении никеля, бронза становится пластичней. Чтобы изделие сделать прочным, наподобие стали, рекомендуется добавить немного железа. Улучшит литейные свойства элемента цинк. С помощью свинца, бронза станет более обрабатываемая.
Сплав – никель и медь
Медноникелевым сплавом называется соединение, в котором основой является медь, а легирующий элемент – это никель, алюминия и свинца не обнаружено. В основном используют электротехническими и конструкционными сплавами.
Соединение, состоящее из меди, никеля и алюминия принято называть куниали. Его основными элементами является никель – 6-13%, немного алюминия – 1,5-3%, все остальное занимает медь. В отличие от серебра, это изделие проходит термическую обработку. Из металла изготавливают детали, имеющие повышенную прочность, к ним относятся электротехнические изделия, а также пружины, как изготавливают из стали.
Изделие, которое представляет собой сплав меди с цинком и никелем носит необычное название – нейзильбер. В его составе содержится никель – 15%, цинк – 20%, весь остальной состав принадлежит меди, и нет свинца. Металл, в отличие от стали, обладает приятным белым цветом, который приближен к окраске серебра. Химический элемент, как и бронза, хорошо выдерживает атмосферную коррозию, он служит неотъемлемой частью приборостроения, а также при производстве часов.

Нейзильбер часто используется как конструкционный материал
Металлы, содержащие медь с никелем в небольшом количестве и марганец, не превышающий 1%, называются мельхиорами. У этих изделий, как и у стали, повышена устойчивость перед коррозией, на них не оказывает влияние морская вода. Металлы чаще всего применяют при изготовлении теплообменных аппаратов, из них делают чеканные и штамповые изделия.
Для изготовления термопар пользуются специальным термоэлектродным сплавом, который называется – копелем. В состав химического элемента входит никель с медью и составляет 43%, а также марганец, в количестве 0,5%.

Марганцовистая бронза — манганин
Сплав, у которого есть высокое удельное электрическое сопротивление, носит название – манганин. Это изделие состоит из марганца, который составляет 12% и меди с никелем, на них отводится 3%, серебра и железа не обнаружено. При изготовлении электронагревательных приборов в отличие от алюминия и стали, медь и бронза используется чаще.
Важным преимуществом такого металла, как медь и бронза является то, что ее применяют в электротехнической промышленности. Металл широко используют при изготовлении электрических проводов. Чем чище химическое изделие, тем высоко его преимущество. Проводимость электричества упадет на 10%, если в меди будет обнаружено 0,02% алюминия.
В определенной области производства изделия из меди, стали и серебра считаются лучшим материалом. Механические детали производственного оборудования не могут быть изготовлены из другого металла, алюминия или железа. Кроме меди и стали в современном мире высоко ценится бронза. А вот сплав меди с оловом считается прочным металлом, в котором сохранена пластичность.
Видео: Добыча Меди
ecology-of.ru
11. Сплавы на медной основе: латуни, бронзы, мельхиоры, нейзильберы, куниали. Состав, марки, структура, способы упрочнения.
Медные сплавы, сплавы на основе меди. Со многими элементами медь образует широкие области твёрдых растворов замещения, в которых атомы добавки занимают места атомов меди в гранецентрированной кубической решётке. Медь в твёрдом состоянии растворяет до 39 % Zn, 15,8 % Sn, 9,4 % Al, a Ni — неограниченно. При образовании твёрдого раствора на основе меди растут её прочность и электросопротивление, снижается температурный коэффициент электросопротивления, может значительно повыситься коррозионная стойкость, а пластичность сохраняется на достаточно высоком уровне. При добавлении легирующего элемента свыше предела растворимости образуются соединения, в частности электронные, т. е. характеризующиеся определённой электронной концентрацией (отношением суммарного числа валентных электронов к числу атомов, которое может быть равно 3/2, 21/13 или 7/4). Этим соединениям условно приписывают формулы CuZn, Cu5Sn, Cu31Sn8, Cu9Al4, CuBe и другие. В многокомпонентных М. с. часто присутствуют сложные металлические соединения неустановленного состава, которые значительно твёрже, чем раствор на основе меди, но весьма хрупки (обычно в двухфазных и многофазных М. с. доля их в структуре намного меньше, чем твёрдого раствора на основе меди).
