- химическую
- электрохимическую
- в сельской местности Швеции скорость разрушения стали составляет 8 мкм в год, цинка — 0,8 мкм в год;
- для города эти цифры составляют 30 и 5 мкм в год соответственно.
- Цинк. Обеспечивает электрохимическую защиту, максимально устойчив к ржавчине и покрывает во время резки профнастила край листа. Оксидная пленка надежно защищает материал, позволяя сверлить его и резать без возникновения коррозии в будущем. Цинковое покрытие используют повсеместно, это гарант качества и долговечности профнастила;
- Полиуретан. Краска хорошо противостоит неблагоприятной внешней среде, защищает лист от дождя и града, переносит солнечные лучи и резкие температурные перепады. Использовать полиуретановое покрытие можно для забора и других сооружений, подверженных частому механическому воздействию;
- Алюцинк. Покрытие состоит из смеси цинка и алюминия с применением кремния и некоторых других элементов. Это более стойкий вариант, чем просто цинк. Алюцинковый профлист лучше справляется с высокими и низкими температурами, медленнее портится и почти не подвергается коррозии;
- Полиэстер. Это покрытие не защитит профнастил от механического повреждения, но придаст ухоженный вид поверхности, а также убережет от влаги и солнца. Коррозия в этом случае возможна при повреждении листа. Краска недорогая, поэтому ее приобретают, если не предвидится серьезных нагрузок на материал;
- ПВДФ. Если покрыть профнастил этой краской, использовать его можно будет в любых видах строительства. Покрытие очень надежное, подходит для использования в любом регионе, так как отлично справляется и с жарой, и с морозом. Его не испортит повышенная влажность или агрессивная среда. Высокая степень защиты поливинилденфторид-акриловой краски позволяет избежать коррозии и других повреждений покрытия;
- Пластизол. Это покрытие одно из самых толстых и прочных. Пластизол намного крепче полиэстера, имеет тиснение. Производители предлагают множество расцветок и фактур, найти подходящий вариант для забора или кровли не составит труда. Профнастил с пластизолом не боится осадков, поверхность способна выдержать повышенную влажность и механические повреждения. Единственный недостаток, который имеет данное покрытие, это постепенное разрушение под прямыми солнечными лучами. Краска блекнет на солнце, под воздействием высокой температуры пластизол портится и теряет свои первоначальные свойства.
- Опоры пришли в негодность;
- Размылся грунт;
- В процессе строительства использовались некачественные материалы;
- Проект сооружения не отвечал требованиям;
- Возникла коррозия.
- 1 Очистите поверхность от грязи. Перед тем, как предпринимать дальнейшие действия, поверхность стали необходимо полностью очистить. Способ очистки зависит от того, что именно необходимо удалить с поверхности.
- Для удаления грязи, жира, масла или пятен краски необходимо использовать слабую кислоту, горячую щелочь, либо биологическое чистящее средство.
- Для очистки от асфальта, эпоксидной смолы, винила, сварочной окалины надо использовать пескоструйную или другую абразивную обработку.
- 2 Вытравите ржавчину. Это делается при помощи соляной или горячей серной кислоты; кислоты удаляют ржавчину и окалину.
- В некоторых случаях абразивной чистки бывает достаточно для удаления ржавчины, в других необходимо сочетание такой обработки с вытравливанием кислотой. Иногда используется абразив с крупными частицами, например, сталь обдувается струей воздуха с крупной дробью.
- 3 Поместите металл в флюс. В данном случае в качестве "флюса” используйте раствор хлорида аммония цинка, который позволяет удалить оставшуюся ржавчину и окалину и защищает сталь от новой ржавчины до его оцинковывания.
- 4 Погрузите сталь в расплавленный цинк. Ванна с расплавленным цинком должна содержать не менее 98 процентов цинка и находиться при температуре 435-455 градусов Цельсия (815-850 градусов Фаренгейта).
- При погружении стали в цинковую ванну железо реагирует с цинком, и в поверхностных слоях образуется целый набор сплавов, вплоть до чистого цинка на самой поверхности.
- 5 Медленно достаньте оцинкованную сталь из ванны с расплавленным цинком. Большая часть избыточного цинка стечет с детали; то, что останется, можно очистить ультразвуком или с помощью центрифуги.
- 6 Охладите оцинкованную сталь. Охлаждение остановит реакцию гальванизации, которая протекает лишь при повышенных температурах, когда сталь погружена в ванну с расплавленным металлом. Охладить сталь можно несколькими способами:
- Погрузите металл в пассивирующий раствор, содержащий гидроксид калия.
- Опустите сталь в воду.
- Охладите сталь на воздухе.
- 7 Осмотрите оцинкованную сталь. После того, как металл охладился, проверьте, хорошо ли выглядит покрытие, не отслоилось ли оно и достаточно ли оно толстое. Существует множество способов проверить качество цинкового покрытия на стали.
- Стандарты для горячего цинкования и проверки качества получившегося покрытия можно найти в ГОСТ 9.307-89[1].
- 1 Подготовьте сталь так же, как ранее к горячему цинкованию. Поверхность металла следует очистить от грязи и ржавчины перед началом процесса цинкования.
- 2 Приготовьте цинковый электролит. Как правило, это раствор сульфата цинка или цианида цинка.
- 3 Опустите сталь в электролит. Начнется реакция раствора с металлом, в результате которой на поверхности стали будет осаждаться слой цинка. Чем дольше сталь будет находиться в электролите, тем толще получится покрытие.
- Хотя данный метод и позволяет лучше контролировать толщину покрытия по сравнению с горячим цинкованием, он, как правило, не позволяет получить относительно толстые покрытия.
- 1 Подготовьте сталь так же, как для других методов цинкования. Очистите поверхность раствором кислоты или, в случае необходимости, пескоструйной обработкой и стравите ржавчину.
- 2 Поместите сталь в закрытый резервуар.
- 3 Плотно обложите сталь порошком цинка.
- 4 Нагрейте металл. При этом цинковый порошок расплавится, а при охлаждении на поверхности стали останется тонкое покрытие.
- Данный метод хорош для нанесения покрытия на детали сложной формы, поскольку покрытие получается однородным по толщине и в труднодоступных местах. Он хорошо работает также для относительно малых стальных деталей.
- 1 Подготовьте сталь так же, как и для других методов. Очистите поверхность от грязи и удалите ржавчину перед нанесением покрытия.
- 2 Напылите тонкое покрытие из расплавленного цинка.
- 3 Нагрейте металл для обеспечения надлежащей адгезии.
- Полученное данным методом цинковое покрытие более пластично и менее подвержено растрескиванию и отслоению, но обладает меньшим сопротивлением к образованию ржавчины под покрытием по сравнению с другими способами.
- Оцинкованную сталь можно дополнительно защитить от коррозии, покрасив ее краской, содержащей цинковую пыль. Краску на основе цинка можно использовать и вместо приведенных выше способов гальванизации.
- Покраска придает гальванизированной стали яркий блеск.
- Оцинкованная сталь обладает высоким сопротивлением коррозии со стороны бетона, извести, алюминия, свинца и, естественно, цинка.
- Гальванизация является одним из видов того, что называется катодной защитой, когда защищаемый металл действует как катод в электрохимической реакции, а защитный металл играет роль анода, то есть материал анода выполняет защитные функции, корродируя вместо основного материала[2]. Металл, покрытый расходуемым анодным слоем, нередко называют анодированным металлом.
