- В диэлектрическую (не проводящую ток) емкость заливается электролит.
- Берется блок питания, способный обеспечить необходимое напряжение постоянного тока на выходе (это может быть аккумулятор или несколько батареек, соединенных в электронные цепи).
- К обрабатываемому предмету подключается зажим «+», и предмет погружается в емкость с раствором.
- Зажим «–» крепится на пластинку из свинца или нержавеющей стали и тоже опускается в жидкость.
- Подключается электрический ток нужной величины, согласно электрохимическому уравнению. Благодаря ему на поверхности изделия начинает выделяться кислород, способствующий образованию прочной защитной пленки.
- Повысить устойчивость к коррозии — благодаря тому, что оксидная пленка препятствует проникновению влаги к металлической основе, обеспечивая надежную защиту. Применение такого процесса на быстро ржавеющих предметах обихода или дисках и деталях бытовой техники способно значительно продлить срок их службы.
- Увеличить прочность металла и стали: оксидированное покрытие намного устойчивее к механическим и химическим повреждениям.
- Обработанная таким образом посуда нетоксична, устойчива к длительному нагреву, пища на ней не пригорает.
- Металлические изделия после анодированной обработки приобретают диэлектрические свойства (совсем или почти не проводят ток).
- Возможность провести гальваническое напыление другого металла (хромовое, титановое). Выполненное своими руками, оно способно значительно увеличить прочностно-механические характеристики или повысить декоративные качества (напыление под золото).
- Поверхности дисков и других деталей из металла хорошо очищаются от загрязнений, моются, шлифуются.
- Проводится обезжиривание Уайт-спиритом или ацетоном.
- Выдерживается необходимое время в щелочном растворе (оно рассчитывается по уравнению, исходя из структуры материала).
- После этого диски или другие металлические изделия погружаются в электролит, где проводится анодная и катодная реакция наращивания оксидной пленки.
- Если проводилось холодное обрабатывание изделия, то после извлечения его из емкости следует тщательно промыть от кислоты, просушить. После завершения этого процесса ему обеспечена долгая надежная защита от коррозии.
- При тепловом процессе пленка будет пористая, мягкая, требующая дополнительного закрепления, проводимого путем окунания в чистую кипящую воду или посредством воздействия горячего пара. Потом ее нужно хорошо промыть.
- Проводя анодирования титана, можно брать натрия хлорид, серную или ортофосфорную кислоты.
- Для алюминия применяют щавелевую, хромовую или серную кислоты.
- Вместо кислот для анодной и катодной обработки дисков или других предметов из стали можно использовать поваренную соль с пищевой содой. Сделать необходимый электролит можно, смешав 9 частей концентрированного содового раствора с одной частью солевого.
- При попадании на кожу из-за того, что используется разбавленный препарат, возможны небольшие ожоги. Но для глаз такая концентрация опасна, поэтому не следует пренебрегать защитными очками и перчатками.
- Под воздействием тока выделяются кислородные и водородные пары, которые при смешивании образуют гремучий газ. Работая в плохо вентилируемом помещении, можно получить взрыв от любой искры, который может привести к смертельному исходу.
- Подготовка металлов к образованию оксидной пленки.
- Подготовка раствора
- Покрытие поверхности металлов или их сплавов оксидной пленкой.
- анодированные алюминиевые профиля приобретают значительные защитные свойства;
- поверхность металла получается матовой и однородной;
- процесс позволяет устранить повреждения на поверхности – царапины, сколы, полосы;
- металл приобретает высокие декоративные свойства;
- толщина защитного слоя достаточно большая.
- Оцинкованная сталь ржавеет ли
- Применение углеродистой стали
- Оцинкованная сталь окрашенная
- Сверление нержавеющей стали
- Виды нержавеющей стали и ее классификация
- Влияние легирующих элементов на свойства сталей
- Межкристаллическая коррозия
- Изготовление стропов из стальных канатов
- Марки коррозионностойкие стали
- Полированная сталь
- Марка нержавеющей стали для пищевой промышленности
Как анодировать металл в домашних условиях? Анодное оксидирование стали
Анодирование в домашних условиях - способы и технология
У многих красивое и непонятное слово «анодирование» ассоциируется со сложным физико-химическими технологиями, лабораторными условиями и прочей научной атрибутикой. Мало кто знает, что этот полезный и несложный процесс можно провести при помощи подручных средств: сделать анодирование титана и других металлов реально даже в домашних условиях. Но что это такое, и зачем это нужно для металла?

Название анодирования носит процесс, протекающий при использовании электролита и электрического тока различной величины и позволяющий получить на изделии прочную оксидную пенку, которая повышает прочность стали и обеспечивает защиту от коррозии. Прочностные и механические характеристики меняются в зависимости от состава металла, плотности и вида электролита, величины анодного и катодного воздействия, рассчитываемых по специальным уравнениям.
Собственно защитное покрытие не наносится, а образуется из самого железа в процессе электрохимической реакции. Технология, используемая в домашних условиях, схематично выглядит так:

Анодное оксидирование (анодирование) различных металлов, проведенное в домашних условиях, конечно, сильно уступает тому, что проводится с применением промышленного оборудования. Но, все же, оно способно обеспечить изделию ряд преимуществ:
Кроме того, процесс дает возможность декорирования. Можно сделать цветное анодное оксидирование. Такой результат можно получить, изменяя уравнения силы подаваемого тока и плотности электролита (это возможно, когда проводится анодирование титана и других твердых материалов) или с использованием краски (чаще для алюминия и других мягких металлов, но этот процесс применяется и на твердых основах). Окрашенные таким образом предметы имеют более ровный и глубокий цвет.
Промышленный метод дает более высокую прочность покрытия, возможность провести глубокое анодирование с одновременным нанесением катодной электрохимической пенки, дающей дополнительную защиту от коррозии. Но, даже проведенная в домашних условиях анодно-катодная обработка поможет сделать диски или другие детали движущихся механизмов более прочными, износостойкими.
Разные способы
Провести процесс оксидированной обработки стали в домашних условиях можно двумя способами. Каждый из них имеет свои недостатки и преимущества.
Теплый метод
Наиболее легкий процесс для проведения своими руками. Успешно протекает при комнатной температуре, при использовании органической краски, позволяет создавать удивительно красивые вещи. Для этой цели можно использовать как готовые краски, так и аптечные красители (зеленку, йод, марганец).
Твердое анодирование по такой технологии получить не удастся, оксидная пенка получается непрочная, дает слабую защиту от коррозии, легко повреждается. Но, если сделать окрашивание поверхности после такой методики, то сцепление (адгезия) покрытия с основой будет очень высокой, нитроэмали или другие краски будут держаться прочно, не облезут, обеспечат высокую степень защиты от коррозии.
