- закалить сталь 1 Начните со стали, содержащей достаточное количество углерода. В процессе закалки стали содержащийся в ней углерод остается в твердом растворе и образуется мартенсит. Если сталь не содержит других легирующих элементов, для ее легкой закалки достаточно около 1,0 процента углерода. Стали с таким содержанием углерода называются высокоуглеродистыми или инструментальными сталями.
- Среднеуглеродистые стали, содержащие 0,7-0,8 процента углерода, также поддаются закалке, но для того, чтобы закалить детали из них на полную глубину, такие стали должны быть легированы еще чем-то кроме углерода.
- Низкоуглеродистые стали с содержанием углерода 0,4 процента и ниже не могут быть закалены напрямую. Тем не менее, для повышения твердости их можно покрыть другим материалом, - такой процесс называется поверхностным упрочнением.
- закалить сталь 2 Нагрейте сталь. Сперва довольно медленно разогрейте всю деталь. Затем разогревайте преимущественно тот участок, который вы собираетесь закалить (например, наконечник долота или отвертки) до тех пор, пока он не раскалится до ярко-красного оттенка.
- закалить сталь 3 Закалите сталь в жидкости. Погружение раскаленной стали в холодную жидкость или газ быстро остужает металл, упрочняя его. Для закалки можно использовать различные жидкости.
- Пресная вода наиболее часто используется для закалки, но она вызывает коррозию стали. Если при закалке образуются пузырьки воздуха, это может замедлить охлаждение и привести к образованию мягких участков на поверхности металла, поэтому воду обычно перемешивают для предотвращения этого.
- В соленой воде сталь закаляется быстрее, чем в пресной, поскольку в первой пузырьки воздуха быстрее отрываются от поверхности металла и всплывают. Однако сразу же после закалки металл необходимо помыть, поскольку в соленой воде сталь корродирует быстрее, чем в пресной.
- Масло, например, минеральное, хлопковое или китовый жир, охлаждает сталь медленнее воды. Сталь, закаленная в масло, будет менее твердой, нежели закаленная в воду, но при этом она будет и менее хрупкой. При закалке масло может дымить, искрить и брызгать, что создает опасность пожара при несоблюдении мер безопасности.
- Водный раствор полимеров типа гликоль дает скорости закалки, промежуточные между водой и маслом, при этом скорость зависит от концентрации раствора. Такие растворы вызывают менее интенсивную коррозию, чем вода, и менее пожароопасны по сравнению с маслом, но для получения нужной скорости закалки необходимо постоянно контролировать концентрацию полимера в растворе.
- Закалка до криогенных температур применяется, чтобы избежать образования мягких и хрупких участков на поверхности материала и чтобы добиться большего упрочнения стали по всему объему. Такая закалка чаще применяется для высокоуглеродистых, нежели для среднеуглеродистых, сталей.
- закалить сталь 4 Очистите сталь. Это удалит остатки закалочной жидкости и подготовит сталь к отжигу. Если при закалке использовалась не вода, а другая жидкость, можете промыть деталь в воде. Если использовалась вода, можете протереть деталь мелкой наждачной шкуркой.
- закалить сталь 5 Нагрейте сталь снова. Этот второй нагрев называется отжигом (отпуском) стали и предназначен для того, чтобы устранить хрупкость, возникшую при закалке. Сталь можно разогреть в печи или в ванне с маслом, смесью нитратов натрия и калия, либо с расплавленным свинцом. Температура отжига определяет твердость стали после отжига: чем выше температура, тем менее твердым, но одновременно и менее хрупким, будет материал.
- Во время отжига поверхность разогретой стали окрашивается в цвета оксидов, в зависимости от температуры: от светло-соломенного примерно при 200 градусах Цельсия до пурпурного при 300 градусах. Этими цветами пользуются, чтобы контролировать температуру отжига. Однако легированные стали приобретают тот же цвет, что углеродистые, при более высоких температурах.
- закалить сталь 6 Дайте стали остыть. На этот раз, в отличие от закалки, сталь можно остужать как быстро, так и медленно, в зависимости от свойств, которые вы хотите получить. Но следует иметь в виду, что те стали, для которых существует опасность повторного охрупчивания уже после отпуска, следует охлаждать медленно.
- Отверстия, просверливаемые в детали перед закалкой и отжигом, должны быть сквозными, и при термообработке их следует заполнить асбестовой ватой во избежание растрескивания.
- 1 Начните со стали, содержащей достаточное количество углерода. В процессе закалки стали содержащийся в ней углерод остается в твердом растворе и образуется мартенсит. Если сталь не содержит других легирующих элементов, для ее легкой закалки достаточно около 1,0 процента углерода. Стали с таким содержанием углерода называются высокоуглеродистыми или инструментальными сталями. http://pad1.whstatic.com/images/thumb/5/5e/Harden-Steel-Step-1-preview.jpg/550px-Harden-Steel-Step-1-preview.jpg http://pad2.whstatic.com/images/thumb/5/5e/Harden-Steel-Step-1-preview.jpg/300px-Harden-Steel-Step-1-preview.jpg http://d5kh3btv85w9n.cloudfront.net/2/2e/Harden Steel Step 1.360p.mp4
- Среднеуглеродистые стали, содержащие 0,7-0,8 процента углерода, также поддаются закалке, но для того, чтобы закалить детали из них на полную глубину, такие стали должны быть легированы еще чем-то кроме углерода.
- Низкоуглеродистые стали с содержанием углерода 0,4 процента и ниже не могут быть закалены напрямую. Тем не менее, для повышения твердости их можно покрыть другим материалом, - такой процесс называется поверхностным упрочнением.
