- Термическая форма оксидирования может осуществляться в ходе нагревания определенного изделия или инструмента в атмосферах пара воды или кислорода. Если происходит оксидирование металлов, например, железа и низколегированной стали, то процесс называют воронением.
- Химическая форма оксидирования характеризует себя, в качестве процесса обработки, посредством использования расплавов или растворов окислителей. Это могут быть представители хроматов, нитратов и т. п. Чаще всего это делается с целью придания изделию защиты от процессов коррозии.
- Оксидирование электрохимического типа характеризуется тем, что протекает внутри электролитов. Его также называют микродуговым оксидированием.
- Плазменную форму оксидирования реально осуществлять только при наличии плазмы с низкой температурой. Она должна содержать О2. Вторым условием является наличие разряда постоянного тока, а также ВЧ и/или СВЧ.
- Толщина тонкослойного покрытия лежит в пределах от 0.1 до 0.4 микрометров.
- Обеспечение электроизоляционных и износостойких свойств возможно в том случае, если толщина будет колебаться от двух-трех до трехсот мкм.
- Защитное покрытие = 0.3 – 15 мкм.
- Могут наноситься слои со свойствами, подобными эмали. Специалисты такую пленку чаще всего называют эматаль-покрытием.
- Щелочной тип характеризуется использованием соответственных растворов, с добавлением окислителей, в условиях температуры от 135 до 150 градусов по Цельсию.
- Кислотный тип воронения использует кислые растворы и химические или электрохимические способы.
- Термическая форма обработки характеризуется использованием достаточно высоких температур (от 200 до 400 °С). Процесс проходит в толще атмосферы перегретого пара воды. Если используют аммиачно-спиртовую смесь, то требования к температуре возрастают до 880 °С, а в расплавленных солях - от 400 до 600 °С. Использование воздушной атмосферы требует предварительного покрытия поверхности запчасти тоненьким слоем лака, который должен быть асфальтным или масляным.
- Использовать емкости, подверженные эмалированию и не имеющие сколов или царапин на внутренней поверхности.
- Наполнить емкость водой и развести соответствующим количеством граммов едкого натра (с расчетом на 1 литр = 50 грамм).
- Перенести сосуд с водой на плиту и сверху расположить изделие.
- Нагревать смесь, приблизительно до 135-150 °С.
-
Оксидирование алюминия
-
Анодное оксидирование алюминия
-
Химическое оксидирование алюминия
-
Электрохимическое оксидирование алюминия
-
Оксидирование стали
-
Оксидирование титана
-
Анодное оксидирование
-
Микродуговое оксидирование
-
Холодное оксидирование
-
Щелочное оксидирование
-
Низкотемпературное оксидирование
-
Электрохимическое оксидирование
Защита от коррозии
Технологический подслой
Защитно-декоративное
Термический
Химический
Fe +O +2NaOH = Na2FeO2 + h3O
2Fe + 3O + 2NaOH = Na2Fe2O4 + h3O
Na2FeO2 + Na2Fe2O4 + 2h3O = Fe3O4 + 4NaOH
Электрохимический способ
- При цеховой температуре, простым ополаскиванием в химически неагрессивном растворе, на деталях формируются покрытия, которые по декоративности (глубоконасыщенный черный цвет) и коррозионной стойкости не уступают покрытиям, получаемым при горячем щелочном оксидировании в нитратных растворах;
- Процесс применим для чернения различных сталей: углеродистых и легированных, конструкционных и инструментальных, холодно- и горячекатаных, после ковки или штамповки, а также чугунов и порошковых металлов; при этом отсутствует образование белого соляного налета, что присуще горячему оксидированию; не происходит также и выщелачивание порошковых металлов и чугунов;
- Одна и та же ванна может использоваться для чернения при комнатной температуре деталей из сталей и чугунов, разных марок и видов;
- Покрытия характеризуются долговечностью, износостойкостью и отличными противозадирными свойствами – приработка сопрягающихся деталей облегчается, свойства режущего инструмента улучшаются;
- Посадочные размеры деталей и твердость сохраняются;
- Отсутствует легко удаляемый темный налет, присущий другим процессам чернения при комнатной температуре;
- Процесс рекомендуется производителям инструмента, подшипников, прецизионных деталей машин, станков, крепежных и других изделий.
- Автоматная сталь
- Химическое оксидирование стали
- Жаростойкая сталь
- Межкристаллитная коррозия
- Пищевая нержавеющая сталь
- Заклепки стальные вытяжные
- Сталь конструкционная
- Жаропрочная сталь
- Стали конструкционные
- Стропы стальные канатные
- Сталь углеродистая
Оксидирование металлов в домашних условиях. Оксидирование стали
Оксидирование металлов в домашних условиях
Эта статья уделит свое внимание разбору явления оксидирования металлов. Здесь мы рассмотрим общее представление о данном явлении, ознакомимся с некоторыми разновидностями и изучим их на примере со сталью. Также читатель узнает, как совершить подобный процесс самостоятельно.
Определение оксидирования
Для начала мы остановимся на понятии самого оксидирования. Это процесс, в ходе которого создается оксидная пленка на поверхностной площади изделия, а также на заготовке. Он становится возможным благодаря проведению окислительно-восстановительных реакций. Чаще всего подобные меры используют при оксидировании металлов, элементов декора и с целью сформировать диэлектрический слой. Среди главных разновидностей выделяют следующие: термическую, плазменную, химическую и электрохимическую форму.
Видовое разнообразие
Останавливаясь на описании выше перечисленных видов, про каждый из них можно сказать, что:
Общее понятие окисления
Чтобы лучше понять, что это – оксидирование металлов, желательно будет также ознакомиться и с общей, краткой характеристикой окисления.
Окисление – это процесс химической природы, который сопровождается увеличением показателя степени атомного окисления вещества, какое подвергается данному явлению. Это происходит посредством пересылки отрицательно заряженных частичек – электронов, от атома, который является восстановителем. Его также могут называть донором. Передача электронов совершается по отношению к окислительному атому, электронному акцептору.
Иногда в ходе окисления молекулы исходных соединений могут становиться нестабильными и распадаться на более маленькие составные фрагменты. При этом некоторая часть атомов, образовавшихся молекулярных частиц, будет обладать большей степенью окисления, чем те же виды атомов, но пребывающие в исходном, первоначальном состоянии.
На примере оксидирования стали
Что это такое – оксидирование металлов? Ответ на данный вопрос лучше будет рассмотреть на примере, для которого мы будем использовать проведение данного процесса со сталью.
Под химическим оксидированием металла – стали, понимают процесс выполнения работы, в ходе которой металлическую поверхность покроют оксидной пленкой. Эту операцию проводят, чаще всего, для образования защитного покрытия или придания новой черты элементу декора; еще это делают с целью создать диэлектрические слоя на изделиях из стали.
Говоря о химическом оксидировании, важно знать: сначала изделие подвергают обработке каким-либо сплавом или раствором хромата, нитрата или некоторого ряда других окислителей. Это придаст металлу защиту против воздействия коррозии. Процедуру можно также проводить с использованием композиций щелочной или кислотной природы.
Химическая форма оксидирования, выполняемая посредством использования щелочей, должна выполняться при температуре от 30 до 180 °С. Для таких процедур необходимо использовать щелочи с примесью небольшого количества окислителей. После того, как деталь обработали щелочным соединением, ее необходимо обязательно очень тщательно промыть, а далее высушить. Иногда заготовку, уже прошедшую через процедуру оксидирования, могут дополнительно промаслить.
Детальнее о кислотном методе
Для применения метода кислотных операций необходимо использовать несколько кислот, чаще это две-три. Основными веществами такого типа являются соляная, ортофосфорная и азотная кислоты. В них добавляются незначительное количество соединений марганца и др. Варьирование температурных показателей, в которых может происходить оксидирование металла – стали, посредством использования кислотного метода, лежит в пределах от 30 до 100 °С.
