- Твердость, сохраняемая в горячем состоянии (горячая твердость). Как известно, любой инструмент, используемый для выполнения обработки резанием, в процессе такой обработки интенсивно нагревается. В результате нагрева обычные инструментальные стали подвергаются отпуску, что в итоге приводит к снижению твердости инструмента. Такого не происходит, если для изготовления была использована быстрорежущая сталь, которая способна сохранять свою твердость даже при нагреве инструмента до 6000. Что характерно, стали быстрорежущих марок, которые часто называют быстрорезы, обладают даже меньшей твердостью по сравнению с обычными углеродистыми, если температура резания находится в нормальных пределах: до 2000.
- Повышенная красностойкость. Данный параметр любого металла характеризует период времени, в течение которого инструмент, изготовленный из него, способен выдерживать высокую температуру, не теряя своих первоначальных характеристик. Быстрорежущие стали в качестве материала для изготовления режущего инструмента не имеют себе равных по данному параметру.
- Сопротивление разрушению. Режущий инструмент, кроме способности переносить воздействие повышенных температур, должен отличаться и улучшенными механическими характеристиками, что в полной мере демонстрируют стали быстрорежущих марок. Инструмент, изготовленный из таких сталей, обладающий высокой прочностью, может успешно работать на большой глубине резания (сверла) и на высоких скоростях подач (резцы, сверла и др.).
- сплавы, в которых кобальта содержится до 10%, а вольфрама до 22%; к таким сталям относятся сплавы марок Р6М5Ф2К8, Р10М4Ф3К10 и др.;
- стали с содержанием не более 5% кобальта и до 18% вольфрама; такими сталями являются сплавы марок Р9К5, Р18Ф2К5, Р10Ф5К5 и др.;
- сплавы, в которых как кобальта, так и вольфрама содержится не более 16%; к таким сплавам относится сталь Р9, Р18, Р12, Р6М5 и др.
- классический метод, который предполагает разливку расплавленного металла в слитки, в дальнейшем подвергающиеся проковке;
- метод порошковой металлургии, при котором расплавленный металл распыляется при помощи струи азота.
- проводят несколько циклов нагрева изделия, выдержки при определенной температуре и охлаждение: многократный отпуск;
- перед выполнением отпуска, изделие подвергается охлаждению до достаточно низкой температуры: до –800.
- Насыщение поверхностного слоя изделия азотом — азотирование. Проводиться такая обработка может в газовой среде, состоящей из азота (80%) и аммиака (20%), либо полностью в аммиачной среде. Время выполнения подобной технологической операции — 10–40 минут, температура, при которой она осуществляется — 550–6600. Использование газовой среды, содержащей азот и аммиак, позволяет сформировать менее хрупкий поверхностный слой.
- Насыщение поверхностного слоя изделия цинком — цианирование, которое может осуществляться в газовой или жидкой среде, насыщенной цинком. Выполняется такая операция при температуре 5600 и продолжается от 5 до 30 минут.
- Сульфидирование, которое выполняется в жидких расплавах сульфидов, куда добавляются соединения серы. Проводится такая процедура на протяжении 45–180 минут, при этом температура расплава должна составлять 450–5600.
- Сталь Р9 рекомендуют для изготовления инструментов простой формы не требующих большого объема шлифовки, для обработки обычных конструкционных материалов. (резцов, фрез, зенкеров).
- Для фасонных и сложных инструментов (для нарезания резьб и зубьев), для которых основным требованием является высокая износостойкость, рекомендуют использовать сталь Р18 (вольфрамовая).
- Кобальтовые быстрорежущие стали (Р9К5, Р9К10) применяют для обработки деталей из труднообрабатываемых коррозионно-стойких и жаропрочных сталей и сплавов, в условиях прерывистого резания, вибраций, недостаточного охлаждения.
- Ванадиевые быстрорежущие стали (Р9Ф5, Р14Ф4) рекомендуют для изготовления инструментов для чистовой обработки (протяжки, развёртки, шеверы). Их можно применять для обработки труднообрабатываемых материалов при срезании стружек небольшого поперечного сечения.
- Вольфрамомолибденовые стали (Р9М4, Р6М3) используют для инструментов, работающих в условиях черновой обработки, а также для изготовления протяжек, долбяков, шеверов, фрез.
- ↑ Мезенин Н. А. Занимательно о железе. — М.: «Металлургия», 1972. — 200 с.
- ↑ 1 2 3 Гуляев А. П. Металловедение. Учебник для втузов. 6-е изд., перераб. и доп. — М.: Металлургия, 1986. — 544 с.
- ↑ Марочник сталей и сплавов / В. Г. Сорокин, А. В. Волосникова, С. А. Вяткин, и др. Под общ. ред. В. Г. Сорокина. — М.: Машиностроение, 1989. — 640 с.
- Гуляев А. П. Металловедение. Учебник для втузов. 6-е изд., перераб. и доп. — М.: «Металлургия», 1986. — 544 с.
- Технология конструкционных материалов. Под ред. А. М. Дальского. — М.: «Машиностроение», 1958.
- Сталь Р9 рекомендуют для изготовления инструментов простой формы не требующих большого объема шлифовки, для обработки обычных конструкционных материалов. (резцов, фрез, зенкеров).
- Для фасонных и сложных инструментов (для нарезания резьб и зубьев), для которых основным требованием является высокая износостойкость, рекомендуют использовать сталь Р18 (вольфрамовая).
- Кобальтовые быстрорежущие стали (Р9К5, Р9К10) применяют для обработки деталей из труднообрабатываемых коррозионно-стойких и жаропрочных сталей и сплавов, в условиях прерывистого резания, вибраций, недостаточного охлаждения.
- Ванадиевые быстрорежущие стали (Р9Ф5, Р14Ф4) рекомендуют для изготовления инструментов для чистовой обработки (протяжки, развёртки, шеверы). Их можно применять для обработки труднообрабатываемых материалов при срезании стружек небольшого поперечного сечения.
- Вольфрамомолибденовые стали (Р9М4, Р6М3) используют для инструментов, работающих в условиях черновой обработки, а также для изготовления протяжек, долбяков, шеверов, фрез.
- Пружинистая сталь
- Стали углеродистые обыкновенного качества
- Трубы бесшовные холоднодеформированные из коррозионностойкой стали
- Как заплести стальной трос схема в петлю
- Труба стальная холоднодеформированная
- Сверление стали нержавеющей
- Термообработка стали нержавеющей
- Сталь пищевая нержавеющая гост
- Марка пищевая нержавеющая сталь
- Рубка листа стального
- Жаропрочная сталь для печи
Быстрорежущая сталь: ГОСТ, состав, твердость, термическая обработка. Сталь быстрорежущая инструментальная
Быстрорежущие стали (быстрорез): марки, свойства, маркировка
Такой материал, как быстрорежущие стали, отличается уникальными свойствами, что дает возможность использовать его для изготовления инструментов, обладающих повышенной прочностью. Характеристики сталей, относящихся к категории быстрорежущих, позволяют производить из них инструменты самого различного назначения.