М. с. получают сплавлением меди с легирующими элементами или с промежуточными сплавами — лигатурами, содержащими легирующие элементы. Для раскисления (восстановления окислов) широко применяют введение в расплав малых добавок фосфора (десятые доли %). М. с. подразделяют на деформируемые и литейные. Из деформируемых М. с. отливают (в изложницы или непрерывным методом) круглые и плоские слитки, которые подвергают горячей и холодной обработке давлением: прокатке, прессованию через матрицу или волочению для производства листов, лент, прутков, профилей, труб и проволоки. М. с. хорошо обрабатываются давлением, и деформированные полуфабрикаты составляют основную долю всего объёма их производства. Литейные М. с. обладают хорошими литейными свойствами, из них отливкой в земляные и металлические формы получают фасонные детали, а также декоративно-прикладные изделия и скульптуру.
Механические свойства М. с. изменяются в широких пределах при холодной обработке давлением и при отжиге. Холодной деформацией можно увеличить твёрдость и предел прочности М. с. в 1,5—3 раза при одновременном снижении пластичности, а последующий рекристаллизационный отжиг позволяет частично или полностью (в зависимости от температуры и его продолжительности) восстановить исходные (до деформации) свойства. Смягчающий отжиг М. с. после холодной обработки давлением проводят при 600—700 °С. Большинство М. с. не подвергают упрочняющей термической обработке (закалке и старению), так как эта обработка или в принципе невозможна, если сплав при всех температурах однофазен, или величина упрочнения очень мала. Для создания термически упрочняемых М. с. используют такие легирующие элементы, которые образуют с медью или между собой интерметаллические соединения (например, CuBe, NiBe, Ni3Al), растворимость которых в твёрдом растворе на базе меди с понижением температуры уменьшается. При закалке таких сплавов образуется пересыщенный твёрдый раствор, из которого при искусственном старении выделяются дисперсные интерметаллические соединения, упрочняющие М. с.
М. с. подразделяют на латуни, бронзы и медно-никелевые сплавы. В латунях главной добавкой является цинк, в бронзах — любой элемент, кроме цинка и никеля. Промышленные марки выпускаемых в СССР М. с. начинаются с первых букв их названий — Л (латуни), Бр. (бронзы) и М (медно-никелевые сплавы). Легирующие элементы обозначают следующими буквами: А — алюминий, Н — никель, О — олово, Ц — цинк, С — свинец, Ж — железо, Мц — марганец, К — кремний, Ф — фосфор, Т — титан. В марке простой (двойной) латуни цифры указывают ср. содержание меди. Например, латунь Л90 содержит 90 % Cu и 10 % Zn. В марке многокомпонентной латуни первые цифры указывают среднее содержание меди, а последующие — легирующих элементов. Например, латунь ЛАН59-3-2 содержит 59 % Cu, 3 % Al и 2 % Ni (остальное цинк). В марках бронз и медно-никелевых сплавов буквы и соответствующие им цифры указывают содержание легирующих элементов. Например, бронза Бр. АЖМц10-3-1,5 содержит 10 % Al, 3 % Fe и 1,5 % Mn. Буква Л в конце марки М. с. обозначает, что он предназначен для фасонного литья (например, ЛК80-3Л). Все М. с. отличаются хорошей стойкостью против атмосферной коррозии. Кислород при комнатной температуре не действует на М. с.; окись углерода с ними не реагирует. Незагрязнённый пар, сухой или влажный действует на бронзы очень слабо. Сероводород уже при незначительной влажности и особенно при повышенных температурах сильно реагирует с М. с. Азотная и соляная кислоты действуют на латуни и оловянные бронзы очень сильно, серная — значительно слабее.
