- Электродный бой.
- Графитовая стружка, оставшаяся после обработки фасонных изделий.
- Нефтяной кокс, пековый кокс.
- Огарки графитовых электродов.
- Графитовый лом.
- Антрацит.
- массовая доля углерода: чистота химического состава оказывает прямое влияние на степень насыщения расплава. Наименьшим содержанием примесей характеризуются материалы, подвергнутые графитации: при упорядочивании структуры атомных слоев происходит и снижение зольности;
- степень усвоения углерода жидким металлом: во многом зависит от типа используемого плавильного агрегата, но значение имеют также и скорость растворения науглероживающих реагентов, их химический и минералогический состав, содержание летучих веществ. Измельченный графит растворяется в расплавах быстро и равномерно даже при относительно низких температурах;
- размер фракций: пылевидные и мелкие частицы могут быть унесены конвективными воздушными потоками; кроме того, они наиболее подвержены окислению. Крупные фракции медленно растворяются. Чтобы правильно рассчитать этот параметр, следует исходить из объема обогащаемой стали (чугуна), а также интенсивности перемешивания;
- зольность: зола состоит из разных химических элементов, которые оказывают негативное влияние на поглощение углерода жидким металлом. Минеральные примеси первыми вступают в реакцию, откладывая тем самым процесс науглероживания. Процентное содержание золы во многом зависит от состава исходного сырья, температуры его обработки и величины частиц.
- снижение себестоимости конечной продукции;
- оптимизация технологического процесса выплавки;
- глубокое, полное и равномерное растворение углерода в металле;
- удобство транспортировки и хранения;
- устойчивость к окислению.
- Технология алитирование стали
- Науглероживание стали в домашних условиях
- Гост углеродистые стали
- Технология алитирование стали
- Гост углеродистые стали
- Марка стали пружинной стали
- Марка стали пружинной стали
- Листовая сталь с полимерным покрытием
- Сталь листовая углеродистая обыкновенного качества марки вст3пс5
- Технические характеристики труба стальная электросварная
- Аустенитные стали что это
Химико-термическая обработка стали. Науглероживание стали в домашних условиях
Химико-термическая обработка стали | Обработка металла – стали и цветных металлов
Такая обработка металла изменяет не только его структуру, а и химический состав его поверхности. Благодаря этому деталь может иметь вяжущую сердцевину, которая выдерживает ударные нагрузки, и высокую твердость и стойкость против воздействия извне. Существует несколько способов химико-термической обработки, но в условиях небольшой мастерской (тем более в домашних условиях) можно выполнить только цементацию.
Цементация – насыщение углеродом поверхностного слоя стали без доступа воздуха, в среде (карбюризаторе), котороя имеет значительное содержимое углерода. Цементируют обычно детали из малоуглеродных сталей, которые после закала поверхностного слоя шлифуют. Карбюризаторы для цементации поверхностного слоя стали могут иметь разный состав, но простейший такой, %:
Углекислый натрий или углекислыйбарий (для ответственных деталей) ………10Углекислый кальций……………………………..3Древесный уголь…………………………………..87
Карбюризатор можно приготовить из углекислого натрия (сода 6-10 %) и пиленного рога или торфяного кокса ( 90-94 %). Мелкие или одиночные детали цементируют в пасте, которая состоит из таких компонентов, %:
Газовая сажа……………………………………….28Кальцинированная сода………………………3,5Желтая кровяная соль………………………..1,5Веретенное масло……………………………….67илиГолландская сажа………………………………30Кальцинированная сода……………………….10Веретенное масло………………………………40Декстрин (клей) ………………………………..20
Хорошую пасту для цементации можно приготовить из художественной краски «Газовая сажа» (продают в тюбиках), к которой домешивают часть за массой кальцинированной соды.Места на деталях, которые не нуждаются в цементации, защищают противо-цементационными обмазками. Простейшая обмазка – это огнеупорная глина с добавкой (10 %) асбестового боя. Замешивают смесь на воде. Удобная в пользовании и такая обмазка, %: тальк-50, каолин – 25, вода – 25.Разводят эту обмазку к нужной плотности жидким стеклом или конторским силикатным клеем. Закладывают детали в цементационные ящики после высыхания обмазки. Цементируют так. В металлический ящик с крышкой на дно насыпают карбюризатор слоем 30— 40 мм и на него кладут подготовленные (обмазанные) детали таким образом, чтобы расстояние между ними, а также между ними и стенками ящика сотовляла около 10-15 мм. Сверху детали присыпают карбюризатором слоем 30—40 мм, закрывают крышкой, промазывают ее кромки огнеупорной глиной и сушат.