- Нагрев с охлаждением участка детали: закалка зубьев колес, концов рельсов, клапанов и др.
- Закалка небольших вращающихся тел с малой шириной обрабатываемого участка: цапфы осей и валов.
- Непрерывно-последовательный способ: перемещение по поверхности пламени, а за ним - охладителя. Производится последовательный нагрев и охлаждение водяными струями узких участков. Аналогично закаливаются поверхности деталей большого диаметра с медленным их вращением относительно неподвижных горелок и форсунок. На краях полос остаются зоны отпуска при вторичном нагреве от соседних участков.
- Комбинированный способ: перемещение вдоль образующей струй пламени, а за ними - охлаждающей среды при вращении цилиндрической детали. Технология применяется для закалки длинномерных изделий. Способ обеспечивает получение однородного твердого слоя на поверхности детали.
- Мощность нагрева. Она зависит от расхода ацетилена и скорости перемещения пламени относительно изделия.
- Расстояние от центра факела до нагреваемой поверхности поддерживается на уровне от 2 до 3 мм.
- Продолжительность нагрева или скорость перемещения нагревателя. От этих характеристик, которые подбираются экспериментально, зависит глубина закалки и твердость поверхности.
- В качестве охладителя большей частью применяется вода с температурой 18-350С, а расход составляет около 1 л/см2.
- Время между нагревом и охлаждением (5-10 сек) или расстояние между зонами нагрева с охлаждением (12-25 мм).
- высокая производительность и экономичность нагрева, когда необходимо нагревать только отдельные участки деталей;
- поверхность детали незначительно окисляется, отсутствует обезуглероживание;
- изделия мало коробятся, меньше образуется трещин;
- точно регулируется глубина закалки;
- возможность автоматизации процесса.
- Одновременный. После нагрева деталь охлаждается водой. Закаливаемая деталь нагревается внутри индуктора. Через заданное время электрический ток отключается и через отверстия нагревателя сильными струями подается вода на охлаждение изделия. Для закалки зубчатых колес применяются кольцевые индукторы, а для плоских деталей - петлевые или зигзагообразные.
- Непрерывно-последовательный. Вдоль неподвижной детали перемещается нагревающий индуктор, а за ним - душирующее устройство.
- Закалка в электролите. Если через водный раствор электролита пропускать электрический ток, где катодом является деталь, которая быстро нагревается. Способ удобен, поскольку после отключения электроэнергии деталь тут же закаливается. Ванна с электролитом одновременно выполняет функции нагревательной печи и закалочной емкости.
- Лазерная закалка. Излучение лазера разогревает поверхность металла до высокой температуры. Толщина упрочнения составляет менее 1 мм. Износостойкость деталей из чугуна возрастает в несколько раз, а предел выносливости стали - до 80 %. Способ часто применяется для упрочнения режущих кромок инструмента.
- Низкий отпуск при 120-2500С - обработка инструмента и др. деталей. Металл имеет стабильную структуру, высокую износостойкость и твердость.
- Средний отпуск при 350-5000С - для штампов, пружин, рессор. Структура имеет хорошую пластичность, высокую упругость.
- Высокий отпуск при 500-6800С - среднеуглеродистые конструкционные стали. Обеспечивает высокую прочность, вязкость, пластичность.
- Минимальный радиус изгиба троса стального
- Вес нержавеющей стали листовой
- Гост 3282 74 проволока стальная
- Сталь р6м5к5 характеристики и применение
- Гост стали
- Труба стальная толстостенная
- Стальная прямоугольная труба
- Сортамент труба стальная
- Сортамент гост 3262 75 трубы стальные электросварные прямошовные
- Вес 1 м трубы стальной
- Труба стальная бесшовная
14.9. Способы закалки сталей. Дефекты, возникающие при закалке. Способы закалки стали
9. Назначение и сущность закалки стали. Способы закалки
Закалка - самый распространенный вид термической обработки. Закаливаются валы, шестерни, пружины, штампы, зубила, резцы, фрезы и другие изделия и инструменты. Столь широкое распространение этого вида термической обработки объясняется тем, что при помощи закалки и последующего отпуска можно изменить свойства стали в очень широком диапазоне. Были рассмотрены превращения, которые протекают в стали, имеющей структуру аустенита, при ее охлаждении с различной скоростью.
Закалка стали основана именно на этих превращениях. Операция закалки состоит в том, что стальные изделия нагревают немного выше критических температур Aci, Асз а иногда и Аст и затем быстро охлаждают. В качестве охлаждающей среды применяют воду, масло и растворы солей. Целью закалки чаще всего является повышение твердости и прочности стальных изделий. При закалке имеют место понижение пластичности и вязкости стали, однако эти качества можно восстановить при последующем отпуске.
Как известно из предыдущего, при увеличении скорости охлаждения аустенита можно получить структуры сорбита, троостита или мартенсита. При закалке, как правило, стремятся получить структуру мартенсита, которая обеспечивает максимальную твердость стали.
