- перлитный,
- мартенситный,
- аустеннтный,
- ферритный.
- двухфазную и
- многофазную.
- Канат стальной гост 2688 80 характеристики
- Стальные канаты
- Труба гофрированная нержавеющая сталь
- Вес стали и алюминия
- Температура закалки и отпуска сталей таблица
- Калькулятор веса труб стальных
- Ферритная нержавеющая сталь
- Как варить 45 сталь
- Хромированная нержавеющая сталь
- Сталь двутавровая
- Сталь 8хф замена
Перлитный класс стали: описание и сварка. Класс стали
Перлитный класс стали: описание и сварка
Перлитный класс стали - это металл, принадлежащий к низколегированному и среднелегированному типу. Чаще всего такое сырье используется в качестве конструкционной или инструментальной стали. Перлитная и ферро-перлитная структура данного материала после прохождения отжига или же после проката отлично поддается обработке любыми режущими инструментами.
Общее описание стали
Для того чтобы перлитный класс стали имел достаточно высокие механические параметры эксплуатации, необходимо провести закалку. Чаще всего для этого используется масло, а также нужно правильно провести процедуру отпуска. Благодаря такой обработке, удается повысить такой параметр, как прочность, к примеру, или износостойкость и твердость.
Стали перлитного класса выделяются минимальным содержанием легирующих элементов. Среднее содержание в мартенстиных сталях, а наибольшее количество в аустенитных.
Из-за малого количества добавок и модификаторов такие свойства, как жаростойкость, к примеру, также достаточно малы потому, что недостаточно хрома в составе. Использовать такой материал с температурой более 550-580 градусов по Цельсию нельзя.
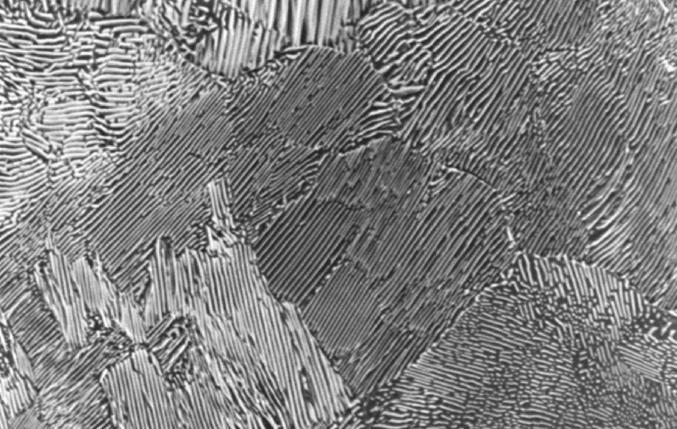
Марки и характеристики
Разнообразие марок стали перлитного класса не слишком большое, всего их около восьми. Среди них есть 12Х1МФ (12ХМФ), 20Х1М1Ф1ТР (ЭП182) и другие. На сегодняшний день используется то название марок, которое идет первым. Маркировка, указанная в скобках - это старая, однако она все еще может кое-где встречаться. Стоит отметить, что сталь данного класса при содержании углерода до 0,35% от всей массы и с количеством легирующих элементов до 2-5% достаточно популярна. Основная причина широкого распространения - это дешевизна и относительно неплохие механические качества.
Сталь перлитного класса чаще всего используется, как конструкционный материал. Стоит также отметить, что свариваемость стали с содержанием углерода до 0,35% и легирующими элементами в пределах 3-4%, достаточно неплохая.
