- вытяжка;
- растяжение;
- штамповка;
- формовка;
- изгиб.
- Холодная штамповка. С ее помощью изготавливают детали из вязких и пластичных материалов. Это сплавы с повышенным процентным содержанием никеля. К ним относятся аустенитные виды нержавеющей стали. Для обработки холодным способом используют листы, ленты, полосы, толщина которых составляет меньше 6 мм.
- Горячая штамповка. Этот процесс предполагает обработку металла при нагреве, что приводит к увеличению его пластичности. В этом случае толщина и масса заготовок не имеют значения. При этом материал должен обладать повышенной прокаливаемостью, быть не восприимчивым к местному нагреву.
- Ротационная. Используется для производства изделий в виде полых тел вращения: конусов, колец, колпаков, посуды, космических и авиационных приборов, деталей для автомобилей, спутниковых антенн. Этот метод отличается от аналогичных способов своей экономичностью. Кроме того, он способствует упрочнению поверхности деталей, позволяет избежать концентрации поверхностных и внутренних слоев металла, не приводит к возникновению микротрещин. Для проведения ротационной вытяжки используют токарно-давильные станки. Она позволяет в сжатые сроки видоизменять технологические процессы и перенастраивать оборудование для выпуска новых видов продукции.
- Глубокая. В основе метода лежит свойство пластической деформации, которое сопровождается утончением стенок заготовки и смещением материала по высоте детали. В отличие от ротационной вытяжки технология данного способа не использует «торможения», материал детали свободно перемещается в инструментах. Для обработки методом глубокой вытяжки применяются специальные прессы. Данный способ используется для заготовок из нержавеющей стали с минимальным значением упрочнения. Полые детали, изготавливаемые этим способом находят применение в космической, авиационной, автомобильной промышленности, в быту, при проведении научных исследований: это стаканы, колбы, баки, корпуса, бытовая и лабораторная посуда.
- производства изделий различных геометрических форм и размеров, качество и точность изготовления которых позволяют сразу использовать их по прямому назначению;
- полной механизации и автоматизации производственных процессов, что достигается, в частности, путем оснащения производства роторно-конвейерным оборудованием для штамповки листового металла;
- серийного производства изделий, геометрические параметры которых отличаются особо высокой точностью (такие изделия могут быть легко заменены друг на друга, если в этом возникает необходимость).
- электрическая и магнитная проводимость материала, который будет подвергаться обработке;
- твердость и механическая прочность металла;
- масса заготовки;
- ударная вязкость, которой обладает обрабатываемый металл;
- теплопроводность металла, а также его теплостойкость;
- степень устойчивости металла к коррозии и его износостойкость, что будет оказывать влияние на долговечность, которой будет обладать штампованный лист.
- Приводной электродвигатель передает движение на кривошипный вал через кинематическую цепочку, состоящую из клиноременной передачи и фрикционной муфты.
- Чтобы сообщить движение ползуну кривошипного механизма, используется шатун, длина которого может регулироваться.
- Чтобы запустить рабочий ход пресса, используют ножную педаль.
- Обозначается структура основных операций, включающая их характер, количество и последовательность выполнения.
- Выполняется расчет первоначальных, промежуточных и готовых размеров детали, а также необходимых деформационных усилий для достижения нужного результата.
- Проводится документальное оформление технологического процесса.
- эксцентриковые прессы;
- прессы с использованием кривошипно-шатунного механизма.
- составляется эскиз штампа;
- с помощью компьютерной схемы штампа, составленной по специальной программе, проводится проверка рационального раскроя материала;
- при необходимости эскиз корректируется, и уточняются размеры штампа;
- обозначаются места расположения отверстий и их размеры, которые затем будут нанесены на поверхность штампа;
- после окончательного согласования чертежей приступают к изготовлению самого штампа.
- необходимость последующей обработки на металлообрабатывающих станках;
- большое количество отходов, уходящих в стружку;
- необходимость в широком перечне металлообрабатывающего оборудования.
- производить детали и изделия различных размеров и конфигураций с чистотой поверхности, позволяющей не прибегать к последующей обработке;
- осуществлять серийное производство продукции, одинаковой по геометрическим параметрам;
- обеспечивать высокую производительность процесса – большинство операций штамповки выполняется на линиях с высоким уровнем автоматизации.
- заготовку нагревают в печи и помещают в нижнюю часть инструмента;
- верхняя часть штампа опускается и сдавливает заготовку;
- металл заполняет объем штампа и приобретает необходимую форму.
- мощности применяемого оборудования недостаточно для осуществления холодной штамповки;
- материал обладает низкой пластичностью;
- толщина листа – более 3 мм.
- вырубку;
- пробивку;
- гибку;
- степень коробления.
- Вырубка. С помощью этой разделительной операции изготавливают плоские детали круглой или другой замкнутой формы, например шайбы. Отделение производится по линиям любой конфигурации.
- Пробивка. Служит для получения отверстий.
- Вытяжка. Это более сложная операция, называемая формообразующей. Применяется для превращения листа в пространственные формы.
- Отбортовка. Чаще всего востребована для формирования бортиков на концах труб.
- Обжим. Служит для сужения торцов полых элементов.
- Гибка. Обеспечивает требуемый изгиб.
- Формовка. При этой операции меняются форма и размеры отдельных участков детали.
- Хром – 16-18%, никель – 6-8%. Эти стали применяют при производстве высоконагруженных изделий. Для изготовления штампованной продукции не рекомендуются.
- Хром – 17-20%, никель – 8-11%. Материалы средней пластичности, могут использоваться для неглубокой вытяжки.
- Хром – 17-18%, никель – 10-12%. Для этой стали характерна высокая пластичность, поэтому она может применяться для глубокой вытяжки.
- Таблица температура плавления стали
- Шх15 сталь подшипниковая
- Классы прочности сталей
- Сталь углеродистая качественная
- Лента стальная упаковочная гост
- Наклеп и рекристаллизация
- Отпуск стали назначение и виды отпуска
- Крепление для стального троса
- Сталь ручные инструменты
- Сталь 3 как закалить
- Производство труб стальных
Штамповка - это процесс обработки металлов. Виды штамповки и оборудование. Холодная штамповка нержавеющей стали
Нержавеющая сталь: штамповка и вытяжка
Сделать заказ можно по телефону
Наши специалисты с радостью вам помогут
+7 495 775-50-79
Нержавеющая сталь различных марок используется для изготовления деталей, приборов, применяемых в промышленности, строительстве и других областях человеческой деятельности. Благодаря таким характеристикам как прочность, пластичность, упругость, она используется для производства: труб, уголков, шестигранников, кругов, лент, листов.