Холодный метод
Эта методика при проведении в домашних условиях требует внимательного контроля за температурой, допуская ее колебания от –10 до +10°C (оптимальная температура для проведения электрохимической реакции согласно уравнению – 0°C). Именно при таком температурном режиме анодная и катодная обработка поверхности протекает наиболее полно, медленно создавая прочную защитную оксидную пленку. Это позволяет домашнему умельцу своими руками провести твердое анодирование, обеспечив стали максимальную защиту от коррозии.
По этой методике можно сделать гальваническое напыление, нанеся на изделие медь, хром или золото, рассчитав силу тока по специальным уравнениям. После такой обработки повредить деталь или диски из стали очень сложно. Защита от коррозии эффективно действует на протяжении многих лет даже при контакте с морской водой, может использоваться для продления срока службы подводного снаряжения.
Маленьким минусом служит то, что краска на такой поверхности не держится. Для придания металлу цвета используется метод напыления (медь, золото) или электрохимическое изменение цвета под воздействием электрического тока (сила тока и плотность электролита высчитываются по специальному уравнению).
Технология анодного оксидирования
Весь процесс, проводимый своими руками, можно разделить на этапы:
Разновидности электролитов
В домашних условиях применяют не только промышленные химические кислотные растворы, но и простые средства, которые можно найти на любой кухне:
Время выдержки дисков, пластин, других металлических предметов в электролитной емкости под током рассчитывается по уравнению, исходя из физико-химических параметров.
Опасные моменты
При использовании кислот в качестве электролита необходимо строго соблюдать правила техники безопасности. Пренебрежение ими может привести к несчастным случаям:
Соблюдая технику безопасности и этапы технологической обработки, можно получать прочные красивые вещи: хромировать автомобильные диски, создавать ювелирные украшения «под золото», добавлять прочности деталям бытовых механизмов в зависимости от применяемых технологий.
kraska.guru
Анодное оксидирование - Большая Энциклопедия Нефти и Газа, статья, страница 3
Анодное оксидирование
Cтраница 3
Антикоррозионное анодное оксидирование производят для получения защитной пленки толщиной от 5 до 30 мк. Покрытие получают при температуре 13 - 26 С, используя постоянный или переменный ток. [31]
Анодное оксидирование стали проводится в 5 % - ном растворе бихромата калия при температуре 45 - 55 С и плотности тока 3 - 5 А / дм2 в течение 10 - 15 мин. После оксидирования детали промывают в воде и подвергают анодной обработке в растворе едкого натра ( 350 - 650 г / л) при 65 - 80 С и плотности тока 3 - 5 А / дм2 в течение 10 - 30 мин. [32]
Анодное оксидирование меди и ее сплавов проводится в растворах 150 - 250 г / л едкого натра при температуре 80 - 90 С, плотности тока 0 6 - 1 3 А / дм2 и продолжительности обработки 2С - 30 мин. Перед началом работы необходима проработка электролита с медными анодами до получения раствора с голубым оттенком. [33]
Анодное оксидирование титана и его сплавов применяется для декоративной отделки деталей. [34]
Анодное оксидирование меди и ее сплавов ведут в растворе, содержащем 150 - 250 г. л NaOH. Температура электролита 80 - 90 С, анодная плотность тока 0 5 - 2 а / дм2, продолжительность оксидирования 20 - 30 мин. [35]
Цветное анодное оксидирование выполняют путем наполнения оксидных пленок opraiui - ческп:: 1 ( адсорбционное окрашг. [36]
Анодное оксидирование титановых сплавов осуществляется следующим путем. После промывки в холодной воде детали оксидируют в одном из щавелевокислых электролитов с составами и режимами, принятыми для алюминия и его сплавов. При этом оксидная пленка приобретает яркий желтый цвет. [37]
Анодное оксидирование магниевых сплавов проводят в щелочных и кислых растворах. [38]
Анодное оксидирование резьбовых деталей из титановых сплавов предложено ( а. СССР) проводить в импульсном режиме, когда подача тока на ванну чередуется с перерывами. В зависимости от соотношения продолжительности этих периодов изменяются толщина и свойства покрытий. Для обработки сплавов ВТЗ-1, ВТ20 применяют электролит, содержащий 360 - 380 г / л h3SO4 и 15 - 30 г / л НзРО4, при анодной плотности тока в импульсе 3 - 5 А / дм2, длительности импульса 0 1 - 0 3 с, перерыва тока 0 8 - 1 с, частоте 60 - 80 импульсов в секунду. Электролит перемешивают, напряжение на ванне к концу электролиза повышается до 80 - 100 В. В течение 30 - 40 мин на сплавах формируются оксидные пленки толщиной 5 - 6 мкм. [39]
Путем анодного оксидирования из алюминиевых сплавов получают архитектурные детали различной расцветки. [40]
Анодному оксидированию подвергаются металлы с малой электронной проводимостью их окислов, следовательно, это будут окислы с р-типом проводимости. [41]
Процесс анодного оксидирования требует особенно прочного контакта детали с токопроводящей штангой ванны, как по причине большого сопротивления, оказываемого оксидной пленкой, так и из-за сильного перемешивания электролита во время оксидирования. Поэтому подвесные приспособления имеют в этом процессе очень большое значение. Кроме обеспечения надежного крепления подвеска должна также обеспечить удобный и быстрый монтаж деталей. Материалом для подвесок может служить только алюминиевый сплав; при всяком другом металле, не образующем в ванне оксидной пленки с большим электрическим сопротивлением, почти весь ток будет проходить через электролит непосредственно с подвески, минуя оксидируемые детали. [42]
Процесс анодного оксидирования в растворе хромовой кислоты следует регулировать по напряжению на клеммах ванны. Толщина пленки составляет около 3 мкм. [43]
После анодного оксидирования меди и ее сплавов поверхности приобретают черный цвет. [44]
После анодного оксидирования детали промывают в воде, сушат при - 100 СС и протирают салфетками, смоченными минеральным маслом. На деталях из меди и медных сплавов образуется черная пленка из оксида меди ( II), имеющая толщину - - - 1 мкм. Она обладает защитными свойствами, эластичностью и высокой механической прочностью. [45]
Страницы: 1 2 3 4
www.ngpedia.ru
Полезное про анодирование стали
Есть много современных способов обеспечить сохранность металлических конструкций. К наиболее популярным методам относится анодирование стали. Этот процесс так же называют электрохимическим или анодным оксидированием. Его наиболее часто применяют при обработке деталей из алюминия или титана. Плохо нанесению оксидной пленки поддается медь.