- 2 Нагрейте сталь. Сперва довольно медленно разогрейте всю деталь. Затем разогревайте преимущественно тот участок, который вы собираетесь закалить (например, наконечник долота или отвертки) до тех пор, пока он не раскалится до ярко-красного оттенка. http://pad3.whstatic.com/images/thumb/6/61/Harden-Steel-Step-2-preview.jpg/550px-Harden-Steel-Step-2-preview.jpg http://pad1.whstatic.com/images/thumb/6/61/Harden-Steel-Step-2-preview.jpg/300px-Harden-Steel-Step-2-preview.jpg http://d5kh3btv85w9n.cloudfront.net/a/a8/Harden Steel Step 2.360p.mp4
- 3 Закалите сталь в жидкости. Погружение раскаленной стали в холодную жидкость или газ быстро остужает металл, упрочняя его. Для закалки можно использовать различные жидкости. http://pad1.whstatic.com/images/thumb/a/a7/Harden-Steel-Step-3-preview.jpg/550px-Harden-Steel-Step-3-preview.jpg http://pad3.whstatic.com/images/thumb/a/a7/Harden-Steel-Step-3-preview.jpg/300px-Harden-Steel-Step-3-preview.jpg http://d5kh3btv85w9n.cloudfront.net/4/44/Harden Steel Step 3.360p.mp4
- Пресная вода наиболее часто используется для закалки, но она вызывает коррозию стали. Если при закалке образуются пузырьки воздуха, это может замедлить охлаждение и привести к образованию мягких участков на поверхности металла, поэтому воду обычно перемешивают для предотвращения этого.
- В соленой воде сталь закаляется быстрее, чем в пресной, поскольку в первой пузырьки воздуха быстрее отрываются от поверхности металла и всплывают. Однако сразу же после закалки металл необходимо помыть, поскольку в соленой воде сталь корродирует быстрее, чем в пресной.
- Масло, например, минеральное, хлопковое или китовый жир, охлаждает сталь медленнее воды. Сталь, закаленная в масло, будет менее твердой, нежели закаленная в воду, но при этом она будет и менее хрупкой. При закалке масло может дымить, искрить и брызгать, что создает опасность пожара при несоблюдении мер безопасности.
- Водный раствор полимеров типа гликоль дает скорости закалки, промежуточные между водой и маслом, при этом скорость зависит от концентрации раствора. Такие растворы вызывают менее интенсивную коррозию, чем вода, и менее пожароопасны по сравнению с маслом, но для получения нужной скорости закалки необходимо постоянно контролировать концентрацию полимера в растворе.
- Закалка до криогенных температур применяется, чтобы избежать образования мягких и хрупких участков на поверхности материала и чтобы добиться большего упрочнения стали по всему объему. Такая закалка чаще применяется для высокоуглеродистых, нежели для среднеуглеродистых, сталей.
- 4 Очистите сталь. Это удалит остатки закалочной жидкости и подготовит сталь к отжигу. Если при закалке использовалась не вода, а другая жидкость, можете промыть деталь в воде. Если использовалась вода, можете протереть деталь мелкой наждачной шкуркой. http://pad1.whstatic.com/images/thumb/e/e7/Harden-Steel-Step-4-preview.jpg/550px-Harden-Steel-Step-4-preview.jpg http://pad3.whstatic.com/images/thumb/e/e7/Harden-Steel-Step-4-preview.jpg/300px-Harden-Steel-Step-4-preview.jpg http://d5kh3btv85w9n.cloudfront.net/e/eb/Harden Steel Step 4.360p.mp4
- 5 Нагрейте сталь снова. Этот второй нагрев называется отжигом (отпуском) стали и предназначен для того, чтобы устранить хрупкость, возникшую при закалке. Сталь можно разогреть в печи или в ванне с маслом, смесью нитратов натрия и калия, либо с расплавленным свинцом. Температура отжига определяет твердость стали после отжига: чем выше температура, тем менее твердым, но одновременно и менее хрупким, будет материал. http://pad1.whstatic.com/images/thumb/a/a1/Harden-Steel-Step-5-preview.jpg/550px-Harden-Steel-Step-5-preview.jpg http://pad2.whstatic.com/images/thumb/a/a1/Harden-Steel-Step-5-preview.jpg/300px-Harden-Steel-Step-5-preview.jpg http://d5kh3btv85w9n.cloudfront.net/8/83/Harden Steel Step 5.360p.mp4
- Во время отжига поверхность разогретой стали окрашивается в цвета оксидов, в зависимости от температуры: от светло-соломенного примерно при 200 градусах Цельсия до пурпурного при 300 градусах. Этими цветами пользуются, чтобы контролировать температуру отжига. Однако легированные стали приобретают тот же цвет, что углеродистые, при более высоких температурах.
- 6 Дайте стали остыть. На этот раз, в отличие от закалки, сталь можно остужать как быстро, так и медленно, в зависимости от свойств, которые вы хотите получить. Но следует иметь в виду, что те стали, для которых существует опасность повторного охрупчивания уже после отпуска, следует охлаждать медленно. http://pad1.whstatic.com/images/thumb/c/ce/Harden-Steel-Step-6-preview.jpg/550px-Harden-Steel-Step-6-preview.jpg http://pad2.whstatic.com/images/thumb/c/ce/Harden-Steel-Step-6-preview.jpg/300px-Harden-Steel-Step-6-preview.jpg http://d5kh3btv85w9n.cloudfront.net/f/f0/Harden Steel Step 6.360p.mp4
- Отверстия, просверливаемые в детали перед закалкой и отжигом, должны быть сквозными, и при термообработке их следует заполнить асбестовой ватой во избежание растрескивания.
