- толщина 0,01-0,6 мм;
- поверхностная твердость – 400-1200 HV;
- повышение износостойкости в 2-11 раз;
- снижение коэффициента трения в 1,5-5 раз;
- хрупкость слоя – отсутствует;
- повышение задиростойкости, включая нержавеющие стали;
- повышение усталостной прочности в 1,5-2 раза;
- повышение коррозионной стойкости перлитных сталей в 1,5-2 раза;
- коробление и поводки длинномерных деталей – практически отсутствуют.
- Притирка доводочной шкуркой зернистостью 360 или мельче;
- Полирование или тонкое шлифование специальными полировочными кругами в непрерывном процессе подобно бесцентровому шлифованию или шлифованию на токарных автоматах;
- Скользящее шлифование в вибрационной емкости;
- Струйная обработка стеклянными шариками диаметром 40-70 мкм.
- высокая твердость и износостойкость поверхности;
- повышение предела контактной устойчивости;
- улучшение показателей предела выносливости при изгибе и кручении.
- твердые;
- газообразные;
- растворы электролитов;
- пасты;
- кипящий слой.
- углекислый натрий, кальций или барий;
- березовый или дубовый уголь, содержание которого в смеси составляет 70-90%.
- Соль и уголь смешивают в твердом состоянии.
- Более предпочтительный способ заключается в обработке древесного угля растворенной в воде солью. Смесь просушивают до достижения уровня влажности 7%. Такая технология позволяет получить более однородную смесь.
- Заготовки укладывают в ящик слоями с пересыпкой карбюризатором.
- Ящики обмазывают огнеупорной глиной и устанавливают в разогретую печь.
- Тару с содержимым прогревают примерно до 800°C. О качественном прогреве свидетельствует отсутствие темных пятен на подине в местах ее соприкосновения с ящиком.
- После прогрева температуру в печи поднимают до 950°C и выдерживают в таких условиях заготовку на протяжении определенного времени. При этом происходит проникновение активных атомов углерода в кристаллическую решетку стали.
- повышается износостойкость, так как поверхность становится тверже;
- возрастает усталостная прочность изделий;
- образуется стойкий антикоррозионный барьер.
- Поверхностный слой изделия приобретает высокую твердость без дополнительной термической обработки. Прочность поверхностного слоя примерно в 2 раза выше, чем после науглероживания.
- Геометрические параметры заготовки после азотирования остаются практически без изменений.
- Может применяться для изделий после закалки с высоким отпуском и шлифованием в размер.
- После науглероживания поверхностный слой сохраняет полученную твердость до температур до 225°C, после диффузионного насыщения азотом – до 600°C.
- части стальных элементов, не предназначенные для насыщения азотом, защищают оловом или жидким стеклом, наносимым по технологии электролиза;
- закладывают в муфель, в который из баллона закачивают аммиак;
- внутри реторты аммиак разлагается на азот и водород;
- атомарный азот проникает в поверхность стальной детали с образованием нитридов, для которых характерна очень высокая твердость;
- после выдержки заготовку в реторте охлаждают вместе с печью, чтобы закрепилась твердость поверхности без окисления.
- Одновременное насыщение азотом и углеродом инициирует появление карбонитридных фаз – более пластичных и менее хрупких, по сравнению с чисто нитридными.
- Карбонитрация – наиболее экономичный процесс, благодаря его небольшой длительности – 0,5-4 часа.
- Равномерность нагрева и диффузии.
- Отсутствие термических напряжений, обеспечивающее минимальные деформации и точность геометрических параметров в пределах микронов.
- Улучшение усталостной прочности изделий до 80%, износостойкости, коррозионной стойкости.
- Уменьшение коэффициента трения до 5 раз.
- Отсутствие хрупкости поверхностного слоя, насыщенного карбонитридами.
- Возможность обработки недорогих низкоуглеродистых сталей, которые не упрочняются традиционным азотированием. В результате карбонитрации они приобретают характеристики, которыми обладают более дорогие и хуже обрабатываемые стали.
- Этот процесс для рядовых деталей является финишным, не требующим дополнительной механической обработки. Ответственные изделия после карбонитрации подвергают хонингованию – полировке на 1-2 мкм.
- На карбонитрацию поступают детали с окончательными размерами. При необходимости оставляют минимальный припуск на посадочных поверхностях для полировки.
- Предварительные мероприятия: очистка, обезжиривание.
- Нагрев в печи и карбонитрация.
- Охлаждение в воде, масле, на воздухе.
- Промывка, сушка.
- режущий инструмент;
- пресс-формы;
- пары трения;
- элементы зубчатых передач;
- детали насосов.
- первоначальная цель – улучшение товарного вида;
- резкое снижение коэффициента трения;
- коррозионная стойкость марок перлитного и аустенитного классов, обработанных способом НОК, превышает аналогичный показатель этих материалов, хромированных гальваническим методом;
- себестоимость на 40% ниже, по сравнению с гальваническими покрытиями.
- карбонитрация;
- охлаждение и выдержка в расплаве ванны оксидирования при 350-400°C;
- охлаждение на воздухе;
- промывка;
- полирование;
- повтор оксидирования;
- промывка.
- Обдирка азотированного слоя на глубину 0,5-0,7 мм.
- Наплавка (аргонодуговая или лазерная).
- Мехобработка.
- Полировка
- Карбонитрация
- Прокошкин Д.А. Химические и термические методы обработки стали. М.-л.: оНтп, 1938.
- Прокошкин Д.Аа. теория и практика цианирования быстрорежущих сталей. М.: ВНиитоМ, 1940.
- Прокошкин Д.А. а.с. 576350 ссср, Мки3 с22с27/0 опубл. в Б. и., №3, 1977.
- Прокошкин Д.А. Химико-термическая обработка металлов – карбонитрация. М.: Машиностроение, Металлургия, 1984, 240 с.
- Супов А.В. создание процесса карбонитрации. сборник научных трудов: «Металловедение. термическая и химико-термическая обработка сплавов». М.: МГту им. Н.Э. Баумана, 2003.
- Цих C.Г., Щеглов М.T., Гришин В.B., Лисицкий В.Н. разработка технологических процессов для карбонитрации крупногабаритных деталей. сборник научных трудов: «Металловедение. термическая и химико-термическая обработка сплавов». М.: МГту им. Н.Э. Баумана, 2003.
- Цих С.Г., Пласконь И.А., Гришин В.И., Лисицкий В.Н. разработка технологической линии жидкостной карбонитрации и процессов упрочнения запасных частей к основному оборудованию и инструменту. Материалы научно-технической конференции «обеспечение эффективного функционирования уренгойского нефтегазодобывающего комплекса», г. анапа,2003 г.- М.: ооо «ирЦ Газпром», 2004.
- Цих С.Г., Щеглов М.Е., Гришин В.И., Лисицкий В.Н., Мурадов А.В. исследование закономерностей комбинированного упрочнения структуры поверхностного слоя стали 25Х1МФ. НтЖ «Защита окружающей среды в нефтегазовом комплексе», 2002, №3, с. 14-17.
- Прокошкин Д.А., Супов А.В., Богомолов А.М., Кошенков В.Н. карбонитрация режущего инструмента в соляных ваннах. МитоМ. № 4, 1981.
- Г. Валь. Влияние режимов нитроцементации и последующего окисления на свойства деталей. МитоМ. № 7, 1991.
- Вес профильной трубы стальной таблица
- Отпуск и закалка стали
- Сталь прокатная
- Стальные водопроводные трубы
- Полосовая сталь
- Бруски из быстрорежущей стали
- Стали твердые
- Закалка и отпуск стали 65г
- Стальной профиль это
- Кобальтовая сталь
- Как отполировать часы из нержавеющей стали
ОПЫТ ПРИМЕНЕНИЯ КАРБОНИТРАЦИИ СТАЛЬНЫХ ДЕТАЛЕЙ И ИНСТРУМЕНТА В МАШИНОСТРОЕНИИ. Карбонитрация стали
Карбонитрация деталей в Москве
Компания Термохим предлагает услуги по карбонитрации деталей в Москве — в нашем Инновационном центре упрочнения.
Карбонитрация сталей и чугуна
Сущность метода карбонитрации заключается в том, что детали машин и инструменты, изготовленные из любых марок стали и чугуна, подвергают нагреву в расплаве солей, синтезированных из аммоноуглеродных соединений (меламин, мелон, дициандиамид), при температуре 540-600oС с выдержками 5-40 мин для режущего инструмента и 1-4 часа для деталей машин и штампового инструмента в зависимости от требуемой толщины упрочненного слоя. Технология используется для повышения износостойкости, усталостной прочности и – в сочетании с оксидированием – для увеличения коррозионной стойкости. Во многих случаях карбонитрация является альтернативой таких процессов, как поверхностная закалка, гальваническое хромирование, цементация и нитроцементация и др.
После карбонитрации на поверхности сталей формируется упрочненный слой, состоящий из нескольких зон. Верхний слой ε– карбонитрид типа Fe3(N,C). Под карбонитридным слоем располагается зона γ’ – фазы типа Fe4(N,C) , под которой находится диффузионная зона (гетерофазный слой). Она состоит из твердого раствора углерода и азота в железе с включениями карбонитридных фаз, твердость которой значительно выше твердости сердцевины. Концентрация азота и углерода при этом существенно снижается.
![]() Технологическая схема процесса оксикарбонитрации | ![]() Структура стали 40Х после карбонитрации |
Применение карбонитрации для обработки деталей повышает усталостную прочность на 50-80%, резко увеличивает износостойкость по сравнению с цементацией, нитроцементацией, газовым азотированием, обеспечивает минимальные величины деформаций в пределах допуска чертежа. Технология применима для упрочнения деталей из любых марок сталей и чугуна обеспечивает микронную точность (см. Таблицу характеристик упрочненного слоя и твердости сердцевины после карбонитрации). Среди технологий низкотемпературного упрочнения карбонитрация в расплавах солей является наиболее экономичным процессом, т.к. сокращает длительность насыщения до 0,5-6 ч, вместо 10-60 ч при газовом азотировании. При этом практически отсутствует хрупкость карбонитрированного слоя. Процесс карбонитрации, как правило, является окончательной операцией.
Свойства карбонитрированного слоя:
![]() Изменение коэффициента трения стали 12Х18Н10Т в зависимости от удельного давления при контактном трении | ![]() Коррозионные испытания штоков автомобильных амортизаторов из стали 40Х с различными видами покрытий |
![]() Зависимость износа стали 18ХГТ от пути трения со смазкой | ![]() Изменение износостойкости по толщине карбонитрированного слоя чугуна ВЧ50 |
![]() Распределении твердости по толщине карбонитрированного слоя сталей и чугуна (580oС 3 ч | ![]() Изменение коэффициента трения по толщине карбонитрированного слоя чугуна ВЧ50 |
![]() Структура и фазовый состав стали 25Х2М1Ф после оксикарбонитрации | ![]() Коэффициент трения различных видов покрытий на стали типа 40Х |
![]() Сравнительные характеристики износостойкости цементированной и карбонитрированной стали 18ХГТ | ![]() |
Технология НОК-PQ
Для придания коррозионных свойств деталям рекомендуется проводить процесс оксидирования в нитритно — щелочном расплаве при температуре 350-400oС или водном растворе при 130-150oС.В результате карбонитрации шероховатость поверхности в среднем ухудшается на 1-1,5 класса, поэтому после оксидирования для восстановления шероховатости поверхности можно использовать различные методы полирования:
При проведении процессов шлифования или полирования возможна потеря коррозионных свойств деталей, поэтому рекомендуется повторное оксидирование.Применение операции оксидирования после карбонитрации приводит практически к полному уничтожению цианидов, находящихся на поверхности.

Технологическая схема НОК-PQ — процесса
Технология карбонитрации в сочетании с оксидированием, полированием и повторным оксидированием, получившая название НОК-PQ (в Германии Tenifer – QPQ) придает деталям машин и инструменту несравнимо более высокие эксплуатационные характеристики.
![]() Свойства оксикарбонитридного слоя | ![]() Поверхностная шероховатость образцов из стали 45 после карбонитрации (580°С 2 ч) с последующей обработкой по различным вариантам |
Она может быть использована взамен гальванического хромирования, например, на деталях гидросистем, запорно- регулирующей арматуры, штампового инструмента и др.
См. Результат теста на коррозионную устойчивость стали С45 (испытательная среда: 3% NaCL;0,1 % h3O2)
См. Примеры применения оксикарбонитрации в арматуростроении, при изготовлении штамповой оснастки и прессформ, в автомобилестроении>>
Стоимость обработки договорная и определяется исходя из сложности, размеров,веса и количества деталей. Для того, чтобы узнать цену карбонитрации, необходимо отправить запрос (с четрежом детали) по одному из адресов, указанном на странице КОНТАКТЫ.
www.termohim.com
Основные виды химико-термической обработки – цементация, азотирование, карбонитрация
Химико-термическая обработка – это комплекс операций по изменению химического состава и микроструктуры поверхности заготовки или изделия с целью получения требуемых характеристик. Такое изменение является результатом взаимодействия поверхности с окружающей средой определенного состояния, состава, температуры. Наиболее распространенные виды химической обработки – цементация (науглероживание), азотирование, карбонитрация (одновременное насыщение углеродом и азотом).
Технология цементации стали
Этот процесс подразумевает диффузионное насыщение поверхностного слоя стальных заготовок углеродом. Обработка осуществляется в карбюризаторе, выделяющем активный углерод, при температурах устойчивости аустенита – 850-950°C, хорошо растворяющего большое количество углерода. Для завершения процесса после цементации проводят закалку и низкий отпуск. Результаты химико-термической и термической обработок в комплексе:
Внимание! Желаемый эффект достигается на сталях с низким содержанием углерода – до 0,2%. Без цементации такие марки закалить невозможно. Чаще всего цементации подвергают легированные стали.
Эта операция является длительной, поскольку процесс науглероживания протекает очень медленно. Основные типы сред для цементации (карбюризаторов):
Цементация в твердой среде: возможность проведения в домашних условиях
Науглероживание стали в твердой среде можно провести в домашних условиях, если есть способ обеспечить длительную выдержку при таких высоких температурах.
Для обработки в твердом карбюризаторе понадобятся:
Все компоненты измельчают и просеивают для удаления пыли. Оптимальные фракции – 3-10 мм. Методики смешивания компонентов:
Внимание! Если перемешивание было недостаточно тщательным, то после завершения процесса на детали образуются пятна.
Цементацию на производстве и в домашней мастерской осуществляют в стальных ящиках, заполненных карбюризатором. Для уменьшения времени прогрева и повышения качества поверхностного слоя ящик для ХТО по форме и размерам должен быть максимально приближенным к обрабатываемой детали. Создать оптимальные условия можно только в герметичной таре, поскольку при этом исключается утечка газов, образующихся во время выдержки. Для обеспечения герметичности зазоры между ящиком и крышкой обмазывают огнеупорной глиной. Оптимальный материал ящиков для науглероживания – жаростойкая легированная сталь. Однако может использоваться и тара из малоуглеродистых сталей.