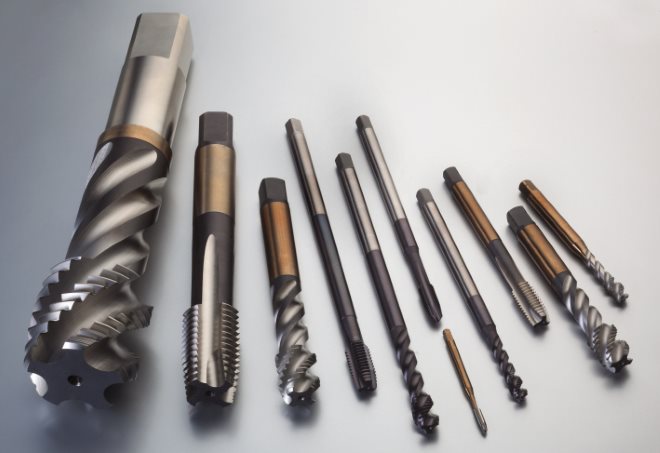
Фрезы, метчики, развертки – типичные изделия, производимые из высококачественной быстрорежущей стали
Характеристики быстрорежущих сталей
К категории быстрорежущие стали относят сплавы, химический состав которых дополнен рядом легирующих добавок. Благодаря таким добавкам сталям придаются свойства, позволяющие использовать их для изготовления режущего инструмента, способного эффективно работать на высоких скоростях. Быстрорежущие инструментальные стали от обычных углеродистых сплавов как раз и отличает то, что инструмент, который из них изготовлен, может с успехом применяться для обработки твердых материалов на повышенных скоростях.
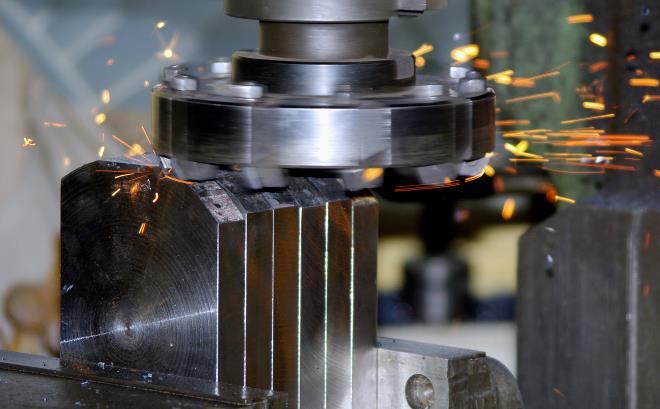
Фрезеровка детали на профессиональном гравировальном станке
К наиболее примечательным характеристикам, которыми отличаются быстрорежущие стали различных марок, нужно отнести следующие.
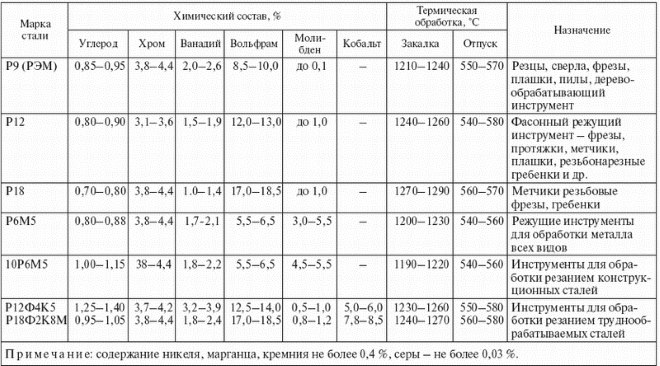
Характеристики и назначение быстрорежущих сталей
Расшифровка обозначения марок сталей
Изначально быстрорежущая сталь как материал для изготовления режущих инструментов была изобретена британскими специалистами. С учетом того, что инструмент из такой стали может использоваться для высокоскоростной обработки металлов, этот материал назвали «rapidsteel» (слово «рапид» здесь как раз и означает высокую скорость). Такое свойство данных сталей и придуманное им в свое время английское название послужили причиной того, что обозначения всех марок данного материала начинаются с буквы «Р».
Правила маркировки сталей, относящихся к категории быстрорежущих, строго регламентированы соответствующим ГОСТ, что значительно упрощает процесс их расшифровки.Первая цифра, стоящая после буквы Р в обозначении стали, указывает на процентное содержание в ней такого элемента как вольфрам, который во многом и определяет основные свойства данного материала. Кроме вольфрама быстрорежущая сталь содержит в своем составе ванадий, молибден и кобальт, которые в маркировке обозначаются, соответственно буквами Ф, М и К. После каждой из такой буквы в маркировке стоит цифра, указывающая на процентное содержание соответствующего элемента в химическом составе стали.
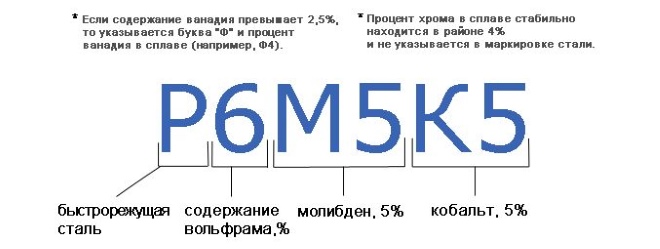
Пример расшифровки марки быстрорежущей стали
В зависимости от содержания в составе стали тех или иных элементов, а также от их количества, все подобные сплавы делятся на три основных категории. Определить, к какой из категорий относится сталь, достаточно легко, расшифровав ее маркировку.
Итак, стали быстрорежущих марок принято разделять на следующие категории:
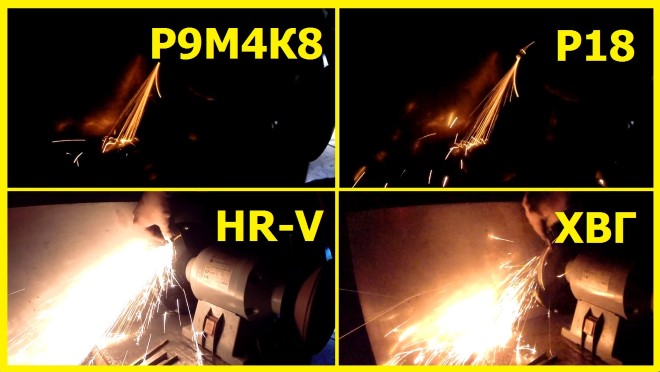
Определение разновидности стали по искре
Как уже говорилось выше, характеристики сталей, относящихся к категории быстрорежущих, преимущественно определяются содержанием в них такого элемента как вольфрам. Следует иметь в виду, что если в быстрорежущем сплаве содержится слишком большое количество вольфрама, кобальта и ванадия, то по причине формирования карбидной неоднородности такой стали режущая кромка инструмента, который из нее изготовлен, может выкрашиваться под воздействием механических нагрузок. Таких недостатков лишены инструменты, изготовленные из сталей, содержащих в своем составе молибден. Режущая кромка подобных инструментов не только не выкрашивается, но и отличается тем, что имеет одинаковые показатели твердости по всей своей длине.
Маркой стали для изготовления инструментов, к которым предъявляются повышенные требования по их технологическим характеристикам, является Р18. Обладая мелкозернистой внутренней структурой, такая сталь демонстрирует отличную износостойкость. Преимуществом использования стали данной марки является еще и то, что при выполнении закалки изделий из нее они не перегреваются, чего не скажешь о быстрорежущих сплавах других марок. По причине достаточно высокой стоимости инструментов, изготовленных из стали этой марки, ее часто заменяют на более дешевый сплав Р9.