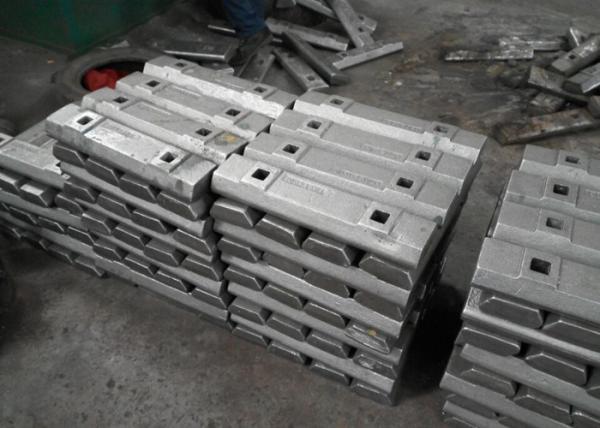
Сварка перлитной стали
Стоит отметить, что при сварке сталей перлитного класса наиболее выгодным будет использовать элементы, которые применяются при сварке стали с низким коэффициентом легирования. Если для этого используется ручная электрическая дуговая сварка, то лучше всего применять такие электроды, которые имеют фтористо-кальциевое покрытие. В таком случае будет обеспечена высокая устойчивость металла шва против таких дефектов, как кристаллизация, к примеру. Кроме того, прочность сварного шва также будет достаточно удовлетворительной.
Что касается режимов сварки, а также температуры, которая должна использоваться для такого материала, то наиболее выгодно использовать те варианты, которые подходят для работы с высоколегированной сталью.
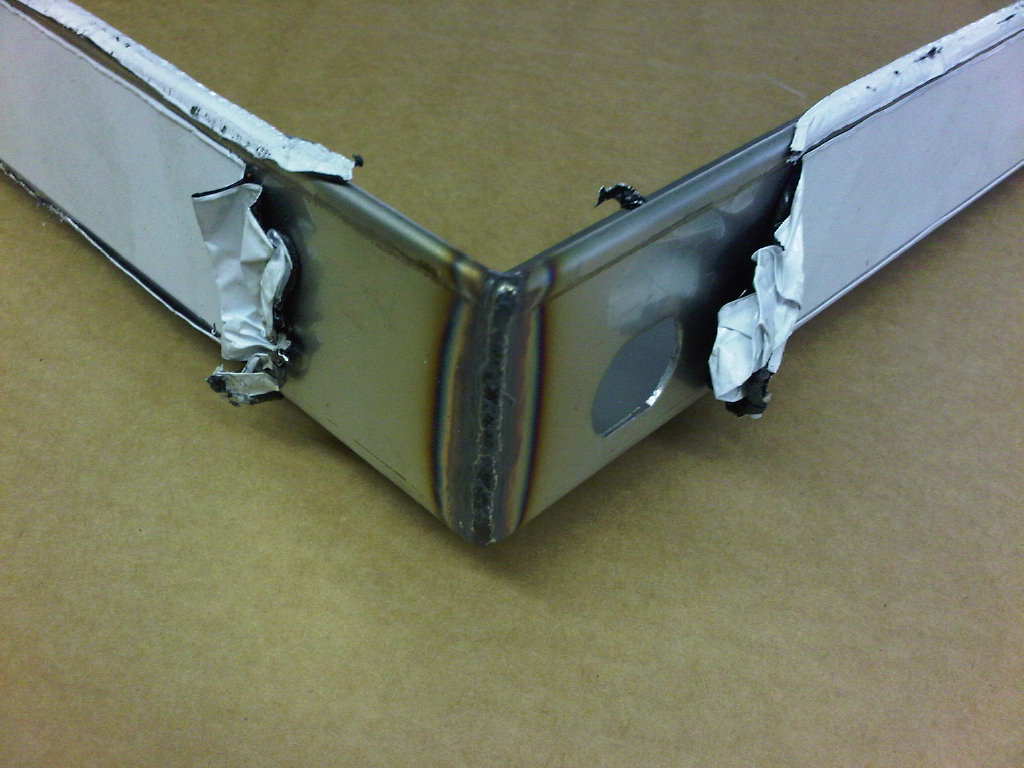
К примеру, если марка перлитной стали 15ХМ или 12ХМ, то температура во время сварки должна быть примерно 400-450 градусов по Цельсию. Для работы применяется ручная электродуговая сварка. В качестве электродов чаще всего выбираются такие марки, как Э42А или проволока типа Св-08А. Что касается процедуры отпуска после сварки, то ее можно не проводить вовсе или же проводить при температуре 630-650 градусов по Цельсию.