Этапы цементации в твердом карбюризаторе
Азотирование: суть процесса и преимущества, по сравнению с цементацией
Азотирование – сравнительно новая технология улучшения характеристик стальных заготовок. Заключается в нагреве деталей до высоких температур в средах, насыщенных аммиаком. Толщина нитридного слоя составляет 0,3-0,6 мм.
Результаты азотирования:
Преимущества такой ХТО, по сравнению с цементацией
Краткая схема азотирования при температурах 500-600°C в стальных ретортах, устанавливаемых в печь:
Таблица результатов азотирования для стали различных марок, в зависимости от целевого назначения ХТО
Марка стали | Изготавливаемые детали | Цель азотирования | Толщина слоя, мм | Твердость по ТУ, HV (по Виккерсу) |
38Х2МЮА | Ручки, валы, кулачки, эксплуатируемые при нормальных температурах | Рост износостойкости и усталостной прочности | 0,2-0,5 | 500-900 |
18Х2Н4ВА | Шестерни, вал-шестерни, валы | Рост износостойкости и усталостной прочности | 0,2-0,3 | 500-650 |
25Х2МФ, 20Х1М1Ф1ТР | Штоки, клапаны, втулки, крепеж | Увеличение износостойкости при Т до 500°C | 0,2-0,5 | 500-800 |
35ХМА | Штоки, клапаны, втулки, крепежные элементы, буксы | Увеличение износостойкости при Т до 400-450°C | 0,2-0,4 | 450-600 |
20Х3МВФ | Штоки, клапаны, втулки, крепежные элементы, буксы | Увеличение износостойкости при Т до 500-535°C | 0,15-0,2 | 500-800 |
25Х2М1Ф | Штоки, клапаны, втулки, крепежные элементы, буксы | Увеличение износостойкости при Т до 535°C | 0,2-0,4 | 500-700 |
1Х13 | Лопатки сопловых аппаратов | Улучшение эрозионной устойчивости в среде пара | 0,1-0,2 | 450-700 |
15Х11МФ15Х12ВМФ | Штоки, буксы, лопатки сопловых аппаратов, клапаны, втулки | Улучшение эрозионной устойчивости и износостойкости при Т 535-565°C | 0,1-0,20,1-0,2 | 450-800450-700 |
40Х | Крепеж | Повышение коррозионной устойчивости | 0,15-0,2 | 400-500 |
50ХФА60С2 | Винтовые пружины | Улучшение коррозионной стойкости во влажной и паровой средах | 0,1-0,20,1-0,2 | 550-750400-600 |
Карбонитрация стали
Популярным видом ХТО стали и чугуна практически любых марок является карбонитрация, или жидкостное азотирование. В этом случае поверхностный слой заготовок насыщается углеродом и азотом в соляных расплавах при температуре 560-580°C. Соляные составы синтезированы из аммоноуглеродных соединений: меламина, мелона, дициандиамида. Карбонитрация сходна с цианированием. Но цианирование осуществляется с использованием токсичного цианида натрия при температурах до 860°C. Для карбонитрации применяют неядовитые соединения, осуществляется она при температурах до 570°.
Преимущества технологии карбонитрации стали
Комбинированное насыщение поверхности азотом и углеродом может применяться даже для высоколегированных и устойчивых к коррозии сталей. На их поверхности присутствует плотная пленка из оксидов хрома и других легирующих добавок, препятствующая процессу чистого азотирования.
Этапы карбонитрации
Дополнительным плюсом этой технологии является возможность частичного погружения детали в солевой расплав, что позволяет упрочнить только отдельные участки.
Последовательность
Таким способом обрабатывают:
Важный плюс этой технологии – соответствие экологическим нормам и безопасность работников, благодаря отсутствию ядовитых соединений в насыщающих средах. Карбонитрация применяется как на крупных промышленных предприятиях, так и в небольших мастерских и в домашних условиях.
Совершенствование комплексного азото-углеродного насыщения – низкотемпературная карбонитрация
НОК-процесс – низкотемпературное оксикарбонитрирование – впервые был разработан российскими учеными, а затем дорабатывался немецкими исследователями и получил название QPQ. Преимущества:
Этапы НОК-процесса:
Данная технология рассматривается в качестве эффективной и экономичной альтернативы гальваническому хромированию для низколегированных сталей перлитного класса и хромистых коррозионностойких.
www.navigator-beton.ru
ВКМ-АРМАТУРА® » Карбонитрация при производстве трубопроводной арматуры. Статья
С.Г. Цих, В.И. Гришин, В.Н. Лисицкий, Ю.А. Глебова, ОАО НПО «ЦНИИТМАШ», МГТУ им. Н.Э. Баумана, г. Москва
На машиностроительных предприятиях России, производящих паровые турбины и запорную арматуру для тепловых и атомных станций, для повышения надежности и долговечности деталей широко используется низкотемпературная технология их поверхностного упрочнения – газовое азотирование. Для большинства деталей применение технологии азотирования имеет целью повышение поверхностной твердости, износостойкости и коррозионной стойкости в паровой, воздушной и масляных средах.
Азотированию подвергаются несколько сотен наименований деталей паровых турбин. Это детали многочисленных узлов регулирования и парораспределения, различного назначения клапаны, втулки, буксы, золотники; штоки, шпиндели, тарелки и другие детали запорной арматуры, к которым предъявляются требования обеспечения хорошей плотности и отсутствия утечек воды или пара. Для этого посадочные места должны иметь высокую твердость и длительно сохранять свои первоначальные размеры до температуры 540 °С. Азотирование применяется и для упрочнения резьбовых соединений с целью предотвращения заедания при высокой температуре, а также как антикоррозионная защита углеродистых сталей. Примеры применения азотирования в турбостроении приведены в таблице
Марка стали | Назначение стали | Цель азотирования | Толщина слоя, мм | Твердость по ТУ, HV |
1 | 2 | 3 | 4 | 5 |
38х2МЮА | втулки, валики, кулачки и др. детали, работающие при нормальной температуре | Повышение износостойкости и усталостной прочности | 0,20-0,50 | 500-900 |
18х2Н4вА | Шестерни, вал-шестерни, валы, шлицевые валы и др | Повышение износостойкости и усталостной прочности | 0,20-0,30 | 500-650 |
25х2МФ (ЭИ 10) 20х1М1Ф1Тр (ЭП 182) | Штоки, втулки, клапаны, буксы, болты, гайки | Повышение износостойкости при температу- ре до 500 °с и для устранения схватывания | 0,20-0,50 | 500-800 |
35хМА | То же | То же, но для температуры 400-450 °с | 0,20-0,40 | 450-600 |
20х3МвФ (ЭИ 415) | То же | То же, но для температуры 500-535 °с | 0,15-0,20 | 500-800 |
25х2М1Ф (ЭИ 723) | То же | То же, но для температуры до 535 °с | 0,20-0,40 | 500-700 |
1х13 | лопатки сопловых аппаратов | для увеличения эрозионной стойкости в паровой среде | 0,10-0,20 | 450-700 |
15х11МФ 15х12вМФ | лопатки сопловых аппаратов, штоки, буксы, втулки, клапаны | для увеличения эрозионной стойкости, износостойкости и устранения схватывания при температуре 535-565 °с | 0,10-0,20 0,10-0,20 | 450-800 450-700 |
40х | Болты, шпильки, гайки, валики | для устранения схватывания и повышения коррозионной стойкости | 0,15-0,20 | 400-500 |
50хФА 60с2 | винтовые пружины и др. детали | для повышения коррозионной стойкости в паровой и влажной среде | 0,10-0,20 0,10-0,20 | 550-750 400-600 |
Углеродистые стали 20, 30, 35, 40, 45 | серьги, поршни, скобы, колесо импеллера, рабочие колеса насосов и др. детали | для повышения коррозионной стойкости в паровой, влажной и масляной среде | до 0,65 | Контролю твердости не подвергаются |
Существенным недостатком технологии газового азотирования является большая длительность технологического цикла, достигающая нескольких десятков часов, и повышенная хрупкость азотированного слоя.
Среди процессов, направленных на интенсификацию скорости насыщения сталей азотом, особое место занимает технология азотирования в жидких средах, при которой происходит преимущественное насыщение сталей азотом и углеродом. Жидкостное азотирование в расплавах солей обеспечивает высокую скорость нагрева, уменьшает термические напряжения и коробление изделий, позволяет регулировать в широких пределах скорость охлаждения после насыщения и т.п.
История низкотемпературного процесса жидкостного азотирования берет начало с 30-х годов прошлого столетия, когда Д.А. Прокошкин [1,2] сообщил о технических возможностях жидкостного цианирования, его простоте и высокой эффективности. Впервые было отмечено, что поверхностное упрочнение при низкотемпературном процессе связано не с формированием мартенситных структур, как в случае высокотемпературного цианирования, а с образованием нитридов и карбонитридов, и сам процесс протекает в условиях, исключающих превращение, как это имеет место при других видах поверхностного упрочнения (цементация, нитроцементация, высокотемпературное цианирование, поверхностная закалка). Поэтому локальные разогревы в месте контакта при трении, контактном нагружении не приводят к местному разупрочнению азотированных и карбонитрированных слоев, чего нельзя избежать в случае мартенситных структур, получаемых при закалке. Это объясняет и предельно малые величины деформации и коробления деталей при низкотемпературном насыщении деталей азотом (газовое азотирование) и азотом и углеродом (жидкостное азотирование, карбонитрация).
Широкое освоение технологии низкотемпературного цианирования сдерживалось использованием в составе расплава высокотоксичных цианидов. В 50-х годах ХХ в. фирма «Дегусса» (Германия) предложила состав ванны, содержащий наряду с цианидами 50% цианатов щелочных металлов и тем самым положила начало знаменитому «Тенифер»-процессу – «мягкому азотированию». По сравнению с цианированием «ядовитость» процесса сократилась вдвое, и он был внедрен на более чем 1000 машиностроительных предприятиях многих стран.
Учитывая высокую эффективность технологии жидкостного азотирования в плане существенного повышения эксплуатационных свойств деталей, технологичность, экономичность и простоту процесса, в дальнейшем развитие технологии было направлено на поиск состава расплава на неядовитой основе.
В результате исследования химизма процесса низкотемпературного цианирования было установлено, что реакции в расплаве идут путем окисления:
2 KCN + O2 = 2 KCNO
2 KCNO + O2 = K2CO3 + 2 N + CO
2 CO = CO2 + C
c выделением атомов азота и углерода в результате окисления цианата. Не сам цианид калия (KCN), а продукт его окисления – цианат калия (KCNO) – является поставщиком активных атомов азота и углерода в рабочем расплаве. В отличие от цианида цианат калия – вещество неядовитое, пожаро- и взрывобезопасное, хорошо растворимое в воде. Именно цианаты представляют интерес и являются наиболее подходящими веществами для осуществления жидкостных процессов химико-термической обработки.
Задача, связанная с разработкой технологически приемлемой жидкой среды для низкотемпературного упрочнения металлических изделий, в середине 70-х годов была решена в МГТУ им. Н.Э. Баумана проф. Прокошки- ным Д.А. [3]. Им предложена и получила промышленное внедрение экологически безвредная технология, которую автор назвал «карбонитрация». Расплав на основе цианата калия (KCNO – 75-85%) и поташа (K2CO3 – 15-25%) обладает высокой химической активностью, хорошей технологичностью, имеет низкую температуру плавления и при рабочих температурах процесса 550-580 °С характеризуется высокой жидкотекучестью.
Среди технологий низкотемпературного упрочнения карбонитрация в расплавах солей является наиболее экономичным процессом, т.к. сокращает длительность выдержки до 0,5-6 ч, вместо 10-60 ч при газовом азотировании. При этом практически отсутствует хрупкость карбонитрированного слоя, характерная для длительных процессов газового азотирования.
Впоследствии, на основе собственных разработок, подобные технологии появились в Германии (новый Тенифер-процесс TF 1), в США («Мелонайт»), в Японии («Мягкое азотирование»), во Франции («Сюрсульф») и др., где заложен тот главный принцип, который впервые был реализован в методе карбонитрации.
Сущность метода карбонитрации заключается в том, что детали машин из конструкционных, нержавеющих, теплостойких инструментальных и быстрорежущих сталей подвергают нагреву в расплаве солей при 540-600 °С с выдержками 5-40 мин для режущего инструмента и 1-6 ч для деталей машин и штампового инструмента в зависимости от требуемой толщины упрочненного слоя. Процесс карбонитрации прост в осуществлении, не требует сложного оборудования. Стоимость обработки в зависимости от размера деталей и компоновки садки не превышает 2-8% стоимости детали.
Применение карбонитрации для обработки деталей повышает усталостную прочность на 50-80%, резко увеличивает износостойкость по сравнению с цементацией, нитроцементацией, газовым азотированием, обеспечивает минимальные величины деформаций и микронную точность деталей. Технология применима для упрочнения деталей из любых марок сталей и чугуна. Процесс карбонитрации позволяет обеспечить: высокую скорость нагрева, равномерность температуры в объеме ванны, в широких пределах регулировать скорость охлаждения и, как правило, является окончательной операцией технологического цикла изготовления деталей. Карбонитрация деталей, изготавливаемых из конструкционных сталей, обеспечивает получение высоких значений поверхностной твердости и сопротивления износу и может применяться без последующей механической обработки.
Рис.1. Структура стали 09Г2С после карбонитрации, 570 °C, 2 ч
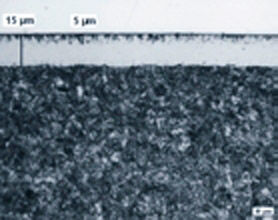
После карбонитрации углеродистых и низколегированных сталей перлитного класса на поверхности деталей образуется упрочненный слой, состоящий из двух зон (рис. 1). Верхняя зона толщиной до 15 мкм по данным рентгеноструктурного анализа представляет собой карбонитрид типа Fe (N,C) или оксикарбонитрид типа 3 Fe (N,C,О) в зависимости от состава стали. Под карбонитридным слоем располагается диффузионная зона (гетерофазный слой), состоящая из твердого раствора углерода и азота в железе с включениями карбонитридных фаз, твердость которой значительно выше твердости сердцевины и плавно снижается от поверхности к основе. В таблице ниже приведены характеристики карбонитрированного слоя. С увеличением легирования конструкционных сталей существенно возрастает поверхностная твёрдость, толщина упрочненного слоя при этом уменьшается.