Если для цементации используют пасту, то деталь намазывают ею слоем толще 3-4 мм, кладут в ящик, закрывают и также обмазывают кромки крышки огнеупорной глиной. После высыхания глины ящик помещают в печь и выдерживают (температуры 930—950 °С) на протяжении 1,5-3 года (с твердым карбюризатором 7-8 лет). При этом слой цементации достигает 1 мм. Иногда в ящике для цементации делают отверстия и в них вставляют 1-2 отрезка мягкого стального провода диаметром 3-4 мм (пробник). Щели хорошо обмазывают огнеупорной глиной. Спустя некоторое время пробник вынимают, отверстие замазывают глиной, а пробник переризают и определяют глубину цементации, т.е. целесообразность дальнейшего прогревания. После цементации детали охлаждают вместе с ящиком, потом нагревают до температуры 760— 780 °С. и закаливают. Упрощенная цементация. Небольшие детали из малоуглеродных сталей цементируют такими способами:желтой кровяной солью ( железо-цианистый калий). Для цементации деталь нагревают, обсыпают солью и снова нагревают до расплавления соли (850 °С), потом вынимают и закаливают. При этом слой цементации сравнительно небольшой – около 0,15 мм. Если необходимо увеличить его, деталь обсыпают солью и нагревают при указанной температуре на протяжении 1 ч, потом сразу же закаливают, чугунными опилками. Это старый кузнечный способ «укрепление в горне». Нагретую к белому цвету деталь, не вынимая из горна, очищают проволочной щеткой и присыпают чугунными опилками, из которых углерод переходит на поверхность детали. Очищение и присыпания повторяют несколько раз. Целесообразно одновременно с опилками присыпать накаленное изделие древесному углем. После этого изделие закаливают восстановительным пламенем горелки. Если в газовую горелку не дать достаточно кислорода, углерод, который есть в ацетилене, не полностью сгорает и может переходить в состав металла на месте сваривания, т.е. происходит местное неглубокое науглеродование. Когда же одновременно применить как присадку стальной провод, который используют в автоматах для наваривания шеек коленчатых и других валов, толщину углеродного пласта можно увеличить до 1-2 мм. Смотрите также термическая обработка стали.
ometals.ru
Технология цементации стали. Закалка в домашних условиях видео.
Важным способом улучшения эксплуатационных свойств стали является химико-термическая обработка (ХТО), которая предполагает воздействие на заготовку реагента при повышенной температуре. В холодном состоянии сталь характеризуется низкой химической активностью, даже образование ржавчины протекает достаточно медленно. Чтобы увеличить скорость реакции, сталь нагревают до высокой температуры. Согласно правилу Вант-Гоффа, повышение температуры на 10° приводит к увеличению скорости химической реакции вдвое. Высокие температуры позволяют выполнить обработку стали за допустимое время для промышленного производства.

В процессе обработки заготовка находится в среде химически активного вещества. Оно формирует на поверхности заготовки слой с особыми свойствами, отличающимися от основной части. В большинстве случаев ХТО позволяет улучшить механические свойства материала, его прочность, твердость и стойкость к износу.
Самыми популярными процессами ХТО выступают цементация, предполагающая насыщение углеродом, и азотирование, в котором ведется обработка азотом. Также высокой эффективностью обладает нитроцементация, которая совмещает азотирование и цементацию. Обработка другими элементами встречается редко. Выбор способа обработки ведется в зависимости от химического состава стали, от содержания углерода и легирующих веществ.
ХТО является одной из завершающих операций в технологическом цикле производства стальных деталей. Она выполняется после формоизменяющих операций, обработки давлением и резанием. В результате ХТО деталь приобретает увеличенную прочность поверхностного слоя, и обработать такую деталь становится гораздо сложнее. ХТО выполняется таким образом, чтобы коробление поверхности было минимальным и не требовалось выравнивать поверхность, срезая верхний слой. После ХТО производится только шлифовка поверхности.
Цементация стальных изделий
Стали, подвергаемые цементации, можно разделить на три группы по химическому составу:
Конструкционные стали, нелегированные или низколегированные: 15, 18, 20, 20Х, 20ХФ, 20ХМ, 18ХГ, 20ХН. Эти стали имеют низкую стоимость, но их невозможно закалить обычным способом из-за недостаточного содержания углерода, поэтому насыщение поверхности – простой способ увеличения их прочности.
Стали, легированные титаном 18ХГТ, 25ХГТ, 30ХГТ, 20ХНТ, 20ХГНТР. В них образуется особо прочное соединение – карбид титана.
