- Межкристаллитная коррозия нержавеющих сталей чигал
- Цинкование стали в домашних условиях
- Коррозия нержавеющей стали
- Почему теплопроводность меди больше чем теплопроводность стали
- Мартенситная нержавеющая сталь
- Конструкционная сталь что это
- Сталь подшипника
- Аппарат для электрополировки нержавеющей стали
- Электрохимполировка стали нержавеющей
- Межкристаллитная коррозия это
- Что такое углеродистая сталь где она используется
Способ термической обработки нержавеющих сталей мартенситного класса. Нержавеющая сталь мартенситная
Нержавеющая сталь - мартенситный класс
Нержавеющая сталь - мартенситный класс
Cтраница 1
Нержавеющая сталь мартенситного класса с объомноцентрированной решеткой азотируется на большую глубину, чем аусте-ыитная сталь, имеющая гранецентриро-ванную решетку. Твердость азотированного слоя зависит гл. [2]
Легирование Ni нержавеющих сталей мартенситного класса, содержащих 12 - 14 % Сг, или сталей полуферритного класса с 15 - 17 % Сг в количестве 2 - 4 % существенно улучшает их механические свойства и увеличивает коррозионную стойкость. Они имеют большую пластичность и вязкость, чем хромистые стали. [3]
При исследовании нержавеющих сталей мартенситного класса было обнаружено [34], что минимальная склонность к коррозионному растрескиванию наблюдается тогда, когда в структуре присутствует от 5 до 10 % дельта-феррита. Трещины концентрировались вокруг дельта-феррита и поэтому было сделано заключение, что дельта-феррит препятствует распространению трещин. [4]
Для испытания нержавеющих сталей мартенситного класса на склонность к коррозии под напряжением рекомендуется раствор 1: 1 НС1 ( уд. Испытания проводятся при комнатной температуре, общая продолжительность испытаний до 50 час. Испытания позволяют выбрать стойкие к коррозионному растрескиванию материалы и оптимальные режимы термической обработки. [5]
Таким образом, нержавеющие стали мартенситного класса после закалки и отпуска характеризуются высокой твердостью, низкими значениями пластичности и свариваемости; их нельзя подвергать гибочным операциям в холодном состоянии. [6]
Дефекты, типичные для нержавеющих сталей мартенситного класса: продольные трещины на слитках и блюмах, грубые рванины при прокатке слитков и заготовок. [7]
Разработан метод для испытания нержавеющих сталей мартенситного класса на склонность к коррозии под напряжением в растворе, содержащем соляную кислоту с добавками селенистого ангидрида и уротропина. [8]
Значительные трудности возникают при изготовлении деталей из кавитационностоиких нержавеющих сталей мартенситного класса, так как сварка таких сталей, как правило, требует подогрева. [9]
Сопротивление коррозии под напряжением этой стали превосходит сопротивление нержавеющих сталей мартенситного класса при одинаковом уровне напряжений. [10]
Что же касается средне и низколегированных сплавов, а также нержавеющих сталей мартенситного класса, то они исследованы очень слабо. Между тем именно среди сталей этого класса чаще всего встречаются сплавы с повышенной прочностью. Однако они же отличаются повышенной склонностью к КР, что создает значительные трудности при применении их в технике. Стали данного класса, как правило, упрочняются до максимального уровня прочности ( ав 160 - 190 кГ / мм2) и применяются при минимальных коэффициентах запаса прочности ( 1 1 - 1 35) для получения благоприятных весовых характеристик изделий. Требуемая прочность обеспечивается соответствующей термической обработкой ( закалка и низкотемпературный отпуск), приводящей к образованию структуры низкоотпущенного мартенсита. Такое состояние материала1 обеспечивает высокую прочность, но характеризуется повышенной чувствительностью к концентраторам напряжений и склонностью к хрупкому разрушению. [11]
Нами исследовано также влияние режимов термической обработки на сопротивление коррозионной усталости во влажном воздухе некоторых нержавеющих сталей мартенситного класса. [13]
Азотированием стали марки Н18К9М5Т при т-ре 450 - 560 С в течение 48 ч получают упрочненный ( - 900 ИV) слой глубиной 0 20 - 0 25 мм. Сопротивление коррозии под напряжением этих сталей превосходит сопротивление нержавеющих сталей мартенситного класса при одинаковом уровне напряжений. Низкое содержание углерода и др. примесей уменьшает плотность точек закрепления дислокаций. [14]
В настоящее время советские металловеды работают над созданием новых высокопрочных, жаростойких и жаропрочныд сталей и сплавов, новых сплавов с особыми физическими свойствами, а также над созданием новых видов термической и химико-термической обработки деталей машин и приборов. При этом наиболее острыми проблемами, выдвинутыми машиностроительной промышленностью, являются разработки: конструкционной стали, имеющей после обычной термической обработки предел прочности более 200 кГ / мм при достаточной пластичности и хорошей свариваемости; нержавеющей стали мартенситного класса, допускающей обработку резанием после закалки и дающей после старения коэффициент прочности более 200 кГ / мм2; методов термо-механической обработки стали, обеспечивающей коэффициент прочности более 250 кГ / мм2; методов термической обработки готовых деталей машин, обеспечивающих стабильность размеров в эксплуатации в пределах десятых долей микрона; новых литейных алюминиевых сплавов, имеющих после термической обработки коэффициент прочности не менее 40 кГ / лми. [15]
Страницы: 1 2
www.ngpedia.ru
Мартенситная нержавеющая сталь - Энциклопедия по машиностроению XXL
Мартенситные нержавеющие стали имеют наилучшую коррозионную стойкость после закалки из аустенитной области. В этом состоянии они обладают высокой твердостью и хрупкостью. Пластичность повышается при отжиге [c.301]После обработки сплавы, бывшие до того стойкими, становятся чувствительными к водородному растрескиванию ферритные и мартенситные нержавеющие стали в результате холодной обработки также проявляют большую склонность к водородному растрескиванию. — Примеч, авт. [c.302]
Мартенситные нержавеющие и дисперсионно-твердеющие стали, термообработанные с целью получения предела текучести- олее 1,24 МПа, самопроизвольно растрескиваются в атмосфере, солевом тумане или при погружении в водные среды, даже если они не находятся в контакте с другими металлами [55—58]. Лопасти воздушного компрессора из мартенситной нержавеющей стали [59 ] разрушались вдоль передней кромки, где были велики остаточные напряжения и конденсировалась влага. Для сверхпрочных мартенситных нержавеющих сталей с 12 % Сг, которые находились в морской атмосфере под напряжением, составляющим 75 % от предела текучести, срок службы не превышал 10 дней [60]. Приведенные данные получили разнообразные объяснения, однако они убедительно доказывают, что сталь в указанных случаях разрушается в результате или водородного растрескивания, или КРН. При наличии в стали высоких напряжений, она может растрескиваться в воде без внедрения водорода, который образуется при взаимодействии воды с металлом. По-видимому, в этом случае вода непосредственно адсорбируется на поверхности и уменьшает прочность металлических связей в степени, достаточной для зарождения трещин (адсорбционное растрескивание под напряжением). [c.320]Мартенситные хромистые нержавеющие стали. Мартенситные нержавеющие стали склонны к коррозионному растрескиванию в морских атмосферах. Степень этой склонности зависит от состава сплава п/или от термообработки, используемой для достижения высокой прочности материала. Очень подверженны коррозионному растрескиванию мартенситные стали, отпущенные при температурах от 340 до 540 °С. [c.75]
В заключение необходимо отметить, что инверсия масштабного фактора при коррозионной усталости характерна для углеродистых, низко-и среднелегированных мартенситных нержавеющих сталей, алюминиевых сплавов. Наиболее заметна она при изменении диаметра образца до 50—60 мм (рис. 69) и проявляется при большой базе испытаний, когда коррозионно-усталостное разрушение контролируется электрохимическим фактором. У нержавеющих сталей, склонных к щелевой коррозии, с увеличением диаметра образцов предел выносливости снижается и при испытании и в воздухе, и в коррозионной среде. [c.136]
Характер распространения остаточных напряжений по глубине наклепанного слоя качественно одинаковый для всех исследуемых мартенситных нержавеющих сталей. Максимальные остаточные сжимающие напряжения имеют место не на поверхности, а на некоторой глубине, сжимающие напряжения плавно уменьшаются при переходе в глубь образца и на глубине 100—150 мкм, в зависимости от режимов обкатки, меняют знак. [c.159]
Результаты испытаний образцов различных материалов на коррозию-в чистой воде при температуре около 250° С позволили следующим образом классифицировать материалы с точки зрения их коррозионной устойчивости. Наилучшей коррозионной стойкостью в воде обладают аустенитные нержавеющие стали, сплавы на основе кобальта, цирконий и гафний. Приемлемые характеристики имеют ферритные и мартенситные нержавеющие стали и сплавы на никелевой или медной основе. Наименее стойкими оказываются углеродистые и низколегированные стали и сплавы на алюминиевой основе. [c.285]
Аустенитно-мартенситные нержавеющие стали получили применение главным образом как высокопрочные. Аустенитно-мартенситные диспер-сионно-твердеющие стали обладают существенно более высокими свойствами, чем чисто аустенит-ные, и применение их предпочтительно, если нет дополнительных требований к магнитным свойствам, так как аустенитные стали немагнитны (табл. 8.24, 8.25 ГОСТ 5632-72 и ГОСТ 5949-75). [c.326]
АУСТЕНИТО-МАРТЕНСИТНЫЕ НЕРЖАВЕЮЩИЕ СТАЛИ) [c.243]
Даны предельные содержания элементов для углеродистых и низколегированных сталей, а также для мартенситных нержавеющих сталей. [c.292]
Коррозионная стойкость мартенситных нержавеющих сталей слегка увеличивается при повыщении температуры свыше 260—360° С, очевидно, вследствие изменения при этом механизма коррозии. [c.57]
На рис. -3.13 показано влияние pH раствора на время до разрушения и скорость коррозии в отсутствие наложенной поляризации от постороннего источника тока. На рис. 3.14, 3.15 показано влияние наложения катодной и анодной поляризации на время до разрушения мартенситной нержавеющей стал в растворах с различным pH. Из полученных в [359] данных следует, что катодная поляризация очень малыми плотностями тока (приблизительно до 0,1 мА/см ) увеличивает стойкость стали при pH 6,5 [c.129]
Феррито-мартенситные нержавеющие стали обрабатываются так же успешно, как и обычные малоуглеродистые стали. Значительно сложнее положение с аустенитными и особенно жаропрочными сложнолегированными сталями и сплавами на никелевой и кобальтовой основе. Это вызвано большой склонностью к наклепу и малой теплопроводностью последних. В процессе резания этих материалов возникают чрезвычайно высокие температура и нагрузка, способствующие усиленному адгезионному и диффузионному износу. [c.168]