Марка стали | Твердость, Н100 | Общая толщина слоя, мкм | Толщина карбонитридного слоя, мкм | |||||||
сердцевина | поверхность | Время карбонитрации, ч | Время карбонитрации, ч | |||||||
1 | 2 | 4 | 6 | 1 | 2 | 4 | 6 | |||
20 | 170 | 400-500 | 220 | 300 | - | - | 5 | 9 | 14 | - |
45 | 190 | 400-500 | 190 | 250 | - | - | 5 | 8 | 13 | - |
60 | 210 | 500-600 | 170 | 220 | - | - | 3 | 6 | 10 | - |
У8 | 220 | 600-700 | - | - | - | - | 2 | 5 | 8 | - |
У10 | 240 | 700-750 | - | - | - | - | - | - | - | - |
40Х | 220 | 550-700 | 190 | 270 | 380 | 460 | 10 | 14 | 20 | 25 |
30ХГСА | 220 | 700-900 | 180 | 260 | 360 | 450 | 9 | 13 | 17 | 20 |
40Х1НВА | 260 | 700-900 | 160 | 240 | 340 | 410 | 8 | 12 | 15 | 18 |
38Х2МЮА | 280 | 800-1200 | 150 | 220 | 320 | 360 | 8 | 12 | 15 | 18 |
18ХГТ | 200 | 700-800 | 180 | 260 | 360 | 440 | 12 | 15 | 19 | 22 |
18Х2Н4ВА | 250 | 700-900 | 160 | 220 | 310 | 390 | 9 | 13 | 16 | 19 |
На рис. 2 и 3 представлены результаты исследования распределения микротвердости по толщине слоя различных конструкционных сталей. С увеличением содержания в сталях нитридо- и карбидообразующих элементов (Cr, Mo, V) общий уровень твердости слоя повышается. Это связано с образованием мелкодисперсных карбонитридов легирующих элементов, плотность распределения которых в твердом растворе углерода и азота в железе уменьшается от поверхности к сердцевине.
Рис. 2. Распределение твердости по толщине слоя сталей 10 (1), 20 (2), 09Г2С (3) после карбонитрации по режимам: 1 – 590 °С, 3 ч, 2 – 570 °С, 2,25 ч, 3 – 570 ° С, 3 ч
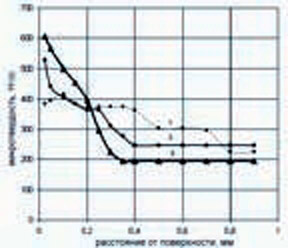
Рис. 3. Распределение твердости по толщине слоя сталей 40Х (1), 40ХН (2), 40ХМФА (3), 30ХГСА (4). Карбонитрация 570 °С, 5 ч
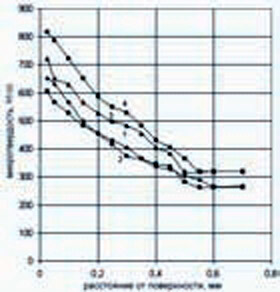
К материалам ряда деталей паровых и гидравлических турбин предъявляются требования высокой коррозионной стойкости в сочетании с износостойкостью.
Так, детали узлов регулирования паровых турбин, работающие при температуре до 565 °С, должны обладать достаточной сопротивляемостью коррозионному и эрозионному воздействию пара, а также удовлетворительной износостойкостью в условиях сухого трения при взаимном перемещении. Детали сервомоторов, работающие в среде конденсата при температуре 70-80 °С, должны иметь высокую коррозионную стойкость и удовлетворительную работоспособность в условиях сухого трения или водяной смазки. Для поверхностного упрочнения этих деталей на заводах применяется технология газового азотирования. Но, как показано ниже, азотированный слой обладает в два раза меньшей стойкостью к износу по сравнению с карбонитрированным.
Испытания карбонитрированного слоя на износостойкость показывают наличие трех стадий. Первая стадия связана с приработкой и износом пористой верхней части карбонитрированного слоя (рис. 1, верхняя часть слоя толщиной 5 мкм) и занимает небольшое место в износе. Вторая характеризуется исключительно низкой скоростью износа карбонитридной фазы. Слой изнашивается без выкрашивания и сколов, что свидетельствует о его высокой пластичности и вязкости. Третья фаза относится к износу гетерофазного слоя. Здесь в массе феррита присутствуют дисперсные карбиды и нитриды железа и легирующих элементов, и такая структура вообще характеризуется высоким сопротивлением износу.
Сравнительные испытания на износостойкость различных видов диффузионных покрытий показывают, например: скорость износа стали 20 после цементации более, чем в 20 раз выше, чем после карбонитрации (см. таблицу) (рис. 4).
Метод химико- термической обработки | Толщина упрочненного слоя, мкм | Условия испытаний | Скорость износа, мг/км пути трения | |
Нагрузка, Н | Скорость скольжения, м/с | |||
Цементация | 800 | 500 | 0,5 | 0,15/180 |
800 | 1000 | 1,5 | ||
Карбонитрация | ||||
Карбонитридный слой | 14 | 500 | 0,5 | 0,007/5,5 |
14 | 1000 | 1,5 | ||
Гетерофазный слой | 270 | 500 | 0,5 | 0,025/150 |
270 | 1000 | 1,5 | ||
Примечание. Указана скорость износа при трении со смазкой (числитель) и без смазки (знаменатель) |
Рис. 4. Зависимость износа стали 20 от пути трения со смазкой. 1 – карбонитрированный слой, 2 – гетерофазный слой, 3 – цементированный слой
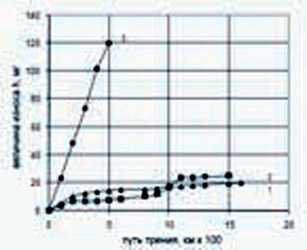
Рис. 5. Сравнительные испытания на свинчивание бурильных замков ЗЛ–152 с фосфатированием и карбонитрацией резьбы. 2 и 6 – фосфатирование, 3 и 5 – карбонитрация 570 °С, 2,5 ч (3) и 5 ч (5)
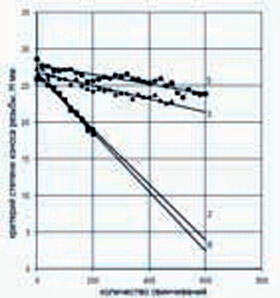
А в сравнении с фосфатированием, используемым в качестве противозадирного покрытия резьбовых соединений, карбонитрация резьбовых соединений из стали 40ХН в 4 раза снижает скорость износа резьбы (рис. 5).
Даже газовое азотирование, являющееся одним из близких аналогов процесса карбонитрации, показывает износостойкость более чем в 2 раза меньшую, чем при карбонитрации (рис. 6).
Рис. 6. Износостойкость рычага рулевого управления снегохода из стали 10 после карбонитрации (1) и серийного режима газового азотирования (2)
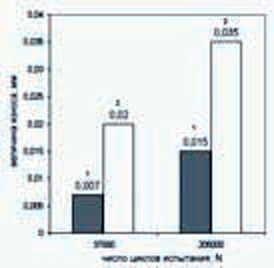
Рис. 7. Распределение твердости по толщине слоя нержавеющих сталей 20Х13 (1), 14Х17Н2 (2), 12Х18Н10Т (3). Карбонитрация 590 °С, 6 ч
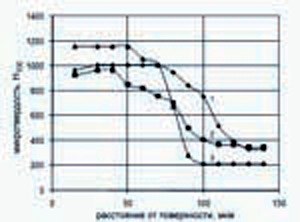
Надежность и долговечность деталей из нержавеющих хромистых и аустенитных сталей, работающих в различных условиях эксплуатации, зависят не только от свойств основного металла, но и от состояния сравнительно тонких поверхностных слоев. В энергомашиностроении для повышения поверхностной твердости, износостойкости, задиростойкости, эрозионной стойкости, усталостной прочности этого класса конструкционных сталей применяют газовое азотирование. Но этот процесс, во-первых, слишком длительный, во-вторых, наблюдается деформация и коробление деталей, в-третьих, – фаза, образующаяся на поверхности при насыщении нержавеющих сталей азотом, оказывается очень хрупкой и её приходится удалять операцией шлифования. Сам технологический процесс газового азотирования усложняется, так как приходится вводить в муфель депассиватор, устраняющий окисную пленку с поверхности нержавеющих сталей.
Процесс жидкостной карбонитрации нержавеющих сталей лишен указанных недостатков. Скорость насыщения в расплаве солей выше, чем в газовых средах, а одновременное насыщение азотом и углеродом позволяет получать на поверхности стальных изделий карбонитридный слой высокой твердости (рис. 7) и практически лишенный хрупкости, в отличие от чисто нитридного. В результате отпадает необходимость последующей механической обработки, и, кроме того, карбонитридный слой существенно повышает износостойкость и снижает коэффициент трения поверхностных слоев контактирующих деталей до 5 раз. Это подтверждают сравнительные исследования значений коэффициента трения стали 10Х18Н10Т после закалки, газового азотирования и карбонитрации (рис. 8).
Рис. 8. Изменение коэффициента трения стали 12Х18Н10Т в зависимости от удельного давления при контактном трении. 1 – закалка 1150 °С, 2 – азотирование 620 °С, 35 ч, 3 – карбонитрация 570 °С, 12 ч
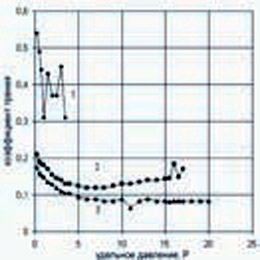
Рис. 9. Распределение твердости по толщине наплавленного слоя стали 25Х1МФ после карбонитрации 570 °С, 3 ч
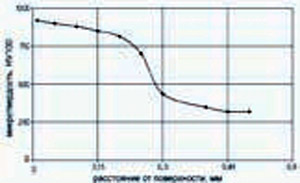
Необходимо отметить, что нами разработана технология ремонта шпинделей из стали 25Х1МФ, подвергнутых газовому азотированию. Технология включает в себя следующие операции:
В результате на поверхности формируется упрочненный слой с высокой твердостью, низким коэффициентом трения (рис. 9).
На ряде фирм карбонитрации подвергаются детали запорной арматуры общего назначения и на высокие параметры температуры и давления энергетического, газо- и нефтедобывающего оборудования (штоки, шпиндели, золотники, в том числе с зубчатым приводом, тарелки, шиберы, оси, втулки, специальной конструкции гайки с обычной и трапециидальной резьбой, пробки шаровых кранов и др.). Технология карбонитрации корпусов вентилей DN 10-50 из сталей 20, 09Г2С, 25Х1М1Ф, помимо существенного повышения эксплуатационных свойств, хорошо зарекомендовала себя и как способ антикоррозионной защиты, что позволило исключить операцию окраски. На рис. 10 представлены примеры деталей, подвергаемые карбонитрации.
Рис. 10.1. Корпус, шпиндель, грундбукса. Сталь 20, 35, 09Г2С, 25Х1М1Ф, 38Х2МЮА, 14Х17Н2.
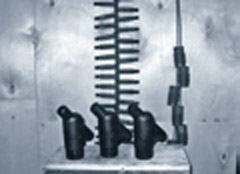
Рис. 10.2. Клапан. Сталь 25Х1М1ФТЮР (l = 1300 мм)
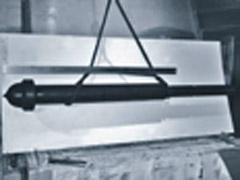
Рис. 10.3. Пробка. Сталь 08Х18Н10Т
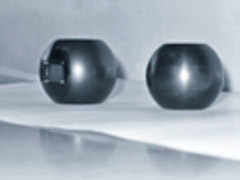
Рис. 10.4. Золотник, рейка, шпиндель. Сталь 14Х17Н2, 12Х1810Т
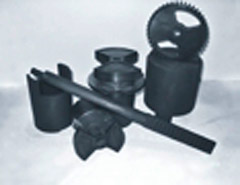
Рис. 10.5. Шпиндель. Сталь 25Х1М1Ф, 25Х2М1Ф (длина до 1500 мм)
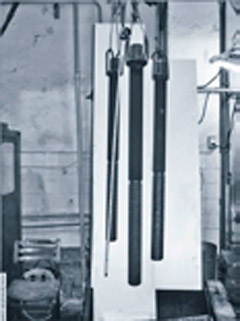
Рис. 11. Технологическая линия жидкостной карбонитрации
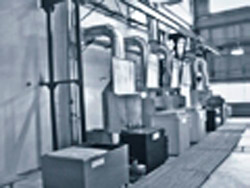
Для реализации технологии жидкостной карбонитрации разработано и изготавливается оборудование, составляющее технологическую линию жидкостной карбонитрации (ТЛЖК) и позволяющее проводить упрочнение деталей длиной до 1300 мм и диаметром до 600 мм. В состав ТЛЖК в промышленном варианте входят: печь подогрева деталей, печь-ванна карбонитрации, ванны промывки, обезжиривания, оксидирования, охлаждения, накопительная ёмкость для промстока и испаритель промстоков. На рис. 11 показана одна из таких линий [6,7].
В совершенствовании технологии жидкостной карбонитрации представляет интерес так называемый НОК-процесс (низкотемпературное оксикарбонитрирование), разработанный российскими исследователями [9]. Позже аналогичный процесс, предложенный фирмой «ДЕГУССА» (Германия), получил название TUFFTRYDE – QPQ. Эта технология, первоначально задуманная для улучшения товарного вида деталей, резко понижает коэффициент трения и, по данным немецких исследователей [10], существенно повышает коррозионную стойкость деталей из сталей перлитного и мартенситного классов. При испытании в солевом тумане, в растворе соли с перекисью водорода коррозионная стойкость деталей, обработанных по технологии QPQ, превосходит стойкость гальванического хромового покрытия.
Себестоимость обработки деталей по технологии QPQ на 40% меньше стоимости технологии нанесения гальванического покрытия.
НОК-процесс включает в себя следующую последовательность операций: карбонитрация → охлаждение и выдержка в нитритно-щелочном расплаве ванны оксидировния при 350-400 °С → охлаждение на воздухе → промывка → полировка → повторное оксидирование в расплаве → промывка.
Низкий коэффициент трения и высокая коррозионная стойкость сталей с оксикарбонитридным покрытием по технологии НОК после проверки эксплуатационных свойств дают основания рассматривать данную технологию в качестве процесса для поверхностного упрочнения деталей из низколегированных сталей перлитного класса и хромистых нержавеющих сталей и, в частности, как замена технологии гальванического хромирования, например, для пробок шаровых кранов из стали 09Г2С и ряда других изделий энергомашиностроения и других отраслей промышленности.
В заключение следует отметить, что технология жидкостной карбонитрации в настоящее время нами внедрена и широко используется при изготовлении различных деталей на таких предприятиях как: «Чеховский завод энергетического машиностроения», «Чеховский завод «Машиностроитель», «Корпорация Сплав» г. Великий Новгород, «Тяжпромарматура» г. Алексин, «Фирма Союз-01» г. Москва, «Севермаш» г. Рыбинск, «Уренгойгазпром», «Сургутнефтегаз», «Нефтегазгеофизика» г. Тверь, «Станкоагрегат» г. Москва, «Газмаш» г. Чайковский, г. Балакирево и др.
www.vkm-armatura.com.ua
Карбонитрация – Карбонитрирование стали в Екатеринбурге
Карбонитрация разработана советскими учеными в 70-х годах 20-го века, но не получила широкой известности, поэтому до настоящего времени конструкторы не добавляют ее в чертежи. Качество поверхности обрабатываемых деталей и их габариты не изменяются в процессе обработки, что делать карбонитрацию финишной операцией. Она выигрывает по трудозатратам в сравнении с цементацией и закалкой ТВЧ.
По своим свойствам упрочненный слой после карбонитрирования соответсвует азотированному, что позволяет применять газовую карбонитрацию для большого перечня номенклатуры. Так же эта технология может заменить такие виды упрочнения, как гальваническое хромирование, цементация, закалка токами высокой частоты ТВЧ
Анализ поверхностного слоя после карбонитрации и азотирования.
