- спокойных, которые получаются, если в ковше и печи процесс раскисления полностью завершен;
- полуспокойных, которые по степени раскисления находятся между спокойными и кипящими сталями; именно такие стали раскисляются и в ковше, и в изложнице, где в них продолжается взаимодействие углерода и оксида железа.
- системы обеспечения аргоном;
- сосуды конверторов и их несущие кольца;
- оборудование для фильтрации пыли;
- система для удаления конверторного газа.
- печи индукционного типа;
- дуговые печи;
- емкости, с помощью которых выполняется загрузка;
- участок складирования металлического лома;
- преобразователи, предназначенные для обеспечения индукционного нагревания.
- очищение стали от серы;
- электрошлаковый переплав;
- создание вакуумной среды.
- LF-оборудование;
- SL-оборудование.
- крышки ковшей;
- ковши литейного и разливочного типа;
- шиберные затворы.
- поворотная станина для манипуляций с разливочными ковшами;
- оборудование для осуществления непрерывной разливки;
- вагонетки, на которых транспортируются промежуточные ковши;
- лотки и сосуды, предназначенные для аварийных ситуаций;
- промежуточные ковши и площадки для складирования;
- пробочный механизм;
- мобильные мешалки для чугуна;
- оборудование для обеспечения охлаждения;
- участки, на которых выполняется непрерывная разливка;
- внутренние транспортные средства рельсового типа.
- Расплавление породы. Сырье, которое используется для производства металла, называют шихтой. На данном этапе при окислении железа происходит раскисление и примесей. Уделяется много внимания тому, чтобы происходило уменьшение концентрации вредных примесей, к которым можно отнести фосфор. Для обеспечения наиболее подходящих условий для окисления вредных примесей изначально выдерживается относительно невысокая температура. Формирование железного шлака происходит за счет добавления железной руды. После выделения вредных примесей на поверхности сплава они удаляются, проводится добавление новой порции оксида кальция.
- Кипение полученной массы. Ванны расплавленного металла после предварительного этапа очистки состава нагреваются до высокой температуры, сплав начинает кипеть. За счет кипения углерод, находящийся в составе, начинает активно окисляться. Как ранее было отмечено, чугун отличается от стали слишком высокой концентрацией углерода, за счет чего материал становится хрупким и приобретает другие свойства. Решить подобную проблему можно путем вдувания чистого кислорода, за счет чего процесс окисления будет проходить с большой скоростью. При кипении образуются пузырьки оксида углерода, к которым также прилипают другие примеси, за счет чего происходит очистка состава. На данной стадии производства с состава удаляется сера, относящаяся к вредным примесям.
- Раскисление состава. С одной стороны, добавление в состав кислорода обеспечивает удаление вредных примесей, с другой, приводит к ухудшению основных эксплуатационных качеств. Именно поэтому зачастую для очистки состава от вредных примесей проводится диффузионное раскисление, которое основано на введении специального расплавленного металла. В этом материале содержатся вещества, которые оказывают примерно такое же воздействие на расплавленный сплав, как и кислород.
- Спокойные, которые прошли процесс раскисления до конца.
- Полуспокойные, которые имеют состояние, находящееся между спокойными и кипящими сталями.
- Мартеновский метод. Данная технология предусматривает применение специальных печей, которые способны нагревать сырье для температуры около 2000 градусов Цельсия. Рассматривая способы производства легированных сталей, отметим, что этот метод также позволяет проводить добавление различных примесей, за счет чего получаются необычные по составу стали. Мартеновский метод основан на применении специальных печей.
- Электросталеплавильный метод. Для того чтобы получить материал высокого качества проводится производство стали в электропечах. За счет применения электрической энергии для нагрева сырья можно точно контролировать прохождение процесса окисления и выделения шлаков. В данном случае важно обеспечить появление шлаков. Они являются передатчиком кислорода и тепла. Данная технология позволяет снизить концентрацию вредных веществ, к примеру, фосфора и серы. Электрическая плавка может проходить в самой различной среде: избыточного давления, вакуума, при определенной атмосфере. Проводимые исследования указывают на то, что электросталь обладает самым высоким качеством. Применяется технология для производства качественных высоколегированных, коррозионностойких, жаропрочных и других видов стали. Для преобразования электрической энергии в тепловую применяется дуговая печь цилиндрической формы с днищем сферического типа. Для обеспечения наиболее благоприятных условий плавки внутреннее пространство отделывается при использовании жаропрочного металла. Работа устройства возможна только при подключении к трехфазной сети. Стоит учитывать, что сеть электрического снабжения должна выдерживать существенную нагрузку. Источником тепловой энергии становится электрическая дуга, возникающая между электродом и расплавленным металлом. Температура может быть более 2000 градусов Цельсия.
- Кислородно-конверторный. Непрерывная разливка стали в данном случае сопровождается с активным вдуванием кислорода, за счет чего существенно ускоряется процесс окисления. Применяется этот метод изготовления и для получения чугуна. Считается, что данная технология обладает наибольшей универсальностью, позволяет получать металлы с различными свойствами.
- Мартеновские печи оборудованы системой, которая обеспечивает подачу тепла и отвода продуктов горения.
- Топливо подается в камеру сгорания поочередно, то с правой, то с левой стороны. За счет этого обеспечивается образование факела, который и приводит к повышению температуры рабочей среды и ее выдерживание на протяжении длительного периода.
- На момент загрузки шихты в камеру сгорания попадает достаточно большое количество кислорода, который и необходим для окисления железа.
- Конвертор – специальное оборудование, которое представлено стальным сосудом грушевидной формы. Вместительность подобного устройства составляет 100-350 тонн. С внутренней стороны конструкция выкладывается огнеупорным кирпичом.
- Конструкция верхней части предполагает горловину, которая необходима для загрузки шихты и жидкого чугуна. Кроме этого, через горловину происходит удаление газов, образующихся в процессе плавления сырья.
- Заливка чугуна и добавление другой шихты проводится при температуре около 1400 градусов Цельсия. Для того чтобы обеспечить активное окисление железа чистый кислород подается под давлением около 1,4 МПа.
- При подаче большого количества кислорода чугун и другая шихта окисляется, что становится причиной выделения большого количества тепла. За счет сильного нагрева происходит расплавка всего шихтового материала.
- В тот момент, когда из состава удаляется излишек углерода, продувка прекращается, фурма извлекается из конвертора. Как правило, продувка продолжается в течение 20 минут.
- На данном этапе полученный состав содержит большое количество кислорода. Именно поэтому для повышения эксплуатационных качеств в состав добавляют различные раскислители и легирующие элементы. Образующийся шлак удаляется в специальный шлаковый ковш.
- Время конверторного плавления может меняться, как правило, оно составляет 35-60 минут. Время выдержки зависит от типа применяемой шихты и объема получаемой стали.
- диффузионное;
- осаждающее.
- спокойную сталь полного раскисления;
- кипящую раскисленную не полностью сталь, когда процесс выведения пузырьков угарного газа СО продолжается в ковше и изложнице.
- применением дополнительного тепла регенераторов, получаемого сжиганием коксовального или доменного газа в струе горячего воздуха;
- отражения от свода закачиваемого газа в результате сгорание топлива в нем происходит над ванной с металлом, что способствует быстрому нагреву содержимого;
- применением реверсирования нагревающего потока.
- рабочего пространства с огнеупорной футеровкой стенок и завалочными окнами;
- подины (основания) из магнезитового кирпича;
- свода печи;
- головки печи;
- шлаковика для выведения пыли;
- регенератора с перекидными клапанами.
- молибден;
- вольфрам;
- ванадий.
- жидкой стали из конвертеров;
- скрапа;
- железной руды.
- углеродистую;
- легированную.
- низколегированная не более 2,5%;
- среднелегированная в диапазоне 2,5–10%;
- высоколегированная свыше 10%.
- Окрашенный стальной лист
- Скорость резания для стали 20
- Флюс для сварки стали
- Немагнитная сталь нержавеющая
- Какой из признаков может характеризовать кипящую сталь
- Сталистая проволока 5 мм
- Малоуглеродистые стали
- Покраска стали рулонной
- Цвет сталь нержавеющая
- Тонкостенные трубы из нержавеющей стали
- Способы закалки стали
Способ производства изделия из стали. Что изготавливают из стали
Производство стали – технология, оборудование, этапы
Производство стали сегодня осуществляется в основном из отработанных стальных изделий и передельного чугуна. Сталь представляет собой сплав железа и углерода, последнего в котором содержится от 0,1 до 2,14%. Превышение содержания углерода в сплаве приведет к тому, что он станет слишком хрупким. Суть процесса производства стали, в составе которой содержится гораздо меньшее количество углерода и примесей, по сравнению с чугуном, состоит в том, чтобы в процессе плавки перевести эти примеси в шлак и газы, подвергнуть их принудительному окислению.
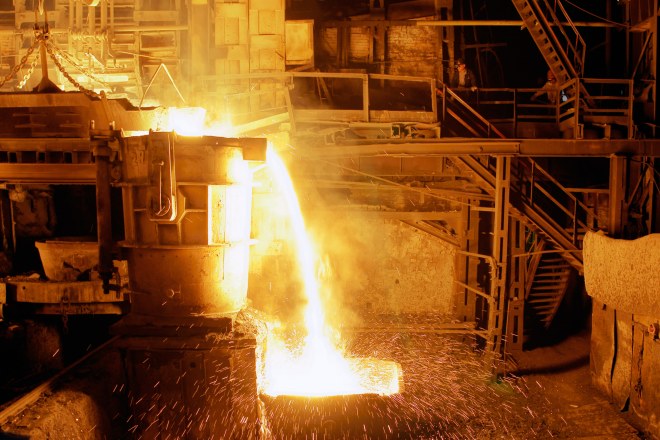
Процесс производства стали
Особенности процесса
Производство стали, осуществляемое в сталеплавильных печах, предполагает взаимодействие железа с кислородом, в процессе которого металл окисляется. Окислению также подвергаются углерод, фосфор, кремний и марганец, содержащиеся в передельном чугуне. Окисление данных примесей происходит за счет того, что оксид железа, образующийся в расплавленной ванне металла, отдает кислород более активным примесям, тем самым окисляя их.
