- Труба стальная бесшовная горячекатаная гост 8732 78
- Прямошовные стальные трубы
- Теплопроводность стали и алюминия
- Пищевая нержавеющая сталь гост
- Сталь аустенитная это
- Обыкновенного качества стали
- Стальные сварные трубы
- Низколегированные стали это
- Из чего состоит нержавеющая сталь
- Сварные стальные трубы
- Трубы сварные стальные
Аустенитные высоколегированные стали. Марки аустенитная сталь
Аустенитная сталь - марка - Большая Энциклопедия Нефти и Газа, статья, страница 1
Аустенитная сталь - марка
Cтраница 1
Высоколегированная хромоникелениобие-вая аустенитная сталь марки Х18Н11Б ( ЭИ-724) имеет структуру, однотипную со сталью марки 1Х18Н12Т, но с заменой титана ниобием и рекомендуется для изготовления паропроводных и пароперегревательных труб, длительно работающих при температурах до 610 С. [1]
Высоколегированные хромоникелевольфра-мониобиевые аустенитные стали марок Х13Н18В2Б ( ЭИ-695) и Х13Н18В2БР ( ЭИ-695Р) с бором предназначены для паропроводных и пароперегревательных труб. Обе марки стали содержат в себе стабилизирующий элемент ниобий, придающий им нечувствительность к межкристаллитной коррозии. [2]
Высоколегированная хромоникелевольфра-мониобиевая аустенитная сталь марки Х13Н18В2БР ( ЭИ-726) с бором предназначена для изготовления пароперегревательных труб, работающих при температуре стенки 650 - - 700 С. [3]
Исследовалась хромо-никелевая аустенитная сталь марки 1Х18Н9Т, для которой питтинг представляет большой практический интерес. [4]
Для аустенитной стали марки ОХ18Н10 и др. различают два вида закалки: стабилизацию, при которой нагрев происходит до температуры 850 С, и аустенизацию, при которой сталь нагревают до 1000 - 1150 С. Закалка способствует растворению карбидов хрома частично или полностью в стали. [6]
Представляют интерес новые коррозионностойкие безникелевые аустенитные стали марок ОЗХ13АП9 ( ЧС-36) и 07Х13АГ20 ( ЧС-46), предназначенные для работы при температурах от 400 до - 210 С. Они устойчивы к действию фосфорной ( 10 % - ной), азотной ( до 50 %) и уксусной ( 10 % - ной) кислот; хлористого натрия ( 10 % - ного) при температуре 50 С, а также к действию различных аминопро-дуктов. Эти стали рекомендуют для изготовления оборудования, работающего в районах Крайнего Севера и вечной мерзлоты. [8]
Трубы из аустенитной стали марки 1Х14Н14В2М испытываются в выборочном порядке на ползучесть, длительную прочность и склонность к тепловой хрупкости. [10]
Химический состав аустенитных сталей марок XSCrNiMoVNb 16 / 13 и K8CrNiNbl6 / 13, использованных для котлов электростанции Хюльс, приведен в табл. 4 - 8 ( гл. [11]
В качестве материала диска обычно используется аустенитная сталь марки ЭИ572 в виде поковок или отливок. В последнем случае диск выполняется заодно с лопатками. [12]
На открытых распределительных устройствах сварку воздухопроводов из аустенитных сталей марки Х18Н10Т ( ГОСТ 9941 - 72) диаметром 14 - 89 мм с толщиной стенки 2 - 6 мм, предназначенных для подачи воздуха от компрессорных к воздушным выключателям и работающих под давлением до 23 МПа, выполняют ручной и полуавтоматической аргонодуговой сваркой неплавящимся электродом на постоянном токе. Для сварки используют источники питания постоянного тока с крутопадающей характеристикой ПСО-300, ПСО-500, ВД-304, ВД-301, ВДУ-504, а также выпрямители серии ВС с балластными реостатами. Аргонодуговые горелки используют с воздушными или водяным охлаждением типов ЭЗР-3-66, АГМ-2, ЭЗР-5-2 и ЭЗР-4-68. Концы труб и арматура, подлежащие сварке, подбираются по внутреннему диаметру с таким расчетом, чтобы разность внутренних диаметров не превышала 0 8 мм. Подготовка кромок под сварку должна производиться механизированным способом; при этом при сварке труб с толщиной стенки до 3 мм кромки подготовляются только со стороны внутреннего диаметра, а при толщине более 3 мм - с обеих сторон. Сборку стыков необходимо производить в кондукторах. Сварка выполняется на постоянном токе прямой полярности при температуре окружающего воздуха не ниже - 15 С. [13]
Сталь ЭШ82 - ВИ разработана в качестве заменителя хромонике-левых аустенитных сталей марок 08Х18Н10Т, 12Х18Н20Т и др. для изготовления теплообменного оборудования химических производств, энергетического оборудования тепловых и атомньгх электростанций. Сталь не склонна к хлоридному коррозионному растрескиванию, пит-тинговой коррозии. [14]
Страницы: 1 2 3
www.ngpedia.ru
Аустенитные высоколегированные стали
Аустенитные высоколегированные стали
К этому классу относятся стали, имеющие повышенное содержание легирующих элементов, которые при всех температурах обеспечивают аустенитную структуру металла. Наиболее распространены стали системы легирования Cr-Ni. Стали этой системы являются аустенитными при содержании хрома и никеля не менее 16 и 7% соответственно. Такие стали немагнитны, обладают высокой хладностойкостью, жаропрочностью, жаростойкостью и коррозионной стойкостью в различных коррозионных средах. Как правило, они содержат минимальное количество углерода, обладая при этом достаточной прочностью и высокой пластичностью. При закалке эти стали приобретают повышенную пластичность.
Структурные состояния сталей этого класса могут быть весьма разнообразными и зависят от содержания в стали элементов ферритизаторов и аустенизаторов (рис. 1). Приведенная на этом рисунке структурная диаграмма Шеффлера может быть использована и для подбора сварочных материалов в связке химсостав-структура. При этом эквивалентное содержание хрома и никеля в металле шва можно определять по формулам
Niэкв =Ni%+30С%+30N%+0,5Mn%;
Crэкв=Cr%+2Mo%+1,5Si%+5Ti%+2Nb%+2Al%+1,5W%+V%
Рис. 1. Структурная диаграмма Шеффлера
Подсчет содержания элементов в металле шва по этим формулам производят с учетом долей основного и дополнительного металла.
Особенностей свариваемости сталей этого класса, которые нужно учитывать при разработке технологии, несколько.
1. Опасность возникновения в металле шва и 3ТВ так называемой межкристаллитной коррозии (МКК). Механизм этого явления, возникающего в определенной температурно-временной области, заключается в обеднении хромом пограничных областей зерен металла за счет его диффузии к границам зерен и образованию там карбидов хрома.
Причиной этому может служить неблагоприятный режим сварки (рис. 2) (малые скорости охлаждения), когда есть достаточно времени для диффузии атомов хрома из приграничных районов зерна к его границам и образованию там карбидов, что приводит к появлению зон металла, обедненных хромом. Они-то и подвергаются коррозионному разрушению при работе изделия в агрессивных средах.