Сталь | 20 | 40 | 18ХГТ | 40Х | Х18Н10 | Р6М5 |
H50 | 490 | 520 | 800 | 950 | 1100 | 1400 |
H50 | 490 | 520 | 800 | 950 | 1100 | 1400 |
Как видно из таблицы, азотированный и карбонитрированный слои идентичны. Благодаря этому рекомендуется применение именно карбонитрации так как позволит сократить трудоемкость и итоговую стоимость упрочнения. А в сравнении с гальваническим хромированием возрастает коррозионная стойкость. Итоговая глубина упрочнения составляет 0,3 мм.
Примеры эффективного применения карбонитрации.
На ФГУП "Уралвагонзавод" производилась карбонитрация деталей занятых при изготовлении стреловых осей, рукоятей ковшей экскаваторов, опорных катков и втулок для дорожно-строительной техники. Результат: повышение износостойкости до 2-х раз, с повышением производительности до 40%.
Срок эксплуатации шестерней (наружный модуль зуба 5) в приводах вращения магнитных сепараторов модели ПБМ120/300 благодаря карбонитрации вырос с 3-х месяцев до 4-х лет.
С помощью карбонитрации достигнуто значительное увеличение срока службы втулок разъема опок линии формовки (изготовленных из стали 40Х), с 3-х до 21-го дня.
На предприятии ОАО "Салдинский металлургический завод" удалось сэкономить более 0,5 миллиона рублей за счет смены объемной закалки на карбонитрирование комплекта направляющих протяжного станка.
На колесопрокатном стане во время ремонта вместо объемной закалки применили карбонитрацию стали для пальцев тяг, результатом стало двукратное увеличение срока их наработки.
На порядок повышен срок наработки клапанов гидропресса на ОАО "Нижнетагильский металлургический комбинат" за счет карбонитрации. Ранее клапана служили примерно 2 месяца, а в текущий момент эксплуатируются уже более 2-х лет и остаются в работе.
Передвижной буровой станок модель СБШ-250 на предприятии ОАО "Качканарский горнообогатительный комбинат". Во время обслуживания редуктора произвели карбонитрацию ведущих валшестерней, что снизило в 10 раз их расход.
Фотографии деталей после карбонитрации


1m63.ru
ОПЫТ ПРИМЕНЕНИЯ КАРБОНИТРАЦИИ СТАЛЬНЫХ ДЕТАЛЕЙ И ИНСТРУМЕНТА В МАШИНОСТРОЕНИИ
Транскрипт
1 Саблев Л.П., Шулаев В.М., Григорьев С.Н. Харьков: ННЦ «ХФТИ», с. 5. Хороших В.М. Капельная фаза эрозии катода стационарной вакуумной дуги// Физическ ая инжен ерия повер хности Т С Аксенов А.И. Вакуумн ая дуга в эрозионных и сточниках плазмы. Харьков: ННЦ «ХФТИ», с. 7. Аксёнов И.И., Падалка В.Г., Хороших В.М. Формирование потоков металлической плазмы: Обзор. М.: ЦНИИатоминформ, с. 8. Сайт фирмы PLATIT: [http://www.platit.com], Локтев Д. А. Наноструктурные покрытия высокопроизводительного инструмента // Стружка (7). С Исследование капельной фазы эрозии катода стационарной вакуумной дуги / Аксенов И.И., Коновалов И.И., Кудрявцева Е.Е. и др. // ЖТ Ф Т С Марахтанов М.К., Марахтанов А.М. Эффект тер моэлектронного вентиля и ритм катодного кратера в низковольтной вакуумной дуге с холодным катодом // Письма в ЖТФ Т. 24. В Структура и особенности движения катодного пятна вакуумной дуги на протяженном титановом катоде / Духопельников Д.В., Жуков А.В., Кириллов Д.В., Марахтанов М.К. // Измерительная техника C Sablev L.P., Shulaev V.M., Grigoriev S.N. Khapkov: NNC CPTI, P Khoroshikh V.M. Drop phase of the cathode erosion of the stationary vacuum arc // Physical engineering of the surface V P Aksenov A.I. Vaccum arc in the erosion sources of plasma. Kharkov: NNC CPTI, P Aksenov I.I., Padalka V.G., Khoroshikh V.M. The formation of metal plasma stream: Review. M.: Central Research Institute atominform, P Site of the firm PLATIT: [http://www/platit.com], Loktev D.A. Nanostructural coatings of the highly-productive instrument // Chipping (7). P Drop phase research of the cathode erosion of the stationary vacuum arc / Aksenov I.I., Konovalov I.I., Kudryavtseva E.E. and others // ZTF V P Marakhtanov M.K., Marakhtanov A.M. The effect of thermoelectronic valve and the rhythm of the cathode crater in the low voltage vacuum arc with a cold cathode // Letters to ZTF V. 24. V Structure and peculiarities of the cathode spot movement of the vacuum arc at the extensive titanic cathode / Dukhopelnik D.B., Zhukov A.V., Kirillov D.B., Marakhtanov M.K. // Instrumentation technology P УДК ОПЫТ ПРИМЕНЕНИЯ КАРБОНИТРАЦИИ СТАЛЬНЫХ ДЕТАЛЕЙ И ИНСТРУМЕНТА В МАШИНОСТРОЕНИИ Карбонитрация высокоэффективная технология поверхностного упрочнения деталей машин, штамповой и прессовой оснастки различного назначения, режущего инструмента. Ее применение взамен газового азотирования позволяет многократно сократить длительность цикла обработки и повысить эксплуатационные свойства упрочняемых деталей. История низкотемпературного процесса жидкостного азотирования берет начало с 30-х годов прошлого столетия, когда Д.А. Прокошкин [1,2] сообщил о технических возможностях жидкостного цианирования, его простоте и высокой эффективности. Впервые было отмечено, что поверхностное упрочнение при низкотемпературном процессе связано не с формированием мартенситных структур, как в случае высокотемпературного цианирования, а с образованием нитридов и карбонитридов, и сам процесс протекает в условиях, исключающих α γ превращение, как это имеет место при других видах поверхностного упрочнения (цементация, нитроцементация, высокотемпературное цианирование, поверхностная закалка). Поэтому локальные разогревы в месте контакта при трении, контактном нагружении не приводят к местному разупрочнению азотированных и карбонитрированных слоев, чего нельзя избежать в случае мартенситных структур, получаемых при закалке. Это объясняет и предельно малые величины деформации и коробления деталей при низкотемпературном насыщении деталей азотом (газовое азотирование) и азотом и углеродом (жидкостное азотирование, карбонитрация). Широкое освоение технологии низкотемпературного цианирования сдерживалось использованием в составе расплава высокотоксичных цианидов. В 50-х годах ХХ в. фирма «Дегусса» (ФРГ) внесла коррективы и предложила состав ванны, содержащий наряду с цианидами 50% цианатов щелочных металлов, и тем самым положила начало знаменитому «Тенифер» процессу «мягкому азотированию». По сравнению с цианированием «ядовитость» процесса сократилась вдвое и он был принят на более чем 1000 машиностроительных предприятиях многих западных стран и Японии. Учитывая высокую эффективность технологии жидкостного азотирования в плане существенного повышения эксплуатационных свойств деталей, технологичность, экономичность и простоту процесса, в дальнейшем развитие технологии было направлено на поиск состава расплава на неядовитой основе. В результате исследования химизма процесса низкотемпературного цианирования было установлено, что реакции в расплаве идут путем окисления: 2 KCN + O 2 = 2 KCNO (1) 2 KCNO + O 2 = K 2 CO N + CO (2) 2 CO = CO 2 + C (3) c выделением атомов азота и углерода в результате окисления цианата. Не сам цианид калия (KCN), а продукт его окисления цианат калия (KCNO) является поставщиком активных атомов азота и углеро- 32

2 Опыт применения карбонитрации стальных деталей и инструмента да в рабочем расплаве. В отличие от цианида цианат калия вещество неядовитое, пожаро- и взрывобезопасное, хорошо растворимое в воде, Именно цианаты представляют интерес и являются наиболее подходящими веществами для осуществления жидкостных процессов химико-термической обработки. Задача, связанная с разработкой технологически приемлемой жидкой средой для низкотемпературного упрочнения металлических изделий, в середине 70-х годов была решена в МГТУ им. Н.Э. Баумана проф. Прокошкиным Д.А. [3]. Им была предложена и получила промышленное внедрение экологически безвредная технология, которую автор назвал «карбонитрация». Расплав на основе цианата калия (KCNO 75 85%) и поташа (K 2 CO %) обладает высокой химической активностью, хорошей технологичностью, имеет низкую температуру плавления и при рабочих температурах процесса С характеризуется высокой жидкотекучестью. Впоследствии, на основе собственных разработок, появились подобные технологии в ФРГ (новый Тениферпроцесс TF 1), в США («Мелонайт»), в Японии («Мягкое азотирование»), во Франции («Сюрсульф») и др., где заложен тот главный принцип, который впервые был реализован в отечественном способе карбонитрации. Сущность метода карбонитрации заключается в том, что детали машин из конструкционных, нержавеющих, теплостойких инструментальных и быстрорежущих сталей подвергают нагреву в расплаве солей при С с выдержками 5 40 мин для режущего инструмента, а штампового инструмента и деталей машин 1 6 ч в зависимости от требуемой толщины упрочненного слоя. Процесс карбонитрации прост в осуществлении, не требует сложного оборудования. Стоимость обработки в зависимости от размера деталей и компоновки садки не превышает 2 8% стоимости детали. Применение карбонитрации для обработки деталей повышает усталостную прочность на 50 80%, резко увеличивает износостойкость по сравнению с цементацией, нитроцементацией, газовым азотированием, обеспечивает минимальные величины деформаций в пределах допуска чертежа. Технология применима для упрочнения деталей из любых марок сталей и чугуна, обеспечивает микронную точность деталей. Среди технологий низкотемпературного упрочнения карбонитрация в расплавах солей является наиболее экономичным процессом, т.к. сокращает длительность выдержки до 0,5 6 ч, вместо ч при газовом азотировании. При этом практически отсутствует хрупкость карбонитрированного слоя, характерная для длительных процессов газового азотирования. Процесс карбонитрации позволяет обеспечить высокую скорость нагрева, равномерность температуры в объеме ванны, в широких пределах регулировать скорость охлаждения и, как правило, является окончательной операцией технологического цикла изготовления деталей. Карбонитрация углеродистых и низколегированных сталей перлитного класса После карбонитрации углеродистых и низколегированных сталей на поверхности деталей образуется диффузионный слой, состоящий из двух зон (рис. 1). Верхняя зона толщиной до 15 мкм по данным рентгеноструктурного анализа представляет собой карбонитрид типа Fe 3 (N,C) или оксикарбонитрид типа Fe 3 (N,C,О) в зависимости от состава стали. Под карбонитридным слоем располагается гетерофазный слой, твердость которого значительно выше твердости сердцевины и плавно снижается от поверхности к основе. В табл. 1 приведены характеристики карбонитрированного слоя некоторых сталей. Карбонитрация деталей, изготавливаемых из конструкционных сталей, обеспечивает высокие поверхностную твердость и сопротивление износу и может применяться без последующей механической обработки. Причем технология карбонитрации удобнее и экономичнее других методов химико-термической обработки. Это определяется особенностями технологии метода обработки и свойствами, приобретаемыми деталями в процессе насыщения совместно азотом и углеродом. Испытание карбонитрированного слоя на износостойкость показывают наличие трех стадий. Первая стадия связана с приработкой и износом пористой верхней части карбонитрированного слоя (см. рис. 1) и занимает небольшое место в износе. Вторая характеризуется исключительно низкой скоростью износа карбонитридной фазы. Слой изнашивается без выкрашивания и сколов, что свидетельствует о его высокой пластичности и вязкости. Третья фаза относится к износу гетерофазного слоя. Здесь в массе феррита присутствуют дисперсные карбиды и нитриды железа и легирующих элементов, такая структура вообще характеризуется высоким сопротивлением износу. Приведенные в табл. 2 данные износа стали 20 после цементации и карбонитрации показывает [3], что гетерофазный слой по сопротивлению износу оказывается близким к карбонитридному слою. Суммарная стойкость карбонитридного и гетерофазного слоев оказалась исключительно высокой и намного превосходит цементованный слой. В условиях трения со смазкой скорость износа карбонитридного слоя в 20 раз меньше, чем цементованного, а при отсутствии смазки в 30 с лишним раз меньше. Износ гетерофазного слоя после карбонитрации в условиях смазки идет втрое быстрее, чем карбонитридного, но в 5 раз медленнее цементованного слоя. Рис. 1. Структура стали 09Г2С после карбонитрации, t=570 C, τ=2 ч Вестни к МГТУ им. Г. И. Носова
3 Гетерофазный слой имеет дисперсную структуру с малым коэффициентом трения и в условиях трения со смазкой имеет существенные преимущества перед цементованным. Наружный слой, состоящий из карбонитридной фазы, обладает исключительно высоким сопротивлением износу и намного превосходит цементованный слой. В подтверждение сказанного ниже приводятся данные по износостойкости широко применяемой в автомобильной промышленности для шестерен стали 18ХГТ, упрочняемой методом цементации или нитроцементации [3]. Износостойкость определялась в системе вал втулка. Образцы подвергались цементации 900 С, 4 ч, закалке с 860 С в масле + низкий отпуск 180 С, 2 ч и карбонитрации 570 С, 2 ч после улучшения. В условиях сухого трения и трения со смазкой нагрузки составляли 500 и 1000 Н при скорости скольжения соответственно 0,5 и 1,5 м/с. В условиях сухого трения износ карбонитрированной стали 18ХГТ составил 5,5 мг/км, а цементованной 180 мг/км. В условиях трения со смазкой цементованный слой показал равномерный износ как при сухом трении, так и при трении со смазкой, причем в обоих случаях с достаточно высокой скоростью. Для сталей 18ХГТ и 20 после карбонитрации скорость износа при трении со смазкой составила соответственно 0,15 и 0,24 мг/км пути, а после цементации соответственно 0,9 и 2,4 мг/км пути (в 6 и 10 раз выше). Определение эффективности технологии упрочнения методом карбонитрации проводилось при сравнительных испытаниях замковой резьбы на износ при многократном свинчивании бурильных замков ЗЛ-152 на буровом стенде, укомплектованным буровой установкой «Уралмаш-4Э» с вышкой ВМ-52. Перед испытанием с помощью переводников ниппель испытываемого замка соединяется со свечой длиной 36 м, составленной из стальных бурильных труб, а муфта с трубой, опущенной в скважину и установленной на столе ротора на элеваторе. Единичный цикл в испытаниях состоит из последовательного проведения следующих операций: установки наращиваемой бурильной свечи в муфту, свинчивания замковых деталей, развинчивания замкового соединения и подъема свечи. Свинчивание и развинчивание замкового соединения производится автоматическим буровым ключом АКБ-3М крутящим моментом 1200 кгс м. Анализ приведенных на рис. 2 результатов показывает, что интенсивность изменения критерия степени износа резьбы «Н» у образцов 3 и 5, упрочненных методом карбонитрации, примерно в 4 раза ниже, чем у серийно выпускаемых замков 2 и 6, имеющих фосфатное покрытие резьбы. Это говорит о многократном повышении износостойкости резьбы с карбонитрированным слоем по сравнению с резьбой, обрабатываемой по серийной технологии. Высокая эффективность процесса карбонитрации достигнута при упрочнении стали 10 (рычаг) и стали 09Г2С (шток) рулевого управления снегохода. Эти марки сталей в практике машиностроения никогда не подвергались поверхностному упрочнению. Усталостная прочность натурных деталей при испытаниях превысила установленный техническими требованиями предел в 10 6 циклов. Стендовые циклические испытания рычагов рулевого управления снегохода из стали 10 в паре со штоком труба со шлицами из стали 09Г2С после упрочнения методом карбонитрации показали износостойкость, более чем в 2 раза превышающую износостойкость серийных деталей, подвергаемых газовому азотированию. За циклов испытания износ серийных деталей достигал 0,06 мм, а карбонитрированных не превышал 0,025 мм (рис. 3). Карбонитрацию стали 09Г2С предлагается использовать при изготовлении корпусов и пробок шаровых кранов взамен гальванического хромирования. Карбонитрация нержавеющих сталей Надежность и долговечность деталей из нержавеющих хромистых и аустенитных сталей, работающих в различных условиях эксплуатации, зависят не только от свойств основного металла, но и от состояния сравнительно тонких поверхностных слоев. В промышленности для повышения поверхностной твердости, изно- Износостойкость стали 20Х после цементации и карбонитрации Метод химико - термической обработки Толщина упрочненого слоя, мкм Условия испытаний Нагрузка, Н Скорость скольжения, м/с Таблица 1 Режимы обработки и характеристики карбонитрированного слоя углеродистых и низколегированных сталей Марка стали Твердость, Н100 Толщина Общая толщина слоя, мкм ридного карбонит- слоя, мкм Время карбонитрации, ч Сердцевина Поверхность У У Х ХГСА Х1НВА Х2МЮА ХГТ Х2Н4ВА Таблица 2 Скорость износа, мг/км пути трения Цемент ация ,5 0,15/ ,5 Карбонитрация Карбонитридный ,5 0,007/5,5 слой ,5 Гетерофазный ,5 0,025/150 слой ,5 Примечание. Указана скорость износа при трении со смазкой (числитель) и без смазки (знаменатель) 34