Мельхиор — является сплавом меди с никелем, иногда с добавками железа и марганца. Мельхиор отличается высокой коррозионной стойкостью, хорошо обрабатывается под давлением в холодном и горячем состоянии. В зависимости от состава, мельхиор может быть электронегативным относительно морской воды, из-за чего применяется в производстве высококачественных деталей морских лодок. Из мельхиора изготовляют также ювелирные изделия, посуду, термогенераторы, точные резисторы и так далее. Большинство современных монет серебристого цвета состоят из мельхиора (обычно 75 % меди и 25 % никеля с незначительными добавками марганца). Помимо мельхиора, существуют и другие сплавы меди с никелем: монель, содержание никеля в котором достигает 67 %, а также нейзильбер, в котором дополнительно присутствует цинк.
Куниаль (по первым буквам составляющих элементов) — сплав Cu (основа) с Ni (4-20 %) и Al (1-4 %).
Различаются две марки: куниаль А (МНА 13-3), содержащий 12—15 % Ni и 2,3—3,0 % Al, и куниаль Б (МНА 6-1,5) содержащий 5,5—6,5 % Ni и 1,2—2,8 % Al.
Куниаль А используется для изготовления деталей специального назначения, которые должны обладать одновременно прочностью и высокой коррозионной стойкостью. Куниаль Б применяется для изготовления пружин и других упругих элементов ответственного назначения, а также в криогенной технике благодаря его высокой морозостойкости.
12. Сплавы на основе алюминия, Состав, структура, марки, способы упрочнения.
Al - самопассивирующийся металл благодаря образованию на его поверхности в окислительной атмосфере плотной защитной пленки Al2O3. Поэтому обладает высокой коррозионной стойкостью на воздухе (и при нагреве - жаростоек), в пресной воде.
Свойства чистого алюминия (99,995% Al) : σв= 50МПа; σт= 15МПа; δ= 45% ; НВ= 15
Первичный Al особой чистоты А999 (есть и 6 девяток, т.е. примесей не более 0,000001%), высокой чистоты –А99,А97, А95, технической чистоты – А85, А8………..А0.
Марки деформированного листового алюминия: АД00, АД), АД, АД1.
Пластичность Al позволяет деформировать в холодную на 99% и получать микронную фольгу!
Вредные примеси в чистом Al – Fe и Si.
Si вызывает хрупкость а из-за широкого интервала кристаллизации – горячеломкость, т.е. появление трещин при твердо-жидком состоянии вследствие неравномерной усадки.
Кристаллизация технически чистого алюминия, как и его сплавов, всегда неравновесная.
Рассмотрим на примере сплавов Al-Si в предположении, что диффузия в твердой фазе крайне мала.
Возьмем сплав, равновесная кристаллизация которого начинается при температуре t1 с выпадения кристаллов α состава а1. При каждой температуре, например t2 , в равновесии с жидкостью (состава ж2 ) находятся кристаллы α (состава а2). Но состав ранее выпавших кристаллов (внутренних частей дендритов) не изменяется и средний состав образовавшейся к этой температуре кристаллической фазы отличается от а2, в них содержится больше алюминия. Поэтому доля жидкости состава ж2 больше, чем а2m/а2ж2 , и определяется отношением а2с1/а2ж2. При температуре t3 кристаллизация не заканчивается, остается жидкость состава ж3 . При дальнейшем охлаждении жидкость сохраняется до температуры tЕ, при которой переходит в эвтектику. Таким образом, первичные кристаллы кремния в составе эвтектики в литом алюминии будут присутствовать при любом сколь угодно малом содержании кремния в сплаве.
Промышленный т.ч. алюминий по существу является тройным сплавом Al-Fe-Si. При одновременном присутствии Fe и Si образуются два соединения α (Al-Fe-Si) и β (Al-Fe-Si) более богатая кремнием, в котором соотношение Fe /Si равно 1,5, поэтому введение железа в достаточном количестве исключает выделение свободного кремния и устраняет появление горячих трещин.