Мартенситная нержавеющая сталь Р. V. Р. 0. 13 /оСг. 0.20/оС Поковка Отпуск [c.528]
УСКОРЕННЫЙ МЕТОД ИСПЫТАНИЯ МАРТЕНСИТНЫХ НЕРЖАВЕЮЩИХ СТАЛЕЙ НА СКЛОННОСТЬ К КОРРОЗИИ ПОД НАПРЯЖЕНИЕМ [c.116]
Стали с полным фазовым превращением ау, при охлаждении на воздухе с температуры несколько выше Лсд дающие структуру мартенсита, — мартенситные нержавеющие стали с повышенным содержанием углерода. [c.8]
Так же, как и в аустенитных сталях, элементом, вызывающим восприимчивость к межкристаллитной коррозии ферритных и мартенситных нержавеющих сталей и швов после быстрого охлаждения с высоких температур, является углерод. Однако в последнем случае отрицательное его влияние проявляется даже при содержании около 0,01%, что обусловлено более низким пределом растворимости углерода в феррите (0,002%) по сравнению с растворимостью его в аустените (0,02%). [c.92]
Козловская В. И. и др. Повышение вязкости и пластичности мартенситной нержавеющей стали при —196° С путем использования эффекта обратного мартенситного превращения. — Металловедение и термическая обработка металлов , 1966, № 5, с. 23—25. [c.189]
Мартенситные нержавеющие стали, как правило, используют либо в смягченном состоянии (отпуск при температуре 650° С или выше), либо в полностью упрочненном состоянии (отпуск при 250° с или ниже), так что существенного снижения коррозионной стойкости, связанного с выделением карбида, не происходит. Однако пайка твердым припоем лезвий ножей может привести к выделению карбида и питтинговой коррозии лезвия ножа вблизи рукоятки. Чтобы избежать этого, при пайке следует принять еобходимые меры. [c.32]
Мартенситные. Мартенсит образуется при сдвиговом типе фазового превращения при быстром охлаждении стали (закалка) из аустеиитной области фазовой диаграммы. Эта структура определяет твердость закаленных углеродистых сталей и твердость мартенситных нержавеющих сталей. У нержавеющих сталей этого класса решетка объемноцентрированная кубическая и сплавы магнитны. Типичное применение — ножевые изделия, лопатки паровых турбин и режущие инструменты. [c.244]
Вспучивание ферритных нержавеющих сталей наблюдалось, когда они были катодно защищены в морской воде. Вероятно, это происходило вследствие того, что были применены защитные плотности тока выше минимальной величины, необходимой для полной защиты. Если при контакте активных металлов с мартенситными нержавеющими сталями образуются гальванические пары, то нержавеющая сталь (катод) может разрушиться вследствие выделения на ней водорода. Такие разрушения наблюдались при лабораторных испытаниях [25]. Наблюдалось самопроизвольное растрескивание винтов из нержавеющей мартенситной стали вскоре после того, как они находились в контакте с алюминием в атмосфере морского побережья. Пропеллеры из упрочненной мартенситной нержавеющей стали, соприкасающиеся со стальным корпусом корабля, вскоре после пуска в эксплуатацию подверглись коррозионному растрескиванию. Сильно наклепанная аустенитная нержавеющая сталь 18-8 также может разрушаться в условиях, описанных для мартенситных сталей [26, 27]. В данном случае сульфиды ускоряют разрушение, и так как сплав при холодной обработке претерпевает фазовое превращение и образуется феррит, то наблюдаемый эффект может служить также примером водородного растрескивания. [c.260]
Мартенситные стали получили название по аналогии с мар-тенситной фазой углеродистых сталей. Мартенсит образуется при фазовом превращении сдвигового типа, происходящем при быстром охлаждении стали (закалке) из аустенитной области фазовой диаграммы, для которой характерна гранецентрированная кубическая структура. Мартенсит определяет твердость закаленных углеродистых сталей и мартенситных нержавеющих сталей. Нержавеющие стали этого класса имеют объемно-центрированную кубическую структуру они магнитны. Типичное применение — инструменты (в том числе и рёжущие), лопатки паровых турбин. [c.296]
Создание гальванической пары из мартенситной нержавеющей стали и электроотрица[тельного металла также может приводить к разрушениям в результате выделения водорода на катодной поверхности стали. Подобные явления наблюдали при лабораторных испытаниях [52]. Как указывалось в разд. 7.4, на практике отмечали случаи разрушения судовых винтов из мартенситной нержавеющей стали. Эти винты самопроизвольно растрескивались вскоре после того, как их приводили в контакт с алюминием в условиях прибрежной атмосферы. Аналогичным образом вели себя винты из упрочненной мартенситной нержавеющей стали, находившиеся в контакте со стальным корпусом корабля они разрушались вскоре после начала эксплуатации. Некоторые марки аустенитных нержавеющих сталей 18-8, подвергнутые [c.319]
Эти кислоты можно получить в лаборатории, пропуская сероводород через воду, насыщенную SO . Для понимания механизма наблюдаемых разрушений следует учесть, что при протекании коррозионных процессов эти кислоты легко катодно восстанавливаются. В связи с этим политионовые кислоты действуют в качестве катодного деполяризатора, который способствует растворению металла по границам зерен, обедненным хромом. Еще одна форма влияния, возможно, заключается в том, что продукты их катодного восстановления (HjS или аналогичные соединения) стимулируют абсорбцию межузельного водорода сплавом, обедненным хромом. Под напряжением этот сплав, если он имеет ферритную структуру, подвергается водородной коррозии вдоль границ зерен. Аустенитный сплав в этих условиях устойчив. Показано, что наличие в морской воде более 2 мг/л серы в виде Na S либо продуктов катодного восстановления сульфитов SOg" или тиосульфатов SjO вызывает водородное растрескивание высокопрочных сталей с 0,77 % С, а та кже ферритных и мартенситных нержавеющих сталей 167]. Предполагают, что и политионовые кислоты оказывают аналогичное действие. [c.323]
Исследование коррозио1шой стойкости-мартенситной нержавеющей стали с 13% Сг в С02-Н25 СГ средах методом рентгено-структурной спектроскопии за 281 [c.28]
Результативным методом является оптимальная термообработка. Для мартенситных нержавеющих сталей наиболее приемлемым является отпуск их в интервале температур 570-600 °С в ряде случаев целесообразен повторный отпуск при 500 С. Из углеродистых и низколегированных сталей наибольшей стойкостью к коррозии под напряжением обладают материалы о сорбигной и перлит-ферритной структурой, наименьшей - с мартенситной. Во многих случаях поверхностная закалка сталей повышает их коррозионно-механическую стойкость. [c.129]
Основная трудность при сравнительном анализе поведения различных микроструктур связана с тем, что большинство исследователей не контролирует условия отпуска и не изучает влияние микроструктуры на характер растрескивания. Важность учета этих вопросов с очевидностью подтверждается наличием связи между охрупчиванием различных микроструктур в результате воздействия среды и отпуска. Такая связь была продемонстрирована для стали 4340 с микроструктурой, соответствующей состоянию закалки и отпуска [52], для французской бейнитной стали 20СПО10 [53], для мартенситных нержавеющих сталей [54], для ннкелъхромовых сталей [11, 41] и для стали Н -130 [12]. Показано, что такие объединенные эффекты могут иметь место при охрупчивании сталей в результате отпуска при 535 или 810 К. Объединенная восприим- [c.62]
Часто утверждается (см. также рис. 8), что стойкость к растрескиванию во внешней среде возрастает с повышением температуры отпуска [9, 15, 23, 27]. При этом, конечно, предполагается, что доллсны быть исключены области температур, вызывающих охрупчивание в результате отпуска [7, 17, 52]. Предполагалось, что этот эффект может быть связан с изменением коэффициента диффузии водорода [15], с облегчением межкристаллитного растрескивания [9] или с растрескиванием смешанного типа [54]. Однако прямых подтверждений какого-либо из этих предположений по существу нет. Более того, следует поставить вопрос о том, насколько общей является взаимосвязь температуры отпуска и стойкости к растрескиванию, поскольку в случае хромистых мартенситных нержавеющих сталей подобной корреляции не обнаружено [54, 56]. [c.63]
В атмосферных условиях и в условиях повышения влажности ненагру-женные детали из мартенситных нержавеющих сталей не подвергаются заметной коррозии. Однако исследования коррозионной стойкости при повышенных температурах (образцы нагревали до 250 или 350°С, окунали в 3 %-ный раствор Na I и переносили во влажную камеру, где при 50°С выдерживали 22 ч. Затем цикл повторялся. База испытаний составляла 30 суточных циклов) с периодическим смачиванием 3 %-ным раствором Na I показали, что эти стали подвержены точечной коррозии. Общим иеж-ду исследованием выносливости сталей при повышенных температурах и периодическом их смачивании коррозионной средой, определением коррозионной стойкости без приложения к образцам внешних нагрузок при повышенных температурах и периодическом смачивании является то, что в обоих случаях металл поверхностных слоев образцов подвержен усталости вследствие резко циклического изменения температуры с большим градиентом. Определение коррозионной стойкости сталей при периодическом смачивании коррозионной средой может дать качественную картину влияния химического состава и структуры стали на ее коррозионно-механическую стойкость при повышенных температурах. [c.109]
Уменьшение предела выносливости с увеличением длины образца подтверждено также автором и Я.Л.Побережным при испытании образцов диаметром 10 мм различной длины из мартенситной нержавеющей стали 13Х12Н2ВМФ (рис. 68). Показано, что поверхностно-активная среда усилила проявление масштабного эффекта. [c.134]
Газовое контактное хромирование мартенситной нержавеющей стали 13Х12Н2ВМФ привело к образованию на поверхности образцов ферритной зоны толщиной около 0,1 мм и неравномерной карбидной зоны толщиной 0,005 мм. Вследствие увеличения концентрации хрома в слое при насыщении до такой, при которой а ->7 ->а-превращения отсутствуют, диффузионный слой состоит из о-таердого раствора хрома в железе и мелкодисперсных карбидов. Микротвердость толстой ферритной зоны равна 2300 МПа, основной структуры — 3500 МПа. [c.176]
Диффузионное хромирование снизило предел выносливости образцов из мартенситной нержавеющей стали с 640 до 230 МПа несмотря на появление в поверхностных слоях остаточных сжимающих напряжений до 600 МПа. В данном случае не подтверждается распространенное мнение об остаточных сжимающих напряжениях как основной причине повышения выносливости. При симметричном циклическом нагружении изгибом остаточные напряжения сжатия, уменьшая растягивающие напряжения, увеличивают суммарные сжимающие напряжения, что у ряда металлов, особенно мягких, уменьшает амплитуду разрушающих циклических напряжений. Усталостные трещины зарождаются в данном случае, как правило, под диффузионным слоем и при дальнейшем увеличении числа циклов нагружении распространяются в глубь основного металла и в диффузионный слой. Хромирование в 1,5 раза увеличило условный предел выносливости стали 13Х12Н2ВМФ в 3 %-ном растворе Na I. [c.176]
