- Покраска стали рулонной
- Цвет сталь нержавеющая
- Тонкостенные трубы из нержавеющей стали
- Способы закалки стали
- Минимальный радиус изгиба троса стального
- Вес нержавеющей стали листовой
- Гост 3282 74 проволока стальная
- Сталь р6м5к5 характеристики и применение
- Гост стали
- Труба стальная толстостенная
- Стальная прямоугольная труба
Большая Энциклопедия Нефти и Газа. Малоуглеродистые стали
Малоуглеродистая сталь - Большая Энциклопедия Нефти и Газа, статья, страница 1
Малоуглеродистая сталь
Cтраница 1
Малоуглеродистые стали, содержащие 0 3 % С, хорошо свариваются любыми методами. [2]
Малоуглеродистые стали можно защищать от действия температур до 700 С обычными грунтовочными эмалями, в которые при помоле добавляют большие количества окиси хрома. Покрытие наносят тонким слоем и обжигают при 1000 - 1200 С. [3]
Малоуглеродистые стали ( СТ27 %) хорошо свариваются любыми методами сварки. Сварка сталей с содержанием углерода более 0 27 % обычно сопряжена с некоторыми затруднениями. Так, наблюдается выгорание углерода, вызывающее появление пористости в металле шва. Вследствие уменьшения теплопроводности и температуры плавления среднеуглеродистых сталей увеличивается опасность перегрева металла в зоне сварки. С повышением содержания углерода растет склонность стали к образованию закалочных структур, обладающих высокой твердостью и хрупкостью, что нередко сопровождается появлением трещин в металле шва или рядом с ним. Поэтому сварку сталей с повышенным содержанием углерода обычно выполняют с предварительным подогревом и последующей термической обработкой. Кроме того, в случаях применения сварки плавлением пользуются присадочным металлом с невысоким содержанием углерода, чтобы избежать эффекта закалки шва. Необходимая прочность соединений достигается при легировании наплавленного металла марганцем, кремнием и другими элементами. [4]
Малоуглеродистые стали можно защищать от действия температур, до 700 С обычными грунтовочными эмалями, в которые при помоле добавляют большие количества окиси хрома. Покрытие наносят тонким слоем и обжигают при 1000 - 1200 С. [5]
Малоуглеродистые стали с содержанием углерода до 0 25 % имеют большую вязкость, но не воспринимают закалки. Для улучшения механических характеристик малоуглеродистых сталей их подвергают химико-термической обработке. [6]
Малоуглеродистые стали ( кипящие и спокойные) и низколегированные свариваются неплавящимся электродом переменным током или постоянным прямой полярности, а плавящимся - постоянным током обратной полярности. [7]
Малоуглеродистые стали имеют небольшой предел текучести и низкое значение отношения предела текучести к пределу прочности. [8]
Малоуглеродистая сталь сваривается практически всеми видами и способами сварки плавлением. [9]
Малоуглеродистые стали ( 0 27 % С) хорошо свариваются любыми методами. Сварка сталей с содержанием углерода более 0 27 % сопряжена с затруднениями. Наблюдается выгорание углерода, вызывающее пористость металла шва. Уменьшение теплопроводности и температуры плавления среднеуглеродистых сталей увеличивает опасность перегрева металла в зоне сварки. С повышением содержания углерода растет склонность стали к образованию закалочных структур. Поэтому сварку сталей с повышенным содержанием углерода выполняют с предварительным подогревом и последующей термической обработкой. [10]
Малоуглеродистые стали хорошо свариваются любыми методами. Сварка сталей с содержанием углерода более 0 27 % сопряжена с затруднениями. Так, выгорание углерода вызывает пористость металла шва. Уменьшение теплопроводности и температуры плавления среднеуглеродистых сталей увеличивает опасность перегрева металла в зоне сварки. С повышением содержания углерода растет склонность стали к образованию закалочных структур. Поэтому сварку сталей с повышенным содержанием углерода выполняют с предварительным подогревом и последующей термической обработкой. [11]
Малоуглеродистая сталь сваривается вакуум-но-герметично в аргоне без присадки лишь при толщинах от 0 5 до 1 5 мм, и то не всегда удачно. [12]
Малоуглеродистая сталь содержит, кроме железа и углерода, ряд примесей ( фосфор, серу, марганец, кремний, алюминий, хром и др.), окисление которых вместе с железом ведет к образованию сложной окалины, состоящей из многокомпонентных слоев. Поэтому после растворения окисной пленки на поверхности малоуглеродистой стали обычно остается черный сажеобразный налет так называемого травильного шлама. В состав шлама входят, кроме особого вида кристаллов магнетита ( Fe3O4) особенно плохо растворяющихся в кислотах, также окислы содержащихся в стали труднорастворимых примесей или неокисленные примеси, например медь. При непосредственном контакте горючих газов с поверхностью металла образуется более толстый слой окалины, чем при непрямом нагреве. Еще меньше окалины образуется при нагреве в электрических печах. [13]
Малоуглеродистая сталь содержит, кроме железа и углерода, ряд примесей ( фосфор, серу, марганец, кремний, алюминий, хром и др.), окисление которых вместе с железом ведет к образованию сложной окалины, состоящей из многокомпонентных слоев. [14]
Малоуглеродистые стали хорошо свариваются как при разогреве кромок ниже температуры плавления, так и в расплавленном состоянии. [15]
Страницы: 1 2 3 4
www.ngpedia.ru
Структура малоуглеродистой стали
Сталь - это сплав железа с углеродом, содержащий легирующие добавки, улучшающие качество металла, и вредные примеси, которые попадают в металл из руды или образуются в процессе выплавки.
В твердом состоянии сталь является поликристаллическим телом, состоящим из множества различно ориентированных кристаллов (зерен). В каждом кристалле положительно заряженные ионы расположены упорядоченно в узлах пространственной решетки. Для стали характерны кубические кристаллические объемно-центрированная и гранецентрированная решетки (рис. 2.1).
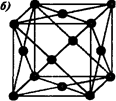
Рис. 2.1. Кубическая кристаллическая решетка:
а - объемно-центрированная; б - гранецентрированная
Структура стали зависит от условий кристаллизации, химического состава, режима термообработки и прокатки.