Рис. 2. Схематическое изображение области появления межкристаллитной коррозии аустенитной стали при ее нагреве:
1 - скорость охлаждения, способствующая выпадению карбидов; 2 - скорость охлаждения, не приводящая к выпадению карбидов; 3 - начало появления склонности металла к МКК; 4 - окончание процесса образования карбидов; 5 - первоначальная склонность к МКК (tим)
Для предупреждения МКК принимают ряд мер. Стараются снизить содержание углерода в стали до 0,02...0,03% (это уменьшает количество карбидов, так как такое содержание углерода полностью растворимо в твердом растворе аустенита). Часто сталь (и сварочные материалы) легируют такими элементами как титан, ниобий, ванадий, тантал. Эти элементы являются более энергичными карбидооразователями, чем хром, и раньше, чем хром, образуют карбиды, подавляя, таким образом, появление карбидов хрома.
Если не удается получить высокую скорость охлаждения сварного соединения, можно применить стабилизирующий отжиг при 850...900°С либо провести аустенизацию - нагрев до 1050...1100°С с последующим быстрым охлаждением. Возможно также создание в шве аустенитно-ферритной структуры с содержанием феррита до 20...25% путем дополнительного легирования хромом, кремнием, молибденом, алюминием и пр.
Реализация некоторых из этих рекомендаций технологическим путем заключается в разработке таких технологий, которые позволяют получать величину скорости охлаждения, попадающей для данной марки стали в инкубационный период образования карбидов хрома (см. рис. 2, кривая 2).
2. Наличие явно выраженной крупнодендритной столбчатой структуры металла шва, что повышает его чувствительность к образованию горячих трещин. Для уменьшения этой опасности рекомендуется применение всех способов, приводящих к измельчению структуры: модифицирование металла титаном и ниобием, применение физических способов (введение вибрации, ультразвука, электромагнитное перемешивание), а также введение в шов элементов ферритизаторов, приводящих к получению в шве островков δ-феррита. Следует также избегать режимов сварки, приводящих к узкой и глубокой форме провара. Актуальным, особенно в глубокоаустенитных швах, является уменьшение содержания таких примесей как фосфор и сера, образующих легкоплавкие эвтектики.
3. Диффузионные процессы (особенно для жаропрочных сталей), происходящие в сварных соединениях при высоких температурах их эксплуатации. Так, термическое старение в диапазоне температур 350...500°С вызывает появление «475-градусной хрупкости».
При температурах 500...650°С наблюдается выпадение карбидов и образование σ-фазы, происходит выпадение интерметаллидов. Все эти процессы теплового старения приводят к охрупчиванию металла при низких температурах и снижению прочности при высоких. Эффективной мерой, предотвращающей вредное действие теплового старения, является уменьшение содержания углерода как в основном металле, так и металле шва.
Технология сварки сталей этого класса должна строиться с учетом как указанных особенностей, так и их теплофизических свойств. Последние характеризуются низкими значениями коэффициента теплопроводности и высокими значениями коэффициента линейного расширения. Отсюда вытекает (при прочих равных условиях по сравнению с перлитными сталями) увеличение глубины проплавления. Для уменьшения деформаций наилучшими способами и режимами сварки будут те, которые характеризуются максимальной концентрацией тепловой энергии.
Технологические способы борьбы с образованием трещин предусматривают изыскание конструктивных форм сварных соединений и режимов сварки, снижающих темп нарастания деформаций в процессе остывания соединения. Важной является форма проплавления, которая не должна быть глубокой при малой ширине (опасность появления горячих трещин по плоскости спайности кристаллитов в сварочной ванне при кристаллизации).
Для сварки этого класса сталей применимы практически все способы сварки плавлением.
При ручной сварке плавящимся покрытым электродом основной трудностью является стабильное обеспечение требуемого химического состава шва в зависимости от его пространственного положения при различных типах сварного соединения с учетом изменения количества наплавленного металла и глубины проплавления основного. Это достигается в основном за счет корректировки состава покрытия (по содержанию в шве необходимого количества феррита).
Тип покрытия – основной (например, фтористокальциевое), ток постоянный обратной полярности. Швы рекомендуется выполнять на малых токах при минимальном диаметре электрода (во избежание появления горячих трещин). При сварке наиболее распространенных коррозионностойких сталей марок 08Х18Н10, 08Х18Н10Т, 12Х18Н10Т, 08Х18Н12Т и т. д. рекомендуется применять электроды типа Э-04Х20Н9, Э-07Х20Н9, Э-08Х19Н10Г2Б марки ЦЛ-11 и др.
При сварке ответственных конструкций следует применять меры, предотвращающие попадание капель расплавленного металла на поверхность основного металла во избежание микротермических ударов, способных при эксплуатации вызвать коррозионное растрескивание под напряжением в этих районах.
Автоматическая сварка под флюсом широко распространена для изготовления конструкций из элементов в толщинах 4,0...60,0 мм. При этом процесс обеспечивает высокая стабильность химического состава шва по длине с одновременной хорошей защитой шва и его формированием. Ток постоянный, полярность – в зависимости от марки применяемых флюсов. Режимы по току невелики (по сравнению с перлитными сталями). Легирование шва производят через флюс или через проволоку. Флюсы безокислительные или малоокислительные (низкокремнистые фторидные или высокоосновные безфтористые). Широко применяются марки АН-26, 48-ОФ-10 и АНФ-14. В зависимости от марки свариваемой стали выбирается система флюс–проволока (например, для стали 20Х23Н8 проволока Св-13Х25Н18, флюс АНФ-5).
При сварке в защитных газах используют как активные газы (СО2), так и инертные (аргон, гелий) либо их смеси. Здесь (особенно при применении смесей) появляется возможность широко регулировать форму проплавления, повышать стабильность горения дуги и уменьшать угар легирующих элементов. При сварке в инертных газах возможно применение как неплавящегося (вольфрамового), так и плавящегося электрода. Первый применяют для сварки металла небольших толщин либо для обеспечения качественного проплавления корня шва. Вольфрамовый электрод применяют в сочетании с аргоном высшего или первого сорта для выполнения соединений в толщинах до 12,0 мм (что не исключает применения способа и для сварки больших толщин).
Сварка ведется на постоянном токе прямой полярности во всех пространственных положениях непрерывной или импульсной дугой. Последний способ при отличном формировании шва на малых толщинах позволяет уменьшить деформации и ширину ЗТВ, получить дезориентированную структуру первичной кристаллизации шва, уменьшая этим опасность возникновения горячих трещин. При сварке плавящимся электродом можно регулировать состав наплавленного металла за счет изменения состава защитной атмосферы.
Сварку плавящимся электродом выполняют как в инертных, так и в активных газах или их смесях. В зависимости от плотности тока и диаметра электродной проволоки перенос металла в дуге может быть капельный и струйный (последний представляется более предпочтительным - при нем практически исключается разбрызгивание).