Структуру сорбита или троостита более целесообразно получать путем отпуска закаленной стали. Закалка является наиболее сложным видом термической обработки, так как она протекает при очень больших скоростях охлаждения, что связано с образованием значительных внутренних напряжений в металле. Поэтому даже небольшие отклонения от установленных режимов обработки приводят к браку в изделии. Существенное влияние на результаты закалки оказывают температура нагрева и скорость охлаждения изделия.
Способы закалки стали:
1. Закалка в одном охладителе (v1).
Нагретую до нужной температуры деталь переносят в охладитель и полностью охлаждают. В качестве охлаждающей среды используют:
воду – для крупных изделий из углеродистых сталей;
масло – для небольших деталей простой формы из углеродистых сталей и изделий из легированных сталей.
Основной недостаток – значительные закалочные напряжения.
2. Закалка в двух сферах или прерывистая (v2).
Нагретое изделие предварительно охлаждают в более резком охладителе (вода) до температуры ~ 3000C и затем переносят в более мягкий охладитель (масло).
Прерывистая закалка обеспечивает максимальное приближение к оптимальному режиму охлаждения. Применяется в основном для закалки инструментов (см. Подкладной инструмент).
Недостаток: сложность определения момента переноса изделия из одной среды в другую.
3. Ступенчатая закалка (v3).
Нагретое до требуемой температуры изделие помещают в охлаждающую среду, температура которой на 30 – 50oС выше точки МН и выдерживают в течении времени, необходимого для выравнивания температуры по всему сечению. Время изотермической выдержки не превышает периода устойчивости аустенита при заданной температуре.
В качестве охлаждающей среды используют расплавленные соли или металлы. После изотермической выдержки деталь охлаждают с невысокой скоростью.
Способ используется для мелких и средних изделий.
studfiles.net
Способы закалки
Закалка в одном охладителе. Этот способ закалки наиболее широко применяется на практике. Деталь нагревают до температуры закалки и охлаждают в одном охладителе. Если охлаждение проводится в жидком охладителе (воде, масле), то для равномерного охлаждения деталь, погрузив в жидкость, перемещают в вертикальном направлении или круговыми движениями.
Для равномерного охлаждения применяется также циркуляция жидкости, что достигается механическим перемешиванием жидкости с помощью специально установленных в закалочном баке лопастей, или создается непрерывное поступление и отвод из закалочного бака охлаждающей жидкости.
Если требуется закалить не всю деталь, а только ее определенную часть, то такая закалка называется местной. Она проводится погружением в охлаждающую жидкость только той части детали, которую необходимо закалить; для этого применяется также струевое охлаждение. В последнем случае деталь помещают в специальное приспособление (аппарат), где места детали, требующие закалки, подвергаются интенсивному охлаждению струями воды.
Недостатком закалки в одном охладителе (если закалка проводится в воде) является возникновение значительных внутренних напряжений, которые могут вызвать появление трещин.
Закалка с подстуживанием. При этом способе закалки деталь вынимают из печи и перед погружением в охлаждающую жидкость некоторое время выдерживают на воздухе – подстуживают. При подстуживании температура детали не должна понижаться ниже критической точки. Подстуживание уменьшает внутренние напряжения и коробление деталей.
Закалка в двух средах. Как указано выше, быстрое охлаждение при закалке необходимо для того, чтобы в процессе охлаждения не происходило распада аустенита на феррито-цементитную смесь в интервале температур 500-600°С. Для превращения аустенита в мартенсит быстрое охлаждение не только не нужно, но и нежелательно, так как именно при быстром охлаждении в интервале мартенситного превращения и могут возникнуть трещины. В интервале мартенситного превращения для уменьшения возникающих структурных внутренних напряжений и для предохранения от возможности возникновения трещин желательно замедленное охлаждение. Этому требованию и удовлетворяет закалка в двух средах. Сущность данного способа заключается в том, что деталь сначала охлаждают до 300-400°С в энергично действующем охладителе – в воде, а затем для окончательного охлаждения переносят в слабый охладитель – в масло. Такая закалка иначе называется закалкой в воде с переброской в масло.
Ступенчатая закалка. Сущность этого способа закалки заключается в том, что нагретую до температуры закалки деталь (или инструмент) охлаждают в расплавленных солях, имеющих температуру немного выше температуры начала мартенситного превращения для этой стали. После выдержки при данной температуре в течение времени, необходимого для выравнивания температуры по всему сечению, деталь вынимают из соляной ванны и охлаждают на воздухе. При выдержке в соляной ванне с температурой, превышающей температуру точки Мн, никаких структурных превращений не происходит и образование мартенсита происходит при охлаждении на воздухе.
В качестве охлаждающей среды при ступенчатой закалке применяют смеси легкоплавких солей, например: смесь, состоящую из 55% азотнокислого калия KNO3 и 45% азотистокислого натрия NaNO2 , температура плавления 137°С; смесь, состоящую из 75% едкого кали KOH и 25% едкого натра NaOH, температура плавления 150°С и др., а также горячее масло.