Высоколегированные конструкционные стали: 12Х2Н4А, 20Х2Н4А, 18Х2Н4ВА, 18Х2Н4МА. Из них изготавливают наиболее прочные и ответственные детали.
Разработка технологии цементации зависит от группы, к которой относится сталь. Чтобы получить высокую твердость поверхности, от 58 HRC и выше, обработанную деталь подвергают закалке с последующим низким отпуском. Таким образом, сердцевина детали остается «мягкой» и вязкой, с твердость 35-40 HRC при высокой твердости поверхности. Благодаря этому обработанная деталь может использоваться при изгибающих нагрузках, которые опасны для хрупких изделий.
Способы выполнения цементации
Наибольшей популярностью пользуется газовая цементация. Она выполняется в печах шахтного типа, то есть установках, где обрабатываемые детали располагаются ниже уровня пола. Такая конструкция связана с несколькими особенностями процесса. Во-первых, так проще обеспечить печи герметичность. Вторая причина – газы, воздействующие на металл, имеют большую плотность, чем у воздуха. Газовая цементация используется на заводах, массово производящие упрочненные детали.
Температура при газовой цементации составляет 920-950 °С. Длительность обработки зависит от требуемой глубины цементированного слоя. Средняя скорость диффузионного распространения углерода 0,15 – 0,18 мм/ч. Обычно требуется упрочненный слой толщиной 0,8 – 1,5 мм, то есть продолжительность процесса может достигать 10 часов. Содержание углерода после обработки в поверхностном слое доходит до одного процента. Процесс цементации и последующее термическая обработка могут выполняться тремя различными режимами в зависимости от степени ответственности деталей. Неответственные детали обрабатывают за 2 нагрева, детали с повышенными требованиями – за 3, а с особенно высокими требованиями – за 4, применяя двойную закалку.
В мелкосерийном производстве достаточно популярен способ цементации при помощи твердого активного вещества, в состав которого входит древесный уголь и кокс, а также катализаторы процесса. Для обработки деталь помещается в стальную емкость. Несколько деталей размещаются таким образом, чтобы не касались друг друга или емкости.
Температура данного способа несколько выше, чем при газовой цементации. Недостатком процесса является сложность контроля над насыщением поверхности углеродом, что может привести к неравномерной твердости.
samara-metall.ru
Закалка ножа в графите
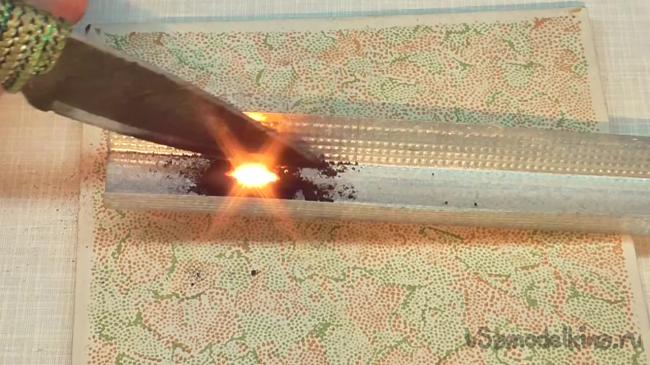
Нам понадобится:- источник постоянного тока;- немного соли;- вода;- графит в порошкообразном состоянии;- небольшой кусок тряпки;- металлический профиль.