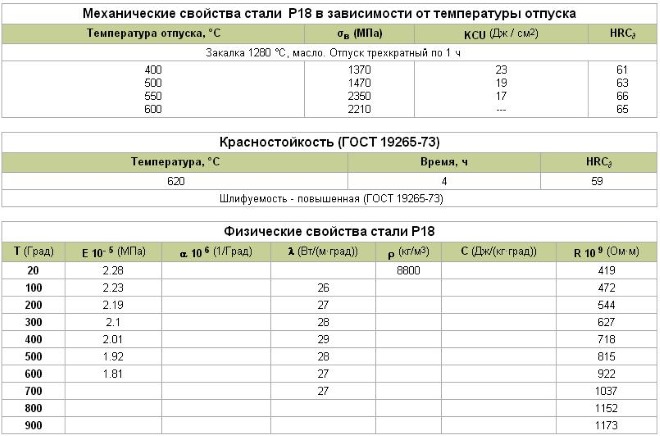
Технические характеристики стали марки Р18
Достаточно невысокая стоимость стали марки Р9, как и ее разновидности — Р9К5, которая по своим характеристикам во многом схожа с быстрорежущим сплавом Р18, объясняется рядом недостатков данного материала. Наиболее значимым из них является то, что в отожженном состоянии такой металл легко поддается пластической деформации. Между тем сталь марки Р18 также не лишена недостатков. Так, из данной стали не изготавливают высокоточный инструмент, что объясняется тем, что изделия из нее плохо поддаются шлифовке. Хорошие показатели прочности и пластичности, в том числе и в нагретом состоянии, демонстрируют инструменты, изготовленные из стали марки Р12, которая по своим характеристикам также схожа со сталью Р18.
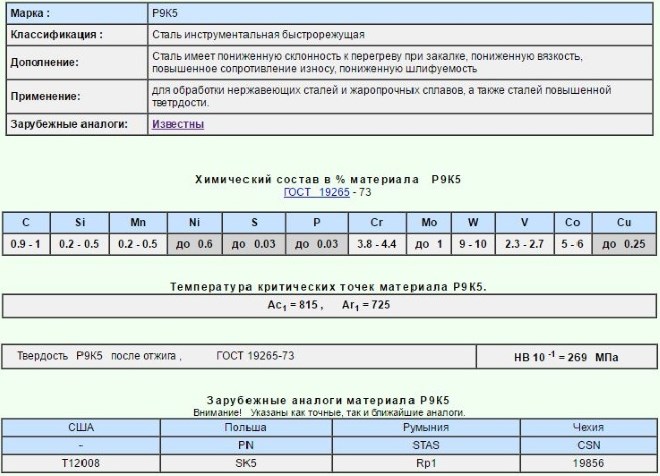
Свойства стали марки Р9К5
Методы производства и обработки
Для производства инструментов, изготавливаемых из быстрорежущих сплавов, используются две основные технологии:
Закалка готовых инструментов, выполненных из быстрорежущего сплава, осуществляется при температурах, которые способствуют лучшему растворению в них легирующих добавок, но в то же время не приводят к росту зерна их внутренней структуры. После выполнения закалки быстрорежущие сплавы имеют в своей структуре до 30% аустенита, что не самым лучшим образом сказывается на теплопроводности материала и его твердости. Для того чтобы уменьшить количество аустенита в структуре сплава до минимальных значений, используются две технологии:
Улучшение характеристики изделий
Чтобы инструменты, изготовленные из быстрорежущих сплавов, обладали высокой твердостью, износостойкостью и коррозионной устойчивостью, их поверхность необходимо подвергнуть обработке, к методам выполнения которой относятся следующие.
Оценка статьи:

Поделиться с друзьями:
Быстрорежущие инструментальные стали
Быстрорежущие инструментальные стали
Из группы высоколегированных сталей для изготовления режущих инструментов используются быстрорежущие стали с высоким содержанием вольфрама, молибдена, кобальта, ванадия.
Современные быстрорежущие стали можно разделить на три группы.
К сталям нормальной теплостойкости относятся вольфрамовые Р18, Р12, Р9 и вольфрамомолибденовые Р6М5, Р6М3, Р8М3. Эти стали имеют твердость в закаленном состоянии 63...66 HRC, предел прочности при изгибе 2900...3400 МПа, ударную вязкость 2,7... 4,8 Дж/м2 и теплостойкость 600...650 °С. Указанные марки сталей получили наиболее широкое распространение при изготовлении режущих инструментов.
Они используются при обработке конструкционных сталей, чугунов, цветных металлов, пластмасс. Иногда применяются быстрорежущие стали, дополнительно легированные азотом (Р6АМ5, Р18А и др.). Легирование азотом повышает режущие свойства инструмента на 20...30 %, твердость - на 1- 2 единицы HRC.
Стали повышенной теплостойкости характеризуются повышенным содержанием углерода — 10Р8МЗ, 10Р6М5; ванадия — Р12ФЗ, Р2МЗФ8, Р9Ф5; кобальта — Р18Ф2К5, Р6М5К5, Р9К5, Р9К10, Р9М4К8Ф и др.
Твердость сталей в закаленном состоянии достигает 66...70 HRC, они имеют более высокую теплостойкость (до 620...670 °С).
Это дает возможность использовать их для обработки жаропрочных и нержавеющих сталей и сплавов, а также конструкционных сталей повышенной прочности и закаленных. Период стойкости инструментов из таких сталей в 3—5 раз выше, чем из сталей Р18, Р6М5.
Стали высокой теплостойкости характеризуются пониженным содержанием углерода, но весьма большим количеством легирующих элементов — В11М7К.23, В14М7К25, ЗВ20К20Х4Ф. Они имеют твердость 69...70 HRC, и теплостойкость 700....720 °С.
Наиболее рациональная область их использования — резание труднообрабатываемых материалов и титановых сплавов. В последнем случае период стойкости инструментов в 30 - 80 раз выше, чем из стали Р18, и в 8 - 15 раз выше, чем из твердого сплава ВК8. При резании конструкционных сталей и чугунов период стойкости возрастает менее значительно (в 3 - 8 раз).
ОСНОВНОЙ НЕДОСТАТОК всех быстрорежущих сталей - высокая стоимость легирующих компонентов. Поэтому, в последнее время, быстрорежущие стали применяются очень ограниченно!!!
ПРИМЕЧАНИЕ:
Молибден является химическим аналогм вольфрама, действующим более эффективно. Замена вольфрама на молибден несколько снижает теплостойкость стали, но значительно увеличивает прочность на изгиб (sи). Сохранение теплостойкости возможно при условии замены вольфрама на молибден в соотношении 1:1,5.
С увеличением содержания молибдена в стали до 3 % и более резко увеличивается её теплопроводность. За счёт этого, тепло из зоны резания отводится хорошо и температура лезвий инструмента не увеличивается. Следовательно, повышается теплостойкость стали.
Высокая прочность на изгиб (sи) и способность хорошо отводить тепло из зоны резания обусловили широкое применение сталей Р6М5 для изготовления осевого инструмента (свёрла, зенкеры, развёртки).
osntm.ru
Быстрорежущая сталь - это... Что такое Быстрорежущая сталь?
Быстроре́жущие ста́ли — легированные стали, предназначенные, главным образом, для изготовления металлорежущего инструмента, работающего при высоких скоростях резания.
Быстрорежущая сталь должна обладать высоким сопротивлением разрушению, твёрдостью (в холодном и горячем состояниях) и красностойкостью.
Высоким сопротивлением разрушению и твердостью в холодном состоянии обладают и углеродистые инструментальные стали. Однако инструмент из них не в состоянии обеспечить высокоскоростные режимы резания. Легирование быстрорежущих сталей вольфрамом, молибденом, ванадием и кобальтом обеспечивает горячую твердость и красностойкость стали.