Обработанные детали становятся гладкими на ощупь и приобретают светлый оттенок серого цвета. После просушки адгезионные свойства металла улучшаются, и изделие без труда можно покрыть бесцветным лаком или краской нужного цвета.
Компания "ГалСервис" предоставит полный спектр услуг по анодированию алюминия. Большой опыт специалистов, а главное и наличие технической базы проводить анодирование крупных изделий - весом до 1 тонны и максимальными размерами: 2800х700х1300мм.Стоит отметить, что анодирование по своей технологии отличается от процессов гальванического цинкования или хромирования. В данном случае защитная пленка не наносится на поверхность метиза, а формируется из самого металла. Поэтому анодное покрытие по истечению длительного срока эксплуатации не отслаивается и не стирается, в связи с чем изоляционные и декоративные свойства не ухудшаются. Существует два различных по структуре и предназначению вида оксидных пленок – это барьерная и пористая. Первая образуется в нейтральных растворах и может служить в качестве самостоятельного защитного покрытия. Вторую получают в кислых электролитах. Она является хорошей основой под лакокрасочные материалы.
Процесс анодирования стали, помимо обеспечения надежной и стойкой защиты изделий, отличается относительно простой технологией исполнения. Электролитический раствор для небольших деталей можно приготовить даже в домашних условиях, используя питьевую соду и поваренную соль. В качестве источника тока отлично подойдет автомобильный аккумулятор. По времени оксидирование занимает от пятнадцати минут до полутора часов. Но работу с конструкциями больших размеров лучше доверить профессионалам своего дела, компаниям, занимающимся гальваническими покрытиями.
Фирма "ГалСервис" рада предложить своим клиентам услуги по анодированию металлов, а так же другие защитные виды обработки. Все гальванические операции происходят с применением современного оборудования и специализированных препаратов. Вы гарантированно получите отличный результат.
В промышленных масштабах анодирование производится с применением 20% раствора серной кислоты, обеспечивающей высшую степень окисления среды. Этот процесс требует строгого соблюдения мер безопасности и технологического процесса. Перед окунанием в раствор, металл нужно очистить от загрязнений и обезжирить специальным средством на основе щелочи. Плотность тока, необходимого для протекания реакции, должна составлять от 10 до 50 мА/см², а подведенное напряжение – примерно 50-100 В. В зависимости от технологического процесса и времени воздействия раствора на изделие, можно получить пленку толщиной от 1 до 200 мкм. После покрытия металлических конструкций защитным слоем, их необходимо осветлить, отполировать и придать презентабельный вид.
Металлические изделия, прошедшие процесс анодного оксидирования могут без нареканий прослужить долгие годы. Защитные свойства нанесенной оксидной пленки позволяют изделиям стойко переносить самые агрессивные внешние воздействия среды. Именно поэтому анодирование получило широкую популярность в автомобилестроении и военной промышленности, в производстве авиалайнеров и многих отраслях строительства.
Заказав услуги по нанесению различных гальванических покрытий в фирме "ГалСервис", Вы обеспечите долгую и надежную службу металлических изделий.
adamant74.ru
Анодирование металла, его процесс на производстве и в домашних условиях
Содержание статьи
В современном мире имеется большое количество методов обработки металлов и металлических изделий. Они применяются и в промышленных масштабах, и в домашних условиях.
Характеристики анодирования
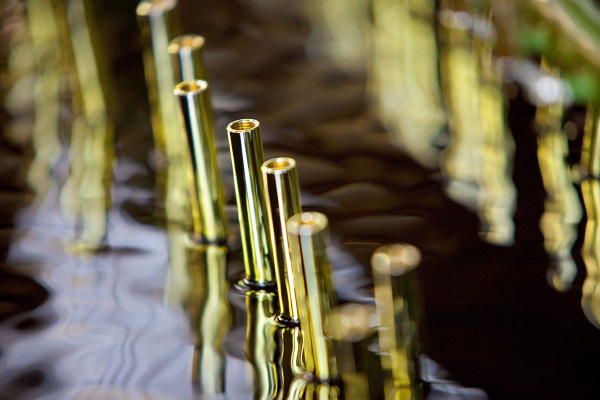
Анодирование представляет собой процедуру образования на поверхности различных металлов оксидной пленки путем анодного окисления. Наращивание оксидной пленки осуществляется в проводящей среде. На поверхности металла такая пленка держится достаточно хорошо.
Наращивание оксидной пленки может осуществлять и благодаря методу повышения температурного режима. Однако при этом она получается низкой по прочности и не держится длительное время. Благодаря электрохимическому способу образования оксидной пленки она получается оптимальной толщины и отлично держится на поверхности материала.
Анодированию можно подвергать разные виды металлов. Основным требованием является то, что они должны иметь возможность образовывать только один оксид. Он должен обладать максимальным уровнем устойчивости. Если металл обладает способностью образовывать сразу несколько оксидов, это может привести к тому, что пленка просто начнет трескаться и не появится защитного эффекта. Именно по этой причине только на редких промышленных объектах встречаются случаи анодирования железа или меди.
Кроме того оксидная пленка на поверхности металлов должна обладать пористой структурой. Это необходимо для того, чтобы электролиты лучше в нее проникали. В результате получается, что лишь небольшая часть всех имеющихся на земле металлов способны удовлетворять данным параметрам. К ним относятся алюминий, тантал, титан. В промышленной и бытовой сфере чаще всего встречается обработка при помощи анодирования алюминиевого материала.
Процесс анодирования
Технология анодирования различных видов металлов является несложной. Главное только иметь под рукой все необходимое для ее осуществления.
Она осуществляется в несколько этапов:
На данном этапе проводятся подготовительные работы для анодирования. Они заключаются в том, чтобы тщательным образом очистить и отмыть поверхность металла. Сначала удаляются все загрязнения и налеты. Затем при помощи воды или специальных растворов проводится промывка материала. После этой процедуры его необходимо высушить.
На данном этапе осуществляется подготовка раствора с кислой или любой другой средой и подключают к положительному плюсу источника тока.
На данном этапе осуществляется погружения металла или изделии я из него в приготовленный раствор.
Материалы для анодирования
Сегодня для анодирования используются различные металлические материалы.
В настоящее время выделяются такие виды анодирования в зависимости от используемых материалов, как:
Анодирование алюминия
Данный процесс сегодня встречается чаще всего. Он заключается в покрытии оксидной пленкой алюминиевого материала. Алюминий в процессе опускается в кислую среду, и к нему проводится положительный плюс источника тока. В результате на материале появляется тонкая оксидная пленка.
Анодирование титана
Всем известно, что титан относится к категории металлов, которые нашли широкое применение в промышленности, но они обладают низким уровнем износостойкости. Для придания ему прочности и устойчивости к разным условиям окружающей среды применяется процедура анодирования. При этом вся анодная обработка металла осуществляется в кислой среде при температуре от 40 до 50 градусов Цельсия.