Ферритные и мартенситпые нержавеющие стали обладают высокой коррозионной стойкостью при определенных условиях. В статических условиях эти стали быстро корродируют и на их поверхности образуется толстый слой окислов — продуктов коррозии. Ферритные и мартенситные нержавеющие стали хорошо сопротивляются окислепию при высокой температуре и поэтому часто применяются там, где требуется стойкость против действия горячих газов. Интересно отметить, что коррозионная стойкость этих сталей в воде слегка повышается в интервале температур от 260 до 360° С очевидно, в этих условиях электрохимическая коррозия превращается в химическую газовую коррозию. [c.60]
Наряду с этим имеются данные , что коррозионная стойкость аустенитных и мартенситных нержавеющих сталей в результате азотирования уменьщается в заметной степени в таких средах, как раствор Na l. Однако в том же исследовании отмечается, что во многих средах, как, например, в атмосфере сероводорода, а также в сульфидах стойкость азотированного слоя нержавеющей стали выше, чем до азотирования. [c.118]
Одним из факторов, определяющих механизм разрушения напряженной стали (коррозионное растрескивание или статическая водородная усталость), является pH среды, окружающей стальное изделие или образец. Влияние pH 3%-ного раствора Na61 на разрушение напряженных путем изгиба (на 75% от предельной прочности) плоских образцов из мартенситной нержавеющей стали USS 12 MoV изучали X. Бат и Е. Фелпс [359]. Сталь (состав в % 0,26 С 0,56 Мп 0,026 Р 0,025 S 0,30 Si 0,75 Ni 12,36 r 0,29 V 1,02 Mo) была аустенизи-рована 15 мин при 1010°С, охлаждена, отпущена 5 мин при [c.128]
Рис, 3.14, Влияние наложения тока на время до момента разрушения образцов из мартенситной нержавеющей стали USS12 MoV в 37о-ном Na l [359] [c.129]
Состав 2 рекомендуется для травления чугуна, углеродистых и инструментальных сталей [115]. Метабисульфит калия растворяют перед травлением. Результаты травления (10—60 сек) аналогичны описанным выше. Для более глубокого травления следует повторное травление без переполировки. В процессе травления образец нужно сильно встряхнуть, чтобы на поверхности шлифа не образовалась пленка сернистого железа, растворяюшаяся в соляной кислоте. По окончании травления образец оставляют неподвижным в растворе до появления осадка, затем промывают и высушивают. С помощью состава 2 можно изучать субструктуру и линии скольжения в различных чугунах и сталях, включая мартенситные нержавеющие стали. [c.32]Мартенситная нержавеющая сталь В. 8.1630А> 130/оСг. 0.150/оС (макс.) Литье Отпуск [c.528]
Для определения склонности к коррозионному растрескиванию аустенитных нержавеющих сталей широко обследован метод испытания в кипящем растворе Mg lj И]. Мартенситные нержавеющие стали испытываются в кипящем растворе Са (N03)3 [1], в HjS + СН3СООН [2] применительно к аппаратуре нефтеперерабатывающего оборудования. Однако работ по испытаниям мартен-ситных нержавеющих сталей на склонность к коррозионному растрескиванию крайне мало. [c.117]
Аустенитно-мартенситные нержавеющие стали. Особую группу представляют аустенитно-мартенситные нержавеющие стали, например сталь Х15Н9Ю, ( 0,09% С, 14—16% Сг, 7—9% N1 и 0,7—1,3 А1). Эти стали наряду с хорошей устойчивостью против атмосферной коррозии обладают высокими механическими свойствами. Аустенитно-мартенситные стали, например Х15Н9Ю, для повышения механических свойств подвергают закалке при тe шe-ратуре 975° С (после закалки структура стали — неустойчивый аустенит и небольшое количество мартенсита) в этом состоянии [c.293]
Аустенито-мартенситные нержавеющие стали. Особую группу представляют аустенито-мартенситные нержавеющие стали, например сталь 09Х15Н8Ю ( 0,09%С 14—16% Сг 7—9% Ы1 и 0,7—1,3 А1). Эти стали наряду с хорошей устойчивостью против атмосферной коррозии обладают высокими механическими свойствами и хорошо свариваются. Сталь 09Х15Н8Ю для повышения механических свойств подвергают закалке при 975°С, после которой структура стали — неустойчивый аустенит и небольшое количество мартенсита. В этом состоянии сталь обладает достаточно высокой пластичностью и может быть подвергнута пластической деформации и обработке резанием. После закалки сталь обрабатывают холодом в интервале от —50 до —75°С для перевода части ( 40%>) аустенита в мартенсит и подвергают отпуску (старению) при 450—500°С. При старении из а-твердого раствора (мартенсита) выделяются дисперсные частицы интерметаллидов типа Ы1зА1. После такой обработки сталь обладает следующими механическими свойствами (в среднем) Ов=120 кгс/мм оо,2=95 кгс/мм и ан=4 кгс-м/см . [c.315]
mash-xxl.info
Высокопрочная нержавеющая сталь мартенситного класса
ВЫСОКОПРОЧНАЯ НЕРЖАВЕЮЩАЯ СТАЛЬ МАРТЕНСИТНОГО КЛАССА, содержащая углерод,хром,никель,марганец,молибден , кремний и железо,о т л и ч а ю щ а я с я тем, что, с целью повышения механических свойств, она дополнительно содержит азот при следующем соотношении компонентов, вес.%: Углерод0,05-0,08 Хром13-14,5 Никель4,5-5,5 Марганец0,1-1,0 Молибден2,3-2,8 Азот0,04-0,08 Кремний0,05-0,07 ЖелезоОстальное (Л
СОЮЗ СОВЕТСКИХ
СОЦИАЛИСТ ИЧЕСНИХ
РЕСПУБЛИН
119) (11) 3151) С 22 С 38 44
ОПИСАНИЕ ИЗОБРЕТЕНИЯ
К ABTOPCHOMY СВИДЕТЕЛЬСТВУ
ГОСУДАРСТВЕННЫЙ НОМИТЕТ СССР
ПО ДЕЛАМ ИЗОБРЕТЕНИЙ И ОТНРЫТИЙ (21) 2775240/22-02
f (22) 04.06.79 (46) 07.10.83. Бюл. Р 37 (72) A. В. Валтаджи, Г. Б. Строганов, P. Е. Шалин, А, Ф. Петраков, Е. Б. Качанов, Н. М. Вознесенская, A. В. Шалькевич, Г. A. Хасин, Л. Л. Савинок, Й. Ф. Хлыстов, A. Г. 6)алимов, )I. М. Осипова, В. И. Готин, С. Л. Натапов и В.В.Липец (53) 669. 15 24 26 28 74-194{088.8) (56) 1. Авторское свидетельство СССР
9 138263, кл. С 22 С 38/50, 1960.
2. Авторское свидетельство СССР
9 404393, кл. С 22 С 38/44, 1972.
3. Авторское свидетельство (ССР
9 380149, кл. С 22 С 38/50, 1971 (прототип)..(54)(57) ВЫСОКОПРОЧНАЯ НЕРЖАВЕЮЩАЯ
СТАЛЬ NAPTEHCHTHOI О КЛАССА, содержащая углерод, хром, никель, марганец,молибден,кремний и железо,о т л и ч а— ю щ а я с я тем, что, с целью повышения механических свойств, она дополнительно содержит азот при следующем соотношении компонентов, вес.Ъ:
Углерод 0,05-0,08
Хром 13-14,5
Никель 4,5-5,5
Марганец О, 1-1,0
Молибден 2,3-2,8
Азот 0,04-0,08
Кремний 0,05-0,07
Железо Остальное
1046323
Изобретение относится к изысканию высокопрочных нержавеющих сталей, обладающих хорошей свариваемостью
° и высоким сопротивлением коррозии под напряжением сварных соединений.
В настоящее время для изготовле ния высокойрочных крупногабаритных сварных деталей широко применяются высокопрочные нержавеющие стали мартцнситного класса BHC-2 (ЭП410-УШ) с прочностью 0 = 135+10 кгс/мм и 10 переходного класса ВНС-5 с прочностью
0" = 150+12 и g> = 160+10 кгс/мм .
Эти стали наряду с высокой прочностью обладают высокой пластичностью и вязкостью и способностью сваривать 15 ся в термически упрочненном состоянии без какой-либо термообработки после сварки (1)и (2).
Однако сталь ВНС-2 обладает пониженным сопротивлением коррозии под напряжением сварных соединений, сталь
BHC-5 имеет пониженную прочность сварных соединений без последующей термообработки Д = 70 кгс/мм, так как способна свариваться в упрочнен25 ном состоянии только "мягкой" аустенитной присадкой св 0,8Х20Н10Гб.
Невозможность сварки стали ВНС-5 . прочной мартенситной присадкой связана с наличием в зоне сплавления сварного соединения большого количестЗ ва остаточного аустенита, который при испытаниях при -70 С превращается в неотпущенный высокопрочный азотистый мартенсит, что приводит к хрупкому разрушению по этой зоне.
Применение аустенитной присадки св 08Х20Н10Гб позволяет исключить разрушение по зоне сплавления в связи с большой пластичностью и мень- 49 шей прочностью сварного шва, по которому и происходит разрушение образцов при испытаниях при -70 С, Наиболее близкой к изобретению 45 является нержавеющая сталь ЭП817 следующего состава, вес.Ъ: углерод
0,05-0,08; хром 13,5-15,0; никель
5, 05-6, О, медь 1, 8-2, 2) титан О, 020,15; марганец 0,1-1,0; молибден
0,8-1,6, лантан 0,01-0,1; церий 0,020,2; ниобий 0,03-0,45; кальций 0,0020,1; кремний 0,05-0,7, железо остальное. !
Сталь ЭП817 после закалки с 55
1000 С + холод — 70 С и старения при 425-450 С имеет следующие механические свойства:
100-120
55-65
120-130
60-65
Предел прочности, кгс/мм . 125-140
Предел текучести, кгс/мм
Относительное удлинение, Ъ 12-18
От нос ит ель н ое сужение, %
Ударная вязкость, кгс/см 12-16
Сталь обладает высокой корроэионной стойкостью под напряжением. Время до образования трещин под напряжением 0 = 100 кг/мм в тропической камере 2 года.
Сталь способна свариваться в термически обработанном состоянии прочной мартенситной присадкой 13).
Однако укаэанная сталь имеет недостаточный уровень прочности и предела текучести.
Целью изобретения является повышение механических свойств.
Поставленная цель достигается тем, что высокопрочная нержавеющая сталь мартенситного класса, содержащая углерод, хром, никель, марганец, молибден, кремний и железо, дополнительно содержит азот при следующем, соотношении компонентов, вес.Ъ:
Углерод 0 05-0,О8
Хром 13-14,5
Никель 4,5-5,5
Марганец 0,1-1,0
Молибден 2,3-2,8
Азот 0,04-0,08
Кремний 0 05-0,07 железо .Остальное
После закалки с 1000-1020 С,обработки холодом при -70 С в течение
2 ч и отпуска 200 С в течение 3 ч сталь имеет следующие механические свойства:
Предел прочности, кгс/мм 140-160
Предел текучести, кгс/мм
Относительное удлинение, Ъ 13-16
Относительное сужение., %
Ударная вязкость, кгс/см 12-14 сварного со- Х единения i 110 кгс/мм
Для получения сплава были выплавлены 3 плавки с различным содержанием азота от 0,04 до 0,08% и с повышенным содержанием молибдена 2,53.
Химический состав и свойства сплава представлены в таблице.
1046323 о>
IO) еc&
i oo
1 Н 4 ! ux
l Xo ! Х а-а
I Х С еoll
I Х ВЕ
i ахи
i оао !
ИВИН
3 !
I
1
I 1
I
I
I
1
1 !
1
I
3
3
3
I
3
t
1
I
I .I !
I
I
I
I
1 !
I !
1
1
Э
ВЕ о
i к
v о
Э Х юн о х Р
ЭЮ хо хо ой
Э о х о
I 1 е е
I 1
I I
I I
1 I б 1
I Х I
I Xece ! 0 I ! m IN
3VtO
l 4
3 g 3 М ! 333 3
I 1 >
1 I
I 1
1 I
3 ! !
1
1
I ! an
1 сае а-1
I
1 !
I
1
1
I мъ а, Е с
3 а-3
1 е
I an
1 Io
1 х х х
oo
Q хя) а. Яи
e VIII
СО с (V а а о аО
an с аа
I г4
I
1 о ! N .3 а-4
I
l o
I ае ! а.е
I
I
I аФ
I o
) с ! о
3 °
1 л
an ! о
I o
I В
1 ! о !
I
1 а-4
3 @0
4! Х
an а0 с Ф о е о о
И И
В а» о lA
Id н и о о
ВВ °
xv
Х Э
ВО иЪ ес о е о о а-Ф аале с а-е Ю
И eo с ао о Е
° . a o с а а
X ch
И
an
ao c аЧ ааЕ аВ .Ю и z
М с о о
М о co an с с с
О .В «Ч
an ааЪ— с@ Ф саЕ
I
1 ,1
° l
° И В
В И о, — о
z z о
z о о и о о K
ВЕ
И A
J I
I 1
I I
-о ! В3.3 ! IIl3CrO
1Н! 4
tv! x t
I mI ! O3%a
1 1
1 Э
1 Х
I Х 1
1u3%« е х е,о"
1Э!ЬЕЕ
1 ВЕ 4
I 1 Х
l I
3 !
