- Рассматриваемая сталь относится к конструкционной легированной группе. Легированная группа характеризуется содержанием большого количества примесей, которые определяют изменение эксплуатационных качеств, в том числе твердости.
- Используется в промышленности при создании валов, осей, штоков, оправок, реек, болтов, втулок, шестерней и других деталей.
- Показатель твердости до проведения термической обработки HB 10-1 = 217 Мпа.
- Температура критических точек определяет момент, при котором сталь 40Х начинает терять свои качества из-за термической обработки: c1= 743 , Ac3(Acm) = 815 , Ar3(Arcm) = 730, Ar1 = 693.
- При температуре отпуска 200 °С HB = 552.
- скорости нагрева металла 40Х;
- времени выдержки;
- от скорости охлаждения.
- разогревается электропечь;
- следует провести разогрев до 860 °C, для чего в некоторых случаях необходимо 40 минут;
- время, необходимое для аустенизации, после которого проводится охлаждение, составляет 10-15 минут. Равномерный желтый цвет изделия – признак правильного прохождения процесса закалки 40Х;
- завершающим этапом становится охлаждение в ванной с водой или другой жидкостью.
- Низкий отпуск определяет разогрев поверхности до 250 °С с выдержкой и охлаждение на воздухе. Применяется для снятия напряжений и незначительного повышения пластичности практически без потери твердости. В случае конструкционного сплава применяется крайне редко.
- Средний отпуск позволяет нагревать изделие до 500 °С. В этом случае вязкость значительно повышается, а твердость снижается. Используют этот метод термообработки при получении пружин, рессор и некоторого инструмента.
- Высокий позволяет раскаливать деталь до 600 °С. В этом случае происходит распад мартенсита с образованием сорбита. Подобная структура представлена лучшим сочетанием прочности и пластичности. Также повышается показатель ударной вязкости. Используют этот метод термообработки для получения деталей, применяемых при ударных нагрузках.
- Отжиг стали 45
- Закалка стали 45
- Отпуск стали 45
- диффузионный отжиг
- полный отжиг
- неполный отжиг
- изотермический отжиг
- рекристализационный
- печи с принудительной циркуляцией воздуха;
- специальные ванны с селитровым раствором;
- специальные ванны с минеральным маслом;
- ванны, заполненные расплавленной щелочью.
- Высокий. Температура нагрева стали составит от +350°С до +600°С до критической отметки. Как правило, такой метод используют для металлических конструкций.
- Средний. Температура обработки составляет от +350°С до +500°С. Этот способ по большей части используется для пружинных изделий и рессор.
- Низкий. Температура нагрева заготовки не превышает +250°С. Подобный способ принято задействовать для достижения высокой прочности и износостойкости.
Образцы, закаленные в воде, загрузить по одному каждой марки в печи с температурами 200, 400 и 600°С.
Выдержать образцы в печах. Время берется из расчета 2-3 мин. на 1мм толщины образца.
Выгрузить детали из печи и охладить на воздухе.
Измерить твердость.
Результаты измерения занести в таблицу 5.
Теоретическая часть с рисунками 1 и 2.
Таблица полученных значений твердости сталей при охлаждении в воде, масле и на воздухе.
Графическая зависимость твердости сталей от скорости охлаждения.
Таблица значений твердости сталей после отпуска при различных температурах.
Графическая зависимость твердости сталей от температуры отпуска.
Выводы.
- Калькулятор веса труб стальных
- Ферритная нержавеющая сталь
- Как варить 45 сталь
- Хромированная нержавеющая сталь
- Сталь двутавровая
- Сталь 8хф замена
- Красностойкость быстрорежущих сталей это
- Стали классификация и маркировка
- Как удалить цинковое покрытие со стали
- Нержавеющая сталь свойства магнитные
- Наплавка латуни на сталь
Отпуск закаленных сталей. Температура закалки и отпуска сталей таблица
твердость, режимы, время, температура, технология
При сильном нагреве практически все материалы изменяют свои физические характеристики. В некоторых случаях нагрев проводится целенаправленно, так как подобным образом можно улучшить некоторые эксплуатационные качества, к примеру, твердость. Термическая обработка на протяжении многих лет используется для повышения твердости поверхности стали. Выполнять закалку следует с учетом особенностей металла, так как технология повышения твердости поверхности создается на основании состава материала. В некоторых случаях провести закалку можно в домашних условиях, но стоит учитывать, что сталь относиться к труднообрабатываемым материалам и для придания пластичности нужно проводить сильный нагрев до высоких температур при помощи определенного оборудования. В данном случае рассмотрим особенности нагрева стали 40Х для повышения пластичности и проведения закалки или отпуска.

Круг из стали 40Х
Сталь 40Х
Как ранее было отмечено, для правильного проведения закалки и отпуска стали следует учитывать ее состав и многие другие особенности. Выбрать правильно режимы термической обработки можно с учетом следующей информации:
Расшифровка стали 40Х говорит о том, что в составе материала находится 0,40% углерода и 1,5% хрома.
