- Высокая энергоёмкость
- Токсичность, пожароопасность и взрывоопасность
- Технологическая сложность
- Ограничение номенклатуры обрабатываемых металлов
- Коррозия оборудования
- Предназначение полировки
- Достоинства электрополировки металла
- Электрополировка с использованием кругов
- Электрохимическая полировка
- Обезжиривание или очистка смачиванием
- Двойное полоскание
- Удаление окалины (необязательно)
- Двойное полоскание
- Электрополирование
- Выемка деталей
- Двойное или тройное полоскание встречным движением
- Сушка
- Процесс полировки происходит при рабочих напряжениях 200...350 В.
- При напряжениях свыше 200 В вблизи анода формируется тончайшая (от 50 до 100 мкм) парогазовая оболочка.
- На микровыступах поверхности детали формируется зона максимальной напряженности электрического поля.
- Достигается минимальная шероховатость поверхности R=0,03...0,02 мкм. В среднем, уровень шероховатости снижается на 2...3 класса. Класс чистоты поверхности доводится до 14 максимального (зеркальной полировки).
- Продолжительность процесса полировки зависит от материала: для нержавеющих сталей – 3...15 мин., цветные металлы и сплавы (в т. ч. бронза, латунь) – 0,5...15 мин.
- Полировка притупляет острые кромки детали и снимает заусенцы до 0,3 мм высотой.
- В зависимости от высоты заусенцев удаление их методом ЭПП происходит за 0,2...30 мин.
- Применение ЭПП очищает поверхность детали от вкраплений абразивов.
- Электроимпульсная полировка удаляет с поверхности последствия применения сварки – цвета побежалости.
- Улучшает поверхностную стойкость к коррозии металла
- перила и ограждения;
- ювелирные изделия;
- элементы дизайна и обстановки помещения;
- оборудование бассейнов
- конструктивные элементы яхт/кораблей и мототехники;
- медицинское оборудование;
- детали и конструкции машиностроения (все отрасли)
- полировка только по НАРУЖНОЙ поверхности;
- полировка сложных форм;
- максимальные габариты изделия не должны превышать (д*ш*в): 3000мм*850мм*850мм, большие размеры по согласованию, возможно за два раза;
- площадь опускания детали не превышает 1,5 м/кв за цикл;
- тестовая обработка БЕСПЛАТНО!
- Контроля состава и температуры используемого электролита;
- Контроля плотности тока;
- Предварительной механической обработки материала.
- Межкристаллитная коррозия это
- Что такое углеродистая сталь где она используется
- Шлифовка стали
- Трубы стальные бесшовные горячедеформированные со снятой фаской
- Сталь оцинкованная окрашенная
- Цементация стали 20
- Нормы выбраковки стальных канатов
- Как завязать трос стальной
- Стальной двухпетлевой строп
- Стальной двухпетлевой строп
- Оцинкованная окрашенная сталь
Электрополирование: особенности процесса. Электрохимполировка стали нержавеющей
Электрохимическая полировка металла
Электрохимическая обработка заменяет трудоемкие механические методы и не приводит к нежелательным структурным изменениям в поверхностном слое изделий. Стравленная поверхность во многих случаях обладает более высокой коррозийной стойкостью и улучшенными механическими свойствами. Электрохимическое полирование — это обработка поверхностей деталей, погруженных в электролит, представляющий собой раствор, обычно содержащий кислоты. В процессе обработки при постоянном напряжении 10–20 В изделие подключается к положительному полюсу (аноду) источника питания.
При анодном электрохимическом полировании процесс сглаживания микрошероховатостей на уровне субмикрорельефа поверхности связан с наличием на металле пассивирующей пленки. Степень уменьшения шероховатостей определяется величиной электрического заряда, прошедшего через электролит. В ходе электролиза, наряду с уменьшением высоты микровыступов, происходит округление их вершин и формирование волнообразного микрорельефа поверхности. Данные процессы вызываются неравномерностью распределения электрического тока по микрорельефу поверхности и концентрационными изменениями электролита в прианодном слое. Качество электрохимической обработки зависит от состава металла или сплава, степени остаточной деформации, толщины обрабатываемой детали.
При использовании электрохимического полирования для получения поверхности хорошего качества необходимо перед обработкой убедиться, что на деталях нет глубоких рисок, забоин, раковин, так как они не устраняются при электрохимической обработке. Наиболее высокий блеск поверхности достигается на небольших деталях, причем плоские поверхности полируются хуже, чем цилиндрические.
Электрохимическое полирование проводится в обычных гальванических ваннах с обязательным плотным контактом подвесного устройства с деталями и электродной штангой. Наиболее долговечна оснастка из титана, который не разрушается в электролитах. Для надежности электрического контакта подвески с деталями рекомендуется образующуюся на них окисную пленку периодически удалять, используя разбавленную серную кислоту.
Основой промышленных электролитов для электрохимического полирования служат ортофосфорная или хлорная кислоты. В хлорнокислых электролитах обрабатывается алюминий, цинк, свинец, титан. В трехкомпонентных фосфорно-серно-хромовокислых электролитах обрабатываются стали различных марок, а в фосфорно-сернокислых — нержавеющие стали аустенитного класса — 12Х18Н10Т, Х17Г9АН4.
Для повышения стойкости к коррозии рекомендуется обрабатывать стальные детали после электрохимического полирования раствором NaOH в течение 15–20 минут при температуре 60–70оС. В случае нанесения на изделие гальванического покрытия, для улучшения сцепления покрытия с деталью необходимо подвергнуть его электрохимической обработке в 3–5 % растворе соляной кислоты.
Несмотря на достаточно широкую область применения, электрохимический метод имеет существенные недостатки, такие как:
Электрополировка своими руками | Строительный портал
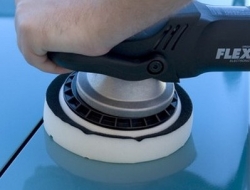
Чтобы добиться блестящей поверхности металла, необязательно материал покрывать лаком. Можно прибегнуть к полировке металла, что используется как декоративный вид обработки детали после нанесения покрытия или в процессе обработки изделия. В одном случае достаточно опилить металл напильником, в другом — поверхность следует довести до блеска путем электрополировки. Все эти манипуляции можно сделать самостоятельно в домашних условиях.
Содержание:
Предназначение полировки
Детали из металла имеют изначально гладкую блестящую поверхность. Но она со временем тускнеет и в процессе эксплуатации царапается. Для скрытых деталей, безусловно, внешний вид не имеет большого значения, но когда металлические детали располагаются на виду, то они должны выглядеть должным образом. Именно так будет смотреться глянцевая поверхность, после того, как вы провели полировку металла.
Полирование металлов предназначается также для улучшения гладкости и чистоты поверхности металлических деталей и устранения следов прошлых обработок – неровностей, царапин и вмятин. Полировку деталей проводят с помощью наждачных кругов, шлифовального порошка, специальной известковой пасты, полировочного раствора или электролита.
Поверхности металлических деталей отделывают не только с целью придания им привлекательного внешнего вида, но и чтобы защитить от ржавления, разъедания щелочами и кислотами. Хорошо полировке поддаются такие металлы, как латунь, бронза и медь. Нержавейку до зеркального блеска не получится довести, а вот придать ей матовый глянец – запросто.
Исходя из вышесказанного, можно утверждать, что полирование бывает двух типов – предварительное и окончательное. Предварительную полировку металлов применяют при механическом удалении неровностей, а окончательную – для создания идеально ровного и глянцевого финишного состояния металлической поверхностей и защиты её от неблагоприятных факторов внешней среды.