Структура литого алюминия и его сплавов всегда имеет дендритную ликвацию. Размер первичных кристаллов зависит от степени перегрева, наличия примесей и скорости охлаждения. Но еще большее важное значение имеет внутризеренная структура, определяемая разветвленностью ветвей кристалла, что в свою очередь определяет размер дендритной ячейки и размер интерметаллидных включений. Внутренняя структура тем тоньше, чем больше скорость охлаждения.
Прессэффект Al – сплавов
Прессэффектом называется повышение прочности в прессованных полуфабрикатах после последующей упрочняющей т.о. по сравнению с отожженными полуфабрикатами после такой же упрочняющей термообработки – эффект упрочнения в некоторых сплавах до 40%.
Основная причина – формирование при горячем прессовании не рекристаллизованной, а полигонизованной структуры. Это возможно, если температура рекристаллизации выше температуры деформации и закалки. Температура рекристаллизации повышается при добавлении переходных металлов, особенно Zn, но также Mn,Cr, Ti после горячей деформации.
Механизм влияния: растворы этих металлов из-за малой растворимости в Al оказываются пересыщенными при т-ре горячего деформирования и при температуре закалки, идет распад с выделением дисперсных частиц Al6Mn, Al7Cr, Al3Zr на дислокациях, что уменьшает их подвижность и задерживает рекристаллизацию. Почему именно прессование: напряженное состояние близко к всестороннему сжатию и в этом случае наименьшая упругая энергия исамая высокая Трек.
Фазы: Si, Mg2Si, Al2Cu(θ), Al3Mg2(β), S(Al2MgCu), T(Al6CuMg4), W (Al-Cu-Mg-Si). Фазы Si, β, T не дают эффекта упрочнения.
Сплавы на основе системы Al-Cu-Mg (c добавками марганца) – дуралюмины
На сплаве этого типа в 1904г Вильм обнаружил эффект естественного старения и в 1908г предложил промышленный сплав, который и назвали дуралюмином. Это - основные сплавы, применяемые в авиации, упрочняемые ТО.
Упрочняющие фазы – θ и S. Соотношение меди и магния, как и их количество в сплавах, определяет длительность естественного старения, его эффективность. Так сплавы Д18 и ВАД65 с длительным временем старения и инкубационным периодом применяются почти исключительно для заклепок (их надо успеть поставить до начала старения).
Все дуралюмины отличаются пониженной коррозионной стойкостью и нуждаются в защите от коррозии (плакировка техническим алюминием (анодом по сравнению с дюралем и это благо) или анодированием).
Сплавы на основе системы Al-Mg-Si
Среди сплавов алюминия, упрочняемых ТО, эти - наименее легированные и поэтому имеют повышенную коррозионную стойкость, удовлетворительно свариваются, высокую технологичность (профили можно прессовать со скоростью в 10 раз быстрее дуралюминов). Прочность после з+ес или ис на уровне 250-350 МПа. Более высокая прочность за счет прессэффекта.
Сплавы находятся по составу вблизи квазибинарного разреза Al-Mg2Si (если % Mg/%Si = 1,73 – то точно). Хром и марганец способствуют прессэффекту и размельчению зерна. Медь повышает прочность (но снижает коррозионную стойкость).
Сплавы на основе системы Al-Mg-Si-Cu
Это – специальные ковочные сплавы, используемые для промзводства поковок и штамповок. Их изюминка – высокая технологическая пластичность и в нагретом состоянии, и в холодном состоянии. Сплавы занимают промежуточное положение между дюралями и авиалями. Упрочняющие фазы W, θ, Mg2Si (не всегда).
Сплавы на основе системы Al-Zn-Mg-Cu (высокопрочные сплавы)
Введение цинка привело к появлению новых упрочняющих фаз : MgZn2 , Al2 Mg3 Zn3 (T –фаза, изоморфная Т- фазе Al2CuMg4 ) в добавление к S- фазе. Поэтому прочность на уровне 600 МПа.