Для придания заготовкам из нержавеющей стали требующейся формы используются различные способы обработки:
Штамповка нержавеющей стали
Процесс обработки заготовок из нержавеющей стали при помощи штампования подразделяют на два вида:
Вытяжка нержавеющей стали
Кроме штамповки, лазерной резки, других способов обработки повышенным спросом пользуется у потребителей вытяжка нержавеющей стали, суть которой состоит в превращении плоской заготовки в деталь полостной формы. Различают два вида вытяжки.
www.globus-stal.ru
Холодная штамповка - Справочник химика 21
из "Технология изготовления химической аппаратуры из нержавеющей стали"
Вырезка. Вырезка деталей из листового проката, вырубка отверстий, обсечка заусенцев на горячештампованных деталях по сути являются аналогичными операциями. [c.52] мация элементарных слоев материала в зоне вырезки. происходит главным образом иод влиянием сжимающих и растягивающих напряжений. Пласт чсская деформация элементарных слоев вблизи поверхности среза создаёт зону наклёпанного металла, чем 1Собенно характерны хромоникелевые нержавеющие стали. [c.52] При вырезке деталей из сталей типа 18-8 необходимо сгредтться к сокращению зоны напряжений обрабатывае.мого материала. [c.52] Величина зоны пластической деформации зависит от состоя ния пластичности материала, величины зазора можд матрицей и пуансоном и от степени остроты режущих кромок пуансона и матрицы. [c.52] При штамповке деталей из листового проката аустенитных ие ржавеющих сталей, в силу прочности обрабатывае.мого материала, потребный расход мощности прессового оборудования превышает почти в два раза мощность, необходимую для выполнения той жг операииш из листового проката малоуглеродистых сталей. [c.52] При вычнсленш величины зазора между рабочими частями штампа рекомендуется пользоваться следующими данными для толщпны вырезаемого. материала до 1 мм зазор между матрицей и пуансоном должен быть равен 0,04 толщины обрабатываемого материала, а для толщин свыше 1 мм зазор должен быть 0,05 толщины материала (на сторону). [c.53] Миннмальный зазор для всех материалов рекомендуется принимать 7,5% от толщины материала на обе стороны, т. е, 0,075 5, где — толщина материала. 6]. [c.53] При пробивке отверстий в малоуглеродистых сталях рекомендуется, чтобы минимальный диаметр отверстия был не менее толщины пробиваемого материала. В случаях же пробивки отверстий в листовом материале из нержавеющих сталей, учитывая их механические свойства, применяют следующие размеры пуансонов. [c.53] Для круглых отверстий диаметр пуансона должен быть н -менее 1,1 для квадратных — сторона квадрата з и для прямоугольных— меньшая сторона прямоугольника 0,8 5, где 5 - - толщина пробиваемого материала в мм. [c.53] Загибка. Конструкции из нержавеющих сталей, аналогично конструкциям пз. малоуглеродистых сталей, требуют значительного количества деталей, выполняемых гибкой. [c.53] Особенностью гибочных операций при изготовлении деталей из нержавеющих сталей является определение величины радиуса закругления пуансона и матр1щы, величины зазора между рабочими частя.ми штампа и формы изгиба заготовки. От неправильно выбранных параметров инструмента иногда возникают трещины в изгибаемом материале в местах перегибов. Образование трещин объясняется наклёпом на кромках, возникающим в процессе резки материала, вследствие которого удлинение материала снижается. Вероятность образования трещин возрастает при гибке заготовки с заусенцами, расположенными наружу и при изгибе детали, волокна материала которой расположены вдоль линии изгиба. [c.53] Радиус загиба зависит от толщины материала, угла за1и6а детали, направления линии гиба относительно направления волокон (прокатки), наличия и располо/кения заусенцев и яаготонке к механических свойств изгибаемого материала. [c.54] Вытяй ка. Аустеннтные нержаве[ощие стали, обладая высокой степенью пластичности, являются хорошим материалом для деталей, получаемых штамповкой путём глубокой вытяжки. [c.54] Детали из нержавеющих аустенитных сталей, полученные в результате повторных вытяжек, после каждой своей операции должны быть подвергнуты тер.мической обработке для снятия наклёпа и напряжений, возникших в результате сдвига частиц материала. В противном случае на них могут самопроизвольно возникать трещины в течение одного часа после предыдущей операции, в особенности при условии образования на детали складки или прп низкой те 1ера уре , с и-и1 и. [c.55]Вернуться к основной статье
chem21.info
Штамповка деталей из листового металла: виды и оборудование
Штамповка деталей из листового металла сегодня является очень распространенной технологией, по которой производят изделия практически для всех отраслей промышленности. Благодаря применению такой технологии из плоского металлического листа можно получать как миниатюрные, так и габаритные детали даже сложной геометрической формы.
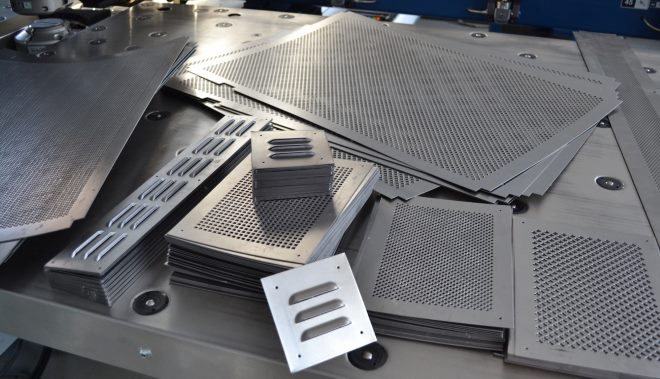
Листовые заготовки, изготовленные на координатно-револьверном прессе
Что собой представляет листовая штамповка
Говоря о штамповке деталей, изготовленных из листового металла, имеют в виду технологическую операцию, при выполнении которой на заготовку оказывается значительное давление. Под воздействием такого давления заготовка деформируется, приобретает требуемую конфигурацию и размеры.
Использовать такую операцию (правда, в значительно упрощенном виде) начали еще наши далекие предки. Именно при помощи воздействия на металл давлением они изготавливали сельскохозяйственные орудия, оружие, предметы домашнего обихода и различные украшения.
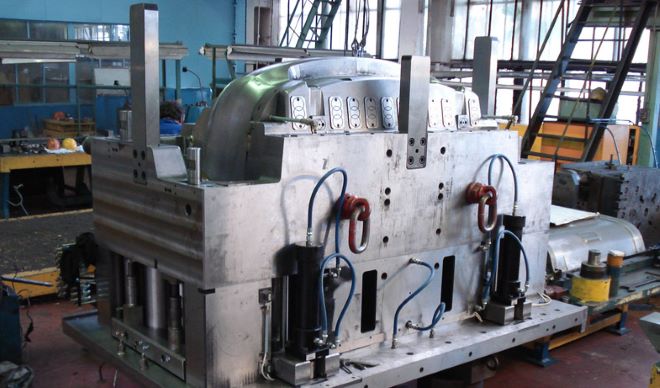
Современный пресс для штамповки кузовных деталей
Активное развитие штамповка как технология производства изделий из листового металла получила в конце XIX века. Именно в тот период (начиная с 1850-х годов) данная технология активно совершенствовалась, а для ее реализации специалисты создали мощное оборудование. Штампованные детали, которые в то время можно было уже производить серийно, отличались достойным качеством и обладали хорошими эксплуатационными характеристиками.
На совершенно новый уровень развития как горячая, так и холодная штамповка вышла уже в начале XX века. Именно благодаря совершенствованию технологии штамповки листового металла стал возможен серийный выпуск автомобилей, для которых с помощью данного метода производились кузовные детали. Начиная с 1930-х годов данную технологию начали активно применять предприятия, работающие в авиа- и судостроительной отрасли, а чуть позже (спустя всего пару десятков лет) при помощи штамповки стали производить детали космических аппаратов.
Высокая популярность, которую штамповка завоевала за относительно долгий период своего развития, объясняется возможностями:

Холодная штамповка на гидравлическом прессе
Использование такой технологической операции, как объемная штамповка, позволяет превратить металлический лист в геометрически сложное и небольшое по массе изделие, прочностные характеристики которого находятся на высоком уровне. Применение методов штамповки деталей из листового металла позволяет изготавливать как очень массивные изделия, используемые при производстве машиностроительной продукции, водных и воздушных судов, так и миниатюрные детали для электронных устройств и часовых механизмов.