Достоинства электрополировки металла
Отдельной веткой полирования является электрополировка стали. Процедура оказывает благоприятное влияние на физико-химические, электрические и магнитные свойства металлических поверхностей, облегчая глубокую вытяжку и штамповку определенных металлов, а также увеличивает уровень их коррозионной стойкости. Этим объясняется широкое применение электрополировки при лабораторных исследованиях металлов и в промышленности.
Электрополирование имеет целый перечень преимуществ перед механической полировкой в отношении простоты, универсальности и скорости. К примеру, нержавеющую сталь механическими методами трудно полировать, так как это длительная и дорогостоящая операция. Электрополировка нержавейки же происходит на протяжении нескольких минут, является дешевой процедурой и позволяет получить поверхность с лучшими отражательными способностями.
Электрополирование уменьшает время обработки изделия по сравнению с механической технологией почти в 5 раз, хотя и повышает чистоту поверхности всего на 1 - 2 класса. При механическом полировании можно добиться высшей чистоты поверхности, однако процесс электрополировки незаменим при обработке изделий сложного профиля с внутренними полостями, деталей топливной системы дизелей и пружин, которые являются неудобными и сложными по форме для механической обработки.
Электрополировка является самым лучшим методом подготовки поверхности перед нанесением гальванического покрытия, потому что демонстрирует высокую прочность сцепления защитного покрытия с отполированной основой. Данную методику применяют для обработки деталей для улучшения скольжения материалов, которые соприкасаются с полированной поверхностью, к примеру, нитеводители в текстильных машинах, для заточки режущего инструмента при производстве мерительного инструмента.
Электрополирование, кроме устранения трудоемких и вредных механических операций шлифования и полирования, ликвидирует затруднения, которые вызываются твердостью или вязкостью полируемого изделия, и операции обезжиривания изделий, что крайне необходимы при механическом полировании. Высокая производительность процедуры при этом не зависит от твердости металла. Электролитической полировке одинаково хорошо поддаются алюминий и мягкая красная медь, закаленная цементированная сталь и инструменты из твердого сплава.
Недостатком является увеличенный расход электроэнергии. Некие неудобства связаны с тем, что практически каждый металл требует своего состава электролита. Продолжительность процесса зависимо от плотности тока достигает 20 - 30 минут. Обычно при таких манипуляциях снимается слой металла, что имеет толщину 2 - 5 мкм.
Электрополировка с использованием кругов
Для шлифовально-полировальной работы принято использовать специальные полировальные станки с валом электрического мотора, который с обеих сторон удлинен для закрепления полировального инструмента. Подобные станки имеют регулятор, который позволяет регулировать частоту вращения щеток и кругов в значительных пределах.
Полировальные диски
Изделия и детали, которые подлежат электрополировке, не должны иметь слишком глубоких рисок и царапин, потому что вывести их с помощью данной методики чрезвычайно трудно, а зачастую почти невозможно. Помните, чем мягче металл, который подвергается полировке, тем легче с него снять слой, но сложнее достичь однородной поверхности. Полирование твердого металла принято проводить с большим удельным давлением на обрабатываемую поверхность.
В качестве полировальных кругов применяют войлочные диски, диски из кожи, шерсти и хлопчатобумажных тканей. Для механического полирования берут щетки, изготовленные из щетины и латуни. Для подобного полирования дополнительно используют смеси или суспензии. Обычно для полировки металла необходимо два круга – войлочный диск для грубой полировки и тканевый для тонкой.
Войлочные полировочные диски для электрополировки нержавейки или алюминия представляют из себя несколько слоев войлока, которые имеют толщину до 4 сантиметров, скрепленных между собой клеем. Слои войлока при изготовлении шлифовочного диска плотно прижимают друг к другу и ставят под пресс.
После того, как они приклеятся, и клеящий состав высохнет, принято проделывать в середине круга отверстие. После этого круг закрепляют на валу электроточила при помощи двух гаек с шайбами. Подобный шлифовальный круг также легко закрепляется в патроне сверлильного станка или электродрели.
Матерчатый диск можно вырезать из хлопчатобумажной ткани, сукна, миткаля или бумазеи, после чего сшиваются слои диска вместе в несколько слоев. Сшитые круги нужно склеить между собой, оставляя по краю 3-4 сантиметра. Диск насаживают на патрон сверлильного устройства таким способом, как и крепился войлочный диск.
Рабочий процесс
Прижмите металлическую поверхность к вращающемуся диску, чтобы начать процедуру электрополировки в домашних условиях. Рабочую поверхность кругов при полировании рекомендуется периодически смазывать специальной полировальной смесью, причем в определенной дозировке.
Помните, что круг будет «салить» деталь при избытке смеси, при её недостатке круг быстро износится, а металл не получит желаемого блеска. Поэтому при смазывании полировальных кругов свободной от полировальной смеси оставляйте примерно четверть рабочей поверхности.
Эластичные круги должны вращаться и прижиматься к деталям с определенным усилием, сама полируемая деталь должна по отношению к кругу свободно передвигаться. Электрополировку с применением смесей можно осуществлять торцом или периферией круга. Перемещение изделий производят непосредственно особым приспособлением или рукой.
Частота вращения круга на полировальном станке составляет 2000—2800 оборотов в минуту. Полировальные станки с большой частотой вращения кругов используют, когда требуется значительное качество обработки. Для достижения зеркального блеска электрополировку алюминия осуществляют при более низких частотах.
Если изделия, которые предстоит подвергнуть воздействию полировки, имеют простую форму — плоскую или квадратную, то вы можете их обработать на универсальном электрическом станке, где установлен полировальный круг прямого профиля. Для проведения грубой обработки предназначены твердые и жесткие круги, для тонкой — мягкие.
Твердые круги интенсивно полируют, но быстро засаливаются, особенно при обработке мягкого цветного и драгоценного металла или его сплава. Мягкие эластичные круги малоэффективны на предварительных операциях и способны деформироваться и расплющиваться при сильном прижатии к обрабатываемой детали.
Периодически отнимайте диск от металлической детали для оценки качества создаваемой полировки. Когда внешний вид металла вас удовлетворит, а деталь станет идеально гладкой, блестящей и ровной, можно остановить процесс. После этого повторите процедуру на тряпичном диске, который способен снять с поверхности металла остатки полировочного вещества.
Электрохимическая полировка
Электрохимическое полирование представляет собой процесс, который характеризуется химическими реакциями между обрабатываемым изделием и электролитом под действием электрического тока. Эта процедура приводит к уменьшению шероховатости и возникновению зеркального блеска.
Микро- и макро-полирование
Для проведения электрохимического полирования обрабатываемое изделие, которое является анодом, соединенным с плюсом источника тока, помещают в ванну с электролитом. Второй электрод – медные катоды. Благодаря специальному составу электролита для электрополировки и созданным условиям (формирование пленки повышенного сопротивления) фиксируется неравномерное растворение.
В первую очередь будут растворяться наиболее выступающие точки, вследствие чего уменьшается шероховатость, а потом исчезнет совсем, и поверхность детали станет блестящей и гладкой. Избирательное растворение подобных торчащих элементов протекает одновременно с получением блеска.
Процесс удаления больших выступов называют макро-полированием, а растворение малых неровностей - микро-полированием. Если эти два процесса протекают одновременно, то поверхность металла будет приобретать гладкость и блеск. Бывают ситуации, когда данные качества являются друг с другом несвязанными, то есть блеск достигается без сглаживания и наоборот.
