- С неупрочняемой сердцевиной. В данную группу входят такие марки цементируемых сталей углеродистых, как 10, 15, 20. Используют их в деталях с небольшими размерами и малоответственными функциями. В данном случае под цементируемым слоем при осуществлении закалки происходит превращение аустенита в феррито-перлитную смесь.
- С сердцевиной, упрочняемой слабо. В состав этой группы включают хромистые низколегированные стали таких марок, как 15Х, 20Х. Здесь проведение дополнительного легирования с помощью малых добавок ванадия обеспечивает получение более мелкого зерна, что приводит к улучшению пластичности и вязкости материала.
- С сильно упрочняемой сердцевиной. Стали данной группы применяют при изготовлении деталей, которые обладают большим сечением или сложной конфигурацией, а также испытывают влияние значительных ударных нагрузок или подвергаются воздействию немалых переменных напряжений. В них осуществляют введение никеля (12Х2Н4А, 12ХНЗА, 20ХН). Из-за дефицитности данного материала иногда проводят его замену марганцем, при этом применяют ввод небольшого количества ванадия или титана для дробления зерна.
- твердую среду;
- жидкую среду;
- газовую среду.
- в твердой среде;
- в жидкости;
- в газе;
- в вакууме.
- Детали, предназначенные под цементацию, закладываются в металлические ящики, при этом равномерно пересыпаются угольным составом.
- Ящики герметизируются и подаются в заранее нагретую печь.
- Первоначально производится прогрев до температурных показаний порядка 700С — 800С.
- Контроль прогреваемости производится визуально. Ящики и подовая плита имеют равномерный цвет без затемненных пятен.
- Далее температуры в печи увеличивают до требующихся 850С 950С. В данном диапазоне происходит диффузия внедрения атомов углерода.
- Длительность выдерживания деталей в печи напрямую зависит от требуемой толщины слоя.
- При данном методе детали помещаются в холодную печь.
- После герметизации камеры нагрева в ней создается вакуум.
- Затем производят нагрев до требуемой температуры.
- Производится выдержка, которая занимает до часа по времени. За это время выравнивается температура и с поверхности нагретых деталей осыпаются загрязнения, мешающие науглероживанию.
- Затем подается в камеру углеводородный газ под давлением. За счет чего происходит активная фаза обогащения поверхностного слоя.
- На следующем этапе происходит диффузионное внедрение углерода. На этом этапе в камере опять создают вакуумическое давление.
- За короткий промежуток времени не получается требуемого науглероженного слоя, поэтому процесс повторяют до тех пор, пока не получится требуемая глубина. Обычно результат получается за три стадии.
- Охлаждение до температуры окружающей среды происходит в печи под действием инертных газов под разным давлением.
- регулирование количества углерода;
- отсутствие кислорода предотвращает образование окислов;
- газ проникает даже в отверстия минимального диаметра;
- чередование процессов происходит при равных условиях;
- полная автоматизация; сокращенные сроки.
- газообразные среды;
- растворы электролитов;
- пастообразные среды;
- кипящий слой;
- твердые среды.
- Компоненты смеси (соль и уголь) тщательно перемешиваются в сухом состоянии. Если пренебречь этим требованием, то после окончания процесса цементации на поверхности изделия могут образоваться пятна.
- Соль растворяют в воде и полученным раствором поливают древесный уголь, после чего его просушивают до достижения влажности не более 7%.
- Подготовленные для обработки детали укладывают в ящики, пересыпая слоями карбюризатора.
- Наполненные ящики, обмазанные огнеупорной глиной, помещают в предварительно прогретую печь.
- Выполняют так называемый сквозной прогрев ящиков с деталями, при котором они нагреваются до температуры 700–800 градусов Цельсия. О том, что ящики хорошо прогрелись, судят по цвету подовой плиты: на ней не должно быть темных пятен в местах соприкосновения с тарой.
- Температуру в печи поднимают до 900–950 градусов Цельсия. Именно при таких значениях проводят цементацию стали.
- нагревают стальную емкость и подают в нее керосин, который при испарении разлагается на смесь газов;
- состав некоторой части (60%) полученного газа модифицируют (крекирование).
- обеспечение лучших условий для обслуживающего персонала;
- высокая скорость достижения требуемого эффекта за счет того, что детали в газовой среде могут выдерживаться меньшее количество времени (к тому же не требуется время для приготовления твердого карбюризатора).
- Благодаря процедуре цементируемые стали становятся прочнее, что повышает износостойкость и прочность материала;
- Свойства эксплуатации металла изменяются за счет нагрева изделий в жидкости, газовой или твердой среде, что улучшает ее характеристики;
- Нагревание деталей можно до разных температур, нет ограниченной константы и точных рекомендаций. В домашних условиях процесс цементации проходит при температуре 500 градусов по Цельсию. В промышленных условиях с использованием профессионального оборудования температура нагрева в печи достигает более 1300 градусов по Цельсию. Следует знать, что температуру выбирают, учитывая концентрацию примесей и углерода.
- Профессионалы рекомендуют в домашних условиях цементировать низкоуглеродистые виды стали (приблизительно 0,2%). Например, лезвие от недорогого кухонного ножа, изготовленного из стали или небольшие детали.
- В структуру стали углерод проникает довольно медленно. Поэтому цементация лезвия ножа в условиях домашней процедуры происходит со скоростью не более 0,1 мл в час. Чтобы это же лезвие выдерживало более сильные нагрузки, нужно усиливать слой толщиной до 0,8 мл в час. Еще важно понимать, что цементация ножа или небольшого вала в условиях домашнего цеха займет минимум восемь часов. При этом следует удерживать определенную температуру в печи, чтобы не нарушить температурный режим.
- В процессе цементации изменяется не только свойство металла, но и его фазовый состав и атомная решетка. В целом поверхность получает такие же характеристики, как и при закалке, но при этом существует возможность контроля в узком диапазоне температур, чтобы избежать различных дефектов материала.
- в твердой;
- в газообразной;
- в растворе электролита;
- в виде специальной пасты;
- в кипящем слое.
- Сталь с неупрочняемой сердцевиной. В эту группу входят следующие марки стали, пригодной для цементирования — 20, 15 и 10. Эти детали имеют небольшой размер, используются для эксплуатации в бытовых условиях. Во время закалки происходит трансформация аустенита в феррито-перлитную смесь.
- Сталь со слабо упрочняемой сердцевиной. В эту группу вошли металлы таких марок, как 20Х, 15Х (хромистые низколегированные стали). В этом случае проводят дополнительную процедуру лигирования с помощью небольших доз ванадия. Это обеспечивает получение мелкого зерна, что приводит к получению более вязкого и пластичного металла.
- Сталь с сильно упрочняемой сердцевиной. Этот вид металла используют для изготовления деталей со сложной конфигурацией или большим сечением, которые выдерживают различные ударные нагрузки, подвергаются воздействию переменного тока. В процессе закалки вводится никель или при его дефиците используют марганец, при этом для дробления зерна добавляют малые дозы титана или ванадия.
- Уголь из дерева поливают солью, которую предварительно растворяют в воде. Получившуюся смесь высушивают, ее влажность должна быть не более 7%.
- Сухой уголь и соль тщательно перемешивают, чтобы исключить возможность появления пятен уже в процессе химической и термической обработки.
- детали, которые необходимо закалить, равномерно укладываются в ящики, наполненные твердым карбюризатором;
- печь разогревают до 900−1000 градусов и подают в нее тару с изделиями;
- прогрев ящиков проходит при температуре от 500 до 700 градусов. Этот прогрев называют сквозным. Сигналом, что печь накалилась до нужной температуры служит однородный цвет подовой плиты, на ней больше нет темных участков под ящиками;
- температуру поднимают до 900 или 1000 градусов по Цельсию.
- в специальную емкость из стали наливают керосин, нагревают до процесса пиролиза — разложения керосина на смесь из нескольких газов;
- примерно 60% этого газа модифицируют и делают подходящим для цементации.
- меньше времени затрачивается на подготовку сырья для цементации;
- более благоприятные и безопасные условия для труда рабочих;
- ускорение процесса закалки за счет сокращения времени на выдержку изделий.
- газовые;
- пастообразные;
- твердые;
- растворы электролитов;
- кипящий слой.