fb.ru
Структурные классы легированной стали
Легированные стали применяются очень широко. Их использование обусловлено, как правило, теми свойствами, которые им придают специально добавленные легирующие элементы. Легированные стали в зависимости от примесей и их количества имеют различную структуру, определяющую не только их свойства, но также и классификацию легированной стали на различные структурные классы, которых насчитывается пять. Структурные классы легированной стали включают в себя перлитный, мартенситный, аустснитный, ферритный и карбидный классы. Легированная сталь перлитного класса имеет структуру перлита, а также может иметь структуру одной из разновидностей перлита: сорбита или троостита. Стали мартенситного класса имеют пониженную скорость закалки, а стали аустснитного класса имеют пониженную температуру распада аустснита – он сохраняется даже при комнатной температуре. Стали ферритного класса отличаются тем, что способны сохранять свою структуру при очень высоких температурах, а также при расплавлении и последующем охлаждении, причем с любой скоростью. Структура карбидных легированных сталей отличается повышенным содержанием различного рода карбидообразующих элементов.
Высокопрочные стали
Высокопрочными называют стали, имеющие предел прочности более 1500 МПа, который достигается подбором химического состава и оптимальной термической обработки. Такой уровень прочности можно получить в среднеуглеродистых легированных сталях, (30ХГСН2А,40ХН2МА), применяя закалку с низким отпуском (при температуре 200…250oС) или изотермическую закалку с получением структуры нижнего бейнита.
После изотермической закалки среднеуглеродистые легированные стали имеют несколько меньшую прочность, но большуюпластичность и вязкость. Поэтому они более надежны в работе, чем закаленные и низкоотпущенные. При высоком уровне прочности закаленные и низкоотпущенные среднеуглеродистые стали обладают повышенной чувствительностью к концентраторам напряжения, склонностью к хрупкому разрушению, поэтому их рекомендуется использовать для работы в условиях плавного нагружения.
Легирование вольфрамом, молибденом, ванадием затрудняет разупрочняющие процессы при температуре 200…300 oС, способствует получению мелкого зерна, понижает порог хладоломкости, повышает сопротивление хрупкому разрушению.
Стали 30ХГСА, 38ХН3МА после низкотемпературной термомеханической обработки имеют предел прочности 2800 МПа,относительное удлинение и ударная вязкость увеличиваются в два раза по сравнению с обычной термической обработкой. Это связано с тем, что частичное выделение углерода из аустенита при деформации облегчает подвижность дислокаций внутри кристаллов мартенсита, что способствует увеличению пластичности.
Износостойкие стали
характеризуются высокой устойчивостью против истирания. В эту группу входят шарикоподшипниковые, высокомарганцовые и другие стали.
Износостойкие стали способны сопротивляться процессу изнашивания.
Износостойкие стали могут быть весьма различными по своим механическим свойствам и строению. Различают износ контактный и абразивный. Контактный износ имеет место при трении одной поверхности о другую, сопровождаемом давлением или ударами. Абразивным износом называют истирание металлической поверхности в результате трения о нее твердых частиц, движущихся в струе жидкости или газа вдоль этой поверхности. [3]
Износостойкие стали обладают большим сопротивлением износу. Износостойкость сталь приобретает в результате легирования ее марганцем. Наиболее распространенной маркой стали является высокомарганцевая сталь Г13 содержащая 1 0 - 1 3 % углерода, 12 - 14 % марганца и другие элементы. Эта износостойкая и одновременно высокопластичная сталь применяется для изготовления звеньев гусениц ( траки), козырьков ковшей экскаваторов и землечерпалок, стрелок и крестовин рельсов, а также других деталей, работающих на удар и подверженных интенсивному износу. [4]
Износостойкие стали обладают большим сопротивлением износу. Износостойкость сталь приобретает в результате легирования ее марганцем. [5]
Большинство износостойких сталей имеет мартенситную основу с равномерно распределенными включениями карбидов. Для сталей, работающих в условиях высоких циклических контактных нагрузок ( шарикоподшипниковая сталь), особую роль играет при этом тонкость строения мартенсита, дисперсность и равномерность распределения карбидной фазы. [6]
Коррозионноустойчивые стали
Устойчивость против коррозии повышается при введении в состав стали хрома,алюминия, кремния. Эти элементы образуют непрерывную прочную оксидную пленку и повышают электродный потенциал, т. е. увеличивают электроположительность стали. Алюминий и кремний повышают хрупкость стали и применяются реже хрома. При содержании хрома более 12 % сталь резко изменяет электродный потенциал с электроотрицательного (–0,6 В) на электроположительный (+0,2 В). На поверхности образуется плотная защитная пленка оксида Сr2О3.