- Home
- Trends
- LIVE
- Home
- Trends
- Live TV
Film & Animation
Autos & Vehicles
Music
Pets & Animals
Sports
Travel & Events
Gaming
Comedy
Entertainment
Howto & Style
Science & Technology
- Copyright © 2007-2017
Free Online Videos Best Movies TV shows. Как сталь закаляют
Сталь 45 характеристики. Как производится закалка стали. Закалка стали 45
Каждый сплав имеет свой уникальный состав. Что же касается такого материала как сталь, то известно, что он содержит в себе железо и углерод в определенных пропорциях. Каждая марка стали имеет своё уникальное название, в котором зашифрован её химический состав и физические характеристики. Сталь 45 – не исключение. В данной статье рассмотрим этот популярный сплав более подробно.
Химический состав
Каждый, кто имеет дело со сплавами, знает, что элементы, которые входят в их состав влияют на их характеристику. Сталь 45 – конструкционная углеродистая качественная. Из названия становится понятным, что в её состав входит углерод – 0,45%. Большая часть, конечно же, приходится на железо – 97%. В остальные же 2,55 % входят такие химические элементы, как марганец (0,7%), кремний (0,2-0,3%), никель (0,25%), хром (0,25%), медь (0,25%), мышьяк(0,08), сера(0,04) и фосфор(0,035%). Каждый из легирующих элементов влияет на характеристику стали 45. Например, марганец присутствует практически во всех марках стали. Он удаляет из неё кислород и уменьшает содержание серы. Кремний влияет на закаливаемость стали. Кроме того, он увеличивает предел текучести и упругости.
Углерод и его влияние на свойства стали
Одним из самых важных компонентов, который упрочняет этот сплав и придает ему твердость, является углерод. Кроме этого, он снижает пластичность и вязкость. Влияние углерода на характеристику стали 45 хорошо видно на диаграмме состояний. От структуры сплава и будут завесить его свойства. Так, например, при перлитной структуре сталь лучше поддается обработке и свариванию. Ферритная структура характеризуется незначительной твёрдостью и высокой пластичностью. Аустенит в сталях всегда жидкий и при его охлаждении может значительно меняться положение зерен углерода в кристаллической решетке.
Структура стали 45
Так, цементит – это химическое соединение Fe3C, а кроме него, в стали также присутствует и феррит (С). Вместе они образуют еще одну структуру – перлит. Поскольку содержание углерода ниже 0,8%, то такая сталь считается доэвтектоидной. И для того чтобы улучшить её свойства, её необходимо закалить или отжечь. Это достигается путем её нагрева, при котором она переходит в аустенитное состояние. Критические точки для этого сплава: АС1=725 °С, АС3=770°С. При нагреве его до 700°С, никаких заметных изменений не произойдет.
Рассмотрим диаграмму состояний стали 45 более подробно.
Так, поскольку в сплаве присутствует 0,45% углерода, на нижней горизонтальной линии, необходимо найти это значение. Поднимаясь, вверх от него можно проследить за всеми превращениями в стали. Так, при нагреве выше линии АС - сплав будет находиться в жидком состоянии.
Затем при понижении температуры атомная решетка железа перестроится из гранецентрированной в объемно-центрированную и соответственно в ней будет преобладать феррит. Большое количество углерода будет постепенно преобразовываться с аустенита в перлит. Конечная структура сплава будет зависеть и от того, каким образом сталь охлаждали после закалки.
Термическая обработка
Если данный сплав не подвергают термической обработке, в его структуре преобладает цементит и феррит, а значит, его невозможно механически обработать. Внутреннее напряжение между атомами этого сплава будет настолько высоким, что при фрезеровании и точении он будет трескаться. Для того чтобы этого избежать применяют термическую обработку. Она может состоять из нескольких процессов: отжиг, нормализация, закалка, отпуск. Сама же термическая обработка будет зависеть от вида изделия (поковка, прокат) и от его технического назначения.
Взглянув еще раз на диаграмму состояний, можно сделать вывод, что 850 °С – это оптимальная температура для закалки. Именно в этой точке для стали с содержанием углерода 0,45% происходит переход в аустенитное состояние.
Поэтому чаще всего закалка стали 45 производится при температуре 850 °С, а отпуск - 550 °С. В таком случае сплав будет обладать пределом прочности – 900 МПа, пределом текучести - 800 МПа, ударной вязкостью – 1,2 МДж/м2, относительным сужением – 65% и твердостью 260. Если повысить температуру отпуска, то предел прочности, текучести и твердость понизятся, а остальные значения, наоборот, увеличатся.
Физические свойства
Как уже было сказано ранее, характеристики сплава в целом будут зависеть от закалки стали 45. Сам по себе феррит мягкий и достаточно пластичный, а перлит является твердым, но более хрупким. Так, перлитная структура выглядит, как слоеное тесто. Кристаллы мягкого феррита чередуются с твердым цементитом. Последние, придают перлиту износостойкость и твердость. Исходя из этого, можно сделать вывод, что при повышении содержания углерода, увеличивается и объем, который занимает перлит и, конечно же, улучшаются свойства сплава.
В общих чертах можно сказать, что сталь 45 является достаточно прочной, выносливой и хорошо поддается механической обработке. Из недостатков можно выделить плохую свариваемость и подверженность коррозии. Детали из стали 45 устойчивы к износу и могут выдержать перепады температур от 200 до 600 °С. Более подробные сведения о физических и механических свойствах можно увидеть в следующей таблице.
