- мебельная фурнитура;
- элементы для оформления домашних и офисных интерьеров;
- автомобильные диски и детали транспортного средства;
- сувенирная продукция;
- сантехническое оборудование.
- при производстве изделий по порошковой технологии;
- при изготовлении пресс-форм, используемых для изготовления изделий из резины и полимерных материалов;
- при производстве отражателей различного назначения;
- для повышения твердости поверхностного слоя и износостойкости режущего, а также специального измерительного инструмента;
- для придания исключительных декоративных характеристик кузовным и другим деталям транспортных средств;
- для обработки деталей, эксплуатируемых в условиях постоянного трения и негативного воздействия внешней среды (элементы парового оборудования и теплосетей, детали автомобильных двигателей и морских судов).
- высокой устойчивостью к коррозии;
- микротвердостью, показатели которой достигают значений 950–1100 единиц по шкале HV;
- высокой пористостью покрытия, его износо- и жаростойкостью;
- низким коэффициентом трения сформированного покрытия;
- большим разбросом толщины хромового слоя (5–300 мкм и даже более).
- хромирование, выполняемое по гальванической технологии;
- диффузионное хромирование, проводимое в герметичной емкости при высокой температуре;
- вакуумное хромирование, требующее использования специальной камеры, в которой создается вакуум;
- каталитическое хромирование, предполагающее, что на поверхность обрабатываемого изделия наносятся специальные жидкости без кислот;
- химическое хромирование изделий из стали и других металлов, которое по технологии выполнения напоминает обычную покраску;
- хромирование по гальванической технологии.
- серную кислоту – 2,25–3 г/л;
- хромовый ангидрид – 225–300 г/л;
- свинец, который обычно входит в состав анода в сочетании с сурьмой или оловом, – 4–6%.
- шлифовка обрабатываемой поверхности, а также ее тщательная полировка;
- промывка изделия и протирание его мягкой тканью;
- изолирование тех участков поверхности, где хромировка не требуется;
- обезжиривание хромируемой детали;
- декапирование изделия, которое позволяет улучшить адгезию наносимого хромового слоя с основным металлом;
- размещение изделия в электролитическом растворе при помощи специального кронштейна.
- Изделие после предварительной подготовки помещается в емкость с электролитическим раствором, в которой уже находится анод.
- Раствор, в который погружают изделие, должен быть предварительно нагрет до требуемой рабочей температуры. Следует иметь виду, что рабочая температура электролитического раствора должна поддерживаться на протяжении всего процесса хромирования. Это необходимо для того, чтобы обеспечить хорошую адгезию наносимого слоя, а также его однородность по структуре и толщине.
- В зависимости от того, какой толщины должен быть хромированный слой, определяют время нахождения изделия в электролитическом растворе.
- Гвоздь финишный оцинкованный
- Покраска оцинкованного листа
- Чем загрунтовать оцинкованное железо автомобиля
- Как согнуть лист оцинковки
- Лист профильный оцинкованный
- Цинк горячий
- Цинк и медь
- Уголок перфорированный оцинкованный
- Оцинкованная гофра для кровли
- Производство труб оцинкованных
- Виды цинкования и их особенности
Электролит для нанесения коррозионностойких покрытий сплавом хром - цинк. Покрытие хром цинк
Хром или Цинк. Статьи компании «"AfrikanParrot"
ЧАСТО ЗАДАВАЕМЫЙ ВОПРОС, ЧТО ЛУЧШЕ (цынк или хром) Оцинкованные ведра, сетки, оцинкованная жесть на крышах домов – вещи настолько привычные, настолько будничные, что мы, как правило, не задумываемся, а почему, собственно, они оцинкованные, а не хром
Цинк
30 | |
Zn | 2 18 8 2 |
ЦИНК | |
65,38 | |
3d104s2 |
Рассказ об элементе №30 – цинке – мы вопреки традиции начнем не с истории его открытия, а с самого важного его применения. Это тем более оправданно, что история цинка не отличается точностью дат. А по значению, это несомненно один из важнейших цветных металлов.
Свидетельством первостепенной важности цинка выступает его дешевизна: на мировом рынке (данные 1960 г.) цинк – третий от конца среди всех металлов. Дешевле его лишь железо и свинец. Дешевизна цинка – 0,29 доллара за килограмм – результат больших масштабов его производства. Ведь и карандаш, к примеру, сделать совсем не просто, но изготовляемые миллионами штук карандаши стоят копейки. Так и с циаком: не «хорош, потому что дешев», а «дешев, потому что хорош».
Цинк и сталь
Как бы громко ни называли наше время: «век полимеров», «век полупроводников», «атомный век» и так далее по сути дела мы не вышли еще из века железного. Этот металл по-прежнему остается основой промышленности. По выплавке чугуна и стали и сейчас судят о мощи государства. А чугун и сталь подвержены коррозии, и, несмотря на значительные успехи, достигнутые человечеством в борьбе с «рыжим врагом», коррозия ежегодно губит десятки миллионов тонн металла.
Нанесение на поверхность стали и чугуна тонких пленок коррозионно-стойких металлов – важнейшее средство защиты от коррозии. А на первом месте среди всех металлопокрытий – и по важности, и по масштабам – стоят покрытия цинковые. На защиту стали идет 40% мирового производства цинка!
Оцинкованные ведра, оцинкованная жесть на крышах домов – вещи настолько привычные, настолько будничные, что мы, как правило, не задумываемся, а почему, собственно, они оцинкованные, а не хромированные или никелированные? Если же такой вопрос возникает, то «железная логика» мигом выдает однозначный ответ: потому что цинк дешевле хрома и никеля. Но дело не в одной дешевизне.
Цинковое покрытие часто оказывается более надежным, нежели остальные, потому что цинк не просто механически защищает железо от внешних воздействий, он его химически защищает.
Кобальт, никель, кадмий, олово и другие металлы, применяемые для защиты железа от коррозии, в ряду активности металлов стоят после железа. Это значит, что они химически более стойки, чем железо. Цинк же и хром, наоборот, активнее железа. Хром в ряду активности стоит почти рядом с железом (между ними только галлий), а цинк – перед хромом.
Процессы атмосферной коррозии имеют электрохимическую природу и объясняются с электрохимических позиций. Но в принципе механизм защиты железа цинком состоит в том, что цинк – металл более активный – прежде, чем железо, реагирует с агрессивными компонентами атмосферы. Получается, словно металлы соблюдают правило солдатской дружбы: сам погибай, а товарища выручай... Конечно, металлы не солдаты, тем не менее, цинк выручает железо, погибая.
Вот как это происходит.
В присутствии влаги между железом и цинком образуется микрогальванопара, в которой цинк – анод. Именно он и будет разрушаться при возникшем электрохимическом процессе, сохраняя в неприкосновенности основной металл. Даже если покрытие нарушено – появилась, допустим, царапина, – эти особенности цинковой защиты и ее надежность остаются неизменными. Ведь и в такой ситуации действует микрогальванопара, в которой цинк принесен в жертву, и, кроме того, обычно в процессе нанесения покрытия железо и цинк реагируют между собой. И чаще всего царапина оголяет не само железо, а интерметаллическое соединение железа с цинком, довольно устойчивое к действию влаги.
Существен и состав продукта, образующегося при «самопожертвований» элемента №30. Активный цинк реагирует с влагой воздуха и одновременно с содержащимся в нем углекислым газом. Образуется защитная пленка состава 2ZnCO3 · Zn(OH)2, имеющая достаточную химическую стойкость, чтобы защитить от реакций и железо, и сам цинк. Но если цинк коррелирует в среде, лишенной углекислоты, скажем, в умягченной воде парового котла, то пленка нужного состава образоваться не может, и в этом случае цинковое покрытие разрушается намного быстрее.
Как же наносят цинк на железо? Способов несколько. Поскольку цинк образует сплавы с железом, быстро растворяя его даже при невысоких температурах, можно наносить распыленный цинк на подготовленную стальную поверхность из специального пистолета. Можно оцинковывать сталь (это самый старый способ), просто окуная ее в расплавленный цинк. Кстати, плавится он при сравнительно низкой температуре (419,5°C). Есть, конечно, электролитические способы цинкования. Есть, наконец, метод шерардизации (по имени изобретателя) применяемый для покрытия небольших деталей сложной конфигурации, когда особенно важно сохранить неизменными размеры.
В герметически закрытом барабане детали, пересыпанные цинковой пылью, выдерживают в течение нескольких часов при 350...375°C. В этих условиях атомы цинка достаточно быстро диффундируют в основной материал; образуется железоцинковый сплав, слой которого не «уложен» поверх детали, а «внедрен» в нее.
Сплавы и немного истории
Уже упоминалось, что история элемента с атомным номером 30 достаточно путана. Но одно бесспорно: сплав меди и цинка – латунь – был получен намного раньше, чем металлический цинк. Самые древние латунные предметы, сделанные примерно в 1500 г. до н.э., найдены при раскопках в Палестине.
Приготовление латуни восстановлением особого камня – χαδμεια (кадмея) углем в присутствии меди описано у Гомера, Аристотеля, Плиния Старшего. В частности, Аристотель писал о добываемой в Индии меди, которая «отличается от золота только вкусом».
Действительно, в довольно многочисленной группе сплавов, носящих общее название латуней, есть один (Л-96, или томпак), по цвету почти неотличимый от золота. Между прочим, томпак содержит меньше цинка, чем большинство латуней: цифра за индексом Л означает процентное содержание меди. Значит, на долю цинка в этом сплаве приходится не больше 4%.