По сравнению с обычной закалкой в одном охладителе, при ступенчатой закалке возникают значительно меньшие внутренние напряжения, уменьшается коробление и возможность возникновения трещин. После выдержке в соляной ванне с температурой, превышающей температуру точки Мн, сталь находится в состоянии пластичного аустенита и детали легко могут быть подвергнуты правке.
При охлаждении в щелочах деталей, нагретых в соляных ваннах,они сохраняют светлую поверхность, так как хлористые соли при нагревании, а щелочи при охлаждении практически не окисляют поверхности детали. Это дает возможность проводить закалку деталей после их окончательной механической обработки без последующей очистки или травления.
Недостатком ступенчатой закалки является ограниченность ее применения – для углеродистой стали только для мелких деталей диаметром до 10 мм. Это объясняется тем, что для крупных деталей скорость охлаждения в соляной ванне является недостаточной для того, чтобы переохладить аустенит до температуры, немного превышающей температуру начала мартенситного превращения. В связи с недостаточной скоростью охлаждения в зоне наименьшей устойчивости аустенита (500-600°С) происходит его частичный распад с образованием феррито-цементитной смеси, и твердость получается пониженной.
Изотермическая закалка. Изотермическая закалка, впервые предложенная Д.К.Черновым, широко применяется на практике. Так же как и при ступенчатой закалке, охлаждение нагретых до температуры закалки деталей проводится в соляных ваннах. Температура соляной ванны при изотермической закалке 250-400°С. Детали выдерживают в соляной ванне в течение времени , необходимого для полного распада аустенита. После выдержки детали охлаждают на воздухе. В результате изотермической закалки образуется бейнит HRC45-55 в сочетании с достаточной пластичностью. Изотермическую закалку целесообразно применять для деталей, склонных к короблению и образованию трещин.
Для нагрева деталей при закалке применяют камерные печи, тигельные электрические и электродные печи – ванны, вакуумные печи, электропечи с защитной атмосферой и др.
Закалка с обработкой холодом. Сущность этого метода обработки (предложен в 1937г. А.П.Гуляевым) заключается в продолжении охлаждения закаленной стали до температуры ниже +20°С, но в интервале Мн – Мк для дополнительного более полного превращения остаточного аустенита в мартенсит.
Обработка холодом целесообразна только для тех сталей, у которых точка конца мартенситного превращения Мк расположена при температурах ниже комнатной. Для углеродистых сталей обработка холодом целесообразна для сталей при содержании углерода более 0,6%.
Обработка холодом является частью общего цикла термической обработки и проводится немедленно после закалки, так как перерыв в охлаждении стабилизирует аустенит и уменьшает эффект обработки. В результате обработки холодом повышается твердость, увеличивается объем, стабилизируются размеры деталей. Наиболее распространенным охладителем является смесь из твердой углекислоты (сухой лед) с ацетоном (-78о).
studfiles.net
14.9. Способы закалки сталей. Дефекты, возникающие при закалке
Способы закалки сталей. Основные способы закалки стали – закалка в одном охладителе, в двух средах, струйчатая, с самоотпуском, ступенчатая и изотермическая.
Закалка в одном охладителе. Деталь, нагретую до температуры закалки, погружают в закалочную жидкость, где она находится до полного охлаждения. Детали из углеродистых сталей охлаждают в воде, а детали из легированных сталей – в масле. Высокоуглеродистые стали закаливают с подстуживанием, это уменьшает внутренние напряжения в деталях и исключает образование трещин.
Закалка в двух средах, или прерывистая закалка (рис. 4.27). Деталь сначала охлаждают в быстро охлаждающей среде – воде, а затем переносят её в медленно охлаждающую среду – масло. Такой способ применяется при закалке инструмента, изготовленного из высокоуглеродистой стали.
Рис. 4.27. Способы охлаждения при закалки сталей: 1 – непрерывное охлаждение; 2 – закалка в двух средах; 3 – ступенчатая закалка; 4 – изотермическая закалка
Струйчатая закалка. Детали, нагретые до температуры закалки, охлаждают струёй воды. Такой способ применяют для закалки внутренних поверхностей, высадочных штампов, матриц и другого инструмента, у которого рабочая поверхность должна иметь структуру мартенсита. При струйчатой закалке не образуется паровая рубашка, что обеспечивает более глубокую прокаливаемость, чем при простой закалке в воде.
Закалка с самоотпуском. Детали выдерживают в охлаждающей среде не до полного охлаждения, а до определённой стадии, чтобы сохранить в сердцевине детали тепло, необходимое для самоотпуска.
Ступенчатая закалка. При этом способе закалки нагретые детали охлаждают сначала до температуры несколько выше точки Мн (в горячем масле или расплавленной соли), затем после короткой выдержки при этой температуре (до начала промежуточных превращений) охлаждают на воздухе.