I t
I 1 и е ц е
1 ЕеЕ I
1 1
I 1
5 — а
an ай о ann о о
° 35 с с с с с
В В В И И °
c— о î Хап л an Oo
О an а-4 О О О с с с С о е оо ч о
"В ° В В ° ° о — lO
r. е- о
I и—
В В u ta.
Х atl aar
m x
1
1
I
1
I
I
1
1
1
1
I
I
I
I !
1
1
1
1
I
I.
l
1
I
1
3
I
1
I
1
1
3
1
1
1
3
I
I
3
1
1
I
1 е
I.
aI3 I
1В 1 о х 1
o .О Ii
1 1 ф!
1
I
1046323
Составитель Л. Голубева
Редактор A. Шандор Техред И.Гайду Корректор A. Повх
Заказ 7668/26 Тираж 627 Подписное
ВНИИПИ Государственного комитета СССР по делам иэобретений и открытий
113035, Москва, Ж-35, Раушская наб., д. 4/5
Филиал ППП "Патент", r. Ужгород, ул. Проектная, 4
Предлагаемый состав стали позволяет повысить предел прочности на 10-15%,пре-, дел текучести на 10-,20% н предел прочности сварного соединения на 15-20%.




www.findpatent.ru
Дисперсионно-твердеющая мартенситная нержавеющая сталь
Изобретение относится к области металлургии, в частности к составу дисперсионно-твердеющей мартенситовой нержавеющей стали с высокой прочностью в сочетании с пластичностью. Сталь содержит компоненты при следующем соотношении, мас.%: 10 - 14 хром, 7 - 11 никель, 0,5 - 6 молибден, до 9 кобальт, 0,5 - 4 медь, 0,4 - 1,4 - титан, 0,05 - 0,6 алюминий, не более 0,05 углерода и азота, любой элемент периодической системы не более 0,5, железо - остальное. 4 з.п. ф-лы, 7 табл.
Данное изобретение относится к дисперсионно-твердеющим мартенситовым хромо-никелевым нержавеющим сталям, особенно к таким, которые твердеют при простой термической обработке.
В частности, оно относится к мартенситовым хромо-никелевым нержавеющим сталям, которые твердеют при простой термической обработке при сравнительно низкой температуре. Одной из целей данного изобретения является создание мартенситовой хромо-никелевой нержавеющей стали, которая проявляет хорошие свойства не только на заводе, например в процессе прокатки и вытягивания, но также в виде готового проката и изделий, таких как полосы и проволока, легко поддается различным операциям формования и изготовления изделий, например, выпрямлению, резке, механической обработке, штамповке, нанесению резьбы, намотке, крутке, изгибу и т.д. Другой целью изобретения является создание мартенситовой хромоникелевой нержавеющей стали, которая не только в канатном или вытянутом состоянии, но также в отвердевшем и упрочненном состоянии обладает очень хорошей пластичностью и жесткостью. Еще одной целью данного изобретения является создание мартенситовой хромо-никелевой нержавеющей стали, которая наряду с комбинацией очень высокой прочности и хорошей пластичности обладает способностью к формованию и изготовлению изделий, таких как пружины, зажимы, хирургические иглы, зубоврачебные и другие медицинские инструменты и т.п. Другие цели изобретения будут от части очевидны и отчасти указаны в нижеследующем описании. В настоящее время многие типы сплавов используются для изготовления вышеупомянутых изделий. Некоторые из этих сплавов являются мартенситовыми нержавеющими сталями, аустенитовыми нержавеющими сталями, нелегированными углеродистыми сталями и дисперсионно- твердеющими нержавеющими сталями. Все эти сплавы обладают хорошей комбинацией корозионной стойкости, прочности, формуемости и пластичности, но каждый из них имеет недостатки и не отвечает требованиям сегодняшнего дня и будущего, предъявляемым к сплавам, используемым для изготовления вышеупомянутых изделий. Эти требования заключаются в лучших свойствах материала, требуемых как для конечного потребителя сплава, например, большей прочности в сочетании с хорошей пластичностью и коррозионной стойкостью, так и для производителя полуфабрикатов, таких как полосы и проволока, и конечных изделий, упомянутых выше, то есть в свойствах, таких как, например, улучшенная способность к формованию и изготовлению изделий, заключающаяся в том, что уменьшается число операций и используется стандартное оборудование, что приводит к уменьшению стоимости продукции и к сокращению времени ее производства. Мартенситовые нержавеющие стали, например AlsI 420- grades, обладают прочностью, но не в сочетании с пластичностью. Аустенитовые нержавеющие стали, например, AlsI 300- series обладают хорошей коррозионной стойкостью в сочетании с высокой прочностью и приемлемой для некоторых целей пластичностью, но для достижения высокой прочности требуется холодное восстановление и это означает, что и полуфабрикат должен иметь очень высокую прочность, что далее означает плохую формуемость. Нелегированные углеродистые стали обладают низкой коррозионной стойкостью, что, безусловно, является большим недостатком, если требуется коррозионная стойкость. Последний тип дисперсионно- твердеющие нержавеющие стали, бывают различных сортов, обладающих различными свойствами. Однако они все имеют общие свойства, например, большинство из них плавятся в вакууме при одностадийном или более обычно при двухстадийном процессе, когда вторая стадия представляет собой переплавку в условиях вакуум-давление. Далее, требуется большое количество образующих дисперсию элементов, таких как алюминий, ниобий, тантал и титан или часть комбинация этих элементов. Термин "большое количество" означает > 1,5% Большое количество способствует повышению прочности, но уменьшает пластичность и формуемость. Один специфический сорт, который используется для изготовления вышеупомянутых изделий, на который дается ссылка в данном описании, описан в пат. США 3408178. Этот сорт обладает приемлемой пластичностью в виде конечного продукта, но в сочетании с прочностью только около 2000 H/мм2. Сталь также обладает некоторыми недостатками в процессе изготовления полуфабрикатов, например, подвержена растрескиванию в отожженном состоянии. Целью изобретения потому было создание сорта стали, который превосходит сорт, описанные выше. Он не требует вакуумной плавки или вакуумной переплавки, но, конечно, это может быть сделано для достижения даже лучших свойств. Он также не требует большого количества алюминия, ниобия, титана или тантала или их комбинацией, и все же обладает хорошей коррозионной стойкостью, хорошей пластичностью, хорошей формуемостью и, в комбинации со всеми этими свойствами, очень высокой прочностью, до 2500 3000 H/мм2 или выше, в зависимости от требуемой пластичности. Следовательно, цель данного изобретения заключается в создании стали, которая отвечает требованиям хорошей коррозионной стойкости, высокой прочности у конечного изделия и хорошей пластичностью как в процессе изготовления, так и в виде конечного изделия. Полученная сталь может быть использована в виде проволоки, трубок, брусков и полос для изготовления зубоврачебного и медицинского оборудования, пружин и зажимов. Требование коррозионной стойкости обеспечивается добавками









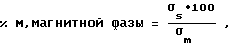



Формула изобретения
1. Дисперсионно-твердеющая мартенситная нержавеющая сталь, содержащая хром, никель, медь, алюминий, титан, углерод, азот, железо, отличающаяся тем, что она дополнительно содержит молибден, кобальт, любой элемент Периодической системы при следующем соотношении компонентов, мас. Хром 10 14 Никель 7 11 Молибден 0,5 6 Кобальт До 9 Медь 0,5 4,0 Алюминий 0,05 0,6 Титан 0,4 1,4 Углерод и азот Не более 0,05 Любой элемент Периодической системы Не более 0,5 Железо Остальное 2. Сталь по п.1, отличающаяся тем, что она содержит кобальт до 6. 3. Сталь по п. 1 или 2, отличающаяся тем, что она содержит медь 0,5 - 3,0. 4. Сталь по любому из пп.1 3, отличающаяся тем, что она содержит молибден 0,5 4,5. 5. Сталь по любому из пп. 1 4, отличающаяся тем, что она содержит медь 0,5 2,5.РИСУНКИ
Рисунок 1, Рисунок 2, Рисунок 3, Рисунок 4, Рисунок 5, Рисунок 6PC4A - Регистрация договора об уступке патента Российской Федерации на изобретение
Прежний патентообладатель:САНДВИК АБ (SE)
(73) Патентообладатель:Сандвик Интеллекчуал Проперти ХБ (SE)
Договор № РД0008307 зарегистрирован 20.04.2006
Извещение опубликовано: 10.06.2006 БИ: 16/2006
www.findpatent.ru
Нержавеющая мартенситная сталь для форм и каркасов форм для литья под давлением
Изобретение относится к области металлургии, а именно к составу мартенситной нержавеющей стали, используемой для изготовления элементов форм или каркасов форм для литья пластмасс под давлением. Сталь содержит элементы при следующем соотношении, мас.%: углерод (С) 0,02-0,09, азот (N) 0,025-0,12, кремний (Si)≤0,25, алюминий (Al)≤0,080, марганец (Mn) 0,55-1,8, хром (Cr) 11,5-16, медь (Сu) до 0,48, в сумме молибден (Мо) и половина вольфрама (W/2) до 0,90, никель (Ni) до 0,90, ванадий (V) до 0,090, ниобий (Nb) до 0,090, титан (Ti) до 0,025, сера (S) до 0,25, железо и образовавшиеся при плавке примеси остальное. Состав стали удовлетворяет условиям 0,05≤C+N≤0,17, Si+23Al≥0,20, Si+0,6Al≤0,25, 0,00025≤Al×N≤0,0020, 6,5≤F=(Cr+Mo)+2(Si+V+Nb)-27(C+N)-(Ni+Mn/2+Сu/3)≤13. Сталь обладает повышенной обрабатываемостью, свариваемостью, коррозионной стойкостью и теплопроводностью. 3 з.п. ф-лы, 1 табл.
Настоящее изобретение относится к нержавеющей мартенситной стали для изготовления форм и каркасов форм для литья полимерных материалов под давлением.
Для литья полимерных материалов под давлением требуются формы и каркасы форм, выполненные из стали с высокой механической прочностью, способной противостоять значительным усилиям при высоких давлениях впрыска. Изготовление форм и каркасов форм сопряжено с многочисленными и длительными операциями по обработке, такими как фрезерование и сверление, для которых требуется хорошая обрабатываемость стали. Кроме того, поскольку формы и каркасы форм предназначены не только для придания отливаемым изделиям соответствующей геометрии, но и для их охлаждения, то сталь, из которой они изготовлены, должна обладать предпочтительно высокой теплопроводностью для облегченного теплоотвода благодаря проводимости конструкции формы. Наконец, формы должны обладать стойкостью против коррозии, которая может вызываться либо нагнетаемыми коррозионными полимерными материалами, либо охлаждающими жидкостями в охлаждающих контурах, либо атмосферным окислением шлифованных полостей литьевых частей формы.
Для соблюдения комплекса этих требований предпринимаются попытки использовать высокопрочные стали, которые являются также нержавеющими. С этой точки зрения ведется поиск нержавеющих сталей мартенситного типа, в частности нержавеющих сталей мартенситного типа из серии AISI 420-440, или сталей, сопоставимых с ними.
Однако такие нержавеющие мартенситные стали имеют относительно высокое содержание углерода, порядка 0,10-0,5% и даже более, и обладают недостатком, проявляющимся в недостаточно высокой коррозионной стойкости и, главным образом, в низкой обрабатываемости. Кроме того, слишком высокое содержание углерода ухудшает способность к сварке, являющейся важным свойством для элементов формы, в частности, при ремонте этих деталей сваркой в том случае, когда требуется их обработка для восстановления.