Можно предполагать, что металл из кадмеи и в древности добавляли в медь не только затем, чтобы осветлить ее. Меняя соотношение цинка и меди, можно получить многочисленные сплавы с различными свойствами. Не случайно латуни поделены на две большие группы – альфа и бета-латуни. В первых цинка не больше 33%.
С увеличением содержания цинка пластичность латуни растет, но только до определенного предела: латунь с 33 и более процентами цинка при деформировании в холодном состоянии растрескивается; 33%Zn – рубеж роста пластичности, за которым латунь становится хрупкой.
Впрочем, могло случиться, что за основу классификации латуней взяли бы другой «порог» – все классификации условны, ведь и прочность латуней растет по мере увеличения в них содержания цинка, но тоже до определенного предела. Здесь предел иной – 47...50% Zn. Прочность латуни, содержащей 45% Zn, в несколько раз больше, чем сплава, отлитого из равных количеств цинка и меди.
Широчайший диапазон свойств латуней объясняется прежде всего хорошей совместимостью меди и цинка: они образуют серию твердых растворов с различной кристаллической структурой. Так же разнообразно и применение сплавов этой группы. Из латуней делают конденсаторные трубки и патронные гильзы, радиаторы и различную арматуру, множество других полезных вещей – всего не перечислить.
И что здесь особенно важно. Введенный в разумных пределах цинк всегда улучшает механические свойства меди (ее прочность, пластичность, коррозионную стойкость). И всегда при этом он удешевляет сплав – ведь цинк намного дешевле меди. Легирование делает сплав более дешевым – такое встретишь не часто.
Цинк входит и в состав другого древнего сплава на медной основе. Речь идет о бронзе. Это раньше делили четко: медь плюс олово – бронза, медь плюс цинк – латунь. Теперь «грани стерлись». Сплав ОЦС-3-12-5 считается бронзой, но цинка в нем в четыре раза больше, чем олова. Бронза для отливки бюстов и статуй содержит (марка БХ-1) от 4 до 7% олова и от 5 до 8% цинка, т.е. называть ее латунью оснований больше – на 1%. А ее по-прежнему называют бронзой, да еще художественной...
До сих пор мы рассказывали только о защите цинком и о легировании цинком. Но есть и сплавы на основе элемента №30. Хорошие литейные свойства и низкие температуры плавления позволяют отливать из таких сплавов сложные тонкостенные детали. Даже резьбу под болты и гайки можно получать непосредственно при отливке, если имеешь дело со сплавами на основе цинка.
Растущий дефицит свинца и олова заставил металлургов искать рецептуры новых типографских и антифрикционных сплавов. Доступный, довольно мягкий и относительно легкоплавкий цинк, естественно, привлек внимание в первую очередь. Почти 30 лет поисковых и исследовательских работ предшествовали появлению антифрикционных сплавов на цинковой основе. При небольших нагрузках они заметно уступают и баббитам и бронзам, но в подшипниках большегрузных автомобилей и железнодорожных вагонов, угледробилок и землечерпалок они стали вытеснять традиционные сплавы. И дело здесь не только в относительной дешевизне сплавов на основе цинка. Эти материалы прекрасно выдерживают большие нагрузки при больших скоростях в условиях, когда баббиты начинают выкрашиваться...
Цинковые сплавы появились и в полиграфии. Так, наряду с сурьмяно-оловянно-свинцовым сплавом – гартом для отливки шрифтов используют и так называемый сплав №3, в котором содержится до 3% алюминия, 1,2...1,6% магния, остальное цинк. К роли цинка в полиграфии мы еще вернемся в рассказе о металлическом цинке.
Металлический цинк и снова немного истории
Когда впервые был выплавлен металлический цинк, точно не установлено. Известно, что в Индии его получали еще в V в. до н.э. Получение металлического цинка (под названием тутии или фальшивого серебра) описано у римского историка Страбопа (60...20 годы до н.э.). Позже, однако, искусство выплавки цинка в Европе было утрачено. Правда, цинк ввозили из стран Востока, но в очень небольших количествах, и до середины XVIII в. он оставался редкостью.
Лишь в 1743 г. в Бристоле заработал первый в Европе цинковый завод. А ведь еще в конце XIII в. Марко Поло описывал, как получают этот металл в Персии. Крупнейшие ученые XVI в. Парацельс и Агрикола в своих трудах уделяли место выплавке цинка. В том же XVI в. были предприняты первые попытки выплавлять его в заводских условиях. Но производство «не пошло», технологические трудности оказались непреодолимыми. Цинк пытались получать точно так же, как и другие металлы. Руду обжигали, превращая цинк в окись, затем эту окись восстанавливали углем...
Цинк, естественно, восстанавливался, взаимодействуя с углем, но... не выплавлялся. Не выплавлялся потому, что этот металл уже в плавильной печи испарялся – температура его кипения всего 906°C. А в печи был воздух. Встречая его, пары активного цинка реагировали с кислородом, и вновь образовывался исходный продукт – окись цинка.
Наладить цинковое производство в Европе удалось лишь после того, как руду стали восстанавливать в закрытых ретортах без доступа воздуха. Примерно так же «черновой» цинк получают и сейчас, а очищают его рафинированием. Пирометаллургическим способом сейчас получают примерно половину производимого в мире цинка, а другую половину – гидрометаллургическим.
Следует иметь в виду, что чисто цинковые руды в природе почти, но встречаются. Соединения цинка (обычно 1...5% в пересчете на металл) входят в состав полиметаллических руд. Полученные при обогащении руды цинковые концентраты содержат 48...65% Zn, до 2% меди, до 2% свинца, до 12% железа. И плюс доли процента рассеянных и редких металлов...
Сложный химический и минералогический состав руд, содержащих цинк, был одной из причин, по которым цинковое производство рождалось долго и трудно. В переработке полиметаллических руд и сейчас еще есть нерешенные проблемы... Но вернемся к пирометаллургии элемента №30 – в этом процессе проявляются сугубо индивидуальные особенности этого элемента.
При резком охлаждении пары цинка сразу же, минуя жидкое состояние, превращаются в твердую пыль. Это несколько осложняет производство, хотя элементарный цинк считается нетоксичным. Часто бывает нужно сохранить цинк именно в виде пыли, а не переплавлять его в слитки.
В пиротехнике цинковую пыль применяют, чтобы получить голубое пламя. Цинковая пыль используется в производстве редких и благородных металлов. В частности, таким цинком вытесняют золото и серебро из цианистых растворов. Как ни парадоксально, но и при получении самого цинка (и кадмия) гидрометаллургическим способом применяется цинковая пыль – для очистки раствора сульфата цинка от меди и кадмия. Но это еще не все. Вы никогда не задумывались, почему металлические мосты, пролеты заводских цехов и другие крупногабаритные изделия из металла чаще всего окрашивают в серый цвет?
Главная составная часть применяемой во всех этих случаях краски – все та же цинковая пыль. Смешанная с окисью цинка и льняным маслом, она превращается в краску, которая отлично предохраняет от коррозии. Эта краска к тому же дешева, эластична, хорошо прилипает к поверхности металла и не отслаивается при температурных перепадах.
Мышиный цвет тоже скорее достоинство, чем недостаток. Изделия, которые покрывают такой краской, должны быть немарки и в то же время опрятны.
На свойствах цинка сильно сказывается степень его чистоты. При 99,9 и 99,99% чистоты цинк хорошо растворяется в кпслотах. Но стоит «прибавить» еще одну девятку (99,999%), и цинк становится нерастворимым в кислотах даже при сильном нагревании. Цпнк такой чистоты отличается и большой пластичностью: его можно вытягивать в тонкие нити. А обычпый цинк можно ппокатать в тонкие листы, лишь нагрев его до 100...150°C. Нагретый до 250°C и выше, вплоть до точки плавления, цинк опять становится хрупким – происходит очередная перестройка его кристаллической структуры.
Листовой цинк широко применяют в производстве гальванических элементов. Первый «вольтов столб» состоял из кружочков цинка и меди. И в современных химических источниках тока отрицательный электрод чаще всего делается из элемента №30.
Значительна роль этого элемента в полиграфии. Мы уже упоминали о типографских сплавах на основе цинка, но главное в другом. Из цинка делают клише, позволяющие воспроизвести в печати рисунки и фотографии. Специально приготовленный и обработанный типографский цинк воспринимает фотоизображение. Это изображение в нужных местах защищают краской, и будущее клише протравливают кислотой. Изображение приобретает рельефность, опытные граверы подчищают его, делают пробные оттиски, а потом эти клише идут в печатные машины.
К полиграфическому цинку предъявляют особые требования: прежде всего он должен иметь мелкокристаллическую структуру, особенно на поверхности слитка. Поэтому цинк, предназначенный для полиграфии, всегда отливают в закрытые формы. Для «выравнивания» структуры применяют отжиг при 375°C с последующим медленным охлаждением и горячей прокаткой. Строго лимитируют и присутствие в таком металле примесей, особенно свинца. Если его много, то нельзя будет вытравить клише так, как это нужно. Если же свинца меньше 0,4%, то трудно получить нужную мелкокристаллическую структуру. Вот по этой кромке и «ходят» металлурги, стремясь удовлетворить запросы полиграфии.
Коротко о соединениях цинка
Еще при первых попытках выплавить цинк из руды у средневековых химиков получался белый налет, который в книгах того времени называли двояко: либо «белым снегом (nix alba), либо «философской птерстью» (lana philosophica). Нетрудно догадаться, что это была окись цинка ZnO – вещество, которое есть в жилище каждого городского жителя наших дней.