Скачать ГОСТ 4543-71 «Прокат из легированной конструкционной стали 40Х»
Процесс закалки
Процесс обработки высокой температурой стали 40Х и иного сплава называют закалкой. Стоит учитывать, что нагрев выполняется до определенной температуры, которая была определена путем многочисленных испытаний. Время выдержки, после которого проводится охлаждение, а также другие моменты можно узнать из специальных таблиц. Провести нагрев в домашних условиях достаточно сложно, так как в рассматриваемом случае нужно достигнуть температуры около 800 градусов Цельсия.

Химический состав стали 40Х
Результатом сильного нагрева и выдержки металла 40Х на протяжении определенного времени с последующим резким охлаждением в воде становится повышение твердости и уменьшение пластичности. При этом результат зависит от нижеприведенных показателей:
При проведении работы в домашних условиях следует учитывать температуру обработки и время охлаждения.

Механические свойства стали 40Х в зависимости от температуры отпуска
При выборе метода разогрева поверхности следует обратить внимание на ТВЧ. Этот метод более популярен, чем обычная объемная обработка по причине достижения необходимой температуры за более короткое время.
В домашних условиях ТВЧ используется крайне редко. После проведения работы при использовании ТВЧ повышается эксплуатационная прочность детали, что связано с появлением поверхностных сжимающих напряжений.
Провести закалку 40Х на примере изделия болта М24 можно следующим образом:
Определить самостоятельно момент, после которого следует охладить металл, в промышленных и домашних условиях невозможно. Именно поэтому по проведенным исследованиям было принято, что для нагрева металла в электропечах необходимо 1,5-2 минуты на один миллиметр, после чего структура может быть перегрета.
Определение твердости проводится по методу Роквелла. Улучшение, проведенное путем отпуска или закалки, можно измерить при помощи обозначения HRC. Стандартное обозначение HR, к которому проводится добавление буквы в соответствии с типом проведенного испытания. Обозначение HRC наиболее часто встречается, последняя буква означает использование алмазного конуса с углом 1200 при испытании.
Отпуск и нормализация
Отпуск проводится непосредственно сразу после завершения закалки, так как есть большая вероятность возникновения трещин в структуре. Разогревается изделие в этом случае до точки ниже критической, проводится выдерживание на протяжении определенного промежутка времени и выполняется охлаждение. Отпуск обеспечивает улучшение структуры, устраняет напряжение и повышает пластичность, устраняет хрупкость стали 40Х.

Механические свойства стали 40Х в зависимости от температуры отпуска
Различают три вида рассматриваемой термообработки:
Еще одним видом распространенной термообработки является нормализация. Зачастую нормализация проводится путем разогрева металла до верхней критической точки с последующей выдержкой и охлаждением в обычной среде, к примеру, на открытом воздухе. Проводят нормализацию для придания мелкозернистой структуры, что приводит к повышению пластичности и ударной вязкости.
Если вы нашли ошибку, пожалуйста, выделите фрагмент текста и нажмите Ctrl+Enter.
stankiexpert.ru
Термообработка стали 45
03.04.2018

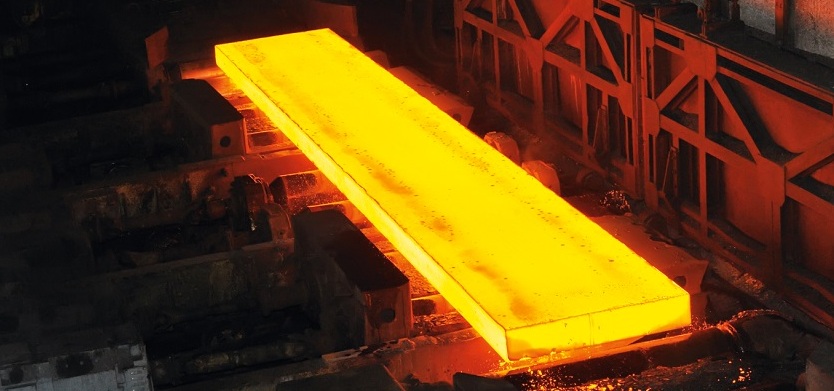
Термообработка стали 45, так же как и термическая обработка любой другой марки стали выполняется для улучшения технических характеристик данного материала. Такая обработка подразумевает первоначальный нагрев металла и последующее его охлаждение. Собственно, в зависимости от времени нагрева материала и скорости охлаждения, термообработка стали 45 и других марок подразделяется на 3 последовательно выполняемых операции:
Отжиг стали 45 — это нагрев материала в специальной печи до очень высокой температуры и последующее его охлаждение, которое выполняется естественным образом, то есть вместе с печью. Существует отжиг первого рода, при котором нагрев идет до критических значений, но не превышает их. Также существует и отжиг второго рода, при котором температура уже превышает критическую отметку и приводит к некоторым изменениям в структуре.