Как и для любой другой стали, для этой перед механической обработкой необходимо делать расчет режимов резания. В них нужно обязательно выбрать правильный режущий инструмент, скорость вращения шпинделя и, конечно же, рассчитать подачу. Несмотря на то, что сталь 45 хорошо поддается механической обработке, при неправильном выборе режимов резания, возможны такие проблемы, как слишком горячая, отлетающая стружка, произвольное уменьшение оборотов шпинделя. Кроме того, для такого вида механической обработки как точение, для этого сплава рекомендуется применять охлаждающую жидкость.
Большое значение имеет и выбор режущего инструмента. Его необходимо выбирать согласно твердости стали 45. Например, отлично подойдет резец Т15К6 и другие со схожими свойствами.
Область использования
Исходя из характеристики стали 45, можно сделать вывод, что сплав находит широкое применение в металлургической промышленности. Так, из него изготавливают шпиндели, цилиндры, кулачки и самые разнообразные валы. Именно эти детали должны обладать повышенной прочностью. Различные предприятия изготавливают форму, сортамент и размеры, которые определяются ГОСТами. Сталь 45 относится к трудно свариваемым сплавам, поэтому большая часть сортамента производится в качестве бесшовных труб.
fb.ru
Как закаляют сталь
13 июляВ третье воскресенье июля в России отмечается один из самых почитаемых профессиональных праздников – День металлурга. В этом году – в юбилейный 60-й раз. В деятельности Атомэнергомаша металлургическое производство играет стратегически важную роль. Рассказываем о работе наших коллег-металлургов с ЭМСС и Атоммаша.

Новые слитки
За последние три года благодаря модернизации и освоению новых технологий Энергомашспецсталь значительно расширила географию поставок. Сегодня ЭМСС тесно сотрудничает с ведущими компаниями более чем в 50 странах мира. Среди партнеров предприятия такие гиганты промышленности, как ArcellorMittal, Alstom, General Electric, BHEL, Siemens AG и многие другие.Изготовленные на ЭМСС валки поставляются на металлургические заводы Европы, Азии, Северной и Южной Америки. Опорные валки из крупнотоннажных слитков массой 355, 415 и 235 тонн были изготовлены и поставлены на предприятия Laiwu Steel Group (Китай), Voest Alpine Gmbh (Австрия), металлургический комбинат ArcelorMittal Galati (Румыния) и другие. В апреле текущего года завод «ЭМСС» выиграл крупный тендер на поставку валков в Мексику. В рамках масштабного проекта по строительству нового прокатного толстолистового стана «1700» меткомбината ArcelorMittal Lazaro Cardenas (Мексика), ЭМСС изготовит и поставит австрийской компании 1500 т валков. В этом же месяце Энергомашспецсталь заключила сделку с китайским производителем стали и металлопроката компанией Anyang Steel. Согласно договору ЭМСС изготовит два крупнотоннажных опорных валка общим весом 230 тонн. Цельнокованые опорные валки предназначены для эксплуатации в толстолистовом стане горячей прокатки «3500».
На ЭМСС постоянно идут работы по освоению новых видов продукции, расширению марочного сортамента, совершенствованию качества выпускаемого металла. В настоящее время металлургами ЭМСС освоено более 300 марок сталей различных стандартов ГОСТ, DIN и ASTM. С 2017 года на предприятии было произведено свыше 2500 т высоколегированных нержавеющих марок стали мартенситного и аустенитного класса для изготовления изделий АЭС, в том числе из марок стали, производимых в прошлые периоды, а также освоена новая марка стали по перспективному проекту EDF.
Кроме того, на ЭМСС было успешно освоено производство слитков из роторной высокохромистой азотированной стали, а также изготовление валов роторов из них с обеспечением технических требований заказчиков в полном объеме. Освоена новая номенклатура товарной продукции – слитки круглого сечения диаметром 1200 мм и весом 33,5 т.
25 455 тонн продукции было отгружено с производственной площадки ЭМСС в 2017 году.
Новые технологии
Только за 6 месяцев 18-го года металлурги Атоммаша освоили несколько новых технологий. При том, что в команде сегодня всего 14 человек.Новинка №1 — ядерная
Атоммаш производит первый в мире реактор по проекту ВВЭР-ТОИ (типовой оптимизированный и информатизированный). А значит и первое в мире днище такого реактора. Габаритные размеры детали превосходят предшественников ВВЭР-1200 и тысячников. В операции нужно задействовать абсолютно новый штамп. И усложняем задачу — марка стали, из которой выполнена поковка, еще никогда и нигде не применялась. Как с этим работать?
Металлурги решают, какие режимы нагрева применить, с какой силой надавить прессом и как вообще вести себя с металлом. Эти специалисты прорабатывают такие технологии, что сталь не крошится и не трещит под давлением, становится податливой, как пластилин, но не деформируется под градусом, а при остывании приобретает новые свойства и становится еще прочнее, чем была.
Успешная штамповка днища ВВЭР-ТОИ, конечно, заслуга большой команды сотрудников «АЭМ-технологий». Но без металлургов — никуда! «Такого еще никто не делал, и сначала это немного настораживало, — рассказывает главный металлург Атоммаша Евгений Заиграев. — На команде очень высокая ответственность. Мы получаем трубную заготовку, а выдаем почти готовое днище. Наша задача — весь передел: от разгибки кованой обечайки до термообработки уже отштампованного днища».
Новинка №2 — низкотемпературная
В 80-х годах трубный пучок (змеевики внутри парогенератора) развальцовывали методом взрыва. Конструкцию вывозили на полигон, взрывали заложенные внутри патроны, и все трубочки расширялись, герметично прилегая к отверстиям в коллекторах. После проводилась низкотемпературная обработка (НТО).
Со временем специалисты развили технологии и перешли к методу гидрораздачи. Теперь каждый змеевик расширяют с помощью жидкости под высоким давлением. В этом случае последующая термообработка не требуется.
