- галтовка
- подводное шлифование
- гидроабразивная обработка
- обработка чугунным песком
- обработка корундовой крошкой
- обработка ультразвуком
- химическое и электротравление
- шлифовка под слоем воды водостойкой шкуркой зернистостью 50–80 мкм
- обработка жесткой металлической щеткой
- электротравление в 10% растворе щавелевой кислоты при напряжении 12 В в течение 5–10 минут с плотностью тока до 2 А/см2
- пескоструйка мелкой чугунной крошкой
- отбеливающее травление в растворе 25% серной и 20% соляной кислоты в объемном соотношении 3/1 при температуре 30–40°C в течение 3–5–10 минут.
- Расход стальной фибры на 1м3 бетона
- Плетение троса стального
- Химполировка нержавеющей стали
- Электрохимическое полирование нержавеющей стали
- Сталь для подшипников
- Фибра стальная для бетона расход на м3
- А1 марка стали
- Сталь жаростойкая и жаропрочная
- Стальные подстропники
- Полирование электрохимическое нержавеющей стали
- Выбраковка канатов стальных
Раствор и способ химического полирования поверхности нержавеющей стали. Полировка химическая стали
Полировка химическая - Справочник химика 21
Этим металлографическим методом можно определять не только число дислокаций, но и ориентировку поверхностей пластинок, вырезанных из кристалла, а также степень неоднородности кристаллов. Чтобы выявить дислокации на пластине германия, сначала ее шлифуют, затем тщательно очищают, подвергают химической полировке, например смесью концентрированной азотной кислоты (7,5 мл), 48%-НОЙ плавиковой кислоты (5 мл), ледяной уксусной кислоты (10 мл) и дистиллированной воды (1,2 мл). Полируют и травят под тягой с соблюдением правил безопасной работы. После полирования пластину отмывают дистиллированной водой и травят для выявления дислокаций, например, в травителе 00 млН О, 12 г КОН и 8 г КзРе(СК)в. [c.140]
Блеск электролитических покрытий может быть достигнут путем механической, электрохимической или химической полировки. Однако при использовании этих методов безвозвратно теряется до 20% от веса покрытия, что приводит к значительному ухудшению защитных свойств покрытия кроме того, требуются дополнительные расходы на оборудование и материалы, электроэнергию, ра- [c.136]
Обсуждение результатов и выводы. Автору неизвестны старые наблюдения образования подобных поверхностных дендритов серебра в процессе электролиза кристаллов при низкой температуре. Результаты описанных выше опытов позволяют утверждать, что такие дендриты образуются только в оптических плоских пластинках, полученных. методом, исключающим механическую полировку (химическое растворение). В присутствии трещин или поверхностных дефектов образуется лишь беспорядочная сетка из нитей серебра. Даже при температуре жидкого воздуха галогениды серебра не легко раскалываются вдоль плоскостей (100), что отличает их от щелочных галогенидов. Гиппель [5] наблюдал образование аналогичных систем дендритов на поверхностях кристаллов галогенидов щелочных металлов, полученных скалыванием по спайности. [c.97]
Реальная поверхность кре.мния содержит весьма тонкий слой оксида кремния (1,0—1,5 нм), который образуется в ходе технологических процессов полировки монокристалла и очистки его поверхности от примесей при химическом удалении поверхностного слоя, нарушенного механической обработкой и окончательной промывкой монокристалла в растворителях и воде. При этом поверхностные атомы кремния оксидной пленки могут быть связаны с гидроксильными группами, кроме того, на поверхности физически адсорбируются молекулы воды. Аналогичная картина имеет место и на поверхности кристаллического оксида кремния— кварца. Исходя из этого химическая гомогенизация поверхности указанных материалов должна включать, с одной стороны, удаление физически сорбированной воды, а с другой — достижение максимальной степени гидроксилирования поверхности. Последнее оказывается одним из важнейших условии при использовании поверхности твердых веществ в качестве матрицы для осуществления на ней направленного синтеза, например, оксидных структур методом молекулярного наслаивания. Предельная степень гидроксилирования обусловливает максимальное заполнение поверхности элемент-кислородными структурными единицами, и, таким образом, вопрос стандартизации гидроксильного покрова поверхности при подготовке к синтезу является одним из важнейших, определяющим сплошность синтезированного методом молекулярного наслаивания слоя. [c.78]
Задание. 1. Определить при помощи химического травления глубину нарушений, вызванных механической обработкой поверхности кремния. 2. Провести химическую полировку поверхности кремния. [c.106]
Инфракрасная (ИК) спектроскопия используется в различных областях науки, и в каждой из них придается- этому термину различный смысл. Для химика-аналитика это удобный метод решения таких задач, как, например, определение пяти изомеров гексахлорциклогексана, качества парафина, смолы, полимера, эмульгатора в эмульсии для полировки, опознание страны, из которой вывезен контрабандный опиум. Физику ИК-спектроскопия представляется методом исследования энергетических уровней в полупроводниках или определения межатомных расстояний в молекулах. Она может быть также полезна и при измерении температуры пламени ракетного двигателя. Для химика-органика это метод идентификации органических соединений, позволяющий выявлять функциональные группы в молекулах и следить за ходом химических реакций. Для биолога ИК-спектроскопия - перспективный метод изучения транспорта биологически активных веществ в живой ткани, ключ к структуре многих естественных антибиотиков и путь познания строения клетки. Физикохимику метод позволяет приблизиться к пониманию механизма гетерогенного катализа и кинетики сложных реакций. Он служит дополнительным источником информации при расшифровке структуры кристаллов. В этих и многих других областях знания ИК-спектроскопия служит исследователям мощным средством изучения тайн вещества. Вероятно, справедливо будет сказать, что из всех инструментальных методов ИК-спектроскопия наиболее универсальна. [c.9]
