- При температуре 650-550 ⁰С невозможно закаливать углеродистые стали, но вполне допустима закалка легированных. Связано это с тем, что в этом температурном коридоре масляная среда охлаждает металл всего в 6 раз медленнее, чем вода.
- При температуре 200 ⁰С скорость охлаждения уже в 28 раз меньше, нежели в воде. Это препятствует возникновению в стали термотрещин и позволяет закаливать крупные детали со сложной формой.
- Необходимо следить, чтобы масляная среда не перегревалась. Рекомендуемый температурный потолок – порядка 80-90 ⁰С. Если она начала слегка дымиться – значит перегревается.
- Совместимы с различными присадками. В частности, это позволяет использовать некоторые специальные закалочные масла при температуре от 70 до 170 ⁰С.
- высокой химической и термической стабильностью;
- стойкостью к испарению;
- хорошими антипенными свойствами;
- оптимальным уровнем вязкости;
- моющими свойствами.
- Отжиг.
- Нормализация.
- Закалка.
- Отпуск.
- Вакуумная – подразумевает под собой закалку жароустойчивой, подшипниковой, инструментальной стали.
- Горячая (165-220оС) – применяется при создании высокоточных деталей.
- Холодная (30-80оС) – используется для обработки высокопрочных винтовых пружин/гаек/болтов, термического улучшения деталей/заготовок и т.п.
- При t=650-550⁰С закалка легированных сталей допустима, а углеродистых невозможна. Это обуславливается тем, что в таком диапазоне температур масло охлаждает металлическое изделие не на много медленнее, чем вода (всего в 6 раз).
- В ходе закалки нужно постоянно следить за температурой масляной среды. Рекомендуемый максимум, которой, как правило, составляет 80-90⁰С.
- При t=200⁰С скорость охлаждения меньше приблизительно в 28 раз, чем в воде. Это предотвращает появление термотрещин в металлических деталях и дает возможность закаливать большие элементы со сложной формой.
- Закалочные масляные жидкости хорошо взаимодействуют с модификаторами. Такое качество позволяет без труда придавать маслам для закалки стали дополнительные уникальные свойства.
Большая Энциклопедия Нефти и Газа. Масло для закалки стали
Масла закалочные. Масла для закалки стали
Когда мы слышим о закалке металлов, то первое, с чем у нас ассоциируется этот процесс – это закалка водой. Однако в качестве охлаждающего материала используют и иные среды. Закалочное масло – одно из них.
При охлаждении раскаленного металла в масляной среде охлаждение изделия идет значительно медленнее, чем в водной. Эта особенность определяет сильные и слабые стороны первого способа закалки.
Плюсы и минусы закалочных масел
Плюсы и минусы есть у любой среды. В случае с маслами для закалки стали можно отметить:
Закалочные масла от ТД «Промсмазки»
ТД «Промсмазки» предлагает свои покупателям только качественные закалочные масла, которые обладают:
Правильный выбор закалочных сред – гарантия качества стального изделия. ТД «Промсмазки» предлагает продукцию высшего качества по низким ценам.
www.promsmazki.ru
Масло для закалки стали
Закалочное масло в основном используется на машиностроительных заводах.Закалка - это тип термической обработки металлических деталей в ходе, которой изделиям придается высокая прочность, твердость и износостойкость. Сама термообработка состоит из 4 процессов:
При этом закалка бывает 3-х видов:
Масло для закалки стали используется в открытых резервуарах и герметичных печах для закалки низколегированной/углеродистой/нелегированной стали и др.
Состав
Закалочные масла состоят из масляной жидкости (минеральной/синтетической или их комбинации) и дополнительных присадок (модификаторов), обуславливающих конечные свойства смазочного вещества.
Плюсы и минусы масляных смесей для закалки стали:
autocode.by
Характеристики закалочных масел
Mасла достаточно часто применяются в качестве закалочной среды для некоторых низкоуглеродистых сталей и для более широкого спектра средне- и высокоуглеродистых сталей различного легирования. На закаливающую способность масла влияет много факторов, основными из которых являются физико-химические характеристики: вязкость и плотность при различных температурах, теплопроводность, стойкость против шлакообразования (стойкость против старения).
Для того, чтобы понимать, как и в какой степени эти факторы влияют на закаливаемость, нужно более детально рассматривать процесс охлаждения стали. Закалка не является идеально прямой линией между осью ординат и областью минимальной устойчивости аустенита.
Эта линия имеет изгибы, соответствующие разной скорости на разных этапах охлаждения. Такие изменения скоростей являются следствием процессов, происходящих в системе деталь — охлаждающая среда при закалке.