Изотермическая закалка. Детали нагревают до заданной температуры и охлаждают в изотермической среде до 220–350°С, что несколько превышает температуру начала мартенситного превращения. Выдержка деталей в закалочной среде должна быть достаточной для полного превращения аустенита в игольчатый троостит. После этого производится охлаждение на воздухе. При изотермической закалке выдержка значительно больше, чем при ступенчатой.
Изотермическая закалка позволяет устранить большое различие в скоростях охлаждения поверхности и сердцевины деталей, которое является основной причиной образования термических напряжений и закалочных трещин. Изотермическая закалка в ряде случаев исключает операцию отпуска, что сокращает на 35–40 % цикл термической обработки.
Светлая закалка. При этом способе закалки детали нагревают в нейтральной безокислительной атмосфере или в расплавленных нейтральных солях. При светлой закалке нагрев деталей или инструмента осуществляют в жидких солях, не вызывающих окисление металла, с последующим охлаждением их в расплавленных едких щелочах.
Дефекты, возникающие при закалке. Основными видами брака являются: образование трещин, деформация и коробление, обезуглероживание и окисление, изменение размеров, появление мягких пятен, низкая твёрдость, перегрев.
Закалочные трещины. В крупных деталях, например в матрицах и ковочных штампах, закалочные трещины могут появляться даже при закалке в масле. Поэтому такие детали целесообразно охлаждать до 150–200 °С с быстрым последующим отпуском.
Чтобы уменьшить скорость охлаждения при закалке легированных сталей и снизить напряжение, эти стали подвергают медленному охлаждению в масле или струе воздуха.
Деформация и коробление. Этот вид брака деталей образуется в результате неравномерных структурных и связанных с ними объёмных превращений и возникновения внутренних напряжений при охлаждении.
Обезуглероживание инструмента при нагреве в электрических печах и жидких средах (соляных ваннах) – серьёзный дефект при закалке, т.к. он в несколько раз снижает стойкость инструмента.
Мягкие пятна. При закалке на поверхности детали или инструмента образуются участки с пониженной твёрдостью. Причинами такого дефекта могут быть наличие на поверхности деталей окалины и загрязнении, участки с обезуглероженной поверхностью или недостаточно быстрое движение деталей в закалочной среде (паровая рубашка). Мягкие пятна полностью устраняются при струйчатой закалке и в подсоленной воде.
Причинами низкой твёрдости являются недостаточно быстрое охлаждение в закалочной среде, низкая температура закалки, а также малая выдержка при нагреве под закалку. Чтобы исправить этот дефект, детали или инструмент сначала подвергают высокому отпуску при температуре 600–625 °С, а затем – закалке.
Перегрев приводит к образованию крупнозернистой структуры, что ухудшает механические свойства стали. Для измельчения зерна и подготовки структуры для повторной закалки перегретую сталь необходимо подвергать отжигу.
Недогрев. Если температура закалки была ниже критических точек Ас3 (для доэвтектоидных сталей) и Ас1 (для заэвтектоидных сталей), то структура закаленной стали будет состоять из мартенсита и зерен феррита, который имеет низкую твёрдость. Недогрев можно исправить отжигом с последующей закалкой.
studfiles.net
4.5. Способы закалки стали.
Выбор того или иного способа охлаждения при закалке определяется во-первых получением наибольшей прокаливаемости и во-вторых минимальным уровнем остаточных внутренних напряжений, чтобы уменьшить коробление деталей.
Используются несколько способов закалки, которые классифицируются по методу охлаждения:
1-закалка в одном охладителе;
2-закалка в двух охладителях;
3-ступенчатая закалка;
4-изотермическая закалка.
Все рассмотренные способы закалки показаны на диаграмме распада переохлажденного аустенита на рис.34.
Закалка в одном охладителе(воде или масле). Это наиболее простой и распространенный способ. Однако, некоторые стали при охлаждении в воде склонны к возникновению трещин. При охлаждении в масле скорость охлаждения меньше, но многие стали при таком охлаждении не закаливаются (скорость охлаждения меньше Vкр и мартенсит не образуется).
Закалка в двух охладителях(через воду в масло). При этом методе в верхнем интервале температур скорость охлаждения велика, но сталь достаточно пластична и значительных напряжений не возникает. При этом способе сталь быстро охлаждается в интервале температур 750–400С, а затем деталь переносится в другую, более мягкую, охлаждающую среду, и в мартенситном интервале охлаждение происходит замедленно, что практически исключает образование трещин. Твердость при таком методе закалки такая же, как при закалке в воде. (рис.34,кривая 2).Это приводит к уменьшению внутренних напряжений и снижает вероятность появления трещин. Примером такой закалки может быть процесс с охлаждением вначале в воде, а затем в масле.
Ступенчатая закалка - заключается в том, что после нагрева детали переносят в печь-ванну с расплавом щелочей (обычно КОН+NaOH). Нагретую до температуры немного выше начала образования мартенсита (на 20-30выше точкиМнт.е. до 350-4000С), выдерживают небольшое время для выравнивания температуры по сечению, а затем охлаждают в масле или на воздухе (рис.34,3). При этом обеспечивается быстрое охлаждение стали в верхней области температур, а затем делается выдержка, во время которой температура по сечению детали выравнивается, и термические напряжения уменьшаются.