Электронно-лучевые приборы в течение первых 2 месяцев теряют товарный вид. Такие детали, как штырьки, кольца, корпуса, предварительно полированные, за это время значительно прокорродировали. Через год после начала испытаний кольца и корпуса из ковара с химической полировкой покрылись продуктами коррозии приблизительно на 85% всей поверхности. Никелевые покрытия по латуни Л62 в течение 6 месяцев оказались более коррозионностойкими по сравнению с коваром, но затем происходит разрушение поверхности примерно на 70%. [c.80]
Химическое Т. применяют в технологии монокристаллов, стекол и поликристаллов (металлов, сплавов, полупроводников и др. неорг. материалов) для очистки от окалины и др. поверхностных загрязнений, выявления дефектов структуры и двойников, определения кристаллографич. ориентации, удаления нарушенных слоев, придания пов-сти определенных св-в (полировка, шлифовка, загрубление, изменение к.-л. характеристик), для повышения мех. прочности изделий, для изготовления рельефа или деталей определенной формы, в частности в планарной технологии полупроводниковых приборов, при изготовлении резонаторов, частотных фильтров, хям. сенсоров и т. п. [c.616]
Если образец представляет собой полированный шлиф, покрытие можно легко удалить, подвергая образец одной из окончательных операций полировки (алмазным порошком размером - 6 мкм или порошком АЬОз с размером зерна - 1 мкм). Если поверхность образца шероховатая или плоский образец нельзя подвергнуть повторной полировке, для удаления покрытия следует применять химические методы. [c.215]
Ожидать вообще какого-либо повышения чистоты препаратов при соединении компонентов не приходится, если не считать частных случаев, в которых незначительный эффект очистки может явиться следствием испарения при весьма высоких температурах. Поэтому следует стараться с самого начала применять металлы в возможно более чистом состоянии, т. е. использовать такие сорта или марки металлов, которые, будучи получены в промышленности или в лаборатории, содержали бы незначительное количество растворенных в них примесей (внутренние загрязнения). Внешние загрязнения, иапример пленки оксидов, можно удалить напильником и полировкой или химическим путем — травлением их соответствующими кислотами. На металлах, подвергаемых механическому измельчению в заводских условиях (порошок, стружка), часто остаются приставшие к ним остатки протирочных, понижающих трение смазочных веществ, которые приходится удалять при помощи органических растворителей, чтобы они не препятствовали образованию сплавов или не способствовали образованию карбидов. Воду и все растворители следует удалять из материалов путем их тщательного высушивания. [c.2143]
Поверхность деталей оборудования должна подвергаться полировке и тщательной очистке, чтобы уменьшить эффективную площадь контакта с UFe и удалить следы смазки или других примесей. Здание для очистки и дезактивации оборудования [3.209, 3.237] содержит установки для химической очистки всех материалов перед их применением, а также установки для извлечения и регенерации радиоактивных материалов из оборудования, демонтированного с завода. [c.136]
Для получения синтетической бирюзы, визуально сходной с природной сетчатой бирюзой, и для придания камню сходства с природной прожилковой бирюзой в исходный материал вводились специальные декоративные присадки. Это позволило получить синтетическую бирюзу, по физическим и химическим свойствам не уступающую природным образцам. Окраска полученной бирюзы ярко-голубая, иногда с голубовато-зеленым оттенком, образцы хорощо воспринимают полировку. Под микроскопом бирюза имеет вид мелкозернистого агрегата неправильных, угловатых и пластинчатых выделений, погруженных в изотропный субстрат. По структуре и типу зернистости она представляется близкой к плотной природной бирюзе. [c.252]
Состояние поверхности металла. В зависимости от чистоты металла, способов его получения и обработки поверхность может быть загрязнена различными растворителями, смазками, поверхностными окислами, сложными окисными фазами. Все это резко снижает скорость и повышает температуру взаимодействия металла с водоро-дами, в некоторых случаях совершенно предотвращая его. Поэтому перед гидрированием металлическая поверхность должна быть очищена от загрязнений. Механические макропримеси на поверхности удаляются обработкой на станке, наждачной бумагой, полировкой, химическим и электрохимическим травлением, промыванием органическими растворителями. Однако такая обработка недостаточна из-за мгновенного окисления активной чистой поверхности металла. Кроме того, глубокие загрязнения невозможно удалить механическим способом без значительной потери металла. [c.10]
Технологический процесс электрохимического полирования состоит из операций механической (шлифовка, полировка), химической (обезжиривание, травление) и электрохимической (электрохимическое обезжиривание) подготовки изделий, самого электрохимического полирования и последующей обработки полироваиных деталей (промывка, обработка в щелочном или бисульфатном растворе, прэмывка и сушка). Подготовительные операции те же, что и в гальваностегии (см. 77). Желательно иметь до электрополировки чистоту поверхности, соответствующей 8—10 классу электрохимическим полированием чистота повышается на два класса. [c.391]
Нужно заметить, что такие общие замечания для котлов, работающих в сульфитной среде, сделанные безотносительно к исходному (до полировки) химическому составу стали плакирующего слоя двухслойной стали обследованных котлов и без данных по отсутствию в исходном плакирующем слое науглероженной поверхности, не могут служить для практического руководства при изготовлении крупногабаритных биметаллических варочных котлов. Этот вопрос нуждается в специальном изучении и исследовании, особенно учитывая постоянно повышающийся уровень отечественной технологии прокатки двухслойного металла и значительную трудоемкость процесса полировки больших поверхностей. [c.169]
Предварительная закалка стеклянного изделия может пошл-сить его термостойкость в 1,5—2 раза. Значительно повышаег термостойкость огненная полировка, химическое травление. [c.66]