При погружении изделия в закалочную ванну, на его поверхности образуется паровая рубашка, которая имеет низкий коэффициент теплопроводности. Охлаждение на этой стадии протекает очень медленно и характеризуется неравномерностью. Данная фаза длится несколько секунд и является самым важным этапом охлаждения, т.к. при завершении паровой фазы, начинается фаза пузырькового кипения со структурообразующими, критическими скоростями. Фактически, паровая фаза сдвигает диаграмму изотермического превращения аустенита влево, ровно на столько, сколько она длится и снижает температуру начала интенсивного охлаждения. Ускорить протекание этого этапа охлаждения можно при помощи активного перемешивания масла. Здесь, основным показателем эффективности этого мероприятия служит кинематическая вязкость масла. Это свойство зависит от температуры процесса и от природы производства масла. Кинематическая вязкость определяет, с какой скоростью будет двигаться масло в закалочной ванне при перемешивании. Однако следует учитывать, что высокие скорости движения среды могут вызвать сильное вспенивание.
Стадия пузырькового кипения начинается когда целостность паровой пленки нарушается и поверхность детали соприкасается с охлаждающей средой. При этом температура поверхности охлаждаемого изделия быстро понижается до температуры кипения масла и остается постоянной до окончания кипения. Интенсивность охлаждения зависит от теплоты парообразования применяемого масла. Чем больше значение теплоты, тем выше скорость охлаждения.
Далее кипение прекращается, и охлаждение происходит в результате конвективного теплообмена. Скорость охлаждения в этой стадии зависит от вязкости и теплопроводности масла, а также от разности температур изделия и охладителя.
Кроме описанных свойств, для оценки качества масла могут применяться и другие характеристики. Температура вспышки - очень важное свойство в плане противопожарной безопасности. Как правило, в производстве используют масла с температурой вспышки на 50-60 градусов выше, чем температура процесса. Плотность масла может указать на природу его происхождения и способ обработки. Однако присадки могут изменить это значение, поэтому характеристика плотности не может служить адекватным показателем качества. Стойкость против старения - показатель экономической эффективности использования того или иного масла. Это время нормальной работы охлаждающей среды до образования продуктов горения и шлака на дне и стенках ванны. Время смены масла чаще определяется практически, по изменению цвета закаливаемых изделий или появлением мягких пятен на поверхности. Производители закалочных масел предпочитают не указывать эту характеристику в документации.
Еще одной экономической характеристикой качества масла является скорость уноса вещества с обрабатываемыми поверхностями деталей. Она не может быть однозначно определена, т.к. в большей степени зависит от конкретных условий использования (одиночный закалочный бак, бак в составе автоматической линии, с учетом времени на стекание или без учета). Однако эта характеристика находится в некоторой корреляции с вязкостью масла и чаще не превышает 1% площади обрабатываемых изделий. При сравнении характеристик масел, нужно обращать внимание на допустимое количество воды и посторонних примесей. Вода в масле может быть причиной неравномерной твердости и возгорания закалочного бака. Чем больше воды в масле, тем больше вероятность этих явлений.
Идеальное закалочное масло должно охлаждать изделия максимально быстро в области минимальной устойчивости аустенита и максимально медленно в области Мн — Мк. Из выше сказанного следует, что при выборе такого идеального и безопасного закалочного масла, в первую очередь следует учитывать его вязкость, теплоту парообразования, теплопроводность и температуру вспышки.

heattreatment.ru
Закалочные масла - Большая Энциклопедия Нефти и Газа, статья, страница 1
Закалочные масла
Cтраница 1
Закалочные масла можно восстанавливать и на установках ЦКФ, РИМ-62 и Р-1000 М при условии подключения к ним центрифуг, тип и производительность которых определяются производительностью маслорегенерационной установки. [1]
Закалочные масла перед загрузкой в мешалку ЦКФ должны быть полностью обезвожены. Они могут быть восстановлены или обработкой отбеливающей землей, активированной аммиачной водой крепостью 25 % из расчета 1 % на отработанное масло, или смесью адсорбента ( отбеливающей земли) в количестве 7 % на отработанное масло и 1 % кальцинированной соды. [2]
Закалочные масла, легко смываемые водой, применяют в тех случаях, когда масло с деталей необходимо удалить без применения дорогостоящих операций очистки. [4]
Закалочные масла в баках и ваннах периодически ( при заливке свежей порции масла или после длительной остановки оборудования) должны подвергаться контролю на содержание в них воды, которая вызывает ценообразование, чем способствует возгоранию масла. Обнаруженная вода должна быть удалена через спускные краны, установленные в нижней части баков. [5]
Высокостабильные закалочные масла используются для контролируемого изменения молекулярной структуры стали по мере ее охлаждения. Закаливание в более легком масле применяется для упрочнения поверхности небольших деталей. Масло для закалки с паузами или многоступенчатой закалки предназначено для обработки высокоуглеродистых и легированных сталей. [6]