Химическое оксидирование, описанное для двух методов, дает человеку возможность получить как в производственной, так и в домашней обстановке, пленку, обуславливающую достаточно сильную защиту изделия. Однако важно будет знать, что предохранение стали и других металлов будет более надежным в случае применения электрохимической процедуры. Именно по причине преимущества электрохим. метода над химическим оксидированием, последнее используют реже по отношению к объектам из стали.
Анодная форма оксидирования
Оксидирование металлов может проходить с применением анодного процесса. Чаще всего электрохимический процесс оксидирования называют именно анодным. Он осуществляется в толще электролитов твердого или жидкого агрегатного состояния. Также применение такого метода позволит нанести на объект пленку высокого качества:
Характеристикой изделия, которое подвергли анодированию, является наличие положительного потенциала. Данная процедура рекомендуется с целью придания защиты элементам микросхем интегрального типа, а также при создании диэлектрического покрытия на поверхности полупроводников, сплавов и сталей.
Процесс оксидирования металлов анодированного типа может, при желании, выполнить любой человек в бытовых условиях, дома. Однако очень важно будет соблюдать все условия техники безопасности, и выполнять это необходимо безоговорочно. Это обуславливается использованием в данном методе очень агрессивных соединений.
Одним из частных случаев анодирования считают способ микродугового оксидирования. Он позволяет человеку получать ряд уникальных покрытий с высокими параметрами декоративного, теплостойкого, защитного, изоляционного и антикоррозийного типа. Микродуговая форма протекания процесса может осуществляться только под воздействием переменного или импульсного тока в толще электролитов, обладающих слабощелочным характером. Рассматриваемый способ позволяет получать толщину покрытия от двухсот до двухсот пятидесяти мкм. После выполнения операции поверхность станет похожа на керамику.
Процесс воронения
Оксидирование черных металлов в профессиональной терминологии называют воронением.
Если говорить о воронении стали, например, об оксидировании, чернении или синении, можно сказать, что это процесс, в ходе которого на чугуне или низколегированной стали образуют слой оксида железа. Как правило, толщина такой пленки лежит в пределах от одного до десяти мкм. Толщина слоя обуславливает и наличие определенного цвета побежалости. В зависимости от возрастания толщины пленочного слоя, цвета могут быть: желтым, бурым, вишневым, фиолетовым, синим и серым.
В настоящее время существует несколько типов воронения:
Ознакомление с термическим оксидированием
Термическое оксидирование металлов – это методика, в ходе которой оксидную пленку наносят на сталь в пространстве атмосферы водяного пара. Также могут использовать и другие кислородосодержащие среды с достаточно высокими температурами. Провести термическую обработку в домашних условиях довольно сложно, а потому, как правило, ее не выполняют. Упоминая о плазменном типе оксидирования, важно знать, что проделать это дома практически невозможно.
Самостоятельное выполнение операции
Оксидирование металла в домашних условиях можно провести самостоятельно. Проще всего подвергать подобной обработке изделия из стали. Для этого сперва необходимо отполировать или зачистить деталь, над которой будет проведена работа оксидирования. Далее следует удалить с поверхности окислы посредством использования растворов пятипроцентной h3SO4 (серной кислоты). Изделие необходимо держать в течение шестидесяти секунд в жидкости.
Дальнейшие действия
После того, как этап помещения детали в ванну с кислотой пройдет, следует ее промыть под теплой водой и провести работу по пассивированию или, другими словами, прокипятить объект в течение пяти минут. Для этого используют раствор воды из водопровода с пятьюдесятью граммами простого хозяйственного мыла. Здесь расчет идет на 1 литр жидкости. Проведя все эти действия, мы подошли к завершению оксидирования. Чтобы реализовать процедуру, необходимо:
Спустя 90 минут деталь можно вытягивать и созерцать собственную работу.
Некоторые данные
Читателю будет знать, что в случае потребности проведения подобной операции, но при отсутствии умения или желания, с такой просьбой можно обратиться к различным специалистам. Оксидирование металлов в Москве, например, может выполняться как специалистами в различных сферах услуг, так и на дому, людьми. Некоторые виды такого средства придания защиты детали, могут быть довольно дорогими. В столице РФ анодированный тип оксидирования будет стоить довольно дорого, однако придаст высокий показатель надежности объекту. Чтобы найти специалистов в подобном деле, достаточно набрать в запросе поиска гугла, например: «выполнение химического оксидирования в … (определенном городе или области)», или нечто подобное.
fb.ru
Сталь оксидирование воронение - Справочник химика 21
Опыт 4. Оксидирование стали. Нанесение оксидных пленок на металлы называется оксидированием, а в случае стали — воронением. [c.177]ВОРОНЕНИЕ — создание окисной пленки (от черного до темно-синего цвета различных оттенков) на поверхности изделий из углеродистой или низколегированной стали и чугуна разновидность оксидирования. Структура, внешний вид и защитные св-ва окисных пленок, гл. обр. из магн. окиси железа, обусловливаются их толщиной. Тонкие пленки (порядка 0,002—0,004 мкм) не меняют внешнего вида поверхности и практически не защищают (из-за пористости) изделия от коррозии металлов. Толстые (более 2,5 мкм) матовые пленки черного или серо-вато-черного цвета механически непрочны. Ввиду этого ири В. создают условия, обеспечивающие формирование плотных и блестящих пленок промежуточной толщины — от [c.216]
Воронение и оксидирование стали (железа). Полировка стали (железа)—более трудоемкий процесс, чем полировка латуни и меди. Для полировки стали лучше всего воспользоваться пастой, составленной из [c.155]
В стакан емкостью 100 мл влейте 75 мл раствора для оксидирования (60 г нитрита натрия и 600 г едкого натра на 1 л воды) и нагрейте его до кипения. В это время железный предмет (шайбу, плоское кольцо) очистите наждачной бумагой, опустите на 2—3 мин в Ш раствор серной кислоты и тщательно промойте водой. Предмет повесьте на крючок стеклянной палочки и опустите его в нагретый раствор (палочка должна лежать на верхних стенках стакана). Включите секундомер и через 3, 5, 10 и 15 мин поднимайте палочку из раствора и наблюдайте изменение окраски железного предмета (соломенно-желтая, светло-шоколадная, бурая и сине-черная). Напишите уравнения всех реакций, протекающих при оксидировании железа. Что называют в технике воронением стали [c.122]
Распространено оксидирование стали в щелочных растворах (воронение). Оксидные покрытия на алюминии (и других металлах) можно получать электрохимическим путем (анодирование). [c.46]
Химическое оксидирование в щелочных растворах. Наибольшее распространение получил метод химического оксидирования черных металлов в щелочных растворах с добавками различных окислителей. Подвески для воронения изготовляют из углеродистой стали. [c.168]
Ряд покрытий, получаемых химической обработкой металла, включает защитные покрытия, образующие непосредственно на поверхности металла. Образование на поверхности металлических изделий защитных оксидных пленок в технике называют оксидированием. Некоторые процессы имеют специальные названия. Так, например, процессы нанесения на сталь оксидных пленок иногда называют воронением, а электрохимическое оксидирование алюминия — анодированием. Оксидные покрытия на стали можно получить при высокотемпературном окислении на воздухе или погружении в горячие концентрированные растворы щелочей, содержащих персульфаты, нитраты или хлораты металлов. В сухом воздухе оксидные пленки достаточно стойки во влажной атмосфере, и особенно в воде, защитные свойства их крайне невысоки. Защитные свойства оксидных пленок повышают пропиткой их маслом. [c.237]