- В качестве основных компонентов используется сухая соль и уголь, которые необходимо основательно перемешать друг с другом, тем самым удастся снизить до минимума риск появления пятен во время химико-термической обработки стали;
- На подготовленный древесный уголь нужно лить соль, предварительно смешанную с водой до растворения. Далее созданную на основе этих компонентов массу необходимо поместить для высушивания, причем оптимально, когда влажность смеси не превышает 7%.
- Нуждающиеся в насыщение углеродом детали следует разместить с чередованием в ящике, заполненном заранее приготовленной смесью;
- Далее готовят к работе печь, для чего ее прогревают до температуры 900-950 градусов, затем туда размещается рабочая тара;
- Сама операция по прогреву ящика выполняется при температуре от 700 до 800 градусов. Определить, что ящики прогрелись достаточно, можно по подовой плите, которая должна иметь однородный цвет;
- На заключительном этапе температуру печи увеличивают до отметки 900-950 градусов Цельсия.
- создание более комфортных условий для персонала;
- сокращение времени, необходимого на выполнение обработки, что достигается благодаря уменьшению срока выдерживания деталей и отсутствию необходимости в длительном приготовлении карбюризатора на основе угля.
Цементирование стали и цементация металла в домашних условиях. Цементация стали 20
Цементация стали - технологический процесс и его описание. Цементация стали в домашних условиях
Сама по себе цементация стали является процессом, в основе которого лежит химико-термическая обработка. Суть ее состоит в осуществлении диффузионного насыщения поверхности указанного материала достаточным количеством углерода при нагревании в определенной среде.
Цементация стали. Цель данного действия
Основной задачей указанного процесса является проведение обогащения верхнего слоя машинных деталей и элементов необходимым количеством углерода, процентное содержание которого в данном случае может составлять 0,8-1,1%. В результате такой операции после осуществления закалки получают высокий уровень твердости материала, при этом его пластичная сердцевина сохраняется. Это немаловажные свойства данного процесса.
Разновидности
По степени прочности образования сердцевины принято выделять три основные группы обрабатываемого материала:
В основном цементация стали используется для образования высокого процентного соотношения твердости поверхности детали, а также для достижения высокой износоустойчивости, которая создается благодаря применению термической обработки после проведения указанного процесса.
Какие детали подвергаются данной операции
Цементация стали применяется для следующих изделий:
- зубчатых колес;
- "пальцев";
- валов;
- осей;
- рычагов;
- "червяков";
- деталей подшипников (крупногабаритных колец и роликов) и др.
Способы цементации
Если существует несколько видов указанного материала, то для каждого из них будет применяться своя собственная методика данного процесса. Как правило, цементированная сталь может создаваться в различных условиях и средах, а также при обязательной температуре от 850 до 950 градусов по Цельсию. Поэтому разделяют несколько методов этого действия:
1. Процесс цементации, происходящий в твердом карбюризаторе. В этом случае возможно использование органических веществ (костей животных, древесины и т.д.) и неорганических (кокса) в сочетании с различными активаторами. Обогащение углеродом будет происходить при проведении химической реакции его окисления. Применение активаторов в данном случае способствует лучшему и быстрому ее протеканию. Такой метод особенно целесообразен для достижения больших глубин науглероживания. Он является эффективным при штучном изготовлении стальных изделий. Однако данный процесс очень трудоемкий, он влечет за собой большие затраты сил, времени и энергии.
2. Процесс цементации, происходящий под воздействием газов. В данном методе принято использовать обогащенные газы (природный, магистральный и др.) или категорию инертных (азот). Все зависит от индивидуального подхода. К тому же цементируемая сталь на основе газов создается с малым процентом алифатических предельных углеводородов, пропана или алканов. Чаще всего этот метод применяется в масштабном производстве, но является очень затратным в плане денежных средств. Похожий способ применяется при термическом производстве. При этом в горячую ротортную печь вводят смеси органических высокомолекулярных соединений (например, скипидара, этилового спирта и т.д.), которые, в свою очередь, обладают способностью распада под влиянием катализаторов (никелевых).
3. Процесс жидкостной цементации. Его применяют в цианидных и бесцианидных ваннах. Каждая из этих сред характеризуется своими особенностями, преимуществами и недостатками. К примеру, цианидные ванны не относятся к категории безвредных. Их принято классифицировать как опасные носители не только для окружающей среды, но и для человека. Поэтому при работе с таким материалом необходимо стараться соблюдать все предписанные меры безопасности, чтобы избежать неблагополучных последствий. А вот метод, основанный на бесцианидной ванне, не рекомендовано применять в силу того, что он ведет к необратимому загрязнению окружающей среды и наносит ей огромный урон. Указанные способы если и применяют на практике, то только лишь для получения небольших глубин науглероживания.
Термообработка цементованных изделий
Данный процесс является также достаточно важным этапом обработки деталей. Ведь даже после цементации изделие не обладает высоким процентом износостойкости и надёжности. Поэтому завершающим шагом в данном случае служит работа по закаливанию и отпуску. Процесс закалки характеризуется рядом особенностей и свойств. Весь процесс цементации проходит под влиянием роста зерна, а его отдача по сечению является неодинаковой и расходуется неравномерно. Поэтому в работе выделяют несколько этапов закалки, каждый из которых происходит в определённых температурных условиях.
Вывод
Ознакомившись с вышесказанным, можно сказать, что организация указанного процесса при изготовлении стальных изделий является очень важной. Данное действие значительно укрепит поверхностный слой детали. При обладании определенными навыками в этой сфере и наличии необходимых материалов и оборудования может быть осуществлена цементация стали в домашних условиях.
fb.ru
Цементация стали: цель, технология процесса, режимы
Цементация металла – это вид термической обработки металлов с использованием дополнительного химического воздействия. Атомарный углерод внедряется в поверхностный слой, тем самым его насыщая. Насыщение стали углеродом, приводит к упрочнению обогащенного слоя.

Цементация стали
Процесс цементации
Целью цементация стали является повышение эксплуатационных характеристик детали. Они должны быть твердыми, износостойкими снаружи, но внутренняя структура должна оставаться достаточно вязкой.
Для достижения данных требований требуется высокая температура, среда, выделяющая свободный углерод. Процесс цементации применим к сталям с содержанием углерода не больше двух десятых долей процента.
Для науглероживания слоя наружной поверхности, детали нагревают с использованием печи до температуры в диапазоне 850С — 950С. При такой температуре происходит активизация выделения углерода, который начинает внедряться в межкристаллическое пространство решетки стали.
Цементация деталей достаточно продолжительный процесс. Скорость внедрения углерода составляет 0,1 мм в час. Не трудно подсчитать, что требуемый для длительной эксплуатации 1 мм можно получить за 10 часов.

Влияние на глубину слоя продолжительности цементации
На графике наглядно показано на сколько зависит продолжительность по времени от глубины наугрероживаемого слоя и температуры нагрева.
Технологически цементация сталей производится в различных средах, которые принято называть карбюризаторами. Среди них выделяют:

Поверхностный слой, получаемый цементацией
Стали под цементацию обычно берутся легированные или же с низким содержанием углерода: 12ХН3А,15, 18Х2Н4ВА, 20, 20Х и подобные им.
Способы цементации
Цементация получила широкое распространение при обработке зубчатых колес и других деталей, работающих при ударных нагрузках. Высокая твердость рабочих поверхностей обеспечивает продолжительный срок работы, а достаточно вязкая середина позволяет компенсировать ударные нагрузки.
Разработаны множество способов науглероживания. Чаще всего используются следующие:
Как происходит процесс цементации с использованием твердой среды
В качестве твердого карбюризатора берется смесь древесного угля (береза, дуб) и соли угольной кислоты с кальцием и другими щелочными металлами. Количество древесного угля может достигать 90%. Для приготовления смеси компоненты дробятся для улучшения выхода углерода. Размер частиц не должен превышать 10 мм. Так же не должно быть микроскопических частив в виде пыли и крошек, поэтому смесь просеивается.

Цементация стали в твердой среде
Для получения готовой смеси пользуются двумя способами. Первый – соль с углем в сухом состоянии тщательно перемешивается. Второй способ – из соли получают раствор. Для этого ее разводят в воде, а после чего этим раствором обильно смачивают древесный уголь. Перед помещением в печь уголь сушат. Его влажность не должна превышать 7%. Получение карбюризатора последним способом более качественно.