К первой группе относят масла для пропитки кож, закалочные масла в металлообработке, масла - поглотители ароматики в коксохимии, висциновые масла для воздухоочистительных фильтров и другие. [8]
В качестве закалочных масел применяют нефтяные масла различного-назначения: трансформаторное, веретенное, машинное и др. Созданы специальные закалочные масла, обладающие специфическими свойствами. [9]
В качестве закалочных масел применяют нефтяные масла различного назначения: трансформаторное, веретенное, машинное и др. Созданы специальные закалочные масла, обладающие специфическими свойствами. [10]
Для применения новой технологии термической обработки в станкостроении внедряются новые методы интенсификации процесса азотирования шпинделей металлорежущих станков; бездымные, негорючие и безвредные закалочные среды, заменяющие закалочные масла; проект автоматизированного участка термической и химико-термической обработки деталей станков, а также методы, приборы и аппаратура для автоматического регулирования степени диссоциации аммиака при азотировании; малодеформируемые марки сталей для изготовления шестерен и валов металлорежущих станков. [11]
Закалка в масле тоже пожароопасна, особенно если металл погружен не полностью. Закалочные масла должны иметь высокую температуру вспышки, их не следует нагревать выше 27 С. [12]
Технологические масла подразделяются на масла общего назначения, для производства химических волокон и мягчители шинных смесей. К первой группе относят масла для пропитки кож, закалочные масла в металлообработке, масла - поглотители ароматических соединений в коксохимии и др. Ко второй группе относят масла марки С-9, С-15 и С-25 типа индустриального И-20 или трансформаторного, которые применяют как компоненты засаливающих препаратов в производстве химических волокон. К третьей группе относят масла-мягчители, которые вводят в состав резиновых смесей при производстве шин для придания им эластичности и улучшения формуемости. В качестве масел используются высокоароматизированные остаточные экстракты селективной очистки ПН-бш и ПН-бк. Свойства каждой марки технологических масел оговариваются специальными ТУ или ОСТ для соответствующей технологической операции. [13]
Страницы: 1
www.ngpedia.ru
Подскажите по закалке в масле.
SOUTHFOX 24-05-2016 10:33Подскажите пожалуйста по закалке в масле. Те стали которые предпочтительно закаливать в масле, для них нужно какое то конкретное масло к примеру ( автомобильное какой то конкретной вязкости ) или подойдёт любое ? А так же интересно можно ли использовать отработанное автомобильное масло или не желательно ? В каком вообще масле предпочтительно закаливать клинок ?
kgb 24-05-2016 10:45Калил в отработку стали У13 и ШХ-15 полет нормальный. Не думаю, что требуется специальное масло, просто перед закалкой нагревал его до 60-70 град. Оно делается жиже, меньше шансов для поводок.
SOUTHFOX 24-05-2016 10:54quote:Изначально написано kgb:Калил в отработку стали У13 и ШХ-15 полет нормальный. Не думаю, что требуется специальное масло, просто перед закалкой нагревал его до 60-70 град. Оно делается жиже, меньше шансов для поводок.Про нагрев масла я знаю а вот про то какое масло предпочтительней использовать информации найти не смог.
alex-wolff 24-05-2016 11:16Масло можно любое, просто не забывать что его тоже надо менять.Если одноразово, можно и отработкой воспользоваться, но оно со временем тоже приходит в негодность как закалочная среда, клинки из простых сталей по мере использования масла, просто будут хуже брать закалку.По статистике, примерно (мне) хватает 3л на 30-40клинков. Свежее, всегда лучше отработки. Покупай самое дешёвое миниральное, разницы нет...или я не заметил.
Ily_a 24-05-2016 11:31Имеет значение скорость охлаждения в закалочной среде, все остальное вряд ли важно, новая отработка, старая, минеральное, синтетическое и т.п. Дак вот, с информацией по скорости охлаждения для различных масел очень негусто, пишут вязкость при 100 С но нам это не особо надо с нашими 780-1050 СПосему или опытный путь или искать инфу.Зы калю в отработку, народ вроде не жалуется, за три года один раз доливал.Масло грею перед закалкой.
SOUTHFOX 24-05-2016 11:36Ребята большое вам спасибо за полезную информацию.
Burchitai 24-05-2016 13:07Отработка пахнет не витаминками. Лучше всего брать новое индустриальное типа И20 или веретенное (промывочное автомобильное). Последнее жиже, а значит лучше охлаждает. Старое можно брать трансформаторное.
Evgeniy13 24-05-2016 13:23quote:Originally posted by Burchitai:Отработка пахнет не витаминками



было в Юморе мастеровых
Almas52 24-05-2016 15:31quote:Originally posted by andrelineff:было в Юморе мастеровыхСолить его надо...RonanBarbarian 24-05-2016 17:16По идее лучше , если масло моторное - у него должна быть выше температура вспышки и , кмк ,лучше синтетика, т.к. она более жидкая, возможно будет меньше пузырей на клине и, как следствие, быстрей остывание-лучше закалка. Но это всё имхо, и для сферической железяки в вакууме)))
Yastreb09 24-05-2016 17:46калю в минералке,отработка.труба 200\1000мм,по горлышко.перед закалкой грею так-нагреваю в горне болванку ок 1кг,на стальной проволочке,булькаю её на дно трубы.горячее масло снизу поднимается,следом калю уже клинки.Тка,кмк,масло равномернее перемешивается,поводок меньше.