Температура плавления чистого железа равна 1539°С. При охлаждении образуются кристаллы d-железа с объемно-центрированной решеткой (рис. 2.1, а); при температуре 1400°С происходит перекристаллизация и d-железо переходит в g-железо с гранецентрированной решеткой (рис. 2.1, б). При 910°С и ниже кристаллы g-железа вновь превращаются в объемно-центрированные с сохранением такого состояния в обычных условиях (a-железо).
При дальнейшем остывании стали образуется твердый раствор углерода в g-железе, называемый аустенитом, в котором атомы углерода располагаются в центре гранецентрированной кристаллической решетки. При температуре ниже 910°С начинается распад аустенита. Образующееся a-железо (феррит) плохо растворяет углерод. По мере выделения феррита аустенит обогащается углеродом и при температуре 727°С превращается в перлит - смесь феррита и карбида железа Fe3С (цементит).
Таким образом, при нормальной температуре сталь состоит из двух основных фаз - феррита и цементита, которые образуют самостоятельные зерна, а также входят в виде пластинок в состав перлита.
Феррит весьма пластичен и малопрочен, цементит тверд и хрупок, перлит обладает промежуточными между ними свойствами. В зависимости от содержания углерода преобладает та или иная структурная составляющая. Величина зерен феррита и перлита зависит от числа очагов кристаллизации и условий охлаждения. Размер зерна существенно влияет на механические свойства стали (чем мельче зерно, тем выше качество металла).
Структура низколегированных сталей
Структура низколегированных сталей аналогична структуре малоуглеродистой стали. Низколегированные стали тоже содержат мало углерода, повышение их прочности достигается легированием - добавками, которые, как правило, находятся в твердом растворе с ферритом и растворяясь, упрочняют его. Легирующие добавки образуют карбиды и нитриды, также упрочняющие ферритовую основу и способствуют образованию мелкозернистой структуры.
Углеродистая сталь обыкновенного качества состоит из железа и углерода с некоторой добавкой кремния или алюминия, марганца, меди.
Углерод (У), повышая прочность стали, снижает ее пластичность и ухудшает свариваемость; поэтому в строительных сталях, которые должны быть достаточно пластичными и хорошо свариваемыми, углерод допускается в количестве не более 0,22 %.
Кремний (С), повышает прочность стали, ухудшает ее свариваемость и стойкость против коррозии. В малоуглеродистых сталях кремний применяется как хороший раскислитель; в малоуглеродистые стали добавляется до 0,3 % кремния, в низколегированные - до 1 %.
Алюминий (Ю) хорошо раскисляет сталь, нейтрализует вредное влияние фосфора, повышает ударную вязкость.
Марганец (Г) повышает прочность и вязкость стали, хороший раскислитель, соединяясь с серой, снижает ее вредное влияние. В малоуглеродистых сталях марганца содержится до 0,64 %, в легированных - до 1,5 %; при содержании марганца более 1,5 % сталь становится хрупкой.
Медь (Д) несколько повышает прочность стали и увеличивает стойкость ее против коррозии. Избыточное содержание (более 0,7 %) способствует старению стали.
Молибден (М)и бор (Р) обеспечивают высокую устойчивость аустенита при охлаждении, что очень важно для получения высокопрочного проката больших толщин. После закалки и высокого отпуска сталь становится мелкозернистой, насыщенной карбидами. Такая сталь обладает высокой прочностью, удовлетворительной пластичностью и почти не разупрочняется при сварке.
Примечание. При обозначении марки стали каждому химическому элементу присвоена буква русского алфавита (указана в скобках около каждого элемента), содержание каждого элемента в процентах с округлением до целых значений указывается после буквы, обозначающей данный элемент (элемент содержащийся в пределах 1 %, цифрами не указывается). Поскольку углерод содержится во всех сталях, его обозначение (буква У) не ставится, а количественное содержание указывается в сотых долях процента в начале обозначения марки. Так, 15Г2СФ означает, что в этой стали среднее содержание углерода 0,15 %, марганца - в пределах 1—2 %, кремния и ванадия - в пределах 1 % каждого.
Азот (А) в несвязанном состоянии способствует старению стали и делает ее хрупкой, особенно при низких температурах. Его не должно быть более 0,008 %.
Повышение механических свойств низколегированной стали осуществляется также присадкой металлов: марганец (Г), хром (Х), ваннадий (Ф), вольфрам (В), молибден (М), титан (Т).
Вольфрам и молибден, значительно повышая твердость, снижают пластические свойства стали.
Вредные примеси. Фосфор - повышает хрупкость стали, особенно при пониженных температурах (хладоломкость), и снижает пластичность при повышенных; сера - делает сталь красноломкой (склонной к образованию трещин при температуре 800 - 1000 °С). Поэтому содержание серы и фосфора в стали ограничивается: так, в углеродистой стали Ст 3 серы должно быть не больше 0,05 % и фосфора - 0,04 %.
Вредное влияние на механические свойства стали оказывает насыщение ее газами, которые могут попасть из атмосферы в металл, находящийся в расплавленном состоянии. Кислород повышает хрупкость стали, несвязанный азоттакже снижает качество стали, водород (всего 0,0007 %) вызывает в микрообъемах высокие напряжения, что приводит к снижению сопротивления стали хрупкому разрушению, снижению временного сопротивления и ухудшению пластических свойств. Поэтому расплавленную сталь (например, при сварке) необходимо защищать от воздействия атмосферы.
Значительного повышения прочности, деформационных и других свойств стали помимо легирования достигают термической обработкой. Под влиянием температуры, а также режима нагрева и охлаждения изменяются структура, величина зерна и растворимость легирующих элементов стали.
Простейшим видом термической обработки являетсянормализация. Она заключается в повторном нагреве проката до температуры образования аустенита и последующего охлаждения на воздухе. После нормализации структура стали получается более упорядоченной, снимаются внутренние напряжения, что приводит к улучшению прочностных и пластических свойств стального проката и его ударной вязкости.
Свойства стали
Надежность и долговечность металлических конструкций во многом определяется механическими свойствами стали.
Прочность - сопротивление материала внешним силовым воздействиям без разрушения.