Истории создания
Сверло с покрытием из нитрида титанаДля обточки деталей из дерева, цветных металлов, мягкой стали резцы из обычной твердой стали были вполне пригодны, но при обработке стальных деталей резец быстро разогревался, скоро изнашивался и деталь нельзя было обтачивать со скоростью больше 5 м/мин[1].
Барьер этот удалось преодолеть после того, как в 1858 году Р.
Мюшетт получил сталь, содержащую 1,85 % углерода, 9 % вольфрама и 2,5 % марганца. Спустя десять лет Мюшетт изготовил новую сталь, получившую название самокалки. Она содержала 2,15 % углерода, 0,38 % марганца, 5,44 % вольфрама и 0,4 % хрома. Через три года на заводе Самуэля Осберна в Шеффилде началось производство мюшеттовой стали. Она не теряла режущей способности при нагревании до 300 °C и позволяла в полтора раза увеличить скорость резания металла — 7,5 м/мин.Спустя сорок лет на рынке появилась быстрорежущая сталь американских инженеров Тэйлора и Уатта. Резцы из этой стали допускали скорость резания до 18 м/мин. Эта сталь стала прообразом современной быстрорежущей стали Р18.
Еще через 5—6 лет появилась, сверхбыстрорежущая сталь, допускающая скорость резания до 35 м/мин. Так, благодаря вольфраму было достигнуто повышение скорости резания за 50 лет в семь раз и, следовательно, во столько же раз повысилась производительность металлорежущих станков.
Дальнейшее успешное использование вольфрама нашло себе применение в создании твердых сплавов, которые состоят из вольфрама, хрома, кобальта. Были созданы такие сплавы для резцов, как стеллит. Первый стеллит позволял повысить скорость резания до 45 м/мин при температуре 700—750 °C. Сплав видиа, выпущенный Круппом в 1927 году, имел твердость по шкале Мооса 9,7—9,9 (твердость алмаза равна 10).
В 1970-х годах в связи с дефицитом вольфрама быстрорежущая сталь марки Р18 была почти повсеместно заменена на сталь марки Р6М5, которая в свою очередь вытесняется безвольфрамовыми Р0М5Ф1 и Р0М2Ф3.
Характеристики быстрорежущих сталей
Горячая твердость
Твердость инструментальных сталей при повышенных температурах[2]На рисунке приведены кривые, характеризующие твердость углеродистой и быстрорежущей инструментальных сталей при повышенных температурах испытаний. При нормальной температуре твердость углеродистой стали даже несколько выше твердости быстрорежущей стали. Однако, в процессе работы режущего инструмента, происходит интенсивное выделение тепла. При этом до 80 % выделившегося тепла уходит на разогрев инструмента. Вследствие повышения температуры режущей кромки начинается отпуск материала инструмента и снижается его твердость.
После нагрева до 200 °C твердость углеродистой стали начинает быстро падать. Для этой стали недопустим режим резания, при котором инструмент нагревался бы выше 200 °C. У быстрорежущей стали высокая твердость сохраняется при нагреве до 500—600 °C. Инструмент из быстрорежущей стали более производителен, чем инструмент из углеродистой стали.
Красностойкость
Если горячая твердость характеризует то, какую температуру сталь может выдержать, то красностойкость характеризует, сколько времени сталь будет выдерживать такую температуру. То есть насколько длительное время закаленная и отпущенная сталь будет сопротивляться разупрочнению при разогреве.
Существует несколько характеристик красностойкости. Приведем две из них.
Первая характеристика показывает, какую твердость будет иметь сталь после отпуска при определенной температуре в течение заданного времени.
Второй способ охарактеризовать красностойкость основан на том, что интенсивность снижении горячей твердости можно измерить не только при высокой температуре, но и при комнатной так как кривые снижения твердости при высокой температуре и комнатной идут эквидистантно, а измерить твердость при комнатной температуре, разумеется, гораздо проще, чем при высокой. Опытами установлено, что режущие свойства теряются при твердости 50 HRC при температуре резання, что соответствует примерно 58 HRC при комнатной. Отсюда красностойкость характеризуется температурой отпуска, при которой за 4 часа твердость снижается до 58 HRC (обозначение K4р58).
Характеристики теплостойкости углеродистых и красностойкости быстрорежущих инструментальных сталей[3] Марка стали Температура отпуска, °C Время выдержки, час Твердость, HRCэУ7, У8, У10, У12 | 150—160 | 1 | 63 |
Р9 | 580 | 4 | |
У7, У8, У10, У12 | 200—220 | 1 | 59 |
Р6М5К5, Р9, Р9М4К8, Р18 | 620—630 | 4 |
Сопротивление разрушению
Кроме «горячих» свойств от материала для режущего инструмента требуются и высокие механические свойства; под этим подразумевается сопротивление хрупкому разрушению, так как при высокой твердости (более 60 HRC) разрушение всегда происходит по хрупкому механизму. Прочность таких высокотвердых материалов обычно определяют как сопротивление разрушению при изгибе призматических, не надрезанных образцов, при статическом (медленном) и динамическом (быстром) нагружении. Чем выше прочность, тем большее усилие может выдержать рабочая часть инструмента, тем большую подачу и глубину резания можно применить, и это увеличивает производительность процесса резания.
Химический состав быстрорежущих сталей
Химический состав некоторых быстрорежущих сталей Марка стали C Cr W Mo V CoР0М2Ф3 | 1,10—1,25 | 3,8—4,6 | — | 2,3—2,9 | 2,6—3,3 | — |
Р6М5 | 0,82—0,90 | 3,8—4,4 | 5,5—6,5 | 4,8—5,3 | 1,7—2,1 | < 0,50 |
Р6М5Ф2К8 | 0,95—1,05 | 3,8—4,4 | 5,5—6,6 | 4,6—5,2 | 1,8—2,4 | 7,5—8,5 |
Р9 | 0,85—0,95 | 3,8—4,4 | 8,5—10,0 | < 1,0 | 2,0—2,6 | — |
Р18 | 0,73—0,83 | 3,8—4,4 | 17,0—18,5 | < 1,0 | 1,0—1,4 | < 0,50 |
Изготовление и обработка быстрорежущих сталей
Быстрорежущие стали изготавливают как классическим способом (разливка стали в слитки, прокатка и проковка), так и методами порошковой металлургии (распыление струи жидкой стали азотом)[2]. Качество быстрорежущей стали в значительной степени определяется степенью ее прокованности. При недостаточной проковке изготовленной классическим способом стали наблюдается карбидная ликвация.
При изготовлении быстрорежущих сталей распространенной ошибкой является подход к ней как к «самозакаливающейся стали». То есть достаточно нагреть сталь и охладить на воздухе, и можно получить твердый износостойкий материал. Такой подход абсолютно не учитывает особенности высоколегированных инструментальных сталей.
Перед закалкой быстрорежущие стали необходимо подвергнуть отжигу. В плохо отожженных сталях наблюдается особый вид брака: нафталиновый излом, когда при нормальной твердости стали она обладает повышенной хрупкостью.
Грамотный выбор температуры закалки обеспечивает максимальную растворимость легирующих добавок в α-железе, но не приводит к росту зерна.
После закалки в стали остается 25—30 % остаточного аустенита. Помимо снижения твердости инструмента, остаточный аустенит приводит к снижению теплопроводности стали, что для условий работы с интенсивным нагревом режущей кромки является крайне нежелательным. Снижения количества остаточного аустенита добиваются двумя путями: обработкой стали холодом или многократным отпуском[2]. При обработке стали холодом ее охлаждают до −80…−70 °C, затем проводят отпуск. При многократном отпуске цикл «нагрев — выдержка — охлаждение» проводят по 2—3 раза. В обоих случаях добиваются существенного снижения количества остаточного аустенита, однако полностью избавиться от него не получается.