Анодирование стали
Анодирование стали является сложным процессом. Для этого используется либо щелочная среда, либо кислая. В результате образуется оксидная пленка, которая придает высокий уровень прочности.
Анодирование меди
Медь является достаточно гибким видом металла. Для придания ей прочности используются различные методы. Одним из них является анодирование. Благодаря помещению медного материала в кислую среду, на поверхности образуется плотная пленка оксида, которая придает материалу большое количество полезных характеристик.
Таблица. Таблица совместимости металлов и сплавов
МатериалАлюминийБронзаДюральЛатуньМедьНикельОловоОловянно-свинцовый сплав (припой ПОС)Сталь нелегиро-ванная (углеро-дистая) / чугунХромЦинкАлюминий | Совм | Не совм | Совм | Не совм | Не совм | Не совм | Не совм | Не совм | Совм | Не совм | Совм |
Бронза | Не совм | Совм | Не совм | Совм | Совм | Совм | Пайка | Пайка | Не совм | Совм | Не совм |
Дюралюминий | Совм | Не совм | Совм | Не совм | Не совм | Не совм | Не совм | Не совм | Совм | Не совм | Совм |
Латунь | Не совм | Совм | Не совм | Совм | Совм | Совм | Пайка | Пайка | Не совм | Совм | Не совм |
Медь | Не совм | Совм | Не совм | Совм | Совм | Совм | Пайка | Пайка | Не совм | Совм | Не совм |
Никель | Не совм | Совм | Не совм | Совм | Совм | Совм | Пайка | Пайка | Совм | нет данных | Совм |
Олово | Не совм | Пайка | Не совм | Пайка | Пайка | II | Совм | Совм | Совм | нет данных | Совм |
Оловянно-свинцовый сплав (припой ПОС) |
Не совм | Пайка | Не совм | Пайка | Пайка | Пайка | Совм | Совм | Совм | нет данных | Совм |
Сталь нелегированная (углеродистая)/ чугун | Совм | Не совм | Совм | Не совм | Не совм | Совм | Совм | Совм | Совм | Совм | Совм |
Хром | Не совм | Совм | Не совм | Совм | Совм | нет данных | нет данных | нет данных | Совм | Совм | Совм |
Цинк | Совм | Не совм | Совм | Не совм | Не совм | Совм | Совм | Совм | Совм | Совм | Совм |
Анодирование в домашних условиях
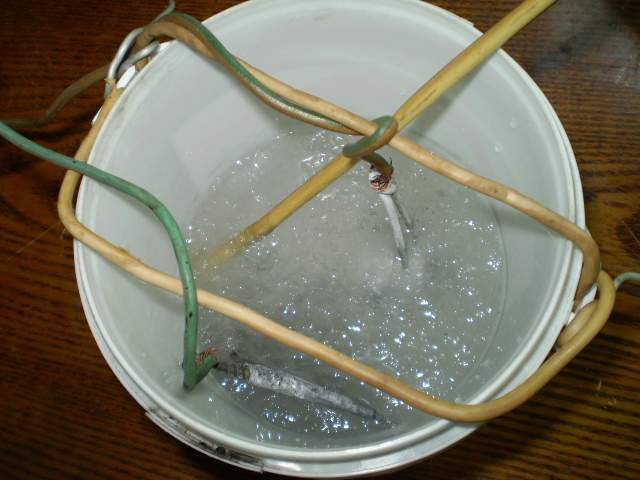
В современном мире в бытовой сфере используется большое количество металлических предметов, которые используются для различных целей. Каждому их владельцу хочется защитить их появления коррозии, чтобы они прослужили длительный период времени. Для этой цели подходит анодирование в домашних условиях.
Важно: Процедуру домашнего анодирования любого металла необходимо осуществлять на улице или на балконе.
Сначала необходимо приготовить раствор. Для этого нужно смешать дистиллированную воду и кислоту в определенной пропорции. С серной кислотой важно обращаться предельно аккуратно, потому что она при попадании в глаза и на кожу может привести к появлению неприятной ситуации.
После этого можно подготовить детали из металлов для обработки. Для этой цели используются всевозможные вещества. Они способны очистить их для проведения процедуры.
На последнем этапе домашнего анодирования осуществляется погружения металлических деталей в раствор и подключение электрического тока.
Видео анодирования в домашних условиях
lkmprom.ru
способы проведения процедуры (+25 фото)
Алюминий – лучший металл для изготовления различных деталей. Его легко обрабатывать, металл имеет легкий вес, высокую прочность и не подвержен коррозии. Но при всех достоинствах внешний вид этого металла не привлекательный. На алюминиевой поверхности очень плохо удерживаются краски, а если на изделие не нанести какое-либо защитное покрытие, то оно покроется темными пятнами. Такая технология, как анодирование алюминия, позволит защитить металл от окисления, а также придаст эффектный внешний вид.
Что такое анодирование?
Анодирование или же анодное оксидирование – процесс, результатом которого является образование на поверхности металла оксидного покрытия. Металл окисляется. Оксидная пленка защищает металлическую поверхность от окислительных процессов, возникающих при взаимодействии алюминия и воздуха. При анодировании окисленное место не удаляется, а формируется более твёрдое покрытие. Технология похожа на воронение.
Для чего анодировать алюминий?
Данный металл при нахождении в естественной среде соединяется с кислородом, на поверхности образуется защитная пленка. Защитный слой не позволяет алюминию окисляться. Однако, эти природные оксиды очень тонкие и могут легко повреждаться. Данная проблема решается при помощи анодирования – это позволит улучшить устойчивость металла к неблагоприятным внешним факторам, а также придать более эффектный вид.
После процедуры анодирования металлу не грозит коррозия. Защитная пленка, которая образуется на металле в процессе анодирования, отличается высокой стойкостью к износу. Такое покрытие не отслоится по пришествию времени.
Покрытие это не является нанесением именно защитного слоя, как это бывает при покрытии стали хромом или цинком. Оксидная пленка в процессе создания анодированного покрытия формируется непосредственно из самого металла. Анодировать можно не только алюминий, но и другие металлы – титан, магний.
Нередко к анодированию прибегают, когда нужно повысить именно декоративные качества данного металла и придать определенный оттенок. Среди цветов популярны светлый или темный золотистый, цвет жемчуга, серебро с матовым блеском. Цвета покрытия можно менять, используют для этого обычные анилиновые красители, использующиеся для одежды.
В промышленных условиях технология анодирования проводится в 20%-ом растворе серной кислоты. Однако, анодирование алюминия в домашних условиях с применением кислоты может быть опасным, кроме того, это очень неудобно. Вы же не станете использовать именно этот метод?