Упругость - свойство материала восстанавливать свою первоначальную форму после снятия внешних нагрузок.
Пластичность - свойство материала сохранять несущую способность в процессе деформирования.
Хрупкость - склонность к разрушению при малых деформациях.
Ползучесть - свойство материала непрерывно деформироваться во времени без увеличения нагрузки.
Твердость - свойство поверхностного слоя металла сопротивляться деформации или разрушению при внедрении в него индентора из более твердого материала.
Прочность металла при статическом нагружении, а также его упругие и пластические свойства определяют испытанием стандартных образцов (прямоугольного или круглого сечения) на растяжение с записью диаграммы зависимости между напряжением s и относительным удлинением e (рис.2.1)
;
, (2.1)
где F – нагрузка;
A – первоначальная площадь поперечного сечения образца;
l0 – первоначальная длина рабочей части образца;
Δl – удлинение рабочей части образца.
Примечание. Большое препятствие образованию сдвигов в зернах феррита создают в стали более прочные зерна перлита поэтому прочность стали значительно выше прочности чистого железа.
Рисунок 2.1 – Образец и диаграмма растяжения стали
а - образец для испытания на растяжение; б – диаграммы растяжения сталей и чугуна (1 – малоуглеродистая сталь; 2 – чугун; 3 – высокопрочная сталь)
Основными прочностными характеристиками металла являются временное сопротивление и предел текучести. Временное сопротивление (su) - предельная разрушающая нагрузка, отнесенная к первоначальной площади поперечного сечения образца. Предел текучести(sy) - напряжение, которое соответствует остаточному относительному удлинению после разгрузки, равному 0,2%. В мягких сталях при таком напряжении начинается интенсивный процесс развития деформаций, которые растут без изменения нагрузки с образованием площадки текучести - металл "течет". Для сталей, не имеющих площадки текучести, вводят понятие условного предела текучести s02, величину которого определяют по тем же правилам.
Мерой пластичности материала служит относительное остаточное удлинение при разрыве d. Перед разрушением в образце в месте разрыва образуется "шейка", поперечное сечение образца уменьшается, и в зоне шейки развиваются большие местные пластические деформации. Относительное удлинение при разрыве складывается из равномерного удлинения на всей длине образца dr и локального удлинения в зоне шейки dloc.
Временное сопротивление, предел текучести и относительное удлинениеустанавливаются в стандартах на сталь.
Упругие свойства материала характеризуют модулем упругостиЕ = tga (a - угол наклона начального участка диаграммы работы стали к оси абсцисс) и пределом упругости sc, т. е. таким максимальным напряжением, после снятия которого остаточные деформации отсутствуют. Несколько ниже scнаходится предел пропорциональности sр - напряжение, до которого материал работает линейно по закону Гука
s = Е e . (2.2)
Похожие статьи:
poznayka.org
1.Основные хар-ки малоуглеродистой стали обычной прочности, повышенной прочности, высокой прочности.
Малоуглеродистые стали обычной прочности. Из группы малоугле- родистых сталей обыкновенного качества, производимых металлургиче- ской промышленностью по ГОСТ 380 — 71, с изм., для строительных ме- таллоконструкций применяется сталь марок CT3 и СтЗГпс.
Сталь марки СтЗ производится кипящей, полуспокойной и спокойной. Малоуглероднстые стали хорошо свариваются. В зависимости от назначения сталь поставляется по следующим трем группам:
А — по механическим свойствам; Б — по химическому составу;
В — по механическим свойствам и химическому составу. Поскольку для несущих строительных конструкций необходимо обеспечить прочность и свариваемость, а также надлежащее сопротивление хрупкому разрушению и динамическим воздействиям, сталь для этих конструкций заказывается по группе В, т.е. с гарантией механических свойств и химического состава.
Сталь марки СтЗ содержит углерода 0,14 — 0,22 %, марганца в кипящей стали — 0,3 — 0,6 %, в полуспокойной и спокойной — 0,4 — 0,65 %, кремния в кипящей стали от следов — до 0,07 %, в полуспокойной
0,05 — 0,17 %, в спокойной — 0,12 — 0,3 %. Сталь марки СтЗГпс с повышенным содержанием марганца имеет углерода 0,14 — 0,22 %, марганца 0,8 -1,1, %, кремния до 0,15 %. В зависимости от вида конструкций и условий их эксплуатации стали, из которой они изготавливаются, предъявляются те или другие требования по ГОСТ 380 — 71 (с изм.). Углеродистая сталь разделена на шесть категорий. Для всех категорий стали марок ВСтЗ и ВСтЗГпс требуется, чтобы при.поставке гарантировались химический состав, временное сопротивление, предел текучести, относительное удлинение, изгиб в холодном состоянии. Требования ударной вязкости для каждой категории различны (табл. 2.2).
Кипящая сталь изготовляется по 2-й категории — ВСтЗкп2, полуспо- койная — по 6-й категории — ВСтЗпс6, спокойная и полуспокойная с по- вышенным содержанием марганца — по 5-й категории — ВСтЗсп5 и ВСтЗГпс5. Маркировка стали согласно ГОСТ 380 — 71 (с изм.): вначале ставится соответствующее буквенное обозначение группы поставки, затем марки, далее степень раскисления и в конце категория, например обозначение 3СтЗпс6. ГОСТ 23570 — 79 «Прокат из стали углеродистой свариваемой для строиельных металлических конструкций» ограничивает содержание азота, мышьяка, устанавливает более строгий контроль механических свойств. В обозначение марки стали по ОСТ 23570 — 79 входят содержание углеродa в сотых долях процента, степень раскисления и при повышенном содержании марганца буква Г. Прокат изготовляют из сталей 18кп, 18пс, 18сп, 18Гпс и 18Гсп. По сравнению с ГОСТ 380 — 71
1.2. (с изм.) несколько повышены прочностные характеристики проката.