Другие сплавы на основе алюминия
Помимо рассмотренных используются и другие сплавы на основе алюминия, обладающие специальными свойствами, например, жаропрочностью, (АК4-1 системы Al-Cu-Mg с добавками Ni и Fe, образующих равномерно распределенные дисперсные включения фазы Al9FeNi). Исключительно интересны сплавы системы Al-Cu-Li, в которых много двухкомпонентных и трехкомпонентных фаз (AlLi, Al7,5Cu4Li, Al2CuLi, Al6Cu4Li3 ). Поэтому прочность на уровне высокопрочных сплавов! Кроме того, повышенный модуль Юнга. Это сплавы ВАД23, 01410.
Литейные алюминиевые сплавы
Главные технологические свойства литейных сплавов: 1.-жидкотекучесть, 2- линейная и объемная усадка, 3- склонность к образованию горячих трещин, 4- склонность к усадочной и газовой пористости, 5- склонность к ликвации. Основной (но не единственный) фактор, определяющий эти свойства – эффективный температурный интервал кристаллизации (не совпадающий с интервалом кристаллизации, определяемой равновесной диаграммой состояния)
Литейные свойства определяют не только возможность получать нужные по конфигурации отливки, но и их конструкционную прочность.
Как говорилось выше, увеличение скорости охлаждения при кристаллизации уменьшает расстояние между ветвями дендритов (размер дендритной ячейки) и увеличивает конструкционную прочность. Поэтому имеет значение способ литья – в землю, в кокиль, литье под давлением. Широко используется также легирование и модифицирование как способы размельчения структуры
В качестве литейных применяются сплавы на основе трех систем Al-Si, Al-Cu, Al-Mg c добавлением других легирующих элементов.
Лучшие литейные свойства характерны для сплавов Al-Si –силуминов.
Наименьший интервал кристаллизации у эвтектических сплавов. В сплавах Al-Si эвтектика содержит относительно небольшое количество хрупкой фазы (Si). В сплавах Al-Cu, Al-Mg доля хрупких фаз в эвтектиках гораздо больше и используются в качестве литейных сплавы доэвтектические с широким интервалом кристаллизации.
Cилумины используются в модифицированном состоянии, так как в результате модифицирования повышается и прочность и пластичность. Легированные силумины подвергаются закалке и старению.
Высокопрочный сплав АК8М (σв 280МПа) предназначается для литья под давлением. Сплав обладает хорошими литейными свойствами, обрабатываемостью резанием, свариваемостью и коррозионной стойкостью. Марганец и титан и большая скорость кристаллизации при литье под давлением способствуют получению пересыщенных растворов и дают возможность проводить искусственное старение (1750С 8 часов) Упрочняющие фазы θ1 и β1.
Сплавы Al-Cu характеризуются высокой прочностью, хорошо обрабатываются резанием, свариваются, но имеют плохие литейные свойства и герметичность. Марганец способствует получению пересыщенных растворов при кристаллизации При нагреве при закалке выделяется мелко дисперсная фаза Al12 Mg2Cu. дополнительно упрочняющая сплав (при старении упрочнение связано с фазой CuAl2) Сплавы Al-Cu используют для деталей при температурах до 3000
Сплавы Al-Mg обладают высокой коррозионной стойкостью вязкостью обрабатываемостью резанием. Легирование Be, Ti, Zr не только устраняет их склонность к окислению и росту зерна, но тормозит естественное старение, снижающее вязкость и пластичность сплавов. Наилучшие свойства – после закалки Без старения!
13. Чугуны. Структура, свойства, способы получения, маркировка.
Чугуны бывают: белые, серые, ковкие, высокопрочные, с вермикулярным графитом, специально легированные.
Вид и структура чугуна определяется содержанием постоянных примесей и легированных элементов, а также скоростью охлаждения.
˄Mn ˅Si ˄Vохл – белый чугун, ˅Mn ˄Si ˅Vохл –серый чугун.
При уменьшении Vохл появляется графитизация.
1 – белый чугун Л+П+ЦII
2 – половинчатый Л+Гр+ П+ЦII
3 - серый чугун с перлитной основой Гр+П
4 – серый чугун с феррито-перлитной основой Ф+П+Гр
5 – серый чугун с ферритной основой Ф+Гр
В серых чугунах графит имеет пластинчатую структуру.