Химическое оксидирование стали и алюминия позволяет получать сплошные слои с малой пористостью и хорошей адгезией, которые имеют защитные свойства в атмосфере с низкой степенью коррозионной агрессивности. Сталь подвергают, например, так называемому воронению, которое в сочетании с консервирующими средствами обеспечивает удовлетворительную защиту стальных изделий от сухой атмосферной коррозии. Окисные слои на алюминии, полученные химическим оксидированием, существенно повышают стойкость не только самого алюминия, но и лакокрасочных систем, нанесенных на окисный слой. [c.74]
Оксидирование является старейшим и известнейшим видом массовой и экономичной защиты черных металлов от коррозии. Вместе с тем оксидные пленки на полированной поверхности имеют красивую декоративную внеш- ность, черный цвет с различными оттенками, чаще всего синевато-черным или фиолетово-черным, цвета воронова крыла, вследствие чего оксидирование стали часто называть воронением. [c.222]
Метод оксидирования черных металлов, известный также под названием воронения, относится к самым старым способам защиты стали от коррозии. Процесс можно проводить химическим, термическим и электрохимическим способами. [c.166]
Издавна известен процесс воронения и синения сталей. По существу, это термический способ их оксидирования. Его проводят на воздухе при температуре 350— 360°С. Поверхность изделий предварительно покрывают тонким слоем 15—20 %-ного раствора асфальтового лака в бензине и подсушивают на воздухе. Такой же эффект может быть получен при оксидирующей обработке изделий в кипящем растворе щелочи в присутствии нитратов и нитритов щелочных металлов. [c.150]
Весьма распространено оксидирование стали в щелочных растворах этот процесс часто называют воронением. Метод применяется для защиты от коррозии прецизионных деталей машин и механизмов, оружия. [c.56]
Хорошее защитное действие пленок, получаемых на поверхности металлов в результате их химкчеокото воздействия с окружающей средой, привело к применению методов искусственного образования или усиления таких пленок для повышения солротивления коррозии. Наряду с оиисными пленками создают пленки окисно)хроматные, фосфатные, сульфидные и др. Оксидирование (воронение) стали и железа осуществляют погружением изделий в ванны с очень концентрированным раствором щелочи, в который добавлены окислители (МпОг, N3 02). Широкое распространение получило анодное окисление (анодирование), осуществляемое в присутствии окислителя или при последующей дополнительной обработке им. Таким путем достигается, например, усиление окисной пленки на алюминии в изделиях, предназначенных для эксплуатации в более жестких условиях. [c.424]
Оксидные пленки (анодное оксидирование алюминиевых сплавов, щелочное воронение стали, фосфатирование) . 0,95 0,93 4 [c.546]
Оксидирование металлов заключается в создании на поверхности плотных пленок их оксидов, что осуществляется либо химическим, либо электрохимическим путем. В. первом случае очищенную от продуктов коррозии и обезжиренную деталь погружают на определенное время в раствор окислителей, который вызывает пассивацию (гл. X, 2) металла. Так проводят воронение стали, для чего стальной предмет можно выдержать до 90 мин в смешанном растворе NaNOз (50 г/л), НаМОг (200 г/л) и МаОН (800 г/л) при 140°С (метод Е. И. Забываёва). Во втором случае обрабатываемый металл помещают в окислительный раствор и для интенсификации его окисления подключают к положительному полюсу источника постоянного ток , делая его анодом. Так получают оксидированный (анодированный) алюминий. [c.197]
Покрытие окисными пленками — оксидирование — применяется для защиты сталей, медных и алюминиевых сплавов ОТ атмосферной коррозии. При оксидировании стали ее поверхность приобретает черный цвет, поэтому процесс оксидирования называют также воронением. [c.40]
При оксидировании стали поверхность ее приобретает синечерный цвет, почему этот процесс называется воронением. [c.239]
Хорошее защитное действие пленок, получаемых на поверхности металлов в результате их химического взаимодействия с окружающей средой, привело к применению методов искусственного образования или усиления таких пленок для повышения сопротивления коррозии. Наряду с окисными пленками, создают пленки окисно-хроматные, фосфатные, сульфиДные и др. Для оксидирования (воронения) стали и железа изделия погружают в ванны с концентрированным раствором щелочи, в которой добавлены окислители (МпОг, НаМОг). [c.473]
Изучение зашитного действия пленок, образующихся на поверхности металлов в естественных условиях, привело к при-.менению методов искусственного создания или усиления их для повышения oпpoтивJreпия металлов коррозии. Наряду с образованием окисных пленок применяется также создание пленок окисно-хроматных, фосфатных, сульфидных и др. Оксидирование (воронение) стали осуществляют погружением изделия в ванну [c.342]
Химические покрытия. Поверхность защищаемого металла подвергают химической обработке с целью получения на нем пленки его химического соединения, стойкой против коррозии. Сюда относятся оксидирование — получение тонких прочных пленок оксидов (алюминия АЬОз, цинка 2пО и др.) фосфатирова-ние — образование на поверхности металла защитной пленки фосфатов, например Рез(Р04)г, Мпз(Р04) азотирование — насыщение поверхности металла (стали) азотом (путем длительного нагревания в атмосфере аммиака при 500—600° С) термическое (воронение стали) — поверхностное взаимодействие металла с органическими веществами при высокой температуре (при этом получается слой Рез04) создание на поверхности металла его соединения с углеродом (цементация) и др. [c.195]
Оксидирование. Путем специальной обработки изделии в сильных окислителях или электрохимическим путем на поверхности металла получают тонкий прочный слой окисла. Например, при оксидировании железа на его поверхности образуется тонкий слой магнитной окиси железа Рез04. Процесс нанесения на сталь черных окисных пленок называется воронением. Оксидированию подвергают главным образом же.лезные и алюминиевые сплавы. [c.340]
Воронение, или оксидирование стали. Способы его выполнения очень разнообразны. Обработка железа паром, а затем восстанавливающими газами при температурах около 900° приводит к образованию пленки окислов, состоящей в наружном слое из Рез04 и в более глубоком — из FeO. Воронение достигается также погружением стали в расплавленную смесь селитры и двуокиси марганца при 300° или кипячением в щелочных окислительных растворах, содержащих, например, едкий натр, селитру и двуокись марганца. В этих случаях в поверхностном слое образуется РегОз. Воронение сообщает изделию красивый бархатистый иссиня-черный цвет, но в качестве коррозионной защиты недостаточно прочно. Оно пригодно лишь при работе в атмосферных условиях и то требует периодической смазки изделия жиром. [c.516]
Для защиты используют также искусственно созданные пленки окислов на поверхности металла, т. е. продукты самой же коррозии. Известно, что в некоторых случаях металл, взаимодействуя с кислородом воздуха, образует на поверхности прочную окисную пленку, которая препятствует дальнейшему разрушению металла. Поэтому путем так называемого оксидирования на поверхности многих металлов, особенно стали, сплавов магния и алюминия, создают искусственные пленки. Защитная пленка, получающаяся при оксидировании стальных изделий, состоит из магнитной окиси — Рвз04. Изделия при этом приобретают красивую черную с темно-синим оттенком окраску, напоминающую цвет воронового крыла. Этот метод иногда называют воронением. [c.259]
chem21.info
Оксидирование стали, титана, алюминия, виды оксидирования, технология, таблицы
Содержание статьи
Виды:
В современном мире имеется большое количество методов, которые используются для борьбы с образованием коррозии на поверхности металлов. Метод образования оксидной пленки является одним из самых эффективных.
Оксидирование металла
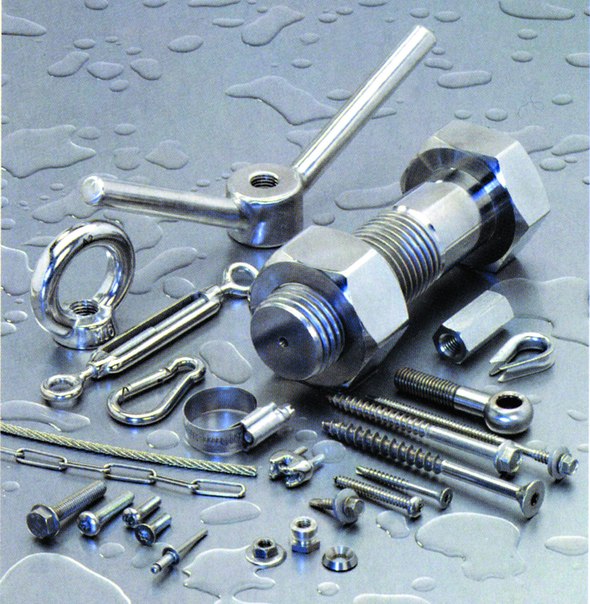
Оксидирование представляет собой особый вид процедуры покрытия металлического материала оксидной пленкой. В результате данного процесса на металлической поверхности появляется тонкая пленка, которая выполняет барьерную функцию. Она защищает материала от попадания воздуха и влаги.