- Оцинкованная сталь тяжелее поддается покраске по сравнению с неоцинкованной.
- Цинковое покрытие на гальванизированной стали подвержено коррозии со стороны кислот и щелочей (оснований). Особенно вредны в этом отношении серная и сернистая кислоты, которые могут образовываться при смешивании сероводорода и диоксида серы с дождевой водой (кислотный дождь), особенно если эта вода взаимодействует с мхом или лишаем. Дождевая вода может также вступать в реакцию цинковым покрытием, образуя карбонат цинка. С течением времени карбонат цинка становится хрупким и в конце концов отслаивается, в результате чего коррозии подвергаются внутренние слои покрытия или даже основной металл.
- Оцинкованная сталь имеет низкое сопротивление коррозии при контакте с любым другим металлом, кроме алюминия, свинца, олова или цинка. Она особенно подвержена коррозии при взаимодействии с железом, неоцинкованной сталью, медью, а также хлоридами и сульфатами, нередко содержащимися в цементе.
- Покрытая цинком сталь имеет пониженное сопротивление усталости, поскольку цинковое покрытие при нагреве значительно расширяется, а при охлаждении сжимается.
- Анодное оксидирование стали
- Оцинкованная сталь ржавеет ли
- Применение углеродистой стали
- Оцинкованная сталь окрашенная
- Сверление нержавеющей стали
- Виды нержавеющей стали и ее классификация
- Влияние легирующих элементов на свойства сталей
- Межкристаллическая коррозия
- Изготовление стропов из стальных канатов
- Марки коррозионностойкие стали
- Полированная сталь
Теория коррозии металлов. Почему ржавеют автомобили? Ржавеет ли сталь оцинкованная
Почему ржавеет кровля
Ржавые потёки на уложенной всего год-два назад металлочерепице – неприятный сюрприз для домовладельца. Однако не стоит пенять друзьям или специалистам, которые посоветовали использовать этот кровельный материал. Он действительно обладает массой достоинств и оптимален для российского климата, однако, как и любой другой, требует соблюдения технологии монтажа. Лучше всего подумать об этом заранее.
Многоликий саморез
Уж сколько раз твердили миру: в строительстве нет мелочей! Плохо размешанный раствор, не та грунтовка, непросушенные брёвна, да мало ли ещё примеров, когда извечное «авось пронесёт» становится причиной серьёзных проблем в ходе эксплуатации дома. «Слабое звено» настила кровель – саморезы. Говорят, привычка – вторая натура. Мы выбираем лучшие кровельные материалы, не жалеем на них денег, а на мелочах традиционно экономим, как будто это поможет серьёзно удешевить смету. В итоге затраты на премиальное покрытие оказываются напрасными, когда через несколько лет оно начинает ржаветь, а то и протекать.
Стальному кровельному крепежу приходится работать в условиях агрессивного воздействия атмосферы, поэтому применяются оцинкованные саморезы (есть также нержавеющие, но они примерно вдвое дороже). От толщины защитного цинкового слоя зависит срок службы всей кровли, поскольку коррозия самореза неизбежно распространится на кромку стального листа в месте, где он её пробил. Если на крепёж изначально было нанесено мало цинка, во время закручивания защитный слой может оказаться повреждённым. В результате и саморез, и кровельное покрытие начнут ржаветь под действием атмосферной влаги. Начавшись на кромке проделанного саморезом отверстия, коррозия распространяется в толще листа металлочерепицы. Со временем полимерное покрытие начинает отслаиваться от нее, корродирует уже сам лист. Через несколько лет последствия могут быть весьма печальны, а виной всему – маленькие саморезы.
Комментарий специалиста
Согласно ГОСТу, защитный слой цинка на них не должен быть тоньше 12 микрон. Однако проверить это самостоятельно не представляется возможным, а потому следует использовать только брендованные саморезы известных марок, качество которых подтверждено испытаниями. «Согласно результатам тестов наших польских партнёров, компании Info-GLOBAL, на большинстве наводнивших российский рынок немаркированных саморезов цинковое покрытие оказалось не толще 1,28-3,6 микрона, то есть примерно в 3,5-10 раз меньше минимально допустимого слоя. Показательно, что на упаковках при этом обычно значится 12 микрон. Не всегда соответствует стандарту и маркированная продукция. Так, на протестированных образцах компаний «ТехКреп», Daxmer, «Московская крепёжная компания» и Gunnebo толщина цинкового слоя составила соответственно 6,39, 8,29, 5,48 и 8,63 микрона. Из 14 исследованных образцов требованиям ГОСТа соответствовала лишь продукция AR2, на которой обнаружилось более 13 микрон цинка», – делится печальным опытом Андрей Мальцев, руководитель департамента кровельных систем Группы компаний Металл Профиль, крупнейшего российского производителя фасадных и кровельных систем. По мнению специалиста, результат весьма неутешительный, ведь исследовалась продукция, которую чаще всего можно встретить на строительных рынках и в специализированных магазинах.
Напомним: скорость коррозии цинка в агрессивно-влажной среде составляет 1,2-2 микрона в год. Это значит, что некачественный саморез начнёт ржаветь уже через 1-2 года. В лист кровельного покрытия вворачивается примерно 8 саморезов на квадратный метр – это 8 очагов коррозии на ту же площадь. Скорее всего, в такой ситуации менять металлочерепицу придётся уже через 5 лет.
Второе слабое звено некачественного кровельного самореза – прокладка. По стандарту она должна быть изготовлена из этиленпропиленовой резины (EPDM) и запрессована в металлическую шайбу. Обычная резина на морозе и под палящим солнцем быстро растрескается и потеряет эластичность. В результате кровля в местах крепления даст течь, а из-за постоянной сырости её коррозия начнётся гораздо раньше предусмотренного свойствами покрытия срока. Толщина прокладки также важна. Тонкая не обеспечит надёжной гидроизоляции, особенно если учесть, что часть саморезов при монтаже всегда оказывается ввёрнута под небольшим углом.
Жертвы «болгарки»
На околостроительных форумах можно найти немало тем, посвящённых важности соблюдения техники безопасности при работе с этим опасным инструментом. Однако список его жертв не заканчивается нерадивыми пользователями. При применении углошлифовальной машины не по назначению пострадать может и обрабатываемый материал, например – металлочерепица или профнастил.
Комментарий специалиста
«Использование «болгарки» для раскроя кровельных материалов из стали с полимерным покрытием, к сожалению, является повсеместной практикой. При этом подобные действия являются грубейшим нарушением технологии и поводом для немедленной дисквалификации кровельщика. Вращающийся со скоростью порядка 6 тысяч оборотов в минуту отрезной круг выжигает вблизи кромки не только полимерное покрытие, но и защитный цинковый слой. В результате отрезная кромка металлочерепицы становится очагом скорой коррозии», – объясняет Андрей Мальцев (Группа компаний Металл Профиль). Для раскроя листов специалист настоятельно рекомендует использовать просечные ножницы. Также можно приобрести вместо них специальную насадку на дрель, выполняющую схожие функции. Оба инструмента позволяют резать металл толщиной до 0,8 мм, чего достаточно для раскроя металлочерепицы. После резки листов кровельного покрытия обрезные кромки рекомендуется обработать ремонтной эмалью соответствующего оттенка. Её же применяют и для закрашивания царапин или повреждений поверхности кровельного покрытия.