Значительная часть проката имеет механические свойства выше установленных ГОСТ 380 — 71 (с изм.). Институтом электросварки им. Е. О. Патона в целях экономии металла прокат из углеродистой стали марок СтЗ, СтЗГпс и низколегированной стали марок 09Г2 и 09Г2С предложенодифференцировать по прочности на 2 группы с минимальны- ми и повышенными показателями прочности, так, для стали ВСтЗ 1-й группы принято б,=250 — 260 МПа, а для 2-й группы б,=280 — 290 МПа (см. рис. 2.3), временное сопротивление отрыву б, повышено на 20— 30 МПа. Прокат из такой стали поставляется по ТУ 14-1-3023-80 «Прокат листовой, широкополосный универсальный и фасонный из углеродистой и низколегированной стали с гарантированным уровнем механических свойств, дифференцированным по группам прочности».
Стали повышенной прочности. Сталь повышенной прочности можно получить как термической обработкой малоуглеродистой стали, так и легированием. Малоуглеродистая термически обработанная сталь марки ВстТ поставляется по ГОСТ 14637 — 79. Эта сталь получается термической обработкой стали СтЗ кипящих, полуспокойных и спокойных плавок. Для металлических конструкций рекомендуются стали полуспокойной и спокойной плавок; стали кипящие как весьма неоднородные не рекомендуются. Сталь марки ВСтТпс имеет предел текучести 295 МПа, временное сопротивление 430 МПа. Показатели ударной вязкости этой стали выше, чем показатели стали СтЗ (0,35 МДж/м' при температуре — 40'С). Повышенная прочность низколегированных сталей получается введением марганца, кремния, хрома, никеля, меди, ванадия. При этом некоторые марки стали подвергаются термическому упрочнению. Подбор легирующих элементов обеспечивает хорошую свариваемость. Прокат из этих сталей поставляется по ГОСТ 19281 — 73 «Сталь низколегированная сортовая и фасонная», по ГОСТ 19282 — 73 «Сталь низколегированная листовая и широкополосная универсальная» и различным техническим условиям.
В зависимости от нормируемых свойств (химического состава, вре- менного сопротивления, предела текучести, ударной вязкости при раз- ных температурах и после механического старения)' согласно ГОСТУ
эти стали подразделяются на 15 категорий. Основные марки сталей повышенной прочности приведены в табл. 2.1. За счет более высоких прочностных характеристик применение сталей повышенной прочности. Приводит к экономии металла до 20 — 25 %.
Сталь высокой прочности. Прокат из стали с пределом текучести
440 МПа и временным сопротивлением 590 МПа и выше получают пу- тем легирования и термической обработки (см. табл. 2.1).
При сварке термообработанных сталей вследствие неравномерного нагрева и быстрого охлаждения в разных зонах сварного соединения
1.3. происходят различные структурные превращения. На одних участках образуются закалочные структуры, обладающие повышенной прочностью и хрупкостью (жесткие прослойки), на других металл подвергается высокому отпуску и имеет пониженную прочность и высокую пластичность (мягкие прослойки). Разупрочнение стали в околошовной зоне может достигать 5 — 30%, что необходимо учитывать при проектировании сварных конструкций из термообработанных сталей. Введение в состав стали некоторых карбидообразующих элементов (молибден, ванадий) снижает эффект разупрочнения. Применение сталей высокой прочности приводит к экономии металла на 25 — 30 % по сравнению с конструкциями из малоуглеродистых сталей и особенно целесообразно в большепролетных и тяжело нагруженных конструкциях.
Таблица 2.1. Основные марки строительных сталей и их механическиехарактеристики.
studfiles.net
Кипящая малоуглеродистая сталь - Большая Энциклопедия Нефти и Газа, статья, страница 1
Кипящая малоуглеродистая сталь
Cтраница 1
Кипящая малоуглеродистая сталь более склонна к росту зерна, чем спокойная и полуспокойная. Поэтому сварные соединения кипящей стали имеют более широкий участок с крупным зерном, чем сварные соединения спокойной и полуспокойной стали. Наследственно мелкозернистые низколегированные стали, легированные молибденом, хромом и ванадием, имеют либо слаборазвитый участок с крупным зерном, либо такой участок отсутствует полностью. Объясняется это малой склонностью аустенита этих сталей к росту зерна. [2]
Кипящая малоуглеродистая сталь склонна к росту зерна, поэтому сварные соединения кипящей стали имеют более широкий участок с крупным зерном, чем сварные соединения спокойной и полуспокойной стали. Наследственно мелкозернистые низколегированные жаропрочные стали имеют либо слабо развитый участок с разросшимся зерном, либо этот участок отсутствует полностью. Объясняется это низкой склонностью к росту зерна аустешита. Очень сильный рост зерна в околошовной зоне наблюдается у хромистых нержавеющих сталей ферритного класса. [4]
Кипящие малоуглеродистые стали сваривают проволокой марки Св-ЮГС с применением флюса АН-8 или двумя проволоками - Св - 08А и Св-ЮГС. [5]
Зерно кипящей малоуглеродистой стали склонно к росту, поэтому в сварных соединениях из нее участок с крупным зерном более широкий, чем в аналогичных соединениях из спокойной и полуспокойной стали. Наследственно мелкозернистые низколегированные жаропрочные стали имеют слабо развитый участок с разросшимся зерном или этот участок отсутствует совсем. Это объясняется тем, что зерно аустенита не склонно к росту. Очень сильный рост зерна в околошовной зоне наблюдается у хромистых нержавеющих сталей ферритного класса. [7]
Черная полированная жесть изготовляется из кипящей малоуглеродистой стали марки 15 кп. [8]
Следует отметить, что листы из кипящих малоуглеродистых сталей ( в том числе марки 08 кп) неоднородны, имеют расслой ( раскатанные пузыри - см. гл. Поэтому наряду с кипящими для этих целей применяют и спокойные или полуспокойные стали ( успокоенные алюминием), лишенные указанных недостатков, хотя и несколько более твердые. [9]
Следует отметить, что листы из кипящих малоуглеродистых сталей ( в том числе марки 08кп) неоднородны, имеют расслой ( раскатанные пузыри, см. гл. Поэтому наряду с кипящими для этих целей применяют и спокойные или иолуспокойпыо стали ( успокоенные алюминием), лишенные указанных недостатков, хотя и несколько более твердые. [10]