4 Опыт применения карбонитрации стальных деталей и инструмента состойкости, задиростойкости, усталостной прочности этого класса конструкционных сталей применяют газовое азотирование. Но этот процесс, во-первых, слишком длительный, во-вторых, наблюдается деформация и коробление деталей, в-третьих, ε-фаза, образующаяся при насыщении нержавеющих сталей азотом, оказывается очень хрупкой и её приходится удалять операцией шлифования. Сам технологический процесс газового Рис. 2. Сравнительные испытания на свинчивание бурильных замков ЗЛ-152 с фосфатированием и карбонитрацией резьбы: 2 и 6 фосфатировани е; 3 и 5 карбонитрация 570 С, 2,5 и 5 ч соответств енно Рис. 3. Износостойкост рычага рулевого управления снегохода из стали 10 после карбонитрации (1) и серийного режима газового азотирования (2) азотирования усложняется, так как приходится вводить в муфель депассиватор, устраняющий окисную пленку с поверхности нержавеющих сталей. Процесс жидкостной карбонитрации нержавеющих сталей лишен указанных недостатков. Скорость насыщения в расплаве солей выше, чем в газовых средах, а одновременное насыщение азотом и углеродом позволяет получать на поверхности стальных изделий менее хрупкий карбонитридный слой, чем чисто нитридный. В результате отпадает необходимость последующей механической обработки, и, кроме того, карбонитридный слой существенно повышает износостойкость и снижает коэффициент трения поверхностных слоев контактирующих деталей. При газовом азотировании упрочнение аустенитных сталей происходит за счет выделения нитридов типа Fe 4 N, а также Fe 3 N. Микроструктурные, рентгеноструктурные, рентгеноспектральные исследования показали, что упрочняющей фазой при карбонитрации являются не указанные выше нитриды, а оксикарбонитридная фаза со сложной решеткой шпинели типа Fe 3 O 4. Присутствие в карбонитрированном слое аустенитных сталей значительных количеств азота, углерода и кислорода являются основными причинами образования совершенно новых по структуре, фазовому, химическому составам и свойствам упрочненных слоев. Фазовый рентгеноструктурный анализ хромистых нержавеющих сталей типа 30Х13, 14Х17Н2 после карбонитрации также обнаруживает на поверхности присутствие оксидной составляющей с решеткой шпинели и явно выраженную оксикарбонитридную фазу типа (Fe,Cr) 3 (N,C,O). В настоящее время технология карбонитрации применяется для обработки серий промышленных партий деталей из сталей 20Х13, 30Х13, 40Х13, ЭИ 961, 14Х17Н2, 10Х18Н10Т, НН-3Б и др. На рис. 4 приведены значения коффициента трения аустенитной стали 10Х18Н10Т после закалки, карбонитрации и газового азотирования, где очевиден эффект и преимущество технологии жидкостной карбонитрации. Карбонитрации подвергаются детали запорной арматуры энергетического, газо- и нефтедобывающего оборудования (штоки, шпиндели, золотники, в том числе с зубчатым приводом, оси, втулки, специальной конструкции гайки с обычной и трапецеидальной резьбой, пробки шаровых кранов и др.). Для специальных редукторов упрочнению подвергаются червяки, шестерни, рейки с модулем m до 6 мм. Технологические возможности печи-ванны (открытое зеркало расплава) позволяют обрабатывать длинномерные детали в подвешенном состоянии с двух сторон, переворачивая их и проводя требуемый режим для каждой стороны. Таким образом, нами обрабатываются зубчатые рейки и планки длиной до 2000 мм из стали 40Х13 для оборудования химической установки. Карбонитрация прессового, штампового и реж ущего инструмента Вытяжные, гибочные штампы, накатной инструмент При гибке или пластическом формообразовании листового металла из-за скольжения по поверхности штампа под высоким давлением возникает сильный Вестни к МГТУ им. Г. И. Носова
5 износ. Иногда проявляется явление сваривания: мелкие частицы металла прилипают к поверхности штампа, что приводит к браку изделий. Высокая износостойкость и низкий коэффициент трения структуры поверхности карбонитрированного слоя исключают это явление. Это относится не только к сталям, но и к цветным сплавам меди и аллюминия. Наиболее высокую стойкость в этих условиях показывают инструментальные стали с 12% хрома, инструментальные стали для горячей штамповки, а также быстрорежущие стали для калибровки. По данным ЗАО «Кольчугцветмет» карбонитрация плавающих оправок из стали Р18 размером 3,4 4,6 мм для капиллярных труб обеспечивает кратное повышение стойкости по сравнению с серийными оправками из стали У10 с покрытием гальваническим хромом. Вырубные, штамповочные и прошивные штампы Штампы этой группы, обработанные методом карбонитрации, отличаются высокой стойкостью режущей части, особенно при прошивке и штамповке мягких материалов. Наличие упрочненого слоя на боковых поверхностях инструмента препятствует привариванию и налипанию частиц металла и благодаря низкому коэффициенту трения уменьшает само усилие отвода прошивного штампа. В зависимости от вида и прочности обрабатываемого металла твердость сердцевины этого типа инструментов должна быть не ниже 50 HRC и они должны изготавливаться из 12%-ных хромистых сталей или сталей для горячей штамповки, показывающих после карбонитрации лучшие результаты. Штампы для деформации в горячем состоянии, прессовый и ковочный инструмент Вследствие высокой температурной нагрузки повышение стойкости у прессовых и ковочных штампов меньше, чем при прессовании выдавливанием. После 2 3-часовых режимов обработки стойкость после карбонитрации повышается на % в зависимости от обрабатываемых марок сталей или цветных сплавов. Инструмент из теплопрочных сталей для деформации в горячем состоянии различных поковок, коленчатых валов, цапф, шатунов двигателей автомобилей и др. подвергаются улучшению на твердость сердцевины HRC, а затем карбонитрации. После износа в ряде случаев возможна повторная карбонитрация штампов. Инструмент из быстрорежущей стали По сравнению с инструментом для штамповой оснастки у инструмента из быстрорежущей стали продолжительность карбонитрации сравнительно короткая 5 40 мин, в основном не более мин. За это время в пределах слоя толщиной несколько сотых миллиметра твердость режущей части повышается до HV, что способствует лучшему сходу стружки. Стойкость разверток, сверл, фрез различного назначения, прошивок, долбяков для зубчатых колес и др. возрастает в 1,5 3 раза. Причем гарантированный успех достигается дополнительным оксидированием карбонитрированного инструмента в соляном расплаве при С. Если быстрорежущий инструмент всесторонне перетачивается, то его можно повторно подвергать карбонитрации. У инструмента с затылованием или затыловочным шлифованием перетачивается только передняя поверхность, т.е. контур сохраняется, и в этом случае инструмент дополнительно не карбонитрируется. Инструмент для литья под давлением Для литья под давлением жидких цинковых, магниевых и алюминиевых сплавов поршни, цилиндры, загрузочные втулки, сопла, распределительные детали и сердечники изготавливаются из сталей для горячей штамповки. После карбонитрации сопротивление вымыванию и прилипанию расплава увеличивается до 300%. Стойкость инструмента из стали типа 4Х5МФС для горячего прессования алюминиевых сплавов после карбонитрации повышается в 2 6 раз. Наличие на поверхности оксикарбонитридной зоны из-за низкого коэффициента трения позволяет избегать налипания выдавливаемого металла, что улучшает и качество поверхности изделия. После срабатывания оксикарбонитридной зоны инструмент может подвергаться многоразовой повторной карбонитрации (имеются сведения о более чем 10-кратном упрочнении пресс-шайб). Пресс-формы и другой инструмент для производства пластмасс Пресс-формы, шнеки, цилиндры и другие детали для производства пластмассовых изделий изготавливаются из низколегированных среднеуглеродистых улучшаемых сталей типа 40Х и классического нитраллоя 38Х2МЮА. Стойкость этих деталей после карбонитрации возрастает многократно. Повышается Рис. 4. Изменение коэффициента трения стали 12Х18Н10Т в зависимости от удельного давления при контактном трении: 1 закалка 1150 С ; 2 азотиров ание 620 С, 35 ч; 3 карбонитрация 570 С, 12 ч 36
6 Опыт применения карбонитрации стальных деталей и инструмента не только стойкость к продавливанию и износу, но изза высокой твердости поверхность может легко полироваться до глянцевого блеска, что обеспечивает качество и товарный вид пластмассовой поверхности. При температурах плавления пластмасс вплоть до 300 С карбонитрированный, равно как и азотированный, слой не разупрочняется. По коррозионной стойкости упрочненная поверхность сопоставима с гальваническим хромовым покрытием. Благодаря низкой температуре обработки и отсутствию структурных превращений изменение размеров и формы прессформ составляет несколько микрон. Технология комбинированного упрочнения Технология комбинированного упрочнения рекомендуется для изготовления и ремонта изношенных деталей путем предварительной наплавки и последующего упрочнения карбонитрацией, обеспечивает эксплуатационные характеристики восстановленных деталей на уровне не ниже свойств стальной детали без применения наплавки. Технология включает в себя наплавку (аргонодуговую или лазерную) с последующей механической обработкой для восстановления геометрических размеров и упрочняющую обработку карбонитрацию 6. Чеховский завод энергетического машиностроения для деталей запорной арматуры тепловых и атомных станций использует технологию карбонитрации для упрочнения тарелок с наплавкой. Эффект повышения ресурса работы до 3 раз по сравнению с новыми запасными частями достигается в настоящее время при ремонте технологического оборудования на предприятии «Астраханьгазпром» и запорной арматуры Калининской АЭС. Толщина наплавленного металла может колебаться в пределах от 0,5 до мм (при многослойной наплавке). Толщина карбонитридного слоя в зависимости от материала наплавки и длительности выдержки достигает 0,5 0,6 мм, а твердость поверхности НV. При комбинированном упрочнении диффузионный слой на наплавке имеет более высокую твердость и толщину, в сравнении с карбонитрированным слоем стали, аналогичной по химическому составу наплавке. Исследование эрозионного разрушения поверхности натурного штока после комбинированного упрочнения, в сравнении с упрочнением методом карбонитрации, показывает увеличение стойкости на 30 35%, на 10 15% повышается задиростойкость, а износостойкость в 1,8 2,0 раза. Для реализации технологии жидкостной карбонитрации разработано и изготовливается оборудование 5-ти типоразмеров, составляющее технологическую линию жидкостной карбонитрации (ТЛЖК) и позволяющее проводить упрочнение деталей длиной до 1200 мм и диаметром до 600 мм. В состав ТЛЖК в промышленном варианте входят: печь подогрева деталей, печь-ванна карбонитрации, ванны промывки, обезжиривания, оксидирования. На рис. 5 показана линия, эксплуатирующаяся на ремонтной базе ООО «Уренгойгазпром», где обрабатываются более 30 наименований деталей и режущий инструмент 6, 7. На Центральной трубной базе ОАО «СУРГУТНЕФ- ТЕГАЗ» для упрочнения замков бурильных труб (переводников) смонтирована и введена в эксплуатацию технологическая линия жидкостной карбонитрации высокой производительности для обработки деталей разных типоразмеров в год. В состав этой линии, занимающей площадь около 200 м 2, помимо основных элементов оборудования включены очистная установка и установка для выпаривания промышленных стоков после промывки деталей для обеспечения высоких требований экологической безопасности. Образующаяся после выпаривания очищенная вода используется в качестве оборотной. Для проведения карбонитрации и регенерации рабочей ванны отработан процесс синтеза слитков солей заданного химического состава, существенно упрощающей эксплуатацию в промышленных условиях. Синтезирование слитков как для процесса карбонитрации (90% КСNО +10% К 2 СО 3 ), так и для регенерации ванны (96% КСNО + 4% К 2 СО 3 ) проводится в отдельном тигле по разработанной нами технологии. Синтезированный расплав соли для карбонитрации разливается в специальные формы. Полученные слитки, ввиду гигроскопичности, подвергаются вакуумной упаковке. В совершенствовании технологии жидкостной карбонитрации представляет интерес так называемый НОК-процесс (низкотемпературное оксикарбонитрирование), разработанный отечественными исследователями [9]. Позже аналогичный процесс, предложенный фирмой «Дегусса» (Германия), получил название TUFFTRYDE QPQ. Эта технология, первоначально задуманная для улучшения товарного вида деталей, резко понижает коэффициент трения и по данным немецких исследователей [10] существенно повышает коррозионную стойкость деталей из сталей перлитного и мартенситного классов. При испытании в солевом тумане в растворе соли с перекисью водорода коррозионная стойкость деталей, обработанных по технологии QPQ, превосходит стойкость гальванического хромового покрытия. Себестоимость обработки деталей по технологии QPQ на 40% меньше стоимости технологии нанесения гальванического покрытия. QPQ-процесс включает следующую последовательность операций: карбонитрация охлаждение и выдержка в ванне оксидировния при С в нитритно-щелочном расплаве охлаждение на воздухе промывка полировка оксидирование в расплаве промывка. Низкий коэффициент трения и высокая коррозионная стойкость сталей с оксикарбонитридным покрытием по технологии QPQ после проверки эксплуатационных свойств может рассматриваться в качестве процесса для поверхностного упрочнения деталей из низколегированных сталей перлитного класса и хромистых нержавеющих сталей и, в частности, как замена технологии гальванического хромирования для пробок шаровых кранов из стали 09Г2С и ряда других изделий. Вестни к МГТУ им. Г. И. Носова