Как выбирать металлочерепицу
Мы специально начали с рассмотрения наиболее распространённых ошибок монтажа, которые могут привести к появлению коррозии на новенькой кровле. Однако и сам материал для неё следует выбирать осознанно, поскольку на любом рынке, как известно, встречается не только качественная продукция.
Первое, на что следует обратить внимание – это гарантия производителя. Например, самым популярным из применяемых в России материалов для производства металлочерепицы, является относительно недорогая оцинкованная сталь с покрытием на основе полиэстера. Обычно на такую продукцию даётся один год гарантии, поэтому стоит поискать более привлекательные варианты. Так, на продукцию из стали с покрытием NormanMP (улучшенный полиэстер) производитель даёт десятилетнюю гарантию. «Мы гарантированно выдерживаем толщину стального листа не менее 0,5 мм, толщину цинкового слоя не менее 140 г/м² и толщину полимерного покрытия не менее 25 мкм. Такие характеристики часто заявляются на рынке, но не всегда соответствуют реальности. Мы в своей продукции уверены и поэтому даём на неё 10 лет гарантии», – объясняет Андрей Мальцев (Металл Профиль).
Кровля Металл Профиль.
Также следует заметить, что в мировой практике с каждым годом усиливается тенденция к замещению полиэстера более устойчивыми покрытиями на основе полиуретана. Сегодня такая металлочерепица производится и в России. Например, это металлочерепица из стали с покрытием PURETAN, гарантия на которую составляет 12 лет, и более дорогая, но и имеющая ещё лучшие качественные характеристики металлочерепица из стали с 50 мкм покрытием Colorcoat Prisma и 20-25-летней гарантией. Покрытия на основе полиуретана не только более эффективно защищают металл от коррозии и механических повреждений, они ещё и более долговечны, а также дают огромный выбор оттенков.
Как не допустить ржавых потёков на фасадах
Кровельная система.
Ещё один объект пристального внимания в связи с коррозией элементов кровельной системы – водостоки. На состояние самой кровли ржавые водостоки никак не влияют, но выглядят крайне неприглядно, а ржавые потёки от них способны испортить поверхность любого фасада.
Если желоба изготовлены из простой оцинковки, то срок их службы в любом случае окажется меньше, чем у качественной металлочерепицы, а сменить водостоки без демонтажа кровельного покрытия проблематично. Поэтому предпочтение лучше отдать долговечной продукции из оцинкованной стали с полимерным покрытием, которая имеет высокую степень устойчивости к коррозии и атмосферным осадкам, не боится механических повреждений, обладает эстетичным внешним видом и не выцветает на солнце. Да и выглядят окрашенные водостоки куда привлекательней, чем простая оцинковка. Что касается пластиковых водостоков, то при первом же морозе они могут потрескаться.
Комментарий специалиста
Как и в случае с кровельными саморезами, креплению водостоков также нужно уделить особое внимание. «К нам периодически поступают жалобы покупателей на некачественные держатели водостоков, которые очень быстро ржавеют. Особенно печальная ситуация с этой продукцией сложилась на юге России: в целях экономии держатели желоба приобретаются кровельщиками не в комплекте поставщика, а отдельно, у небольших производителей. Для заказчика экономия получается копеечной, при этом на металле может быть слишком тонкий слой оцинковки, а в некоторых случаях его нет вообще. Попадаются также образцы с неоцинкованными торцами, окрашенные некачественной краской. Свою продукцию мы изготавливаем из оцинкованной с четырёх сторон стальной полосы, закупаемой в Бельгии, и покрываем краской специального состава, в который входят различные присадки – пластификаторы, УФ-стабилизаторы и другие компоненты, обеспечивающие надёжность и долговечность защитного слоя», – комментирует Андрей Мальцев (Металл Профиль).
В большом деле нет мелочей. Выбирая материалы для кровли, следует внимательно отнестись к качеству всех комплектующих. Оптимальным вариантом будет заказ комплектной кровельной системы у одного производителя, который даст на неё общую гарантию.
library.stroit.ru
Коррозия металлов. Почему ржавеют автомобильные кузова?
Коррозия металлов, как известно, приносит много бед. Уж не вам ли, уважаемые автовладельцы, объяснять, чем она грозит: дай ей волю, так от машины одни покрышки останутся. Поэтому, чем раньше начнется борьба с этим бедствием, тем дольше проживет автомобильный кузов.
Чтобы быть успешными в борьбе с коррозией, необходимо выяснить, что же это за «зверь» и понять причины ее возникновения.
Сегодня вы узнаете
Есть ли надежда?
Ущерб, наносимый человечеству коррозией, колоссален. По разным данным коррозия «съедает» от 10 до 25% мировой добычи железа. Превращаясь в бурый порошок, оно безвозвратно рассеивается по белому свету, в результате чего не только мы, но и наши потомки остаемся без этого ценнейшего конструкционного материала.
Но беда не только в том, что теряется металл как таковой, нет — разрушаются мосты, машины, крыши, памятники архитектуры. Коррозия не щадит ничего.
Неизлечимо больна та же Эйфелева башня — символ Парижа. Изготовленная из обычной стали, она неизбежно ржавеет и разрушается. Башню приходится красить каждые 7 лет, отчего ее масса каждый раз увеличивается на 60-70 тонн.
К сожалению, полностью предотвратить коррозию металлов невозможно. Ну, разве что полностью изолировать металл от окружающей среды, например поместить в вакуум. 🙂 Но какой прок от таких «консервированных» деталей? Металл должен «работать». Поэтому единственным способом защиты от коррозии является поиск путей ее замедления.
В незапамятные времена для этого применяли жир, масла, позднее начали покрывать железо другими металлами. Прежде всего, легкоплавким оловом. В трудах древнегреческого историка Геродота (V в. до н.э.) и римского ученого Плиния-старшего уже есть упоминания о применении олова для защиты железа от коррозии.
Интересный случай произошел в 1965 году на Международном симпозиуме по борьбе с коррозией. Некий индийский ученый рассказал об обществе по борьбе с коррозией, которое существует около 1600 лет и членом которого он является. Так вот, полторы тысячи лет назад это общество принимало участие в постройке храмов Солнца на побережье у Конарака. И несмотря на то, что эти храмы некоторое время были затоплены морем, железные балки прекрасно сохранились. Так что и в те далекие времена люди знали толк в борьбе с коррозией. Значит, не все так безнадежно.
Что такое коррозия?
Слово «коррозия» происходит от латинского «corrodo – грызу». Встречаются ссылки и на позднелатинское «corrosio – разъедание». Но так или иначе:
Коррозия – это процесс разрушения металла в результате химического и электрохимического взаимодействия с окружающей средой.
Хотя коррозию чаще всего связывают с металлами, ей также подвергаются бетон, камень, керамика, дерево, пластмассы. Применительно к полимерным материалам, правда, чаще используется термин деструкция или старение.
Коррозия и ржавчина — не одно и то же
В определении коррозии абзацем выше не зря выделено слово «процесс». Дело в том, коррозию частенько отождествляют с термином «ржавчина». Однако это не синонимы. Коррозия — это именно процесс, в то время как ржавчина — один из результатов этого процесса.