Смесь насыпается в ящики. После чего в них помещают детали. Для исключения оттока газа, получаемого во время нагрева, ящики подвергаются герметизации. Плотно закрывающую крышку дополнительно замазывают шамотной глиной.
Ящики подбираются в зависимости от формы детали, их количества и объема засыпанной смеси. Обычно они бывают прямоугольными и круглыми. Материалом для изготовления ящиков может служить сталь как жаростойкая, так и низкоуглеродистая.
Технологический процесс цементации стали можно представить в следующем порядке:
Как происходит процесс цементации в газовой среде
Цементация стали в среде газов производится при массовом выпуске деталей. Глубина цементации не превышает 2-х мм. Используемые газы – естественные или искусственные газы, содержащие углерод. Обычно используется газ, получающийся при распаде нефтепродуктов.

Цементация стали в газовой среде
Его получают в большинстве случаев нагреванием керосина. Больше половины газа подвергают модификации, его крекируют.
Активный углерод при данном способе обработки получается при распаде, и формула имеет следующий вид:
2СО=СО2+С
СН4=2Н2+С
Если пиролизный газ использовался без модифицированного, то в результате обогащенный слой металла будет недостаточным. К тому же пиролизный газ создает обильную сажу.
Печи для данного способа цементации должны быть герметичными. Обычно пользуются стационарными печами, но как вариант методическими.
Цементацию стали и технологический процесс можно представить в следующем порядке:
Подвергаемые цементации изделия помещаются в печь. Температура поднимается порядка 910С — 950С. Производится подача газа в печь. Выдержка в газовой среде определенное время.
Длительность термического воздействия составляет 15 часов при температуре в 920С с получаемым слоем 1,2 мм. Для ускорения производственного процесса температуру поднимают. Уже при 1000С получить такой же науглероженный слой возможно за 8 часов.
В последнее время широкое применение нашел способ проведения процесса в эндотермической среде. Во время активного науглероживания в газовой среде поддерживается значительный потенциал углерода за счет введения природного газа (пропана, бутана или метана). На этот период концентрация газ из нефтепродуктов устанавливается на уровне 1%.
Процесс проведения цементации в жидкой среде
Жидкая среда – это расплавленные соли. В качестве солей используются карбонаты металлов, правда, металлы должны быть щелочными с низкой температурой плавления. Температура проведения цементации при данном методе составляет 850С. Процесс происходит во время погружения деталей в ванну с расплавом и выдерживании их там.

Цементация стали в жидкой среде
Цементация в жидкой среде отличается не большим насыщенным слоем, который не превышает 0,5 мм. Соответственно времени занимает до 3 часов. Среди достоинств следует отметить: обработанные детали имеют незначительную деформацию, а также возможна закалка без промежуточного этапа.
Как происходит процесс цементации в вакууме
Недостаточное давление, создаваемое в печи, значительно сокращает время проведения обработки. Цементацию стали и технологический процесс можно представить в следующем порядке:

Печь для вакуумной цементации
Процесс полностью компьютеризирован. За подачей газа, температурой, давлением следит программа, отвечающая за весь технологический процесс. Среди достоинств следует отметить:
Процесс проведения цементации пастами
При производстве разовых работ рациональнее пользоваться пастами для проведения цементации. В составе пасты находятся: сажа с пылью древесного угля. Толщина слоя наносимой пасты должна быть восьмикратно увеличена для получения требуемого насыщенного слоя.
После нанесения состав просушивается. Для процесса цементации используются индукционные высокочастотные печи. Температура проведения процесса достигает 1050С.
Как происходит процесс цементации в электролитическом растворе
Процесс во многом схож с гальваническим покрытием. В нагретый раствор электролита помещается заготовка. Подведенный ток вызывает получение активного углерода и способствует его проникновению в поверхность стальной заготовки.
Таким способом подвергают обработке детали, имеющие небольшой размер. Параметры для прохождения цементации: напряжение тока – 150-300В, температура 450-1050С.
Свойства металла после обработки
После проведения цементации твердость науглероженного слоя достигает: 58-61 HRC на легированных сталях и 60-64 HRC на низкоуглеродистых сталях. Длительное нахождение стали при высоких значениях температуры, вызывает изменение структуры металла.

Структура стали после цементации
Для исправления крупного зерна металла детали после цементации подвергаются повторному нагреву и закалке с последующим отпуском или нормализацией.
Закалка производится при температуре, не превышающей 900С. В металле происходит измельчение зерна за счет получения перлита и феррита.
Вместо закалки для легированных сталей производят нормализацию. После сквозного прогрева в середине детали образуется мартенсит. Нагрев детали зависит от марки стали, из которой она была изготовлена.

Режимы термической обработки стали после цементации
В качестве заключительной фазы проводят низкотемпературный отпуск, который позволяет устранить поверхностные напряжения и деформации, вызванные высокотемпературной обработкой.
Недостатки цементации
Как было выше сказано основным недостатком после цементации остается изменение структуры металла. В связи с этим требуется дополнительная обработка, что увеличивает время и так длительного процесса цементации.
Для проведения работ требуется обученный и высококвалифицированный персонал. Среди недостатков следует выделить необходимость подготовки карбюризатора.
В заключение стоит отметить, что цементация позволяет использовать, стали с низким содержанием углерода для изготовления ответственных деталей с длительным сроком эксплуатации, что значительно снижает конечную стоимость.
Для защиты поверхностей, не предназначенных под цементацию, пользуются пастами, намеднением или закладывают увеличенные допуски под обработку.
Если вы нашли ошибку, пожалуйста, выделите фрагмент текста и нажмите Ctrl+Enter.
stankiexpert.ru
Цементация металла – виды цементации стали и нюансы процесса
Цементация, осуществляемая в различных средах и исключительно под воздействием высоких температур, является очень распространенным методом химико-термической обработки металла, успешно применяемым уже не один десяток лет.
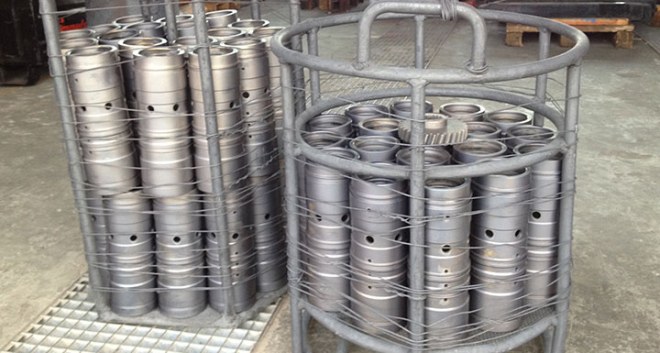
Подготовка деталей для цементации
Сущность процесса цементации
Смысл любых методов химико-термической обработки металлов, к числу которых относится и цементация стали, заключается в том, что изделие нагревают до высокой температуры в специальной среде (жидкой, твердой или газообразной). Такое воздействие приводит к тому, что меняется химический состав металла – поверхность обрабатываемого изделия насыщается углеродом, в итоге становится более твердой и износостойкой. Что важно, сердцевина обработанных деталей остается вязкой.
Добиться желаемого эффекта после такого воздействия на металл можно лишь в том случае, если обработке подвергают низкоуглеродистые стали, в составе которых углерода содержится не более 0,2%. Для того чтобы выполнить цементацию, изделие нагревают до температуры 850–950 градусов Цельсия, а состав среды подбирают таким образом, чтобы она при нагреве выделяла активный углерод.
Если цементацию стали проводить квалифицированно, можно не только изменить химический состав металлического изделия, но также преобразовать его микроструктуру и даже фазовый состав. В результате удается значительно упрочнить поверхностный слой детали, придать ему характеристики, сходные со свойствами закаленной стали. Для того чтобы добиться таких результатов, необходимо правильно подобрать параметры химико-термической обработки металла – температуру нагрева и время выдержки обрабатываемого изделия в специальной среде.