Felinosaurus Rex 24-05-2016 18:32Я за трансформаторное масло. Оно горит меньше и воняет не так сильно, как отработка.
------------------Albion delenda est
Шалим 24-05-2016 19:37Калю в отработке.Перед закалкой подогреваю его.Проблем с закалкой не было.
SOUTHFOX 25-05-2016 18:09А ещё такой вопрос. Какую всё таки емкость лучше использовать ? Глубокую для вертикального опускания клинка или же чашеобразную чтоб опускать горизонтально под углом, лезвием вниз ?
El Diesel 25-05-2016 18:35quote:Изначально написано Felinosaurus Rex:Я за трансформаторное масло. Оно горит меньше и воняет не так сильно, как отработка.главное, на "совол" и ему подобные не нарваться...
Калю на отработку-синтетику, раньше грел( зимой) летом не греюнорм все,поводок нет. Емкость 150/150/500- сварил сам С ув, Роман
На подсолнечное никто не пробовал?
Шалим 26-05-2016 10:02quote:На подсолнечное никто не пробовал?Калил и на подсолнечном, когда отработки не было.Разницы с моторным маслом не заметил. Только жареной картошкой пахло))))guns.allzip.org
Закалка в управляемом потоке масла. - 23 Октября 2011 - Технологии
Закалка в управляемом потоке масла – новый взгляд на привычные проблемы.
Введение.
Закалка – один из самых древних и наиболее широко известных процессов термообработки.
За столетия она «обросла» массой легенд, суеверий и предрассудков.Однако, несмотря на кажущуюся простоту процесса и обилие материала в справочной литературе, термист-практик подчас сталкивается с серьезными проблемами. Особенно часто это происходит при освоении новой продукции или при повышении требований конечного пользователя к качеству продукции.
Закалить болт М22 из стали 40Х на твердость 40...45HRC для любого не проблема.
Обеспечить при этом прочность по 10-му классу при производительности 120 кг/час, это уже вопрос.Оба этих параметра - и рост требований и повышение гибкости производства - являются сегодня непременными атрибутами нашей жизни.Целью данной работы было, используя многолетний опыт, дать термисту-практику в новых условиях гибкий и надежный инструмент, обеспечивающий достаточно простое решение сложных вопросов.
Закалочные баки – немаловажная составная часть комплектного оборудования.
Для большинства средне и экономно легированных сталей наибольший интерес представляет закалка на масло.
И наиболее распротранено индустриальное И-20А.
Однако наличие массы нерешенных вопросов на практике закалки привело к поиску различных путей решения. Бурное развитие некоторое время назад получили синтетические закалочные среды - водные растворы полимеров.
В штучном производстве, при наличии мастерства и заинтересованности термиста, результаты получались прекрасные.
Термист сам чувствует, когда и на сколько надо скорректировать закалочный раствор, какие детали и до какой степени подрагивания крючка или клещей надо «качать», а когда положить.
Сложнее задача оказалась в производстве, начиная с мелкосерийного, при необходимости закалки садок деталей, зачастую весом до 200…300 кг.
И это при сменной работе персонала на фоне общего падения квалификации в условиях зачастую не определенной мотивации кадров.
Здесь корректировка раствора нужна практически ежедневная и не на глаз, а с помощью специальной аппаратуры для определения закаливающей способности раствора.
В противном случае достаточно легко получить как низкую твердость, так и трещины с неприемлемыми деформациями.
Стоимость подобной аппаратуры начинается от 100 тысяч рублей.
Обязательное условие – наличие обученного персонала, могущего с высокой степенью надежности интерпретировать результаты испытаний и предпринять правильные действия.
Подобные решения доступны далеко не всем, и технолог-термист зачастую остается один на один с масляным баком, «пятнистыми» деталями и справочником термиста.
Из курса технологии термообработки нам известно – основная задача при закалке на масло это снятие паровой рубашки с поверхности деталей. Справочник рекомендует обычно три решения: -барботаж сжатым воздухом,-возвратно-поступательное перемещение садки в масле и-масляный насос.Если имеется компрессорная, выбирают первое решение.
Если нет, но удается «пробить», ставят насос для циркуляции, НШ-40 или НШ-100.
Если ни того ни другого, остается произвол термиста, работающего на тельфере.Однако, первые два пути имеют свои подводные камни.
Сколько дать сжатого воздуха и в какое место бака, в зависимости от конфигурации садки совершенно не однозначно.
Чаще всего закаливающая способность бурно «кипящего» масла снижается – воздух прекраный теплоизолятор.
Доступные масляные насосы, обеспечивая высокое давление, чаще всего не имеют нужных нам показателей по производительности, и, опять же, неоднозначно как направить поток на садку деталей.Немаловажно и то, что абсолютно герметичных насосов по приемлемой цене не существует и возникает проблема борьбы с подтеканием масла.