Особенности технологии
В качестве исходного сырья для штамповки может выступать металлический лист, стальная полоса или тонкая лента. Наибольшее распространение по целому ряду причин получила холодная листовая штамповка. Технологию горячей штамповки применяют в тех случаях, когда мощности используемого оборудования не хватает для деформирования металла в холодном состоянии или когда обработке необходимо подвергнуть деталь из металла, отличающегося невысокой пластичностью. Как правило, по технологии горячей штамповки выполняют обработку листовых заготовок, толщина которых не превышает 5 мм.
В зависимости от того, что в процессе выполнения штамповки необходимо сделать с листовым металлом, различают разделительные и формоизменяющие технологические операции. В результате выполнения первых от заготовки отделяется часть металла, что может происходить по прямым или кривым линиям, а также по определенному контуру. Отделение металла в таких случаях происходит из-за сдвига его частей относительно друг друга.
Существует целый ряд разделительных штамповочных операций, для выполнения которых используется пресс, оснащенный специальным инструментом. РезкаВ процессе резки части металлической детали отделяются друг от друга по прямой или фигурной линии. Пресс, при помощи которого выполняется такая операция, правильнее называть ножницами, которые могут быть дисковыми, вибрационными или гильотинными. При помощи резки получают готовые к дальнейшей эксплуатации изделия или формируют заготовки для их дальнейшей обработки другими методами.
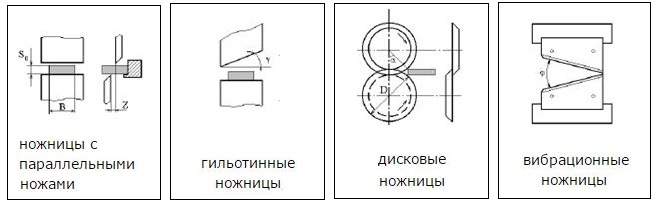
Схемы резки листового металла ножницами
ПробивкаЭта операция используется для того, чтобы сформировать в листовой заготовке отверстия различной конфигурации.
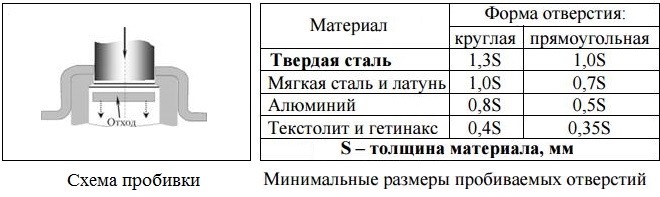
В процессе пробивки часть материала удаляется в отход
ВырубкаПри помощи вырубки из металлической детали формируют готовое изделие с замкнутым контуром.
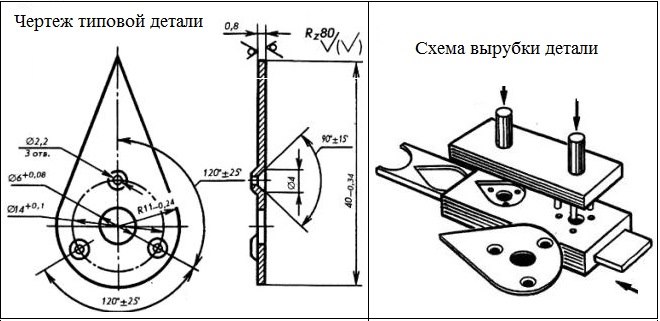
Пример детали, изготовляемой из полосы вырубкой
Формоизменяющие штамповочные операции в полном соответствии со своим названием используются для того, чтобы без механического разрушения изменить форму листовой металлической заготовки, а также ее размеры. ОтбортовкаЭто технологическая операция штамповки листового металла, в результате выполнения которой вокруг отверстий в металлической заготовке, а также по ее контуру формируются бортики требуемых размеров и формы. Чаще всего отбортовке подвергают концы труб, на которых впоследствии планируется фиксировать фланцы.
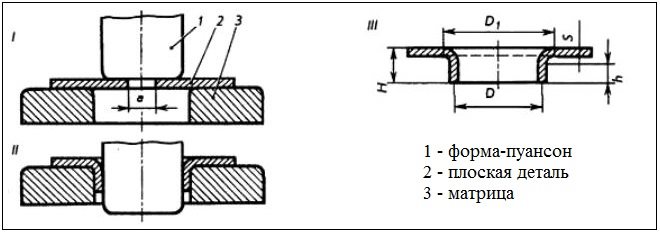
Схема отбортовки детали вокруг заранее пробитого отверстия
ВытяжкаЭто по-настоящему объемная штамповка, целью которой является получение из плоского металлического листа полых пространственных изделий. При помощи такой технологической операции можно изготавливать предметы коробчатой, полусферической, цилиндрической, конической и других форм.
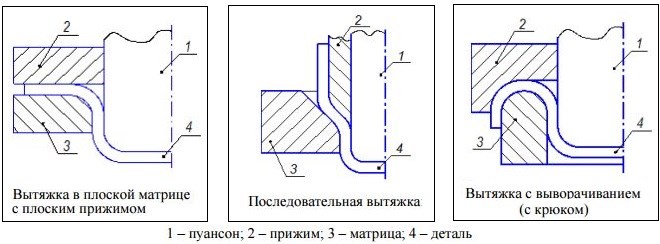
Инструментальные способы вытяжки
ОбжимДанная операция выполняется при помощи матрицы конического типа. Целью обжима является сужение торцов полых деталей, изготовленных из листового металла.
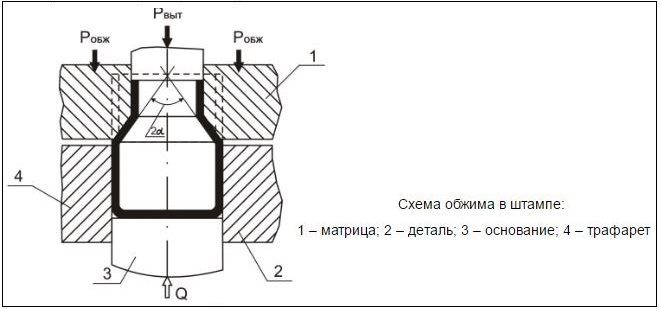
При обжиме конец заготовки вталкивается в воронкообразное отверстие матрицы
ГибкаПри помощи такой технологической операции штамповки заготовкам из листового металла придают требуемый изгиб.
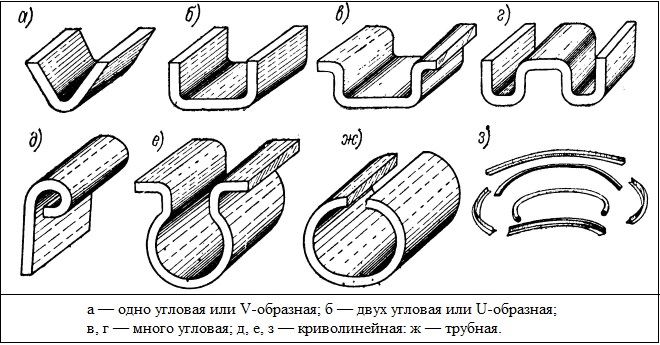
Гибка позволяет получать детали разнообразных форм, в зависимости от которых различают типы гибки
ФормовкаЭто такое изменение формы и размеров локальных участков заготовки, при котором внешний контур изделия остается неизменным.