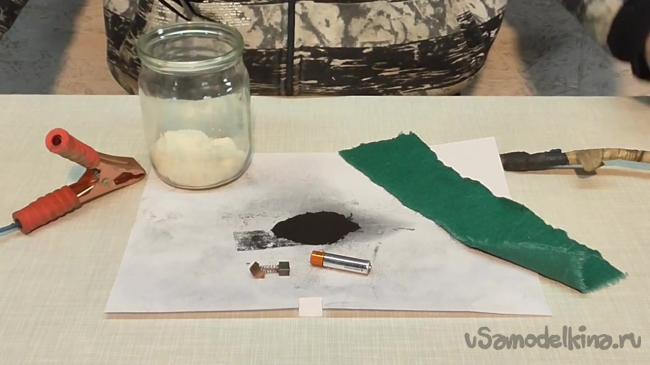
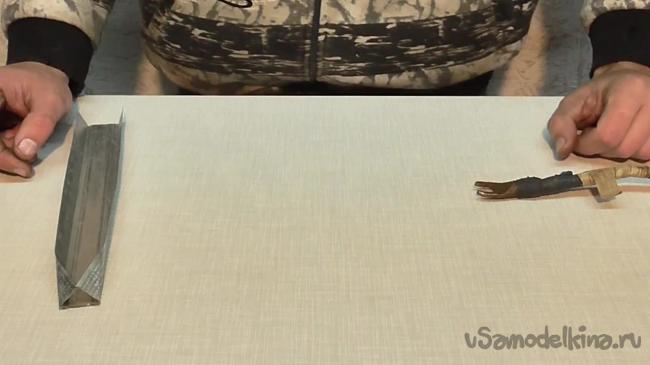
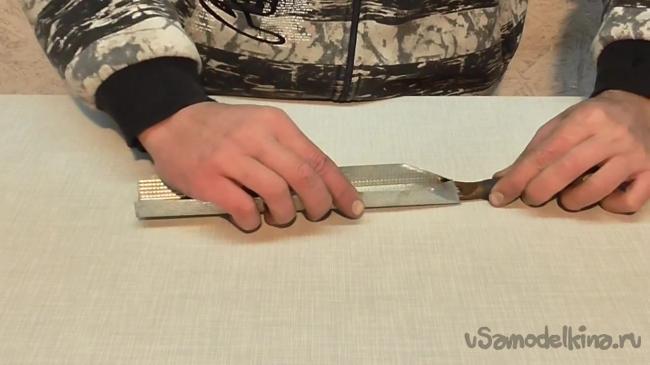
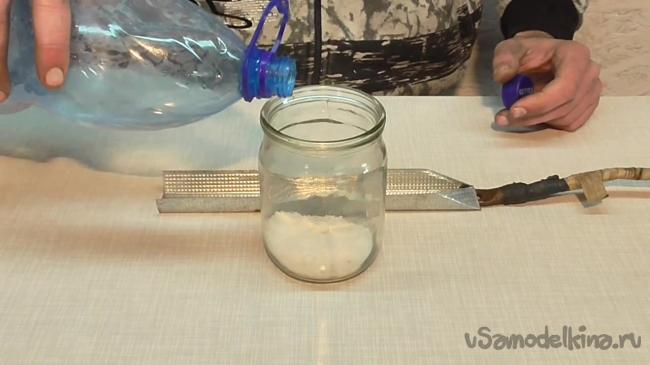
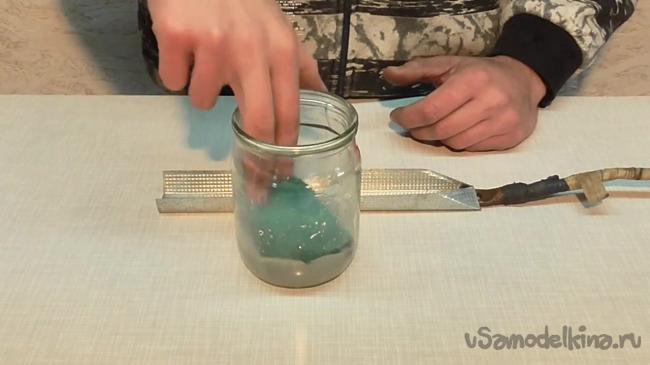
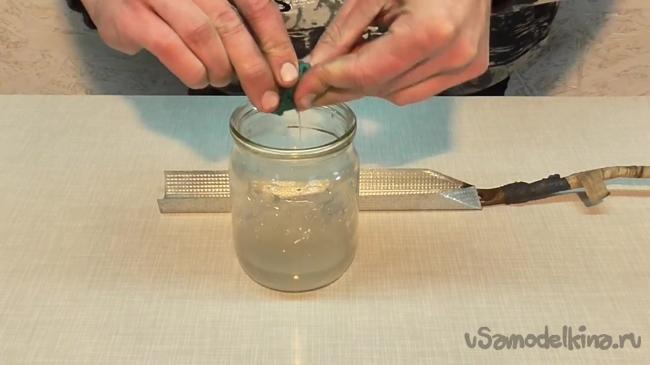
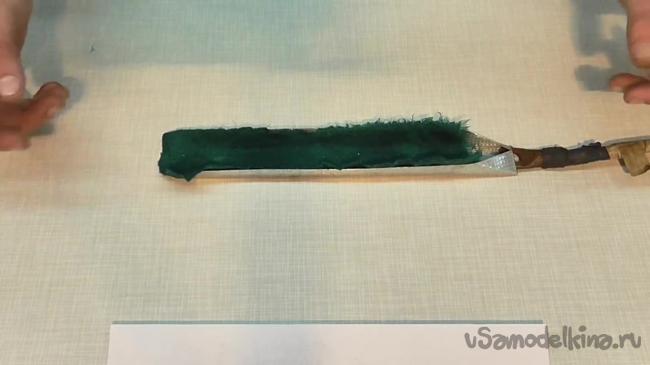
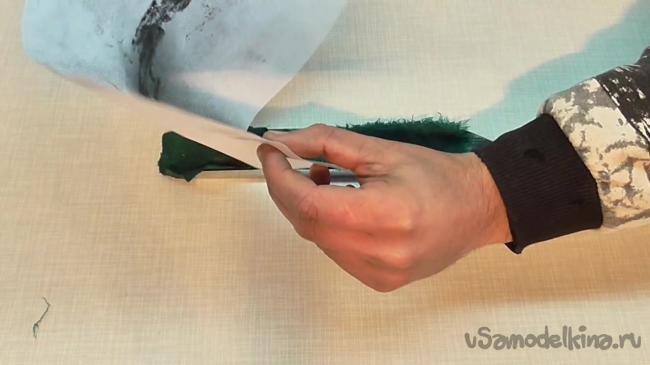
usamodelkina.ru
Химико-термическая обработка стали
Благодаря такой обработке меняется не только структура металла, но и химический состав его верхнего слоя и деталь может иметь вязкую сердцевину, выдерживающую ударные нагрузки, высокую твердость и износность. Из существующих способов химико-термической обработки стали в условиях небольшой мастерской можно выполнять только цементацию. Цементация - это науглероживание поверхности стали. Этому процессу подвергают чаще всего изделия из малоуглеродистых сталей, содержащих не более 0,2% углерода и некоторых легированных сталей. Детали, предназначенные для цементации, сначала очищают. Поверхности не подлежащие науглероживанию, покрывают специальными предохранительными противоцементными обмазками.
1-ый состав простейшей обмазки: огнеупорная глина с добавлением 10% асбестового порошка, вода. Смесь разводят до консистенции густой сметаны и наносят на нужные участки поверхности изделия. После высыхания обмазки можно производить дальнейшую цементацию изделия.
2-ой состав применяемой обмазки: каолин - 25%, тальк - 50%: вода - 25%. Разводят эту смесь жидким стеклом или силикатным клеем.
Цементацию делают после полного высыхания обмазки.
Вещества, которые входят в состав обмазки, называют карбюризаторами. Они бывают твердые, жидкие и газообразные.
В условиях домашней небольшой мастерской удобнее осуществлять цементацию с помощью пасты. Это цементация в твердом карбюризаторе. В состав пасты входят: сажа - 55%, кальцинированная сода - 30%, щавелевокислый натрий - 15%, вода для образования сметанообразной массы. Пасту наносят на нужные участки изделия, дают высохнуть. Затем изделие помещают в печь, выдерживая при температуре 900-920°С в течение 2-2,5 часов. При использовании такой пасты цементация обеспечивает толщину науглероженного слоя 0,7-0,8 мм.