Этот «снег», будучи замешанным на олифе, превращается в цинковые белила – самые распространенные пз всех белил. Окись цинка нужна не только для малярных дел, ею широко пользуются многие отрасли промышленности. Стекольная – для получения молочного стекла и (в малых дозах) для увеличения термостойкости обычных стекол. В резиновой промышленности и производстве линолеума окись цинка используют как наполнитель. Известная цинковая мазь на самом деле не цинковая, а окисноцинковая. Препараты на основе ZnO эффективны при кожных заболеваниях.
Наконец, с кристаллической окисью цинка связана одна из самых больших научных сенсаций 20-х годов нашего века. В 1924 г. один из радиолюбителей города Томска установил рекорд дальности приема. Детекторным приемником он в Сибири принимал передачи радиостанций Франции и Германии, причем слышимость была более отчетливой, чем у владельцев одноламповых приемников. Как это могло произойти? Дело в том, что детекторный приемник томского любителя был смонтирован по схеме сотрудника нижегородской радиолаборатории О.В. Лосева.
Лосев установил, что если в колебательный контур определенным образом включен кристалл окиси цинка, то последний будет усиливать колебания высокой частоты и даже возбуждать незатухающие колебания, В наши «веселые транзисторные дни» такое событие прошло бы почти незамеченным, но в 1924 г. изобретение Лосева представлялось революционным. Вот что говорилось в редакционной статье американского журнала «Radio-News», целиком посвященной работе нижегородского изобретателя: «Изобретение О.В. Лосева из Государственной радиоэлектрической лаборатории в России делает эпоху, и теперь кристалл заменит лампу!»
Автор статьи оказался провидцем: кристалл действительно заменил лампу; правда, это не лосевский кристалл окиси цинка, а кристаллы других веществ. Но, между прочим, среди широко применяемых полупроводниковых материалов есть соединения цинка. Это его селениды и теллуриды, антимопид и арсенид.
Еще более важно применение некоторых соединении цинка, прежде всего его сульфида, для покрытия светящихся экранов телевизоров, осциллографов, рентгеновских аппаратов. Под действием коротковолнового излучения или электронного луча сернистый цинк приобретает способность светиться, причем эта способность сохраняется и после того, как прекратилось облучение.
Резерфорд, впервые столкнувшись с явлением послесвечения сернистого цинка, воспользовался им для подсчета вылетающих из ядра альфа-частиц. В несложном приборчике, спинтарископе, ударяясь об экран, покрытый сульфидом цинка, эти частицы высекали вспышку, видимую глазом. А если частицы падают на экран достаточно часто, то вместо вспышек появляется постоянное свечение.
Биологическая роль цинка
Фармацевты и медики жалуют многие соединения элемента №30. Со времен Парацельса до наших дней в фармакопее значатся глазные цинковые капли (0,25%-ный раствор ZnSO4). Как присыпка издавна применяется цинковая соль стеариновой кислоты. Фенолсульфонат цинка – хороший антисептик. Суспензия, в которую входят инсулин, протамин и хлорид цинка – эффективное средство против диабета, действующее лучше, чем чистый инсулин.
И вместе с тем многие соединения цинка, прежде всего его сульфат и хлорид, токсичны.
Цинк – один из важных микроэлементов. И в то же время избыток цинка для растений вреден.
Биологическая роль цинка двояка и не до конца выяснена. Установлено, что цинк – обязательная составная часть фермента крови карбоангидразы. Этот фермент содержится в эритроцитах. Карбоангидраза ускоряет выделение углекислого газа в легких. Кроме того, она помогает превратить часть CO2 в ион НCO3–, играющий важную роль в обмене веществ.
Но вряд ли только карбоангидразой ограничивается роль цинка в жизни животных и человека. И если бы было так, то трудно было бы объяснить токсичность соединений элемента №30.
Известно, что довольно много цинка содержится в яде змей, особенно гадюк и кобр. Но в то же время известно, что соли цинка специфически угнетают активность этих же самых ядов; как показали опыты, под действием солей цинка яды не разрушаются. Как объяснить такое противоречие? Считают, что высокое содержание цинка в яде – это то средство, которым змея от собственного яда защищается. Но такое утверждение еще требует строгой экспериментальной проверки. Ждут выяснения и многие другие детали общей проблемы «цинк и жизнь»...
Что можно сказать в заключение об элементе №30. Только одно: элемент этот не очень эффектный (как не очень эффектно и цинковое покрытие). Но для всех нас он разносторонне важен.
Бурундучная рудаНаиболее распространенный минерал цинка – сфалерит, или цинковая обманка ZnS. Разнообразные примеси придают этому веществу всевозможные цвета. Видимо, за это минерал и называют обманкой. Цинковую обманку считают первичным минералом, из которого образовались другие минералы элемента №30: смитсонит ZnCO3, цинкит ZnO, каламин 2ZnO · SiO2 · Н2O. На Алтае нередко можно встретить полосатую «бурундучную» руду – смесь цинковой обманки и бурого шпата. Кусок такой руды издали действительно похож на затаившегося полосатого зверька.
Слово «цинк»Латинское zincum переводится как «белый налет». Откуда пошло это слово, точно не установлено. Некоторые историки науки и лингвисты считают, что оно идет от персидского «ченг», хотя это название относится не к цинку, а вообще к камням. Другие связывают его с древнегерманским «цинко», означавшим, в частности, бельмо на глазу.
За многие века знакомства человечества с цинком название его неоднократно менялось: «спелтер», «тутия», «шпиаутер»... Общепризнанным название «цинк» стало лишь в 20-х годах нашего столетия.
Цинковый чемпионВо всяком деле есть свой чемпион: чемпион по бегу, по боксу, по танцам, по скоростной варке пищи, по отгадыванию кроссвордов... С именем Чемпиона (Чемпиона с большой буквы) связана история первых в Европе цинковых производств. На имя Джона Чемпиона был выдан патент на дистилляционный способ получения цинка из окисленных руд. Случилось это в 1739 г., а к 1743 г. был построен завод в Бристоле с ежегодной продукцией 200 т цинка. Через 19 лет тот же Д. Чемпион запатентовал способ получения цинка из сульфидных руд.
Не в ночь под Ивана КупалуПо старинным преданиям, папоротник цветет лишь в ночь под Ивана Купалу и охраняет этот цветок нечистая сила. В действительности папоротник как споровое растение не цветет вообще, но слова «папоротниковые цветы» можно встретить на страницах вполне серьезных научных журналов. Так называют характерные узоры цинковых покрытий. Эти узоры возникают благодаря специальным добавкам сурьмы (до 0,3%) или олова (до 0,5%), которые вводят в ванны горячего пинкования. На некоторых заводах «цветы» получают иначе, – прижимая горячий оцинкованный лист к рифленому транспортеру.
Не батарея, но аккумуляторПервый в мире электромотор был сконструирован академиком Б.С. Якоби. В 1838 г. всеобщее восхищение вызвал его электроход – лодка с электрическим двигателем, возившая вверх и вниз по Неве до 14 пассажиров. Мотор получал ток от гальванических батарей. В хоре восторженных откликов диссонансом прозвучало мнение известного немецкого химика Юстуса Либиха: «Гораздо выгоднее прямо сжигать уголь для получения теплоты или работы, чем расходовать этот уголь на добывание цинка, а затем уже сжиганием его в батареях получать работу в электродвигателях». В конечном счете Либих оказался прав наполовину: как источник питания электродвигателей батареи скоро перестали применять. Их заменили аккумуляторами, способными восполнять запасы энергии. В аккумуляторах до последнего времени цинк не применяли. Лишь в наши дни появились аккумуляторы с электродами из серебра и цинка. В частности, такой аккумулятор работал на борту третьего советского искусственного спутника Земли.
afrikanparrot.com.ua
Электролит для нанесения коррозионностойких покрытий сплавом хром
Изобретение относится к области гальваностегии, в частности к электролитам для нанесения коррозионностойких покрытий сплавом хром-цинк, и может применяться для защиты поверхности изделий от коррозии и износа. Электролит для нанесения покрытия хром-цинк содержит, г/л: хромовый ангидрид 200-300; сернокислый цинк, гидрат 40-60 и азулен 2-4. Использование электролита позволяет повысить коррозионную стойкость, снизить энергозатраты процесса осаждения. 1 табл.
Изобретение относится к области гальваностегии, в частности к электролитическому осаждению сплава хром-цинк, и может найти применение для защиты изделий от коррозии и износа.