Струйный перенос кроме критического тока связан с составом газовой атмосферы. Так, добавка 3...5% кислорода уменьшает величину критического тока и (за счет окисления) уменьшает пористость, вызванную водородом. Последнее достигается смесью 85...80% Аг +15...20% СО2. Эта смесь дешевле чистого аргона, однако, здесь существует опасность выгорания легирующих элементов из наплавляемого металла. Этот же процесс сопутствует сварке в чистом СО2, как и определенное науглероживание наплавленного металла.
Сила тока при сварке вольфрамовым электродом выбирается в зависимости от его диаметра, а при сварке плавящимся электродом – в зависимости от диаметра электродной проволоки и толщины свариваемых элементов. Так, для толщины 4,0 мм встык без разделки кромок сварка ведется в один проход dэ=1,0...1,6мм; Iсв=160...280А; расход аргона φ = 6...8 л/мин, а сварка толщины 8,0 мм с V-образной разделкой – в два прохода проволокой dэ= 1,6...2,0 мм при силе тока Iсв= 240...340 А, при расходе φ =12...15 л/мин.
oitsp.ru
Магнитные свойства высококачественных аустенитных нержавеющих сталей
Магнитные свойства высококачественных аустенитных нержавеющих сталей.
Метизы BEST-Крепёж из нержавеющих сталей АISI 304 и АISI 316 позволяют сформировать надёжное крепление, стойкое к образованию коррозии. На них возлагают повышенную ответственность в строительстве и промышленной индустрии, на пищевом и химическом производстве – везде, где ожидается воздействие различных агрессивных сред. В силу чего важно знать: из какой стали сделан крепёж. В быту сформировалось мнение о том, что коррозионностойкие сплавы немагнитны. Поэтому на строительных площадках состав сплава принято определять при помощи бытового магнита. Суть теста проста, если металлическое изделие его притягивает – значит: «..это крепёж не из нержавейки, а из обычный стали..».
На самом деле определение стали, опираясь на магнитные свойства изделия, непрофессионально и, зачастую вводит в заблуждение. Когда мы говорим о «магнитности» того или иного сплава, на самом деле рассматриваем вопрос: какова его магнитная проницаемость (или магнитная восприимчивость).
Хромоникелевые стали А2 и А4 по ГОСТ Р ИСО 3506-1 (согласно АISI они соответствуют сплавам 304 и 316) относят к аустенитным коррозионностойким сталям. Среди прочих они выделяются низким содержанием углерода на фоне повышенного содержания хрома и никеля. Сплавы марок A4 дополнительно легируют молибденом для повышения коррозионной стойкости в агрессивных средах:
Марка стали по ГОСТ Р ИСО 3506 |
Химический состав, % |
||||||||
C |
Mn |
P |
S |
Si |
Cr |
Ni |
Mo |
Cu |
|
A2 |
≤0,1 |
≤2 |
≤0,05 |
≤0,03 |
≤1 |
14 - 20 |
8 – 19 |
- |
≤4 |
A4 |
≤0,08 |
≤2 |
≤0,045 |
≤0,03 |
≤1 |
10 - 15 |
10 - 15 |
2 - 3 |
≤4 |
Хромоникелевые сплавы после закалки на аустенит обладают высокой пластичностью благодаря в первую очередь высокому содержанию никеля (8-14%) вкупе с малым содержанием углерода (не более 0,08%). Благодаря аустенитной структуре их магнитная проницаемость близка к значению немагнитных материлов: 1,002 и выше. Несмотря на это, стали марок А2 и А4 нельзя назвать немагнитными, т.к. их магнитная проницаемость выше μr=1. Различные легирующие элементы заметно изменяют магнитные свойства получаемых сплавов. Так например, некоторые стали марки А2 обладают μr=1,8.
Ко всему прочему термомеханические процессы производства существенно изменяют магнитную и фазовую структуру изделий из хромоникелевых сплавов. При холодных деформациях заготовок обязательных в ходе производственных процессов происходит увеличение магнитной проницаемости готовой продукции из-за структурной трансформации аустенита. Изменения магнитных свойств обусловлены образованием ферромагнитных фаз в структуре этих сталей. В результате чего проверка изделий из аустенитных сталей при помощи магнита или измерителя магнитной восприимчивости может дать неожиданный результат для сплава, который рассматривается как немагнитный. Метизы подвергнутые в ходе производства механическому воздействию, как например, волочение, гибка, нагартовка и т.д., могут вызывать притяжение к себе магнита, даже будучи выполненными из марок сталей А2 по ГОСТ Р ИСО 506.
Единственно достоверным показателем качества метизов из аустенитной сталей является определение её состава. Только крепёжные изделия из регламентированных сплавов обеспечат долговечность эксплуатации крепления даже под воздействием различных агрессивных сред.
Компания BEST-Крепёж специализируется на поставках крепёжных и анкерных элементов из коррозионностойких аустенитных сталей марок А2 и А4 по ГОСТ Р 3506-2009 с 2003 года. Отобранные нами за это время производители метизов зарекомендовали себя неизменным высоким качеством своей продукции, которая проходит обязательную сертификацию в Европе. Кроме того, каждую партию изделий BEST-Крепёж подвергают обязательному входному контролю на определение сплава при помощи спектрометра. Эти предупредительные меры дают нам полную уверенность в соответствии состава легирующих элементов стали требованиям ГОСТ. В особенно сложных вопросах или спорных случаях мы обращаемся за экспертизой к научным сотрудникам Московского института сталей и сплавов (НИТУ МИСиС). Тем не менее, Вы вправе сами подтвердить полученные результаты в любой другой независимой лаборатории.
Специалистами BEST-Крепёж накоплен большой опыт в области нержавеющих крепёжных и анкерных изделий промышленного и строительного направления. По необходимости мы подтверждаем состав легирующих элементов Протоколом анализа с указанием соответствующей марки стали. Кроме того, специалисты компании оказывают помощь в подборе и расчёте крепёжных изделий.
Обращайтесь в технический отдел BEST-Крепёж за консультацией на любой стадии проекта.
www.best-krepeg.ru
Сварка аустенитных сталей
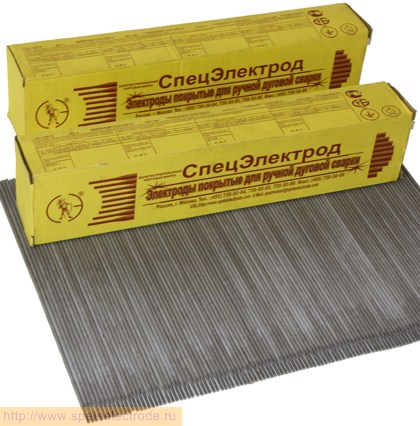
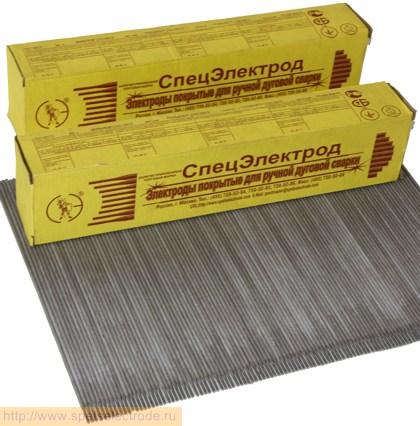
Особенности сварки высоколегированных типов сталей, зависит прежде всего от количественного содержания в сплаве Cr. Один из типов таких легированных сталей – аустенитные стали, имеют составляющую Cr, начиная от 17%, что делает эти марки сталей очень удобными для проведения сварочных работ. Тем более что такие специфические качественные показатели, как удлинение, коэффициент вязкости и показатели при которых сталь теряет свои качества и начинает становиться хрупкой намного выше, чем у других представителей класса высоколегированных сталей – ферритных и мартенситных видов.