Существует и другая технология, она предполагает использование растворов углекислого натрия и хлористого натрия. Это сода и соль, которые есть на каждой кухне.
На видео: как работает анодирование.
Преимущества процедуры
Можно выделить несколько преимуществ, которые дает данная технология:
Способы анодирования алюминия
Теплое анодирование
Эта технология считается сравнительно простой. Ее можно повторить своими руками. Процесс проводится при комнатной температуре. С помощью простых манипуляций можно получить красивое цветное покрытие при помощи органических красителей. Если приложить определенные усилия, то можно получить несколько цветов на одной и той же детали.
Стоит вспомнить советское оружие – РПО-2, РПС-3, РПО-3. Эти ружья были зелеными, а этот цвет является результатом анодирования алюминия. В качестве красителя применяли зеленку, которая продается в каждой аптеке.
Технология имеет преимущества, но присутствуют и недостатки. Так, анодированный алюминий, обработанный таким образом, не имеет действительно высокой защиты от коррозии. В морской воде, а также в местах контакта с агрессивными металлами возникает коррозия. Обработка металла таким способом также не дает мощной механической защиты – поверхность легко царапается обыкновенной иголкой. Если технология нарушена, то покрытие и вовсе стирается рукой.
Такое покрытие служит основой для покраски. Трудно представить такую высокую адгезию. Если после анодирования алюминиевого профиля окрасить его эпоксидной краской, то получится очень надежное покрытие и эстетичность. Эпоксидная краска будет держаться на поверхности очень много времени.
Теплое анодирование проводится очень просто. Первым делом обезжиривают детали и закрепляют их в подвесе. Выполняют анодирование до молочного оттенка, промывают деталь холодной водой. Окрашивают в горячем растворе красителя и закрепляют окрашенную поверхность в течение часа.
Холодная технология
Этот способ выполняется при низких температурах – от -10° до +10°. Метод изобрели по нескольким причинам: высокое качество, прочность, твердость анодного слоя, а также низкая скорость растворения поверхности и большая толщина слоя. Обычно в домашних условиях анодирование алюминиевых сплавов проводят именно таким образом.
Слой со стороны металла растет, а с внешней стороны – растворяется. Скорость равна тому же показателю при теплом анодировании. Однако, холодная технология может продемонстрировать низкие скорости растворения внешней пленки. Из-за этого и формируется толстый слой. При теплом методе внешний слой растворяется так же быстро, как растет внутренний – получить твердую пленку значительно сложней.
Данная технология требует хорошего охлаждения деталей – только так можно получить качественный результат. Покрытие будет твердым и износостойким. Так, подводному ружью, которое анодировано таким образом, соленая морская вода уже не сможет навредить.
Единственный минус процедуры – невозможность использования органических красителей. Окраска – это естественный процесс, а цвет зависит от состава материала, который обрабатывается. Оттенки в процессе меняются – от зеленого до темного, нередко такая технология дает черный цвет.
Вначале деталь обезжиривают и закрепляют в специальном подвесе. Затем металл анодируют до получения плотного слоя. Далее – промывают в горячей или холодной воде. В конце закрепляют слой с помощью проварки в дистиллированной воде.
Технология твердого анодирования
Твердое анодирование алюминия также позволяет получить твердую и прочную пленку. Технология эта широко применяется в промышленности. Особенность этого способа в том, что в процессе задействован не один, а несколько электролитов. Так, используется не только серная кислота, но и борная, винная, уксусная или щавелевая. Плотность тока медленно растет и за счет изменения структуры на поверхности растет пленка повышенной прочности.
Необходимое оборудование
Мы знаем, что такое анодирование, а теперь следует узнать, какое оборудование для анодирования нужно. Для работы потребуется несколько ванн для разных деталей по размеру. Ванны должны быть алюминиевыми. Еще один вариант – пластик или полиэтилен. Дно и стенку ванны из пластика покрывают алюминиевой фольгой. Это нужно для создания анодно-катодной установки.
Ванна должна обладать хорошими характеристиками теплоизоляции – тогда электролит не будет сильно нагреваться, и его не придется часто менять.
Далее изготавливают катод из свинца. Его делают из листового материала. Площадь этого катода должна быть в два раза выше, чем площадь поверхности обрабатываемой детали. Катодная пластина должна иметь отверстия – через них будут выходить газы.
Когда катод готов, следует приготовить электролит, залить его в ванну, окунуть деталь и подключить к плюсовой клемме источника тока. Свинцовую пластину соединяют с минусовой клеммой. Чтобы металл анодировал, подойдет источник питания на 12 В и 1,5 А. Что касается временных затрат, то для небольших деталей процесс займет около получаса. Для процесса анодирования алюминиевого профиля потребуется несколько часов.
Цвет может быть различным в зависимости от режимов анодирования. С помощью анилиновых красителей алюминиевые детали окрашиваются даже в черный цвет.
Для изготовления анодированного алюминия в домашних условиях у каждого в доме есть необходимое оборудование. Это значит, что можно легко создавать эффектные детали, на которых будет прочный защитный и декоративный слой.