Производство стали предполагает прохождение трех стадий, каждая из которых имеет свое значение. Рассмотрим их подробнее.
Расплавление породы
На данном этапе расплавляется шихта и формируется ванна из расплавленного металла, в которой железо, окисляясь, окисляет примеси, содержащиеся в чугуне (фосфор, кремний, марганец). В процессе этого этапа производства из сплава необходимо удалить фосфор, что достигается за счет содержания в шлаке расплавленного оксида кальция. При соблюдении таких условий производства фосфорный ангидрид (Р2О5) создает с оксидом железа (FeO) неустойчивое соединение, которое при взаимодействии с более сильным основанием — оксидом кальция (CaO) — распадается, и фосфорный ангидрид превращается в шлак.
Чтобы производство стали сопровождалось удалением из ванны расплавленного металла фосфора, необходима не слишком высокая температура и содержание в шлаке оксида железа. Чтобы удовлетворить эти требования, в расплав добавляют окалину и железную руду, которые и формируют в ванне расплавленного металла железистый шлак. Содержащий высокое количество фосфора шлак, формирующийся на поверхности ванны расплавленного металла, удаляется, а вместо него в расплав добавляются новые порции оксида кальция.
Кипение ванны расплавленного металла
Дальнейший процесс производства стали сопровождается кипением ванны расплавленного металла. Такой процесс активизируется с повышением температуры. Он сопровождается интенсивным окислением углерода, происходящим при поглощении тепла.

Процесс производства стали в электропечах
Производство стали невозможно без окисления излишков углерода, такой процесс запускают при помощи добавления в ванну расплавленного металла окалины или вдувания в нее чистого кислорода. Углерод, взаимодействуя с оксидом железа, выделяет пузырьки оксида углерода, что создает эффект кипения ванны, в процессе которого в ней снижается количество углерода, а температура стабилизируется. Кроме того, к всплывающим пузырькам оксида углерода прилипают неметаллические примеси, что способствует уменьшению их количества в расплавленном металле и приводит к значительному улучшению его качества.
На данной стадии производства из сплава также удаляется сера, присутствующая в нем в форме сульфида железа (FeS). При повышении температуры шлака сульфид железа растворяется в нем и вступает в реакцию с оксидом кальция (CaO). В результате такого взаимодействия образовывается соединение CaS, которое растворяется в шлаке, но раствориться в железе не может.
Раскисление металла
Добавление в расплавленный металл кислорода способствует не только удалению из него вредных примесей, но и увеличению содержания данного элемента в стали, что приводит к ухудшению ее качественных характеристик.
Чтобы уменьшить количество кислорода в сплаве, выплавка стали предполагает осуществление процесса раскисления, который может выполняться диффузионным и осаждающим методом.Диффузионное раскисление предполагает введение в шлак расплавленного металла ферросилиция, ферромарганца и алюминия. Такие добавки, восстанавливая оксид железа, снижают его количество в шлаке. В результате растворенный в сплаве оксид железа переходит в шлак, распадается в нем, высвобождая железо, которое возвращается в расплав, а высвобожденные оксиды остаются в шлаке.
Производство стали с осаждающим раскислением осуществляется путем введения в расплав ферросилиция, ферромарганца и алюминия. Благодаря наличию в своем составе веществ, обладающих большим сродством к кислороду, чем железо, такие элементы образуют соединения с кислородом, который, отличаясь невысокой плотностью, выводится в шлак.
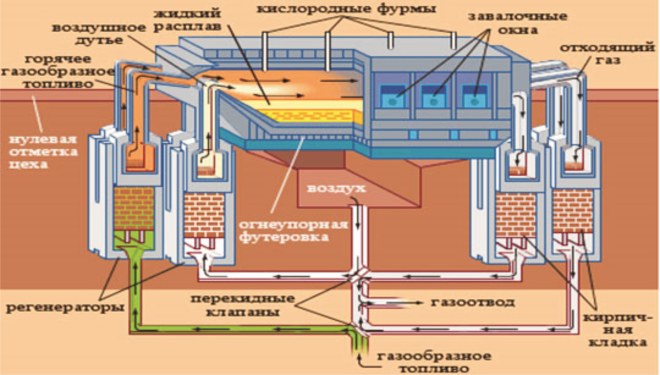
Производство стали в мартеновских печах
Регулируя уровень раскисления, можно получать кипящую сталь, которая не полностью раскислена в процессе плавки. Окончательное раскисление такой стали происходит при затвердевании слитка в изложнице, где в кристаллизующемся металле продолжается взаимодействие углерода и оксида железа. Оксид углерода, который образуется в результате такого взаимодействия, выводится из стали в виде пузырьков, также содержащих азот и водород. Полученная таким образом кипящая сталь, содержит незначительное количество металлических включений, что придает ей высокую пластичность.
Производство сталей может быть направлено на получение материалов следующего типа:
Если производство стали предполагает введение в расплав чистых металлов или ферросплавов, то в результате получаются легированные сплавы железа с углеродом. Если в стали данной категории необходимо добавить элементы, которые имеют меньшее сродство к кислороду, чем железо (кобальт, никель, медь, молибден), то их вводят в процессе плавки, не опасаясь за то, что они окислятся. Если же легирующие элементы, которые необходимо добавить в сталь, имеют большее сродство к кислороду, чем железо (марганец, кремний, хром, алюминий, титан, ванадий), то их вводят в металл уже после его полного раскисления (на окончательном этапе плавки или в ковш).
Необходимое оборудование
Технология производства стали предполагает использование на сталелитейных заводах следующего оборудования.
Участок кислородных конверторов:
Участок электропечей:
Участок вторичной металлургии, на котором осуществляется:

Кипящая сталь
Участок для реализации ковшовой технологии:
Ковшовое хозяйство, обеспечивающее производство стали, также включает в себя:
Производство стали также предполагает наличие оборудования для непрерывной разливки стали. К такому оборудованию относится:
Оценка статьи:

Поделиться с друзьями:
met-all.org
Производство стали: технология, способы, процесс
Сталь является одним из самых распространенных материалов на сегодняшний день. Она представляет собой сочетание железа и углерода в определенном процентном соотношении. Существует огромное количество разновидностей этого материала, так как даже незначительное изменение химического состава приводит к изменению физико-механических качеств. Сырье для производства стали сегодня представлено отработанными стальными изделиями. Также было налажено производство конструкционной стали из чугуна. Страны-лидеры в металлургической промышленности проводят выпуск заготовок согласно стандартам, установленным в ГОСТ. Рассмотрим особенности производства стали, а также применяемые методы и то, как проводится маркировка полученных изделий.
Особенности процесса производства стали
В производстве чугуна и стали применяются разные технологии, несмотря на достаточно близкий химический состав и некоторые физико-механические свойства. Отличия заключаются в том, что сталь содержит меньшее количество вредных примесей и углерода, за счет чего достигаются высокие эксплуатационные качества. В процессе плавки все примеси и лишний углерод, который становится причиной повышения хрупкости материала, уходят в шлаки. Технология производства стали предусматривает принудительное окисление основных элементов за счет взаимодействия железа с кислородом.

Выплавка стали в электропечи
Рассматривая процесс производства углеродистой и других видов стали, следует выделить несколько основных этапов процесса:
Кроме этого, в зависимости от особенностей применяемой технологии могут быть получены материалы двух типов:
При производстве материала в состав могут добавляться чистые металлы и ферросплавы. За счет этого получаются легированные составы, которые обладают своими определенными свойствами.
Способы производства стали
Существует несколько методов производства стали, каждый обладает своими определенными достоинствами и недостатками. От выбранного способа зависит то, с какими свойствами можно получить материал. Основные способы производства стали:
Способы производства оцинкованной стали не сильно отличаются от рассматриваемых. Это связано с тем, что изменение качеств поверхностного слоя проходит путем химико-термической обработки.
Существуют и другие технологии производства стали, которые обладают высокой эффективностью. Например, методы, основанные на применении вакуумных индукционных печей, а также плазменно-дуговой сварки.
Мартеновский способ
Суть данной технологии заключается в переработке чугуна и другого металлолома при применении отражательной печи. Производство различной стали в мартеновских печах можно охарактеризовать тем, что на шихту оказывается большая температура. Для подачи высокой температуры проводится сжигание различного топлива.

Схема мартеновской печи
Рассматривая мартеновский способ производства стали, отметим нижеприведенные моменты:
При получении стали мартеновским способом время выдержки шихты составляет 8-16 часов. На протяжении всего периода печь работает непрерывно. С каждым годом конструкция печи совершенствуется, что позволяет упростить процесс производства стали и получить металлы различного качества.
В кислородных конвертерах
Сегодня проводится производство различной стали в кислородных конвертерах. Данная технология предусматривает продувку жидкого чугуна в конвертере. Для этого проводится подача чистого кислорода. К особенностям этой технологии можно отнести нижеприведенные моменты:

Кислородно-конверторный способ
Стоит учитывать, что производительно подобного оборудования составляет порядка 1,5 миллионов тонн при вместительности 250 тонн. Применяется данная технология для получения углеродистых, низкоуглеродистых, а также легированных сталей. Кислородно-конвертерный способ производства стали был разработан довольно давно, но сегодня все равно пользуется большой популярностью. Это связано с тем, что при применении этой технологии можно получить качественные металлы, а производительность технологии весьма высока.