В процессе электрохимической полировки на поверхности анода образуется гидроокисная или окисная пленка. Если она покрывает поверхность равномерно, то создаются условия, что необходимы для микро-полирования. Внешняя часть подобной пленки будет непрерывно растворяться в электролите.
Поэтому для успешной процедуры требуются условия, в которых существует равновесие между скоростями формирования окисной пленки и ее химического растворения, чтобы толщина пленки была неизменной. Наличие пленки подразумевает возможность совершения обмена электронами между полируемой деталью и ионами электролита без риска разрушения агрессивным электролитом металла.
Процесс макро-полирования зависит от наличия прианодной пленки, которая является более толстой в углублениях и тонкой на выступах. Подобная пленка способствует быстрому растворению выступов, потому что на них создается высокая плотность тока, а электросопротивление над ними будет меньше, чем над различными углублениями.
Эффективность действия прианодной пленки увеличивается с возрастанием ее внутреннего сопротивления. Электролиты, которые содержат комплексные соли или соли слабодиссоциирующих кислот, способны повышать сопротивление прианодной пленки.
Электролиты и растворители
На течение процесса электрополировки кроме прианодной пленки оказывают действие и другие факторы, такие как движение анода, что состоит в механическом перемешивании электролита. Электролиты некоторого состава способны нормально функционировать только при нагреве. Общее правило кроется в следующем: увеличение температуры способно снижать скорость нейтрализации и повышать скорость растворения пленки.
Значимыми факторами, которые влияют на течение процедуры электрохимической полировки, выступают напряжение и плотность тока. Зависимо от обрабатываемого металла и состава электролита принято вести полирование при режимах, которые соответствуют разным участкам кривой. К примеру, полировку меди в фосфорной кислоте проводят при режиме предельного тока без образования кислорода.
Самое большее распространение получили электролиты, изготовленные на основе серной, хромовой и фосфорной кислоты. Для увеличения вязкости раствора в него вводят метилцеллюлозу и глицерин. В качестве ингибиторов травления принято добавлять в электролит триэтаноламин и сульфоуреид.
Для очистки изделий после процедуры электрополировки принято использовать растворители, которые изготовлены на основе хлорированных углеводородов — перхлорэтилен и трихлорэтилен.
Эти вещества являются негорючими, их способность к удалению паст и жировых загрязнений с изделий выше, чем у этилового спирта или бензина. Изделия нужно загрузить в ванну, обработать мягкой волосяной щеткой, перегрузить в сосуд с нагретым нашатырным спиртом, где удаляться остатки паст и жир.
В качестве щелочного моющего средства применяют щелочи (едкое кали, едкий натр), поташ, соду и нашатырный спирт. В последние годы популярностью все больше пользуются моющие составы на основе всевозможных поверхностно-активных веществ. С успехом можно использовать ванны, в которых процесс очистки проводится в поле ультразвука, что существенно увеличивает производительность и качество очистки поверхности.
Ванны для электрополировки
Для электрохимического полирования принято изготавливать специальные ванны. Помните, что они являются очень опасными для здоровья, особенно при высокой температуре. Для полировки изделий из цветных и черных металлов, в частности из углеродистой стали, самым популярным остается универсальный электролит.
Его состав такой: ортофосфорная кислота (65%), серная кислота (15%), хромовый ангидрид (6%), вода (14%). Режим работы: температура около 70-90 градусов по Цельсию, напряжение на уровне 6-8 В, анодная плотность тока примерно 40-80 а/дм2, выдержка 5-10 минут.
Электрополировку нержавеющей стали - хромоникелевой и хромоникельмолибденовой принято проводить в следующем растворе: ортофосфорная кислота (65%), серная кислота (15%), хромовый ангидрид (6%), глицерин (12%), вода (13%).
Режим работы данного раствора: температура порядка 45-70 градусов по Цельсию, анодная плотность тока близко 6-7 а/дм2, уровень напряжения 4,5-6 В. Выдерживают деталь в такой ванне 4- 30 минут: для штампованных изделий достаточно 4-6 минут, для деталей после термической обработки или сварки 10-12 минут, для литых отпескоструенных изделий из стали - полчаса.
Для полирования изделий из алюминия или его сплава применяют хорошо зарекомендовавший себя электролит такого состава: ортофосфорная кислота (65-70%), хромовый ангидрид (8-10%), вода (20-27%). Режим работы: температура на уровне 70-80 градусов, в свежеприготовленном растворе плотность тока должна достигать 10-30 а/дм2, в насыщенном солями растворе - 10-20 а/дм2. Выдерживают деталь 5 минут и больше.
Для электрополировки деталей из дюралюминия необходим такой состав раствора: серная кислота (40%), ортофосфорная кислота (45%), хромовый ангидрид (3%), вода (11%). Режим работы: температура в пределах 60-80 градусов Цельсия, анодная плотность тока на уровне 30-40 а/дм2, уровень напряжения 15-18 В, выдержка – пара минут.
Таким образом, при необходимости электрополировки деталей в домашних условиях вы можете пойти двумя путями – изготовить специальное оборудование с валом электромотора и полировально-шлифовальными кругами или оборудовать ванну полирования и приготовить нужный для данного случая электролит. Что ближе – выбирать вам!
strport.ru
Электрополирование: особенности процесса
Главная » Литература » Статьи » Электрополирование: особенности процессаАвтор: Стивен Ф. Руди
В данной статье речь пойдет о практическом применении, режимах, рабочих параметрах, требованиям к оборудованию, анализе, решении проблем и контроле процесса полирования.
Источник энергии не должен находиться в непосредственной близости от высоко-агрессивного раствора полирования, то же самое относится ко всему сопутствующему оборудованию.
Важно знать всю информацию о безопасности, относящуюся к обработке, хранению и транспортировке растворов для полирования. Это включает в себя защитное обёртывание и понимание относящихся к вопросу документов, таких как технические бюллетени и данные о материальной безопасности (с копиями в офисе и Министерстве профессиональной безопасности и здравоохранения). Резервуары должны быть правильно помечены согласно местным и федеральным законам, а также законам штата. 0,001 квадратных дюйма меди несут примерно 1,0 А тока. Расположенная ниже информация – типичный пример нержавеющей электрополированной стали. Держатель и температура ванны могут быть изменены, так чтобы соответствовать требованиям обработки других металлов и сплавов.