Твердость после такой закалки такая же, как и в предыдущих способах, но напряжения и вероятность образования трещин еще меньше. В качестве жидких сред для ступенчатой закалки используют расплавы щелочей, селитры, легкоплавких металлов.
Ступенчатая закалка применяется только для мелких изделий (до 10мм) из углеродистых сталей. Для более крупных деталей ее не применяют, так как в расплаве щелочей скорость охлаждения внутри детали мала.
Для легированных сталей, обладающих высокой устойчивостью переохлажденного аустенита, такую закалку применять нецелесообразно, так как они обычно хорошо закаливаются в масле, которое достаточно медленно охлаждает при температурах образования мартенсита.
Изотермическая закалка проводится так же как и ступенчатая, но в расплаве щелочей детали выдерживают более длительное время (до полного распада аустенита на бейнит (рис.34,4). При этом существенных напряжений не возникает, но твердость получается ниже, чем при других способах закалки. Преимуществом этого способа является то, что после него не требуется отпуска. Изотермическая закалка обычно применяется для деталей сложной формы, склонных к деформациям и образованию трещин.
Обработка стали холодом.
Обработку стали холодом применяют для уменьшения количества остаточного аустенита в закаленных высокоуглеродистых сталях. При охлаждении до -70..-1900С остаточный аустенит превращается в мартенсит.
Обработку холодом проводят непосредственно после закалки путем погружения изделий в смесь авиационного бензина с жидким азотом на 1-1,5 часа.
Обработка холодом обычно применяется:
1. Для инструмента из быстрорежущих сталей и деталей
шарикоподшипников с целью повышения твердости;
2. Для улучшения свойств постоянных магнитов;
3. Для стабилизации размеров точного измерительного инструмента (например, калибров)
Закалка с самоотпуском.
При сквозной прокаливаемости все точки детали имеют практически одинаковую твердость. Однако, для ударного инструмента типа зубил, долот, штампов необходимо иметь высокую твердость рабочей поверхности и напротив высокую ударную вязкость хвостовой части. Этого можно добиться специальными способами охлаждения.
1.Охладить в воде только рабочую поверхность, вынуть деталь из воды и контролировать ее разогрев до нужной температуры по цветам побежалости.
2.Закалить всю деталь, а затем разогревать ее хвостовую часть, контролируя разогрев рабочей поверхности.
studfiles.net
Способы закалки. Способы закалки стали. Виды закалки стали. Технология закалки стали. Режимы закалки сталей.
В зависимости от формы изделия, марки стали и нужного комплекса свойств применяют различные способы охлаждения при закаливании стали.
Закалка стали. Закалка металла. Виды закалки. Температура закалки. Закаливаемость. Прокаливаемость. Критический диаметр.
Режимы закалки стали
1. Закалка в одном охладителе (V1).
Нагретую до нужной температуры деталь переносят в охладитель и полностью охлаждают. В качестве охлаждающей среды используют:
Основной недостаток – значительные закалочные напряжения.
Термическая обработка металла. Термическая обработка металлов и сплавов. Виды термической обработки металлов. Виды термообработки.
2. Закалка в двух сферах или прерывистая (V2).
Нагретое изделие предварительно охлаждают в более резком охладителе (вода) до температуры ~ 3000C и затем переносят в более мягкий охладитель (масло).
Прерывистая закалка обеспечивает максимальное приближение к оптимальному режиму охлаждения. Применяется в основном для закалки инструментов (см. Подкладной инструмент).
Недостаток: сложность определения момента переноса изделия из одной среды в другую.
3. Ступенчатая закалка (V3).
Нагретое до требуемой температуры изделие помещают в охлаждающую среду, температура которой на 30 – 50oС выше точки МН и выдерживают в течении времени, необходимого для выравнивания температуры по всему сечению. Время изотермической выдержки не превышает периода устойчивости аустенита при заданной температуре.
В качестве охлаждающей среды используют расплавленные соли или металлы. После изотермической выдержки деталь охлаждают с невысокой скоростью.
Способ используется для мелких и средних изделий.
Отжиг стали. Отжиг второго рода. Полный отжиг. Неполный отжиг. Полный и неполный отжиг. Изотермический отжиг.Отжиг стали. Отжиг первого рода. Диффузионный отжиг. Отжиг рекристаллизационный. Отжиг для снятия напряжений.
4. Изотермическая закалка (V4).
Отличается от ступенчатой закалки продолжительностью выдержки при температуре выше МН, в области промежуточного превращения. Изотермическая выдержка обеспечивает полное превращение переохлажденного аустенита в бейнит.При промежуточном превращении легированных сталей кроме бейнита в структуре сохраняется аустенит остаточный. Образовавшаяся структура характеризуется сочетанием высокой прочности, пластичности и вязкости. Вместе с этим снижается деформация из-за закалочных напряжений, уменьшаются и фазовые напряжения.