Сталь, содержащая 12 – 14 % Сr, устойчива против коррозии в атмосфере, морской воде, ряде кислот, щелочей и солей. Кроме хрома, в состав коррозионностойких сталей вводят также другие элементы – чаще никель. С ростом содержания хрома коррозионная стойкость стали растет.
Коррозионностойкие стали (corrosion-resistant steel) обычно делят на хромистые ферритные, содержащие 12 – 25 % Сr и 0,07 – 0,2 % С и хромистые мартенситные, содержащие 12 – 18 % Сr и 0,15 – 1,2 % С, а также аустенитные стали, содержащие 12 – 18 % Сr, 8 – 30 % Ni и 0,02 – 0,25 % С.
Хромистые стали коррозионностойки при температуре до 300°С в водопроводной воде, влажной атмосфере, растворах азотной кислоты и многих органических кислотах. В морской воде хромистые стали подвержены коррозионному растрескиванию под напряжением.
Содержание углерода в коррозионностойких аустенитных сталях ограничено, и желательно, чтобы оно было ниже предела растворимости углерода в легированном никелем аустените при 20°С, составляющего 0,04 %. Присутствие в стали более высоких концентраций углерода может приводить к образованию карбидов хрома типа Сr23С6, вследствие чего твердый раствор обедняется хромом и создается двухфазная структура. При этом снижается коррозионная стойкость стали. Для предотвращения образования карбидов хрома, особенно при технологических нагревах, связанных с проведением операций сварки или пайки и опасностью возникновения межкристаллитной коррозии, в сталь вводят дополнительно титан, ниобий или тантал. Эти элементы связывают углерод в карбиды типа TiC, NbC, TaC, оставляя хром в твердом растворе. Необходимое количество титана для введения в сталь определяют по формуле
Ti = (С – 0,02)*5 - (6.9)
где С – содержание углерода в стали.
Стали, не склонные к межкристаллитной коррозии, называют стабилизированными. Эффект стабилизации может быть достигнут, помимо введения сильных карбидообразующих элементов, снижением содержания углерода ниже 0,04 %.
Хромоникелевые коррозионностойкие стали содержат дефицитный и дорогостоящийникель и поэтому имеют высокую стоимость. В ряде случаев применяют более дешевые стали, в которых весь никель или часть его заменены марганцем. Например, до температур –196°С и в слабоагрессивных средах вместо стали 12Х18Н10Т может быть использована сталь 10Х14Г14Н4Т.
Азот повышает стабильность аустенита, поэтому для повышения коррозионной стойкости можно использовать более высокие концентрации хрома и молибдена, не увеличивая склонность стали к выделению интерметаллидных фаз. Примером может служить сталь 03Х20Н16АГ6, используемая в криогенной технике.
Жаропрочные стали
Жаропро́чная сталь — это вид стали, который используется в условиях высоких температур (от 0,3 части от температуры плавления) в течение определённого времени, а также в условиях слабонапряжённого состояния.
Главной характеристикой, определяющей работоспособность стали, является жаропрочность.
Жаропрочность — это способность стали работать под напряжением в условиях повышенных температур без заметной остаточной деформации и разрушения. Основными характеристиками жаропрочности являются ползучесть и длительная прочность. Сопротивление стали разрушению при длительном воздействии температуры характеризуется длительной прочностью.