Принципы легирования быстрорежущих сталей
Высокая твердость мартенсита объясняется растворением углерода в α-железе. Известно, что при отпуске из мартенсита в углеродистой стали выделяются мельчайшие частицы карбида. Пока выделившиеся карбиды еще находятся в мельчайшем дисперсном рассеянии (то есть на первой стадии выделения при отпуске до 200 °C), твердость заметно не снижается. Но если температуру отпуска поднять выше 200 °C, происходит рост карбидных выделений, и твердость падает.
Чтобы сталь устойчиво сохраняла твердость при нагреве, нужно ее легировать такими элементами, которые затрудняли бы процесс коагуляции карбидов. Если ввести в сталь какой-нибудь карбидообразующий элемент в таком количестве, что он образует специальный карбид, то красностойкость скачкообразно возрастает. Это обусловлено тем, что специальный карбид выделяется из мартенсита и коагулирует при более высоких температурах, чем карбид железа, так как для этого требуется не только диффузия углерода, но и диффузия легирующих элементов. Практически заметная коагуляция специальных карбидов хрома, вольфрама, молибдена, ванадия происходит при температурах выше 500 °C.
Таким образом, красностойкость создается легированием стали карбидообразующими элементами (вольфрамом, молибденом, хромом, ванадием) в таком количестве, при котором они связывают почти весь углерод в специальные карбиды и эти карбиды переходят в раствор при закалке. Несмотря на сильное различие в общем химическом составе, состав твердого раствора очень близок во всех сталях, атомная сумма W+Mo+V, определяющая красностойкость, равна примерно 4 % (атомн.), отсюда красностойкости и режущие свойства у разных марок быстрорежущих сталей близки. Быстрорежущая сталь, содержащая кобальт, превосходит по режущим свойствам остальные стали (он повышает красностойкость), но кобальт очень дорогой элемент.
Маркировка быстрорежущих сталей
В советских и российских марочниках сталей марки быстрорежущих сталей обычно имеют особую систему обозначений и начинаются с буквы «Р» (rapid — скорость). Связанно это с тем, что эти стали были изобретены в Англии, где такую сталь называли «rapid steel». Цифра после буквы «Р» обозначает среднее содержание в ней вольфрама (в процентах от общей массы, буква В пропускается). Затем указывается после букв М, Ф и К содержание молибдена, ванадия и кобальта. Инструменты из быстрорежущей стали иностранного производства обычно маркируются аббревиатурой HSS (High Speed Steel).
Применение
В последние десятилетия использование быстрорежущей стали сокращается в связи с широким распространением твёрдых сплавов. Из быстрорежущей стали изготавливают в основном концевой инструмент (метчики, свёрла, фрезы небольших диаметров) В токарной обработке резцы со сменными и напайными твердосплавными пластинами почти полностью вытеснили резцы из быстрорежущей стали.
По применению отечественных марок быстрорежущих сталей существуют следующие рекомендации.
Примечания
Литература
dic.academic.ru
2.Требования к инструментальным материалам
1.Роли и значения обработки резанием. Исторический обзор развития учения о резании металлов.
Обработка металлов и других конструкционных материалов резанием на металлорежущих станках — весьма распространенный производственный процесс, назначением которого является придание заготовкам с помощью режущего инструмента правильной геометрической формы, требуемых размеров и чистоты поверхности. На большинстве машиностроительных заводов трудоемкость обработки резанием составляет 45—60% от общей трудоемкости изготовления машин, и поэтому совершенствование технологии резания металлов является актуальной народнохозяйственной задачей.
Изучение закономерностей явлений, связанных с резанием металлов, конструкцией режущих инструментов и металлорежущих станков, необходимо не только для сознательного управления процессами резания, но и для проектирования более совершенных технологических процессов изготовления деталей машин и приборов.
-высокая твёрдость (к сталям 22HRC…35HRC)
-высокая прочность
-температуростойкость (θкр=2200-15000)(красностойкость)
-коэффициент линейного расширения(должен быть как можно меньше)
-коэффициент трения(чтобы материалы имели незначительный элемент)
-технологичность
-недефицитность
-низкая способность к слипанию с обрабатыв. материалом
3. Углеродистые и лигированые инструментальные стали и их области применения.
Углеродистые:У7,У7А-топоры; У8,У8А-зубила,долота;У9,У9А-стамески,лезвия,пилы по дереву;У10,У11-нажовочные полотна,плашки,свёрла;У11,У12-резцы по металлу, плашки для станков;У13-напильники. Θкр=2200С.Vкр=до 30м/мин.Используются на низких скоростях, критическая скорость 15-20м/мин.Лигированные:ХВ5,ХВГ,9ХС Θкр=250-3000С.Используются на относительно небольших скоростях резания. Сталь ХВ5 обладающая высокой размерной стойкостью, применяется для изготовления разверток, фасонных резцов. Из стали ХВГ инструменты мало деформируются при закалке, используются для изготовления протяжек, имеющих большую длину при относительно небольшом диаметре.9ХС для и згот. свёрл, разверток, метчиков малых размеров.
4.Быстрорежущие инструментальные стали и их область применения.
Обладают высокой твёрдостью,прочностью и теплостойкостью.Они разделяются на несколько групп:Вольфрамовые:Р18- 18%вольфрама,82% железа,Р9- 9%вольфрама, 91%железо(фрезы,свёрла и др.инструменты,работ относительно при высоких скоростях).Вольфрамомолибденовые:
Р6М5-6%вольфрам,5%молибден,89%железо(фрезы,зуборезный инструмент,свёрла),Ванадиевые:Р9Ф5-9%вольфрам,5%ванадий,86%железо(развёртки,метчики.Недостаток-низкая шлифуемость).Кобольтовые:Р9К5() Θкр=6200С.Vкр=60м/мин.
5.Металлокерамические твёрдые сплавы и их область применения.
Твёрдоиспеченные металлокерамические сплавы на основе карбидов вольфрама(WC),карбидов титана(TiC),карбидов тантала(TaC) находят высокое применение для изгот.режущих инструментов.Металлокерамические твёрдые сплавы разделяют на:вольфрамовые ВК2-2%кобольт,98%вольфрам Θкр=9500С.Vкр=200м/мин,вольфрамотитановые Т30К4 30%карбидтитан,4%кобольт,66%карбидвольфрам. Θкр=11000С.Vкр=300м/мин,вольфрамотитанотанталовые.
6.Минералокирамические инструментальные материалы и их область применения.
Минералокерамика представляет собой окись алюминия Al2O3 подвергнутую специальной термической обр-ке и выпускаемой в форме пластинок белого цвета,разнообразных профилей и размеров.Минералокерамика превосходит nуступает им в отношении вязкости и теплопроводимости.Резцы с минералокерамическими пластинками применяют на честовых операциях,т.е.при работе с высокими скоростями резания(до 200м/мин).При подачах до 0.15…0.6мм/об при обр-ке стали и до 0.3…0.8мм/об при обр-ке чугуна.
7.Сверхтвёрдые инструментальные материалы и их область применения.
Для чистого и тонкого точения применяют гексонит(P) и синтетические поликресталические алмазы(типа корбонадо).Резцы из гексаната применяют для обр-ки закалённых сталей,жаропрочных сталей,твёрдых сплавов Θкр=850..15000С.Vкр=до 200м/мин.Резцы оснащённые алмазами карбонадо используют для обр-ки неметаллов,цветных металлов и сплавов Θкр=6500С.Vкр=300…1200м/мин.