Следует отметить, что листы из кипящих малоуглеродистых сталей ( в том числе марки 08кп) неоднородны, имеют расслоение ( раскатанные пузыри, см. гл. Поэтому наряду с кипящими сталями для этих целей применяют и спокойные или полуспокойные ( успокоенные алюминием - марка 08Ю), лишенные указанных недостатков, хотя и несколько более твердые. [11]
На рис. 50, а показан серный отпечаток стального котельного листа из кипящей малоуглеродистой стали. Такая структура, когда лист состоит из трех слоев, резко отличающихся по химическому составу, называется трехслойной. [12]
На рис. 52, а показан отпечаток по Бауману стального котельного листа из кипящей малоуглеродистой стали. Такая структура, когда лист состоит из трех слоев, резко отличающихся по химическому составу, называется трехслойной. [13]
При сварке ряда металлов применение таких газов не обязательно, а иногда ( например, для кипящих малоуглеродистых сталей) может даже создавать трудности в получении швов необходимого качества. Однако использование в этих случаях так называемых активных газов вполне оправдано и по техническим, и по экономическим соображениям. Наиболее широко в качестве активного защитного газа в сварочной технике применяется углекислый газ, иногда в виде смесей с добавлением аргона или даже кислорода. Сварка в углекислом газе, впервые предложенная в СССР [44], получила широкое применение и у нас, и за границей. Обычным методом использования таких защитных газов является струйная защита. [14]
Как показывает практика обследований резервуаров, часто в паспортах РВС отсутствуют сведения о марке стали и механических свойствах металла корпуса. Для резервуаров, находящихся в эксплуатации длительное время, качество металла нередко не отвечает современным требованиям, предъявляемым к резервуарным сталям, в том числе и по химическому составу. В настоящее время требованиями нормативно-технической документации запрещено применение кипящих малоуглеродистых сталей для изготовления несущих элементов корпуса РВС, что обусловлено их повышенной склонностью к деформационному старению, трещинообразованию. [15]
Страницы: 1 2
www.ngpedia.ru
Свойство - малоуглеродистая сталь - Большая Энциклопедия Нефти и Газа, статья, страница 1
Свойство - малоуглеродистая сталь
Cтраница 1
Свойства малоуглеродистой стали также могут быть значительно улучшены, по мнению автора, за счет повышения содержания углерода, кремния и меди. [2]
На рис. 87 показано изменение свойств малоуглеродистой стали ( 0 20 % С) при изменении температуры от 20 до 600 С. В интервале так называемой синеломкости ( 200 - 300 С) повышается прочность и снижается пластичность стали, поэтому следует избегать пластического деформирования малоуглеродистой стали в этом интервале температур. Синеломкость обусловлена выделением мелкодисперсных частиц. [3]
Кислородная резка почти не оказывает влияния на свойства малоуглеродистых сталей вблизи места реза. При резке сталей с повышенным содержанием углерода, марганца, хрома и молибдена кромки реза подвергаются закалке, становятся более твердыми, возможно появление трещин, особенно если сталь при этом имеет значительную толщину и резка ведется по сложному замкнутому контуру. [4]
Кислородная резка почти не оказывает влияния на свойства малоуглеродистой стали вблизи места разреза. При резке сталей с повышенным содержанием углерода кромки разреза становятся более твердыми, так как в месте ipaspesa такая сталь под-вергается частичной закалке. [5]
На рис. 2 - 5 показано изменение свойств малоуглеродистой стали ( 0 20 % С) в интервале температур от 20 до 600 С. В интервале так называемой синеломкости ( 200 - 300 С) повышается прочность и снижается пластичность стали, поэтому следует избегать пластического деформирования малоуглеродистой стали в этом интервале температур. Синеломкость обусловлена выделением мелкодисперсных частиц. [7]
Физические свойства аустенитных нержавеющих сталей приведены в табл. 2; для сравнения даны также свойства малоуглеродистой стали Ст. [9]
Одним из главных недостатков индукционного метода обогрева является свойственный ему низкий коэффициент использования мощности вследствие индуктивного влияния реактора, усиливаемого свойствами малоуглеродистой стали. Для увеличения коэффициента использования мощности на дне реактора устанавливают дополнительную нагревательную секцию сопротивления. Индукционные катушки иногда наматывают вблизи стенки аппарата, используя изолированную окисью магния алюминиевую ленту с более высоким сопротивлением, чем медная. [11]
Мартенсит малоуглеродистых сталей ( 0 1 - 0 2 % С), особенно легированных, отличается заметно более высокой прочностью и твердостью по сравнению с этими свойствами малоуглеродистой стали с обычной структурой, состоящей из феррита и малых количеств перлита - при достаточно высокой пластичности и ударной вязкости. Поэтому стали со структурой, содержащей малоуглеродистый - мартенсит, применяют в котлостроении, что будет более подробно освещено в разделах о легированных сталях. [12]
Из способов холодной сварки особого внимания заслуживает сварка стальным электродом с интенсивным охлаждением - отвод тепла проточной водой, подводимой к стороне противоположной завариваемой. При этом способе поверхностный слой наплавки сохраняет свойства малоуглеродистой стали, а зона отбела концентрируется по линии сплавления основного металла с наплавленным. [13]
Для малоуглеродистых сталей с этой целью применяют цементацию - увеличение в поверхностном слое углерода - с последующей закалкой. При этом закаливается только науглероженный поверхностный слой, а основная часть материала сохраняет свойства малоуглеродистой стали. [14]
Для малоуглеродистых сталей с этой целью применяют цементацию - увеличение в поверхностном слое углерода - с последующей закалкой. При этом закаливается только науглероженный поверхностный слой, а основная часть материала сохраняет свойства малоуглеродистой стали. [15]
Страницы: 1 2
www.ngpedia.ru
Малоуглеродистая конструкционная сталь - Большая Энциклопедия Нефти и Газа, статья, страница 1
Малоуглеродистая конструкционная сталь
Cтраница 1