В качестве охлаждающей среды используют расплавленные соли и щелочи.
Применяются для легированных сталей.
Нормализация стали. Температура нормализации стали. Процесс нормализации стали.
5. Закалка с самоотпуском.
Нагретые изделия помещают в охлаждающую среду и выдерживают до неполного охлаждения. После извлечения изделия, его поверхностные слои повторно нагреваются за счет внутренней теплоты до требуемой температуры, то есть осуществляется самоотпуск (см. Отпуск стали). Применяется для изделий, которые должны сочетать высокую твердость на поверхности и высокую вязкость в сердцевине (инструменты ударного действия: молотки, зубила).
www.mtomd.info
Способы закалки - Закалка с полиморфным превращением - Закалка
Так как нет такой закаливающей среды, которая давала бы быстрое охлаждение в интервале температур 650 — 400 °С и медленное охлаждение выше и главным образом ниже этого интервала, то применяют различные способы закалки, обеспечивающие необходимый режим охлаждения.
Закалка через воду в масло
Закалка через воду в масло (закалка в двух средах):
1 — нормальный режим; 2 — недодержка в воде; 3 — передержка в воде.
Для уменьшения скорости охлаждения в мартенситном интервале применяют закалку в двух средах. Вначале деталь погружают в воду и после короткой выдержки в воде переносят в масло. Поэтому такой способ закалки называют закалкой через воду в масло.
Быстрое охлаждение вводе предотвращает перлитное превращение, а последующее замедленное охлаждение в масле уменьшает закалочные напряжения в мартенситном интервале. Наиболее ответственный момент — выдержка в воде, продолжительность которой устанавливают для каждого конкретного изделия. И передержка, и недодержка в воде могут привести к браку.
При недодержке в воде происходит частичный или полный распад аустенита и получается заниженная твердость, а при передержке возникают более сильные закалочные напряжения, которые могут привести к короблению и образованию трещин.
Несмотря на указанные недостатки, закалку через воду в масло широко применяют в производстве режущего инструмента из углеродистой стали (углеродистая сталь обладает небольшой прокаливаемостью, и режущий инструмент из нее нельзя закаливать в масле).
Закалка в воде и горячих средах
Закалка в воде и горячих средах:
1 — закалка в воде; 2 — ступенчатая закалка; 3 — изотермическая закалка.
Другой способ уменьшения скорости охлаждения в мартенситном интервале — ступенчатая закалка. Нагретое до температуры закалки изделие быстро погружают в ванну с горячей средой, а затем после некоторой выдержки выдают на воздух или погружают в холодное масло. Впервые закалка в горячей среде была описана Д. К. Черновым.
В 1885 г. в известном докладе «О приготовлении стальных бронепробивающих снарядов» Д. К. Чернов сообщил, что снарядная сталь при закалке в расплаве свинца с оловом приобретает такую же твердость, как и при закалке в холодной воде. При выборе режима ступенчатой закалки помогает С-диаграмма. Температуру горячей среды (температуру «ступеньки») выбирают вблизи мартенситной точки (на 20 — 30 °C выше нее) в области высокой устойчивости переохлажденного аустенита.
Время выдержки в горячей среде (длина «ступеньки») должно быть меньше инкубационного периода при соответствующей температуре. Ступенчатая закалка более проста в исполнении, чем закалка через воду в масло, и дает более стабильные результаты.
Другое важное преимущество ступенчатой закалки — выравнивание температуры по сечению изделия при выдержке в горячей среде. Мартенситное превращение после этой выдержки происходит при медленном охлаждении и одновременно по всему объему, в результате чего уменьшаются закалочные напряжения.
Наконец, весьма существенное преимущество — то, что сталь при температуре «ступеньки» находится в аустенитном состоянии. После извлечения из горячей среды изделие некоторое время пластично, и его можно править для устранения коробления.
Это особенно ценно для тонких и длинных изделий, при закалке которых даже в горячей среде неизбежно коробление. Часто используют правку вручную, но наилучшие результаты дает правка под прессом. Правка может продолжаться при охлаждении ниже точки Мн, так как непосредственно в момент мартенситного превращения (но не после его окончания) пластичность повышена.
Основной недостаток ступенчатой закалки — малая скорость охлаждения в горячей среде. Поэтому применение ступенчатой закалки к углеродистым сталям ограничено изделиями небольшого сечения (до 8 — 10 мм толщиной).
Изделие большого сечения охлаждается в горячей среде медленно, и аустенит успевает претерпеть эвтектоидный распад. Изделия из легированных сталей, у которых меньше критическая скорость охлаждения, проще подвергать ступенчатой закалке. Так, например, ступенчатой закалкой широко пользуются при обработке инструментов и деталей машин из хромистой стали (ШХ16, ХВГ и 9ХС).