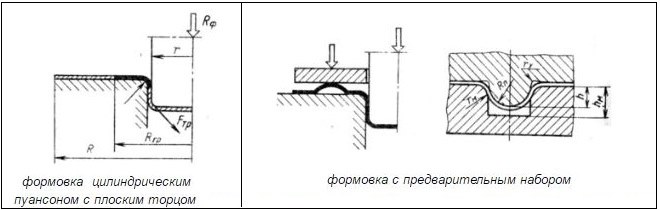
Схемы формовки
Обработке по технологии холодной штамповки могут подвергаться не только листы из углеродистых и легированных сталей, но также детали из меди, алюминия и их сплавов. Более того, используя пресс и соответствующие штампы листовой штамповки, можно выполнять обработку таких материалов, как кожа, картон, резина, полимерные сплавы.
Детали, для производства которых была использована холодная штамповка, отличаются не только точностью своих геометрических параметров, но и высоким качеством поверхности. Чистота последней в отдельных случаях может соответствовать 8-му классу. В среднем чистота поверхности штампованных изделий находится в интервале 2–6 классов, что вполне устраивает потребителей такой продукции.
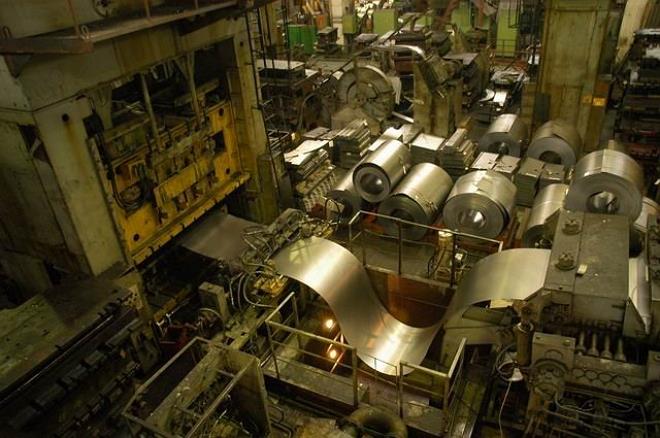
Производственный цех, в котором ведется процесс листовой штамповки
Следует иметь в виду, что выполнение холодной штамповки листового металла сопровождается увеличением его прочностных показателей.Выбирая пресс для выполнения такой технологической операции, а также занимаясь проектированием штампов листовой штамповки, следует учитывать целый ряд параметров исходного сырья. Только так можно обеспечить высокое качество готовых изделий. К таким параметрам, в частности, относятся:
Оборудование, инструменты и приспособления
Для штамповки деталей, изготовленных из листового металла, необходимы пресс и сам рабочий орган такого оборудования – штамп. В свою очередь рабочими органами штампа, элементы конструкции которого изготавливаются из инструментальных сталей, являются матрица и пуансон. Деформирование обрабатываемого листа как раз и осуществляется матрицей и пуансоном, а происходит это в тот момент, когда они сближаются друг с другом.
В процессе обработки двигается только верхняя часть штампа, которая фиксируется на ползуне пресса. Нижняя часть рабочего инструмента, являющаяся неподвижной, устанавливается на рабочем столе оборудования. В отдельных случаях, когда штамповке подвергают не листовую сталь, а более мягкий материал, рабочие элементы штампа могут изготавливаться из древесины или полимерных сплавов.
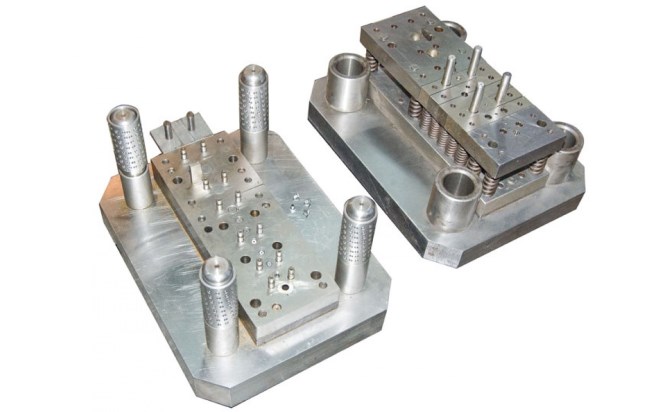
Штамповая оснастка для вырубки
Когда методом штамповки необходимо изготовить крупногабаритную единичную деталь, нередко используют не пресс, а несложное приспособление, состоящее из бетонной или чугунной матрицы и контейнера, наполненного жидкостью, в качестве которой выступает вода. Обрабатываемый металлический лист укладывают на матрицу, а жидкий пуансон располагают над ним.
Чтобы создать в жидкости давление, которое деформирует лист металла по форме матрицы, в ней подрывают пороховой заряд или создают электрический разряд требуемой мощности. Для выполнения такой технологической операции, как резка, используют не пресс, как уже говорилось выше, а ножницы, отдавая предпочтение моделям вибрационного типа.
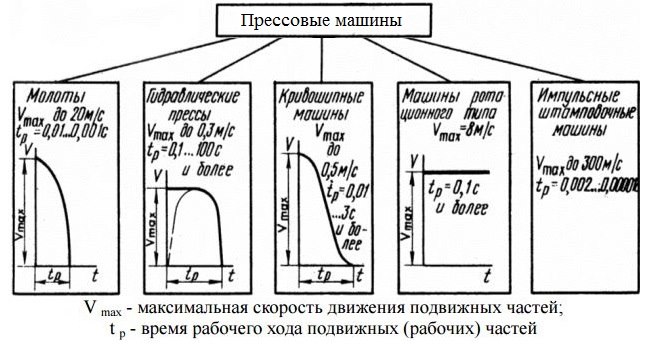
Классификация прессовых машин по кинематической схеме
Собираясь выполнить штамповку изделия из листового металла, следует уделить особое внимание выбору пресса. Чаще всего в качестве такого оборудования выбирают устройства кривошипного типа, которые могут быть оснащены одним, двумя или четырьмя кривошипными механизмами. Принцип работы этого устройства достаточно прост и заключается в следующем.
Штамповочное оборудование, которое применяется для изготовления изделий сложной конфигурации, может быть оснащено не одним, а несколькими ползунами.
Оценка статьи:

Поделиться с друзьями:
met-all.org
Штамповка деталей из листового металла: технология, прессы
Изготовление деталей с помощью штамповки занимает ведущее место в технологии обработки металлов давлением и используется в разных отраслях промышленности.
Особое значение имеет штамповка металлических изделий из листового проката. В ее основе лежит пластическое деформирование металла без его нагрева с помощью специальных штампов. Такой способ пластической деформации деталей широко применяется для изготовления деталей разных размеров и сложных форм с большой точностью, что невозможно осуществить с помощью других способов обработки.
Они используются для сборки крупногабаритных изделий машиностроительной отрасли, в автомобилестроении и судостроении, а также в приборостроительной сфере и быту, где часто требуются различные миниатюрные детали.
Технология штамповки деталей из металлических листов и ее виды
Штамповкой называют процесс придания деталям нужной формы и получение определенного документами размера путем механического воздействия на них с помощью давления. Основное направление штамповки – это производство деталей из заготовок, в качестве которых используется листовой прокат. Под действием сдавливающего усилия заготовка подвергается деформации и приобретает нужную конфигурацию.
Различают штамповку, выполненную горячим способом с нагревом заготовки и холодным способом без ее предварительного нагрева. Штамповка деталей из листового металла осуществляется без их предварительного нагрева.
Деформацию давлением с нагревом заготовки используют при изготовлении деталей из металла, не обладающего достаточной пластичностью, и в основном применяют при производстве небольших партий объемных изделий из металлического листа, имеющего толщину в пределах 5 миллиметров.