Известен электролит для нанесения коррозионностойких покрытий сплавом хром-цинк, содержащий хромовый ангидрид и сернокислый цинк, гидрат. Недостатком данного электролита является получение покрытий с удовлетворительной коррозионной стойкостью лишь при высокой температуре электролита 50oC и высокой плотности тока 35 А/дм2. Кроме того, присутствие в электролите серной кислоты повышает его агрессивность и усложняет очистку сточных вод. Целью изобретения является повышение коррозионной стойкости покрытий, снижение энергозатрат процесса электроосаждения и облегчение очистки сточных вод. Сущность изобретения заключается в том, что электролит для нанесения коррозионностойких покрытий сплавом хром-цинк, содержащий хромовый ангидрид и сернокислый цинк, гидрат, дополнительно содержит азулен формулы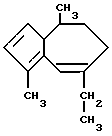
Формула изобретения
Электролит для нанесения коррозионностойких покрытий сплавом хром цинк, содержащий хромовый ангидрид и сернокислый цинк, отличающийся тем, что он дополнительно содержит азулен формулы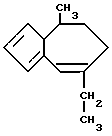
РИСУНКИ
Рисунок 1Похожие патенты:
Изобретение относится к области гальваностегии, в частности к электролитическому осаждению сплава хром-магний, и может найти применение для защиты изделий от износа и коррозии
Изобретение относится к области гальваностегии, в частности к электролитическому нанесению микротвердых покрытий на основе хрома, а именно сплава хром-алюминий, и может найти применение для защиты поверхности изделий от коррозии и износа
Изобретение относится к гальваностегии, в частности к электролитическому осаждению сплава медь-кобальт
Изобретение относится к гальваностегии, в частности, к электролитическому осаждению сплава хром - молибден
Изобретение относится к гальваностегии, в частности к электрическому осаждению сплава цинк-железо, с целью восстановления изношенных поверхностей деталей машин, например, корпусов гидравлических насосов, посадочных мест блоков цилиндров двигателей внутреннего сгорания, коробок передач и др
Изобретение относится к гальванотехнике, в частности к электролитическому осаждению никелевых покрытий, легированных индием до 1%, и может быть использовано в качестве функциональных в радиоэлектронной промышленности для обеспечения сварки ультразвуком, а также в качестве коррозионно-стойких, защитно-декоративных покрытий в ряде отраслей приборостроения и машиностроения
Изобретение относится к электроосаждению покрытий на основе сплава никель-бор и может найти применение в пищевом, электронном машиностроении и медицинской технике как износостойкое покрытие, не содержащее вредных примесей
Изобретение относится к области гальваностегии, в частности к нанесению покрытий сплавами цинка из кислых электролитов, и может быть использовано в радиоэлектронной, автомобильной, электротехнической и других отраслях промышленности
Изобретение относится к области нанесения гальванических покрытий, в частности к электрохимическому осаждению палладия и его сплавов
Изобретение относится к гальваностегии
Изобретение относится к гальваностегии, в частности к электролитическому осаждению сплава медь-никель
Изобретение относится к гальваностегии, в частности к электролитическому осаждению хромовых покрытий на медные и стальные изделия
Изобретение относится к гальванической ванне сплава олово-цинк и способу нанесения гальванического покрытия при ее применении
Изобретение относится к защитным покрытиям на основе никеля, содержащим железо и вольфрам и используемым в разнообразных устройствах для увеличения срока их работоспособности
Изобретение относится к области гальваностегии, в частности, к электроосаждению сплава висмут-марганец, а именно к получению стабильных электролитов с высокой рассеивающей способностью для осаждения качественных коррозионно-стойких покрытий
Изобретение относится к защитным покрытиям на основе никеля, используемым в разнообразных компонентах и устройствах для увеличения срока их работоспособности
Изобретение относится к восстановлению и упрочнению деталей, преимущественно крупногабаритных изделий сложной формы, и может быть использовано в промышленности и ремонтном производстве при повышении долговечности и восстановлении изношенных рабочих поверхностей деталей машин, например шеек коленчатых валов, плунжеров, стержней клапанов двигателей внутреннего сгорания, кулачковых распределительных механизмов и других тел вращения путем нанесения электролитических покрытий на основе железа
Изобретение относится к области гальваностегии, в частности к электролитам для нанесения коррозионностойких покрытий сплавом хром-цинк, и может применяться для защиты поверхности изделий от коррозии и износа
www.findpatent.ru
Цинкование и хромирование стали
14 ноября 2013
Несмотря на то, что сталь является весьма крепким металлом и изделия из неё отличаются высокой прочностью, у неё есть один крайне опасный враг. Время способно сделать даже такой материал хрупким и податливым, особенно сильно в этом направлении старается ржавчина.
Но существуют проверенные временем способы замедления этих вредных процессов. Продлить срок жизни металлических изделий поможет цинкование. Благодаря ему, на стальной поверхности появляется особая «броня», противостоящая негативному воздействию времени и погодных условий до самого конца.
Существуют разные способы нанесения на изделие слоя цинка. Они отличаются между собой не только затратами, а также используемой техникой, но и получающимся на выходе результатом. Наиболее простой и распространенный метод, который используется не только в промышленности, но и в домашних условиях, это гальванизация с использованием электролита. Под воздействием тока, ионы цинка образуют защитный слой на поверхности изделия.
Но провести данную операцию можно и другими методами. Например, холодное цинкование применяется в тех случаях, когда требуется покрыть защитным слоем большой объект. А антипод данного метода подразумевает опускание в емкость с расплавленным цинком стального изделия, в результате чего на поверхности образуется прочный металлический сплав. Но самым высокотехнологичным методом является термодиффузионное цинкование, при котором, под воздействием высоких температур, ионы цинка проникают в верхние слои изделия.
Для придания продукции особых свойств, используется другой метод, называющийся хромирование. Он позволяет, за счет покрытия изделий слоем хрома, делать их прочными, устойчивыми к колебаниям, либо более гибкими. Также применение данной технологии позволяет сделать детали более износостойкими, способными работать в условиях высоких температур, а также предотвратить возникновение и распространение ржавчины.
Хромирование применяется для изделий, которые будут использоваться в медицине, бытовой технике, а также экстремальных условиях. Такое защитное покрытие позволяет продлить срок службы деталей, испытывающих постоянное трение.
Помимо чисто практических целей, данная технология нашла применение в декоративной среде. Покрытие хромом детали, обладают необычным внешним видом. После прохождения данной процедуры, изделия приобретают блестящую, либо приятно молочную фактуру. Разница во внешнем виде, также показывает различие в свойствах предмета.
Читайте также:metalurg.su
Защитно-декоративное хромирование изделий из цинкового сплава (литья под давлением)
Изделия из цинкового сплава широко применяют в автомобильной промышленности, в производстве других видов транспорта, предметов широкого потребления и т. д. Так, например, около 40% деталей кузова легкового автомобиля изготавливают литьем под давлением цинкового сплава. Большая часть таких деталей подвергается защитно-декоративному хромированию по схеме медь — никель — хром. Поскольку толщина хромового покрытия незначительна, то не исключается возможность работы короткозамкнутых элементов никель — хром, причем в обычной атмосфере никель является анодом в паре с хромом. Кроме того, цинковый сплав сам по себе относится к категории материалов с невысокой коррозионной стойкостью.
Несравненно чаще приходится сталкиваться с коррозией хромированных изделий из цинкового сплава, чем с коррозией стальных, хромированных деталей, причем коррозия цинкового сплава проявляется в виде вздутий, в то время как коррозия стальных деталей после защитно-декоративного хромирования обычно проявляется в виде ржавых пятен. 1 Встречающиеся иногда в литературе, особенно патентной, рекомендации непосредственного хромирования цинкового сплава без промежуточного меднения и никелирования не выдерживают никакой критики. Во-первых, коэффициенты линейного расширения цинка и хрома настолько отличаются друг от друга, что в процессе эксплуатации изделий неизбежно образование трещин, в которых интенсивно будет корродировать цинк, а объемистые продукты коррозии цинка будут приподымать (вздувать) лежащее над ним хромовое покрытие. Во-вторых, вследствие пористости самого цинкового литья, в нем застревают обезжиривающие, травильные и другие растворы, и вследствие амфотерности цинка происходит непрерывное взаимодействие его с застрявшими растворами, что также приводит к образованию вздутий.
Изысканию методов усовершенствования защитно-декоративного хромирования изделий из цинкового литья под давлением посвящено большое число исследований, главным образом Американским институтом цинка и Институтом американской телефонной компании.
В целях повышения коррозионной устойчивости хромированных цинковых сплавов было исследовано около 50 различных вариантов хромирования с промежуточным меднением и никелированием. На основании этих исследований были установлены следующие три варианта: 1) с применением двухслойного никеля поверх обычной меди и под обычным хромом; 2) с применением блестящего, беспористого хрома, несколько повышенной против обычной толщины в сочетании с двухслойным никелем и обычной медью; 3) с применением хромового покрытия с микротрещинами по блестящему никелю и обычной меди.
Измерения электродных потенциалов и коррозионных токов на моделях из блестящего никеля и пассивного хрома показали, что скорость коррозионного процесса может быть существенно уменьшена при добавлении к коррозионной среде небольшого количества соединения шестивалентного хрома. Так, добавление 0,01% Na2Cr2O7 к 5%-ному NaCl снижает скорость коррозии до 5%. Это наблюдение дало основание искать причину замедления коррозии в пленке. Из различных методов обработки поверхности хромированного цинка лучшие результаты были получены при катодной обработке в течение 30 с в растворе, содержащем 5 г/л Na2Cr2O7. Плотность тока при катодной обработке 5— 10 мА/дм2 температура 25—27° С. Оптическим методом не удалось обнаружить пленку; рентгенографически было установлено, что пленка в основном состоит из гидратированной окиси хрома и имеет толщину, превышающую 50 Å.
Ускоренные коррозионные испытания, осуществлявшиеся путем распыления раствора медной соли показали, что катодная обработка хромированных цинковых образцов в растворе бихромата натрия оказывает ингибирующее действие на коррозию никеля в порах тонкого (0,25 мкм) слоя хрома. Если без катодной обработки поверхностные дефекты прокорродировавшего никеля под действием струи медной соли появлялись через 18 ч, то после катодной обработки — через 90 ч.
Механическое воздействие, например, окисью магния снимает пленку, образующуюся при катодной обработке в растворе бихромата натрия, но, по-видимому, не всегда полностью, о чем можно судить по результатам некоторых коррозионных испытаний.