Для устранения отмеченных недостатков была предложена, в частности, в патенте США №6,358,334 нержавеющая мартенситная сталь для изготовления форм для литья пластмассы под давлением, в которой содержание углерода не превышает 0,08% и которая содержит значительную добавку серы в количестве 0,06-0,3% для улучшения обрабатываемости. Эта сталь, содержащая в основном 12-14% хрома, 0,03-0,06% углерода, 1-1,6% марганца, 0,25-1% кремния, 0,01-0,1% ванадия, 0,02-0,08% азота, содержит также добавку меди в количестве 0,5-1,3% для повышения своей теплопроводности. Однако эта сталь, свойства которой более пригодны для изготовления элементов для форм или каркасов форм, чем нержавеющие мартенситные стали из серии AISI 420-440, и твердость которой составляет около 300 НВ, обладает двойным недостатком. С одной стороны, она с трудом подвергается деформации горячей прокаткой, так как ее ковкость в горячем состоянии не является очень высокой. С другой стороны, ее сложно повторно использовать, так как содержание меди в ней значительно превышает среднее содержание меди в отходах из нержавеющей стали.
Цель настоящего изобретения состоит в устранении приведенных недостатков, для чего предлагается нержавеющая сталь с высокими свойствами, пригодная для изготовления форм или каркасов форм для литья пластмассы под давлением, которая одновременно легко обрабатывается, легко сваривается, обладает высокой коррозионной стойкостью и высокой теплопроводностью и не вызывает больших проблем при изготовлении, в частности проблем, связанных с ковкостью и повторным использованием.
Поэтому предметом изобретения является элемент формы или каркаса формы для литья полимерных материалов под давлением, выполненный из нержавеющей мартенситной стали, состав которой включает в себя, мас.%:
0,02%≤С≤0,09%,
0,025%≤N≤0,12%,
при 0,05≤C+N≤0,17%,
Si≤0,34%,
Al≤0,080%
при Si+23Al≥0,20%,
Si+0,6Al≤0,25%,
и 0,00025≤Al×N≤0,0020,
0,55%≤Mn≤1,8%,
11,5%≤Сr≤16%,
при необходимости до 0,48% меди, до 0,90% от суммы Мо+W/2, до 0,90% никеля, до 0,090% ванадия, до 0,090% ниобия, до 0,025% титана, при необходимости до 0,25% серы,
остальное - железо и примеси, образовавшиеся при плавке, при этом состав кроме того удовлетворяет условию:
6,5≤F=(Cr+Мо)+2(Si+V+Nb)-27(С+N)-(Ni+Mn/2+Cu/3)≤13.
Предпочтительно, чтобы состав нержавеющей мартенситной стали удовлетворял одному или нескольким следующим условиям:
Si+0,6Al<0,25%,
Сu≤0,4%,
Al×N≥0,00050.
Предпочтительно, чтобы состав нержавеющей мартенситной стали удовлетворял по меньшей мере одному из следующих условий:
Ni≥0,10%,
V≥0,015%,
Mo+W/2≥0,10%.
Содержание нержавеющей мартенситной стали может удовлетворять следующему условию:
7,0≤F≤8,9
в том случае, когда требуется очень высокая способность к шлифованию, или удовлетворять условию:
9,0≤F≤11,5
в остальных случаях.
Элемент формы или каркаса формы для литья пластмассы под давлением выполнен из нержавеющей мартенситной стали согласно изобретению после ее закалки и отпуска.
Предпочтительно, чтобы структура стали для изготовления этого элемента содержала менее 20% феррита δ, остальное - мартенсит. Еще более предпочтительно, чтобы структура стали содержала менее 10% феррита δ, остальное - мартенсит.
Ниже изобретение подробнее поясняется с помощью примеров, не являющихся ограничительными.
Неожиданно авторы изобретения установили, что в нержавеющих мартенситных сталях положительное влияние на теплопроводность вместо меди может быть достигнуто добавкой значительно меньшего количества кремния, а положительного влияния на коррозионную стойкость можно достигнуть увеличением содержания молибдена или азота.
На основе этих наблюдений авторы заключили, что можно получить нержавеющую мартенситную сталь с удовлетворительными свойствами для изготовления элементов формы, а также с высокой ковкостью при существенном снижении содержания меди и кремния и при добавке, в случае необходимости, молибдена или азота или комбинации этих элементов.
С учетом этих наблюдений сталь согласно изобретению представляет собой нержавеющую сталь мартенситного типа, в состав которой входят следующие элементы:
- более 0,02 маc.%, предпочтительно более 0,03 маc.% углерода для повышения дисперсионного твердения, не более 0,09 мас.%, предпочтительно не более 0,06 маc.%, предпочтительно не более 0,05 маc.% углерода для предупреждения снижения коррозионной стойкости;
- не менее 0,025 маc.%, предпочтительно не менее 0,035 маc.% азота для повышения механической прочности стали и ее коррозионной стойкости, но менее 0,12 маc.%, предпочтительно менее 0,10 маc.%, даже менее 0,075 маc.% азота для снижения способности образовывать нежелательные нитриды хрома; эти нитриды хрома вызывают охрупчивание и способствуют снижению содержания свободного хрома, что неблагоприятно сказывается на коррозионной стойкости;
- содержание углерода и азота задается таким, чтобы в указанных пределах суммарное содержание углерода и азота превысило или было равно 0,05 маc.%, предпочтительно превысило или было равно 0,07 маc.% для обеспечения достаточного воздействия на дисперсионное твердение при отпуске в результате образования карбидов и нитридов, однако суммарное содержание углерода и азота не должно превышать предпочтительно 0,17 маc.%, более предпочтительно 0,14 маc.%, еще более предпочтительно 0,11 маc.%, с тем чтобы исключить дисперсионное твердение, являющееся чрезмерным при данном назначении, и предупредить слишком значительное снижение вязкости и коррозионной стойкости локальным уменьшением содержания хрома, частично зафиксированного в виде карбонитридов.
С целью улучшения обрабатываемости, в частности способности к фрезерованию и сверлению, может вноситься добавка серы, в частности, в том случае, когда не требуется высокого качества поверхности (качество шлифования или механически очищенные поверхности), а именно в том случае, когда сталь предназначена для изготовления из нее каркасов форм или полостей для литья пластмассы, к внешнему виду которой не предъявляют строгих требований. В этом случае содержание серы должно составлять преимущественно не менее 0,05%, предпочтительно не менее 0,075%, еще более предпочтительно не менее 0,10%. Однако максимальные показатели содержания должны составлять менее 0,25%, предпочтительно 0,20%, более предпочтительно 0,15% для предупреждения снижения ковкости стали, ее коррозионной стойкости и вязкости.
Кремний и алюминий способствуют хорошему раскислению ванны жидкой стали, и с этой точки зрения их присутствие является необходимым. В частности, необходимо, чтобы содержание кремния и алюминия было таким, чтобы Si+23×Аl≥0,20%, предпочтительно ≥0,35%. Однако авторы изобретения обнаружили, что максимально возможное снижение содержания кремния и, в меньшей степени, содержания алюминия позволяет частично, но очень эффективно, компенсировать очень неблагоприятное воздействие большого содержания хрома на теплопроводность стали. Однако такая низкая теплопроводность сталей с высоким содержанием хрома является особенно неблагоприятной при использовании их для изготовления форм для литья пластмассы под давлением, в которых эффективный теплоотвод для обеспечения быстрого затвердевания изделий из нагнетаемой пластмассы представляет собой одно из важных эксплуатационных свойств.
Для достижения хорошей теплопроводности необходимо, следовательно, чтобы содержание кремния и алюминия составляло: Si+0,6×Al≤0,25%, предпочтительно ≤0,17%.
Кроме того, для обеспечения удовлетворительной способности к прокатке или ковке, т.е. для достижения достаточно широкого диапазона температуры для горячей деформации, позволяющего, как правило, прокатку за один нагрев, без промежуточного подогрева, содержание алюминия и азота должно составлять: Al≤0,0020/N, предпочтительно ≤0,0010/N. Кроме того, для обеспечения контроля за ростом зерен с целью ограничения их размера во время термообработки и таким образом для достижения удовлетворительного размера зерен после обработки для получения необходимого качества содержание алюминия и азота должно составлять: Al≥0,00025/N, предпочтительно ≥0,00050/N.
Присутствие марганца особо желательно для связывания серы в виде сульфидов марганца для ограничения неблагоприятного воздействия серы на охрупчивание стали. По этой причине содержание марганца должно составлять преимущественно: Мn≥0,3%+5×S.
Кроме того, при содержании марганца возрастает закаливаемость и снижается содержание ферритов по существу в мартенситной структуре, образовавшейся после закалки.
По этой причине содержание марганца должно превышать или быть равным 0,55%, предпочтительно превышать или быть равным 0,75%, еще более предпочтительно превышать или быть равным 1,05%. Однако в том случае, когда содержание марганца слишком высокое, то оно неблагоприятно влияет на вязкость стали. Поэтому содержание марганца должно составлять менее или быть равным 1,8%, предпочтительно менее или быть равным 1,6%.
Содержание хрома, обеспечивающего стойкость к коррозии, должно превышать или быть равным 11,5%, предпочтительно превышать или быть равным 12%. Однако для ограничения в полученных после закалки структурах содержания феррита δ, являющегося снижающим твердость компонентом, содержание хрома должно составлять менее или быть равным 16%, предпочтительно менее или быть равным 15%, более предпочтительно менее или быть равным 14% и еще более предпочтительно менее или быть равным 13%.
Содержание меди составляет менее или равно 0,48%, предпочтительно менее или равно 0,4%, оно может быть также настолько малым, насколько это требуется для предупреждения снижения способности к горячей деформации и для получения отходов, которые могли бы более легко повторно использоваться.
Как уже указывалось выше, хотя медь и оказывает благоприятное воздействие на коррозионную стойкость и на содержание феррита дельта, однако авторами изобретения установлено, что возможно сохранить и даже увеличить преимущества, обеспечиваемые высоким содержанием меди, в частности, добавкой молибдена и максимальным снижением содержаний кремния.
Однако медь часто присутствует в остаточном количестве в скрапе, так что для снижения расходов, связанных с сортировкой скрапа, необходимой для получения очень низкого содержания меди, можно ограничиться содержанием меди в скрапе, составляющим более 0,1%, даже более 0,2% и даже более 0,31%, предпочтительно более 0,35%.
Молибден обеспечивает преимущество, заключающееся в повышении закаливаемости, что способствует получению мартенситной микроструктуры, необходимой для достижения оптимального компромисса между прочностью на растяжение и вязкостью.
Данный элемент существенно способствует также повышению стойкости против понижения твердости после отпуска. Наконец он значительно повышает коррозионную стойкость. Однако этот элемент является очень дорогим и способствует образованию феррита δ. Поэтому его максимальное содержание не должно превышать 0,90%, предпочтительно 0,48%, более предпочтительно 0,35%. Присутствие данного элемента не является необходимым и его минимальное содержание может составлять 0% или следы. Однако предпочтительно, чтобы минимальное содержание молибдена составляло не менее 0,10%, предпочтительно не менее 0,20%, более предпочтительно 0,30%.
При необходимости молибден может быть заменен вольфрамом из расчета 2% вольфрама на 1% молибдена. Однако не желательно заменять молибден вольфрамом, в частности, в связи с тем, что его стоимость чрезвычайно высока.
Также может вводиться и кобальт, оказывающий схожее воздействие. Однако это нежелательно, поэтому содержание данного элемента предпочтительно поддерживать на уровне менее или равном 0,010%, т.е. этот элемент присутствует в виде следов или примеси.
Никель оказывает благоприятное воздействие на вязкость стали. С другой же стороны, он является аустенитообразующим элементом, позволяющим компенсировать влияние образующих альфа-фазу элементов, добавляемых для увеличения коррозионной стойкости. Следовательно, данный элемент может добавляться, но его присутствие не является необходимым. Минимальное содержание никеля может составлять 0% или следы, однако предпочтительно, чтобы его содержание было более или равно 0,10%, предпочтительно более или равно 0,20%. Однако его высокая стоимость не позволяет применять его при содержании свыше 0,95%. Предпочтительно, чтобы содержание никеля составляло менее или было равно 0,48%.