В заключение отметим, что в домашних условиях провести производство стали практически невозможно. Это связано с необходимостью нагрева шихты до достаточно высокой температуры. При этом процесс окисления железа весьма сложен, как и удаления вредных примесей
Если вы нашли ошибку, пожалуйста, выделите фрагмент текста и нажмите Ctrl+Enter.
stankiexpert.ru
05 Производство стали
Производство стали
Сталью называют железоуглеродистые сплавы, с содержанием углерода до 2 %.При производстве стали происходит снижение содержания углерода и примесей, присутствующих в чугуне (Mn, Si, S, Р и др.), за счет окисления кислородом воздуха и кислородом, содержащимся в руде. Снижению содержания углерода и примесей способствует закись железа FeO, которая образуется в начале плавки 2Fe+O2= 2FeO и далее C+FeO = CO+Fe. Так как излишняя закись железа вызывает хрупкость стали, производят раскисление жидкой стали путем введения ферросплавов (ферромарганца, ферросилиция, ферроалюминия) по следующим схемам:
Mn + FeO->MnO + Fe; Si + 2FeO->SiO2+2Fe; 2А1 + 3FeO->Al2O3+3Fe.
Образовавшиеся оксиды всплывают и удаляются вместе со шлаком.
В зависимости от степени законченности раскисления различают спокойную сталь (си), т.е. наиболее раскисленную. Такая сталь в слитке имеет плотное и однородное строение, более качественная и дорогая; кипящую сталь (кп), в которой процесс раскисления прошел не до конца, в ней имеются пузырьки газа СО, которые остаются в прокате. Кипящая сталь сваривается, удовлетворительно обрабатывается, но при температуре 10 °С проявляет хрупкость. Кипящая сталь дешевле спокойной. Полуспокойная сталь (пс) по свойствам занимает промежуточное положение между (сп) и (кп).
Выплавку стали осуществляют в мартеновских печах, в конвертерах и электропечах.
Мартеновский способ
Схема работы мартена A. Вдувание газо-воздушной смеси B. Теплообменник (нагрев) C. Жидкий чугун D. Горн E. Теплообменник (охлаждение) F. Выхлоп сгоревших газов
В процессе производства стали мартеновским способом, участвует специальная отражательная печь. Для того чтобы нагреть сталь до нужной температуры (2000 градусов), в печь вводят дополнительное тепло с помощью регенераторов. Это тепло получают за счет сжигания топлива в струе нагретого воздуха. Топливом служит газ (смесь доменного, коксовального и генераторного). Обязательное условие топливо должно полностью сгорать в рабочем пространстве. Особенностью мартеновского способа производства стали является то, что количество кислорода, подаваемого в печь, превышает необходимый уровень. Это позволяет создать воздействие на металл окислительной атмосферы. Сырье (чугун, железный и стальной лом) погружается в печь, где подвергается плавлению в течение 4 …6 или 8... 12 часов. Производительность печи за одну плавку до 900 т. В процессе плавления есть возможность проверять качество металла, путем взятия пробы. В мартеновской печи возможно получать специальные сорта стали. Для этого в сырье вводят необходимые примеси.
В мартеновских печах (9.3) помимо чугуна может быть произведена переплавка металлического лома, руды и флюса. В мартеновских печах (9.3) может быть произведена переплавка металлического лома (до 60...70%), возможны автоматизация процесса плавки, повышенная точность химического состава стали. Недостатки плавки стали в мартеновских печах: периодичность процесса плавки, сложность оборудования, более высокая стоимость выплавляемой стали. Для интенсификации производства стали в мартеновских печах широко применяют кислород, что обеспечивает повышение производительности печей на 25...30 % Большую экономию топлива дает использование теплоты остывающих мартеновских печей, для чего используют принцип работы двухванных печей, при котором теплота от одной остывающей ванны направляется в соседнюю, а затем происходит изменение направления потока, теплоты.
Мартеновский способ производства стали, наиболее распространенный (90%), состоит в получении стали в мартеновской печи путем переплавки чугуна и лома металлов. При нагревании от газа, сгорающего в печи, происходит выгорание кремния, марганца и углерода. Процесс продолжается несколько часов, что дает возможность лаборатории определять химический состав выплавляемой стали в различные периоды плавки и получать сталь любого качества. Емкость мартеновских печей достигает 500т.
Конверторный способ получения стали.
Конвертерный способ производства стали заключается в продувке расплавленного чугуна воздухом под давлением. Процесс продувки длится 16–20 мин.
Позволяет использовать в качестве шихты жидкий чугун, до 50 %' металлического лома, руду, флюс. Сжатый воздух под давлением (0,3...0,35 МПа) поступает через специальные отверстия. Теплота, необходимая для нагрева стали, получается за счет химических реакций окисления углерода и примесей, находящихся в чугуне. Далее при разливке осуществляется так называемое раскисление металла.
Производство стали в конверторах постепенно вытесняет ее в мартеновских печах. Емкость современных конверторов достигает 600 т. Наибольшее развитие получает кислородно-конверторное производство стали, так как дополнительное использование кислорода обеспечивает резкое повышение производительности (на 40 % выше). Недостатки способа: повышенный расход огнеупоров и высокий угар металлов.
Мартеновская сталь лучщё и чище конвертерной. Конвертерная сталь содержит больше серы и фосфора, насыщена азотом и кислородом, содержит пузырьки воздуха, ухудшающие ее качество. Конвертерная сталь применяется для неответственных не сварных конструкций.
Кислородно-конвертерный способ
Первое использование кислородно-конвертерного способа приходится на пятидесятые годы двадцатого столетия. В процессе производства стали, чугун продувают в конвертере чистым кислородом. При этом, процесс происходит без затраты топлива. Для того, чтобы переработать 1 тонну чугуна в сталь требуется около 350 кубометров кислорода. Стоит отметить, что кислородно-конвертерный способ получения стали является наиболее актуальным на сегодняшний день. При этом, процесс не ограничивается на одном способе вдувания кислорода. Различают кислородно-конвертерный процесс с комбинированной, верхней и нижней поддувкой. Конвертерный способ производства стали с комбинированной поддувкой является наиболее универсальным.
Электросталеплавильный способ
В результате электросталеплавильного способа, получают специальные и высококачественные стали. Сталь выплавляют в дуговых или индукционных электропечах. Наиболее распространены дуговые электропечи емкостью до 270 т. При электроплавке стали используют как стальной скрап и железную руду, так и жидкие стали, поступающие из мартеновской печи или конвертера. Основной принцип электросталеплавильного способа производства стали использование электроэнергии для нагрева металла. Механизм производства следующий: в результате прохождения тока через нагревательный элемент выделяется тепло, за счет преобразования электроэнергии в тепловую энергию. Важно отметить, что процесс выплавки связан с применением шлаков. Качество получаемой стали во многом зависит от количества и состава шлаков. Основной причиной образования шлаков, в процессе производства стали, является окисление шихты и примесей.
Благодаря шлакам, происходит связывание оксидов, которые образуются в процессе окисления чугуна, а так же удаление ненужных примесей. Кроме этого, шлаки являются передатчиками тепла и кислорода. Определенное соотношение количества шлаков выводит из стали ненужные вредные примеси, например, фосфор, серу.
Кроме вышеперечисленных способов производства стали, известны и такие способы, как производство стали в вакуумных индукционных печах, плазменно-дуговой переплав.
Давайте подробнее остановимся на способе производства особо чистой стали, а так же жаропрочных сплавов. Суть способа состоит в выплавке в вакуумных печах. После мартеновской выплавки, сталь дополнительно переплавляют в вакууме, что дает возможность получения качественной однородной стали. Такая сталь применяется, в основном, в авиакосмической промышленности, атомной энергетике и других важных отраслях.
Выбор способа всегда зависит от поставленных задач, удобства применения оборудования, необходимого качества полученной стали и от других факторов. Естественно, что каждый способ имеет свои преимущества и свои недостатки.
Производство стали в дуговых электрических печах обладает рядом преимуществ перед конвертерным и мартеновским способами, так как достигаемая в этих печах высокая температура позволяет выплавлять легированные стали, которые содержат тугоплавкие элементы,– вольфрам, ванадий и молибден. При электроплавке почти полностью удаляются из металла сера и фосфор, являющиеся вредными примесями.
Процесс получения доменного чугуна из руд и последующая переработка его в сталь связаны со значительными затратами топлива, флюсов, электроэнергии и др. Поэтому наряду с производством чугуна в доменных печах все шире используют более экономичные процессы прямого восстановления железа из руд. Один из таких процессов осуществлен на Оскольском электрометаллургическом комбинате. Изготовленные из обогащенной железной руды окатыши загружают в шахтную печь. Восстановление железа из окатышей производится водородом и оксидом углерода, получаемых из смеси природного и доменного газов. В восстановительной зоне печи создается температура 1000...1100°С, при которой водород и оксид углерода восстанавливают железную руду в окатышах до твердого губчатого железа. В результате получаются металлизованные окатыши с содержанием железа 90...95%. Охлажденные окатыши поступают на выплавку высококачественных сталей в электропечах.
Сталь отличается от чугуна меньшим содержанием углерода (до 2%) и постоянных примесей кремния, марганца, серы и фосфора.
По содержанию углерода различают сталь низкоуглеродистую – менее 0,3% С, углеродистую – от 0,3 до 0,65% С и высокоуглеродистую – от 0,65 до 1,5% С. В строительствепреимущественно применяют низкоуглеродистые и углеродистые стали.
Чтобы повысить механические свойства сталей и чугунов, к ним добавляют различные легирующие (улучшающие их свойства) вещества – кремний, марганец, хром, никель, молибден, алюминий, медь.
Легированные стали принято делить на низколегированные – с суммарным содержанием легирующих элементов не более 4%, среднелегированные – от 4–5 до 8–10% и высоколегированные – более 10%. В строительствепреимущественно применяют низколегированные стали. Введение соответствующих легирующих веществ повышает коррозийную стойкость, прочность, ковкость, упругость.