При ускоренных испытаниях распылением струи медной соли очаги коррозии основного металла (цинкового сплава) в виде вздутий показывались через 108 ч на образцах, не подвергнутых катодной обработке или подвергнутых с последующей чисткой окисью магния; на образцах, обработанных без последующего механического воздействия, такие очаги появлялись лишь после 252 ч распыления медного раствора. Наружные испытания в различных районах США хромированных цинковых образцов с катодной обработкой в бихромате натрия и без нее дали те же результаты. На цинковых образцах, покрытых медью, двухслойным никелем общей толщиной 30 мкм и хромом толщиной 0,25 мкм с последующей катодной обработкой в бихромате точечные дефекты спустя 10 месяцев были значительно меньше, чем через 5 месяцев на образцах с такими же покрытиями, но без катодной обработки в бихромате натрия. В районе Детройта очагов коррозии на катодно обработанных образцах спустя 10 месяцев было столько же, сколько спустя 5 месяцев на образцах без катодной обработки.
Помимо повышения коррозионной стойкости хромированных цинковых образцов, пленка, образующаяся при катодной обработке в бихромате натрия, повышает также адгезию лакокрасочных покрытий. Установлено целесообразным в раствор бихромата натрия вводить небольшое количество сернокислого хрома, в присутствии которого пленка приобретает повышенное сопротивление механическим воздействиям. Для катодной обработки хромированного цинка рекомендуется следующий состав раствора (г/л) и оптимальный режим: Na2Cr2O72h3O - 50, Cr2(SO4)3 — 1, рН=2,0÷2,3, аноды из нержавеющей стали, продолжительность обработки 1—2 мин.
При обработке, не превышающей 2,5 мин, получается тонкая, невидимая пленка. При прохождении 1,5 А·мин/дм2 пленка получается толще и окрашивается в синий или коричневый цвет.
На сопротивляемость пленки механическим воздействиям влияет температура и рН раствора. С повышением температуры до 94° С сопротивление пленки механическим воздействиям возрастает. Не рекомендуется поддерживать значения рН раствора ниже 1,5 и выше 2,5.
Приведенный метод дополнительной катодной обработки хромированного цинка существенно не повышает общую стоимость процесса и достаточно технологичен.
www.stroitelstvo-new.ru
Хромирование деталей - декоративное покрытие хромом: технология
Под термином «хромирование» может пониматься как диффузионное насыщение поверхности обрабатываемого изделия слоем хрома, так и нанесение хрома по гальванической технологии. Существует также более общий термин – «металлизация». Под ним подразумевается нанесение на обрабатываемую поверхность слоя металла, в роли которого может выступать в том числе и хром.
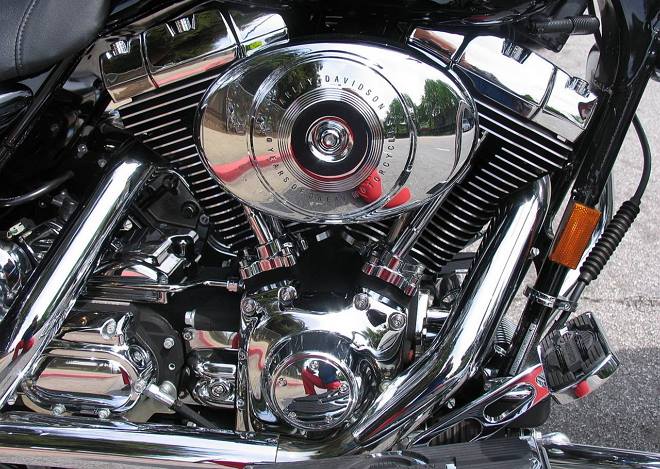
Истинные фанаты хромирования не прочь покрыть хромом все, что только можно
Среди гальванических методов нанесения металла покрытие хромом является наиболее популярным. Именно поэтому термин «металлизация» часто используется в качестве синонима слова «хромирование».
Для чего нужен хромовый слой
Нанесение слоя хрома может выполняться для улучшения декоративных характеристик изделия из металла (декоративное хромирование), а также для защиты металлической детали от коррозии и придания ее поверхности большей твердости. Таким образом, за счет хромирования можно не только улучшить механические и декоративные характеристики изделия, но и значительно продлить срок его эксплуатации.
Множество разнообразных хромированных изделий можно встретить как в быту, так и в разных отраслях промышленности. Использование изделий из металла, на поверхность которых нанесен слой хрома, актуально в тех случаях, когда они будут эксплуатироваться в условиях постоянного воздействия агрессивных сред и интенсивного трения.
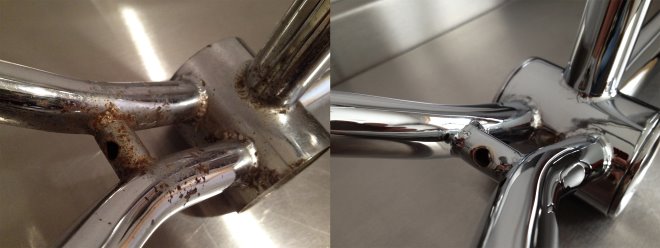
Восстановление хромированного покрытия возвращает былой внешний вид и продлевает срок службы конструкции
В бытовых условиях наиболее активно используются следующие изделия с хромированным покрытием:
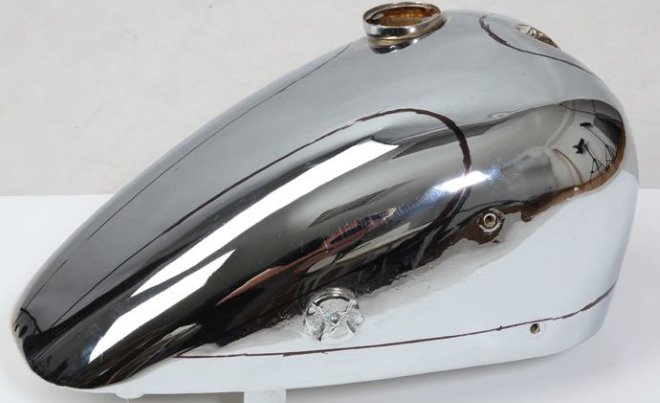
Хромированный бензобак
В промышленности технология хромирования применяется в следующих целях:
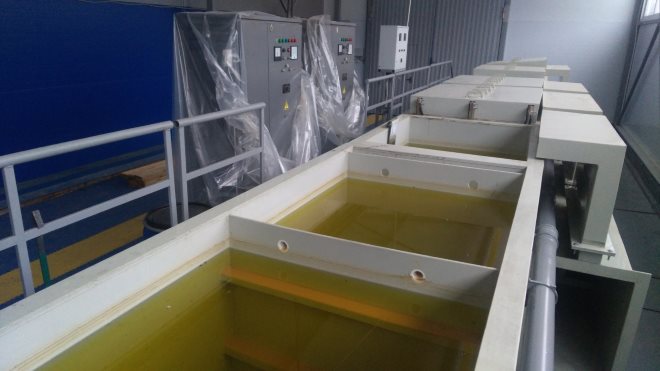
Промышленная гальваническая линия, предназначенная для нанесения твердого хрома на изделия из сталей и цветных металлов
Хромированные детали отличаются следующими характеристиками:
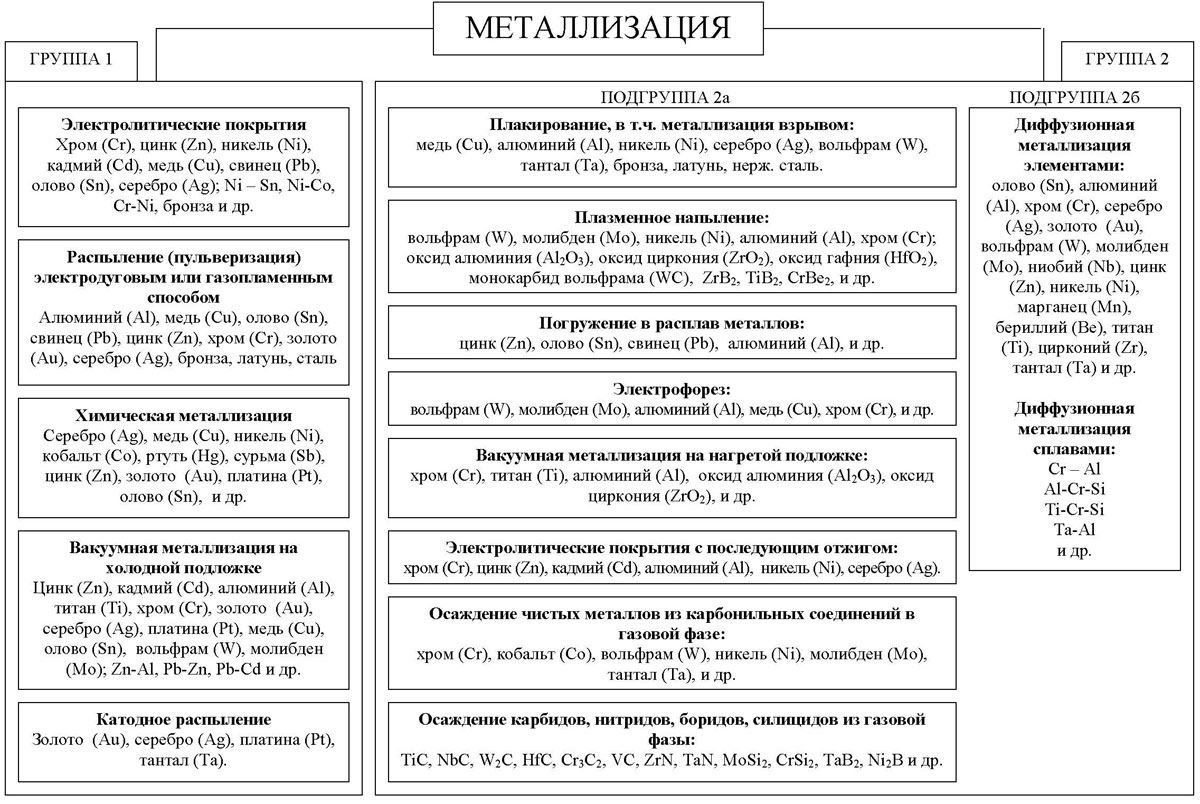
Разновидности металлизации по способу взаимодействия металлизируемой поверхности с наносимым металлом (нажмите для увеличения)
Основные методы
На сегодняшний день выделяют следующие виды хромирования, каждый из которых отличается своими преимуществами и недостатками:
Гальваническое хромирование
Покрытия, получаемые в результате гальванического хромирования, могут быть нескольких типов.