Ванадий может присутствовать в остаточном количестве. В связи с содержанием хрома в стали при плавке традиционным способом в электропечи могут образовываться остаточные содержания в количестве до около 0,05%, при этом не гарантируется контрольная минимальная величина. Тем не менее ванадий может применяться, в случае необходимости, в качестве контрольной добавки для дисперсионного твердения при отпуске, при этом его минимальное содержание составляет 0,015%. Однако ввиду, в частности, его стоимости и неблагоприятного воздействия на обрабатываемость стали, желательно, чтобы содержание ванадия не превышало 0,090%.
Ниобий оказывает влияние, аналогичное влиянию ванадия, и, следовательно, его содержание не должно превышать 0,090%. Кроме того, данный элемент оказывает неблагоприятное воздействие на ковкость. По этой причине желательно, чтобы его содержание было менее 0,020%, предпочтительно менее 0,010%, еще более предпочтительно только в виде следов.
Хотя присутствие титана нежелательно из-за твердости нитридов или карбидов титана, способных существенно снизить обрабатываемость, однако этот элемент может вводиться факультативно для контроля за ростом зерен во время термообработок. В этом случае содержание титана не должно превышать 0,025%, предпочтительно, чтобы оно составляло 0,010 - 0,020%.
Кроме того, для обеспечения малого размера нитридов титана, составляющего, в частности, менее около 1 мкм, весьма желательно, чтобы добавка титана в ванну жидкой стали производилась в момент выплавки постепенно через шлак и при очень медленном введении при контакте металла с нитридом.
Остаток содержания приходится на железо и примеси.
Помимо описанных условий, касающихся содержания каждого из элементов, необходимо указать, что состав следует задавать с возможностью ограничения содержания феррита δ, который не способен превращаться в мартенсит и наличие которого вредно влияет на шлифуемость, прочность и коррозионную стойкость. В частности, желательно, чтобы количество феррита δ составляло менее или было равно 20%, предпочтительно менее или равно 10%, главным образом при мартенситной структуре.
Для этого состав должен удовлетворять следующему условию:
6,5≤F≤13,
предпочтительно 7,0≤F≤11,5,
при этом F=(Сr+Мо)+2(Si+V+Nb)-27(С+N)-(Ni+Mn/2+Cu/3).
В этих пределах можно выделить две подобласти. С одной стороны, подобласть, соответствующую F от 7,0 до 8,9 и являющуюся более благоприятной для обеспечения высокой однородности металла и высокой шлифуемости, и, с другой стороны, подобласть, соответствующую F от 9,0 до 11,5. Оптимальным компромиссом является величина 8,5 или значение F, которое меньше или равно 10,5.
Как правило, данная сталь выплавляется с помощью известных способов, например, в электропечи. При необходимости добавки титана его вводят в шлак, обеспечивая при этом попадание титана в ванну жидкой стали в результате контакта металла со шлаком, при этом сталь отливается в виде слябов или чушек, деформируемых в горячем состоянии либо прокаткой, либо ковкой. Затем проводится термообработка аустенизацией при температуре около 950°С с последующим охлаждением для превращения аустенита в мартенсит (охлаждение может быть простым охлаждением на воздухе при толщинах менее около 100 мм или применяться любое другое средство закалки), а также отпуском при температуре предпочтительно от 500 до 550°С для получения твердости от 250 до 400 НВ или, как правило, около 300 НВ. После этого изготавливают элементы для формы или каркаса формы.
В качестве примера можно указать на получение сталей, химический состав которых приведен в таблице.
В этой таблице также указаны процентное содержание феррита δ, твердость по Бринеллю после термообработки в виде отпуска при 520°С, теплопроводность стали и показатель склонности к коррозии, равный:
Cr+3,3 Мо+Сu+30 N.
Сталь, приведенная в первой строке таблицы, представляет собой сталь для сравнения, известную из уровня техники, остальные же стали являются сталями согласно изобретению.
Как можно заключить на основании таблицы, содержание феррита δ постоянно сохраняется менее 20% и составляет, как правило, величину в районе 10%, что аналогично стали из уровня техники. Твердость стали по Бринеллю изменяется от 295 до 350 НВ, показатель коррозионной стойкости изменяется от 14,5 до 18,2, этот показатель существенно превышает показатель коррозионной стойкости сравниваемой стали. Наконец теплопроводность изменяется от 22,8 до 26,1 Вт/м·°С, что в любом случае превышает, даже существенно, теплопроводность сравниваемой стали. Кроме того, сталь согласно изобретению способна легко подвергаться деформации в горячем состоянии, при этом ковкость постоянно сохраняется весьма удовлетворительной. Следует отметить, что содержание меди, которое сохраняется менее или равным 0,43%, приближается к содержанию, типичному для скрапа, что позволяет без труда вторично использовать отходы стали согласно изобретению.
1. Элемент формы или каркаса формы для литья пластических масс под давлением, выполненный из нержавеющей мартенситной закаленной и отпущенной стали следующего состава, мас.%:0,02≤С≤0,090,025≤N≤0,12при 0,05≤C+N≤0,17Si≤0,25Al≤0,080при Si+23Al≥0,20и Si+0,6Аl≤0,25и 0,00025≤Al×N≤0,00200,55≤Mn≤1,811,5≤Сr≤16Сu до 0,48Мо+W/2 до 0,90Ni до 0,90V до 0,090Nb до 0,090Ti до 0,025S до 0,25железо и примеси, образовавшиеся при плавке - остальное, при этом состав удовлетворяет условию:6,5≤F=(Сr+Мо)+2(Si+V+Nb)-27(С+N)-(Ni+Mn/2+Cu/3)≤13.
2. Элемент по п.1, отличающийся тем, что он выполнен из стали, химический состав которой удовлетворяет по меньшей мере одному из следующих условий:Сu≤0,4%,Al×N≥0,00050,Ni≥0,10%,V≥0,015%,Mo+W/2≥0,10%,Nb<0,020%,C+N≤0,14%,в структуре стали содержится менее 20% феррита δ, остальное - мартенсит, преимущественно менее 10% феррита δ, остальное - мартенсит.
3. Элемент по любому из пп.1 и 2, отличающийся тем, что он выполнен из стали, химический состав которой удовлетворяет условию:7,0≤F≤8,9.
4. Элемент по любому из пп.1 и 2, отличающийся тем, что он выполнен из стали, химический состав которой удовлетворяет условию:9,0≤F≤11,5.
www.findpatent.ru
Стали нержавеющие мартенситные - Энциклопедия по машиностроению XXL
Механические свойства нержавеющих сталей аустенито-мартенситного класса [c.495]По составу нержавеющие стали делятся на хромистые и хромоникелевые. Кроме основных элементов (углерода, хрома, никеля) нержавеющие стали могут быть дополнительно легированы молибденом, титаном, ниобием, медью, кремнием, которые вводят для повышения коррозионной стойкости, механических и технологических свойств стали. Нержавеющие стали бывают нескольких структурных классов ферритного, ферритно-мартенситного, мартенситного, аустенит- [c.31]
При высоких температурах (200—700 °С) и давлении до 20 МПа высокой коррозионной стойкостью обладают нержавеющие стали аустенитного, мартенситного и ферритного классов, а также ряд сплавов на основе никеля (табл. 18.1, рис. 18.1, 18.2). [c.274]Хромистые жаропрочные и нержавеющие стали феррито-мартенситного класса на базе 12% хрома применяются в сварных конструкциях лопаточного аппарата, рабочих колес центробежных машин и других узлах турбин, работающих в широком диапазоне температур от комнатной до 600°. В табл. 3 приведены наиболее распространенные стали этого класса с указанием областей и температуры применения. [c.30]
Ротор турбины цельнокованый, диаметром 860 мм и изготовлен из нержавеющей мартенситной стали следующего состава в % С — 0,24 8Юавоздушное охлаждение. На направляющих лопатках установлены бандажи, а на роторе — уплотнительные пластинки, благодаря которым между ротором и бандажом создается лабиринтовое уплотнение. В направляющих лопатках первых двух ступеней имеются продольные сверления, через которые охлаждающий воздух поступает в лабиринтовые уплотнения в таком количестве, что выходит из них как в направлении потока, так и против него. Таким образом, охлаждающий воздух непосредственно омывает основания рабочих лопаток. При этом полностью устраняется контакт между горячим газом и ротором вплоть до второй ступени. Температура на поверхности ротора не превышает 500° С. Первые две ступени турбины активные, а четыре последние — реактивные. Максимальная температура ротора в зоне третьей ступени примерно на 200° С ниже максимальной температуры газа. Только лопатки двух первых ступеней изготовляются из аустенитной стали, на других же ступенях — из хромистой стали с содержанием 13% Сг. [c.85]
К сталям переходного класса, в которых после высокотемпературной закалки образуется аустенит, а их упрочнение достигается отпуском с последующим старением или обработкой холодом с последующим старением, примыкают нержавеющие стали, имеющие мартенситную структуру после проведения высокотемпературного нагрева с последующим охлаждением. Эти стали подвержены дополнительному упрочнению после старения благодаря дальнейшему образованию мартенсита или выделению упрочняющих фаз. Температура мартенситного превращения таких сталей должна быть выше комнатной, так как это позволяет получать повышенные прочностные свойства уже при закалке вследствие протекания мартенситного превращения. Для обеспечения определённой степени мартенситного превращения при закалке нержавеющие мартенситные стали выплавляют с низким содержанием С, а иногда вводят в них Nb или Ti, которые способны связывать С в карбиды. [c.47]
Стали мартенситного класса — высоколегированные стали, которые при закалке, как и при нормализации, дают мартенситную структуру, а при полном отжиге марганцовистые и никелевые стали — структуру из мартенсита и троостита закалки. Поэтому они не поддаются обработке обычным режущим инструментом и имеют редкое применение, хромистые же нержавеющие стали с мартенситной структурой применяются для ножей, а после отжига [c.324]
Г у л я е в А. П. и Макаров В. М. Мартенситное превращение, механические свойства и структура нержавеющих сталей аустенитно-мартенситного класса. Металловедение и термическая обработка металлов , 1960, № 8. [c.325]
БЕЗУГЛЕРОДИСТЫЕ НЕРЖАВЕЮЩИЕ МАРТЕНСИТНО-СТАРЕЮЩИЕ СТАЛИ [c.160]
Установлено также, что хорошая вязкость при значительной прочности может быть получена на нержавеющих мартенситно-стареющих сталях, содержащих максимально возможное (около 9—10%) количество никеля. [c.162]
Влияние содержания никеля и углерода на механические свойства нержавеющей мартенситно-стареющей стали [120] [c.162]
Высокая пластичность и вязкость безуглеродистых нержавеющих мартенситно-стареющих сталей в закаленном состоянии сохраняется при криогенных температурах, несмотря на отсутствие в структуре остаточного [c.164]
Почти полное отсутствие углерода в интенсивно стареющих нержавеющих сталях обеспечивает им еще два важных преимущества над малоуглеродистыми нержавеющими сталям и мартенситного и переходного классов высокую коррозионную стойкость (общую и коррозию под напряжением) основного металла и сварных швов без последующей закалки после сварки, а также нечувствительность к охрупчиванию при медленном охлаждении в процессе пайки. [c.167]
К этому классу относятся стали, имеющие температуру начала мартенситного превращения при 20—60°С. С увеличением содержания в нержавеющих сталях практически всех легирующих элементов, кроме алюминия и титана (поскольку последний образует нерастворимые при аустенитизации карбонитриды), температура мартенситного превращения понижается и сталь из мартенситного класса переходит в аустенитный. При этом резко падает предел текучести и возрастает пластичность и вязкость стали. Стали переходного класса, лежащего между мартенситным и аустенитным, в зависимости от термической обработки, обладают свойствами, близкими к свойствам сталей аустенитного или мартенситного классов [123]. [c.167]
Важнейшим преимуществом сталей переходного класса перед мартенситными является возможность легирования их большим количеством хрома с целью увеличения коррозионной стойкости. Как правило, увеличение содержания хрома в нержавеющих сталях лимитируется образованием в структуре б-феррита, который понижает пластичность и вязкость стали, а также ухудшает способность ее к горячей деформации. Увеличением содержания никеля или других аустенитообразующих элементов б-феррит можно устранить, однако повышение содержания хрома, никеля и других элементов понижает температуру мартенситного превращения, что приводит к выходу стали из мартенситного класса. [c.169]
Нержавеющие мартенситные стали Электрошлаковы дуговой переплав Кольца, шарики, ролики 0,020 0,030 1 1 1.5 1,5 1,5 1,0 2,0 ЧМТУ 1279-65 [c.210]
Выявлена большая группа металлов, которые обладают высокой коррозионной стойкостью в высокотемпературной зоне. К ним относятся высоколегированные нержавеющие стали аустенитного, мартенситного и ферритного классов, а также ряд сплавов на основе никеля (табл. 2.1) [5, 6]. [c.54]