7 Список литературы 1. Прокошкин Д.А. Химические и термические методы обработки стали. М.; Л.: ОНТП, Прокошкин Д.А. Теория и практика цианирования быстрорежущих сталей. М.: ВНИИТОМ, А.с СССР, МКИ 3 С22С27/ Прокошкин Д.А. 4. Прокошкин Д.А. Химико-термическ ая обработк а мет ал - лов карбонитрация. М.: Машиностроение; Металлургия, 1984, 240 с. 5. Супов А.В. Создание процесса карбонитрации // Металловедени е. Т ермическая и хи мико-тер мическ ая обработка сплавов: Сб. науч. тр. М.: МГТУ им. Н.Э. Баумана, Разработка технологических процессов для карбонитрации крупногабаритных деталей / Цих С.Г., Щеглов М.Е., Гришин В.И., Лисицкий В.Н. // Металловедение. Т ермическая и химико-термическая обработка сплавов: Сб. науч. тр. М.: МГТУ им. Н.Э. Баумана, Разработка технологической линии жидкостной карбонитрации и процессов упрочнения запасных частей к основному оборудованию и инструменту / Ци х С.Г., Пласконь И.А., Гришин В.И., Лисицкий В.Н. // Обеспечение эффективного функционирования Уренгойского нефтегазодобывающего комплекса. М.: ООО «ИРЦ Газпром», Исследов ание законо мерност ей комбиниров анного упрочнения структуры поверхностного слоя стали 25Х1МФ / Цих С.Г., Щеглов М.Е., Гришин В.И., Лисицкий В.Н., Мурадов А.В. // Защита окружающей среды в н ефтегазовом комплексе С Карбонитрация р ежущего инструмента в соляных ваннах / Прокошкин Д.А., Супов А.В., Богомолов А.М., Кошенков В.Н. // МиТОМ Валь Г. Влияние режимов нитроцементации и последующего окисления на свойства деталей // МиТОМ List of literature 1. Prokoshkin D.A. Chemical and thermal methods of the steel treatment. M.: L.: ONTP, Prokoshkin D.A. Theory and practice of the high-speed steelcyanidation. M.: VNIITOM, A.s USSR, MKI3 C22C27 / Prokoshkin D.A. 4. Prokoshkin D.A. Chemical and thermal methods of the steel treatm ent carbonization. M.: Machine-building; Metallurgy, P Supov A.V. Carbonization process formation // Adaptive metallurgy. T hermal and chemical and thermal alloy treatm ent: Collection of the scientific work. M.: MSTU named after N. E. Bauma, T echnological processes for carbonization o f the l arge capacity parts / Tsikh S.G., Tscheglov M.E., Grishin V.I., Lisitsky V.N. // Adaptive metallurgy. Thermal and chemical and thermal alloy treatment: Collection of the scientific work. M.: MSTU named after N.E. Bauma, Technological line of the liquid-column carbonization and strength processes of the spare parts for the main equipment and instrument / Tsikh S.G., Plaskol I.A., Grishin V.I., Lisitsky V.N. // Effective operation of Urengoysky oil-producing complex. M.: limited liability company IRC Gasprom, Regularity research of the combined strength of the surface coating structure in steel 25X1MF / Tsikh S.G., Tscheglov M.E., Grishin V.I., Lisitsky V.N, Muradov A.V. // The environment protection in the oil-producing complex P Carbonization of the cutting tool in the salt baths / Prokoshkin D.A., Supov A.V., Bogomolov A.M., Koshenkov V.N // MiTOM Val G. The impact of carbonitriding modes and further oxidation on the properties of the parts // MiTOM
docplayer.ru
Карбонитрация и хромонитридизация - Let's glock them all
Модернизировать российские промышленные предприятия можно не только с помощью импортируемых технологий. Опыт компании «Термохим-инжиниринг» по коммерциализации технологий упрочнения поверхностей металлов показывает, как можно успешно использовать в этом процессе высококлассные технологические заделы советского периодаЗащитить кандидатскую Сергею Циху не удавалось довольно долго. В 1980-е, в самом начале своей карьеры, нынешний генеральный директор компании «Термохим» и заведующий лабораторией химико-термической обработки НПО ЦНИИТМАШ попал в историю, очень характерную для отраслевой науки того времени. Любые разработки хотя бы с намеком на двойное назначение, не говоря уже об оборонных, тогда умело засекречивались, и зачастую сотрудники того или иного исследовательского учреждения не знали, чем конкретно занимаются работающие с ними бок о бок коллеги. За несколько месяцев до защиты, рассказывает Сергей Цих, умер его научный руководитель профессор Дмитрий Прокошкин. И после его смерти в МВТУ им. Баумана объединили две кафедры: термообработки, которую Прокошкин возглавлял, и металловедения. Предзащита аспиранта проходила уже на объединенной кафедре. В то время между кафедрами шло жесткое соперничество, и обсуждение диссертации вылилось в ожесточенную дискуссию. Ученые с бывшей кафедры Прокошкина, на которой учился, а затем окончил аспирантуру Сергей Цих, работу единодушно поддержали; вторая же сторона сочла ее незавершенной. Особенно много вопросов касалось практической значимости работы, причем на главные претензии оппонентов: для чего же нужны эти «теоретические выкладки? — автор ответить просто не имел права. Между тем научные результаты были получены при выполнении совершенно конкретной исследовательской работы и предназначались для использования в ракетной технике, в частности для разрабатываемого ядерного ракетного двигателя (ЯРД), и находились под грифом «совершенно секретно». Убедить членов кафедры в том, что ссылки на секретность — это не просто попытка уйти от ответа, не удалось, и диссертацию молодого ученого положили «в стол» на целых два года.В диссертации Циха рассматривались различные аспекты применения технологии плазменного азотирования — одного из методов упрочнения поверхности металла. Речь шла об участии Бауманки в секретном проекте создания ядерного ракетного двигателя: по заказу химкинского КБ «Энергомаш» перед кафедрой термообработки ставилась задача увеличить высокотемпературную прочность капилляров-трубопроводов, которые и без того изготавливались из самого жаропрочного из существующих тантал-вольфрамового сплава для работы с ураново-марганцевой средой при температурах свыше 1700 °C. Из опыта запуска ракет другого типа было известно, что сам сплав без специальной обработки при таких условиях быстро корродирует и разрушается, но при этом сопла ракет с упрочненным покрытием деталей из этого же сплава могут выдерживать колоссальные температуры. В случае с заказом «Энергомаша» необходимо было обрабатывать поверхность внутренней части трубопроводов, и бауманцы справились с этой задачей, создав технологию азотирования в тлеющем разряде.
Профессор, пьющий цианат
Известно, что рабочие характеристики деталей не только ракетного двигателя, но и любого металлического изделия вообще во многом зависят от качества обработки его поверхности. Существуют десятки технологий улучшения свойств поверхностного слоя металла — прочности, вязкости, износо-, задиро-, коррозионной и других видов стойкости, — придающих инструменту и деталям машин несравнимо более высокие эксплуатационные характеристики, которые достигаются за счет диффузионного насыщения этого слоя различными веществами. Для этого применяют в том числе химико-термические способы обработки: цементацию, азотирование, диффузионную металлизацию. В компании «Термохим-инжиниринг» занимаются как раз этими традиционными, известными во всем мире химико-термическими методами. Но есть в арсенале компании и две технологические «звезды», которые во многом обеспечивают коммерческий успех предприятия: это технологии жидкостной карбонитрации и так называемой хромонитридизации (этой технологией, речь о ней пойдет ниже, кроме компании Циха, в мире не обладает никто).
Первую технологию Сергей Цих «вытащил» из Бауманки. Ее автор — тот самый Дмитрий Прокошкин, учитель и научный руководитель Циха. Его имя мало что говорит обывателю, тем более, как нередко бывает с выдающимися отраслевиками, это ученый без всяких академических регалий. Между тем Прокошкин — мировая величина в материаловедении, автор отечественной теории диффузии и всей базовой теории химико-термической обработки металлов. В 1938 году вышел его фундаментальный труд «Диффузия элементов в твердое железо: химические и термические методы обработки стали», предопределивший все дальнейшее развитие советского металловедения в области обработки материалов. С 1954-го по 1959 год он служил ректором МВТУ им. Баумана и долгое время курировал в Министерстве высшего образования все техническое образование в СССР.
Еще до войны был известен метод цианирования. Суть его в том, что детали машин, изготовленные из различных видов сталей, подвергают азотированию в нагретом расплаве солей, содержащих в том числе цианистый калий, что, естественно, сильно ограничивает использование этой эффективной технологии. В 1970-х Дмитрий Прокошкин выяснил, что в процессе диффундирования участвуют не сами цианиды, а их оксидные производные — цианаты, и предложил использовать в составе солей именно их. На лекциях, вспоминает Сергей Цих, профессор для убедительности тезиса о безопасности своей технологии растворял цианат калия в воде и медленно выпивал раствор на глазах у изумленных студентов. В отечественной технологии карбонитрация как безвредный процесс упрочнения заменила цианирование. Эта технология используется в качестве альтернативы таким процессам обработки, как поверхностная закалка, гальваническое хромирование и цементация для повышения усталостной прочности и увеличения коррозионной стойкости, уменьшения коэффициента трения, кратно — до десяти раз — улучшая износостойкость металла. Но, как часто бывало с отечественными разработками, до развала Союза карбонитрация быстрой популярности не приобрела. Внедрять эту технологию начали в 1980-е на единичных производствах, развитие она получила в основном на оборонных предприятиях, в частности, использовалась для обработки танковых орудийных стволов. За границей же, прочитав публикации Прокошкина, напротив, очень быстро технологию подхватили и развили, и ее разновидности под названием «тенифер-процесс» или «тафтрайдинг-процесс» получили значительно более широкое распространение. Сам метод стал широко доступным и для специалистов секрета не представляет, в отличие от солей, состав которых каждый производитель (тот же «Термохим») держит в строгом секрете. В западных солях, кстати, сохраняется небольшая доля цианистого калия. Цих не видит в этом никакой технологической целесообразности и связывает это с желанием западных компаний сохранить патентную чистоту именно своих методов. В 2000-е они уже вовсю стучались в ворота российских производств, спотыкаясь лишь об извечную технологическую косность управленцев, к тому же занятых не модернизацией, а поиском возможностей выживания своих предприятий. До сих пор, приезжая на некоторые предприятия как раз в связи с решением модернизационных проблем, рассказывает Сергей Цих (он, кроме прочего, выступает экспертом в компании «Вебер Комеханикс», занимающейся комплексным перевооружением металлообрабатывающих предприятий), сталкиваешься с тем, что об этой технологии знают мало. Технологи заводов часто хватаются за голову, говорит руководитель «Термохима»: как же мы раньше о ней не знали! Между тем результаты такой обработки применимы в любой отрасли — от пищевой промышленности до космоса, на каждом предприятии машиностроения — везде, где трутся детали, где нужно понизить характеристики износа металла.
Как умножить стипендию
Учиться применять эту технологию Сергей Цих начал еще студентом на кафедре термообработки факультета автоматизации и механизации производства Бауманки. Причем он не просто изучал, но к окончанию аспирантуры практически освоил ее среди других основных химико-термических технологий упрочнения поверхности металлов, какими занимались тогда в МВТУ. Сейчас от многих руководителей предприятий или институтских лабораторий часто можно слышать стенания по поводу отвратительной вузовской подготовки инженеров-специалистов и выводы о смерти всей системы подготовки технарей. Сам Цих, который ежегодно выпускает несколько дипломников в Бауманке и МИСиСе, убежден: инженерное образование в стране по сути разрушено. Как же в советское время удавалось воспитать практические инженерные навыки еще во время обучения в вузе? В Бауманке в то время обучали не только теории, рассказывает Сергей Цих, у ученых-преподавателей и их студентов была живая связь с предприятиями, они совместно разрабатывали технологии и впоследствии внедряли их на производстве. В том же МВТУ существовал порядок, характерный для многих других советских технических вузов и обеспечивающий такие взаимосвязи. В подчинении заведующего кафедрой находилось несколько доцентов, в обязанности которых входило не только преподавание, но и ведение хоздоговорных тем, причем большинство из них носило поисковый, исследовательский характер. В исследовательскую работу обязательно вовлекали аспирантов, в свою очередь курировавших дипломников-старшекурсников, которым предстояло защититься по соответствующей теме. Оказавшись втянутым в такую систему подготовки, Цих получил основательный теоретический и технологический задел для своей будущей деятельности, в которой ученого очень трудно оторвать от производственника. Мало того что он учился под руководством автора самих методов обработки, специалиста мирового уровня, но еще и выполнял под его руководством практические работы, упрочняя детали и инструменты по договорам на существовавшем при кафедре экспериментально-производственном оборудовании, зачастую собранном самими преподавателями и студентами. Получалось, что работа, сопряженная с учебой, опиралась, во-первых, на теоретические и экспериментальные наработки самого учебного заведения, а во-вторых, прямо переводила этот ученый опыт в плоскость практического применения. Причем в таком трансфере были материально заинтересованы все участники исследовательско-производственного процесса. По крайней мере, в аспирантские годы, по словам Сергея Циха, за счет такой работы ему удавалось иногда подработать еще несколько «стипендий». Надо отметить, что до поступления в аспирантуру выпускник был обязан отработать три года на производстве.
Генеральный директор компании «Термохим» Сергей Цих мечтает построить центры упрочнения по всей России expert_798_066.jpg Генеральный директор компании «Термохим» Сергей Цих мечтает построить центры упрочнения по всей РоссииНашему герою тоже пришлось пройти через этот опыт. Из кузницы квалифицированных инженерных кадров для ВПК, какой была Бауманка, он сразу попадает в королёвскую фирму — закрытое КБ «Химмаш» имени А. М. Исаева, известное своими разработками жидкостных реактивных двигателей для ракет различного назначения, где работает мастером в литейном цехе отдела, который занимался разработкой корректировочно-тормозных двигательных установок.