Длительная прочность — это условное напряжение, под действием которого сталь при данной температуре разрушается через заданный промежуток времени
Жаропрочные свойства в первую очередь определяются температурой плавления основного компонента сплава, затем его легированием и режимами предшествующей термообработки, определяющими структурное состояние сплава. Основой жаропрочных сталей являются твёрдые растворы или пересыщенныё раствор, способные к дополнительному упрочнению вследствие дисперсионного твердения.
Для кратковременной службы применяются сплавы с высокодисперсным распределением второй фазы, а для длительной службы — структурно-стабильные сплавы. Для длительной службы выбирается сплав несклонный к дисперсионному твердению.
Самым распространённым легирующим элементом в жаропрочных сталях является хром (Cr), который благоприятно влияет на жаростойкостьи жаропрочность.
Высоколегированные жаропрочные стали из-за различных систем легирования относятся к различным классам:
ферритные (08Х17Т, 1Х13Ю4, 05Х27Ю5),
мартенситные (20Х13, 30Х13),
мартенситно-ферритные (15Х12ВН14Ф),
аустенитные (37Х12Н8Г8МФБ).
Внутри каждого класса различаются стали с различным типом упрочнения:
карбидным,
интерметаллидным,
смешанным (карбидно-интерметаллидным).
Для котельных установок, работающих длительное время (10 000—100 000 часов) при температурах 500—580 °C, рекомендуются сталиперлитного класса, введение молибдена в которые повышает температуру рекристаллизации феррита и тем самым повышает его жаропрочность.
Однако бо́льшую часть жаропрочных сталей, работающих при повышенных температурах, составляют аустенитные стали на хромоникелевой и хромомарганцевой основах с различным дополнительным легированием. Эти стали подразделены на три группы:
гомогенные (однофазные) аустенитные стали, жаропрочность которых обеспечивается в основном легированностью твёрдого раствора;
стали с карбидным упрочнением;
стали с интерметаллидным упрочнением.
infopedia.su
Сталь - перлитный класс - Большая Энциклопедия Нефти и Газа, статья, страница 1
Сталь - перлитный класс
Cтраница 1
Стали перлитного класса - это низко - и среднелегированные, наиболее распространенные как конструкционные, так и инструментальные стали. В состоянии проката или после отжига они благодаря перлитной или ферритно-перлитной структуре хорошо обрабатываются режущим инструментом. Для получения высоких механических свойств, твердости и износостойкости их подвергают закалке, большей частью в масле, и соответствующему отпуску. [1]
Стали перлитного класса характеризуются относительнее малым содержанием легирующих элементов, мартенситного - более значительным и, наконец, аустенитного - высоким содержанием легирующих элементов. [3]
Стали перлитного класса, как не содержащие большого количества хрома, естественно, не обладают высокой жаростойкостью и их нельзя применять при температурах выше 550 - 580 С. [5]
Стали перлитного класса выпускаются восьми марок: 12MJ 12Х1МФ ( 12ХМФ), 20Х1М1Ф1ТР ( ЭП182), 20Х1М1Ф1Б1 ( 20ХМФБ, ЭП44 25ХМФ ( ЭИ10), 25Х2М1Ф ( ЭИ723), 18ХЗМВ ( ЭИ578), 20ХЗМВФ ( ЭИ415, ЭИ579; В скобках указано старое название марок. [6]
Стали перлитного класса при содержании 0 1 - 0 8 % С имеют обычно не более 2 - 5 % специальных примесей и структуру, аналогичную углеродистой стали, а именно: феррит и перлит в доэвтектоидной стали, перлит в эвтектоидной стали и перлит и цементит ( карбиды) в заэвтектоидной стали. [7]
Стали перлитного класса с содержанием углерода не выше 0 35 % и легирующих элементов в сумме до 2 - 5 % пользуются широким распространением благодаря повышенным механическим свойствам и относительно невысокой их стоимости. [8]
Стали перлитного класса являются в основном конструкционными, мартенситного и карбидного - инструментальными, а феррит-ного и аустенитного - сталями с особыми химическими и физическими свойствами. [9]
Стали перлитного класса с содержанием углерода не выше 0 35 % и легирующих элементов в сумме до 3 - 4 % свариваются в большинстве случаев вполне удовлетворительно. [10]