Широкое распространение получила так называемая фосфид-ная теория [15, с. 133]. Бик при изучении влияния тритолилфос-фита на процесс граничного трения пришел к выводу, что под действием высоких контактных температур трения на металлических поверхностях образуется легкоплавкая эвтектическая х месь фосфидов металлов, которая способствует процессу химической полировки поверхности. Этот вывод подтвержден при изучении термического разложения- триалкилфосфитов при 250—260°С. Сначала триалкилфосфиты адсорбируются на поверхности трения, но при больших нагрузках и высокой контактной температуре разлагаются на более простые соединения — фосфорную кислоту, фосфин и непредельные углеводороды, причем фосфин затем взаимодействует с металлической поверхностью, образуя на ней пленку фосфидов металлов. [c.134]
Итак, измеряется маслянистость просто — понижением трения, но взгляды на причины, обусловливающие маслянистость масел и механизм этого явления, весьма противоречивы. Ряд исследователей полагает, что полярные вещества (известные как добавки, повышающие маслянпстость), прочно адсорбированные и ориентированные на поверхности металла, являются защитой новерхности от износа. Другие же, как, например, К. С, Рамайя [43], считают это мнение несостоятельным, полагая, что вещества, повышающие маслянистость, снижают трение за счет химического действия на поверхность и полировки последней. [c.410]
В случае химического сродства между атомами растворенного и o нoв roгo (Ре) элементов на поздних стадиях деформационного старения происходит образование частиц выделения. Образцы подвергались ц]лифовке, полировке и травлению в ц%-ном растворе ННОз в спирте. На металлографических снимках (рис. I), снятых с этих образцов, на полосах скольжения (а они образуются в результате движения дислокации) видны образования зародышей карбидных частиц. Эти структурные изменения, как известно [2], несомненно приводят к охрупчиванию металла труб при длительной эксплуатации. [c.137]
Такое поведение прочности объясняется тем, что малые безопасные отпечатки приводили к образованию дефектов, не превышающих по размерам уже имеющиеся, возникающие при изготовлении стекла. Если же исходная поверхность подвергалась предварительной химической полировке, а следовательно, исходные поверхностные дефекты были удалены, то глубина безопасных отпечатков значительно сокраш,алась. [c.313]
ПЕМЗА (лат. ритех) — пористая, губ-чато-ноздреватая вулканическая горная порода. Образуется во время вулканических извержений при быстром застывании кислых лав (68—70% 5102), насыщенных водяным паром и газами. Цвет П. в зависимости от содержания и валентности железа изменяется от белого и голубого до желтого, бурого и черного. Для П. характерна малая теп-ло- и звукопроводность, хорошая газопроницаемость. П. огнестойка и химически инертна. Применяётся как абразивный материал для полировки дерева и металлических изделий, в строительстве, стеклопроизводстве, в кожевенной и химической промышленности. Из П. изготовляют фильтры, сушильные аппараты, их используют как основу для катализаторов, добавки к цементам, в качестве наполнителей и др. [c.187]
Перевод пробы в удобоанализируемую форму. К этому этапу относятся операции предварительного обогащения (флотация, магнитная сепарация) и последующей химической обработки (сплавление, растворение, выщелачивание, обжиг, хлорирование и т. д.), каждая из которых должна проводиться с учетом возможных потерь и дополнительного привнесения определяемого компонента в анализируемую пробу. В ряде методов, например в рентгенофлуоресцентном анализе, важную роль играет состояние поверхности анализируемых образцов. Во избежание больших ощибок, связанных с эффектами рассеяния и переизлучения на микротрещинах и иных неоднородностях поверхностных слоев, необходимо прибегать к особым приемам (сплавление, полировка, травление), обеспечивающим стандартизацию условий измерения. [c.19]
Не менее важное значение для получения надежных картин травления имеет правильная обработка поверхности образца. Обычно кристаллы шлифуются и механически полируются, однако иногда уместна электролитическая полировка. Для выявления дислокаций в поликристаллических образцах карбида ниобия шлиф обрабатывался после химического травления в ванне с раствором [пН2504 + тНЫ0з + рНР]. Полученные ямки, плотность которых 10 см-2, образовывали характерные субграницы. При многократном травлении их расположение практически не изменялось. Часто П0 виду и расположению ямок травления можно определить направление дислокационных линий. Так, при исследовании поликристаллических образцов природного кварца методом гидротермального травления были обнаружены плоскодонные и пирамидальные ямки. Плоскодонные ямки соответствовали промежуточному положению дислокаций. Применяя послойное травление, можно определить пространственное распределение линейных дефектов. [c.160]
Для некоторых электродов необходима дополнительная химическая или электрохимическая полировка. С этой целью в открытый стаканчик наливают полировочный раствор, опускают электрод и инертный катод. Свинцовый электрод полируют в растворе состава 80 мл бидистиллята, 315 мл СНдСООН (ледяная), 60 г Hз OONa при этом плотность анодного тока 0,1—0,15 А/см . После полирования электрод промывают большим количеством бидистиллята и ставят в установку. Электрод из индия полируют в растворе, содержащем 550 г ЫН45 Оз в 1 л концентрированной HNOз. Электрод затем промывают бидистиллятом. [c.252]
Оксид Сг. О.) используется в качестве абразивного материала для тонкой полировки металлических изделий (паста ГОИ), поскольку он обладает высокой твердостью и может быть приготовлен в виде очень мелкодисперсного порошка, например, путем термического разложения (ЫН4)2Сг20,. Благодаря интенсивному зеленому цвету и химической инертности на воздухе СГ2О3 применяется также в качестве масляной краски (хромовая зелень). В качестве пигментов красок используют также хроматы свинца и цинка, а вольфрамовые бронзы служат пигментами лаков. Хромокалиевые квасцы или сульфат хрома (+3) используют в кожевенной промышленности для дубления кожи ( хромовая кожа), а также в качестве протравы при крашении. [c.349]