Жидкостная цементация также возможна в небольшой мастерской при наличии печи-ванной, в которой и происходит науглероживание инструментов и других изделий. В состав жидкости входят: сода - 75-85%, 10-15% хлористого натрия, 6-10% карбида кремния. Печь-ванну наполняют этим составом и погружают изделие или инструмент. Процесс протекает при температуре 850-860°С в течение 1,5-2 часов; толщина науглероженного слоя достигает при этом 0,3-0,4 мм.
Газовую цементацию производят в смеси раскаленных газов, содержащих метан, окись углерода в специальных камерах при температуре 900-950°С и только в производственных условиях. После цементации детали охлаждают вместе с печью, затем закаляют при 760-780°С е окончательным охлаждением в масле.
Нагрев заготовки - ответственная операция. От правильности ее проведения зависят качество изделия, производительность труда. Необходимо знать, что в процессе нагрева металл меняет свою структуру, свойства и характеристику поверхностного слоя и в результате от взаимодействия металла с воздухом атмосферы, и на поверхности образуется окалина, толщина слоя окалины зависит от температуры и продолжительности нагрева, химического состава металла. Стали окисляются наиболее интенсивно при нагреве больше 900°С, при нагреве в 1000°С окисляемость увеличивается в 2 раза, а при 1200°С - в 5 раз. Хромоникелевые стали называют жаростойкими потому, что они практически не окисляются. Легированные стали образуют плотный, но не толстый слой окалины, который защищает металл от дальнейшего окисления и не растрескивается при ковке. Углеродистые стали при нагреве теряют углерод с поверхностного слоя в 2-4 мм.