Решение, между тем, существует.
Универсальные печи, проходные толкательные агрегаты, СНЦА, Пекаты, Холкрофты, конструкции ЗИЛ и т.п. Все они имели мешалки масла в закалочных баках.
Конечно, проблемы были, но несоизмеримо меньшие, чем при других вариантах.
Основным направлением были поиск и разработка новых закалочных масел с целью расширения температурного интервала в порядке борьбы с деформациями.
Сложилась уникальная ситуация: крупные предприятия, имеющие прекрасные закалочные баки в линиях термообработки зачастую не работают на полную мощность, а малые и средние предприятия, быстро развивающиеся в условиях растущей децентрализации и специализации производства, не имеют возможности использовать подобное оборудование.
Чаще всего для большинства термистов доступны шахтные и камерные нагревательные электропечи. И не только ввиду стоимости собственно оборудования. Инженерная обвязка универсальной печи с встроенным закалочным баком, агрегатированной в комплексе с моечной машиной и отпускными печами стоит неизмеримо больше.
Одно из условий, принятое во внимание при принятии решения состоит в том, что наш закалочный бак должен быть гибким инструментом.
Немногие наши партнеры могут сказать, что они калят одну и ту же деталь каждый день в течение года. Растет номенклатура деталей и количество обрабатываемых марок сталей.
Общее решение: наш бак должени иметь мешалку с возможностью регулирования потока масла, т.е. управляемый потокообразователь закалочного масла.
В этом случае технолог должен иметь возможность легко регулировать процесс закалки. Например, на тонких деталях, где нет проблем с прокаливаемостью, создавать меньший поток для снижения деформаций, на деталях большего сечения увеличивать поток для обеспечения снятия паровой рубашки.Серьезная проблема – обеспечение равномерного снятия паровой рубашки на деталях, загружаемых в оснастку «навалом».
Всем этим условиям удовлетворяет одна из идей первой половины 70-х годов, прошедшая, по странному стечению обстоятельств, незамеченной широкой общественностью термистов. Причина, возможно, кроется в том, что именно в этот период набирало темпы всеобщее увлечение водными растворами полимеров.Однако, в технической литературе встречались теоретические разработки, доказывавшие очевидную истину: именно ламинарный поток закалочной среды обеспечивает равномерное удаление паровой рубашки с поверхности обрабатываемых деталей.
Линейная скорость потока определяет скорость охлаждения и получаемый при закалке результат.
Линейная скорость потока определяется соотношением ламинарной и турбулентной составляющих.
Повышение турбулентности потока ведет к снижению его ламинарности и снижению его линейной скорости.
Для специалиста по плотинам, турбинам и вообще гидродинамике это очевидные, прописные истины. В приложении к технологии, имеющей 2-х тысячелетнюю историю, они звучат как откровении.В течение последних 20 лет автором данной работы идея реализовывалась при модернизации оборудования на 12 объектах и с обязательным положительным результатом. Доведение же до серийного продукта, в отсутствии объективной потребности и производственной базы, не представлялось целесообразным.
В порядке инициативных исследовательских и опытно-конструкторских работ Компании был изготовлен масляный закалочный бак объемом 700 л.Бак был оснащен системой регулирования температуры: нагреватели ТЭН мощностью 16 кВт, термометр сопротивления градуировки Pt100, регулятор «Термодат-10».При превышении температуры включался насос охлаждения НШ-40, перекачивающий масло через водоохлаждаемый теплообменник.Для создания управляемого потока масла бак был оснащен 4-х лопастной крыльчаткой, установленной в отделенной от основного пространства перегородкой части бака.Крыльчатка имела привод от асинхронного двигателя переменного тока мощностью 4 кВт и максимальным числом оборотов 930 об/мин, рис. 1.
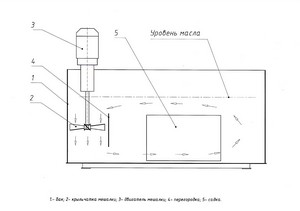
Рабочей температурой был выбран интервал 50…70°С.Первичные испытания методом замера движения марок в потоке показали, что c увеличением числа оборотов скорость потока растет, Рис. 2.
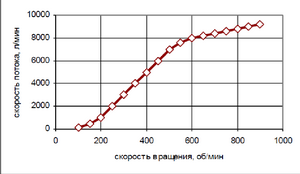
Как видно из приведенных результатов, в диапазоне от 200 до 500 об/мин имеется практически прямо пропорциональная линейная зависимость скорости потока от скорости вращения крыльчатки.
Интересна и достигаемая с двигателем 4 кВт при 600 об/мин скорость потока 8 м.куб./мин.
Закономерен вопрос: каких размеров насос может это обеспечить?