Сталь перлитного класса гораздо больше других распространена в машиностроении. Она содержит небольшое количество легирующих элементов, хорошо поддается обработке режущим инструментом и после окончательной термической обработки весьма значительно улучшает свои механические свойства. [11]
Стали перлитного класса наиболее распространены. Структура сталей этого класса после нормализации или отжига состоит из феррита или перлита или феррита и карбидов. Такие стали содержат небольшое количество легирующих примесей и относятся к низко - и среднелегированным сталям. Обладают хорошей обрабатываемостью режущим инструментом. Многие стали этого класса, содержащие 0 / 15 - 0 2 % С, хорошо свариваются. [12]
Стали перлитного класса являются низколегированными сталями. [14]
Стали перлитного класса используют для изготовления крепежа, труб, паропроводов, пароперегревателей и коллекторов энергетических установок, длительно работающих при температурах 500 - 550 С. Стали этого класса используют в закаленном или нормализованном и высокоотпущенном состоянии. [15]
Страницы: 1 2 3 4
www.ngpedia.ru
Структуры сталей и их свойства, классификация сталей по структуре
Структуры сталей и их свойства
Феррит — твердый раствор углерода (обычно низкой концентрации, порядка сотых долей процента) и других элементов в α-железе α — Fe (почти чистое железо α). Феррит имеет кубическую объемноцентрированную решетку. Он ферромагнитен (ниже 769 °С), мягок и пластичен.
Аустенит — твердый раствор углерода и легирующих элементов в γ-железе γ — Fe. Кристаллическая решетка — куб с центрированными гранями. Аустенит немагнитен, плотность его больше, чем плотность других составляющих стали.
Сорбит, тростит, мартенсит относятся к неравновесным структурам стали.
Сорбит — продукт превращения (распада) аустенита в интервале (районе) температур 600 — 650 °С, смесь феррита и сфероидального цемента, отличающаяся от перлита большей дисперсностью составляющих и более высокой твердостью.
Тростит — продукт превращения аустенита в интервале температур 500 — 600 °С, смесь феррита и цементита еще большей дисперсности и твердости, чем сорбит.
Мартенсит — твердый раствор углерода и других элементов в γ-железе, полученный в результате бездиффузнонного превращения. Мартенсит обладает высокой твердостью, ферромагнитен, имеет игольчатое строение — содержание углерода в мартенсите равно исходному его содержанию в аустените.
По структуре стали подразделяют на следующие классы:
Если в структуре преобладают две и более фаз, то сталь разделяют на:
Стали перлитного класса имеют невысокую устойчивость переохлажденного аустенита. При охлаждении на воздухе они приобретают структуру перлита, сорбита или тростита, в которой могут присутствовать также избыточные феррит и карбиды. К сталям перлитного класса относятся углеродистые и низколегированные. Эта большая группа дешевых, широко применяемых сталей для деталей машин и аппаратов, для работы при нормальной или повышенной температуре (не выше 45 °С) и в неагрессивных средах.
Стали мартенситного класса отличаются высокой устойчивостью переохлажденного аустенита; при охлаждении на воздухе они закаливаются на мартенсит. К этому классу относятся средне- или высоколегированные стали.
Стали аустенитного класса из-за повышенного количества никеля или марганца (обычно в сочетании с хромом) имеют интервал мартенситного превращения ниже 0 °С и сохраняют аустенит при температуре 20 — 25 °С.
Для сталей ферритного класса микростроение, размеры зерна и субструктура феррита зависят от условий его образования при полиморфном γ—α превращении. При небольшом переохлаждении образуются приблизительно равноосные, полиэдрические зёрна; при больших переохлаждениях и наличии легирующих элементов (Cr, Mn, Ni) феррит возникает по мартенситному механизму и вследствие этого упрочняется. Укрупнение зёрен аустенита часто приводит к образованию при охлаждении видманштеттова феррита, особенно в литых и перегретых сталях. Выделение доэвтектоидного феррита происходит преимущественно на границах аустенитных зёрен.
material.osngrad.info