Разновидностью ступенчатой закалки является закалка в горячей среде, температура которой несколько ниже мартенситной точки. Более низкая температура «ступеньки» обеспечивает большую прокаливаемость, а так как количество мартенсита еще невелико, то основные преимущества ступенчатой закалки сохраняются. Но править изделие при этом уже нельзя.
При ступенчатой закалке используют три группы горячих сред: минеральные масла, расплавы селитр и расплавы щелочей.
Если длина «ступеньки», находящейся в температурном интервале бейнитного превращения, больше времени изотермического распада аустенита, то операцию термообработки называют изотермической или бейнитной закалкой. Бейнитное превращение является промежуточным между перлитным и мартенситным (смотрите Бейнитное превращение).
Сталь со структурой нижнего бейнита по механическим свойствам ближе к закаленной на мартенсит, чем к стали с перлитной структурой. При бейнитном превращении происходит мартенситная γ → α-перестройка. По способу практического осуществления рассматриваемый процесс мало отличается от ступенчатой закалки. Поэтому его относят к закалке с полиморфным превращением.
Изотермическую закалку проводят в тех же горячих средах, что и ступенчатую. Время выдержки в горячей среде должно быть больше времени изотермического превращения аустенита, и его можно ориентировочно выбрать, руководствуясь С-диаграммой. Изотермической закалке можно подвергать изделия небольшого сечения, так как в горячей среде охлаждение идет медленно.
При выдержке в горячей среде температура по сечению изделия успевает выровняться еще в большей степени, чем при ступенчатой закалке.
Резкое уменьшение закалочных напряжений и коробления — важное преимущество изотермической закалки.
Кроме уменьшения закалочных напряжений, у изотермической закалки есть и другое преимущество. При одинаковой твердости вязкость нижнего бейнита больше, чем у стали, отпущенной после закалки на мартенсит.
Одной из причин этого считают более однородное распределение карбидных частиц в бейните. При бейнитном превращении в некоторых легированных сталях сохраняется большое количество остаточного аустенита, который не превращается в мартенсит при охлаждении после изотермической выдержки.
Изотермическая закалка таких сталей обеспечивает высокую ударную вязкость, резко уменьшает чувствительность к надрезу и перекосам по сравнению с закаленной на мартенсит и отпущенной сталью. Следовательно, изотермическая закалка позволяет повысить конструктивную прочность стали.
Ниже сравниваются свойства стали 30ХГС после обычной закалки с отпуском и изотермической закалки:
σв, кгс/мм2 | σ0,2, кгс/мм2 | ан, кгс * м/см2 | |
Закалка с 880 °С в воде + отпуск при 520 °С | 110 | 85 | 4,5 |
Изотермическая закалка с 880°С в селитре при 300 °С | 165 | 130 | 6 |
«Теория термической обработки металлов»,И.И.Новиков
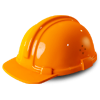
Режим охлаждения при закалке должен прежде всего обеспечить необходимую глубину прокаливаемости. С другой стороны, режим охлаждения должен быть таким, чтобы не возникали сильные закалочные напряжения, приводящие к короблению изделия и образованию закалочных трещин. Закалочные напряжения складываются из термических и структурных напряжений. При закалке всегда возникает перепад температур по сечению изделия. Разная величина термического сжатия наружных…

Во многих сталях мартенситный интервал (Мн — Мк) простирается до отрицательных температур (смотрите рисунок Зависимость температур). В этом случае в закаленной стали содержится остаточный аустенит, который можно дополнительно превратить в мартенсит, охлаждая изделие до температур ниже комнатной. По существу такая обработка холодом (предложена в 1937 г. А. П. Гуляевым) продолжает закалочное охлаждение, прерванное при комнатной…

Многие изделия должны иметь высокую поверхностную твердость, высокую прочность поверхностного слоя и вязкую сердцевину. Такое сочетание свойств на поверхности и внутри изделия достигается поверхностной закалкой. Для поверхностной закалки стального изделия необходимо нагреть выше точки Аc3 только поверхностный слой заданной толщины. Этот нагрев должен совершаться быстро и интенсивно, чтобы сердцевина вследствие теплопроводности также не прогрелась до…

Сквозной нагрев под закалку Превращения в стали при нагревании описаны в Образовании аустенита при нагревании. Температуры нагрева под закалку углеродистых сталей можно выбрать по диаграмме состояния. Доэвтектоидные стали закаливают с температур, превышающих точку А3 на 30 — 50 °С. Наследственно мелкозернистая сталь допускает более высокий нагрев. При перегреве наследственно крупнозернистой стали закалка дает структуру крупноигольчатого…

Прокаливаемость и критическая скорость охлаждения При закалке на мартенсит сталь должна охлаждаться с закалочной температуры так, чтобы аустенит, не успев претерпеть распад на ферритокарбидную смесь, переохладился ниже точки Мн. Для этого скорость охлаждения изделия должна быть выше критической. Критическая скорость охлаждения (критическая скорость закалки) — это минимальная скорость, при которой аустенит еще не распадается на…
www.ktovdome.ru
способы и технологии. Закалка металлов :: SYL.ru
Термическая обработка стали производится для улучшения ее характеристик (твердости, прочности, износостойкости). Основные требования к качеству преимущественно предъявляются к наружному слою изделий, который в наибольшей степени подвергается действию внешних нагрузок.