Общие операционные параметры
Температура | От 80 до 220 Фаренгейт (27 – 104 градуса Цельсия) |
Оборудование (*) | Устойчивые к кислоте материалы |
Откачка | Требуется |
Энергоснабжение | DC Ректификатор, 6-20 вольт |
Встряхивание | Движение раствора (циркуляционный насос или воздух) |
Подогревание | Паровые кольца, электропогружение |
Катоды | Медь, свинец или нержавеющая сталь |
Держатель | Медь, титан или медь, покрытая пластизолем (с титановыми вкраплениями) |
(*) Ванна электрополирования нержавеющей стали должны поддерживать раствор плотностью приблизительно 1,7 кг на литр |
Типичные операционные параметры для электрополирования нержавеющей стали
Температура(никелевые сплавы) | 130 - 180 Фаренгейт (54 – 820С) |
Температура(неникелевые сплавы) | 190 – 210 Фаренгейт (88 – 990С) |
Плотность тока | 150 – 450А (кв. фут) (16,1 – 48,4 А/дм2) |
Рабочее напряжение | 6 – 18 вольт |
Соотношение катодов и анодов | 10:1 к 1:1 |
Время электрополирования | 3 минуты (как обычно) |
Максимальный токовый вход | 5 А/галлон |
Расстояние от частейдо катодов | 2 – 6 дюймов |
Расстояние до днища резевуара | По крайней мере 6 дюймов |
Во время электрополирования количество удаляемого металла может варьироваться от 0,00005 до 0,00001 дюймов на обрабатываемую поверхность за минуту электрополирования. Это зависит от рабочей плотности тока. Расстояние от катода до края критично для обеспечения предпочитаемого химического действия. Небольшое расстояние может привести к разъеданию и вытравливанию. Важно, чтобы части в нижнем ряду были по крайней мере на 6 дюймов выше нижнего ряда. Во время процесса электрополирования появляются металлические осадки. Данная рекомендация минимизирует контакт частей с осадком (если ванна обрабатывается надлежащим образом). Если превзойти максимальный токовый вход, то электролит перегреется, и потребуется источник охлаждения, такой как катушка. Требуемое напряжение основано на температуре ванны, рабочей нагрузки, формы частей, требованиях к обработке поверхностей и расстояния от частей до катодов. Электрополирование обладает низкой рассеивающей способностью, поэтому требуется сравнительно высокая плотность тока.Типичные стадии процесса:
Очень важно, чтобы поверхность не содержала масел и жиров. Электрополирование не удалит эти типы органических загрязнений. Удаление окалины необязательно, так как электрополирование хорошо удаляет окалину. Важно также полоскание после электрополирования, не только для того, чтобы смыть электролит с частей, но и минимизировать содержание воды с растворённым металлом. Чтобы ускорить промывание сложных форм или частей, где остаётся растворённая кислота – электролит, можно использовать погружение в мягкий щелочной раствор кальцинированной соды для нейтрализации. Затем промойте чистой водой. Обычно нержавеющая сталь не требует никакой дополнительной обработки. Анализ и контроль поддержания в исправном состоянии.
Большинство методов аналитического контроля требуют нескольких стандартных процедур для поддержания оптимального химического баланса электролита. Вот это можно резюмировать следующим образом:
Титрование кислот. К примеру, электролиты нержавеющей стали содержат по крайней мере две неорганические кислоты вдобавок к другим поддерживающим добавкам. Кислоты можно разложить титрованием, используя двухэтапную процедуру, включая разные конечные точки pH. С распадом каждой кислоты определяется соотношение. Текущие или корректирующие добавки (определяется по ситуации) могут быть сделаны, если электролит концентрирует или разделяет кислоты.
Относительная плотность. Измерение относительной плотности используется там, где электролит находится в рекомендуемом диапазоне рабочей ванны, при определённой температуре раствора. Сюда включаются все растворённые металлы и вода. В этой статье данные составляющие ванны описываются приблизительно. Параметры ванны надо измерять ежедневно, если ванна постоянно используется в производстве. Полученные данные позволяют вовремя изменять параметры всей ванны или её части добавлением концентрированного электролита или воды.
Распад растворённых металлов. Эта реакция связана с относительной плотностью. Когда ванна электрополирования накапливает ампер-часы операции, концентрация растворённых металлов растёт. По ходу этого процесса относительная плотность электролита будет увеличиваться, и также будет наблюдаться тенденция к появлению осадка. На некоторые реакции электрополирования негативно влияет появление некоторых металлов, таких как железо, при обработке нержавеющей стали. Существует точка, на которой рекомендуется замещение электролита, иногда на базе ампер-часов. Такое восстановление важно для поддержания желаемых результатов при обработке поверхности электрополированием.
Аналитический контроль не сложен, но его важность нельзя недооценивать или игнорировать. Как с любыми другими процессами металлообработки, хорошие покрытия основаны на контроле качества процесса, происходящего в ванне. Совместите это с оптимальными параметрами, и Вы добьетесь высокого качества электрополирования на постоянной основе.
Проблемы в процессе
Проблема |
Исправление |
Недостаточная обработка | Изменить операционные параметры и откорректировать химический состав ванны |
Разъедание | Откорректировать уровень очистки и интенсивность перемешивания и параметры ванны |
Ржавчина | Плохое, медленное, недостаточное или загрязнённое ополаскивание |
Выделения газа, полоски | Изменить напряжение или интенсивность перемешивания раствора |
Тусклость, наличие пятен | Улучшите очистку перед электрополированием |
Другие проблемы включают в себя механические и электрические аспекты (плохое соединение или проблемы с выпрямителем). Проблема может состоять в том, что был выбран неправильный электролит или электрополирование нельзя применять в конкретном случае.
Ограничения
Электрополирование необязательно скроет или покроет дефекты поверхности, такие как неметаллические включения или швы. Грубые и агрессивные царапины могут остаться. Если определённые дефекты, такие, как углубления от вытравливания, шероховатость или тусклость обнаруживаются на одной из заключительных стадий, то их устранение может оказаться серьезной проблемой. Некоторые характеристики поверхности, такие как серьёзная «апельсиновая корка» или мягкая структура, не позволяют проводить электрополирование. Сплавы должны быть проверены на совместимость. Например, мультифазовые сплавы требуют другого подхода, чем обычная анодная обработка. Литые металлы из-за высокой пористости плохо поддаются электрополированию.
echemistry.ru
Электрохимполировка нержавеющей стали | Химполирвока нержавейки
Электрополировка — это электрохимический процесс удаления металлического материала; в этом смысле она может рассматриваться как метод, противоположный электроосаждению. После замыкания цепи ток начинают циркулировать внутри системы, и на металлической поверхности образуется анодная плёнка. Считается, что при определённых условиях эта анодная плёнка может быть ответственной за выравнивание и поверхностную полировку. Тип и характер этой плёнки наряду с оперативными условиями определяют, осуществляется ли полировка и выравнивание одновременно или по отдельности; на самом деле следует напомнить, что одно совсем не подразумевает другое. Помимо анодной плёнки, есть и другие факторы, влияющие на конечный результат. Среди них стоит упомянуть механические колебания системы из-за движения воздушных масс или анодного вращения, нагрев системы (с термостатическим контролем температуры), плотность приложенного тока или напряжения. С увеличением напряжения плотность тока также возрастает, пока не достигнет критической точки, где сила тока резко снижается, в то время как разность потенциалов продолжает увеличиваться (потенциал первичной пассивации). За пределами этой точки ток остаётся почти постоянным, сколько бы ни увеличивался потенциал. Это так называемый «этап пассивации» — момент, когда материал покрывается оксидным слоем, защищающим его от коррозийного воздействия анодного тока. Интервал, в котором ток остаётся постоянным, изменяется в зависимости от режима работы и материала. Когда потенциал доходит до критической точки транспассивации, ток снова начинает увеличиваться пропорционально напряжению, достигая впоследствии предельного значения, где образование газа начинает преобладать над растворением металла. Электрополировка происходит только тогда, когда плотность тока выше, чем в критической точке (ток, соответствующий потенциалу первичной пассивации). В большинстве методов электрополировки используется постоянный ток, хотя в некоторых из недавно опубликованных статей говорится о возможности использования переменного тока при соблюдении особых условий. Обычно используемые значения — 1-10 A/cm2.
passivator.ru
Электрополировка нержавеющей стали, алюминия, титана, латуни и меди
Электролитно-плазменная полировка — современный метод финишной обработки поверхности металла, основанный на процессах в приповерхностного слоя. Для снятия микрослоя поверхности деталь (анод) погружают в раствор солей аммония.
Сущность метода
Доказано, что качество электроплазменной полировки зависит от рабочего напряжения.