С повышением скорости вращения крыльчатки характер роста скорости потока меняется, прирост скорости потока с увеличением числа оборотов уменьшается, что косвенно свидетельствует об изменении характера потока масла. Для качественной оценки явления были проведены замеры гидростатического давления потока масла. Измерения проводились посредством погруженной в поток трубки, соединенной с U-образным водным манометром.Результаты приведены на Рис. 3.
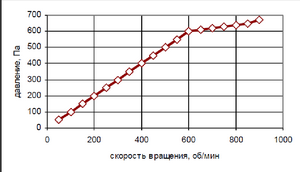
Как видно из приведенных результатов, при достижении и превышении 550…600 об/мин практически не меняются как скорость, так и давление потока масла.
Были проведены замеры распределения давления по сечению бака при различной частоте вращения крыльчатки.
До 600 об/мин разница в давлении в разных точках потока практически не наблюдалась.
С превышением указанной величины разница давления по разным точкам замера достигала 500 Па, наблюдались точки с давлением, равным атмосферному. Естественным следует вывод о переходе потока масла из преимущественно ламинарного в турбулентный при превышении частотой вращения величины 600 об/мин. Для рассматриваемой задачи – получения управляемого закалочного устройства с равномерными и повторимыми результатами - предположительно был необходим интервал именно преимущественно ламинарного потока.Таким образом, для натурных испытаний управляемого потокообразователя был выбран диапазон частоты вращения крыльчатки 100…600 об/мин.Испытания свойств устройства проводили при закалке деталей ст. 40Х в виде пластин толщиной 16 мм и габаритами 120Х200 мм.
Детали загружались в жаропрочную корзину Ø550 мм, высотой 400 мм.
Суммарная загрузка составляла 140 кг, с учетом корзины масса садки составляла 180 кг.
Между деталями размещали образцы-свидетели из сталей 40Х и 30ХГСА Ø30 мм и длиной 50 мм.
Пластины укладывались вертикально с обеспечением возможности их омывания потоком масла, при этом в целях полной загрузки касания пластин не исключали.Нагрев под закалку проводили в шахтной электропечи СШЦМ-6.6/9,5 с защитной атмосферой, температура нагрева 860°С, выдержка 30 минут по достижении температуры.Время выдержки установили контрольным замером с помощью погружной термопары на первой садке и в дальнейшем не меняли.Перенос садки на закалку осуществлялся электротельфером, время переноса составляло в среднем 10 сек.
Температура масла в момент погружения деталей составляла 50°С, при 60°С включался насос охлаждения масла, в дальнейшем температура масла поднималась до 70°С, далее снижалась до установленной.Закалку опытных садок проводили при частотах вращения крыльчатки 15, 250, 350, 450 и 550 об/мин.
На поперечных шлифах образцов-свидетелей и, выборочно, деталей оценивали микроструктуры и изменение твердости по сечению.
Измерение твердости проводили на твердомере Роквелл с нагрузкой 150 кгс. Микроструктуру оценивали после травления 5 % спиртовым раствором HNO3 при увеличении 400 крат.
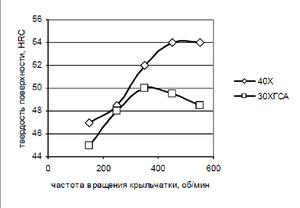
Как видно из приведенных на рис. 4 результатов, твердость поверхности стали 40Х с увеличением числа оборотов растет до 54 HRC при 450 об/мин и далее не меняется.
Твердость поверхности стали 30ХГСА растет с увеличением числа оборотов до 350 об/мин, далее несколько снижается.
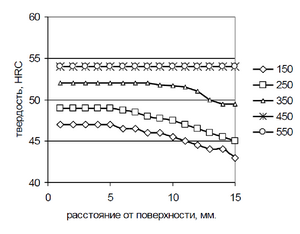
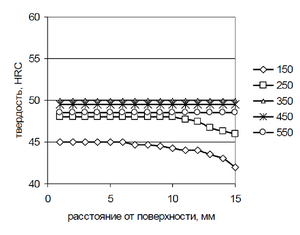
Анализ микроструктуры, например рис. 7 и рис. 8, объясняет снижение микротвердости от поверхности к сердцевине.
Во всех случаях имеет место появление все большего количества феррита.
Его исключение путем подбора оптимальных характеристик работы потокообразователя позволяет обеспечить сквозную закалку с гомогенной твердостью и высокие прочностные характеристики деталей.
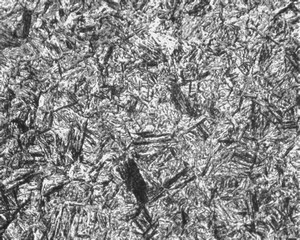
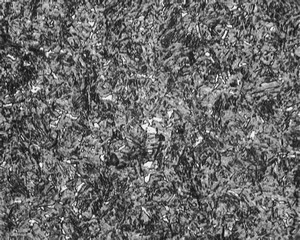
Интересен так же результат по зависимости твердости от скорости потока закалочного масла: для стали 40Х оптимальный диапазон 450…550 об/мин, а для стали 30ХГСА 350 об/мин.