Сталь хорошо обрабатывается давлением, имеет более высокую механическую прочность и пластичность, чем чугун. Основным сырьем для получения стали, как уже говорилось, служит передельный чугун и стальной лом. Процесс переработки чугуна в сталь заключается в уменьшении содержания примесей в нем путем их окисления.
Конвертерный способ производства стали заключается в продувке расплавленного чугуна воздухом под давлением. Процесс продувки длится 16–20 мин.
Примеси, входящие в определенных количествах в состав стали, различным образом влияют на ее качества.
Углерод основной элемент, влияющий на свойства стали. С увеличением в стали содержания углерода возрастает ее прочность, но снижается пластичность и ухудшается свариваемость. Обычное содержание углерода в строительных сталях, предназначенных для изготовления стальных конструкций, должно быть не более 0,22%. Марганец является полезной примесью и имеется во всех сортах стали. Он ослабляет вредное влияние серы и повышает прочность стали. Содержание марганца в строительной стали составляет около 0,41–0,65%.
Кремний, как и марганец, повышает прочность стали, но ухудшает ее свариваемость. Содержание кремния в строительных сталях составляет не более 0,3%.
Сера является вредной примесью. Содержание серы в стали, применяемой для изготовления стальных конструкций, не должно превышать 0,055%.
Фосфор также является вредной примесью; его содержание не должно превышать 0,05%.
Металлургическая промышленность выпускает различные по качеству и назначению стали. Это объясняется тем, что элементы стальных конструкций воспринимают разнообразные по действию нагрузки: балки – изгиб, колонны – сжатие, некоторые части ферм и арматура в железобетоне – растяжение, подкрановые пути – удар, а изготовление стали, одинаково хорошо воспринимающей все виды нагрузок, связано с большими затратами.
5
studfiles.net
Производство стали: способы, технология и сырье
Сталь – это прочный материал и основной конструкционный материал для машиностроения. Он представляет сплав железа с углеродом, содержание которого в структуре составляет 0,01–2,14%. В состав также входят в незначительных количествах кремний, марганец и сера. Этот материал обладает исключительными механическими свойствами: твердостью и ковкостью, благодаря им он считается основным конструкционным материалом в машиностроении. Трудно представить, что могло бы заменить материал. Но активное развитие производство стали и других металлов. Из стали изготавливаются самые разнообразные изделия – от канцелярских скрепок до станин многотонных прессов и обшивки корпусов морских судов.
Процесс производства
Производится сталь плавкой. Исходным сырьем служат чугун, лом самой стали или чугуна, окатыши, флюсы и ферросплавы.
Сам чугун по природе – недостаточно твердый и хрупкий материал, поэтому имеет ограниченное применение.
Однако, он незаменим в качестве сырья для получения стали. Суть плавки состоит, в случае применения передельного чугуна, в снижении процентного содержания углерода в нем до требуемого уровня.
Выводятся не предусмотренные в конечной рецептуре примеси. Традиционный состав шихты представляет 55% чугуна и 45% стального лома (скрапа). Существует также рудный процесс, когда к компонентам добавляется рудный материал или скрап-процесс для переработки отходов машиностроительного производства.
Чтобы в процессе плавки примеси и углерод легче выводился из состава компонентов, они переводятся в газы и шлак. В первую очередь при взаимодействии чугуна с кислородом железо окисляется, образуя закись железа FeO.
Одновременно окисляются C, Si, Mn и P, при этом происходит отдача кислорода оксидом железа химически активным примесям. К массе шихты добавляют флюс для лучшего растворения металла: известняк или известь, боксит. В качестве топлива используют каменноугольную пыль, жидкий мазут, природный или коксовый газ.
Особенности процесса
Процесс производства стали происходит последовательно в три этапа.
Первый этап – расплавление породы. На этапе его проведения формируется расплав в ванне и окисляется металл, отдавая одновременно кислород кремнию, фосфору и марганцу.
Одна и главных задач этого этапа – удаление фосфора. Для ее осуществления требуется сравнительно невысокая температура и присутствие в достаточном количестве FeO. При взаимодействии ингредиентов фосфорный ангидрид образует с оксидом железа нестойкое соединение (FeO)3 + P2O5.
Присутствие в шлаке более стойкого основания СаО вызывает замещение FeO. В результате оно связывает фосфорный ангидрит в другое соединение (CaO)4 х P2O5 + 4 Fe, чего и требовалось добиться.
Чистый Fe высвободился в расплаве, а фосфор образовал шлак, который удаляется с зеркала металла и утилизируется за ненадобностью. Поскольку фосфорный ангидрид преобразует состав шлака, процесс должен идти непрерывно.
Поэтому FeO должен непрерывно пополняться за счет загрузки новых партий железной руды и окалины, наводящих в расплаве железистый шлак.
Особенности второго этапа
Технология производства стали на втором этапе называется кипением стали. Основное назначение заключается в процентном снижении содержания углерода за счет окисления. FeO + C = CO + Fe.
Реакция окисления происходит более интенсивно при кипении и сопровождается поглощением тепла. Поэтому необходимо создавать постоянный приток тепла в ванну, а также для выравнивания температуры в расплаве.
При такой реакции окисления интенсивно выделяется газ оксида углерода CO, что вызывает бурное кипение в жидком агрегатном состоянии, по этой причине процесс называют кипением. Чтобы излишки углерода интенсивнее преобразовывались в окись, производство качественной стали предусматривает вдувание чистого кислорода и добавление в расплавленную структуру окалины. Поэтому таким важным является качество сырья для производства стали. Все исходные материалы проходят щепетильную проверку.
Немаловажным на этом этапе является вывод серы, благодаря чему повышается качество конечной стали. Используемая в компонентах сера, присутствует не в прямом виде, а в форме сульфида железа FeS.
При высоких температурах компонент также взаимодействует с оксидом СаО, образуя сульфид кальция CaS, который растворяется в шлаке, не соединяясь с железом. Это позволяет беспрепятственно выводить сульфид за пределы ванны.
Конвертерное производство стали
Раскисление
Третий этап – раскисление металла. После добавления кислорода (на предыдущем этапе) требуется снизить его содержание в чистой стали. Использованием О2 удалось добиться окисления примесей, но его остаточное присутствие в конечном продукте снижает качественные характеристики металла. Требуется удалить или преобразовать окислы FeO, связав кислород с другими металлами.
Для этого существуют два метода раскисления:
При диффузионном методе в расплавленный состав вводят добавки: алюминий, ферромарганец и ферросилиций. Они восстанавливают оксид железа и переводит в шлак. В шлаке оксид распадается и высвобождает чистое железо, которое поступает в расплав. Второй высвободившийся элемент – кислород улетучивается в окружающую среду.
Осаждающий метод предусматривает введение добавок, имеющих большее сродство с кислородом, чем Fe. Происходит замещение этими веществами железа в окисле. Они, как менее плотные, всплывают и выводятся вместе со шлаком.
Процесс раскисления продолжается при затвердевании слитка, в кристаллической структуре которого оксид железа и углерод взаимодействуют. В результате чего вместе с пузырьками азота, водорода он выводится.
Чем больше при раскислении выводится включений различных металлов, тем выше ковкость получаемой стали. Для проверки раскаленный кусок металла подвергают ковке, на нем не должны образовываться трещины. Такая проверка пробы говорит о правильном проведении процесса раскисления.
В зависимости от степени раскисления специалисты могут получить:
Для получения легированных сталей с добавками некоторых металлов в расплавленный металл добавляются ферросплавы или чистые металлы. Если они не окисляются (Ni, Co, Mo), то такие добавки могут вводиться на любом этапе плавки. Более чувствительные к окислению металлы Si, Mn, Cr, Ti добавляют в ковш или, что обычно и происходит, в форму для отливки металла.
Существуют основные способы получения стали в сталеплавлении.
Мартеновский способ
Этот способ применяется для производства сталей высокого качества, применяемых в особо ответственных деталях машинах и точных механизмах.
В свое время он заменил трудоемкие и малопроизводительные тигельную и пулдинговую плавки, применявшиеся ранее.
Емкость загрузки одной отражательной печи, используемой при этом методе, достигает 500 тонн. Особенностью мартеновского способа является возможность переплавки не только передельного чугуна, но и металлургических отходов, металлического лома.
Температура нагрева жидкой стали достигает 2 тыс. градусов. Этот результат достигается специальной конструкцией мартеновской печи:
Мартеновская печь состоит из следующих элементов:
Процесс плавки занимает от 4 до 12 часов. С целью ускорения процесса плавки объем закачиваемого кислорода превышает потребности, что повышает производительность плавки на 20–30%.
Конвертерный метод
В конверторах выплавляют сорта стали для производства автомобильного листа, инструментальной стали сварных конструкций и других стальных заготовок. По качеству они уступают мартеновскими применяются для изготовления менее ответственных изделий.
В них содержится больше примесей, чем при мартеновском изготовлении. Благодаря высокому объему загрузки одной печи до 900 тонн, способ считается самым производительным, поэтому получил широкое распространение.
Производство стали и другого вида металла этим методом основано на продувке жидкого чугуна воздухом или кислородом под давлением 0,3–0,35 МПа, при этом металл разогревается до 1600 градусов. Плавка скоротечна и длится до 20 минут. За это время происходит окисление углерода, кремния и марганца, содержащихся в сырье, которые извлекаются из ванны с расплавом шлака.
Конвертер представляет сосуд ретортообразной (грушевидной) формы, состоящий из стальных листов с футеровкой изнутри. Для заливки чугуна и выпуска готовой стали используется одно отверстие, в него также загружается чугун и скрап.
Рождение стали
Особенности процесса
Вместе с ними загружаются шлакообразующие вещества: известь и бокситы. Корпус охвачен опорным кольцом, прикрепленным к поворотным цапфам. С их помощью сосуд наклоняется и через это отверстие – летку выливается готовая сталь. Нижняя продувка осуществляется через сквозные отверстия (фурмы), сделанные в днище печи.