«Твердый хром»Нанесение покрытий данного типа осуществляется при использовании тока, отличающегося высокой плотностью (более 100 А/дм2). Температура электролитического раствора не должна превышать значения 40°. Слой хрома, нанесенный по данной технологии, делает поверхность изделия более твердой, но в то же время и более хрупкой.
«Блестящий хром»Покрытия данного типа наносятся с использованием тока, плотность которого находится в интервале 30–100 А/дм2 и в растворе с температурой в пределах 45–60°. Поверхностный слой металла, на который хромовое покрытие нанесено по данной технологии, приобретает исключительно высокую твердость и износостойкость, а также зеркальный блеск.
«Молочный хром»Для получения хромированных покрытий данного типа используется ток минимальной плотности (до 25 А/дм2). Данный метод хромирования деталей не позволяет получать на них покрытия высокой твердости. Слой хрома, наносимый на поверхность изделия в таких случаях, напоминает очень эластичную массу, в структуре которой практически отсутствуют поры.
Для выполнения такого хромирования необходим трех- или шестивалентный хром. При хромировании металла с применением трехвалентного хрома в качестве основного компонента электролитического раствора используется хромовый ангидрид. При применении шестивалентного хрома в роли такого элемента выступает хлорид или сульфат хрома.
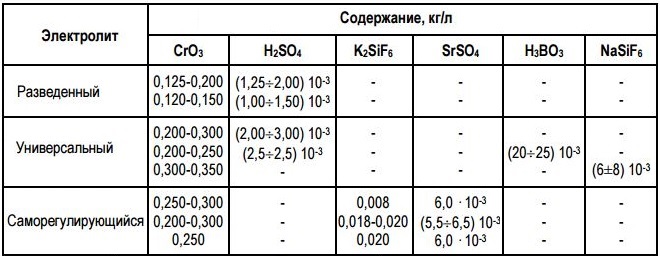
Составы электролитов для хромирования
Растворы, выполненные на основе шестивалентного хрома, содержат в своем составе следующие компоненты:
Большое значение для качества наносимого хромированного покрытия имеет пропорция серной кислоты и хромового ангидрида в используемом электролитическом растворе. Как правило, такое соотношение стараются выдерживать в пределах 1:100. Если оно будет меньше, то поверхность хромируемой детали не будет отличаться высоким качеством, на ней могут возникать отслоения, матовость и различные пятна. Например, если для хромирования используется электролитический раствор, в котором серная кислота и хромовый ангидрид содержатся в соотношении 1:50, то хромовое покрытие не получит достаточно высокой кроющей и рассеивающей способности.
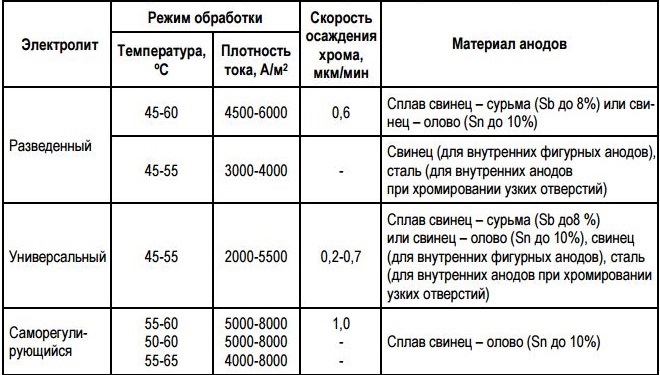
Режимы хромирования и материалы для анодов
Важными параметрами при нанесении хромированного покрытия также являются плотность электрического тока (не выше 310 кА/дм2) и температура электролитического раствора (45–60°). Если увеличить плотность тока, то на угловых и торцевых элементах хромируемой детали могут формироваться дендриты, которые значительно ухудшают декоративные характеристики изделия.
Кроме свинцовых анодов, химический состав которых дополнен сурьмой (не более 6%), для выполнения хромирования сегодня используются аноды из титана, покрытого платиновым слоем. При проведении хромирования желательно не применять растворимые аноды: для изготовления таких элементов лучше использовать листы или стержни из металла, сечение которых составляет порядка 1,5 см.
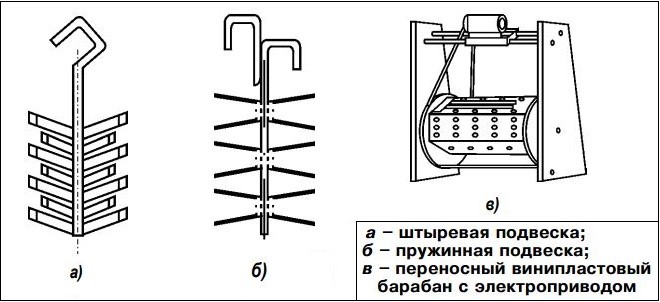
Для погружения изделий в ванну используются специальные контактные приспособления
Аноды для хромирования, изготовленные из свинца, необходимо регулярно чистить при помощи металлической щетки, так как на их поверхности постоянно образуется хромовокислый налет. В том случае, если для нанесения хрома используются титановые аноды, покрытые слоем платины, такую чистку выполнять не потребуется. Если аноды, при помощи которых осуществляется хромирование изделий из стали и других металлов, не применяются в течение нескольких дней, их необходимо извлечь из электролитического раствора и держать все это время в воде.
Как подготовить изделие
Технология декоративного хромирования (как и нанесение слоя хрома в защитных целях) предусматривает тщательную подготовку изделия. Такая подготовка заключается в выполнении таких процедур, как:
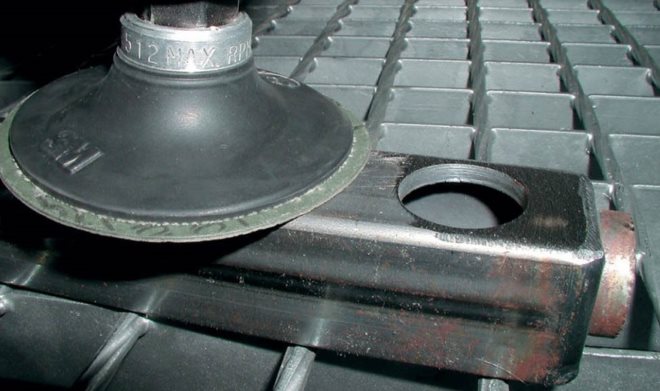
Шлифовка изделия перед хромированием
В отдельных случаях технология декоративного хромирования предусматривает предварительное травление обрабатываемой поверхности и нанесение на нее слоя другого металла (меди или никеля), что способствует увеличению прочности хромового покрытия.
Как проводят процедуру хромирования
Сама технология декоративного хромирования заключается в следующем.

Рекомендуемые режимы сушки хромированных изделий
Технология декоративного хромирования предусматривает также выполнение термообработки детали (этот этап нужен для того, чтобы хромовое покрытие было более твердым и прочным). Изделие, на поверхность которого уже нанесен слой хрома, выдерживают в течение нескольких часов в нагревательной печи при температуре порядка 200°.
На видео ниже подробно показан процесс гальванического хромирования с комментариями в виде субтитров.Химический способ
В настоящее время активно применяется технология декоративного хромирования, не предполагающая использования электролитического раствора. Таким способом, суть которого заключается в том, что хром из рабочего раствора осаждается на поверхности обрабатываемого изделия, выполняется хромирование алюминия и других металлов, а также деталей из полимерных материалов.
Рабочий раствор, используемый для выполнения такого хромирования, готовится на основе хромосодержащего реагента, дистиллированной воды и гипофосфита натрия. В процессе хромирования, которому подвергается алюминиевый или любой другой сплав, гипофосфит натрия восстанавливает хром из его солей, и металл оседает тонким слоем на поверхности обрабатываемого изделия. За счет того, что в используемых для выполнения такого хромирования химических реагентах содержится фосфор, готовый хромовый слой, частично насыщаемый данным элементом, отличается достаточно высокой прочностью.