Оксидирование металла является одним из самых действенных методов для его защиты от образования на поверхности ржавчины. Пленка покрывает его достаточно плотным слоем. После проведения процедуры все процессы окисления металла полностью прекращаются. В итоге изделия, которые обработаны методом оксидирования, служат дольше и сохраняют свои привлекательные внешние качества на долгие годы.
Данная процедура обработки разных видов изделий применяется не только для того, чтобы защитить металлические изделия от коррозии. Данная ее функция известна многим. Однако в некоторых ситуациях она используется для того, чтобы придать металлическому изделию декоративные качества.
Сегодня процедуре оксидирования подвергаются многие виды металлов.
В связи с этим выделяют:
Данная процедура встречается достаточно частою. Для нее используется:
В результате после обработки металл получает небольшой слой оксидной пленки, которая обладает отличными защитными качествами.
Сама процедура не отнимает много времени. Она проводится после предварительной подготовки металла. Его поверхность должна быть чистой и обезжиренной, чтобы оксидная пленка имела лучшее сцепление с алюминием.
Для алюминия применяется еще технология под название цветное оксидирование алюминия. Благодаря этому на поверхности металла образуется пленка определенного цвета. Этот процесс носит декоративный характер. Эффект от этого метода длится достаточно продолжительный период времени.
Сегодня не редко проводится оксидирование стальных изделий. Они являются подверженными образованию коррозийной пленки.
Химическое оксидирование стали
Для обработки стального материала применяется химический вид оксидирования. Он заключается в том, что сталь погружается в специально приготовленный кислый раствор, который способствует образованию на поверхности стали оксидную пленку. Она обладает небольшой толщиной. Однако у нее высокий уровень прочности.
Перед тем, как металл будет обработан оксидирующим веществом, его тщательным образом подготавливают. Для этого используются специальные средства для удаления загрязнений и жирной пленки.
Как известно такой металл, как титан и его сплавы обладают низким уровнем износостойкости. Для того чтобы металл приобрел прочность и твердость применяются разные методы. Одним из них является оксидирование. Благодаря нему на поверхности металла появляется защитная пленка, которая увеличивает прочность титана в разы.
Таблица 1. Оксидирование металла - подготовка поверхности.
Состав и режимНомер раствора123Состав, массовая доля, % | |||
серная кислота (плотность 1,8 г/см3) | - | 90—92 | 20—30 |
азотная кислота (плотность 1,4 г/см3) | 95-97 | 5-6 | 40—60 |
фтористоводородная кислота или ее соли | 3-5 | 0,5—1 | 10—12 |
Рабочая температура, К | 290—300 | 290—300 | 290—300 |
Выдержка, мин | 0,1—0,2 | 1—2 | 0,2—0,3 |
Технология оксидирования
Технология заключается в том, чтобы создать такие условия, чтобы на металлической поверхности образовалась оксидная пленка, предотвращающая проникновение кислорода и воды. Для этого используются специализированные растворы и подводится электрический ток при необходимости. Процесс может проводиться и холодным методом и горячим. Выбор метода зависит от вида металла.
Перед началом процедуры все металлы проходят подготовку. Это является первым этапом. На нем с поверхности удаляются все загрязнения. Также она обезжиривается.
Затем металл опускают в ту или иную среду и под действием внешних агрессивных условий определенного вида на них образуется плотная оксидная пленка.
Виды оксидирования
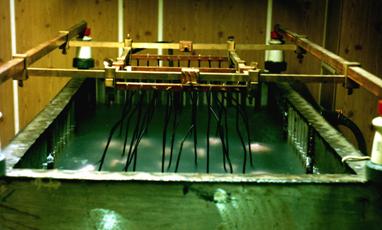
Сегодня используется большое количество видов. Они представлены следующими категориями:
Этот вид является достаточно распространенным. Он представляет собой образование на металле оксидной пленки для предотвращения появления коррозии методом их поляризации их анодов в среде, которая создается при помощи подключения электрического тока. Данный метод применяется для таких металлов, как алюминий, магний, титан.
Данная процедура заключается в том, что оксиды многих метало, которые были получены методом электрохимического окисления, подвергаются химической модификации с использованием электрического тока. Благодаря периодически возникающим электрическим импульсам на поверхности металлов появляется плотная пленка, которая служит надежной защитой от появления коррозии. Данная процедура носит еще одно название плазменно-электролитическое оксидирование. Оно используется лишь на небольшом количестве предприятий.
Эта процедура применяется только по отношению к стальным материалам разного типа. Ее еще называют чернением.
Сегодня не редко для обработки металлов используется щелочная среда. Для проведения данного процесса идеально подходят поверхности из стали. Технология проведения щелочного оксидирования предусматривает изготовление щелочной среды для того, чтобы при взаимодействии с металлом на его поверхности в результате взаимодействия образовалась оксидная пленка.
Данный вид процесса образования оксидной пленки является нейтральным. В процесс используется метод нагревания до невысоких температур, что обеспечивает покрытие металла слабой оксидной пленкой.
Этой процедуре подвергаются разные виды металлов. Металлы погружаются в среду электролита.
Таблица 2. Составы растворов для декапирования.
Декапирование алюминия и его сплавовТемператураВремя обработкиСостав 1 : | ||
Азотная кислота 10-15% раствор (по объему) | 20°С | 5-15 с |
Таблица 3. Составы растворов для окрашивания алюминия в черный цвет.
Для окрашивания в черный цвет:г/л (воды)Температура и время обработкиСостав 1: | ||
Молибдат аммония = молибденовокислый аммоний = ammonium molybdate = парамолибдат аммония= (Nh5)6Mo7O24 | 10-20 | 90-100°С / 2-10 мин |
Хлорид аммония = хлористый аммоний = Nh5Cl | 5- 15 |
Таблица 4. Составы растворов для окрашивания алюминия в серый цвет.
Для окрашивания в серый цвет:г/л (воды)Температура и время обработкиСостав 1: | ||
Оксид мышьяка (III) = триокись мышьяка = трехокись мышьяка = arsenic trioxide As2O3 | 70-75 | Кипение / 1-2 мин |
Кальцинированная сода = карбонат натрия = натрий углекислый . Химическая формула, Na2CO3 | 70-75 |
Таблица 5. Составы растворов для окрашивания алюминия в зеленый цвет.
Для окрашивания в зеленый цвет:г/л (воды)Температура и время обработкиСостав 1: | ||
Ортофосфорная кислота | 40-50 | 20-40°С / 5-7 мин |
Кислый фтористый калий = калий бифторид = калий гидрофорид = kalium bifluoratum = potassium bifluoride = kaliumbifluorid = KHF2 | 3-5 | |
Хромовый ангидрид = оксид хрома(VI) = трёхокись хрома = CrO3 (весьма химически активное вещество, способен вызвать при соприкосновении с органическими веществами возгорания и взрывы) | 5-7 |
Таблица 6. Составы растворов для окрашивания алюминия в оранжевый цвет.
Для окрашивания в оранжевый цвет:г/л (воды)Температура и время обработкиСостав 1: | ||
Хромовый ангидрид = оксид хрома(VI) = трёхокись хрома = CrO3 (весьма химически активное вещество, способен вызвать при соприкосновении с органическими веществами возгорания и взрывы) | 3-5 | 20-40°С / 8-10 мин |
Фторсиликат натрия = кремнефтористый натрий = Na2SiF6 | 3-5 |
Таблица 7. Составы растворов для окрашивания алюминия в желто-коричневый цвет.