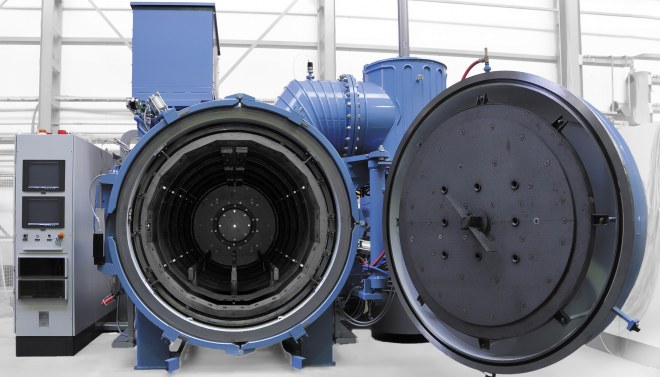
Оборудование для вакуумной цементации стали
Данная технологическая операция является достаточно продолжительной по времени, так как процесс насыщения поверхностного слоя стали углеродом проходит очень медленно (0,1 мм за 60 минут). Учитывая тот факт, что упрочненный поверхностный слой для большинства изделий должен составлять не менее 0,8 мм, можно рассчитать, что на выполнение цементации металла необходимо будет затратить не менее 8 часов. Основными типами сред для выполнения цементации металла (или, как их правильно называют, карбюризаторами) являются:
Наиболее распространенными являются газообразные и твердые карбюризаторы.

Зависимость толщины цементованного слоя от времени и температуры обработки
Проведение цементации стали в твердой среде
Чаще всего для выполнения цементации металла в твердой среде используется смесь, состоящая из углекислого натрия, бария или кальция и березового или дубового древесного угля (70–90%). Перед этим все компоненты такой смеси измельчаются до фракции 3–10 мм и просеиваются, что необходимо для удаления слишком мелких частиц и пыли.
После того, как компоненты смеси для химико-термической обработки металла подготовлены, их можно смешать несколькими способами.
Следует отметить, что второй способ предпочтительнее, так как позволяет получить смесь с более равномерным составом.
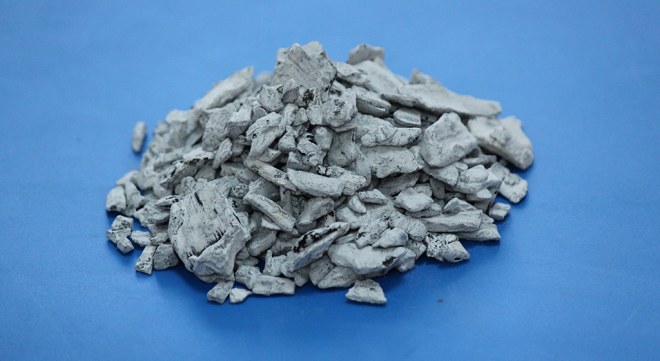
Древесноугольный карбюризатор
Как в производственных, так и в домашних условиях цементация изделий из стали выполняется в ящиках, в которые засыпан карбюризатор. Чтобы улучшить качество поверхностного слоя обрабатываемого металла, а также сократить время, идущее на прогрев ящиков, лучше всего изготавливать их максимально приближенными к размерам и формам деталей.
Оптимальные условия для протекания цементации стали можно создать, исключив утечку газов, образующихся в карбюризаторе в процессе нагрева. Для этого ящики, у которых должны быть плотно закрывающиеся крышки, тщательно обмазывают огнеупорной глиной перед помещением в печь.Естественно, использовать специально изготовленные ящики целесообразно лишь в промышленных условиях. Для цементации металла в домашних условиях применяют ящики стандартных размеров и формы (квадратные, прямоугольные, круглые), подбирая их в зависимости от количества обрабатываемых деталей и внутренних размеров печи.
Оптимальным материалом для таких ящиков является жаростойкая сталь, но может быть использована и тара из малоуглеродистых сплавов. Технологический процесс цементации изделий из металла выглядит следующим образом.
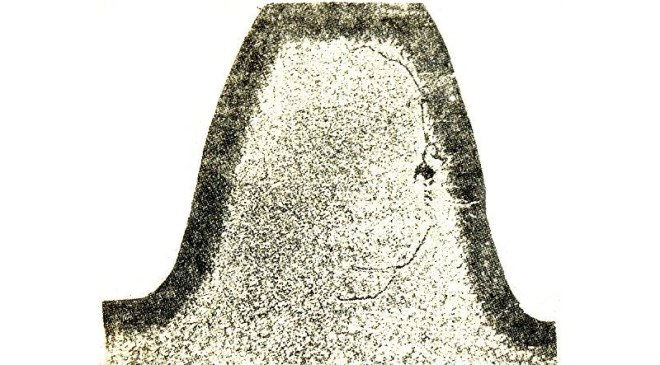
Наглядное изображение изменения структуры после цементации
Высокая температура и специальная среда, в которой находится металл, способствуют тому, что происходит диффузия атомов активного углерода в кристаллическую решетку стали. Следует отметить, что выполнение цементации стали возможно в домашних условиях, но часто не позволяет добиться желаемого эффекта. Объясняется это тем, что для процесса цементации необходима длительная выдержка детали при высокой температуре. Как правило, это трудно обеспечить в домашних условиях.
Цементация деталей в газовой среде
Авторами данной технологии являются С. Ильинский, Н. Минкевич и В. Просвирин, которые под руководством П. Аносова впервые использовали ее на комбинате в г. Златоусте. Суть данной технологии заключается в том, что обрабатываемые детали из металла нагреваются в среде углеродосодержащих газов, которые могут быть искусственного или природного происхождения. Чаще всего используется газ, который образуется при разложении продуктов нефтепереработки. Такой газ получают следующим способом:
Полученная смесь и используется для выполнения химико-термической обработки стали.
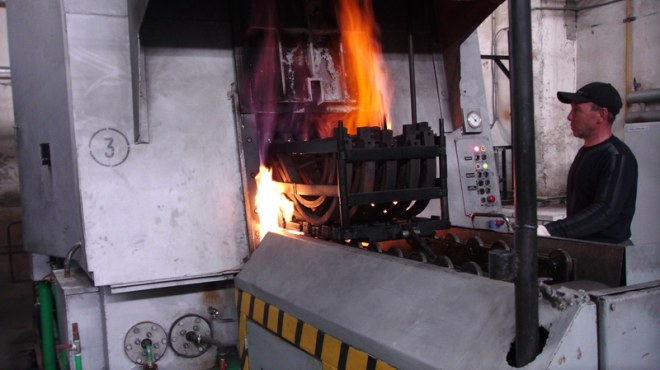
Процесс цементации стали
Если цементацию стали провести с применением только пиролизного газа, без добавления крекированного, то глубина науглероженного слоя будет недостаточной. Кроме того, в таком случае на поверхности обрабатываемой детали осядет большой слой сажи, на удаление которого может уйти много времени и сил.
Печи, которые используются для выполнения газовой цементации металла, должны герметично закрываться. На современных производственных предприятиях применяют два основных типа таких печей: методические и стационарные. Сам процесс цементации в газовой среде выглядит следующим образом. Обрабатываемые детали помещают в печь, температуру в которой доводят до 950 градусов Цельсия. В нагретую печь подают газ и выдерживают в нем детали определенное время.
По сравнению с цементацией стали с использованием твердого карбюризатора, данная технология имеет ряд весомых преимуществ:
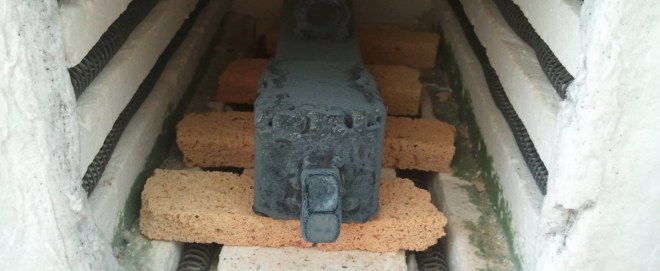
Цементация стали в домашних условиях
В каких еще средах может проводиться цементация стали
Отдельные сорта углеродистых, низкоуглеродистых и легированных сталей, в частности 15, 20, 20ХГНР, 20Х, 20Х2Н4А, 18Х2Н4ВА, 20Г, 12ХН3А и др., могут проходить цементацию в других средах.
Электролитический растворВ такой среде можно науглероживать только детали, отличающиеся небольшими размерами. Основывается данный метод на анодном эффекте, благодаря которому и происходит насыщение поверхности металла углеродом, содержащимся в растворе электролита. Для того чтобы раствор содержал достаточное количество активного углерода, в него добавляют глицерин, ацетон, сахарозу и другие вещества. Перед тем, как поместить деталь из стали в раствор, его нагревают до температуры 450–1050 градусов Цельсия (в зависимости от обрабатываемого металла и размеров детали). Для разогрева раствора используют электрический ток с напряжением 150–300 В.