Сейчас в производстве Атоммаша парогенераторы для двух блоков АЭС «Куданкулам». Теплообменники для первых двух блоков были изготовлены еще в советские годы с использованием взрыва и НТО. Теперь индийская сторона выдвинула требование в порядке референтности выполнить процедуру низкотемпературной обработки и на текущих парогенераторах.
Евгений Заиграев: «Как это выполнить, если с того времени допускаемый правилами АЭС температурный диапазон сократился: раньше было 400-520, а теперь всего 400-450 градусов. Как сохранить всего 50 градусов на таких толщинах?.. Металлурги «поскрипели мозгами», создали абсолютно новую нагревательную установку, откатали ее. Действительно добились того, чего казалось бы невозможно добиться». Сейчас металлурги Атоммаша готовятся провести операцию НТО на штатном парогенераторе. Операция совершенно уникальная, не имеющая аналогов.
Новинка №3 — зарубежная
Атоммаш впервые за свою историю изготовил ядерное оборудование зарубежного дизайна. Пока это только пробная деталь-демонстратор. Металлургам вновь поставили задачу проработать технологию работы с непривычной маркой стали и по новым для предприятия европейским требованиям.
«Это своеобразный пропуск к участию в тендере на производство ядерного оборудования для зарубежной станции, — рассказывает Евгений Заиграев. — Конкурс будет на прямые участки трубопровода. А «на пробу» представители Заказчика дали более сложное задание — гнутоштампованное колено. Мы смогли провести операцию в соответствии со всеми требованиями».
Новые продуктовые направления
Активно выходит на новые рынки дочернее общество АО «АЭМ-технологии» — ООО «Литейный завод «Петрозаводскмаш». Год назад машиностроительный дивизион Росатома, АО «Атомэнергомаш», заключил соглашение о намерениях с концерном DMG MORI. Документ подписали Андрей Никипелов, генеральный директор АО «Атомэнергомаш», Вадим Тряпичкин, директор ООО «Литейный завод «Петрозаводскмаш», Дирк Хулльманн, управляющий директор «ГИЛЬДЕМАЙСТЕР Бетайлигунген ГмбХ», и Алексей Антипин, генеральный директор ООО «Ульяновский станкостроительный завод».В Соглашении стороны заявили о заинтересованности в долгосрочном сотрудничестве и реализации совместных проектов по локализации производства станкоинструментальной продукции. Согласно подписанному документу, «Литейный завод «Петрозаводскмаш» будет поставлять чугунные отливки компонентов станков для Ульяновского станкостроительного завода и европейских заводов DMG MORI.
Первой партией изделий, которые петрозаводские металлурги поставили станкостроителям в Ульяновск, стали литые станины для токарного станка CTX-310. Станины были приняты к серийному производству, и стороны приняли решение расширить сотрудничество.
Сегодня завод расширяет поставки станкостроительного литья. По заказу компании «СТАН» была изготовлена партия оснований высокоточных пятикоординатных фрезерных обрабатывающих центров. В процессе изготовления находится основание токарно-карусельного станка. Это деталь диаметром 6 метров и весом около 40 тонн.
В этом году, после десятилетнего перерыва, Литейный завод возобновил работу по традиционному направлению — оборудование для целлюлозно-бумажной промышленности. Летом 2017 года был подписан контракт на изготовление 50 валов для бумагоделательной машины. Чугунные заготовки для валов отлили на кессонном участке литейного производства, механическую обработку, сборку крышек и цапф провели в механосборочном производстве ООО «Литейный завод «Петрозаводскмаш». Хорошее качество изделий и готовность предприятий к дальнейшему сотрудничеству позволили уже в этом году подписать ещё два контракта на поставку аналогичной продукции.
Основная специализация «Литейного завода «Петрозаводскмаш» — отливки из чугуна различных марок массой до 120 тонн, в том числе, высокопрочного чугуна с шаровидным графитом. Из чугуна именно этой уникальной марки, прочного и пластичного одновременно, были отлиты массивные кольца тепловой защиты для многоцелевого исследовательского реактора на быстрых нейтронах (МБИР), который строится в Димитровграде на площадке Государственного научного центра «НИИАР». Наружный диаметр толстостенных колец — 4,5 метра. Всего Литейный завод изготовил восемь чугунных отливок общей массой 265 тонн.
Новая продукция литейщиков Петрозаводска по атомному направлению — опорные стаканы системы предварительного натяжения бетона защитной оболочки (СПЗО) реакторного отделения АЭС. По заказу ООО «Следящие тест-системы» (ООО «СТС»), которое является главным конструктором и поставщиком оборудования, Литейный завод Петрозаводскмаша уже изготовил пилотную серию опорных стаканов для подтверждения технологии изготовления отливки и качества продукции, получил положительный результат. Первой станцией, на которой будут применены стаканы СПЗО, изготовленные карельскими металлургами, станет Курская АЭС. С учетом «дорожной карты» строительства АЭС, данное изделие может стать для Литейного завода серийным. Кроме того, это продуктовое направление открывает «Литейному заводу «Петрозаводскмаш» новые рынки изготовления современных строительных конструкций, которые используют системы предварительного натяжения бетона при возведении мостов, виадуков и других высоконагруженных бетонных конструкций.
vestnik-aem.ru
Как закалить сталь Как? Так!
Содержимое:
Сталь - это сплав на основе железа, используемый в конструкциях при изготовлении металлических инструментов и для других целей. Если при эксплуатации необходимы высокие прочность и износостойкость, сталь нужно закалить и затем отжечь (отпустить) для реализации ее прочностного потенциала. Пользуясь правильными инструментами и имея небольшой опыт, вы сможете без проблем сделать это.