Так или иначе, любой из данных способов позволяет избавиться от неоднородности состава, а также снять внутреннее напряжение материала и достичь зернистой структуры. Кроме того, проведение отжига стали 45 поможет снизить твердость сплава, что значительно облегчит в дальнейшем процесс переработки. Примечательно, что отжиг второго рода подразделяется на несколько следующих категорий, различающихся по их назначению и исполнению:
Как правило, для углеродистых сталей применяется полный отжиг. Суть данной технологии состоит в том, что заготовки нагреваются до температуры, которая превышает критическую отметку (верхняя точка Ас3) примерно на значение от +30°С до +50°С. После этого сталь 45 охлаждают с медленной скоростью от +150°С до +200°С до тех пор, пока ее температура не сравняется со значением температуры в рабочем интервале от +500°С до +550°С.
Кстати говоря, при отжиге первого и второго рода охлаждение материала происходит в печи, в которой был произведен нагрев. Если же процесс охлаждения производят уже на открытом воздухе, то такая технология будет называться не отжиг стали 45, а нормализация. Поскольку при нормализации стали охлаждение происходит быстрее, перлит получает тонкое строение и наибольшую твердость. Поэтому нормализованная сталь тверже отожженной.
Закалка стали 45
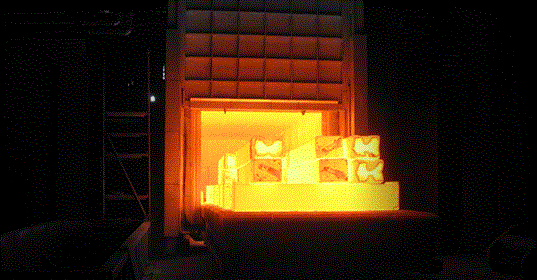
В целом, отжиг стали или же ее нормализация являются подготовкой сплава к последующим процессам термообработки. Вторым по счету процессом обработки идет закалка стали 45. С виду может показаться, что этот этап полностью дублирует отжиг и нормализацию: Закалка стали 45 также состоит из двух основных технологических операций: нагрева и охлаждения. Однако у него имеются свои довольно важные отличительные характеристики.
Если быть точнее, то этой важной отличительной чертой будет скорость охлаждения стали. В случае с закалкой стали 45 заготовка сперва нагревается до температуры, которая превышает критическую. После этого сталь будет сразу же охлаждена в специальной жидкости. В роли такой жидкости может выступать чистая вода, вода с растворами солей, вода с содержанием в составе 5%-й каустической соды, либо же различные минеральные масла (рис. 1)
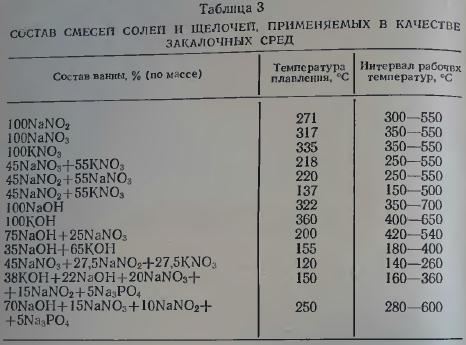
Закалка стали 45 в воде производится при температуре жидкости от +20°С до +30°С. Если в качестве закалочной среды используют раствор каустической соды, то его температура будет составлять от +50°С до +60°С. Температура закалки стали 45, при которой этот материал помещают в охлаждающую жидкость, составляет от +820°С до +860°С. Визуально подобные температуры соответствует диапазону от светло-красного до темно-оранжевого цвета.
Нагрев стали до этих значений обычно выполняется в специальных печах. Но в некоторых случаях также применяется закалка стали 45 токами высокой частоты (ТВЧ). Между этими двумя методами существует разница во времени выдержки заготовки. Это обусловлено тем, что данные установки имеют различные режимы нагрева. При этом с помощью ТВЧ сталь 45 будет нагрета за более быстрый промежуток времени в сравнении с обычной печью.
Устройство для нагрева стали |
Температура нагрева стали |
Печь |
От +820°С до +860°С |
ТВЧ |
От +880°С до +920°С |
Несмотря на то, что при использовании ТВЧ нагрев стали 45 нужно выполнять до чуть более высоких температур, как такового перегрева материала не происходит. Размер и структура у зерна остается прежним, так как для нагрева через ТВЧ требуется намного меньше времени. Кстати говоря, с помощью проведения закалки токами высокой частоты, твердость стали 45 возрастает по шкале Роквелла (HRC) возрастает приблизительно на 2-3 единицы.
При нагреве стали 45 до температуры, превышающей критическое значение на отметку в +30°С — +50°С, материал достигнет своего аустенитного состояния. Иначе говоря, атомная решетка железа (Fe) изменит объемно-центрированной вид на решетку гранецентрированной формы. Углерод (С), содержащийся в перлите как кристаллы соединения Fe3C (цементита) примет вид твердого раствора — атомы внедрятся в гранецентрированную решетку.
После помещения раскаленного материала в охлаждающую ванну для закалки, температура стали 45 очень быстро понижается до значения комнатной от +20°С до +25°С. Само собой, в связи с этим в структуре сразу происходит процесс обратной перестройки атомной решетки металла — из гранецентрированной она возвращается в исходную объемно-центрированную. Именно это и придает итоговому материалу высокую твердость и прочность.