Для окрашивания в желто-коричневый цвет:г/л (воды)Температура и время обработкиСостав 1: | ||
Кальцинированная сода = карбонат натрия = натрий углекислый . Химическая формула, Na2CO3 | 40-50 | 80-100°С / 3-20 мин |
Натрия хромат = хромовокислый натрий = Na2CrO4 | 10-15 | |
Гидроксид натрия = каустическая сода = каустик = Едкий натр = едкая щёлочь. Химическая формула NaOH | 2-2,5 |
lkmprom.ru
20 Оксидирование (сталь, цветные металлы)
Оксидирование – это преднамеренное окисление поверхности с целью создания пассивной пленки.
Назначения:
Оксидируют все марки стали, медь, чугун, алюминий, магний, титан. Защитную функцию пленка выполняет только в том случае, если она будет беспориста и прочно сцеплена с основой. FeO, Fe2O3, Fe3O4 (в большей степени)
Оксидная пленка беспориста в том случае, когда ее объем чуть больше массы Ме, на который она наносится. Пленка должна быть под небольшим давлением сжатия.→Способы оксидирования стали
В кислородосодержащей атмосфере на поверхности стали образуется Fe3O4. Термическая окалина на горячекатаном металле (швеллера, уголки). Применяется очень редко – большие энергозатраты, при оксидировании закаленных сталей происходит отжиг (теряют твердость)
Окисление происходит за счет использования более сильного окислителя
Состав электролита:
NaOH – 500 г/л
NaNO3 – 50-100 г/л
NaNO2 – 200-250 г/л
t – 130-150°C
Процесс ведется при легком кипении с образованем гипоферритов и ферритов
Когда у поверхности накопится много гипоферритов, то происходит
Влияние различных факторов
↓ С окисл → ↓количества центров кристаллизации→↑размера кристаллов→↑пористости
↑ Сокисл →↑ количества центров кристаллизации→пленка тонкая
NaNO3 окрашивает пленку в матовый черный цвет, более стойкое
NaNO2 окрашивает в блестящий синий, менее стойкое
Если только NaOH без окислителей и температуры – это раствор для снятия окалины (разрыхление).
Влияние NaOH
↓ С NaOH →↓ t→↓ центров кристаллизации→↑размера кристаллов→↑пористости
↑ С NaOH→↑ t→↑ количества зародышей →пленка тонкая
Также ↑ С NaOH →сдвиг рекции (3) влево растворение окалины
Влияние перемешивания при обработке барабанов приводит к отводу продуктов реакции от поверхности деталей, но скорость меньше
Время оксидирования
Зависит от марки стали, чем больше С, тем меньше время
Высокоулеродистые – 10-30 мин
Среднеуглеродистые – 30-50 мин
Низкоуглеродистые – 60-90 мин
Толщина 5-10 мкм
Процесс оксидирования не совсем безобиден для стали, может привести к коррозионному растрескиванию
NaNO3 и NaNO2 не вводят, деталь делают анодом в горячем растворе щелочи на аноде выделяется кислород. Он и является окислителем
Недостатки: трудность в оксидировнаии деталей сложной конфигурации(ток не проходит во все внутренние полые поверхности)
Бесщелочное оксидирование
Оксидно-фосфатное покрытие
Состав электролита
h4PO4 – 2-10 г/л
Ca(NO3)2 – 60-100 г/л
MnO2 – 10-20 г/л
t° - 98°
Процесс сопровождается выделением водорода
Прекращается выделение водорода указывает на то, что пленка сформирована, для повышения коррозионной стойкости оксидно-фосфатное покрытие хроматируют в растворе бихромата натрия 50-70 г/л и пропитывают маслом
Их намыливают для того чтобы лучше пропиталось маслом. Если маслом нельзя, то обрабатывают гидрофобизирующей жидкостью, растворенной в толуоле или бензине
Пассивирование
Производится с целью некоторого повышения стойкости при хранении и транспортировке.
Пассивируют в концентрированной HNO3, если она не концентрированная, то добавляем Na2Cr3O7.
Углеродистые стали в слабощелочном растворе бихромата. Если газ выделяется, то значит происходит растравливание стали
После пассивации в кислых растворах детали быстро промывают и нейтрализуют в слабом растворе аммиака 2-3%
Для защиты межоперационного хранения применяют раствор NaNO3 – 5-7 г/л, Na2CO3 – 3-5 г/л, t° =60°C, 5-10 мин.
Надежная защита NaNО3 – 300 г/л
21 Нанесение рисунков. Фотометод. Фоторезисты. на основе спирта и сухие пленочные, свойства, фотошаблоны, способы изготовления, экспозиция, проявление, задубливание, шелкография и тампография. Локальное нанесение цветных механических покрытий.
Фоторезисты – полимерный органический материал обладающий фоточувствительностью, под действием у/ф лучей растворимость изменится.
Фоторезисты, бывают позитивные и негативные, жидкие и сухие пленочные, жидкие наносят окунанием или обливом, распылением, это первые на основе поливинилового спирта. Поливиниловый спирт хорошо растворяется в воде, но если добавить бихромат аммония и облучить, то он переходит в нерастворимое соединение. Облучение через фотошаблон. Разрешение макс 50 линий*1мм
Фоторезисты на основе диазо-соединений – позитивные. После облучения растворимые. Более стойкие дорогие и токсичные. Разрешение 350-400мм*1мм
Positiv resist – светочувствительный лак, при облучении становится растворимым, прменяется для изготовления плат, матриц, при гравировании меди и сплавов.
Фотометод применяется наиболее часто.Т примерно 1 сек.
Сетка натяг на рамку, сетку пропитывается фоточувствительным составом .
Затем готовят фотошаблон (в любой граф программе и распеч на прозр пленке на лазерном принтере с мах разрешением). Затем рисунок накл на сетку и облучают кварц лампой (экспозиция). Далее проявление в растворе соды. Травление в FeCl3. Там где пов-ть облучена, там задубливается, а где не облучена там смывается теплой водой (если позитивный фоторизист, то при облучении становится раствор, а без облучение не растворим в воде; негативный – наоборот).
Далее под сетку подставл дет, наливается типогр краска и ракилем прогоняется в другой конец сетки.
Сухой пленочный фоторезист – 3х слойная композиция, в которой верхний и нижний слой полиэтилен, в другой – лавсан.
Тампография
Прим-ся для нанес рисунков небольшого размера. Н: цифры на клавиатуре, в автомобилях на кнопках управления, на значки. Время нанесения составляет доли секунд.
Берут Ме пластину, шлифуют, полируют (механически). На эту заготовку с помощью шелкографии или другим способом (фотохимическим) наносят рисунок. Проводят травление, после рисунок снимают.
studfiles.net
ХИМИЧЕСКОЕ ОКСИДИРОВАНИЕ СТАЛИ С ПРОМАСЛИВАНИЕМ: ООО "НПП Электрохимия"
Главная → Химическое оксидирование стали с промасливанием
--> Заказать ХИМИЧЕСКОЕ ОКСИДИРОВАНИЕ СТАЛИ С ПРОМАСЛИВАНИЕМ
Оксидирование стали производится термическим, химическим и электрохимическим методом. Химическое оксидирование стали сегодня можно разделить на два способа: холодное, горячее.
Горячее химическое оксидирование стали делается в щелочных и не щелочных составах.
Безщелочное химическое оксидирование стали производится при более низких температурах и за меньшее время.
Щелочное химическое оксидирование производится в смеси щелочи с окислителями. В результате оксидирования на стали образуется пленка магнитной окиси железа Fe3O4. Во втором случае используется раствор, состоящий из фосфорной кислоты и окислителей - азотнокислые соединения кальция или бария. Такое оксидное покрытие состоит уже из фосфатов и оксида железа.