Лаборатория,предназначенная для выполнения практикума, должна быть соответствующим образом оборудована. В ней необходимо организовать специализированные участки вакуумный участок с газовой горелкой для стеклодувных и кварцедувных работ участок травления с местной вытяжной вентиляцией термический участок, в котором сосредоточены печи для одно- и двухтемпературного синтеза, диффузии и других работ, требующих применения высоких температур участок механической шлифовки и полировки образцов участок физико-химических методов анализа, где расположены пирометрические установки, аппаратура для изучения давления диссоциации и т. п., а также участок физико-химических исследований и электрофизических измерений, где проводится изучение микроструктуры, измерение микротвердости, определение удельного сопротивления, термо-э.д.с., изучение вольт-амперных, вольт-емкостных характеристик и т. п. [c.4]
Методика приготовления образцов. Образцы для приготовления иикрошлифов выбирают из той части слитка, которая представляет в данном исследовании наибольший интерес. Изготовление микрошлифа проводится в определенной последовательности. Шлифовкой выравнивают поверхность среза или излома. Эту операцию производят на абразивных кругах или шлифовальной бумаге с последовательно уменьшаюш,ейся зернистостью. При переходе от более грубой бумаги к более тонкой шлиф очищают каждый раз от наждачной пыли и поворачивают на 90 . Затем шлифуют на очередном номере наждачной бумаги до тех пор, пока не сотрутся следы предыдущей обработки. Обычно шлифовку проводят на 4—5 номерах шлифовальной бумаги. После тонкой шлифовки образец очищают от пыли, промывают и проводят механическую полировку (возможна также химическая или электролитическая полировка). Полировка также может быть осуществлена на специальном полировальном станке или вручную. Для этого на стекло кладут кусок фетра или диск станка обтягивают фетром (сукном), который смачивают полировальной жидкостью. Последняя представляет собой мелкодисперсные взвеси в воде одного из окислов А12О,,, СггОд, РеаО..) и т. п. При полировке не следует сильно нажимать на образец. Заканчивают полировать тогда, когда поверхность образца становится зеркальной, а под микроскопом не видны риски отшлифовки. После полировки шлиф промывают водой, обезжиривают спиртом, эфиром или ацетоном и высушивают. [c.50]
Травление образцов увеличивает контраст между фазами, обнаруживает бловдость в структуре, позволяет охарактеризовать взаимное расположение отдельных зерен. Выбор травителя определяется обычно экспериментально на основе химической природы составляющих фаз. Существует несколько способов нанесения травителя на шлиф. При одном из них полированную поверхность погружают в сосуд с травите-лем. При этом необходимо перемешивание, чтобы травление происходило равномерно и продукты травления не оседали на шлифе. Этот метод требует большого расхода реактивов. При других способах травящие реагенты наносят из капельницы на полированную поверхность или втирают в нее ватой. Время действия травителя определ51Ют опытным путем, просматривая шлиф под микроскопом. Визуально это определить нельзя, так как некоторые сплавы сохраняют блестящую поверхность и в травленном виде. Недотравленные образцы снова полируют в течение 1—3 мин, а затем травят более продолжительное время. Если шлифы были приготовлены заранее, то перед травлением их поверхность активизируют кратковременной полировкой. Приготовление шлифов для изучения микротвердости производится таким же образом. Микротвердость измеряют на травленных образцах, причем выбирают такой травитель, который характеризуется меньшей скоростью взаимодействия с поверхностью образца. [c.51]
Химическая полировка кремния. Травлению для выявления дислокаций должна обязательно предшествовать химическая полировка, в процессе которой удаляется поверхностный слой и получается зеркальная поверхность, на фоне которой четко выявляется дислокационная сгруктура монокристалла кремния. Полирование поверхности можно проводить в указанных травителях в течение 40—50 с. Можно использовать боле е мягкий травитель с добавлением уксусной кислоты состава HNOз HF СН3СООН = 3 2 2. Травление проводить Е тёчённе 2—3 мин. Образцы после травления тщательно промывают дистиллированной водой и высушивают. [c.107]
Двуокись — глушитель эмалей, придает им белый цвет и непрозрачность. Эмали с 4% ггОа высокостойки против действия растворов и щелочей при повышенной температуре. Используется в производстве высококачественных оптических, термостойких, химически стойких стекол и хрусталя. Применяется в производстве радиокерамики. Тонкодисперсная (до 0,3 мк) используется для полировки оптических стекол и подложек в производстве эпитаксиальных полупроводниковых слоев [72, 73]. [c.307]
Величина, внешнего перемагничивающего поля, при котором происходит зарождение нового домена в ферромагнетике, так называемая коэрцитивная сила (см. гл. VI), чувствительна к совершенству и размерам образца. У чистого железа коэрцитивная сила обычно составляет 0,01—1 Э. Теоретическая же величина при 25° С равна 560 Э. У толстых ЙК она не отличается от коэрцитивной силы обычных материалов. В совершенных участках монодом(енного НК железа она оказалась равной 504 Э, что лишь на 10% ниже теоретической величины. Коэрцитивная сила непостоянна вдоль длины образца и изменяется при нагреве, сопровождающемся изменением его формы, а также после химической полировки. [c.498]
Хорошо известно, что приготовление полупроводниковых электродов не обходится без химического или электрохимического травления [6]. Его основная цель удалить с полупроводника поверхностные загрязнения и дефекты и в первую очередь — так называемый нарушенный слой, возникающий на образце в результате его механической обработки (резка, шлифовка, полирование) и содержащий множество структурньгх макро-и микродефектов, искажающих присущие данному полупроводнику электрические свойства. К сожалению, для алмаза не существует удобного способа химического травления. (Правда, в нем обычно не возникает особой нужды, потому что полировка алмаза может проводиться без применения абразива и, по-видимому, не сопровождается образованием нарушенного слоя и ухудшением полупроводниковых характеристик поверхности алмаза. Алмаз полируют на чугунном круге под действием развивающегося нагрева поверхность алмаза графитизируется, а графит испаряется.) [c.26]