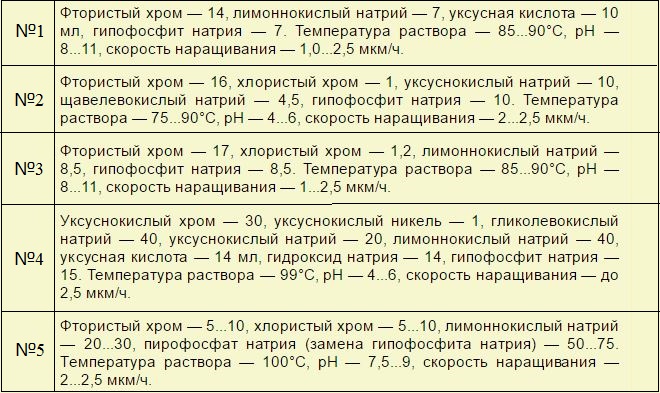
Составы растворов для химического хромирования
Химический способ нанесения хромового покрытия отличается не только простотой реализации, но и большей экологической безопасностью, если сравнивать его с другими технологиями хромирования. Такой способ, при помощи которого можно хромировать алюминий, сталь и даже полимерные материалы, используют даже в домашних условиях.
Выполняя хромирование деталей автомобиля или других изделий по химической технологии, следует иметь в виду, что готовое покрытие получается матовым и отличается непривлекательным сероватым оттенком. Чтобы придать такому покрытию характерный хромовый блеск, необходимо провести финишную полировку.
При помощи технологии хромирования изделиям из различных металлов и полимерных материалов можно придавать не только защитные свойства, но и исключительные декоративные характеристики. Например, возможно нанесение на различные детали черного хрома, покрытие из которого делает их внешний вид эффектным и презентабельным.Оценка статьи:

Поделиться с друзьями:
met-all.org
Хроматные покрытия - Справочник химика 21
Хроматные покрытия наносят на поверхности цинковых, оцинкованных или кадмированных деталей. Применяются они также для защиты от коррозии деталей из магния, меди, алюминия и других металлов. Основным компонентом хро-матных покрытий являются соединения трех- и шестивалентного хрома и хромата металла основы. Тонкие, светлые покрытия состоят преимущественно из соединений трехвалентного хрома, тогда как более толстые слои желтого цвета содержат одновременно соединения трех- и шестивалентного хрома. Процесс хроматирования осуществляется в растворе, содержащем чаще всего хромовый ангидрид, бихромат натрия или калия, небольшие количества серной и азотной кислот, а также активаторы — муравьиную кислоту, хлорное железо, нитрат цинка. [c.129] ХРОМАТНЫЕ ПОКРЫТИЯ на цинке получают, погружая очищенный металл на несколько секунд в раствор бихромата натрия (например, 200 г/л), подкисленный серной кислотой (например, 8 мл/л) при комнатной температуре, а затем подвергая его промывке и сушке (хроматирование). Хромат цинка, образующийся на поверхности, придает ей желтоватый цвет и защищает металл от образования пятен и изменения цвета под действием сконденсированной влаги. Он несколько увеличивает также срок службы цинка в атмосферных условиях. Аналогичные покрытия рекомендуются и для нанесения поверх цинк-алюминиевых [131 и кадмиевых покрытий на стали. [c.247]Толстые хроматные покрытия после осветления можно окрашивать в водных растворах некоторых органических красителей. Это очень рекламировалось разными фирмами, однако такой процесс не нашел практического применения из-за малой стойкости получаемого цвета. [c.107]
Процесс нанесения хроматных покрытий. состоит из следующих операций [c.188]
Хроматирование применяют на цинке, алюминии, магнии и латуни. Обработку проводят, используя водный раствор хромовой кислоты или хромата, часто содержащий другие добавки, например фосфорную и соляную кислоты. На поверхности образуется тонкое (0,1-2,0 г/м ) хроматное покрытие зеленого, желтого, черного или бледно-голубого цвета, которое заметно улучшает ее коррозионную стойкость. Хроматирование широко применяют для оцинкованной стали с целью защитить ее от образования белой ржавчины во время транспортировки и хранения. Его значительное неудобство состоит, однако, в том, что у работающих с некоторыми типами хроматированных материалов, может возникнуть аллергическая экзема в результате контакта с шестивалентным хромом. Другое неудобство состоит в том, что такие средства защиты от белой ржавчины труднее удаляются и могут впоследствии затруднить окрашивание. В настоящее время предпринимают значительные усилия чтобы разработать эффективную защиту против белой ржавчины, не имеющую недостатков свойственных хроматированию. [c.84]
Хроматирование широко применяют так же для алюминия, как при его подготовке к окрашиванию, так и для получения самостоятельного декоративного покрытия. Желтое хроматирование улучшает адгезию лакокрасочного покрытие к алюминиевой поверхности. Зеленые хроматные покрытия (без окрашивания) часто можно видеть в Швеции на алюминиевых крышах. [c.84]
Предложенное хроматное покрытие хорошо защищает алюминий от коррозии под слоем краски, так как наряду с ионом хромата содержит ионы бария, нитрата и фторсиликата. Это покрытие на алюминии противостоит воздействию солевого тумана в течение 386 ч. Покрытие образуется на металле при комнатной температуре в течение 1 мин pH раствора поддерживается в пределах 1,2—1,6. Для его при- [c.117]
С какой целью наносятся фосфатные и хроматные покрытия [c.191]
Хроматные покрытия наносятся как сами по себе, так и под окраску. Они становятся неэффективными прч удалении из пленки (под действием влаги) всего шестивалентного хрома или после нагревания. Они могут лакироваться и окрашиваться. [c.157]
Комбинированное хром-хроматное покрытие также обладает более высокой защитной способностью по сравне нию с хромовым. Хром-хроматное покрытие можно получить обработкой полученного хромового покрытия на катоде в растворе хромового ангидрида 50. .. 100 г/л и гидроокисей или карбонатов щелочных или щелочноземельных металлов, взятых в количестве 20. .. 50 % от массы хромового ангидрида. На поверхности хромовых покрытий образуются плотные прочные прозрачные пленки хроматов. [c.692]
Главными компонентами хроматных покрытий являются соединения трех- и шестивалентного хрома и хроматы металла-основы. Тонкие (светлые) покрытия состоят преимущественно из соединений трехвалентного хрома, в то время как толстые (желтые) слои содержат одновременно соединения Сг (III) и Сг (VI). Соединения шести валентного хрома легче растворяются в водных растворах, именно поэтому твердость и коррозионная стойкость покрытия определяется наличием соединений трехвалентного хрома. Для получения покрытий повышенной твердости проводится дополнительная операция ( осветление ), заключающаяся в том, что предметы с цинковой или кадмиевой поверхностью погружают на 5—10 с в 2%-ный раствор едкого натра. [c.188]
Защитное действие этих хроматных покрытий невелико. Но во многих случаях бывает достаточным увеличение коррозионной стойкости в 15 раз 536], Если же необходимо получить очень хорошую защиту, то целесообразнее на хроматную пленку или иа цинковое покрытие, подвергнутое другой предварительной обработке, нанести слой лака. Предварительное хроматирование цинкового слоя или обработка другим способом даст при этом сцепляющий подслой [53в]. [c.705]
Хроматные покрытия на цинке [c.929]
О фосфатных и хроматных покрытиях, получаемых химическими способами см. стр. 59. [c.106]
ХРОМАТНЫЕ ПОКРЫТИЯ НА ЦИНКЕ [c.929]
Радужный оттенок, вызванный хроматированием, можно удалить в осветляющей ванне, содержащей едкий натр ( 20 г/л) за 5—10 с при комнатной температуре. После осветления необходима очень тщательная промывка. Осветление снижает в определенной степени защитные свойства хроматных покрытий и применяется в том случае, когда радужный цвет не приемлем. [c.107]
Хроматное покрытие затрудняет пайку, особенно когда оно получено в растворах, дающих интенсивное окрашивание слоя. В таких случаях следует не применять хроматирования или наносить очень тонкие слои, сократив время обработки. Ванны для хроматирования — из винипласта. Нагрев не нужен, если температура в помещении >18°С. [c.107]
Стандарты на хроматные покрытия [c.108]
Стандарт PN-82/H-97018 на обычные хроматные покрытия на цинке и кадмии содержит ряд подробностей, с которыми должны быть ознакомлены работники мастерских, занятые цинкованием и кадмированием. [c.108]
Норма предусматривает следующие виды хроматных покрытий А — бесцветные с легким голубым оттенком, В — бесцветное с легким опаловым оттенком, С — желтое, О — оливковое. [c.108]
Методы получения хроматных покрытий. В последние годы разработано несколько усовершенствованных методов получения хроматных покрытий, обеспечивающих быструю обработку по- [c.526]
При обработке цинка или кадмия в подкисленном растворе бихромата наибольшая скорость роста пленки наблюдается в первые 15—20 с, после чего она уменьшается, а через 50—60 с рост пленки прекращается. Предельная толщина пленки зависит от температуры раствора, кислотности и содержания в нем ионов-активаторов. С учетом этого детали с пассивированным цинковым или кадмиевым покрытиями не следует промывать в горячей воде — при этом может произойти частичное растворение хроматов, а сушка деталей при температуре выше 70 С способствует разложению компонентов пленки. В обоих случаях будет ухудшаться защитная способность покрытий. При 120 °С хроматное покрытие разрушается. [c.269]
Хроматные покрытия на магниевых сплавах 931 [c.931]
ХРОМАТНЫЕ ПОКРЫТИЯ НА МАГНИЕВЫХ СПЛАВАХ [c.931]