Обращают на себя внимание также непривычно высокие для данных марок сталей величины твердости.Представляется, что обнаруженные эффекты должны быть темой более подробного изучения с привлечением тонких методов исследования.
В целом испытания показали оправданность сделанного выбора.
Cозданный потокообразователь обеспечивает быструю, с минимальным набором измерительных средств и за минимальное время, отладку и оптимизацию процесса закалки для каждой марки стали в зависимости от конфигурации деталей и вида оснастки.
В дальнейшем один раз отработанная технология обеспечивает высокую степень повторимости результатов.
Применяемый фазо-частотный преобразователь показал высокую надежность в работе, простоту настройки и гибкость в управлении.
Управление скоростью врашения осуществляется либо потенциаметром с контролем установленной величины, либо набором тумблеров на заранее запрограммированные частоты. При этом предусматривается возможность дежурного режима – медленное перемешивание масла при разогреве для исключения локалного перегрева в зоне расположения нагревателей.
В течение года эксплуатации на собственном термическом производстве практически не имелось проблем с заниженной или неравномерной твердостью деталей после закалки. Компания, исходя из стратегической линии на комплексное и максимально полное обеспечение требований заказчиков, приступила к комплектации серийных масляных ванн (масляных закалочных баков) управляемых потокообразователем закалочного масла.ЗАО «НПК «Накал»
Читать...
lmx.ucoz.ru
Оборудование и материалы для закалки металлов

Металлы и их сплавы закаливают для повышения твёрдости. Этот процесс имеет многовековую историю – от кузнечного горна и ведра с водой, в которое с шипением опускался раскалённый клинок, до высокотехнологичного оборудования современных металлургических производств.
Закалка металлов и сплавов
Суть закалки состоит в том, что материал нагревают до той температуры, при которой он приобретает новые свойства, а потом резко охлаждают, фиксируя это состояние. Закаливают сталь, а также сплавы цветных металлов (бериллиевую бронзу, например). После закалки металл подвергают отпуску, суть в том, чтобы убрать хрупкость, придав эластичность.
Наиболее широко разработаны процессы закалки стали – с разнообразным оборудованием, материалами, технологиями.
Сталь – сплав железа с легирующими добавками и углеродом, нагревают до той температуры, при которой атомы железа и добавок выстраиваются в кубические гранецентрированные решётки. Внутри этих структур «растворены» атомы углерода. Это аустенит.
Затем материал охлаждают так, что решётки железа с добавками становятся кубическими, а атомы углерода выстраиваются в прямоугольные «пакеты», расположенные между кубическими структурами. Это мартенсит, имеющий игольчатое строение и высокую твёрдость.
Так происходит закалка стали. Основные операции: раскалить и остудить – обеспечивает соответствующее нагревательное оборудование и охлаждающие материалы.
Нагревательное оборудование
В зависимости от глубины и степени закалки, формы и размеров закаливаемой детали применяют разные способы её разогрева.
ТВЧ-установка
создаёт высокую температуру за счёт электромагнитной индукции: средне- и высокочастотный переменный ток, который проходит по петлям индуктора, создаёт вихревые токи на поверхности закаливаемого изделия, расположенного рядом с ним, и нагревает её.
Чем выше частота переменного тока, тем больше раскаляется поверхность изделия.
Понизив частоту, можно достичь нагрева более глубоких участков.
Однако детали большого сечения, а также имеющие сложную поверхность, обработать этим способом не удастся.
Таким образом, к преимуществам установок ТВЧ относится: экономичность и скорость нагрева, отсутствие окалины, деформаций и трещин при закалке, автоматический контроль и механизация процесса.
Недостатками является неэффективность при работе со сложными профилями и массивными деталями.
Соляная электродная ванна
нагревает детали за счёт электролиза соляного расплава. Она представляет собой наполненную солью ёмкость из керамики или металла. В неё погружены электроды, а также электронагреватель, который производит пуск ванны, расплавляя соль. Ванна защищена корпусом и зонтом, расположенным над ней. Такое оборудование обеспечивает быстроту и равномерность нагрева деталей, погружаемых в расплав.
Преимуществами являются: скоростной нагрев, равномерность поля температур (погрешность не выше 1ºС), частичный нагрев (если в ванну погружён только нужный участок детали), отсутствие окисления поверхности металла, высокие температуры (от 800 до 1300ºС, в зависимости от применяемой соли).
К недостаткам относится: выделение вредных испарений с поверхности расплавленной соли, а также взрывной выброс расплава, если в него попадает вода или загружаются влажные изделия.
Камерная печь имеет плотно закрывающийся отсек с обогревом и хорошей теплоизоляцией, во внутреннем пространстве которого создаются высокие температуры — от 800 до 1400ºС. В зависимости от того, чем производится обогрев, камерные печи бывают электрическими, нефтяными и газовыми.
Преимущества таких печей– равномерный нагрев, разработанные механизмы регулирования температуры и управления процессом.