Дело в том, что при комнатной температуре рабочей среды атомы будут иметь крайне малую степень подвижности. Поэтому при резком охлаждении они попросту не успевают выйти из состояния раствора и образовать цементит. Получается, что сам углерод силой удерживается в решетке железа, тем самым образовывая перенасыщенный твердый раствор. В решетке при этом создается избыточное внутреннее напряжение от атомов углерода.
Они попросту распирают решетку, за счет чего она вытягивается вдоль одного направления. Таким образом, все ячейки из кубической формы переходят в тетрагональную. Иначе говоря, ячейки решетки образуют форму прямоугольной призмы (рис. 2). Естественно, это влияет на структуру материала, которая становится игольчатой. Подобную игольчатую конфигурацию у материала принято называть специальным термином — мартенсит.

Сами кристаллы мартенсита имеют вид пластин с небольшой толщиной. Если рассматривать данные пластины в поперечном сечении микрошлифа, то они будут иметь форму игл. Кстати, раствор мартенсит отличается достаточно высокими показателями по твердости и прочности. В первую очередь, это объясняется тем, что удельный объем мартенсита будет чуть больше в сравнении с удельным объемом аустенита, из которого он образован.
Это объясняется тем, что образование самого мартенсита обуславливается возникновением в кристаллах мартенсита множества дислокаций, которые образуются за счет большого числа внутренних напряжений. Напряжения вызваны тем, что возникающая пластина мартенсита воздействует на аустенит, который, в свою очередь, отвечает уже обратным сопротивлением к мартенситу, создавая тем самым ответное давление к данной пластине.
Таким образом, при попытке деформировать закаленную сталь с мартенситной структурой, можно встретить серьезное препятствие. Этим препятствием будут движущиеся в различных направлениях дислокации, которые взаимно блокируют друг друга, не давая перемещаться. Именно эти препятствия передвижения дислокаций увеличивают сопротивление деформации материала, соответственно, увеличивая степень твердости и прочности.
Кроме того, с учетом воздействия внутренних напряжений, кристаллы мартенсита образуют раздельные блоки (рис. 3). При этом те плоскости, которые должны быть параллельными в пределах одного кристалла, на самом деле имеют искажение под небольшим углом. Но такие искажения у атомной решетки как раз и оказывают препятствие к перемещению дислокаций. За счет этих особенностей мартенсита сталь и имеет высокую прочность.
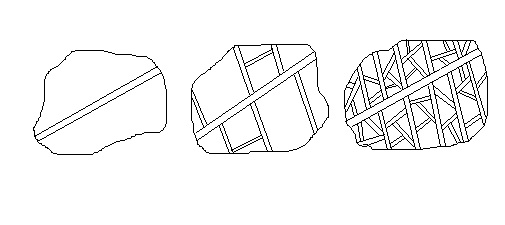
Отпуск стали 45
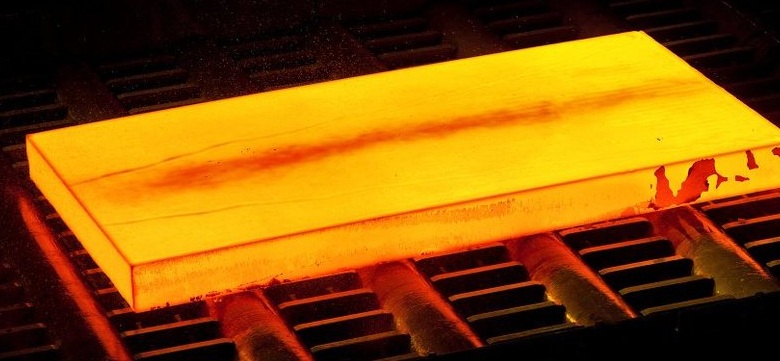
Отпуск стали 45 производят сразу после этапа закалки. Эта разновидность термообработки нужна для того, чтобы существенно уменьшить или полностью снять остаточное напряжение в материале, которое появилось после изменения структуры посредством его закаливания. В целом, отпуск стали 45 позволяет также повысить вязкость заготовок и уменьшить степень их хрупкости. Однако этот процесс немного уменьшает твердость стали.
Технология процесса отпуска стали 45, в зависимости от температуры, выполняется через:
Принцип отпуска стали 45 состоит в том, что материал первоначально нагревают до отметки ниже, чем критический уровень, а после этого охлаждают. Однако такой режим термической обработки имеет несколько различных способов проведения, которые будут отличаться друг от друга в зависимости от скорости охлаждения заготовки и температуры её нагрева. Отпуск углеродистых сталей принято классифицировать на 3 следующие категории:
Таблица значений термической обработки стали 45
Марка стали |
Твёрдость (HRC) |
Температура закалки, °С |
Температура отпуска, °С |
Температура закалки ТВЧ, °С |
Температура отжига, °С |
Среда закалки |
Сталь 45 |
20…25 |
820…860 |
550…600 |
|
|
Вода |
20…28 |
550…580 |
|
|
|||
24…28 |
500…550 |
|
|
|||
30…34 |
490…520 |
|
|
|||
42…51 |
180…220 |
|
|
|||
49…57 |
200…220 |
880…920 |
|
|||
До 22 |
|
|
780…860 |
Перейти в каталог
s-agroservis.ru
Отпуск закаленных сталей
Отпуск - процесс, обусловливающий превращение неустойчивых структур закаленной стали в более устойчивые.