Кипящий слойЦементацию стали по данной технологии проводят в среде раскаленного газового потока, формируемого при прохождении метана и эндогаза через слой нагретого мелкоизмельченного (0,05–0,2 мм) корунда.
Пастообразные составыДля науглероживания поверхности металла по данной технологии используются специальные пасты, состоящие из желтой соли, древесной пыли и сажи. Перед обработкой деталь обмазывают такой пастой и просушивают, а только затем нагревают до температуры 910–1050 градусов Цельсия при помощи токов высокой частоты.
По какой бы технологии ни была выполнена цементация стали, после ее окончания рекомендуется провести отпуск металла.Оценка статьи:

Поделиться с друзьями:
met-all.org
что это и как осуществить
В основе процесса цементации заложен принцип химической и термической обработки металла. Вся суть процедуры в насыщении поверхности стали необходимым количеством углерода при определенных температурных условиях.
Несколько лет назад эту процедуру в домашних условиях было практически невозможно реализовать. Сегодня это возможно с использованием среды графита или их аналогов. Главное — это желание и некоторые знания.
Общая информация о процессе
В первую очередь необходимо понимать основы термической обработки стали.
К особенностям цементации металла относят следующие факторы:
Осуществить цементацию нержавеющий стали немного сложнее, но в то же время это качественно улучшит характеристики этого вида металла.
В какой среде возможна цементация стали
Процесс закалки проходит в различных условиях среды:
Чаще всего в условиях домашнего цеха проводится цементация стали графитом. Это сильно упрощает процесс, так как не нужно дополнительно еще заботиться о сильной герметичности печи.
В промышленном производстве чаще всего используют газ, так как этот способ сокращает время, затраченное на закалку.
Разновидности металла, который можно обрабатывать
Выделяют три основные группы металла, который используется для закалки:
В целом процесс цементации стали необходим для улучшения износостойкости и прочности деталей.
Чаще всего цементации подвергаются валы, оси, лезвия ножей, детали подшипников и зубчатые колеса.
Как происходит цементация стали в твердой среде на предприятии и в условиях домашнего цеха?
Смесь для твердой цементации готовится из бария, кальция с древесным углем и углекислого натрия. Уголь лучше брать из дуба или березы и разделить его небольшие фракции, не более десяти миллиметров. Чтобы удалить лишнюю пыль, уголь рекомендуют просеять. Соли тоже измельчают до состояния порошка и пропускают через сито.
Существует две методики для приготовления смеси:
При этом, первая методика считается более качественной. Так как она гарантирует, что смесь выйдет равномерной, а результат без пятен и разводов. Готовую смесь еще называют карбюризатором.
Сам процесс твердой цементации проходит в специальных ящиках, где насыпана смесь в нужном количестве. Идеально, если ящики соответствуют размеру и форме изделия, которое обрабатывают. Так как в этом случае снижаются затраты времени на прогрев тары, а качество слоя цементации улучшается. Для избежания утечки газа щели замазывают специальной огнеупорной глиной и накрывают все плотно прилегающей крышкой.
Следует обратить внимание, что изготавливать тару, идеально подходящую, экономически выгодно, если речь идет о конвейерной процедуре. Если же нужно одну или две детали закалить, то лучше выбрать тару универсальной формы — квадратную, круглую или прямоугольную.
Ящики выбирают из малоуглеродистой или жаростойкой стали.
Сам процесс цементации в твердой смеси проходит следующим образом:
Именно при таком температурном режиме происходят диффузные изменения в структуре деталей на уровне атомов.
В домашних условиях достаточно сложно нагреть печь до нужной температуры и выдержать весь температурный режим от начала и до конца. При этом все возможно. Следует помнить, что эффективность домашней цементации намного ниже, чем промышленной.
Цементуемые стали с помощью газа
Впервые цементацию стали газом осуществили на Златоусовском комбинате под бдительным руководством П. Аносова. Этот эффективный способ разработали В. Просвирин, С. Ильинский и Н. Минкевич.
Суть процесса достаточно проста — металл цементируется под влиянием углеродсодержащего газа (природного, искусственного или генераторного) в герметически закрытой печи.
Самый доступный и часто используемый газ — это состав, который получают при разложении нефтепродуктов.
Его изготавливают следующим способом:
Смесь из модифицированного газа и чистого пиролизного газа используют для цементации. Необходимость модификации части газа вызвана тем, что от использования чистого пиролизного газа на стали получается недостаточная цементация, а на некоторых деталях может оседать немного сажи, которую сложно удалять.
Сам процесс цементации стали с помощью газа проводят на специальных печах-конвейерах непрерывного действия. Либо используют уникальные стационарные агрегаты.
Сначала в печь, ее муфель, помещают деталь. Установку закрывают и накаляют печь до 950 градусов. Потом подают заранее подготовленный газ.
Провести эту процедуру в домашних условиях практически нереально.
В то же время она имеет несколько преимуществ перед твердым способом обработки:
Самое важное при цементации стали — это грамотно организованный процесс и качественное оборудование и сырье. Твердый способ вполне можно реализовать в домашних условиях при наличии печи, карбюризатора и металлических форм. А также определенных умений и навыков, связанных с этим процессом закалки стали.
tokar.guru
Цементация
Цементация
Под цементацией принято понимать процесс высокотемпературного насыщения поверхностного слоя стали углеродом. Так как углерод в α-фазе практически нерастворим, то процесс цементации осуществляется в интервале температур 930–950 °С — т. е. выше α → γ-превращения. Структура поверхностного слоя цементованного изделия представляет собой структуру заэвтектоидной стали (перлит и цементит вторичный), поэтому для придания стали окончательных — эксплуатационных — свойств после процесса цементации необходимо выполнить режим термической обработки, состоящий в закалке и низком отпуске; температурно-временные параметры режима термической обработки назначаются в зависимости от химического состава стали, ответственности, назначения и геометрических размеров цементованного изделия. Обычно применяется закалка с температуры цементации непосредственно после завершения процесса химико-термической обработки или после подстуживания до 800–850 °С и повторного нагрева выше точки АС3 центральной (нецементованной) части изделия. После закалки следует отпуск при температурах 160–180 °С.
Цементация как процесс химико-термической обработки, в основном, применяется для низкоуглеродистых сталей типа Ст2, СтЗ, 08, 10, 15, 20, 15Х, 20Х, 20ХНМ, 18ХГТ, 25ХГТ, 25ХГМ, 15ХГНТА, 12ХНЗА, 12Х2Н4А, 18Х2Н4ВА и др., однако в ряде случаев может быть использована при обработке шарикоподшипников — стали ШХ15, 7Х3 и коррозионностойких сталей типа 10Х13, 20Х13 и т. д. Стали, рекомендуемые для цементации, должны обладать хорошей прокаливаемостью и закаливаемостью цементованного слоя, которые должны обеспечить требуемый уровень прочности, износостойкости и твердости. Прокаливаемость сердцевины должна регулироваться в весьма узком диапазоне твердостей, который составляет 30–43 HRCЭ. Учитывая длительность процесса цементации и высокую температуру процесса, рекомендуется при этом виде химико-термической обработки использовать наследственно мелкозернистые стали, размер зерна которых не должен превышать 6–8 баллов. В противном случае в ходе цементации отмечается значительный рост зерна сердцевины изделия, что приводит к снижению его эксплуатационных свойств.
Цементация производится в углероднасыщенных твердых, жидких или газообразных средах, называемых карбюризаторами, основные составы которых приведены в табл. 9.3, а в табл. 9.4 и 9.5 даны рекомендации по режимам термической обработки цементованных изделий.