Образец с припоем помещали в специальную установку, обеспечивающую нагрев, освещение и горизонтальное положение образца. Образец размером 40 X 40 X 3 из меди М1 был фрезерован по краям и правлен на прессе. В центре образца по стороне 40 X 40 снизу сверлили глухое отверстие для горячего спая термопары. Поверхность образца обрабатывали наждачным полотном (№ 280 перпендикулярно к направлению съемки), травлением (в 10%-ном водном растворе персульфата аммония) и полировкой. Перед загрузкой в печь поверхность образца обезжиривали и на нее помещали припой в виде компактного куска, объемом 64 и 300—400 мм флюса. При загрузке в печь образец укладывали на подложку из нержавеющей стали, расположенную на уровне съемки и нагретую до температуры пайки. Температуру образца замеряли хромель — алюмелевой термопарой. При температуре несколько ниже температуры начала плавления припоя включали кинокамеру и на секундомере фиксировали начало съемки. Контактный угол смачивания и линейный размер капли в процессе растекания определяли при проектировании кинопленки на экран (X 6). По времени, фиксированном на секундомере, и записи температуры определяли температуру в контакте медной пластины и припоя в различные моменты его растекания. Для исследования были выбраны три припоя РЬ (С-000), практически не взаимодействующий с медью и цинком, вытесняемым из реактивных флюсов 8п (ОВЧ-000)— способное к химическому взаимодействию с медью и контактно-реактивному плавлению с цинком припой П0С61 эвтектического состава (61% 8п, РЬ — остальное, Гпл = 183° С), слабее взаимодействующий с медью, чем олово. [c.81]
Ковар, защищенный никелевым покрытием 15 мкм. а также латунь марок Л62 и Л68, защищенная гальваническим никелем 12 мкм и более, с последующей пропиткой гидрофобной жидкостью ГКЖ94, анодированный алюминий с последующей пропиткой хромпиком и церезином в субтропиках обладают достаточной стойкостью. Изготовление электронно-лучевых приборов из сплава 29НК (ковара) для субтропического климата является неприемлемым. Все детали, изготовленные из сплава 29НК с предварительной химической полировкой, за 7 месяцев испытаний подверглись сильной коррозии (70—80% поверхности). [c.81]
Основные компоненты зубной пасты следующие абразивные, связующие, загустители, пенообразующие. Абразивные вещества обеспечивают механическую очистку зуба от налетов и его полировку. В качестве абразивов чаще всего применяют химически осажденный мел СаСОз. Установлено, что компоненты зубной пасты способны влиять на минеральную составляющую зуба и, в частности, на эмаль. Поэтому в качестве абразивов стали применять фосфаты кальция СаНР04, Саз(Р04)2, Са2Р20г, а также малорастворимый полимерный метафосфат натрия (ЫаРОз) с. Кроме того, в качестве абразивов в различных сортах паст применяют оксид и гидроксид алюминия, диоксид кремния, силикат циркония, а также некоторые органические полимерные вещества, например метилметакрилат натрия. На практике часто используют не одно абразивное вещество, а их смесь. [c.104]
Невозобновляющаяся поверхность электрода легко загрязняется продуктами электродной реакции, поэтому для получения нравильньк и воспроизводимьк результатов ее нужно периодически очищать. Иногда очистку необходимо проводить перед регистрацией каждой вольтамперограммы. Пригодны механические (полировка тонкой наждачной и фильтровальной бумагой), химические (обработка кислотой или каким-то другим реагентом) и электрохимические (выдерживание электрода в течение некоторого времени нри высоком положительном или отрицательном потенциале) методы очистки. Лучший способ выбирают эмпирически. По- [c.182]
Для получения спектра НПВО образец прижимается к рабочей поверхности призмы или элемента многократного отражения (рис. 4.7,6), через которую излучение посредством специальной оптической системы направляется в спектрофотометр. Призма изготовляется из материала с высоким показателем преломления, такого, как Ag l, KRS-5 или Ge (табл. 4.1). Материал призмы должен быть прозрачным при толщине до нескольких сантиметров, прочным, поддаваться полировке до высокого класса и химически инертным. [c.100]
Этот процесс может использоваться как завершаюш,ая стадия очистки для полировки или, напротив, как первая стадия осаждения фосфора в зависимости от размеров пруда и количества добавляемых химических веществ. Почвенные пруды типа показанного на рис. 10.20 функционируют как большие вторичные отстойники для химических флокул, образовавшихся при добавлении химических веществ. Если такой пруд достаточно большой, то он будет действовать как пруд с водорослями. В таком случае добавление химических осадителей в поступающий в него сток может не понадобиться. Однако может возникнуть необходимость в проведении химического осаждения для отделения водорослей от воды на выходе из пруда. [c.412]
Известно несколько способов травления кристаллов ИАГ в смеси газов 5р4 и 5Рб, химическая полировка и травление кри сталлов в смеси серной и ортофосфорной кислот при температура 473—573 К. Последний процесс характернзуетсй выделением вред ных паров кислот. Кроме того, во избежание обезвоживания орто-фосфорной кислоты и ее перехода в пирофосфорную травление проводят в присутствии паров воды, что усложняет технологический процесс. [c.222]
chem21.info
методы, виды и способы обработки металлических изделий
Недостатки традиционных видов полировки металла
Первые три из перечисленных способов обработки поверхности металлов имеют ряд ограничений применения. Основным ограничением для ряда промышленных предприятий является невозможность автоматизации при использовании механического, химического или электрохимического методов обработки поверхностей изделий в больших партиях массового производства.