Технологический процесс горячей штамповки металла во многом совпадает с последовательностью операций холодной обработки заготовок. Отличие состоит в предварительном нагреве исходных заготовок в печах до температуры, обеспечивающей пластичность металла. При этом учитывается степень коробления детали при остывании, а также ее утяжка при деформационной обработке, влияющая на ее размер. Чтобы исключить отклонения от требуемых размеров для деталей, полученных горячей штамповкой, делают большие допуски.
Видео:
При производстве штампованных деталей из листового металла в основном используют метод холодной штамповки.
Холодная штамповка листового металла
Технология холодной деформации листового проката с помощью штампов подразумевает изменение формы и размеров изделия с сохранением их первоначальной толщины.
В качестве материала для получения штампованных изделий холодным способом используют полосы, листы или тонкую ленту в основном из низкоуглеродистых и легированных пластичных сталей, а также медных, латунных (содержащих свыше 60% меди), алюминиевых, магниевых, титановых и других пластичных сплавов. Применение для штамповки сплавов, обладающих хорошей пластичностью, связано с тем, что они легко поддаются деформационному изменению.
Для осуществления холодной штамповки листового металла используют различные операции, которые зависят от поставленной задачи достижения определенной формы заготовки. Их подразделяют на разделительные и формоизменяющие воздействия.
1. При разделительных деформациях материал заготовки частично отделяют по заданному контуру. Отделение осуществляется путем сдвига части металла по отношению к основной заготовке. Такими операциями являются резка, вырубка, пробивка и другие.
Рассмотрим, как осуществляются некоторые операции разделительного характера.
Резка
При проведении резки от детали отделяется определенная часть путем ее разрезания по фигурной или прямой линии. Такая разделительная операция выполняется с помощью пресса, выполненного в виде ножниц разной конструкции.
Такая операция предназначена в основном для подготовки заготовки к другим способам обработки.
Пробивка
Операцию, называемой пробивкой, используют для создания в заготовке отверстия разной формы. Часть металла при пробивке из заготовки удаляется совсем, и ее вес уменьшается.
На рисунке показана схема процесса пробивки.
Вырубка
С помощью процесса вырубки металлической детали придают готовый вид изделия, имеющего замкнутый контур.
На рисунке показана схема изготовления детали с помощью вырубки.
2. Формообразующие деформации включают изменение формы и размеров изделия при перемещении его отдельных областей, не приводящем к его общему разрушению. К ним относят вытяжку, гибку, рельефную формовку, скручивание, обжим и другие операции.
Рассмотрим некоторые виды операций, не приводящие к физическому разрушению формы.
Вытяжка
С помощью вытяжки из листовых плоских заготовок получают полые объемные изделия. Например, таким способом изготавливают детали, имеющие форму полусферы, цилиндра, конуса, куба и других видов. На рисунке показаны разные варианты выполнения вытяжки.
Гибка
С помощью операции гибки листовому изделию придается заданная форма его изгиба. В зависимости от вида гибки такая операция дает возможность получать изогнутые изделия разной конфигурации. Некоторые из них показаны на рисунке.
Рельефная формовка
Этот вид операции подразумевает видоизменение локальных частей изделия, его внешняя конфигурация остается без изменения. На рисунке изображена схемы некоторых операций формовки:
Возможно также применение комбинированных операций, включающих разделение и формообразование одной детали.
Технологический процесс проведения холодной штамповки состоит из этапов, которые связаны с характером деформационной операции и зависят от вида используемого штампового оборудования.
Разработка техпроцесса проводится в следующей последовательности:
В техпроцесс могут быть внесены дополнительные операции, с помощью которых заготовка приводится к виду, удобному для обработки. К ним относятся очистка, правка листов, нанесение смазки и другие операции.
Видео:
Штамповочный пресс для металла
Все операции холодной штамповки можно осуществлять при наличии специального оборудования, главным из которых является штамповочный пресс. Его устройство может быть на основе механики, либо с использованием гидравлики.
К механическим видам относят:
Для осуществления операций пробивки, вырубки и вытяжка используется штамповочный пресс кривошипного типа.
Устройство и принцип работы пресса кривошипного типа
Любой пресс, предназначенный для штамповки изделий, включает основные узлы, к которым относится: механизм, приводящий его в действие и устройство, осуществляющее непосредственную штамповку.
Действующий механизм – это кривошипный вал, который приводится в движение с помощью электропривода. Для этого электродвигатель при вращении маховика передает вращение кривошипному механизму с помощью зубчатой передачи.
Совершая возвратно-поступательные действия, ползун кривошипа приводит в работу штамповое устройство, которое с усилием давления осуществляет пластическую деформацию.
Основные детали такого пресса выполнены из высокопрочных сталей и дополнительно укреплены с целью придания необходимой жесткости.
Видео:
Устройство гидравлического пресса
Штамповочный пресс для металла гидравлического типа применяется для создания объемных форм с помощью продавливания металла.
Принцип действия такого механизма основан на давлении жидкости, помещенной в двух резервуарах, которые снабжены поршнями. Резервуары соединены трубопроводом. В результате давления в жидкости, возникающего в момент ее нагнетания в цилиндр из другого резервуара, оно передается на ползун и приводит его в движение. При перемещении ползун с большим усилием продавливает заготовку.
Видео:
Изготовление штампов для холодной штамповки металла
Рабочим устройством любого прессового станка является сам штамп. Он включает две рабочие части, называемые матрицей и пуансоном. В процессе работы подвижной является только верхняя деталь штампа – пуансон, закрепленный на ползуне. Матрица расположена снизу и остается неподвижной.
Деформирование листа осуществляется во время прижимания пуансона к матрице с расположенной на ней заготовкой.
Разработке чертежей и изготовлению штампов для пресса предъявляются повышенные требования, т. к. от их точности зависит правильность формирования изделия.
Выполняются такие работы поэтапно в следующей последовательности:
Видео:
Современные станки для штамповки изделий оснащены штампами, изготовленными с большой точностью при помощи компьютерных технологических программ.

plavitmetall.ru
Штамповка листовой стали: применяемые марки, технологии, получаемая продукция
Штамповка деталей из листовой стали – распространенная технология, применяемая при производстве изделий практически для всех областей народного хозяйства. Заключается в обработке заготовок высоким давлением, под воздействием которого они деформируются и приобретают требуемую конфигурацию и размеры, плоскую или объемную форму. Получаемые детали могут быть самыми разными: от миниатюрных для часовых механизмов и электронных устройств до крупногабаритных, применяемых в машиностроении. По форме: от простых до самых сложных. Исходная заготовка – лист, очень тонкая лента, полоса. Процесс может быть холодным или горячим.
Штамповка как разновидность ковки
Выделяют свободную ковку и штамповку, которые различаются по технологии и качеству результата.
Свободная ковка
Может применяться для заготовок любой массы и объема. Производится на молотах или прессах. Заготовки укладывают на основание без закрепления, обрабатывают ударами паровоздушного или пневматического молота. После обжима с одной стороны полуфабрикат поворачивают и продолжают обработку до полной готовности поковки. Процесс на прессах проходит приблизительно так же. Недостатком свободной ковки является невозможность получения точных размеров, следствием чего являются:
Штамповка
Основное отличие от свободной ковки – ограничение растекания металла заготовки штампом, состоящим из двух частей: нижняя неподвижно закреплена на наковальне, а верхняя свободно перемещается вверх и вниз. Получаемые изделия – штамповки – гораздо ближе по размерам к желаемому результату, по сравнению с кованой продукцией.Объемная штамповка позволяет получать из листа небольшое по массе, геометрически сложное изделие.