Рассматривая процесс сварки в аустенитных сплавах, нужно отметить, что в практическом рассмотрении они более приспособлены к сварочным работам поскольку не требуют дополнительной подготовки и обработки, а кроме этого сварочный шов в таких видах сталей не имеет тенденции к образованию трещин ни в процессе сварочных работ (горячих трещин) ни в обычном состоянии (холодных трещин).
Сортамент марок сталей аустенитного класса и их состав
Основной список марок сталей аустенитного класса поддающихся свариванию содержит стали марки серии 12Х…, 15Х…, но чаще всего используемая марка аустенитной стали с включением хромоникелевого компонента – Х18Н10.
Характеристики этого вида сталей зависят от многих факторов, каждый из которых по-своему влияет на качества сварочного шва и свойства стали в целом. 8% содержания никеля при пластической деформации стали преобразовывается в мартенсит уже при обычной комнатной температуре +21+23 градуса. Жаропрочность таких сталей достигается достижением около 25% хрома в составе сплава, при этом никельсодержащая часть может достигнуть и 38% от общей массы. При проведении сварочных работ необходимо понимать, что легирование этого сорта сталей производится внесением с компонент кремния или алюминия в доле около 1% массы.
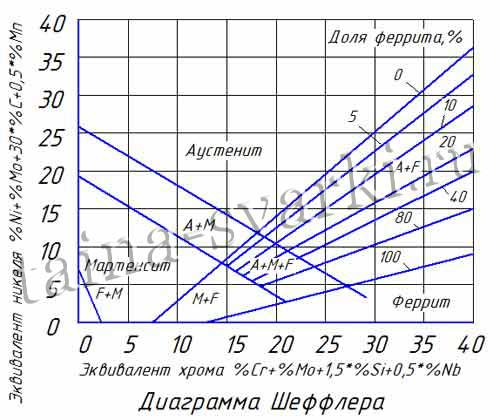
Характеристики сварных швов в зависимости от содержания хрома и никеля определяются чаще всего по диаграмме Шеффлера. Это универсальная диаграмма для расчета сварных швов электродуговой сваркой. Особенностью работы с графиком является возможность применения, кроме имеющихся коэффициентов дополнительных методов, например, использование в качестве расчетного эквивалента показателя содержания меди (коэф. 0,6) или азота применимого в пределах коэффициента 10-30 единиц. Дополнительно можно использовать и другие коэффициенты, например, вольфрама – 0,5 или титана 2-5.
Использование в расчетах диаграмма Шеффлера применимо в основном к ручной дуговой сварке, поскольку изменения структуры сварного шва при других методах соединения, например, с использование газосварочного метода или пайки в диаграмме попросту не отображается.
Однако дуговая сварка аустенитных сталей характеризуемая качеством сварного шва и образования разрывов в виде трещин, как горячего, так и холодного периодов во многом соответствует данному графику и зависит от доли содержания феррита. Повышение, ферритной составляющей в сварном шве от 2 до 6 %, обеспечивает существенное снижение вероятности образования трещин в швах. Такие положительные качества присутствия феррита, с одной стороны, имеют и весьма негативные последствия – снижения вязкости металла соединения, увеличивает температуру и снижает коррозийную стойкость к основным факторам воздействия.
Особенностью наплавленного шва, когда в процессе сварки вязкость сварочной ванны будет особенно высокой, может проходить образование микротрещин, разрывов, отслоений и других видов дефектов сварочного шва. Возможность устранения этих дефектов возможна применения легирования кремнием, с содержанием 0,3-0,7%. Данный интервал позволяет избежать растрескивания шва, но необходимость четко придерживаться данного коридора значений вызвана тем, что при превышении этого значения происходит резкое увеличение процессов образования трещин.
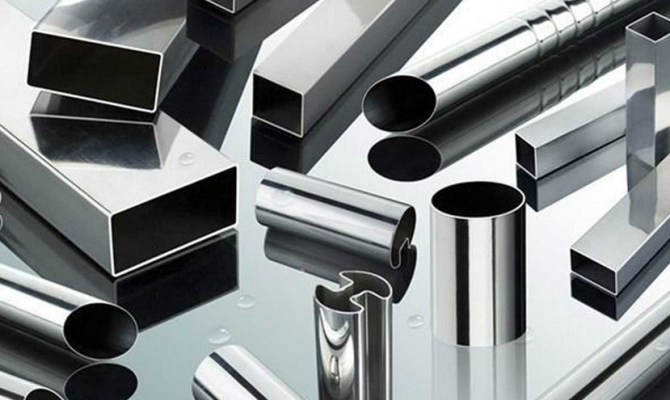
По аналогии с кремнием, также влияет на сварочный шов и марганец, правда нужно отметить, что появление трещин оказывается намного меньше. Одной из особенностей аустенитных сталей хромоникелевого состава выступает специфические деформации сварного шва при остывании – отпускные трещины возникают при остывании места соединения в связи с высоким содержанием углерода в стали.
Особенности изменения структуры металла в процессе сварки аустенитных сталей
Особенностью дуговой сварки аустенитных сталей с содержанием хрома выступает увеличение объема зерен. Этот процесс протекает равномерно постепенно увеличивающиеся зерна в отличие от нелегированных марок конструкционных сталей. Естественным препятствием этого процесса выступает карбидная фаза сварки, во время которой рост зерен не проходит.
Карбидная фаза, растворение которой происходит в зоне перегрева, образует карбиды двух видов – карбид хрома Cr23C6 и карбид титана, образование других видов карбидов, например, ниобия и ванадия проходит несколько в меньшей степени. Кроме карбидов в зоне появляются и нитриды Cr2N. В химическом плане, растворение небольшого количества этих соединений выливается в образовании пленки из растворенных карбидов по границе зерен. Впоследствии эти процессы выступают как места образования очагов внутренней межкристаллитной коррозии.