Затруднения использования традиционных видов полирования металла имеют как экономические, так и технологические причины. Экономические трудности связываются с высокой стоимостью производственных роботов и станков с ЧПУ. Технологические же причины трудностей использования традиционных видов финишной обработки металлов связаны с трудностями построения полностью автоматизированного процесса производства. Вынужденное использование ручного труда на этапе полирования изделий, активации поверхности или ее очистки не позволяет наладить бесперебойную работу промышленных автоматизированных линий. Нередко из-за использования устаревших методов обработки металлов производственная линия принимает форму конвейера, что значительно удорожает производство и в итоге отрицательно сказывается на конкурентоспособности производимой продукции.
Сравнение видов полировки металла
Механическая полировка | Химическая полировка | Электро-химическая полировка | Электролитно-плазменная полировка | |
Производительность | Средняя | Низкая | Средняя | Высокая |
Ограничение по геометрии | Простой профиль | Сложный профиль | Сложный профиль | Сложный профиль |
Изменение материала | Подверженность внедрению инородных частиц | Неравномерность обработки, травление | Плохая обработка плоских поверхностей | Возможно упрочнение материала |
Сложность обработки | Средняя | Средняя | Высокая | Средняя |
Возможность автоматизации | Нет | Нет | Есть | Есть |
Затраты на материалы | Высокие | Высокие | Высокие | Низкие |
Срок амортизации установки | 25 лет | 5 лет | 20 лет | 25 лет |
Занимаемая произв. пл. | Малая | Средняя | Средняя | Средняя |
Экологичность | Низкая | Низкая | Низкая | Высокая |
Пожароопасность | Низкая | Высокая | Средняя | Низкая |
Энергопотребление | Среднее | Низкое | Высокое | Высокое |
Квалификация работников | Высокая | Средняя | Средняя | Средняя |
Широкое внедрение в промышленность более производительной электролитно-плазменной полировки металла позволит со временем практически везде заменить токсичный электрохимический метод обработки. Его преимуществами, в сравнении с другими способами полировки поверхностей, являются высокая производительность и эффективность, соблюдение экологической чистоты окружающей среды, высокие качества и скорость выполняемых операций, невысокая стоимость.
Электролитно-плазменный метод полировки поверхностей является экологически чистым и удовлетворяет санитарным нормам, для очистки отработанного электролита не требуются специальные очистные сооружения.
Методы полирования поверхности металла путем комбинирования различных способов и видов обработки поверхностей
Часто полировке подвергаются изделия без предварительной поверхностной обработки с неподготовленной, достаточно шероховатой поверхностью, имеющей грубый рельеф, что влечет за собой необходимость длительной электролитно-плазменной обработки, которая сопровождается снятием значительного слоя металла, и ведет к перерасходу электроэнергии.
Кроме того, в процессе обработки грубой разветвленной поверхности наблюдается явление, когда плотность тока на первой стадии обработки иногда вдвое выше, чем на заключительной стадии. Это связано с тем, что первоначальная площадь шероховатой поверхности, контактирующая с электролитом, по-видимому, вдвое больше, чем получаемая в результате обработки.
На практике полирование изделий лучше осуществлять в два этапа, на первом провести очистку и обезжиривание поверхности, а на втором этапе – собственно полировку. Очистка деталей перед полированием необходима потому, что при изготовлении изделий из металлов литьем, либо при их термообработке, даже в нейтральных средах не удается полностью избежать соприкосновения поверхности с окислительной средой (например, воздухом) в области высоких температур, когда происходит поверхностное окисление металла. С целью очистки перед полированием применяют такие виды обработки поверхностей как:
Виды обработки поверхности металла после газоплазменной резки
Сглаживание шероховатостей поверхности, полученной после такого популярного вида обработки металла плазмой как газоплазменная резка, не обязательно осуществлять путем срезания выступов. Предварительная обработка может быть проведена путем поверхностного пластического деформирования. В ряде случаев механические методы обработки поверхностей пастами состоят не в срезании выступов, а в их разминании, для чего в состав паст входят специальные смазывающие, химически активные, поверхностно-активные вещества, разупрочняющие поверхность и мелкодисперсные окисные частицы, например, инертная окись хрома.