Благодаря этой технологии, возможно:
Внимание! Полностью отказаться от свободной ковки в пользу штамповки невозможно, потому что изготовление штампа – дорогой и сложный процесс, оправдывающий себя при массовом производстве.
По температуре, при которой осуществляется операция, различают горячую и холодную штамповку.
Особенности горячей штамповки
Суть процесса:
Определение! Штампы бывают открытыми и закрытыми. В первом случае заготовки имеют заусенцы, во втором – нет.
Горячая технология применяется в случаях, если:
Применяется для изготовления полушарий, буев, днищ котлов, корпусов других изделий, используемых в судостроении. При конструировании деталей, подвергаемых горячей штамповке, учитывают припуски на:
Холодная штамповка
Этот процесс отличается от горячего тем, что нагрев заготовки не осуществляется. Применяется для тонколистовых стальных заготовок, а также произведенных из мягких металлов и сплавов, полимеров. Используется при производстве: изделий для автотракторной индустрии, шайб различных типов, любых других нагружаемых высокоточных изделий. Для технологии характерны: высокая производительность, точность размеров и качественная поверхность продукции, чистота которой в отдельных случаях соответствует 8-му классу.
Основные операции, выполняемые с помощью технологии холодной штамповки:
Штампуемые стали
Для холодной штамповки востребованы низкоуглеродистые стали, содержание Cв которых не превышает 0,2%, марганца – 0,4%, количество азота, кислорода и водорода минимально. Наиболее популярная марка – 08 кп/сп/пс. Также применяются «черные» углеродистые стали – 05 кп, 10, 15, 20, Ст 1, Ст 3.
Для изготовления высокопрочных изделий применяют низколегированные стали – 03ХГЮ, 06ХГСЮ, 12ХМ, 06Г2СЮ. В качестве легирующих элементов они содержат марганец, кремний, хром, небольшие добавки алюминия и вольфрама.
Нержавеющие стали по процентному соотношению хрома и никеля делят на следующие группы:
При добавлении титана и ниобия снижается пластичность, для компенсации этого явления повышают содержание никеля.
Оборудование для штамповки
Для осуществления горячей и холодной штамповки листа применяется пресс, рабочим органом которого является штамп. Его элементы – пуансон и матрица – изготавливаются из инструментальной стали. При обработке мягких материалов эти элементы могут изготавливаться из древесины или полимеров.
Для холодной штамповки используются в основном гидравлические прессы, имеющие различную мощность и функциональные возможности. Для вырубки и пробивки востребованы прессы простого действия, для вытяжки – двойного действия. По конструкции прессы делятся на одно-, двух- и четырехкривошипные. На оборудование последних двух видов устанавливают ползуны больших размеров.Для нагрева стали перед горячей штамповкой применяют нагревательные устройства: электрические, плазменные и другие.
www.navigator-beton.ru
Стали для холодной штамповки — МегаЛекции
Холодная штамповка является одним из основных видов ОМД.
К ним относятся вытяжка, формовка, обтяжка, гибка и др. Наиболее часто применяемой операцией холодной штамповки является вытяжка.
Вытяжка — холодная пластическая деформация, при которой из листовой заготовки получается объемная деталь сложной формы.
Основными требованиями к сталям, предназначенным для холодной штамповки, являются:
- хорошая штампуемость, т.е. способность пластически деформироваться в холодном состоянии.
- высокое качество поверхности после деформации.
Эти требования обеспечиваются механическими свойствами и структурой стали.
Требования по механическим свойствам включают в себя минимальную твердость (обычно не более 45HRВ) и максимальную пластичность. Способность к пластической деформации оценивается относительным удлинением и отношением предела текучести к пределу прочности. Этот показатель называют числом текучести. Хорошая штампуемость наблюдается в сталях с числом текучести σт/σв = 0,5-0,6и δ = 33 – 45%.
Требования к структуре включают в себя:
1.Среднее зерно феррита.
2.Мелкие выделения зернистого перлита.
3.Отсутствие карбидной сетки цементита третичного по границам зерен.
4.Отсутствие полосчатости структуры.
5.Отсутствие текстуры.
6.Отсутствие разнозернистости.
Сталь должна иметь среднее зерно (средний бал зерна 6-8 мм). Мелкое зерно не желательно, т.к. вызывает повышенную жесткость листа и, следовательно, быстрый износ штампов. Крупное зерно не желательно, т.к. ухудшает качество поверхности после штамповки. На поверхности появляются шероховатость, которую называют апельсиновой коркой. Особенно нежелательно иметь в сталях для холодной штамповки разнозернистость. При деформации такой стали в первую очередь растягиваются крупные зерна, как более пластичные, и в этих местах затем появляются мелкие трещины и надрывы, что является непоправимым браком.
Цементит в сталях для холодной штамповки должен иметь округлую форму, т.е. быть сферическим. Это обеспечивает наилучшую штампуемость. Недопустимо в таких сталях образование цементитной сетки по границам зерен, т.к. это приводит к резкому снижению пластичности. Нежелателен также мелкий сорбитообразный перлит, т.к. это резко повышает жесткость и упругость листа.
Полосчатость структуры и текстура прокатки также нежелательна т.к. вызывают неоднородность деформации по разным направлениям и на штамповках появляются фестоны (рис. 13).
А б
Рис.13. Различие свойств по разным направлениям (а) в листе
и фестоны после штамповки (б)
Наиболее часто для холодной штамповки применяют углеродистые стали с содержанием углерода 0,05 — 0,2%, Mn ≤ 0,4% и минимальным содержанием газов N, O2, h3. Например, 05кп, 08кп, 08пс, 08сп, 10, 15, 20, Ст. 1 — Ст. 3.
Основной маркой стали для холодной штамповки является сталь 08кп. Она отличается наилучшей пластичностью и минимальной стоимостью. Однако недостатком этой стали является повышенная газонасыщенность. Повышенное содержание газов вызывает склонность этой стали к деформационному старению.
Деформационное старение это повышение предела текучести стали вызванное накапливанием атомов N2 и О2 вокруг дислокаций. Создание таких атмосфер атомов называют атмосферами котрелла.
Рис. 14. Диаграммы растяжения для стали склонной к деформационному
старению (а) и нестареющей (б).
Они блокируют перемещение дислокации и требуют большего усилия для начала пластической деформации. После отрыва дислокаций напряженность сдвига понижается и пластическая деформация облегчается. В результате на кривой растяжения появляется пик на площадке текучести (рис.14).
Отрыв дислокаций от атмосфер примесных атомов проходит неравномерно. В результате объем металла начинает деформироваться по плоскостям наиболее благоприятно ориентированным по отношению к действующей нагрузке. Такая преимущественная деформация проявляется в виде появления линий скольжения на поверхности металла. Сетка таких линий выглядит как царапины и снижает качество поверхности, что является дефектом для деталей после холодной штамповки. Для устранения этого дефекта применяется предварительная деформация металла в прокатных валках с обжатием 2%. Она называется дрессировка. Малая пластическая деформация вызывает отрыв дислокаций от атмосфер примесных атомов и последующая штамповка уже не вызывает появлений скольжения. Однако эффект от дрессировки сохраняется от 10 до 12 дней.