Малоуглеродистые конструкционные стали хорошо свариваются при содержании до 0 27 % С и удовлетворительно - до 0 35 % С. Для получения высокого качества сварных соединений из этих сталей при электродуговой и газовой сварке надо правильно выбирать режим сварки и обеспечивать надежную защиту наплавленного металла от воздействия окружающей среды. [2]
Малоуглеродистые конструкционные стали, содержащие до 0 3 % углерода, в результате СТЦО по режиму 5 - и 6-кратного нагрева до 800 С и охлаждения на воздухе претерпевают существенные структурные изменения. На рис. 3.1 показано измельчение зерна в стали после СТЦО. [4]
Для малоуглеродистых конструкционных сталей величина mF равна 0 07 при растяжении и 0 09 при изгибе. [6]
Листовой прокат малоуглеродистой конструкционной стали вакуумно плотен поперек проката даже при толщине листа в 0 3 мм. [7]
Для сварки малоуглеродистых и конструкционных сталей применяются электроды марок ОММ-5, ЦМ-7, УОНИ-13 и др. В состав покрытия электродов, например ОММ-5, входят: 37 % ти-танового концентрата, 21 % марганцевой руды, 13 % полевого шпата, 20 % ферромарганца, 9 % крахмала и 25 % ( от веса всех компонентов) жидкого стекла. [8]
При сварке малоуглеродистых и конструкционных сталей большое значение имеют процессы окисления марганца и других элементов. Флюс надо выбирать так, чтобы он хорошо раскислял металл в сварочной ванне. Температура плавления флюса при автоматической сварке не должна превышать 1200 С, а его вязкость в расплавленном состоянии должна быть незначительной. Для автоматической сварки применяют флюсы, в состав которых обычно входит ферросилиций, марганцевая руда, известняк, доломит, плавиковый шпат, глинозем. [9]
При сварке малоуглеродистых и конструкционных сталей большое значение имеют процессы окисления марганца и других элементов. Поэтому флюс надо выбирать так, чтобы он мог хорошо рас-кислять металл в сварочной ванне. Температура плавления флюса при автоматической сварке не должна превышать 1200 С, а его / Т вязкость в расплавленном состоянии должна быть незначительной. Для автоматической сварки применяют флюсы, в состав которых обычно входит ферросилиций, марганцевая руда, известняк, доломит, плавиковый шпат, глинозем. [10]
При сварке малоуглеродистых и конструкционных сталей большое значение имеют процессы окисления марганца и других элементов. Поэтому флюс надо выбирать так, чтобы он мог хорошо раскислять металл в сварочной ванне. Температура плавления флюса при автоматической сварке не должна превышать 1200 С, а его вязкость в расплавленном состоянии должна быть незначительной. Для автоматической сварки применяют флюсы, в состав которых обычно входит ферросилиций, марганцевая руда, известняк, доломит, плавиковый шпат, глинозем. [11]
При сварке малоуглеродистых и конструкционных сталей большое значение имеют процессы окисления марганца и других элементов. Флюс надо выбирать так, чтобы он хорошо раскислял металл в сварочной ванне. Температура плавления флюса при автоматической сварке не должна превышать 1200 С, а его вязкость в расплавленном состоянии должна быть незначительной. Для автоматической сварки применяют флюсы, в состав которых обычно входит ферросилиций, марганцевая руда, известняк, доломит, плавиковый шпат, глинозем. [12]
Сталь 20ХГС принадлежит к малоуглеродистым конструкционным сталям повышенной прочности и вязкости. Наличие повышенного содержания марганца и кремния в стали обеспечивает полноту раскисления и получение повышенной вязкости. Высокие прочностные свойства стали приобретают после соответствующей термической обработки. [13]
Весь корпус камеры изготовлен из малоуглеродистой конструкционной стали. [14]
Сталь 20ХМ принадлежит к группе малоуглеродистых конструкционных сталей повышенной прочности и вязкости. Присутствие хрома и молибдена придает стали высокое сопротивление ползучести. Высокие прочностные свойства сталь получает после соответствующей термической обработки. [15]
Страницы: 1 2 3
www.ngpedia.ru
Малоуглеродистая сталь - Справочник химика 21
Подвесные приспособления для железнения должны обеспечивать жесткость крепления и одинаковое расстояние между поверхностью катода и анодами. Контакты на подвеске и анодах тщательно зачищаются. Аноды изготавливаются из малоуглеродистых сталей. [c.96]Рис. 52. Зависимость склонности углеродистой и малоуглеродистой сталей к растрескиванию от температуры и концентрации щелочи при наличии напряжений | ![]() |
Разумеется, этот вид восстановления применим только к мелким и тонкостенным деталям из пластичных материалов —латуни, малоуглеродистой стали (при нагреве до 800—900 °С). Деформации могут подвергаться детали, имеющие простейшую геометрическую форму (втулки из цветных металлов, поршневые пальцы и т. д.). [c.99]
Примером коррозионного растрескивания под напряжением может служить каустическая хрупкость стали в щелочных растворах. Опыт показал, что для возникновения каустической хрупкости необходимо совместное действие концентрированных щелочных растворов при повышенной температуре и высоких внутренних растягивающих напряжений. На рис. 52 показана область склонности углеродистой и малоуглеродистой сталей к рас- [c.89]
Площадь поверхности нагрева аппарата достигает 1860 м . Корпус аппарата изготовлен обычно из чугуна, а трубки — из малоуглеродистой стали. Применение других материалов повышает стоимость аппарата. [c.120]Наиболее экономичным применением титана для химического оборудования является облицовка внутренней поверхности резервуара из малоуглеродистой стали и чугуна. [c.217]
Смачивание расплавом наплавляемой поверхности непосредственно после флюса и интенсивное удаление продуктов флюсования обеспечивает надежное прилегание наплавляемого металла к основному. Литейные, дефекты наплавляемого слоя устраняют подпиткой кристаллизующегося сплава из перегретого на 20 -40 °С питателя в пуансоне давлением сжатого газа. Для питания кристаллизующегося сплава в течение всего времени кристаллизации охлаждение ведут последовательно в направлении, обратном подаче подпитки. В качестве наплавляемого материала можно использовать, например, баббит Б83 и Б16 и заготовки из малоуглеродистой стали. [c.230]