Также стоит отметить, что ржавчина — продукт коррозии исключительно железа и его сплавов (таких как сталь или чугун). Поэтому, когда говорим «ржавеет сталь», мы подразумеваем, что ржавеет железо в ее составе.
Если ржавчина относится только к железу, значит другие металлы не ржавеют? Не ржавеют, но это не значит, что они не корродируют. Просто продукты коррозии у них другие.
Например, медь, корродируя, покрывается красивым по цвету зеленоватым налетом (патиной). Серебро на воздухе тускнеет — это на его поверхности образуется налет сульфида, чья тонкая пленка придает металлу характерную розоватую окраску.

Патина — продукт коррозии меди и ее сплавов
Механизм протекания коррозионных процессов
Разнообразие условий и сред, в которых протекают коррозионные процессы, очень широко, поэтому сложно дать единую и всеобъемлющую классификацию встречающихся случаев коррозии. Но не смотря на это, все коррозионные процессы имеют не только общий результат — разрушение металла, но и единую химическую сущность — окисление.
Упрощенно окисление можно назвать процессом обмена веществ электронами. Когда одно вещество окисляется (отдает электроны), другое, наоборот, восстанавливается (получает электроны).
Например, в реакции…
… атом цинка теряет два электрона (окисляется), а молекула хлора присоединяет их (восстанавливается).
Частицы, которые отдают электроны и окисляются, называются восстановителями, а частицы, которые принимают электроны и восстанавливаются, называются окислителями. Два этих процесса (окисление и восстановление) взаимосвязаны и всегда протекают одновременно.
Такие вот реакции, которые в химии называются окислительно-восстановительными, лежат в основе любого коррозионного процесса.
Естественно, склонность к окислению у разных металлов неодинакова. Чтобы понять, у каких она больше, а у каких меньше, вспомним школьный курс химии. Было там такое понятие как электрохимический ряд напряжений (активности) металлов, в котором все металлы расположены слева направо в порядке повышения «благородности».
Так вот, металлы, расположенные в ряду левее, более склонны к отдаче электронов (а значит и к окислению), чем металлы, стоящие правее. Например, железо (Fe) больше подвержено окислению, чем более благородная медь (Cu). Отдельные металлы (например, золото), могут отдавать электроны только при определенных экстремальных условиях.
К ряду активности вернемся немного позднее, а сейчас поговорим об основных видах коррозии.
Виды коррозии
Как уже говорилось, критериев классификация коррозионных процессов существует множество. Так, различают коррозию по виду распространения (сплошная, местная), по типу коррозионной среды (газовая, атмосферная, жидкостная, почвенная), по характеру механических воздействий (коррозионное растрескивание, явление Фреттинга, кавитационная коррозия) и так далее.
Но основным способом классификации коррозии, позволяющим наиболее полно объяснить все тонкости этого коварного процесса, является классификация по механизму протекания.
По этому критерию различают два вида коррозии:
Химическая коррозия
Химическая коррозия отличается от электрохимической тем, что протекает в средах, не проводящих электрический ток. Поэтому при такой коррозии разрушение металла не сопровождается возникновением электрического тока в системе. Это обычное окислительно-восстановительное взаимодействие металла с окружающей средой.
Наиболее типичным примером химической коррозии является газовая коррозия. Газовую коррозию еще называют высокотемпературной, поскольку обычно она протекает при повышенных температурах, когда возможность конденсации влаги на поверхности металла полностью исключена. К такому виду коррозии можно отнести, например, коррозию элементов электронагревателей или сопел ракетных двигателей.
Скорость химической коррозии зависит от температуры — при ее повышении коррозия ускоряется. Из-за этого, например, в процессе производства металлического проката, во все стороны от раскаленной массы разлетаются огненные брызги. Это с поверхности металла скалываются частички окалины.
Окалина — типичный продукт химической коррозии, — оксид, возникающий в результате взаимодействия раскаленного металла с кислородом воздуха.
Помимо кислорода и другие газы могут обладать сильными агрессивными свойствами по отношению к металлам. К таким газам относятся диоксид серы, фтор, хлор, сероводород. Так, например, алюминий и его сплавы, а также стали с высоким содержанием хрома (нержавеющие стали) устойчивы в атмосфере, которая содержит в качестве основного агрессивного агента кислород. Но картина кардинально меняется, если в атмосфере присутствует хлор.
В документации к некоторым антикоррозионным препаратам химическую коррозию иногда называют «сухой», а электрохимическую — «мокрой». Однако химическая коррозия может протекать и в жидкостях. Только в отличие от электрохимической коррозии эти жидкости — неэлектролиты (т.е. не проводящие электрический ток, например спирт, бензол, бензин, керосин).
Примером такой коррозии является коррозия железных деталей двигателя автомобиля. Присутствующая в бензине в качестве примесей сера взаимодействует с поверхностью детали, образуя сульфид железа. Сульфид железа очень хрупок и легко отслаивается, освобождая свежую поверхность для дальнейшего взаимодействия с серой. И так, слой за слоем, деталь постепенно разрушается.
Электрохимическая коррозия
Если химическая коррозия представляет собой не что иное, как простое окисление металла, то электрохимическая — это разрушение за счет гальванических процессов.
В отличие от химической, электрохимическая коррозия протекает в средах с хорошей электропроводностью и сопровождается возникновением тока. Для «запуска» электрохимической коррозии необходимы два условия: гальваническая пара и электролит.
В роли электролита выступает влага на поверхности металла (конденсат, дождевая вода и т.д.). Что такое гальваническая пара? Чтобы понять это, вернемся к ряду активности металлов.
Смотрим. Cлева расположены более активные металлы, справа — менее активные.
Если в контакт вступают два металла с различной активностью, они образуют гальваническую пару, и в присутствии электролита между ними возникает поток электронов, перетекающих от анодных участков к катодным. При этом более активный металл, являющийся анодом гальванопары, начинает корродировать, в то время как менее активный коррозии не подвергается.

Схема гальванического элемента
Для наглядности рассмотрим несколько простых примеров.
Допустим, стальной болт закреплен медной гайкой. Что будет корродировать, железо или медь? Смотрим в ряд активности. Железо более активно (стоит левее), а значит именно оно будет разрушаться в месте соединения.

Стальной болт — медная гайка (корродирует сталь)
А если гайка алюминиевая? Снова смотрим в ряд активности. Здесь картина меняется: уже алюминий (Al), как более активный металл, будет терять электроны и разрушаться.
Таким образом, контакт более активного «левого» металла с менее активным «правым» усиливает коррозию первого.
В качестве примера электрохимической коррозии можно привести случаи разрушения и затопления кораблей, железная обшивка которых была скреплена медными заклепками. Также примечателен случай, который произошел в декабре 1967 года с норвежским рудовозом «Анатина», следовавшим из Кипра в Осаку. В Тихом океане на судно налетел тайфун и трюмы заполнились соленой водой, в результате чего возникла большая гальваническая пара: медный концентрат + стальной корпус судна. Через некоторое время стальной корпус судна начал размягчаться и оно вскоре подало сигнал бедствия. К счастью, экипаж был спасен подоспевшим немецким судном, а сама «Анатина» кое-как добралась до порта.