Шаги
Предупреждения
Прислал: Лебедева Мария . 2017-11-06 14:05:28
kak-otvet.imysite.ru
как закалить сталь Видео
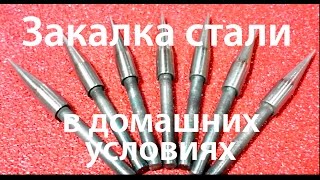
2 г. назад
Технология закалки высокоуглеродистой стали в домашних условиях. Плейлисты: Рыбалка - https://goo.gl/HnTbjq Своими...
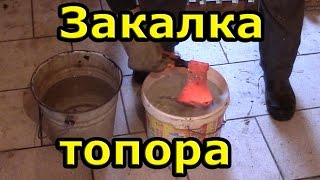
2 г. назад
Видео-Самоучитель Плотника http://srub-banya.by/shop/ Автор Валерий Самович. В этом ролике на примере топора хочу...
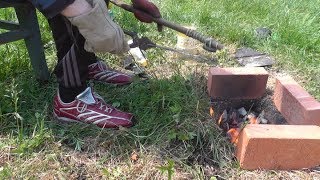
5 г. назад
Видео о закалке самодельного ножа в домашних условиях, для плейлиста, посвященного изготовлению ножа с...
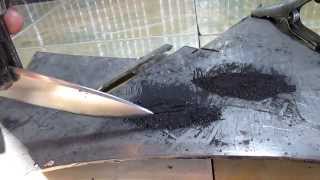
3 г. назад
Подписаться на канал-https://www.youtube.com/evgeniidem ГРУППА ВКонтакте-http://vk.com/club63976996 Facebook ...
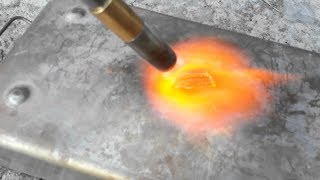
1 г. назад
КИРПИЧНАЯ СТЕНА В СТИЛЕ ЛОФТ - https://www.youtube.com/watch?v=STyMLjX-j6g КАК ЗАКАЛИТЬ МЕТАЛЛ своими руками. ЗАКАЛКА МЕТАЛЛА...

2 г. назад
Как правильно закаливать заготовку или лезвие ножа в домашних условиях.
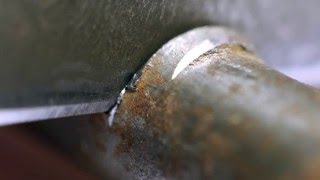
2 г. назад
Как влияет неправильная закалка на сталь. Зонная закалка вылезла только после травления и я решил сломать...
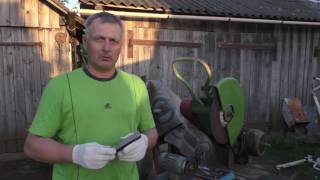
2 г. назад
Есть несколько способов для отличия 45 стали от обычной. Два самых простых - это снять с изделия стружку...
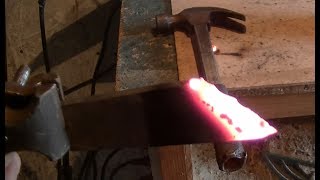
4 мес. назад
Я покажу, как закаливать металл без использования огня за 10 секунд. Без горелки, паяльной лампы, резака,...

8 мес. назад
Инстаграм - https://www.instagram.com/piwell_inst/ Паблос - https://vk.com/pi_well TWITCH - https://go.twitch.tv/piwellrazor GoodGame ...
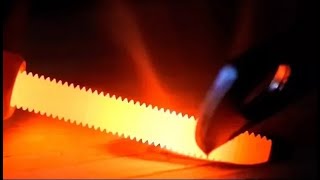
1 г. назад
КИРПИЧНАЯ СТЕНА В СТИЛЕ ЛОФТ - https://www.youtube.com/watch?v=STyMLjX-j6g КАК ЗАКАЛИТЬ МЕТАЛЛ своими руками. ЗАКАЛКА МЕТАЛЛА...

1 г. назад
https://vk.com/iddeddin я ВК Еще давно решил изготовить нож из напильника но столкнулся с проблемой при закалке,данно...

1 г. назад
Как закалялась сталь. я знаю что оговорился ауслит - аустенит, но всем пофиг. Паблос - https://vk.com/pi_well Инстаграм...
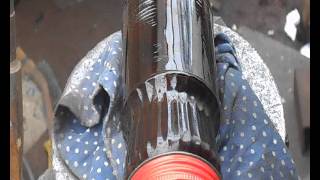
2 г. назад
https://vk.com/id27742556 https://www.livemaster.ru/platonov-mihail https://www.livemaster.ru/platonov-mihail.
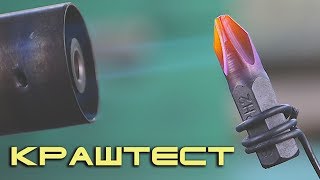
9 мес. назад
Это видео https://www.youtube.com/watch?v=YYuQsIAOe0U набрало более 700 000 просмотров значит нужно провести КРАШТЕСТ закалка...
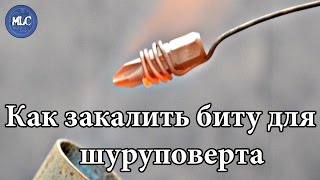
2 г. назад
Простой способ продлить жизнь биты для шуруповерта, закалить её в масле. Подписаться на канал: https://goo.gl/1CBapH...

6 мес. назад
Сталь - это сплав на основе железа, используемый в конструкциях при изготовлении металлических инструменто...