Главной реакцией процесса химического оксидирования стали является взаимодействие стали со щелочью и окислителями. Растворяясь в горячем концентрированном щелочном растворе, железо дает соединение Na2FeO2. Под воздействием окислителей в растворе образуется соединение трехвалентного железа Na2Fe2O4. Образующаяся при химическом оксидировании на поверхности металла оксидная пленка образуется по реакции:
Na2FeO2 + Na2Fe2O4 + 2h3O -> Fe3O4 + 4NaOH
Формирование пленки начинается с появления на поверхности оксидируемого металла кристаллических зародышей. По мере того как оксид покрывает металл, изолируя его от взаимодействия с раствором, уменьшается скорость растворения железа и формирования оксидной пленки. Скорость роста оксидного слоя и его толщина зависят от соотношения скоростей образования центров кристаллизации и роста отдельных кристаллов. При большой скорости образования зародышей кристаллов их количество на поверхности металла быстро растет, и кристаллы смыкаются, образуя тонкую сплошную пленку. Если скорость формирования зародышей при химическом оксидировании относительно невелика, то до того, как они соединятся, создаются благоприятные условия для их роста и получения оксидной пленки большой толщины.
При химическом оксидировании стали процесс образования оксидной пленки определяется условиями оксидирования. При большой концентрации в растворе окислителя возрастает скорость образования зародышей оксида и, следовательно, уменьшается толщина формирующейся оксидной пленки. При уменьшении концентрации окислителя в растворе химического оксидирования стали способствует росту толщины оксидной пленки, но в сильно концентрированных растворах на поверхности стали может выделяться рыхлый осадок гидроксида железа и защитные свойства оксидного покрытия уменьшаются.
Скорость растворения стали в растворе химического оксидирования зависит от химического состава стали и ее микроструктуры. Высокоуглеродистые стали оксидируются быстрее, чем малоуглеродистые. Поэтому при оксидировании малоуглеродистой стали применяются растворы с увеличенным содержанием щелочи. Состав стали оказывает влияние и на цвет оксидной пленки: на малоуглеродистых сталях она получается глубоко черного цвета, в то время как на высокоуглеродистых - черного с серым отливом.
Сегодня предпочтение часто отдается холодному химическому оксидированию. Составы для холодного химического оксидирования стали запатентованы и продаются в виде готовых, обычно двухкомпонентных, растворов.
Химическое оксидное покрытие без промасливания применяется редко ввиду низкой коррозионной стойкости. Промасливание обеспечивает улучшение антикоррозионных характеристик покрытия и более глубокий черный цвет.
Промасленное химическое оксидное покрытие на стали применяется для защиты деталей от коррозии, декоративной отделки, как антибликовое покрытие на инструменте.
Химическое оксидное покрытие на стали может использоваться как грунт под покраску.
Данная статья является интеллектуальной собственностью ООО "НПП Электрохимия" Любое копирование без прямой ссылки на сайт www.zctc.ru преследуется по закону. Текст статьи обработан сервисом Яндекс "Оригинальные тексты"
zctc.ru
Обработка металла – стали и цветных металлов
Оксидирование — покрытие поверхности изделия тонкой пленкой оксидов, которая защищает от коррозии и придает хороший вид. Сталь оксидируют в черный цвет, так: приготовленный раствор (табл.2) нагревают в эмалированной или стеклянной посуде, заполненной на 1/3, погружают в него после декапирования изделие и начинают подогревать.
Табл. 2.
Легированную и высоколегированную сталь выдерживают в растворе дольше в полтора раза, чем указано в таблице. В третьем растворе нитрит натрия можно не прибавлять, а взять 25 г нитрата натрия. Раствор № 7 готовят без воды, а нагревают смесь скипидара с серой на водяной бане. Чтобы оксидная пленка на детали сложной формы была одинаковой толщины, ее через каждые 25-30 мин вынимают, всполаскивают водой и погружают снова другим боком.
После оксидирования деталь промывают в горячей воде и погружают на 1-2 мин в раствор хромпика (100—120 г/л), нагретый до температуры 60-70 °С. Можно также промыть деталь в проточной воде, а потом прокипятить на протяжении 3—5 мин в растворе хозяйственного мыла (20-30 г/л). После этого деталь высушивают, смазывают машинным маслом и вытирают. Сталь оксидируют в различные цвета в растворах, состав которых приведено в таблице 3.
Табл. 3
Раствор № 4 сначала готовят из двух частей – в половине воды растворяют гипосульфит, а во второй – уксуснокислый свинец.Растворы смешивают, нагревают до кипению, опускают подготовленные к покрытию детали и снова кипятят до появлению синего или темно-синего цвета. В раствор № 5 деталь не погружают, а мягкой кистью смачивают всю ее поверхность и дают высохнуть. Так повторяют несколько раз, пока поверхность не приобретет желаемый красный цвет. Если при этом появятся ржавые пятна, их осторожно снимают влажной кисточкой и снова наносят раствор.Раствор № 6 – это электролит, т.е. оксидирование в нем проводят под действием электрического тока плотностью 1-1,5 А/дм2, напряжением б—8 В. Как анод используют свинцовую пластину, площадь которой в 1,5 раза больше площади детали. Закончив оксидирование любым раствором, кроме № 6; детали обрабатывают, как и после оксидирования, в черный цвет, а после электролитического оксидирования (№ 6) их просушивают при температуре 100— 110 ° С. Оксидирование цинка, его сплавов и оцинкованных изделий можно выполнять термически-химическим и химическим способами. При первом способе очищенную и обезжиренную поверхность смачивают раствором, приготовленным из равных частей за массой 25% уксуснокислой меди и 30% уксусной кислоты, и нагревают на протяжении 1-2 мин до температуры 300 °С. Обработку поверхности повторяют дважды.Для оксидирования химическим способом приготавливают такой раствор, г:
Фосфорная кислота………………..2-10Азотнокислый натрий…………70-100Вода……………………………………….1000
Обработка детали длится 30—40 мин при температуре 80—100 °С. Потом изделие промывают, сушат и смазывают.Алюминий и его сплавы оксидируют химическим и электрохимическим способами в окислительных растворах (табл.). При оксидировании на поверхности изделия образовывается антикоррозийная пленка из окиси алюминия, которая может иметь разные цвета, а также, может служить основой, которая хорошо поглощает красители.
К раствору № 1 можно прибавить 0,25 части за массой едкого натра, чтобы он глубже проник в металл. После оксидирования деталь погружают на 10-15 мин в 2 %-ной раствор хромового ангидрида температурой 18-20 °С или же промывают ее в воде и кипятят 15-20 мин, чтобы удалить остатки реактивов. Потом деталь сушат. Очень хорошо, если оксидированную поверхность защитить лаком. Оксидируют алюминий до образования пленки с перламутровым блеском так: поверхность изделия очищают от грязи, обезжиривают органическим растворителем и проволочной щеткой (наждачной кожицей № 60 или 80) обрабатывают ее в разных направлениях. Потом деталь нагревают до температуры 80-100 °С, покрывают, нагретым до 90—100 °С 10%-им раствором едкого натрия и сушат на воздухе. Покрытая прозрачным лаком поверхность не теряет цвета на протяжении трех лет.
ometals.ru
Оксидирование.Чернение стали и чугуна.Меднение. - 17 Декабря 2011 - Технологии
Технология химического оксидирования металла.
Декоративное химическое оксидирование гальванопластических изделий из меди, а также изделий из бронзы и латуни позволяет отделывать их разноцветными оксидными пленками. Результаты получаются различные в зависимости от применяемых растворов, их концентрации, температуры и прочих параметров обработки.
При химическом оксидировании изделий из бронзы и латуни играет важную роль состав этих материалов.При химическом оксидировании изделия обрабатывают растворами или расплавами окислителей (нитратов, хроматов и др.).Химическое оксидирование используют для пассивации металлических поверхностей с целью защиты их от коррозии, а также для нанесения декоративных покрытий на чёрные и цветные металлы и сплавы.Химическое оксидирование чёрных металлов проводят в кислотных или щелочных составах при 30-100ºС.Обычно используют смеси соляной, азотной или ортофосфорной кислот с добавками соединений Мn, Ca(NO3)2 и др.