Отпуск осуществляется путем нагрева закаленных сталей до заданных температур, лежащих ниже Ас1. При отпуске с повышением температуры происходит превращение по схеме мартенсит-троостит-сорбит. Чем выше температура нагрева, тем более равновесна будет получаемая структура, меньше внутренние напряжения, выше ударная вязкость (рисунок 4).
Рисунок 4 – Влияние температуры отпуска на механические свойства углеродистой стали |
В процессе отпуска также различают три периода – нагрев, выдержку при заданной температуре и охлаждение.
Время нагрева с выдержкой можно принять из расчета 2-3 мин на 1мм толщины детали. Для углеродистых сталей охлаждение после отпуска можно проводить на воздухе.
Порядок выполнения работы Закалка
1.Загрузить по 5 образцов каждой марки стали в печи с заданными температурами;
для стали марки 40 температура нагрева 830-850°С;
для стали марки У8 температура нагрева 750-770°С.
2. Выдержать образцы в печи при заданной температуре. Время равно сумме первого и второго периода.
3. По окончании выдержки охладить образцы в соответствующих средах.
Таблица 3 – Распределение образцов
Марка стали | Количество образцов, охлаждаемых: | ||
в воде | в масле | на воздухе | |
40 | 3 | 1 | 1 |
У8 | 3 | 1 | 1 |
4. Охлажденные образцы очистить абразивной шкуркой и измерить их твердость на твердомере Роквелла по шкале С.
5.Результаты измерения занести в таблицу 4.
Таблица 4 – Твердость образцов после охлаждения с закалочных температур
Марка стали | Твердость, НRС | ||||
Охлаждение в воде | Охлаждение в масле | Охлаждение на воздухе | |||
1 образец | 2 образец | 3 образец | |||
40 | |||||
У8 |
Отпуск
Таблица 5 – Твердость образцов после отпуска.
Марка стали | Твердость после отпуска при температуре | ||
200°С | 400°С | 600°С | |
40 | |||
У8 |
6.Табличные результаты изобразить графически.
7. Результаты проанализировать и сделать выводы. Требования к отчету
studfiles.net
Закалка и отпуск углеродистых сталей
Лабораторная работа 4
Тема: " Закалка и отпуск углеродистых сталей"
Цель: Научиться правильно проводить различные виды термообработок, устанавливать зависимость изменения механических свойств от вида термообработки.
Задание:
1. Описать порядок применение закалки углеродистых сталей и определить температуру закалки согласно заданию.
2. Определить время закалки согласно заданию.
3. Описать назначение отжига и определить его время согласно заданию.
4. Результаты работы оформить в виде протокола.
Ход работы:
1. Методика проведения закалки.
1.1. Определить температуру закалки стали, пользуясь для этого нижней частью диаграммы железо–цементит рисунок 4.1. Для среднеуглеродистых доэвтектоидных сталей (40–65) нормальной температурой закалки является температура на 30–50 °С выше линии GSт.е. Ас3 + (30–50 °С). Для высокоуглеродистых заэвтектоидных сталей (У9 – У12) нормальной температурой закалки является температура на 30–50 °С выше линии PSKт.е. Ас1 + (30–50 °С).
1.2. Определить время нагрева образцов из расчета 1,5 мин на 1 мм диаметра или толщины образца.
1.3. Образцы поместить в печь, нагретую до температуры закалки для стали данной марки, и выдержать в печи требуемое время. При нагревании до температуры закалки образцов из стали 40 – 65 исходная феррито-перлитная структура превратится в структуру аустенита, а в образцах из стали У9 – У12 при температуре закалки будет структура аустенит и цементит, т.е. часть цементита остается нерастворенной.
1.4. Образцы последовательно один за другим вынуть из печи и охладить в воде (часть образцов) и в масле при непрерывке энергичном движении образца в охлаждающей жидкости. При охлаждении в воде происходит распад аустенита с образование мартенсита. При охлаждении в масле образуется смешанная мартенсито-трооститная структура.
1.5. Оба торца образцов зачистить на шлифовальной шкурке.
Рисунок 4.1 Оптимальный интервал температуры закалки углеродистой стали
2. Определение время закалки
1,5 мин. 14 = 21 минут – температура закалки.
3. Методика проведения отпуска
Чтобы обеспечить равномерность нагрева образцов, низкотемпературный отпуск (200 °С) надо проводить в масляной ванне, среднетемпературный и высокотемпературный отпуск (300–600 °С) – в соляной ванне. При отсутствии масляной и соляной ванн может быть использована электрическая муфельная печь.
3.1. Определить время выдержки при температуре отпуска из расчета 2–3 мин на 1 мм диаметра или толщины образца.