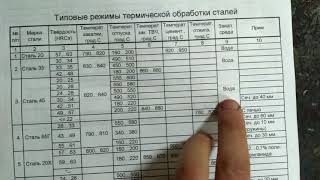
6 мес. назад
Закалка матриц из 45 стали производиться на воду, отпуск низкотемпературный. Если вам необходимо закалить...
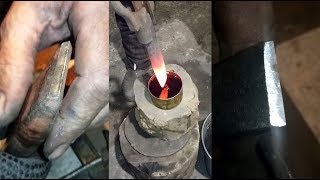
8 мес. назад
Кого интересует партнёрская программа, проходите по ссылке https://youpartnerwsp.com/join?108188 Как сделать зуб на старой...
videohot.ru
Сталь - это сплав на основе железа, используемый в конструкциях при изготовлении металлических инструментов и для других целей. Если при эксплуатации необходимы высокие прочность и износостойкость, сталь нужно закалить и затем отжечь (отпустить) для реализации ее прочностного потенциала. Пользуясь правильными инструментами и имея небольшой опыт, вы сможете без проблем сделать это. ШагиПредупреждения |
ves-mir.3dn.ru
Закалка сталей
Закалка - это процесс термической обработки, заключающийся в нагреве стали до температуры выше критической и последующем быстром охлаждении, со скоростью подавляющей распад аустенита на феррито-цементитную смесь и обеспечивающей структуру мартенсита.
Содержание
Мартенсит и мартенситное превращение в сталях
Мартенсит - это пересыщенный твердый раствор углерода в α-железе (α-Fe). Что такое аустенит, цементит, феррит и перлит читаем здесь. При нагреве эвтектоидной стали (0,8 % углерода) выше точки А1, исходная структура перлит превратится в аустенит. При этом в аустените растворится весь углерод, который имеется в стали, т. е. 0,8 %. Быстрое охлаждение со сверхкритической скоростью (см. рисунок ниже), например в воде (600 °С/сек), препятствует диффузии углерода из аустенита, но кристаллическая ГЦК решетка аустенита перестроится в тетрагональную решетку мартенсита. Данный процесс называется мартенситным превращением. Он характеризуется сдвиговым характером перестройки кристаллической решетки при такой скорости охлаждения, при которой диффузионные процессы становятся невозможны. Продуктом мартенситного превращения является мартенсит с искаженной тетрагональной решеткой. Степень тетрагональности зависит от содержания углерода в стали: чем его больше, тем больше степень тетрагональности. Мартенсит - это твердая и хрупкая структура стали. Находится в виде пластин, под микроскопом выглядит, как иглы.
Температура закалки для большинства сталей определяется положением критических точек А1 и А3. На практике температуру закалки сталей определяют при помощи марочников сталей. Как выбрать температуру закалки стали с учетом точек Ас1 и Ас3 читаем по ссылке.
Микроструктура стали после закалки
Для большинства сталей после закалки характерна структура мартенсита и остаточного аустенита, причем количество последнего зависит от содержания углерода и качественного и количественного содержания легирующих элементов. Для конструкционных сталей среднего легирования количество остаточного аустенита может быть в пределах 3-5%. В инструментальных сталях это количество может достигать 20-30%.
Вообще, структура стали после закалки определяется конечными требованиями к механическим свойствам изделия. Наряду с мартенситом, после закалки в структуре может присутствовать феррит или цементит (в случае неполной закалки). При изотермической закалке стали ее структура может состоять из бейнита. Структура, конечные свойства и способы закалки стали рассмотрены ниже.
Частичная закалка стали
Частичной называется закалка, при которой скорости охлаждения не хватает для образования мартенсита и она оказывается ниже критической. Такая скорость охлаждения обозначена синей линией на рисунке. При частичной закалке как-бы происходит задевание "носа" С-кривой стали. При этом в структуре стали наряду с мартенситом будет присутствовать троостит в виде черных островковых включений.
Микроструктура стали с частичной закалкой выглядит примерно следующим образом
Частичная закалка является браком, который устраняется полной перекристаллизацией стали, например при нормализации или при повторном нагреве под закалку.
Неполная закалка сталей
Закалка от температур, лежащих в пределах между А1 и А3 (неполная закалка), сохраняет в структуре доэвтектоидных сталей наряду с мартенситом часть феррита, который снижает твердость в закаленном состоянии и ухудшает механические свойства после отпуска. Это понятно, так как твердость феррита составляет 80НВ, а твердость мартенсита зависит от содержания углерода и может составлять более 60HRC. Поэтому данные стали обычно нагревают до температур на 30–50 °С выше А3 (полная закалка). В теории, неполная закалка сталей не допустима и является браком. На практике, в ряде случаев для избежания закалочных трещин, неполная закалка может использоваться. Очень часто это касается закалки токами высокой частоты. При такой закалке необходимо учитывать ее целесообразность: тип производства, годовую программу, тип ответственности изделия, экономическое обоснование. Для заэвтектоидных сталей закалка от температур выше А1, но ниже Асm дает в структуре избыточный цементит, что повышает твердость и износоустойчивость стали. Нагрев выше температуры Аcm ведет к снижению твердости из-за растворения избыточного цементита и увеличения остаточного аустенита. При этом происходит рост зерна аустенита, что также негативно сказывается на механических характеристиках стали.
Таким образом, оптимальной закалкой для доэвтектоидных сталей является закалка от температуры на 30–50 °С выше А3, а для заэвтектоидных – на 30–50 °С выше А1.
Скорость охлаждения также влияет на результат закалки. Оптимальной охлаждающей является среда, которая быстро охлаждает деталь в интервале температур минимальной устойчивости переохлажденного аустенита (в интервале носа с-кривой) и замедленно в интервале температур мартенситного превращения.