Недостаток – образование окалины в результате взаимодействия металла с атмосферным воздухом при нагреве до высоких температур.
В дополнительно герметизированных печах с устройствами для нагнетания в рабочую камеру защитного газа (аммиак, лёгкие углеводороды) окалина не образуется.
Печь непрерывного горения
В том случае, если технологический процесс предусматривает постоянное закаливание деталей, применяют непрерывно действующие печи. В них, в соответствии с требованиями технологии, производят нагрев и выдержку изделий при заданной температуре в течение контролируемого времени.
По способу подачи изделий на закалку печи непрерывного горения подразделяются на конвейерные, толкательные и протяжные.
Процессы нагрева и выдержки автоматизированы и управляемы. Вместе с тем, закалка в таких печах (без защитного газа) сопряжена с образованием окалины и обезуглероживанием стали.
Вакуумная печь отличается от обычных камерных тем, что внутри неё, помимо высокой температуры, создаётся вакуум – до 5х10-6мбар. В результате снимаются проблемы, связанные с образованием окалины, обезуглероживанием и науглероживанием стали.
Эти печи, снабжённые, помимо нагревателей и теплоизолирующего корпуса, вакуумным насосом, выпускаются в промышленном, более масштабном варианте и с относительно небольшими габаритами – для исследовательских, лабораторных целей.
Материалы для закаливания: среда охлаждения.
При закалке изделие после нагрева требуется охладить. Для этого разогретую деталь погружают в среду с более низкой температурой. Такие среды могут быть жидкими и газообразными.
Вода
является часто используемой для охлаждения стали жидкостью. Если в такой воде присутствует даже малое количество солей либо моющих средств, параметры охлаждения меняются. Поэтому вода должна быть чистой. Частой её замены не требуется. Температура воды должна находиться в интервале от 20 до 30 градусов. Недопустимо охлаждение закаляемой детали в проточной воде.
Недостатком водного охлаждения является возникновение трещин и деформация при этом процессе. Поэтому закаливают в воде преимущественно несложные по форме изделия.
Водный раствор каустической соды
применяют, чтобы закалить изделия сложной конфигурации, изготовленные из конструкционной стали. Концентрация раствора – 50%. Он может быть холодным либо нагретым до 50-60ºС. При такой закалке образуются едкие пары, поэтому рабочее пространство должно обязательно иметь эффективную вытяжную вентиляцию.
Используют также горячие концентрированные растворы щелочей NaOH и KOH.
Минеральное масло
используют при закалке стали с легирующими добавками. В масляной ванне скорость, с которой охлаждается деталь, не зависит от температуры масла. Если масло нагрето до ста градусов и ниже, при попадании воды деталь может растрескаться, но при температуре масла выше 100ºС трещины не образуются.
Масляная закалка, вместе с тем, имеет недостатки: образуются вредные газы; изделие покрывается налётом; закаливающая способность постепенно снижается. Кроме того, минеральные масла легко воспламеняются.
Растворы солей
Горячие (от 150 до 500ºС) расплавы солей и их концентрированные растворы применяют для ступенчатой и изотермической закалки. При этом используются нитраты и нитриты калия и натрия. Интенсивность охлаждения в таких ваннах можно повышать, дополнительно вводя воду. Она поступает в глубину расплава/раствора, частично испаряется, частично поглощается солью. При этом в условиях данной температуры соль поглощает строго определённое количество воды. В результате создаются стабильные условия охлаждения. Температура ванны и содержание в ней воды контролирует автоматика.
Газ
также может охладить раскалённую сталь. С этой целью применяют обдувку изделия осушённым воздухом, подаваемым с помощью компрессора или вентилятора. Кроме того, используют охлаждение с помощью потоков азота, аргона. Продувание изделия инертным газом особенно эффективно при охлаждении в вакуумных печах.
Полное описание процесса закалки
Рассмотрим закалку стального изделия на конкретном примере.
Оборудование: камерная печь. Охлаждающий материал: масло.
Допустим, есть изделие из нержавеющей стали марки 40Х13.
Температура закалки для неё составляет 1050-1100ºС.
Проводят расчёт скорости нагрева. Этот расчёт учитывает форму изделия, расположение его в печи, а также нагревательную среду.
Изделие помещается в камерную печь и нагревается до нужной температуры с рассчитанной скоростью.
По достижении назначенной температуры деталь выдерживается в этих температурных условиях определённое время, чтобы произошёл полный её прогрев и нужные структурные превращения металла.
Затем изделие извлекают и постепенно, круговыми движениями, погружают, до полного остывания, в ванну с минеральным маслом — подходящей охлаждающей средой для легированных сталей, к которым относится 40Х13.
Место, где стоит охлаждающая ванна, должно иметь вытяжную вентиляцию.
Правильно подобранный режим закалки с использованием соответствующего оборудования и материалов позволяет значительно повысить твёрдость металлических изделий.
www.m-deer.ru