Это грозит металлу уменьшением прочности, твердости стали и ухудшается закаливание. Особенно пагубно обезуглероживание для поковок небольших размеров с последующей закалкой.
Заготовки из углеродистой стали с сечением до 100 мм можно быстро нагревать и потому их кладут холодными, без предварительного прогрева, в печь, где температура 1300°С. Во избежание появлений трещин высоколегированные и высокоуглеродистые стали необходимо нагревать медленно.
При перегреве металл приобретает крупнозернистую структуру и его пластичность снижается. Поэтому необходимо обращаться к диаграмме "железо-углерод", где определены температуры для начала и конца ковки. Однако перегрев заготовки можно при необходимости исправить методом термической обработки, но на это требуется дополнительное время и энергия. Нагрев металла до еще большей температуры приводит к пережогу, от чего происходит нарушение связей между зернами и такой металл полностью разрушается при ковке. Пережог - неисправимый брак. Если заготовку ковать нагрев до температуры ниже Тн, то это приведет к образованию трещин.
При температуре на 20-30°С выше температуры Тк в металле происходит раскристаллизация и структура остается мелкозернистой. На этом этапе надо заканчивать ковку.
При ковке изделий из низкоуглеродистых сталей требуется меньше число нагревов, чем при ковке подобного изделия из высокоуглеродистой или легированной стали.
Итак. При нагреве металла требуется следить за температурой нагрева, временем нагрева и температурой конца нагрева. При увеличении времени нагрева - слой окалины растет, а при интенсивном, быстром нагреве могут появиться трещины. Известно из опыта, что на древесном угле заготовка 10-20 мм в диаметре нагревается до ковочной температуры за 3-4 минуты, а заготовки диаметром 40-50 мм прогревают 15-25 минут, отслеживая цвет каления.
www.kefa.ru
Закалка и науглероживание металлов - Кустарь
Закалка имеет целью придать стали особую твердость, свойственную стали, нагретой выше 700 °C и быстро охлажденной. При операциях закалки большое значение имеет правильный накал металла (отсутствие пережога) и равномерное быстрое охлаждение. При накаливании металла следует избегать излишнего окисления поверхности. Лучше всего накаливаемую сталь покрывать особым составом, который содержит в себе углерод. Углерод этот переходит в сталь (науглероживание) и сообщает ей особую твердость. 1. Ванны для закаливания по Шену. Примененная опытной рукой водяная баня является самым дешевым средством для закаливания металлов. Нужно только позаботиться, чтобы водяная баня была продолжительное время одинаковой температуры, лучше всего 27°. При более теплой воде металл делается ломким, при горячей воде — недостаточно твердым. Выгоднее всего при каждом сорте товара пробным опытом установить верную температуру и уже держаться ее при работе. 2. Особый прием закалки стали. Как известно, стали можно придать путем особой закалки такую твердость, что она будет резать стекло, подобно алмазу. Но не всем известно, что для сообщения стали такой твердости существует простой способ. Шило, лезвие ножа или другой инструмент следует накалить до ярко красного свечения и тотчас же погрузить в обыкновенный сургуч на одну лишь секунду. Операцию погружения в сургуч нужно повторить несколько раз, выбирая каждый раз для погружения свежее место в сургуче до тех пор, пока сталь не остынет и не будет уже более входить в сургуч. Тогда процесс закалки считается законченным. Остается очистить приставшие частицы сургуча. При употреблении закаленного таким способом острия или лезвия из стали, советуется каждый раз смачивать его скипидаром. 3. Составы для науглероживаиия закаливаемой стали. а) Хорошим составом для науглероживания закаливаемой стали может быть следующий: берут 1 толченого стекла, 200 поваренной соли, 8 животного угля, 2 древесного угля, 2,5 ржаной муки, 25 канифоли и 1200 желтой кровяной соли, растирают все составные части в порошок и замешивают в спирте до получения густого теста. Этим составом Покрывают стальные предметы перед закалкой. Особенно пригоден он для инструментов, как напр., напильников и т. п. б) Вместо указанного выше рецепта можно применить следующий. Берут 700 канифоли, 300 железисто- синеродистого калия (желтой кровяной соли), 100 медного купороса и 100 льняного масла. Эти составные части, начиная с канифоли, варятся в горшке при постоянном помешивании (по Бруккерту) до тех пор, пока останется остаток в 1000 (улетучивают таким образом 200). Массу выливают в ящики, где она затвердевает. Чтобы закалить инструмент, его нагревают до вишнево-красного каления и втыкают в массу, которая под влиянием разогретого инструмента становится сразу мягкой. Хорошую сталь еще раз нагревают и погружают затем в холодную воду, отчего сталь становится очень упругой. Сталь худшего качества нужно 2 — 3 раза подряд погружать, каждый раз перед этим накаливая ее, в закаливающуюмассу. 4. Закалка напильников. Напильники обсыпаются смесью из 5 роговой муки, 5 древесного угля в порошке, 2 поваренной соли в порошке и 1 железисто-синеродистого Калия (желтой кровяной соли). Автор: Г. Бродерсен |