Щелочное оксидирование проводят в растворе щелочи с добавками окислителей при 30-180ºС.Оксидные плёнки на поверхности чёрных металлов получают также в расплавах, состоящих из щелочи, NaNO3 и NaNO2, MnO2 при 250-300ºС.После оксидирования изделия промывают, сушат и иногда подвергают обработке в окислителях (K2Cr2O7) или промасливают.
Химическое оксидирование применяют для обработки некоторых цветных металлов.Наиболее широко распространено химическое оксидирование изделий из магния и его сплавов в растворах на основе K2Cr2O7.Медные или меднёные изделия окисляют в составах, содержащих NaOH и K2S2O8.Иногда химическое оксидирование используют для оксидирования алюминия и сплавов на его основе (дуралюминов).В состав раствора входят Н3РО4, СrО3 и фториды.
Однако по качеству оксидные плёнки, полученные химическим оксидированием, уступают плёнкам, нанесённым методом анодирования.Различают помимо химического также и термические электрохимические (или анодные) и плазменные методы оксидирования.
Пассивация металлов. Пассивация металлов – это технологический процесс антикоррозийной защиты металлов при помощи специальных растворов. Как правило, пассивация производится при помощи солей или окислов (в том числе нитрата натрия). Целью пассивации является сделать металлическую поверхность неактивной к атмосферному воздуху.Пассивация может производиться двумя основными способами – химическим и электрохимическим.При химической пассивации детали погружаются в раствор с нужным химическим веществом, в результате чего при определенной температуре образуется защитная пленка.Электрохимическая пассивация производится следующим образом.Вещества, которые необходимо нанести на поверхность, смешиваются с электролитом. Далее при пропускании электрического тока они оседают на поверхности изделия. Защитный слой, нанесенный электрохимическим путем, является более равномерным, но данный метод по материальным затратам значительно дороже химического.
Пассивация металлических деталей подразумевает образование фазовых слоев (пленок) при взаимодействии металлов с компонентами растворов в определенных условиях. Пленка представляет собой плотный водонепроницаемый барьер, который и препятствует появлению ржавчины.Растворы, применяемые для пассивации, изготавливаются на основе окисляющих агентов, которые образуют труднорастворимые в воде соединения.К ним относятся хроматы, молибдаты, нитраты в среде щелочи.Как правило, пассивированная деталь или изделие подвергается дополнительной обработке.На них могут быть нанесены ингибиторы (вещества, которые замедляют или останавливают течение нежелательных химических реакций и процессов), грунты, краски и/или лаки.
ООО НПФ „Крас-Прибор"
Меднение. Электрохимическое покрытие.
Медь - пластичный, легко полирующийся металл. Плотность меди 8930 кг/м3, температура плавления 1083°С, атомная масса 63,54 удельное электрическое сопротивление 0,017∙10-6Ом∙м, теплопроводность 319,50 Вт/(м∙К). В химических соединениях медь может быть одно- и двухвалентна. Электрохимически осажденная медь имеет розовый цвет. Электрохимические покрытия медью не следует применять в качестве самостоятельных защитно-декоративных без дополнительного нанесения других покрытий или специальных лаков, так как в атмосферных условиях они легко взаимодействуют с влагой и углекислотой воздуха. В атмосферных условиях и ряде агрессивных сред медь с железом образует гальванопару (медь — катод). В большинстве случаев медные покрытия применяют для улучшения пайки по стали (до 3 мкм), для деталей, подвергаемых глубокой вытяжке (до 9 мкм), для увеличения электропроводности (до 24 мкм), для защитно-декоративных целей при эксплуатации в помещениях, а также в качестве подслоя под никель, хром, серебро, золото и др. Для нанесения медных покрытий существует большое количество электролитов, так, например, цианистые, цианидферратные, этилендиаминовые, пирофосфатные, сернокислые, полиэтиленполиаминовые, щелочные бесцианистые и т. д. Но наибольшее применение в различных областях промышленности нашли цианистые, пирофосфатные и сернокислые. Обладая высокой рассеивающей способностью и хорошей электропроводностью они обеспечивают получение высококачественных мелкокристаллических осадков, имеющих надежное сцепление с большинством металлов и сплавов. Они обладают низкой коррозионной стойкостью, поэтому в технике разработаны и внедрены электролиты, обеспечивающие получение сплавов на основе меди. Медь - цинк, медь - олово, медь - никель, медь - свинец, медь - сурьма, медь - висмут и другие сплавы обладают не только повышенными коррозионными свойствами, но и рядом специальных свойств, не присущих медным покрытиям.Открыть | ЗакрытьХолодное чернение стали, чугунов.
Техпроцесс "Инста-Блэк 333"Разработка "EPI" - фирменное название "Insta-Blak 333"Обработка с сохранением размеров
Преимущества холодного чернения.
Антикоррозионная защита – на годы продлевается срок службы деталей, увеличивается срок их хранения на складе.Совместно с уплотнением в фирменных антикоррах «E-Teк» технология обеспечивает превосходную коррозионную стойкость, до 150 часов в камере солевого тумана.Долговечность, износостойкость – черное химическое конверсионное покрытие не выкрашивается, не растрескивается, не отслаивается.Противозадирные свойства – в случае приработки сопряженных деталей, при первоначальном контакте и во время последующего притирания происходит выработка черного, обеспечивающего смазку трущихся поверхностей, слоя с одновременным формированием нагартованных поверхностей.Скольжение – пропитка в антикоррах «Е-Тек» не только увеличивает коррозионную стойкость изделий, но и при необходимости делает их поверхность маслянистой, что обеспечивает плавную работу сопрягаемых деталей.Стабильность размеров – размеры при чернении существенно не меняются, они увеличиваются лишь на 0,12 – 0,25 мкм; это означает, что свойства поверхности детали после чернения сохраняются – полированные поверхности остаются блестящими, твердость по Роквеллу термообработанных деталей не изменяется.Размеры прецизионных деталей сохраняются, отсутствует коробление, которое может иметь место при нагревании.Декоративные свойства – деталь приобретает глубоконасыщенный черный цвет, что улучшает ее внешний вид и товарные качества.Удобство – легко применять на месте, не передавая детали на обработку субподрядчикам; не надо ждать, когда нагреется раствор для чернения; не надо подстраиваться под график поставок извне; не нужно тратиться на выполнение чернения на стороне; сохраняется контроль производственного процесса и качества; можно использовать при любых объемах производства; особенно хорошо происходит чернение больших партий мелких деталей во вращающихся барабанах (скорость вращения 1-2 об./мин).Более высокая производительность – детали могут оксидироваться за 2 – 4 минуты в отличие от 15 – 30 минут при горячем оксидировании.Обычно в два раза больше деталей может оксидироваться за то же время, что и при горячем оксидировании, т.е. можно организовать работу в одну смену вместо двух.Достаточно большие временные допуски на чернение – от 2 до 5 минут позволяют автоматизировать процесс (алогичные технологии других фирм допускают лишь короткое 90-секундное погружение).Технологичность – процесс малочувствителен к вариациям концентрации основного препарата «Инста-Блэк 333 6Х» – одинаковые результаты можно получить при его содержании 15, 20 или 25 мл/л.Широкие технологические допуски, простота контроля и корректировки рабочего раствора делают процесс легко управляемым, благодаря чему различные операторы могут обеспечить достижение надлежащего качества обработки.Продолжительный срок службы ванны – раствор может восполняться непрерывно посредством периодического добавления свежего препарата; некоторые ванны работают уже по 10-15 лет.Расширение ассортимента черненых деталей – процесс легко внедрить и применять; это позволяет придавать деталям, которые раньше никак не обрабатывались, прекрасный декоративный товарный вид и заодно обеспечить им отличную антикоррозионную защиту.Снижение энергетических затрат – чернение осуществляется при комнатной температуре по сравнению с горячим оксидированием при 145 °С.Безопасность – для приготовления раствора оксидирования используются неагрессивные водоразбавляемые химикаты без запаха, отсутствует необходимость в принудительной вентиляции, как в случае горячего, вредного для здоровья, оксидирования; не применяются опасные едкие вещества с вредными испарениями; при доливании в раствор отсутствует опасность разбрызгивания горячих, оставляющих ожоги на коже, химикатов.Низкие капитальные затраты и более продолжительный срок службы оборудования – нет необходимости в установке дорогостоящего оборудования и аппаратуры; устанавливаются обыкновенные семь ванн без нагревательных устройств, контрольно-измерительных приборов и вытяжной вентиляции, подобных используемым в случае горячего оксидирования.Низкие затраты на выполнение обработки – обеспечиваются высокой технологичностью процесса – простота осуществления, возможность в одной и той же ванне обрабатывать стали и чугуны разных марок и видов; возможность обработки детали насыпью и т.д.Низкие нормы расхода – на чернение до 180 м2 поверхности деталей затрачивается примерно 1 л 6-кратного концентрата «Инста-Блэк 333 6Х».