Олово и цинк. «Опасные» и «безопасные покрытия
Возьмем еще пример. Допустим, кузовная панель покрыта оловом. Олово — очень стойкий к коррозии металл, кроме того, оно создает пассивный защитный слой, ограждая железо от взаимодействия с внешней средой. Значит, железо под слоем олова находится в целости и сохранности? Да, но только до тех пор, пока слой олова не получит повреждение.
А коль уж такое случается, между оловом и железом тут же возникает гальваническая пара, и железо, являющееся более активным металлом, под воздействием гальванического тока начнет корродировать.
Кстати, в народе до сих пор ходят легенды о якобы «вечных» луженых кузовах «Победы». Корни этой легенды таковы: ремонтируя аварийные машины, мастера использовали паяльные лампы для нагрева. И вдруг, ни с того ни с сего, из-под пламени горелки начинает «рекой» литься олово! Отсюда и пошла молва, что кузов «Победы» был полностью облужен.
На самом деле все гораздо прозаичнее. Штамповая оснастка тех лет была несовершенной, поэтому поверхности деталей получались неровными. Вдобавок тогдашние стали не годились для глубокой вытяжки, и образование морщин при штамповке стало обычным делом. Сваренный, но еще не окрашенный кузов приходилось долго готовить. Выпуклости сглаживали наждачными кругами, а вмятины заполняли оловяным припоем, особенно много которого было вблизи рамки ветрового стекла. Только и всего.
Ну, а так ли «вечен» луженый кузов, вы уже знаете: он вечен до первого хорошего удара острым камешком. А их на наших дорогах более чем достаточно.
А вот с цинком картина совсем иная. Здесь, по сути, мы бьем электрохимическую коррозию ее же оружием. Защищающий металл (цинк) в ряду напряжений стоит левее железа. А значит при повреждении будет разрушаться уже не сталь, а цинк. И только после того, как прокорродирует весь цинк, начнет разрушаться железо. Но, к счастью, корродирует он очень и очень медленно, сохраняя сталь на долгие годы.

а) Коррозия луженой стали: при повреждении покрытия разрушается сталь. б) Коррозия оцинкованной стали: при повреждении покрытия разрушается цинк, защищая от коррозии сталь.
Покрытия, выполненные из более активных металлов называются «безопасными», а из менее активных — «опасными». Безопасные покрытия, в частности оцинковка, давно и успешно применяются как способ защиты от коррозии автомобильных кузовов.
Почему именно цинк? Ведь помимо цинка в ряду активности относительно железа более активными являются еще несколько элементов. Здесь подвох вот в чем: чем дальше в ряду активности находятся друг от друга два металла, тем быстрее разрушение более активного (менее благородного). А это, соответственно, сокращает долговечность антикоррозионной защиты. Так что для автомобильных кузовов, где помимо хорошей защиты металла важно достичь и продолжительного срока действия этой защиты, оцинковка подходит как нельзя лучше. Тем более, что цинк доступен и недорог.
Кстати, а что будет, если покрыть кузов, например, золотом? Во-первых, будет ох как дорого! 🙂 Но даже если золото стало бы самым дешевым металлом, такого делать нельзя, поскольку оно окажет нашей «железке» плохую услугу.
Золото ведь стоит очень далеко от железа в ряду активности (дальше всего), и при малейшей царапине железо вскоре превратится в груду ржавчины, покрытую золотой пленкой.
Автомобильный кузов подвергается воздействию как химической, так электрохимической коррозии. Но главная роль все же отводится электрохимическим процессам.
Ведь, чего греха таить, гальванических пар в автомобильном кузове воз и маленькая тележка: это и сварные швы, и контакты разнородных металлов, и посторонние включения в листовом прокате. Не хватает только электролита, чтобы «включить» эти гальванические элементы.
А электролит тоже найти легко — хотя бы влага, содержащаяся в атмосфере.
Кроме того, в реальных условиях эксплуатации оба вида коррозии усиливаются множеством других факторов. Поговорим о главных из них поподробнее.
Факторы, влияющие на коррозию автомобильного кузова
Металл: химический состав и структура
Конечно, если бы автомобильные кузова изготавливались из технически чистого железа, их коррозионная стойкость была бы безупречной. Но к сожалению, а может быть и к счастью, это невозможно. Во-первых, такое железо для автомобиля слишком дорого, во-вторых (что важнее) — недостаточно прочно.
Впрочем, не будем о высоких идеалах, а вернемся к тому, что имеем. Возьмем, к примеру, сталь марки 08КП, широко применяемую в России для штамповки кузовных элементов. При изучении под микроскопом эта сталь представляет собой следующее: мелкие зерна чистого железа перемешаны с зернами карбида железа и другими включениями.
Как вы уже догадались, подобная структура порождает множество микрогальванических элементов, и как только в системе появится электролит, коррозия потихоньку начнет свою разрушительную деятельность.
Интересно, что процесс коррозии железа ускоряется под действием серосодержащих примесей. Обычно она попадает в железо из каменного угля при доменной выплавке из руд. Кстати, в далеком прошлом для этой цели использовался не каменный, а древесный уголь, практически не содержащий серы.
В том числе и по этой причине некоторые металлические предметы древности за свою многовековую историю практически не пострадали от коррозии. Взгляните, к примеру, на эту железную колонну, которая находится во дворе минарета Кутуб-Минар в Дели.
Она стоит уже 1600 (!) лет, и хоть бы что. Наряду с низкой влажностью воздуха в Дели, одной из причин такой поразительной коррозионной стойкости индийского железа является, как раз-таки, низкое содержание в металле серы.
Так что в рассуждениях на манер «раньше металл был чище и кузов долго не ржавел», все-таки есть доля правды, и немалая.
Кстати, почему же тогда не ржавеют нержавеющие стали? А потому, что хром и никель, используемые в качестве легирующих компонентов этих сталей, стоят в электрохимическом ряду напряжений рядом с железом. Кроме того, при контакте с агрессивной средой они образуют на поверхности прочную оксидную пленку, предохраняющую сталь от дальнейшего корродирования.
Хромоникелевая сталь — наиболее типичная нержавейка, но кроме нее есть и другие марки нержавеющих сталей. Например, легкие нержавеющие сплавы могут включать алюминий или титан. Если вы были во Всероссийском выставочном центре, вы наверняка видели перед входом обелиск «Покорителям космоса». Он облицован пластинками из титанового сплава и на его блестящей поверхности нет ни единого пятнышка ржавчины.
Заводские кузовные технологии
Толщина листовой стали, из которой изготавливаются кузовные детали современного легкового автомобиля, составляет, как правило, менее 1 мм. А в некоторых местах кузова эта толщина — и того меньше.
Особенностью процесса штамповки кузовных панелей, да и вообще, любой пластической деформации металла, является возникновение в ходе деформации нежелательных остаточных напряжений. Эти напряжения незначительны, если шпамповочное оборудование не изношено, и скорости деформирования настроены правильно.
В противном случае в кузовную панель закладывается этакая «часовая бомба»: порядок расположения атомов в кристаллических зернах меняется, поэтому металл в состоянии механического напряжения корродирует интенсивнее, чем в нормальном состоянии. И, что характерно, разрушение металла происходит именно на деформированных участках (изгибах, отверстиях), играющих роль анода.
Кроме того, при сварке и сборке кузова на заводе в нем образуется множество щелей, нахлестов и полостей, в которых скапливается грязь и влага. Не говоря уже о сварных швах, образующих с основным металлом все те же гальванические пары.