Таблица 3
Основные марки стали, применяемые для холодной штамповки
Предел прочности МПА | Относительное удлинение, % | ||
Марка | Примечание | ||
Ст.2-Ст3 08кп 08пс, 10кп 15кп 15, 20кп | 340-420 280-390 280-420 300-440 320-460 340-480 350-510 400-550 | 26 - 31 30—34 28—32 28—30 27—29 25—27 24—26 23—24 | Группы вытяжки Н, Г, ВГ |
08кп 08Фкп 08Ю | 260—330 260—340 | 42 - 44 | СВ, ОСВ СВСВ |
Устранить склонность стали к деформационному старению можно введением в нее алюминия или ванадия в процессе получения. Малые добавки этих элементов в количестве 0,02 — 0,05% связывают атомы азота в нитриды. В результате диффузия атомов азота блокируется. Такая сталь называется нестареющей, например 08Ю, 08Ф, 08ЮА, 08ГСЮТ, 08ГСЮФ.
Для обеспечения высокой пластичности стали для холодной штамповки, основным видом термообработки для нее является отжиг на рекристаллизацию. Стальной лист после холодной прокатки обладает повышенной прочностью, в результате наклепа и для его устранения применяют отжиг при температуре 660 — 680ºС. Отжиг применяют для стали в рулонах либо для пачек нарезанных листов. Продолжительность такого отжига определяется массой рулона и составляет 10-20 час. Для того чтобы получить после такого отжига среднее зерно необходимо, чтобы предшествующая деформация составляла 30-40%. При малой деформации возможно появление крупно зернистости. А при большой степени деформации возможно образование текстуры.
Для штамповки изделий, требующих повышенной прочности, применяют низколегированные «двухфазные стали» со структурой, ‘состоящей из высоко-пластичной ферритной матрицы и упрочняющей фазы мартенсита или бейнита в количестве 20—30 %. Такие стали называют двухфазными ферритно-мартенситными (ДФМС). Для получения такой структуры в сталь добавляют легирующие элементы и проводят перед штамповкой предварительную, упрочняющую термообработку. В качестве основных легирующих элементов вводят Mn – 1,4-2%,Si от 0,5 до 1,5%, Cr – до 08 - 1%, Mo - до 0,2-0,4%, а так же небольшие добавки Al и W. Количество углерода в этих сталях 0,03-0,06%.
Типовые марки сталей:
03ХГЮ
06ХГСЮ
12ХМ
06Г2СЮ
Для создания необходимой структуры стали при её производстве проводят ускоренное охлаждение после горячей прокатки, либо дополнительно нагревают и охлаждают сталь с температурой превышающей точку А1, но ниже точки А3.. По своей сути такая термообработка называется неполной закалкой. В результате структура такой стали состоит из 70% феррита и 30% мартенсита. Феррит обеспечивает высокую пластичность, хорошую штампуемость, а мартенсит повышенную прочность. В процессе штамповки деформация сосредотачивается в зернах феррита, и повышенная степень наклепа увеличивает прочность готового изделия. После штамповки предел прочности такой стали в 1,3÷1,5раза превышает предел прочности обычных углеродистых сталей. Дополнительный отпуск не требуется.
Читайте также:
B) Просмотрите текст вновь и скажите, верны ли данные утверждения. Измените предложения, содержащие неправильную информацию так, чтобы они тоже стали верными.B) Просмотрите текст вновь и скажите, верны ли данные утверждения. Измените предложения, содержащие неправильную информацию так, чтобы они тоже стали верными.II Раздаточный материал из сборника задач по технологии горячей и холодной прокатки стали и сплавов. Протасов А.А. Изд-во «Металлургия» М.1972, 320 с.Атмосферно коррозионностойкие сталиБлоковая политика в период «Холодной войны»БОЕВЫЕ ДЕЙСТВИЯ НА ВНУТРЕННЕМ СТАЛИНГРАДСКОМ ОБВОДЕ И НАЧАЛО БОЕВ В ЧЕРТЕ ГОРОДА (1-26.09.1942)БОИ НА СЕВЕРНЫХ ОКРАИНАХ СТАЛИНГРАДА (27.09-08.10.1942)В XX веке свой вклад в марксизм или «марксизм-ленинизм» внесли Ленин, Сталин, Мао Цзэдун и многие другие.В блиндаже командования 62-й армией. Слева направо генералы: Крылов Н.И., Чуйков В.И., Гуров К.А., Родимцев А.И., Сталинград 1942 г.Ведомость определения степени коррозионной агрессивности грунтов к бетону, алюминиевой и свинцовой оболочке кабеля, углеродистой стали
megalektsii.ru
это процесс обработки металлов. Виды штамповки и оборудование
Технологический процесс, при котором происходит обработка заготовок, позволяющий получить плоские или объёмные готовые изделия различных форм и размеров, - это штамповка. Рабочим инструментом для такой цели является штамп, который закреплён на прессе или другом оборудовании. Штамповка - это два вида технологии, которые в зависимости от условий выполняются горячим или холодным способом, а потому и оборудование, и технологические нормы отличаются друг от друга.
Категории
Помимо разделения технологии на холодный и горячий способы, штамповка - это целый ряд категорий, на которые подразделяются методы обработки материала. Зависит выбранный способ чаще всего от назначения изделия, но и технологические условия тоже на него влияют. Например, есть способ, при котором отделяется часть заготовки, и это штамповка разделительная. Сюда же входят пробивка, рубка, резка деталей. Есть категория операций, когда применяется горячая штамповка, посредством которой лист металла меняет форму. Их ещё называют формовкой. В результате детали подвергаются гибке, вытяжке и другим процедурам.
Холодная и горячая штамповка реализуются с использованием одного и того же принципа, который предполагает деформирование материала, но в остальном изготовление продукции этими методами имеет много отличий. Предварительный нагрев деталей до определённых (и достаточно высоких) температур предполагается в основном на крупных промышленных предприятиях, каким является, например, металлообрабатывающий завод. Это связано со сложностью такого технологического процесса, большим количеством операций, качественно выполнить которые можно только с точным предварительным расчётом и соблюдением высокой точности степени нагрева заготовки.
Горячий способ
Штампованные детали, обработанные по горячей технологии, должны обладать отменным качеством, поскольку, например, из листового металла разной толщины изготавливают такие ответственные вещи, как днища котлов и другие полусферические изделия, в том числе и ответственные элементы в судостроении. Для нагрева металлической детали используют оборудование, обеспечивающее правильный температурный режим.
Эти устройства и печи могут быть плазменными, электрическими или другими, их достаточно много видов. Перед подачей горячей детали на штамповочный пресс нужно не только норму нагрева рассчитать, но и разработать подробный чертёж уже готового изделия, где обязательно учесть усадку металла после остывания.
Холодная штамповка
Выполнение штамповки холодным способом подразумевает формирование изделия посредством давления, которое оказывают на заготовку рабочие элементы пресса. Усадке такие изделия не подвержены, потому что предварительно их не нагревают. Дальнейшая механическая доработка таким изделиям тоже не нужна после того, как окончена штамповка. Способы штамповки могут быть разными, холодный же является и более удобным, и экономически выгодным.
Материалы, хорошо поддающиеся холодной штамповке, относятся не только к углеродистым или легированным сталям. Штамповочное производство успешно работает и на алюминиевых, и на медных сплавах. Холодный способ выполняется преимущественно с помощью гидравлических прессов, и производство их регулируется ГОСТом. Серийные модели весьма разнообразны, а потому появляется возможность подобрать подходящий станок для производства любых конфигураций и размеров изделий. Штампы для штамповки металлов по своему оснащению очень сильно отличаются от тех, которые работают с такими материалами, как кожа, резина, картон, полимерные сплавы и тому подобное.