8.Условные обозначения элементов кинематических схем станков.
9.Типы механизмов(клиноремённая,цепная,зубчатая и червячные передачи) их хар-ка.
12.Механизмы бесступенчатого регулирования скоростей,их достоинства и недостатки.
C помощью механизмов бесступенчатого регулирования скоростей можно наиболее точно установить необходимые скорость резания и величину подачи. Механизмы бесступенчатого регулирования скоростей бывают электрические, механические и гидравлические (гидроприводы). Электрический механизм бесступенчатого регулирования частоты вращения представляют собой шунтовой электродвигатель постоянного тока. Регулирование частоты вращения производится при помощи реостата, включоного в цепь возбуждения. Диапазон регулирования
Недостаток такого привода в том, что для его питания необходим постоянный ток.
studfiles.net
ГОСТ, состав, твердость, термическая обработка :: SYL.ru
Для того чтобы рабочая поверхность инструмента сохраняла заданные свойства длительное время, необходимо использование специальных сплавов и сталей для изготовления таких элементов. На сегодняшний день детали режущего инструмента производятся из твердых сплавов, инструментальных марок стали. Для фрез, резцов, зубил используется в основном быстрорежущая сталь.
Основные требования к сплавам для режущего инструмента
Детали такого типа длительное время работают в условиях трения и повышенных температур. Однако рабочая поверхность должна сохранять свои свойства, обладать высокой износостойкостью и твердостью. При больших скоростях, которые набирает инструмент в процессе резанья, нагревается и его кромка, и сама деталь, и стружка. Поэтому основная характеристика, которой должна обладать быстрорежущая сталь – теплостойкость. Для труднообрабатываемых материалов используют порошковые быстрорежущие стали. Они имеют более высокие режущие свойства. Недостатком таких сплавов является затруднительная обработка заготовок. Все необходимые характеристики достигаются путем введения определенных легирующих элементов и специальной термической обработкой.
Маркировка стали
Быстрорежущая сталь маркируется буквой Р, которая ставится впереди. Основными легирующими элементами являются вольфрам, хром. Также дополнительно вводят такие элементы, как ванадий, молибден. Цифра после буквы Р указывает процентное содержание вольфрама в стали. Как правило, в состав быстрорежущей стали входит около 4% хрома. Данный элемент в маркировке не указывается. Если цифры стоят перед буквой Р, то они указывают на процентное содержание углерода (например, сталь 11Р3АМ3Ф2 содержит 1,1% углерода). В основном стали данной группы являются высоколегированными.
Влияние легированных элементов на свойства стали
Высокую теплостойкость быстрорежущих марок стали обеспечивают вольфрам, молибден. На их основе образовываются карбиды, которые частично переходят в твердый раствор. После термообработки обеспечивается структура мартенсита. Вольфрам, молибден, а также ванадий замедляют его распад. Именно это обеспечивает необходимую красностойкость. Продолжительное время использовалась быстрорежущая сталь, легированная только вольфрамом. Однако из-за дефицитности данного металла его начали частично заменять молибденом. Этот элемент также положительно влияет на склонность вольфрамовых марок стали к карбидной неоднородности. Наиболее твердый карбид образовывает ванадий. Однако при этом содержание углерода должно быть достаточным для большего насыщения твердого раствора. Чем больше вводится ванадия, тем больше должно быть углерода в составе сплава. Основная задача хрома – придание стали высокой прокаливаемости. Красностойкость также повышает и кобальт.
Быстрорежущая сталь (твердость при легировании данным элементом повышается до 70 HRC) в данном случае будет иметь пониженную прочность. Стоит отметить, что введение хрома широко не применяется из-за большой стоимости элемента.
Термообработка быстрорежущей стали
Данные марки стали поступают в состоянии ковки (температура около 1200 °С). Производится нагрев до 860 °С, затем металл выдерживается при температуре около 760 °C. Термическая обработка инструмента включает закалку и отпуск. Стоит отметить, что такая обработка имеет свои особенности. Во-первых, необходим медленный, постепенный нагрев. Так как сталь высоколегированная, ее теплопроводность довольно низкая, стремительное нагревание может привести к образованию трещин. При этом очень важно нагревать заготовку равномерно. Используются электрические печи, соляные ванны. Процесс обработки быстрорежущей стали довольно трудоемкий, он требует четкого соблюдения всех этапов технологического процесса.
Главная задача закалки – растворение карбидов в аустените. Как правило, карбиды на основе вольфрама и хрома растворяются при 1200 °С, ванадий требует более высоких температур. После данного этапа структура имеет избыточные (те, что не растворились) карбиды. Они сдерживают рост зерна. Высокие температуры обеспечивают мелкозернистый аустенит. Охлаждение происходит в масле или расплаве солей. Температура по сечению детали выравнивается. Такая обработка быстрорежущей стали позволяет избежать появления трещин. После закалки сталь имеет следующую структуру: мартенсит, остаточный аустенит, карбиды.
Отпуск быстрорежущей стали
Отпуск стали способствует превращению мартенсита закалки в мартенсит отпуска, аустенита в мартенсит (так как первый не обладает достаточной твердостью), снятию остаточных напряжений. Как правило, термическая обработка быстрорежущей стали включает многократный отпуск. Начинается данный процесс при температуре 150 °С. Далее при 550 °С происходит дисперсионное твердение (выделяются карбиды из твердого раствора). В результате возрастает твердость сплава. Более высокие температуры отпуска нежелательны, так как будет происходить процесс распада мартенсита, и, соответственно, снижение твердости. Вольфрамовые стали после единичного отпуска имеют в составе остаточный аустенит. Полностью он превращается в мартенсит при втором отпуске. Остаточные напряжения снимаются в процессе третьего отпуска. Стали с содержанием кобальта могут подвергаться отпуску и в четвертый раз.
Нарушение технологии термообработки
Снижение количества углерода на поверхности заготовки может быть следствием плохой расскисленности соляной ванны, а также перегрева при аустенизации. Превышение температуры ведет к оплавлению границ зерна. Также обработанная деталь может иметь трещины. Такое явление возникает из-за быстрого нагрева металла. Еще одна причина – ускоренное охлаждение. Низкое значение твердости может быть следствием недостаточного легирования структуры мартенсита, нарушением температурного режима при отпуске, при котором остается остаточный аустенит. Еще один возможный дефект заготовки – нафталинистый излом.
Наиболее распространенные марки быстрорежущей стали
Быстрорежущая сталь (ГОСТ 19265-73) делится на сплавы нормальной и повышенной теплостойкости. Первая группа включает такие марки, как Р18, Р6М5. Твердость их достигает 63 HRC. Основное их предназначение – обработка чугунов, медных, алюминиевых сплавов. Более высокой теплостойкостью обладают вольфрамовые стали. Их применяют для изготовления сверл, фрез, резцов. Сталь Р6М5, которая содержит молибден, немного уступает в режущих свойствах, однако она существенно дешевле. К тому же пластичность ее несколько выше, а склонность к образованию трещин не столь высока. Более теплостойкие стали имеют в составе ванадий и кобальт (10Р6М5, Р9Ф5). Их твердость досягает 66 HRC. Используются они для обработки более прочных конструкционных сталей, жаропрочных сплавов, при изготовлении чистового инструмента. Характерно, что данные марки имеют более высокую износостойкость (благодаря наличию в составе ванадия). В последнее время все чаще применяется метод порошковой металлургии. Такие инструменты имеют более высокие режущие свойства.
www.syl.ru
Быстрорежущая сталь - основа инструментальных материалов
Автор: редакционная статья
Категории: металлообработка
Определение. История. Характеристики. Применение.