Влияние окружающей среды при эксплуатации
Среда, в которой эксплуатируются металлические конструкции, в том числе и автомобили, с каждым годом становится все более агрессивной. В последние десятилетия в атмосфере повысилось содержание сернистого газа, оксидов азота и углерода. А значит, автомобили омываются уже не просто водичкой, а кислотными дождями.
Коль уж зашла речь о кислотных дождях, вернемся еще раз к электрохимическому ряду напряжений. Наблюдательный читатель подметил, что в него включен также и водород. Резонный вопрос: зачем? А вот зачем: его положение показывает, какие металлы вытесняют водород из растворов кислот, а какие — нет. Например, железо расположено левее водорода, а значит вытесняет его из растворов кислот, в то время как медь, стоящая правее, на подобный подвиг уже не способна.
Отсюда следует, что кислотные дожди для железа опасны, а для чистой меди — нет. А вот о бронзе и других сплавах на основе меди этого сказать нельзя: они содержат алюминий, олово и другие металлы, находящиеся в ряду левее водорода.
Замечено и доказано, что в условиях большого города кузова живут меньше. В этой связи показательны данные Шведского института коррозии (ШИК), установившего, что:
Немаловажны и климатические условия, в которых эксплуатируется автомобиль. Так, в условиях морского климата коррозия активизируется примерно в два раза.
Влажность и температура
Насколько велико влияние влажности на коррозию мы можем понять на примере ранее упомянутой железной колонны в Дели (вспомним сухость воздуха, как одну из причин ее коррозионной стойкости).
Поговаривают, что один иностранец решил раскрыть тайну этого нержавеющего железа и каким-то образом отколол небольшой кусочек от колонны. Каково же было его удивление, когда еще на корабле по пути из Индии этот кусочек покрылся ржавчиной. Оказывается, на влажном морском воздухе нержавеющее индийское железо оказалось не таким уж и нержавеющим. Кроме того, аналогичную колонну из Конарака, расположенного поблизости моря, коррозия поразила очень сильно.
Скорость коррозии при относительной влажности до 65% сравнительно невелика, но когда влажность возрастает выше указанного значения — коррозия резко ускоряется, поскольку при такой влажности на металлической поверхности образуется слой влаги. И чем дольше поверхность остается влажной, тем быстрее распространяется коррозия.
Вот почему основные очаги коррозии всегда обнаруживаются в скрытых полостях кузова: cохнут-то они гораздо медленнее открытых частей. Как результат — в них образуются застойные зоны, — настоящий рай для коррозии.
Кстати, применение химических реагентов для борьбы с гололедом коррозии тоже на руку. Вперемешку с подтаявшими снегом и льдом антигололедные соли образуют очень сильный электролит, способный проникнуть куда угодно, в том числе и в скрытые полости.
Что касается температуры, то мы уже знаем, что ее повышение активизирует коррозию. По этой причине вблизи выхлопной системы следов коррозии всегда будет больше.
Доступ воздуха
Интересная все-таки вещь эта коррозия. Насколько интересна, настолько же и коварна. К примеру, не удивляйтесь, что блестящий стальной трос, с виду абсолютно не тронутый коррозией, внутри может оказаться проржавевшим. Так происходит из-за неравномерного доступа воздуха: в тех местах, где он затруднен, угроза коррозии больше. В теории коррозии это явление называется дифференциальной аэрацией.
Принцип дифференциальной аэрации: неравномерный доступ воздуха к разным участкам металлической поверхности приводит к образованию гальванического элемента. При этом участок, интенсивно снабжаемый кислородом, остается невредимым, а участок хуже снабжаемый им, корродирует.
Яркий пример: капля воды, попавшая на поверхность металла. Участок, находящийся под каплей и потому хуже снабжаемый кислородом, играет роль анода. Металл на этом участке окисляется, а роль катода выполняют края капли, более доступные влиянию кислорода. В результате на краях капли начинает осаждаться гидроксид железа — продукт взаимодействия железа, кислорода и влаги.
Кстати, гидроксид железа (Fe2O3·nh3O) и является тем, что мы называем ржавчиной. Поверхность ржавчины, в отличие от патины на медной поверхности или оксидной пленки алюминия, не защищает железо от дальнейшего корродирования. Изначально ржавчина имеет структуру геля, но затем постепенно происходит ее кристаллизация.
Кристаллизация начинается внутри слоя ржавчины, при этом внешняя оболочка геля, который в сухом состоянии очень рыхлый и хрупкий, отслаивается, и воздействию подвергается следующий слой железа. И так до тех пор, пока все железо не будет уничтожено или в системе не закончится весь кислород с водой.
Возвращаясь к принципу дифференциальной аэрации, можно представить, сколько существует возможностей для развития коррозии в скрытых, плохо проветриваемых участках кузова.
Ржавеют… все!
Как говорится, статистика знает все. Ранее мы упоминали о таком известном центре борьбы с коррозией, как Шведский институт коррозии (ШИК) — одной из наиболее авторитетных организаций в данной области.
Раз в несколько лет ученые института проводят интересное исследование: берут кузова хорошо потрудившихся автомобилей, вырезают из них наиболее полюбившиеся коррозии «фрагменты» (участки порогов, колесных арок, кромок дверей и т.д.) и оценивают степень их коррозионного поражения.
Важно отметить, что среди исследуемых кузовов есть как защищенные (оцинковкой и/или антикором), так и кузова без какой либо дополнительной антикоррозионной защиты (просто окрашенные детали).
Так вот, ШИК утверждает, что наилучшей защитой автомобильного кузова является лишь сочетание «цинк плюс антикор». А вот все остальные варианты, включая «просто оцинковку» или «просто антикор», по словам ученых — плохи.
Оцинковка — не панацея
Сторонники отказа от дополнительной антикоррозионной обработки часто ссылаются на заводскую оцинковку: с ней, мол, никакая коррозия автомобилю не грозит. Но, как показали шведские ученые, это не совсем так.
Действительно, цинк может служить в качестве самостоятельной защиты, но только на ровных и плавных поверхностях, к тому же не подверженных механическим атакам. А на кромках, краях, стыках, а также местах, регулярно подвергающихся «обстрелу» песком и камнями, оцинковка перед коррозией пасует.
К тому же, далеко не у всех автомобилей кузова оцинкованы полностью. Чаще всего цинком покрыто лишь несколько панелей.
Ну и не нужно забывать, что цинк хоть и защищает сталь, но в процессе защиты неизбежно расходуется сам. Поэтому толщина цинкового «щита» со временем будет постепенно снижаться.
Так что легенды о долгожительстве оцинкованных кузовов правдивы лишь в тех случаях, когда цинк становится частью общего барьера, дополнением к регулярной дополнительной антикоррозионной обработке кузова.
Пора заканчивать, но на этом тема коррозии далеко не исчерпана. О борьбе с ней мы продолжим говорить в следующих статьях рубрики «Антикоррозионная защита».
artmalyar.ru
защитие покрытия листа от ржавчины и повреждений
Наибольшим деформациям подвержены заборы и крыши, поэтому материал для них нужно выбирать тщательно, обращая внимание на качество, толщину и возможный срок службы. Хотя профилированный лист считают надежным вариантом и часто используют в строительстве заборов и в качестве покрытия кровли, со временем с ним могут появиться проблемы.