Необходимость поверхностной закалки и отпуска
Поверхностная закалка деталей делается для достижения лучших характеристик наружного слоя, а в сердцевине металл остается вязким и пластичным. Таким образом удается изменить физико-механические свойства металла.
Чтобы уменьшить хрупкость и остаточные напряжения, металл затем подвергают отпуску, после чего его твердость несколько снижается, а свойства становятся более стабильными.
Температура закалки поверхности стали составляет 820-900 0С. Ее можно различать по цвету.
Для получения необходимой глубины термической обработки после быстрого разогрева поверхность детали охлаждают воздухом или водой.
Газопламенная закалка
Температурные режимы, связанные с нагревом и охлаждением, могут быть непрерывными или цикличными. Поверхностная закалка выполняется четырьмя способами.
Технология газопламенной закалки
Поверхностная закалка производится на станках, где процессы перемещения нагревательно-охлаждающих приспособлений и деталей механизированы. Процесс широко применяется в промышленности. Для него требуются простые устройства. В качестве источника энергии применяется смесь ацетилена с кислородом, природный газ или керосин. Иногда газопламенный нагрев применять более выгодно, чем ТВЧ. Особенно это относится к крупногабаритным изделиям, для которых сложно изготовить индукторы. Способ часто применяют в мелкосерийном производстве, когда к качеству деталей не предъявляются высокие требования. Закалочные горелки инжекторного типа содержат сменные наконечники для регулирования мощности пламени. Мундштуки выполняются в соответствии с профилем обрабатываемых деталей. Их делают с большим количеством сопел или щелевыми. Разбрызгиватели струйного типа подают воду на охлаждение.
Механизмы для перемещений инструментов и деталей применяются специализированные или универсальные. Предприятия часто самостоятельно их изготавливают на базе металлоообрабатывающих станков.
Закалка металлов зависит от состава, а также от размеров и формы изделий.
Параметры процесса
Регулируемые параметры следующие.
Технология закалки стали включает процессы нагрева металла, выдержку для выравнивания температуры с прохождением необходимых структурных превращений и охлаждение с заданной скоростью. Отличительной особенностью поверхностной закалки является быстрый нагрев.
Подготовка деталей перед закалкой заключается в сглаживании острых углов и очистке разными способами: пескоструйная, химическая, щетками вручную.
Поверхностная закалка при правильном режиме обеспечивает повышение стойкости деталей в 2-5 раз. Выбор режимов охлаждения позволяет плавно увеличивать твердость закаленного слоя до 700 HB. Процесс должен проходить быстро. На конечном этапе, когда температура составляет 200-3000С, скорость охлаждения замедляется. В результате уменьшается образование трещин и изделия не коробятся.
При перегреве легированных сталей твердость может уменьшиться, что рассматривается как брак. Здесь также отсутствует возможность точной регулировки толщины закаленного слоя. Кроме того, при работе с газом требуются дополнительные меры по обеспечению безопасных условий труда.
Закалка токами высокой частоты (ТВЧ)
Высокочастотный нагрев является одним из наиболее эффективных способов упрочнения поверхности. Применение ТВЧ до 10 тыс. кГц существенно сокращает время термической обработки. Через водоохлаждаемый медный индуктор пропускается высокочастотный ток. Образующееся электромагнитное поле проникает в деталь из стали, образуя в ней вихревые токи, тем самым вызывая нагрев. Основная энергия сосредотачивается в поверхностных слоях. Глубина прогрева зависит от магнитной проницаемости стали, электросопротивления и частоты тока. Регулируя эти параметры, можно изменять величину закаленного слоя.
Достоинства индукционного метода
К недостаткам метода закалки ТВЧ относится высокая стоимость и сложность изготовления индукционных устройств.
Медные индукторы изготавливаются с душирующими устройствами или без них.
Существуют следующие виды поверхностной закалки.
Нагрев ТВЧ позволяет создавать автоматизированные агрегаты в потоке цехов механической обработки. За счет этого нет необходимости в транспортировке деталей в термические цеха.
Другие способы поверхностной закалки стали
Отпуск после закалки
Закалка и отпуск - это 2 процесса, дополняющих друг друга и обеспечивающих получение качественных деталей. Назначение отпуска - заключительная операция после закалки, формирующая окончательные, более устойчивые свойства металла, обеспечивающая снятие внутренних напряжений. Изделие из стали определенной марки нагревают и выдерживают при соответствующей температуре, после чего охлаждают на воздухе.
Заключение
Закалка и отпуск металла требуют строгого выполнения технологии, которая подбирается для каждой марки стали. При правильном подходе закалка металлов может производиться в домашних условиях.
www.syl.ru