3.2. Образцы поместить в масляную ванну, нагретую до 2000 С, выдержать в ней необходимое время и охладить на воздухе.
В результате отпуска при 2000 С происходит превращение мартенсита закалки в мартенсит отпуска, снижение внутренних напряжений и хрупкости; твердость остается почти без изменений.
3.3. Оба торца зачистить на шлифовальной бумаге.
3.4. Определить твердость по HRC.
3.5. Образцы поместить в соляную ванну, нагретую до 400 °С, выдержать в ней необходимое время и охладить на воздухе. В результате отпуска при 400 °С происходит превращение мартенсита в тростит отпуска (мелкодисперсную феррито-цементитную смесь), твердость снижается.
3.6. Оба торца зачистить на шлифовальной шкурке.
3.7. Определить твердость по HRC.
3.8. Образцы поместить в соляную ванну, нагретую до 6000 О, выдержать в ней необходимое время и охладить на воздухе. В результате отпуска при 600 °С образуется сорбит отпуска, феррито-цементитная смесь более крупная, чем тростит, твердость еще более снижается.
3.9. Оба торца зачистить на шлифовальной шкурке.
3.10. Определить твердость по HRC.
Определение времени отпуска
2,5 мин.14 = 35 минут – температура отпуска.
Рисунок 4.2 Кривые влияние температуры отпуска на изменение твёрдости закаленных углеродистых сталей с различным содержанием углерода.
4. Протокол
Вывод: С помощью проведение различных вид термообработке, можно установить зависимость изменение механических свойств углеродистых сталей.
mirznanii.com
Отпуск закаленных сталей
Поиск ЛекцийТЕРМИЧЕСКАЯ ОБРАБОТКА СПЛАВОВ
МЕТОДИЧЕСКИЕ УКАЗАНИЯ
к проведению лабораторных работ по дисциплине «Материаловедение»
для студентов всех специальностей
очной и заочной форм обучения
Тюмень 2006
Утверждено редакционно-издательским советом
Тюменского государственного нефтегазового университета
Составители: старший преподаватель Прожерин А.Е.
доцент, к.т.н., доцент Нассонов В.В.
Тюменский государственный нефтегазовый университет, 2006
ТЕРМИЧЕСКАЯ ОБРАБОТКА УГЛЕРОДИСТЫХ СТАЛЕЙ
Цели работы:приобрести навыки выбора режимов термической обработки изделий из углеродистых сталей, изучить влияние
термообработки на их свойства.
Задачи:
1.провести закалку нормализацию и отпуск образцов сталей с разным содержанием углерода;
2.определить изменение твердости углеродистых сталей в зависимости от содержания углерода и режимов термической обработки
Оборудование, материалы:
1. Печи лабораторные камерные с температурами 850, 770, 600, 400 и 200 °С;
2. Пирометры для измерения температуры;
3. Закалочные баки с водой и машинным маслом;
4. Твердомер Роквелла;
5. Образцы углеродистых сталей марок 40 и У8;
6. Клещи;
7. Шкурка абразивная;
8. Ветошь.
ВВЕДЕНИЕ
Термическая обработка сплавов имеет несколько разновидностей. Углеродистые стали могут с успехом подвергаться: отжигу, нормализации, закалке, отпуску. Эффект от термообработки сталей обеспечивается благодаря полиморфному превращению железа
Термическая обработка сталей основана на четырех основных превращениях, происходящих в сталях при нагреве и охлаждении. Рассмотрим их на примере эвтектоидной стали.
1. В эвтектоидной стали при нагреве выше температуры А1 перлит, представляющий собой дисперсную смесь феррита и цементита превращается в аустенит – твердый раствор углерода в гранецентрированной кубической решетке железа (П→ А) (рисунки 1 и 2). До аустенитного состояния сталь нагревают для отжига, нормализации, закалки, а также для обработки давлением: ковки, прокатки, штамповки.
2. При медленном охлаждении аустенита ниже температуры А1 происходит диффузионное превращение его в дисперсную пластинчатую смесь феррита и цементита, называемую перлитом. Это превращение реализуется при отжиге стальных заготовок перед их механической обработкой (А→П).
3. При быстром охлаждении аустенита диффузия железа и углерода, необходимая для образования равновесных фаз – феррита и цементита, произойти не успевает. В этом случае гранецентрированная кристаллическая решетка железа перестраивается в объемно-центрированную бездиффузионно, путем коллективного сдвига ионов железа на расстояния меньше межатомных. Образуется пересыщенный твердый раствор углерода в ОЦК решетке железа – мартенсит. Мартенситное превращение реализуется при закалке стальных деталей и инструментов (А→М) (рисунок 3).
4. Мартенсит, полученный из аустенита, благодаря очень быстрому охлаждению, является термодинамически неустойчивой фазой. При его нагреве по мере возрастания диффузионной подвижности атомов углерода, а затем и железа, происходит выделение атомов углерода из решетки железа и образование карбидов железа. Образуется двухфазная структура, представляющая смесь феррита и цементита. Это превращение М → (феррит + карбиды) реализуется при отпуске закаленных изделий.