Минимальное пороговое значение напряжения | В |
Нержавеющие стали | 220 |
Медь и сплавы на основе меди (бронза, латунь) | 260 |
Сплавы на основе алюминия | 270...290 |
Сплавы на основе титана | 280...300 |
Обработка детали методом ЭПП – идеальная подготовка поверхности к последующему нанесению слоя ионно-вакуумного покрытия (нитрида титана и др.).
Что дает применение метода
Технические характеристики поверхности после обработки.
В течение нескольких минут обработки деталь приобретает зеркальный блеск. Методика отработана для применение электролитно-импульсной полировки деталей из нержавеющих сталей, сплавов на основе меди (латуней и бронз различного состава), алюминия, титана – доводит поверхность до зеркального блеска. Применительно к хромистым сталям нержавеющего класса, марки 201, 304, 316, 321 по классификации AISI (от 08Х18Н10 до 12Х18Н10Т, 12Х15Г9НД), чем больше хрома в нержавеющей стали тем лучше будет «эффект зеркала».
Методом электролитно-плазменной обработки полируют изделия из сталей и сплавов цветных металлов:
Компания ООО «АЦИА» принимает заказы на электролитно-плазменную полировку изделий и деталей из нержавейки, латуни, бронзы, сплавов титана и алюминия до зеркального блеска: перила, корпуса светильников, закладные бассейнов, торговое оборудование и многое другое.
Стоимость работы зависит от материала и площади обработки – рассчитывается индивидуально.
Важные особенности полировки:
Компания ООО "АЦИА" также выполняет полировку горячекатаной нержавеющей стали.
acea-spb.ru
Электрохимическое полирование - Химическая обработка

Категория:
Химическая обработка

Электрохимическое полирование представляет собой процесс, обратный гальваническому осаждению металлов: обрабатываемую деталь помещают в качестве анода в ванну с электролитом и при заданном режиме (плотности тока, температуре и времени погружения) осуществляют съем металла. Процесс анодного растворения используют в операциях очистки поверхности металла, удаления заусенцев и грата, заострения, полирования.
Наибольший интерес представляет электрохимическое полирование. Такое полирование наиболее широко распространено в промышленности, но оно весьма трудоемко, плохо поддается механизации и автоматизации. Этим процессом определяются такие важнейшие критерии качества поверхностного слоя, как макро- и микрогеометрия, наклеп, микроструктура, остаточные напряжения. В прямой зависимости от этих критериев находятся эксплуатационные свойства деталей машин и механизмов — усталостная прочность, отражательная, теплоизлучающая и теплопоглощающая способность, обтекаемость жидкостями и газами, коррозийная стойкость.
Полирование определяет также эстетику изделия.
Сущность процесса
Электрохимическое полирование основано на анодном растворении обрабатываемой поверхности при режимах, которые обеспечивают интенсивное растворение микровыступов шероховатой поверхности и замедленное растворение во впадинах. В результате неравномерной скорости растворения шероховатая поверхность сглаживается, и появляется заметный блеск.
Только в случае преимущественного растворения микровыступов на поверхности металла происходит полирование (сглаживание).
Преимущественное растворение микровыступов может происходить тогда, когда у поверхности металла в результате электролиза образуется пленка низкой электропроводности, состоящая из продуктов анодного растворения.
Рис. 1. Схема образования вязкой пленки:а — впадины; б — вязкая пленка; в — выступы; г — силовые линии тока.
В этом случае толщина пленки, а следовательно, и электрическое сопротивление ее в микровпадинах будут больше, чем на выступах, что и приведет к более интенсивному растворению выступов.
Растворимость анодных продуктов в электролите, скорость диффузии их в электролит, состав и физико-химические свойства анодной пленки имеют существенное значение для процесса полирования. Поэтому этот процесс у различных материалов происходит неодинаково. У многих металлов и сплавов (медь, никель, алюминий, нержавеющие хромистые и хромоникелевые стали) сглаживание сопровождается появлением блеска на обработанной поверхности. У некоторых сплавов (стали карбидного класса, бронзы, латуни) наблюдается блеск без заметного сглаживания шероховатостей. Ряд металлов и сплавов (олово, свинец, серый чугун, высококремнистые стали) вовсе не полируется. Вместо сглаживания образуется’ сильно травленая поверхность с толстыми темными пленками.
Существует несколько гипотез, по-разному объясняющих процесс электрохимического полирования, причем следует отметить, что ни одна из них не объясняет полностью все данные опыта. Наиболее вероятной и логически объясняющей сущность процесса является гипотеза вязкой пленки. Согласно этой гипотезе, электрохимическое полирование может происходить лишь при образовании на поверхности анода в процессе анодного растворения вязкой пленки.
Вязкая пленка состоит из продуктов анодного растворения, обладающих высоким электрическим сопротивлением. Покрывая тонким слоем шероховатую поверхность полируемого металла, эта пленка приобретает неодинаковую толщину на различных участках поверхности. На выступах толщина пленки и соответственно ей критическое сопротивление меньше, чем во впадинах.
Вследствие различного сопротивления пленки и способности электрического тока концентрироваться на остриях плотность тока на выступах будет больше, чем во впадинах. Поэтому скорость растворения вершин выступов будет больше скорости растворения дна впадин. В результате неравномерного распределения плотности тока и вследствие этого различной скорости растворения возникает сглаживание шероховатой поверхности.
Достоинства и недостатки электрохимического полирования
Электрохимическое полирование металлов имеет свои достоинства и недостатки. Главное достоинство метода — высокая производительность. Время полирования практически составляет не более 10 мин., причем габариты детали и форма ее не влияют на производительность. Возможна одновременная обработка такого количества деталей, какое помещается в ванне. Производительность процесса не зависит от твердости и вязкости обрабатываемого материала. Электрохимическое полирование позволяет обрабатывать детали не только простых очертаний, но и сложного профиля, а также внутренние полости, трудно доступные или вовсе не доступные при механическом полировании.
Основное отличие электрохимически полированной поверхности от механически полированной — отсутствие на ней каких-либо следов деформации и структурных изменений. Это — естественное следствие сущности электрохимического процесса, который осуществляется не только без приложения каких бы то ни было механических усилий к обрабатываемой поверхности, но и вовсе без физического прикосновения к ней.
Больше того, электрохимическое полирование удаляет механически деформированный поверхностный слой металла и восстанавливает его истинное строение. В результате анодного растворения поверхность оказывается свободной от механических и термических изменений. Улучшается микрогеометрия; блеск поверхности оказывается больший, чем у механически полированной.
Электрохимическое полирование выявляет дефекты в металле (неметаллические включения, трещины, волосовины, неоднородность структуры).
Поверхности, электрохимически полированные, пассивируются и благодаря этому в 4—6 раз лучше сопротивляются коррозии; они обладают повышенными оптическими свойствами.
Процесс не требует применения полировальных станков, фетровых кругов, абразивных порошков, паст. Возможны автоматизация обработки и одновременное обслуживание нескольких ванн. Значительно облегчаются и оздоровляются условия труда.
Перечисленные достоинства характеризуют несомненное превосходство электрохимического метода над механическим. Однако на нынешней ступени развития этому методу присущи и серьезные недостатки, которые ограничивают применение электрохимического полирования.
Один из основных недостатков — незначительная эффективность сглаживания. Электрохимическим полированием можно улучшить чистоту поверхности на 1—2 класса, причем оно эффективно, если исходная шероховатость не грубее 4—5-го классов. Поэтому при необходимости достигнуть 12—13-го классов приходится механически подготовлять поверхности до 10—11-го классов. Грубо обработанная поверхность (после точения, фрезерования, шлифования), подвергнутая электрохимическому полированию, почти сохраняет макрорельеф поверхности. Сглаживаются полностью лишь отдельные микровыступы и наблюдается закругление гребешков.