После окончания аспирантуры в 1989 году Сергея Циха распределяют в другой крупный материаловедческий центр страны — НПО ЦНИИТМАШ. Этот головной технологический центр энергомашиностроительной отрасли, один из первенцев советской прикладной науки (он создан в 1929 году), сейчас входит в структуру «Росатома». С самого начала перед институтом была поставлена задача разработки материалов, технологий и оборудования, которые позволили бы отказаться от импорта машиностроительной продукции. И в свое время, как известно, эта задача была решена, по крайней мере в части энергомашиностроения, включая атомное. По словам Сергея Маркова, бывшего заместителя директора института, ЦНИИТМАШ с самого начала был определен головной организацией, которая должна заниматься вопросами стратегического характера в отраслях, связанных с тяжелым машино- и гидротурбостроением. Специфическая черта этой организации, по словам Маркова, заключалась в том, что в связи со сложностью решаемых проблем с самого начала во главу угла всех институтских исследований ставилась комплексность, всесторонность подхода. В институте исследовалась и разрабатывалась вся технологическая цепочка — от создания материалов (прежде всего металлургии: сталей и различных сплавов), выпуска пилотных образцов оборудования для их производства до создания технологий выпуска продукции из этих материалов.
Сергей Цих начинает здесь работать в лаборатории химико-термической обработки — одной из самых мощных в Советском Союзе, основанной еще одним советским корифеем металловедения мирового уровня — Юлием Грибоедовым. Под его руководством, рассказывает Цих, в СССР было создано новое научное направление — диффузионная металлизация поверхности металлов. Разработанные им принципы легли в основу технологий, которые позволяют внедрять в поверхность — к примеру в стальную — практически любой металл, что нашло широкое применение в защите от износа и коррозии, повышении жаростойкости деталей, в том числе из аустенитных сталей, в паротурбостроении и атомном реакторостроении. Одна из них — хромонитридизация — послужила залогом научного и материального выживания лаборатории в смутные для отечественной науки и производства 1990-е и дала старт компании «Термохим».
Институт дал «добро»
История развития хромонитридизации уходит корнями опять-таки в область двойных технологий. В 1960–1970-е в СССР разрабатывались атомные подводные лодки проектов 705, 705К «Лира» с реакторами на быстрых нейтронах (подробнее см. «Не тормозите нейтроны», «Эксперт» № 21 за 2001 год), за счет мощности которых скорость лодок могла достигать 70 км в час. Теплоносителем в реакторе выступал жидкометаллический свинцово-висмутовый расплав. Метод традиционного азотирования оказался непригодным для обработки поверхности деталей, выполненных из аустенитных сталей, работающих в условиях длительной эксплуатации с жидким металлическим сплавом (или с натриевым расплавом в быстром ректоре БН-600 «мирной» Белоярской АЭС). Дело в том, что аустенитные стали — а это стали с низким содержанием углерода и высоким содержанием хрома и никеля — характеризуются высокими коррозионными и жаростойкими свойствами, но обладают крайне низкими свойствами по износо- и задиростойкости. Как говорят инженеры, аустенитные стали мягкие, как пластилин. Технологий поверхностного упрочнения аустенитных хромоникелевых сталей, которые существенно повышают твердость, износостойкость, задиростойкость, немало. Но при этом они почти в сто раз ухудшают коррозионные свойства сталей — свойства, ради которых они, собственно, создавались. Разработанный в ЦНИИТМАШЕ метод, который представляет собой комплексное диффузионное насыщение поверхности стали вначале хромом, а затем азотом, всех этих недостатков не имеет и считается лучшим в мире способом поверхностного упрочнения сталей без потери необходимых свойств.
В 1970-х на территории ЦНИИТМАША была создана первая опытно-промышленная установка, затем еще две появились на оборонных предприятиях, работающих на военно-морской флот: на Горьковском машиностроительном и Калужском турбинном заводах. В самом начале 1990-х начали создавать комплекс оборудования для упрочнения крупногабаритных деталей запорно-регулирующей арматуры для «мирных» тепловых турбин на параметры перегретого пара больше 560 ºC. Руководил проектом заведующий лабораторией химико-термической обработки Виталий Гришин, один из отцов технологии хромонитридизации, по оценке Сергея Циха, ученый энциклопедических знаний в области материаловедения, имеющий большой практический опыт создания современных термических производств. В 1993 году, рассказывает Сергей Цих, был согласован большой контракт с харьковским «Турбоатомом» — флагманом бывшего советского энергомашиностроения. Харьковчане заключили крупный договор с Индией на поставку турбин и сопутствующего оборудования и были готовы заплатить за доводку оборудования для хромонитридизационной обработки деталей, например запорно-регулирующей арматуры из аустенитных сталей идущих на экспорт агрегатов. Любопытно, что для своего рынка жаропрочное энергооборудование изготавливалось из более дешевых теплостойких перлитных сталей. Оно работало не более года, а затем требовало замены. Для экспорта такой подход не годился. Но возникла проблема: деньги, перечисляемые на счета ЦНИИТМАША, списывались тогда за долги института в безакцептном порядке. Виктор Гришин и Сергей Цих обратились к руководству института с просьбой разрешить создать компанию, чтобы иметь оперативный простор для управленческих и финансовых решений. Пообещав не мешать, но и не помогать, тогдашний директор института Александр Зубченко дал «добро» на учреждение компании «Термохим». Забегая вперед, можно сказать, что в итоге в выигрыше остались обе стороны. Сейчас большой объем контрактов приходит в «Термохим» от энергетиков, в выполнении которых субподрядчиком является ЦНИИТМАШ, на счетах которого в итоге остается до половины суммы договора. Дело в том, что институт является держателем технических условий по многим технологиям и владельцем части авторских прав. ЦНИИТМАШ заинтересован и в том, что сама компания, совершенствуя свои технологии, по сути, развивает и лабораторную науку, которая имеет высокий мировой научный рейтинг. Понятно, что и «Термохиму» выгодно работать под научной и технологической крышей института».
Контракт с «Турбоатомом» был исполнен («Недавно нам рассказали, — не без гордости замечает директор “Термохима”, — что те самые обработанные нами аустенитные детали работают без замены уже семнадцать лет»), а у предприятия появилась своя производственная база. Вскоре она приросла и оборудованием для карбонитрации.
В те годы в компанию за помощью как-то обратился главный инженер Чебоксарского дизельпрома Александр Трусков: его предприятие, которое производило крупные установки для золото- и алмазодобытчиков, несло крупные убытки по причине простоя агрегатов из-за частой поломки небольших втулок дизеля. «О цене он не спрашивал, — вспоминает Цих, — и даже предоплатил наличными небольшую установку, которую мы собрали буквально на коленке за два-три дня. Я спросил его, почему он не стал торговаться, когда мы на переговорах наобум назвали первую сумму, пришедшую в голову. Оказалось, что до работы с нами завод только в Якутии держал две бригады, которые лишь тем и занимались, что летали по приискам, собирая и разбирая двигатели в пятидесятиградусный мороз. После нашей обработки детали перестали ломаться, и многих ремонтников пришлось сократить. В “Термохим” по принципу сарафанного радио стали поступать новые заказы. Оставшаяся после заказа дизелистов установка стала приносить по 500 долларов в день за обработку деталей, и это в то время, когда зарплата 100 долларов считалась очень приличной. Тогда мы и начали понемногу вкладывать деньги в исследовательскую работу».
Центр обработки в складчину
Настоящий бизнес пошел, когда на «Термохим» вышли газовики, вынужденные все чаще ремонтировать импортное оборудование, которое стало массово выходить из строя. «Термохим» поставил нескольким газпромовским предприятиям оборудование для карбонитрации, подсадив их на иглу поставки солей, секрет производства которых компания не раскрывает. Но, как сейчас признает сам Цих, он совершил стратегический просчет. Уже в середине 1990-х у компании были серьезные обороты, но 80–90% составляли заказы «Газпрома», и казалось, что так будет всегда. Однако после дефолта 1998 года и смены руководства «Газпрома» обороты фирмы упали почти в десять раз. Пришлось приложить колоссальные усилия, чтобы раскрутить деятельность по новой (сейчас оборот «Термохима» составляет около 2 млн долларов).
Из-за нарастающей необходимости ремонтных работ карбонитрация оказалась востребована и энергетиками. Технологию аттестовали: выпустили технические условия, провели на паях с предприятиями отрасли весь комплекс исследований и получили разрешение на ее применение в энергетике, включая атомную. Вслед за эксплуатирующими компаниями в «Термохим» пришли сервисные, работающие с теми же газовиками и нефтяниками. В 2000-е, когда начался рост экономики, увеличился поток деталей, направляемых на обработку методом карбонитрации, от производственных компаний, прежде всего работающих на добывающие отрасли и энергетику. Технологию начали активно использовать многие арматурные заводы, работающие на атомную энергетику, предприятия, выпускающие буровую технику. Сергей Цих вышел на своих конкурентов — мирового лидера в расплавных технологиях немецкую компанию Durferrit GmbH, которая выпускает 13 тыс. тонн солей в год, и заключил эксклюзивный договор на поставку их оборудования и солей в Россию.
Руководитель «Термохима» признается, что очень многому научился у немцев и многое у них перенял. Это касается и самой технологии «тенифер-процесс», и организации работ, и того, как работает подобный рынок на Западе. Если многие российские предприятия, унаследовавшие еще советский уклад, зачастую имеют весь цикл переделов вплоть до финишной термической и химико-термической обработки поверхности метизов, то, например, у немцев такое могут себе позволить только большие корпорации, подобные «Мерседесу». Средние и мелкие фирмы обслуживаются в центрах обработки, каких в одной Германии более 150. В таких центрах работает в среднем около 20 человек, они обрабатывают до 10 тонн изделий, зарабатывая примерно по 4–5 млн евро в год. Зародилась идея создания подобных центров и в России. План таков: большинство занимающихся термообработкой подразделений предприятий имеет одряхлевшую инфраструктуру, в лучшем случае тридцатилетней давности, из-за чего качество продукции на выходе зачастую просто неконкурентоспособно. Многие ищут пути к модернизации, но для большинства производственных компаний выйти на технологически новый уровень, переоборудовав свою обработку, представляется неподъемной задачей. В то же время создавать отдельные центры упрочняющей обработки, современная начинка которых, по западному опыту, стоит 2–3 млн евро, тоже непросто, поскольку маркетинг и поиск сторонних заказов оттянет сроки возврата инвестиций и сделает весь проект непривлекательным. Но если начать создавать такие центры не на пустом месте, а совместно с предприятиями, которые на первом этапе начнут загружать их собственными заказами, получая обслуживание по цене ниже рынка, то можно выйти на уровень безубыточности довольно быстро — в течение года-двух. Со временем подтянутся и сторонние заказы.
Сергей Цих начинает искать инвесторов для реализации своих замыслов и активизирует маркетинговую деятельность. Один из уже предпринятых шагов — участие в экспертовском Конкурсе русских инноваций, где его проект по жидкостной нанокарбонитрации получил в прошлом году гран-при. После короткой публикации об итогах конкурса в нашем журнале Сергей Цих познакомился с руководством завода экспериментальных машин, которое быстро подхватило идею создания предприятия химико-термической обработки с современными технологиями, включая обе ключевые технологии «Термохим-инжиниринга». С апреля этот центр уже начал работу. Решением созданной в прошлом году совместной комиссии по инновационным проектам «Роснано» и «Росатома» проект создания сети самостоятельных центров упрочнения попал в список ее приоритетных программ.http://expert.ru/expert/2012/15/zakalka-ot-zadira/
glockmeister.livejournal.com
Способ карбонитрирования деталей из высокохромистых сталей
Изобретение относится к области металлургии, в частности к химико-термической обработке деталей, инструмента, оснастки в твердых карбюризаторах. Детали помещают в контейнер и засыпают порошковой смесью, состоящей из следующих компонентов: активированного древесного угля, карбамида и трилона-Б. Используют порошковую смесь, в которой указанные компоненты содержатся в соотношении 1:1:1. Перед помещением в контейнер с порошковой смесью детали покрывают обмоткой из поливинилхлоридной клейкой ленты, на липкую часть которой предварительно наносят порошковую смесь. После засыпки деталей порошковой смесью в контейнере его переносят в вакуумную реторту с остаточным давлением 50-80 Па, предварительно разогретую до температуры 980-1000°С, и выдерживают в течение 4-6 часов при температуре карбонитрирования 960-980°С. Затем проводят закалку в масло от температуры карбонитрирования, после закалки проводят охлаждение деталей в контейнере на воздухе, затем проводят отпуск на воздухе при температуре 250-320°С в течение 2-3 часов. Улучшаются основные эксплуатационные свойства карбонитрированных деталей из высокохромистых сталей, а именно повышаются твердость и износостойкость. 6 ил., 1 табл., 3 пр.
Изобретение относится к области металлургии, в частности к химико-термической обработке деталей, инструмента, оснастки в твердых карбюризаторах, в частности в порошковых смесях, на основе активированных древесных углей. Оно может найти применение в приборостроении, производстве электрических реактивных двигателей малой тяги, а так же в электронике, на малых ремонтных предприятиях и ювелирных цехах.
Известны способы диффузионного насыщения сталей и сплавов в порошковых смесях с введением в составы хлорсодержащих соединений - хлористого аммония, хлористого натрия для депассивации поверхности склонных к окислению хромистых сталей и титановых сплавов (Химико-термическая обработка металлов и сплавов. Справочник. Бориченок Г.В., Васильев Л.А., Ворошин Л.Г. и др. М.: Металлургия, 1981. 424 с.).
Описанные способы получили ограниченное применение из-за недостаточной технологичности и универсальности.
Известны составы и способы активизации диффузионного насыщения сталей с содержанием хрома до 17% (RU №2314363 С1, МПК С23С 8/76, опубл. 10.01.2008 г.) и титановых сплавов (RU №2378411 С2, МПК С23С 8/76, опубл. 20.08.2009 г.) в порошковых смесях на древесноугольной основе, включающих активированный древесный уголь и добавки-активаторы - карбамид, трилон-Б, триэтаноламин.
Вышеописанные технические решения имеют следующий недостаток: невысокая степень депассивации поверхностей названных сталей и сплавов, и, как следствие, замедление скорости насыщения поверхностей и необходимость заключительного шлифования, заточки рабочих поверхностей для снятия менее твердого слоя «внутреннего окисления» глубиной до 0,15 мм.
За ближайший аналог взят способ карбонитрирования деталей из высокохромистых сталей, включающий помещение деталей в контейнер и их засыпку порошковой смесью, состоящей из активированного древесного угля, карбамида и трилона-Б. Температура карбонитрирования - 960-980°С (RU 2237744 С1, МПК С23С 8/76, 10.10.2004, формула, таблица, пример 1).
К недостаткам описанного способа можно отнести невысокие эксплуатационные свойства деталей, обработанных карбонитрированием, в частности, их недостаточная твердость и износостойкость, что является следствием нестабильности толщины насыщенного поверхностного слоя и его неоднородности по составу и количеству карбидов.
Изобретение решает задачу улучшения основных эксплуатационных свойств карбонитрированных деталей из высокохромистых сталей, а именно повышение твердости и износостойкости, за счет увеличения стабилизации толщины насыщенного поверхностного слоя и повышения его однородности по составу и количеству карбидов.