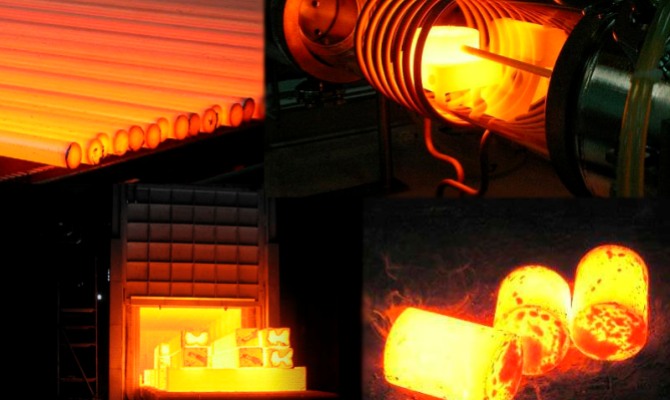
Решить проблему коррозии можно путем стабилизации стали, но даже в случае применения отдельных видов сварки, таких, как сварка под флюсом или электрошлаковая сварка стабилизация стали не спасет от проявления коррозии. Единственным способом повысить прочность сварного шва при дуговой сварке аустенитных сталей выступает применения азота при сварке.
Способы термообработки свариваемых аустенитных сталей
Чаще всего для снятия внутренних напряжений перед сваркой применяется в качестве одного из методов обработки прогрев стали до 200°С. Прогретая сталь, при остывании сварного шва позволяет снять напряжения, но окончательно решить проблему коррозии не вследствие напряжений в месте сварки не удается.
Для решения проблемы коррозионных проявлений вследствие внутренних напряжений применим метод отпуска. Оптимальная температура для этого составляет около 800-850 °C. Для конструкций, применяемых в агрессивных средах, такая температура может быть увеличена до 950-1050°C. Такое повышение температуры способствует скорейшему разрушению карбидной пленки.
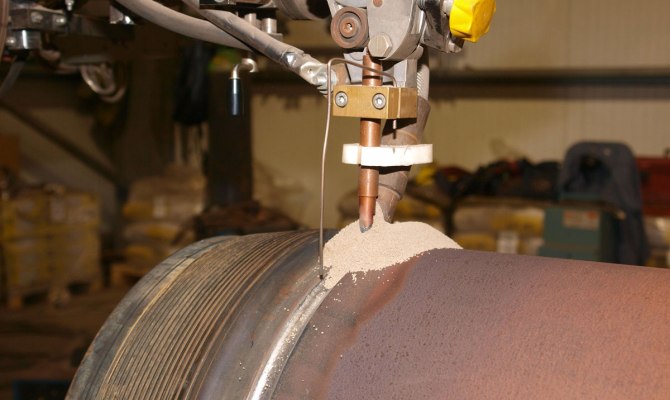
А вот относительно сталей типа Х18Н8 – Х25Н20 характерно при отпускании образование трещин.
Сварка газом аустенитных сталей
Структура стали с содержание хрома очень чувствительна к применению газосварочных технологий, ацетилено-кислородный метод для этого вида сталей наиболее приемлемый, поскольку в отличие от окислительного вида пламени он не сжигает хром. В качестве сварочной проволоки рекомендованы марки с пониженным содержание углерода и легированных ниобием или титаном. При работах с листовым материалом диаметр сварочной проволоки подбирается равным толщине основного материала.
Применение флюсов при газосварочных работах осуществляется с помощью обработки раствора флюса с жидким стеклом на кромки свариваемых поверхностей. Начало работ проводится после высыхания флюса
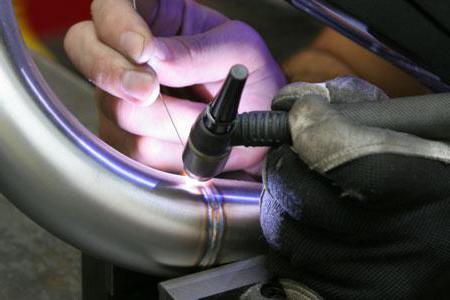
Дуговая сварка аустенитных сталей
Учитывая то, что сами по себе легированные стали обладают отличными конструктивными свойствами и легко поддаются сварочным работам, аустенитные стали не являются в этом перечне исключением. Единственным моментом, требующим основательной проработки, выступает необходимость использования наиболее подходящего расходного материала.
Одним из важнейших условий сварки с помощью ручной электродуговой сварки выступает отсутствие в сварочных электродах ферритной составляющей. Для сварки аустенитных сталей чаще применяю аустенитные электроды УОНИ-13/НЖ, использующие в качестве покрытия состав ЦЛ-2 или ЦЛ-4.
Применение аргонодуговой сварки для соединения тонких листовых материалов стали 12Х18Н9Т дает хорошие результаты с применением флюса. Вместе с тем, необходимо контролировать процесс сварки, поскольку может сложиться ситуация, когда будет резко возрастать количество углерода в сварном шве, что резко скажется на стойкости металла.
Практически для всего сортамента аустенитных сталей чаще всего применяются аустенитные электроды УОНИ-13/НЖ, это практически универсальные для этого вида сталей электрод. Расчет силы тока проводится из пропорции 30-35 Ампер на 1 мм диаметра электрода. Полярность при сварке выбирается обратная, а шов накладывается небольшими участками.