Исторически повелось, что используемый везде способ называется томасовским, бессемеровским. В прошлом веке преобладающим стал мартеновский процесс. Нагрев регенератора осуществляется продувкой печных газов, после чего он нагревается холодный воздух, поступающий на расплав.
В современных конструкциях чаще применяют верхний способ, при котором продувка на огромной скорости осуществляется через опускаемые к поверхности металла сопла. В России преимущественно используется именно верхняя продувка печей.
Находясь под струей воздуха, чугун интенсивно окисляется в зоне контакта. Поскольку его концентрация значительно больше других примесей, преимущественно образуется оксид железа. Но он растворяется в шлаке. Поэтому металл обогащается выделяемым кислородом.
Окисляются C, Cr и Mn, снижая процентное содержание в структуре металла. Окисление сопровождается выделением тепла. Благодаря присутствию шлаков СаО и FeO до разогрева происходит выведение фосфора в самом начале продувки.
Шлак с ним сливается и наводится новый. Производство стали сопровождается экспресс-анализами и контролем текущих изменений приборами контроля, вмонтированных в печь. Содержание фосфора в чугуне не должно превышать 0,075%.
Кислородно-конвертерный способ получения стали
Производство стали сегодня осуществляется в основном этим способом. На долю кислородно-конверторного производства совсем недавно приходилось до 60% мирового производства стали.
Однако, этот процент снижается в связи с появлением электродуговых печей (ЭДП). Продувка печей осуществляется чистым кислородом (99,5%) под высоким давлением.
Продукт кислородно-конвертерной печи представляет сталь с заданными химическими свойствами. Она поступает в машину непрерывного литья заготовок (МНЛЗ), где материал застывает в форме блюма или плиты. Для получения определенных жестких параметров металл подвергается вторичной переработке.
Электросталеплавильный способ
Производство стали электрической плавкой обладает рядом неоспоримых преимуществ. Этот способ считается основным при выплавке высококачественных легированных сталей.
Достигаемая при этом высокая температура позволяет выплавлять стали, содержащие тугоплавкие металлы:
Высокое качество достигается практическим отсутствием в сталях фосфора, серы и кислорода. Этот способ также применяется для производства широкой номенклатуры строительных сталей.
Выделение тепла не связано с потреблением окислителя, а происходит в результате преобразования электрической энергии в тепловую. Она выделяется при прохождении электрической дуги или наведения вихревых токов. В зависимости от принципа работы печи подразделяются на электродуговые и индукционные.
Электродуговая печь способна принять одновременно от 3,5 до 270 тонн сырья:
Она имеет несколько электродов из графитосодержащего материала, к которым подводится электрическое напряжение. Время плавки составляет до 1,5 часа, при этом температура дуги достигает 6 тыс. градусов.
Особенности электроиндукционных печей
В электроиндукционных печах сталь выплавляют в небольших по объему (4,5–60 тонн) емкостях, именуемых огнеупорными тиглями. Вокруг тигля располагается индуктор, состоящий из большого количества витков провода.
При прохождении переменного тока внутри индуцируются вихревые токи большой силы, вызывающее плавление содержимого тигля. Электромагнитные силы одновременно перемешивают расплав стали. Продолжительность плавки в таких печах не превышает 45 мин.
Электросталеплавильный способ производит мало дыма, пыли и меньше излучает световой энергии. Однако, высокая стоимость электрооборудования при малой вместительности ограничивает применение этого способа.
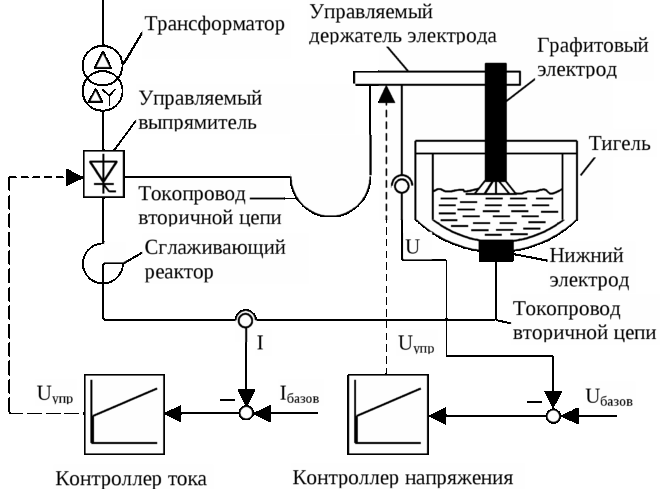
Схема электросталеплавильной печи
Помимо рассмотренных вариантов, существуют не только основные способы производства стали. В современном сталеплавлении используется плавка в вакуумных индукционных печах и обогащение процентного содержания железа в окатышах плазменно-дуговым переплавом.
Виды получаемых сталей по химическому составу
Производимая этими методами сталь делится, в зависимости от химического состава, на две большие группы:
Процентное содержание элементов в углеродистой стали:
Наименование | Fe | С | Si | Mn | S | P |
Содержание в процентах | до 99,0 | 0,05–2,0 | 0,15–0,35 | 0,3–0,8 | до 0,06 | до 0,07 |
В углеродистых сталях прочность недостаточно сочетается с пластичностью. Недостаток устраняется введением добавок других металлов, такая сталь называется легированной.
Согласно ГОСТ 5200 выделяют три группы легированных сталей с допустимым содержанием примесей:
С каждым годом способы плавки усовершенствуются благодаря вводу в строй нового высокотехнологичного оборудования. Это позволяет получать в сталелитейной промышленности высококачественные стали с оптимальным содержанием добавок и металлов.
Видео по теме: Производство чугуна и стали
promzn.ru
История производства стали
До н.э. в Европе уже повсюду производили кованое железо. Многие великолепные Греческие и Римские здания были построены из камня с применением железных инструментов в форме бабочки, покрытых свинцом. В 500 году до н. э. этруски, жившие на западном побережье Италии производили более 4,5 тысячи килограмм железа в год. Ковку железа осуществляли в кузнице, а для поддержания огня использовали древесный уголь. Огонь раздували при помощи специальных мехов, сшитых из шкур животных. Позже маленькие каменные печи разобрали, и начали массовую выплавку железа. Руду к печам доставляли на парусных судах. В связи с тем, что метод обработки руды, который использовали этруски, был малоэффективен, ее запасы быстро истощились. К тому же производство древесного угля резко сократило количество лесов на западе Италии.
Первая сталь была создана кельтами около 200 года н. э. Они резали кованое железо на тонкие полоски и складывали их в контейнер с обожженными костями и углем, после чего все это нагревали в печи в течение 10-12 часов на очень сильном огне. В результате поверхность металла обогащалась углеродом. Затем они эти полоски сваривали между собой посредством ковки и таким образом создавали ножи. Эти ножи стали предшественниками клинков, которые мы ошибочно называем дамасскими. Кельтский процесс производства стали в 1050 году был скопирован викингами и немцами. С тех пор в этих странах производили стальные клинки, метод изготовления которых, был строго засекречен. Дамасскую сталь производили в Пакистане и в виде булатных заготовок отправляли в Сирию, где изготавливали знаменитые дамасские клинки. Процесс производства дамасской стали очень сложный, поскольку ее необходимо было нагревать до очень высокой температуры, и если температуру превысить, то материал мог разрушиться.
Со временем температура плавления железа в печах становилась все выше, поэтому полученное железо, содержало 3-4% углерода. Оно было хрупким и подходило только для литья. Из него нельзя было делать ножи и детали для транспорта. К тому же к этому времени огромная часть лесов в Европе была вырублена для строительных целей и производства древесного угля. Тогда король Англии издал указ о том, что леса вырубать больше нельзя, и производителям стали пришлось придумать способ переработки угля в кокс. В Англии разработали метод лужения стали, при этом они смешивали расплавленное железо, с силикатом железа и оксидом железа. Силикат железа является одним из компонентов кованого железа.
Печи, работающие на угле, назвались кричным горном. Один работник должен был помешивать полученную смесь, в результате чего образовывался диоксид углерода, поэтому температура плавления железа становилась выше, и начинался процесс лужения. Внутрь помещались крупные куски весом от 90 кг до 130 кг. Другой работник с помощью пары больших щипцов брал эти куски и помещал под пресс, чтоб из них выдавить силикат железа. После пресса куски помещали в прокатный стан, где из них формировались полоски кричного железа. Эти полоски нарезали на короткие кусочки и соединяли между собой, после чего помещали их в углубление, заполненное углеродом, и нагревали до температуры сварки. После этого полоски кричного железа снова отправляли в прокатный стан и получали сортовое железо. Этот способ использовали не только в Европе, но на востоке Соединенных Штатов.
Чтоб получить сталь, тонкий сортовой прокат помещали в углубление, заполненное углеродом, полученным в результате сожжения костей, и нагревали при высокой температуре в течение нескольких дней. Углерод поглощался железом, и в результате получалась пузырчатая сталь. Пузырчатой называли цементную сталь или томленку. Это понятие появилось благодаря внешнему виду полосок, извлеченных из углеродной ямы, которые были покрыты пузырями. После этого полоски складывали вместе и ковали, затем снова складывали и ковали, таким способом получали сталь высокого качества.
Англия нуждалась в высококачественной стали, чтоб создать флот, который смог бы пресечь океан. Один предприимчивый англичанин заметил, что стеклодувы в своих печах могут получать очень высокую температуру. Он взял полоски пузырчатой стали и поместил их в керамический тигель, после чего поставил емкость в печь стеклодувов. В результате сталь расплавилась, силикат железа испарился, а углерод остался, и получилась сталь очень высокого качества. На тот момент за процессом наблюдало много людей, и он не смог сохранить его в секрете. Таким способом получали литую сталь, из которой в США было сделано большое количество старых инструментов, с маркировкой «литая сталь». Многие ошибочно считают их литыми, что следует из названия.