При твердофазной цементации процесс ведут следующим образом. Цементуемые детали упаковываются в цементационные ящики таким образом, чтобы их объем, в зависимости от сложности конструкции детали, занимал от 15 до 30 % объема цементационного ящика. Ящики загружают в печь, нагретую до температур от 600–700 °С и нагревают до температуры цементации — 930–950 °С. По окончании процесса цементации ящики вынимаются из печи — охлаждение деталей ведется внутри цементационных ящиков на воздухе. К числу недостатков цементации в твердых карбюризаторах относятся: невозможность регулирования степени насыщения и невозможность проведения закалки непосредственно после цементации, дополнительный непродуктивный расход энергии на прогрев цементационных ящиков и т. п. Однако простота метода, возможность проводить процесс на стандартном печном оборудовании без установки дополнительных устройств делают этот метод весьма распространенным в условиях мелкосерийного производства в ремонтных цехах и на участках крупных предприятий. Цементация в жидкофазном карбюризаторе применяется для мелких деталей. К недостаткам этого процесса относятся неравномерность глубины цементованного слоя и необходимость частых регенераций углероднасыщенного расплава. В случае серийного и крупносерийного производства цементованных изделий наибольшее распространение получила цементация в газообразных карбюризаторах. Этот метод обеспечивает наибольшую равномерность по толщине и свойствам цементованного слоя, снижает время, затрачиваемое на процесс химико-термической обработки, а в ряде случаев позволяет производить закалку изделий непосредственно после цементации. В последнее время получил распространение процесс вакуумной цементации. Печи для вакуумной цементации состоят из нагревательной камеры, снабженной вентилятором для обеспечения интенсивной циркуляции воздуха, закалочного бака и транспортных устройств. Подготовленные для вакуумной цементации детали помещают в нагревательную печь, вакуумируют и нагревают до 1000–1100 °С, затем в печь подается газообразный карбюризатор — очищенный природный газ, пропан или бутан. Этот метод позволяет ускорить процесс цементации, повысить качество получаемого слоя.
studfiles.net
технология процесса, выбор рабочей среды
Во время изготовления металлических конструкций приходится прибегать к различным методам химико-термической обработки. Среди них достаточно распространенным является цементация стали. Этот способ примечателен тем, что может применяться в разных средах при относительно высоких температурах рабочей среды.
Процесс цементации металла — общие сведения
Химико-термическая обработка или цементация, это процедура, при которой на изделия воздействуют высокой температурой при помещении их в жидкую, газовую или твёрдую среду, что делается для придания им измененного химического состава. Причем этот эффект обеспечивает насыщение углеродом поверхностного слоя обрабатываемых объектов. Благодаря такой обработке можно обеспечить изделиям высокие характеристики устойчивости к износу и повышенную твердость. Примечательно то, что сердцевина этих деталей сохраняет свою начальную вязкость.
Эффективность метода цементации наблюдается при условии, что работа проводится с низкоуглеродистыми сталями, в составе которых доля углерода не превышает значения 0,2%. Термическая обработка обеспечивает насыщение поверхностного слоя деталей, причем для этого их помещают в специально подобранную среду, которая может легко выделить активный углерод, где поддерживается температура в диапазоне от 850 до 950 градусов Цельсия.
Создание подобных условий обработки позволяет изменять помимо химического состава обрабатываемых элемента и микроструктуру вместе с фазовым составом. Положительный эффект от такой обработки заключается в повышении прочности, в результате по характеристикам такая деталь не отличается от изделий, прошедших операцию закалки. Для достижения наилучших результатов особое внимание следует уделить грамотному расчету времени, в течение которого деталь должна выдерживаться в создаваемой среде, а также подбору температуры цементации.
Особенностью цементации стали является то, что на эту процедуру уходит достаточно много времени. Чаще всего процесс насыщения поверхности и придания ей специальных свойств проходит со скоростью около 0,1 мм за один полный час выдержки. Многие элементы нуждаются в создании упрочненного слоя толщиной более 0,8 мм, что позволяет говорить о том, что на эту обработку придется потратить как минимум 8 часов. На текущий момент технология цементации металла предусматривает использование нескольких сред:
Обычно при выборе среды для обработки металла используют газовые и твёрдые карбюризаторы.
Цементация металла в твердой среде
В качестве материала для твердого карбюризатора используется смесь углекислого натрия, бария или кальция с древесным углем, который необходимо применять в измельченном виде, представленном фракциями размером порядка 3-10 мм. Причем обязательно эту основу необходимо просеять, чтобы убрать пыль. Обязательной процедурой, которой подвергаются соли, является измельчение с целью придания им порошкообразного состояния, после чего эту массу просеивают через сито.
Для создания смеси могут применяться два основных способа:
Из этих методик наиболее предпочтительной является вторая ввиду ее более высокого качества. Это проявляется в том, что с ее помощью можно создать более равномерную смесь для насыщения поверхности углеродом. В составе готового карбюризатора на долю древесного угля приходится порядка 70-90%, а остальное занимает углекислый кальций и углекислый барий.
Для проведения твердой цементации применяют ящики, куда помещают карбюризатор. Лучше всего использовать ящик, соответствующий форме обрабатываемых изделий. Дело в том, что это поможет улучшить качество цементированного слоя, при этом удастся сократить до минимума время, которое требуется для прогрева тары. Важно позаботиться об отсутствии утечки газов: эту проблему решают путем замазывания ящиков глиной, а затем накрывают сверху герметичными крышками.
Важным моментом является и то, что прибегать к рассматриваемому варианту создания для непосредственного использования тары специальной формы имеет смысл в тех случаях, когда необходимо обработать посредством химико-термического метода большое количество деталей. Наибольшее распространение получили ящики, имеющие стандартную форму, которые различаются геометрическими размерами. Это дает возможность подбирать из них наиболее оптимальный вариант, который в наибольшей степени учитывает количество обрабатываемых изделий и размеры печи.
Обычно ящики изготавливают на основе малоуглеродистой или жаростойкой стали. Причем при выполнении обработки деталей при помощи твердого карбюризатора придерживаются следующей схемы:
Создание указанного температурного режима обеспечивает условия для проникновения диффузии в кристаллическую структуру металла активного углерода. Теоретически этот метод может применяться и для химико-термической обработки зданий, причем отдельные мастера способны справиться с этой задачей и своими силами. Однако в плане эффективности подобная обработка, проводимая в домашних условиях, отличается довольно невысокой эффективностью, причиной чего является долгая обработка и необходимость в создании высокого температурного режима.
Газовая цементация
Авторами теоретических материалов, в которых раскрывается суть подобной цементации, являются С. Ильинский, Н. Минкевич и В. Просвирин. При этом первый опыт практического воплощения имел место на Златоустовском комбинате, где всеми работами руководил П. Аносов.
Особенностью этого метода является использование среды углеродсодержащих газов, в качестве основного рабочего оборудования выступают герметичные нагревательные печи. Среди известных искусственных газов чаще всего используют состав, являющийся результатом разложения нефтепродуктов. Технология его изготовления предусматривает проведение нескольких этапов:
Необходимо взять стальную емкость, нагреть ее и заполнить керосином, далее же приступают к выполнению процесса пиролиза, подразумевающего разложение керосина на смеси газов;
Определенную часть пиролизного газа (примерно 60%) подвергают крекированию, суть которого сводится к изменению состава.
Смесь крекированного газа и чисто пиролизного выступает основой, при помощи которой выполняется химико-термическая обработка, обеспечивающая обогащение углеродом. Заниматься выработкой крекированного газа приходится по той причине, что в случае применения одного пиролизного состава глубина цементирования стали оказывается небольшой, при этом обрабатываемые детали покрываются большим количеством сажи, которую сложно убрать.
В качестве оборудования для выполнения газовой цементации используются конвейерные печи непрерывного действия или же стационарные агрегаты. Детали, которым необходимо придать более прочные характеристики, кладут в муфель печи, а после закрытия доводят температуру внутри до отметки 950 градусов. Далее начинают подавать туда подготовленный газ. Из плюсов этой процедуры, которая отличается на фоне обработки изделий при помощи твердого карбюризатора, необходимо выделить следующие:
Цементация в менее популярных карбюризаторах
В ситуации, когда приходится подвергать химико-термической обработке стали 20, 15, а также легированные стали с низким содержанием углерода, допускается использовать следующие карбюризаторы.
Раствор электролита
Суть подобного метода сводится к использованию анодного эффекта, за счет которого можно обогатить при помощи многокомпонентных электролитов углерода изделия, характеризующиеся небольшими размерами. Обработка этих деталей требует создания температурного режима в диапазоне 450-1050 градусов и напряжения 150-300 В. Обязательной операцией является введение в электролит сахарозы, ацетона, глицерина, а также отдельных веществ, имеющих в своем составе углерод.
Кипящий слой
По своей структуре он имеет вид восходящего потока метана и эндогаза, который «пронзает» мелкие частицы корунда, распределяемые на печной газораспределительной решетке.