svarkagid.com
Аустенитная сталь - марка - Большая Энциклопедия Нефти и Газа, статья, страница 2
Аустенитная сталь - марка
Cтраница 2
На рис. 7 - 14 приведены фотографии поврежденных труб из аустенитной стали марки ЭИ-257. Образование трещин у изгиба труб указывает на значительную хрупкость металла, появившуюся в результате деформации металла при его гнутье в холодном состоянии. [16]
Применение стали 12Х18Н9ТЛ без гарантированного содержания ферритной фазы, а также однофазных аустенитных сталей марок ЛА-1 и ЛА-3 и им подобных не рекомендуется из-за низкой их литейной технологичности и опасности массового появления трещин в околошовной зоне сварных соединений. [17]
По данным Р. П. Залетаевой, Н. С. Крещановпкого п Л. Л. Кунина [128], присадка 0 5 % Са в аустенитную сталь марки Х15Н25, склонную к столбчатой кристаллизации, сильно уменьшая поверхностное натяжение этой стали в расплавленном состоянии, способствует резкому измельчению ее структурных составляющих. [18]
Роторы газовых турбин [151] работают при температуре свыше 600 С, поэтому для их изготовления используются аустенитные стали марок ЭИ405 и ЭИ572, обладающие высокой жаропрочностью и хорошей свариваемостью. [19]
Другим примером аналогичного конструктивного решения является боковая паровая коробка турбины СВК-150 ЛМЗ, изготовленная из поковок аустенитной стали марки ЭИ405 ( фиг. Данный узел конструктивно и технологически весьма сложен, и поэтому подобное решение следует считать вынужденным в связи с отсутствием в то время качественных отливок из аустенитных сталей. [20]
Рассмотрим вначале возможность применения широко распространенных электродов или сварочных проволок типа ЭА-1 ( Х18Н9) для сварки аустенитной стали марки 1Х18Н9Т с малоуглеродистой сталью ( фиг. [21]
ПВД и детали насосов; хромистая сталь для деталей насосов и других деталей, способных подвергаться коррозионно-эрозионному разрушению; аустенитная сталь марки 1Х18Н9Т для изготовления трубок ПНД при окислительных ( кислородные и перекись-водородные) водно-химических режимах ( см. гл. [22]
В качестве эталонов обрабатываемости обычно берут либо наиболее распространенную конструкционную сталь марки 45 в состоянии нормализации или отжига, либо аустенитную сталь марки 1 X 1 8Н9Т, обрабатываемость которой мало зависит от термической обработки. [23]
При сварке перлитной стали марок 20, 15ГС, 12Х1МФ и подобных присадочная проволока подается вслед движению электрода; при сварке аустенитной стали марки 08Х18Н10Т и подобных - навстречу движения электрода. [24]
В качестве материала для направляющих и рабочих лопаток газовых турбин при длительной работе с температурой газа до 650 С в отечественной практике находят применение аустенитные стали марок ЭИ-69, ЭЙ-123, ЭИ-405 и др., образованные на хромоникелевой основе ( 13 - г - 16 % Сг и 12 - - 15 % Ni) с добавкой в небольших количествах молибдена, вольфрама, титана и ниобия. Выбор стали производится в зависимости от напряжений. Материалом для барабанов и дисков газовых турбин служат стали того же класса, что и для рабочих лопаток. [25]
Электрод ЦТ-15 ( марка стали стержня Св - 1Х18Н9Т) применяется для приварки арматуры из аустенитных сталей к трубопроводам из стали марки 1Х18Н12Т, а также для сварки наиболее важных узлов установок сверхвысокого давления из аустенитной стали марки 1Х18Н12Т, работающих при температурах 600 - 650 С. [26]
Подобное же конструктивное решение [88 ] нашло применение в турбине фирмы Вестингауз установки Эддистоун на параметры пара 650, 315 ата ( фиг. Аустенитная сталь марки AJSJ316 ( 16 % Сг; 13 % Ni; 3 % Мо) применена в паропроводе. В показанной конструкции приняты также меры к тому, чтобы затруднить передачу тепла от горячего паропровода к соединительному патрубку и способствовать постепенному и равномерному снижению температуры патрубка от температуры паропровода до температуры цилиндра. Отличительной особенностью является также изготовление выходного патрубка в виде поковки, вваренной в литой цилиндр, что значительно упростило отливку последнего. [27]
Сталь Х17Н2 сваривается всеми видами сварки. В качестве присадочной проволоки применяют аустенитные стали марок ОХ18Н9 или Х18Н12М2 ( ЭИ400) с обмазкой НЖ1 или электроды ЦЛ-11 / св. [29]
Двухслойные стали состоят чаще всего из низкоуглеродистой стали и покрывающего ее слоя коррозионностойкой стали. В качестве антикоррозионного слоя применяют аустенитные стали марок 08Х18Н10Т, 08Х17Н13МЗТ и подобных им. Дуговая сварка двухслойной - стали по технике выполнения швов аналогична сварке однослойного металла. Чаще всего шов выполняется вначале со стороны углеродистой стали, затем наплавленный металл со стороны плакирующего слоя зачищается и сваривается уже плакирующий слой. Электроды по химическому составу должны быть однородны с металлом плаки-пуюшегп например. [30]
Страницы: 1 2 3
www.ngpedia.ru
Аустенитная сталь - марка - Большая Энциклопедия Нефти и Газа, статья, страница 3
Аустенитная сталь - марка
Cтраница 3
Двухслойные стали состоят чаще всего из низкоуглеродистой стали и покрывающего ее слоя коррозионно-стойкой стали. В качестве антикоррозионного слоя применяют аустенитные стали марок 08Х18Н10Т, 08Х17Н13МЗТ и подобных им. Дуговая сварка двухслойной стали по технике выполнения швов аналогична сварке однослойного металла. Для сварки аустенитными электродами применяют постоянный ток обратной полярности. [31]
Влияние режима азотирования на кавитационную стойкость стали. / - сталь марки 38ХМЮА, азотирование по режиму 525 С, 35 ч. 2 - сталь марки 38ХМЮА, шестикратное азотирование по режиму 510 С, 12 ч 540 С, 40 ч. 3 - сталь марки 38ХМЮА, азотирование по режиму 510 С, 12 ч 540 С, 40 ч, с последующим шлифованием на 0 05 мм. 4 - сталь марки 38ХМЮА после улучшения. 5 - сталь марки 1Х18Н9 без азотирования. 6 - сталь марки 1Х18Н9Т после азотирования по режиму 600 С, 75 ч. 7 - ЭИ123 ( X14HI4B2C2T без азотирования. 8 - ЭИ123 после азотирования по режиму 650 С, 120 ч. [32] |
Кавитационная стойкость стали после азотирования возрастает ( рис. 40 к Так стойкость стали марки 38ХМЮА после азотирования более чем в 17 раз превышает стойкость ее в улучшенном состоянии и в 8 раз - стойкость цинкового покрытия с пассивированием этой же стали. Положительное влияние оказывает азотирование и на кавитационную стойкость аустенитной стали марок 1Х18Н9Г, ЭИ123 и др. Наличие е фазы в слое снижает сопротивление кавитации. Поэтому шлифование азотированных деталей приводит к повышению сопротивления кавитационной эрозии. [33]
Из различных элементов, которые стабилизируют феррит, алюминий является наиболее эффективным. Так, например, при введении алюминия в состав аустенитной стали марки 1Х18Н9Т сужается у-область и повышается степень двухфазности стали за счет большего развития а-6 - области. Как ферритизатор, алюминий в 10 - 15 раз сильнее хрома. Введение алюминия в сталь до 1 или 2 % улучшает до некоторой степени сопротивление окислению при высоких температурах путем образования защитной пленки окислов алюминия. Однако при содержании в стали алюминия более 1 % разрезаемость ее ухудшается. [34]