Пример хроматное покрытие получено из раствора, содержащего, г/л СгО, 6, Ba(N03>j 2, Na SiFj 1,4. Раствором обрабатывают алюминиевые сплавы 6063 и 7075, которые используются для архитектурного оформления зданий. Показатель pH раствора поддерживается в пределах 1,3—1,4. Время обработки сплава раствором составляет 1 мин при температуре 29 °С получаемое покрытие бесцветно. Покрытие подвергалось и пытaниюJв 5 %-ном солевом тумане согласно MIL- -5541A в течение 336 ч. По окончании испытаний следов коррозии не наблюдалось. [c.118]
Хроматные покрытия образуют окисную пленку, пассивирующую поверхность металла. Толщина хроматной пленки достигает 1 мкм. При хорошей подготовке поверхности металла и правильном проведении пассивации пленка получается беспори-стой и прочно сцепляется с основой. Хроматные покрытия иногда применяются в качестве подслоя перед нанесением лакокрасочных или других органических покрытий. Хроматирование используется для защиты алюминия, серебра, магния, кадмия, цинка. [c.56]
Хроматные покрытия чаще всего создаются на поверхности цинковых или оцинкованных изделий, а также на поверхности кадмнрованных деталей. Они также применяются для защиты магния, меди, алюминия и других металлов. [c.188]
Коррозионная стойкость хроматных покрытий Иридит на различных металлах [c.656]
Способ подготовки поверхности зависит от природы склеиваемых материалов, конструктивных особенностей изделия, условий эксплуатации и типа используемого клея. Способь подготовки поверхности можно резделить на физические (механические), химические и физико-химические. Наиболее эффективны химические способы. Для повышения коррозионной стойкости соединений на склеиваемые поверхности после обработки или непосредственно после обезжиривания целесообразно наносить защитные покрытия (хроматные покрытия, анодные пленки и т. д.). Склеивание деталей со свежеподготовленными поверхностями, как правило, повышает прочность и долговечность клеевых соединений [252, с. 32]. [c.156]
Укажем ряд стандартов ПНР, пригодных для практики работы мастерских РМ-82/Н-97005 — Электролитические цинковые покрытия , РЫ-82/Н-97008 — Электролитические кадмиевые покрытия , РЫ-74/Н-97011 — Электролитические оловянные покрытия на стали, меди и ее сплавах , РН-81/Н-97010 — Электролитические серебряные покрытия , РМ-83/Н-97006 — Электролитические никелевые, никельхромовые и медьникельхромовые покрытия , PN-83/H-97009 — Электролитические никелевые и никельхромовые покрытия на меди и ее сплавах , РН-83/Н-97017 — Электролитические медьни-келевые и медьникельхромовые покрытия на сплавах цинка , РЫ-82/Н-97018 — Хроматные покрытия на цинке и кадмии , РМ-80/Н-04605 — Определение толщины металлических покрытий разрушающими методами , РН-79/Н-04607 — Электролитические металлические покрытия. Определение сцепляемости качественными методами , РН-76/Н-04623 — Измерение толщины металлических покрытий неразрушающими методами , РН-73/Н-04652 — Металлические покрытия. Назначение и обозначение , РК-80/Н-97023 — Анодные оксидные покрытия на алюминии , РК-68/Н-04650 — Классификация климатов. Способы изготовления технических изделий , РМ-71/Н-04651 — Классификация и определение агрессивности коррозионных сред , РЫ-72/Н-01015 — Гальванотехника. Названия и определения [c.28]
Хроматные пленки, полученные указанными способами, обладали достаточным сцеплением с основой и коррозионной стойкостью, позволяющей рекомендовать эти хроматные покрытия для проверки на опытной партии алюминиевых радиаторов автомащин. [c.100]
Хроматные покрытия наносят на цинк погружением очищенного металла на несколько секунд в раствор бихромата натрия, подкисленного Н2504 (например, 200 г/л ЧааСгзО , [c.198]
chem21.info
Заказать бесцветное цинкование в Екатеринбурге. Срочно. Цены
Заказать
Есть вопросы? elhim.ekb@yandex.ru // 8-912-044-66-44, 8-953-822-86-85
Пример обозначения цинкового покрытия толщиной 9 мкм с бесцветным хромитированием (без Cr6+): Ц9хр.бцв
Оптимальный ряд толщин: 6-50 мкм (возможна и большая толщина).
Заказать оцинковку стали с бесцветным хромитированием по ГОСТ 9.305-84 вы можете по телефонам и электронной почте, указанным в разделе "КОНТАКТЫ". Для ускорения расчетов просим воспользоваться специальной формой для on-line заказа. Гарантия на покрытие согласно ОСТ5 Р.9048-96.
Описание покрытия. Белая оцинковка чаще всего применяется для защиты стальных деталей от коррозии в легких условиях эксплуатации (сухие отапливаемые помещения). Блестящий бесцветный цинк по внешнему виду похож на хром или никель и это определяет область его применения в качестве условно-декоративного покрытия (нужно учитывать возможность изменения цвета и потускнения цинка со временем, в отличие от хрома). По защитной способности белая оцинковка уступает радужной и оливковой. В зависимости от необходимой степени защиты металлической поверхности (что напрямую связано с классом агрессивности окружающей среды и предполагаемым сроком эксплуатации изделия) толщина цинка может составлять от 1 мкм до 50 мкм. Оптимальными же следует признать толщину покрытия от 6-9 мкм. Толщина белой хромитной пленки составляет не более 0,025-0,08 мкм, шестивалентного хрома в ней не содержится. Стойкость белого цинка без дополнительной обработки полимерными составами в 5% солевом тумане составляет 20-80 часов. Применение нового раствора для хромитирования позволяет увеличить стойкость в солевой камере до 240 часов.
Микротвердость цинка, наносимого электрохимическим способом, составляет в среднем 490-1180 МПа (50-120 кгс/мм2), причем блестящие покрытия отличаются большей твердостью и меньшей пластичностью, чем полублестящие. Вид пассивации практически не влияет на микротвердость.
Удельное электрическое сопротивление гальванического цинка при температуре 18°С составляет 5,75⋅10-8 Ом⋅м, что несколько больше, чем у металлургического из-за вхождения в состав покрытия углерода и серы из электролита. Следует помнить, что переходное сопротивление цинка может меняться в зависимости от способа пассивации (бесцветная пленка будет обладать самым низким сопротивлением, радужная - средним, оливковая и фосфатная - самым большим).
Допустимая рабочая температура цинкового покрытия - 300°С, выше нее покрытие повреждается.
Достоинства цинкового покрытия на стали с бесцветным хромитированием:
а) Белое цинковое покрытие анодно по отношению к стали и защищает ее от коррозии до 70°С. При более высоких температурах покрытие катодно. Анодный характер позволяет защищать стальные изделия от коррозии даже при наличии повреждений цинкового покрытия (царапины, поры, сколы). По способности защищать сталь от коррозии в нейтральных средах цинк превосходит все виды оксидирования и пассивации, а также все виды катодных покрытий (никель, хром, медь и т.п.) при равной толщине.
б) ХромИтирование наряду с увеличением коррозионной стойкости также улучшает внешний вид оцинкованных изделий за счет эффекта химической полировки. Бесцветная хромИтная пассивация сегодня одна из наиболее часто применяемых в промышленности.
в) ХромИтные бесцветные пленки не содержат токсичного шестивалентного хрома и соответствуют самым жестким европейским экологическим требованиям.
г) Также как и другие виды цинка, белый цинк предотвращает контактную коррозию стали при сопряжении с деталями из алюминия и его сплавов.
д) Бесцветная оцинковка обеспечивает легкую свинчиваемость резьбовых деталей.
е) Хромитированное цинковое покрытие может применяться для обеспечения электропроводности и при опрессовке пластмассами при температуре выше 100°С.
ж) Наносимый на нашем предприятии блестящий цинк хорошо выдерживает пластические деформации: гибку, развальцовку.
Недостатки цинкового покрытия на стали с бесцветным хромитированием:
а) ХромИтная пленка на цинке очень тонкая и механически сравнительно непрочная. Она теряет свой декоративный вид при условии постоянного механического воздействия.
б) Электрохимическое цинкование вызывает некоторую потерю пластичности сталей вследствие наводороживания. Стали с пределом прочности выше 1380 МПа; (140кг/мм2) цинкованию не подлежат.
в) Цинк обладает повышенной хрупкостью при температурах выше 250°С и ниже минус 70°С.
г) Белое цинковое покрытие слабоустойчиво к воздействию продуктов, выделяющихся при старении органических материалов.
д) Бесцветная хромИтная пленка не обладает свойством "самозалечивания", т.е. не способна восстанавливать свои свойства при небольших механических повреждениях, например, царапинах, в отличие от хроматных пленок.
Принимаем заказы на оцинковку как в Свердловской области (Екатеринбург, Алапаевск, Асбест, Березовский, Верхняя Пышма, Верхотурье, Ирбит, Каменск-Уральский, Камышлов, Краснотурьинск, Красноуфимск, Нижний Тагил, Новоуральск, Полевской, Ревда, Реж, Серов, Североуральск и другие), так и по всему Уралу и России (Челябинск, Пермь, Уфа, Тюмень, Казань, Новосибирск Москва и другие).
Подробнее о цинковании стали:
О ГАЛЬВАНИЧЕСКОМ ЦИНКОВАНИИ (ОЦИНКОВКЕ) СТАЛИ.
О РАЗЛИЧНЫХ ВИДАХ ПАССИВАЦИИ ЦИНКОВЫХ ПОКРЫТИЙ.
ЗАКАЗАТЬ ОЦИНКОВКУ СТАЛИ В ЕКАТЕРИНБУРГЕ.
КОНТРОЛЬ КАЧЕСТВА ПОКРЫТИЙ
ЦИНКОВАНИЕ АВТОМОБИЛЬНЫХ ИЗДЕЛИЙ
zctc.ru