Пасты
Применение подобного карбюризатора для обработки изделий подразумевает создание на поверхности стальной детали, нуждающейся в обогащении углеродом, слоя пасты, ее последующее просушивание и нагрев током высокой или промышленной частоты. Стоит заметить, что одной цементацией обработку детали не следует заканчивать. Рекомендуемой здесь операцией является термообработка стали в виде отпуска. Также положительный эффект достигается и посредством шлифования металла.
Заключение
Довольно часто определенным конструкциям требуется придать повышенные характеристики прочности, чтобы они смогли успешно выполнять задачу, которая перед ними ставится. Решается же это путем использования различных методов обработки, среди которых достаточно эффективным является цементация металла. При этом для получения необходимого результата нужно учитывать важные особенности этого процесса.
Помимо грамотного подбора рабочей среды, для цементации металла важно в точности следовать технологии проведения подобной обработки. Ведь малейшая ошибка способна негативно повлиять на химический состав изделия, что в дальнейшем может уменьшить срок службы конструкции, в составе которой оно будет применяться. По этой причине важно уделять внимание каждому моменту, не допуская отклонений от действующих норм и правил относительно проведения химико-термической обработки металлических деталей.
Оцените статью: Поделитесь с друзьями!stanok.guru
Сталь цементация - Справочник химика 21
Другой метод обработки поверхности стали—цементация— основан на внедрении атомов углерода в поверхностный слой металла. Цементацию обычно проводят, нагревая сталь до 900—950°С в атмосфере окиси углерода и углеводородов (например, метана), которые при этом частично распадаются с образованием свобод)юго углерода [c.64]В гальваностегии медные покрытия применяются для защиты стальных изделий от цементации, для повышения электропроводности стали (биметаллические проводники), а также в качестве промежуточного слоя на изделиях из стали, цинка и цинковых и алюминиевых сплавов перед нанесением никелевого, хромового, серебряного и других видов покрытий для лучшего сцепления или повышения защитной способности этих покрытий. Для защиты от коррозии стали и цинковых сплавов в атмосферных условиях медные покрытия небольшой толщины (10—20 мкм) непригодны, так как в порах покрытия разрушение основного металла будет ускоряться за счет образования и действия гальванических элементов. Кроме того, медь легко окисляется на воздухе, особенно при нагревании. [c.396]
Палец изготовляют из сталей 45 и 40Х с последующей обработкой токами высокой частоты для получения поверхностной твердости НR 50— 58 или из сталей 20, 15Х и 15ХМА с двухсторонней цементацией на глубину слоя в пределах 0,5—1,5 мм (для готового изделия) и закалкой на твердость HR 56—62. С целью повышения износостойкости класс чистоты внешней поверхности пальца — не ниже V9. Полировка поверхности отверстия пальца для удаления рисок от шлифования увеличивает его усталостную прочность в два раза. Посадка пальца в поршне — скользящая по 2-му классу. Самые лучшие результаты дает селективная сборка с соблюдением зазора в пределах 3—10 мкм, что потребовало бы при обычной сборке обработки по 1-му классу точности. [c.395]Цементация является одним нз наиболее ранних процессов обработки металлов. Ещё в древние времена была известна способность углерода проникать вовнутрь мягкого железа. В то время цементация углеродом применялась главным образом в металлургических целях. Этим способом пользовались для превращения железа в сталь путём томления при тигельном процессе. В более позднее время в связи с появлением совершенных и более дешёвых способов получения стали цементация как металлургический процесс потеряла своё значение. [c.23]
Упрочнения поверхности стали можно добиться специальными методами ее термической обработкой — поверхностной закалкой с нагревом токами высокой частоты и химико-термической обработкой цементацией и азотированием. Цементация и азотирование — процессы диффузионного насыщения поверхностного слоя детали углеродом и азотом, соответственно. Данной обработке подвергают такие детали машин и аппаратов, которые должны иметь износостойкую рабочую поверхность и вязкую сердцевину зубчатые колеса, коленвалы, кулачки,червяки и др. [c.631]
Для повышения поверхностной твердости и, следовательно, увеличения стойкости против износа детали, изготовленные из стали марок 10, 15, 20 и 25, иногда подвергаются цементации или цианированию. Вместо стали марок 15, 20 и 25 для изготовления ответственных деталей нефтегазопромыслового и заводского оборудования может быть рекомендована сталь с повышенным содержанием марганца марок 15Г и 20Г, Эта сталь по сравнению со сталями с нормальным содержанием марганца обладает большей прочностью при сохранении высоких пластических свойств. При цементации деталей из стали с повышенным содержанием марганца образуется более однородный цементованный слой, и после закалки такие детали имеют высокую и равномерную поверхностную твердость. Сталь с повышенным содержанием марганца марок 40Г и 45Г обладает после закалки и высокого отпуска повышенной прочностью, хорошей вязкостью и сопротивляемостью износу. Для изготовления пружин, пружинных шайб и колец целесообразно применять стали с повышенным содержанием марганца, например, сталь марки 65Г. [c.26]
Отжиг нержавеющей стали, трансформаторного железа, малоуглеродистой стали Цементация.............. [c.85]
Механическая точение, фрезерование, сверление, растачивание для качественных сталей — цементация, закалка до твердости ННС 34—38 [c.162]
Лестерни шестеренных насосов изготавливаются из легированной стали, зубья шестерен подвергаются цементации на глубину 0,9—1,5 мм и закалке до твердости HR 58—62. При работе шестерни изнашиваются по наружному диаметру зубьев и линии зацепления зубьев, по торцовым поверхностям, по цапфам. Ведущая шестерня испытывает большие нагрузки, чем ведомая, поэтому и износ ее больше, чем ведомой шестерни. [c.245]
Поршневые пальцы изготовляют из сталей 45 и 40Х с последующей закалкой током высокой частоты или из сталей 20, 15Х и 15ХМА с цементацией и закалкой. Класс чистоты внешней поверхности пальца не ниже девятого. Пальцы закрепляются в бабышках установочными винтами. Широко распространены также плавающие пальцы, не закрепленные в бобышках поршня н проворачивающиеся в них. Плавающий палец фиксируется пружинящими кольцами, устанавливаемыми по его концам в проточках внутри бобышек. [c.200]
Природный газ применяется и в металлургии. Здесь он используется не только как топливо, но и в процессе термической обработки металла — так называемой цементации стали. Цементацией стали называется процесс науглероживания поверхности стальных изделий при высокой температуре в печах особого устройства. При этих условиях метан разлагается на простые вещества [c.266]
Твердость азотированной стали выше 1000 по Бринелю, тогда как твердость цементированной (науглероженной) стали не выше 800. Антикоррозийные свойства азотированной стали также значительно выше. Так как процесс азотирования протекает при более низкой температуре, чем цементация, то деформация тонких предметов почти исключается. Глубину проникновения нитрида железа легко варьировать, изменяя температуру и время процесса. Кроме того, в процессе азотирования происходит заметное увеличение объема стали и поэтому стертые калибры, лекала и др. инструменты можно довести до прежнего размера. Известен нитрид железа состава Ре4Ы, устойчивый до 680° С. [c.361]
Изменением состава легирующих элементов легко можно получить стали с требуемыми прочностными или пластическими свойствами, химической стойкостью, жаростойкостью и т. д. Сталь легко подвергается обработке любым технологическим способом отливкой, ковкой, штамповкой, прокаткой, резанием, давлением и др. Термическая обработка позволяет изменять свойства стали в широком диапазоне как по поверхности стали, так и по всему сечению химико-термическая обработка стали — цементация, азотирование, металлизация и другие — позволяет еще больше расширить эти возможности. Малоуглеродистые стали хорошо свариваются. Применением соответствующих легирующих добавок, специальных электродов и последующей термической обработкой можно создавать прочные сварные соединения также из легированных сталей. [c.110]
Цианистый натрий применяется главным образом в горной промышленности, в гальваностегии, для цементации сталей, для окуривания и для производства красок и других химикалий. Его значение в горной промышленности упало по сравнению с прошлыми годами, ибо он заменяется в этой области более дешевым цианистым кальцием. В этом отношении повторилась старая история цианистый калий, который сначала исключительно применялся в металлургической промышленности, уступил место более дешевому цианистому натрию, а этот последний, "в свою очередь, был заменен еще более дешевым цианистым кальцием. [c.35]