Общий недостаток медно-железных электродов - неоднородная структура шва: мягкая медная основа и очень твердые включения железной составляющей, затрудняющие обработку и препятствующие получению высокой чистоты обработанной поверхности. Несколько лучшей обрабатываемостью обладают швы, выполненные электродами марки АНЧ-1, стержень которых состоит из аустенитной стали марки Св - 04Х18Н9 и медной оболочки. [35]
Аустенитные стали с содержанием 18 % Сг и 9 % Ni, в частности сталь марки Х18Н9Т, широко применяются для изготовления внутреннего сосуда резервуаров. Они характеризуются высокой прочностью, хорошей свариваемостью и низкой теплопроводностью. Перспективным конструкционным материалом для резервуаров является аустенитная сталь марки Х14Г14НЗТ, содержащая лишь 3 % никеля. [36]
Газопровод имеет двухслойную цилиндрическую конструкцию с внутренней изоляцией толщиной 90 мм. Наружный корпус изготовлен из стали 12МХ толщиной 8 мм, диаметр его 1036 мм. Внутренняя рубашка диаметром 810 мм выполнена из аустенитной стали марки 1Х18Н9Т толщиной 5 мм. С целью компенсации температурных расширений на газопроводе расположено 12 линзовых компенсаторов. [37]
Решетка разгружена от действия изгибающих усилий, воспринимаемых стойками, выдолбленными в корпусе. Такая конструкция полностью свободна от протечек пара. В связи с изготовлением данного узла из аустенитной стали марки ЭИ612 сварка его производится без подогрева. После сварки узел подвергается стабилизации для снятия напряжений. [38]
Теплоноситель реакторов типа PWR представляет собой простую жидкую фазу, поэтому возможно введение твердых или газообразных добавок, которые остаются в растворе и оказывают ингибирующее действие. Первый контур реактора PWR менее разветвлен и более надежен, чем контур реактора BWR, поэтому возможность разуплотнения его меньше, что позволяет точно определять и длительное время сохранять неизменным состав теплоносителя в реакторе PWR на оптимальном уровне. У большинства легководных реакторов контуры почти полностью изготовлены из аустенитных сталей марок 304 и 321, а в реакторах CANDU и типа PWR, кроме того, используются углеродистые или низколегированные ферритные стали. Максимальная концентрация продуктов коррозии в контуре реактора такого типа в период работы колеблется от 0 020 мг / кг при концентрации водорода 2 см3 / кг до 0 200 мг / кг при концентрации водорода 2 см3 / кг. После завершения кампании максимальная концентрация их достигает 50 мг / кг. Высокое значение рН обычно сохраняют, добавляя гидроокись лития или поддерживая содержание кислорода на возможно более низком уровне. Последнее достигается деаэрацией воды и поддержанием постоянного давления водорода в резервных водяных емкостях. Кроме того, в теплоноситель реактора PWR обычно добавляют борную кислоту для изменения реактивности. Ее влияние чаще всего положительное, но она может адсорбироваться продуктами коррозии и, если последние выделяются в активной зоне, может иметь место скачок реактивности. Однако-обычно нарушения работы водяного контура реактора PWR происходят редко. [39]
При всех способах сварки легированных труб режимы оговариваются в специальных инструкциях или технических условиях. Отклонения могут быть лишь при сварке корневого и облицовочных слоев шва. Так, при сварке труб диаметром 57 - 159 мм из аустенитной стали марки 1Х18Н10Т неплавящимся вольфрамовым электродом в среде аргона с использованием автомата АТВ корневой шов сваривается без присадки электродом диаметром 2 - 2 5 мм на сварочном токе 170 - 180 а, напряжением 10 - 11 в со скоростью 13 - 14 м / ч и расходом аргона 8 - 10 л / мин. [41]
Страницы: 1 2 3
www.ngpedia.ru
Марки стали
20Х13 | Детали с повышенной пластичностью, подвергающиеся ударным нагрузкам (клапаны гидравлических прессов, предметы домашнего обихода), а также изделия, подвергающиеся воздействию слабоагрессивных сред (атмосферные осадки, водные растворы солей органических кислот при комнатной температуре и др.). Клапаны гидравлических прессов, лопатки паровых турбин, тарелки и седла клапанов, поршневые кольца и др. детали, подвергающиеся ударным нагрузкам и работающие при температуре до +450-500 С; изделия, подвергающиеся воздействию слабоагрессивных сред. | |
08Х13 | Детали с повышенной пластичностью, подвергающиеся ударным нагрузкам (клапаны гидравлических прессов, предметы домашнего обихода), а также изделия, подвергающиеся действию слабоагрессивных сред (атмосферные осадки, водные растворы солей органических кислот при комнатной температуре и др.). Лопатки, бандажи, трубы, а также другие изделия, для которых требуется сопротивление окислению до +800 С. Сталь ферритного класса. | |
12Х13 | Детали с повышенной пластичностью, подвергающиеся ударным нагрузкам (клапаны гидравлических прессов, предметы домашнего обихода), а также изделия, подвергающиеся действию слабоагрессивных сред (атмосферные осадки, водные растворы солей органических кислот при комнатной температуре и др.). Турбинные лопатки, бандажи, скрепляющая проволока, детали, работающие при температуре +450-500 С; детали, работающие в атмосферных условиях и слабоагрессивных средах. | |
30Х13, 40Х13 | Режущий, измерительный и хирургический инструмент, пружины, карбюраторные иглы, предметы домашнего обихода, клапанные пластины компрессоров | |
12Х17 | Предметы домашнего обихода и кухонной утвари, оборудование заводов, пищевой и легкой промышленности. Сталь для изготовления сварных конструкций не рекомендуется. | |
08Х17Т | Рекомендуется в качестве заменителя стали марки 12X18Н10Т для конструкций, не подвергающихся воздействию ударных нагрузок, и эксплуатирующихся при температуре не ниже -20 С. Применяется для тех же целей, что и сталь марки 12X17, в том числе для сварных конструкций. | |
15Х25Т | Рекомендуется в качестве заменителя стали марки 12X18Н10Т для сварных конструкций, не подвергающихся действию ударных нагрузок, эксплуатирующихся при температуре не ниже -20 С для работы в более агрессивных средах по сравнению со средами, для которых рекомендуется сталь марки 08X17Т. Трубы для теплообменной аппаратуры, работающей в агрессивных средах, арматура нагревательных печей, чехлы термопар, электроды искровых зажигателей, трубы пиролизных установок. Не рекомендуется эксплуатировать в интервале температур 400-700 С. | |
08Х22Н6Т | Рекомендуется как заменитель стали марок 12X18Н10Т и 08X18Н10Т для изготовления сварной аппаратуры в химической, пищевой и других отраслях промышленности, работающей при температуре не выше 300 С. Обладает более высокой прочностью по сравнению со сталью 12X18н10Т и 08X18Н10Т. Сварные аппараты и сосуды для химического машиностроения, камеры горения и другие конструктивные элементы газовых турбин, корпуса аппаратов, днища, фланцы, детали внутренних устройств аппаратов, трубные доски и пучки, работающие при температуре от -70 С до +300 С, и соприкасающиеся с коррозионными средами. | |
08Х21Н6М2Т | Рекомендуется как заменитель марки 10X17Н13М2Т для изготовления деталей и сварных конструкций, работающих в средах повышенной агрессивности: уксуснокислых, сернокислых, фосфорнокислых средах. Обладает более высокой прочностью по сравнению со сталью 10X17Н13М2Т. Ректификационные колонны, экстракционные, насадочные, продувные емкости, хранилища, баки, сборники и другое оборудование, работающее в окислительно-восcтановительных средах, например, при органическом синтезе, серно-кислотном производстве, в целлюлозно-бумажной промышленности. | |