Разделительное штампование
Одной из самых распространённых технологическх операций является разделительное штампование, которое отделяет от заготовки часть металла. Этот способ используется почти на всех производственных предприятиях. На штамповочный пресс устанавливают специальные инструменты, которые производят резку, вырубку и пробивку материала. Благодаря этому процессу можно разделять металлические детали хоть по кривой, хоть по прямой линии реза. Резку выполняют самые разные устройства: гильотинные ножницы, вибрационные и дисковые станки и тому подобное. Используется резка для того, чтобы для дальнейшей обработки раскроить заготовки.
Вырубка - другая технологическая операция. Например, нержавеющий лист из металла нужно превратить в детали с замкнутыми контурами. Листовой металл при помощи пробивки снабжают отверстиями любой конфигурации. Нужно сказать, что и этот технологический процесс требует тщательной предварительной подготовки и подробного плана, с расчётом геометрических параметров инструмента, который используется. Иначе качественное изделие может и не получиться. Технологических операций, касающихся штамповки, очень много, потому что требуется изменить начальную конфигурацию деталей. Это гибка, формовка, отбортовка, вытяжка и обжим.
Технологические операции
Наиболее распространённая операция, изменяющая форму детали, это гибка, которая формирует на поверхности заготовки из металла запланированные участки с изгибом. Вытяжкой называется объёмная штамповка. Это операция, с помощью которой получается объёмное изделие из такой плоской металлической поверхности, как, например, металлический нержавеющий лист. Именно с помощью вытяжки он превращается в цилиндр, конус, полусферу или принимает коробчатую конфигурацию. Изделия из листового металла должны иметь бортик по краю и вокруг отверстий, если они внутри заготовки выполнены. Например, отбортовка должна завершать конец трубы, чтобы установить на неё фланец. Такая операция требует наличия специального инструмента.
При помощи обжима происходит обратное действие. Отбортовка расширяет концы заготовок из листового металла, а обжим сужает. Те же концы труб или край полости требуют такой операции, которая осуществляется посредством конической матрицы наружно. Формовка тоже относится к основным операциям, относящимся к штамповке. Она помогает изменить форму отдельным элементам штампованной детали, а наружный контур оставляет неизменным. Объёмная штамповка требует работы специального оборудования и сложных предварительных чертежей, а потому в домашних условиях практически никогда не реализуется.
Выбор пресса
Для обработки металлов, даже самых мягких (например, для штамповки алюминия), требуется специальное оборудование: гидравлический или кривошипный пресс или гильотинные ножницы. И конечно же, необходимы многие знания. Например, как произвести расчёты по расходу материала и выполнить технические чертежи. Требования ГОСТа при этом обязательно учитываются.
Чтобы выбрать нужный пресс для штамповки, сначала нужно чётко представить себе задачу, которую ему предстоит решать. Выполнение таких операций, как пробивка или вырубка, требует использования штамповочного оборудования простого действия, с небольшим ходом ползуна и шайб в процессе обработки. Но уже для вытяжки необходимо совсем другое, более мощное оборудование, где ползун и шайбы совершают значительно более широкий ход. Такая способность есть у оборудования двойного действия.
Оборудование по ГОСТу
Выполнение штамповки в зависимости от условий задачи может быть совершено на оборудовании следующих типов: одно-, двух- и четырёхкривошипном. Последнее - с установкой ползунов крупных размеров. Однако оснащение штамповочного пресса матрицей не зависит от конструктивного исполнения. Основную работу посредством движения выполняет ползун, соединённый нижней своей частью с подвижным штампом. А чтобы ползун пресса двигался, приводной электродвигатель снабжён элементами кинематической цепи: клиноременной передачей, пусковой муфтой, шайбами, кривошипным валом, шатуном, регулирующим величину хода ползуна.
Запускается ползун с помощью ножной пресс-педали, которая связана с пусковой муфтой, после чего начинаются его возвратно-поступательные движения, направленные на рабочий стол пресса. Четырёхшатунный пресс имеет другой принцип действия. Его рабочие органы направляют всё усилие в середину четырёхугольника, который образуют четыре шатуна. Такое устройство успешно используют для изготовления изделий самой сложной конфигурации: асимметричных или габаритных.
Для сложных изделий
Чтобы получить качественные изделия сложной конфигурации, очень широко используется пресс пневматического типа с двумя или тремя ползунами. Пресс двойного действия работает двумя ползунами одновременно: внешний фиксирует заготовку, а внутренний производит вытяжку поверхности металлического листа. Тонкие листы металла штампуют специальными фрикционными прессами, а толстые - гидравлическими, которые имеют более надёжные шайбы.
Отдельная категория штамповочного оборудования - штамповка, управляемым взрывом. Такие устройства направляют мощность взрыва на отдельные участки металлической заготовки (обычно значительной толщины). Это инновационное оборудование, работа которого даже на видео выглядит весьма эффектно. Сгибы и общую конфигурацию сложного изделия обрабатывают с помощью встроенных вибрационных ножниц.
Листовая штамповка
Листовая штамповка (например, изготовление перфолиста) подразумевает процесс пробивания листового металла. Вся остальная штамповка - объёмная. Применяемая оснастка для штамповочного оборудования разделяется на виды. Она может быть инструментальной, импульсной (взрыв, магнитный или гидроимпульс), валковой или штамповкой эластичными средами. Листовой штамповкой можно изготовить пространственные и плоские детали различной массы - от долей грамма, и различных размеров - от долей миллиметра (здесь можно посмотреть на секундную стрелку наручных часов). Также листовой штамповкой изготавливаются детали во многие десятки килограммов по массе и в несколько метров величиной (автомобильная облицовка, ракеты и самолёты).
Используют для этого преимущественно низкоуглеродную сталь, а также и легированную - с особой пластичностью, латунь, медь, алюминий и магний со сплавами, титан и многое другое. Листовая штамповка - это почти все отрасли промышленности: ракето-, самолёто-, тракторо-, авто-, приборостроение, электротехническая промышленность и так далее, можно перечислять всё. Преимущества её велики.
Объёмная штамповка
Объёмная штамповка может быть выполнена и холодным, и горячим способами. Горячая - обработка давлением, где формообразование поковки осуществляется с помощью штампа. Заготовками служат прокат прямоугольного, круглого, квадратного профиля, который разрезается на мерные заготовки (иногда не разрезают, а штампуют прямо из прутка, отделяя затем поковку прямо штамповочной машиной).
Объёмная штамповка применяется при массовом производстве и серийном, что повышает производительность труда и снижает отходы металла. Качество изделий тоже соответствует высоким стандартам. Такой штамповкой получают изделия, исключительно сложные по форме, которые нельзя получить даже свободной ковкой.
Штампы открытые и закрытые
Открытые штампы позволяют наблюдать зазор между неподвижной и подвижной частями станка. При горячей штамповке в зазор вытекает облой - металл, закрывающий выход из полости и заставляющий остальную массу заполнить полость полностью. В процессе деформирования в облой попадают излишки металла. Но удалять облой трудно.
Закрытые штампы не позволяют заглядывать внутрь и наблюдать процесс - полость закрыта. Облой тоже не предусмотрен. Устройство такого штампа зависит от типа станка. Здесь нужно очень строго соблюдать точность объёмов и равенство их в заготовках и поковках: недостаток металла оставит пустыми углы полости, а избыток его сделает поковку больше требуемой по высоте.
fb.ru