Попытки многих исследователей повысить эффективность сглаживания и, по существу, решить задачу электрохимического шлифования практически не привели к положительным результатам. Повышение эффективности сглаживания требует прежде всего применения высоких плотностей тока (более 100 а/см2), что, в свою очередь, приводит к растворению больших толщин металла (0,5—1 мм).
Необходимое время полирования обычно определяется опытным путем и находится, как правило, в пределах 8—10 мин. при полировании сталей. Увеличение производительности полирования сверх 10 мин. не только не ведет к улучшению качества поверхности, но часто, наоборот, ухудшает ее.
Сглаживание следов механической обработки происходит постепенно: после первых 3—4 мин. электрохимического полирования наблюдается уничтожение мелких рисок и появление гладких полированных площадок; после 10 мин. на поверхности остается рельеф грубых рисок, которые в дальнейшем полностью не исчезают, а лишь закругляются, образуя волнистую поверхность. Мы проводили исследования сглаживания при изменении времени полирования от 2 до 20 мин.
Увеличение времени полирования приводит к еще большему растворению металла. Кроме того, оно может вызвать в сплавах вытравливание отдельных структурных составляющих.
Данные этой таблицы показывают, что при возрастании времени полирования шероховатость поверхности улучшается. Однако, начиная с 10 мин. выдержки, улучшение это незначительно, и через 15 и 20 мин. сглаживание наших образцов (сталь У10 закаленная) происходило примерно с одинаковой эффективностью. К этому следует добавить, что значительная эффективность сглаживания сопровождается большим съемом металла. В процессе полирования за 10 мин. растворяется слой металла толщиной 60—100 мк.
Это резко искажает форму и размеры деталей, подвергаемых полированию, и превосходит припуски, оставляемые обычно на полирование.
Кроме того, интенсивное растворение металла приводит к накоплению в электролите большого количества железа (Ре20з). При накоплении Fe203 в количестве 6% к весу электролита полирование становится невозможным.
Так, например, ванна емкостью 10 л при полировании деталей с поверхностью 0,5 дм2 способна практически работать 4—6 суток. Затем железо должно быть удалено из раствора или электролит следует заменить вновь приготовленным.
Однако еще задолго до полного насыщения электролита железом состав электролита в процессе эксплуатации изменяется. Контроль его производят ежедневно, определяя удельный вес, и соответственно корректируют. Убыль воды в результате испарения восполняют довольно частым добавлением горячей воды.
Помимо контроля удельного веса электролита необходимо периодически осуществлять анализ на содержание Сг03, Cr203, h3S04, Н3РО4 и Fe203 и корректировать состав электролита.
При накоплении в электролите 1,5% Сг20з производят под действием тока окисление трехвалентного хрома в шестивалентный, а после окисления электролит прогревают в течение часа при 90—110 °С.
Анализ и корректировка кислот и удаление железа из электролита являются еще более затруднительными операциями. Таким образом, сложность корректировки состава электролита и, в конечном счете, короткий срок службы электролита являются еще одним весьма существенным недостатком электрохимического полирования. Расчеты показывают, что в результате непродолжительного действия электролита и, следовательно, большого удельного расхода кислот электрохимическое полирование в ряде случаев оказывается экономически нерентабельным.
Рис. 2. Зависимость съема металла от времени полирования (углеродистые стали).
Оборудование для электрохимического полирования
Оборудование, предназначенное для осуществления процесса электрохимического полирования, весьма сходно по конструкции с оборудованием, имеющимся в цехах металлопокрытий для операции хромирования.
Основным оборудованием являются ванны, источники постоянного тока низкого напряжения и приборы для измерения и регулирования электрического режима.
Ванны.
Ванны должны быть снабжены электронагревателями, помещенными в защитных, химически стойких, оболочках внутри самой ванны, и водяной рубашкой. Применение двойного нагрева необходимо потому, что при приготовлении и проработке электролита приходится нагревать его до 110—120°С, а в процессе полирования необходимо поддерживать температуру 70—80 °С. Применение водяной рубашки исключает возможность перегрева электролита. Кроме того, она используется для охлаждения проточной водой электролита, который часто перегревается в процессе полирования.
Внутренняя поверхность ванны должна быть облицована химически и температуростойким материалом. В качестве таких материалов для наиболее агрессивного сернофосфорнохромового электролита следует применять свинец, фторопласт-4 либо покрытия из суспензии фторопласта ЗМ или химически стойкой силикатной эмали марки ЛК-1.
В лабораторных условиях могут быть использованы жаростойкое стекло, фарфор, керамика.
Источником питания ванн обычно служат выпрямители селеновые марки ВСГ-ЗМ, купрокеный ВКГ-100 либо германиевый ВАГЗ-9/12-600. При необходимости возможна совместная работа нескольких выпрямителей.
Регулирование тока осуществляется по-разному, в зависимости от режима работы ванны и источника питания. В последнее время в промышленности применяется плавное бесступенчатое регулирование тока изменением напряжения в первичной обмотке трансформатора. Трансформатор смонтирован совместно с селеновым или германиевым выпрямителем. Подробное описание оборудования и схем для регулирования электрического режима можно найти в специальной литературе.
Составы электролитов, их приготовление и корректирование
Для электрохимического полирования предложены сотни различных по составу электролитов.
Это свидетельствует прежде всего о том, что до сих пор не найден состав электролита, который бы удовлетворял следующим основным требованиям:1) высокой сглаживающей способностью;2) длительной работоспособностью;3) способностью полирования многих металлов и сплавов;4) безопасностью в эксплуатации.
В результате испытаний разных электролитов установлено, что наиболее универсальным в современной технике является электролит, основой которого служит фосфорная кислота с добавлением серной кислоты и хромового ангидрида (фосфорносернохромовый электролит). Всестороннее изучение указанного электролита показало, что в нем практически возможно полировать большое количество марок сталей — от углеродистых до высоколегированных, включая нержавеющие и инструментальные стали. В этом электролите также возможно полировать медь, алюминий и некоторые марки сплавов на их основе.
Рис. 3. Ванна для электрохимического полирования:1 — корпус наружной ванны; 2 — корпус внутренней ванны; 3 — нагреватель.
Приготовление и корректирование электролита
Порядок приготовления электролита следующий: смешивают фосфорную кислоту уд. веса 1,54 и серную кислоту уд. веса 1,82.
В отдельном сосуде растворяют в воде хромовый ангидрид. После отстаивания сливают его в ванну полирования. Затем вливают в ванну расчетное количество ортофосфорной кислоты уд. веса 1,54, а затем серной уд. веса 1,82. Полученную смесь прогревают при 140° С в течение примерно 1,5—2 час. до достижения уд. веса 1,73—1,74 (для полирования углеродистых сталей) и при 110—120 °С — до удельного веса 1,64 (для полирования нержавеющих сталей).
Опыт эксплуатации фосфорносернохромового электролита показывает, что работоспособность его во многом зависит от того, насколько поддерживается в процессе полирования соотношение соединений шестивалентного и трехвалентного хрома.
Если прикатодное пространство не изолировано от общего объема ванны, то в процессе полирования на катоде происходит восстановление хромовой кислоты, причем продукты восстановления повышают вязкость электролита, доводя его до непригодного состояния. Поэтому рекомендуется прикатодную зону изолировать пористой диафрагмой.