Новый импульс производство стали получило, когда был изобретен Бессемеровский процесс производства стали. Такую сталь применяли для строительства крупных объектов, таких как плотина Гранд-Кули, потому как она не подвержена действию коррозии. В начале 20 века приступили к производству различных сплавов. Тогда в газовых мартеновых печах к железу стали добавлять марганец, хром, никель и другие элементы. Во время Второй мировой войны, когда потребность в металле возросла, производство сплавов получило новый мощный толчок. С тех пор был сделан огромный шаг в производстве и совершенствовании различных сталей.
Сталь имеет более высокие физико-механические свойства по сравнению с чугуном: ее можно ковать, прокатывать, она имеет высокую прочность и значительную пластичность, хорошо обрабатывается резанием. В расплавленном состоянии сталь обладает достаточной жидкотекучестью для получения отливок.
Мягкая сталь с содержанием углерода менее 0,25% обладает высокой пластичностью, способностью хорошо свариваться, легко куется и прокатывается в горячем и холодном состояниях. Поэтому такая сталь является основным материалом для современного машиностроения, транспорта и других отраслей народного хозяйства страны.
В древности мягкую сталь (техническое железо) получали непосредственно из руд в тестообразном состоянии. Позднее научились получать сталь из чугуна в кирпичном горне, также в тестообразном состоянии. В 1740 г. в Англии стал применяться способ получения жидкой стали в тиглях, задолго до того известный на Востоке. С 1784 г. начали применять пудлингование — получение стали в тестообразном состоянии из чугуна окислением его примесей на поду пламенной печи. Все эти способы были мало производительны, требовали больших затрат топлива и труда.
Бурный рост промышленности и железнодорожного транспорта во второй половине XIX в. потребовал громадного количества стали, а старые способы ее получения не могли удовлетворить эту потребность. Были созданы новые, более производительные способы плавки стали. В 1856 г. появился бессемеровский способ (названный по имени его изобретателя Г. Бессемера), а в 1878 г. — томасовский способ (предложенный С. Томасом) получения литой стали из жидкого чугуна в конвертерах. В 1857 г. крупный русский металлург П. М. Обухов получил привилегию на изобретенный им способ производства орудийной стали путем сплавления чугуна и мягкой стали. Орудийная сталь П. М. Обухова по качеству превосходила лучшие заграничные стали. С 1864 г. применяется мартеновский способ получения стали в пламенных печах (названный по имени его изобретателя П. Мартена), а с 1899 г. — способ производства стали в электропечах, основанный на применении явления электрической дуги, открытой в 1802 г. акад. В. В. Петровым.
Задача передела чугуна в сталь состоит в том, чтобы из чугуна удалить избыток углерода, кремния, марганца и других примесей. Особенно важно при этом удалить вредные примеси серы и фосфора. Углерод чугуна, соединяясь с кислородом, превращается в газ (окись углерода СО), который улетучивается. Другие примеси переводятся в окислы и другие соединения, нерастворимые или мало растворимые в металле; эти соединения вместе с флюсами образуют на поверхности металла шлак. При сгорании марганец и кремний образуют нерастворимые в металле окислы MnO и SiO2. При сгорании фосфора образуется его окись Р2О5, которая хорошо растворяется в металле. Чтобы удалить фосфор из металла, наводят шлак с избытком извести (состоящей преимущественно из СаО), которая и связывает Р2О5 в прочное соединение (СаО)4 • Р2О5, нерастворимое в металле.
Сера растворена в чугуне в составе соединения FeS; ее удаляют из металла с помощью марганца или извести, которые образуют с ней или плохо растворимое в металле соединение MnS или нерастворимое соединение CaS.
В настоящее время в металлургии страны применяются следующие способы получения стали: конвертерный, мартеновский и электроплавка.
Электроплавка применяется, главным образом, для получения высококачественной стали и за последние годы усиленно развивается.
Технический прогресс в сталеплавильном производстве характеризуется интенсивным наращиванием мощностей плавильных агрегатов, широким применением кислородно-конверторного процесса и непрерывной разливки стали, повышением качества металла.
biofile.ru
Способ производства изделия из стали
Изобретение относится к области производства стального листа или стальной полосы. Для обеспечения высокого предела текучести, изотропной деформируемости и пластичности при низких температурах способ включает получение сляба из стали, содержащей, мас.%: С: <1,00, Mn: 7,00-30,00, Al: - 1,00-10,00, Si: >2,50-8,00, Al+Si: >3,50-12,00, В: <0,01, Ni: <8,00, Cu: <3,00, N: <0,60, Nb: <0,30, Ti: <0,30, V: <0,30, Р: <0,01 железо и неизбежные примеси - остальное, нагрев сляба, как минимум, до 1100°С и горячую прокатку, конечная температура которой составляет минимум 800°С, смотку горячекатаной полосы при температуре от 450 до 700°С, холодную прокатку горячекатаного листа со степенью деформации от 30 до 75% в холоднокатаный лист, рекристаллизационный отжиг при температуре от 600 до 1100°С и холодную деформацию со степенью деформации от 2,5 до 25%. 2 н. и 16 з.п. ф-лы, 1 табл.
Изобретение касается способа производства изделия из стали, имеющего высокий предел текучести. Изделие согласно изобретению является, в частности, стальным листом или стальной полосой.
Для производства деталей кузовов автомобилей и применения в низкотемпературных условиях из документа DE 19727759 C2 известна легкая конструкционная сталь, содержащая наряду с железом от 10 до 30% марганца, от 1 до 8% алюминия и от 1 до 6% кремния, причем сумма содержаний алюминия и кремния не превосходит 12%. В этой известной стали углерод содержится на уровне примеси.
В известной из документа DE 19900199 A1 легкой конструкционной стали углерод предусмотрен как опциональный легирующий элемент. Известная легкая сталь содержит от 7 до 27% марганца, от 1 до 10% алюминия, от 0,7 до 4% кремния, менее 0,5% углерода, менее 10% хрома, менее 10% никеля и менее 0,3% меди. Кроме того, в стали могут содержаться азот, ванадий, ниобий, титан и фосфор, причем сумма этих элементов не превышает 2%.
Стали представленного выше вида обладают TWIP-свойствами ("TWIP" = "Twinning Induced Plasticity"). Это значит, что они обладают высокой пластичностью при, одновременно, хорошей прочности и незначительном весе. В соответствии с этим из легкой конструкционной TWIP-стали может изготавливаться изделие с крайне высокими пределами прочности и растяжения. У стального листа, произведенного из известной легкой конструкционной TWIP-стали, минимальный предел текучести лежит, как правило, в диапазоне от 260 до 330 МПа.
Еще более высокие характеристики текучести при одновременно хорошей деформируемости могут достигаться, например, у сталей с TRIP-эффектом ("TRIP" = "Transformation Induced Plasticity") или у сталей, которые обладают TWIP- и TRIP-свойствами. Однако все варианты известных листовых сталей, произведенных из легкой конструкционной стали указанного вида, имеют характерные недостатки при пределе текучести более 330 МПа. Так, например, могут встречаться разбросы температуры от вязкого разрушения к хрупкому, сильное изменение свойств в зависимости от температуры и анизотропный характер деформации.
Поэтому задача изобретения состояла в том, чтобы предложить способ, который обеспечивает надежное производство стальных изделий из легкой конструкционной стали, при котором достигается изотропный характер при наличии высокого предела текучести и обеспечивается пластичность при низких температурах.
Эта задача решается в способе производства стального изделия, в частности листа или полосы из стали,
- при котором полосу или лист производят из стали, содержащей, мас.%:
углерод менее 1,00
марганец 7,00-30,00,
алюминий 1,00-10,00,
кремний более 2,50-8,00,
алюминий + кремний более 3,50-12,00,
бор менее 0,01,
никель менее 8,00,
медь менее 3,00,
азот менее 0,60,
ниобий менее 0,30,
титан менее 0,30,
ванадий менее 0,30,
фосфор менее 0,01
и в качестве остатка - железо и неизбежные примеси,
и затем для производства готового стального изделия предусмотрена деформация в холодном состоянии со степенью деформации от 2 до 25%.
Согласно изобретению высокие пределы текучести готовых стальных изделий устанавливаются в процессе деформации в холодном состоянии, которому подвергается стальная полоса, после того, как она проходит обыкновенные этапы производства стальной полосы. При использовании легкой конструкционной стали заявленного согласно изобретению состава в способе можно производить изделия, которые обладают высоким пределом текучести при одновременно хорошей деформируемости как из горячекатаной полосы, так и из холоднокатаной полосы. Существенно при этом, что деформация в холодном состоянии проводится с достаточными степенями деформации по окончании производства горячей или холодной полосы.
Согласно изобретению деформация в холодном состоянии может проводиться, к примеру, последующей прокаткой или правкой с растяжением и гибкой листовой стали или стальной полосы. В этих случаях произведенным согласно изобретению изделием является лист или полоса, предел текучести которой лежит выше 330 МПа.
Этого минимального значения, а также уверенно получаемых пределов текучести можно достигать также посредством того, что проведенная согласно изобретению деформация в холодном состоянии является частью технологии производства готовой конструктивной формы детали. Таким образом, можно проводить на последнем этапе соответствующего изобретению способа конечную деформацию в холодном состоянии, к примеру, также глубокой вытяжкой, обтяжкой или гидроформингом. Существенным является при этом лишь то, что достигается достаточная степень деформации, которая лежит выше получаемой при обычном традиционном формовании степени деформации.
Неожиданно выяснилось, что исходя из использованного согласно изобретению сплава стали посредством деформации в холодном состоянии, проведенной к окончанию способа производства без следующего повторного прокаливания, происходит отчетливое повышение предела текучести без ухудшения изотропии или пластичности материала. Таким образом, произведенные согласно изобретению изделия, в частности лист или полоса, отличаются оптимальной комбинацией из предельного относительного удлинения при разрыве и предела текучести. Дополнительно они обладают TWIP-свойствами. Они отчетливо превосходят подобные, традиционно производимые изделия из легкой конструкционной стали. С помощью способа согласно изобретению возможно простым способом производить изделия из легкой стали с наибольшими пределами текучести, которые отличаются хорошей деформируемостью при незначительном весе.