При кислородно-флюсовой резке максимальная глубина слоя с измененным химическим составом не превышает 0,3 мм. Глубина зоны термического влияния [49] в сталях с аустенитной структурой достигает 1— 1,1 мм, в сталях с мартенситной структурой— 1,1— 1,2 мм. В обоих случаях у поверхности реза на глубине 0,1—0,7 мм образуется участок литого металла с дендритным строением. После резки слой металла, обедненного легирующими эле.ментами, целесообразно удалить шлифованием на глубину 0,5 мм. В то же время результаты испытания образцов сварных соединений, выполненных по кромкам, полученным после резки без последующей механической обработки, свидетельствуют о возможности использования кислородно-флюсовой резки без последующей обработки для подготовки кромок нержавеющей стали под сварку. [c.140]
Ниобий широко используют как легирующий элемент для хромоннкелевых нержавеющих сталей, а также хромистых, хромо-марганцевых и др. Ниобий предохраняет сталь от воздушной закалки с образованием хрупкой мартенситной структуры, увеличивает вязкость, свариваемость, тягучесть, жаропрочность сталей. Нержавеющие стали, содержащие обычно более 1,5% КЬ, используют для изготовления реактивных двигателей, деталей самолетов, газовых турбин. [c.403]
Вспучивание ферритных нержавеющих сталей наблюдалось, когда они были катодно защищены в морской воде. Вероятно, это происходило вследствие того, что были применены защитные плотности тока выше минимальной величины, необходимой для полной защиты. Если при контакте активных металлов с мартенситными нержавеющими сталями образуются гальванические пары, то нержавеющая сталь (катод) может разрушиться вследствие выделения на ней водорода. Такие разрушения наблюдались при лабораторных испытаниях [25]. Наблюдалось самопроизвольное растрескивание винтов из нержавеющей мартенситной стали вскоре после того, как они находились в контакте с алюминием в атмосфере морского побережья. Пропеллеры из упрочненной мартенситной нержавеющей стали, соприкасающиеся со стальным корпусом корабля, вскоре после пуска в эксплуатацию подверглись коррозионному растрескиванию. Сильно наклепанная аустенитная нержавеющая сталь 18-8 также может разрушаться в условиях, описанных для мартенситных сталей [26, 27]. В данном случае сульфиды ускоряют разрушение, и так как сплав при холодной обработке претерпевает фазовое превращение и образуется феррит, то наблюдаемый эффект может служить также примером водородного растрескивания. [c.260]
В зависимости от структуры различают три основных класса нержавеющих сталей. Каждый класс включает ряд сплавов, которые несколько различаются по составу, но обладают сходными физическими, магнитными и коррозионными свойствами. Здесь приводятся обозначения сталей в соответствии с классификацией Американского института железа и стали (AISI), которую часто используют на практике. Перечень основных марок нержавеющих сталей, выпускаемых промышленностью, представлен в табл. 18.2. Основными классами нержавеющих сталей являются мартенситный, ферритный и аустенитный. [c.296]
Мартенситные стали получили название по аналогии с мар-тенситной фазой углеродистых сталей. Мартенсит образуется при фазовом превращении сдвигового типа, происходящем при быстром охлаждении стали (закалке) из аустенитной области фазовой диаграммы, для которой характерна гранецентрированная кубическая структура. Мартенсит определяет твердость закаленных углеродистых сталей и мартенситных нержавеющих сталей. Нержавеющие стали этого класса имеют объемно-центрированную кубическую структуру они магнитны. Типичное применение — инструменты (в том числе и рёжущие), лопатки паровых турбин. [c.296]
Несмотря на то что нержавеющие стали и сплавы созданы специально для эксплуатации в различных агрессивных средах, их коррозионная усталость изучена меньше, чем углеродистых сталей. В ранних работах, выполненных в 20-х годах Мак Адамом и другими исследователями, показано, что нержавеющие стали хорошо сопротивляются коррозионноусталостному разрушению в пресной воде и ее парах, 3 %-ном растворе Na I, а также других сравнительно малоагрессивных средах. Однако некоторые нержавеющие-стали, например мартенситного класса, обладая высокой коррозионной стойкостью в ненапряженном состоянии, имеют низкое сопротивление коррозионной усталости. Часто условный предел коррозионной выносливости этих сталей такой, как и обычных углеро- [c.58]
На основании анализа опубликованных данных можно заключить, что обработка поверхности роликами увеличивает предел выносливости образцов из углероди- Tbix, низколегированных и нержавеющих мартенситных сталей при циклическом изгибе на 20-30 %, а образцов с концентратором напряжения - на 100 % и. выше. Более эффективна обкатка для деталей, работающих на циклический изгиб и растяжение-сжатие и менее эффективна — для деталей, подвергнутых циклическому кручению. [c.158]
Большинство источников указывает на то, что полуферритные и ферритные хромистые стали практически не подвержены коррозионному растрескиванию в растворах хлоридов. Хромистые же стали, имеющие мартенситную структуру, подвержены коррозии под напряжением. Между коррозионным растрескиванием аустенитных и мартенситных сталей имеется определенное различие. В аустенитных сталях растрескивание интенсифицируется при анодной поляризации, а в мартенситных — катодной. Последнее обстоятельство позво-ляетпредположить, что растрескивание мартенситных сталей связано а водородной хрупкостью. При наличии катодной поляризации увеличивается скорость выделения водорода и интенсифицируется коррозионное растрескивание мартенситных сталей. Контакт с более электроотрицательным металлом, например алюминием, также ускоряет процесс растрескивания мартенситных сталей. При растрескивании стали 410 (12—13% хрома) разрушение распространяется вдоль неотпущенного мартенсита по граням прежних аустенитных зерен. Отпуск при температуре 635° С снижает склонность стали к коррозионному растрескиванию [111,156]. Д. С. Поль [111,36] считает, что ферритные и мартенситные стали с низкой твердостью не склонны к коррозионному растрескиванию под напряжением в воде высокой частоты при температуре до 300° С. Мартенситные же нержавеющие стали, закаленные до твердости Ядс= 30, коррозионному растрескиванию в этих условиях подвержены. Хромистые стали, так же как и малолегированные и аустенитные нержавеющие стали. [c.177]
Высокая способность противостоять эрозионно-усталостному разрущению при микроударных воздействиях. Это свойство в большой степени зависит от природы сплава, его структуры и фазового состава (Л. 4. Наибольшей стойкостью против эрозионного разрушения обладают нержавеющие стали с мартенситной структурой, наименьшей— с ферритной. Эрозионная стойкость сталей с аусте-нитной структурой зависит от природы и свойств аусте-нита и его способности к упрочнению при пластических деформациях. [c.79]
В высоколегированных сталях (быстрорежущие, мар-тенситно стареющие нержавеющие мартенситные стали и др ) структурная наследственность проявляется в щиро ком диапазоне скоростей нагрева, т е не только при быст ром и медленном нагреве, но и при промежуточных уме ренных скоростях нагрева Следовательно, в таких сталях структурная наследственность наблюдается в обычно при нятых на практике условиях нагрева, так как восстанов ленное зерно аустенита длительное время не рекристалли зуется Так, при повторном нагреве под закалку быстроре жущей стали независимо от скорости нагрева при аустени тизации происходит восстановление исходного зерна и наблюдается нафталинистый излом В мартенситно старею щих сталях восстановление крупного зерна происходит при обычной технологии их термической обработки [c.79]
Обычно оборудование для этого процесса выполняется из углеродистой стали, лричем нержавеющая сталь используется только в ответственных узлах. Найдено, что хромникелевые нержавеющие стали достаточно стойки, однако они склонны к коррозионному растрескиванию в этих средах. По этой причине использование в этих случаях хромовых нержаве10щих сталей, имеющих мартенситную или ферритную структуру, сопряжено со значительными проблемами. [c.90]
Состав 2 рекомендуется для травления чугуна, углеродистых и инструментальных сталей [115]. Метабисульфит калия растворяют перед травлением. Результаты травления (10—60 сек) аналогичны описанным выше. Для более глубокого травления следует повторное травление без переполировки. В процессе травления образец нужно сильно встряхнуть, чтобы на поверхности шлифа не образовалась пленка сернистого железа, растворяюшаяся в соляной кислоте. По окончании травления образец оставляют неподвижным в растворе до появления осадка, затем промывают и высушивают. С помощью состава 2 можно изучать субструктуру и линии скольжения в различных чугунах и сталях, включая мартенситные нержавеющие стали. [c.32]
Сталь мартенситного класса с повышенным содержанием углерода и высоким содержанием легирующих элементов редко применяется в машиностроении из-за плохих технологических качеств (затруднения при обработке резанием). К ней относится хромистая нержавеющая сталь с мартенситной структурой, содержащая 13% Сг, и высоколегированные марки хромоникелевольфрамовой стали, принимающие закалку при охлаждении на воздухе. [c.296]
Важное значение для практики применения стали 08Х15Н5Д2Т и других нержавеющих мартенситно-стареющих сталей имеет деформационное старение. [c.151]
В работе [121] описываются свойства нержавеющей мартенситно-стареющей стали Х12Н10Д2ТБ, содержа-щейизготовлению упругих элементов. Закалка стали производится с 870°С, т. е. с температуры, практически достаточной для растворения в аустените избыточных фаз. После закал- [c.160]
Важным преимуществом безуглеродистых нержавеющих мартенситно-стареющих сталей является более высокая статическая выносливость по сравнению с обычными среднелегированньши высокопрочными сталями. Так, например, надрезанные образцы (ак = 2,2) из Сг—N1— [c.165]
Рис. 51. Изменение предела текучести нержавеющих стаяеВ при изменении класса стали от мартенситного в переходный и аустенитный (схема) | ![]() |
Изготовление соединений с применением клея ВК 7. Изготовление клее-сварных соединений с применением клея ВК7 возможно по обоим технологическим вариантам. Однако наилуч-шие результаты дает второй вариант, при котором клей вводится в зазор соединения после сварки. Опробование клея ВК7 в клее-сварных соединениях производилось на различных образцах и опытных панелях из сплава Д16Т толщиной 1,5+1,5 и 2 + 2 мм п нержавеющей стали аустенито-мартенситного класса типа СП толщиной 1,2 +1,2 мм. Образцы и панели сваривали на машинах с импульсом постоянного тока МТПТ 600 и переменного тока МТП 200. [c.114]
Сварка высокохромистых нержавеющих сталей ферритного, мартенситного и феррито-мартенситного типов марок 1X13, Х17, ОХ17Т и др. выполняется двумя способами. [c.238]
Некоторые металлы растрескиваются, находясь в напряженном состоянии в агрессивных средах, и при этом коррозия не является необходимым условием ни для зарождения трещины, ни для ее последующего роста. В таких случаях термин коррозионное растрескивание не вполне подходит, несмотря на некоторое сходство этих явлений. Например, нержавеющая мартенситная сталь с 12% Сг в напряженном состоянии, погруженная в разбавленный раствор Nad, может растрескаться после выдержки в течение нескольких месяцев. У той же стали при погружении в разбавленную серную кислоту растрескивание может произойти за время меньше 5 мин. В обоих случаях разрушение по внешнему виду сходно с коррозионным растрескиванием, однако при катодной поляризации сплава трещины продолжают появляться (иногда даже через меньший промежуток времени). Катодная поляризация при прочих одинаковых условиях устраняет коррозионное растрескивание аустенитных сталей в кипящем растворе Mg la. Кроме того, при добавлении в кислоту каталитических ядов , [c.115]
В дальнейшем эта теория была развита в общую теорию выделения структурных составляющих [10]. Отличительной чертой последней является положение о том, что значительные местные напряжения, ускоряя выпадение избыточной составляющей сплава, ускоряют тем самым процесс образования местных гальванических элементов. Трещины увеличиваются за счет растворения вновь образующихся анодных участков. В мягкой стали такой составляющей (выделяющейся фазой) служит нитрид железа, в аустенитных нержавеющих сталях — продукты мартенситного распада. Теория выделения избыточных составляющих сплавов объясняет также процесс травления под напряжением в том смысле, что ускоренная коррозия может происходить на гетерогенных макроучастках, образующихся при выделении избыточных составляющих под влиянием деформации. [c.600]
mash-xxl.info
Способ термической обработки нержавеющих сталей мартенситного класса
Изобретение относится к металлургии, в частности к способам термической обработки сталей. Целью изобретения является повышение ударной вязкости при отрицательных температурах и снижение критической температуры хрупкости стали. Предлагаемый способ включает нормализацию и двукратный отпуск первый отпуск проводят при 675 - 695°С, второй отпуск при 500 - 600°С. Использование способа позволяет повысить ударную вязкость при отрицательных температурах и снизить вероятность хрупкого разрушения деталей. 2 табл.