Цементация этой стали проводится при температуре 930—960° С. После цементации рекомендуется проводить двойную закалку с низким отпуском. Первая закалка обычно производится с цементационного нагрева в масле, вторая закалка с температуры 750—790° С, отпуск — при температуре 180—200° С.. [c.56]
Следовательно, метан является поставщиком СО, и его обычно добавляют при газовой цементации металла для предотвращения обезуглероживания. Ряд работ свидетельствует о том, что науглероживание и последующее окисление сталей наблюдается также в среде чистого СО [39—41]. [c.165]
Крейцкопф выполнен как одно целое с башмаками из чугуна, модифицированного ферробором. Поверхность башмаков закаливают токами высокой частоты для получения нужной твердости. Крейцкопф соединен со штоком двумя закладными гайками, что позволяет регулировать зазор между торцами поршня и цилиндра в верхней и нижней мертвых точках. Палец крейцкопфа из хромоникелевой стали подвергают цементации и закалке. При сборке палец запрессовывают в тело крейцкопфа и стопорят пружинным кольцом. [c.368]
При цементации деталей из стали с повышенным содержанием марганца образуется более однородный цементованный слой, а после закалки такие детали имеют высокую и равномерную поверхностную твердость. Сталь с повышенным содержанием марганца цементуют при температуре 900—920° С. После цементации детали следует подвергнуть промежуточной термической обработке— закалке в масле или нормализации с температуры 820—840° С — для улучшения цементованной сердцевины. Окончательная закалка производится с температуры 780—800° С. Крупные изделия при закалке охлаждаются в воде или через воду и масло, а мелкие — в масле. Отпуск производится при температуре 180—200° С. [c.36]
Цементация этой стали производится прн температуре 920—950° С с последующей закалкой с температуры 800—820° С в масле и отпуском прп 180— 200° С. Время выдержки при температуре цементацип ориентировочно может быть определено из расчета 1 ч на 0,1 мм толщины цементованного слоя. [c.49]
При всех различиях, существующих в составе и структуре закаленной, облагороженной и высокопрочной стали, ее поведение при электролитическом покрытии одинаково, например в отношении водородной хрупкости (см. стр. 160). В этой работе не говорится о процессах, возникающих при закалке (обычная закалка, по верхностная закалка сильно углеродистых сталей, цементация или азотирование слабоуглеродистых сталей) и при-улучшении стали термообработкой, а также о возникающих нри этом структурных изменениях. Однако в рамках гальванотехники имеют значения те изменения механических свойств, которые эти стали получают в процессе покрытия или при сопутствующих предварительной или последующей обработках. Почти всегда при этом ухудшаются показатели прочности (предел прочности на растяжение, прочность на знакопеременный изгиб и т. д.) эти ухудшения следует отнести главным образом за счет водорода, проникшего в металл в результате диффузии. Естественно, что такое поглощение водорода (рис. 137) имеет место-не только у названных выше сталей, но и у всех сталей вообще. У закаленных, облагороженных и сталей высокой прочности поглощение водорода оказывается особенно неприятным, так как эти стали подвергаются действию повышенных механических напряжений. [c.340]
Червячные колеса выполняют из бронзы и ковкого чугуна, звездочки приводных роликовых и втулочных цепей из сталей 40,45,40Х с закалкой ТВЧ зубчатого венца до твердости 40 - 50 НКС, а также из стали 15 и 20 с цементацией и закалкой до твердости ИКС 52 60 или серого чугуна СЧ18-36 с последующей термообработкой цоНВ 363 - 429. [c.318]
Для подтверждения этой гипотезы были получены образцы из углеродистых качественных сталей марок 10, 15, 20 с размерами 120х50х50мм, предназначенные для проведения газовой цементации. Процесс цементации осуществлялся в карбюризаторе, представляющем собой многокомпонентную систему, состоящую из К -СОз-СО-Нг-НгО-СНд. Образцы выдерживались разное время для получения цементованного слоя толщиной 1, 1,5, 2 мм при температуре 950 С и медаенно охлаждались. Микрострук-турный анализ показал наличие трех зон в структуре цементованного слоя [c.25]
ТОПОХИМИЧЕСКИЕ РЕАКЦИИ (греч. topos — место) — реакции, происходящие в твердой фазе, например, дегидратация кристаллогидратов, окисление металлов и др. К наиболее важным Т. р. относятся процессы обжига, восстановления, хлорирования руд тяжелых и цветных металлов, изготовление катализаторов, получение ферритов, цементация стали, производство керамики, фарфора, огнеупоров, разложение взрывчатых веществ и многие др. [c.252]
ЦЕМЕНТАЦИЯ СТАЛИ - насыщение поЕерхности стальных изделий угле- [c.282]
Сталь 20ХНЗА применяется после цементации для изготовления высоконагруженных деталей, работающих при больших скоростях и ударных нагрузках шестерен, кулачковых муфт, силовых иишлек, валиков, втулок, зубчатых колес тяжелонагружеиных и быстроходных зубчатых передач буровых установок, собачек роторных клиньев, сухарей трубных ключей и т. д. [c.56]
Химические покрытия. Поверхность защищаемого металла подвергают химической обработке с целью получения на нем пленки его химического соединения, стойкой против коррозии. Сюда относятся оксидирование — получение тонких прочных пленок оксидов (алюминия АЬОз, цинка 2пО и др.) фосфатирова-ние — образование на поверхности металла защитной пленки фосфатов, например Рез(Р04)г, Мпз(Р04) азотирование — насыщение поверхности металла (стали) азотом (путем длительного нагревания в атмосфере аммиака при 500—600° С) термическое (воронение стали) — поверхностное взаимодействие металла с органическими веществами при высокой температуре (при этом получается слой Рез04) создание на поверхности металла его соединения с углеродом (цементация) и др. [c.195]
Не ниже 906° С при выплавке чугуна образуется феррит, который непосредственно соединяется с углеродом, образуя карбид железа или цементит формулы РсзС. Карбид железа образуется также на поверхности стальных изделий при нагревании их до соответствующей температуры в присутствии угольного порошка, соды и других углеродсодержащих продуктов. Процесс этот называется цементацией. Цементированные изделия так же, как и азотированные, приобретают поверхностную твердость (например, оси, рельсы и др.). В последнее время цементацию стали производить, нагревая стальные изделия в присутствии светильного газа с обязательным удалением освобождающегося водорода (аналогично процессу азотирования). [c.361]
Другим примером может служить реакция цементации с помощью метана, используемая для увеличения твердости стали путем цементации — обогащения ее поверхности углеродом СН4г=С+2Н2г. [c.37]
Наиболее эффективное средство повышения сопротивления стали усталости и коррозионной усталости среди расмотренных способов это создание белых> слоев механоультразвуковой обработкой. Она эффективна даже без цементации — сложного и дорогостоящего технологического процесса. Положительное влияние белого слоя, образующегося на поверхности стальной детали при больших скоростях резания (80—200 м/мин) или при импульсной обработке расширяет возможность применения углеродистых сталей для изготовления газонефтепромыслового оборудования. [c.18]
Для повышения поверхностной твердости и, следовательно, увеличения стойкости против износа детали, изготовленные из стали марок 15, 20 и 25, в ряде случаев подвергаются цементации или цианированию (например, пальцы крейцкопфов, щестерии, оси). [c.35]
Сталь марки 12ХН2 является цементуемой. Цементация производится при 900—920° С с последующей закалкой в масле с температуры 780—800° С и отпуском при 170—1180° С. Эта сталь применяется для изготовления метчиков и колоколов для ловильных работ в бурении, илашек труболовок, поршневых [c.51]
Цементация стали 18ХГТ производится прп 940—950° С с последующей закалкой с температуры 780—800° С в масле и отпуском при 180—200° С. [c.53]
Цементация шарошек и лап долот производится, как правило, в древесноугольном карбюризаторе. Шарошки и лапы из стали 12ХН2 цементуют ири температуре 930—960° С. [c.94]
Детали опытных долот, изготовленные нз стали марки ЗОХГС, подвергались цемептации по технологии, принятой для серийных долот. Закалка после цементации производилась с температуры 880° С в масле, отпуск — ири температуре 200—220° С. [c.100]
Известно, что главной причиной разрушения цементуемых деталей являются дефекты цементации резкие колебания концентрации углерода в Еоверх-ностном слое между отдельными партиями деталей и невозможность точного регулирования содержания углерода в поверхностном слое, особенно при цементации U твердом карбюризаторе, рост зерна в процессе цементации, возможное насыщение стали при цементации кислородом и т. д. [c.102]
chem21.info