www.sdelaysam.info
Сталь - Советы мастеру
Термическая обработка стали. Отжиг — нагревание стального изделия до температуры 700—900°С (в зависимости от марки стали) и охлаждение вместе с печью. Отжиг применяют при изготовлении из одного закаленного изделия другого или в случае неудачной закалки.Если закаливать неотожженные изделия, в них могут возникнуть трещины, структура металла станет неоднородной, что резко ухудшает качество изделия.Мелкие детали отжигают, нагревая их на массивных стальных плитах, которые предварительно раскаляют. После этого детали медленно остывают одновременно с плитой. Иногда изделие нагревают ацетиленовой горелкой, которую потом постепенно удаляют от изделия, делая процесс его охлаждения медленным. Этот метод применяют для отжига небольших стальнУх деталей.Нормализация — нагрев стали до температуры 900°С с последующим охлаждением на воздухе (в нормальных условиях) для улучшения внутренней микроструктуры стали и повышения механических свойств, а также для подготовки ее к последующей термической обработке.Закалка заключается в придании стальному изделию высокой прочности и твердости. Однако при закалке сталь становится более хрупкой. Этот недостаток ликвидируют в процессе отпуска стали.При закалке изделие нагревают до высокой температуры, а затем быстро охлаждают в специальных охлаждающих средах. В зависимости от режима закалки у изделия из одной и той же стали можно получить различные структуры и свойства.Для достижения наилучших результатов стальное изделие нагревают до температуры 750—850°С. Разогрев должен происходить равномерно. Затем разогретое изделие быстро охлаждают до температуры около 400°С. Скорость охлаждения должна быть не меньше 150°С в секунду, то есть охлаждение изделия должно произойти в течение всего 2—3 с. Дальнейшее охлаждение до нормальной температуры может протекать при любой скорости, так как полученная при закалке структура достаточно устойчива и скорость дальнейшего охлаждения на нее не оказывает влияния.В качестве охлаждающих средств чаще всего употребляют воду и трансформаторное масло. Скорость охлаждения в воде больше, чем в масле: при температуре воды 18°С скорость охлаждения достигает 600°С в секунду, а в масле — 150°С. Иногда для повышения закаливающей способности в воду добавляют поваренную соль (до 10 %) или серную кислоту (10—12 %), например, при закалке плашек и метчиков. Более высокий нагрев, чем это необходимо, равно как и чрезмерная скорость охлаждения в холодной воде, приводит к нежелательным результатам — деформации стали и появлению в ней паразитных напряжений.При закалке инструментов из углеродистой стали применяют закалочные печи с температурой нагрева до 900°С, а для нагрева легированных и быстрорежущих сталей — до 1325°С. Печи для закалки бывают следующих видов: камерные, или пламенные, в которых изделия нагревают открытым пламенем; муфельные, нагревающие за счет сопротивления электрических обмоток; печи-ванны, представляющие собой тигли, наполненные расплавами солей, например хлористым барием.Закалочное нагревание в ваннах удобно вследствие того, что температура содержащегося в ней расплава всегда постоянна и закаливаемое изделие не может нагреться выше этой температуры. Кроме того, нагрев в жидкой среде происходит быстрее, чем в воздушной. В небольших мастерских целесообразно использовать для закалочного нагрева муфельные электрические печи, например МП-8. Инструмент или деталь помещают в холодную муфельную печь, потом ее включают и начинают медленно нагревать до требуемой температуры. Поскольку время нагрева продолжительно, внутренние напряжения, возникающие в изделии, минимальны.После закалки изделия производят его отпуск. Он смягчает негативные явления при закалке, повышает вязкость и уменьшает хрупкость изделия. Кроме того, отпуск устраняет большую часть внутренних напряжений, возникших при закалке.