Надежность, с которой достигается согласно изобретению возможный производственный результат, можно повысить посредством того, что степень деформации в холодном состоянии составляет не более 15%, в частности не более 10%.
Как исходный продукт для производства стальных продуктов согласно изобретению можно использовать горяче- или холоднокатаные полосы. При этом производство горячекатаной полосы может включать обыкновенные технологические этапы. Таким образом, сталь с составом согласно изобретению может отливаться в слябы, тонкие слябы или литые полосы. Эти полупродукты затем прокатывают в горячекатаную полосу, которую сматывают в рулоны.
После смотки полученная горячекатаная лента может быть деформирована в холодном состоянии соответствующим изобретению способом непосредственно в изделие. Альтернативно горячекатаная лента может быть сначала прокатана в холодном состоянии в холоднокатаную полосу, которая затем подвергается рекристаллизационному отжигу, прежде чем она на последнем этапе способа согласно изобретению снова подвергается деформации в холодном состоянии со степенью холодной деформации, составляющей от 2 до 25%.
Если, в частности, при применении слябов перед горячей прокаткой требуется повторный нагрев, то температура повторного нагрева не должна лежать ниже 1100°C. В противоположных случаях, в которых исходный продукт в непрерывном технологическом процессе после разливки подводится к горячей прокатке, она может происходить также без промежуточного повторного нагрева, горячим садом. Когда горячая лента согласно изобретению при температурах горячей прокатки, составляющих минимум 800°C, подвергается горячей прокатке и сматывается при низких температурах, то положительное действие углерода, поскольку он присутствует, и, в частности бора, используется в полном объеме. Таким образом, бор и углерод в листовых сталях при горячей прокатке в этой области обеспечивают достижение более высоких значений предела прочности и предела текучести при по-прежнему приемлемых значениях относительного удлинения при разрыве. С возрастающей температурой горячей прокатки предел прочности и предел текучести снижаются, в то время как значение удлинения увеличивается. Вариацией температур прокатки в заявленных изобретением рамках можно, таким образом, целенаправленно и простым способом обеспечивать желаемые качества полученных листов.
Ограничением температуры смотки до значения не более 700°C уверенно предотвращают возникновение хрупкости материала. Было зафиксировано, что при более высоких температурах смотки могут образовываться хрупкие фазы, которые вызывают, к примеру, расслаивания материала и затрудняют или даже делают невозможной дальнейшую обработку.
Если стальной продукт производится из холоднокатаной полосы, то степень деформации в холодном состоянии при предшествующей рекристаллизационному отжигу холодной прокатке лежит, предпочтительно, в диапазоне от 30 до 75%, чтобы надежно достигать оптимальных характеристик деформации и механических свойств готового стального изделия.
Температура нагрева при рекристаллизационном отжиге лежит, предпочтительно, между 600 и 1100°C. При этом отжиг может проводиться в кожухе в области температур от 600 до 750°C или в методической печи для отжига при температурах от 750 до 1100°C.
Вследствие содержания кремния 2,50 мас.%, предпочтительно выше 2,70 мас.%, листовая сталь согласно изобретению хорошо поддается холодной прокатке, в отличие от легких листовых сталей или жести, которые обладают более незначительными содержаниями кремния. Высокая добавка кремния обеспечивает более равномерные значения пределов текучести и прочности, а также более высокое относительное удлинение при разрыве и степень равномерности растяжения. Кремний в стали согласно изобретению ведет исходя из этого к более высоким значениям r и n, а также к изотропному распределению механических качеств. Предел суммарного содержания алюминия и кремния лежит при 12%, так как превышающая эту границу сумма содержаний алюминия и кремния привела бы к опасности возникновения хрупкости.
Неожиданно выявилось, что целенаправленное добавление бора в сталь согласно изобретению может вести к улучшению и воспроизводимости свойств. Поэтому предусмотрено согласно предпочтительному варианту осуществления изобретения, чтобы сталь содержала бор. Поскольку бор добавляется для улучшения согласования пределов текучести и деформируемости, содержание бора может лежать для этого в диапазоне от 0,002 до 0,01 мас.%, в частности от 0,003 до 0,008 мас.%.
Благоприятные влияния сплава на механико-технологические качества соответствующей изобретению листовой стали могут достигаться при минимальном содержании углерода 0,10 мас.% в стали согласно изобретению.
За счет особенного спектра свойств изделий, произведенных способом согласно изобретению, в частности холоднокатаной полосы, их используют для изготовления несущих, а также устойчивых к повреждениям деталей кузова для транспортных средств. Они могут использоваться при незначительном весе, к примеру, для особенно эффективной защиты пассажиров транспортного средства. Произведенные, согласно изобретению продукты отличаются в этой связи особенно высокой энергопоглощающей способностью при внезапно появляющихся нагрузках.
Незначительный вес при, одновременно, хорошей деформируемости и прочности делает возможным производить колеса для транспортных средств, в частности грузовых автомобилей, из произведенных согласно изобретению изделий.
Также можно производить из произведенных согласно изобретению изделий детали, которые используются в области техники низких температур. Благоприятный спектр свойств произведенной согласно изобретению холоднокатаной ленты сохраняется также при низких, в области криотехники, и обычных температурах.
Достигнутые в способе производства согласно изобретению хорошие энергопоглощающие способности, исходя из этого, делают способ согласно изобретению, особенно подходящим для производства изделий, которые используются в качестве защитных элементов, предназначенных для защиты от возникающих импульсных нагрузок.
Далее изобретение поясняется при помощи примеров изготовления.
Легкая сталь (указания в мас.%) с 0,0070% углерода, 25,9% марганца, 0,013% фосфора, 0,0006% серы, 2,83% кремния, 2,72% алюминия, 0,0045% азота и, остаток, железо, а также неизбежные примеси, к которым относятся, к примеру, незначительные содержания меди, хрома, никеля, мышьяка, олова, титана, ванадия, ниобия, брома и магния, отливалась в слябы.
Стальные слябы после повторного нагрева до 1150°C подвергались горячей прокатке при 850°C в горячекатаную полосу, которая затем сматывалась при температуре смотки 500°C. Затем горячекатаная полоса прокатывалась в холодном состоянии в холоднокатаную полосу толщиной 1 мм при степени деформации до 65%. После прокатки в холодном состоянии холоднокатаная полоса при температуре 950°C подвергалась рекристаллизационному отжигу.
В этом состоянии холоднокатаная полоса была изотропной. Ее установленные, соответственно, в продольном направлении механические качества занесены в таблицу (степень деформации в холодном состоянии = 0%).
Степень деформации | Rp0,2 | Rm | Ag | A80 | nкоэффициент упрочнения | rперпендикулярная анизотропия |
[%] | [МПа] | [МПа] | [%] | [%] | ||
0 | 326 | 657 | 52,8 | 58,8 | 0,373 | 0,93 |
2,5 | 400 | 675 | 47,5 | 53,4 | 0,307 | 0,90 |
5 | 464 | 699 | 41,8 | 48,2 | 0,257 | 0,85 |
10 | 568 | 748 | 30,9 | 40,5 | 0,199 | 0,80 |
30 | 870 | 1039 | 3,0 | 12,1 | - | - |
50 | 1051 | 1225 | 2,9 | 5,4 | - | - |
Для доказательства результата изобретения после рекристаллизационного отжига образцы холоднокатаной ленты были прокатаны в холодном состоянии со степенью деформации в 2,5%, 5%, 10%, 30% и, соответственно, 50%. Установленные механические свойства для каждого из образцов, соответственно, в продольном направлении также занесены в таблицу.
Выяснилось, что у полученного - после последующей прокатки в холодном состоянии - холоднокатаного изделия оптимальная комбинация из пределов растяжения и текучести достигаются тогда, когда при последующей прокатке в холодном состоянии устанавливалась степень деформации в холодном состоянии в 10%. Так, предел текучести Rp0,2 поднялся при степени деформации в холодном состоянии в 10% более чем на 70%, а предел прочности Rm улучшился более чем на 10%. При этом среднее значение удлинения Ag и значение удлинения A80, значения r и n оставались на уровне, который лежит далеко поверх того, чего достигают при обычной стали со сравнимым пределом текучести. Только при степени деформации в холодном состоянии от 30% наблюдалось падение свойств удлинения.
В другом эксперименте была произведена следующая холоднокатаная полоса того же состава и с совпадающим до окончания рекристаллизационного отжига режимом обработки. Из отрезка этой холоднокатаной полосы затем было произведено - без деформации в холодном состоянии - профилированное полое испытательное тело. Другой образец подвергнутой рекристаллизационному отжигу холоднокатаной полосы был, напротив, подвергнут последующей прокатке в холодном состоянии в соответствии со способом согласно изобретению со степенью деформации в холодном состоянии 7%. Из таким образом произведенного согласно изобретению холоднокатаного продукта затем также было произведено профилированное полое испытательное тело.
Оба испытательных тела весом примерно 150 кг затем в эксперименте с падением, при котором они попадали на препятствие со скоростью падения в 50 км/ч, были исследованы относительно их способности поглощать энергию. Выяснилось, что произведенное из подвергнутой согласно изобретению последующей прокатке в холодном состоянии холоднокатаной ленты испытательное тело, вопреки тому, что толщина его стенок при дополнительной деформации в холодном состоянии была уменьшена против той же у другого испытательного тела, обладало лучшей энергопоглощающей способностью.