Покраска алюминия в домашних условиях (2 видео)
Анодированный алюминий (25 фото)
gidpokraske.ru
Сталь анодное оксидирование - Энциклопедия по машиностроению XXL
От ванн обезжиривания, травления, покрытия в щелочных, цианистых и хромовых электролитах, фосфатирования, бондеризации, анодного оксидирования алюминия и стали и т.п. отсос воздуха производится посредством местных вентиляционных кожухов (бортовые отсосы). От шлифовальных и полировальных станков отсос производится посредством вентиляционных кожухов от каждого шпинделя. [c.314] Анодное оксидирование (или анодирование) алюминия и его сплавов и фосфатирование стали широко применяются во многих отраслях промышленности. Большая часть деталей, изготовленных из алюминиевых сплавов, подвергается анодированию. [c.3]Ванну анодного оксидирования в хромовом ангидриде (фиг. 18) изготавливают из стали. Ванну подогревают через водяную рубашку 2 такой вид обогрева обеспечивает [c.104]
Оксидные пленки (анодное оксидирование алюминиевых сплавов, щелочное воронение стали, фосфатирование) . 0,95 0,93 4 [c.546]
При сочленении деталей недопустимы контакты магниевых сплавов со сталями, алюминием, медью, никелем и их сплавами допустимы контакты с цинком, оловом, кадмием или деталями из других сплавов, покрытыми этими металлами, а также с деталями из алюминиевых сплавов, прошедшими анодное оксидирование и специально загрунтованными. При наличии лакокрасочного покрытия деталей из магниевого сплава допустим их контакт с деталями из алюминиевых сплавов, не имеющими грунтовки. [c.184]
Анодное оксидирование стали проводится в 5 %-ном растворе бихромата калия при температуре 45—55 °С и плотности тока 3—5 А/дм в течение 10—15 мин. После оксидирования детали промывают в воде и подвергают анодной обработке в растворе едкого натра (350—650 г/л) при 65—80 °С и плотности тока 3—5 А/дм в течение 10—30 мин. [c.485]
Особое внимание должно быть уделено конструированию и изготовлению приспособлений, применяемых для хромирования, анодного оксидирования деталей, изготовленных из алюминия и его сплавов, и электрохимического полирования деталей из стали, меди и ее сплавов и никелевых покрытий. [c.660]
Для анодного оксидирования стали можно использовать 40-процентный раствор едкого натра. Обработку ведут в течение 10—30 мин при температуре 122° С и плотности тока 5—10 а дм . По другим рекомендациям плотность тока может быть понижена до 3—5 а дм при температуре электролита 65—80° С [131. [c.13]
Анодная обработка сопровождается небольшим травлением металла, достаточным, однако, для того, чтобы заметно уменьшился его блеск. Сохранить металлический блеск алюминия можно, лишь предотвратив сопутствующий оксидированию процесс травления. Это достигается применением химического или, что более эффективно, электрохимического полирования. Образующаяся на поверхности металла при такой обработке тонкая пассивирующая пленка препятствует травлению в начальный, самый ответственный период оксидирования и одновременно не создает затруднений для формирования оксидного покрытия. Только благодаря применению в одном технологическом цикле операций анодного полирования и последующего анодного оксидирования, а также адсорбционного окрашивания стало возможным реализовать отделку алюминиевых изделий под золото. [c.241]
Сообщалось об успешном применении анодно-окисных алюминиевых покрытий, полученных погружением в горячий расплав и методом электрофореза. Однако при этом имеются трудности в получении беспористого покрытия. Кроме того, оно должно быть достаточной толщины, чтобы обеспечить возможность анодного оксидирования (анодирования). Дело в том, что анодная пленка толщиной 0,025 мм образуется при расходе металла примерно 0,05 мм от исходной поверхности. В ванне для анодирования поверхность стали должна быть полностью закрыта (изолирована). [c.406]
Лопасть несущего винта вертолета по профилю и конструкции напоминает крыло самолета. Она может иметь пустотелый лонжерон переменного сечения из стали или алюминиевого сплава, нервюры и обшивку из алюминиевого сплава или стеклопластика. Перед окраской лонжерон, нервюры и обшивки из алюминиевых сплавов подвергаются анодному оксидированию в серной или хромовой кислотах. [c.278]
Оксидирование стали с последующей окраской или обработкой маслами. Анодное оксидирование алюминия и его сплавов с последующим нанесением лакокрасочного покрытия или пропиткой маслами. Фосфатирование стали и чугуна с последующей обработкой маслами и лаком [c.81]
К этому виду покрытий относятся оксидирование стали (воронение), меди и ее сплавов, фосфатирование стали, хроматирование цинка и кадмия, анодное оксидирование алюминия (анодирование). [c.150]
Оксидную пленку на стали можно получить в горячем растворе щелочи и селитры, анодным окислением в растворе щелочи, в расплаве нитрата и нитрита натрия или в атмосфере водяного пара, а также методом оксидирования в кислых электролитах. [c.189]
При оксидировании меди температура электролита 80—90° С, при оксидировании латуни 60—70° С. Отношение анодной и катодной поверхности составляет 1 5. Катодами служат пластины из стали. [c.152]
Для электрохимического оксидирования стали используется раствор, содержащий 40% едкого натра. Обработка производится при анодной плотное тока 5—10 а дм , температуре электролита 122°, в течение 10—30 мин. По другим данным, хорошие результаты были получены при следующем режиме оксидирования анодная плотность тока 2,5—5 a/ лi , температура электролита 65—80°, продолжительность электролиза — 10—30 мин. Последний режим более экономичен. Помимо снижения расхода электроэнергии, он позволяет использовать для подогрева ванны пар, что в цеховых условиях иногда более доступно, чем электрический обогрев. [c.15]
В заключение отметим, что электрохимический способ оксидирования стали, который заключается в анодной обработке деталей в горячих щелочных растворах, на практике применяется очень редко. [c.105]
Анодизационные покрытия — анодирование анодное оксидирование) — используются для деталей из нержавеющей стали, магниевых и алюминиевых сплавов. [c.162]
Рефлекторы изготовляют серебрением поверхности соответствующим образом отформованного полиакрилатного элемента или полировкой и анодным оксидированием заготовки, изготовленной из листа алюминия или нержавеющей стали. Рефракторы состоят из нескольких рассеивающих (как было описано выше) свет призм. [c.412]
Хорошими покрытиями для отделки подобных деталей являются фосфатные, оксидо-фосфатные и никелевые однослойные покрытия. Не допускается производить анодное оксидирование алюминиевых литейных сплавов с арматурой из стали, латуни, бронз и т. д. [c.648]
Анодное оксидирование бериллия производят в электролите, состоя щем из 20-процентного раствора хромового ангидрида при рабочей тем пературе 10° С и плотности тока 10 а/дм с катодами из стали 0Х18Н10Т При выдержке 1 ч оксидная пленка имеет черный цвет, толщину 15—17 мкм пористость до 40% и высокое электрическое сопротивление. [c.184]
Шсцдные пленки (анодное оксидирование алюми-ниевых сплавов, оксидирование стали, фосфатирование) Ванна 0,8 [c.545]
Сульфатный электролит обладает высоким травящим действием, поэтому не пригоден для анодного оксидирования сложнопрофильных, сварных и клепаных деталей. Для уменьшения растравливающего действия в электролит вводят щавелевую кислоту в количестве 10—20 г/л электролит во время работы перемешивают очищенным воздухом, а температуру поддерживают в интервале 18—24 °С. Для охлаждения электролита используют водяные рубашки и змеевики или фреоновые холодильные установки из коррозионностойкой стали или титана. [c.492]