Стадии охлаждения при закалке
Наиболее распространенными закалочными средами являются вода различной температуры, полимерные растворы, растворы спиртов, масло, расплавленные соли. При закалке в этих средах различают несколько стадий охлаждения:
- пленочное охлаждение, когда на поверхности стали образуется «паровая рубашка»;
- пузырьковое кипение, наступающее при полном разрушении этой паровой рубашки;
- конвективный теплообмен.
Более подробно про стадии охлаждения при закалке можно прочитать в статье "Характеристики закалочных масел"
Кроме жидких закалочных сред используется охлаждение в потоке газа разного давления. Это может быть азот (N2), гелий (Не) и даже воздух. Такие закалочные среды часто используются при вакуумной термообработке. Здесь нужно учитывать факт возможности получения мартенситной структуры - закаливаемость стали в определенной среде, т. е. химический состав стали от которого зависит положение с-кривой.
Факторы, влияющие на положение с-кривых:
- Углерод. Увеличение содержания углерода до 0,8% увеличивает устойчивость переохлажденного аустенита, соответственно с-кривая сдвигается вправо. При увеличении содержания углерода более 0,8%, с-кривая сдвигается влево;
- Легирующие элементы. Все легирующие элементы в разной степени увеличивают устойчивость аустенита. Это не касается кобальта, он уменьшает устойчивость переохлажденного аустенита;
- Размер зерна и его гомогенность. Чем больше зерно и чем оно однороднее структура, тем выше устойчивость аустенита;
- Увеличение степени искажения кристаллической решетки снижает устойчивость переохлажденного аустенита.
Температура влияет на положение с-кривых через все указанные факторы.
Способы закалки сталей
На практике применяются различные способы охлаждения в зависимости от размеров деталей, их химического состава и требуемой структуры (схема ниже).
Схема: Скорости охлаждения при разных способах закалки сталей
Непрерывная закалка стали
Непрерывная закалка (1) – способ охлаждения деталей в одной среде. Деталь после нагрева помещают в закалочную среду и оставляют в ней до полного охлаждения. Данная технология самая распространенная, широко применяется в условиях массового производства. Подходит практически для всех типов конструкционных сталей.
Закалка в двух средах
Закалка в двух средах (скорость 2 на рисунке) осуществляется в разных закалочных средах, с разными температурами . Сначала деталь охлаждают в интервале температур например 890–400 °С например в воде, а потом переносят в другую охлаждающую среду – масло. При этом мартенситное превращение будет происходить уже в масляной среде, что приведет к уменьшению поводок и короблений стали. Такой способ закалки используют при термообработке штампового инструмента. На практике часто используют противоположный технологический прием - сначала детали охлаждают в масле, а затем в воде. При этом мартенситное превращение происходит в масле, а в воду детали перемещают для более быстрого остывания. Таким образом экономится время на осуществление технологии закалки.
Ступенчатая закалка
При ступенчатой закалке (скорость 3) изделие охлаждают в закалочной среде, имеющей температуру более высокую, чем температура мартенситного превращения. Таким образом получается некая изотермическая выдержка перед началом превращения аустенита в мартенсит. Это обеспечивает равномерное распределение температуры по всему сечению детали. Затем следует окончательное охлаждение, во время которого и происходит превращение мартенситное превращение. Этот способ дает закалку с минимальными внутренними напряжениями. Изотермическую выдержку можно сделать чуть ниже температуры Мн, уже после начала мартенситного превращения (скорость 6). Такой способ более затруднителен с технологической точки зрения.
Изотермическая закалка сталей
Изотермическая закалка (скорость 4) делается для получения бейнитной структуры стали. Данная структура характеризуется отличным сочетание прочностных и пластических свойств. При изотермической закалке детали охлаждают в ванне с расплавами солей, которые имеют температуру на 50–150 °С выше мартенситной точки Мн, выдерживают при этой температуре до конца превращения аустенита в бейнит, а затем охлаждают на воздухе.
При закалке на бейнит возможно получение двух разных структур: верхнего и нижнего бейнита. Верхний бейнит имеет перистое строение. Он образуется в интервале 500-350°С и состоит из частиц феррита в форме реек толщиной <1 мкм и шириной 5-10 мкм, а также из тонких частиц цементита. Структура верхнего бейнита отличается более высокой твердостью и прочностью, но пониженной пластичностью. Нижний бейнит имеет игольчатое мартенситоподобное строение, образуется в интервале 350-200 °С. Нижний бейнит состоит из тонких частиц ε-карбидов, расположенных в пластинках феррита. Бейнитное превращение никогда не идет до конца. В структуре всегда есть мартенсит и остаточный аустенит. Более предпочтительной, в плане эксплуатационных характеристик, является структура нижнего бейнита. Изделия с такой структурой используются в вагоностроении, в деталях испытывающих ударно-растягивающие напряжения. Технология закалки на бейнит требует специального закалочного оборудования. Дополнительные материалы по этой технологии можете найти в статье "Технология закалки на бейнит".
Обработка холодом (5) применяется для сталей, у которых температура конца мартенситного превращения Мк находится ниже комнатной температуры.
Обработке холодом подвергают быстрорежущие стали, цементованные детали, мерительные инструменты, и другие особо точные изделия. Подробнее про этот нестандартный способ термообработки можете прочитать в статье "Обработка холодом стальных деталей"
Зависимость твердости мартенсита от содержания углерода
Твердость стали после закалки зависит от твердости мартенсита, которая в свою очередь зависит от содержания углерода. С увеличением содержания углерода увеличивается и твердость после закалки стали. Графическая зависимость приведена на рисунке.
График зависимости твердости мартенсита от содержания углерода
heattreatment.ru
как закалить сталь
Categories

vevo.site