Малоуглеродистая сталь 05, 08 и 10 имеет высокие пластические свойства, поэтому применяется для изготовления изделий холодной штамповкой, высадкой и волочением. Кипящая сталь 05, 08, 10 используется для изготовления листов, ленты, труб и проволоки. Низкоуглеродистая сталь марок 05, 08, 10 для повышения прочности и улучшения обрабатываемости подвергается нормализации с температурой 930—950 С. Эти стали хорошо свариваются. Механические свойства сталей при повышенных температурах приведены в табл. 4.5, длительная прочность — в табл. 4.6. [c.182]
Сталь малоуглеродистая. Сталь, легированная кремнием (трансформаторная) Олово — свинец (сплав) [c.556]
На современном крупном нефтеперерабатывающем заводе прокладывают до 4000 км трубопроводов, при протяженности трубопроводов внутри отдельных установок свыше 20 км. Около 90 % общей протяженности трубопроводов составляют трубы из малоуглеродистой стали диаметром 50—300 мм. [c.338]
Указанные трубы широко применяют для сооружения различных коммуникаций для неагрессивных или слабо коррозионных сред при температурах до 450 °С. Кроме бесшовных труб из малоуглеродистой стали используют также электросварные трубы, которые иногда с успехом заменяют бесшовные. [c.344]
Сварка трубопроводов из малоуглеродистых сталей [c.355]
Следовательно, так как при pH =4ч-10 коррозия ограничена скоростью диффузии кислорода через слой оксида, небольшие изменения состава стали, термическая и механическая обработка ее не повлекут за собой изменений коррозионных свойств металла, пока диффузионно-барьерный слой остается неизменным. Скорость реакции определяют концентрация кислорода, температура или скорость перемешивания воды. Это важно, так как pH почти всех природных вод находится в пределах 4—10. Значит, любое железо, погруженное в пресную или морскую воду, будь то низко-или высокоуглеродистая сталь, низколегированная сталь, содержащая, например, 1—2 % N1, Мп, Мо и т. д., ковкое железо, чугун, холоднокатаная малоуглеродистая сталь, будет иметь практически одинаковую скорость коррозии. Этот вывод подтверждается большим количеством лабораторных и промышленных данных для разнообразных типов железа и стали 111]. Некоторые из них приведены в табл. 6.1. Эти данные опровергают распространенное мнение, что ковкое железо, например, является более коррозионностойким, чем сталь. [c.107]
Борьбу с этим очень опасным видом коррозии ведут а) применяя металлы, менее склонные к коррозионному растрескиванию (например, малоуглеродистую сталь, содержащую 0,2% С, с фер-рито-перлитной структурой) б) используя коррозионностойкое легирование (например, сталей хромом, молибденом) в) проводя отжиг деформированных металлов для снятия внутренних напряжений (например, отжиг деформированных латуней) г) создавая в поверхностном слое металла сжимающие напряжения (например, путем обдувки металла дробью или обкаткой роликом) д) тщательной (тонкой) обработкой поверхности для уменьшения на ней механических дефектов е) проводя обработку коррозионной среды (например, питательной воды котлов высокого давления) ж) вводя в электролит замедлители коррозии з) нанося защитные покрытия [c.335]
Искры, возникающие при ударах и трении стали, представляют собой небольшие (0,1—0,5 мм) кусочки металла, оторванные при механическом воздействии, частично окисленные и нагретые до высоких температур (например, для нелегированных малоуглеродистых сталей 1650 "С). В присутствии легирующих добавок, особенно вольфрама, температура искр трения снижается. [c.205]
Понижение содержания углерода. Аустенитные стали, содержащие менее 0,03% с углерода, не склонны к межкристаллитной коррозии. Малоуглеродистые стали могут легко науглероживаться при температуре, близкой к температуре плавления стали (например, при сварке). [c.447]
Один из методов, который применяется для определения приблизительной стоимости, заключается в оценке общей массы использованного металла и умножении этой величины на цену единицы массы. Небольшие простые уловители часто выполняются из стали толщиной 0,9 мм, а крупное оборудование —из стали толщиной 1,6 мм и более тяжелых профилей. Приблизительные расчеты могут быть выполнены, если принять стоимость 1 т малоуглеродистой стали (в 1970 г.), равной 200 долл. Монтажные работы составляют не более 25—45 долл./т. Конструкции из нержавеющей стали могут стоить до 1000 долл./т. [c.548]
Влияние растворенного кислорода на скорость коррозии малоуглеродистой стали в кислотах [12] [c.109]
Так, гидрататор, имеющий днища сферической формы, должен быть изготовлен из цельнокованых и литых деталей. Трубопроводы должны быть бесщовиы-ми и изготовленными из хорощо сваривающихся малоуглеродистых сталей. Особое внимание следует обращать на вибрацию технологического оборудования и трубопроводов, которая не должна превышать установленных норм. Вибрация оборудования вызывается работой компрессоров и пульса- Цией газа в трубопроводах. Она может привести к нарушению прочности отдельных узлов, плотности фланцевых соединений и разрыву сварных швов. [c.86]Основную стадию процесса — сульфирование — целесообразно осуществлять в изотермических герметичных реакторах с высоким гидродинамическим режимом. Таким аппаратом является разработанный ВНИИНефтехимом совместно с ЛенНИИХим-машем бессальниковый реактор с перемешивающим устройством пропеллерного типа. Конструкция реактора позволяет довести съем спирта до 380 кг м ч. Такая производительность не достигалась до последнего времени ни на одном аппарате. Полезный объем реактора 1,52м , поверхность теплообмена 37 м , фактически потребляемая мощность 15,5 кет, вес 5 т. Реактор выполняется из малоуглеродистой стали [51]. [c.82]
Особенностью приведенной конструкции печи является оборудование ее горячими циклонами, благодаря которым используется большая часть пылевидной обожженной извести, выносимой пз камеры об лшга с потоком газов. Кроме того, улучшается работа газораспределительных решеток верхних камер, так как продуваемый через них газ оказывается менее запыленным. Горячий циклон выполнен из малоуглеродистой стали и футерован внутри огнеупорным материалом. [c.196]