Важно понять, что стало причиной коррозии или другого повреждения, чтобы беспрепятственно исправить ошибки и улучшить состояние изделия. Нельзя скупиться на качественные модели, также не забывайте о финишных покрытиях, оберегающих металл от ржавчины.
Защитные покрытия

Защитное покрытие выполняет также декоративную функцию, делая забор или крышу красивыми внешне. Но главное, что нужно учитывать, выбирая средство, это его свойства, позволяющие сохранить стальной лист в идеальном состоянии долгие годы.
Можно выделить шесть видов покрытия профнастила:
Каким бы ни было защитное покрытие профнастила, периодически требуется делать ремонт, избавляя листы от повреждений.
Причины ремонта
Мелкий профилактический ремонт, освежающий сооружение из профнастила, следует делать периодически. Но иногда причиной ремонта становятся конкретные проблемы с крышей и забором. Особенно часто страдает ограждение, так как:

В процессе строительства забора нужно следить, чтобы опоры глубоко входили в фундамент. В противном случае ограда будет стоять непрочно и со временем сломается. Закрепление столбов также важная часть возведения забора из профнастила. Выбирать нужно толстые столбы, чтобы в будущем избежать провисания.
Справиться с неудачно выбранными опорами легко, нужно их тут же заменить на новые. Точно так же поступают с крепежными элементами. Хуже, если под ограждением размыт грунт, и проблема именно в этом. Чтобы фундамент был более прочным и мог удерживать тяжелую конструкцию из профлиста, следует установить подпорки.
Приводить в порядок заборы из профнастила сложно, так как иногда страдает сам металл. Заменить его проблематичнее, чем опоры и другие части ограждения. Появление следов окисления свидетельствует, что покрытие не защищает профнастил в полной мере. Такое может быть, если листы покрыли краской в один слой или предварительно не прогрунтовали.
Появление коррозии на профнастиле означает, что конструкция установлена плохо. Сначала необходимо найти причину, по которой появилась ржавчина, и только потом приступить к ее устранению.
Устранение коррозии
После выявления основной проблемы, нужно привести в порядок профнастил с коррозией. Для этого надо взять наждачную бумагу и хорошо очистить испорченную поверхность металла. Зачищенное место обезжиривают, а потом грунтуют. Грунтовку надо накладывать в несколько слоев, иначе в скором времени снова придется прибегать к ремонту. Только после этого можно покрыть профнастил краской.
Хорошо, если забор красили в однотонный цвет, так как ремонт расписного ограждения намного сложнее и занимает больше времени. Коррозия может появиться в любых местах, часто проблема возникает вокруг саморезов. Любые трещины и сколы необходимо мгновенно ликвидировать, даже если коррозии еще нет. Поврежденный профнастил обязательно начнет ржаветь и прогибаться, поэтому мелкий ремонт очень важен.
Сооружения из профнастила отличаются прочностью и долговечностью, поэтому не требуют регулярного вмешательства. Чтобы сохранить внешний вид кровли или забора и уберечь их от коррозии, достаточно периодически осматривать поверхность и вовремя ликвидировать мелкие недостатки.Хотя профнастил подвержен коррозии, этот материал считается наиболее удачным решением в строительстве. Его охотно применяют для возведения сооружений различной сложности. Монтаж листов легко осуществить самостоятельно. Профнастил изготавливают различной толщины, волны и расцветки. Он подходит для кровли, ограждений и временных строений.
Рекомендации по эксплуатации профнастила

Технические характеристики листа профнастила влияют на его срок службы, но многое зависит от дальнейшей эксплуатации материала. Монтаж забора или крыши должен проходить аккуратно, использовать болгарку категорически запрещено. Любая искра моментально испортит покрытие. Хотя металлические листы прочные, обращаться с ними нужно осторожно, избавляя от преждевременных повреждений.
Саморезы и шурупы нужно вводить в лист только под прямым углом. Обязательно используйте подкладку между шурупом и поверхностью листа, это спасет от проникновения влаги и ржавчины металла. Все срезы необходимо закрашивать по той же причине. Коррозия появляется на необработанных краях, в местах повреждений и трещин.
Покрытие защищает профнастил, увеличивая срок службы на несколько лет. От качества, стойкости и свойств защитной краски зависит не только будущее состояние забора и кровли, но и стоимость материала. Экономить на защитном покрытии не рекомендуется, так как его отсутствие или низкие защитные свойства подвергают профнастил коррозии и другим проблемам, возникающим в процессе эксплуатации.
Остановиться на бюджетном варианте можно, если забор из профнастила - временное сооружение. В остальных случаях следует присмотреться к техническим характеристикам материала и выбрать тот, который прослужит долго, сохранив все свои свойства.
profnastil.center
Почему не ржавеют сетки из оцинковки
http://remont-kuzova.narod.ru/mat_izg_3.htm
В чем причина высоких антикоррозионных свойств оцинкованной стали? Коррозия стального листа происходит в результате взаимодействия кислорода воздуха с железом в присутствии влаги. Следствием такого взаимодействия является образование пористого слоя ржавчины, свободно пропускающего кислород воздуха и влагу вглубь металла. Однажды начавшийся процесс коррозии не прекратится до тех пор, пока весь металл не превратится в ржавчину.
Корродированию стального листа можно воспрепятствовать, если покрыть его цинком. Антикоррозионный эффект, достигаемый благодаря цинкованию, обусловлен тем, что цинк образует прочно связанный с поверхностью стали оксидный слой (ZnO), препятствующий доступу кислорода воздуха к нижерасположенным слоям стального листа и, таким образом, выполняющий роль барьера.
Исходя из этого большинство покупателей предпочитает приобретать просечно-вытяжные сетки изготовленные из оцинкованного листа в качестве заготовки
Если произошло механическое повреждение слоя цинка, нанесенного на поверхность стального листа (железа), в присутствии влаги оба металла образуют локальный гальванический элемент, и в результате электрохимической реакции разрушению подвергается не железо, а цинк.
Барьерный эффект цинка проявляется также при соединении стальных листов контактно-точечной сваркой. Если внутренние поверхности двух наложенных друг на друга стальных листов оцинкованы, в момент точечной сварки цинк плавится, переходя в жидкое состояние. Электроды выдавливают расплавленный цинк наружу, вследствие чего вокруг сварной точки возникает скопление цинка. Расплав цинка после охлаждения образует кольцеобразную барьерную зону, которая будет препятствовать проникновению кислорода воздуха к центру сварной точки. Аналогичный эффект обеспечивает краска на основе цинковой пыли, которую обычно наносят на место предстоящей точечной сварки оцинкованных листов
Приведем тут информацию по данным Гентского университетаЛаборатории электронной микроскопииДиректор: Проф. А.Винкер
При корродировании металлы распадаются на электроны и положительные ионы (катионы) согласно следующей схематической реакции:
Ме = Ме z+ + z e-
Электроны, полученные таким образом, вступают в другую реакцию, которая в большинстве случаев является реакцией восстановления кислорода, соответственно следующей реакции:
О2 + 2 Н2О + 4 е- = 4 ОН-
Далее, ионы гидроксильной группы (ОН-) будут реагировать с катионами металла противоположной полярности для образования нового малорастворимого соединения в соответствии со следующей реакцией:
х Ме z+ + y ОН- = Ме х (ОН) y
Так сталь покрывается железосодержащим соединением FeO(ОН), более известным, как "Ржавчина".