Свойства чугуна зависят от размера графитовых включений, чем больше графита, тем хуже. Измельчают графит с помощью модификации – вставки готовых центров кристаллизации, т.е. Si. Если не принимать никаких мер, то чугун будет с определенным содержанием серы и марганца - Mn ˄S ˅Vохл – серый хрупкий чугун с графитовыми включениями, хорошо работает на сжатие и плохо на растяжение.
Предел прочности увеличивается: Ф+Гр => Ф+П+Гр => П+Гр.
Маркировка серого чугуна СЧσвдесятков МПа. Чем толще отливка тем меньше прочность.
Высокопрочные чугуны.
При модифицировании Mg, графит принимает глобулярную форму – возникают сильные внутренние напряжения. Маркировка ВЧσвдесятков МПа. Требует жесткого соблюдения химического состава.
Чугун с вермикулярным графитом.
Для получения такового применяют модифицирование редкоземельными металлами. Маркируют ЧВГσвдесятков МПа.
Ковкий чугун.
Это литейный, пластический материал.
Форма графитовых включений – хлопьевидная, получается вследствие отжига отливок из белого чугуна.
Подбирают химический состав таким образом, чтобы %Mn и %Si давали отливки белого чугуна, затем отжигают.
1 – нагрев
2 – первая стадия графитизации Ц => А+Сотж
3 – вторая стадия графитизации А => А+ЦII ; ЦII => А+Сотж
4 – эвтектоидное превращение (рисовать горизонтальную линию) Ц => Ф+Сотж
5 – Ф+Сотж
Маркируют КЧσв-δ%, δ%-относительное удлинение.
Специальные чугуны – с целью повышения износостойкости, коррозионной стойкости, жаропрочности, чугуны легируют Cr, Ni, Cu, Al. Соединения легированных элементов отмечают в марке чугуна.
ЧХ1…ЧХ28; ЧН15ДХ2 (Д – Cu), ЧС15 (Si)
Специальные чугуны могут иметь мартенситную и аустенитную структуру.
14. Пластическая деформация. Скольжение, двойникование. Системы скольжения.
Способность пластически деформироваться - большое технологическое преимущество материалов с металлическим типом связи, обеспечивающее не только возможность получения требуемых размеров фасонного и сортового проката, поковок, листа, проволоки и т.д., но и мощный способ повышения конструкционной прочности деталей и заготовок.
Механизм пластической деформации
При низкой температуре основной механизм пластической деформации – сдвиг, осуществляемый скольжением или двойникованием.
Основными механизмами сдвиговой пластической деформации кристаллических тел являются скольжение и двойникование. Скольжение-это такое перемещение одной части кристалла относительно другой, при котором кристаллическое строение обеих частей остается неизменным. В области сдвига кристаллическая решетка остается такой же, как и в обеих частях кристалла, и каждый атом в этой области перемещается на одинаковые расстояния, составляющие целое число периодов повторяемости решетки. Отполированная поверхность кристалла после деформации скольжением при рассмотрении в оптическом микроскопе оказывается покрытой одной или несколькими системами параллельных тонких линий, называемых линиями скольжения. Эти линии представляют собой ступеньки на поверхности, возникающие в результате сдвига кристалла вдоль плоскости, которая и называется плоскостью скольжения, а направление сдвига в этой области -направлением скольжения. Комбинация данной плоскости и направления скольжения в ней составляет систему скольжения.
Сдвиг: d - расстояние между плоскостями сдвига; b - между атомами в направлении сдвига
Двойникование: Кристаллическая решетка двойника – представляет собой зеркальное отражение решетки кристалла от плоскости двойникования
Жесткий (одновременный сдвиг) по плоскости сдвига требует очень больших напряжений, определяемых теоретической прочностью кристаллов металлов.
τтеор= Gb/2πd (По порядку величин- 1т/мм2 !)