Диафрагма представляет собой узкий керамический пористый сосуд (прямоугольный или цилиндрический), в который помещается катод. Материалом для изготовления диафрагм служит смесь красной и шамотной глины (30% шамотной глины) и песка. В зависимости от габаритов катодов и ванны диафрагма формуется с возможно более тонкими стенками и обжигается при 1000— 1100 °С.
При пользовании диафрагмой срок службы электролита возрастает в 5—6 раз. Анодное окисление трехвалентного хрома при накоплении его свыше 2% ведут при анодной плотности тока 10—15 а/дм2, напряжении 10—12 в и температуре электролита 60 °С. Соотношение анода к катоду 1 : 10. Материалом анодов и катодов служит свинец. После окисления электролит рекомендуют прогреть в течение часа при 90—110 °С.
Особенности электрохимического полирования
Исследование работы фосфорносернохромового электролита показывает, что все три кислоты оказывают взаимно благоприятное влияние. Увеличение содержания фосфорной кислоты позволяет понизить плотность тока и напряжение, тогда как увеличение содержания серной кислоты повышает пределы плотности тока. Изменяя концентрацию и соотношение кислот, возможно установить области полирования для заданной марки материала.
Рис. 4. Схема изоляции прикатодной зоны:1 — электролит в ванне; 2 — диафрагма; 3 — электролит прикатодной зоны; 4 — катод; 5 — анод.
Рис. 5. Полирующая способность фосфорносернохромовых электролитов при полировании: а — углеродистых и низколегированных сталей; б — нержавеющих хромистых сталей.
Полирование сталей. Фосфорносернохромо-вые электролиты обладают полирующей способностью в широких пределах концентраций: от 60 до 85% фосфорной кислоты и от 15 до 40% —серной кислоты. На рис. 26 приведены диаграммы, иллюстрирующие области полирующей способности электролита углеродистых и нержавеющих групп сталей. Электрохимическое полирование каждой группы сталей имеет свою особенность. При полировании углеродистых сталей, если необходимо максимально сгладить шероховатости и не требуется блеск, следует увеличить содержание воды в электролите до 30—35%, а хромовой кислоты — до 12—15%. В этом случае при плотности тока 15—25 а/дм2 и температуре электролита 70 °С обрабатываемая поверхность приобретает серебристый цвет. Если необходимо сгладить шероховатость с получением блеска, то целесообразнее осуществить процесс в двух растворах: сгладить в электролите с большим содержанием воды и придать блеск в другом электролите с меньшим содержанием воды.
Рис. 6. Профилограммы шероховатости механически обработанных и электрохимически полированных поверхностей нержавеющей стали:а — фрезерованная и электрохимически полированная после фрезерования; о — шлифованная и электрохимически полированная после шлифования.
Качество поверхности зависит от содержания углерода в стали и ее структуры. Наиболее легко полируются стали со структурой равномерно распределенного феррита и перлита. С увеличением содержания углерода в стали изменяется величина предельного тока, при котором наступает анодная пассивность.
Наименьший ток соответствует низкоуглеродистой стали (0,1%) с почти ферритной структурой; наибольший — среднеуглеродистой стали (0,45%) при соотношении феррита и перлита 1:1. При дальнейшем увеличении содержания углерода, когда структура становится более однородной и преобладает перлитная составляющая, предельный ток вновь снижается.
При полировании хромистых нержавеющих сталей в электролите при плотности тока 20—30 а/дм2 поверхность получается травленой и сглаживания не наблюдается. При плотности тока 40 а/дм2 наблюдается блеск без сглаживания. Наиболее эффективное сглаживание, сопровождаемое блеском, происходит при плотности тока в пределах 50—70 а/дм2. Этой плотности соответствуют профилограммы шероховатости поверхностей различно обработанной нержавеющей стали марки 2X13.
Из профилограмм следует, что поверхность, шлифованную абразивным кругом зернистостью 12 до 7-го класса, возможно отполировать до 9-го класса. Фрезерованную поверхность с шероховатостью 6-го класса возможно отполировать до 9-го класса.
Следует заметить, что в ряде случаев волнистость поверхности не мешает улучшению ее эксплуатационных свойств. Так, например, исходная фрезерованная поверхность после электрохимического полирования, будучи волнистой, обладает повышенной усталостной прочностью, лучшим сопротивлением коррозии и полным отсутствием деформированного слоя.
Температура электролита
Значительное влияние на качество поверхности оказывает температура. При низких температурах (30— 40 °С) полирования не происходит, и поверхность оказывается травленой, матовой. С повышением температуры поверхность становится более блестящей, но травление сохраняется. При температурном интервале 70—80°С получены лучшие результаты.
Для каждого электролита, режима полирования и полируемого сплава существуют пределы температур электролита, отвечающие лучшему качеству поверхности. При чрезмерном снижении температуры электролита против оптимальной повышается вязкость электролита и соответственно вязкость пленки на аноде, а также затрудняется диффузия продуктов анодного растворения. В результате замедляется процесс анодного растворения, полирующее действие электролита ослабляется или полностью прекращается и наблюдается травленая поверхность.
Чрезмерное повышение температуры ускоряет процесс анодного растворения, снижает вязкость электролита и пленки на аноде, облегчает диффузию и уменьшает омическое сопротивление электролита. С повышением температуры усиливается газообразование, на обрабатываемой поверхности появляются полосы и наблюдаются травленые участки.
Несоблюдение главным образом электрического и температурного режимов приводит к появлению различных дефектов при электрохимическом полировании.
Расстояние между электродами и их перемешивание
Расстояние между электродами оказывает заметное влияние на равномерность удаляемого слоя. Так, при расстоянии 20—40 мм происходит значительное растворение (от 0,2 до 0,6 мм). Увеличение расстояния до 150 мм не приводит к существенному улучшению равномерности съема. Увеличение расстояния не позволяет использовать необходимый ток вследствие высокого удельного сопротивления электролита.
Перемешивание электролита ухудшает качество поверхности, покрывая ее темным налетом, причем эффективность сглаживания не возрастает.
Особенности полирования меди
Возможно полирование меди и некоторых ее сплавов (латуней) и в одной ортофосфорной кислоте уд. веса 1,5 (716 г/л Н3Р04). Однако добавление к ортофосфорной кислоте хромового ангидрида позволяет осуществлять процесс полирования в широких пределах плотности тока (20—70 а/дм2) и сократить время полирования до 1—3 мин. Катодами служат свинцовые пластины. Соотношение поверхностей анода и катода 1 : 3.
В процессе полирования меди, как и при полировании сталей, уменьшается содержание воды, кислоты и происходит восстановление Сг03 до Сг20з. Корректирование электролита осуществляется так же, как и при полировании сталей. Вода добавляется до необходимого удельного веса, а кислота — по данным химического анализа. Сгг03 окисляется на аноде в Сг03.
Эффективность сглаживания электролита невелика. Поэтому подготовка механическим шлифованием должна заканчиваться на зернистости 5. Хорошо полируется без всякой предварительной подготовки листовой холоднокатаный материал. В этом случае должна быть проявлена забота о тщательном сохранении поверхности листа от царапин, забоин и других повреждений.
Следует иметь в виду, что раковины, поры и включения хорошо выявляются электрохимическим полированием. Скорость растворения меди при плотности тока 50 а/дм2 составляет 1 мк/мин, причем снижение удельного веса электролита с 1,5 до 1,3 ускоряет процесс растворения.
Особенности полирования алюминия
Характерная особенность полирования алюминия — интенсивное пассивирование полируемой поверхности и вследствие этого снижение плотности тока до очень малых плотностей (1—2 а/дм2) и повышение напряжения до 15—25 в. Эта особенность не должна смущать, хотя она наступает через 2—4 мин. после завешивания детали и несколько ухудшает блеск.