Если электроны, необходимые для восстановления кислорода, получаются из другого металла, а не из железа, коррозия железа может быть остановлена, в то время как другой металл будет расходоваться и, соответственно, производить электроны, необходимые для процесса восстановления. Таким металлом, например, может быть цинк.
В случае массивного слоя цинка, как после горячего оцинковывания, проблемы движения электронов в пределах цинкового слоя и между слоем цинка и сталью не возникает.
Собранная информация позволяет делать выводы об отсутствии либо существенном понижении процесса коррозии на грани просечно - вытяжных сеток, подвергшихся рассеканию в процессе производства, что подтверждают протоколы исследований лаборатории по контролю качества продукции.
Используемая нами в производстве оцинкованная сталь ММК, содержит слой цинка, достаточный для длительного антикоррозийного воздействия на граничащие с ним поверхности (0,5 мм) основы стального листа (120 и более).
Время последней модификации 1412232064tksprut.ru
Как оцинковывать сталь
4 методика:Горячее цинкованиеЭлектрогальванизацияДиффузионное оцинковываниеНапыление Оцинковка, или гальванизация стали состоит в нанесении на ее поверхность слоя цинка для защиты металла от коррозии. Впервые цинк был применен в качестве конструкционного материала еще во времена разрушения Помпеи, но первое его использование для оцинковки стали (точнее железа) датировано 1742 годом, и данный процесс был запатентован в 1837 году. Оцинкованная сталь используется для водосливов и водосточных труб, кровельных желобов, а также наружных креплений и гвоздей. Существует несколько технологий оцинковывания стали: горячее цинкование, электрогальванизация, диффузионное оцинковывание, металлизация напылением. ШагиМетод 1 из 4: Горячее цинкованиеМетод 2 из 4: ЭлектрогальванизацияМетод 3 из 4: Диффузионное оцинковываниеМетод 4 из 4: НапылениеСоветыПредупреждения |
ves-mir.3dn.ru
Различие между нержавеющей и оцинкованной сталью
Как нержавеющая, так и оцинкованная сталь зачастую используются в одних и тех же отраслях промышленности, в основном как сырье для производства изделий, неподверженных коррозии, частей и узлов станков, установок и агрегатов. Основное различие между нержавеющей и оцинкованной сталью заключается, прежде всего, в сроке эксплуатации, то есть промежутке времени, в течение которого материал сохраняет свои антикоррозионные свойства.
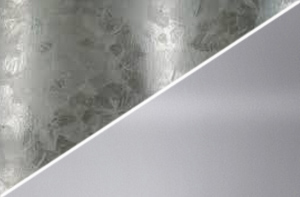
При значительной разнице в цене между нержавейкой и оцинковкой не исключены случаи, когда под видом нержавеющей стали покупателю могут поставить оцинкованную.
Как можно отличить оцинковку от нержавейки?
Самый точный и надежный способ, это спектральный анализ, определение химического состава стали с помощью специальных приборов. Такой способ требует специального оборудования и времени. Однако есть более простые, но менее точные способы, основанные на различиях между нержавеющей и оцинкованной сталью.
Внешние отличия между нержавейкой и оцинковкой могут дать быстрый ответ. Оцинкованная сталь может иметь характерные пятна, известные многим по оцинкованным ведрам, производимым когда-то во времена СССР, так называемый узор кристаллизации (см. рисунок).
Кроме того, визуально нержавеющая сталь обычно имеет более матовую поверхность, чем оцинковка, особенно если нержавейка не была подвержена чистовой зеркальной обработки. Оцинкованная сталь без узоров кристаллизации почти всегда имеет зеркальную поверхность, с едва уловимым синеватым отливом. Однако при качественной обработке нержавеющей стали, например, по стандарту BA, визуально отличить ее от оцинкованной стали достаточно сложно. Если лист достаточно большой толщины будет нелишним внимательно рассмотреть место среза на предмет однородности.
Можно использовать электромагнитные различия между оцинковкой и нержавейкой. Если магнит притягивается к стали, то с большой долей уверенности можно сказать что это оцинкованная сталь, в то время как большинство нержавеющих сталей и титановых сплавов не магнитятся.
Химический способ, при котором используется соляная кислота, основан на свойствах цинка, который, взаимодействуя с покрытием оцинкованного листа, активно выделяет водород. Достаточно небольшой капли соляной кислоты чтоб начался заметный невооруженным глазом химический процесс – поверхность начинает пузыриться, цинковый слой постепенно исчезает.
И еще один способ – выбрать надежного, заслуживающего доверия поставщика нержавеющей стали и юридически грамотно оформить сделку.
sdlc.ru
Дефекты горячего цинкования
Безупречное цинкование
Безупречное горячее цинкование означает погружение готовых деталей, на которых нет дефекта, в расплав цинка. В результате на стальной или чугунной поверхности образуются слой железо-цинкового сплава и, находящегося поверх него, слой цинка. При горячем цинковании толстостенных изделий или изделий из марок стали, которые быстро вступают в реакцию в расплавленном цинке, цинковое покрытие состоит только из слоя железо-цинкового сплава. Во время горячего цинкования в ванне с алюминием, этот слой подавляется, и покрытие состоит только из внешнего цинкового слоя.Формирование
При погружении изделий из стали или чугуна в сплав цинка, как правило, на верхней поверхности образуется толстый слой железо-цинкового сплава. При вынимании изделия из ванны горячего цинкования, поверх железо-цинкового сплава ложится тонкий слой расплавленного цинка, который застывает после охлаждения изделия. Во время охлаждения деталь преобразовывается за счет увеличения толщины сплава. У деталей с большой теплоемкостью, как правило, внешний слой цинка полностью исчезает и цинковое покрытие состоит только из слоя железо-цинкового сплава. В стальных конструкциях, с содержанием кремния от 0,03% до 0,12% и выше 0,2% может образовываться рыхлый слой вместо плотного слоя железо-цинкового сплава. Он увеличивается, в зависимости от длительности погружения. Такая быстрая реакция ведет к тому, что образуется толстое цинковое покрытие, вследствие которого внешний цинковый слой отсутствует из-за увеличения слоя сплава во время охлаждения изделия. Во время горячего цинкования в расплавленном цинке с содержанием алюминия около 0,07% образование слоя железо-цинкового сплава замедляется. На месте обычных слоев, в зависимости от содержания алюминия, температуры и длительности погружения, образуются очень тонкие слои алюминий-содержащих соединений железа и цинка или железо-алюминиевых соединений. Алюминиевые покрытия такого вида значительно тоньше и состоят главным образом из внешнего цинкового слоя.Распознавание
После горячего цинкования поверхность изделия блестит. На верхней поверхности можно четко увидеть затвердевание верхнего слоя цинка в виде листков папоротника. В поперечном разрезе через такие покрытия можно увидеть на стальной поверхности слой железо-цинкового сплава и прилегающий сверху внешний слой цинка.На деталях с переменной толщиной места с более большей теплоемкостью при цинковании становятся серыми, вследствие проникновения слоя железо-цинкового сплава.
Во время цинкования стальных конструкций с критичным содержанием кремния часто можно увидеть это серое покрытие, так как эти стальные конструкции очень быстро взаимодействуют с цинком и поэтому очень трудно избежать проникновения слоя железо-цинко
polygonal.com.ua