Эксперимент показывает, что скольжение действительно происходит по плоскостям наиболее плотного расположения атомов (d-максимально) в направлении с минимальным расстоянием b между ними.
Такие плоскости и направления определяют системы скольжения.
ГЦК - 12 систем
ОЦК {110} {112} {123} 48 сисем
ГПУ <> (0001) 3 cистемы
Дислокационная субструктура, формирующаяся при холодной пластической деформации зависит от многих факторов
1. Вид нагруженного состояния (стесненная или не стесненная, Число систем скольжения и т.д.)
2. Температура и скорость деформирования (подвижность вакансий, условия переползания и поперечного скольжения и т.д.)
3. Свойства дислокаций и твердого раствора (энергия дефектов упаковки, наличие атомного порядка, торможение атомами внедрения)
4. Плотность дислокаций и относительная роль механизмов их взаимодействия.
15. Изменение структуры и свойств в результате холодной пластической деформации.
Рассмотрим холодную пластическую деформацию поликристалла. Пластическая деформация металлов и сплавов как тел поликристаллических, имеет некоторые особенности по сравнению с пластической деформацией монокристалла.
Деформация поликристаллического тела складывается из деформации отдельных зерен и деформации в приграничных объемах. Отдельные зерна деформируются скольжением и двойникованием, однако взаимная связь зерен и их множественность в поликристалле вносят свои особенности в механизм деформации.
Плоскости скольжения зерен произвольно ориентированны в пространстве, поэтому под влиянием внешних сил напряжения в плоскостях скольжения отдельных зерен будут различны. Деформация начинается в отдельных зернах, в плоскостях скольжения которых возникают максимальные касательные напряжения. Соседние зерна будут разворачиваться и постепенно вовлекаться в процесс деформации. Деформация приводит к изменению формы зерен: зерна получают форму, вытянутую в направлении наиболее интенсивного течения металла (поворачиваются осями наибольшей прочности вдоль направления деформации). Изменение структуры при деформации показано на рис. 8.1.
Металл приобретает волокнистое строение. Волокна с вытянутыми вдоль них неметаллическими включениями являются причиной неодинаковости свойств вдоль и поперек волокон. Одновременно с изменением формы зерен в процессе пластической деформации происходит изменение ориентировки в пространстве их кристаллической решетки.
Когда кристаллические решетки большинства зерен получают одинаковую ориентировку, возникает текстура деформации.
При холодной пластической деформации происходит трехстадийное упрочнение металла.
Стадия 1:
Стадия легкого скольжения. Металлографически выделяется в виде параллельных полос скольжения. Эти полосы представляют собой ступеньки на поверхности кристалла с высокой до 5 нм, расстояние между отдельными плоскостями 20-30 нм.
На этой стадии активной является только одна система скольжения.
Стадия 2:
Это стадия линейного упрочнения. Коэффициент деформационного упрочнения (угол наклона) имеет постоянное значение.
2-ая стадия начинается тогда, когда внешнее напряжение достигнет такого значения, что движение дислокаций (скольжение) начинается по вторичным плоскостям, то есть в процесс вступают другие системы скольжения, а первичные оказываются блокированными. На этой стадии дислокации имеют достаточно короткий свободный пробег.
Упрочнение обусловлено взаимодействием скользящих дислокаций с дислокационными барьерами.
Для этой стадии также характерна активная работа источников Франка-Рида (резко увеличивается плотность дислокаций, в большом количестве образуются «сидячие» дислокации), происходит наиболее активное упрочнение в монокристалле. Активный вклад вносят пересечение винтовых дислокаций между собой, так как в результате образуется два порога, которые очень малоподвижны (см. выше).
Стадия 3 (динамический возврат):
При достижении определенного значения τ3 происходит качественное изменение в поведении дислокаций – они начинают огибать барьеры.
Для этой стадии характерно: резкое уменьшение коэффициента деформационного упрочнения; развитие процессов поперечного скольжения.
По завершению стадии формируется ячеистая слабоориентированная (доли градуса) структура. Стадия предшествует разрушению кристалла.
nex7.narod.ru