В предлагаемой лабораторной работе предстоит провести закалку, нормализацию и отпуск конструкционной среднеуглеродистой стали 40 и высокоуглеродистой инструментальной стали У8.
Закалка
1. Выбор температуры нагрева под закалку
Доэвтектоидные стали под закалку следует нагревать до однородного аустенитного состояния. Оно достигается за сравнительно короткий отрезок времени, если температура нагрева находится на 30—50оС выше температуры Ас3. Температура Ас3, при которой в реальных условиях нагрева произойдет полная замена феррита на аустенит, зависит от скорости нагрева (рисунок 1). Чем выше скорость нагрева, тем больше разность между Ас3 и А3. При медленном печном нагреве она небольшая. Поэтому температуру нагрева под закалку доэвтектоидных сталей назначают на 30 – 50оС выше равновесной А3, которую, в свою очередь, находят на диаграмме состояния железо – углерод, на пересечении концентрации углерода в стали с линией GS (рисунок 2).
![]() |
Рисунок 1 – Влияние температуры и скорости нагрева на превращение перлита в аустенит |
В заводской практике критические температуры используемых сталей определяют по справочникам, а в случае необходимости уточняют с помощью термического анализа.
![]() |
Рисунок 2 - Часть диаграммы ЖЕЛЕЗО–УГЛЕРОД, используемая для выбора температуры нагрева при термообработке углеродистых сталей. |
Заштрихованная область на диаграмме показывает рекомендуемые температуры нагрева под закалку. Для сталей доэвтектоидных температура нагрева на 20-30°С выше линии Асз т.е. находится в области аустенита. Сталь марки 40 (0,4%С) нагревается до температуры t1 , сталь марки У8 (0,8%С) нагревается до температуры t2.
2. Период нагрева
Время нагрева можно рассчитывать или воспользоваться справочными данными (таблица 1).
Таблица 1 – Время нагрева плоских стальных деталей
Нагревательный аппарат | Температура нагрева, °С | Время нагрева на 1мм толщины детали, сек. | |
углеродистая сталь | легированная сталь | ||
Пламенная печь | 800-900 | 60-70 | 65-80 |
Электропечь | 720-820 | 60-65 | 70-75 |
820-880 | 50-55 | 60-65 | |
Соляная ванна | 770-820 | 12-14 | 18-20 |
3. Период выдержки при заданной температуре
Время выдержки необходимо для равномерного распределения температуры по всему сечению образца (прогрев детали) и для завершения структурных превращений. Оно определяется расчетом или берется из соответствующих справочников. Для образцов, используемых в данной работе, можно принять время выдержки из расчета 1 мин на 1мм толщины детали.
4. Период охлаждения
Главнейший фактор этого периода - скорость охлаждения детали. В зависимости от скорости охлаждения аустенит может превращаться в различные структуры. На рисунке 3 изображена диаграмма изотермического превращения переохлажденного аустенита (изображен общий случай). А – аустенит, П – перлит. V1, V2, V3, V4, VК – скорости охлаждения, град/сек. МН – температура начала мартенситного превращения.
У сталей углеродистых с уменьшением скорости охлаждения получается более равновесная структура и меньше твердость. Например, при скорости V1 образуется структура крупнопластинчатого перлита, при скорости V2 более дисперсная структура перлита (и более твердая). Чтобы получить структуру мартенсита (обладающую наибольшей твердостью) необходима скорость охлаждения VК (критическая скорость) или еще более высокая V4.Для углеродистых сталей она равна примерно 500 оС/с.
![]() |
Рисунок 3 – Диаграмма изотермического превращения переохлажденного аустенита эвтектоидной стали. |
Скорость охлаждения зависит от разности температур, от соотношения площади поверхности детали к её объёму, от теплофизических свойств охлаждающей среды и материала детали и некоторых других факторов.
Таблица 2 – Скорости охлаждения в различных средах
Охлаждающая среда | Скорость охлаждения в интервале температур, °С/сек | |
550-650°С | 200-220°С | |
Вода при 18°С | ||
Вода при 20°С | ||
Раствор в воде 18% NaCl | ||
Раствор в воде 20% Na2CО3 | ||
Машинное масло | ||
Спокойный воздух |
Отпуск закаленных сталей
Отпуск - процесс, обусловливающий превращение неустойчивых структур закаленной стали в более устойчивые.
Отпуск осуществляется путем нагрева закаленных сталей до заданных температур, лежащих ниже Ас1. При отпуске с повышением температуры происходит превращение по схеме мартенсит-троостит-сорбит. Чем выше температура нагрева, тем более равновесна будет получаемая структура, меньше внутренние напряжения, выше ударная вязкость (рисунок 4).
![]() |
Рисунок 4 – Влияние температуры отпуска на механические свойства углеродистой стали |
В процессе отпуска также различают три периода – нагрев, выдержку при заданной температуре и охлаждение.