В третьем эксперименте производилась, наконец, подвергнутая рекристаллизационному отжигу холоднокатаная лента вышеуказанного состава и при применении уже описанных этапов способа. Произведенная таким образом холоднокатаная лента затем была деформирована в холодном состоянии посредством обтяжки соответствующим изобретению способом. При этом достигнутая степень деформации в холодном состоянии составляла снова 10%. Предел текучести на уровне 320 МПа после рекристаллизационного отжига за счет деформации увеличился до 520 МПа этой деформацией в холодном состоянии на 520 МПа после следующей за рекристаллизационным отжигом деформации в холодном состоянии. Предел прочности также возрос с 640 до 710 МПа. Значение r практически не изменилось. Значение удлинения, правда, уменьшалось при возрастании степени деформации от 60% на примерно 50% и значения n - от 0,39 до 0,27. Тем не менее, эти значения также лежали намного выше удлинения и n-значений, которые могут фиксироваться у обычно производимой стали с таким же классом твердости и сопоставимым пределом текучести. Изделие, полученное при деформации в холодном состоянии холодной ленты посредством обтяжки имело, таким образом, оптимальную комбинацию значений пределов текучести и удлинения.
1. Способ производства листа с высоким пределом текучести, включающий получение горячекатаного листа из сляба, изготовленного из стали, содержащей, мас.%:
углерод | менее 1,00 |
марганец | 7,00-30,00 |
алюминий | 1,00-10,00 |
кремний | 2,50-8,00 |
сумма алюминий и кремний более | 3,50-12,00 |
бор | менее 0,01 |
никель | менее 8,00 |
медь | менее 3,00 |
азот | менее 0,60 |
ниобий | менее 0,30 |
титан | менее 0,30 |
ванадий | менее 0,30 |
фосфор | менее 0,01 |
железо и неизбежные примеси | - остальное, |
холодную прокатку горячекатаного листа в холоднокатаный лист, отличающийся тем, что лист подвергают холодной деформации со степенью
деформации от 2,5 до 25%.
2. Способ по п.1, отличающийся тем, что холодную деформацию проводят со степенью деформации не более 15%.
3. Способ по п.1, отличающийся тем, что холодную деформацию проводят со степенью деформации не более 10%.
4. Способ по п.1, отличающийся тем, что горячекатаный лист получают путем горячей прокатки сляба в горячекатаный лист, проводят смотку горячекатаного листа, холодную прокатку горячекатаного листа в холоднокатаный лист.
5. Способ по п.4, отличающийся тем, что сляб нагревают перед горячей прокаткой, как минимум, до 1100°С.
6. Способ по п.4, отличающийся тем, что горячей прокатке подвергают сляб с температурой, составляющей минимум 1100°С.
7. Способ по п.4, отличающийся тем, что конечная температура горячей прокатки составляет минимум 800°С.
8. Способ по п.4, отличающийся тем, что температура смотки составляет от 450 до 700°С.
9. Способ по п.4, отличающийся тем, что холоднокатаный лист после холодной прокатки подвергают рекристаллизационному отжигу, а затем проводят холодную деформацию.
10. Способ по п.9, отличающийся тем, что рекристаллизационный отжиг проводят при температуре от 600 до 1100°С.
11. Способ по п.10, отличающийся тем, что отжиг проводят под кожухом при температуре от 600 до 750°С.
12. Способ по п.10, отличающийся тем, что отжиг проводят при непрерывном движении листа при температуре от 750 до 1100°С.
13. Способ по п.9, отличающийся тем, что холодную прокатку проводят со степенью деформации от 30 до 75%.
14. Способ по п.1, отличающийся тем, что сталь содержит более 2,70 кремния, мас.%.
15. Способ по п.1, отличающийся тем, что сталь содержит от 0,002 до 0,01 бора, мас.%.
16. Способ по п.15, отличающийся тем, что сталь содержит от 0,003 до 0,008 бора, мас.%.
17.Способ по п.1, отличающийся тем, что сталь содержит от 0,1 до 1,0 мас.% углерода.
18. Лист, изготовленный из стали, отличающийся тем, что он получен способом по любому из пп.1-17.
www.findpatent.ru
Сталь
Одним из важнейших общемировых процессов является сталь, и её применений в виде произведенной стальной продукции – металлические изделия, предназначенные для усовершенствования жизни человека.
Понятие стали
Сталь – это наиважнейший, имеющий фундаментальное значение ресурс для любого государства. Природный ресурс, на основе которого начинается и берет свои истоки все, что нас на сегодняшней день окружает. Сталь это продукт развития и модернизации металлургии. Получение стали разных марок это очень трудоемкий химико-физический процесс, несущий в себе контроль соблюдения времени, температуры плавки и добавок различных по своим химическим свойствам легирующих элементов. Из стали разных марок производятся практически все механические, электрические и прочие изделия, за счет которых человечество может активно вести свою деятельность. Марки стали для производства тех или иных изделий подбираются исходя из предъявленных к детали требований, таких как: повышенная твердость, контактная прочность, стойкость к ударным нагрузкам, стойкость к трению, высокая поверхностная твердость, тяжело нагруженные детали, работающие при температурах до 400 С°, сложная конфигурация, повышенные механические свойства в работе при температуре более 500 С°, работа под давлением, робота при высоких отрицательных нагрузках и т.д. Все эти свойства приобретаются за счет добавления легирующих элементов, термообработки, поверхностного упрочнения. В связи с этим различные изделия из стали имеют применение в разнообразных областях: от самых простых по требованиям конструкционных элементах до сложных, где различным свойствам стали приходится справляться со сложными физическими и температурными нагрузками.
Стратегическое значение стали
Производство и изготовление стали это не только очень важный для любого вида промышленности материал, сталь так же несет в себе и очень важный стратегический характер. Проведя небольшой анализ по количеству выпускаемого железа в государствах, можно заметить следующий факт: лидерами по выпуску стали являются самые передовые и развитые государства во всем мире. Государство, освоившее выпуск стали может позволить себе устойчиво развиваться в выпуске тех или иных изделий, существенно сокращая свои собственные расходы, которые уходили бы на закуп данного ресурса. Ни одна ферма не может существовать без колодца. Вода есть начало всему живому, как и сталь для промышленности.
Человек, не знающий своей истории, не имеет будущего
История обработки человеком металлов зародилась вместе с умением добывать огонь. Существует версия, что, когда человек научился разводить костер, его постоянно раздувало, и была необходимость в его поддержки. Первобытные люди пришли к решению данного вопроса, придумав маленькую хитрость. А заключалась она в следующем: костры обкладывались по кругу камнями, что способствовало повышению температуры в очаге возгорания, тем самым выделялось гораздо больше полезного и важного в то время для человека тепла. Соответственно, среди этих камней попадались куски металлической руды, богатой содержанием меди. На протяжении долгого времени первобытное общество не замечало столь чудесных процессов, происходящих с медной рудой при воздействии температур. После того, как люди заметили свойства медной руды к плавке, её специально стали загружать на костры, дабы получить столь полезный и нужный в то время материал. Медь, добытая таким образом из руды, имела более полезные свойства и качества, но все еще уступала в крепости каменным породам за счет своей мягкости. Соответственно, талантливые, любознательные и одаренные люди были и есть в любую эпоху. Так человеческая любознательность и проведенные опыты выявили, что сплав меди и олова имеет более ярко выраженные прочностные свойства. В наше время данный сплав называется «бронза». Соответственно, благодаря своей твердости и меньшей гибкости, бронза вытеснила медные орудия труда. Далее на протяжении большого отрезка времени люди экспериментировали в выплавке и смешивании металлов и разных материалов. Появились первые металлургические заводы. Считается, что в металлургической промышленности первый сплав стали был получен в 1840 году русским ученым-изобретателем П.П. Аносовым. Данное открытие было научно обосновано и получило название «Булат». Метод его получения состоял в объединении науглероживания и плавления с последующей закалкой. Закалка в наше время – это один из видов термообработки. Отсюда и берет начало история получения стали с её столь полезными и важными свойствами.
Производство и выплавка стали
На сегодняшний день сталь получают на огромных, специально оборудованных заводах, где изначально куски железной руды расплавляют в огромных доменных печах. После процесса отделения металла от примесей из обогащенной руды образуется чугун. В последствие, чугун переплавляют в уже более технологичных печах: конвертерах и электропечах с добавкой различных материалов, временной и температурной выдержкой. После чего из чугуна получают сталь с её характерно выраженным металлическим блеском. Над всем этим процессом кропотливо трудятся: инженеры-металлурги, агломератчики, горновые, сталеплавильщики, стропальщики, разливщики и др. Металлургическая отрасль дает работу и хлеб миллионам людей. Зная свою историю, мы можем адекватно понимать важность и актуальность металлургической промышленности.
Поставленные нами цели
Мы с вами знаем, какую важность несет в себе такой продукт как сталь. На данный момент у человечества нет ни одного более универсального материала. Но развитие данной отрасли несет в себе непоправимые последствия и наносит огромный вред мировой экологии. Мы не хотим сидеть сложа руки и наблюдать за процессом разрушения экосистемы. Именно поэтому мы считаем своей истинной целью развить организации, посвящающие свою деятельность сбору и переработке металлолома и твердых бытовых отходов. Наша цель вырастить из ломозаготовителей современных металлургов, работающих на высокотехнологичных мини металлургических заводах по производству и выплавке стали. Основным ресурсом работы такого завода является электричество, что делает данный завод лекарем экосистемы. Вдобавок, ресурсом для производства стали является металлолом (мусор). Современные технологии не стоят на месте и позволяют уже сегодня производить сталь более эффективно, экономично, ну и самое главное - экологично. Мини заводы по выплавке стали работают на электроэнергии – это следующий шаг человечества для сохранения природы без отказа от столь ценного ресурса. Ведь мини завод не делает таких вредных и существенных в объеме выбросов. Даже если взять во внимание, что комбинат по производству стали производит такой же объем продукции, как и аналогичный мини завод, то по затратам электроэнергии для производства стали мини завод наиболее экономичен. Оставим будущее для своих детей чистым, выводы делать Вам!
alfaspk.ru