10Х14Г14Н4Т | Рекомендуется как заменитель стали марки 12X18Н10Т для изготовления оборудования, работающего в средах слабой агрессивности, а также при температурах -196 С. Обладает удовлетворительной сопротивляемостью межкристаллитной коррозии. | |
10Х17Н13М2Т, 10Х17Н13М3Т | Рекомендуется для изготовления сварных конструкций, работающих в условиях действия кипящей фосфорной, серной, 10% уксусной кислоты и сернокислых средах. Аппараты и сосуды, работающие в средах повышенной агрессивности. Лопатки газодувки, штампуемые из листовой стали, заклепки, изготавливаемые методом горячей высадки, поковки дисков, покрышек, валов и других деталей компрессорных машин, детали турбин. | |
08Х17Н15М3Т | Рекомендуется для изготовления сварных конструкций, работающих в условиях действия кипящей фосфорной, серной, 10% уксусной кислоты и сернокислых средах. Практически не содержит ферритной фазы. Обладает более высокой стойкостью против точечной коррозии, чем сталь марки 10X17Н13М2Т в средах, содержащих ионы хлора. | |
03Х17Н14М2 | Рекомендуется для изготовления сварных конструкций, работающих в условиях действия кипящей фосфорной, серной, 10 уксусной кислоты и сернокислых средах. Обладает более высокой стойкостью против межкристаллитной и ножевой коррозии, чем сталь 08X17Н15М3Т и 10X17Н13М2Т. | |
15Х18Н12С4ТЮ | Рекомендуется для сварных изделий, работающих в воздушной и агрессивных средах, в частности для концентрированной азотной кислоты. | |
08Х10Н20Т2 | Рекомендуется как немагнитная сталь для производства крупногабаритных деталей, работающих в морской воде | |
04Х8Н10 | Применяется для тех же целей, что и сталь марки 08X18Н10Т, и для работы в азотной кислоте и азотнокислых средах при повышенных температурах. Обладает более высокой стойкостью к межкристаллитной коррозии. | |
03Х18Н11 | Применяется для тех же целей, что и сталь марки 08X18Н10Т, и для работы в азотной кислоте и азотнокислых средах при повышенных температурах. Обладает более высокой стойкостью к межкристаллитной коррозии и с повышенной стойкостью к ножевой коррозии по сравнению со сталью 12X18Н12Б. | |
08Х18Н10Т | Рекомендуется для изготовления сварных изделий, работающих в средах более высококй агрессивности, чем сталь марок 12Х18Н10Т и 12Х18Н12Т. Сталь обладает повышенной сопротивляемостью межкристаллитной коррозии по сравнению со сталью 12Х18Н10Т и 12Х18Н12Т. Детали и узлы основного оборудования и трубопроводов АЭУ с водяным теплоносителем. Сварная аппаратура, работающая в растворах азотной, фосфорной, уксусной кислот, растворов щелочей и солей, теплообменники, муфели, трубы, детали печной арматуры, изделия автомобилестроения, торгового машиностроения, товары широкого потребления | |
12Х18Н10Т | Детали и узлы основного оборудования и трубопроводов АЭУ с водяным теплоносителем. Лопатки, трубы и другие детали энергетического машиностроения, работающие при температуре до +600 С. Сварные аппараты и сосуды, работающие в разбавленных растворах азотной, уксусной, фосфорной кислот, растворах щелочей и солей; днища адсорбера, регенераторы, теплообменники и др. Корпуса и другие детали, работающие под давлением при температуре от -196 С до +600 С, а при наличии агрессивных сред — до +350 С. | |
02Х22Н5АМ3 | Для изготовления сварных труб и теплообменного оборудования | |
10Х13Г12С2Н2Д2Б | Жаростойкая, жаропрочная аустенитная сталь до температуры 700 С для элементов оборудования теплоэнергетической (трубы поверхностей нагрева котлов энергоблоков, работающих на высоко-агрессивных органических топливах с высоким содержанием ванадия, серы и др.), нефтеперерабатывающей, нефтехимической и др. областей промышленности. | |
08Х14МФ | Трубы теплообменного оборудования, трубы, лист, поковки для энергооборудования, а также оборудования для пищевой промышленности. | |
12Х18Н9 | Применяется в виде холоднокатанного листа и ленты повышенной прочности для различных деталий конструкций, свариваемых точечной сваркой, а также изделий, подвергаемых термической обработке (закалке). Сварные детали и конструкции различного назначения, муфели термических печей, детали крепежа теплообменников, опорные элементы кладки печей. | |
08Х18Н10 | Применяется в виде холоднокатанного листа и ленты повышенной прочности для различных деталей конструкций, свариваемых точечной сваркой, а также изделий, подвергаемых термической обработке (закалке). Детали из тонкого листа и ленты в автомобилестроении, торговом машиностроении, для товаров ширпотреба, для изделий, подвергаемых закалке, для сварных аппаратов и сосудов химического машиностроения, для работы в средах, не вызывающих межкристаллитную коррозию. | |
12Х18Н12Т | Детали и узлы основного оборудования и трубопроводов АЭУ с водяным теплоносителем; трубы для перегревателей и коллекторов тепловых электростанций, работающие при температуре +610-640 С. Сварные аппараты и сосуды, работающие в коррозионно-активных средах (разбавленные растворы азотной и фосфорной кислот, растворы щелочей и солей). | |
06ХН28МДТ | Для сварных конструкций, работающих при температурах до 80 С в серной кислоте различных концентраций, за исключением 55% уксусной и фосфорной кислот, в кислых и сернокислых средах, в производстве сложных минеральных удобрений. | |
10Х23Н18 | Трубы и детали установок для конверсии метана, пиролиза, листовые детали | |
20Х23Н18 | Детали установок в химической и нефтяной промышленности, газопроводы, камеры сгорания ( может применяться для нагревательных элементов сопротивления | |
Сплавы на железоникелевой основе | ||
ХН32Т | Газоотводящие трубы, листовые детали высокотемпературных установок в нефтехимическом машиностроении с длительным сроком службы при температурах +700-850С | |
ХН35ВТ | Лопатки газовых турбин, диски , роторы, крепежные детеали, плоские пружины и другие детали, работающие при температуре до +650С | |
ХН45Ю | Детали горелочных устройств, чехлы термопар, листовые и трубчатые детали печей ( напрмер производство вспученного перлита) | |
Сплавы на никелевой основе | ||
ХН60ВТ | Листовые детали турбин, детали газопроводных систем, жаровые трубы, детали камер сгорания, уплотнения и другие детали высокотемпературных газовых турбин | |
ХН65МВУ | Применяется для изготовления сварных конструкций, работающих при повышенных температурах в агрессивных средах окислительно-востановительного характера ( серная , уксусная, влажный хлор, хлориды и т.д.). Сплав устойчив к межкристаллитной коррозии в агрессивных средах. | |
Н70МФВ | Применяется для изготовления сварных конструкций, работающих при высоких температурах в соляной, серной, фосфорной кислоте и других средах восстановительного характера. Сплав устойчив к межкристаллитной коррозии в агрессивных средах восстановительного характера | |
ХН77ТЮР | Газовые диски и рабочие лопатки турбин | |
ХН78Т | Жаровые трубы, детали газопроводных систем, сортовые детали |
www.centravis.com