Для получения необходимого технического результата в известном способе карбонитрирования деталей из высокохромистых сталей, включающем помещение деталей в контейнер и их засыпку порошковой смесью из активированного древесного угля и карбамида, и трилона-Б при температуре карбонитрирования 960-980°С, предлагается использовать упомянутую порошковую смесь, в которой компоненты содержатся в соотношении 1:1:1, перед помещением в контейнер с порошковой смесью детали покрывать обмоткой из поливинилхлоридной клейкой ленты, на липкую часть которой предварительно наносить подготовленную для карбонитрирования порошковую смесь. После засыпки деталей в контейнере порошковой смесью, его предлагается переносить в вакуумную реторту с остаточным давлением 50-80 Па, предварительно разогретую до температуры 980-1000°С, и выдерживать в течение 4-6 часов при температуре карбонитрирования 960-980°С, затем проводить закалку в масле от температуры карбонитрирования, после закалки проводить охлаждение деталей в контейнере на воздухе, а затем проводить отпуск на воздухе при температуре 250-320°С в течение 2-3 часов.
Поставленная задача в известном способе химико-термической обработки с использованием порошковых смесей из активированного древесного угля и азотоуглеродосодержащих компонентов - карбамида и трилона-Б, решалась последовательным выполнением следующих операций: механически обработанные в окончательный размер детали покрывают обмоткой из полихлорвинильной клейкой ленты. Подготовленную для карбонитрирования порошковую смесь из карбамида, трилона - Б, толченого древесного угля предварительно наносят на клейкую упаковку садки. После чего переносят контейнер с деталями в вакуумную реторту малоэнергоемкой электропечи при остаточном давлении 50-80 Па, предварительно разогретую до 980-1000°С, и выдерживают там в течение 4-6 часов при температуре карбонитрирования 960-980°С. Закалку после карбонитрирования лучше проводить в масле от температуры карбонитрирования, но можно и на воздухе в контейнере. После чего детали охлаждают в контейнере на воздухе. Отпуск проводят при температуре 250-320°С в течение 2-3 часов на воздухе.
При проведении карбонитрирования деталей предлагаемым способом происходят следующие химико-термические процессы.
Вначале с рабочими поверхностями деталей непосредственно контактирует хлорсодержащее органическое вещество - поливинилхлорид [-Ch3CHCl-]n, плотность - 1,40 мг/см3, с температурой плавления 150-200°С, разлагающееся выше 110°C с выделением хлористого водорода НСl. В процессе прогрева, неизотермического разложения до температур высокотемпературного карбонитрирования, в начальной стадии активно идет депассивация поверхностей высокохромистой стали. К моменту диссоциации карбамида (NН2)2СО и трилона - Б (C10H8O10)Na2N2 поверхности активированы, подготовлены к адсорбции атомарных углерода и азота.
После прогрева, при высокотемпературной выдержке атомарный углерод поливинилхлорида, избыточный углерод и азот активнее диффундируют в присутствии щелочного натрия с образованием избыточных карбидов глобулярных, сросшихся типа (Fe, Сr)7С3, (Fе, Сr)23С6 в сталях марки 20Х13, 30Х13, 14Х17Н2. Как результат активации и стабилизации массопереноса углерода и азота растет скорость карбонитрирования, количество упрочняющих фаз и слоев.
Нагрев и выдержка контейнеров в вакуумной реторте, разогретой до 980-1000°С, позволяет улучшить условия диссоциации компонентов насыщающей среды по следующим схемам:
поливинилхлорид [СН2-CHl]n→(С2Н2)n+n НСl,
nС2Н2→n2Сaт.+nН2
карбамид (Nh3)2CO→NН3+СО+0,5 Н2+0,5 N2
трилон -Б (C10H8O10)Na2N2→9СО+3СН4+0,5N2+1,5Н2+-Na2O
На прилагаемых к описанию графических материалах изображено:
фиг.1 - эскиз малоэнергоемкой печи с вакуумной ретортой;
фиг.2 - микроструктура карбидного слоя на стали 20Х13 с высоким содержанием карбидов х150;
фиг.3 - микроструктура карбидного слоя на стали 20Х13 с содержанием карбидов и карбонитридов 80-90% ×300;
фиг.4 - графики распределения карбидов и углерода в поверхностном карбонитрированном слое стали 20Х13 в зависимости от температуры карбонитрирования: кривые I-980°С; II-990°С; III-1000°С;
фиг.5 - эскиз роликов закаточных машин консервирования рыбопродуктов из стали 20Х13, карбонитрированных по предложенному способу;
фиг.6 - микроструктура магнитомягкой стали 16Х-ВИ после карбонитрирования в порошковой смеси, предварительно обмотанной полихлорвидной лентой при температуре карбонитрирования 960°С с выдержкой в печи 4 часа ×100.
На схемах приняты следующие обозначения:
1 - вакуумная реторта; 2 - быстросъемная крышка; 3 - нихромовые нагреватели; 4, 5 - контейнеры с упакованными деталями для карбонитрирования.
В вакуумной реторте 1 малоэнергоемкой печи с нихромовыми нагревателями 3, оборудованной быстросъемной крышкой 2, устанавливают контейнеры 4 и 5 с деталями. Выбранный вакуум порядка 50-80 Па позволяет стабилизировать диссоциацию обмотки деталей в процессе прогрева в смеси, эвакуацию продуктов газообразования через вакуумный вывод и вакуумный насос по трубопроводу за пределы участка химико-термической обработки. Время выдержки контейнеров в вакуумной реторте выбрано в пределах 4-6 часов, что достаточно, как показали проведенные испытания, для формирования карбидных слоев с высоким содержанием карбидов (фиг.2) повышенной микротвердости.
В процессе выдержки при пониженном давлении ускоряются процессы диффузионного насыщения углеродом и азотом из общего объема порошковой смеси контейнера, в котором распределены упрочняемые детали после полного израсходования компонентов пластифицированной поливинилхлоридной обмотки с наполнителем, количество карбидов и карбонитридов превышает 80-90% при микротвердости по толщине слоя различных легированных хромсодержащих сталей выше всех известных способов химико-термической обработки в твердых древесноугольных составах с активаторами (фиг.3 и фиг.4).
Условия закалки от температур карбонитрирования через воздух в масле необходимы для повышения прочности и вязкости высокотемпературных сталей в сердцевине, а при охлаждении в контейнере на воздухе для получения высоких магнитных свойств магнитомягких высокохромистых сталей типа 16Х, 10Х13 в основе износостойкой поверхности с мелкодисперсными карбидами.
Оптимальными температурами для снижения напряжений карбонитрированных сталей при отпуске являются 250-370°С, охлаждение на воздухе.
Сравнительный анализ полученных показателей, характеризующих эксплуатационные свойства карбонитрированных деталей из высокохромистых сталей по предлагаемому способу и по способу, описанному в ближайшем аналоге, приводится в таблице.
Таблица | ||||
Способ химико-термической обработки, условия карбонитрирования и последующей термообработки *) | Суммарная (эффективная) толщина карбидного слоя, мкм | Микротвердость, Н0,5H слоя | Тип и количество карбидов, %-вес | Износостойкость, **) (абразивное трение) |
1 | 2 | 3 | 4 | 5 |
Предложенный | 1120- | |||
- с обмоткой полихлорвинидной | 1090- | |||
пленкой с нанесением порошка | 1040- | (Fe,Сr)7Сз, | ||
из равных количеств карбамида, | 506-580 | 980- | (Fе,Сr)23С6 | 1,6-1,8 |
трилона-Б, угля активированного | 840- | 81%-85% | ||
древесного, 1000°С 6 часов, в | ||||
вакууме 80Па, закалка в масле, | ||||
отпуск 250°С, 3 часа. | - | |||
Известный | 944- | |||
- без пленки, в контейнере из | 840- | (Fе,Сr)7С3, | ||
смеси карбамид, трилон-Б по | 310-370 | 807- | 68%-69% | 1,0 |
15%, уголь активированный | 767 | |||
древесный - остальное, 960°С, 6 час, | ||||
охлаждение - воздух | ||||
*) - энергоемкость и стоимость обработки в предложенном способе 0,7 в сравнении с известным способом **) - при трении о супермикронную абразивную бумагу, 15 мин, относительная. |
При обработке по предложенному способу диффузионный слой на стали 20Х13 был абсолютно ровным по толщине, скорость формирования карбидного слоя составила 0,11-0,12 мм/ч против 0,07-0,08 мм/ч при обработке в известном способе без полихлорвинидной ленты.
Осуществление способа иллюстрируется примерами производственных испытаний и обработки мелкоразмерных деталей в условиях малых предприятий.
Пример 1.
Ролики закаточных машин консервирования рыбопродуктов из стали 20Х13, диаметром 60-80 мм после механической обработки по посадочному и профильному наружному диаметрам карбонитрировали по предложенному способу. Поливинилхлоридной лентой по ГОСТ 16214-86 с нанесенной порошковой смесью из равных объемных количеств толченого древесного активированного угля по ГОСТ 20464-73, карбамида по ГОСТ по ГОСТ 6691-77 и трилона - Б по ГОСТ 10652-73 проводили обмотку в 2 слоя наружной рабочей поверхности. После укладки роликов в цилиндрические контейнеры проводили засыпку этим же порошковым составом, закрывали слоем асбеста и помещали в реторту вакуумной печи (фиг.1), разогретую до 1000°С, и вакуумным плунжерным насосом создавали вакуум 80 Па. Время выдержки составило 6 часов, далее проводили закалку, высыпая детали из контейнера в машинное масло. Отпуск проводили в малоэнергоемкой печи Пл-10 при 270°С в течение 3 часов.
Обработка позволила сформировать на рабочей поверхности роликов износостойкий, равномерный по глубине карбидный слой повышенной твердости H0,5H=1050-1020 с монотонным снижением к основе Н0,5н 890…795…640…480…(фиг.2×150). Микротвердость, прочность основы превосходили на 20-25% аналогичные физикомеханические свойства, получаемые в известном способе химико-термической обработки. Длительность эксплуатации роликов, вследствие повышения износостойкости, в том числе при повышенной влажности в условиях морского промысла возросла в 1,4-1,5 раза в сравнении со стандартными из сталей Х12, 95Х18. При этом снизились энергозатраты, трудоемкость обработки в условиях тарного комбината на 30-35%, обеспечилась экологическая чистота процесса химико-термической обработки.
Пример 2.
Концевой инструмент, шорожки для снятия и зачистки облоев после горячей штамповки и литья деталей из алюминиевых сплавов типа АЛ-2, АЛ-9, АК-4 изготовляли токарной обработкой с последующей накаткой остроугольной режущей части из стали 20Х13 и 30Х13 и упрочняли карбонитрированием по предложенному способу.
Порошковую смесь из карбамида, трилона-Б, древесного угля, взятых в соотношении 1:1:1, наносили на ленту изоляционную поливинил-хлоридную и проводили обмотку резьбовой, остроугольной, режущей части в один слой. Затем помещали в контейнеры для карбонитрирования, засыпая порошковой смесью этого же состава, и переносили в печь с вакуумной «горячей» ретортой СШОЛ-ВНЦ, разогретую до 980°С, вакуумировали печь до 50 МПа откачкой механическим центробежным насосом. После прогрева до 980°С выдерживали в течение 4 часов и закаливали, разгерметизируя реторту, детали из контейнера охлаждали в масле. В результате обработки на режущих поверхностях получены диффузионные карбидные слои с содержанием карбидов до 85% переменного состава, содержащих (Fe, Сr)7С3, (Fе, Сr)23С6 твердостью Н0,5H 1480-1510. Прочность основного металла составила σв=1580-1600 МПа, что обеспечивало жесткость концевых шорожек при скоростной заточке и при шлифовании тонкостенных деталей из керамик, повышалась чистота, точность обработки. При этом, как показано на фиг.3, фиг.4, микроструктура поверхностей и по всей глубине слоя оптимальна для повышения контактной прочности, износостойкости. Обработка при карбонитрировании в пределах заявляемых температур обработки и времени выдержки 4-6 часов оптимальна для получения карбонитридных слоев с высоким содержанием углерода в карбидах (фиг.4). За пределами заявляемых температур и длительностей выдержки эффект химико-термической обработки существенно снижался.
Предложенный способ позволил за счет температурной активизации поверхностей хлорсодержащим компонентом высокохромистых сталей формировать диффузионные слои с содержанием карбидов до 80-90% (фиг.4). В результате обработки износостойкость шорожек превзошла аналогичные, стандартизованные из У 10, У 12, в 3,5 - 4 раза. Сокращение энергозатрат, удельных затрат на обработку аналогичных деталей в условиях термических участков малых предприятий составило 15-20%.
Пример 3.
Якоря электроклапанные регулирования расхода газов из магнитомягких сталей 16Х-ВИ, механически обработанные для карбонитрирования в порошковой смеси, вначале обматывали по цилиндрической части (фиг.6) поливинилхлоридной лентой с нанесением на липкую часть состава из равных количеств древесного угля, карбамида и трилона-Б. Карбонитрирование вели в вакуумной реторте печи СНОЛ-1,6.2,5.1,0/10И2-М, разогретой до 1000°С, помещая контейнеры в засыпке из порошка этого же состава с плотной упаковкой в рабочее пространство, выдерживая в течение 6 часов в реторте при остаточном давлении 80 Па. Охлаждали контейнеры с якорями выгрузкой из реторты на воздух, а после охлаждения и доводки проводили отпуск при 320°С, 2 часа. Обработка позволила сформировать диффузионный слой толщиной 500-550 мкм микротвердостью H0,5H=630-640, износостойкий при контактном трении, равномерный по толщине, с минимальной зоной 3-6 мкм поверхностного «внутреннего» окисления (фиг.6), что невыполнимо во всех ранее известных способах обработки. Одновременно сердцевина якорей имела крупнозернистую структуру, определяющую оптимальные магнитные свойства, коэрцитивную силу НC=48-50 А/м и магнитную индукцию B50=1,45-1,49 Тл, что позволило иметь ресурс работы клапанов на уровне 107 циклов, что превышает ресурс работы клапанов, обработанных способом, описанным в ближайшем аналоге. Энергозатраты при совмещении отжига на заданные магнитные характеристики с упрочняющей химико-термической обработкой уменьшились в 1,2 раза. Технология позволяла соблюдать экологическую безопасность, была проста в осуществлении, доводка алмазной пастой была минимальной на глубину не более 20 мкм.
Способ карбонитрирования деталей из высокохромистых сталей, включающий помещение деталей в контейнер и их засыпку порошковой смесью из активированного древесного угля, карбамида и трилона-Б при температуре карбонитрирования 960-980°С, отличающийся тем, что используют упомянутую порошковую смесь, в которой компоненты содержатся в соотношении 1:1:1, перед помещением в контейнер с порошковой смесью детали покрывают обмоткой из поливинилхлоридной клейкой ленты, на липкую часть которой предварительно наносят подготовленную для карбонитрирования порошковую смесь, после засыпки деталей в контейнере порошковой смесью его переносят в вакуумную реторту с остаточным давлением 50-80 Па, предварительно разогретую до температуры 980-1000°С, и выдерживают в течение 4-6 ч при температуре карбонитрирования 960-980°С, затем проводят закалку в масле от температуры карбонитрирования, после закалки проводят охлаждение деталей в контейнере на воздухе, затем проводят отпуск на воздухе при температуре 250-320°С в течение 2-3 ч.
www.findpatent.ru