Время нагрева с выдержкой можно принять из расчета 2-3 мин на 1мм толщины детали. Для углеродистых сталей охлаждение после отпуска можно проводить на воздухе.
poisk-ru.ru
Термообработка металла
Журнал "Моделист-конструктор", №5 за 1994 г., с.24 А. Виноградов ТЕРМООБРАБОТКА МЕТАЛЛА Моделистам постоянно приходится сталкиваться с необходимостью повысить прочность и твёрдость металла или инструмента, а иногда, наоборот, сделать металл более мягким, легче поддающимся обработке. Этого можно достичь термическим воздействием, заключающимся в нагреве материала до определённой температуры с последующим быстрым или медленным охлаждением. Нагревание деталей, конечно, удобнее всего производить в электрических муфельных печах; но можно использовать и паяльные лампы, бензиновые и газовые горелки и даже конфорки домашних газовых плит - для нагрева мелких деталей. Важнейшим условием правильной термообработки сталей является подбор необходимого температурного режима в зависимости от марки стали. Но ввиду того, что в свободной продаже имеется ограниченное число марок стали, приходится в основном использовать либо вторичное сырьё, либо изготавливать одни инструменты из других. Маркировки углеродистой стали обыкновенного качества обозначаются двумя буквами и цифрой (Ст.1 - Ст.7). Цифра в данном случае показывает примерное содержание углерода в сотых долях процента. В марках углеродистых качественных сталей - конструкционных (сталь 30; сталь 45) и автоматных сталях (А12; А30) цифры также показывают примерное содержание углерода в сотых долях процента. Наиболее широкоприменяемые стали - инструментальные (У7; У8; У8А; У10А…) - цифра в их маркировке означает содержание углерода в десятых долях процента; буква А в конце марки показывает, что в этих сталях пониженное содержание вредных примесей. Легированные стали маркируются буквами и цифрами. Буквы обозначают наличие в стали одного или целой группы легирующих компонентов: В - вольфрам; Г - марганец; К - кобальт; М - молибден; Н - никель; С - кремний; Ф - ванадий; Х - хром; Ю - алюминий. Например, сталь марки 65Х13 имеет в своём составе 0,065% углерода и 0,013% хрома. Наиболее ходовые марки сталей для изготовления инструмента приведены в таблице 1. Таблица 1.
Термическая обработка стали разделяется на закаливание, отпуск и отжиг. Закаливание стали применяется для повышения её твёрдости. Мягкие малоуглеродистые стали (Ст.25) и "железо" (Ст.10; Ст.20) не калятся; углеродистые (сталь 45; сталь 50) и инструментальные (У8; У9; У10; У10А и другие) увеличивают свою твёрдость при закалке в три-четыре раза. Процесс закаливания состоит в нагревании стали до температуры калки (для каждой марки своя) и в быстром охлаждении в масле или воде. Температурные режимы закалки приведены в таблице 2. Таблица 2.
В домашних условиях, при отсутствии приборов температуру нагрева приближённо можно определить по цвету. Для ориентации цвета каления стальных изделий в неосвещённой солнцем комнате приведены по порядку их появления в зависимости от температуры (в °С): тёмно-коричневый (заметен в темноте) 530-580 коричнево-красный 580-650 тёмно-красный (вишнёвый) 650-730 вишнёво-красный (багровый) 730-770 вишнёво-алый 770-800 светло-вишнёво-алый 800-830 ярко-красный 830-870 красный 870-900 оранжевый 900-1050 тёмно-жёлтый 1050-1150 светло-жёлтый 1150-1250 жёлто-белый 1250-1300 ослепительно белый св. 1300. В закалённом состоянии сталь обладает большой твёрдостью, но вместе с тем и хрупкостью. Чтобы придать ей вязкость, производится отпуск стали после закалки. Для этого её нагревают до температуры 220-300°С и медленно охлаждают в воздухе. Твёрдость стали при этом несколько уменьшается, структура её изменяется, и она становится более вязкой. Меняя температуру отпуска, можно получить разные механические свойства. При нагреве стали на воздухе её поверхность окрашивается в различные цвета, называемые цветами побежалости. Каждый цвет побежалости соответствует вполне определённой температуре и может служить указателем для определения степени нагрева при отпуске стали. Термические режимы и соответствующие им цвета побежалости приведены в таблице 3. Таблица 3.
Отпуск выполняется следующим образом: стальную деталь зачищают в каком-нибудь месте до блеска, помещают в огонь и следят за появлением цветов побежалости. Отпуск закалённой детали должен быть проведён в течение 24 часов после её закалки. Отжиг стали служит для выполнения задачи обратной закалки в случаях, когда закалённую деталь требуется обработать режущим инструментом, согнуть или разрезать. Отжиг стали заключается в нагревании её до температуры 800-900°С с последующим медленным охлаждением. После отжига сталь легко поддаётся обработке. * * * Подписная научно-популярная серия "Сделай сам" (издательство "Знание"), №1 за 1990 г., с. 88, 89. Отжиг цветных металлов. При обработке цветных металлов (чеканка, выколотка и др.) иногда приходится снимать напряжения, возникшие при обработке. Для этого необходимо отжечь заготовку. Отжиг цветных металлов проводят при следующих температурах:
На главную ![]() |
bubomix.narod.ru