Фосфатированию можно подвергать углеродистые и низколегированные стали, чугун, некоторые цветные и легкие металлы алюминий, магний, цинк, кадмий. Высоколегированные стали фосфатируются с трудом и дают пленки более низкого качества. Фосфатные пленки на алюминии и магнии являются менее надежной защитой этих металлов от коррозии, чем пленки, полученные анодным оксидированием. [c.95]
Значительное улучшение защитных свойств цинковых покрытий достигнуто [35] благодаря осаждению их на сталь, предварительно оксидированную в горячем растворе, содержащем 600 г/ л NaOH и 500 г/л NaNOs. Никелевые покрытия из электролита с добавкой 2,6—2,7-дисульфонафталиновой кислоты и медные из сульфатного раствора показали хорошее сцепление с низкоуглеродистой сталью и сравнительно небольшую пористость, если их осаждали на предварительно анодно оксидированный металл. Анодирование проводили в течение 3 мин при комнатной температуре в электролите, содержащем по 200 г/л КОН и NaaP04 [36 . [c.71]
Анодная обработка в щелочной ванне производится следующим образом. Навеска с деталями после промывки помещается на штангу щелочной ванны, нагретой до 65—70° и обрабатывается током плотностью 25—40 а/дм-в течение от 30 секунд до двух минут. Направление тока через 30—45 секунд меняется, если первоначально деталь завешивалась на катод, и остается постоянным, если деталь сразу служила анодом. В последнем случае время обработки несколько увеличивается. Продолжительность обработки зависит от плотности тока, от марки стали и от возраста работающего электролита. Известно, что различные марки стали оксидируются с разной скоростью. В процессе работы по новому способу на заводе Авторемлес замечено, что чем дольше работает щелочной электролит, тем скорее протекает оксидирование деталей. Время обработки определяется визуально обработку можно считать достаточной после того как по верхность (нетравленых) деталей слегка потемнеет от образовавшейся оксидной пленки и приобретет такой вид, будто детали слегка прокоптили над костром. Если после 30-секундной обработки такого потемнения не обнаруживается, обработку продолжают еще 30 секунд и т. д. Неравномерностью потемнения смущаться не следует, на качество травления эта неравномерность влия ния не оказывает. Неравномерность потемнения объясняется различной толщиной образовавшейся оксидной пленки, что зависит от рассеивания электрического поля ванны. В дальнейшем вся пленка уничтожается в электролите осталивания и нужно лишь следить, чтобы были удалены и наиболее темные места (участки с наиболее толстой пленкой). [c.44]
Несколько неожиданные результаты были получены с дюралюминием, который имел на своей поверхности анодную окисную пленку. Если в отсутствие окисной пленки потеря механических свойств у плакированного сплава была незначительной, то у оксидированного ллакированного дюралюминия наблюдалась значительная потеря меха-лических свойств, когда он находился в контакте с катодными металлами (рис. 54). Иначе говоря, Павлов пришел к заключению, что катодные контакты представляют для оксидированного плакированного дюралюминия большую опасность, нежели для неоксидированного. Объясняет эти результаты автор следующим образом наличие окисной пленки на ловерхности плакированного дюралюминия способствует, с одной стороны, локальной коррозии, а с другой, исключает возможность электрохимической защиты плакированного слоя, поскольку он стал менее активным. Из-за наличия относительно толстой окисной пленки плакированный слой перестает, по мнению Павлова, выполнять свою основную функцию — электрохимически защищать сплав сердцевины. [c.170]
Автоматические линии оснащаются вспомогательным оборудованием ваннами селективной очистки, установками БРП (бесконтактный переключатель), буферными и запасными ваннами. Ванны селективной очистки предназначены для электрохимической очистки никелевых электролитов от металлических загрязнений. Они изготовлены из стального футерованного корпуса, двух катодных и четырех анодных рядов. Установка БРП устанавливается на ванне для включения и выключения реле времени, технологического тока и воздуха. Буферные ванны используются при очистке зеркала электролита в ваннах обезжиривания и состоят из корпуса со сливным карманом и крышки с люком. Запасные ванны служат для приготовления или хранения электролитов при ремонте ванн или фильтрации растворов и состоят из сварного корпуса и крышки с люком. Эти ванны имеют три модификации для цианистых и кислых электролитов, для электролитов фосфатирования и хромирования и электролитов щелочного лужения и оксидирования стали. Автооператорные линии для цинкования на подвесках модели АЛГ-35М разработаны ЦКБ ГП (рис. 3. 38 и 3.39). [c.125]
Оксидирование черных металлов нашло широкое применение в технике защиты их от атмосферной коррозии. Оксидную пленку на стали можно получить как электрохимическим (анодным) окислением в электролитах, так и путем химической обработки стали -в кислых или чаще щелочных окислительных средах при повышенных температурах, например в концентрированных растворах щелочи и селитры, в расплаве нитрата натрия, а также нагревом в атмосфере водяного пара (паротермический метод). Наибольшее распространение [c.230]
Анодирование сталей имеет декоративное или вспомогательное значение как средство получения подслоя для других более эффективных покрытий. Обработка производится в 40—56% растворе NaOH при анодной плотности тока 2,5—10 А/дм и 80—120 °С. Оксидирование хрома в отличие от других металлов производят катодной обработкой. [c.56]
Процессы пассивации металлов, т. е. их перехода в пассивное состояние, имеют значение не только при электроосаждении металлов, но и для процессов анодного и химического оксидирования. Здесь наиболее важным является получение на поверхности металла плотной, прочносцепленной оксидной пленки с заданными свойствами. Поэтому процесс электрохимического оксидирования всегда проводили, задавая металлу потенциал в области пассивности или перепассивации, т. е. в той области поляризационной кривой, где на электроде возможен рост пассивирующей пленки, причем неважно, задается ли потенциал от внешнего источника напряжения (электрохимическое оксидирование) или составом раствора, содержащего окислитель (химическое оксидирование). Качественно рассмотрим процесс хими ческого оксидирования стали в щелочи при повышенной температуре. При контакте железа с раствором устанавливается стационарный потенциал Ест, соответствующий равенству токов растворения железа и восстановления кислорода. Как видно из рис. 1.9, потенциал будет находиться в области пассивности железа и на нем образуется пассивная пленка. [c.26]
Покрытия, наносимые путем распыления (пульверизации) расплавленного металла на поверхность изделий. Наиболее распространена металлизация алюминием, цинком, кадмием, никелем. свинцом, оловом, бронзой, медью и нержавеющей сталью Покрытия, получаемые анодной обработкой защищаемого металла в соответствующих электролитах с применением тока от внешнего источника с образованием окисных защитных пленок на железе, алюминии и алюминиевых сплавах, а также на меди, медных сплавах и цинке Покрытия, получаемые на поверхности металлов при воздействии химических реагентов, без применения тока оксидирование и фосфатирование черных металлрв, оксидирование магниевых сплавов, меди, медных сплавов, цинка и др. [c.14]