Быстрорежущая сталь
Быстрорежущие стали — легированные стали, предназначенные, главным образом, для изготовления металлорежущего инструмента, работающего при высоких скоростях резания.
Быстрорежущая сталь должна обладать высоким сопротивлением разрушению, твёрдостью (в холодном и горячем состояниях) и красностойкостью.Высоким сопротивлением разрушению и твердостью в холодном состоянии обладают и углеродистые инструментальные стали. Однако инструмент из них не в состоянии обеспечить высокоскоростные режимы резания. Легирование быстрорежущих сталей вольфрамом, молибденом, ванадием и кобальтом обеспечивает горячую твердость и красностойкость стали.
Истории создания
Для обточки деталей из дерева, цветных металлов, мягкой стали резцы из обычной твердой стали были вполне пригодны, но при обработке стальных деталей резец быстро разогревался, скоро изнашивался и деталь нельзя было обтачивать со скоростью больше 5 м/м.Барьер этот удалось преодолеть после того, как в 1858 году Р. Мюшетт получил сталь, содержащую 1,85 % углерода, 9 % вольфрама и 2,5 % марганца. Спустя десять лет Мюшетт изготовил новую сталь, получившую название самокалки. Она содержала 2,15 % углерода, 0,38 % марганца, 5,44 % вольфрама и 0,4 % хрома. Через три года на заводе Самуэля Осберна в Шеффилде началось производство мюшеттовой стали. Она не теряла режущей способности при нагревании до 300 °C и позволяла в полтора раза увеличить скорость резания металла — 7,5 м/мин.Спустя сорок лет на рынке появилась быстрорежущая сталь американских инженеров Тэйлора и Уатта. Резцы из этой стали допускали скорость резания до 18 м/мин. Эта сталь стала прообразом современной быстрорежущей стали Р18.Еще через 5—6 лет появилась, сверхбыстрорежущая сталь, допускающая скорость резания до 35 м/мин. Так, благодаря вольфраму было достигнуто повышение скорости резания за 50 лет в семь раз и, следовательно, во столько же раз повысилась производительность металлорежущих станков.Дальнейшее успешное использование вольфрама нашло себе применение в создании твердых сплавов, которые состоят из вольфрама, хрома, кобальта. Были созданы такие сплавы для резцов, как стеллит. Первый стеллит позволял повысить скорость резания до 45 м/мин при температуре 700—750 °C. Сплав вида, выпущенный Круппом в 1927 году, имел твердость по шкале Мооса 9,7—9,9 (твердость алмаза равна 10).В 1970-х годах в связи с дефицитом вольфрама быстрорежущая сталь марки Р18 была почти повсеместно заменена на сталь марки Р6М5, которая в свою очередь вытесняется безвольфрамовыми Р0М5Ф1 и Р0М2Ф3.
Характеристики быстрорежущих сталей
Горячая твердость
Твердость инструментальных сталей при повышенных температурахНа рисунке приведены кривые, характеризующие твердость углеродистой и быстрорежущей инструментальных сталей при повышенных температурах испытаний. При нормальной температуре твердость углеродистой стали даже несколько выше твердости быстрорежущей стали. Однако, в процессе работы режущего инструмента, происходит интенсивное выделение тепла. При этом до 80 % выделившегося тепла уходит на разогрев инструмента. Вследствие повышения температуры режущей кромки начинается >отпуск материала инструмента и снижается его твердость.После нагрева до 200 °C твердость углеродистой стали начинает быстро падать. Для этой стали недопустим режим резания, при котором инструмент нагревался бы выше 200 °C. У быстрорежущей стали высокая твердость сохраняется при нагреве до 500—600 °C. Инструмент из быстрорежущей стали более производителен, чем инструмент из углеродистой стали.
Красностойкость
Если горячая твердость характеризует то, какую температуру сталь может выдержать, то красностойкость характеризует, сколько времени сталь будет выдерживать такую температуру. То есть насколько длительное времязакаленная и отпущенная сталь будет сопротивляться разупрочнению при разогреве.Существует несколько характеристик красностойкости. Приведем две из них.Первая характеристика показывает, какую твердость будет иметь сталь после отпуска при определенной температуре в течение заданного времени.Второй способ охарактеризовать красностойкость основан на том, что интенсивность снижения горячей твердости можно измерить не только при высокой температуре, но и при комнатной так как кривые снижения твердости при высокой температуре и комнатной идут эквидистантно, а измерить твердость при комнатной температуре, разумеется, гораздо проще, чем при высокой. Опытами установлено, что режущие свойства теряются при твердости 50 HRC при температуре резания, что соответствует примерно 58 HRC при комнатной. Отсюда красностойкость характеризуется температурой отпуска, при которой за 4 часа твердость снижается до 58 HRC.
Характеристики теплостойкости углеродистых и красностойкости быстрорежущих инструментальных сталей | |||
Марка стали | Температура отпуска, °C | Время выдержки, час | Твердость, HRCэ |
У7, У8, У10, У12 | 150—160 | 1 | 63 |
Р9 | 580 | 4 | |
У7, У8, У10, У12 | 200—220 | 1 | 59 |
Р6М5К5, Р9, Р9М4К8, Р18 | 620—630 | 4 |
Сопротивление разрушению
Кроме «горячих» свойств от материала для режущего инструмента требуются и высокие механические свойства; под этим подразумевается сопротивление хрупкому разрушению, так как при высокой твердости (более 60 HRC) разрушение всегда происходит по хрупкому механизму. Прочность таких высокотвердых материалов обычно определяют как сопротивление разрушению при изгибе призматических, не надрезанных образцов, при статическом (медленном) и динамическом (быстром) нагружении. Чем выше прочность, тем большее усилие может выдержать рабочая часть инструмента, тем большую подачу и глубину резания можно применить, и это увеличивает производительность процесса резания.Химический состав быстрорежущих сталей
Химический состав некоторых быстрорежущих сталей | ||||||
Марка стали | C | Cr | W | Mo | V | Co |
Р0М2Ф3 | 1,10—1,25 | 3,8—4,6 | — | 2,3—2,9 | 2,6—3,3 | — |
Р6М5 | 0,82—0,90 | 3,8—4,4 | 5,5—6,5 | 4,8—5,3 | 1,7—2,1 | < 0,50 |
Р6М5Ф2К8 | 0,95—1,05 | 3,8—4,4 | 5,5—6,6 | 4,6—5,2 | 1,8—2,4 | 7,5—8,5 |
Р9 | 0,85—0,95 | 3,8—4,4 | 8,5—10,0 | < 1,0 | 2,0—2,6 | — |
Р18 | 0,73—0,83 | 3,8—4,4 | 17,0—18,5 | < 1,0 | 1,0—1,4 | < 0,50 |
Изготовление и обработка быстрорежущих сталей
Быстрорежущие стали изготавливают как классическим способом (разливка стали в слитки, прокатка и проковка), так и методами порошковой металлургии (распыление струи жидкой стали азотом). Качество быстрорежущей стали в значительной степени определяется степенью ее прокованности. При недостаточной проковке изготовленной классическим способом стали наблюдается карбидная ликвация.При изготовлении быстрорежущих сталей распространенной ошибкой является подход к ней как к «самозакаливающейся стали». То есть достаточно нагреть сталь и охладить на воздухе, и можно получить твердый износостойкий материал. Такой подход абсолютно не учитывает особенности высоколегированных инструментальных сталей.Перед закалкой быстрорежущие стали необходимо подвергнуть отжигу. В плохо отожженных сталях наблюдается особый вид брака: нафталиновый излом, когда при нормальной твердости стали она обладает повышенной хрупкостью.Грамотный выбор температуры закалки обеспечивает максимальную растворимость легирующих добавок в α-железе, но не приводит к росту зерна.После закалки в стали остается 25—30 % остаточного аустенита. Помимо снижения твердости инструмента, остаточный аустенит приводит к снижению теплопроводностистали, что для условий работы с интенсивным нагревом режущей кромки является крайне нежелательным. Снижения количества остаточного аустенита добиваются двумя путями: обработкой стали холодом или многократным отпуском. При обработке стали холодом ее охлаждают до −80…−70 °C, затем проводят отпуск. При многократном отпуске цикл «нагрев — выдержка — охлаждение» проводят по 2—3 раза. В обоих случаях добиваются существенного снижения количества остаточногоаустенита, однако полностью избавиться от него не получается.