В ремонтном производстве для восстановления валов часто применяют электродуговую наплавку под слоем флюса, в ср>еде диоксида углерода, в струе охлаждающей жидкости, с комбинированной защитой дуги, порошковой лентой и др. Автоматическую электродуговую наплавку под слоем флюса широко применяют для наплавки валов, изготовленных из нормализованных и закаленных среднеуглерюдистых и низколегированных сталей, а также из малоуглеродистых сталей, не подвергающихся термической обработке, имеющих износ от 0,3 до 4,0 мм при однослойной наплавке и свыше 4 мм - при многослойной. Производительность процесса очень высока. Валы диаметром до 50 мм этим способом восстанавливать сложно, так как шлак, не успев затвердеть, стекает с наплавляемого изделия. [c.49]Измерения иитеисивиости излучения искр, образующихся при трении, позволили определить температуру их поверхности. Для нелегированных малоуглеродистых сталей она оказалась равной 1640—1670 °С. Легирующие добавки, особенно вольфрам, заметно понижают температуру поверхности искр. [c.147]
Погружной конденсатор-холодильник состоит из трубчатого змеевика, который помещен в стальной прямоугольный сварной ящик, заполненный проточной водой. Если в ящике устанавливают несколько змеевиков разного технологического назначения, то ящик разделяют на несколько отсеков внутренними вертикальными перегородками. Стенки ящика выполняют из малоуглеродистой стали и укрепляют вертикальными стойками, которые скрепляют между собой горизонтальными связями из стального прутка диаметром 16—20 мм. Натягивают связи резьбовыми муфтами. Для придания ящику дополнительной жесткости стеики соединяют с днищем косынками, которые приваривают изнутри по осям вертикальных стоек, а верхнюю часть ящика укрепляют обвязочным уголком. Днище ящика сварное из листов толщиной 4—6 мм. Размеры ящика в плане 11x23 г прн высоте до 2,8 м. [c.275]
После сварки труб пз малоуглеродистых сталей с толи],и-ной стенки более 27 мм для снятия внутренних напряжснгп производят отпуск с нагревом в течение 2 ч до 560—580 " С с последующим медленным охлаждением. [c.355]
Сварка труб нз легированных сталей, представляюпгая более сложную задачу, чем сварка труб нз малоуглеродистых сталей, должна выполняться ири самом тщательном соблюдении технологии сварки. Кроме того, при сварке любых легированных сталей следует руководствоваться правилом, чтобы [c.355]
Приварку труб из стали 12Х5МА к узлам из малоуглеродистой стали осуществляют электродами УОНИ-13/45. Прн этом обеспечиваются высокие механические свойства сварного соединения 8п>400 МПа, 200—210 НВ, угол изгиба 100—ПО", [c.357]
Старение — это способность наклепанного металла постепенно изменять свои свойства и структуру со временем при нормальных тет ратурах. При работе в интервале температур 200—300 С процесс старения стали значительно ускоряется. При старении повышаются твердость, предел прочности и предел текучести с одновременным снижением пластических свойств, особенно ударной вязкости. На развитие старения оказывает влияние химический состав. Наиболее склонны к старению малоуглеродистые стали, с повышением содер кания угле-рода эта склонность ослабляется. Спокойные, раскисленные большим количеством алюминия (не менее 0,5%) стали устойчивы против старения. [c.175]
Поджигание фрикционными искрами. При истирании стальных предметов или ударах по ним образуются яркие искры, которые мы будем именовать фрикционными. Они представляют собой кусочки металла размером 0,1—0,5 мм, оторванные при механическом воздействии, частично окисленные и сильно нагретые. Оптические измерения показали, что температура фрикционных искр Тг малоуглеродистых сталей в воздухе равна 1650 °С. Тг значительно превосходит Г любых взрывча- [c.97]
Растворы атаноламинов вызывают коррозионное действие на медь, цинк и их сплавы. В кипящих водных растворах МЭА малоуглеродистые стали также подверхшигся коррозии под действием u и При- [c.219]
Питерс п Тиммархаус [636] считают, что степень 0,6 действительна для теплообменников из углеродистой стали, для центробежных вентиляторов она должна составлять 0,96, а для центробежных компрессоров — 1,22. Применение вместо малоуглеродистой стали других материалов приведет к изменению экспоненты до величин, превышающих единицу. [c.550]
Класс 600. Среди других видов контролируемых атмосфер следует упомянуть аммиачные атмосферы. Каталитически конвертирот ванный аммиак применяют при отжиге нержавеющих сталей, а также в качестве газа-носителя для азота и пропана при нитрировании, карбюризации и карбонитрировании. Однако самой характерной областью применения этой атмосферы является поверхностная закалка малоуглеродистых сталей. Диссоциация аммиака на водород и азот может быть осуществлена путем частичного сжигания газа в присутствии некоторых катализаторов. После этого газ необходимо осушить. Его снова можно использовать для защиты хромистых сталей и в качестве газа-носителя. [c.321]
Как при карбюризации, так и при карбонитрировании расходуется дополнительное количество СНГ. При поверхностной закалке детали из малоуглеродистых сталей и сплавов нагревают в камерных или методических печах, оборудованных соответствующими приспособлениями и средствами, до 950 °С. Нагрев осуществляют в карбюризирующей атмосфере, т. е. в эндогазе или конвертированном аммиаке с добавкой до 10—15% (по объему) пропана или бутана (карбюризация) или 5—10 7о (по объему) аммиака (карбонитрирование). [c.321]
В присутствии избытка МНд, например в растворах минеральных удобрений, скорость коррозии в МН4ЫОз при комнатной температуре может достигать очень высоких значений — до 50 мм/год [21—24] (рис. 6.13). Комплексное соединение, образующееся в этом случае, имеет формулу [Ре(МНз)в ](ЫОз)2 [24]. Реакция, очевидно, идет с анодным контролем так как контакт низколегированной стали с платиной (при равной площади образцов) не влияет на скорость коррозии. Структура металла влияет на коррозионную стойкость. Так, нагартованная малоуглеродистая сталь корродирует с большей скоростью, чем закаленная при повышенной температуре. Это свидетельствует, что коррозия протекает не с диффузионным контролем, а зависит от скорости образования ионов металла на аноде и, возможно, до некоторой степени от скорости деполяризации на катоде. [c.119]chem21.info