Полировка металлических изделий электрольтно-плазменным методом с предварительной подготовкой
Для экономии электроэнергии целесообразно использовать технологию электролитно-плазменной полировки в два этапа, когда на первом этапе сглаживается грубый рельеф поверхности с помощью различных энергосберегающих способов обработки поверхностей, а затем на втором этапе применяется финишная кратковременная электролитно-плазменная полировка.
Например, при полировке деталей из нержавеющей стали, которая является пластичной и достаточно мягкой, на первом этапе могут применяться следующие способы обработки поверхности:
Последующая электролитно-плазменная полировка изделий может проводиться в 5%-м водном растворе сульфата аммония при температуре 80°C.
Методы обработки металла перед электролитно-плазменной полировкой
Способы обработки металла с помощью зачистки
Если исходный образец, поверхность которого предварительно обработана грубой шкуркой зернистостью 500 мкм, полируется до зеркального блеска в течение 5–6 минут со снятием слоя металла 0,05 мм, то образцы, обработанные до матового состояния шкуркой зернистостью 50–80 мкм, полируются в два раза быстрее за время менее 3 минут, и при этом снимается слой металла толщиной всего 0,02–0,03 мм. Экономия электроэнергии при использовании предварительной обработки поверхности шкуркой составляет около 40%.
Виды обработки металла с помощью крацевания
Весьма эффективна также предварительная обработка металлическими щетками грубо шлифованной или обработанной резцом поверхности. По-видимому, рельеф поверхности при такой обработке выравнивается за счет пластической деформации металла, а частично за счет крацевания, т.е. стирания, царапания металла. Также снимается окисная пленка, препятствующая равномерной полировке изделия в тех случаях, когда оно выполнено сваркой или подвергалось высокотемпературной термообработке.
Методы обработки металла с помощью травления
Неплохие результаты получены при химическом травлении, особенно образцов, которые подвергались термообработке, так как при этом на стали образуется окалина, трудно снимаемая электролитно-плазменной обработкой в течение 15 и более минут. Травление таких образцов в растворах серной и соляной кислот создает шероховатую, чистую от окалины поверхность без дефектов. Последующая обработка образцов в сульфате аммония при напряжении 260 В в течение 4 минут позволяет получить блестящую поверхность.
plasmacraft.ru
Раствор и способ химического полирования поверхности нержавеющей стали
Изобретение относится к химической обработке металлов, в частности к химическому полированию поверхностей из нержавеющих сталей. Сущность изобретения: раствор для химического полирования поверхности нержавеющей стали содержит: соляная кислота 0,5 - 5,0 моль, азотная кислота 0,005 - 1,0 моль, фосфорная кислота 0,005 - 1,0 моль, гидроксибензойная кислота 0,001 - 5,0 г, первичный амин, включающий более 10 атомов углерода, 0,001 - 1,0 г и вода - до 1 л. Первичный амин имеет число атомов углерода 11 - 20, предпочтительно 12 - 18. Раствор дополнительно содержит 0,5 моль/л хлорной кислоты или ее растворимых солей, а также 0,5 г/л добавки, способной разлагать азотистую кислоту, выбранную из мочевины и ее производных. Способ химического полирования поверхности нержавеющей стали включает обработку поверхности вышеуказанными растворами при температуре 20 - 65oC. 2 c. и 5 з.п. ф-лы.
Изобретение относится к области химической обработки металлов. Предметом настоящего изобретения является состав ванн для химической полировки поверхностей из нержавеющей стали.
Химическая полировка металлических поверхностей является хорошо известным методом. Она заключается в обработке металлических поверхностей, подлежащих полированию, при помощи окисляющих ванн. Для химической полировки аустенитных нержавеющих сталей применяют обычно ванны, содержащие смесь хлороводородной, фосфорной и азотной кислот в водном растворе [1] Для улучшения качества полировки обычным является введение в эти ванны соответствующих добавок, таких как поверхностно-активные агенты, регуляторы вязкости и агенты для придания блеска. Известен состав ванны для химической полировки поверхностей из нержавеющей стали [2] содержащий в водном растворе смесь хлороводородной кислоты, азотной кислоты и фосфорной кислоты, регулятор вязкости, выбираемый среди водорастворимых полимеров, поверхностно-активное вещество и сульфосалициловую кислоту в качестве агента для придания блеска. Эти известные ванны для полировки имеют особенность атаковать металл с очень большой скоростью. Обработка для полирования поверхности из нержавеющей стали при помощи таких ванн не может обычно превышать несколько минут, чтобы не вызвать местной коррозии. Эта большая скорость воздействия известных ванн для полировки является недостатком, т.к. она делает их непригодными в некоторых случаях, особенно для полировки внутренней поверхности перегородок в баках больших размеров, таких как перегонные кубы (котлы), автоклавы или кристаллизаторы. Поскольку время, необходимое для заполнения и опорожнения таких баков, обычно значительно превышает продолжительность обработки для оптимальной химической полировки, то действительно становится невозможным получить однородную полировку перегородки, причем некоторые области последней являются недостаточно полированными, другие же являются сильно корродированными. Большая скорость воздействия известных ванн для химической полировки делает, с другой стороны, трудным контроль за полировкой. Известны также ванны для химической полировки с очень медленным воздействием, которое тем самым избегает указанных выше недостатков. Эти известные ванны содержат в водном растворе