Принципы легирования быстрорежущих сталей
Высокая твердость мартенсита объясняется растворением углерода в α-железе. Известно, что при отпуске из мартенсита в углеродистой стали выделяются мельчайшие частицы карбида. Пока выделившиеся карбиды еще находятся в мельчайшем дисперсном рассеянии (то есть на первой стадии выделения при отпуске до 200 °C), твердость заметно не снижается. Но если температуру отпуска поднять выше 200 °C, происходит рост карбидных выделений, и твердость падает.Чтобы сталь устойчиво сохраняла твердость при нагреве, нужно ее легировать такими элементами, которые затрудняли бы процесс коагуляции карбидов. Если ввести в сталь какой-нибудь карбидообразующий элемент в таком количестве, что он образует специальный карбид, то красностойкость скачкообразно возрастает. Это обусловлено тем, что специальный карбид выделяется из мартенсита и коагулирует при более высоких температурах, чем карбид железа, так как для этого требуется не только диффузия углерода, но и диффузия легирующих элементов. Практически заметная коагуляция специальных карбидов хрома, вольфрама, молибдена, ванадияпроисходит при температурах выше 500 °C.Таким образом, красностойкость создается легированием стали карбидообразующими элементами (вольфрамом, молибденом, хромом, ванадием) в таком количестве, при котором они связывают почти весь углерод в специальные карбиды и эти карбиды переходят в раствор при закалке. Несмотря на сильное различие в общем химическом составе, состав твердого раствора очень близок во всех сталях, атомная сумма W+Mo+V, определяющая красностойкость, равна примерно 4 % (атомн.), отсюда красностойкости и режущие свойства у разных марок быстрорежущих сталей близки. Быстрорежущая сталь, содержащая кобальт, превосходит по режущим свойствам остальные стали (он повышает красностойкость), но кобальт очень дорогой элемент.
Маркировка быстрорежущих сталей
В советских и российских марочниках сталей марки быстрорежущих сталей обычно имеют особую систему обозначений и начинаются с буквы «Р» (rapid — быстрый). Связанно это с тем, что эти стали были изобретены в Англии, где такую сталь называли «rapid steel». Цифра после буквы «Р» обозначает среднее содержание в ней вольфрама (в процентах от общей массы, буква В пропускается). Затем указывается после букв М, Ф и К содержание молибдена, ванадия и кобальта. Инструменты из быстрорежущей стали иностранного производства обычно маркируются аббревиатурой HSS (High Speed Steel).
Применение
В последние десятилетия использование быстрорежущей стали сокращается в связи с широким распространением твёрдых сплавов. Из быстрорежущей стали изготавливают в основном концевой инструмент (метчики, свёрла, фрезы небольших диаметров) В токарной обработке резцы со сменными и напайными твердосплавными пластинами почти полностью вытеснили резцы из быстрорежущей стали.По применению отечественных марок быстрорежущих сталей существуют следующие рекомендации.
www.metaljournal.com.ua
Быстрорежущая сталь. Ее свойства и классификация
В наше время быстрорежущая сталь продолжает оставаться ведущим материалом для производства разнообразных металлообрабатывающих насадок и режущего инструмента. Такие сплавы часто используются при изготовлении станочных пил, сверл и рабочих головок буров. Несмотря на появившееся сейчас большое разнообразие всевозможных твердосплавных композитных и керамических материалов, обеспечивающих даже большую производительность обработки, быстрорежущие инструментальные стали прочно удерживают свои позиции.
Широкое применение таких сплавов для производства сложнопрофильных режущих инструментов обусловлено сочетанием в них высокого показателя прочности (до 68 HRC) и теплостойкости (они не теряют своих рабочих свойств даже при температуре 650°С) с высоким значением вязкости, значительно превышающим аналогичный показатель для твердосплавных композитных материалов. К тому же быстрорежущая сталь обладает чрезвычайно высокой технологичностью, что подразумевает хорошую обрабатываемость способом давления и резания.
Какие свойства будет иметь такой сплав, зависит от легирующих добавок. Обычно быстрорежущая сталь представляет собой многокомпонентную систему с содержанием хрома, молибдена, вольфрама, кобальта и ванадия. Наличие различных составляющих, а также их содержание в процентном отношении указывается при маркировке. Литера Р здесь означает, что сталь является быстрорежущей, последующая цифра указывает содержание вольфрама в процентах. Дальнейшие буквы обозначают наличие других легирующих элементов, а цифры, идущие вслед за литерами, – их процентную массовую долю в сплаве. Так, буква М означает наличие в системе молибдена, Ф – ванадия, К – кобальта, А – азота.
По содержанию легирующих добавок быстрорежущая сталь может классифицироваться на вольфрамовую, молибденовую, вольфрамо-молибденовую. В особую группу выделяются металлы, легированные кобальтом. Такие сплавы, как правило, применяются при изготовлении инструментов для обработки труднообрабатываемых деталей из жаропрочных сплавов. Быстрорежущая сталь, легированная ванадием главным образом предназначена для производства инструментов так называемой "чистовой" отделки – протяжек, разверток и прочих.
Самая распространенная и, пожалуй, старейшая марка быстрорежущей стали Р18 служит для изготовления сложных и фасонных резьбонарезных инструментов. Средства же стандартной формы для высококачественной обработки металла изготавливаются преимущественно из сплава марки Р9. Из нее делают фрезы, резцы и тому подобное.
По рабочему температурному режиму быстрорежущие стали делятся на три категории: сплавы с нормальной, повышенной и высокой теплостойкостью. К первой группе принадлежат вольфрамовые (Р18, Р9) и вольфрамо-молибденовые (Р6М5). Такие марки применяются при обработке цветных металлов, конструкционных сталей и чугуна.
Для материалов второй категории характерным является чрезвычайно высокое содержание кобальта, углерода и ванадия. Наиболее популярная марка в данной группе - Р6М5Ф3. Ванадиевым сталям свойственна повышенная износостойкость. Единственный их серьезный недостаток – плохая шлифуемость, так как твердость карбидов ванадия не уступает аналогичному показателю электрокорундового шлифовального диска.
И, наконец, стали третьей категории характеризуются невысоким процентом содержания углерода, что делает их пригодными для обработки жаропрочных, нержавеющих и титановых сплавов. Еще одна их характерная отличительная черта – большого число легирующих элементов. К этой группе относятся такие марки, как 3В20К20Х4Ф, В11М7К23 и др.
fb.ru