Если полирование осуществляется с целью получения высокой отражательной способности, рекомендуется в этом случае разрушать образующуюся окисную пленку кратковременным переключением тока с анода на катод (реверсированием) либо выключением тока на несколько секунд.
Резкое ухудшение качества полированной поверхности алюминия наступает в результате анодного растворения алюминия. При накоплении в электролите 30 г/л алюминия, по существу, прекращается работа ванны. Контроль и корректирование раствора осуществляют так же, как и в процессе полирования сталей.
Применение электрохимического полирования
Несмотря на существенные недостатки электрохимического полирования и все продолжающиеся исследования в данной области, этот процесс уже сейчас находит эффективное применение в некоторых производствах.
В то же время из-за отсутствия объективных данных и незнания особенностей электрохимического полирования часто возникают значительные затруднения или принимаются ошибочные решения в выборе этого метода.
Применение электрохимического полирования на нынешней стадии развития целесообразно прежде всего там, где затруднено или невозможно механическое полирование (недостаточные для механического полирования поверхности, недопустим нагрев или силовое воздействие, дефекты материала или механической обработки). Так, например, электрохимическому полированию подвергают различные детали арматуры.
Электрохимически полируют детали карбюратора (в частности, клапан подачи горючего из нержавеющей стали или фольги), тончайшую ленту, проволоку и трубы. Особый интерес представляет полирование труб длиной 6—8 м из нержавеющей стали Х18Н9Т. Механическая очистка внутренней поверхности длинных труб вызывает значительные трудности. Химическая очистка труб не решает задачи—она растравливает поверхность и не полностью очищает от окалины. Электрохимическим полированием внутренняя поверхность становится более гладкой, блестящей, повышается коррозийная стойкость, уменьшается трение жидкости и газов о стенки, обеспечивается высокая производительность процесса.
При полировании длинных труб крупного диаметра (больше 100 мм) и других крупных полых деталей внутренняя полость используется в качестве ванны-электро-лизера. Катод в этом случае монтируется в центре трубы. Полирование ведется с протоком электролита через трубу. Трудности полирования больших поверхностей труб заключаются в необходимости применения тока порядка 10 000 а. Столь большой ток вызывает чрезмерный разогрев электролита и выделение большого количества газов. К тому же трудно выполнима подводка большого тока, поэтому трубы крупных диаметров полируют на небольших участках, непрерывно подвигая катод вдоль трубы. Длина катода зависит от диаметра трубы. Например, для трубы диаметром 200 мм длина катода должна быть 170 мм. Электролит циркулирует под давлением до 4 атм, скорость перемещения катода — до 8 м/мин.
В настоящее время разработано несколько конструкций установок для полирования внутренней и наружной поверхностей труб различных диаметров.
Электрохимическое полирование находит применение и в производстве режущего инструмента. Образующийся при шлифовании инструмента дефектный слой легко снимается электрохимическим полированием. В результате повышаются стойкость инструмента и защита от коррозии. Например, электрохимическое полирование канавок сверл обеспечивает более легкий сход стружки при сверлении и меньший разогрев сверла.
Полирование сверл осуществляется партиями, а не по одному сверлу, как при механическом полировании. Объем ванны емкостью 150 л позволяет загружать одновременно до 30 сверл диаметром 10— 15 мм. Для быстрой загрузки сверл сконструированы приспособления — рамки.
Рис. 7. Полирование сверл:а — механическое; б — электрохимическое.
Для полирования 1000 сверл диаметром 10 мм в среднем расход электролита составляет 8,7 кг. Соответственно расходуется ортофосфорной кислоты 5,4 кг, серной кислоты — 2,5 кг и хромового ангидрида — 0,8 кг.
Уже указывалось, что электрохимическое полирование удаляет поверхностный слой металла, а многие дефекты материала выступают наружу. Когда преследуют цель декоративной отделки деталей, это свойство является недостатком метода. В случаях необходимости контроля качества поверхности это — несомненное достоинство.
Высокая чувствительность электрохимического полирования к неоднородности состава все больше используется в практике металловедческих лабораторий для контроля качества сталей: выявления микро- и макроструктуры, трещин, флокенов, волосовин, неметаллических включений и других нарушений сплошности металла; определения карбидной неоднородности, склонности сплавов к интеркристаллитной коррозии; обнаружения деформированных участков, явлений термического отпуска тонкого поверхностного слоя. При подготовке шлифов для микроскопического исследования достоинства электрохимического полирования особенно заметны. Поверхность шлифа, полированная электрохимически, освобождается от всех термических и механических изменений (наклепа), неизбежных при механических способах обработки. Она свободна также от каких-либо загрязнений полирующими веществами и пленок, в том числе и окисных, образовавшихся ранее. И хотя полированная поверхность анодно пассивированная, она остается чистой и активной.
Отсутствие на поверхности следов термических воздействий и деформаций и повышенная чистота полированной поверхности позволяют наблюдать истинную, неискаженную структуру исследуемого материала. Электрохимически полированная поверхность особенно удобна для рассмотрения при больших увеличениях. Здесь отчетливо выявляются тончайшие детали структуры, обычно искаженные при механической подготовке (первичное зерно, микроликвация). Электрохимическое полирование в сочетании с химико-механическим методом ускоряет процесс приготовления шлифов.
Читать далее:
Электро-химико-механическая обработка
Статьи по теме:
pereosnastka.ru
Полировка нержавейки: электрохимическая полировка нержавеющей стали
Нередко для различных нужд требуется полировка нержавейки до зеркального блеска. Такая обработка характерна для поручней, дверных ручек, медицинских изделий, отдельных деталей для автомобиля, сантехники – смесителей, кранов, полотенцесушителей, моек и т.д. Процедура обработки нержавеющей стали не только позволяет сделать поверхность эстетически привлекательной, но и скрывает любые дефекты поверхностей и сварных швов.
Первые этапы работ проводят с использованием различных типов абразивов. С каждым подходом размер зерна уменьшается. Но у механических методов есть предел максимальной точности. Чтобы добиться лучшего качества поверхности, применяется химическая обработка кислотными растворами и электрополировка нержавеющей стали. Также есть технологии объединяющие воздействие кислот и гальванический эффект.
Электрохимическая полировка нержавеющей стали
Если вас интересует качественная электрохимполировка нержавейки в СПб, обращайтесь в компанию «Региональный дом металла». Мы применяем передовые технологии поверхностной полировки металлических поверхностей. Это может быть листовая сталь, либо готовые изделия.
Какие преимущества даёт этот метод воздействия? В большинстве случаев, электрохимполировка нержавеющей стали быстрее других способов позволяет добиться высокой точности. Также обработанная поверхность обладает великолепными адгезионными свойствами. К минусам технологии можно отнести более высокую стоимость работы, присутствие потенциально опасных реактивов. То есть, требуется уделить особое внимание технике безопасности.
Также электрохимическое полирование требует:
Полировка нержавеющей стали
Процесс дополнительной полировки даёт важные преимущества. Чем хороша полированная нержавеющая сталь помимо превосходного внешнего вида? С её поверхности устраняются микротрещины, впадины, перепады, другие дефекты, в которые проникают вода и химикаты. Следовательно, изделие намного лучше защищено от разрушения и межкристаллитной коррозии.
Важно понимать, чем и как отполировать для получения определенных характеристик и придания необходимых свойств. У специалистов «РДМ» есть необходимое оборудование и опыт для проведения подобных работ. Мы проконсультируем вас и примем заказ в работу.
rdmetall.ru