СОЮЗ СОВЕТСКИХ
СОЦИАЛИСТИЧЕСНИХ
РЕСПУБЛИК (5l ) 5 С 21 1) 6/00
ОПИСАНИЕ ИЗОБРЕТЕНИЯ
Й АBTOPCHOMY СВИДЕТЕЛЬСТВУ
ГОСУДАРСТВЕННЫЙ. КОМИТЕТ
ПО ИЗОБРЕТЕНИЯМ И ОТКРЫТИЯМ
ПРИ ГКНТ СССР (21) 4395247/23 -02 (22) 26. 01 . 88 (46) 30.01 90. Бюл. М 4 (71) Научно-производственное объедиF нение по технологии машиностроения
ЦНИИТМАШ (72) Н.b. Непилов, Е.Г. Валов, А.Ф. Дегтярев, Л.)0. Гордюк, А.Г. Ковалев, 10.П. Минин и В.Т. Козлов (53) 621.785.79(088.8) (56) Авторское свидетельство ЧССР
Н 202815, кл. С 2! 1) б/00, 1980.
Авторское свидетельство СССР
И 458596, кл. С 21 и 1/78, 1971.
Изобретение относится к металлур" гии, в частности к способам термической обработки сталей, и может быть использовано для термической обработки сталей мартенситного класса, содержащих до 0,064 углерода, до 1(3 хрома и до 6/ никеля и др.,нприменяемых для изготовления лопастей и сварных рабочих колес гидротурбин.
Целью изобретения является повышение ударной вязкости стали при отрицательных температурах и снижение критической температуры хрупкости стали, Пример. Объектом испытаний являлся листовой прокат стали марки
06Х12НЗД, имеющий следующий химический состав, мас. : углерод 0,04; кремний 0,16,марганец 0,31; хром 12,8;никель 3 15; медь 0,94; сера 0,016;
ФосФор g 014; железо - остальное.
„„SU„„1539221 А 1
2 (54) СПОСОБ ТЕРМИЧЕСКОИ ОБРАБОТКИ НЕРЖАВЕ)0ЦИХ СТАЛЕЙ МАРТЕНСИТНОГО КЛАССА (57) Изобретение относится к металлургии, в частности к способам термической обработки сталей. Цель изобретения - повышение ударной вязкости при отрицательных температурах и снижение критической температуры хруп- кости стали, (1редлагаемый способ включает нормализацию и двукратный отпуск; первый отпуск проводят при 675-695 С, второй отпуск при 500-600 С. Использование способа позволяет повысить ударную вязкость при отрицательных температурах и снизить вероятность хрупкого разрушения деталей. 2 табл. с
С::
Сталь выплавляли в 50-тонной злектродуговой печи с разливкой s ковочные слитки, ковали и прокатывали на лист 150 мм. ь4
Металл листов разрезали на фаготов- (,Я ки 15х15 мм злектроискровым способом (д и подвергали термической обработке по различным режимам: двойная нормализация от температур 1100 и 8500С, о у р 675-695 500-600 С. Про/ должительность отпуска 6 ч.
Механические свойства определяли на разрывных образцах диаметром 6 мм и ударных образцах с радиусом надреза
0,25 мм. 3, Критическую температуру определяли по результатам испытания ударных образцов при температуре +20, -40, -80 С. В качестве критерия при опре- дЕлении критической температуры хруп1539221
Табл и ц а 1
Способ термиеской обработки (Предел текучести, МПа
Предел прочности, ИПа
ТемпеОтносит.
Относительное
Ударная вязкость, KCV Дж/см2 при температуре, С
Критическая температура хрупкости, С ра тура
1-го отпуска, С удл., ф суж., о
+20 -40 -80
1 редлагаемый: ормализация 11.00 и 850 С, 1-й отпуск 675-б РС, 2-й отпуск
500 С
67 5 127
139
66,0 135
65,7 139
64,8 131 62, о Т44
66 4 118 0 121
62,2 116
59, 6 127
753 858
786 874
827 933
826 918
Г97 95
66и
682 789
727 309
720 "77 965
938 1057
64 48 -50 Б 53 -55
66 56 -60
71 5о
75 52 -70
777 % -75
52 41 -30
% 1 3
60 44 -40
62 Ж 15
16,7
ll5|
17 9
Т7,4
15, 9.
15,5
17,0
16,2
Известный: нормализация
1100 и 85O Ñ, 1-й отпуск .620-6/O С, 2-й отпуск
500 С
6 0 654 789
67 4 98
Д7 Р09- 7,1 102
672 804 67 0 .88
650 3 94
670 739 819
66,8 122
7 9 9 83 > 66, 7 133
49 32
50 30
52 36
3F
59 46
-l0
-15
-20
-25
-40
--45
П р и м е ч а н и е. В числителе и знаменателе указаны минимальные и максимальные значения свойств. Окончательный отпуск 500 С. ости стали принимали значение ударной яэкости равное 60 Дж/см2.
Проведение в предлагаемом способе первого отпуска при 675-695 С, вместо
620-670 С в известном способе, приво ит к полному устранению отпускной хрупкости стали и к образованию в структуре за счет обратного с(у превращения 90-95 ь метастабильного аустенита, против 25-853 в способе-прототипе, который превращается полностью мартенсит при охлаждении и создает азовый наклеп, в результате чего поышается ударная вязкость при отрицаельных температурах и снижается криическая температура хрупкости стали.
При понижении температуры первого тпуска в предлагаемом способе ниже нижнего предела уменьшится: в процессе обратного d у превращения объем образовавшегося метастабильного аустенита, что приведет .к образованию при охлаждении меньшего обьема мартенсита 25 с меньшей степенью фазового наклепа, в результате чего понизится ударная вязкость стали. При понижении температуры отпуска ниже 650 С уменьшится растворимость сегрегаций вредных примесей на границах зерен и проявится отпускная хрупкость стали.
Повышение температуры первого отпуска в предлагаемом способе выше верхнего предела полностью переводит сталь в аустенитное состояние, а также интенсифицирует процесс коагуляции карбидной фазы, что приводит к огрублению границ зерен, снижению ударной вязкости и повышению критической температуры хрупкости стали.
В табл. 1 и 2 приведены конкретные режимы термообработки, механические свойства и критические температуры хрупкости стали 06Х12НЗД после предлагаемого и известного способов термической обработки (двойная нормализация от 1100 и 850 C (и отпуск при
620-670 и 500-600 С, 6 ч).
1539221
Т а б л и ц а 2
Предел прочн., МПа
Способ термической обработки
Тем-ра
1-го
Предел текуч., МПа
Относи- Относительное тельное
Ударная вязкость, KCV, Дж/см2, при
Критич. темпер. хруп. оС отпуска, OC удлин., сужен., о
+20 С -40 С -80 С
Предлагаемый: нормализация
1100 и 850 С, 1-й отпуск
675-695 С, 2-й отпуск
&00 С
17,4
11F
-80
--85
57
675
-85
-90
59., Г7
И
17,7
1ТЛ
18,4 l,1
685
-95
695
49
-60"
- 65
19,2
ill,1
660
-75 17 5
, 3
720
33
-15
-20
62о
Известный: нормализация
1100 и 850 С, 1-й отпуск
620-6?о с, ?-й отпуск
600 С
634 . 732
6 7 73
656 - 757
662
136. 68
137 70
147 85
llE 35
47
7о 1
70,9
-50
-55
68,8
676
17,7
16,9
-70
-75
57
П р и м е ч а н и е. В числителе .и знаменателе указаны минимальные и максимальные значения свойств. Окончательный отпуск 600 С.
I плуатационной надежности приблизитель" но на 10i, что увеличивает межремонтный период на ГЭЕ с 4,5 до 5 лет. формула изобретения
Способ термической обработки нержавеющих сталей мартенситного класса, включающий нормализацию и двухкратный отпуск с температурой второго отпуска 500 600 С, о т л и ч а ю щ и йс я тем, что, с целью повышения ударной вязкости при отрицательных температурах и снижения критической температуры хрупкости стали, первый отпуск проводят при 675-695 С.
Составитель. В. Русаненко
Техред М.Ходанич : Корректор С аекмар
Редактор Т. Лазоренко
Заказ 192 Тираж 504 Подписное
ВНИИПИ Государственного комитета по изобретениям и открытиям при ГКНТ СССР 113035, Москва, Ж-35, Раушская наб., д. 4/5
Производственно-издательский комбинат ".Патент", г.Ужгород, ул.Гагарина, 101
664 763
ТГГ 7?о
672 769
689 776
692 7772
648 738
657 744
696 ?84
7077 799
636 762
649 ?И9
Как видно из результатов табл. 1 и 2, предлагаемый способ термической обработки обеспечивает ударную вязкость при отрицательных температурах выше, а критическую температуру хруп.кости стали ниже, чем по известному 40 способу термической обработки при. сохранении механических свойств практически на одинаковом уровне.
Использование предлагаемого способа термической обработки стали при из-45 готовлении отливок лопастей поворотно" лопастных гидротурбин и сварных рабочих колес радиально-осевых гидротур-. бин приводит к снижению вероятности хрупкого разрушения и повышению экс- 50
69,3
ГГ;!
68,4
oOo, l
67,4
66,7
69,8
69Л
65 8 1
67,7 9
149 89
Т58 92
149 90
156 96
154 95 . l 59 9 "
142 72
146 76
147 78
151 3
104 46
108 49



www.findpatent.ru