Обработка осуществляется в семь стадий (ванны одного размера).
Если детали не подвергались термообработке, изготовлены из обыкновенных сталей или после струйно-абразивной обработки, то возможен и пятистадийный процесс (без активации и последующей промывки).1. Химическое обезжиривание – такие загрязнения, как смазочно-охлаждающие жидкости, эмульсии, смазки и ингибиторы коррозии должны быть удалены.Загрязнения могут замедлять последующие процессы или препятствовать им, отрицательно влиять на адгезию и внешний вид пленки.Рекомендуется погружение деталей на 2–5 минут при 50 – 65 °С в 10 %-ный щелочной раствор препарата «Е-Клин 148 Е» (E-Kleen 148 E).2. Промывка погружением в ванну с холодной проточной водопроводной водой на 30 – 60 с.Неотмытая, прилипшая пленка щелочного раствора обезжиривания быстро загрязнит ванну на следующей операции активации или чернения, что приведет к плохой адгезии чёрной оксидной пленки и появлению пятен на поверхности.3. Активация погружением на 0,5 – 5 мин в 20 %-ный водный раствор препарата «Е-Преп 258» (E-Prep 258) при 18 – 30°С.4. Промывка погружением в ванну с холодной проточной водопроводной водой на 30 – 60 с для удаления остатков раствора активации.5. Чернение – погружением на 2 – 4 мин при комнатной температуре в кислый раствор (рН 1,8), содержащий 17 – 20 мл/л препарата «ИнстаБлэк 333 6Х».Процесс малочувствителен к вариациям концентрации – одинаковые результаты можно получить при 17, 25 и 40 мл/л.Легко управляется разными операторами.6. Промывка погружением в ванну с холодной проточной водопроводной водой на 30 – 60 с для удаления остатков раствора чернения.7. Уплотнение погружением деталей на 1 мин в один из фирменных пленкообразующих ингибированных гидрофобизирующих составов, именуемых антикоррами «Е-Тек».При этом антикор быстро вытесняет влагу, остающуюся на поверхности детали после предшествующей промывки, и впитывается порами покрытия, что обеспечивает долговременную защиту детали от коррозии.
Дистрибьютор в РФ и СНГ – ООО «СОНИС», г. Москва
Методы химического окрашивания металлов.Химическое оксидирование сталей.
Оксидированию подвергаются углеродистые и низколегированные стали. Значительное содержание легирующих элементов может повлиять на цвет окрашенной детали, чаще всего он становится ближе к красному. Неизвестны способы оксидирования нержавеющих сталей химическими методами.Перед нанесением на металлические поверхности покрытий необходимо осуществить подготовительные операции, то есть удалить с этих поверхностей загрязнения различной природы.От качества проведения подготовительных операций в сильной степени зависит конечный результат всех работ.К подготовительным операциям относятся очистка поверхностей, обезжиривание и травление.
Обезжиривание
Процесс обезжиривания поверхности металлических деталей проводят, как правило, когда эти детали только что обработаны (отшлифованы или отполированы) и на их поверхности нет ржавчины, окалины и других посторонних продуктов. Любые защитные покрытия, например цинковое, также нужно предварительно удалить. С помощью обезжиривания с поверхности деталей удаляют масляные и жировые пленки. Для этого применяют водные растворы некоторых химреактивов (силикат и гидроксид натрия; тринатрийфосфат для смачиваемости), хотя для этого можно использовать и органические растворители. Последние имеют то преимущество, что они не оказывают последующего коррозионного воздействия на поверхность деталей, но при этом они токсичны и огнеопасны. Обычно используют ацетон, он хорошо справляется с удалением как органических жиров, так и минеральных масел. На результат работы также влияет чистота реактивов и качество воды.Есть несколько типов составов для химического оксидирования - щелочные составы, составы на основе диоксида марганца, на основе тиосульфата натрия.Действие щелочных составов основано на окислении железа до оксида в щелочной среде, как наиболее эффективные, но и самые агрессивные.Оксидные пленки получаются «радикально черного» цвета, устойчивы к истиранию, матовые или глянцевые в зависимости от содержания реагентов.
Составы покрытий.
1. Едкий натр - 750, азотнокислый натрий - 175. Температура раствора - 135°С, время обработки - 90 мин. Пленка плотная, блестящая. 2. Едкий натр - 500, азотнокислый натрий - 500. Температура раствора - 140°С, время обработки - 9 мин. Пленка интенсивная. 3. Едкий натр - 1500, азотнокислый натрий - 30. Температура раствора - 150°С, время обработки - 10 мин. Пленка матовая. 4. Едкий натр - 750, азотнокислый натрий - 225, нитрит натрия - 60. Температура раствора - 140°С, время обработки 90 мин. Плёнка блестящая.Приготовление и применение растворов этого типа выглядит так.Навески реактивов растворяются в требуемом объеме воды при энергичном перемешивании.При этом происходит сильное разогревание раствора.Емкость должна быть стеклянной, керамической или из нержавейки.Если вы используете стеклянную химическую емкость, посмотрите, чтобы на ней были буквы 'ТС', то есть термостойкая.Ни в коем случае не используйте алюминиевые или эмалированные емкости.Приготовленный раствор нагревается до кипения и туда помещается деталь.Контролировать температуру совсем не обязательно, главное - состав должен кипеть.Ждем положенное время, при необходимости подливая водички в раствор по мере выкипания (осторожно - состав при этом бурно вскипает!), вынимаем деталь, смотрим на ее цвет.Если он равномерный, насыщенный и без пятен, тщательно промываем деталь водой, просушиваем и смазываем нейтральным маслом.Лучше не стоит передерживать деталь в растворе, от этого портится качество оксидной пленки.Гранулы твердой щелочи, попадая на деталь, могут привести к пятнистой окраске.
Следующий состав менее опасен в обращении.5. Азотнокислый кальций - 30, ортофосфорная кислота - 1, диоксид марганца - 1.Температура раствора - 100 °С, время обработки - 45 мин.
В процессе работы состав необходимо помешивать нерастворимый в воде диоксид марганца, дабы он не лежал на одном месте, а равномерно распределялся по поверхности детали.Пленка получается рельефная, черного матового цвета, но не особо устойчивая к истиранию.После оксидирования деталь промыть горячей водой, высушить и смазать.
В отличие от вышеприведенных составов с высокой рабочей температурой, следующий работает при комнатной.6. Тиосульфат натрия - 80, хлористый аммоний - 60, ортофосфорная кислота - 7, азотная кислота - 3.Температура раствора - 20 °С, время обработки - 60 мин.
Сначала в воде растворяются тиосульфат натрия и хлористый аммоний, затем вливаются кислоты и раствор перемешивается.Раствор мутнеет вследствие выпадения элементарной серы.Сразу же помещаем туда предварительно обезжиренную деталь.После чернения деталь кипятим 15 мин. в растворе дихромата калия (120 г/л) чтобы удалить налипшую серу, промываем горячей водой, сушим и смазываем.Пленка часто получается серого цвета, имеет тенденцию со временем рыжеть.
lmx.ucoz.ru