смесь хлороводородной, азотной и фосфорной кислот, сульфосалициловую кислоту, алкилпиридинийхлорид и метилцеллюлозу. Эти известные ванны для полировки с медленным воздействием задуманы для работы при температурах, по меньшей мере равных 40oC, а обычно 45 100oC [3] Целью изобретения является разработка ванн, предназначенных для осуществления медленного и эффективного химического полирования поверхностей из нержавеющей стали при рабочих температурах, меньших 50oC. Следовательно, изобретение относится к ваннам для химического полирования поверхностей из нержавеющей стали, содержащим в водном растворе смесь хлороводородной кислоты, азотной кислоты и фосфорной кислоты, гидроксибензойную кислоту, в случае необходимости замещенную, и растворимый в воде амин. В ваннах по изобретению гидроксибензойная кислота служит в качестве агента для придания блеска. Она может быть незамещенной, такой как салициловая кислота, или замещенной, такой как сульфосалициловая кислота. Салициловая кислота является предпочтительной. Амин может выбираться среди первичных аминов, вторичных аминов и третичных аминов. Предпочитают амины, молекула которых содержит более 10 атомов углерода, например 11 20 атомов углерода. Первичные алкиламины, содержащие от 11 до 16 атомов углерода в своей молекуле, являются предпочтительными. Ванны в соответствии с изобретением могут содержать смесь аминов. Оптимальное содержание амина зависит от природы выбранного амина. В общем случае оно находится между 0,001 и 1 г на литр водного раствора. В частном варианте осуществления изобретения водный раствор ванны содержит помимо амина добавку, выбираемую среди хлорной кислоты и растворимых в воде солей хлорной кислоты. Оптимальное содержание этой добавки 0,001 0,5 моль на литр водного раствора. В другом варианте осуществления ванн в соответствии с изобретением водный раствор содержит растворимую в воде добавку, способную разлагать азотистую кислоту. Эта добавка имеет назначение разлагать по меньшей мере часть азотистой кислоты, которая образуется в ходе полировки стальной поверхности вследствие окисления ионов двухвалентного железа, выделяемых в ванну в ходе полировки. Она выбирается предпочтительно среди мочевины и ее производных, таких как тиомочевина и диалкилмочевины, а ее оптимальное содержание 0,01 5 г на литр водного раствора. Ванны, соответствующие этому варианту осуществления изобретения, особенно пригодны для обработок полированием, в которых отношение поверхности контакта с ванной и объема последней превышает 10 м-1. Весовые количества, соответствующие различным компонентам ванн в соответствии с изобретением, зависят от вида нержавеющей стали, подвергаемой полированию, а также от условий полирования, особенно от профиля стального изделия, подвергаемого полированию, от его объема, от объема ванны, от его температуры и от встряхивания, которому его подвергают, в случае необходимости. Тем самым, они должны определяться в каждом частном случае в результате обычных опытов в лаборатории. Примеры ванн, соответствующих изобретению, пригодных для полировки аустенитных нержавеющих сталей, содержащих хром и никель, при температурах 20 50oC, содержат на литр водного раствора: 0,5 5 моль хлороводородной кислоты (предпочтительно 1 3 моль), 0,005 1 моль азотной кислоты (предпочтительно 0,05 0,5 моль), 0,005 1 моль фосфорной кислоты (предпочтительно 0,01 0,5 моль), 0,001 5 г гидроксибензойной кислоты, замещенной или незамещенной (предпочтительно 0,005 0,3 г, в случае незамещенной кислоты), 0,001 1 г амина (предпочтительно 0,005 0,300 г), 0 0,5 моль добавки, выбираемой среди хлорной кислоты и растворимых в воде солей хлорной кислоты (предпочтительно 0,001 0,2 моль), 0 5 г добавки, способной разлагать азотистую кислоту (предпочтительно 0,01 и 5 г). Ванны для полировки в соответствии с изобретением могут, в случае необходимости, содержать добавки, обычно присутствующие в известных ваннах для химической полировки металлов, например поверхностно-активные агенты, спирты и регуляторы вязкости. Они могут, в частности, содержать растворимое в воде абиетиновое соединение, которое является химическим соединением, содержащим абиетильный радикал с общей формулой:

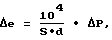


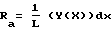
Формула изобретения
1. Раствор химического полирования поверхности нержавеющей стали, содержащий соляную, азотную, фосфорную и гидроксибензойную кислоты, а также аминсодержащее вещество, отличающийся тем, что в качестве аминсодержащего вещества он содержит первичный амин, включающий более 10 атомов углерода, при следующем соотношении компонентов: Кислота соляная, моль 0,5 5,0 азотная, моль 0,005 1,0 фосфорная, моль 0,005 1,0 гидроксибензойная, г 0,001 5,0 Первичный амин, г 0,001 1,0 Вода До 1 л 2. Раствор по п.1, отличающийся тем, что он содержит первичный амин с числом атомов углерода 11 20. 3. Раствор по п.1, отличающийся тем, что он содержит первичный амин с числом атомов углерода 12 18. 4. Раствор по п.1, отличающийся тем, что он дополнительно содержит до 0,5 моль/л хлорной кислоты или ее растворимых солей. 5. Раствор по п.1, отличающийся тем, что он дополнительно содержит до 0,5 г/л добавки, способной разлагать азотистую кислоту. 6. Раствор по п.5, отличающийся тем, что добавка, способная разлагать азотистую кислоту, выбрана из мочевины и ее производных. 7. Способ химического полирования поверхности нержавеющей стали, включающий обработку водным раствором, содержащим соляную, азотную, фосфорную и гидроксибензойную кислоты, а также аминсодержащее вещество, при повышенной температуре, отличающийся тем, что обработку ведут раствором по любому из пп.1 6 при 20 65oС.www.findpatent.ru