Для определения температуры при отпуске изделия пользуются цветами побежалости. Если очищенное от окалины стальное изделие нагреть до 220°С, на нем образуется тонкая пленка окислов железа, придающая изделию различные цвета — от светло-желтого до серого. С повышением температуры или увеличением времени пребывания изделия при данной температуре окисная пленка утолщается и цвет ее изменяется. Цвета побежалости одинаково проявляются как на сырой, так и на закаленной стали. При отпуске закаленных изделий применяют два способа:1. Поверхность закаленного изделия хорошо отшлифовывают мелкой шкуркой и нагревают. По мере того как температура нагрева повышается, на чистой поверхности изделия появляются цвета побежалости. Когда изделие будет нагрето до определенной температуры и появится нужный цвет, его быстро охлаждают в воде2. При закалке многих инструментов, например чеканов, штихелей, резцов, молотков и т. п., требуется, чтобы закаленной была только рабочая часть, а сам инструмент оставался бы незакаленным, сырым. В этом случае закалку производят так: инструмент нагревают немного выше режущего (рабочего) конца до требуемой температуры, после чего опускают в воду только рабочую часть, а металл выше рабочей части остается горячим. Вынув инструмент из воды, быстро зачищают его рабочую часть (наждачной шкуркой или трением о землю). Тепло, оставшееся в неохлажденной части, поднимет температуру охлажденного конца, и после появления на нем нужного цвета побежалости инструмент окончательно охлаждают.Образование на поверхности изделия окалины приводит к угару металла, деформации, уменьшению теплопроводности, что понижает скорость нагрева изделия в печи. Кроме того, возрастает твердость и затрудняется механическая обработка. Окалину удаляют с изделий либо механическим способом, либо травлением.Обезуглероживание стали заключается в выгорании углерода с поверхности изделия. Обезуглероженный слой обладает пониженными прочностными характеристиками. Интенсивность, с которой происходит окисление и обезуглероживание, зависит от состава атмосферы печи и температуры нагрева. Чем выше нагрев, тем процессы идут быстрее Чтобы избежать образования окалины при нагреве, под закалку иногда применяют пасту, состоящую из жидкого стекла — 100 г, огнеупорной глины — 75 г, графита — 25 г, буры — 14 г, карборунда — 30 г, воды — 200 г.Пасту наносят на изделие и дают ей просохнуть, затем изделие нагревают обычным способом. После закалки его промывают в горячем содовом растворе. Для предупреждения образования окалины на инструментах из быстрорежущей стали часто применяют покрытие бурой. Для этого инструмент, нагретый до 850°С, погружают в насыщенный водный раствор или порошок буры.Теперь рассмотрим особенности закаливания некоторых стальных изделий. Углеродистые стали при закалке лучше охлаждать сначала в воде до температуры 400—350°С, а потом в масле. Это предотвращает возникновение внутренних напряжений. Во время охлаждения изделие рекомендуется быстро перемещать сверху вниз.Тонкостенные длинные детали (например, ножи) при охлаждении опускают в воду или масло строго вертикально, в противном случае они могут сильно деформироваться.Зубила целесообразно закаливать в мокром песке, который увлажняют раствором соли.Тонкие сверла закаливают в сургуче. Для этого разогретый до светло-красного цвета конец сверла погружают в сургуч и оставляют там до полного охлаждения.
sovmasteru.ru
Науглероживатель: производство, особенности, применение
В процессе выплавки чугунов и сталей углерод вводят в расплав или подают на зеркало металла в момент его разлива. Для этого используют специальные углеродсодержащие материалы, которые называют науглероживателями (или карбюризаторами). Науглероживатель придает сплавам железа дополнительную прочность, твёрдость, снижает их вязкость и пластичность, а также предупреждает окисление отливок во время охлаждения.
В качестве карбюризаторов активно применяется искусственный измельченный графит разных марок.
Производство науглероживателя
Технология получения основывается на глубокой термообработке исходного материала, в результате которой он приобретает совершенную (или приближенную к совершенной) кристаллическую решетку с упорядоченно расположенными атомами. Процесс протекает при высоких температурах (2400-2600 °С) в промышленных условиях без доступа воздуха.
Сырьем для производства служат:
Для карбюризаторов характерно особо низкое содержание азота, т.к. при массовой доле выше 0,009% он формирует структурные дефекты — газовые поры или трещины.
Особенности выбора
Основные показатели, определяющие целесообразность использования материала той или иной марки, следующие:
Материалы, имеющие природное происхождение, отличаются повышенной зольностью (по сравнению с искусственными).
Область применения
Карбюризаторы предназначены для получения стали и чугуна определенного химического состава с заданными свойствами. Основные преимущества использования для их производства искусственного измельченного графита:
Помимо обогащения сталей, науглероживатели широко применяются для вспенивания шлаков, при изготовлении углеграфитовых продуктов и материалов, а также служат наполнителями для графитопластов.
doncarb.com