В отличие от химических способов электрохимическое оксидирование более универсально и позволяет получать прочные черные пленки на меди и большинстве сплавов на ее основе, включая и оловянистые бронзы. Процесс ведут в обычной стальной ванне при анодной плотности тока 0,5—1,5 а1дм . Электролитом является 207о-ный раствор едкого натрия, нагретый до температуры 80—90° С. В качестве катодов применяются пластины из нержавеющей стали или никеля. Время обработки не превышает 30 мин. При этом необходим надежный контакт деталей с медными электродными подвесками. Большая, по сравнению с химическим, трудоемкость электрохимического оксидирования медных сплавов окупается дешевизной и стабильностью рабочего раствора, а также лучшим качеством оксидной пленки. [c.106]
Часто для повышения антикоррозионных свойств анодных пленок на магнии и его сплавах оксидированные детали обрабатывают в слабых растворах бихромата калия. В качестве катодов в хромовокислых электролитах применяется листовой свинец, а в щелочных — ма[Лоуглеродистая сталь. Ванны не отличаются по конструкции от применяемых при оксидировании алюминиевых сплавов. Нагрев электролита через водяную рубаш- [c.111]
mash-xxl.info
Электрохимическое оксидирование - Большая Энциклопедия Нефти и Газа, статья, страница 3
Электрохимическое оксидирование
Cтраница 3
Обычно химическое и электрохимическое оксидирование производится в растворе едкой щелочи. Электрохимическое оксидирование имеет длительность 10 - 30 мин при анодной плотности постоянного тока 5 - М0 А / дм2 и температуре электролита 122 С. Подготовка поверхности заключается, как и при гальванических методах, в механической обработке, обезжиривании и травлении. Качество пленок при химическом и электрохимическом оксидировании стали - почти равноценное. Толщина пленок составляет 0 6ч - 0 8 мкм, но может достигать 1 5ч - 3 мкм. Пленки - эластичные, но непрочные и не могут быть использованы для деталей, работающих в условиях трения. Вследствие малой толщины и значительной пористости оксидные пленки защищают от коррозии при работе в легких условиях. Защитная способность их может быть повышена обработкой смазочными маслами или покрытием лаками. Размеры деталей при оксидировании практически не изменяются. Цвет оксидной пленки на малоуглеродистых сталях - черный, на высокоуглеродистых - черный с серым оттенком. [31]
Различают химическое и электрохимическое оксидирование ( анодное окисление) алюминия. Электрохимические методы, несмотря на их сложность, используют чаще, так как получаемые при этом оксидные пленки обладают самыми разнообразными свойствами. [32]
Для электрохимического оксидирования в качестве электролита применяется раствор хромовой, серной или щавелевой кислоты. В СССР для этой цели применяется только раствор хромовой или серной кислоты. [33]
Примером электрохимического оксидирования может служить анодирование алюминия. В ванну, заполненную 20 % - ной ( по массе) h3S04, загружают на 20 мин изделия, соединенные с положительным полюсом. [34]
Примером электрохимического оксидирования может служить анодирование алюминия. В ванну, заполненную 20 % - ной h3SO4, загружают на 20 мин изделия, соединенные с положительным полюсом. [35]
Для электрохимического оксидирования меди и ее сплавов применяют раствор, содержащий 150 - 250 г. л едкого натра. Продолжительность оксидирования составляет 20 - 30 мин. Раствор перед пуском в эксплуатацию прорабатывают с медными анодами до появления светло-голубой окраски. Катодами при оксидировании служат листы стали. Детали загружают в ванну на медных подвесках с хорошими электрическими контактами. При этом рекомендуется выдерживать детали в электролите без тока I / - 2 мин, затем включать ток и вести электролиз, постепенно повышая плотность тока. Продолжительность оксидирования может быть сокращена за счет соответствующего увеличения плотности тока. [36]
Для электрохимического оксидирования стали используется раствор, содержащий 40 % едкого натра. Обработка производится при анодной плотноста тока 5 - 10 а / дм2, температуре электролита 122, в течение 10 - 30 мин. По другим данным, хорошие результаты были получены при следующем режиме оксидирования: анодная плотность тока 2 5 - 5 а / дм2, температура электролита 65 - 80, продолжительность электролиза - 10 - 30 мин. Последний режим более экономичен. Помимо снижения расхода электроэнергии, он позволяет использовать для подогрева ванны пар, что в цеховых условиях иногда более доступно, чем электрический обогрев. [37]
Для электрохимического оксидирования магния и его сплавов применяются щелочные и хромовокислые электролиты. Обрабатываемые детали завешиваются в ванну в качестве анода. [38]
Метод электрохимического оксидирования металлов, при котором оксидируемое изделие является анодом. [39]
Для электрохимического оксидирования меди и ее сплавов применяется раствор, содержащий 150 - 250 Г 1л едкого натра. Продолжительность оксидирования составляет 20 - 30 мин. Раствор перед пуском в эксплуатацию прорабатывают с медными анодами до появления светло-голубой окраски. Катодами при оксидировании служат листы стали. Детали загружают в ванну на медных подвесках с хорошими электрическими контактами. При этом рекомендуется выдерживать детали в электролите без тока 1 - 2 мин. Продолжительность оксидирования может быть сокращена за счет соответствующего увеличения плотности тока. Рекомендуется следующий форсированный режим оксидирования: в течение первых 5 мин. [40]
При электрохимическом оксидировании большое влияние на скорость растворения металла и образования окисной пленки оказывает электрический режим процесса. Повышение анодной плотности тока ускоряет растворение железа и образование центров кристаллизации. Более толстые оксидные пленки получаются при сравнительно низких плотностях тока. [41]
При электрохимическом оксидировании скорость растворения металла и образования окисла определяется не только составом раствора, но и электрическим режимом процесса. Повышение анодной плотности тока ускоряет растворение железа и образование центров кристаллизации. Более толстые оксидные пленки получаются при сравнительно низких плотностях тока. [42]
При электрохимическом оксидировании в качестве анода используется изделие, а катодом являются свинцовые пластины. Получаемые на поверхности алюминия оксидные пленки служат хорошей основой для лакокрасочных покрытий и широко применяются для защиты от коррозии. Кроме того, они хорошо адсорбируют красители, поддаются окраске в различные цвета и имеют красивый внешний вид. [43]
При электрохимическом оксидировании размеры деталей почти не изменяются; пленки получаются более прочными, чем при химическом оксидировании, но обработка дороже и сложнее. [44]
При электрохимическом оксидировании толщина оксидных пленок достигает 100 мк и выше. Пленки, полученные электрохимическим путем, обладают ценными механическими, электриче - скими и физико-химическими свойствами. Поэтому анодная обработка алюминия и его сплавов применяется не только для защиты деталей от коррозии и их декоративной отделки, но и для получения электроизоляционного слоя, повышения стойкости против истирания, получения фотоизображений на поверхности изделий. [45]
Страницы: 1 2 3 4
www.ngpedia.ru